浅析压力容器分析设计的塑性措施
压力容器设计制造的问题及解决对策

压力容器设计制造的问题及解决对策压力容器是一种用于储存或运输压缩气体或液体的设备,其设计和制造质量直接关系到人们的生命财产安全。
在压力容器的设计和制造过程中,可能会遇到各种问题,这些问题可能对压力容器的安全性和可靠性造成严重影响。
为了确保压力容器的设计和制造质量,需要针对可能出现的问题提出对策并加以解决。
压力容器设计制造过程中可能存在的问题包括材料选择、几何尺寸设计、焊接工艺、非破坏检测以及使用条件等方面。
在材料选择方面,压力容器的材料应具有良好的可焊性、蠕变性、韧性和抗腐蚀性能,同时还要考虑其价格和可获得性等因素。
解决这一问题的对策包括严格按照材料标准选择合适的材料、加强对材料供应商的质量管理,并进行材料的质量检测。
在几何尺寸设计方面,压力容器的设计应符合国家相关标准和规范,同时还要考虑到容器的强度、刚度、密封性等方面。
解决这一问题的对策包括开展力学计算和有限元分析、进行应力、应变的模拟和实测测定。
在焊接工艺方面,焊接是压力容器制造中一个重要环节,焊接质量直接关系到压力容器的安全性。
解决这一问题的对策包括严格按照焊接标准和规范执行焊接工艺、加强焊缝的质量控制,并进行焊接缺陷的检测和修复。
在非破坏检测方面,压力容器的质量检验是制造过程中的重要环节,通过非破坏检测可以及时发现和排除容器内部的缺陷,保障容器的安全性和可靠性。
解决这一问题的对策包括选择合适的非破坏检测方法,进行全面和精细的检测,推广先进的非破坏检测技术。
在使用条件方面,压力容器的安全性和可靠性与使用条件密切相关,恶劣的使用条件可能导致压力容器的损坏和事故。
解决这一问题的对策包括严格执行使用规程和操作规范、加强容器的检测和监控,并进行定期的维护和检修。
除了解决这些问题之外,加强压力容器设计制造的管理和监督也是非常重要的。
企业应建立健全设计制造管理体系,划定责任和权限,并加强对全过程的管理和控制。
相关部门应加强对压力容器设计制造的监督和检查,确保设计制造过程的合规性和质量可控性。
浅谈压力容器设计中的常见问题及对策

浅谈压力容器设计中的常见问题及对策1. 引言1.1 背景介绍压力容器是工业生产中常用的装置,用于存储、运输或处理各种气体、液体或固体物质。
在压力容器设计过程中,常常会遇到一些问题,如果不加以注意和解决,可能会带来安全隐患和经济损失。
因此,对于压力容器设计中的常见问题及对策的探讨变得尤为重要。
在压力容器设计中,材料选择不当是一个常见的问题。
如果选择的材料强度不足或者耐蚀性差,容器可能会在工作过程中出现断裂或腐蚀现象,从而导致事故发生。
另外,设计计算不准确也是容易被忽视的问题之一。
如果设计计算不够精确,容器的承载能力可能无法满足实际工作条件,导致容器失效。
此外,几何形状不合理和操作条件考虑不周也会影响压力容器的安全性和稳定性。
为了解决这些问题,需要严格控制材料选择,确保选用符合标准和要求的材料。
同时,进行精确的设计计算,确保容器在工作过程中能够承受各种力的作用。
优化几何形状也是提高容器稳定性的重要措施,可以减少应力集中和减轻负荷。
最后,充分考虑操作条件,包括温度、压力、介质性质等因素,确保容器在各种工况下都能够正常工作。
通过有效地解决压力容器设计中的常见问题,可以提高容器的安全性和可靠性,保障工业生产过程的顺利进行。
在面对不断增长的工业需求和严格的安全要求下,压力容器设计师需要不断总结经验,不断改进设计方法,以确保压力容器的质量和安全性。
2. 正文2.1 压力容器设计中的常见问题在压力容器设计中,常见问题包括材料选择不当、设计计算不准确、几何形状不合理、以及操作条件考虑不周等方面。
材料选择不当可能导致压力容器的强度不足或耐久性不足,从而造成安全隐患。
设计计算不准确可能导致压力容器在使用过程中出现失效或漏气等问题。
几何形状不合理可能导致应力集中、疲劳破坏等问题,影响压力容器的使用寿命。
操作条件考虑不周可能导致压力容器在实际操作中受到过大的压力或温度变化,从而影响其安全性和稳定性。
对策包括严格控制材料选择,确保选择符合压力容器设计要求的材料;精确进行设计计算,确保设计计算符合相应标准和规范;优化几何形状,避免应力集中和疲劳破坏;充分考虑操作条件,确保压力容器在不同操作条件下的安全性和稳定性。
压力容器制造过程中变形问题的控制对策分析

压力容器制造过程中变形问题的控制对策分析压力容器是工业生产中不可或缺的设备之一,它的制造涉及到多个工艺环节,其中变形问题在制造过程中不可避免。
变形问题严重影响了产品的质量,更具有安全隐患。
因此,通过对变形问题进行分析与控制,对提高产品质量和安全性具有重要作用。
压力容器的变形问题主要包括壁厚偏差、圆度误差、直线度误差、端面平行度误差等。
造成变形问题的原因主要有以下几方面:一是材料本身的特点,不同的材料在受到外力或加工过程中的变形特点不同。
例如铝合金的塑性大,容易产生变形。
二是制造工艺的工艺参数调节不当。
例如,焊接温度过高或者过低,焊接速度过快或者过慢,焊接角度不合适,都会导致容器的变形。
三是生产设备的问题。
设备的精度不高、设备的磨损以及设备的调试不当等问题都可能导致容器的变形。
针对以上问题,可以采取以下控制对策:一是合理选材。
生产压力容器需要选用合适的材料,合理控制材料的性能,以减小变形的发生。
二是严格控制生产工艺。
生产中需要对工艺参数进行严格控制,对于焊接温度、速度、角度、压力等参数进行监测和控制。
三是加强设备维护。
坚持定期检修、保养,确保设备正常操作,从而保证生产过程中的精度和稳定性。
四是应用数控技术。
数控技术可以大大提高生产过程中的精度和稳定性,减小变形的产生。
总之,控制压力容器制造中的变形问题是提高产品质量和安全性的有效措施。
只有在加强材料选择、严格控制生产工艺、加强设备维护和应用数控技术等方面,才能减小变形的产生,保证产品的质量和安全性。
压力容器接管区应力集中弹塑性有限元分析

压力容器接管区应力集中弹塑性有限元分析压力容器在石油化工企业生产过程中是一种非常常见的设备,压力容器设备具有储存液体、气体的作用。
压力容器主要包括:储运容器、反应容器、热换器以及分离器。
压力容器接管区的主要目的是为了符合工艺需求,但是也造成接管区出现复杂的应力状态,通过对压力容器接管区应力进行对比和分析,在掌握压力容器的筒体、接管以及连接部位应力状况的基础上,对比压力容器接管区应力集中弹性塑形变化,并提出相关的解决措施,能够有效提高压力容器接管区的强度。
不断对压力容器进行改进,使压力容器的设计,制造,检验以及使用等环节都能得到充分保障,实现了压力容器的迅速发展。
标签:压力容器;应力集中;有限元分析压力容器是一种广泛应用于石油化工企业的常用设备,压力容器由于结构和工艺要求存在差异性,一般情况下需要进行开孔装接管。
但是压力容器在运行过程中具有突变的几何形,在接管区域往往会形成不连续的应力变化,导致接管区出现应力集中的情况,引起压力容器局部发生高应力现象,因此,需要利用有限元分析开孔接管区的应力集中变化,确保压力容器能够安全运行。
一般情况下,压力容器接管器具有复杂的应力状况,导致该现象的原因主要包括:第一,对压力容器进行开孔会对容器壳体造成破坏,缩小容器承载面积,导致压力容器边缘接管区域出现应力集中。
第二,压力容器接管区会出现断层性结构,接管区域和壳体在受到内压影响下会发生变形,在协调变形中会出现边缘应力,因此,需要利用有限元分析法进行压力容器应力集中计算。
1模型的有限元分析1.1几何模型机载荷在进行模拟过程中使用有限元模型主要是根据压力容器的结构特性和荷载特征。
但是在实际应用过程中,压力容器的结构特征和载荷特征为轴对称,因此在实验过程中,可以在对称面施加一定的对称约束力,并且在接管端不施加轴向移位约束,并对压力容器的筒体以及接管区域施加压力载荷,可以忽略重力及外压对计算结果的影响。
1.2网格划分基于仅是对于在内压作用下接管应力的研究,因此针对这些情况,可以实行结构对称性应用,利用有限元模型对接关系进行建模,接管除外伸长度与筒体长度都要比起边缘应力缩减长度要大。
压力容器设计制造的问题及解决对策

压力容器设计制造的问题及解决对策压力容器是一种用来贮存液体或气体的设备,广泛应用于化工、石油、医药、食品等行业。
在压力容器的设计与制造中,存在一些问题需要解决,以保证容器的安全使用。
1. 材料选择问题:压力容器需要根据储存介质的性质和工作条件选择合适的材料。
如压力容器在高温、高压下工作时,需要选择耐高温、耐腐蚀的材料。
解决对策是仔细分析介质特性和工作条件,选择合适的材料。
2. 结构设计问题:压力容器的结构设计需要符合力学原理和工程要求,以承受内部压力和外部载荷的作用。
特别是在复杂工况下,如地震、爆炸等,需要特别关注结构的强度和稳定性。
解决对策是通过合理的结构设计和分析,确保容器在各种工况下的安全运行。
3. 缺陷检测问题:压力容器制造过程中可能存在缺陷,如焊接缺陷、材料内部缺陷等。
这些缺陷可能导致容器在使用过程中发生泄漏或破裂,造成严重的安全事故。
解决对策是对制造过程进行质量控制,使用非破坏性检测技术,如超声波、射线等,对容器进行检测和评估。
4. 压力控制问题:压力容器的工作压力需要得到有效的控制,避免超过容器的承载能力。
解决对策是安装合适的压力控制设备,如安全阀、压力表等,对容器的内压进行监测和控制,避免超压导致事故发生。
5. 检修与维护问题:压力容器在使用一段时间后,需要进行定期的检修和维护,以确保容器的安全性能。
解决对策是建立完善的检修与维护制度,定期对容器进行检查、清洗、维修和更换损坏的部件,及时发现和解决潜在的问题。
6. 法律法规遵守问题:压力容器设计制造需要符合相关的法律法规,如压力容器安全技术监察条例、设备制造许可证等。
解决对策是加强对法律法规的宣传和培训,确保设计制造过程合法合规。
压力容器设计制造的问题主要包括材料选择、结构设计、缺陷检测、压力控制、检修与维护以及法律法规遵守等方面。
解决这些问题的对策是通过合理的工艺和技术手段,保证容器的安全使用,从而保障生产和人员的安全。
压力容器的弹塑性应力及可靠性分析

=
=
( u -P ) P- 1 n+
- R _ +丁 K n n C n 1 n
( 性) 鳢
式 中, 比;
1 风 分 别 为第 n层 内外 半径 , 一和 P 分 别为第 n层 内外 界面上 的压 力 。 为第 n层 外 内半径 和 l
为材料 体积 弹性模量 ;C 为 与材料 性 能相 关的量 。对于 双层 容器 ,当材 质不 同的两层 容器均 部分 进
采用基于均值和信息熵不变原则的随机一模糊参量转换方法及相应的随机可靠性方法或模糊可靠性方法可以同时对含随机模糊因素的厚壁压力容器的安全可靠性进行近似分析但随机方法更适用于随机特征更强的问题而模糊方法适用于模糊特征更强的问题
维普资讯
工
程
15 2
采用 基于 实数 编码 的遗传算 法对 复杂布 局 问题进 行求解 ,并对 实数编 码遗 传算 法进 行 改进 ,直接将 问
进行预处理,主要包括问题的简化、相关工程因素的处理等。求解过程 中,首先引入模拟退火算法的思想
对 中间过 程解 进行选 择 ,以防止算 法 出现 “ 熟 ” 象( 早 现 即防止算 法 出现 超级 个体 而导 致其控 制整个 进化群
体) ;然后 对离 散变量 采用 直接交 叉 的方法 ,对 离散变 量 采用整 体算 术交 叉 的方法 ,并 在连 续变 量变 异前对 其 随机加 一 个扰动 量 ,以控 制其搜 索 范 围;在算法 进化 过程 中 ,对求 解 的中 间结果 按最优 保 留策略进行 处
可靠性 分析 ,将 问题 中的模 糊参 量等 效转 换为 随机参 量 ,再与强度 极 限结合 ,得 容器 可靠度 为 9. %。同 54 5 样按 “ 均值 ”和 信息熵 不变 原则 ,将 问题 中的随 机参量 等效 转换 为正态 型模 糊参量 ,再利用 水平截集 法,
浅谈压力容器制造过程中存在的问题及相应解决措施
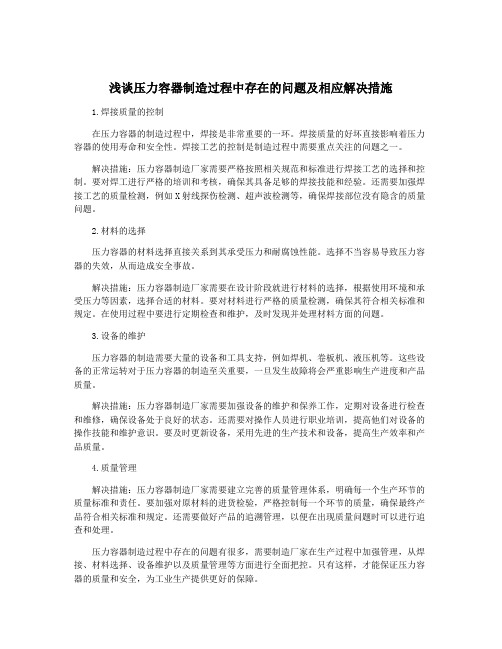
浅谈压力容器制造过程中存在的问题及相应解决措施1.焊接质量的控制在压力容器的制造过程中,焊接是非常重要的一环。
焊接质量的好坏直接影响着压力容器的使用寿命和安全性。
焊接工艺的控制是制造过程中需要重点关注的问题之一。
解决措施:压力容器制造厂家需要严格按照相关规范和标准进行焊接工艺的选择和控制。
要对焊工进行严格的培训和考核,确保其具备足够的焊接技能和经验。
还需要加强焊接工艺的质量检测,例如X射线探伤检测、超声波检测等,确保焊接部位没有隐含的质量问题。
2.材料的选择压力容器的材料选择直接关系到其承受压力和耐腐蚀性能。
选择不当容易导致压力容器的失效,从而造成安全事故。
解决措施:压力容器制造厂家需要在设计阶段就进行材料的选择,根据使用环境和承受压力等因素,选择合适的材料。
要对材料进行严格的质量检测,确保其符合相关标准和规定。
在使用过程中要进行定期检查和维护,及时发现并处理材料方面的问题。
3.设备的维护压力容器的制造需要大量的设备和工具支持,例如焊机、卷板机、液压机等。
这些设备的正常运转对于压力容器的制造至关重要,一旦发生故障将会严重影响生产进度和产品质量。
解决措施:压力容器制造厂家需要加强设备的维护和保养工作,定期对设备进行检查和维修,确保设备处于良好的状态。
还需要对操作人员进行职业培训,提高他们对设备的操作技能和维护意识。
要及时更新设备,采用先进的生产技术和设备,提高生产效率和产品质量。
4.质量管理解决措施:压力容器制造厂家需要建立完善的质量管理体系,明确每一个生产环节的质量标准和责任。
要加强对原材料的进货检验,严格控制每一个环节的质量,确保最终产品符合相关标准和规定。
还需要做好产品的追溯管理,以便在出现质量问题时可以进行追查和处理。
压力容器制造过程中存在的问题有很多,需要制造厂家在生产过程中加强管理,从焊接、材料选择、设备维护以及质量管理等方面进行全面把控。
只有这样,才能保证压力容器的质量和安全,为工业生产提供更好的保障。
浅谈压力容器制造过程中存在的问题及相应解决措施

浅谈压力容器制造过程中存在的问题及相应解决措施压力容器是工业生产中常见的一种设备,用于储存和输送气体或液体,并承受内部的压力。
在化工、石油、医药、食品等领域都有广泛的应用。
在压力容器的制造过程中,由于材料、工艺、设计等方面的因素,会出现一些问题,影响其质量和安全性。
解决这些问题是非常重要的。
本文将从材料选择、焊接工艺、质量控制等方面,浅谈压力容器制造过程中存在的问题及相应的解决措施。
一、材料选择问题1.材料强度不足:在制造压力容器时,选择材料的强度不足,可能导致在受到内部压力时产生变形或破裂。
解决措施:在材料选择时,必须严格按照相关标准和规范,选择符合要求的材料,同时要进行充分的材料强度计算和验证。
2.材料腐蚀问题:在一些特殊的工作环境下,压力容器会遭受腐蚀,导致材料的性能下降,甚至产生裂纹。
解决措施:在选择材料时,必须考虑到工作环境的特殊性,选择耐蚀性好的材料,并在制造过程中做好表面涂层保护。
二、焊接工艺问题1.焊接变形:在焊接过程中,由于温度变化引起的材料变形,可能会使压力容器的结构产生缺陷。
解决措施:采用合适的焊接方法和工艺参数,控制焊接温度和预热温度,采取合适的焊接顺序和焊接顺序等措施,减小焊接变形。
2.焊接裂纹:在焊接过程中,由于焊接质量不合格或热应力引起的裂纹,会导致压力容器的安全性下降。
解决措施:进行合格的焊工培训,掌握良好的焊接技术,采用适当的预热和后热处理工艺,保证焊接质量。
三、质量控制问题1.内部缺陷:在压力容器内部产生缺陷(如气孔、夹杂等),可能导致结构疲劳破坏或爆炸事故。
解决措施:采用适当的无损检测方法对压力容器进行全面检测,及时发现和修复内部缺陷。
2.尺寸偏差:在制造过程中,由于加工、装配等环节的误差,可能导致压力容器的尺寸偏差较大。
解决措施:严格控制每个环节的加工精度,采用合适的检测仪器对尺寸进行测量,做好记录和标识。
四、运输安装问题1.运输损坏:在压力容器运输过程中,由于操作不当或外部环境因素,可能导致容器结构损坏。
浅谈压力容器设计中的常见问题及对策

浅谈压力容器设计中的常见问题及对策压力容器是工业生产中常见的设备,用于加工、储存和输送各种气体、液体和粉末。
它们承受着高压、高温或低温等复杂的工作环境,因此在设计和制造过程中要特别注意安全性和可靠性。
在压力容器设计中常常会遇到一些问题,下面就让我们来浅谈一下这些常见问题及对策。
一、焊接质量问题焊接是压力容器制造过程中最关键的环节之一,焊接质量直接影响着容器的安全性和可靠性。
常见的焊接质量问题包括焊接缺陷、焊接接头设计不合理和焊接接头处的应力集中等。
为了解决这些问题,首先应该加强焊工的技术培训,提高他们的焊接水平和质量意识;其次要严格控制焊接工艺参数,确保焊接质量符合标准要求;最后要设计合理的焊接接头结构,减少应力集中并提高接头的疲劳寿命。
二、材料选择和损伤问题压力容器的材料选择直接关系到其抗压性能和耐腐蚀性能。
选择不当或材料损伤都会导致容器失效。
为了避免这些问题,首先应该在设计阶段就对材料进行严格筛选和检测,确保材料符合要求;其次要加强对材料的管理和保养,及时发现并处理材料损伤问题;最后要严格按照材料的使用规范来设计和制造压力容器,确保其安全性和可靠性。
三、安全阀和压力表问题安全阀和压力表是压力容器的重要保护装置,它们直接关系到容器的安全运行。
常见的问题包括安全阀和压力表的选择不当、安装位置不合理和维护不及时等。
为了解决这些问题,首先应该对安全阀和压力表的性能和使用要求有清楚的了解,确保其选择和安装符合标准要求;其次要加强对安全阀和压力表的维护保养,及时发现并处理问题;最后要加强对安全阀和压力表的使用管理,确保其在容器运行过程中起到应有的作用。
四、设备结构设计问题压力容器的结构设计直接关系到其承压性能和使用寿命。
常见的结构设计问题包括受力分析不合理、结构尺寸设计不合理和支撑方式选择不当等。
为了解决这些问题,首先应该加强对设备结构设计的理论研究和实践经验总结,确保设计合理性;其次要加强对设备结构的计算分析,确保其受力性能符合要求;最后要结合实际情况对设备结构进行合理优化,确保容器的安全运行。
压力容器设计制造的问题及解决对策

压力容器设计制造的问题及解决对策压力容器是一种常见的工艺设备,在化工、医药、食品等行业都有广泛应用。
随着工业发展的迅猛,压力容器的设计制造也面临着一些问题和挑战。
本文将探讨压力容器设计制造中存在的问题,并提出相应的解决对策。
一、设计问题1.材料选择不当。
压力容器的制造材料通常是金属材料,而不同的工作条件对压力容器材料的性能要求也不同。
选材不当可能导致容器在工作过程中出现失效或事故。
解决对策:对于不同工作条件下的压力容器,应根据具体情况选择合适的材料,并对材料进行充分的测试和验证,确保其符合设计要求。
2.设计强度不够。
在使用压力容器的过程中,可能会受到内部或外部的压力,如果设计强度不够,就会存在安全隐患。
解决对策:在设计压力容器时,必须充分考虑各种工作条件下的压力情况,进行强度计算和模拟分析,确保设计的容器具有足够的强度和稳定性。
3.焊接质量不合格。
焊接是压力容器制造中不可或缺的工艺,焊接质量直接影响到容器的使用性能和安全性。
解决对策:在焊接过程中,必须严格按照相关规范和标准进行操作,保证焊接质量符合要求。
对焊接接头进行全面的检测和检验,确保质量合格。
二、制造问题1.工艺方面存在缺陷。
在压力容器的制造过程中,可能会出现工艺方面的不足,例如工艺流程不合理、设备不足等问题,影响容器的制造质量。
解决对策:在制造过程中,应充分合理规划工艺流程,确保每个环节都符合相关标准和要求。
对关键工艺环节进行监控和控制,及时发现和解决问题。
2.质量管理不到位。
如果在压力容器的制造过程中质量管理不到位,就很容易出现质量问题,导致产品的安全性和可靠性受到影响。
解决对策:建立完善的质量管理体系,对每个制造环节进行严格的控制和管理,确保产品质量满足设计要求。
三、技术问题1.缺乏相关技术人才。
压力容器的设计制造需要丰富的工程经验和专业知识,缺乏相关技术人才会影响产品质量和生产效率。
解决对策:加强人才培养和引进工作,培养一批具有丰富经验和专业知识的技术人才,确保能够满足压力容器设计制造的需求。
浅谈压力容器制造过程中存在的问题及相应解决措施
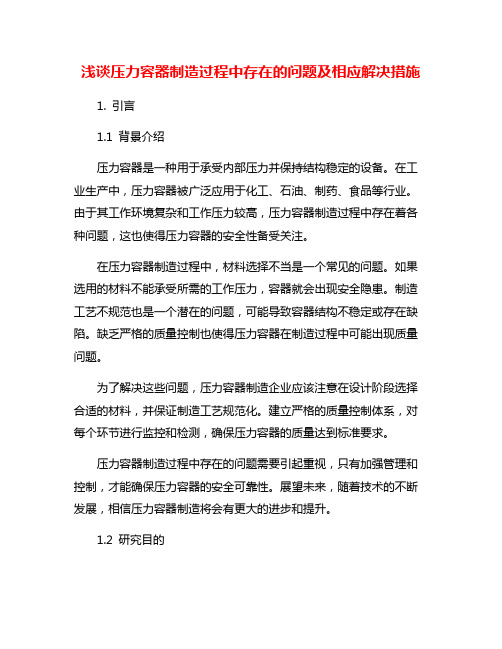
浅谈压力容器制造过程中存在的问题及相应解决措施1. 引言1.1 背景介绍压力容器是一种用于承受内部压力并保持结构稳定的设备。
在工业生产中,压力容器被广泛应用于化工、石油、制药、食品等行业。
由于其工作环境复杂和工作压力较高,压力容器制造过程中存在着各种问题,这也使得压力容器的安全性备受关注。
在压力容器制造过程中,材料选择不当是一个常见的问题。
如果选用的材料不能承受所需的工作压力,容器就会出现安全隐患。
制造工艺不规范也是一个潜在的问题,可能导致容器结构不稳定或存在缺陷。
缺乏严格的质量控制也使得压力容器在制造过程中可能出现质量问题。
为了解决这些问题,压力容器制造企业应该注意在设计阶段选择合适的材料,并保证制造工艺规范化。
建立严格的质量控制体系,对每个环节进行监控和检测,确保压力容器的质量达到标准要求。
压力容器制造过程中存在的问题需要引起重视,只有加强管理和控制,才能确保压力容器的安全可靠性。
展望未来,随着技术的不断发展,相信压力容器制造将会有更大的进步和提升。
1.2 研究目的研究目的是为了深入探讨压力容器制造过程中存在的问题及相应解决措施,通过对材料选择不当、制造工艺不规范、缺乏严格质量控制等方面进行分析和总结,为压力容器制造行业提供一些具体的改进建议和指导意见。
通过本研究,希望能够促进压力容器制造工艺的不断完善和提升,确保压力容器的安全性和可靠性,保障人民生命财产安全,推动我国压力容器制造行业的健康发展。
2. 正文2.1 压力容器制造过程中存在的问题在压力容器制造过程中,存在着诸多问题需要引起重视和解决。
材料选择不当是一个常见的问题。
由于一些厂家为了降低成本,使用劣质材料或者不符合标准的材料进行制造,导致容器的使用寿命大大缩短,甚至存在安全隐患。
制造工艺不规范也是一个常见问题。
一些制造企业为了赶工期或者降低成本,忽略了制造工艺的严谨和规范性,造成了制造过程中的各种质量问题,影响了容器的使用效果和安全性。
压力容器分析设计的塑性分析方法

支持 科研技 术人 员参 加压 力容器 学会 组 织的学 术交 流活 动 , 特从 这 次 学术会 议 交 流论 文 中挑 选 了数篇
文章 , 杂志上 刊登 , 在 以飨读 者 。
E up n set n& R sac ntue B in 0 0 3 C ia q imet np c o I i eerh Istt, e ig10 1 , hn ) i j
Absr t Plsi n lss meh d o e in b n l sso r su e v s esa e ito uc d a d r ve d t ac : a t a a y i t o sf rd sg y a ay i fp e s r e s l r n r d e n e iwe c
中 图分 类 号 : 6 1T 15 T一 5 ;B 2 文 献标 识 码 : A 文 章 编 号 :0 1— 8 7 2 1 ) 1 0 3 0 10 4 3 (0 1O ~ 0 3— 7
di1 .9 9 ji n 10 — 87 2 1. 10 7 o:0 3 6/.s .0 1 4 3 .0 10 .0 s
i hsp p r h ME Ⅷ 一2 2 0 s tk n a h il e o h nr d cin n h uo e n n ti a e .T e AS 0 7 i a e ste mani fte it u t .a d t e E rp a n o o
d ci n u to .
Ke r s:i t—la n lss ea t y wo d lmi o d a ay i ; lsi c—p a tc sr s nay i d r c o t d sg y a ay i fp e — lsi te s a l ss; ie tr u e; e in b n l ss o r s
浅谈压力容器设计中的常见问题及对策

浅谈压力容器设计中的常见问题及对策一、常见问题1. 异常温度在压力容器的运转过程中,由于介质温度异常升高或者降低,也会导致压力容器的变形或破裂。
温度异常的原因可能是介质的变化,也可能是周围环境的变化引起的。
2. 屈服屈服是指压力容器由于承受过大的外力,超出了其承载能力而导致变形或塑性变形。
长期的屈服容易导致压力容器的持久性损伤,降低其安全性能和使用寿命。
3. 疲劳疲劳是指压力容器长期受到循环外力的作用,容器壁发生裂纹和变形,严重时甚至可能导致裂纹扩展和破裂。
4. 腐蚀腐蚀是指压力容器在接触到腐蚀性介质时,材料表面发生化学反应,导致材料性质的变化。
腐蚀是导致压力容器损坏的主要原因。
5. 泄漏泄漏是指压力容器的密封性能不足,介质向外泄漏的现象。
泄漏可能是由于材料的缺陷、制造中的疏忽、操作不当等导致的。
二、对策1. 合理选择材料在压力容器的设计和制造过程中,材料的选择非常重要。
应根据压力容器的工作条件、介质性质和环境因素等,合理选择材料,例如使用高强度的材料、抗腐蚀的材料等,以提高压力容器的耐久性和安全性。
2. 优化结构设计在压力容器的设计过程中,应优化结构设计,增加压力容器壁厚,减小压力容器体积,减少压力容器的连接点以及减少压力容器的焊缝等,以提高其强度和耐久性能。
3. 严格控制制造过程良好的制造过程是保证压力容器质量和安全的关键。
应对制造过程加强质量控制和品质管理,从原材料的品质控制、生产工艺优化、检测手段完善等多方面入手加强管理,保证制造过程的稳定性和可控性。
4. 做好维护保养压力容器在使用过程中,需要定期进行维护保养。
应定期检查和更换容器内部的密封件、阀门等部件,保证设备的运行效率和安全性能。
5. 加强安全教育和培训压力容器是高危性设备,对于使用和维护人员进行安全教育和培训非常重要,需要全方位宣传安全知识,提高人员的安全意识和操作技能。
只有全面加强安全教育和培训,才能有效提升压力容器的安全性能和可靠性,确保生产过程中的安全和稳定。
压力容器设计制造的问题及解决对策

压力容器设计制造的问题及解决对策【摘要】压力容器在工业生产中扮演着至关重要的角色,但设计制造中存在一系列安全隐患。
本文从安全隐患、材料选择与制造工艺、老化和腐蚀问题、设计标准以及生产质量控制等方面进行了深入分析,提出了相应的解决对策。
针对存在的问题,本文建议采取严格的质量控制措施,加强材料科研与生产质量监管,提高设计标准的严谨性和完备性。
通过对压力容器设计制造问题的全面剖析和解决对策的提出,旨在进一步提高压力容器的安全性和可靠性,保障工业生产过程中的安全稳定。
展望未来,应加强科研与产业界的合作,促进压力容器行业的技术升级和创新发展,为工业生产提供更加可靠的设备保障。
【关键词】压力容器、设计、制造、安全隐患、材料选择、制造工艺、老化、腐蚀、设计标准、质量控制、问题、对策、发展方向。
1. 引言1.1 背景介绍压力容器是一种用于贮存或传递气体、液体或蒸汽等介质的设备,在化工、石油、医药、食品等行业广泛应用。
随着工业的发展和现代化生产的需求增加,对于压力容器的设计和制造要求也越来越高。
由于压力容器的特殊性和工作环境的复杂性,设计制造过程中往往会存在一些安全隐患和质量问题。
压力容器设计中存在的安全隐患主要包括设计不当导致的结构强度不足、焊接质量不合格、腐蚀等问题。
针对这些问题,可以通过加强材料的选择和制造工艺控制、增加厚度、采用适当的支撑和防护装置等方式来解决。
在压力容器的使用过程中,老化和腐蚀是一个普遍存在的问题。
要解决这一问题,可以采用定期检测和维护保养的方法,及时更换老化部件。
压力容器设计制造中存在的问题需要多方面的对策来解决,包括提高设计水平、加强质量控制、完善管理制度等方面。
只有不断改进和完善,才能确保压力容器在工业生产中的安全可靠运行。
结束。
1.2 问题概述压力容器是工业生产中常见的一种设备,用于承受内部或外部的压力,并在其中储存或处理液体、气体等物质。
压力容器设计制造中存在着一些安全隐患,给工作人员和环境带来潜在的风险。
压力容器设计制造的问题及解决对策
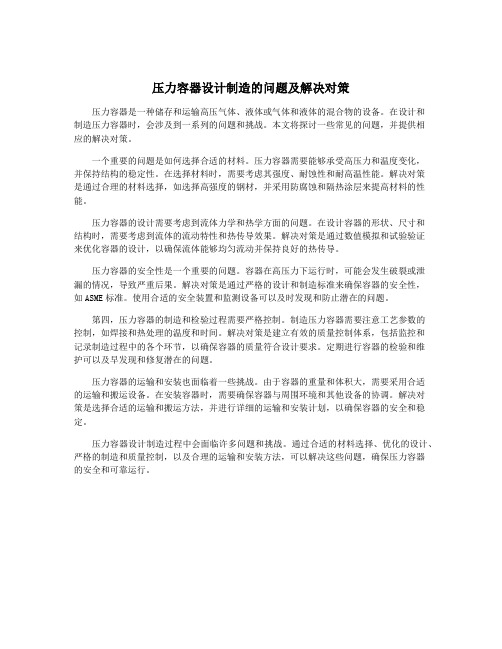
压力容器设计制造的问题及解决对策压力容器是一种储存和运输高压气体、液体或气体和液体的混合物的设备。
在设计和制造压力容器时,会涉及到一系列的问题和挑战。
本文将探讨一些常见的问题,并提供相应的解决对策。
一个重要的问题是如何选择合适的材料。
压力容器需要能够承受高压力和温度变化,并保持结构的稳定性。
在选择材料时,需要考虑其强度、耐蚀性和耐高温性能。
解决对策是通过合理的材料选择,如选择高强度的钢材,并采用防腐蚀和隔热涂层来提高材料的性能。
压力容器的设计需要考虑到流体力学和热学方面的问题。
在设计容器的形状、尺寸和结构时,需要考虑到流体的流动特性和热传导效果。
解决对策是通过数值模拟和试验验证来优化容器的设计,以确保流体能够均匀流动并保持良好的热传导。
压力容器的安全性是一个重要的问题。
容器在高压力下运行时,可能会发生破裂或泄漏的情况,导致严重后果。
解决对策是通过严格的设计和制造标准来确保容器的安全性,如ASME标准。
使用合适的安全装置和监测设备可以及时发现和防止潜在的问题。
第四,压力容器的制造和检验过程需要严格控制。
制造压力容器需要注意工艺参数的控制,如焊接和热处理的温度和时间。
解决对策是建立有效的质量控制体系,包括监控和记录制造过程中的各个环节,以确保容器的质量符合设计要求。
定期进行容器的检验和维护可以及早发现和修复潜在的问题。
压力容器的运输和安装也面临着一些挑战。
由于容器的重量和体积大,需要采用合适的运输和搬运设备。
在安装容器时,需要确保容器与周围环境和其他设备的协调。
解决对策是选择合适的运输和搬运方法,并进行详细的运输和安装计划,以确保容器的安全和稳定。
压力容器设计制造过程中会面临许多问题和挑战。
通过合适的材料选择、优化的设计、严格的制造和质量控制,以及合理的运输和安装方法,可以解决这些问题,确保压力容器的安全和可靠运行。
浅谈压力容器制造过程中存在的问题及相应解决措施

浅谈压力容器制造过程中存在的问题及相应解决措施【摘要】压力容器在工业生产中起着至关重要的作用,但其制造过程中存在着一系列问题。
本文将就材料选择不当、焊接质量、设计不合理以及检验过程中的问题进行分析,并提出相应的解决措施。
针对材料选择不当的问题,应注重材料的强度和耐腐蚀性,并进行全面评估选择合适材料。
对于焊接质量问题,应该严格按照规范执行焊接工艺,并加强工人的培训。
设计不合理问题可以通过引入先进的设计软件和更严格的设计审查来解决。
在检验过程中,应加强对检验人员的培训和购置更先进的检测设备。
加强质量管理意识、持续改进工艺技术以及严格执行相关标准和规范是确保压力容器制造质量的关键。
【关键词】压力容器、制造过程、问题、解决措施、材料选择、焊接质量、设计、检验、质量管理、工艺技术、标准、规范。
1. 引言1.1 压力容器的重要性压力容器是一种用于贮存及输送气体、液体或混合物的设备,扮演着重要的安全保障角色。
在工业生产中,压力容器承担着承受高压力、高温等极端条件下的重要任务,如化工、石油、电力、食品等领域都需要使用压力容器。
压力容器的安全性和可靠性直接影响到生产厂家和使用者的安全,一旦发生事故可能导致严重的人员伤亡和财产损失。
正确制造压力容器具有极其重要的意义。
压力容器的质量问题可能导致设备泄漏、爆炸等严重事故,因此制造过程中一定要严格按照相关标准和规范进行,确保质量可控、符合要求。
加强压力容器的质量管理,持续改进工艺技术,严格执行相关标准和规范,是确保压力容器安全可靠运行的重要保障措施。
通过提高制造过程中的质量管理水平,可以有效降低事故风险,保障压力容器在使用过程中的安全性和稳定性。
1.2 本文主要内容本文主要内容将围绕压力容器制造过程中存在的问题及相应解决措施展开讨论。
我们将探讨压力容器制造过程中常见的问题,包括材料选择不当、焊接质量问题、设计不合理以及检验过程中存在的问题。
针对这些问题,我们将提出相应的解决措施,包括正确选择合适的材料、加强焊接质量控制、优化设计方案以及改进检验流程。
浅谈压力容器制造过程中存在的问题及相应解决措施

浅谈压力容器制造过程中存在的问题及相应解决措施压力容器是一种用于储存或转运高压气体、液体或多相介质的设备。
其主要由壳体、封头、管道连接部分等组成。
在制造压力容器的过程中,可能会出现一些问题,比如材料选择、焊接缺陷、设计计算不足等。
为了确保压力容器的安全运行,需要采取相应的解决措施。
材料选择是制造压力容器时需要重点考虑的问题。
压力容器所使用的材料需要具备足够的强度和耐腐蚀性能。
解决方案是通过对不同材料的性能进行评估和测试,选择合适的材料。
要确保材料的供应渠道可靠,避免使用低质量或伪劣材料。
焊接缺陷是另一个制造压力容器时容易出现的问题。
焊接连接是压力容器的关键部分,焊接缺陷可能导致泄漏或断裂。
解决方案是采用合适的焊接工艺和技术,如自动化焊接、气体保护焊接等。
还需要对焊接接头进行严格的质量检验,包括焊缝的无损检测等。
设计计算不足也是制造压力容器时常见的问题之一。
设计计算的不足可能会导致容器的结构强度不足或者失稳。
解决方案是对压力容器的设计进行充分的强度和稳定性计算,在设计阶段充分考虑不同工况的影响,并进行相应的优化。
还需要遵守国家相关设计标准和规范,确保设计的合理性和安全性。
制造过程中还需要注意工艺控制、质量检验等方面的问题。
使用适当的工艺控制措施,如热处理、表面处理等,可以提高材料的性能和耐腐蚀性。
在质量检验方面,要对制造过程中的关键环节进行全面的检测和测试,确保产品的质量和安全性。
制造压力容器是一个非常复杂和严谨的工艺过程,需要充分考虑材料选择、焊接缺陷、设计计算等方面的问题。
只有在不同方面都进行合理的措施和规范的操作下,才能制造出安全可靠的压力容器。
压力容器分析设计的应力分类法与塑性分析法

压力容器分析设计的应力分类法与塑性分析法压力容器在石油化工行业的应用非常广泛,通过分析压力容器分析设计的应力分类法与塑性分析法的发展,可以实现压力容器应用前景的扩大,并为其良好运行提供参考意见。
进一步推动压力容器在石油化工行业的应用,有效提高压力容器的经济效益。
标签:压力容器;应力分类法;塑性分析法近年来很多研究学者对压力容器的工作原理、性能等方面进行研究,并取得了显著效果。
以往的压力容器在设计过程中,都是采用薄膜应力的方式进行设计,将其他应力影响包括在安全系数之中。
但是在实际应用过程中,压力容器及承压部件中,除去介质压力所形成的薄膜应力之外,还会受到热胀冷缩变形而导致的温差应力以及局部应力,因此,在进行压力分析设计时,需要利用应力分类法和塑性分析法,才能够明确不同应力对压力容器安全性的影响,从而有效提高压力容器的科学性和合理性。
1应力分类法1.1一次应力一次应力是指压力容器因为受到外载荷的影响,压力容器部件出现剪应力。
一次应力超过材料屈服极限时压力容器就会发生变形破坏。
主要可以分为以下几种情况:第一,总体薄膜应力。
因压力容器受到内压的影响在壳体上出现薄膜应力,总体薄膜应力会在整个壳体上均匀分布,当应力超过材料屈服极限时,壳体壁厚的材料会发生变形。
第二,局部薄膜应力。
是指压力容器的局部范围内,应受到机械载荷或者压力所导致的薄膜应力,其中主要包括支座应力以及力距所形成的薄膜应力。
第三,一次弯曲应力。
由于压力容器受到内压作用的影响,在平板盖中央位置会出现弯曲引力,随着载荷的不断增加,应力会进行重新调整。
1.2二次应力二次应力是指压力容器部件受到约束而出现的剪应力。
二次应力满足变形条件。
例如,在压力容器的半球形封头以及薄壁圆筒的连接位置,由于受到压力容器内压的作用,两者会出现不同的径向位移,因此两者的连接部位会形成相互约束关系,出现变形协调情况。
在这种情况下,连接部位会附加剪力应力,从而形成二次应力。
浅析压力容器分析设计的塑性措施

浅析压力容器分析设计的塑性措施浅析压力容器分析设计的塑性措施引言《压力容器》“压力容器应力分析设计方法的进展和评述” 力容器分析设计的弹性应力分析方法(又称应力分类法)一步介绍和评述压力容器分析设计的塑性分析方法,包括方法、弹塑性应力分析方法和欧盟的直接方法等。
压力容器设计是一个创新意识非常活跃的工程领域,它紧跟着科学技术的发展而不断地更新设计方法。
随着弹性理论、板壳理论和线性有限元分析方法的成熟,20世纪60年代,压力容器界提出了基于弹性应力分析和塑性失效准则的“弹性应力分析设计方法”。
进入21世纪后,由于塑性理论和非线性有限元分析方法的日趋成熟,欧盟标准和ASMEK 范又先后推出了压力容器的塑性分析设计方法。
其中涉及许多新的基本概念和新的分析方法,需要我们及时学习领会和消化吸收,以提高我们的分析设计水平,并结合国情进一步修订我国的压力容器设计规范。
ASM 岳口欧盟的新规范都是以失效模式为主线来编排的。
ASME 考虑了以下4种模式:(1)防止塑性垮塌。
对应于欧盟的“总体塑性变形(GPD )”失效模式。
(2)防止局部失效。
(3)防止屈曲(失稳)垮塌。
对应于欧盟的“失稳(I )”失效模式。
(4)防止循环加载失效。
对应于欧盟的“疲劳(F )”和“渐增塑性变形(PD ” 2种失效模式。
欧盟还考虑了“静力平衡(SE ”失效模式,即防止设备发生倾薄。
文中讨论的塑性分析设计方法主要应用于防止塑性垮塌和防止局部失效2种情况。
1、极限载荷分析法在一次加载情况下,结构的失效是一个加载历史过程,即随着载荷的增加从纯弹性状态到局部塑性状态再到总体塑性流动的失效状态。
对无硬化的理想塑性材料和小变形情况,结构进入总体塑性流动时的状态称为极限状态,相应的载荷称为极限载荷。
此时,结构变成几何可变的垮塌机构,将发生不可限制的塑性变形,因而失去承载能力。
一般的弹塑性分析方法都要考虑上述复杂的加载历史过程,但极限载荷分析法(简称极限分析)则另辟蹊径,跳过加载历史,直接考虑在最终的极限状态下结构的平衡特性,由此求出结构的承载能力(即极限载荷)。
防止压力容器塑性垮塌的分析方法研究

防止压力容器塑性垮塌的分析方法研究
压力容器的分析设计(DBA)作为规则设计(DBF)的并行设计方法越来越受到
设计人员的重视,对于高温、高压容器或者规则设计所不能涵盖的非标设备,分析设计的使用尤为广泛。
防止压力容器塑性垮塌失效是分析设计的重要任务之一,然而不同规范采用不同弹塑性分析方法。
本论文通过数值分析的手段对六种重要弹塑性分析方法展开研究,主要包括以下内容:1.简要介绍欧盟EN13445-3标准附录B中总体塑性变形设计校核及其应用,通过对比二次外推法的两种外推方式得出以下结论:按EN13445外推法计算时,应首先将表面支点的应变分量二次外推到热点处,然后求热点处的主结构
应变。
2.提出基于应变线性化的主结构应变计算方法,根据建模方式的差异性对同一结构确定六种计算结构应变的方法,通过对比分析六种方法的计算结果得出:应变线性化方法与二次外推法所得结果偏差最小;应变线性化方法可以计算压力容器构件中任何位置的结构应变,包括二次外推法无法使用的情况。
3.与EN13445直接法使用的最大主结构应变准则相对应,提出可以用于总体塑性变形校核的最大当量结构应变准则,该准则更适用于压力容器常用的韧性材料。
4.实现了零曲率准则的程序化并给定了载荷——应变或者载荷——变形(P-w)曲线上零曲率点的判据,可以准确快速地判断P-w曲线上某点是否为零曲率点或者确定零曲率点在曲线上的位置,从而可以使用载荷-抗力系数法进行设计校核。
5.通过对典型结构进行极限分析和弹塑性分析,对比六种弹塑性分析方法得出:零曲率准则为确定极限载荷的最佳准则;垮塌载荷和极限载荷确定许用载荷大小关系与结构的几何强化特性相关,故可以选择两者的较小值作为结构的最终许用载荷。
- 1、下载文档前请自行甄别文档内容的完整性,平台不提供额外的编辑、内容补充、找答案等附加服务。
- 2、"仅部分预览"的文档,不可在线预览部分如存在完整性等问题,可反馈申请退款(可完整预览的文档不适用该条件!)。
- 3、如文档侵犯您的权益,请联系客服反馈,我们会尽快为您处理(人工客服工作时间:9:00-18:30)。
引言《压力容器》“压力容器应力分析设计方法的进展和评述”中曾介绍和评述了压力容器分析设计的弹性应力分析方法(又称应力分类法)的最新进展。
本文将进一步介绍和评述压力容器分析设计的塑性分析方法,包括ASME的极限载荷分析方法、弹塑性应力分析方法和欧盟的直接方法等。
压力容器设计是一个创新意识非常活跃的工程领域,它紧跟着科学技术的发展而不断地更新设计方法。
随着弹性理论、板壳理论和线性有限元分析方法的成熟,20世纪60年代,压力容器界提出了基于弹性应力分析和塑性失效准则的“弹性应力分析设计方法”。
进入21世纪后,由于塑性理论和非线性有限元分析方法的日趋成熟,欧盟标准和ASME规范又先后推出了压力容器的塑性分析设计方法。
其中涉及许多新的基本概念和新的分析方法,需要我们及时学习领会和消化吸收,以提高我们的分析设计水平,并结合国情进一步修订我国的压力容器设计规范。
ASME和欧盟的新规范都是以失效模式为主线来编排的。
ASME考虑了以下4种模式:(1)防止塑性垮塌。
对应于欧盟的“总体塑性变形(GPD)”失效模式。
(2)防止局部失效。
(3)防止屈曲(失稳)垮塌。
对应于欧盟的“失稳(I)”失效模式。
(4)防止循环加载失效。
对应于欧盟的“疲劳(F)”和“渐增塑性变形(PD)”2种失效模式。
欧盟还考虑了“静力平衡(SE)”失效模式,即防止设备发生倾薄。
文中讨论的塑性分析设计方法主要应用于防止塑性垮塌和防止局部失效2种情况。
1、极限载荷分析法在一次加载情况下,结构的失效是一个加载历史过程,即随着载荷的增加从纯弹性状态到局部塑性状态再到总体塑性流动的失效状态。
对无硬化的理想塑性材料和小变形情况,结构进入总体塑性流动时的状态称为极限状态,相应的载荷称为极限载荷。
此时,结构变成几何可变的垮塌机构,将发生不可限制的塑性变形,因而失去承载能力。
一般的弹塑性分析方法都要考虑上述复杂的加载历史过程,但极限载荷分析法(简称极限分析)则另辟蹊径,跳过加载历史,直接考虑在最终的极限状态下结构的平衡特性,由此求出结构的承载能力(即极限载荷)。
它是塑性力学的一个重要分支。
极限分析求得的极限载荷与对弹性-理想塑性材料结构进行弹塑性小变形分析的结果是完全一致的。
极限载荷分析法的基础是极限平衡理论。
它由如下2个定理组成:(1)下限定理:满足平衡方程和外力边界条件、且不违反屈服条件(“不违反屈服条件”的含义是:结构中的应力都在屈服面内或屈服面上,而不能在屈服面之外。
以理想塑性材料受单向应力作用为例,应力可以小于或等于屈服限,但不能大于屈服限)的应力场称为“静力容许场”。
与静力容许场相对应的载荷是极限载荷的下限解。
(2)上限定理:满足几何约束条件、且能形成几何可变的垮塌机构的位移(速度)场称为“机动容许场”。
与机动容许场相对应的载荷是极限载荷的上限解。
用下限定理按静力容许场的平衡条件和屈服条件求极限载荷下限的方法称为极限分析的静力法;用上限定理按机动容许场的内力功等于外力功的条件求极限载荷上限的方法称为极限分析的机动法。
下限定理给出了结构不垮塌的必要条件,上限定理则给出了结构垮塌的充分条件。
静力容许场和机动容许场都可以有许多种,所以用下限(上限)定理可以求得无穷多个极限载荷的下限(上限)近似值,其中越大(越小)越接近真实的极限载荷,极限载荷是下限(上限)近似值的最大(最小)者。
如果分别用下限和上限定理求得的极限载荷近似值相等,则该值就是真实的极限载荷。
由于要事先预测复杂结构的机动容许场有一定的难度,上限定理在工程应用中受到一些限制;又由于下限解是小于真实极限载荷、偏保守的近似解,所以ASME 规范在极限载荷分析法中只要求计算极限载荷的下限。
基于上、下限定理人们已经找到许多简单结构的极限载荷解析解,读者可以查阅各种塑性力学的教科书。
霍奇的专著是关于板壳结构极限分析基本理论和解析解的经典著作。
极限分析的数值解法主要有两类:一类是基于理想塑性材料和小变形假设用弹塑性有限元分析方法来计算极限载荷;另一类是基于下限定理用线性(或非线性)规划算法来计算极限载荷。
目前后者尚未见公认的通用软件,主要用于科研领域。
前者已是许多著名有限元软件的核心功能之一,并已积累了不少工程应用经验,所以ASME 规范选择了前者。
下面对前者做进一步的介绍。
1.1 数值模型用于极限载荷分析的有限元数值模型采用如下3个基本假设:(1)采用弹性-理想塑性材料模型(弹性通常是线弹性)。
理想塑性材料是无冷作硬化的材料,进人塑性后应力始终保持为屈服限。
它是有硬化的实际材料的一种偏保守的简化模型。
“理想塑性”材料包括“弹性-理想塑性”和“刚性-理想塑性”(简称“刚塑性”)两种材料模型。
用这两种模型得到的极限载荷是相同的。
有限元分析常用前者,求解析解时常用后者。
ASME新版还规定理想塑性材料模型中的屈服限取为1. 5S,以控制那些屈服限较高的高强材料。
这里S是材料在设计温度下的基本许用应力 (即以前版本中的S)。
m(2)采用线性的应变-位移表达式。
(3)参照未变形结构形状建立平衡关系。
综合(2)和(3),称为“线性小变形(小位移)理论”。
采用线性应变-位移关系、但参照已变形结构形状建立平衡关系的理论称为“大挠度理论”,一般用于板、壳等弹性薄壁结构。
采用非线性应变-位移关系、且参照已变形结构形状建立平衡关系的理论称为“大变形(大位移)理论”。
“大挠度理论”和“大变形理论”都属于“几何非线性理沦”。
在欧盟标准中将“线性小变形理论”和“大挠度理论”分别称为“一阶理论”和“二阶理论”。
(4)采用冯•米赛斯(Von Mises)屈服准则和关联流动法则。
米赛斯屈服准则就是大家熟悉的第四强度理论,它对应于一个椭球形的屈服面。
当应力达到屈服面时,材料发生塑性流动。
塑性流动的方向可以用塑性应变增量的矢量方向来表示。
德鲁克(Drucker,D.C.)根据塑性变形过程中塑性功非负的假设提出:塑性应变增量的矢量应与屈服面正交,称为“正交流动法则”。
塑性力学中有2个函数:一个是屈服函数,其等值面就是屈服面;另一个是塑性势函数,塑性应变增量的矢量沿其等值面的外法线方向。
于是,若令塑性势函数与屈服函数相等(相关联)就得到正交流动法则,所以德鲁克流动法则也称为“关联流动法则”。
塑性势函数与屈服函数不相等的另一类法则称为“非关联流动法则”,此时塑性应变增量的矢量与屈服面不再正交。
“关联流动法则”适用于大多数金属材料,而岩土和混凝土等材料则宜采用较复杂的“非关联流动法则”。
1.2载荷施加(1)采用由零到最大值的、逐步递增的一次加载方式。
与极限载荷对应的是一次加载情况下的失效模式,所以弹塑性有限元计算的载荷增量必须恒正。
虽然在进人塑性后为了使迭代收敛载荷增量需要逐步减小,但不能出现增量为负的卸载情况。
(2)当受多种载荷联合作用时,应采用比例加载方式。
即各种载荷按相同的百分比同时由零增加到最大值。
ASME规范在表5.4中给出了极限载荷分析中应考虑的各种载荷组合情况,这些载荷组合都按比例加载方式施加。
1.3 评定准则ASME - VIII - 2老版本对极限载荷的评定准则是:若结构的规定设计载荷不超过极限载荷的2/3,则设计是可行的。
老版本中同时规定:根据试验或数值计算的结果绘制载荷-最大位移(或最大应变)曲线,然后用两倍弹性斜率法来确定极限载荷。
这样确定的“极限载荷”实际上是真实极限载荷的一个保守程度较大的下限近似值。
极限载荷是结构开始发生无限制总体塑性流动时的载荷。
在采用位移法有限元的弹塑性分析中,当极小的载荷增量也会导致计算不收敛时,就达到了极限载荷。
ASME - VIII - 2新版本中定义:“极限载荷是导致总体结构不稳定的载荷。
这表现为对小的载荷增量不能求得平衡解(即解将不收敛)”。
与两倍弹性斜率法相比,这是对极限载荷更为准确的定义。
需要指出的是,进入塑性后有限元计算中的载荷增量必须逐步减小,若载荷增量设置过大,会直接导致计算不收敛,称为“数值发散”。
不能将数值发散误认为达到了极限载荷。
为了避免数值发散,许多有限元软件都添加了弹塑性计算自动加载子程序。
该子程序对进入塑性后的每个加载步都会先采用上一步的载荷增量(或乘以0.8至1.0的减缩系数)进行试算。
若收敛,则继续加载;若发散,则自动将载荷增量减半后再重新计算。
这里介绍一种判断是否达到了极限载荷的数值处理方法:绘制载荷-最大位移(或最大应变)曲线。
当该曲线已经算到趋于水平(该加载步的曲线斜率已小于弹性斜率的百分之一)的阶段,则达到了极限载荷。
若该曲线在斜率较大时不能收敛,则属于数值发散,应该减小载荷增量再重新计算。
如上所述,精确计算和判定极限载荷的过程还比较复杂。
为了避免先要精确计算极限载荷的麻烦,参照美国土木工程规范ASCE 7 - 05的做法,ASME - VIII - 2新版在评定时引进了“载荷与抗力系数设计(LRFD)”的概念。
该方法将安全系数(考虑可能出现的各种不确定性的设计系数)乘到载荷上(详见该规范的表5.4),然后用经过该系数放大后的载荷对结构加载,进行极限载荷分析。
只要对表5.4中规定的所有载荷情况组合,当载荷达到表中规定值时计算都能收敛,就说明这些施加了安全系数的载荷都小于极限载荷,评定可以通过。
若计算发散,先检查一下是否是数值发散,若否,则应修改设计方案。
在ASME新版中,除上述强度评定准则外还增加了一条由业主规定的“使用准则”,详细讨论见下文2.1节的弹塑性分析法。
1.4 适用范围(1)极限载荷分析可用于替代ASME新版5. 2. 2节弹性应力分析法中一次应力极限的校核(即满足Pm ≤S,PL≤1.5S和PL+Pb≤1.5S三个评定准则),但不能替代一次加二次应力极限的校核。
因为极限载荷分析只做一次加载,而二次应力是要循环加载的。
(2)极限载荷分析可用于计算极限载荷的大小,但计算给出的位移或应变的大小是无意义的。
因为极限载荷分析的基本假设和实际情况有一定差距,而且从理论上说,达到极限载荷后塑性流动不可限制,位移和应变都是不确定的。
若业主在使用准则中要求对位移或应变加以限制,则应采用下节的弹塑性分析法。
(3)当出现较大面积、中面内的压应力区时,有可能在达到极限载荷前先出现屈曲垮塌。
必须按ASME新版5. 4节对容器另做“防止屈曲垮塌”的评定。
在英文中“失稳”(instability,或译成“不稳定性”)是个含义较广的概念。
弹性(或弹塑性)屈曲(buckling )、塑性垮塌(collapse,如单向拉伸试件的颈缩现象),还有丧失静力平衡(如倾覆)都会使结构丧失稳定性。
在基于弹性分析的规则设计中人们往往对屈曲和失稳不加区分,习惯上把buckling也翻译成“失稳”,但考虑塑性分析后将buckling准确地翻译成“屈曲”是必要的。