SMT制程常见缺陷分析与改善
SMT制程不良原因及改善措施精选文档

产;
? 26、清洗钢网并用风枪吹钢网。
3
短路
? 产生原因
? 1、钢网与 PCB板间距过大导致锡膏印刷过 厚短路;
? 2、元件贴装高度设置过低将锡膏挤压导 致短路;
? 3、回焊炉升温过快导致; ? 4、元件贴装偏移导致; ? 5、钢网开孔不佳(厚度过厚,引脚开孔
过长,开孔过大); ? 6、锡膏无法承受元件重量; ? 7、钢网或刮刀变形造成锡膏印刷过厚; ? 8、锡膏活性较强; ? 9、空贴点位封贴胶纸卷起造成周边元件
锡膏印刷过厚; ? 10、回流焊震动过大或不水平; ? 11、钢网底部粘锡; ? 12、QFP吸咀晃动贴装偏移造成短路。
? 不良改善对策
? 1、调整钢网与 PCB 间距0.2mm-1mm ; ? 2、调整机器贴装高度,泛用机一般调
整到元悠扬与吸咀接触到为宜(吸 咀下将时); ? 3、调整回流焊升温速度 90-120sec ; ? 4、调整机器贴装座标; ? 5、重开精密钢网,厚度一般为 0.12mm-
0.15mm ; ? 6、选用粘性好的锡膏; ? 7、更换钢网或刮刀; ? 8、更换较弱的锡膏; ? 9、重新用粘性较好的胶纸或锡铂纸贴; ? 10、调整水平,修量回焊炉; ? 11、清洗钢网,加大钢网清洗频率; ? 12、更换 QFP吸咀。
4
直立
? 产生原因
? 1、铜铂两边大小不一产生拉力不均; ? 2、预热升温速率太快; ? 3、机器贴装偏移; ? 4、锡膏印刷厚度不均; ? 5、回焊炉内温度分布不均; ? 6、锡膏印刷偏移; ? 7、机器轨道夹板不紧导致贴装偏移; ? 8、机器头部晃动; ? 9、锡膏活性过强; ? 10、炉温设置不当; ? 11、铜铂间距过大; ? 12、MARK点误照造成元悠扬打偏; ? 13、料架不良,元悠扬吸着不稳打偏; ? 14、原材料不良; ? 15、钢网开孔不良; ? 16、吸咀磨损严重; ? 17、机器厚度检测器误测。
SMT制程不良原因及改善对策

短路
产生原因
1、钢网与PCB板间距过大导致锡膏印刷过 厚短路; 2、元件贴装高度设置过低将锡膏挤压导 致短路; 3、回焊炉升温过快导致; 4、元件贴装偏移导致; 5、钢网开孔不佳(厚度过厚,引脚开孔 过长,开孔过大); 6、锡膏无法承受元件重量; 7、钢网或刮刀变形造成锡膏印刷过厚; 8、锡膏活性较强; 9、空贴点位封贴胶纸卷起造成周边元件 锡膏印刷过厚; 10、回流焊震动过大或不水平; 11、钢网底部粘锡; 12、QFP吸咀晃动贴装偏移造成短路。
1、PCB 板上有异物; 2、胶量过多; 3、红胶使用时间过久; 4、锡膏中有异物; 5、炉温设置过高或反面元件过重; 6、机器贴装高度过高。
改善对策
1、印刷前清洗干净; 2、调整印刷机或点胶机; 3、更换新红胶; 4、印刷过程避免异物掉过去; 5、调整炉温或用纸皮垫着过炉; 6、调整贴装高度。
错件
改善对策
1、调整回焊炉温度或链条速度; 2、调整回焊度回焊区温度; 3、更换新锡膏。
偏移
产生原因
1、印刷偏移; 2、机器夹板不紧造成贴偏; 3、机器贴装座标偏移; 4、过炉时链条抖动导致偏移; 5、MARK点误识别导致打偏; 6、NOZZLE中心偏移,补偿值偏移; 7、吸咀反白元件误识别; 8、机器X轴或Y轴丝杆磨损导致贴装 偏移; 9、机器头部滑块磨损导致贴偏; 10、驱动箱不良或信号线松动; 11、783或驱动箱温度过高; 12、MPA3吸咀定位锁磨损导致吸咀 晃动造成贴装偏移。
直立
产生原因
1、铜铂两边大小不一产生拉力不均; 2、预热升温速率太快; 3、机器贴装偏移; 4、锡膏印刷厚度不均; 5、回焊炉内温度分布不均; 6、锡膏印刷偏移; 7、机器轨道夹板不紧导致贴装偏移; 8、机器头部晃动; 9、锡膏活性过强; 10、炉温设置不当; 11、铜铂间距过大; 12、MARK点误照造成元悠扬打偏; 13、料架不良,元悠扬吸着不稳打偏; 14、原材料不良; 15、钢网开孔不良; 16、吸咀磨损严重; 17、机器厚度检测器误测。
【SMT】制程宝典--SMT常见不良原因分析与改善对策

作业
方法
印刷后锡膏被人碰到.
要求作业员小心作业.
教导并监督作业员小心作业.
贴片位移,炉前作业员用手拨正时形成短路.
用防焊胶纸粘起零件,让机器重打.
让机器打正,昼量不用手拨.
因调机(机器故障)时间过长,达??分钟,此板印刷后等待贴片时间达??分钟,Flux活化剂有所挥发,贴片时的压力造成锡膏瘫蹋,因pitch为0.5mm,造成短路.
IC脚弯? (附上图片)
1.更换另一盘料.
2.记录厂牌,Data Code,保留不良样品,知会QE、IQC.
1.上料前检查. 3.通知QE,IQC,要求供货商改善.
第二章:空焊
原因分析
临时对策
永久对策
环境
?月?日?点的车间温度(或湿度)超标,已达到??.
1.马上通知工务组改善.
2.E-MAIL给管理部及品保部.
临时对策
永久对策
环境
?月?日?点的车间温度(或湿度)超标,已达到??.
1.马上通知工务组改善.
2.E-MAIL给管理部及品保部.
1.随时注意车间温度(或湿度)并作好记录,如发现超标立即通知工务组.
2.E-MAIL给管理部及品保部.
锡膏
锡膏太稀.
1.刮去上层的一部份flux.
2换另一瓶新锡膏.
1.与锡膏厂商联系,要求改善锡膏品质, 2.换别的厂牌的锡膏.
Fine Pitch IC PAD位于板边,印刷时太靠近夹轨. (附上图片)
调宽印刷机轨道,由原来的??mm改为??mm.
反馈给PE、QE,与PCB客户协商改善方案.
锡膏厚度过高.(附上数据)
SMT制程不良原因及改善对策

SMT制程不良原因及改善对策SMT制程(Surface Mount Technology)是一种常用的电子组装技术,广泛应用于电子产品的制造过程中。
然而,由于各种原因所引起的不良现象在SMT制程中时有发生。
本文将讨论SMT制程不良原因以及改善对策。
1.焊接不良:焊接不良可以导致焊点虚焊、焊接断裂等问题。
常见的原因包括焊接温度不够、焊接时间不足、焊接设备不稳定等。
改善对策包括提高焊接设备的质量和稳定性、增加焊接温度和时间的控制精度等。
2.贴装不良:贴装不良可以导致元件偏移、元件漏贴等问题。
常见的原因包括贴装位置错误、贴装头磨损、胶垫损坏等。
改善对策包括提高贴装机的精度和稳定性、定期更换贴装头和胶垫等。
3.元件损坏:元件在SMT制程中容易受到机械损伤、电静电等因素的影响而受损。
改善对策包括提供合适的防护措施,如使用防静电设备、增加元件存储和运输的保护等。
4.焊盘不良:焊盘不良可以导致焊点接触不良、导致电路连通性问题。
常见的原因包括锡膏质量不佳、焊盘形状不准确等。
改善对策包括使用高质量的锡膏、提高焊盘生产过程的精度等。
5.引脚弯曲:引脚弯曲会导致元件无法正确插入或连接。
常见的原因包括元件存储和运输过程中引脚受到碰撞、搬运过程中的不当操作等。
改善对策包括提供合适的存储和运输保护措施、培训操作人员正确操作等。
改善SMT制程不良有很多对策,下面列举了其中一些常见的:1.提高设备的质量和稳定性:定期对设备进行维护和保养,确保其正常运行和精度稳定。
采用高质量的设备和工具,可大大降低不良率。
2.优化工艺参数:根据产品要求和设备特性,合理的调整焊接温度、焊接时间等工艺参数,以确保焊接效果和质量。
3.加强员工培训:提供必要的培训和指导,使操作人员熟悉SMT制程的原理和操作技巧,减少人为失误和操作不当导致的不良。
4.严格品质管理:建立完善的品质管理体系,包括设备校验、材料检测、过程控制等环节,确保产品质量稳定。
5.提供合适的存储和运输保护:对元件进行正确的存储和运输保护,避免机械损伤、静电损伤等因素导致的元件损坏。
SMT制程不良原因及改善措施分析

14、机器贴装高度设置不当; 15、锡膏较薄导致少锡空焊; 16、锡膏印刷脱膜不良。 17、锡膏使用时间过长,活性剂挥发掉; 18、机器反光板孔过大误识别造成; 19、原材料设计不良; 20、料架中心偏移; 21、机器吹气过大将锡膏吹跑; 22、元件氧化; 23、PCB贴装元件过长时间没过炉,导致活性 剂挥发; 24、机器Q1.Q2轴皮带磨损造成贴装角度 偏信移过炉后空焊; 25、流拉过程中板边元件锡膏被擦掉造成 空焊; 26、钢网孔堵塞漏刷锡膏造成空焊。
产生原因
1、真空泵碳片不良真空不够造成缺件; 2、吸咀堵塞或吸咀不良; 3、元件厚度检测不当或检测器不良; 4、贴装高度设置不当; 5、吸咀吹气过大或不吹气; 6、吸咀真空设定不当(适用于MPA); 7、异形元件贴装速度过快; 8、头部气管破烈; 9、气阀密封圈磨损; 10、回焊炉轨道边上有异物擦掉板上元 件; 11、头部上下不顺畅; 12、贴装过程中故障死机丢失步骤; 13、轨道松动,支撑PIN高你不同; 14、锡膏印刷后放置时间过久导致地件无 法粘上。
产生原因
改善对策
1、更换活性较强的锡膏; 2、开设精确的钢网; 3、将来板不良反馈于供应商或钢网将焊 盘间距开为0.5mm; 4、调整刮刀压力; 5、将元件使用前作检视并修整; 6、调整升温速度90-120秒; 7、用助焊剂清洗PCB; 8、对PCB进行烘烤; 9、调整元件贴装座标; 10、调整印刷机; 11、松掉X、Y Table轨道螺丝进行调整; 12、重新校正MARK点或更换MARK点; 13、将网孔向相反方向锉大;
SMT工艺之不良缺陷及改善
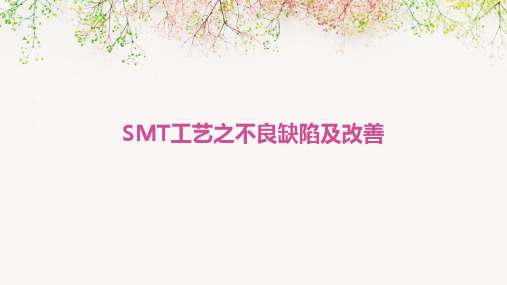
翘曲缺陷改善措施
翘曲缺陷:在SMT工 艺中,翘曲是指PCB 板或元器件发生弯曲 或翘起的现象,通常 是由于温度变化或材 料热膨胀系数不匹配 所导致。
改善措施
控制温度变化幅度, 避免过大的温度变化 导致PCB板或元器件 发生翘曲。
选择与PCB板和元器 件相匹配的热膨胀系 数的材料,以减少翘 曲的可能性。
锡洞缺陷改善措施
控制回流温度和时间,确保焊锡 能够充分流动并填满焊点。
改善措施
优化焊点的设计,使其更容易被 焊锡填满。
锡洞缺陷:在SMT工艺中,锡洞 是指焊点内部出现的小孔或空洞 ,通常是由于焊锡未完全填满焊 点所导致。
在焊接过程中增加振动或敲击, 以帮助焊锡更好地填满焊点。
组件移位缺陷改善措施
01
组件移位缺陷:在SMT工艺中,组件移位是指元器件 在印刷或回流过程中偏离了正确的位置,通常是由于 吸嘴压力不均或温度过高所导致。
02 改善措施
03
调整吸嘴压力,确保元器件在印刷和回流过程中保持正确的 位置。
04
控制回流温度和时间,避免温度过高导致元器件移位 。
05
使用定位辅助工具,如定位销或夹具,以帮助元器件 保持在正确的位置。
翘曲缺陷
总结词
翘曲缺陷是指PCB板在经过热历程后 产生的弯曲或扭曲现象。
详细描述
翘曲缺陷的产生可能与PCB板的材料 、设计、层数、元件布局和重量分布 等因素有关。翘曲缺陷可能导致焊接 不良、对准问题以及电路性能问题。
03
SMT工艺不良缺陷原因分析
锡珠缺陷原因
锡珠缺陷是指焊点表面出现圆形小珠的现象,主要 原因是焊膏过量、印刷厚度不均、贴片压力过大等 。
锡桥缺陷
总结词
锡桥缺陷是指两个或多个焊点之间形成的不期望的连接。
SMT制程不良原因及改善对策

PAD 离轨道边小 于3mm.
PAD氧化
未及时收板,PCB在回焊 炉中碰撞
零件过大过重
零件脚弯
人为手抹锡膏
零件厚度不均
备料时料带过紧
零件氧化
手放散料
异形零件
空气流通速度过快
手推撞板
焊盘上有异物
室温过高 锡膏印刷后硬化
PCB印刷后露置 空气中过久
人为手拨 缺锡
手摆料
PAD间距与组 件长度不符
零件与PAD不符
PCB
通风不畅
室内过于潮湿
温度高
手推撞板
零件
手碰零件
旧
超过
手放散料 缺乏教育训练
新工上线 缺乏责任感
反 破过 向 损周
期
锡 不 搅 使用 锡粉径 膏 均 拌 时间 粒过大
锡 膏
将锡膏加到钢网开口处
锡膏厚 短路
手印锡膏
有异 含 松 物 量香
锡 有锡 膏 水膏
手抹锡膏
印 手印台
零件间距离太近
稀 份内
钢网贴纸未贴好 手拨零件
(3) WHERE——何处?在哪里做?从 哪里入手?
(4) WHEN——何时?什么时间完成? 什么时机最适宜?
(5) WHO——谁?由谁来承担?谁来 完成?谁负责?
(6) HOW ——怎么做?如何提高效率? 如何实施?方法怎样?
(7) HOW MUCH——多少?做到什么 程度?数量如何?质量水平如何?费用产 出如何?
发明者用五个以w开头的英语单词和两 个以H开头的英语单词进行设问,发现解 决问题的线索,寻找发明 5W2H分析法思 路,进行设计构思,从而搞出新的发明项 目,这就叫做5W2H法。
(1) WHY——为什么?为什么要这么做? 理由何在?原因是什么?造成这样的结果 为什么?
smt制程不良原因及改善措施
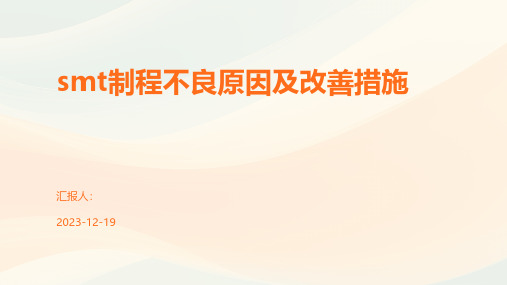
smt制程不良原因及改善措施汇报人:2023-12-19•SMT制程简介•SMT制程不良原因分析•SMT制程改善措施探讨目录•案例分析:成功改善SMT制程不良的实践经验分享•未来发展趋势预测与挑战分析•总结回顾与展望未来发展前景01SMT制程简介表面贴装技术(Surface Mount Technology,简称SMT)是一种将电子元件通过焊接或贴装的方式固定在印制电路板表面的电子制造技术。
高密度、高速度、高自动化、高质量、低成本、环保等。
SMT制程定义与特点SMT制程特点SMT制程定义20世纪60年代,SMT制程开始应用于电子制造领域。
初期阶段20世纪70年代至90年代,SMT制程逐渐普及,技术不断进步。
发展阶段21世纪初,SMT制程已经成为电子制造领域的主流技术。
成熟阶段SMT制程发展历程提高生产效率降低成本提高产品质量促进电子产业发展SMT制程重要性01020304SMT制程可以实现自动化生产,提高生产效率。
SMT制程可以减少人工操作,降低生产成本。
SMT制程可以实现高精度、高质量的焊接和贴装,提高产品质量。
SMT制程是电子制造领域的重要技术,对电子产业的发展具有推动作用。
02SMT制程不良原因分析原材料问题原材料问题是导致SMT制程不良的主要原因之一。
详细描述原材料的质量、稳定性、一致性等不符合要求,可能导致贴片机的识别问题、焊接不良等问题。
总结词设备故障是SMT制程不良的常见原因之一。
详细描述设备故障可能导致贴片机、焊接设备等不能正常运行,从而影响生产效率和产品质量。
设备故障操作失误总结词操作失误是SMT制程不良的常见原因之一。
详细描述操作失误可能包括操作流程不规范、参数设置错误等,导致生产过程中出现各种问题。
环境因素影响总结词环境因素对SMT制程不良具有一定的影响。
详细描述环境因素可能包括温度、湿度、灰尘等,这些因素可能影响设备的正常运行和产品的质量。
03SMT制程改善措施探讨提升原材料质量标准建立严格的原材料质量检验制度对所有原材料进行严格的质量检验,确保符合生产要求。
SMT-缺陷分析及对策

SMT 缺陷分析及对策一、桥联引线之间出现搭接的常见原因是端接头(或焊盘或导线)之间的间隔不够大。
再流焊时,搭接可能由于焊膏厚度过大或合金含量过多引起的。
另一个原因是焊膏塌落或焊膏黏度太小。
波峰焊时,搭接可能与设计有关,如传送速度过慢、焊料波的形状不适当或焊料波中的油量不适当,或焊剂不够。
焊剂的比重和预热温度也会对搭接有影响.桥联出现时应检测的项目与对策。
检测项目一:印刷网版与基板之间是否有间隙.对策:1、检查基板是否存在挠曲,如有挠曲可在再流焊炉内装上防变形机构;2、检查印刷机的基板顶持结构,使基板的保持状态与原平面一致;3、调整网版与板工作面的平行度。
检测项目二:对应网版面的刮刀工作面是否存在倾斜(不平行)。
对策:调整刮刀的平行度.检测项目三:刮刀的工作速度是否超速.对策:重复调整刮刀速度(刮刀速度过快情况下的焊膏转移,会降低焊膏黏度而在焊膏恢复原有黏度前就执行脱版,将产生焊膏的塌边不良)。
检测项目四:焊膏是否回流到网版的反面一侧。
对策:1、网版开口部设计是否比基板焊接区要略小一些;2、网版与基板间不可有间隙;3、是否用微间隙组装用的焊膏,微间隙组装常选择粒度小的焊膏,如有必要,可更换焊膏。
检测项目五:印刷压力是否过高,有否刮刀切入网板开口部现象。
对策:1、聚酯型刮刀的工作部硬度要适中,太软易产生对网版开口部的切入不良;2、重新调整印刷压力。
检测项目六:印刷机的印刷条件是否合适.对策:检测刮刀的工作角度,尽可能采用60度角。
检测项目七:每次供给的焊膏量是否适当。
对策:可调整印刷机的焊膏供给量。
二、焊料球焊料球是由于焊膏焊接中最普通的缺陷形式,其原因是焊料合金被氧化或焊料合金过小,由焊膏中溶剂的沸腾而引起的焊料飞溅的场合也会出现焊料球缺陷,还有一种原因是存在有塌边缺陷,从而造成的焊料球。
焊料球出现时应检测的项目与对策:检测项目一:基板区是否有目测不到的焊料小球(焊料合金被氧化造成).对策:焊膏是否在再流焊过程中发生氧化。
smt不良分析及改善措施

SMT生产工艺的发展趋势
01
02
03
智能化
通过引入人工智能技术, 实现SMT生产线的智能化 管理,提高生产效率和产 品质量。
绿色环保
随着环保意识的提高, SMT生产工艺将更加注重 绿色环保,减少对环境的 污染。
高精度、高密度
随着电子产品小型化、轻 量化的发展趋势,SMT生 产工艺将向高精度、高密 度方向发展。
详细描述
元件偏移可能是由于贴片机精度问题 、PCB定位不准确、焊盘设计不合理 或焊膏印刷不均匀导致的。元件偏移 可能导致焊接不良或电气性能下降。
翘曲
总结词
翘曲是指PCB在经过焊接后出现弯曲的现象。
详细描述
翘曲可能是由于PCB材料不均匀、温度变化差异大、焊接温度过高或冷却速度 过快导致的。翘曲可能会影响PCB的性能和外观。
提高员工技能和素质
定期对员工进行技能培训和考 核,提高员工的技能水平。
加强员工的质量意识和责任心 教育,提高员工的工作积极性 和主动性。
建立完善的激励机制,鼓励员 工提出改进意见和建议。
05
SMT不良改善案例分析
案例一:通过优化设备参数解决焊点不良问题
优化设备参数
在生产过程中,发现焊点不良问题较为突出。经过分析,发现设备参数设置不当 是主要原因。通过调整设备参数,如温度、压力和时间等,优化了焊点质量,减 少了不良品。
工艺因素
工艺参数设置不当
工艺参数设置不合理,如温度、时间、压力等,可能导致焊接不良。
工艺流程问题
工艺流程设计不合理,如焊膏印刷、元件放置等环节出现问题,也可能导致焊接不良。
环境因素
环境温湿度问题
生产环境温湿度不适宜,可能影响生产质量。
环境清洁度问题
smt不良分析及改善措施

如零件本身的质量问 题或由于放置不当造 成的损坏。
04
焊接不良
如焊接点不足、过多 或虚焊等。
不良品产生原因
如部件质量问题、焊料质量问题 等。
如车间温度、湿度、清洁度等环 境条件不良。
设备故障 材料问题 操作失误 环境因素
如贴片机、印刷机等设备故障或 参数设置不正确。
如操作人员技能不足、工作疏忽 等。
原因和分布情况。
效果评估方法
过程能力指数评估
利用过程能力指数评估生产过程的稳定性、 一致性和可预测性。
不良率统计
统计不良品的数量与总生产量的比例,计算 出不良率。
质量成本评估
评估因质量问题导致的损失,包括返工、报 废、保修等成本。
持续改进计划
01
针对主要不良原因 进行改善
针对主要的不良原因,制定相应 的改善措施,如优化工艺流程、 更换原材料供应商等。
smt不良分析及改善措施
汇报人: 日期:
目录
• SMT不良分析 • SMT不良改善措施 • SMT不良品追踪及效果评估 • SMT不良预防措施
01
SMT不良分析
Chapter
常见不良现象
01
部件丢失
如电阻、电容等部件 在组装过程中丢失或 未正确放置。
02
部件错位
如IC芯片位置偏离或 翻转。
03
注意事项
培训应结合实际生产情况,注重理论和实践的结 合,同时要定期评估培训效果。
实施质量管理体系,加强质量控制
总ቤተ መጻሕፍቲ ባይዱ词
实施质量管理体系,加强质量控制是减少SMT不良的有效方法 。
详细描述
建立完善的质量管理体系,包括来料检验、过程控制、成品检验 等环节,确保产品质量符合预期要求。
SMT制程常见异常分析

SMT制程常见异常分析SMT制程(表面贴装技术)是一种在电子元件制造中常用的制程技术,用于将电子元件贴装在印刷电路板(PCB)上。
然而,在SMT制程中,常会出现一些异常情况,如焊接不良、元件丢失等问题。
本文将针对SMT制程常见的异常进行分析。
1.焊接不良:焊接不良是SMT制程中常见的问题之一、焊接不良可能由于锡膏的质量问题、焊垫的尺寸偏差、焊接设备的操作不当等原因引起。
常见的焊接不良有焊接剪切、焊锡球、云母等问题。
焊接不良会导致元件与PCB之间的电连接不良,影响产品的性能和可靠性。
2.元件丢失:元件丢失是SMT制程常见的问题之一、元件丢失可能由于操作不当、元件自身缺陷、供应链问题等原因引起。
元件丢失会导致产品的功能性能下降,严重的情况下可能导致产品不能正常工作。
3.印刷问题:印刷问题是SMT制程中常见的问题之一、印刷问题可能由于锡膏的质量问题、印刷设备的操作不当、PCB的表面不平整等原因引起。
常见的印刷问题有锡膏剪切、印刷偏移、印刷污染等问题。
印刷问题会导致焊接质量不良,影响产品的性能和可靠性。
4.质量控制问题:质量控制问题是SMT制程中常见的问题之一、质量控制问题可能由于生产过程中缺乏足够的质量控制措施、操作工人技术水平不足、设备维护不良等原因引起。
质量控制问题会导致产品的性能和可靠性不稳定,严重的情况下可能导致产品不合格。
针对SMT制程常见的异常,可以采取以下措施进行分析和解决:1.异常分析:对于出现的异常情况,首先要进行详细的分析,排查出具体的原因。
可以通过观察异常的形态特征、分析生产过程中的操作记录、检查原材料的质量等方式进行分析。
2.数据收集:在SMT制程中可以采集相关的数据,如焊接温度、湿度、气压等参数,以及生产过程中的记录。
这些数据可以用于分析异常情况的原因,帮助找出潜在的问题。
3.过程优化:针对分析结果,可以进行制程的优化。
例如,对于焊接不良问题,可以优化焊接设备的参数,选择质量更好的焊接材料,加强操作工人的培训等。
SMT制程不良原因及改善措施分析

改善对策
1、印刷前清洗干净; 2、调整印刷机或点胶机; 3、更换新红胶; 4、印刷过程避免异物掉过去; 5、调整炉温或用纸皮垫着过炉; 6、调整贴装高度。
产生原因
1、机器贴装时无吹气抛料无吹气,抛料 盒毛刷不良; 2、贴装高度设置过高元件未贴装到位; 3、头部气阀不良; 4、人为擦板造成; 5、程序修改错误; 6、材料上错; 7、机器异常导致元件打飞造成错件。
1、锡膏活性较弱; 2、钢网开孔不佳; 3、铜铂间距过大或大铜贴小元件; 4、刮刀压力太大; 5、元件脚平整度不佳(翘脚、变形) 6、回焊炉预热区升温太快; 7、PCB铜铂太脏或者氧化; 8、PCB板含有水份; 9、机器贴装偏移; 10、锡膏印刷偏移; 11、机器夹板轨道松动造成贴装偏移; 12、MARK点误照造成元件打偏,导致空焊; 13、PCB铜铂上有穿孔;
产生原因
1、原材料不良; 2、规正器不顺导致元件夹坏; 3、吸着高度或贴装高度过低导致; 4、回焊炉温度设置过高; 5、料架顶针过长导致; 6、炉后撞件。
改善对策
1、检查原材料并反馈IQC处理; 2、维修调整规正座; 3、调整机器贴装高度; 4、调整回焊炉温度; 5、调整料架顶针; 6、人员作业时注意撞件。
产生原因
改善对策
1、调整回流焊温度(降低升温速度); 2、锡膏在使用前必须回温4H以上; 3、将室内温度控制到30%-60%); 4、将PCB板进烘烤; 5、避免在锡膏内加稀释剂; 6、重新开设密钢网; 7、更换适用的锡膏,按照规定的时间对锡膏 进行搅拌:回温4H搅拌4M。
smt不良分析及改善措施

材料问题
原材料缺陷:如PCB板、电子元器件等原材料存 在缺陷,将直接影响SMT产品的品质。
使用过期材料:使用过期的原材料进行生产,可 能导致产品性能不稳定,产生不良品。
储存不当:原材料在储存过程中未按照要求进行 保管,可能导致性能受损,进而影响SMT产品质 量。
针对以上原因,可以采取相应的改善措施,如加 强员工培训、规范操作流程、定期维护设备、严 格把控原材料质量等,以降低SMT不良品率,提 高产品质量和生产效率。
03
SMT不良改善措施
人员培训和管理
提高技能水平
定期举办技术培训课程,提升员工在SMT操作、维护、质检等方面 的技能水平,确保员工熟悉并掌握设备操作规程和质量标准。
严格考核与奖惩制度
建立员工绩效考核体系,对操作规范、良品率等方面进行考核,奖 励优秀员工,对操作不规范、产品质量差的员工进行惩罚和再培训 。
强化质量意识
通过定期的质量教育活动,增强员工的质量意识,使其充分认识到产 品质量对企业和个人的重要性。
设备维护和管理
制定维护计划
根据设备使用情况和维护要求,制定合理的设备维护计划,确保 设备按时进行保养、检修,减少设备故障。
监控设备运行状况
通过设备自带的监测系统或额外安装传感器等方式,实时监测设备 运行状况,及时发现异常,避免故障扩大。
• 焊接不良:包括冷焊、虚焊、 焊盘脱落等问题,主要由于焊 接温度、时间等参数设置不当 或焊接材料质量差引起。
• 基板不良:包括基板变形、裂 纹、污染等,可能由基板材料 、设计或生产工艺导致。
SMT不良现象对生产的影响
01
02
03
生产效率下降
SMT不良现象会增加检修 、返工等工作量,降低生 产效率。
SMT制程不良原因及改善对策

调整印刷机平台的水平度平行度;
6
基板表面异物造成周边元件锡膏印刷 过厚;
基板使用前进行除尘作业;
7
一次面基板背面残留锡膏过炉形成锡 珠,二次面锡膏印刷时垫起钢网形成 多锡;
避免一次面基板粘附锡膏,避免洗 板作业;
8 修理员回锡过多;
指导修理员按标准作业。
11
立起
产生原因
1 铜铂两边大小不一产生拉力不均; 2 预热升温速率太快; 3 机器贴装偏移; 4 锡膏印刷厚度不均; 5 回流焊内温度分布不均; 6 锡膏印刷偏移; 7 机器轨道夹板不紧导致贴装偏移; 8 机器头部晃动贴装偏移; 9 焊盘两端的散热程度不一致融化速度差异; 10 炉温设置不当; 11 铜铂间距过大; 12 MARK点误照造成元件打偏; 13 料架不良,元件吸着不稳打偏; 14 原材料不良; 15 钢网开孔不良;
发形成干锡膏,混入印刷产生钢网堵孔。
改善对策
10
多锡
产生原因
改善对策
1 钢网开孔过大或厚度过厚;
按标准制作钢网;
2 锡膏印刷厚度过厚;
调整印刷参数(压力、脱模等) ;
3 钢网底部粘锡;
清洗钢网;
4 IC元件底部接地焊盘锡膏溢出形成多 接地焊盘开孔适当减小,贴装高度适
锡;
当调高;
5
印刷平台不平行或高于基板导致印刷 多锡;
19 原材料设计不良;
反馈IQC联络供应商;
20 料架中心偏移;
校正料架中心;
21 机器吹气过大将锡膏吹跑;
将贴片吹气调整为0.2mm/cm² ;
22 元件氧化;
更换OK之材料;
23 PCB贴装后长时间没过炉,导致活性剂挥发; 及时将PCB-A过炉,生产过程中避免堆积;
smt制程不良原因及改善措施
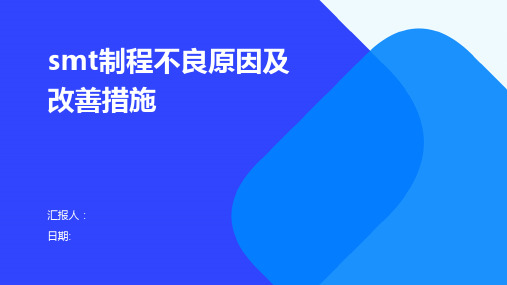
3
检测不良
PCB板翘曲变形、尺寸偏差等
环境因素(温度、湿度)影响检测结果
检测不良
01
改善措施
02
提高检测设备精度,定期校准和维护保养
03
优化检测程序,提高检测灵敏度和准确性
检测不良
01
加强PCB板的质量控制,防止翘 曲变形和尺寸偏差等问题
02
控制环境因素,确保检测环境稳 定和适宜的温度、湿度等条件
03
SMT制程改善措施
原材料控制
确保供应商的原材料质量稳定可 靠,进行严格的进料检验和测试 ,防止不良原材料进入生产环节
。
与供应商建立长期稳定的合作关 系,定期对供应商进行评估和审 计,确保供应商遵循质量标准和
要求。
对原材料存储和保管进行严格控 制,避免潮湿、污染和氧化等问
题的发生。
设备维护与保养
产成本,增强市场竞争力。
质量管理体系的运行与维护
质量管理体系的运行
企业需要建立专门的质量管理部门或质量管理团队来负责质 量管理体系的运行和维护,确保质量管理体系的有效性和持 续性。
质量管理体系的维护
企业需要定期对质量管理体系进行审查和更新,以确保其适 应市场和客户需求的变化,同时及时发现和解决潜在问题。
检查和返工
检查焊接质量和零件放置位置 ,对不良品进行返工。
SMT制程重要性
01
02
03
提高生产效率
SMT制程可以实现自动化 和批量生产,从而提高生 产效率。
提高产品质量
SMT制程可以提供高精度 的零件放置和稳定的焊接 质量,从而提高产品质量 。
降低成本
SMT制程可以减少零件的 包装和运输成本,同时也 可以降低人力成本。
SMT贴片制程不良原因及改善对策

4,调整回焊炉温度;
5,料架顶针过长导致;
5,调整料架顶针;
6,炉后撞件。
6,人员作业时注意撞件。
十四,少锡
产生原因
不良改善对策
1,PCB焊盘上有惯穿孔;
1,开钢网时避孔处理;
2,钢网开孔过小或钢网厚度太薄;
2,开钢网时按标准开钢网;
3,锡膏印刷时少锡(脱膜不良);
3,调整印刷机刮刀压力和PCB与钢网间距;
3,红胶使用时间过久;
3,更换新红胶;
4,锡膏中有异物;
4,印刷过程避免异物掉过去;
5,炉温设置过高或反面元件过重;
5,调整炉温或用纸皮垫着过炉;
6,机器贴装高度过高。
6,调整贴装高度。
八,错件
产生原因
不良改善对策
1,机器贴装时无吹气抛料无吹气,抛料盒毛刷不良;
1,检查机器贴片吹气气压抛料吹气气压抛料盒毛刷;
四、缺件
产生原因
不良改善对策
1,真空泵碳片不良真空不够造成缺件;
1,更换真空泵碳片,或真空泵;
2,吸咀堵塞或吸咀不良;
2,更换或保养吸膈;
3,元件厚度检测不当或检测器不良;
3,修改元悠扬厚度误差或检修厚度检测器;
4,贴装高度设置不当;
4,修改机器贴装高度;
5,吸咀吹气过大或不吹气;
5,一般设为0.1-0.2kgf/cm2;
六,翘脚
产生原因
不良改善对策
1,原材料翘脚;
1,生产前先对材料进行检查,有NG品修好后再贴装;
2,规正座内有异物;
2,清洁归正座;
3,程序设置有误;
3,修改程序;
4,MK规正器不灵活;
4,拆下规正器进行调整。
- 1、下载文档前请自行甄别文档内容的完整性,平台不提供额外的编辑、内容补充、找答案等附加服务。
- 2、"仅部分预览"的文档,不可在线预览部分如存在完整性等问题,可反馈申请退款(可完整预览的文档不适用该条件!)。
- 3、如文档侵犯您的权益,请联系客服反馈,我们会尽快为您处理(人工客服工作时间:9:00-18:30)。
发生原因
改善方法
1)在曲线图规定条件内适当增高回流区的温度与时间范围,使锡膏得到充分融化 2)更换过期锡膏,另外可加入阻焊剂再充分搅拌(一般不采用) 3)针对有大型元件的基板,回流时可适当增加各温区的温度,使锡膏能吸收到充 分的热量,而充分融化。 4)对回流更换产品时,轨道调整到比基板宽出0.5~1mm。使基板能顺畅通过。 5)适当调整回流炉的参数设置,降低链速设定或增大风机频率设定。
发生原因
改善方法
SMT制程常见缺陷分析与改善
不良项目 沾锡粒
不良概述
由于回流过程中加热急速造成的锡颗粒分散在元件的周围或基板上,冷却后形成
1)锡膏接触空气后,颗粒表面产生氧化或锡膏从冰箱里取出后没有充分的解冻,使回流后锡颗 粒不能有效的结合在一起。 2)回流炉的预热阶段的保温区时间或温度不充分,使锡膏内的水分与溶剂未充分挥发溶解。 3)网板擦拭不干净,印刷时使残留在网板孔壁的锡颗粒印在基板上,回流后形成。 4)印刷锡量较厚(主要为Chip元件)贴装时锡膏塌陷,回流过程中塌陷的锡膏扩散后不能收回 5)针对电解电容沾锡粒,主要是由于两铜箔锡量太多,大部分的锡都压在元件本体树脂下面, 回流后锡全部从树脂底下溢出形成锡粒。 6)锡膏超过有效期,阻焊剂已经沉淀出来与锡颗粒不能融合在一起,回流后使锡颗粒扩散形成 7)回流炉保温区与回流区的温度急剧上升,造成锡颗粒扩散后不能收回。
发生原因
改善方法
SMT制程常见缺陷分析与改善
不良项目 漏装
不良概述
指元件根本就没有贴装在基板上的铜箔上,或铜箔上的锡膏红胶也没有被元件装过 的痕迹。
1)吸嘴沾脏未及时清洗或吸嘴真空气管破裂使吸嘴真空太小,头部在旋转过程中将 原件甩落,未装在基板上。 2)NC程序错,无此元件的贴装坐标。 3)基板铜箔上漏印刷锡膏或红胶,元件贴上后由于未被固定而致漏装。 4)设备故障死机,关机时没有记忆,重新开机时未找点生产而致漏装。 5)NC程序中元件贴装数据项被SKIP, 6)网板制作时,漏开口,元件贴装时被打飞。 7)元件库数据中元件厚度设置不当。 1)清洗吸嘴或更换破裂气管,增大真空气压。 2)修改NC程序,增加此元件的贴装数据 3)清洗网板网孔,使其正常印刷,对漏印刷的采用人工补胶后再投入生产。 4)对设备故障重新开机时采用找点法重新找点后再生产。 5)恢复NC程序中的SKIP项, 6)对新网板制作投入生产前需按要求对网板进行确认,对发现漏开孔,应立即送 外补开网孔。 7)根据元件的实际厚度进行设定。
SMT制程控制
制程控制需要重点考虑以下几个方面 1:明确装配要求,工艺流程,工艺参数设定。 2:作业流程规范化,包括标准的制定和指导文件的 规范化 3:需要有培训合格的作业员,使他们能够适应新的 工艺和新的设备与技术。 4:新产品试做时应了解各个环节的问题,再进行改 善,便于量产的正常生产。 实际上SMT制程控制中做关键的工序还是印刷工 序,是影响制程品质的重点所在。
SMT制程常见缺陷分析与改善
不良项目 不良概述 生半田(冷焊) 锡膏在过回流炉后未彻底的融化,存在像细沙一样的颗粒,焊点表面无光泽 1)主要由于回流炉的回流温度偏低,回流区时间偏短,使锡膏未完全融化而形成 2) 锡膏过期,在正常的回流温度下使锡膏未得到充分的融化。 3)较大元件回流时由于部品吸热较多,使锡膏没有吸收到较大的热量而出现。 4)回流过程中基板被卡在回流炉中间,未通过回流区便人为取出,导致锡膏未彻 底溶化。 5)回流炉的链速设定过快或风机频率设定偏低,使锡膏未彻底的回流融化。
发生原因
Hale Waihona Puke 改善方法1)适当增大印刷压力,使锡量减少或将有0.5pitch的IC印刷网板的钢片厚度改为0.15MM或 0.13MM,减少锡量厚度,另外可调整贴装压力,使部品轻放在锡膏上而不产生塌陷。 2)调整印刷位置,使锡膏印在铜箔正中间位置。 3)合理布置顶针,再调整印刷脱模速度与距离。 4)此类部品一般根据有铅与无铅做适当的开口或减少钢片厚度,网板建议采用电抛光加工方法 5)调整贴装坐标或吸料位置,较大的部品可适当调慢吸料贴装速度。 6)调整印刷机程序中PCB厚度设置值,减少印刷锡量
SMT制程常见缺陷分析与改善
不良项目 移位
不良概述
元件的端子或电极片移出了铜箔,超出了判定基准
1)贴装坐标或角度偏移,元件未装在铜箔正中间 2) 实装机部品相机识别方式选择不适当,造成识别不良而贴装移位 3)基板定位不稳定,MAEK电设置不适当或顶针布置不合适造成移位。 4)吸料位置偏移,造成贴装时吸嘴没有吸在元件的中间位置而移位 5)印刷时锡量偏少而不均匀,回流时由于张力作用拉动部品使其移位。 6)部品数据库中数据参数设置错误,(如:吸嘴设置不适当)使贴装移位。
发生原因
改善方法
1)避免锡膏直接与空气接触,对停留在网板上长时间不使用的锡膏则回收再锡膏瓶内,放进冰 箱。从冰箱内取出锡膏放在室温下回温到适宜的时间并按规定时间搅拌后才能使用。 2)适当增加预热温度,延长回流曲线图的预热时间,使锡膏中的焊料互相融化。 3)擦拭网板采用适当的擦拭形式,如:湿,干式等。 4)针对Chip元件开网板时采用防锡珠开口方式,减少锡量。 5)此类元件网板开口时通常要采用将其向外平移0.3~0.6mm的方法,使其锡量大部分印刷在 元件树脂以外的铜箔上。 6)更换过期锡膏,按锡膏的有效期使用,严格要求按先入先出的原则适用。 7)适当调整回流炉的保温区与回流区的温度,使温度上升速度缓慢上升,一般保温区控制在 0.3~0.5℃/S,回流区控制在2~5 ℃/S.
发生原因
改善方法
SMT制程常见缺陷分析与改善
不良项目 浮起
不良概述
元件本体或端子未贴紧在基板的铜箔上,有一定的间隙。
1)红胶印刷的厚度偏高,使元件不能紧贴基板,或者由于印刷锡量较厚。 2)贴装移位,元件回流后由于张力作用将元件轻微拉致浮起。 3)基板沾有基板屑或异物,元件贴装后使其浮起或贴装装乱,贴装元件底部掉落 了其它元件,使其浮起。 4)FPC软基板变形或翘起,元件贴装后另一端未装在铜箔上而且有一定的间隙。 5)对电解电容浮起,主要由于回流后此元件树脂底部沾锡粒所致。 6)元件本体底部来料不平整或端子翘起,实装后元件与基板之间就形成间隙。
SMT制程控制
SMT制程常见缺陷有:锡少,胶少,沾锡粒,生 半田(冷焊),移位,短路,竖立,未焊锡(假 焊),浮起,脱落,漏装,损伤,装错,印字不 清,方向反,相挨,交叉,
SMT制程常见缺陷分析与改善
不良项目 不良概述 锡少 指元件端子或电极片的锡量到不到高度要求及端子前端没有锡轮廓 1)印刷机刮刀压力过大,使刮刀将网孔中的锡膏刮掉,印刷在基板铜箔上的 效果 为四周高中间底,使回流后元件锡量少。 2)印刷网板的网孔由于未清洗干净,锡粒粘附在开口部周边凝固后造成网孔堵塞 而导致印刷锡少 3)印刷网板开口偏小或网板厚度偏薄不能满足元件回流后的端子锡量 4)贴装移位造成元件回流后锡少 5)印刷速度过快,锡膏在刮刀片下滚动过快,使锡膏来不及充分的印刷在网孔中 6)网板开口表面光洁度不够且粗糙,使锡粒子印刷下锡量较少 1)减少印刷刮刀压力,使印刷锡量增加,另外可轻微增大网板与基板之间的印刷 间距,使锡量增加。 2)增加网板擦拭频率,自动擦拭后适当采用手动擦拭,另外对网板清洗的网板一 定要用显微镜进行检查。 3)适当加大网板开口尺寸,使其铜箔有足够的锡量。 4)调整贴装坐标及元件识别方法,使元件贴在铜箔正中间。 5)调整印刷机参数设定,使印刷速度降低。 6)网板开口工艺采用激光加工法,对细间距IC通常采用电抛光加工
发生原因
改善方法
SMT制程常见缺陷分析与改善
不良项目 不良概述 未焊锡/假焊 指元件端子没有与铜箔的锡膏熔接在一起,即没有焊好 1)chip类元件两端铜箔印刷锡量不均匀,部品回流后由于锡量多的一侧张力大拉起部品使锡少 的一侧造成未焊锡/假焊。 2)元件贴装时移位(主要针对排阻和1005型chip元件)锡膏有熔化至冷却凝固状态的过程中, 部品沾锡膏多的一侧冷却凝固时牵引力较沾锡膏少的那侧要大,从而拉动元件移向锡较多的一 侧而形成。 3)元件端子轻微向上翘起变形或端子来料氧化,回流后锡膏不能侵到端子上而造成 4)回流的预热区时间或温度不够高,造成锡与端子熔接时未完全侵润 5)锡膏超过印刷至回流的有效期,回流时锡膏不能与端子完全熔化形成焊锡不良 6)锡膏过期,回流时由于锡膏的焊料变质,不能与原件的电极片或端子熔接在一起形成。 1)适当均匀分布顶针,使印刷锡量均匀,同时再确认印刷刮刀片是否变形,磨损,更换不良的 刮刀片 2)调整贴装位置,使其装在铜箔正中间 3)端子变形的需要整形后在贴装,来料氧化联络供应商处理改善。 4)适当增加回流预热区的温度与时间,使其充分熔接。 5)严格控制印刷至回流的时间, 6)更换过期锡膏,严格控制按锡膏的有效期于先入先出进行管理使用。
发生原因
改善方法
1)调整实装程序的X,Y坐标或角度 2)更改贴装时部品相机识别方式,特别是QFP,较密集的CN类元件。 3)确认轨道宽度(轨道宽度设置一般是比基板宽度宽0.5MM),确认顶针布置均 匀合理,MAER数据正常,设置位置合理,不会错识别到旁边点。 4)调整吸料位置,使吸嘴吸在元件中间无偏移。 5)适当减少印刷刮刀压力及均匀分布顶针,使印刷锡量增加且均匀 6)根据元件实际尺寸设置元件数据,正确选择吸嘴。
SMT制程控制序言
在SMT生产过程中,都希望基板从印刷工序开始 到回流焊接工序结束,质量处于零缺陷状态,但实际 上这是很难达到。由于SMT工序较多,不能保证每道 工序不出现差错。因此在SMT生产过程中会碰到一些 焊接缺陷这些缺陷由多种原因造成。对于每个缺陷应 分析其产生的根本原因,这样才能消除这些缺陷,做 好后续的预防工作。那么怎样才能控制这些缺陷的产 生呢?首先要认识什么是制程控制。简单来说,制程 控制是运用最合适的设备,工具或者方法材料,控制 制造过程中各个环节,使之能生产出品质稳定的产品。 实际上实施制程控制的目的也就是希望提高生产效率, 提高生产品质,稳定工艺流程,用最经济的手段得到 最佳的效益,这些主要体现在生产能力的提升上。