电动车动力电池安全性测试与仿真
电动车动力电池检测
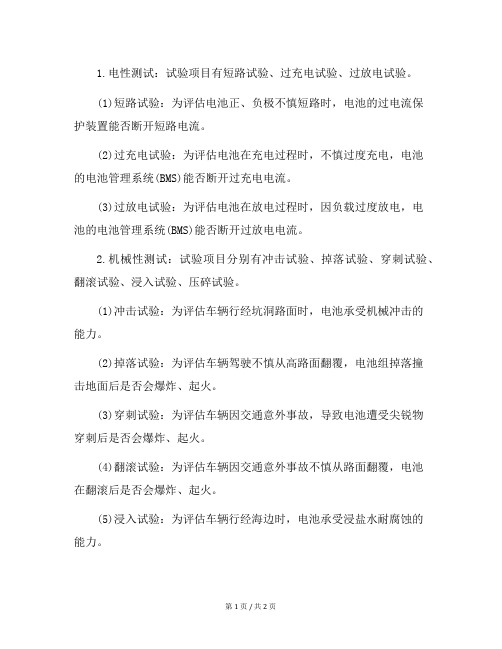
1.电性测试:试验项目有短路试验、过充电试验、过放电试验。
(1)短路试验:为评估电池正、负极不慎短路时,电池的过电流保护装置能否断开短路电流。
(2)过充电试验:为评估电池在充电过程时,不慎过度充电,电池的电池管理系统(BMS)能否断开过充电电流。
(3)过放电试验:为评估电池在放电过程时,因负载过度放电,电池的电池管理系统(BMS)能否断开过放电电流。
2.机械性测试:试验项目分别有冲击试验、掉落试验、穿刺试验、翻滚试验、浸入试验、压碎试验。
(1)冲击试验:为评估车辆行经坑洞路面时,电池承受机械冲击的能力。
(2)掉落试验:为评估车辆驾驶不慎从高路面翻覆,电池组掉落撞击地面后是否会爆炸、起火。
(3)穿刺试验:为评估车辆因交通意外事故,导致电池遭受尖锐物穿刺后是否会爆炸、起火。
(4)翻滚试验:为评估车辆因交通意外事故不慎从路面翻覆,电池在翻滚后是否会爆炸、起火。
(5)浸入试验:为评估车辆行经海边时,电池承受浸盐水耐腐蚀的能力。
(6)压碎试验:为评估车辆因交通意外事故,导致电池遭受机械性破坏后是否会爆炸、起火。
3.热测试:试验项目有高温危险试验、热稳定试验、无热管理循环试验、热冲击循环试验、被动传播电阻试验。
(1)高温危险试验:为评估车辆因意外不慎着火,电池承受高热的能力。
(2)热稳定试验:为评估车辆在高温环境下,电池承受高热的稳定性。
(3)无热管理循环试验:为评估电池的电池管理系统(BMS)失效时,电池的充放电循环能力。
(4)热冲击循环试验:为评估车辆在高低温的温差环境下,电池承受高低温剧烈变化能力。
(5)被动传播电阻试验:为评估电池模组或电池组内的单一个单电池发生热破坏现象,是否热破坏现象会传播至邻近的单电池。
实验报告(动力电池性能测试)
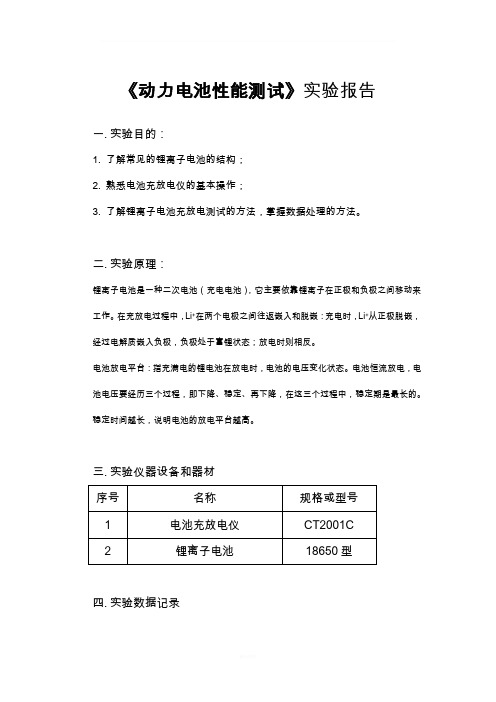
《动力电池性能测试》实验报告一.实验目的:1. 了解常见的锂离子电池的结构;2. 熟悉电池充放电仪的基本操作;3. 了解锂离子电池充放电测试的方法,掌握数据处理的方法。
二.实验原理:锂离子电池是一种二次电池(充电电池),它主要依靠锂离子在正极和负极之间移动来工作。
在充放电过程中,Li+在两个电极之间往返嵌入和脱嵌:充电时,Li+从正极脱嵌,经过电解质嵌入负极,负极处于富锂状态;放电时则相反。
电池放电平台:指充满电的锂电池在放电时,电池的电压变化状态。
电池恒流放电,电池电压要经历三个过程,即下降、稳定、再下降,在这三个过程中,稳定期是最长的。
稳定时间越长,说明电池的放电平台越高。
三.实验仪器设备和器材四.实验数据记录五.实验数据分析1.写出采集数据的大致操作过程将锂离子电池固定在电池充放电仪上,打开蓝电电池测试系统,设置电池充放电的各项参数:1.将锂电池在充放电仪上静置一小时;2.根据下列要求设置充放电电流及电压,并打开通道;3.取下锂离子电池,读取数据。
2.根据采集的数据作图(电脑作图后打印粘贴)图1:循环1-4容量-电压关系图图2:循环5-7容量-电压关系图图3:表格数据循环1-15放电容量&效率关系图(实际为循环5-19)六. 实验思考与讨论1.由图1可知,循环1-4充电电流均保持300mA,达到4.2V时保持恒压充电。
循环1-4充电曲线趋势重合,容量有轻微下降,推测有两种可能性:①电解液分解、自放电、电极不稳定造成的容量轻微衰减(可根据实验原理排除过充);②实验本身误差。
放电时,循环1-4分别以300mA, 600mA,1500mA,3000Ma恒流放电,可以看到,随着电流密度增大,放电容量明显降低,且容量随电压降减小的更快。
这是因为电流密度大则电极反应速度快,电化学极化和浓差极化就越严重,阻碍了反应的深度,使活性物质不能充分被利用。
2.由图2可知,循环5-7各条件不变,充放电电流均保持300mA,以研究相同倍率下锂离子电池的循环充放电特性。
解析新能源汽车的动力性能仿真技术

解析新能源汽车的动力性能仿真技术新能源汽车的发展势不可挡,其动力系统是其核心竞争力之一。
为了进一步优化新能源汽车的动力性能,仿真技术成为了不可或缺的工具。
本文将针对新能源汽车的动力性能仿真技术展开详细解析。
动力性能仿真的定义动力性能仿真是利用计算机模拟新能源汽车动力系统运行过程的技术。
通过建立数学模型,模拟不同工况下的动力需求与动力系统输出之间的关系,用以评估新能源汽车的加速性能、续航能力、能耗等指标。
动力性能仿真的重要性动力性能仿真技术可以在产品设计阶段快速、准确地评估不同动力系统配置在实际使用中的表现。
通过仿真可以提前发现问题,降低开发成本,缩短产品上市时间,提高产品竞争力。
动力性能仿真的步骤建立数学模型:包括车辆动力学模型、电池模型、电机模型等,模型精确性将直接影响仿真结果的准确性。
设定仿真工况:根据实际道路行驶工况、车辆负载情况等因素,设定不同工况下的仿真条件。
进行仿真计算:利用仿真软件对所建立的数学模型在设定工况下进行仿真计算,得出动力性能指标。
评估结果:根据仿真结果评估新能源汽车在不同工况下的动力性能表现,发现问题并进行优化调整。
动力性能仿真技术的应用动力系统优化:通过仿真技术,优化电池容量、电机功率匹配等,提高动力系统整体效率。
节能降耗:仿真可以帮助优化能量管理策略,降低新能源汽车的能耗,延长续航里程。
性能预测:在产品设计阶段,可以利用仿真技术对新能源汽车性能进行预测,为后续研发工作提供参考。
动力性能仿真技术对于提升新能源汽车的竞争力具有重要意义。
通过精确的仿真分析,可以为新能源汽车的研发与生产提供有力支持,促进行业持续发展。
让我们共同关注和推动新能源汽车动力性能仿真技术的发展,为清洁能源汽车行业注入更多活力和创新。
动力性能仿真技术是新能源汽车发展中不可或缺的重要环节,其应用将进一步推动新能源汽车行业的发展,提升技术水平和竞争力。
动力电池热失控仿真技术
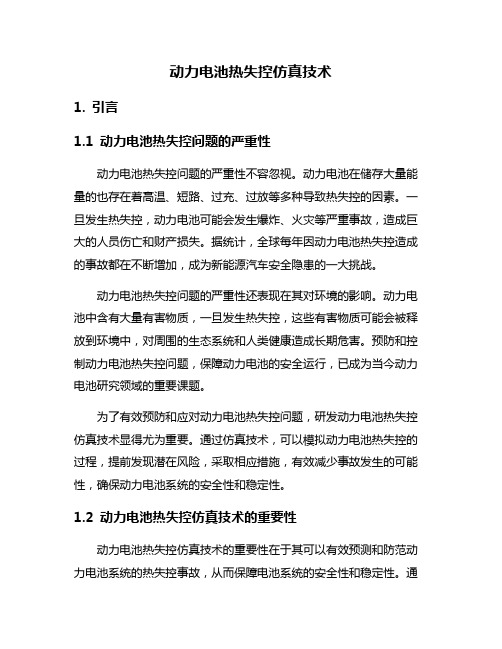
动力电池热失控仿真技术1. 引言1.1 动力电池热失控问题的严重性动力电池热失控问题的严重性不容忽视。
动力电池在储存大量能量的也存在着高温、短路、过充、过放等多种导致热失控的因素。
一旦发生热失控,动力电池可能会发生爆炸、火灾等严重事故,造成巨大的人员伤亡和财产损失。
据统计,全球每年因动力电池热失控造成的事故都在不断增加,成为新能源汽车安全隐患的一大挑战。
动力电池热失控问题的严重性还表现在其对环境的影响。
动力电池中含有大量有害物质,一旦发生热失控,这些有害物质可能会被释放到环境中,对周围的生态系统和人类健康造成长期危害。
预防和控制动力电池热失控问题,保障动力电池的安全运行,已成为当今动力电池研究领域的重要课题。
为了有效预防和应对动力电池热失控问题,研发动力电池热失控仿真技术显得尤为重要。
通过仿真技术,可以模拟动力电池热失控的过程,提前发现潜在风险,采取相应措施,有效减少事故发生的可能性,确保动力电池系统的安全性和稳定性。
1.2 动力电池热失控仿真技术的重要性动力电池热失控仿真技术的重要性在于其可以有效预测和防范动力电池系统的热失控事故,从而保障电池系统的安全性和稳定性。
通过仿真技术,可以模拟和分析各种可能导致热失控的因素,如过充、过放、短路等,从而提前发现潜在问题并采取措施进行预防。
动力电池热失控仿真技术还可以为电池系统的设计和优化提供重要参考,帮助提高系统的性能和效率。
在实际应用中,通过仿真技术可以节省大量的时间和成本,避免真实系统的损坏和风险,同时也能够不断改进和完善仿真模型,提高预测的准确性和可靠性。
动力电池热失控仿真技术的重要性不容忽视,对于推动电动车行业的发展和普及具有重要意义。
通过不断改进和创新仿真技术,可以更好地保障电动车的安全性和可靠性,促进行业的健康发展。
2. 正文2.1 动力电池热失控的成因分析1. 过充电和过放电:当电池过充电或过放电时,会导致电池内部产生过多的热量,从而引发热失控现象。
动力电池的检测实训报告

一、实训背景随着我国新能源汽车产业的快速发展,动力电池作为新能源汽车的核心部件,其性能和质量直接影响到新能源汽车的运行效率和安全性。
为了提高我国动力电池检测技术水平,培养一批具备实际操作能力的检测人才,我校组织了动力电池检测实训课程。
本次实训旨在让学生掌握动力电池检测的基本原理、方法和设备操作,提高学生的动手能力和实践技能。
二、实训目的1. 了解动力电池的基本结构、工作原理和性能指标。
2. 掌握动力电池检测的基本方法、设备操作和数据处理。
3. 提高学生的动手能力和实践技能,为今后从事动力电池检测工作打下基础。
三、实训内容1. 动力电池基础知识(1)动力电池的结构:电池壳体、正负极材料、电解液、隔膜等。
(2)动力电池的工作原理:化学反应产生电能,电能通过电路传输到电动机,驱动车辆行驶。
(3)动力电池的性能指标:能量密度、循环寿命、安全性能、充放电倍率等。
2. 动力电池检测方法(1)外观检查:观察电池壳体、正负极材料、电解液、隔膜等部件是否存在异常。
(2)电性能测试:测量电池的电压、电流、内阻、容量等参数。
(3)热性能测试:测量电池在不同温度下的充放电性能、热稳定性等。
(4)安全性能测试:测试电池在短路、过充、过放等异常情况下的安全性。
3. 动力电池检测设备操作(1)万用表:测量电池的电压、电流、内阻等参数。
(2)电池内阻测试仪:测量电池的内阻。
(3)电池充放电测试仪:模拟电池的实际充放电过程,测试电池的容量、循环寿命等参数。
(4)热像仪:测量电池在不同温度下的热分布情况。
4. 动力电池检测数据处理(1)收集测试数据:将测试过程中的电压、电流、内阻、温度等数据记录下来。
(2)数据分析:对收集到的数据进行整理、分析和处理,得出电池的性能指标。
(3)结果判断:根据电池的性能指标,判断电池的质量和寿命。
四、实训过程1. 实训前期:学生通过查阅资料、课堂学习,了解动力电池的基本知识、检测方法和设备操作。
2. 实训中期:学生在指导下,进行实际操作,熟悉检测设备的操作流程,掌握检测方法。
动力电池安全性评估与风险控制

动力电池安全性评估与风险控制一、绪论随着全球对于环保和可持续发展的要求逐渐增加,电动汽车的出现成为了一种新的交通工具,也受到了不同程度的关注。
然而,随着电动汽车的普及,电动车的动力电池已经成为一个重要的问题,其安全性评估与风险控制迫在眉睫。
二、动力电池的构成和技术动力电池是由多个电池单体组成的,主要由正负极集合体、分隔膜、电解质和电池外壳等组成。
动力电池通常采用锂离子电池或钴酸锂电池,也有部分采用三元材料的电池。
在电池工作的过程中,电池单体内部的化学反应会导致电池内部的电压和温度变化,当电压和温度超过一定的范围,就会导致电池的损坏或爆炸。
因此,动力电池需要对其进行安全评估和风险控制。
三、动力电池的安全评估和风险控制1. 动力电池安全评估动力电池的安全评估主要目的是评价电池的性能和安全性。
安全评估需要从以下几个方面进行:(1)正常工作条件下的温度和压力变化在正常工作条件下,动力电池单体内部的温度和压力是有一定的变化范围的。
不同工作条件下,变化的范围不一样。
因此,需要对不同的工作条件进行测试。
(2)异常工作条件下的安全性在车辆事故等异常情况下,电池单体的电压和温度变化比较大,这样,就会导致电池的损坏或爆炸。
因此,需要对异常情况下的安全性进行测试。
(3)电池使用寿命由于动力电池的使用寿命有限,电池单体的性能有所变化,因此需要进行寿命测试,并对使用寿命进行预测。
2. 动力电池的风险控制动力电池的风险控制主要是为了降低动力电池的损坏和爆炸的风险。
因此,风险控制需要从以下几个方面进行:(1)电池的加热控制当电池单体内部温度升高时,需要立即停止充电和放电过程,保证电池的温度在安全范围内。
同时,需要对电池进行控制,使其进入休眠状态。
(2)电池的过压和欠压保护当电池单体电压超过安全范围时,需要立即停止充电和放电过程,保证电池的电压在安全范围内。
同时,需要对电池进行控制,使其进入休眠状态。
(3)电池的短路和过流保护在电池内部出现短路和过流时,需要立即停止充电和放电过程,保证电池的温度在安全范围内。
动力电池的安全性能测试与评估方法

动力电池的安全性能测试与评估方法动力电池是电动汽车的重要组成部分,其安全性能的测试和评估对于电动汽车的安全性能有着至关重要的作用。
本文将介绍动力电池的安全性能测试与评估方法,以确保电池的可靠性和安全性。
一、电池性能测试方法1. 循环测试:通过模拟实际使用情况,进行充放电循环测试,以评估电池的耐久性和寿命。
2. 高温测试:将电池置于高温环境中,进行充放电测试,以评估电池在极端条件下的性能和稳定性。
3. 低温测试:将电池置于低温环境中,进行充放电测试,以评估电池在低温环境下的性能和可靠性。
4. 短路测试:对电池进行短路测试,以评估电池在短路情况下的安全性和稳定性。
5. 冲击测试:对电池进行冲击测试,以评估电池在碰撞等意外情况下的安全性能。
二、电池安全性能评估方法1. 阻燃性测试:对电池进行阻燃性测试,以评估电池在火灾情况下的安全性能。
2. 过充保护测试:对电池进行过充保护测试,以评估电池在过充情况下的安全性能。
3. 过放保护测试:对电池进行过放保护测试,以评估电池在过放情况下的安全性能。
4. 渗漏测试:对电池进行渗漏测试,以评估电池的密封性和防护性能。
5. 振动测试:对电池进行振动测试,以评估电池在振动环境下的安全性能。
三、电池安全性能评估标准1. 国际标准:如ISO 12405-1、IEC 62660-1等,这些标准对于电池的安全性能测试和评估提供了详细的要求和指导。
2. 行业标准:各个电动汽车制造商和研究机构会制定相应的行业标准,以满足自身产品的安全性要求。
四、电池安全性能的重要性1. 保障电动汽车的行驶安全:电池是电动汽车的能量源,其安全性能直接关系到车辆的行驶安全。
2. 预防火灾和爆炸事故:动力电池一旦发生故障可能引发火灾和爆炸事故,因此必须对其进行严格的安全性能测试和评估。
3. 提高用户信心:通过对电池的安全性能测试和评估,可以提高用户对电动汽车的信心,促进电动汽车市场的发展。
综上所述,动力电池的安全性能测试与评估方法是确保电动汽车安全性能的重要环节。
新能源汽车动力电池性能测试与评价实验报告

新能源汽车动力电池性能测试与评价实验报告一、实验目的随着新能源汽车的快速发展,动力电池作为其核心部件,其性能直接影响着车辆的续航里程、动力性能和安全性。
本次实验旨在对新能源汽车动力电池的性能进行全面测试与评价,为新能源汽车的研发、生产和使用提供科学依据。
二、实验设备与材料1、测试设备电池充放电测试系统:能够精确控制电池的充放电过程,并实时监测电池的电压、电流、容量等参数。
温度控制系统:用于控制实验环境温度,确保测试结果的准确性。
内阻测试仪:用于测量电池的内阻。
电池循环寿命测试设备:对电池进行多次充放电循环,评估其循环寿命。
2、测试样品选取市场上常见的几种新能源汽车动力电池,包括三元锂电池、磷酸铁锂电池等。
3、辅助材料连接线缆、夹具等。
三、实验方法1、容量测试将电池充满电后,以恒定电流放电至截止电压,记录放电时间和放电容量,计算电池的实际容量。
2、内阻测试使用内阻测试仪在电池不同状态(满电、半电、亏电)下测量其内阻。
3、循环寿命测试对电池进行多次充放电循环,设定一定的充放电深度,观察电池容量衰减情况,直至电池容量低于初始容量的 80%,记录循环次数。
4、高低温性能测试将电池分别置于不同温度环境(高温、低温)中,进行充放电测试,观察电池性能变化。
5、安全性能测试进行过充、过放、短路、针刺等实验,观察电池的反应,评估其安全性能。
四、实验结果与分析1、容量测试结果不同类型的电池容量存在差异。
三元锂电池在本次测试中的平均容量为_____Ah,磷酸铁锂电池的平均容量为_____Ah。
容量的大小直接影响着新能源汽车的续航里程。
随着电池使用次数的增加,容量会逐渐衰减。
经过多次充放电循环后,三元锂电池的容量衰减速度相对较快,而磷酸铁锂电池的容量衰减较为缓慢。
2、内阻测试结果电池内阻随着电池的充放电状态和使用次数而变化。
在满电状态下,内阻较小;随着电量的减少,内阻逐渐增大。
经过长期使用后,内阻会明显增大,这会影响电池的放电性能和充电效率。
纯电动汽车动力性匹配设计与模型仿真

Modeling and Simulation 建模与仿真, 2020, 9(3), 357-366Published Online August 2020 in Hans. /journal/moshttps:///10.12677/mos.2020.93036Dynamic Matching Design and ModelSimulation of Pure Electric VehicleWentao Zhang, Li Ye, Zhijun Zhang, Huan Ye, Mengya ZhangSchool of Power Engineering, University of Shanghai for Science and Technology, ShanghaiReceived: Aug. 6th, 2020; accepted: Aug. 20th, 2020; published: Aug. 27th, 2020AbstractBased on the selection of basic vehicle parameters and the determination of performance indica-tors, this paper carries out the design matching of dynamic performance parameters of pure elec-tric vehicles. Then, a pure electric vehicle dynamic simulation model is established by vehicle si-mulation software, and the vehicle dynamic performance index is simulated and analyzed by in-putting relevant parameters. Finally, the rationality of simulation model and parameter matching is verified by real car test. This study can provide theoretical basis for the matching design of var-ious systems in the initial stage of pure electric vehicles, carry out range and performance test evaluation of vehicle performance, and provide reference for the analysis of dynamic performance and economic index of pure electric vehicles.KeywordsPure Electric Vehicle, Parameter Design Matching, Vehicle Power Model, Simulation Analysis纯电动汽车动力性匹配设计与模型仿真张文韬,叶立,张志军,叶欢,张梦伢上海理工大学动力工程学院,上海收稿日期:2020年8月6日;录用日期:2020年8月20日;发布日期:2020年8月27日摘要本文基于对整车基本参数的选取与性能指标的确定,进行了纯电动汽车动力性能参数的设计匹配。
新能源汽车动力电池的性能测试与评估

新能源汽车动力电池的性能测试与评估新能源汽车正逐渐成为人们生活中的一部分,而动力电池作为新能源汽车的重要组成部分,其性能测试与评估显得尤为重要。
一、动力电池的性能动力电池是新能源汽车的动力来源,其性能主要包括电容量、工作电压、充电速率、循环寿命等。
电容量是指电池储存电能的能力,通常以千瓦时为单位。
工作电压是指电池正负极间的电压差,一般为200至400伏。
充电速率是指电池能够承受的充电电流强度,通常以C值表示,C值越大说明充电速度越快。
循环寿命是指电池能够进行多少次充放电循环,也成为电池的使用寿命。
二、测试与评估方法1.静态测试静态测试是在室温下对电池进行测试,测试电池的容量、电压和内阻等指标。
首先对电池进行放电,在一定间隔时间后进行充电,测量电池的容量和电压,以此判断电池的性能表现。
2.动态测试动态测试是将电池装入新能源汽车中进行测试,模拟实际使用环境,测试电池的充电时间、续航里程、电池温度等指标。
由于电池在实际使用中受到路况、气温、车速等因素的影响,所以动态测试更能反映电池的实际性能。
3.循环测试循环测试是模拟实际使用中对电池进行多次充放电循环测试,测试电池的循环寿命。
此测试方式能够更准确地反映电池的使用寿命。
4.安全测试安全测试是对电池进行外部短路、过充、过放等条件进行测试,测试电池的安全性能。
此测试方式是为了避免电池出现燃烧、爆炸等安全隐患。
三、评估指标1.电池容量电池容量是反映电池能否满足车辆续航需求的重要指标。
一般来说,车辆电池容量应该能够满足日常使用需求,并且必须考虑到气温、使用环境等因素对电池容量的影响。
2.充电速率充电速率是电池充电所需时间的重要指标。
电池充电速率越快,车辆的使用效率就越高。
同时,也可以防止电池充电过程中受到过度损伤。
3.循环寿命循环寿命是反映电池使用寿命的重要指标。
电池的循环寿命越长,车辆使用寿命也就越长。
4.安全性安全性是电池评估中重要的一个指标,主要包括电池的过充、过放、短路、温度过高等安全问题。
电动汽车用动力电池模型仿真及寿命特性研究

电动汽车用动力电池模型仿真及寿命特性研究一、本文概述随着环保理念的深入人心和能源结构的逐步转型,电动汽车(EV)在全球范围内得到了广泛的关注和应用。
作为电动汽车的“心脏”,动力电池的性能和寿命直接决定了电动汽车的行驶里程、使用成本和安全性。
因此,对电动汽车用动力电池模型仿真及寿命特性的研究,不仅有助于提升电动汽车的整体性能,也对推动电动汽车产业的可持续发展具有重要意义。
本文旨在通过深入研究电动汽车用动力电池的模型仿真技术,探讨其寿命特性的影响因素和变化规律。
本文将系统介绍电动汽车用动力电池的种类、结构和工作原理,为后续的研究提供理论基础。
通过构建动力电池的数学模型和仿真平台,模拟电池在不同工况下的运行状态,分析电池性能参数的变化趋势。
在此基础上,本文将重点研究动力电池的寿命特性,包括循环寿命、日历寿命和荷电状态(SOC)对寿命的影响,揭示动力电池性能衰减的内在机理。
结合实验结果和仿真数据,提出延长动力电池寿命的有效措施和建议,为电动汽车的设计和制造提供参考。
本文的研究方法包括文献综述、理论分析、模型构建、仿真实验和实验研究等。
通过综合运用这些研究方法,力求全面、深入地揭示电动汽车用动力电池的寿命特性,为电动汽车产业的健康、快速发展提供有力支撑。
二、动力电池模型仿真研究随着电动汽车的快速发展,动力电池作为其核心部件,其性能对电动汽车的整体性能起着决定性作用。
因此,对动力电池的模型仿真研究显得尤为重要。
模型仿真不仅可以对电池的性能进行预测和优化,还能为电池管理系统的设计提供理论支持。
动力电池模型仿真的关键在于建立准确的电池模型。
目前,常用的电池模型主要包括电化学模型、热模型、电学模型等。
其中,电化学模型能够详细描述电池内部的电化学反应过程,对于理解电池性能衰减机制具有重要意义。
热模型则主要关注电池在工作过程中产生的热量分布和散热情况,对于电池热管理系统的设计至关重要。
电学模型则主要描述电池的电气特性,如内阻、开路电压等,是电池管理系统进行电池状态估计和能量管理的重要依据。
《2024年电动汽车动力系统设计及仿真研究》范文

《电动汽车动力系统设计及仿真研究》篇一一、引言随着全球对环境保护和能源消耗的日益关注,电动汽车的研发与推广已成为当今汽车工业的重要方向。
电动汽车动力系统作为其核心部分,其设计及性能直接关系到整车的运行效率、续航里程及用户体验。
本文旨在研究电动汽车动力系统的设计方法及其仿真研究,为电动汽车的进一步发展提供理论支持。
二、电动汽车动力系统设计1. 电池组设计电池组是电动汽车的动力来源,其设计直接关系到车辆的续航里程和充电速度。
电池组的设计应考虑电池类型(如锂离子电池、镍氢电池等)、电池容量、电池包结构等因素。
在设计中,需要确保电池组具有良好的安全性能、较长的使用寿命及快速充电的能力。
2. 电机及其控制器设计电机及其控制器是电动汽车动力传递的核心部分。
电机设计需考虑其功率、扭矩、效率等因素,以实现高效的动力输出。
控制器则需根据电机的特性进行优化设计,确保电机在不同工况下都能稳定运行。
3. 传动系统设计传动系统包括变速器、主减速器等部件,其设计需考虑传动效率、噪音、振动等因素。
在设计中,应尽量减小传动损失,提高传动效率,同时保证车辆的驾驶舒适性。
三、仿真研究仿真研究是电动汽车动力系统设计的重要环节,通过建立动力系统的仿真模型,可以对设计方案进行验证和优化。
1. 仿真模型建立根据动力系统的设计要求,建立包括电池组、电机、控制器、传动系统等部分的仿真模型。
在建模过程中,需考虑各部件的特性和相互关系,确保模型的准确性和可靠性。
2. 仿真分析通过仿真分析,可以得出动力系统的性能参数,如输出功率、扭矩、效率等。
同时,还可以对不同设计方案进行对比,找出最优的设计方案。
在仿真分析中,还需考虑不同工况(如城市道路、高速公路等)对动力系统性能的影响。
四、结论通过对电动汽车动力系统的设计和仿真研究,可以得出以下结论:1. 电池组的设计应考虑电池类型、容量及结构等因素,以确保车辆具有较长的续航里程和快速的充电速度。
2. 电机及其控制器的设计需考虑功率、扭矩、效率等因素,以实现高效的动力输出和稳定的运行。
新能源汽车动力电池安全性能测试研究

新能源汽车动力电池安全性能测试研究第一章介绍近年来,新能源汽车越来越受到关注,其中电动汽车成为热门产品之一。
动力电池是电动汽车最重要的组件之一,其安全性能直接影响整车的安全性能。
因此,动力电池的安全性能测试显得尤为重要。
本文将介绍新能源汽车动力电池安全性能测试的研究现状和未来的发展方向。
第二章动力电池安全性能测试2.1 电池热失控电池热失控是一种比较严重的安全问题,可以导致电池发生爆炸或者火灾。
电池热失控包括过充、过放、外部短路、撕裂等。
针对电池热失控问题,目前采用的测试方法主要有充放电测试、热冲击测试、振动测试、碰撞测试、穿刺测试等。
2.2 电池性能衰减电池性能衰减是指电池在使用过程中,由于自然老化、充放电循环次数等因素导致电池性能逐渐下降。
电池的性能衰减会导致电量减少、续航里程缩短等问题,为了延长电池的使用寿命,测试电池的性能衰减是非常必要的。
2.3 电池安全防护电池安全防护是为了保证电池在发生热失控时能够及时得到控制,避免电池造成更大范围的危害。
目前,最常用的电池安全防护措施是采用BMS(电池管理系统)来对电池进行监控和控制。
BMS会实时监测电池温度、电压、电流等参数,并在必要时通过控制器对电池进行保护。
第三章测试方法为了保证动力电池的安全性能,需要对其进行多种测试。
根据测试目的、测试标准和测试条件的不同,测试方法也各有特点。
主要测试方法如下:3.1 充放电测试采用外部电源对电池进行充电和放电,记录电池充电和放电过程中的电压、电流、温度等参数。
通过分析电池的充放电性能,可以判断电池的单体电池容量、循环寿命、放电性能等指标。
3.2 热冲击测试将电池放入高温或低温环境中,使其在很短的时间内快速升温或降温,然后观察电池是否会热失控。
通过热冲击测试,可以测试电池的耐高温和耐低温性能。
3.3 振动测试将电池进行频率和幅度不同的振动,观察电池是否会发生异响或变形。
通过振动测试,可以测试电池的耐振性能。
新能源汽车动力电池的安全性研究

新能源汽车动力电池的安全性研究在当今汽车行业的快速发展中,新能源汽车凭借其环保、节能等优势逐渐崭露头角。
然而,新能源汽车的动力电池安全性问题一直是人们关注的焦点。
动力电池作为新能源汽车的核心部件,其安全性直接关系到车辆的使用安全以及消费者的生命财产安全。
新能源汽车动力电池主要包括锂离子电池、镍氢电池等类型。
其中,锂离子电池因其能量密度高、循环寿命长等优点,成为目前新能源汽车最常用的动力电池类型。
但锂离子电池在使用过程中也存在一些安全隐患,如热失控、过充过放、短路等。
热失控是新能源汽车动力电池最严重的安全问题之一。
当电池内部温度过高时,可能会引发一系列连锁反应,导致电池起火甚至爆炸。
造成热失控的原因主要有内部短路、外部短路、过充、高温等。
内部短路可能是由于电池生产过程中的瑕疵,或者在使用过程中电池受到挤压、穿刺等机械损伤导致。
外部短路则可能是由于车辆电路故障或者外部环境因素引起。
过充会使电池内部产生过多的热量,而高温环境会加速电池内部的化学反应,增加热失控的风险。
过充过放也是影响动力电池安全性的重要因素。
过充会导致电池内部结构损坏,产生大量气体,增加电池内部压力,严重时可能引发爆炸。
过放则会使电池活性物质减少,降低电池的容量和寿命,甚至可能导致电池内部短路。
为了避免过充过放,新能源汽车通常配备了电池管理系统(BMS),对电池的充放电过程进行实时监测和控制。
然而,BMS 也并非万无一失,如果出现故障或者误判,仍然可能导致过充过放的情况发生。
短路是另一个常见的安全隐患。
短路可能是由于电池内部的正负极直接接触,或者外部导体使电池的正负极短路。
短路会导致电流瞬间增大,产生大量热量,引发安全事故。
此外,电池在使用过程中的振动、碰撞等也可能导致电池内部结构松动,增加短路的风险。
为了提高新能源汽车动力电池的安全性,科研人员和汽车厂商采取了一系列措施。
在电池材料方面,不断研发新型的正负极材料和电解质,提高电池的稳定性和安全性。
动力电池的安全性与可靠性分析
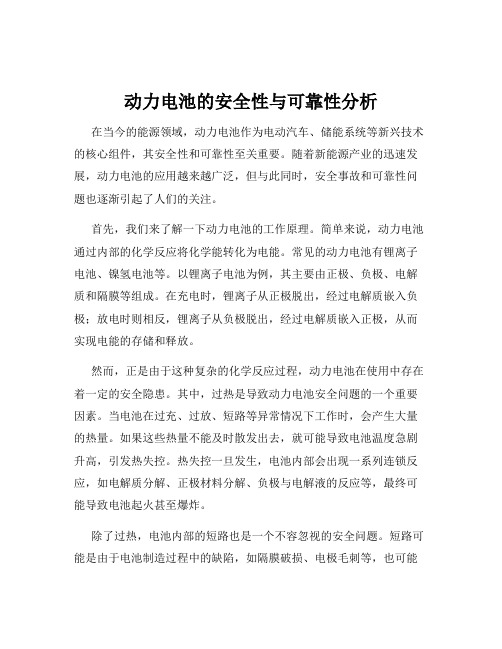
动力电池的安全性与可靠性分析在当今的能源领域,动力电池作为电动汽车、储能系统等新兴技术的核心组件,其安全性和可靠性至关重要。
随着新能源产业的迅速发展,动力电池的应用越来越广泛,但与此同时,安全事故和可靠性问题也逐渐引起了人们的关注。
首先,我们来了解一下动力电池的工作原理。
简单来说,动力电池通过内部的化学反应将化学能转化为电能。
常见的动力电池有锂离子电池、镍氢电池等。
以锂离子电池为例,其主要由正极、负极、电解质和隔膜等组成。
在充电时,锂离子从正极脱出,经过电解质嵌入负极;放电时则相反,锂离子从负极脱出,经过电解质嵌入正极,从而实现电能的存储和释放。
然而,正是由于这种复杂的化学反应过程,动力电池在使用中存在着一定的安全隐患。
其中,过热是导致动力电池安全问题的一个重要因素。
当电池在过充、过放、短路等异常情况下工作时,会产生大量的热量。
如果这些热量不能及时散发出去,就可能导致电池温度急剧升高,引发热失控。
热失控一旦发生,电池内部会出现一系列连锁反应,如电解质分解、正极材料分解、负极与电解液的反应等,最终可能导致电池起火甚至爆炸。
除了过热,电池内部的短路也是一个不容忽视的安全问题。
短路可能是由于电池制造过程中的缺陷,如隔膜破损、电极毛刺等,也可能是由于外部因素,如碰撞、挤压等导致的。
短路会使电池瞬间释放出大量的能量,产生高温和火花,从而引发安全事故。
此外,动力电池的可靠性也是影响其广泛应用的一个关键因素。
可靠性主要包括电池的循环寿命、容量保持率、自放电率等指标。
循环寿命是指电池在经过一定次数的充放电循环后,其性能下降到一定程度所经历的循环次数。
容量保持率则反映了电池在使用过程中容量的衰减情况。
自放电率则表示电池在闲置状态下电量的损失速度。
如果动力电池的可靠性不高,不仅会增加用户的使用成本,还会影响整个系统的稳定性和可靠性。
为了提高动力电池的安全性和可靠性,科研人员和企业采取了一系列措施。
在电池设计方面,通过优化电极材料、电解质配方、隔膜结构等,提高电池的热稳定性和安全性。
动力电池产品的电池包安全设计与验证
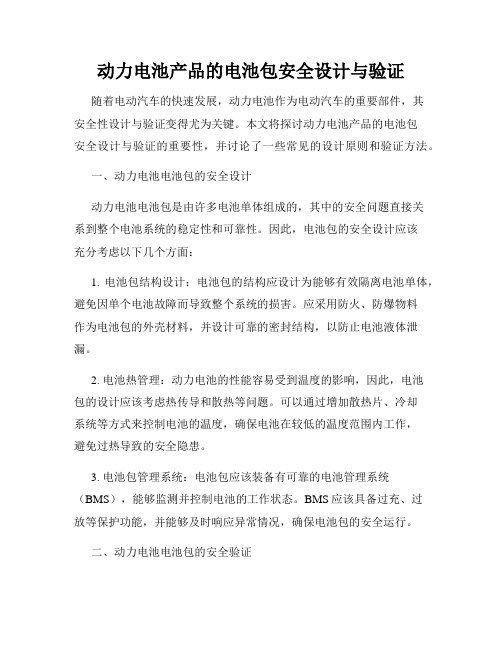
动力电池产品的电池包安全设计与验证随着电动汽车的快速发展,动力电池作为电动汽车的重要部件,其安全性设计与验证变得尤为关键。
本文将探讨动力电池产品的电池包安全设计与验证的重要性,并讨论了一些常见的设计原则和验证方法。
一、动力电池电池包的安全设计动力电池电池包是由许多电池单体组成的,其中的安全问题直接关系到整个电池系统的稳定性和可靠性。
因此,电池包的安全设计应该充分考虑以下几个方面:1. 电池包结构设计:电池包的结构应设计为能够有效隔离电池单体,避免因单个电池故障而导致整个系统的损害。
应采用防火、防爆物料作为电池包的外壳材料,并设计可靠的密封结构,以防止电池液体泄漏。
2. 电池热管理:动力电池的性能容易受到温度的影响,因此,电池包的设计应该考虑热传导和散热等问题。
可以通过增加散热片、冷却系统等方式来控制电池的温度,确保电池在较低的温度范围内工作,避免过热导致的安全隐患。
3. 电池包管理系统:电池包应该装备有可靠的电池管理系统(BMS),能够监测并控制电池的工作状态。
BMS应该具备过充、过放等保护功能,并能够及时响应异常情况,确保电池包的安全运行。
二、动力电池电池包的安全验证动力电池电池包的安全验证是指通过一系列审查和测试,确认电池包的设计和制造满足特定的安全标准和要求。
常见的验证方法包括以下几个方面:1. 环境适应性测试:电池包应在不同的环境条件下进行测试,包括高温、低温、高湿度等,以验证其在各种复杂环境下的安全性能。
2. 电池短路测试:通过模拟电池短路情况,测试电池包的短路保护功能。
测试时可以使用外部短路装置,将电池正负极短路并观察电池包的反应和安全保护措施是否能够及时生效。
3. 振动与冲击测试:电池包应该在振动和冲击条件下进行测试,以验证其抗振性和抗冲击性。
测试时可以采用模拟道路行驶的振动和冲击,检测电池包在路况不良时的安全性能。
4. 过充与过放测试:通过模拟过充和过放条件,测试电池包的过压保护和过放保护功能。
动力电池包仿真评价标准
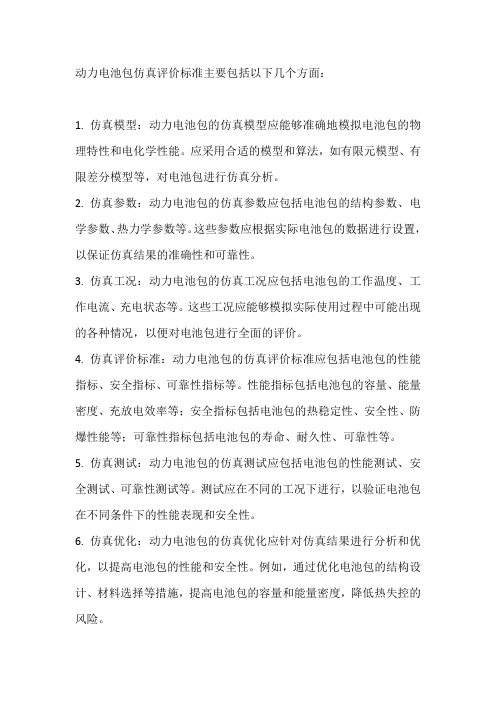
动力电池包仿真评价标准主要包括以下几个方面:
1. 仿真模型:动力电池包的仿真模型应能够准确地模拟电池包的物理特性和电化学性能。
应采用合适的模型和算法,如有限元模型、有限差分模型等,对电池包进行仿真分析。
2. 仿真参数:动力电池包的仿真参数应包括电池包的结构参数、电学参数、热力学参数等。
这些参数应根据实际电池包的数据进行设置,以保证仿真结果的准确性和可靠性。
3. 仿真工况:动力电池包的仿真工况应包括电池包的工作温度、工作电流、充电状态等。
这些工况应能够模拟实际使用过程中可能出现的各种情况,以便对电池包进行全面的评价。
4. 仿真评价标准:动力电池包的仿真评价标准应包括电池包的性能指标、安全指标、可靠性指标等。
性能指标包括电池包的容量、能量密度、充放电效率等;安全指标包括电池包的热稳定性、安全性、防爆性能等;可靠性指标包括电池包的寿命、耐久性、可靠性等。
5. 仿真测试:动力电池包的仿真测试应包括电池包的性能测试、安全测试、可靠性测试等。
测试应在不同的工况下进行,以验证电池包在不同条件下的性能表现和安全性。
6. 仿真优化:动力电池包的仿真优化应针对仿真结果进行分析和优化,以提高电池包的性能和安全性。
例如,通过优化电池包的结构设计、材料选择等措施,提高电池包的容量和能量密度,降低热失控的风险。
浅谈新能源汽车动力电池包安全性检测的重要性
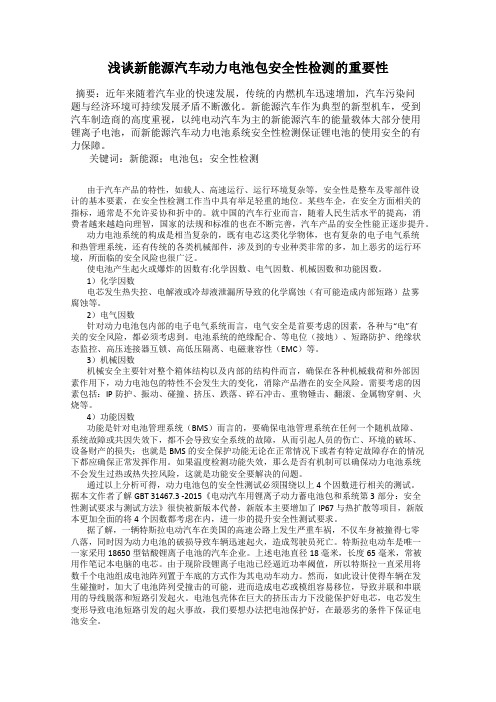
浅谈新能源汽车动力电池包安全性检测的重要性摘要:近年来随着汽车业的快速发展,传统的内燃机车迅速增加,汽车污染问题与经济环境可持续发展矛盾不断激化。
新能源汽车作为典型的新型机车,受到汽车制造商的高度重视,以纯电动汽车为主的新能源汽车的能量载体大部分使用锂离子电池,而新能源汽车动力电池系统安全性检测保证锂电池的使用安全的有力保障。
关键词:新能源;电池包;安全性检测由于汽车产品的特性,如载人、高速运行、运行环境复杂等,安全性是整车及零部件设计的基本要素,在安全性检测工作当中具有举足轻重的地位。
某些车企,在安全方面相关的指标,通常是不允许妥协和折中的。
就中国的汽车行业而言,随着人民生活水平的提高,消费者越来越趋向理智,国家的法规和标准的也在不断完善,汽车产品的安全性能正逐步提升。
动力电池系统的构成是相当复杂的,既有电芯这类化学物体,也有复杂的电子电气系统和热管理系统,还有传统的各类机械部件,涉及到的专业种类非常的多,加上恶劣的运行环境,所面临的安全风险也很广泛。
使电池产生起火或爆炸的因数有:化学因数、电气因数、机械因数和功能因数。
1)化学因数电芯发生热失控、电解液或冷却液泄漏所导致的化学腐蚀(有可能造成内部短路)盐雾腐蚀等。
2)电气因数针对动力电池包内部的电子电气系统而言,电气安全是首要考虑的因素,各种与“电”有关的安全风险,都必须考虑到。
电池系统的绝缘配合、等电位(接地)、短路防护、绝缘状态监控、高压连接器互锁、高低压隔离、电磁兼容性(EMC)等。
3)机械因数机械安全主要针对整个箱体结构以及内部的结构件而言,确保在各种机械载荷和外部因素作用下,动力电池包的特性不会发生大的变化,消除产品潜在的安全风险。
需要考虑的因素包括:IP防护、振动、碰撞、挤压、跌落、碎石冲击、重物锤击、翻滚、金属物穿刺、火烧等。
4)功能因数功能是针对电池管理系统(BMS)而言的,要确保电池管理系统在任何一个随机故障、系统故障或共因失效下,都不会导致安全系统的故障,从而引起人员的伤亡、环境的破坏、设备财产的损失;也就是BMS的安全保护功能无论在正常情况下或者有特定故障存在的情况下都应确保正常发挥作用。
动力电池包仿真评价标准(一)
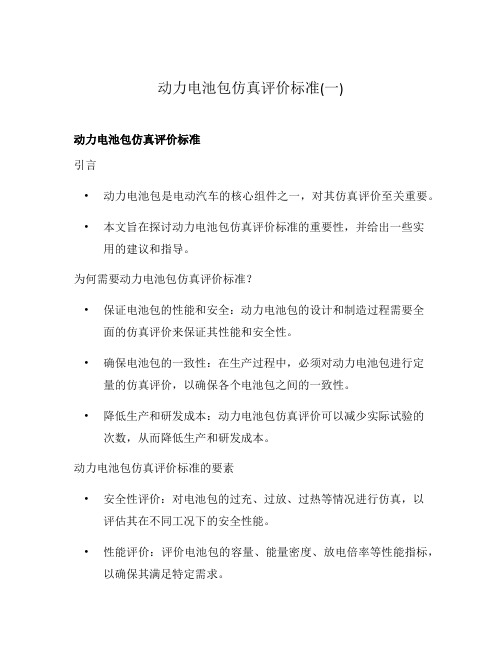
动力电池包仿真评价标准(一)动力电池包仿真评价标准引言•动力电池包是电动汽车的核心组件之一,对其仿真评价至关重要。
•本文旨在探讨动力电池包仿真评价标准的重要性,并给出一些实用的建议和指导。
为何需要动力电池包仿真评价标准?•保证电池包的性能和安全:动力电池包的设计和制造过程需要全面的仿真评价来保证其性能和安全性。
•确保电池包的一致性:在生产过程中,必须对动力电池包进行定量的仿真评价,以确保各个电池包之间的一致性。
•降低生产和研发成本:动力电池包仿真评价可以减少实际试验的次数,从而降低生产和研发成本。
动力电池包仿真评价标准的要素•安全性评价:对电池包的过充、过放、过热等情况进行仿真,以评估其在不同工况下的安全性能。
•性能评价:评价电池包的容量、能量密度、放电倍率等性能指标,以确保其满足特定需求。
•故障模拟:模拟电池包内部的故障情况,例如电芯失效、电芯短路等,以评估电池包在故障情况下的安全性能。
•生命周期评价:模拟电池包在不同使用条件下的寿命表现,以评估其寿命和可靠性。
•环境适应性评价:评估电池包在不同环境条件下的性能和安全性,包括高温、低温、高湿度等。
•效率评估:评估电池包的能量效率和循环效率,以提高电池包的能源利用率。
动力电池包仿真评价的应用•评估不同设计方案的性能和安全性,以选择最佳方案。
•优化电池管理系统的算法,提高电池包的性能和使用寿命。
•预测电池包在实际使用中的性能衰减趋势,以便及时维护或更换电池包。
结论•动力电池包的仿真评价标准对于保证其性能、安全性和一致性至关重要。
•各种评价要素可以帮助设计师和制造商选择最佳方案,优化电池管理系统,并预测电池包的寿命表现。
注:本文参考了相关技术资料和研究成果,并进行了整理和总结。
如需详细了解动力电池包仿真评价标准,请参考相关的技术文献和标准。
- 1、下载文档前请自行甄别文档内容的完整性,平台不提供额外的编辑、内容补充、找答案等附加服务。
- 2、"仅部分预览"的文档,不可在线预览部分如存在完整性等问题,可反馈申请退款(可完整预览的文档不适用该条件!)。
- 3、如文档侵犯您的权益,请联系客服反馈,我们会尽快为您处理(人工客服工作时间:9:00-18:30)。
电动车动力电池安全性测试与仿真来源:仪商网原载:汽车测试网关于电动车动力电池安全性测试,目前国内大部分企业已依据《电动汽车用动力蓄电池安全要求》报批稿(以下简称报批稿)开展。
该报批稿预计在2019年上半年作为强制性国家标准发布,以代替GB/T31467.3-2015《电动汽车用锂离子动力蓄电池包和系统第3部分:安全性要求与测试方法》。
与GB/T 31467.3相比,报批稿在试验项目和试验环境条件方面都有多项更新,涵盖了电池单体和电池包。
其中与电池包结构相关的测试项目变化主要如下:1.振动疲劳。
随机振动的RMS水平有明显降低,例如Z轴加速度RMS由1.44G降为0.64G;每个方向的振动持续时间也从21小时缩短到12小时;增加了24Hz定频振动(中间有过一个版本还增加了扫频振动,后来取消);取消了加载次序必须按Z-Y-X的规定,检测机构可自行选择加载次序,以节省转换时间。
2.机械冲击。
由Z向3次25g半正弦波冲击改为正负Z向各6次7g半正弦冲击,并规定了半正弦波形的容差范围。
3.模拟碰撞。
报批稿的测试要求与GB/T 31467.3基本相同,测试对象水平安装在带有支架的台车上,根据测试对象的使用环境给台车施加规定的脉冲,脉冲分为X向和Y向施加。
报批稿还规定,试验对象存在多个安装方向(X/ Y/ Z)时,按照加速度大的安装方向进行试验。
4.挤压。
挤压截止力由200kN降为100kN;增加了三拱形挤压头作为可选项,试验时可选择单拱形压头,也可选择三拱形压头;明确了X向和Y向的挤压测试可分开在两个试验对象上执行。
从以上几点变化可以看出,报批稿对电池包结构强度要求至少降低了一半。
只要电池包结构的设计不是特别单薄,通过报批稿规定的测试项目难度并不大。
但报批稿只考虑了最基本的安全要求,企业进行测试和仿真分析时应该采用更加严苛的标准。
振动疲劳仿真电池包振动测试是模拟试验场强化道路激励,考察电池包的结构耐久性能,试验装置如图1所示。
图1 电池包振动测试设备振动测试包含三个方向的随机振动测试和和三个方向的24Hz定频测试,必须在同一个试验对象上实施。
报批稿要求电池在振动试验后无泄漏、外壳破裂、起火或爆炸现象,但疲劳仿真分析无法对起火和爆炸做出判断,只能判断电池包结构是否发生开裂。
建议将仿真分析目标值设定为电池包结构的损伤值<0.2,留出一定安全裕度。
电池包随机振动测试是施加单通道加速度激励,随机载荷用如图2所示的PSD曲线描述,大多数疲劳软件都能模拟这种工况。
推荐采用频域疲劳分析软件CAEFatigue,也可采用更常见的Femfat和nCode软件。
图2 报批稿规定的随机载荷PSD曲线虽然报批稿中的载荷PSD曲线是来源于多个车型在通州试验场的路试,但根据本人做的一点研究,对于国内大部分整车企业的整车耐久路试规范,报批稿所规定的随机振动载荷强度是略低于试验场强化路工况的。
也就是说,即使电池包通过了报批稿规定的随机振动测试,在试验场强化路进行整车耐久试验时,仍有可能出现疲劳破坏。
所以建议进行随机振动疲劳测试和仿真时,将图2的PSD曲线提升20%。
根据本人经验,PSD曲线提升20%后,三个方向各持续激励12小时后所造成的电池包总的结构损伤大致相当于整车在盐城、襄樊或垫江试验场的综合坏路上行驶2000-3000公里(不含连接路面)。
报批稿中的24Hz定频试验,对应实际场景是车辆匀速通过通州试验场的搓板路。
实际上,搓板路工况虽然对悬架和悬置系统是比较严苛的考验,但对电池包结构的伤害并不大。
对于定频振动疲劳分析,采用疲劳软件中最基本的等幅载荷分析功能即可,例如Femfat的Basic模块。
我们一般要求电池包一阶固有频率大于30Hz,只要满足这个要求,24Hz定频激励下电池包结构各点的应力响应基本都能控制在疲劳极限之下,计算出的损伤值非常接近0。
机械冲击仿真机械冲击测试模拟车辆以较高速度通过障碍物或坑洼时电池包受到的冲击,试验装置如图3所示。
图3 机械冲击测试装置机械冲击测试只考虑Z向载荷,正负Z向各进行6次持续时间为6ms的半正弦冲击,规定冲击加速度峰值为7g,容差上限为8.05g,下限为5.95g。
按报批稿规定,电池包在冲击试验后不发生泄漏、外壳破裂、起火或爆炸即算合格。
实际上这种冲击工况发生后,用户有很大可能性不更换电池包而是继续使用,所以考察标准应适当加严,应要求电池包在冲击试验后无破损和可见变形、系统功能正常,内部结构无损坏,无安全隐患。
对于仿真分析,建议目标值设置为壳体材料等效塑性应变<0.2A,其中A为断后延伸率。
机械冲击仿真分析比较简单,采用Ls-dyna等显式有限元软件,将电池包有限元模型约束到一刚性体上,在刚性体上施加加速度波形即可。
机械冲击试验要求的加速度峰值为7g,即使按照容差上限,最大也不超过8.05G,但实际车辆在冲击路沿、高速过坎、通过深坑时,即使有悬架缓冲,电池包的加速度峰值也经常会超过十几个g。
所以建议测试和仿真都将冲击载荷适当放大,采用峰值20g持续时间为6ms 的半正弦加速度波形。
如图4所示。
图4 报批稿规定的冲击波形和本文建议波形模拟碰撞仿真模拟碰撞测试用来再现整车发生正面、后面或侧面高速碰撞时电池包的响应,试验装置如图5。
电池包安装在台车上,分别施加X向和Y向的脉冲。
图5 模拟碰撞测试装置高速碰撞发生后,车辆需要报废或者大修,电池包需要更换或者全面检查维修。
所以不要求模拟碰撞试验后电池包功能正常,只要不发生电解液或冷却液泄漏、外壳破裂、起火或爆炸即可。
仿真分析也只要求电池壳体结构不发生破裂,建议目标值设置为壳体材料等效塑性应变<0.8A ,其中A为材料断后延伸率。
模拟碰撞仿真与机械冲击仿真类似,也是采用Ls-dyna等显式有限元软件,将电池包模型约束到一个代表台车的刚性体上,然后施加加速度载荷。
因为台车正碰和侧碰试验都要求用同一个试验对象,所以仿真时也要在同一次分析里先后施加X和Y向加速度载荷。
报批稿规定,X向载荷最大值为28g,Y向载荷最大值为15g,如图6所示。
但整车在进行50公里正碰和64公里偏置碰试验时,电池包等效加速度一般在35g 以上;在进行50公里侧碰试验时,电池包等效加速度一般在25g以上。
所以建议测试和仿真时将加速度波形放大,X向加速度提升至38g,Y向加速度提升至28g。
图6 报批稿规定的模拟碰撞试验波形和建议波形挤压仿真挤压测试是模拟电池包在某些事故中受到挤压的情形,试验装置如图7所示。
采用图8所示的单拱或者三拱挤压头对电池边框施加载荷,分别沿X向和Y向进行测试,允许X向和Y向分别采用不同的试验对象。
图7 挤压测试装置挤压动作近似准静态,速度不超过2mm/s,挤压力达到 100 kN 或挤压变形量达到挤压方向的整体尺寸的 30%时停止挤压。
要求不起火、不爆炸。
仿真分析无法对不起火不爆炸这个指标进行量化,所以建议仿真目标值为挤压力达到100kN 时,内部管线不发生挤压和撞击,电池芯体的应变<5%。
现行法规要求电池芯体至少能承受15%的变形而不发生起火爆炸,所以仿真目标设定为芯体应变<5%是比较稳妥的。
电池挤压仿真可选择显式或隐式有限元法,用一刚性体模拟挤压板,通常只考虑单拱型挤压板即可。
图8 单拱形和三拱形挤压板仿真分析中需考虑材料弹塑性、大变形和接触这三重非线性因素。
采用显式算法时,无法实施2mm/s的缓慢加载,通常要将加载速度提高至少100倍,有可能造成仿真结果与实际不符。
所以推荐使用隐式算法,例如Abaqus/standard。
报批稿规定的挤压载荷只有100kN,强度偏低。
是电池包通常都是受到车身结构的保护,实际很难出现侧边直接被挤压的场景。
所以我们的测试和仿真并不需要将考察标准加严,满足报批稿要求即可。
在后续的整车级试验和仿真中,再根据结果再决定是否要加强电池包框架结构。
但也有例外情况,某些车型的电池包边框局部直接暴露,未受到车体结构保护,发生事故时可能直接受到撞击或挤压,此时100kN的载荷不足以覆盖实际工况。
所以建议对这些边框局部位置,采用500kN的挤压载荷进行考核。
结语振动疲劳、机械冲击和模拟碰撞测试,都是将电池包与一刚性框架连接,再将刚性框架固定在试验台架或者台车上。
电池包和刚性框架的连接必须与实车电池包和车身的连接一致。
进行仿真分析也需要保证电池包有限元模型的约束符合实际装车状态。
对于挤压测试,电池包平放于试验台面上,一侧紧靠刚性壁面,另一侧用挤压头加载。
电池包与试验台面之间不能有固定连接。
如果加载时电池包会移动,可以在电池包和刚性壁面之间增加辅助支撑。
进行仿真分析时也需要再现测试状态,在有限元模型中体现电池包侧边与刚性壁之间的接触约束。
本文建议测试和仿真都采用比报批稿更严苛的载荷条件,这就要求电池包框架和外壳要设计得更强壮,将导致整包质量增加和能量密度降低,影响补贴金额。
为解决电池包结构加强导致能量密度降低的问题,可以考虑为电池包设计一个加强托架,电池包用螺栓连接到托架上,托架再连接到车身上,如图9所示。
图9 电池包螺接托架按照现行法规,对于加强托架与电池包本体螺接的情况,企业可以将托架归属到车身,测试能量密度时就可不带托架,当然进行报批稿中各项测试时也不能带托架。
因此,我们可以将电池包壳体和内部框架结构尽可能减重,只保证满足报批稿中的基本要求,以实现整包能量密度的提升。
本文建议的更严苛的考核指标则是通过托架的加强作用来达成。
对于电池包结构,仅考核振动疲劳、机械冲击、模拟碰撞和挤压这几个工况是非常不充分的,至少还要考察电池包的整体和局部刚度、模态以及极限工况下的强度,还应考虑整车状态下电池包的结构安全,尤其要关注底部球击和刮底这两个整车工况。