固定床流化床设计计算
精选固定床反应器的工艺设计
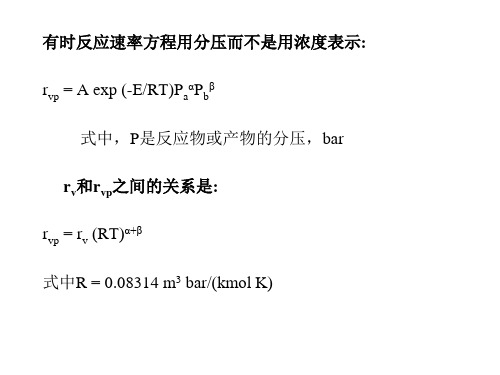
CA = PFyo(1-x)/(RG*T(6.5555Fyo+ 急冷量)) CB = P(Fyo(5-x)+0.9急冷量)/(RG*T (6.5555Fyo+急冷量))若把这些CA和CB项代入式(6-32),则: rv = - dCA/dθ = kCACB0.5 = Aexp(-E/RGT) (P/(RG*T(6.5555Fyo+ 急冷量)))1.5 Fyo(1-x) (Fyo(5-x)+0.9急冷量)0.5将上式与(6-8)合并:dx/dz = AcAexp(-E/RGT)(P/RG*T(6.5555Fyo+急冷量))1.5(1-x) (Fyo(5-x)+0.9急冷量)0.5
压降方程
开始可计算出∆P/z值,而后在每一步进行适当的压力校正。
实例,恒温反应器设计
H2C=CH2十H2 → CH3一CH3 (6-9)这是一个放热反应,但它可在很小的恒温反应器中进行。铜—氧化镁为催化剂,把这些催化剂装在一个内径为9.35mm、长为280mm带水夹套的黄铜制的反应器管中。由于把37.85 l/min的水循环通过夹套,因而可得到大于5.67kJ/(m2 S K)的水膜传热系数和恒定的管壁温度。在此反应器内,9—79℃范围内的各种恒定温度下进行的许多试验证明,对氢气来说,式(6-9)表示的反应是一级的。通过给定下列条件可写出反应速率方程:rv = kCH (6-10)该系统中, η = 1
有时反应速率方程用分压而不是用浓度表示:rvp = A exp (-E/RT)PaαPbβ 式中,P是反应物或产物的分压,bar rv和rvp之间的关系是:rvp = rv (RT)α+β 式中R = 0.08314 m3 bar/(kmol K)
第六章 固定床

水力半径
• 湿周---在总流的有效截面上,流体与固体壁面的接 触长度称为湿周,用字母L表示。
• 水力半径---总流的有效截面积A和湿周L之比。用字
母RH表示
RH = A / L
44
• 对于圆形截面的管道,其几何直径用水力半径表示 时可表示为
• A=(1/4)×πd2 • L=πd • 则 R=A/L=(1/4)×d → d = 4 R
当ReM>1000 湍流, 局部阻力损失为主, f≈1.75 , 略去第一项
结论: 对ΔP影响最大的是ε和u
49
Pf L
'(duSm 2 )(1B3B)
f ' 1501.75 ReM
一般床压不宜超过床内压力的15%,所以颗粒不 能太细,应做成圆球状。
50
➢ 压降的计算 ΔP=ΔP1+ ΔP2
= 15fu 0 OG L 0(1)21.75fuO 2 G L 0(1)
dS 2
3
dS
3
Pa
式中混合物的粘度
1
yi
fi M
2 i
f
1
yiM
2 i
kg/m.s
51
6.3 固定床中的传热
传热包括: 粒内传热,颗粒与流体间的传热,床层与器壁的传热
给热系数 αP 给热系数αW ,λer 总给热系数α t
当单纯作为换热装置时,以床层的平均温度tm与 管壁温差为推动力-----总给热系数αt
n
算术平均直径: d xWidi i1
调和平均直径:
1 n xWi
d
d i1 i
几何平均直径:
di
didi
30
6.2.3 床层空隙率及分布
生物接触氧化法固定床与流化床比较

生物接触氧化法固定床与流化床比较
1、固定床一般用弹性填料,半软性填料,比表面积只有100-180m3/m2;流化床用立体柱状空心填料,比表面积可达到1000 m3/m2。
2、固定床填料更换麻烦,需更换支架,要固定安装;流化床填料更换简单,只需从柱修孔加入即可。
3、固定床填料寿命一般只有2-3年;流化床立体柱状空心填料寿命在10年以上。
4、固定床填料生物相单一,水力停留时间长;流化床填料集硝化与反硝化于一体,生物相集中,处理效率高,水力停留时间短。
5、固定床设备体积大,占地多,投资高;流化床设备体积小,占地少,投资省。
6、陶粒每二年增加10%,生物炭每二年增加5%。
7、系统剩余污泥一般为3-6个月抽吸一次,具体时间根据实际定。
江苏鹏鹞集团有限公司
吴彩莉
2002年1月31日
北京西二旗创业者家园污水排放标准
江苏鹏鹞集团有限公司
吴彩莉
2002年1月31日。
化工基础实验 固定床和流化床实验

• 防止指示液冲出,如流量过猛或过大也易造成指示液冲 出。
13
五、实验结果整理
• 定流速与压降和高度的关系,并仔细观察实验现象,将 数据和现象详细记录。下表可供记录参考:
流体流量计
这种床层称为流化床,如图(c)、(d)所示。
• 流化床阶段,每一个空塔速度对应一个相应的床层空隙 率,流体的流速增加,空隙率也增大,但流体的实际流 速总是保持颗粒的沉降速度μt不变,且原则上流化床有 一个明显的上界面。
C、颗粒输送阶段
• 当立体在床层中的实际流速超过颗粒的沉降速度μt时, 流化床的上界面消失,颗粒将虚浮在流体中并被带出器
固定床和流化床实验
2021/7/22
1
预习复习系统
• 实验目的 • 实验原理 • 实验装置图 • 注意事项 • 实验结果整理 • 实验报告内容 • 思考题
2
一、实验目的
•
观察固定床与流化床的总体性状;
•
观察固定床向流化床转变的过程及流化现象;
•
观察液固系统与气固系统流态化的差异;
•
测定两系统的流化关系曲线即(∆P~w曲线);
外,如图(e)所示。
6
此时,实现了固体颗粒的气力或液力输送,相应的床 层称为相输送床层。
2、两种不同流化形式 A、散式流化 • 散式流化状态的特点:固体颗粒均匀的分散在流化介
质中,故称均匀流化。当流速增大时,床层逐渐膨胀 而没有气泡产生,颗粒彼此分开,颗粒间的平均距离 或床层中各处的空隙率均匀增大,床层高度上升,并 有一稳定的上界面。通常两相密度差小的系统趋向散 式流化,故大多数液—固流化属于“散式流化”。
化工基础实验 固定床和流化床实验

流化床压力与气速的关系
log
固定床
流化床
带出开始
C
B
A
D
A 起始流化速度
带出速度
logu
图 3-28 流化床压力降与气速关系
三、实验装置图
图2 气固系统流程图 1.鼓风机 2.孔板流量计 3.孔板压差计 4. 压差计 5.床身 6.接收管 7.旋风分离器 8.按钮开关
图2 液固系统流程图 1. 旋液分离器 2. 接收器 3.床身 4. 压差计 5. 孔板压差计 6.水槽 7.水泵 8. 孔板流量计 9. 按钮开关
ቤተ መጻሕፍቲ ባይዱ
B、 聚式流化
对于密度差较大的系统,则趋向于另一种流化 形式——聚式流化。例如,在密度差较大的 气—固系统的流化床中,超过流化所需最小气 量的那部分气体以气泡形式通过颗粒层,上升 至床层上界面时即行破裂。在这些气泡内可能 夹带有少量固体颗粒。这时床层内分为两相, 一相是空隙小而固体浓度大的气固均匀混合物 构成的连续相,称为乳化相;另一相则是夹带 有少量固体颗粒而以气泡形式通过床层的不连 续相,称为气泡相。由于气泡在上界面处破裂, 所以上界面是以某种频率上下波动的不稳定界 面,床层压强降也随之作相应的波动。
实验装置
四、注意事项
在全部的操作中,流量调节是关键,要求流量调节要缓 慢,由其是在临界流化点附近要更加缓慢,做出流化曲 线的全部过程,至少要做15—20个点左右,点并均匀分 布。
由于实验完毕后,床层颗粒的孔隙率增大,为了使下一 次实验数据准确性好些,用手轻轻拍一下床体,使固体 的孔隙率减小,床层高度为实验前原有的高度。
本实验室装置为二维床。便于观察现象。但固体颗粒回 收到床内,并不十分方便。所以操作中注意流量调节不 要过猛,防止颗粒带出。
反应器选型与设计
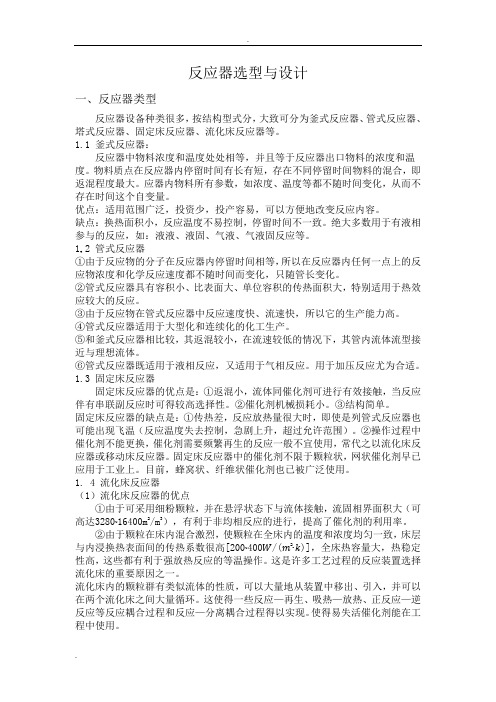
反应器选型与设计一、反应器类型反应器设备种类很多,按结构型式分,大致可分为釜式反应器、管式反应器、塔式反应器、固定床反应器、流化床反应器等。
1.1釜式反应器:反应器中物料浓度和温度处处相等,并且等于反应器出口物料的浓度和温度。
物料质点在反应器内停留时间有长有短,存在不同停留时间物料的混合,即返混程度最大。
应器内物料所有参数,如浓度、温度等都不随时间变化,从而不存在时间这个自变量。
优点:适用范围广泛,投资少,投产容易,可以方便地改变反应内容。
缺点:换热面积小,反应温度不易控制,停留时间不一致。
绝大多数用于有液相参与的反应,如:液液、液固、气液、气液固反应等。
1.2 管式反应器①由于反应物的分子在反应器内停留时间相等,所以在反应器内任何一点上的反应物浓度和化学反应速度都不随时间而变化,只随管长变化。
②管式反应器具有容积小、比表面大、单位容积的传热面积大,特别适用于热效应较大的反应。
③由于反应物在管式反应器中反应速度快、流速快,所以它的生产能力高。
④管式反应器适用于大型化和连续化的化工生产。
⑤和釜式反应器相比较,其返混较小,在流速较低的情况下,其管内流体流型接近与理想流体。
⑥管式反应器既适用于液相反应,又适用于气相反应。
用于加压反应尤为合适。
1.3 固定床反应器固定床反应器的优点是:①返混小,流体同催化剂可进行有效接触,当反应伴有串联副反应时可得较高选择性。
②催化剂机械损耗小。
③结构简单。
固定床反应器的缺点是:①传热差,反应放热量很大时,即使是列管式反应器也可能出现飞温(反应温度失去控制,急剧上升,超过允许范围)。
②操作过程中催化剂不能更换,催化剂需要频繁再生的反应一般不宜使用,常代之以流化床反应器或移动床反应器。
固定床反应器中的催化剂不限于颗粒状,网状催化剂早已应用于工业上。
目前,蜂窝状、纤维状催化剂也已被广泛使用。
1. 4 流化床反应器(1)流化床反应器的优点①由于可采用细粉颗粒,并在悬浮状态下与流体接触,流固相界面积大(可16400m2/m3),有利于非均相反应的进行,提高了催化剂的利用率。
应用化工技术专业《流化床反应器结构尺寸及反应器压力降的计算》
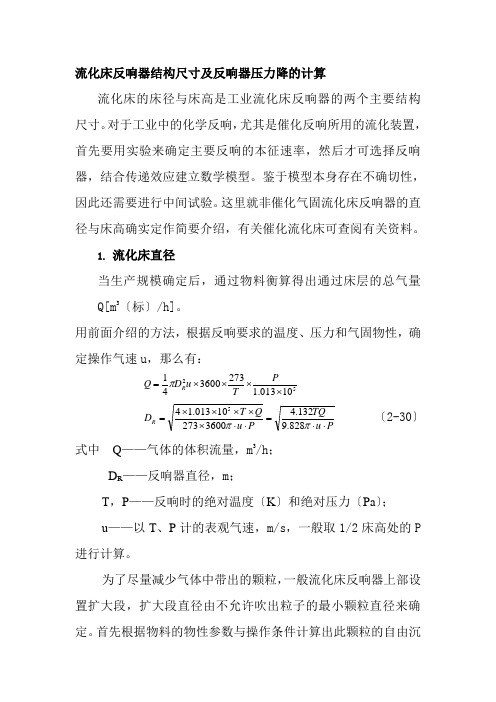
流化床反响器结构尺寸及反响器压力降的计算流化床的床径与床高是工业流化床反响器的两个主要结构尺寸。
对于工业中的化学反响,尤其是催化反响所用的流化装置,首先要用实验来确定主要反响的本征速率,然后才可选择反响器,结合传递效应建立数学模型。
鉴于模型本身存在不确切性,因此还需要进行中间试验。
这里就非催化气固流化床反响器的直径与床高确实定作简要介绍,有关催化流化床可查阅有关资料。
1. 流化床直径当生产规模确定后,通过物料衡算得出通过床层的总气量Q[m 3〔标〕/h]。
用前面介绍的方法,根据反响要求的温度、压力和气固物性,确定操作气速u ,那么有:5210013.1273360041⨯⨯⨯⨯=P T u D Q R π P u TQ P u Q T D R ⋅⋅=⋅⋅⨯⨯⨯⨯⨯=ππ828.9132.4360027310013.145 〔2-30〕式中 Q ——气体的体积流量,m 3/h ;D R ——反响器直径,m ;T ,P ——反响时的绝对温度〔K 〕和绝对压力〔Pa 〕; u ——以T 、P 计的表观气速,m/s ,一般取1/2床高处的P 进行计算。
为了尽量减少气体中带出的颗粒,一般流化床反响器上部设置扩大段,扩大段直径由不允许吹出粒子的最小颗粒直径来确定。
首先根据物料的物性参数与操作条件计算出此颗粒的自由沉降速度,然后按下式计算出扩大段直径L D 。
013.12733600412P T u D Q t L ⋅⋅⋅⋅=π P u TQD t L ⨯⨯⨯=π828.9013.14〔2-31〕2.流化床床高一台完整的流化床反响器高度包括流化床高度、扩大段高度和别离高度。
而流化床高又包括临界流化床高mf L ,流化床高f L 与别离段高度D L 。
临界流化床高mf L ,也称静止床高D L 。
对于一定的流化床直径和操作气速,必须有一定的静止床高。
对于生产过程,可根据产量要求算出固体颗粒的进料量W P 〔kg/h 〕,然后根据要求的接触时间τ〔h 〕,求出固体物料在反响器内的装载量M 〔kg 〕,继而求出临界流化床时的床高mf L 。
化工基础实验固定床和流化床实验

流化床阶段,每一个空塔速度对应一个相应的床层空隙 率,流体的流速增加,空隙率也增大,但流体的实际流 速总是保持颗粒的沉降速度μt不变,且原则上流化床有 一个明显的上界面。
C、颗粒输送阶段 当立体在床层中的实际流速超过颗粒的沉降速度μt时,
流化床的上界面消失,颗粒将虚浮在流体中并被带出器 外,如图(e)所示。
流化床压力与气速的关系
log
固定床
流化床
带出开始
C
B
A
D
A 起始流化速度
带出速度
logu
图 3-28 流化床压力降与气速关系
三、实验装置图
图2 气固系统流程图 1.鼓风机 2.孔板流量计 3.孔板压差计 4. 压差计 5.床身 6.接收管 7.旋风分离器 8.按钮开关
图2 液固系统流程图 1. 旋液分离器 2. 接收器 3.床身 4. 压差计 5. 孔板压差计 6.水槽 7.水泵 8. 孔板流量计 9. 按钮开关
此时,实现了固体颗粒的气力或液力输送,相应的床 层称为相输送床层。
2、两种不同流化形式 A、散式流化 散式流化状态的特点:固体颗粒均匀的分散在流化介
质中,故称均匀流化。当流速增大时,床层逐渐膨胀 而没有气泡产生,颗粒彼此分开,颗粒间的平均距离 或床层中各处的空隙率均匀增大,床层高度上升,并 有一稳定的上界面。通常两相密度差小的系统趋向散 式流化,故大多数液—固流化属于“散式流化”。
二、实验原理
1.流态化现象 当一种流体自上而下流过床层时,随着
流速的增大会出现三种不同的情况:
A、 固定床阶段 当流体通过床层的空塔速度较低时,若床
层空隙中流体的实际流速u小于颗粒的沉降速 度ut,则颗粒静止不动,颗粒层为固定床。
固定床反应器设计

孔隙率分布
4、流体在固定床中流动的特性
流体在固定床中的流动情况较之在空管中的流动要复杂得多。 固定床中流体是在颗粒间的空隙中流动,颗粒间空隙形成的孔道 是弯曲的、相互交错的,孔道数和孔道截面沿流向也在不断改变。
空隙率是孔道特性的一个主要反映。在床层径向,空隙率分布的 不均匀,造成流速分布的不均匀性。
催化剂微孔内的扩散过程对反应速率有很大的影响。反应物进入微孔后, 边扩散边反应。如扩散速率小于表面反应速率,沿扩散方向,反应物浓度 逐渐降低,以致反应速率也随之下降。采用催化剂有效系数对此进行定量 的说明。
实际催化反应速率 催化剂化剂内表面与外温度, 浓度相同时的反应速率
rP rS
结论:当 ≈1时,反应过程为动力学控制,当 <1时,反应过程为内
扩散控制。
内扩散不仅影响反应速率,而且影响复杂反应的选择性。如平行反应中, 对于反应速率快、级数高的反应,内扩散阻力的存在将降低其选择性。又 如连串反应以中间产物为目的产物时,深入到微孔中去的扩散将增加中间 产物进一步反应的机会而降低其选择性。
注意事项:
固定床反应器内常用的是直径为3~5mm的大颗粒催化剂,一般难 以消除内扩散的影响。实际生产中采用的催化剂,其有效系数为 0.01~1。因而工业生产上必须充分估计内扩散的影响,采取措施 尽可能减少其影响。在反应器的设计计算中,则应采用考虑了内扩 散影响因素在内的宏观动力学方程式。
外扩散过程
流体与催化剂外表面间的传质。
NA kcASe cGA cSA
在工业生产过程中,固定床反应器一般都在较高流速下 操作。因此,主流体与催化剂外表面之间的压差很小, 一般可以忽略不计,因此外扩散的影响也可以忽略。
结论:外扩散的影响也可以忽略。
0402流化床工艺计算(精)

➢ 扩大段高度h2
经验取:h2=D2
4.锥底高h3
h3
1 2
D1ctg 2
H=hf+h1+h2+h3
一般锥角θ=60度或90度
直径
➢ 反应器主体直径D1
D1
4v0
u0
v0-----操作条件下的气体体积流量
➢ 扩大段直径D2
D1
4vd
ut
vd------扩大段的气体体积流量
流态化的工艺计算
在两个目数间隔内颗粒平均直径可按几何平均值计算,即
dP d1d2
目数 >120 100-120 80-100 60-80 40-60 <40
dPi 0.121 0.133 0.163 0.208 0.298 0.360
xi 0.99 0.752
d Pi
0.797 1.680 0.839 0.139
重量% 12 10
13
35 25 5
催化剂颗粒密度ρP=1120[kg.m-3] 气体密度ρ=1.10[kg.m-3]
气体粘度μ=0.0302[cp]
解 1.计算颗粒平均粒径 根据标准筛的规格,目数与直径关系如下:
目数
120 100 80 60 40
直径[mm] 0.121 0.147 0.175 0.246 0.360
6
d
3 p
s
g
1 2
CD
g
g
d
2 p
4
ut2
CD 曳力系数
对于单颗粒,有半经验公式:
CD
24 Re
10 CD 1
Re 2
CD 0.43
Re 2
对应
流化床设计

化工原理课程设计任务书设计任务:年处理_1.6__万吨某颗粒状物质从气流干燥器来的细颗粒物料,其中含水量为8%(湿基,下同),要求在卧式多室流化床中干燥至0.8%。
已知参数如下:被干燥物料:处理湿物料量G 1 2000kg/h 平衡含水量X * 0颗粒密度ρs 1400kg/m3 临界含水量X c 0.013kg 水/kg 绝干料 堆积密度ρb 450kg/ m 3颗粒平均直径d m 0.15mm 干物料比热容c s 1.256 kJ /(kg·℃) 进口温度θ1 30℃在干燥系统要求收率99.5%(回收5μm 以上颗粒)干燥介质——湿空气:进预热器温度t 0 30℃进干燥器温度t 1 100℃初始湿度H 0 0.013kg /kg 绝干气热源:392.4kPa 的饱和水蒸气。
年工作日------300天,连续生产试设计干燥器主体并选择合适的风机及气固分离设备。
图纸:带控制点工艺流程图一张(A3图纸);主体设备工艺条件图一张(A2图纸)。
前 言干燥是一门跨学科、跨行业、具有实验科学性的技术。
传统的干燥器主要有箱式干燥器、隧道干燥器、转筒干燥器、带式干燥器、盘式干燥器、桨叶式干燥器、流化床干燥器、喷动床干燥器、喷雾干燥器、气流干燥器、真空冷冻干燥器、太阳能干燥器、微波和高频干燥器、红外热能干燥器等。
干燥设备制作是密集型产业,我国的国产干燥设备价格相对低廉,因此具有较强的竞争力。
主要包括:(1)物料静止型或物料输送型干燥器;(2)物料搅拌型干燥器;(3)物料热风输送型干燥器;(4)物料移动状态;(5)辐射能干燥器将大量固体颗粒悬浮于运动着的流体之中,从而使颗粒具有类似于流体的某些表观特性,这种接触状态称为固体流态化。
流化床干燥器就是将流态化技术应用于固体颗粒干燥器德 一种工业设备,目前在化工、轻工医学、食品以及建材工业中得到广泛的应用。
流化干燥器又名沸腾干燥器,是固体流态化技术在干燥器上的应用。
固定床反应器和流化床反应器

固定床反应器1.概述凡是流体通过不动的固体物料所形成的床层而进行反应的装置都称作固定床反应器,其中尤以用气态的反应物料通过由固体催化剂所构成的床层进行反应的气-固相催化反应器占最主要的地位。
如炼油工业中的催化重整,异构化,基本化学工业中的氨合成、天然气转化,石油化工中的乙烯氧化制环氧乙烷、乙苯脱氢制苯乙烯等等。
此外还有不少非催化的气—固相反应,如水煤气的生产,氮与电石反应生成石灰氮(CaCN2) 以及许多矿物的焙烧等,也都采用固定床反应器。
2.固定床反应器优点1)固定床中催化剂不易磨损;2)床层内流体的流动接近于平推流,与返混式的反应器相比,可用较少量的催化剂和较小的反应器容积来获得较大的生产能力。
3)由于停留时间可以严格控制,温度分布可以适当调节,因此特别有利于达到高的选择性和转化率,在大生产中尤为重要。
3.固定床反应器缺点1)固定床中的传热较差;2)催化剂的更换必须停产进行。
4.类型固定床反应器形式多种多样,按床层与外界的传热方式分类,可有以下几类:●绝热式固定床反应器●多段绝热式固定床反应器●列管式固定床反应器,●自热式反应器。
(1)绝热式固定床反应器下图是绝热式固定床反应器的示意图。
它的结构简单,催化剂均匀堆置于床内,床内没有换热装置,预热到一定温度的反应物料流过床层进行反应就可以了。
典型的例子是乙苯脱氢制苯乙烯。
反应需供热140kJ/mol,是靠加入高温(710℃)水蒸汽来供应的(乙苯:水蒸汽=1: 2.6(质量)),混合后在630℃入床,离床时降到565℃。
在此,水蒸汽的作用是:a) 可以带入大量的显热;b) 起稀释作用,使反应的平衡向有利于生成苯乙烯的方向移动,提高单程转化率;c) 使催化剂可能产生的结炭随时得到清除,从而保持反应器长期连续运转。
(2)多段绝热式固定床反应器热效应大,常把催化剂床层分成几段(层),段间采用间接冷却或原料气(或惰性组分)冷激,以控制反应温度在一定的范围内 。
固定床流体力学
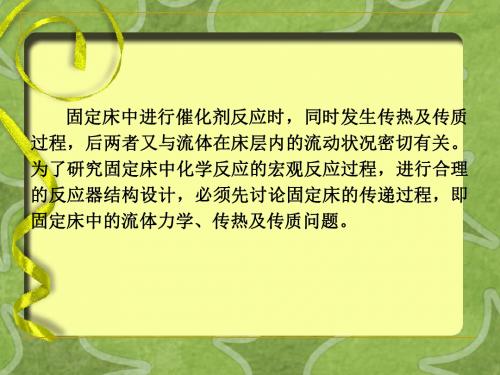
床层空隙率对压力降的影响十分显著,当 (1 ) 3 ReM>1000时,压力降正比于 , 由0.4增至0.5时, 压力降可降至原来的1/2.3。床层空隙率的大小与颗粒的 形状、粒度分布、填充方法、颗粒直径与容器直径之比 值等因素有关。混合颗粒的粒度越不均匀,小颗粒填充 在大颗粒之间,所组成的床层空隙率越小。催化剂在使 用过程中逐渐破碎、粉化,当质量流率不变时,由于空 隙率减小,床层压力降相应地逐步增大。催化剂使用后 期床层压力降较前期压力降增加的程度随催化剂的机械 强度而定。即使不计入破损,操作一段时期后,由于床 层中颗粒填实,使床层下沉,空隙率降低而增高压力降。
d 2
上式应用于固定床时,u0e应为流体在床层空隙中的 真正平均流速ue,圆管的直径应以固定床的当量直径de 代替,而管长则应以流体在固定床中的流动途径来代替。 将 ue u0 和 de ( 2 / 3 )[ε[ε1 ε)]ds, 代入式(5-12),又考虑 到流体在固定床中的流动途径远大于固定床的高度 L, 并等于L的若干倍,则固定床的压力降可表示为 2 (5-13) ρ f u0 1 ε
三. 径向流动反应器中流体的分布
径向流动反应器的优点: 流体流通截面积大、流速 小、流道短,床层压力降 小。 径向流动反应器的结构如 图5-9。
四. 固定床流体的径向及轴向混合
1. 固定床径向及轴向混合有效弥散系数 (effective dispersion coefficient)
当流体流经固定床时,不断发生分散与汇合, 形成了一定程度的径向及轴向混合,尤其当固定床 中进行化学反应而又与外界换热时,床层中不同径 向位置处流速、温度及反应速率都不相同,也就必 然存在着径向浓度分布,更加加剧床层中径向及轴 向的混合过程,而其中径向混合比轴向更加显著。
第六章固定床催化反应器设计-化学反应工程

第六章气-固相催化反应器设计本章核心内容:本章讨论的气固相催化反应反应器包括固定床反应器和流化床反应器。
在固定床反应器部分,介绍了气固相催化反应器的各种类型和固定床层的流动特性,给出了固定床反应器的两种设计方法:经验或半经验法和数学模型法。
在流化床反应器部分,在对固体颗粒流态化现象和流态化特征参数介绍的基础上,讨论了流化床反应器的分类和工业应用。
6-1 固定床反应器的型式反应器内部填充有固定不动的固体催化剂颗粒或固体反应物的装置,称为固定床反应器。
气态反应物通过床层进行催化反应的反应器,称为气固相固定床催化反应器。
这类反应器除广泛用于多相催化反应外,也用于气固及液固非催化反应,它与流化床反应器相比,具有催化剂不易跑损或磨损,床层流体流动呈平推流,反应速度较快,停留时间可以控制,反应转化率和选择性较高的优点。
工业生产过程使用的固定床催化反应器型式多种多样,主要为了适应不同的传热要求和传热方式,按催化床是否与外界进行热量交换来分,分为绝热式和连续换热式两大类。
另外,按反应器的操作及床层温度分布不同来分,分为绝热式、等温式和非绝热非等温三种类型;按换热方式不同,分为换热式和自热式两种类型;按反应情况来分,分为单段式与多段式两类;按床层内流体流动方向来分,分为轴向流动反应器和径向流动反应器两类;根据催化剂装载在管内或管外、反应器的设备结构特征,也可以对固定床催化反应器进行分类。
图6-1、6-2、6-3分别是轴向流动式、径向流动式和列管式固定床反应器结构示意图。
其中,图6-1和图6-2所示的反应器为绝热式,图6-3所示的反应器为连续换热式。
图6-1 轴向流动式图6-2径向流动式图6-3列管式固固定床反应器固定床反应器定床反应器6-1-1 绝热式固定床反应器绝热式固定床催化反应器有单段与多段之分。
绝热式反应器由于与外界无热交换以及不计入热损失,对于可逆放热反应,依靠本身放出的反应热而使反应气体温度逐步升高;催化床入口气体温度高于催化剂的起始活性温度,而出口气体温度低于催化剂的耐热温度。
流化床反应器的设计
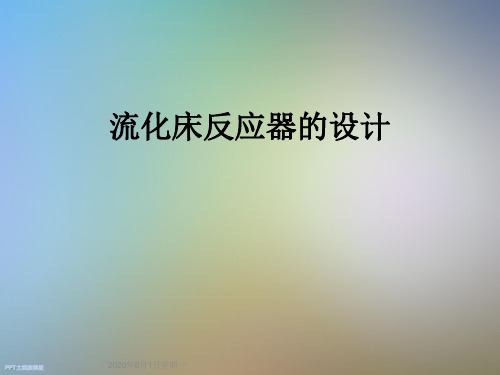
二、流化床反应器(Fluidized Bed )
流化床反应器是:利 用气体或液体自下而 上通过固体颗粒床层 而使固体颗粒处于悬 浮运动状态,并进行 气固相反应或液固相 反应的反应。在用于 气固系统时,又称沸 腾床反应器。
•1、概述
• 流化床反应器广泛应用于气固催化反应 器,由于流化床反应器具有传热性能好、温 度均匀的特点,已成为强放热反应或对温度 特别敏感的反应过程重要设备。如成功应用 于萘催化氧化制备邻苯二甲酸酐、丙烯氨氧 化制备丙烯腈等。
•(小颗粒 )
•(大颗粒)
•由上式看出,影响临界流化速度的因素有 :
•①颗粒直径 ②颗粒密度 ③流体黏度
➢ 带出速度ut
➢ 实际操作气速u0
•①选定依据是流化数即u0/umf,通常为1.5~10 •②还可以按照u0/ut =0.1~0.4原则选取,所用气 体流速一般在0.15~0.5 左右。
•2、流化床床反应器的工艺计算
•液固流化为散式流化
•散式流化床 •聚式流化床
•颗粒与流体之间的密度差是它们主要区别
•气固流化为聚式流化
•②特殊(压力1较、高流的气态固化系统的或形者用式较轻的液体流化
较重的颗粒)情况下两种流化床判别:
•
wilhelm和郭慕孙首先先用弗劳德数来区分两种流化态:
•研究表明:
•为散式流化 •为聚式流化
带动固体颗粒运动的。
• 固体流态化分为几种形式如下:
• (a)固定床
•
(b)临界流化床
•
(c)流化床
•
(d)气流输送床
1、流态化的形式
•2.散式流化1、床和流聚式态流化化床的形式
•(1)散式流化床:
•
①颗粒均匀地分布在整个流化床。
流化床的基本原理

保持固定床状态的最大空床气速 umax 床层பைடு நூலகம்态由固定床向流化床转换的临界条件:
u1
u1,max umax fixedbed
u1,maxut
up 0
ut
umaxu1,ma xut
umax为维持固定床状态的最大表观 气速。
起始流化速度:umf=umax
如果是均一的颗粒,其ut 可以计算出
um f ut fi xebd e d
2、Reh气固两相操作图
回忆与总结
1. 固定床
流速较低时,颗粒静止不动,流体只在颗粒之间的缝隙中通过 料层高度不变 实际流速线形增长 通风阻力随风速的平方关系增大
2. 流化床
颗粒不再由布风板所支持,而全部由流体的摩擦力所承托。此时, 对于单个颗粒来讲,可在床层中自由运动;就整个床层而言,具有 了许多类似流体的性质—流态化。此时:
umax为维持固定床状态的最大表观 气速。 当流体速度到达最小流化速度后,床层处于流化床阶段,在此阶段,床层阻力根本上保持恒定。 5、上升到床层外表破碎时,将大量颗粒抛入床层上方,使流化床颗粒损失。
m<1,固定床/移动床 2 最小流态化速度
随着流体流量的增加 和 空隙率的减小,又出现 1、 床层物料具有很高的颗粒表面积
空隙率即等于横截面上空隙面积的分率。
qv1uu1
u
qV D2
4
u u1
u1
ut
流体
〔1〕固定床阶段
up u1ut
颗粒的直径一定,在流体介质中的沉降速度ut 一定。
如果流体介质静止或者上升流速u1 , u1<ut
up0,即颗粒绝对 下速 ,度 沉方 落向 而 。 向 堆
随着上升流体流量的增大,u1增大,当到达u1=ut时,颗粒的表 观速度up=0 。 当u1 稍微大于ut时,颗粒便会上升,发生由固定 床向流化床的转化。
固定床流化床设计计算

固定床流化床设计计算炔烃液相选择加氢固定床床反应器设计计算由于固定床反应器具有结构简单、操作方便、 操作弹性大、建设投资低等优点,而广泛应用于各类油品催化加氢裂化及精制、低碳烃类选择加氢精制等领域。
将碳四馏分液相加氢新工艺就是采用单台固定床绝热反应器进行催化选择加氢脱除碳四馏分中的乙基乙炔和乙烯基乙炔等。
在工业装置中,由于实际所采用的流速足够高,流体与催化剂颗粒间的温差和浓差,除少数强放热反应外,都可忽略。
对于固定床反应器来讲最重要的是处理好床层中的传热和催化剂粒子内扩散传质的影响。
一、 固定床反应器设计碳四馏分选择性加氢反应器一般采用绝热固定床反应器。
在工程上要确定反应器的几何尺寸,首先得确定出一定生产能力下所需的催化剂容积,再根据高径比确定反应器几何尺寸。
反应器的设计主要依据试验结果和技术要求确定的参数,对反应器的大小及高径比、催化剂床层和液体分布板等进行计算和设计。
1. 设计参数反应器进口温度: 20℃进口压力:0.1MPa进料量(含氢气进料组分)体积流量:197.8m 3/h质量流量:3951kg/h液相体积空速:400h -12. 催化剂床层设计计算正常状态下反应器总进料量为2040m 3/h液体体积空速400h -1则催化剂用量3R V V V /S 2040/400 5.1m ===总催化剂堆密度3850/B kg m ρ=催化剂质量850 5.14335B B R m V kg kg ρ=⨯=⨯=求取最适宜的反应器直径D:设不同D 时,其中高径比一般取2-10,设计反应器时,为了尽可能避免径向的影响,取反应器的长径比5,则算出反应器的直径和高度为:按正常进料量32040m h /及液体空速400h -1,计算反应器的诸参数: 取床层高度L=5m ,则截面积2R S V /L 5.1/51.02m === 床层直径4/4 1.02/3.14 1.140D S m π=⨯=因此,圆整可得反应器内径可以选择1200mm 此时,床层高度02244 5.1L 4.5123.14 1.2R V m D π⨯===⨯ 反应器选型表4-1和表4-2为反应器类型。
流化床反应器流化高度的计算 - 干燥机干燥设备天力干燥 …

第 4 期 李 伟等 1 流化床反应器流化高度的计算 · 2 75 ·
随之增加 。在实际的生产中 ,催化剂储量由生产 能力 、催化剂负荷而定 ,同时 ,也受到催化剂流化 高度的限制 。如果流化高度超高 ,则不能再增加 催化剂储量 ,即不能再提高生产能力 。 3. 3 总进气量对催化剂流化高度的影响
流化床反应器流化高度的计算李伟张述伟王长英刘长厚张沛存严仲明王效斗大连理工大学化工学院辽宁大连116012齐鲁石化公司丙烯腈厂山东淄博255068摘要研究开发了工业生产流化床反应器流化高度的计算数学模型并讨论了催化剂平均颗粒直径催化剂储量进气量反应温度反应压力对催化剂流化床层高度的影响
研究与开发 Q齐IL鲁U石 P油E化TR工OC,H2E0M0 1IC,A2L9
© 1995-2005 Tsinghua Tongfang Optical Disc Co., Ltd. All rights reserved.
· 2 74 · 齐 鲁 石 油 化 工 第 29 卷
但该公式还不能直接应用 。必须根据实际数
例如 , 某丙烯腈厂 , 根据已知的数据 : 催化 剂储量 、总进气量 、反应压力 、反应温度 、原料 比 , 产物的产率 、流化高度等 , 利用数学模型反 算出反应器中催化剂颗粒的平均直径 。2000 年 6 月 1 日~7 月 29 日近两个月的计算结果如图 7 。
图化高度的影响如图 2 所示 。
Hf = Hmf (1 - εmf ) Π(1 - εf )
(8)
即可求出催化剂流化高度 。
公式 (1) ~ (8) 构成了流化床流化高度计算的
数学模型 。上述数学模型具有以下几个优点 : (1)
模型简便 、实用 ; (2) 从流化状态出发计算湍流状
- 1、下载文档前请自行甄别文档内容的完整性,平台不提供额外的编辑、内容补充、找答案等附加服务。
- 2、"仅部分预览"的文档,不可在线预览部分如存在完整性等问题,可反馈申请退款(可完整预览的文档不适用该条件!)。
- 3、如文档侵犯您的权益,请联系客服反馈,我们会尽快为您处理(人工客服工作时间:9:00-18:30)。
炔烃液相选择加氢固定床床反应器设计计算由于固定床反应器具有结构简单、操作方便、操作弹性大、建设投资低等优点,而广泛应用于各类油品催化加氢裂化及精制、低碳烃类选择加氢精制等领域。
将碳四馏分液相加氢新工艺就是采用单台固定床绝热反应器进行催化选择加氢脱除碳四馏分中的乙基乙炔和乙烯基乙炔等。
在工业装置中,由于实际所采用的流速足够高,流体与催化剂颗粒间的温差和浓差,除少数强放热反应外,都可忽略。
对于固定床反应器来讲最重要的是处理好床层中的传热和催化剂粒子内扩散传质的影响。
一、固定床反应器设计碳四馏分选择性加氢反应器一般采用绝热固定床反应器。
在工程上要确定反应器的几何尺寸,首先得确定出一定生产能力下所需的催化剂容积,再根据高径比确定反应器几何尺寸。
反应器的设计主要依据试验结果和技术要求确定的参数,对反应器的大小及高径比、催化剂床层和液体分布板等进行计算和设计。
1.设计参数反应器进口温度:20 C进口压力:O.IMPa进料量(含氢气进料组分)体积流量:197.8m3/h质量流量:3951kg/h液相体积空速:400h-12.催化剂床层设计计算正常状态下反应器总进料量为2040nVh液体体积空速400h-1贝U催化剂用量 V R二V总/S V =2040/400 =5.1m3催化剂堆密度订=850kg/m3催化剂质量 m B二订 V R =850 5.1kg = 4335kg求取最适宜的反应器直径D:设不同D时,其中高径比一般取2-10,设计反应器时,为了尽可能避免径向的影响,取反应器的长径比5,则算出反应器的直径和高度为:按正常进料量 2040m3/h及液体空速400h-1,计算反应器的诸参数:取床层高度L=5m则截面积S=V R/L =5.1/5=1.02m2床层直径D 二4S/ …=、4 1.02/3.14 = 1.140m 因此,圆整可得反应器内径可以选择1200mm 此时,床层高度L°二普二总■ =4.512m反应器选型表4-1和表4-2为反应器类型表4-1固定床反应器类型比较、流化床反应器设计1.1反应器设计原则(1)具有适宜的流体力学条件,流动性能好,有利于热量传递和质量传递;(2)合理的结构,能有效的加速反应和水的脱除;(3)保证压力和温度符合操作条件;(4)操作稳定,调节方便,能适应各种操作条件的变化。
1.2流化床反应器的设计以Superflex工艺为依托,以C4为原料,以ZSM-5分子筛为催化剂活性组分,通过流化床反应器,将C 4转换为乙烯、丙烯产品。
其特点是在2个独立的流化床反应器(区)中分别进行(乙烯和丁烯歧化反应)过程,产物汇总后进入分离系统,乙烯、丙烯产品出装置,C4及G以上组分循环返回反应器继续转化G及以上组分两股物流在返回烯烃转化反应区之前有少量驰放,以免惰性组分积累。
催化剂顺次通过反应器,经汽提后进入再生器烧焦,再生催化剂连续返回反应器以实现连续反应-再生。
1.3流化床反应器计算说明1.基本参数:催化剂颗粒密度:-1500kg/m3催化剂堆密度:"B = 700kg / m3催化剂平均粒径:d p =0.12m=1.2 10°m (属于B区粒子)混合气体粘度:—2.0 10-5Pa.s反应温度:T=550 o C反应压力:P= 0.2MPaC4处理流量:m0 = 30584m3 / h混合气体密度:?二 m0/V0 = 30584/17505 =1.75 kg/m3流化床出口流量:V1 = 29667 m3/h4・2・2 工艺计算当流体流过颗粒床层的阻力等于床层颗粒重量时,床层中的颗粒开始流动起来,此时流体的流速称为起始流化速度,记作U mf。
起始流化速度仅与流体和颗粒的物性有关,其计算公式如下式所示:d u |对于R ep = < 20的小颗粒mfrl I 1 p对于R ep二p f1000的大颗粒由于C4裂解反应需要较长的接触时间,故流化床的操作线速不必太高4.221 操作气速(1) 起始流化速度U mf 的确定故假设Re ::: 20合理。
2将U mf 带入弗鲁德准数公式Fg f 二作为判断流化形式的依据。
散式流化, d p g F rmf <0. 13 聚式流化,Fg f 0.13代入已知数据求得根据反应动力学,为了确保 C4馏分在一定时间内保持较高的转化率,需控制 C4馏分 质量空速为I 〜5h _ 10 C4馏分质量流量为30584kg/h 。
根据操作空速为3h ",以反应空速计 算催化剂装填量为 m cat =30584/3=10195kg(3) 静床层高度L o 的确定催化剂堆密度:-700kg / m 33 流化床操作气速操作速度U 0表示流化床在正常操作时流体的速度,一般U mf < U0 ::: U t 。
根据C4裂解反应流化床操作速度围为6.41 10"m/s :::u ° :: 0.574m/ s ,两个速度之比为89.5,所选气速不 应太接近这一允许气速范围的任一极端。
故可取 u 0 =0.25m/s 。
4.2.2.2 流化床反应器尺寸 (1) 流化床浓相段直径的确定经计算,采用单个流化床反应器圆整为5000mm设 Re ::: 20 , U mf d p (P p — P)g ( 1.2<10 ‘)2 3x( 1500 — 1650」_ 165^ 2.0 10^= 6.41 10‘m/s复核Re 值,Re 二呼1.2 10* 6.41 10” 1.752.0如0*= 0.0673 ::: 20将U mf 复带入弗鲁德准数公式F mf2如d p g3 2(6.41 10 ) 1.2 10* 9.8= 0.035 :: 0.13 流化形式为散式流(4)流化床床层高度的确定查阅资料知,对于带有挡板流化床,可采用下面的公式计算膨胀比:R0.5170 1924适用范围0.07 ::: u 乞0.921 -0.76u式中u为流化床的操作气速,m/s。
在通入气体起到起始流化时,床高 L mf L0=0.74m所以浓相段床高 L f=RL mf =1.24 0.74 =0.92m稀相段床高由阿基米德数,有挡板时,由经验方程估算,(5)扩大段直径的确定在流化过程中,小颗粒容易被流体带到反应器的上部或外部当气体速度较大的操作状态下,被气体带走的固体颗粒数量较大,为了回收这部分颗粒,在流化床中必须设有气固分离装置。
设计采用的是在反应器上部连接一个扩大段作为自由沉降段,气速降低,部分颗粒自由沉降分离。
由于,反应的催化剂使用寿命极短,所以要像乙烯催化裂化装置一样另设一个再生器与之串联,且有研究表明催化剂床层下部的积炭程度较轻,床层内存在积碳分布,高失活区域位于催化剂床层上部;如此必须加强床层上部催化剂颗粒与气体的分离,可在稀相段设置一个气固初步分离器,在扩大段设置一个串联的二级旋风分离器,分离出来的固体,通过一个倒锥体一部分进入再生器,一部分进入浓相段。
⑹扩大段的计算最小颗粒的带出速度:圆整后取D2 =6m(2) 催化剂装填量的确定二6.3m 3600 3.14 0.264 :沁「扩大段高度,取经验值L 3=D 2=6m(7) 锥体部分固定流化床反应器锥体角度不大于45°,选取反应器锥体的角度为45°。
根据反应器 直径计算可知锥体段高度,下面接口管的直径为 0.6m ,由此可以推出:综上,流化床反应器反应器高度(8) 各段壁厚的计算设计压力0.25MPa 设计温度550r ,材料为0Cr18Ni9,则其许用应力为100MP©根 据壁厚公式计算,浓稀相段厚度心=程C 2仁8.36mm2冋七①_巳2"0山0.85—0.25考虑钢板负偏差G 圆整后,C^ 0.8mm (参考化工机械基础•陈国恒 P161)表4-6钢板厚度负偏差钢板厚度2.0 2.2 2.5 2.8~3.0 3.2~3.5 3.8~4.0 4.5~5.5负偏差C : 0.18 0.19 0.20 0.22 0.25 —0.30 0.50 厂 钢板厚度 6.0~7.0 8.0~25 26~30 32~34 36~40 42~50 52~60 负偏差C 「 0.6 0.8 0.9 1. 0 1.1 1.2 1.3故取、n =10mm过渡段半锥角为60C ,取R/D j =0.5,则f=0.5圆整后去,=10mm密相段与过渡段连接部分的厚度 K=0.5 : p KP c D i 0.5x5(W0.25、d 二 t — - C 21 = 3.68mm :: 10mm ,2[二]门—0.5P c : :■:■: 0.85 —0.5 0.25故取、n =10mm& 二 fP c D i°=[;才「—0.5P」":0.85 -0.5 0.251 = 8.36mm扩大段厚度 P c D j旷2[才:—巳C 20.25x60001 = 9.84mm , C^0.8mm :Q 0.85-0.25取n=11mm上部封头壁厚故取备=11mm;根据JB/T 4737-95 椭圆形封头深度为1500mm直边高度为50mm(9 )气体分布器气体分布器是流化床反应器的主要构件之一,具有支承催化剂、均匀分布气体、证催化剂正常流化而不出现沟流,偏流,实现流化床稳定操作、强化传热传质等过程的重要部件。
而反应器为双层流化床反应器,其中下层采用管式分布器,上层采用板式分布器。
分布器的开孔率均为1%(10)分布板压力降计算气体通过分布板的压力降可用下式计算:式中:E为阻力系数,其取值范围为1.5〜2.5 ; ©为开孔率;u为空塔气速(11)挡板或挡网挡板或挡网是流化床反应器的重要构件之一,床内加设挡板或挡网后,能够破坏气泡的生成和长大,改善气体在床内的停留时间分布和两相接触,在相当程度上减轻气体返混, 从而提高了反应转化率。
其一般厚度为2〜6mm(12)内旋风分离器内旋风分离器是装在反应器内部的气固分离器,目前在流化床反应器中已得到广泛采用。
它能将经过床层反应后气体中夹带的固体颗粒分离出来,以减少催化剂的浪费,降低生产成本。
内旋风分离器的圆筒直径取2m,选型可以参照下表进行:表1-2内旋风分离器旋风分离器型式进口形状及位置器身形状及尺寸型式进口宽度进口高度排气管直径圆筒高度圆锥高度排灰口直径P c D i2[;才:门C20.琢0000.85 -0.5仁 8.83mm G 二 0.8mm2g2g 2(10)(13)裙座裙座结构有圆筒形和圆锥形两种形式,均由裙座筒体、基础环、地脚螺栓座、人孔、排气孔、引出管通道、保温支承圈等组成。
(14)排气孔和排气管塔设备运行过程中有可能有气体逸出,积聚在裙座与塔底封头之间。