稀氧燃烧介绍
超临界流体氧气燃烧技术的研究和应用
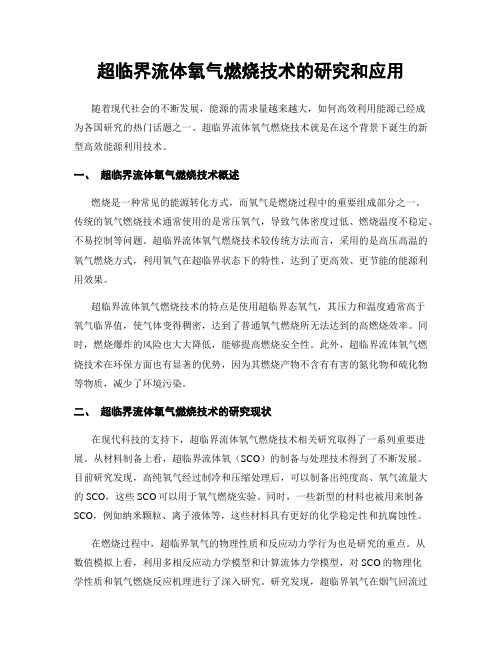
超临界流体氧气燃烧技术的研究和应用随着现代社会的不断发展,能源的需求量越来越大,如何高效利用能源已经成为各国研究的热门话题之一。
超临界流体氧气燃烧技术就是在这个背景下诞生的新型高效能源利用技术。
一、超临界流体氧气燃烧技术概述燃烧是一种常见的能源转化方式,而氧气是燃烧过程中的重要组成部分之一。
传统的氧气燃烧技术通常使用的是常压氧气,导致气体密度过低、燃烧温度不稳定、不易控制等问题。
超临界流体氧气燃烧技术较传统方法而言,采用的是高压高温的氧气燃烧方式,利用氧气在超临界状态下的特性,达到了更高效、更节能的能源利用效果。
超临界流体氧气燃烧技术的特点是使用超临界态氧气,其压力和温度通常高于氧气临界值,使气体变得稠密,达到了普通氧气燃烧所无法达到的高燃烧效率。
同时,燃烧爆炸的风险也大大降低,能够提高燃烧安全性。
此外,超临界流体氧气燃烧技术在环保方面也有显著的优势,因为其燃烧产物不含有有害的氮化物和硫化物等物质,减少了环境污染。
二、超临界流体氧气燃烧技术的研究现状在现代科技的支持下,超临界流体氧气燃烧技术相关研究取得了一系列重要进展。
从材料制备上看,超临界流体氧(SCO)的制备与处理技术得到了不断发展。
目前研究发现,高纯氧气经过制冷和压缩处理后,可以制备出纯度高、氧气流量大的SCO,这些SCO可以用于氧气燃烧实验。
同时,一些新型的材料也被用来制备SCO,例如纳米颗粒、离子液体等,这些材料具有更好的化学稳定性和抗腐蚀性。
在燃烧过程中,超临界氧气的物理性质和反应动力学行为也是研究的重点。
从数值模拟上看,利用多相反应动力学模型和计算流体力学模型,对SCO的物理化学性质和氧气燃烧反应机理进行了深入研究。
研究发现,超临界氧气在烟气回流过程中可以产生更多的OH自由基,加速了反应速率,使得氧气燃烧反应更加强烈。
此外,燃烧产物的种类和分布特征也在一定程度上受SCO的化学稳定性和扩散能力影响。
综上所述,研究SCO的物理化学性质和反应动力学行为对于研究和应用超临界流体氧气燃烧技术具有重要的意义。
211274148_稀氧燃烧技术在铜冶炼中的应用

世界有色金属 2023年 2月下26冶金冶炼M etallurgical smelting稀氧燃烧技术在铜冶炼中的应用刘存标(山东恒邦冶炼股份有限公司,山东 烟台 264100)摘 要:随着科技技术的提高,稀氧燃烧技术在铜冶炼中的广泛使用取代了传统的煤气燃烧,不但大大提高了燃烧的效率,而且在稀氧燃烧技术下所熔炼产生的铜的纯度和品质也更高。
而稀氧燃烧技术是在新科技下发展的重要化工技术,这项技术不但可以减少在传统煤气燃烧中产生的安全隐患问题,还可以利用稀氧燃烧技术的同时提高布尘,从而提高烟气中铜的回收率,还可以高效处理生态环境问题,使在烟气质量能够达标以后再加以排放。
该文重点从稀氧燃烧技术在使用之前生产铜的状况,以及使用稀氧燃烧工艺之后生产铜的状况入手,对稀氧燃烧工艺在铜冶炼中的运用从以下四个方面展开了论述,以便于进一步提高稀氧燃烧工艺在冶金铜中的技术水平。
关键词:稀氧燃烧技术;铜冶炼;应用中图分类号:F416.32 文献标识码:A 文章编号:1002-5065(2023)04-0026-3Application of dilute oxygen combustion technology in copper smeltingLIN Cun-biao(SHANDONG HUMON SMELTING CO.,LTO.,Yantai 264100,China)Abstract: With the improvement of science and technology, dilute oxygen combustion technology is widely used in copper smelting instead of traditional gas combustion, which not only greatly improves the efficiency of combustion, but also produces higher purity and quality of copper smelted by dilute oxygen combustion technology. Dilute oxygen combustion technology is one of the important chemical technology development under the new technology, the technology can not only reduce the security hidden danger in traditional gas burning question, still can use dilute oxygen combustion technology at the same time improve the dust cloth, so as to improve the recovery rate of copper in flue gas, can efficiently deal with ecological environment problem, make quality standard will be later in the flue gas emissions. This paper focuses on the production of copper before and after the use of dilute oxygen combustion technology, and discusses the application of dilute oxygen combustion technology in copper smelting from the following four aspects, in order to further improve the technical level of dilute oxygen combustion technology in metallurgical copper.Keywords: Dilute oxygen combustion technology; Copper smelting; application收稿日期:2023-01作者简介:刘存标,男,汉族,生于1987.7,山东菏泽人,工程师,大专学历,研究方向:冶金技术。
稀薄燃烧
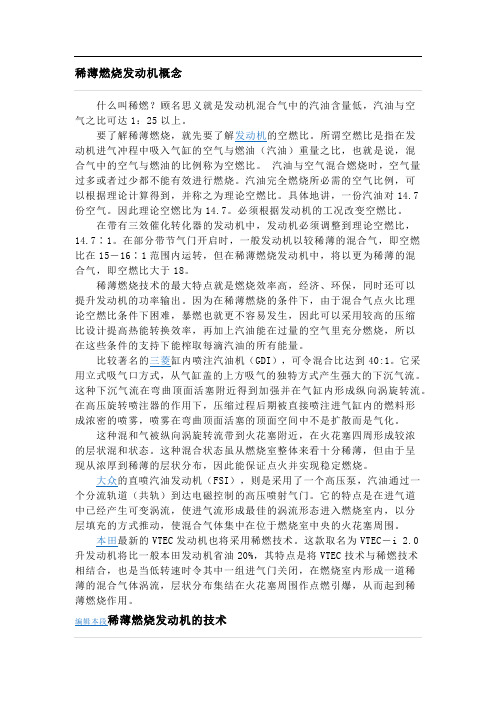
什么叫稀燃?顾名思义就是发动机混合气中的汽油含量低,汽油与空气之比可达1:25以上。
要了解稀薄燃烧,就先要了解发动机的空燃比。
所谓空燃比是指在发动机进气冲程中吸入气缸的空气与燃油(汽油)重量之比,也就是说,混合气中的空气与燃油的比例称为空燃比。
汽油与空气混合燃烧时,空气量过多或者过少都不能有效进行燃烧。
汽油完全燃烧所必需的空气比例,可以根据理论计算得到,并称之为理论空燃比。
具体地讲,一份汽油对14.7份空气。
因此理论空燃比为14.7。
必须根据发动机的工况改变空燃比。
在带有三效催化转化器的发动机中,发动机必须调整到理论空燃比,14.7∶1。
在部分带节气门开启时,一般发动机以较稀薄的混合气,即空燃比在15-16∶1范围内运转,但在稀薄燃烧发动机中,将以更为稀薄的混合气,即空燃比大于18。
稀薄燃烧技术的最大特点就是燃烧效率高,经济、环保,同时还可以提升发动机的功率输出。
因为在稀薄燃烧的条件下,由于混合气点火比理论空燃比条件下困难,暴燃也就更不容易发生,因此可以采用较高的压缩比设计提高热能转换效率,再加上汽油能在过量的空气里充分燃烧,所以在这些条件的支持下能榨取每滴汽油的所有能量。
比较著名的三菱缸内喷注汽油机(GDI),可令混合比达到40:1。
它采用立式吸气口方式,从气缸盖的上方吸气的独特方式产生强大的下沉气流。
这种下沉气流在弯曲顶面活塞附近得到加强并在气缸内形成纵向涡旋转流。
在高压旋转喷注器的作用下,压缩过程后期被直接喷注进气缸内的燃料形成浓密的喷雾,喷雾在弯曲顶面活塞的顶面空间中不是扩散而是气化。
这种混和气被纵向涡旋转流带到火花塞附近,在火花塞四周形成较浓的层状混和状态。
这种混合状态虽从燃烧室整体来看十分稀薄,但由于呈现从浓厚到稀薄的层状分布,因此能保证点火并实现稳定燃烧。
大众的直喷汽油发动机(FSI),则是采用了一个高压泵,汽油通过一个分流轨道(共轨)到达电磁控制的高压喷射气门。
它的特点是在进气道中已经产生可变涡流,使进气流形成最佳的涡流形态进入燃烧室内,以分层填充的方式推动,使混合气体集中在位于燃烧室中央的火花塞周围。
燃烧反应和非燃烧反应的基本概念与分类
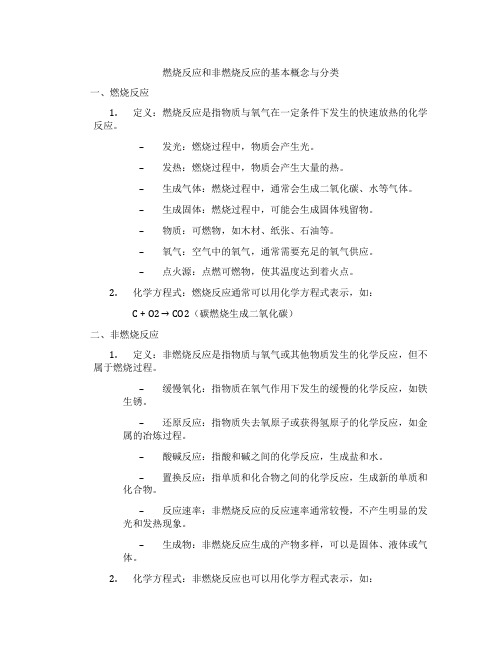
燃烧反应和非燃烧反应的基本概念与分类一、燃烧反应1.定义:燃烧反应是指物质与氧气在一定条件下发生的快速放热的化学反应。
–发光:燃烧过程中,物质会产生光。
–发热:燃烧过程中,物质会产生大量的热。
–生成气体:燃烧过程中,通常会生成二氧化碳、水等气体。
–生成固体:燃烧过程中,可能会生成固体残留物。
–物质:可燃物,如木材、纸张、石油等。
–氧气:空气中的氧气,通常需要充足的氧气供应。
–点火源:点燃可燃物,使其温度达到着火点。
2.化学方程式:燃烧反应通常可以用化学方程式表示,如:C + O2 → CO2(碳燃烧生成二氧化碳)二、非燃烧反应1.定义:非燃烧反应是指物质与氧气或其他物质发生的化学反应,但不属于燃烧过程。
–缓慢氧化:指物质在氧气作用下发生的缓慢的化学反应,如铁生锈。
–还原反应:指物质失去氧原子或获得氢原子的化学反应,如金属的冶炼过程。
–酸碱反应:指酸和碱之间的化学反应,生成盐和水。
–置换反应:指单质和化合物之间的化学反应,生成新的单质和化合物。
–反应速率:非燃烧反应的反应速率通常较慢,不产生明显的发光和发热现象。
–生成物:非燃烧反应生成的产物多样,可以是固体、液体或气体。
2.化学方程式:非燃烧反应也可以用化学方程式表示,如:Fe + O2 → Fe2O3(铁与氧气反应生成三氧化二铁)总结:燃烧反应和非燃烧反应都是化学反应的重要分类,燃烧反应具有明显的发光、发热现象,而非燃烧反应则通常反应速率较慢,产物多样。
掌握这些基本概念和分类,有助于我们更好地理解化学反应的本质。
习题及方法:1.习题:木炭在氧气中燃烧的化学方程式是什么?解题方法:根据燃烧反应的定义,我们知道燃烧反应是物质与氧气发生的快速放热的化学反应。
木炭是一种可燃物,因此在氧气中燃烧时会生成二氧化碳。
所以,木炭在氧气中燃烧的化学方程式是C + O2 → CO2。
2.习题:铁生锈是一种什么类型的化学反应?解题方法:铁生锈是铁与氧气发生的化学反应,但反应速率较慢,属于缓慢氧化。
阳极炉稀氧燃烧技术革新
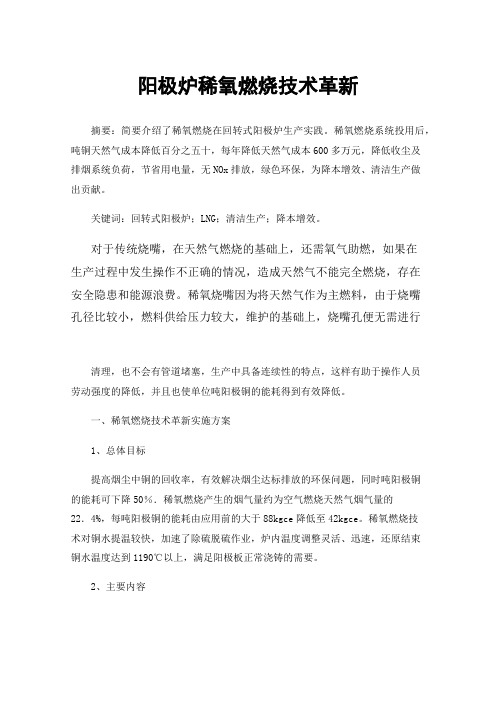
阳极炉稀氧燃烧技术革新摘要:简要介绍了稀氧燃烧在回转式阳极炉生产实践。
稀氧燃烧系统投用后,吨铜天然气成本降低百分之五十,每年降低天然气成本600多万元,降低收尘及排烟系统负荷,节省用电量,无NOx排放,绿色环保,为降本增效、清洁生产做出贡献。
关键词:回转式阳极炉;LNG;清洁生产;降本增效。
对于传统烧嘴,在天然气燃烧的基础上,还需氧气助燃,如果在生产过程中发生操作不正确的情况,造成天然气不能完全燃烧,存在安全隐患和能源浪费。
稀氧烧嘴因为将天然气作为主燃料,由于烧嘴孔径比较小,燃料供给压力较大,维护的基础上,烧嘴孔便无需进行清理,也不会有管道堵塞,生产中具备连续性的特点,这样有助于操作人员劳动强度的降低,并且也使单位吨阳极铜的能耗得到有效降低。
一、稀氧燃烧技术革新实施方案1、总体目标提高烟尘中铜的回收率,有效解决烟尘达标排放的环保问题,同时吨阳极铜的能耗可下降50%.稀氧燃烧产生的烟气量约为空气燃烧天然气烟气量的22.4%,每吨阳极铜的能耗由应用前的大于88kgce降低至42kgce。
稀氧燃烧技术对铜水提温较快,加速了除硫脱硫作业,炉内温度调整灵活、迅速,还原结束铜水温度达到1190℃以上,满足阳极板正常浇铸的需要。
2、主要内容解决目前空气及富氧燃烧系统天然气不完全燃烧造成的生产安全隐患,提高烟尘中铜的回收率, 辐射热高,有利于物料加热,增加产能,提高物料处理能力。
4、重点解决的关键技术问题4.1技术特点以纯氧为助燃介质进行助燃,以高速卷吸理念为设计依据,通过氧气高速射流卷吸炉内烟气,降低火焰温度(烟气再循环率R与炉内温度曲线表见右图),采用自身冷却方式,无需任何强制冷却措施。
4.2纯氧卷吸燃烧原理5%~15%氧与燃料以较低速度从烧嘴轴线进入,85%~95%氧气从周围环绕的小孔中高速喷出,卷吸炉内烟气,降低火焰温度。
纯氧卷吸燃烧优点①、火焰温度可控制1500℃内,对炉子耐火材料要求大大降低;②、自身冷却,无需任何冷却措施;③、辐射热高,有利于物料加热,增加产能;④、热损失小,节能率50%;⑤、后续烟气回收系统减小,节约投资,同时降低生产成本;NOx 排放少,绿色环保。
易燃材料的氧指数

易燃材料的氧指数易燃材料的氧指数易燃材料被广泛应用于工业生产中,但是它们往往会产生火灾和爆炸风险。
因此,对于易燃材料的安全性评估是非常重要的。
其中,氧指数被用来描述一个材料在氧气存在下的燃烧特性,是一种常用的安全性评估指标。
根据氧指数,材料可以分为多个等级,每个等级的范围是 0-100。
该指标表明了一种材料所需要的最小氧浓度,使其能够持续燃烧。
因此,氧指数越大,表明材料的耐燃性越强。
根据氧指数的等级,易燃材料可以被分为以下几类:一类材料:氧指数大于 95。
这类材料的燃烧性很低,一般不会发生火灾或爆炸,因此安全性非常高。
例如,黄铜和不锈钢。
二类材料:氧指数在 85-95 之间。
这类材料的热分解温度很高,燃烧性较低,不容易引起火灾和爆炸。
但是,在高温下它们可能会分解,因此在高温环境下应特别小心。
例如,玻璃纤维。
三类材料:氧指数在 75-85 之间。
这种材料的燃烧性能较强,易燃程度中等。
在使用时要格外小心,以免引起火灾和爆炸。
例如,聚丙烯和橡胶。
四类材料:氧指数在 45-75 之间。
这种材料的燃烧性较高,易燃程度较大,容易引发火灾和爆炸。
例如,PVC和乙烯基乙酸酯。
五类材料:氧指数小于 45。
这种材料的燃烧性能最强,极易引起火灾和爆炸,安全性非常低。
例如,棉花和纸张。
因此,根据材料的氧指数,可以很容易地识别出哪些材料更安全,哪些材料更危险。
在工业生产中,使用氧指数来评估材料的安全性,可以有效地避免事故的发生,保障生产的安全。
除了在工业生产中使用氧指数进行安全性评估,我们在日常生活中也可以从中受益。
比如,最近购买地毯时,我就关注到氧指数。
经过查找和比较,我选择了氧指数较高的地毯,以确保家庭的安全。
综上所述,氧指数是一种非常有用的指标,可以帮助我们确认材料的燃烧特性和安全性。
在工业生产和日常生活中,大家可以使用氧指数来做出更明智的选择。
稀氧燃烧节能技术在铜冶炼生产中的应用
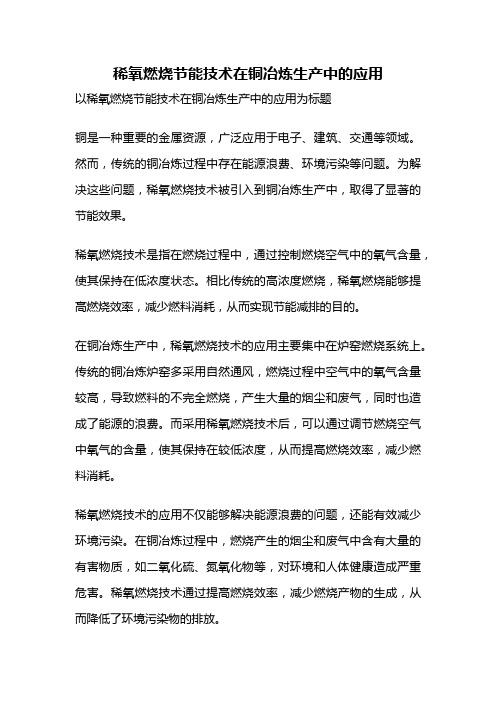
稀氧燃烧节能技术在铜冶炼生产中的应用以稀氧燃烧节能技术在铜冶炼生产中的应用为标题铜是一种重要的金属资源,广泛应用于电子、建筑、交通等领域。
然而,传统的铜冶炼过程中存在能源浪费、环境污染等问题。
为解决这些问题,稀氧燃烧技术被引入到铜冶炼生产中,取得了显著的节能效果。
稀氧燃烧技术是指在燃烧过程中,通过控制燃烧空气中的氧气含量,使其保持在低浓度状态。
相比传统的高浓度燃烧,稀氧燃烧能够提高燃烧效率,减少燃料消耗,从而实现节能减排的目的。
在铜冶炼生产中,稀氧燃烧技术的应用主要集中在炉窑燃烧系统上。
传统的铜冶炼炉窑多采用自然通风,燃烧过程中空气中的氧气含量较高,导致燃料的不完全燃烧,产生大量的烟尘和废气,同时也造成了能源的浪费。
而采用稀氧燃烧技术后,可以通过调节燃烧空气中氧气的含量,使其保持在较低浓度,从而提高燃烧效率,减少燃料消耗。
稀氧燃烧技术的应用不仅能够解决能源浪费的问题,还能有效减少环境污染。
在铜冶炼过程中,燃烧产生的烟尘和废气中含有大量的有害物质,如二氧化硫、氮氧化物等,对环境和人体健康造成严重危害。
稀氧燃烧技术通过提高燃烧效率,减少燃烧产物的生成,从而降低了环境污染物的排放。
稀氧燃烧技术的应用还能提高铜冶炼的生产效率。
传统的铜冶炼炉窑存在能量损失严重的问题,而稀氧燃烧技术的应用可以提高燃烧效率,减少能源的浪费,提高生产效率。
此外,稀氧燃烧技术还可以降低炉温,减少炉膛的热损失,进一步提高生产效率。
稀氧燃烧技术在铜冶炼生产中的应用虽然带来了诸多好处,但也存在一些挑战和问题。
首先,稀氧燃烧技术的应用需要专业的设备和技术支持,增加了生产成本。
其次,稀氧燃烧技术对燃料的选择和控制要求较高,需要进行详细的燃烧工艺设计和调试。
此外,稀氧燃烧技术的应用还需要针对不同的冶炼工艺进行优化和调整,以适应不同的生产需求。
稀氧燃烧技术在铜冶炼生产中的应用能够有效解决能源浪费、环境污染等问题,提高生产效率,减少生产成本。
然而,稀氧燃烧技术的应用还需要进一步完善和优化,以适应不同的冶炼工艺和生产需求。
稀氧燃烧使用手册

稀氧燃烧使用手册
1. 引言
1.1 目的和范围
1.2 定义
2. 稀氧燃烧基础知识
2.1 燃料与空气混合比例掌握要点
- 气体混合物中可燃成分浓度计算方法及公式示例。
- 不同类型的常见可用于稀氧环境下的主要工业或实验室应用场景。
3. 设备准备与操作规程
3 .l 准备设施、仪器以及其他必需品清单
- 列出进行稀有元素制取所需要具有特殊性能(如耐腐蚀,高温等)的装置、材料。
并给予相对详细描述,并附上相关图片说明。
4.安全注意事项
4.l 使用前检查
对各种可能存在危险因素( 如泄漏, 高压) 进行排除并记录在案.
提供一份简明易操纵且容易理解之“启动/停止”程序指南.
5.故障处理技巧行为
l 故障现象判断
根据经验总结列出已发生过的故障现象及其解决办法.
附上相关图片说明.
6.常见问题与答案
列出使用稀氧燃烧技术时经常遇到的一些典型问题,并给予相应解答。
7. 维护保养
l 设备维修
- 提供设备日常检查和定期维护所需步骤。
- 包括清洁、润滑以及更换易损件等内容。
8. 目录
9 .参考文档
10 .致谢
本文档涉及附件:
1. 图片示例:包含了实验室中可能用到的装置或材料图像,帮助用户理解并准确操作。
2. 表格样式:提供混合比例计算公式表格范本,方便用户进行数据记录和计算。
注释:
1) 稀氧环境: 指空气中低于正常大气压力下(通常是0.lMPa以下)的纯度较高(如>90%) 的O2 浓度区域, 及/ 或者其他可使火焰温度升高而得到某种特殊效果 ( 如金属划线割断 ) 能量浓集地点;。
稀氧燃烧技术在铜冶炼中的应用研究
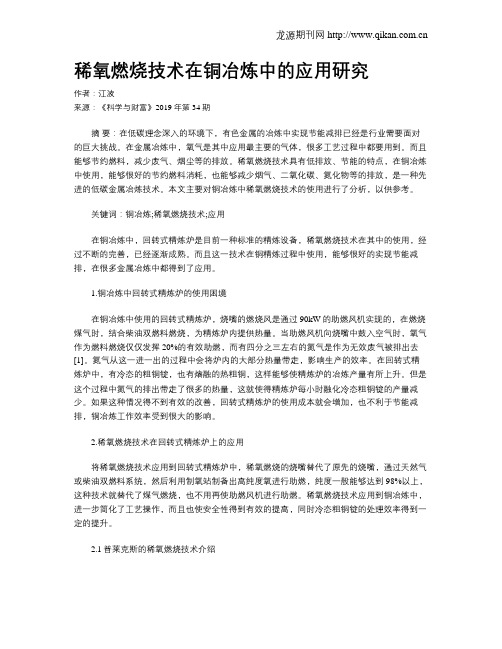
稀氧燃烧技术在铜冶炼中的应用研究作者:江波来源:《科学与财富》2019年第34期摘要:在低碳理念深入的环境下,有色金属的冶炼中实现节能减排已经是行业需要面对的巨大挑战。
在金属冶炼中,氧气是其中应用最主要的气体,很多工艺过程中都要用到。
而且能够节约燃料,减少废气、烟尘等的排放。
稀氧燃烧技术具有低排放、节能的特点,在铜冶炼中使用,能够很好的节约燃料消耗,也能够减少烟气、二氧化碳、氮化物等的排放,是一种先进的低碳金属冶炼技术。
本文主要对铜冶炼中稀氧燃烧技术的使用进行了分析,以供参考。
关键词:铜冶炼;稀氧燃烧技术;应用在铜冶炼中,回转式精炼炉是目前一种标准的精炼设备,稀氧燃烧技术在其中的使用,经过不断的完善,已经逐渐成熟。
而且这一技术在铜精炼过程中使用,能够很好的实现节能减排,在很多金属冶炼中都得到了应用。
1.铜冶炼中回转式精炼炉的使用困境在铜冶炼中使用的回转式精炼炉,烧嘴的燃烧风是通过90kW的助燃风机实现的,在燃烧煤气时,结合柴油双燃料燃烧,为精炼炉内提供热量。
当助燃风机向烧嘴中鼓入空气时,氧气作为燃料燃烧仅仅发挥20%的有效助燃,而有四分之三左右的氮气是作为无效废气被排出去[1]。
氮气从这一进一出的过程中会将炉内的大部分热量带走,影响生产的效率。
在回转式精炼炉中,有冷态的粗铜锭,也有熔融的热粗铜,这样能够使精炼炉的冶炼产量有所上升。
但是这个过程中氮气的排出带走了很多的热量,这就使得精炼炉每小时融化冷态粗铜锭的产量减少。
如果这种情况得不到有效的改善,回转式精炼炉的使用成本就会增加,也不利于节能减排,铜冶炼工作效率受到很大的影响。
2.稀氧燃烧技术在回转式精炼炉上的应用将稀氧燃烧技术应用到回转式精炼炉中,稀氧燃烧的烧嘴替代了原先的烧嘴,通过天然气或柴油双燃料系统,然后利用制氧站制备出高纯度氧进行助燃,纯度一般能够达到98%以上,这种技术就替代了煤气燃烧,也不用再使助燃风机进行助燃。
稀氧燃烧技术应用到铜冶炼中,进一步简化了工艺操作,而且也使安全性得到有效的提高,同时冷态粗铜锭的处理效率得到一定的提升。
烯烃氧化反应燃烧通式

烯烃氧化反应燃烧通式
烯烃氧化反应是指烯烃与氧气发生反应产生的化学反应。
烯烃
是一类碳氢化合物,其分子中含有碳-碳双键。
烯烃氧化反应的通式
可以用一般化学方程式表示为,CnH2n + (3n+1/2)O2 → nCO2 +
nH2O。
在这个方程中,CnH2n代表烯烃分子,(3n+1/2)O2代表氧气
分子,nCO2代表生成的二氧化碳分子,nH2O代表生成的水分子。
烯烃氧化反应是一种燃烧反应,其过程中烯烃分子和氧气分子
发生燃烧,生成二氧化碳和水。
燃烧是一种氧化反应,通过释放能
量将有机物质氧化为二氧化碳和水。
燃烧反应通常伴随着放热现象,因为燃烧反应释放了化学键的能量。
需要注意的是,烯烃氧化反应的实际反应过程可能会受到反应
条件、催化剂等因素的影响,因此在实际应用中可能会有一定的变化。
但是上述通式可以作为烯烃氧化反应的一个基本表示,帮助我
们理解烯烃氧化反应的基本原理和特点。
总的来说,烯烃氧化反应的通式可以用简单的化学方程式表示,但在实际应用中可能会有一些变化,需要根据具体的反应条件和催
化剂来进行具体分析。
希望这个回答能够全面地解答你的问题。
石墨烯在氧气中完全燃烧的化学方程式

石墨烯在氧气中完全燃烧的化学方程式石墨烯是一种由碳原子组成的二维材料,具有许多出色的物理和化学性质。
在氧气中,石墨烯可以发生燃烧反应,产生二氧化碳和水蒸气。
石墨烯的燃烧反应可以用以下化学方程式表示:C6H6 + 9O2 → 6CO2 + 3H2O在这个化学方程式中,C6H6表示石墨烯分子,O2表示氧气分子,CO2表示二氧化碳分子,H2O表示水分子。
石墨烯的燃烧反应是一种氧化反应,也是一种可逆反应。
当石墨烯与氧气接触时,氧气分子与石墨烯分子中的碳原子发生反应,产生二氧化碳和水蒸气。
这个过程是放热的,释放出大量的能量。
石墨烯的燃烧反应可以分为几个步骤。
首先,氧气分子与石墨烯分子表面的碳原子发生吸附,形成氧化碳中间物。
然后,氧化碳中间物进一步反应,形成二氧化碳分子。
同时,部分碳原子与氧气反应生成水蒸气。
石墨烯的燃烧反应是一种高温反应,需要提供足够的热量才能开始。
一旦反应开始,它将自持续进行,释放出大量的热量。
这是因为石墨烯的结构紧密,具有较高的燃烧温度和较高的燃烧速率。
石墨烯在氧气中燃烧的化学方程式符合标题中心扩展的描述。
在文章中,我详细解释了石墨烯燃烧的化学反应过程,并提供了相应的化学方程式。
此外,我还描述了石墨烯燃烧反应的步骤和条件,并强调了反应释放的能量。
最后,我还提到了石墨烯的燃烧反应是一种高温反应,并需要提供足够的热量才能开始。
总的来说,石墨烯在氧气中的完全燃烧是一种重要的化学反应,产生二氧化碳和水蒸气。
石墨烯的燃烧反应具有高温和高速的特点,释放出大量的能量。
了解石墨烯的燃烧反应对于研究其应用和安全性具有重要意义。
稀氧燃烧技术-铜冶炼应用

热效率和燃料节约
——空气-燃料燃烧 和 氧气-燃料燃烧
理想氧燃比
氧气
热效率
Copper
空气1000℃
空气400℃
空气25℃
烟气温度
燃烧的热效率
(不同烟气温度、不同空气预热温度)
燃料节约
(不同烟气温度、不同空气预热温度)
“稀氧燃烧”技术(DOC)
基本概念:
Stabilizing 一次氧 Oxygen
• 节约燃料成本 • 符合环保法规 • 可以处理低成本的原材料 • 降低风机和烟囱负荷
氧气提高燃烧效率
热平衡 (有效热提高)
——氧气-燃料燃烧
高的热辐射系数 (eAIR = 0.17 vs. eOXY = 0.33)
Energy 能量
炉气停留长 热效率高
有效热 有效热
烟气
空气-燃料
氧气-燃料
燃料
物料加热 炉壁损失
ON CTI A E R E ZON
反应区
燃料 Fuel Fuel 氧气 Oxygen Oxygen
MIXIN G ZONE
烟气 Flue
混合区
燃料和氧气分别通过不同喷嘴以高速射入炉膛 燃料和氧气被炉膛中已经存在的燃烧产物气体迅速稀释
燃烧过程中有效的氧浓度在2%到10%左右
漫射的、火焰温度一致的燃烧造成一种非常均匀的加热体系 低火焰温度使NOx的排放降到最低。
按照用户工况设计的燃烧控制系统
• 氧气 • 天然气\LPG\煤气 • 燃料油(重油或柴油)
结论
随着铜冶金技术的不断发展和人们对环保的日益重视,氧 气在铜冶炼过程中将扮演越来越重要的角色
普莱克斯的稀氧燃烧技术已成功应用于阳极炉精炼,在节 约燃料的同时,极大的减少了烟气和污染物的排放,特别 是CO2和NOx 排放 稀氧燃烧技术已成为铜冶炼企业节能、降耗、减排的有效 手段之一
氧瓶燃烧法

氧瓶燃烧法之答禄夫天创作1 简述氧瓶燃烧法系指将含有卤素或硫等元素的有机物,在布满氧气的燃烧瓶中,在铂丝的催化作用下进行燃烧,便有机化合物快速分解为水溶性的无机离子型产物.燃烧过程的局部温度约达1000~1200℃,燃烧产物被吸入吸收液后,采纳适宜的分析方法检查或测定相应元素的含量.本法亦可用于含硒、镉等化合物的燃烧分解.吸收液经常使用水、稀酸、稀碱、过氧化氢溶液或含有过氧化氢的稀酸、稀碱溶液.2 仪器与用具2.1 燃烧瓶磨口硬质、质地均匀的耐压玻璃或石英玻璃锥形瓶,容量一般用500ml、1000ml或2000m1,瓶口上部呈喇叭形.2.2 燃烧瓶塞空心、磨口的硬质玻璃塞,底部熔封铂丝一根(直径约lmm),铂丝下端作成网状或螺旋状载样装置,瓶塞塞入燃烧瓶后,铂丝载样装置下端距瓶底约为瓶身高度的1/3.2.3 无灰滤纸称取和包裹供试品用,按《中国药典》2010年版二部附录Ⅶ C图2.2.4 透明胶纸袋称取液体供试品用,按《中国药典》2010年版二部附录Ⅶ C.3 试药与试液3.1 供氧装置一般用氧气瓶.3.2 吸收液按各该品种项下的规定.4 把持方法4.1 燃烧瓶的选择4.1.1根据取样量几多,选择适当容量的燃烧瓶:取样10~20mg时,可选用容量为500ml燃烧瓶;取样100mg左右,一般要选用容量为1000m1燃烧瓶;取样200mg时,则要用容量为2000ml的燃烧瓶. 4.1.2测定含氟有机物时,需选用石英燃烧瓶.4.2 取样按各该品种项下的规定,精密称取供试品;如为固体应研细,并置准备好的无灰滤纸中心,液体样品置由透明胶纸折叠好的纸袋中;按《中国药典》附录规定的方法折叠后,固定于铂丝下真个螺旋处或网内,露出滤纸条.4.3 通氧在燃烧瓶内按规定加入吸收液,用水将瓶口湿润;用清洁的胶管接在氧气瓶出口处,另一端连接一根玻璃滴管;将玻璃滴管拔出燃烧瓶吸收液上方,急速通氧约1分钟,并小心将玻璃管由吸收液上方逐渐移至瓶口,务使瓶内的空气排尽,但玻璃管不要触及瓶壁及液面,立即用概况皿覆盖瓶口,移置他处远离氧气瓶.4.4 燃烧扑灭包有供试品的滤纸尾部,迅速将瓶塞拔出燃烧瓶中,按紧瓶塞,并用少量水封闭瓶口;此时,供试品在燃烧瓶中剧烈燃烧,伴之发生年夜量烟雾.4.5 吸收燃烧完毕(应无灰色、黑色碎片或颗粒,若燃烧后留有灰色、黑色碎片或颗粒,暗示供试品燃烧不完全,遇此情况应重新取样燃烧),立即充沛振摇,使生成的烟雾完全吸入吸收液中,放置15min,开启瓶塞,用少量水冲刷瓶塞及铂丝载样器,合并洗液及吸收液,按规定方法进行检查或测定,并同时同法作空白试验.5 注意事项5.1 取样用的无灰滤纸剪裁和折叠成药典附图时,手不能接触滤纸,特别是测定和检查氯化物,可将无灰滤纸夹在其他洁净的纸张中间,剪后用镊子折叠并夹入螺旋状铂丝中;取样用透明胶纸,可采纳上海出品的熊猫牌胶纸带,液体样品取样亦可在供固体取样的无灰滤纸中心一格位置加垫1~2张小无灰滤纸片,将少量供试品滴加在小滤纸片上,立即按规定折叠.液体及易挥发的样品,应在燃烧瓶内加入吸收液,通氧气后取样,以减少样品的挥发及在滤纸上的渗透.5.2 将铂丝绕成螺旋状,在把持中尽量将螺旋底部缠密,使孔隙小,并坚持铂丝干燥,便于供试品燃烧完全;夹持包有供试品的滤纸要松紧适度,夹不紧易失落下,夹过紧则不容易燃烧完全.5.3 燃烧瓶中氧气是否充分,对保证燃烧完全相当重要,应以年夜流量急速通氧,保证充分氧气;通氧气时注意平安,周围不能有明火.5.4 有的品种取样量年夜,一次燃烧不完全,可分两次取样燃烧;即在第一次取规定量的半量,按法把持,俟燃烧完毕后的烟雾完全被吸入吸收液后,再取规定量的另一半量,在原燃烧瓶通氧后燃烧,吸收入同一吸收液中.如甲状腺粉的含量测定,一次不容易燃烧完全时,可分2次取样燃烧、吸收.5.5 扑灭样品包燃烧时要压紧瓶塞,防止发生的热气顶冲瓶塞,烟雾逸出;燃烧后瓶内为负压,若瓶塞打不开,可微微加温,但温度不要太高,以免瓶塞冲出.5.6 整个把持务必小心防爆,为保证平安,样品燃烧时要有防爆办法,把持人员可戴防护面罩,也可用透明塑料或有机玻璃档板遮挡;在一般情况下,燃烧在瞬间完成,不致呈现危险.焚烧燃烧把持应远离氧气瓶.——本规范依据《中国药典》2015年版四部通则0703氧瓶燃烧法制定.。
发动机稀燃技术与分层燃烧技术

• 这种两级分层燃烧发动机的优点是: ① 等熵指数高 ② 可以采用高压缩比,当采用高辛烷值的汽油时,
压缩比可以提高到11~12,因而大大提高了发动 机的动力性和经济性。 ③ 燃烧温度低,传热损失和高温分解的热损失小 ④ 排污少 • 分层燃烧发动机的缺点:
燃烧缓慢,等容度低
本田CVCC燃烧系统
• 本田CVCC(Compound Vortex Controlled Combustion 复合涡流控 制燃烧)系统通过控制 燃烧过程来实现稀薄燃 烧。
• CVCC在传统火花塞位置 上设置一个副燃烧室 (预燃室),并配有一 个副进气门。副燃烧室 有两个火焰喷孔,孔径 6mm,总面积1.565cm2。
发动机稀燃技术与分层燃 烧技术
发动机稀燃技术
• 稀燃:是指发动机可以燃用汽油含量很低的可燃混合 气
• 从理论上讲,混合气越稀,越接近与空气循环(理论循 环),等熵指数κ值越大,热效率越高。
• 传统汽油机燃烧系统的缺陷:
– 空燃比变化范围非常狭窄(A/F=12.6~17); – 低负荷时进气节流损失大,经济性差; – 点火所需的混合气较浓,传播速度大,容易暴燃; – 汽油机始终以点火范围内的空燃比工作,热效率低。如能采用稀
本田CVCC系统的工作原理
• 进气过程:
– 进气时,大量稀混合气和极少浓混合气由独立的化油器分别供给 主燃烧室和副燃烧室。副燃烧室中的浓混合气通过火焰喷孔流到 主燃烧室和稀混合气混合,并形成空燃比梯度(分层进气)。
• 压缩过程:
– 压缩时,一部分稀混合气被压入复燃烧室,形成中等浓度混合气, 因此在压缩终了时形成:在火花塞周围是着火性能较好的浓混合 气;在主燃烧室的火焰喷孔附近形成适于火焰传播的中等浓度的 混合气;在主燃烧室其余部分是很稀的混合气。
论稀氧燃烧技术在铜冶炼中的应用
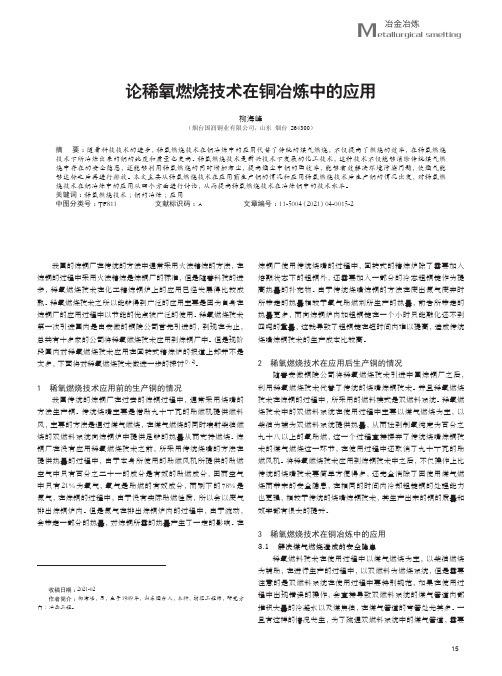
15Metallurgical smelting冶金冶炼论稀氧燃烧技术在铜冶炼中的应用柳海峰(烟台国润铜业有限公司,山东 烟台 264300)摘 要:随着科技技术的进步,稀氧燃烧技术在铜冶炼中的应用代替了传统的煤气燃烧,不仅提高了燃烧的效率,在稀氧燃烧技术下所冶炼出来的铜的纯度和质量也更高。
稀氧燃烧技术是新兴技术下发展的化工技术,这种技术不仅能够消除传统煤气燃烧中存在的安全隐患,还能够利用稀氧燃烧的同时增加布尘,提高烟尘中铜的回收率,能够有效解决环境污染问题,使烟气能够达标之后再进行排放。
本文主要从稀氧燃烧技术在应用前生产铜的情况和应用稀氧燃烧技术后生产铜的情况出发,对稀氧燃烧技术在铜冶炼中的应用从四个方面进行讨论,从而提高稀氧燃烧技术在冶炼铜中的技术水平。
关键词:稀氧燃烧技术;铜的冶炼;应用中图分类号:TF811 文献标识码:A 文章编号:11-5004(2021)04-0015-2 收稿日期:2021-02作者简介:柳海峰,男,生于1989年,山东烟台人,本科,助理工程师,研究方向:冶金工程。
我国的炼铜厂在传统的方法中通常采用火法精炼的方法,在炼铜的过程中采用火法精炼是炼铜厂的标准,但是随着科技的进步,稀氧燃烧技术在化工精炼铜炉上的应用已经发展得比较成熟。
稀氧燃烧技术之所以能够得到广泛的应用主要是因为自身在炼铜厂的应用过程中以节能的优点被广泛的使用。
稀氧燃烧技术第一次引进国内是由安徽的铜陵公司首先引进的,到现在为止,总共有十多家的公司将稀氧燃烧技术应用到炼铜厂中。
但是现阶段国内对稀氧燃烧技术应用在回转式精炼炉的报道上却并不是太多,下面将对稀氧燃烧技术做进一步的探讨[1,2]。
1 稀氧燃烧技术应用前的生产铜的情况我国传统的炼铜厂在过去的炼铜过程中,通常采用烧嘴的方法生产铜。
传统烧嘴主要是借助九十千瓦的助燃机提供燃料风,主要的方法是通过煤气燃烧,在煤气燃烧的同时喷射柴油燃烧的双燃料系统向炼铜炉中提供足够的热量从而支持燃烧。
稀氧燃烧技术在铜阳极精炼炉上的应用

蓝 师 聪 陈延进
石龙祥( 紫金铜业有限公司, 福建 龙岩 3 6 4 2 0 4 )
摘 要: 本文简要介绍了紫金铜业铜阳极炉的稀氧燃烧 技术改 造实践 , 并分析 了传统铜 冶炼 阳极炉 喷嘴的 缺陷及稀 氧燃烧技术的原理与优势 。稀氧燃烧技术改造后 , 阳极炉每吨合格阳极板重油 单耗由约 l 9 k g 降至 1 O k g 以下 , 以月产 阳 极板 3 0 0 0 0吨计算 , 每月可节省约 8 0 . 8 万元的重油费用 。此外 , 改造 后炉 温升 温更快 , 有助于炉况的控制 。阳极炉 烟气 量 仅为原工艺的 3 0 % 以下 , 大大减少了烟气带走的热量 , 降低 了烟气处理 系统 负担 , 并有效改善了重油燃烧不完 全带来的 低
2 . 2经 济 效 益 对 比
成本 节 约方 面 , 稀 氧燃 烧 技术 改 造 前后 , 取 同炼厂 阳极 炉于 2 0 1 5年 9月份年 修期间, 仅 用 了一 个 月便 完成控 制系 统、 重油阀 组、 氧气 阀组、 氧气管道 、 烧嘴砖的安装及调试 , 将 原有的蒸汽雾化 、 空气助燃 系统改为稀氧燃烧系
统。 2 . 1稀 氧 燃烧技 术 对工 艺过程 的影 响
践
粗铜约含有 1 %~ 3 % 的杂质 , 无法浇铸为合 格的阳极板供 电解使用 , 需 要采 用氧化 一还原精 炼工艺将粗铜中的杂质造渣除去。粗铜中杂质尤 其是硫含量不足 , 其氧化放热无法实现反应 自热 , 需要额外提供燃料保证氧化反应过程 中及浇铸期 间炉内温度。传统 阳极炉通 过蒸汽 雾化、 空气助 燃方 式达 到 重 油 燃 烧 , 炉 体 保 温 的 效 果 。但 根 据 现场使用情况观察 , 该工艺存在重油燃烧不完全 、 重油 单耗 高 、 低 空 污 染 较 严 重 等 状 况 。其 主 要 原 因在 于空 气 中能够 参 与助燃 反应 的氧 气 含 量仅 占 2 1 %, 使得重油燃烧不完全 , 且无用氮气 带走大量 的热 量 , 降低 了燃烧 的 效率 , 也增 加 了废 气 的 处理 量。使用富氧燃烧或纯氧燃烧是提高燃烧效率 、 降 低燃烧 过 程 中 燃料 消 耗 , 减 少 烟 气 排 放 的 有 效 手段 。
- 1、下载文档前请自行甄别文档内容的完整性,平台不提供额外的编辑、内容补充、找答案等附加服务。
- 2、"仅部分预览"的文档,不可在线预览部分如存在完整性等问题,可反馈申请退款(可完整预览的文档不适用该条件!)。
- 3、如文档侵犯您的权益,请联系客服反馈,我们会尽快为您处理(人工客服工作时间:9:00-18:30)。
安全切断阀故 障或失效 重油温度低
在重油温度低的情况下,系统 无法启动并报警。系统运行时 若出现压力低报警,则系统自 动切换至低流量运行状态。
氧燃比失调
若超出比例范围则自动转入低 流量运行状态,并报警,若在 点火状态和低流量运行状态下 仍旧报警,则系统停止。
无论在哪个控制模式或运行步骤下,系统的控制逻辑永远确保安全和工艺操作 需要,不管是机械故障还是操作错误,为了避免瞬时干扰引起的误报警,出现 现场报警后延时触发安全连锁报警。
LOGO LOGO
稀氧燃烧系统简介
熔炼二车间
内容
配置简介 结构及功能 完善的联锁
使用效果 存在的问题
稀氧燃烧配置
1 稀氧燃烧系统为氧气—重油燃烧系统,这 个系统由三部分组成: (1)控制阀站:阀门,管件,仪器仪表、 (2)操作站:PLC控制柜,操作台,人机控 制界面。 (3)烧嘴系统:JL烧嘴,点火枪,火焰探测 器,枪前软管附件,阀门,管件。
使用效果
120
70 75 38 35
31
阳极炉重油单耗由传统空气燃烧的 74.74kg/t•Cu 板 ( 2010 年 度 ) 降 至 38.5kg/t•Cu 板( 2011 年度),随着应 用经验的不断成熟,目前重油单耗已 达30.8 kg/t•Cu板,节能效果明显且还 有一定的潜力可挖。
2010
2011
2012
2013
阳极炉重油单耗
存在问题
1、纯氧 纯氧燃烧,要防止火焰 直接烧在炉衬上。 要加强点检,防止漏炉。 2、喷溅
炉内的喷溅可能会烧伤
枪嘴。 应定期更换枪芯。另外 在还原期应拆下枪芯。
LOGO LOGO
熔炼二车间
反应,从而产生低火焰峰值温
度的“反应区域”,燃烧系统中, J枪氧气主要作用是用来控制燃 烧火焰的强度,L枪氧气作用主 要用来控制燃烧火焰的扩散面
积。
构及功能
完善的联锁
当安全切断阀(氧气,重油) 在接收到信号后未完全关闭 或为完全打开,HMI会显示 系统报警。 在气源压力低的情况下,系 统无法启动并报警
稀氧燃烧配置
现场布置图
稀氧燃烧配置
烧嘴:J枪和L枪 烧嘴砖
稀氧燃烧配置
J枪由进油管、雾化风管、氧管组成。
当空压风不稳定时,可采用蒸汽雾化 L枪为氧管 氧气阀站
稀氧燃烧配置
重油阀站
结构及功能
氧气和燃料由不同喷嘴射入 炉内,高速氧气和燃料射流因
为和炉内气体发生卷吸作用而
被稀释,然后再彼此混合燃烧。 重油和经过稀释的氧化剂进行