第二章轮廓类2D零件加工编程样式典范和参数设定
轮廓零件的程序编写、加工

2、轮廓零件的程序编写、加工例1、如图所示零件,已知材料为45钢,毛坯为150×120×30,试编写零件的加工程序。
【分析】1.根据图样要求、毛坯,确定工艺方案及加工路线1)以毛坯的底面和侧面为定位基准,用通用台虎钳夹紧工件前后两侧面(宽度),并将台虎钳固定于铣床工作台上。
2)选用平底立铣刀,一次切深5mm,直接加工工件的轮廓外形。
3)采用G41加工方式,有利于保证侧面表面粗糙度。
4)起刀点和抬刀点,建立刀补和撤消刀补都要在工件内部完成。
2.选择机床设备根据零件图样要求,选用VMC-600型数控立式铣床。
3.选择刀具与参数现采用Ø 8-Ø20的平底立铣刀皆可,现在选用Ø10立铣刀,并把该刀具的半径输入刀具半径补偿参数表中。
4.确定切削用量主轴转速:n=1000V/πD (V表示刀具切削速度。
高速钢刀具一般取20m/s;硬质合金刀具一般50-100m/s,具体还应考虑被加工材料的切削性能)进给速度:F=f z Zn (f z表示每齿进给量;Z表示齿数;n表示转速)切削用量的具体数值应根据该机床性能、相关的手册并结合实际经验确定,详见加工程序。
5.确定工件坐标系在XOY平面内选择工件对称中心为工件原点,Z方向选择工件上表面为工件原点,建立工件坐标系(编程坐标系)。
(将X、Y、Z坐标值均输入到G54中去,直接调用G54中的X、Y、Z值)6.编写程序按该机床规定的指令代码和程序段格式,把加工零件的全部工艺过程编写成程序清单。
该工件的加工程序如下(该程序用于VMC-600型数控铣床/加工中心):O5003;(程序名)N10 G80 G40 G49 G69 G50 G15 G21;(取消所有固定循环功能,并采用公制mm编程)N20 G00 G90 G54 X0 Y0;(绝对编程,调用G54坐标,刀具快速走到编程原点)N30 M03 S636;(启动主轴)N40 G00 X0 Y0;(快速到达起刀点)N50 G00 Z10;(刀具快速下到工件表面10mm处)N60 G01 Z-5 F100;(按指定速度到达5mm切深处)N70 G01 G41 X0 Y-40 D01 F100;(在工件内部按指定速度从1点切削进给到2点,并在从1点到2点的过程中建立刀具半径补偿左补偿)N80 G01 X40 Y-40 F80;(3点)N90 G03 X55 Y-25 R15;(4点)N100 G01 X55 Y25;(5点)N110 G03 X40 Y40 R15;(6点)N120 G01 X-20 Y40;(7点)N130 G03 X-20 Y-40 R40;(8点)N140 G01 X0 Y-40;(9点)N150 G01 G40 X10 Y0;(按指定速度从9点切削进给到10点,并在从9点到10点的过程中撤消刀具半径补偿)N130 G00 Z100;(快速抬刀至100mm处)N140 M30;(程序结束,光标并返回程序起始处)按照上面程序加工后会出现图形如图所示的现象――在终点处有部分工件未被完全切除的现象,分析产生原因?思考:对程序如何进行修改,才能避免此类现象的发生。
二D外开铣削加工参数
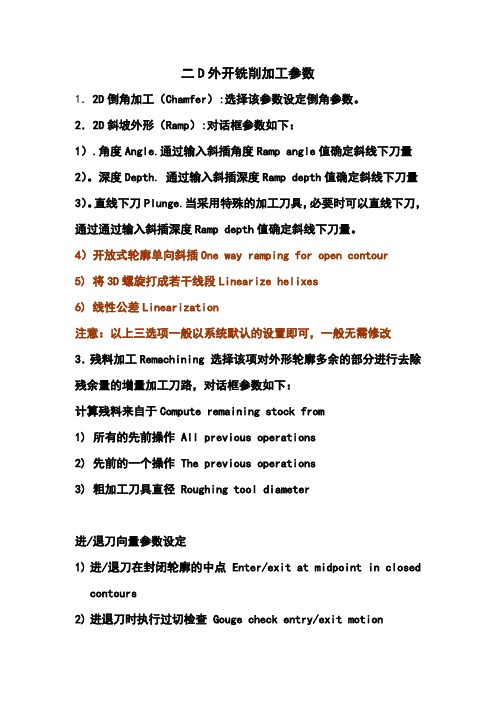
二D外开铣削加工参数
1.2D倒角加工(Chamfer):选择该参数设定倒角参数。
2.2D斜坡外形(Ramp):对话框参数如下:
1).角度Angle.通过输入斜插角度Ramp angle值确定斜线下刀量2)。
深度Depth. 通过输入斜插深度Ramp depth值确定斜线下刀量3)。
直线下刀Plunge.当采用特殊的加工刀具,必要时可以直线下刀,通过通过输入斜插深度Ramp depth值确定斜线下刀量。
4)开放式轮廓单向斜插One way ramping for open contour
5) 将3D螺旋打成若干线段Linearize helixes
6) 线性公差Linearization
注意:以上三选项一般以系统默认的设置即可,一般无需修改
3.残料加工Remachining 选择该项对外形轮廓多余的部分进行去除残余量的增量加工刀路,对话框参数如下:
计算残料来自于Compute remaining stock from
1)所有的先前操作 All previous operations
2)先前的一个操作 The previous operations
3)粗加工刀具直径 Roughing tool diameter
进/退刀向量参数设定
1)进/退刀在封闭轮廓的中点 Enter/exit at midpoint in closed
contours
2)进退刀时执行过切检查 Gouge check entry/exit motion
3)重叠量Overlap:该项应用于封闭外形铣削的退刀点,在退出刀具
路径前,刀具用该距离超过刀具路径端点,然后进行退刀
4)。
轮廓类2D零件加工编程范例和参数设定
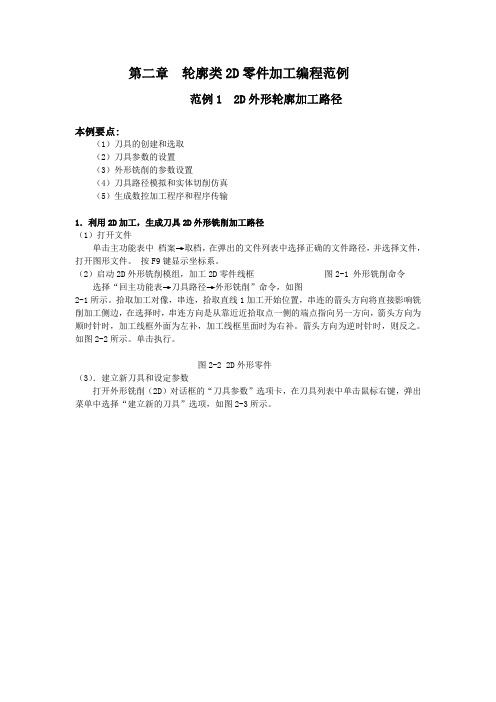
第二章轮廓类2D零件加工编程范例范例1 2D外形轮廓加工路径本例要点:(1)刀具的创建和选取(2)刀具参数的设置(3)外形铣削的参数设置(4)刀具路径模拟和实体切削仿真(5)生成数控加工程序和程序传输1.利用2D加工,生成刀具2D外形铣削加工路径(1)打开文件单击主功能表中档案→取档,在弹出的文件列表中选择正确的文件路径,并选择文件,打开图形文件。
按F9键显示坐标系。
(2)启动2D外形铣削模组,加工2D零件线框图2-1 外形铣削命令选择“回主功能表→刀具路径→外形铣削”命令,如图2-1所示。
拾取加工对像,串连,拾取直线1加工开始位置,串连的箭头方向将直接影响铣削加工侧边,在选择时,串连方向是从靠近近拾取点一侧的端点指向另一方向,箭头方向为顺时针时,加工线框外面为左补,加工线框里面时为右补。
箭头方向为逆时针时,则反之。
如图2-2所示。
单击执行。
图2-2 2D外形零件(3).建立新刀具和设定参数打开外形铣削(2D)对话框的“刀具参数”选项卡,在刀具列表中单击鼠标右键,弹出菜单中选择“建立新的刀具”选项,如图2-3所示。
图2-3 外形铣削视窗系统将弹出如图2-4所示的“定义刀具”对话框,首先进入刀具类型选择,单击“平刀”选项,系统自动切换到“刀具→平刀”选项卡,从中可以设置刀具参数,,如图2-5所示。
图2-4 定义刀具视窗图2-5 刀具-平刀设置直径为10,其余参数均按默认值。
再点击“参数”设置刀具加工参数如图2-6所示,图2-6 刀具参数点击“工作设定”弹出“工作设定”视窗,进给率的计算选择为依照刀具。
如图2-7所示。
图2-7 工作设定视窗在“外形铣削”视窗中,选择“外形铣削参数”选项卡,设置XY方向预留量设为0,由于零件上表面的Z=0,故设置进给下刀位置为和参考高度设置为,加工深度按零件要求设为-15。
注意绝对坐标和增量坐标的选择,参数设置如图2-8所示。
图2-8 外形铣削参数设置设置分层铣深参数。
任务6 具有非圆曲线轮廓的零件加工编程与操作第2版(FANUC)

能 报
4.手动安装φ20mm粗加工两刃立铣刀至主轴。
国
5.用铣刀直接对刀,将X、Y对刀值输入G54地址,设置工件坐标系零点偏置 值,G54地址中的Z地址须为0。在每把刀的刀补界面输入Z对刀值及刀具半径补偿
值。工件坐标系的原点设在工件上表面的对称中心。
1166
四、任务实施
勤 学
(二)零件加工
苦
6.输入程序,并反复检查。检查无误后,自动状态下进行外轮廓粗加工。
勤 学 苦 练
技 能
任务六 具有非圆曲线轮廓的零件
报
加工编程与操作
国
11
一、任务导入
勤 (一)任务描述
学
使用FAUNC系统数控铣床,对如图2-40所示的非圆曲线
苦
练
类零件进行编程及加工。
技 能 报 国
图2-40 二维椭圆零件
22
一、任务导入
勤
学 (二)知识目标
苦 1.掌握FANUC数控系统宏指令的使用与编程。 练 2.掌握FANUC数控系统条件转移或循环语句在非圆曲线轮廓编
抬刀,取消刀具长度补偿,回到机床原点
1133
四、任务实施
勤 (一)编写零件加工程序
学
表2-37 加工主程序
苦
N80 M00;
(机床动作暂停,手工装φ20mm 三刃立铣刀)
练
N90 M03 S500 G00 X62. Y5.; (设置T2主轴转速,快移至加工定位点,)
N100 G01 G43 Z5. F1000 H02; 带入刀具长度补偿,下移至工件上5mm处
练
7.粗加工完毕后,机床暂停,手动测量工件,如数据与理想状态相符,则不
需修改精铣刀刀补值。
mastercam二维零件设计与轮廓加工刀具路径
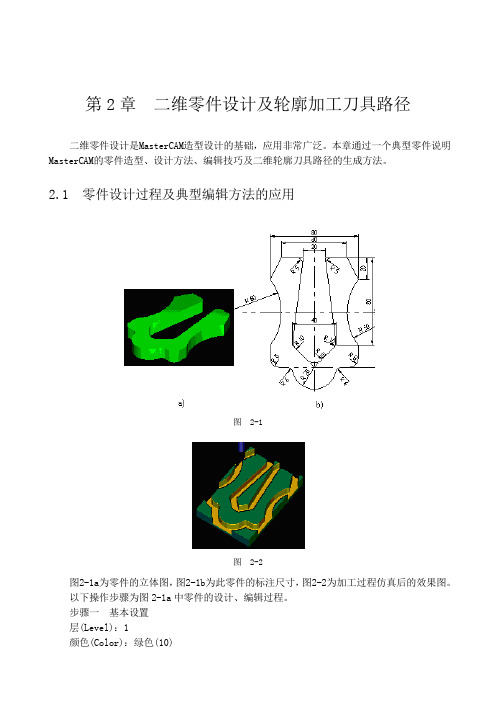
第2章二维零件设计及轮廓加工刀具路径二维零件设计是MasterCAM造型设计的基础,应用非常广泛。
本章通过一个典型零件说明MasterCAM的零件造型、设计方法、编辑技巧及二维轮廓刀具路径的生成方法。
2.1 零件设计过程及典型编辑方法的应用图 2-1图 2-2图2-1a为零件的立体图,图2-1b为此零件的标注尺寸,图2-2为加工过程仿真后的效果图。
以下操作步骤为图2-1a中零件的设计、编辑过程。
步骤一基本设置层(Level):1颜色(Color):绿色(10).专业整理..学习帮手.Z向深度控制:0线型(Style):实线(Solid)线宽(Witdth):2绘图面(Cplane):俯视图(T)视图面(Gview):俯视图(T)步骤二建立工件设计坐标系,绘制一矩形按功能键F9,在屏幕中间出现一个十字线,即为工件设计坐标系。
绘制矩形方法如下:选择主菜单(Main Menu)-绘图(Create)-矩形(Rectangle)-两点(2 points)输入左上方端点:-40,50 回车右下方端点: 0,-50 回车结果如图2-3所示。
图 2-3 图 2-4步骤三绘制圆选择主菜单(Main Menu)-绘图(Create)-圆弧(Arc)-圆心、半径(Circ pt+rad)输入半径:50 回车圆心:-80,0 回车按Esc键结束绘制圆。
结果如图2-4所示。
步骤四打断圆与直线选择主菜单(Main Menu)-修整(Modify)-打断(Break)-两段(2 pieces)用鼠标拾取图2-4中的圆C1,并拾取断点位置于圆上P1位置,则圆被打断为两段,断点分别为P1和P2,如图2-4所示;拾取图2-4中的直线L1,并拾取断点位置于直线中点P3位置;打断后的图素与原图素只有拾取图素时才能分辨出,拾取选中的部分,颜色会发生变化。
步骤五修剪选择主菜单(Main Menu)-修整(Modify)-修剪(Trim)-两图素(2 entities)用鼠标分别拾取图2-4所示的直线L1上位置P4和圆C1上位置P5,得到图2-5;用鼠标分别拾取图2-5所示的直线上位置P1和圆上位置P2,得到图2-6。
二维轮廓加工
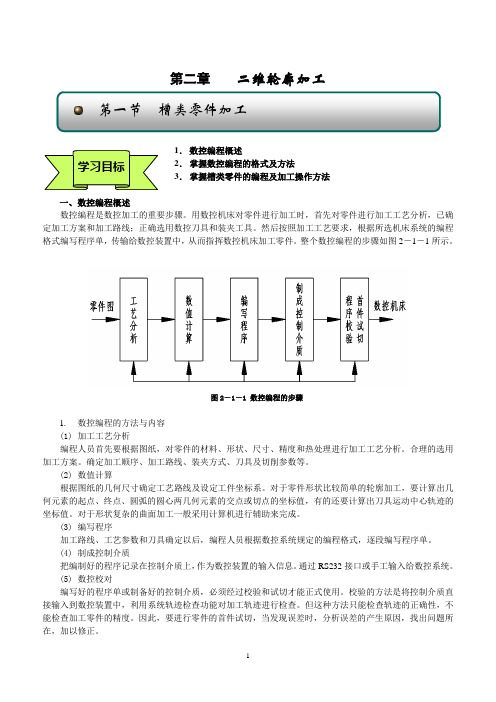
第二章 二维轮廓加工1. 数控编程概述2. 掌握数控编程的格式及方法3.掌握槽类零件的编程及加工操作方法一、 数控编程概述数控编程是数控加工的重要步骤。
用数控机床对零件进行加工时,首先对零件进行加工工艺分析,已确定加工方案和加工路线;正确选用数控刀具和装夹工具。
然后按照加工工艺要求,根据所选机床系统的编程格式编写程序单,传输给数控装置中,从而指挥数控机床加工零件。
整个数控编程的步骤如图2-1-1所示。
图2-1-1 数控编程的步骤1.数控编程的方法与内容(1) 加工工艺分析编程人员首先要根据图纸,对零件的材料、形状、尺寸、精度和热处理进行加工工艺分析。
合理的选用加工方案。
确定加工顺序、加工路线、装夹方式、刀具及切削参数等。
(2) 数值计算根据图纸的几何尺寸确定工艺路线及设定工件坐标系。
对于零件形状比较简单的轮廓加工,要计算出几何元素的起点、终点、圆弧的圆心两几何元素的交点或切点的坐标值,有的还要计算出刀具运动中心轨迹的坐标值。
对于形状复杂的曲面加工一般采用计算机进行辅助来完成。
(3) 编写程序加工路线、工艺参数和刀具确定以后,编程人员根据数控系统规定的编程格式,逐段编写程序单。
(4) 制成控制介质把编制好的程序记录在控制介质上,作为数控装置的输入信息。
通过RS232接口或手工输入给数控系统。
(5) 数控校对编写好的程序单或制备好的控制介质,必须经过校验和试切才能正式使用。
校验的方法是将控制介质直接输入到数控装置中,利用系统轨迹检查功能对加工轨迹进行检查。
但这种方法只能检查轨迹的正确性,不能检查加工零件的精度。
因此,要进行零件的首件试切,当发现误差时,分析误差的产生原因,找出问题所在,加以修正。
第一节 槽类零件加工2.数控编程的种类数控编程可分为手工编程和自动编程两种。
(1)手工编程加工零件形状比较简单、计算量小、程序不多的零件,采用手工编程比较容易,而且经济,因此手工仍应用较为广泛。
对于复杂形状的零件,特别是具有非圆曲线及曲面组成的零件,用手工编程就有一定的难度,出错概率大,有时甚至无法编出程序,必须用自动编程的方法进行编程。
参考答案-《数控机床编程与操作(第四版 数控铣床 加工中心分册)习题册》-A02-3585

数控机床编程与操作(第四版数控铣床加工中心分册)习题册参考答案第一章数控铣床/加工中心及其编程基础第一节数控铣床/加工中心概述一、填空题1. 数控技术2. 车削加工3. 铣削镗削4. 刀库刀具自动交换装置5. 采用点位控制系统刀具移动轨迹6. 数控装置刀库和换刀装置7. 分盘式刀库链式刀库8. 法那科西门子华中数控广州数控二、选择题1.C2.D3.B4.D5.C6.D三、判断题1.×2.×3.×4.√5.√6.×第二节数控加工与数控编程概述一、填空题1. 加工程序数字控制2. 加工程序加工精度3. 手工编程自动编程4. 确定加工工艺数值计算制作控制介质5. 软磁盘移动存储器硬盘6. 语言式交互式CAD/CAM7. 程序程序数控编程8.UG PRO/E MASTERCAM POWERMILL二、选择题1.A2.C3.B4.C5.A6.B三、判断题1.×2.×3.×4.√5.√第三节数控铣床/加工中心编程基础知识一、填空题1. 标准坐标系2. X Y Z3. 主轴X远离4. 右右5. 程序号程序内容程序结束6.O 四位数字7.M02 M30 M17 M02 RET8. 字—地址使用分隔符固定9. ( ) ; 10. 基准参考正二、选择题1.C2.A3.D4.C5.A6.D7.B8.B9.D三、判断题1.×2.×3.√4.√5.×6.×7.×8.√9.√10.×第四节数控机床的有关功能及规则一、填空题1. 准备功能辅助功能其他功能2. 1号刀具2号刀沿3. 每分钟每转mm / min mm / r4.G96 G97 v =πDn / 10005.M03 M04 M056. 模态代码续效非模态非续效7. XY ZX YZ8. 绝对坐标相对坐标9. 合成速度圆弧的切线方向的速度10. 50%~120%二、选择题1.D2.A3.A4.C5.D6.A7.A8.C9.C 10.D 11.C 12.B三、判断题1.×2.×3.×4.√5.×6.√7.√8.×9.√10.√第五节数控铣床/加工中心编程的常用功能指令一、填空题1.G00 G01 顺时针圆弧插补逆时针圆弧插补2. 圆弧半径起点到圆心矢量3.M98 M99 M08 M094. 正值负值5.G006. 镗平面锪孔7. 工件坐标系8. 暂停10s9. 至绝对坐标X-30.0 处10. G75二、选择题1.D2.C3.D4.C5.B6.A7.B8.B9.B 10.A 11.A 12.A三、判断题1.×2.×3.√4.√5.√6.×7.√8.×9.√10.√11.√12.√13.√14.×15.√四、编程题略。
数控铣床编程模块2 外轮廓零件加工

2 平底铣刀
立铣刀是数控机床上用得最多的一种铣刀。立铣刀的圆柱表面和端 面上都有切削刃,圆柱表面的切削刃为主切削刃,端面上的切削刃为副 切削刃,它们可同时进行切削,也可单独进行切削。主切削刃一般为螺 旋齿,这样可以增加切削平稳性,提高加工精度。由于普通立铣刀端面 中心处无切削刃,所以立铣刀不能进行轴向进给,端面刃主要用来加工 与侧面相垂直的底平面。
在加工过程中,当刀具需要在两点间移动而不切削时,是否要提刀到 安全平面呢?当设定为抬刀时,刀具将先提高到安全平面,再在安全平面 上移动;否则将直接在两点间移动而不提刀。直接移动可以节省抬刀时间 ,但是必须要注意安全,在移动路径中不能有凸出的部位,特别注意在编 程中,当分区域选择加工曲面并分区加工时,中间没有选择的部分是否有 高于刀具移动路线的部分。在粗加工时,对较大面积的加工通常建议使用 抬刀,以便在加工时可以暂停,对刀具进行检查。而在精加工时,常使用 不抬刀以加快加工速度,特别是像角落部分的加工,抬刀将造成加工时间 大幅延长,如图2-7所示。
图2-7 起止高度与安全高度
图2-8 安全高度
图2-9 Z向下刀
2 水平方向进/退刀方式
为了改善铣刀开始接触工件和离开工件表面时的状况,数控编程时一般要 设置刀具接近工件和离开工件表面时的特殊运行轨迹,以避免刀具直接与工件 表面相撞和保护已加工表面。水平方向进/退刀方式分为“直线”与“圆弧”两种方 式,分别需要设定进/退刀线长度和进/退刀圆弧半径。
精加工轮廓时,比较常用的方式是,以被加工表面相切的圆弧方式接触 和退出工件表面,如图2-10所示,图中的切入轨迹是以圆弧方式与被加工表 面相切,退出时也是以一个圆弧轨迹离开工件。另一种方式是,以被加工表 面法线方向进入和退出工件表面,进入和退出轨迹是与被加工表面相垂直( 法向)的一段直线,此方式相对轨迹较短,适用于表面要求不高的情况,常 在粗加工或半精加工中使用。
数控加工程序编制_铣削编程2平面轮廓类零件程序编制
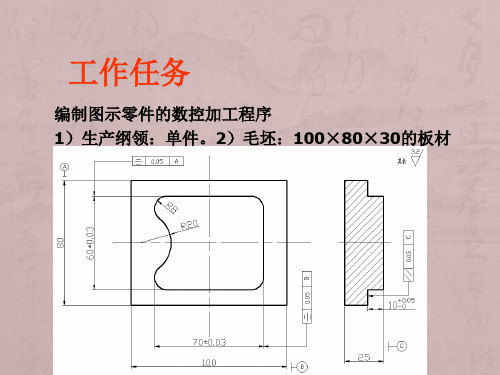
二、相关知识
(六)功能指令
在执行G00时,为避免刀具与工件或夹具相撞,通常 采用三轴不同段的编程方法,即:
刀具从上向下移动时:
刀具从下向上移动时:
编程格式:G00 X- YZ-
编程格式:G00 ZX- Y-
当刀具从上向下移动时,先在XY平面内定位,然后再沿 Z轴下降;当刀具从下向上运动时,刀具先沿Z轴上升,然 后再在XY平面内定位。
二、相关知识
(二)平面加工方法的选择
加工方案 粗车→半精车 粗车→半精车→精车 粗车→半精车→磨削
粗刨(或粗铣)→精刨(或精铣)
粗刨(或粗铣)→精刨(或精 铣)→刮研
粗刨(或粗铣)→精刨(或精 铣)→宽刃精刨
粗刨(或粗铣)→精刨(或精 铣)→磨削
粗刨(或粗铣)→精刨(或精 铣)→粗磨→精磨
粗刨→拉
功能
快速点定位 直线插补
XY平面选择 XZ平面选择 YZ平面选择
英寸
指令
G71 G54*~G59
G90* G91 G94* G95
带“*”号的G指令表示接通电源时,即为G指令的状态。
功能
毫米 工件坐标系选择
绝对值编程 增量值编程 每分钟进给
每转进给
二、相关知识
(六)功能指令
1.坐标平面选择指令(G17,G18,G19) 应用数控铣床/加工中心进行零件加工前,只有先指
G00 X-30Y-30
(刀具从F点快速返回至A点)
…………………
G01、F指令都是续效指令,不必在每个程序段中都写入
G01及F指令。
二、相关知识
(六)功能指令
5.圆弧插补:G2,G3
项目3-2 平面轮廓编程与加工
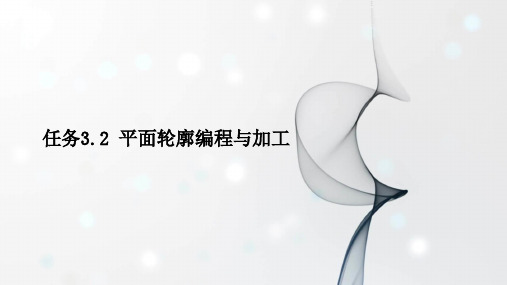
N50 G91 G01 Z-4 F80;
N60 G41 G01 X15 Y0 D01 F150;
N70 G03 I-15 J0; N80 G40 G00 X-15 Y0; N90 G91 G01 Z-4 F80;
N100 G41 G01 X15 Y0 D01 F150;
N110 N120 N130 N140
立在工件上表面中心 • 刀具进刀方式:选择A点法向进刀
• 直槽加工程序
段号
N10 N20 N30 N40 N50 N60 N70 N80 N90 N100 N110 N120 N130 N140
加工程序 O0001; G54 G90 G17; M03 S1000; G00 X-40 Y-40; Z5; G01 Z-3 F100; Y40; X30; G02 X40 Y30 R10; G01 Y-30; G02 X30 Y-40 R10; G01 X-40; G00 Z100; M05; M30;
N4
Z5 M08;
N5 G01 Z-5 F300;
N6 G42 G00 X-55 Y-30 D01;
N7 G01 X20 F300;
N8 G02 X40 Y-10 I20 J0;
N9 G01
Y20;
N10 G03 X30 Y30 I-10 J0;
N11 01 X-10;
N12
X-40 Y20;
N13
XYZ表示终点,需经过与G28指令中设置 的中间点,不能独立使用。
绝对坐标编程 XYZ表示表示绝对坐标尺寸
相对坐标编程 XYZ表示表示相对坐标尺寸
进给单位指定 F单位mm/min
进给单位指定 主轴恒切削速 度 直接转速
F单位mm/r S单位m/s S单位r/min
第2讲 机械零件轮廓图的绘制技巧与技术要领
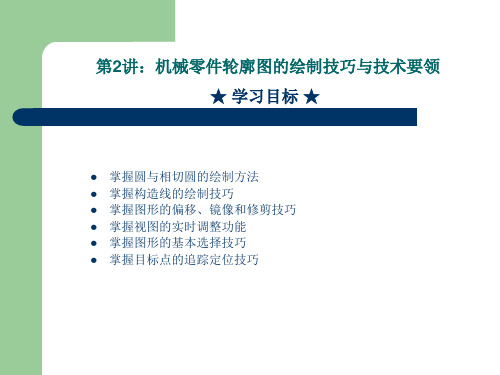
选择要偏移的对象,或 [退出(E)/放弃(U)] <退出>: //选择刚绘制的直线 指定要偏移的那一侧上的点,或 [退出(E)/多个(M)/放弃(U)] <退出>: //在线段的一侧拾取一点 选择要偏移的对象,或 [退出(E)/放弃(U)] <退出>: //选择圆图形 指定要偏移的那一侧上的点,或 [退出(E)/多个(M)/放弃(U)] <退出>: //在圆的内部拾取一点 选择要偏移的对象,或 [退出(E)/放弃(U)] <退出>: // Enter,退出命令,偏移结果如右图所示。
定点偏移:所谓“定点偏移”,指的就是按照指定的通过点,进行偏移对象。现假 设对某圆的直径进行定点偏移,则可以按如下步骤进行操作: 1.首先使用画线和画圆命令绘制如下图所示的图形。 2.在命令行中输入Offset按Enter键,或输入简写O按Enter键,执行命令。 执行【偏移】命令后,根据AutoCAD命令行的操作提示,进行偏移对象。
修剪图形:【修剪】命令用于沿指定 的修剪边界修剪掉目标对象中不需 要的部分。如右图所示。所选择的 修剪边界与目标对象可以相交,也 可以不相交。
执行【修剪】命令主要有以下几种方式: 1.菜单栏:单击菜单【修改】/【修剪】命令。2.工具栏:单击【修改】工 具栏上的按钮。3.命令行:在命令行输入Trim。4.快捷键:在命令行输 入TR。 修剪到实际交点:所谓“修剪到实际交点”,指的是修剪边界与修剪对象存在有 实际的交点,在此交点处将修剪对象的一部分断开并删除。现假设以右图所 示的水平直线段作为位于边界,将位于其下侧的倾斜线段修剪掉,则可以按 如下步骤进行操作: 1.绘制如下图所示的两条相交线段。 2.单击“修改”工具栏上的修剪按钮,激活“修剪”命令。 3.在命令行“选择剪切边...选择对象或 <全部选择>:”提示下,选择水平直线 段作为修剪边界。 4.继续在“选择对象:”提示下敲击Enter键结束选择。 5.在“选择要修剪的对象,或按住 Shift 键选择要延伸的对象,或[栏选(F)/窗交 (C)/投影(P)/边(E)/删除(R)/放弃(U)]:”提示下,在斜线段的下侧单击左键, 结果位于修剪边界下侧的部分被修剪,如下图所示。
项目六 平面轮廓零件的数控编程与加工

使用刀具半径补偿的注意事项 使用刀具半径补偿时应避免过切削现象。 (1) 使用刀具半径补偿时应避免过切削现象。这 又包括以下三种情况: 又包括以下三种情况: 使用刀具半径补偿和取消刀具半径补偿时, ① 使用刀具半径补偿和取消刀具半径补偿时 , 刀具必须在所补偿的平面内移动, 刀具必须在所补偿的平面内移动,移动距离应大于刀 具补偿值。 具补偿值。 加工半径小于刀具半径的内圆弧时, ② 加工半径小于刀具半径的内圆弧时 , 进行半 径补偿将产生过切削 只有过渡圆角R≥刀具半径r 过切削。 R≥刀具半径 径补偿将产生过切削。只有过渡圆角R≥刀具半径r+ 精加工余量的情况下才能正常切削。 精加工余量的情况下才能正常切削。 被铣削槽底宽小于刀具直径时将产生过切削 过切削。 ③ 被铣削槽底宽小于刀具直径时将产生过切削。
Y50.0; Y50.0; X50.0; X50.0;
刀刀刀刀刀刀
Y20.0; Y20.0; X10.0; X10.0; Z50.0; G00 Z50.0; G40 X0 Y0 ; 抬刀到起始高度 取消补偿
G54
X
M30; ;
Y 50 40 30 20 10 10 O 20 30 40 50
刀具半径补偿过程描述
N20 Z10.0; ; 安全高度 N25 G41 G00X20.0 Y10.0 D01;刀具 ; 半径补偿, 半径补偿,D01为刀具半径补偿号 为刀具半径补偿号 N30 G01 Z-10.0; 落刀,切深 mm ; 落刀,切深10 N35 Y50.0; ; N40 X50.0; ;
G41左偏,G42右偏, G41左偏,G42右偏,偏置大小为指定的偏置 左偏 右偏 号(D01)地址中的数值。在这里N25坐标点与 (D01)地址中的数值。在这里N25坐标点与 地址中的数值 N25 N35坐标点运动方向垂直于X N35坐标点运动方向垂直于X轴,所以刀具中 坐标点运动方向垂直于 心的位置应在(X20.0,Y10.0)左面刀具半径 心的位置应在(X20.0,Y10.0)左面刀具半径 (X20.0 处。
- 1、下载文档前请自行甄别文档内容的完整性,平台不提供额外的编辑、内容补充、找答案等附加服务。
- 2、"仅部分预览"的文档,不可在线预览部分如存在完整性等问题,可反馈申请退款(可完整预览的文档不适用该条件!)。
- 3、如文档侵犯您的权益,请联系客服反馈,我们会尽快为您处理(人工客服工作时间:9:00-18:30)。
第二章轮廓类2D零件加工编程范例范例1 2D外形轮廓加工路径本例要点:(1)刀具的创建和选取(2)刀具参数的设置(3)外形铣削的参数设置(4)刀具路径模拟和实体切削仿真(5)生成数控加工程序和程序传输1.利用2D加工,生成刀具2D外形铣削加工路径(1)打开文件单击主功能表中档案→取档,在弹出的文件列表中选择正确的文件路径,并选择3-1.mc9文件,打开图形文件。
按F9键显示坐标系。
(2)启动2D外形铣削模组,加工2D零件线框图2-1 外形铣削命令选择“回主功能表→刀具路径→外形铣削”命令,如图2-1所示。
拾取加工对像,串连,拾取直线1加工开始位置,串连的箭头方向将直接影响铣削加工侧边,在选择时,串连方向是从靠近近拾取点一侧的端点指向另一方向,箭头方向为顺时针时,加工线框外面为左补,加工线框里面时为右补。
箭头方向为逆时针时,则反之。
如图2-2所示。
单击执行。
图2-2 2D外形零件(3).建立新刀具和设定参数打开外形铣削(2D)对话框的“刀具参数”选项卡,在刀具列表中单击鼠标右键,弹出菜单中选择“建立新的刀具”选项,如图2-3所示。
图2-3 外形铣削视窗系统将弹出如图2-4所示的“定义刀具”对话框,首先进入刀具类型选择,单击“平刀”选项,系统自动切换到“刀具→平刀”选项卡,从中可以设置刀具参数,,如图2-5所示。
图2-4 定义刀具视窗图2-5 刀具-平刀设置直径为10,其余参数均按默认值。
再点击“参数”设置刀具加工参数如图2-6所示,图2-6 刀具参数点击“工作设定”弹出“工作设定”视窗,进给率的计算选择为依照刀具。
如图2-7所示。
图2-7 工作设定视窗在“外形铣削”视窗中,选择“外形铣削参数”选项卡,设置XY方向预留量设为0,由于零件上表面的Z=0,故设置进给下刀位置为3.0和参考高度设置为30.0,加工深度按零件要求设为-15。
注意绝对坐标和增量坐标的选择,参数设置如图2-8所示。
图2-8 外形铣削参数设置设置分层铣深参数。
在“Z轴分层铣深”前打勾,单击“Z轴分层铣深”按钮,打开“Z 轴分层铣深设定”对话框,如图2-9所示,设置分层铣深参数。
最大粗切量为0.5mm;精铣次数为0;其余参数按照默认值单击“确定”按钮返回到外形铣削参数对话框。
图2-9 Z轴分层铣深设定设置进/退刀参数。
单击“进/退刀向量”按钮,打开“进/退刀向量设定”对话框,如图2-10所示,设置进退刀向量参数。
激活“进刀向量”选项;引线为“相切”;长度为0.0,斜向高度为0.0圆弧半径值为5.0;扫掠角度为180;螺旋高度为0.0其它设置按默认单击中间的箭头,将进刀向量参数复制到退刀向量参数。
单击“确定”按钮返回到外形铣削参数对话框。
图2-10 进/退刀向量设定单击确定按钮,系统即按设置参数计算出刀具路径,屏幕显示刀具2D加工路径,如图2-11所示。
图2-11 2D加工路径2.刀具路径模拟和实体切削仿真实体模拟刀削可对工件进行比较逼真的模拟切削,能过切削模拟可以提高程序的安全性和合理性,通过实体切削模拟可以发现在实际加工时某些存在的问题,以便编程人员及时修正,避免工件报废。
通过实体模拟切削还可以反应加工后的实际形状,为后面的程序编制提供直观的参考。
选择操作管理,弹出“操作管理员”视窗,如图2.12所示。
图2-12 操作管理员视窗单击“刀具路径模拟”。
单击“手动控制”多次,屏幕上依次显示刀具路径,或者单击“自动控制”,自动显示出刀具路径。
使用实体切削仿真来验证刀具路径的正确性。
单击“实体切削验证”,弹出“实体验证”视窗,如图2-13所示。
图2-13 实体切削验证单击最左边的“参数设定”,弹出“实体验证之参数设定”视窗,设定参数,单击“确定”,如图2-14所示图2-14 实体验证之参数设定单击“持续执行”,实体切削仿真如图2-15所示。
图2-15 实体切削仿真提示:实体验证的结果图形的变更,可以通过动态旋转的方法,选择一个最佳的观察角度进行检视。
3.生成数控加工程序和程序输送(1)生成数控加工程序在“操作管理员”视窗中,单击“执行后处理”,视窗中,选中“储存NC档”、“编辑”“询问”,在MasterCAM系统文件中,有自带一个默认的后处理PST文件,也可以在图2-16中单击“更改后处理程式”按钮,选择一个合适的后处理文件。
单击确定。
图2-16 后处理程序输入一个NC文件名,系统自动生成数控加工程序,如图2-17所示。
图2-17 数控加工程序(2)程序输送选择“回主功能表→档案→下一页→DNC传输”命令,在“传输参数”中设置参数,注意设置传输速率应与机床数控系统的设置相同。
选择“传送”选取加工程序文件名,则系统将加工程序输送给数控机床。
如图2-18所示。
图2-18 数控加工程序传输参数4.保存图形文件选择“回主功能表→档案→存档”命令,键入文件名:2-1A.mc9。
储存的图形文件和最终的刀具路径。
范例2 对2D外形轮廓边缘作倒角加工本例要点:(1)刀具路径的复制(2)外形铣削倒角的参数设置(3)刀具路径的镜像(4)刀具路径的平移(5)刀具路径模拟和实体切削仿真(6)生成数控加工程序和程序传输1.复制刀具路径,对轮廓边缘作倒角加工打开范例1保存后的图形,选择“回主功能表→刀具路径→操作管理”,打开“操作管理员”视窗,复制“1-外形铣削(2D)”,贴上成“2-外形铣削(2D)”,如图2-19所示。
图2-19 复制、贴上操作单击“2-外形铣削(2D)”的参数,在“刀具参数”选项卡中,选取12.0倒角刀。
单击“外形铣削参数”,在外形铣削型式下拉式列表中选择“2D倒角”,单击“倒角加工”,设置宽度为1.2,尖部补偿为2.5,单击“确定”。
设置深度0.0,增量坐标方式,如图3-20所示。
单击确定。
图2-20 2D倒角加工提示:2D倒角加工将不能作分层加工,能做加工最大深度的这一层的加工。
回到“操作管理员”视窗中,单击“重新计算”。
单击“全选”,单击“实体切削验证”,单击“持续执行”,结果如图2-21所示,储存图形文件。
图2-21 实体切削验证2.对已生成的刀具路径,进行镜向系统提供了一个对刀具路径的转换功能,可以对已生成的刀具路径进行旋转,平移,镜向转换,生成新的刀具路径。
选择“回主功能表→刀具路径→下一页→路径转换”,在“转换操作之参数设定”视窗中,单击1群组,选中二个刀具路径,选中“镜射”,选中“产生新的操作及图形”,如图2-22所示。
图2-22 路径转换单击镜射,设置参数图2-23所示,选择对Y轴镜射,打开“更改刀具路径方向”开关,以保证生成的刀具路径同原刀具路径的加工方向一样,仍为逆铣。
确定,生成刀具路径如图2-24所示。
图2-23 镜射参数设定图2-24 镜射后的刀具路径范例3 生成二维轮廓零件的刀具路径和旋转刀具路径本例要点:(1)刀具的创建和选取(2)刀具参数的设置(3)外形铣削的参数设置(4)刀具路径的旋转(5)刀具路径模拟和实体切削仿真(6)生成数控加工程序和程序传输1.利用2D加工,生成刀具2D外形铣削加工路径(1)打开文件单击主功能表中档案→取档,在弹出的文件列表中选择正确的文件路径,并选择2-2. mc9文件,打开图形文件。
按F9键显示坐标系。
(2)启动2D外形铣削模组,生成一个槽的轮廓加工刀具路径。
选择“回主功能表→刀具路径→外形铣削”命令,选取加工起始位置A,执行,如图2-25所示。
图2-25 二维零件图(3).建立新刀具和设定参数打开外形铣削(2D)对话框的“刀具参数”选项卡,在刀具列表中单击鼠标右键,弹出菜单中选择“建立新的刀具”选项,系统将弹出“定义刀具”对话框,首先进入刀具类型选择,单击“平刀”选项,系统自动切换到“刀具→平刀”选项卡,从中可以设置刀具参数,设置直径为16mm,其余参数均按默认值。
再点击“参数”设置刀具加工参数,如图2-26所示点击“工作设定”弹出“工作设定”视窗,进给率的计算选择为依照刀具。
图2-26 刀具参数设置(4).设置外形铣削的加工参数在“外形铣削”视窗中,选择“外形铣削参数”选项卡,补正方向为右,设置XY方向预留量设为0,由于零件上表面的Z=0,故设置进给下刀位置为3.0和参考高度设置为30.0,加工深度按零件要求设为-5。
注意绝对坐标和增量坐标的选择,参数设置如图2-27所示。
图2-27 2D外形铣削参数在外形铣削型式下拉式列表中选择“螺旋式渐降斜插”,单击“渐降斜插”设置参数,如图3-28所示。
设置平面多次铣削参数。
在“平面多次铣削”前打勾,单击“平面多次铣削”按钮,打开“平面多次铣削设定”对话框,如图2-29所示,设置分层铣深参数。
粗铣次数:2粗铣间距:8其余参数按照默认值单击“确定”按钮返回到外形铣削参数对话框。
图2-28 渐降斜插参数提示:螺旋式渐降斜插式轮廓铣削主要有三种下刀方式:角度(指定每次斜插的角度)、深度(指定每次斜插的深度)和直线下刀(不作斜插,直接以深度作垂直下刀)。
采用螺旋式渐降斜插方式后,分层切削选项将不再起作用,同时也不能激活。
图2-29 平面多次铣削参数设置进/退刀参数。
单击“进/退刀向量”按钮,打开“进/退刀向量设定”对话框,如图3-30所示,设置进退刀向量参数。
激活“进刀向量”选项;引线为“相切”;长度为0.0,斜向高度为0.0圆弧半径值为2.0;扫掠角度为180;螺旋高度为0.0其它设置按默认单击中间的箭头,将进刀向量参数复制到退刀向量参数。
单击“确定”按钮返回到外形铣削参数对话框。
图2-30 进/退刀参数单击确定按钮,系统即按设置参数计算出刀具路径,屏幕显示刀具2D加工路径,如图2-31所示。
图2-31 一个槽的刀具路径模拟2.刀具路径的旋转选择“回主功能表→刀具路径→下一页→路径转换”命令,在“旋转操作之参数设定”视窗中,选择型式为旋转,方法为坐标,即生成的所有刀具路径在同一坐标平面,如图2-32所示。
图2-32 刀具路径的旋转单击“旋转”按钮,设置旋转次数为2,起始角度为120,旋转角度为360/3=120,旋转的基准点为原点,如图2-33所示,单击“确定”。
图2-33 旋转参数设置刀具路径如图2-34所示。
图2-34 转换后的刀具路径模拟3.刀具路径模拟和实体切削仿真选择操作管理,弹出“操作管理员”视窗,如图2-35所示图2-35 “操作管理员”视窗单击“刀具路径模拟”。
单击“手动控制”多次,屏幕上依次显示刀具路径,或者单击“自动控制”,自动显示出刀具路径。
使用实体切削仿真来验证刀具路径的正确性。
单击“实体切削验证”,弹出“实体验证”视窗,如图2-36所示。
图2-36 实体验证单击最左边的“参数设定”,弹出“实体验证之参数设定”视窗,设定参数,单击“确定”,单击“持续执行”,实体切削仿真如图2-15所示。