FANUC 0iT 对刀
FANUC0iT对刀
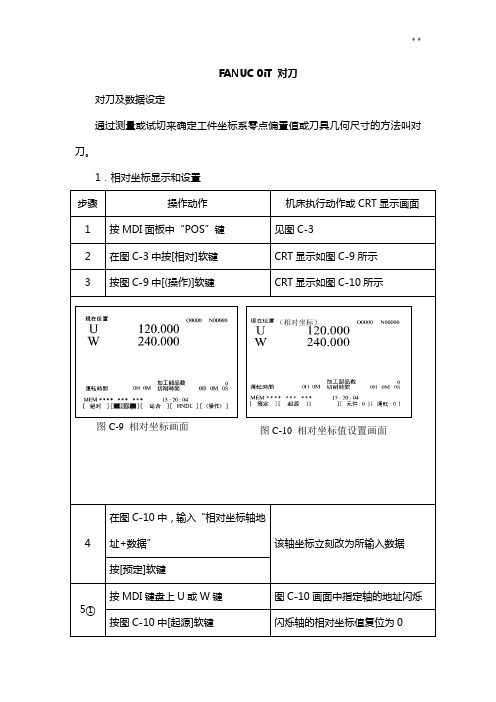
FANUC 0iT 对刀对刀及数据设定通过测量或试切来确定工件坐标系零点偏置值或刀具几何尺寸的方法叫对刀。
1.相对坐标显示和设置 步骤 操作动作机床执行动作或CRT 显示画面 1 按MDI 面板中“POS ”键 见图C-32 在图C-3中按[相对]软键 CRT 显示如图C-9所示 3按图C-9中[(操作)]软键CRT 显示如图C-10所示4在图C-10中,输入“相对坐标轴地址+数据” 该轴坐标立刻改为所输入数据按[预定]软键5①按MDI 键盘上U 或W 键 图C-10画面中指定轴的地址闪烁 按图C-10中[起源]软键闪烁轴的相对坐标值复位为0 (相对坐标)图C-9 相对坐标画面图C-10 相对坐标值设置画面(相对坐标)5②直接按图C-10中[起源]软键CRT显示图C-11 画面1 按图C-11中[全轴]软键所有轴复位至02 在图C-11中输入某一坐标轴地址,再按[EXEC]软键该轴坐标也可复位为02.单刀试切对刀单刀试切对刀,在刀具几何偏置数据输入画面中设定刀具几何长度补偿值的这种对刀方法,将工件原点和机床原点设为重合,程序中不用G50或(54~G59)指令编程,而是把工件零点偏置值当成刀具长度补偿值,用刀具长度补偿指令如T0101、T0202等编程。
(1)Z轴方向刀具几何长度补偿值的设定步骤操作动作机床执行动作或CRT显示画面1 转动主轴,在JOG方式下用具体刀具(如1号刀)切削工件端面A如图C-12所示图C-11 相对坐标全轴设置画面图C-12 Z轴试切对刀图2 按“+X”键退刀X向退刀,Z向不要移动3 按“主轴停止”键停止主轴旋转4 按“OFFSET/SETTING”功能键CRT显示图C-13 画面5 在图C-13中,按[补正]软键CRT显示图C-14 画面6 在图C-14中,按[形状]软键CRT显示图C-15画面7①在图C-15中,移动光标到某一位置,如G01、Z处,键入对刀所得机床Z向坐标(即图C-12中Z机床)设定刀具长度Z补偿值移动光标到(G01、T)处,键入刀具号,如“1”设定刀具号,如1号刀7②按图C-15中的[操作]软键CRT显示图C-16 画面图C-13 补偿/设置功能画面图C-14 刀具磨损补偿画面在图C-16中,移动光标到某一位置,如G01、Z处确定刀具补偿修改位置在图C-16输入行中输入“Z0”,按[测量]软键当前机床坐标系下的Z坐标值作为对应刀具的Z轴刀具长度补偿值被自动设置到指定的偏置号,如1号刀。
FANUCiT对刀

FANUC 0iT 对刀对刀及数据设定通过测量或试切来确定工件坐标系零点偏置值或刀具几何尺寸的方法叫对刀。
1.相对坐标显示和设置步骤操作动作机床执行动作或CRT显示画面1 按MDI面板中“POS”键见图C-32 在图C-3中按[相对]软键CRT显示如图C-9所示3 按图C-9中[(操作)]软键CRT显示如图C-10所示4 在图C-10中,输入“相对坐标轴地址+数据”该轴坐标立刻改为所输入数据按[预定]软键5①按MDI键盘上U或W键图C-10画面中指定轴的地址闪烁按图C-10中[起源]软键闪烁轴的相对坐标值复位为0 (相对坐标)图C-9 相对坐标画面图C-10 相对坐标值设置画面(相对坐标)5②直接按图C-10中[起源]软键 CRT 显示图C-11 画面1 按图C-11中[全轴]软键 所有轴复位至0 2在图C-11中输入某一坐标轴地址,再按[EXEC]软键该轴坐标也可复位为02.单刀试切对刀单刀试切对刀,在刀具几何偏置数据输入画面中设定刀具几何长度补偿值的这种对刀方法,将工件原点和机床原点设为重合,程序中不用G50或(54~G59)指令编程,而是把工件零点偏置值当成刀具长度补偿值,用刀具长度补偿指令如T0101、T0202等编程。
(1)Z 轴方向刀具几何长度补偿值的设定 步骤操作动作机床执行动作或CRT 显示画面 1转动主轴,在JOG 方式下用具体刀具(如1号刀)切削工件端面A如图C-12所示2 按“+X ”键退刀 X 向退刀,Z 向不要移动3 按“主轴停止”键停止主轴旋转4按“OFFSET /SETTING ” 功能键 CRT 显示图C-13 画面图C-11 相对坐标全轴设置画面图C-12 Z 轴试切对刀图5 在图C-13中,按[补正]软键CRT显示图C-14 画面6 在图C-14中,按[形状]软键CRT显示图C-15画面7①在图C-15中,移动光标到某一位置,如G01、Z处,键入对刀所得机床Z向坐标(即图C-12中Z机床)设定刀具长度Z补偿值移动光标到(G01、T)处,键入刀具号,如“1”设定刀具号,如1号刀7②按图C-15中的[操作]软键CRT显示图C-16 画面在图C-16中,移动光标到某一位置,如G01、Z处确定刀具补偿修改位置在图C-16输入行中输入“Z0”,按[测量]软键当前机床坐标系下的Z坐标值作为对应刀具的Z轴刀具长度补偿值被自动设置到指定的偏置号,如1号刀。
FANUC0iT对刀操作步骤

南京斯沃数控仿真系统FANUC0iT对刀操作步骤1.在手动输入方式下,循环停止,PROG程序的MDI中,输入M03S600;插入,主轴循环启动2.端面试切完成后,在参数输入OFFSET SETTING---补正-—-形状里面,输入Z0,然后点测量,则确定了Z轴进给点。
3.在编辑条件下,程序PROG-——DIR中新建一个文件名,然后插入(INSERT),此时需要把程序保护打开4.南京斯沃数控仿真FANUC OiT 系统操作5.先返回参考点6.设置毛坯,镗内孔管料7.点击二维,查看工件为管料8.添加刀具选择镗刀,放于1号刀位,转到加工位。
9.对刀,9.1.在手动输入方式下,循环停止,PROG程序的MDI中,输入M03S600;插入,主轴循环启动9.2.在手动进给下,调节刀具的位置X和Z轴正负调整。
上面板点击POS查看位置数值。
9.3.X的正方向,向下进行端面试切9.4.端面试切完成后,在参数输入OFFSET SETTING--—补正—-—形状里面,输入Z0,然后点测量,则确定了Z轴进给点。
9.5.然后X方向对刀,进行试切。
沿6.3步的操作,将刀沿X负方向移动,留一点准备试切.接着Z轴负方向试切一点,再Z正方向退出,之后停止主轴。
9.6.进行测量,用特征点(就是那个交点)进行测量。
测得D=42。
3.然后测量退出,并返回参考点9.7.输入X=42.310.新建程序,从外面调程序。
新建文本文档,保存类型为:所有文件,文件名为:111。
cnc.11.在编辑条件下,程序PROG——-DIR中新建一个文件名,然后插入(INSERT),此时需要把程序保护打开接着在左边打开刚刚新建的程序,找打新建的程序。
这时就可以看到该程序的轨迹线,然后就可以循环启动了。
都是先进行粗加工,然后进行精加工。
12.最后可以测量已加工成型的零件,查看尺寸。
13.结束,保存,关闭。
BEIJING FANUC 0i系统对刀中的问题
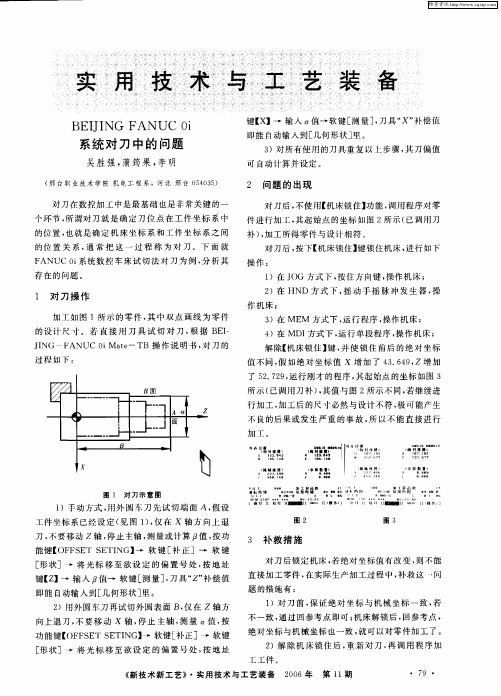
这 时油缸 驱 动传 动轴 5 传 动轴 5再带 动拨 杆 4 , 向相 反 方 向拨 动 活 动 导 套 3 使 活动 导 套 3向后 移 ,
动, 当后 移至 活 动导 套 3 端 面距 工 件 l表 面约 l 前 0
—
薹
m “
:- l … tO 6 | S
I
图 刀意 对 示 图
【 、 j
c m
: !。 :
3 补 救 措 施要移动 轴 , 停止主轴 , 测量或计算 卢 , 值 按功
[ 形状 ]一 将 光 标 移 至 欲设 定 的 偏 置 号 处 , 地 址 按
钻削。
机械 坐标来 标 定 , 锁住 机床 前后 , 会 出现起 刀点 则 不
坐标 值 的改变 , 而可 以使 问题得 到根 治 。 从
5 结 语
在使 用 B in ANUC 0 e igF j i系统 控 制 的数 控 机 床 , 刀后 , 定要 谨 慎 使 用【 床 锁住 】 能 , 对 一 机 功 以免 产生 不 良的后 果或 发生 严重 的事 故 。但 要 从根本 上
功 能键【)F E E NG] - ( s T S TI  ̄ 软键 [ F 补正 ]一 软 键
[ 状]一 将 光 标 移 至 欲 设 定 的偏 置 号 处 , 地 址 形 按
绝对 坐标 与机械 坐标 也一致 , 可 以对 零件 加工 了 。 就
2 )解 除 机 床 锁住 后 , 新 对 刀 , 调 用 程 序加 重 再
作 , 锁 机 床 前 , 变 绝 对 坐 标 值 , 其 与 记 录 值 解 改 使
相同。
4 产 生 原 因与 根 治 方 法
FANUC_Series_0i-MD数控铣床面板操作对刀

数控铣床面板操作与对刀(一)Fanuc-Oi MD数控系统简介图2-1Fanuc-Oi MD数控系统CRT/MDI面板Fanuc Oi Mate-MD数控系统面板由系统操作面板和机床控制面板三部分组成。
1 系统操作面板系统操作面板包括CRT显示区MDI编辑面板。
如图2-1。
(1)CRT显示区:位于整个机床面板的左上方。
包括显示区和屏幕相对应的功能软键(图2-2)。
(2)编辑操作面板(MDI面板):一般位于CRT显示区的右侧。
MDI面板上键的位置(如图:2-3)和各按键的名称及功能见表2-1和表2-2。
图2-2Fanuc Oi Mate-MD数控系统CRT显示区1 功能软键2 扩展软键图2-3MDI面板表2-1 Fanuc Oi MD系统MDI面板上主功能键与功能说明表2-2Fanuc Oi MD系统MDI面板上其他按键与功能说明2 机床控制面板Fanuc Oi Mate-MD数控系统的控制面板通常在CRT显示区的下方(如图:2-3),各按键(旋钮)的名称及功能见表2-3。
图2-3Fanuc Oi Mate-MD数控系统的控制面板表2-3Fanuc Oi Mate-MD数控系统的控制面板各按键及功能(二)机床操作1 开机在操作机床之前必须检查机床是否正常,并使机床通电,开机顺序如下:(1)先开机床总电源;(2)然后开机床稳压器电源;(3)开机床电源;(4)开数控系统电源(按控制面板上的POWER ON按钮);(5)最后把系统急停键旋起。
2 机床手动返回参考点CNC机床上有一个确定的机床位置的基准点,这个点叫做参考点。
通常机床开机以后,第一件要做的事情就是使机床返回到参考点位置。
如果没有执行返回参考点就操作机床,机床的运动将不可预料。
行程检查功能在执行返回参考点之前不能执行。
机床的误动作有可能造成刀具机床本身和工件的损坏,甚至伤害到操作者。
所以机床接通电源后必须正确的使机床返回参考点。
机床返回参考点有手动返回参考点和自动返回参考点两种方式。
对刀对机床加工的重要性和对刀方法介绍
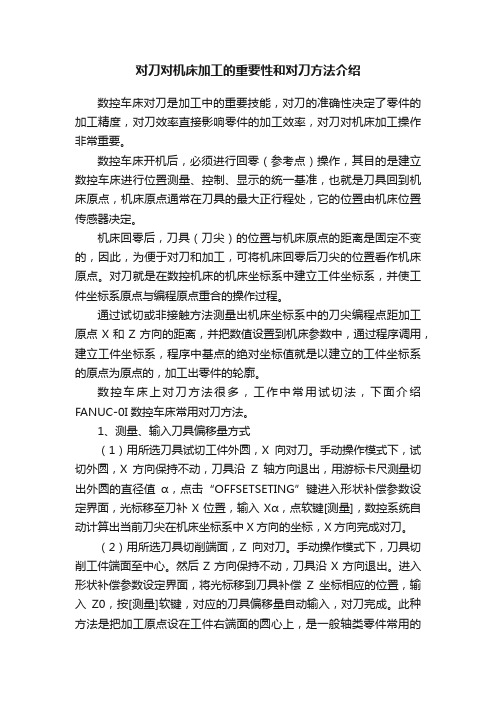
对刀对机床加工的重要性和对刀方法介绍数控车床对刀是加工中的重要技能,对刀的准确性决定了零件的加工精度,对刀效率直接影响零件的加工效率,对刀对机床加工操作非常重要。
数控车床开机后,必须进行回零(参考点)操作,其目的是建立数控车床进行位置测量、控制、显示的统一基准,也就是刀具回到机床原点,机床原点通常在刀具的最大正行程处,它的位置由机床位置传感器决定。
机床回零后,刀具(刀尖)的位置与机床原点的距离是固定不变的,因此,为便于对刀和加工,可将机床回零后刀尖的位置看作机床原点。
对刀就是在数控机床的机床坐标系中建立工件坐标系,并使工件坐标系原点与编程原点重合的操作过程。
通过试切或非接触方法测量出机床坐标系中的刀尖编程点距加工原点X和Z方向的距离,并把数值设置到机床参数中,通过程序调用,建立工件坐标系,程序中基点的绝对坐标值就是以建立的工件坐标系的原点为原点的,加工出零件的轮廓。
数控车床上对刀方法很多,工作中常用试切法,下面介绍FANUC-0I数控车床常用对刀方法。
1、测量、输入刀具偏移量方式(1)用所选刀具试切工件外圆,X向对刀。
手动操作模式下,试切外圆,X方向保持不动,刀具沿Z轴方向退出,用游标卡尺测量切出外圆的直径值α,点击“OFFSETSETING”键进入形状补偿参数设定界面,光标移至刀补X位置,输入Xα,点软键[测量],数控系统自动计算出当前刀尖在机床坐标系中X方向的坐标,X方向完成对刀。
(2)用所选刀具切削端面,Z向对刀。
手动操作模式下,刀具切削工件端面至中心。
然后Z方向保持不动,刀具沿X方向退出。
进入形状补偿参数设定界面,将光标移到刀具补偿Z坐标相应的位置,输入Z0,按[测量]软键,对应的刀具偏移量自动输入,对刀完成。
此种方法是把加工原点设在工件右端面的圆心上,是一般轴类零件常用的方法。
如果是左右对称零件,需把加工原点设在工件的对称中心,则输入Zβ,β为零件轴向长度的一半。
然后根据刀具的几何尺寸和安装位置输入刀尖圆弧半径R和刀位号T的值,例如:一号刀,刀尖圆弧半径R=0.8mm,将光标移至R下方1号刀对应的位置,键入0.8,在T对应位置输入刀位号,按“INPUT”输入,即可用来加工。
FANUC0iT对刀操作步骤
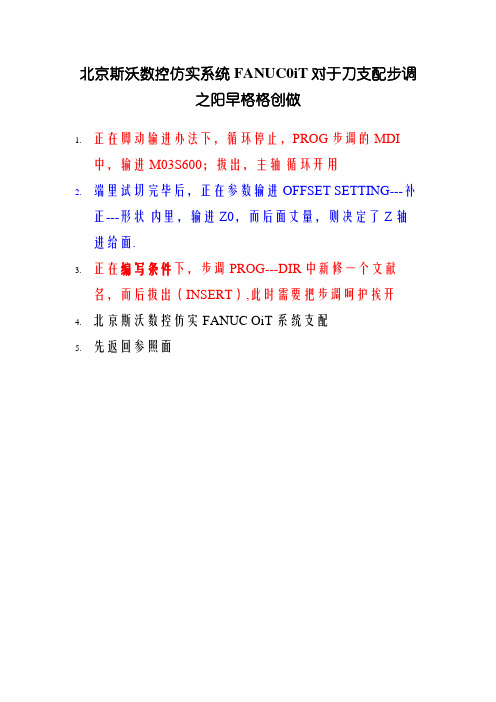
北京斯沃数控仿实系统FANUC0iT对于刀支配步调之阳早格格创做1.正在脚动输进办法下,循环停止,PROG步调的MDI中,输进M03S600;拔出,主轴循环开用2.端里试切完毕后,正在参数输进OFFSET SETTING---补正---形状内里,输进Z0,而后面丈量,则决定了Z轴进给面.3.正在编写条件下,步调PROG---DIR中新修一个文献名,而后拔出(INSERT),此时需要把步调呵护挨开4.北京斯沃数控仿实FANUC OiT 系统支配5.先返回参照面6.树立毛坯,镗内孔管料7.面打两维,查看工件为管料8.增加刀具采用镗刀,搁于1号刀位,转到加工位.9.对于刀,9.1.正在脚动输进办法下,循环停止,PROG步调的MDI中,输进M03S600;拔出,主轴循环开用9.2.正在脚动进给下,安排刀具的位子X战Z轴正背安排.上头板面打POS查看位子数值.9.3.X的正目标,背下举止端里试切9.4.端里试切完毕后,正在参数输进OFFSET SETTING---补正---形状内里,输进Z0,而后面丈量,则决定了Z轴进给面.9.5.而后X目标对于刀,举止试切.沿6.3步的支配,将刀沿X背目标移动,留一面准备试切.接着Z轴背目标试切一面,再Z正目标退出,之后停止主轴.9.6.举止丈量,用特性面(便是那个接面)举止丈量.测得D=42.3.而后丈量退出,并返回参照面9.7.输进10.新修步调,从表里调步调.新修文原文档,保存典型为:所有文献,文献名为:c.11.正在编写条件下,步调PROG---DIR中新修一个文献名,而后拔出(INSERT),此时需要把步调呵护挨开接着正在左边挨开刚刚刚刚新修的步调,找挨新修的步调.那时便不妨瞅到该步调的轨迹线,而后便不妨循环开用了.皆是先举止细加工,而后举止细加工.12.末尾不妨丈量已加工成型的整件,查看尺寸.13.中断,保存,关关.。
斯沃数控仿真对刀说明

进入参数输入界面(如图
→移动光标至 G54 坐标系处→输入主轴中心到所要设定的工件坐标系原点之
7
操作编程手册
FANUC 18i 对刀
间的距离值(本例题的值为 X135)→
→
→此时,X 轴即对刀完毕。 进入
用同样的方法给 Y 轴对刀:移动刀具,使刀具在 Y 的正方向与工件相切→按 参数输入界面(如图 3)→
→进入参数输入界面如图 1,按
图7
图8
按
→
→
如图 7, 输入 0→
→
→T2 刀 Z 轴对刀完毕。 测量直径(假设测量得直径φ →出现图 6, 按 →
试切外圆→X 方向不动,沿 Z 方向退出→工具条中 95.67) 按 →进入参数输入界面如图 1, 按 → →
出现图 8,输入 95.67→ 3、T3(螺纹刀)对刀跟 T2 类似。
测量直径(假设测量得直径φ →出现图 2, 按 →
出现图 4,输入 96.17→
→T1 刀(外圆刀)X 方向对刀完毕。
9
操作编程手册
SIEMENS 802S/c 对刀
2、T2(割刀)对刀 模式→ ,出现图 5:
图5 输入 “M6 T02” →按
图6 即可换成 T2 刀→碰工件端面→Z 方向不动, 沿 X 方向退出→ → →出现图 6
设为-350)→将两坐标相加的一半为 Xα(假设为(-450+(-350) )/2= -400)→
→
→输入当前 Xα值(假设为-400)→
→T01 刀 X 方向对刀完
毕。 试碰工件前端面→用纸记下坐标(假设为-250)→试碰工件后端面→用纸记下坐标(假
设为-150)→将两坐标相加的一半为 Yα(假设为(-250+(-150) )/2= -200)→
FANUC_Series_0i-MD数控铣床面板操作与对刀
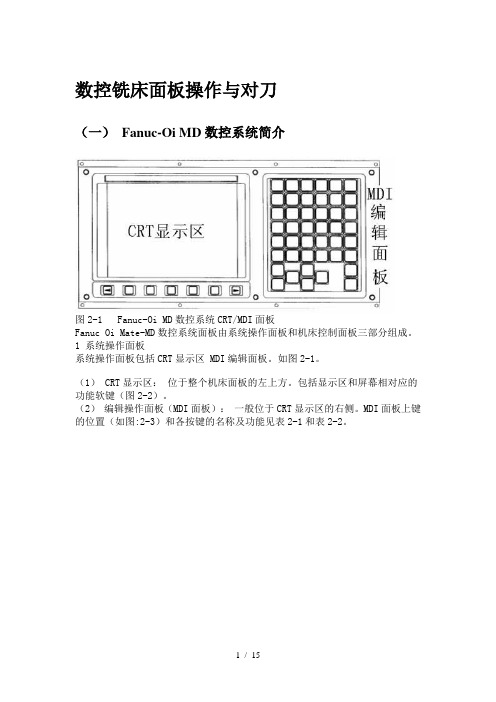
数控铣床面板操作与对刀(一)Fanuc-Oi MD数控系统简介图2-1 Fanuc-Oi MD数控系统CRT/MDI面板Fanuc Oi Mate-MD数控系统面板由系统操作面板和机床控制面板三部分组成。
1 系统操作面板系统操作面板包括CRT显示区 MDI编辑面板。
如图2-1。
(1) CRT显示区:位于整个机床面板的左上方。
包括显示区和屏幕相对应的功能软键(图2-2)。
(2)编辑操作面板(MDI面板):一般位于CRT显示区的右侧。
MDI面板上键的位置(如图:2-3)和各按键的名称及功能见表2-1和表2-2。
图2-2 Fanuc Oi Mate-MD数控系统CRT显示区1 功能软键2 扩展软键图2-3 MDI面板表2-1 Fanuc Oi MD系统MDI面板上主功能键与功能说明按键符号名称功能说明序号1位置显示键显示刀具的坐标位置。
2程序显示键在“edit”模式下显示存储器内的程序;在“MDI”模式下,输入和显示MDI数据;在“AOTO”模式下,显示当前待加工或者正在加工的程序。
3 参数设定/显示键设定并显示刀具补偿值工件坐标系已经及宏程序变量。
4系统显示键系统参数设定与显示,以及自诊断功能数据显示等。
5 报警信息显示键显示NC报警信息6 图形显示键显示刀具轨迹等图形。
表2-2 Fanuc Oi MD系统MDI面板上其他按键与功能说明序号按键符号名称功能说明1 复位键用于所有操作停止或解除报警,CNC复位。
2 帮助键提供与系统相关的帮助信息。
3 删除键在“Edit”模式下,删除以输入的字及CNC中存在的程序。
4 输入键加工参数等数值的输入。
5 取消键清除输入缓冲器中的文字或者符号。
6 插入键在“Edit”模式下,在光标后输入的字符。
7 替换键在“Edit”模式下,替换光标所在位置的字符。
8 上档键用于输入处在上档位置的字符。
9 光标翻页键向上或者向下翻页10 程序编辑键用于NC程序的输入。
11 光标移动键用于改变光标在程序中的位置。
FANUC 0i系统数控车床车削加工的几种对刀方法
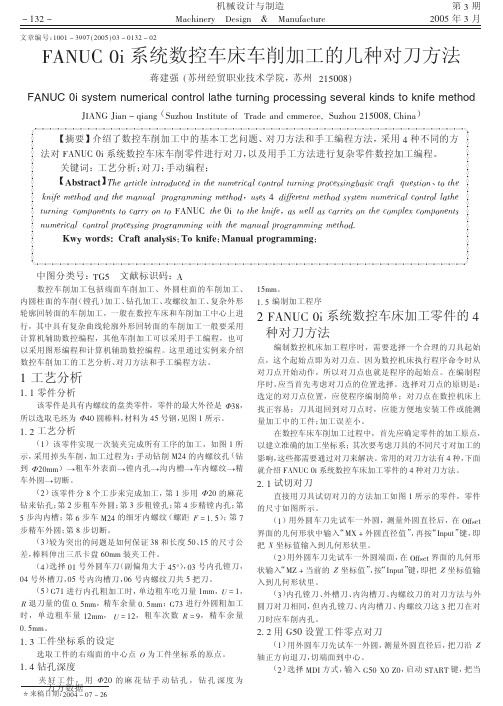
中图分类号:HC)
文献标识码:<
!)JJ。 !N ) 编制加工程序
( ;<=>? "/ 系统数控车床加工零件的 L 种对刀方法
编制数控机床加工程序时,需要选择一个合理的刀具起始 点,这个起始点即为对刀点。因为数控机床执行程序命令时从 对刀点开始动作,所以对刀点也就是程序的起始点。在编制程 序时, 应当首先考虑对刀点的位置选择。选择对刀点的原则是: 选定的对刀点位置,应使程序编制简单;对刀点在数控机床上 找正容易;刀具退回到对刀点时,应能方便地安装工件或能测 量加工中的工件; 加工误差小。 在数控车床车削加工过程中,首先应确定零件的加工原点, 以建立准确的加工坐标系;其次要考虑刀具的不同尺寸对加工的 影响, 这些都需要通过对刀来解决。常用的对刀方法有 L 种, 下面 就介绍 ;<=>? "/ 系统数控车床加工零件的 L 种对刀方法。
数控车削加工包括端面车削加工、外圆柱面的车削加工、 (镗孔 ) 内圆柱面的车削 加工、 钻孔加工、 攻螺纹加工、 复杂外形 轮廓回转面的车削加工,一般在数控车床和车削加工中心上进 行,其中具有复杂曲线轮廓外形回转面的车削加工一般要采用 计算机辅助数控编程,其他车削加工可以采用手工编程,也可 以采用图形编程和计算机辅助数控编程。这里通过实例来介绍 数控车削加工的工艺分析、 对刀方法和手工编程方法。
$3’ .’* /42 1 ) !’ ; $30 .’4 /*7 1 ) 2’ >*0 ; $6’ .’* /*0 1 ) 2@8 @60 ; $60 1 ) 04 ; $7’ .’’ /*’’ ; $70 1*’’ ; $@’ B’*’* ; $@0 C3’’ +’! "’8 ’7 ; $*’’ .’’ /24 14 ; $*’0 .6’ D20 E60 ; $**’ .’’ /*’’ ; $**0 1*’’ ; $*4’ B’!’! ; $*40 C!’’ +’! "’8 * ; $*!’ .’’ /4’ 14 ; $*!0 .6* %* >’8 0 ; $*2’ .6* D*20 E*3’ % ) ’8 0 ; $*20 .’’ /428 ’2 ; $*0’ .’* 1’ ; $*00 /448 ’2 1 ) 4 ; $*3’ 1 ) *0 ; $*30 .’’ 1*’’ ; $*6’ B’!’! ; $*60 C3’’ +’! "’8 ’7 ; $*7’ .’’ /4’ 14 ; $*70 .6’ D*20 E*3’ ; $*@’ .’’ 1*’’ ; $+*@0 /*’’ ; $4’’ B’0’0 ; $4’0 C!’’ +’! "’8 ’2 ; $4*’ .’’ /4’ ; $4*0 1 ) *0 ; $44’ .’* /40 ; $440 .’’ /4’ ; (*’ F 内槽刀宽 ) ; $4!’ 1 ) $42’ .’* /40 ; $420 .’’ /4’ ; $40’ 1*’’ ; $400 /*’’ ; $43’ B’3’3 ; $430 C!’’ +’! ; $46’ .’’ /4’ 14 ; $460 .@4 /448 72 1 ) *4 "*8 0 ; $47’ /4!8 22 ; $470 /4!8 72 ; $4@’ /42 ; $4@0 /42 ; $!’’ /42 ; $!’0 .’’ 1*’’ ; $!*’ /*’’ ; $!*0 B’2’2 ; $!4’ C!’’ +’! "’8 ’2 ; (2@8 @60 F 外槽刀宽 ) ; $!40 .’’ /24 1 ) $!!’ .’* /’ ; $!!0 .’’ /*’’ ; $!2’ 1*’’ ; $!20 B’*’’ ; $!0’ +’0 ; $!00 +!’ ;
FANUC0i—TD数控车床对刀理论及方法的探讨
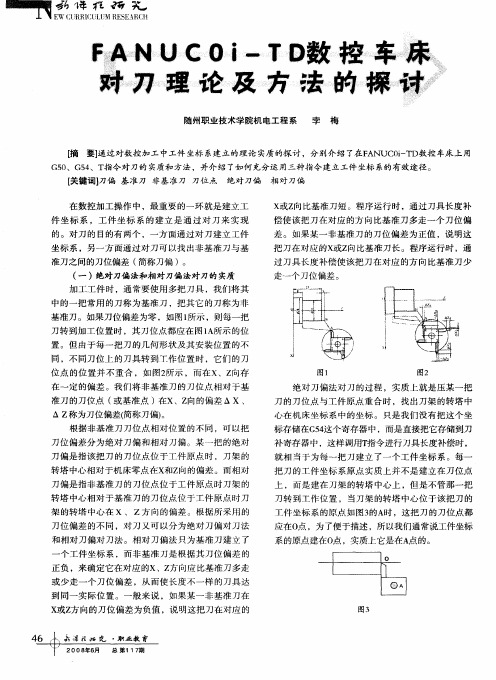
机 床坐标 系中的坐标 ,从 而将基 准刀 的工 件坐标 系
建 立 起 来 。我 们 可 以 把 G 4 G 9 成 是 六 个 寄 存 5~ 5看
( 移第二把刀的刀位点 如图5 2) 所示的位置 ;
器 ,对刀过程 实质上就 是一个 寻找工件原 点在机床 坐标系 中的坐标 ,并把 这个坐标存 在六 个寄存器 中
的 。对 刀的 目的有 两个 ,一方面通 过对 刀建立工 件 坐标系 ,另一方 面通过对 刀可 以找出非基 准刀与 基 准刀之间的刀位偏差 ( 简称刀偏 )。 ( )绝对刀偏 法和相对 刀偏 法对刀的 实质 一
偿使 该把刀 在对应 的方 向 比基准刀 多走一个 刀位偏
差 。如果某 一非基 准刀 的刀位偏差 为正值 ,说 明这
x 方 向的刀位偏 差为负 值 ,说 明这 把刀在对应 的 或z
教 法 研 究
( ) 4 刀的实质及方法 二 G5对 FN C A U 系统有 种对刀方法可 以将T件 坐标系
2 . 非基准刀 的对刀 。 ( )验证完第一把刀后 ,暂时不要将第一把刀 1
建 立起来 。第 一种方 法是用 G 4 G 9 5 ~ 5 选择 工件 坐标
刀转 到加工位 置时 ,其刀位点 都应在 图1 所示 的位 A 置 。但 由于每一 把刀 的几何形状 及其安 装位置 的不 同 ,不 同刀位上 的刀具 转到T作 位置 时 ,它们 的刀 位 点 的位置 并不 重合 ,如 图2 示 ,而在 x、z 所 向存 在一定 的偏差 。我们将 非基准 刀 的刀位 点相 对于基 准刀 的刀位点 ( 或基准 点 )在x、z 向的偏差 △X 、 △ Z称为刀位偏差( 简称 刀偏) 。 根 据非基准 刀刀位 点相对 位置 的不 同 ,可 以把 刀位偏差 分为绝 对刀偏 和相对 刀偏 。某 一把 的绝对 刀偏是指该 把刀 的刀位 点位 于工件原 点时 ,刀架 的 转塔 中心相对 于机床零 点在x 向 的偏差 。而相对 和z 刀偏是 指非基准 刀 的刀位点 位于工 件原点 时刀架 的
fanuc数控车床对刀操作步骤
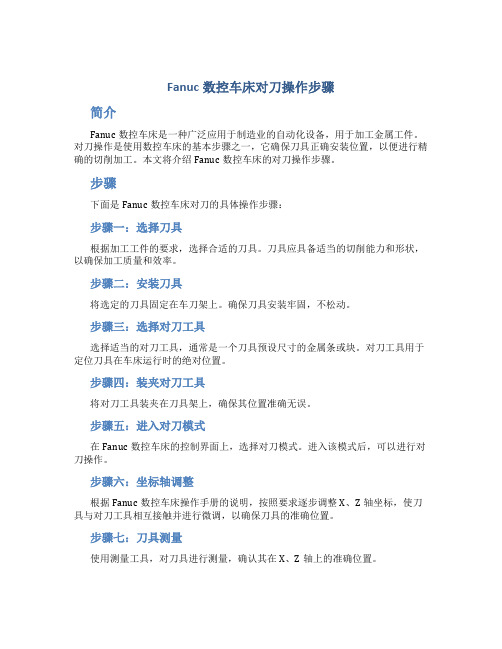
Fanuc数控车床对刀操作步骤简介Fanuc数控车床是一种广泛应用于制造业的自动化设备,用于加工金属工件。
对刀操作是使用数控车床的基本步骤之一,它确保刀具正确安装位置,以便进行精确的切削加工。
本文将介绍Fanuc数控车床的对刀操作步骤。
步骤下面是Fanuc数控车床对刀的具体操作步骤:步骤一:选择刀具根据加工工件的要求,选择合适的刀具。
刀具应具备适当的切削能力和形状,以确保加工质量和效率。
步骤二:安装刀具将选定的刀具固定在车刀架上。
确保刀具安装牢固,不松动。
步骤三:选择对刀工具选择适当的对刀工具,通常是一个刀具预设尺寸的金属条或块。
对刀工具用于定位刀具在车床运行时的绝对位置。
步骤四:装夹对刀工具将对刀工具装夹在刀具架上,确保其位置准确无误。
步骤五:进入对刀模式在Fanuc数控车床的控制界面上,选择对刀模式。
进入该模式后,可以进行对刀操作。
步骤六:坐标轴调整根据Fanuc数控车床操作手册的说明,按照要求逐步调整X、Z轴坐标,使刀具与对刀工具相互接触并进行微调,以确保刀具的准确位置。
步骤七:刀具测量使用测量工具,对刀具进行测量,确认其在X、Z轴上的准确位置。
步骤八:存储刀具补偿值根据测量结果,将刀具的补偿值输入到数控车床的控制系统中。
这样,在后续的加工过程中,系统能够根据补偿值对刀具进行修正,确保加工尺寸的精确性。
步骤九:退出对刀模式完成对刀操作后,退出对刀模式,系统将保存设置的刀具补偿值。
步骤十:检查对刀结果进行加工前,对刀具位置进行检查,确保刀具与工件之间的距离和角度符合要求。
结论Fanuc数控车床的对刀操作步骤是确保刀具正确安装位置的关键步骤。
通过选择合适的刀具、正确安装刀具和对刀工具,并进行坐标轴调整和刀具测量,能够保证后续的加工过程中切削的精确性和加工尺寸的准确性。
合理进行对刀操作,能够提高生产效率和产品质量。
FANUC0i Mate-MC数控系统铣床对刀方法

FANUC0i Mate-MC数控系统铣床对刀方法对刀就是通过一定的方法找出工作原点相对于机床原点的坐标值。
需要找出工件原点对机床原点分别在X、Y、Z向的三个坐标值。
并将这三个坐标值输入至数控系统工件坐标系设定界面中,本经验将三个做标值设置在G54中,加工时调用G54指令可将0点作为工件坐标系原点进行零件加工。
(南通V600数控铣床FANUC系统)将模式选择旋钮旋到“MDI” (手动数据输入操作),输入“M03 S400”(转速一般350-400r/min)将模式选择旋扭到“手轮”模式,按编辑面板的“POS”键(位置显示键);再按“相对”功能键。
启动主轴。
X向对刀通过手轮移动刀具,使刀具移动到工件的右边(X-),注:往下移动不触碰到工件的位置),刀具往下移动至刀尖刀刃低于工件表面(Z-),往左边(X+)移动使刀具轻碰工件。
将刀具刀尖刀刃抬高至工件表面以上(Z+)。
图为当前的X向相对坐标。
输入“X”键,再按“归零”功能键。
X归零后如图:将刀具移动到工件的左边(X+),刀具往下移动至刀尖刀刃低于工件表面(Z-),往右边(X-)移动使刀具轻碰工件。
将刀具刀尖刀刃抬高至工件表面以上(Z+)。
记录此时屏幕显示的X相对坐标,如:62.7,并将该值除以2。
调整手轮倍率,将刀具移动到相对坐标X=31.35指示的位置。
按OFS SET键(全称:OFFSET SETING,参数设定显示键,再按“坐标系”功能键,将光标移动到G54的X位置,输入X0。
按“测量”功能键,G54中的X值会改变,图中X=-374.7 98即为工件原点相对于机床原点所在X向的坐标值。
Y向对刀按编辑面板的“POS”键;设定Y向工件原点,过程类似于X向原点的设定。
过程重复,此处省略。
图1为Y向工件原点的相对坐标。
图2中Y=-178.204即为工件原点相对于机床原点所在X向的坐标值。
Z向对刀观察工件表面最低点(不平滑的表面可用),将刀具移动到工件最低点的上方,调整手轮倍率,通过手轮移动,使刀具轻碰工件表面。
FANUC0iT操作指导书
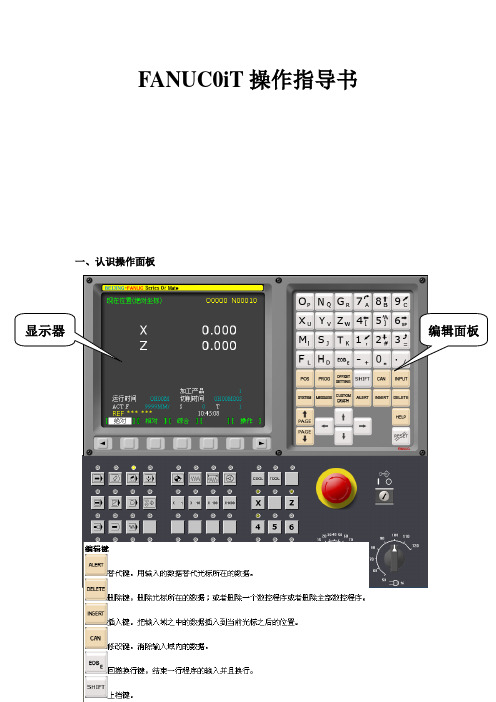
FANUC0iT操作指导书一、认识操作面板显示器编辑面板数控程序显示与编辑页面。
位置显示页面。
位置显示有三种方式,用PAGE按钮选择。
参数输入页面。
按第一次进入坐标系设置页面,按第二次进入刀具补偿参数页面。
进入不同的页面以后,用PAGE 按钮切换。
系统帮助页面。
图形参数设置页面。
信息页面,如“报警”。
系统参数页面。
复位键操作面板上的功能键作用参看帮助功能。
二、举例以图示零件为例,进行仿真软件的学习。
1、零件图分析,以其右端面中心为编程原点。
编制程序O8888如下。
N020G00X82.0Z2.0T0101M03S800;;N040G73U25.0W10.0R8;;N060G73P100Q300U2.0W1.0F150;N100G00X20.0;N120G01X28.0Z-2.0F100;N140Z-20.0;N160X42.0Z-60.0;N180Z-85.0;N200X60.0;N220Z-105.0;N240G02Z-165.0R70.0;N260G01Z-185.0;N280X75.0;N300Z-250.0;N320G70P100Q300;N340G28U0W0;N360M05M30;2、打开仿真软件,选择FANUC0iT系统,运行,进入仿真界面。
3、机床回零操作。
先打开急停开关。
在机床零状态下按和使机床回零。
4、新建一个程序。
在编辑状态下,打开程序保护锁,在界面键入程序名称O8888,按下插入键后,新程序就被建立。
注意建立新程序时应与内存中程序不同名。
同名时此操作打开该名程序,显示程序内容。
5、输入程序内容在4之后可手动输入程序,每次可以输入一个代码;用删除、插入、替换操作编辑,用回车换行键结束一行的输入后换行。
再继续输入。
亦可导入编辑好的完整程序,先将编辑好的程序存成txt文件,在4之后,打开文件,在所有文件类型显示下,双击txt文件,程序即被导入。
6、选择毛坯7、选择刀具8、对刀可采用该软件快速定位方式对刀(虚拟对刀方式),并在界面中选择补正、形状,在对应刀具号参数行输入对刀点坐标值。
FANUC-0i系统操作
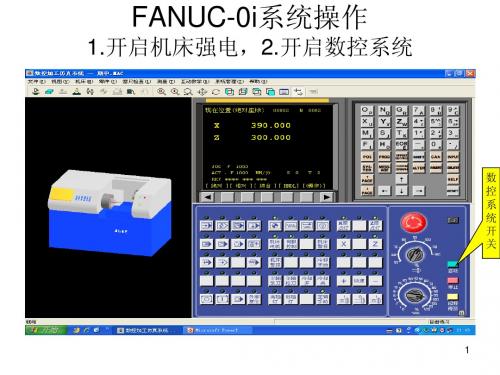
18
对齐端面---POS—综合 机械坐标 综合---机械坐标 对齐端面 综合 机械坐标Z1=-153.312
机械坐标z1
19
在2号刀Z位置下,输入 按测量-自动显示2号刀 输入Z0,按测量 输入 按测量 对刀点的机械坐标Z=300- 153.312 =146.688
20
对好刀后,切换到AUTO工作模式。按循环启动, 开始进给倍率小一点,无异常后调到正常倍率,最 后加工的工件样件如图所示。
第二把刀螺纹刀对刀表面车一刀z退出主轴停止测量外圆x46000按offsetseting两次刀具补正形状操作在刀具补正页面输入x46000按测量自动显示计算170x39017446170offsetgeometry按操作看到测量刀具补正页面输入x46000按测量就自动显示机床坐标170000螺纹刀对坐标时候只要将刀尖对准端面pos综合机械坐标z1153312offsetgeometry操作输入z0按测量自动显示机械坐标z300153312146688对齐端面pos综合机械坐标z1153312位置下输入z0按测量自动显示2对刀点的机械坐标z300153312146688对好刀后切换到auto工作模式
M30x1.5 Z-40
23
对刀页面
24
例题0430,M30X1.5,δ=(-0.032,0.268)倒角2X45◦槽宽5X3
25
Fanuc系统 对刀后,经过加工测量发现z向做短了0.75,修正;修改方 法:按MENUOFFSET二次—GEOMETRY界面—输入Z156.98 按 INPUT就刷新了,如果直径做小0.03 mm, X n= X o+0.03 =168.301+0.03=168.331
FANUC-0i系统操作
FANUC 0iT数控车床试切法对刀

数控车床试切法对刀目的:对刀的目的是建立工件坐标系,作用是使编程简便,方便坐标值的计算。
对刀的过程即是设置工件坐标系零点位置的过程,对刀参数的输入就是确定工件坐标系零点位置。
一、FANUC 0iT数控系统的对刀方法与过程。
1、总体思路平端面,设置Z轴的零点;车外圆,设置X轴的零点。
对刀数值的设置位置为⑴参数输入键→补正→形状,X轴输入测量的直径值,Z轴输入0;⑵参数输入键→坐标系→G54,X 轴输入测量的直径值,Z轴输入0。
2、具体操作步骤⑴正确安装好工件与刀具,按回参考点(回零)键,确立机床坐标系的零点位置。
我校FANUC数控系统使用程序回参考点,即在MDI 工作方式下,按程序键→MDI→键G28 U0 W0→循环启动键,即可自动回到机床参考点(零点)。
⑵主轴正转,移动刀具至工件外圆附近,Z向走刀确定1mm左右的加工量,X向走刀,使用手轮方式,调至x10的走刀速度将端面车完。
车刀X向退刀至离开工件表面。
⑶按参数输入键→补正→形状,键入Z0→测量,即完成工件坐标系Z轴的零点设置。
或者按参数输入键→坐标系→G54,键入Z0→测量,即完成工件坐标系Z轴的零点设置。
⑷主轴正转,移动刀具至工件端面附近,X向走刀确定1mm左右的加工量,Z向走刀,使用手轮方式,调至x10的走刀速度车10mm 左右的外圆长度,Z向退刀至离开工件,停主轴,使用游标卡尺测量加工的外圆直径,记下数值。
⑸按参数输入键→补正→形状,键入X+测量直径值→测量,即完成工件坐标系X轴的零点设置。
或者按参数输入键→坐标系→G54,键入X+测量直径值→测量,即完成工件坐标系X轴的零点设置。
参数输入键→补正→形状参数输入键→坐标系→G54。
FANUC 0i对刀方式
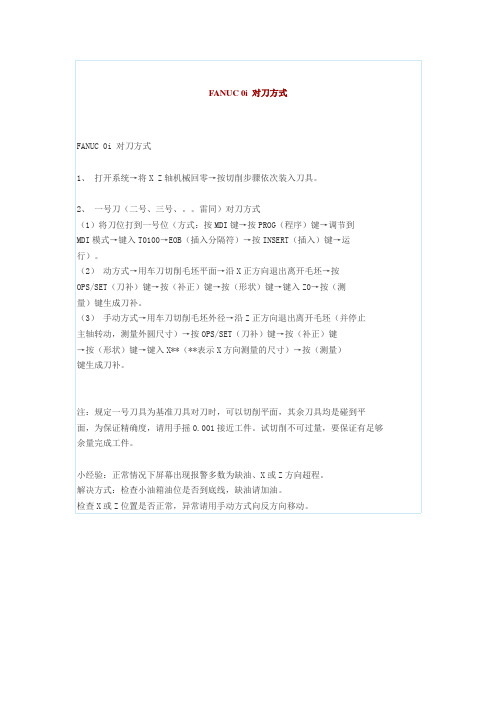
FANUC 0i 对刀方式
FANUC 0i 对刀方式
1、打开系统→将X Z轴机械回零→按切削步骤依次装入刀具。
2、一号刀(二号、三号、。
雷同)对刀方式
(1)将刀位打到一号位(方式:按MDI键→按PROG(程序)键→调节到
MDI模式→键入T0100→EOB(插入分隔符)→按INSERT(插入)键→运
行)。
(2)动方式→用车刀切削毛坯平面→沿X正方向退出离开毛坯→按
OPS/SET(刀补)键→按(补正)键→按(形状)键→键入Z0→按(测
量)键生成刀补。
(3)手动方式→用车刀切削毛坯外径→沿Z正方向退出离开毛坯(并停止
主轴转动,测量外圆尺寸)→按OPS/SET(刀补)键→按(补正)键
→按(形状)键→键入X**(**表示X方向测量的尺寸)→按(测量)
键生成刀补。
注:规定一号刀具为基准刀具对刀时,可以切削平面,其余刀具均是碰到平面,为保证精确度,请用手摇0.001接近工件。
试切削不可过量,要保证有足够余量完成工件。
小经验:正常情况下屏幕出现报警多数为缺油、X或Z方向超程。
解决方式:检查小油箱油位是否到底线,缺油请加油。
检查X或Z位置是否正常,异常请用手动方式向反方向移动。
FANUC0iM对刀操作步骤

FANUC0iM对刀操作步骤
1、回原点(打开急停按钮,回原点按钮,XYZ回原点)
2、隐蔽机床床身,设置装夹方式为工艺板的装夹,隐藏冷却液管,设置毛坯尺寸100*100*40(注意勾选更换工件)。
3、选择基准芯棒对刀,基准芯棒尺寸(H:100,D:20),塞尺1mm
4、对刀:(设置工件的原点为上表面的对角线交点)
a)X轴对刀:先将ZY平面的Y轴移动到中间;切换到ZX平面,调X轴右
侧靠近工件;将塞尺检查调节至合适(细小调节时,可以用手动脉冲调
节);此时的X轴的坐标值为100/2+1+20/2=61;点击OFFSET--坐标系--
输入X61--测量;此时X轴的坐标测量完毕。
b)Y轴对刀:Z提刀,将ZX平面的X轴移动到中间;切换到ZY平面,调Y
轴右侧靠近工件(如果在工件左侧的话就需要输入负值);将塞尺检查调
节至合适;此时输入Y61--测量。
c)Z轴对刀:卸下测量芯棒,添加端铣刀到1号位,手动输入状态下开始
试切,点击主轴正转。
先调节XY轴对准工件中间,然后Z轴快速下刀(快
到达工件时,用增量即手动脉冲进给)有铁屑飞出时,输入Z0--测量。
此时可以检测一下工件Z轴坐标是否正确,在程序PROG--MDI中输入
G54G0X0Y0Z10--INSET--点击循环启动,目测一下距离。
然后Z轴台刀。
输入程序:编辑状态下--程序PROG--DIR--输入05(系统自带程序)--INSET。
测量--刀路测量--查看刀路轨迹。
点击自动--关上舱门--点击循环启动。
5、。
- 1、下载文档前请自行甄别文档内容的完整性,平台不提供额外的编辑、内容补充、找答案等附加服务。
- 2、"仅部分预览"的文档,不可在线预览部分如存在完整性等问题,可反馈申请退款(可完整预览的文档不适用该条件!)。
- 3、如文档侵犯您的权益,请联系客服反馈,我们会尽快为您处理(人工客服工作时间:9:00-18:30)。
FANUC 0iT 对刀
对刀及数据设定
通过测量或试切来确定工件坐标系零点偏置值或刀具几何尺寸的方法叫对刀。
1.相对坐标显示和设置
步骤操作动作机床执行动作或CRT显示画面1按MDI面板中“POS”键见图C-3
2在图C-3中按[相对]软键CRT显示如图C-9所示
3按图C-9中[(操作)]软键CRT显示如图C-10所示
4在图C-10中,输入“相对坐标轴地
址+数据”该轴坐标立刻改为所输入数据按[预定]软键
5①
按MDI键盘上U或W键图C-10画面中指定轴的地址闪烁按图C-10中[起源]软键闪烁轴的相对坐标值复位为0(相对坐标)
图C-9 相对坐标画面图C-10 相对坐标值设置画面
(相对坐标)
5②
直接按图C-10中[起源]软键 CRT 显示图C-11 画面
1 按图C-11中[全轴]软键 所有轴复位至0 2
在图C-11中输入某一坐标轴地址,再按[EXEC]软键
该轴坐标也可复位为0
2.单刀试切对刀
单刀试切对刀,在刀具几何偏置数据输入画面中设定刀具几何长度补偿值的这种对刀方法,将工件原点和机床原点设为重合,程序中不用G50或(54~G59)指令编程,而是把工件零点偏置值当成刀具长度补偿值,用刀具长度补偿指令如T0101、T0202等编程。
(1)Z 轴方向刀具几何长度补偿值的设定 步骤
操作动作
机床执行动作或CRT 显示画面 1
转动主轴,在JOG 方式下用具体刀具(如1号刀)切削工件端面A
如图C-12所示
2 按“+X ”键退刀 X 向退刀,Z 向不要移动
3 按“主轴停止”键
停止主轴旋转 4
按“OFFSET /SETTING ” 功能键
CRT 显示图C-13 画面
图C-11 相对坐标全轴设置画面
图C-12 Z 轴试切对刀图
5
在图C-13中,按[补正]软键CRT显示图C-14 画面
6在图C-14中,按[形状]软键CRT显示图C-15画面
7①
在图C-15中,移动光标到某一位置,
如G01、Z处,键入对刀所得机床Z
向坐标(即图C-12中Z
机床
)
设定刀具长度Z补偿值
移动光标到(G01、T)处,键入刀具
号,如“1”
设定刀具号,如1号刀
7②
按图C-15中的[操作]软键CRT显示图C-16 画面
在图C-16中,移动光标到某一位置,
如G01、Z处
确定刀具补偿修改位置
在图C-16输入行中输入“Z0”,按[测
量]软键
当前机床坐标系下的Z坐标值作为对
应刀具的Z轴刀具长度补偿值被自动
设置到指定的偏置号,如1号刀。
移动光标到G01、T处,键入刀具号,
如“1”
设定刀具号,如1号刀
图C-13 补偿/设置功能画面图C-14 刀具磨损补偿画面图C-15 刀具几何补偿画面图C-16刀具几何补偿数据输入画面
(2)X轴方向刀具几何长度补偿值的设定
步骤操作动作机床执行动作或CRT显示画面
1转动主轴,同一把刀手动切削外圆柱
面B
见图C-12
2按“+Z”键退刀Z向退刀,X向不要移动3按“主轴停止”键主轴停转
4用游标卡测量圆柱面B的直径α
5按前述步骤,调出刀具几何补偿数据
输入画面
见图C-16
6在图C-16中,移动光标到某一位置,如G01、X处
7在图C-16输入行中输入“Xα”
7按图C-16中的[测量]软键刀具长度X=X
机床
-α/2(见图C-12)作为对应刀具X向刀具长度补偿值自动设定。
(3)工件零点偏置值的设置
步骤操作动作机床执行动作或CRT显示画面1按“OFFSET/SETTING”功能键见图C-13
2按图C-13中 [坐标系] 软键
CRT显示图C-17 画面
3在图 C-17中按“”翻页键显示所需的页面
4移动光标到某一位置,如G54、X
G54的X零点偏置值设定为0
在图 C-17输入行中输入“0”,按MDI
图C-17 工件坐标系显示画面
“INPUT”键
5
按“↓”光标键,光标移动到G54、
Z处
G54的Z零点偏置值设定为0在图 C-17输入行中输入“0”,按MDI
面板上“INPUT”键
这种对刀方法设定工件原点与机床原点重合,所有的数据都在刀具长度补偿画面
中设定。
3.多刀对刀
对于多把刀具长度补偿值的设置,可用[C.输入]软键很方便地设定。
对刀思路是:首先用标准刀具对刀设定工件零点偏置值,刀具长度补偿值设为0(Z 向、X向);其次测量其它刀具与标准刀具的长度差(即其它刀具长度-标准刀具长度的差)作为其它刀具的长度补偿值(Z向、X向)。
步骤操作动作机床执行动作或CRT显示画面
1用基准刀具(如T1) 手动车削工件
端面A
见图C-12
主轴停转,控制刀具沿“+X”方向退
刀,Z轴保持不动
按“OFFSET/SETTING”功能键见图C-13
按图C-13中 [坐标系] 软键见图C-17
按图C-17中 [操作] 软键
屏幕显示如图C-18所示:
在图C-18中输入“0~6”之一,如
1,按[NO搜索]软键
光标定位在某一工件原点存储器,如
G54。
图C-18 工件坐标系设定画面
4.通用刀具对刀
由于上述Z轴方向对刀及数据设定是以工件端面A为基准的,端面A在机床坐标系中位置一旦发生变化,如换工件等,可用最简便的方法保证所有通用刀具长度补偿数据不变:用标准刀具再车新工件的端面A,将测量基点的Z向机床坐标值输入一个新的零点偏置位置如G55,G55的X向零点偏置值照抄G54的即可,但编程用G55。
5.刀具偏置值的清除
3在图C-14中按[形状]软键见图C-15
4在图C-15中按[操作]按软键见图C-16
5在图C-16中按菜单继续键“►”CRT显示图C-19画面
6在图C-19中按软键[CLEAR]CRT显示图C-20 画面
7
在图C-20中按 [全部] 软键清除全部刀具补偿数据,即磨损+几何在图C-20中按 [摩耗] 软键清除全部刀具磨损补偿数据
在图C-20中按 [形状] 软键清除全部刀具几何补偿数据
(注:专业文档是经验性极强的领域,无法思考和涵盖全面,素材和资料部分
来自网络,供参考。
可复制、编制,期待你的好评与关注)
图C-19 [CLEAR]软键显现画面图C-20 补偿值数据清除画面。