浅谈机床类灰铸铁件化学成分的选择
灰球铸铁铸件检验标准完成

液压铸铁铸件检验标准范围本标准规定了用灰铸铁和球墨铸铁铸造的液压铸铁件的技术要求和验收规范。
本标准适用于液压泵、液压马达、液压缸和液压阀等液压元件的铸造承压壳体或结构件的铸件。
本标准使用于砂型或导热性与砂型相当的铸型中铸造的灰铸铁件,使用其他铸型铸造的灰铸铁件也可以参考使用。
术语和定义GB/T 5611确立的术语以及下列术语和定义适用于本标准。
1)铸件的主要壁厚 relevant wall thickness铸件的主要壁厚是指用以确定铸件材料力学性能的铸件断面厚度,由供需双方商定。
2)石墨球化处理 graphite spheroidizing treatment在铁液中加入球化剂,使铁液凝固过程析出的碳形成以球状石墨形态为主的工艺过程。
灰球铸铁件3.1 灰铸铁件3.1.1 灰铸铁牌号本标准的材料牌号表示方法,符合GB/T 5612的规定。
本标准中,单铸试棒是以直径Φ30mm的单铸试棒加工的标准试样所测得的最小抗拉强度。
附铸试棒(块)是根据铸件的实际壁厚,选择相应的截面尺寸与铸件一同冷却的附铸试棒(块)加工的标准拉伸试样。
本体试样为取自铸件本体材料制成的标准拉伸试样。
标准拉伸试样的形状和尺寸应按GB/T 9439-2010的规定。
本公司常用的HT200、HT250、HT300及HT350灰铸铁件的力学性能及金相组织见表1。
3.1.2 灰铸铁件的化学成分若需方的技术条件中包含化学成分的验收要求时,按需方规定执行。
若需方对化学成分没有要求时,化学成分由供方自行确定,化学成分不作为铸件的验收依据。
但化学成分的选取必须保证铸件材料满足本标准所规定的力学性能和金相组织的要求。
化学成分的检测频次和数量,供需双方商定或由供方自行确定。
3.1.3 灰铸铁的力学性能在单铸试棒上还是在铸件本体或附铸试棒上测定力学性能,以抗拉强度还是以硬度作为性能验收指标,均必须在订货协议或需方技术要求中明确规定。
铸件的力学性能验收指标应在订货协议中明确规定。
铸铁化学成分

铸铁化学成分
铸铁是一种重要的材料,在工业生产中有着广泛的应用。
其主要成分包括铁、碳、硅、锰、硫等元素,其中碳含量较高,可达2%以上。
根据碳的含量和形态,铸铁分为灰铸铁、球墨铸铁和白口铸铁等不同种类。
灰铸铁中的碳主要以石墨形式存在,因此具有良好的润滑性和耐磨性,适用于制造摩擦零件和机械零件。
球墨铸铁中的碳则以球状石墨存在,具有较高的强度和韧性,适用于制造高强度和高韧性的零件。
白口铸铁中的碳则以铁碳化合物形式存在,硬度较高,适用于制造切削工具等。
硅是铸铁中的另一个重要元素,它可以提高铸铁的流动性和凝固性,同时也可以增加铸铁的耐腐蚀性和抗疲劳性。
锰可以提高铸铁的硬度和韧性,同时也可以降低铸铁的脆性和热裂纹倾向性。
硫的含量对铸铁的性能影响较大,过高的硫含量会导致铸铁脆性增加,而过低的硫含量则会影响铸铁的流动性和凝固性。
总之,铸铁化学成分的合理控制可以有效地提高铸铁的性能和使用寿命,从而更好地满足工业生产的需求。
- 1 -。
铸铁 球墨铸铁

铸铁球墨铸铁
铸铁和球墨铸铁是两种常见的金属材质,主要用于制造各种机械设备和结构件。
它们之间的重要区别在于它们的化学成分和制造工艺。
铸铁是一种普通的灰铸铁,它的含碳量较高,一般在 2.0% 以上,通过铸造工艺制成。
由于铸铁的石墨化较好,具有良好的耐蚀性和耐磨性,因此被广泛用于制造各种机床床身、桥梁、汽车发动机外壳、机器外壳等。
但是,铸铁的机械性能较差,硬度低,易于变形,因此常用于制造要求不高的零件。
球墨铸铁是通过在铸造过程中添加球状石墨元素制成的。
这种材料的含碳量与铸铁相似,但在铸造过程中通过孕育处理,使得石墨球化,提高了材料的硬度和强度。
球墨铸铁具有良好的机械性能和耐磨性,通常用于制造要求较高的机器结构件,如汽车发动机缸体、机器轴等。
总的来说,铸铁和球墨铸铁具有不同的化学成分和制造工艺,适用于不同的制造需求。
灰铸铁中各元素作用
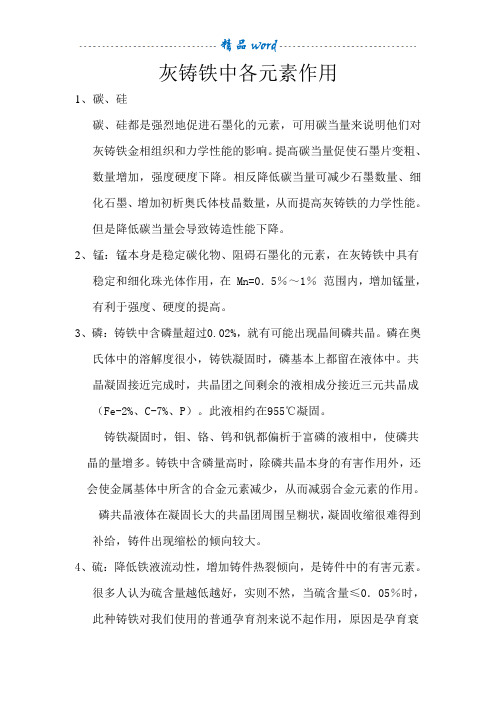
灰铸铁中各元素作用1、碳、硅碳、硅都是强烈地促进石墨化的元素,可用碳当量来说明他们对灰铸铁金相组织和力学性能的影响。
提高碳当量促使石墨片变粗、数量增加,强度硬度下降。
相反降低碳当量可减少石墨数量、细化石墨、增加初析奥氏体枝晶数量,从而提高灰铸铁的力学性能。
但是降低碳当量会导致铸造性能下降。
2、锰:锰本身是稳定碳化物、阻碍石墨化的元素,在灰铸铁中具有稳定和细化珠光体作用,在 Mn=0.5%~1%范围内,增加锰量,有利于强度、硬度的提高。
3、磷:铸铁中含磷量超过0.02%,就有可能出现晶间磷共晶。
磷在奥氏体中的溶解度很小,铸铁凝固时,磷基本上都留在液体中。
共晶凝固接近完成时,共晶团之间剩余的液相成分接近三元共晶成(Fe-2%、C-7%、P)。
此液相约在955℃凝固。
铸铁凝固时,钼、铬、钨和钒都偏析于富磷的液相中,使磷共晶的量增多。
铸铁中含磷量高时,除磷共晶本身的有害作用外,还会使金属基体中所含的合金元素减少,从而减弱合金元素的作用。
磷共晶液体在凝固长大的共晶团周围呈糊状,凝固收缩很难得到补给,铸件出现缩松的倾向较大。
4、硫:降低铁液流动性,增加铸件热裂倾向,是铸件中的有害元素。
很多人认为硫含量越低越好,实则不然,当硫含量≤0.05%时,此种铸铁对我们使用的普通孕育剂来说不起作用,原因是孕育衰退的很快,常常在铸件中产生白口。
5、铜:铜是生产灰铸铁最常加入的合金元素,主要原因是由于铜熔点低(1083℃),易熔解,合金化效果好,铜的石墨化能力约为硅的1/5,因此能降低铸铁的白口倾向,同时铜也能降低奥氏体转变的临界温度,因此铜能促进珠光体的形成,增加珠光体的含量,同时能细化珠光体和强化珠光体及其中的铁素体,因而增加铸铁的硬度及强度。
但是并非铜量越高越好,铜的适宜加入量为0.2%~0.4%当大量地加铜时,同时又加入锡和铬的做法对切削性能是有害的,它会促使基体组织中产生大量的索氏体组织。
6、铬:铬的合金化效果是非常强烈的,主要是因为加铬使铁水白口倾向增大,铸件易收缩,产生废品。
灰铸铁200化学成分
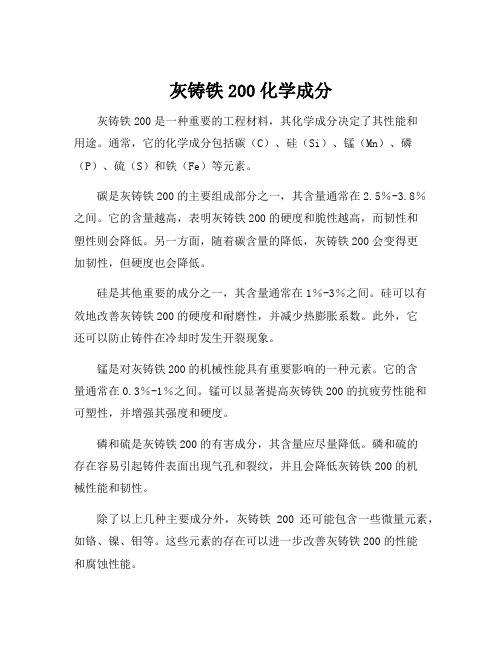
灰铸铁200化学成分灰铸铁200是一种重要的工程材料,其化学成分决定了其性能和用途。
通常,它的化学成分包括碳(C)、硅(Si)、锰(Mn)、磷(P)、硫(S)和铁(Fe)等元素。
碳是灰铸铁200的主要组成部分之一,其含量通常在2.5%-3.8%之间。
它的含量越高,表明灰铸铁200的硬度和脆性越高,而韧性和塑性则会降低。
另一方面,随着碳含量的降低,灰铸铁200会变得更加韧性,但硬度也会降低。
硅是其他重要的成分之一,其含量通常在1%-3%之间。
硅可以有效地改善灰铸铁200的硬度和耐磨性,并减少热膨胀系数。
此外,它还可以防止铸件在冷却时发生开裂现象。
锰是对灰铸铁200的机械性能具有重要影响的一种元素。
它的含量通常在0.3%-1%之间。
锰可以显著提高灰铸铁200的抗疲劳性能和可塑性,并增强其强度和硬度。
磷和硫是灰铸铁200的有害成分,其含量应尽量降低。
磷和硫的存在容易引起铸件表面出现气孔和裂纹,并且会降低灰铸铁200的机械性能和韧性。
除了以上几种主要成分外,灰铸铁200还可能包含一些微量元素,如铬、镍、钼等。
这些元素的存在可以进一步改善灰铸铁200的性能和腐蚀性能。
在生产灰铸铁200时,合理的化学成分控制非常重要。
无论是选择原材料,还是设计铸造工艺,都需要有针对性地控制化学成分,以保证其性能和质量。
此外,在使用灰铸铁200的过程中,也需要根据其化学成分和特性,采用合适的加工方法和工艺,以避免出现问题。
总之,灰铸铁200的化学成分对于其性能和用途具有重要意义。
对于生产者和使用者来说,了解灰铸铁200的化学成分和特性,将有助于提高其质量和性能,实现更加优质的制造和应用。
铸铁件配料方法

铸铁件配料方法,及锰铁铬铁加入量配比HT250是珠光体灰铸铁。
化学成分:碳C :3.16~3.30硅Si:1.79~1.93锰Mn:0.89~1.04硫S :0.094~0.125磷P :0.120~0.170根据化学成分考虑原料的成分及烧损就可以知道配料了影响铸铁、铸钢件组织和性能的因素,有化学成分、孕育(变质)处理、冷却速度、炉料的“遗传性”、铁水过热温度等,在这几个因素中,化学成分含量的高低对铸件物理性能的影响相对更大些,而且是第一因素。
所以在生产过程中,根据铸件物理性能的要求,正确的配料或调料,严格控制材质的各化学成分含量尤为重要。
在生产实践中,作为冶炼技术人员和炉工来说,配料和调料应该是熟练掌握的一般性技术问题。
但是对予刚毕业的学生和大多数炉工来说,欲能系统、灵活的掌握,也确非易事。
要想控制铸件的化学成分与配料,必须事先了解以下几下问题:1、铸件的目标化学成分。
2、库存各种金属炉料的化学成分。
3、各种炉料在冶炼过程中化学成分的增减变化率。
4、配料方法。
一、目标化学成分现在大部分铸件,根据其牌号要求的不同,国标中已做出了相应的要求,从铸造手册中即可查到。
但是随着科技的进步,根据铸件的服役状况,市场需要更多物理性能各不相同的铸件,并对铸件的综合性能质量提出了更高的要求,科研单位也不断研究出新材质而取代旧材质,例如某水泥研究设计院研究的“中碳多元合金钢”,成功的代替了原需进口的球磨机衬板,代替了高锰钢,用该材质生产直径φ2.4甚至直径φ4.2的中大型球磨机衬板上,降低了生产成本,取得了良好的经济效益。
另外,如某厂生产出口国外石油钻井用的泥浆泵高铬双金属缸套及采石场600×900破碎机用的锤头,都是超高铬铸铁,这些材质的详细化学成分要求,在铸造手册中是查不到的。
在接受生产绪如上述产品时,如果自己没有完全掌握铸件化学成分要求,以及没有详细了解铸件的服役状况时,应让用户提供尽可能详细的化学成分要求范围及热处理工艺。
铸件化学成分

一.一般工程用碳素钢铸件(EQY-18-2000):
二.焊接结构用碳素钢铸件(GB/T7659-1987) :
三.优质碳素结构钢(GB/T 699-1999) :
四.球墨铸铁铸件(GB/T 1348-1988)
五.灰铸铁件(GB/T 9439-1988) :
1 .化学成分:%
2. 力学性能:详见副页
材料名称:优质碳素结构钢
牌号:08Al
标准:GB/T 5213-1985
●特性及适用范围:
是AL脱氧的优质碳素结构钢,为厚度0.8~3.0mm深冲压用的低碳冷轧薄钢板。
与普通冷轧薄钢板相比,具有更好的综合力学性能和成形性能。
广泛用于各种车辆中形状复杂的深冲压零件。
如汽车、拖拉机的车身、驾驶室、发动机外壳等不承受载荷的各种冲压零件。
●化学成份:
碳C :≤0.08
硅Si:痕迹
锰Mn:0.30~0.45
硫S :≤0.030
磷P :≤0.020
●力学性能:
抗拉强度σb (MPa):255~324
屈服强度σs (MPa):≤196
伸长率δ5 (%):≥44
硬度:≤44HB
试样尺寸:试样。
灰铸铁件技术要求-
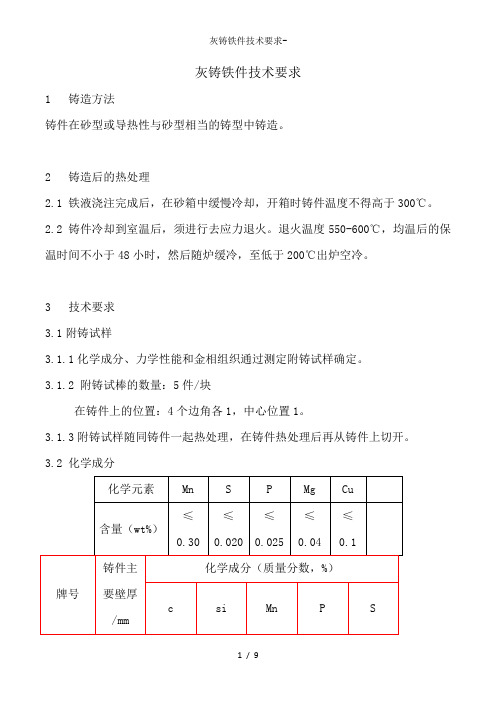
灰铸铁件技术要求1 铸造方法铸件在砂型或导热性与砂型相当的铸型中铸造。
2 铸造后的热处理2.1 铁液浇注完成后,在砂箱中缓慢冷却,开箱时铸件温度不得高于300℃。
2.2 铸件冷却到室温后,须进行去应力退火。
退火温度550-600℃,均温后的保温时间不小于48小时,然后随炉缓冷,至低于200℃出炉空冷。
3 技术要求3.1附铸试样3.1.1化学成分、力学性能和金相组织通过测定附铸试样确定。
3.1.2 附铸试棒的数量:5件/块在铸件上的位置:4个边角各1,中心位置1。
3.1.3附铸试样随同铸件一起热处理,在铸件热处理后再从铸件上切开。
3.2 化学成分3.3 力学性能3.4 金相组织按GB/T7216-2009执行3.5 复验3.5.1 复验条件如果首次测试的结果不能满足材料的力学性能要求,允许进行重复试验。
3.5.2 试验的有效性如果不是由于铸件本身的质量问题,而是由于下列原因造成实验结果不符合要求时,则试验结果无效:a)试样在试验机上装卡不当或试验机操作不当。
b)试样表面有铸造缺陷或试样加工不当(如过渡圆角、表面粗糙度和尺寸不合要求等)。
c)拉伸试样在标距外断裂。
d)拉伸试样端口上存在明显的铸造缺陷。
在上述情况下,应在同一试块上重新取样或从同一批浇注的试块上重新取样再次试验。
3.5.3 铸件以去应力退火的状态交货。
如果力学性能不合格,允许供货方将铸件和代表该铸件的试块一起进行热处理,并再次提交验收。
为复验而进行的热处理次数不得超过两次。
3.5.4 复验的结果作为最终结果。
复验结果都达到要求,可判定该件铸件力学性能合格。
若复验结果仍达不到要求,则判断该件铸件力学性能不合格。
4 无损检测4.1顺序:目测、超声波探伤和加工表面的磁粉探伤。
4.2要进行试验的表面必须清洁无油、无油脂、无砂子或其他污物,表面粗糙度不大于Ra12.5,无影响试验或结果解释的异物存在。
4.3无损检测工作应由具备GB/T 9445规定的2级或以上资格的人员来完成。
灰铸铁件生产技术

毽7 P r e d u c t i o n T e c h n i q u e s
使铸 铁 的 白 口倾 向增 强 。虽然 在铸铁 中加 硅 、并进 行孕 育处 理 , 对 减轻 铬造成 的 白口倾 向有效 , 但 对于
凝 固过程的体积收缩率 , 使铸件的热应力增加 , 容易 在凝固、 冷却 过程 产生热 裂或 冷裂 _ 8 l 。
熔 炼所 用原 材料 为低碳 优 质废钢 、铸 造用 生 铁 和 同类 产 品 回炉 铁 。废钢 为优 质螺纹 切 头 , 无 锈蚀 , 无油污 ; 生铁 为 z 1 8生铁 ; 回炉 铁 经 清砂 处 理 , 表 面 光 洁 。孕育 剂为 B a 含量 1 0 %的 S i — B a 孕 育剂 , 主 要 成 分 见表 1 。其它 合 金 材料 还 有 F e — S i 、 F e — M n 、 F e —
1 试 验条 件及 方法 笔 者 公 司 生 产 的龙 门铣 床 横 梁 ( 见图 1 ) , 材 料
共晶体积分数均不超过 1 %。 石墨形态 以A型为主,
允 许 有少 量 的 型 、 C型源自, 石 墨 长度 4 ~ 6级 , 要 求 分
布 均匀 。
造 型 工 艺 为 呋 喃树 脂 砂 手 工 造 型 , 2台 1 2 t 的 中频感 应 电炉 熔炼 铁液 , 2个 1 2 t 的浇 包 同时 浇注 。 采用包内孕育和随流孕育相结合的复合孕育方式 , 铁 液 经过 1 5 2 0 c C 温度 过热 后 出炉进 行 浇 注 ,出炉
3 结 论
消除铬所致的晶间渗碳体则效果欠佳 。此外 ,铬细 化珠光体从而提高铸铁强度的作用也不太明显 。灰 铸铁 中, 加入 0 . 5 % 左右的铬 , 能使石墨细化 , 减少铁 素体 , 增加珠光体。通过试验 , 采用感应电炉生产高 强度 厚大 断 面灰铸 铁件 时 , 其 加 入量控 制 在 0 . 2 5 %~
提高灰铸铁性能的途径

提高灰铸铁性能的途径为提高灰铸铁的性能,常采取下列几种措施:选择合理的化学成分;改变炉料组成,过热处理铁液;孕育处理;微量或低合金化。
采取何种措施取决于所要求的性能及生产条件,往往同时采取两种以上措施。
1、化学成分的合理选配(1)碳、硅及硅碳比灰铸铁的含碳量大多在2.6%~3.6%,含硅量在1.2%~3.0%,碳硅都是强烈地促进石墨化的元素,可用碳当量CE来说明它们对灰铸铁金相组织和力学性能的影响.提高碳当量促使石墨化变粗,数量增多,强度和硬度下降.降低碳当量可减少石墨数量,细化石墨,增加初析奥氏体枝晶,从而是提高灰铸铁力学性能时常采取的措施.但降低碳当量会导致铸造性能降低,铸件断面敏感性增大,铸件内应力增加,硬度上升加工困难等问题,因此必须辅以其它的措施.在碳当量保持不变的条件下,适当提高Si/C比(一般由0.5左右提高至0.7左右),在凝固特性,组织结构与材质性能方面有以下变化:a 组织中初析奥氏体数量增多,有加固基体的作用;b 由于总碳量的降低,石墨量相应减少,减轻了石墨片对基体的切割作用;c 固溶于铁素体中的硅量增多,强化了铁素体(包括珠光体中的铁素体);d 提高了共析转变温度,珠光体在较高温度下生成,易粗化,会降低强度;e 降低了奥氏体的含碳量,使奥氏体在共析转变时易生成铁素体;f 硅高碳低情况下,易使铸件表层产生过冷石墨并伴随有大量铁素体,有利于切削加工,但不加工面的性能有所削弱;g 提高了液相线凝固温度,降低了共晶温度,扩大了凝固范围,降低了铁液流动性,增大了缩松渗漏倾向.综合以上各种固素的利弊,在碳当量较低时,适当提高Si/C,强度性能会有所提高,切削性能有较大改善,但要注意缩松渗漏倾向的增加和珠光体数量的减少。
在较高碳当量时(具体取决于生产条件)提高Si/C反而使抗拉强度下降。
此时提高硅碳比仍能有减少白口倾向的优点,适用于性能要求不高的薄壁铸件的铸造。
(2)锰和硫锰和硫本身都是稳定碳化物、阻碍石墨化的元素。
灰铸铁的组织和几种合金元素的影响

灰铸铁的组织和几种合金元素的影响2008-5-14 过去半个世纪中,灰铸铁的熔炼和孕育处理有了很大的进展,对于铸铁的合金化、生核和凝固以及固态的相变都作了不少研究。
在材料科学日新月异的今天,灰铸铁仍能作为一种结构材料而具有相当的竞争能力,是与这些研究工作分不开的。
目前,许多重要的机器零件,如机床床身、内燃机缸体、缸盖、壳体、歧管、压缩机缸体和液压阀等,都是用灰铸铁制成的。
当然,对灰铸铁性能的要求也越来越高了。
既要保证强度高,又要有良好的加工性能和厚、薄截面组织的一致性;还要求铸铁的刚度高(弹性模量大),铸件的尺寸稳定。
生产高牌号灰铸铁件,进行有效的孕育处理,是至关重要的,但是,正确地确定化学成分,必要时配加少量合金元素,也是不可忽视的条件。
如处理得当,选定化学成分和孕育处理可以有相辅相成的叠加效果。
这里,我们要扼要地讨论有关控制灰铸铁化学成分的一些问题,将不涉及孕育处理。
一、灰铸铁的组织和合金元素的影响灰铸铁的强度和综合质量,决定于其最终的显微组织,生产高牌号灰铸铁件,控制其显微组织的目标,大致有以下几方面:◆有较多的初生奥氏体枝状晶;◆无游离渗碳体和晶间渗碳体;◆石墨细小而且是A型;◆基体组织95%以上为珠光体,游离铁素体不多于5%;◆珠光体细小。
上述5项目标中,前3项要在铸铁凝固过程中建立,后2项则要通过控制铸铁的固态转变来达成。
1.铸铁的凝固过程要分析铸铁的凝固过程,不能不回顾一下铁-碳合金的相图。
铁-碳合金的相图是双重的,有稳定的铁-石墨系和介稳定的铁-渗碳体系。
制成高性能的灰铁件,当然不希望出现游离的渗碳体,所以要使铸铁按稳定的铁-石墨系凝固。
图1中简略地表示了铁-碳合金相图的共晶部分,并表示了一些合金元素对铁-石墨系和铁-渗碳体系共晶温度的影响。
图1 合金元素对铁-石墨系和铁-渗碳体系平衡共晶温度的影响铁-石墨系的共晶温度高于铁-渗碳体系的共晶温度,如果共晶成分的铁水冷却到铁-石墨共晶温度以下,同时又在铁-渗碳体的共晶温度以上,此时,对铁-石墨系而言铁水已经有了过冷度,可以进行石墨加奥氏体(γ)的共晶结晶,对铁-渗碳体系而言,则系统的自由能仍较高,设有进行渗碳体加奥氏体共晶结晶的可能。
灰口铸铁的化学成分
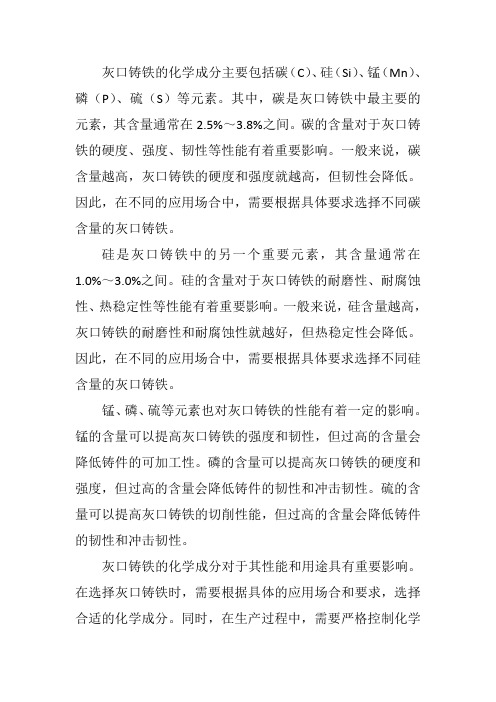
灰口铸铁的化学成分主要包括碳(C)、硅(Si)、锰(Mn)、磷(P)、硫(S)等元素。
其中,碳是灰口铸铁中最主要的元素,其含量通常在2.5%~3.8%之间。
碳的含量对于灰口铸铁的硬度、强度、韧性等性能有着重要影响。
一般来说,碳含量越高,灰口铸铁的硬度和强度就越高,但韧性会降低。
因此,在不同的应用场合中,需要根据具体要求选择不同碳含量的灰口铸铁。
硅是灰口铸铁中的另一个重要元素,其含量通常在1.0%~3.0%之间。
硅的含量对于灰口铸铁的耐磨性、耐腐蚀性、热稳定性等性能有着重要影响。
一般来说,硅含量越高,灰口铸铁的耐磨性和耐腐蚀性就越好,但热稳定性会降低。
因此,在不同的应用场合中,需要根据具体要求选择不同硅含量的灰口铸铁。
锰、磷、硫等元素也对灰口铸铁的性能有着一定的影响。
锰的含量可以提高灰口铸铁的强度和韧性,但过高的含量会降低铸件的可加工性。
磷的含量可以提高灰口铸铁的硬度和强度,但过高的含量会降低铸件的韧性和冲击韧性。
硫的含量可以提高灰口铸铁的切削性能,但过高的含量会降低铸件的韧性和冲击韧性。
灰口铸铁的化学成分对于其性能和用途具有重要影响。
在选择灰口铸铁时,需要根据具体的应用场合和要求,选择合适的化学成分。
同时,在生产过程中,需要严格控制化学
成分的含量,以确保铸件的质量和性能。
国家标准《灰铸铁件》解读

国家标准《灰铸铁件》解读?756?Ju1.2009V oI.58NO.7国家标准铸铁解读洪晓先,张寅(1.东风汽车有限公司工艺研究所,湖北十堰442001;2.沈阳铸造研究所,辽宁沈阳110022)1标准的历史概况及修订的必要性2新标准和旧标准主要内容的差异20世纪50年代,我国灰铸铁件生产是采用当时原苏联国家标准FOCT1412_48和经修订的FOCT1412—54铸铁标准.60年代初,我国制定了自己的灰铸铁件标准JB/T297一l962,其基本内容与FOCT14l2—54完全相同.1967年我国制定了灰铸铁件国家标准,即GB/T976—1967荻铸铁件分类及技术条f牛》,并于1968年1月试行.标准中按单铸试棒的抗弯,抗拉强度等级,将灰铸铁分为7级,牌号分别为HT10.26,HT15—33,HT20—40,HT25—47,HT30—54,HT35.61和HT40—68.该标准规定,灰铸铁的力学性能以qb30rnnl单铸试棒的抗拉强度和抗弯强度作为验收依据,以抗拉强度为主.由于抗弯强度试棒不需机加工,实际生产中通常是以抗弯强度作为验收依据,抗拉强度只是在抗弯强度不合格时才测定.GB/T976一l967一直沿用了近20年.到了80年代,改革开放政策促进铸造业有了较大发展,铸件出口也从无到有地发展起来,GB/T976—1967已不能满足生产与外贸的需要,1985年GB/T5675--1985铸铁分级》应运而生.GB/T5675--1985是等效采用国际标准ISO/DIS185(1983年草案)制定的,但这只是一个牌号分级标准,在技术条款方面仍沿用GB/T976一l967 的技术条款.为了方便使用,同时也考虑与球墨铸铁件,可锻铸铁件等国家标准在结构上一致,经国家技术监督局批准,决定编制铸铁件》国家标准.1988年6月25日经国家标准局批准发布了GB/T 9439—1988铸铁件》,1989年3月1Et实施,GB/T 9439---1988是等效采用国际标准ISO/DIS185—1983 铁件分和ISO/DP7191一l987《铸铁件交货通用技术条件》编制的,为推荐性国家标准.2001年11月,中国加人世界贸易组织,随之而来国家各项与经贸密切相关的基础标准需要与国际标准接轨.2005年国家标准化管理委员会对铸造国家标准清理评价,决定重新修订《灾铸铁件》国家标准.GB/T9439---2009等同采用国际标准ISO185:2005,并参考国外先进标准.为提高标准的市场适应性,新国家标准中增加了贸易性的内容,实现从产品型标准向贸易型标准的转变.新标准的主要内容与旧标准基本相近,但几乎在每个章节和条款上表述的方式都有所不同.新标准等同采用国际标准的同时,还保留,完善了旧标准中有利于标准可操作性,完整性的章节.新标准给出了更多的技术指标和数据,在取样要求,试验方法和检验规则等章节将各条款规定的更详细,更明确,在结构编排上也更趋合理.2.1适用范围新版标准规定了灰铸铁的术语和定义,灰铸铁牌号,技术要求,取样要求,试验方法,检验规则,以及铸件标识,包装和储运要求.标准所规定的范围阐述更为具体.2.2规范性引用文件在规范性引用文件中,引用的文件一律采用最新版的标准名称和编号,删除已作废的引用标准.新标准共引用了18项国家标准,全部为非注日期引用.比旧标准多引用的5项标准是:GB/T228金属材料室温拉伸试验方法GB/T4336碳素钢和中低合金钢火花源原子发射光谱分析方法(常规法)GB/T5611铸造术语GB/T8170数值修约规则GB/T11351铸件重量公差2.3术语和定义增加了术语和定义章节,对铸件主要壁厚定义为:指用以确定铸件材料力学性能的铸件断面厚度.2.4灰铸铁牌号在灰铸铁牌号一章中,等同采用了国际标准ISO 185:2005的牌号分级,增加了HT225和HT275两个新牌号,这是新,旧标准的最显着差别.2.5订货要求将旧标准放在资料性附录中的订货要求纳入正文,并作为独立章节.规定需方订货时最少应提供材料牌号和特殊需求,其他技术参数如需方不了解,供方可帮助确定,简化了需方的专业知识要求.这是产品型标准向贸易型标准转变的一个特征.2.6生产方法和化学成分(1)增加了生产方法和化学成分章节.铸造洪晓先等:国家标准《:扼铸铁解读(2)规定铸件的生产方法一般由供方自行决定,对特殊要求可双方商定.(3)规定如需方的技术条件中包含化学成分的验收要求时,按需方规定执行.化学成分按供需双方商定的频次和数量进行检测.体现了买方市场,满足用户需求的理念.(4)规定当需方对化学成分没有要求时,化学成分由供方自行确定,化学成分不作为铸件验收的依据. 但化学成分的选取必须保证铸件材料满足本标准所规定的力学性能和金相组织要求.2_7技术要求(1)力学性能试棒取自单铸试棒还是铸件本体,性能验收指标是抗拉强度还是硬度,均必须在订货协议或需方技术要求中明确规定.铸件的力学性能验收指标应在订货协议中明确规定.因铸件的形状,壁厚不同,力学性能验收指标应根据具体铸件确定.(2)除力学性能外,金相组织也是铸件验收的主要指标,比旧标准要求更严格.(3)新标准的表1将旧标准的三表合一,易于对照.(4)表1增加了HT225和HT275牌号铸件在不同壁厚时的最小抗拉强度值.(5)表1中,HT150的主要壁厚增加了两档.铸件本体预期抗拉强度略有调低.(6)将旧标准表2中的不同尺寸附铸试棒和附铸试块整合到一起,根据铸件壁厚选择30rnlTl或50mm附铸试棒,如选附铸试块也同样有Rl5和R25两种规格.铸件主要壁厚小于80mm的选用小规格试棒(块),801/11/1及以上壁厚选用大规格试样(块).(7)旧标准中铸件壁厚在40~80mm时,可选用qb30mm附铸试棒也可选用qb50mm附铸试棒,因此导致了同一牌号,同样壁厚范围,因采用附铸试样或附铸试块产生两个不同的最小抗拉强度值.新标准避免了这种情况,即壁厚大于80iYinl时,均采用大规格试棒或试块,而不同壁厚规定的最小抗拉强度值,基本上是采用旧标准的附铸试块强度值.因为附铸试块的抗拉强度略低于附铸试棒的抗拉强度,附铸试块的铸造也较为方便.(8)HT300牌号铸件在不同壁厚范围内,附铸试棒(块)的性能略有降低或提高.(9)新,旧标准对附铸试棒(块)最小抗拉强度规定的差异见表1.(10)新标准与国际标准ISO185:2005相比,在牌号HT150,HT200中缺少壁厚2.5~5inln档及对应的铸件本体预期抗拉强度,数据有待补充.因为随着直读光谱,孕育,保温浇注和整体组芯等新技术的应用,主要壁厚小于5Inl-n的铸件时常可见,尤其是小型发动机气缸体,最小壁厚通常仅为4innl左右.旧标准中HT100,HT150和HT200对应的最小壁厚为2.5~10mnl, 太宽泛,也不尽合理,在今后该标准修订时应予以补充. (11)铸件本体取样位置,试样尺寸和抗拉强度值可由供需双方商定,若需方有明确规定时,应符合需方图样及技术要求.若需方要求从铸件本体上取样,但未指定本体取样位置时,供方可根据铸件结构和受力状况,自行决定取样位置.(12)标准给出8种规格的本体试样加工尺寸(见表2),方便使用,符合用户对铸件本体质量要求不断提高的趋势.规定铸件本体抗拉强度的检测频次和数量,由供需双方商定.(13)将铸件硬度牌号规定,由旧标准的附录性文件改为纳入正文中,体现了实际生产中,用户对铸件本体硬度日益重视,同时也更易于通过铸件硬度对供方铸件的质量进行监测.新标准按不同壁厚对铸件本体硬度作了更详细的规定,见表3.将旧标准中的硬度牌号H145改为H155,使每个硬度牌号等级间的硬度差均为20HBW.(14)给出单铸试棒抗拉强度的同时还给出了单铸试棒的硬度值,见表4.(15)规定硬度检测应在铸造面1.5rnrn以下处测试, 因为铸件表面可能存在过冷组织,热处理贫碳和抛丸应力等影响材质的真实硬度.(16)没有推荐采用易割片作敲落式铸件附铸硬度试块,这种方法在大量生产中不常用.2.8取样要求单铸试棒应在本批次铁液浇注后期浇注试棒,以保证试棒的代表性.2.9试验方法(1)样件,试生产铸件需提交全尺寸检测报告,检测数量由供需双方商定.量产供货的铸件应按批次提交关键尺寸(或重要尺寸)检测报告,检测频次和数量由供需双方商定.此规定的目的是保证铸件按生产流程的要求进行试制,试产和量产,以保证铸件品质的一致性,稳定性和可追溯性.(2)如供需双方同意,可选用等效的方法测定抗拉强度,布氏硬度,金相组织,如用测定楔压强度替代测定抗拉强度.楔压强度通常用于受铸件毛坯尺寸限制或已机加工后的铸件无法切取出本体抗拉试样的场合.2.10检验规则在取样批次的划分章节,.增加了2条新规定.(1)同一模具生产的同一炉铁液浇注的铸件构成一个取样批次.即铸件是以炉次为最大批次,条件是该炉次浇注的铸件应是采用同一型,芯模具,造型,?758?FOUNDRYV o1.58No.75lOlO2O2040HT2254080一一19O1708Ol50l55一一一l50300145一一一23020017015013510202040HT27540808015Ol50300205190l75250220190l75新版:表中斜体字数值表示指导值,其余抗拉强度值均为强制性值,铸件本体预期抗拉强度值不作为强制性值.旧版:1.壁厚150---300mm铸件的附铸试棒(块)最小抗拉强度没有规定指导值,均为强制性值.2.HT100牌号太低,没有实用价值,表中没有列出HT100牌号.3.HTI50,HT200,HT250牌号中没有5~10rnln和10---20nlnl档,以及对应的铸件本体预期抗拉强度.制芯工艺也是一样的.(2)在某一时间间隔内,如炉料,工艺条件或化学成分有变化时,在此期间连续熔化的铁液浇注的所有铸件,无论时间间隔有多短,都作为一个取样批次.强调无论是连续熔化还是间歇熔化,只要炉料,工艺条件或化学成分有变化,这个变化期间浇注的铸件都应该作为一个单独的批次.如感应炉熔化时,某包铁液加入了某种合金元素;同炉次铁液孕育剂,孕育方法的改变..浇注同样铸件但浇注工艺或浇注系统的改变等,都应该作为一个单独批次.铸造洪晓先等:国家标准锹铸铁牛》解读'759.注:1.在铸件应力最大处或铸件最重要工作部位或在能制取最大试样尺寸的部位取样.2.加工试样时应尽可能选取大尺寸加工试样.表3灰铸铁的硬度等级和铸件硬度表4单铸试棒的抗拉强度和硬度值规定供方应保存所有完整的试验和检查记录,留客户复查.需方没有特殊规定时,同一批次的拉伸试样和未做试验的试样应自填写试验报告之日起保存3个月以上.2.11附录为了方便设计者和用户,增加了"灰铸铁的力学性能和物理性能","灰铸铁件的抗拉强度,硬度和截面厚度的关系"以及"楔压强度"的附录.3标准的特点3.1由产品型标准向贸易型标准转变旧标准在内容和表述方式偏重于灰铸铁件自身的牌号等级规定,技术要求,试验方法和检验规则等,其考虑更多的是站在供方的角度指导制造商按国家标准的基本规定生产灰铸铁件.新标准虽然在主体内容上和旧标准相近,但是站在中间的立场,并以用户(需方)需求为上的理念来阐述标准的规定.3.1.1突出用户要求在很多情况下,用户对铸件的使用条件,工况和质量要求比铸件制造商更清楚,尽管用户可能对铸造工艺,材料技术本身不那么内行.反之铸件制造商虽然对铸件和铸件生产技术是内行,但其对该铸件的用途,使用工况并不一定了解.所以新标准给用户预留了更多的话语权.特别是在技术,质量要求方面,当用户有专门要求时,经供需双方协商同意,可按用户提出的要求验收.体现出在市场经济下,供方应不拘泥于标准的规定,尽可能满足客户需求,以需求拉动技术,质量提升的发展趋势.3.1.2强调供需双方协商准则标准只能做到确立规则,规定一般事件的处理方法,而实际生产,贸易中不同的情形和需求无法预知. 新标准几乎在所有重要条款中都规定了供需双方协商一致的原则,因为贸易本身就是不断洽谈协商,相互理解和妥协的过程.从某种意义上说,新标准是为供需双方协商提供了一个法定规则的平台.3.1_3重要环节和细节都列出了相应条款和具体要求铸造生产环节多,流程长,在签署订货协议中难免有漏项.新标准在主要技术,质量,检验等环节都给出了较为详细的条款,对供需双方都有提示或警示作用.?760?FOUNDRYdu1.2oo9VOI.58N0.73.2主要内容等同采用了国际标准的最新文本3.2.1与国际标准接轨与国际标准接轨是编制新标准的基本原则,为了更好地促进对外贸易和交流,国家标准应不低于国际标准已成为不言而喻的共识.新标准在主要技术内容方面等效采用了国际标准ISO185:2005((Greycast irons.Classification)),但在标准的编写结构上不完全对应.3.2.2表格合并与简化标准中规定的技术指标和技术参数多以表格的形式表述.与旧标准相比,新标准合并了一些相近内容的表格,还提供了更多的表格数据,在数据内容上更加完整.3.2-3新增加了两个灰铸铁牌号等同采用了国际标准的牌号分级.该标准的2005版,增加了HT225和HT275两个新牌号,这是新标准与旧标准的最显着差异.HT200.HT300牌号是用量最多,且随着牌号提高铸造性能恶化也较为显着的区域,为了充分挖掘灰铸铁材料的力学性能潜力,减缓铸造性能的恶化倾向,将牌号细分可为用户提供更多的选择,同时有利于物尽其用.铸造配料,熔化,炉前成分检测,孕育等新技术也为灰铸铁牌号的细分提供了技术保障.美国材料试验学会标准ASTMA48/A48M--2003 ((StandardSpecificationforGrayIronCastings))标准中,灰铸铁牌号按抗拉强度分级,从150至400,每增加25]VIVa 为一个牌号等级,分150,175,200,225,250,275,300,325,350,375和400共11个牌号.美国汽车工程师协会标准SAEJ431,将灰铸铁也分为8个等级.新标准中没有抗拉强度为375MPa和400MPa这2个级别的牌号,因为我国和许多工业国家一样,由于球墨铸铁,蠕墨铸铁的发展,实际上已很少生产这2种高强度的灰铸铁件了.对灰铸铁强度要求过高的并不总是有利的,因为它会恶化铸造性能,机加工性能和减震性.3.2.4将硬度牌号及验收指标纳入正文硬度牌号和抗拉强度牌号一样,也可以作为灰铁件的验收条件.以硬度牌号作为验收条件,一般是用于对切削性能或耐磨性能要求较高的灰铸铁件,且铸件主要壁厚小于80mill.3.2.5硬度牌号的分级硬度牌号分级的3位数字是表示各硬度牌号铸件在壁厚40mnl时所对应规定硬度的上限值,如硬度牌号H195,表示铸件壁厚40rnm部位,硬度的最大值不大于195HBW.3.2.6灰铸铁材料的性能指标附录中给出了不同牌号灰铸铁常用的力学,物理性能指标,抗拉强度和铸件壁厚的关系,以及楔压强度试验和换算方法,为标准使用者提供了方便.3.3保留,完善了旧国家标准中不可或缺的精华的部分对旧标准几十年实践证明不可或缺的部分予以保留,完善.如技术要求章节中的几何形状,尺寸,尺寸公差,加工余量,表面质量,铸造缺陷;检验规则章节中的检验权利,检验地点,取样批次的划分,试验数据保存,试样保存;铸件标识,包装,储运要求章节中的铸件标识和质量报告,表面防护,包装,储运要求等.上述条款强调了灰铸铁件作为商品的属性和商品交货时应符合的质量状态要求.这些内容国际标准ISO185: 2005((Greycastirons—Classification))均没涉及.3.4灰铸铁牌号单铸试棒的硬度值在3Omm单铸试棒上测试材质硬度是生产中常用的方法,但因单铸试棒硬度和铸件本体硬度有一定的差异,在供需双方没有事先商定的情况下,经常会因铸件硬度的定义发生争议.本标准既给出了单铸试棒的硬度范围也给出了铸件本体的硬度范围.4标准的应用铸铁件》是铸造标准中的基础性标准,应用面广,使用频率高,因此供需双方在应用新标准时应注意下列事项.4.1标准的适用范围新标准不适用于连铸型材,离心铸管,金属型铸造等非砂型灰铸铁件.4.2灰铸铁牌号的化学成分化学成分是保证力学性能的重要依据,因此在铸造企业自己的技术标准中通常都明确规定不同灰铸铁牌号的化学成分范围.而新,旧标准都没有对化学成分做出规定是因为:(1)化学元素之间有交互性和互补性,在某些元素增加的情况下,减少另外一些元素可得到同样的力学性能和硬度值范围.各铸造厂的情况和工艺方法差别很大,规定了成分就牺牲了灵活性,多样性,后果也不经济.(2)除化学成分外,还有很多其他因素对铸件的力学性能有重要影响,如微量元素,孕育,熔化过热,激冷倾向,替代元素,冷却方式,后续处理等.也就是说,即使化学成分合格或不合格,并不能完全主导铸件的力学性能和硬度.(3)中小冲天炉熔化和炉料比较复杂的情况下,难以做到对化学成分范围做比较准确的控制,铁液出炉后木已成舟,只能用综合调控手段来保证铸件力学性能.(4)对一个具体铸造企业,其条件和工艺已确定,经供需双方协商同意,可规定化学成分范围的要求.铸造洪晓先等:国家标准锹铸铁解读?761?对有特殊要求的铸件,甚至可将某些化学元素作为主要验收依据之一.(5)当需方没有提出化学成分范围要求时,铸件的化学成分由制造商自行决定,因为制造商比需方更清楚满足该牌号要求应选择的各化学元素范围,同时也有利于采用制造商的化学成分体系,检测验收体系, 实现规模化生产.(6)当需方提出具体的化学成分范围,经供需双方协商同意后,还应确认哪些元素属于强制性要求和强制性要求元素的波动范围以及超出范围时的处理办法等.4.3灰铸铁牌号灰铸铁牌号指30mm单铸试棒的最小抗拉强度,它只能间接反映铸件本体的力学性能.同样牌号的铸件,因形状,尺寸,壁厚不同,铸件本体性能力学性能和硬度会有不同.4.4HT_225和HT275~号特点提高灰铸铁牌号通常是用降低碳,硅含量或是添加合金元素来实现,而随着抗拉强度牌号的提高,灰铸铁的工艺性明显恶化,尤其是收缩倾向,白口倾向大和流动性差.新增加的2个牌号对工艺性较敏感的薄壁箱体件,薄壁小件,形状复杂件,盘类件等用途较大.4.5HT350以上牌号HT350以上牌号的铸造工艺性差,实际生产中已很少采用.对于更高强度牌号的要求,推荐采用蠕墨铸铁或球墨铸铁.虽然蠕墨铸铁和球墨铸铁各有自身特点,但除减震性外,其铸造工艺性,切削加工性和成本等都有较强的竞争力.建议在选用HT350牌号的同时应考虑对比选用蠕墨铸铁或球墨铸铁的可能性.4.6单铸试棒与本体试棒性能的差异铸造的特点是适于制造形状不规则,结构复杂的零件,因此壁厚差异较大会导致不同部位的冷速不同, 造成各部位力学性能和硬度有一定差异.单铸试棒只能代表该牌号材质特定壁厚的力学性能和硬度,铸件本体试样才能代表本体I生能.4.7附铸试棒(块)规格的选取以铸件主要壁厚80nlrn为界,壁厚小于80rnn'l时,选用小规格的附铸试棒(块),壁厚大于等于80mnl时,选用大规格试棒(块).4.8抗拉强度性能的差异(1)对于同档尺寸规格的单铸或附铸试棒,如加工成A型抗拉强度试样,其统计强度值要略高于B型试样. 因为A型试样标距内的平行段短,可能碰到组织不均匀影响的几率小,所以更能代表材质本身的真实抗拉强度.(2)对于同档尺寸规格的附铸试棒或附铸试块,附铸试棒的统计强度值要略高于附铸试块,因为附铸试棒的冷速要快一些,内部组织也致密一些.(3)附铸试棒(块)的性能还不能完全代表铸件本体性能,只是比单铸试棒性能的代表性更好一些,只有本体试样才能如实反映铸件本体性能.铸件本体性能可根据标准附录中给出的壁厚与抗拉强度,硬度的关系图估算.4.9铸件本体抗拉强度测定铸件本体抗拉强度时,抗拉强度试样的加工应尽可能选用尺寸较大的规格,大规格试样l:LsJ,规格试样的测试数据更稳定,准确.4.10抗拉强度的强制值和指导值灰铸铁各牌号等级规定的最小抗拉强度是强制性值,但对应于壁厚>150mm,≤300mi/l的铸件,新标准中给出的附铸试棒(块)抗拉强度值为指导值,在表中用斜体字表示.表中给出的铸件本体预期抗拉强度值也不是强制性值.4.11铸件的本体硬度范围可以小于新标准中规定的范围当供需方同意在铸件本体的指定部位测试硬度,则该指定部位硬度值的上,下限范围应不小于40HBW. 此条款一般用于大量生产的铸件.因为标准中给出的硬度值范围是泛指,所以对给定的铸件和硬度测试部位,经供需双方协商同意,可适当缩小硬度值范围.4.12硬度检验规则新标准取消了旧标准列在规范性附录中的硬度检验规则,因为影响硬度的因素较多,测试误差也较大,而且实际中容易测试多点,多部位的硬度值来综合判断铸件材质情况,不像抗拉强度,误差较小,也比较单一.但在实际应用中硬度检测规则和抗拉强度检测规则是一样的,即在事先规定的部位测试硬度,如该部位硬度合格则材质合格,若测试结果达不到要求,又不是试样制备或操作不当造成的,则可在硬度测定点附近再选定2处测定硬度,进行复验.如复验中,其中一处硬度不合格,则判该铸件材质不合格.铸件本体硬度的测试比例,检测频次,硬度合格率及抽取铸件的代表性等,由供需双方商定.4.13铸件本体硬度检测铸件本体硬度检测简单,方便,可以不损坏铸件,甚至可100%在线检测.对大批量生产的铸件,越来越多地用本体硬度来代替抗拉试棒检测,特别是汽车灰铸铁件.以检测本体硬度为主时,应在本企业生产条件下事先做出该铸件本体硬度和单铸试棒,本体试棒之间的函数关系,以此确定本体硬度的上,下限范围,并经需方同意及确定抽检比例后才可实施.大型铸件一般检测附铸试块的硬度.4.14灰铸铁的化学成分新标准和国际标准ISO185:2005都没有规定灰铸铁的化学成分,但化学成分的控制还是尽可能控制在较窄的范围.铸造熔化中炉料分选,分类,配比定量,?762?FoUNDRYJu1.2009VOI.58NO.7熔化参数稳定,过热,保温控制,炉前检验,调整等都是缩小化学成分范围的重要环节.与先进国家相比, 我国铸件化学成分波动范围较大,缩小成分波动范围是今后努力的方向.4.15灰铸铁件的金相组织(1)如果需方没有要求,则金相组织一般不作为验收项目.如果要求检测金相组织,则应规定铸件本体的检测部位.新标准虽然没有对灰铸铁件的金相组织要求和取样方法做详细的规定,实际中可参照铸件本体抗拉强度试样的作法进行.特别是铸件非正常损坏失效或铸件残体碎片,检测金相组织是判断铸件性能的一种常用方法.(2)影响灰铸铁力学性能的金相组织首先是石墨形态和石墨长度,其次是珠光体和铁素体比例.因为灰铸铁本身是脆性材料,所以少量碳化物和磷共晶对力学性能基本没有影响,一般要求总量≤3%,高牌号灰铸铁可以放宽到≤5%.共晶团数,珠光体片间距和石墨量等均不作为铸件的验收依据.4.16铸造残余应力灰铸铁件一般以铸态交货,不做消除残余应力处。
浅谈机床类灰铸铁件化学成分的选择

浅谈机床类灰铸铁件化学成分的选择浅谈机床类灰铸铁件化学成分的选择梁学亮,魏永强(陕西秦川机床工具集团有限公司铸造厂技术科,721009)摘要机床类灰铸铁件有着高于其它灰铸铁件的性能要求,生产中应该在确保配料中废钢比例的基础上,合理选择铁水的化学成分,规范的加料、熔化操作,才能保证生产出符合质量要求的机床类灰铸铁件。
关键词机床类灰铸铁件性能要求废钢比例机床类灰铸铁件除了要满足国家标准GB/T9497-2010外,还要满足机械行业标准JB/T3997-94,这是因为作为工作母机的机床对其铸件还要有着特殊的要求,这就是:1.较高的抗压强度与抗拉强度;2.良好的精度稳定性;3.高的弹性模量;4.良好的耐磨性;5.较好的减震性;6.良好的切削性能;7.良好的铸造性能;8.较好的尺寸精度和表面光洁度[1]。
而对于灰铸铁而言,在配料不变、原材料成分稳定、加料称量准确的前提下,化学成分决定铸件的金相组织,金相组织决定铸件的性能,由此可见,机床类灰铸铁件化学成分的选择就尤为重要。
下面就机床类灰铸铁件的配料和化学成分的选择谈一些自己看法。
1.配料配料可以说是所有合金熔炼的基础。
举一个极端的例子来说明,两种配料,一种是全部用生铁熔化出ωC为3.20%的铁水(在中频电炉熔炼条件下,在春节长假期间,需要给炉内加生铁,连续几天烘炉以防止水冷系统冷却水结冻(北方),这样的情况下,全部用生铁熔化出ωC为3.20%的铁水);还有一种就是完全用普通碳素钢类废钢加增碳剂熔化出ωC为3.20%的铁水,在其它元素含量类似情况下,那一种铁水浇铸出的铸件更好呢?在灰铸铁熔炼中,废钢在配料中的比例很大程度上决定了铸件的性能。
这里,我提一下炉料的遗传性,在一些资料中,提到炉料的遗传性,更多的谈到新生铁对铁水的不利影响;其实,炉料的遗传性含义应该是很广的,它应该是指所有炉料对铁水、铸件的影响,除了生铁,还有废钢、回炉铁、铁合金、增碳剂、增硫剂、碳化硅等等,都会给铁水带来自己独特的影响。
灰铸铁化学成分标准

灰铸铁化学成分标准
灰铸铁是一种铸造铁,其化学成分对于铸件的性能和用途具有重要影响。
灰铸
铁的化学成分标准通常包括碳含量、硅含量、磷含量、锰含量等指标。
下面将对灰铸铁的化学成分标准进行详细介绍。
首先,碳含量是影响灰铸铁性能的重要指标之一。
通常灰铸铁的碳含量在
2.7%~4.0%之间。
碳含量的增加可以提高铸件的硬度和强度,但会降低其韧性。
因此,在不同的使用要求下,可以通过控制碳含量来调整灰铸铁的性能。
其次,硅含量也是影响灰铸铁性能的重要因素。
硅是灰铸铁中的主要合金元素
之一,其含量通常在1.0%~3.0%之间。
适当的硅含量可以提高灰铸铁的流动性和耐磨性,但过高的硅含量会导致铸件产生气孔和疏松组织。
另外,磷和锰的含量也对灰铸铁的性能有一定影响。
磷的含量通常控制在0.1%以下,过高的磷含量会导致灰铸铁的脆性增加。
而锰的含量通常在0.3%~0.8%之间,适当的锰含量可以提高灰铸铁的强度和韧性。
总的来说,灰铸铁的化学成分标准对于铸件的性能和用途具有重要影响。
在生
产过程中,需要严格控制每种元素的含量,以确保灰铸铁具有良好的力学性能和耐磨性。
同时,也需要根据具体的使用要求,对化学成分进行合理的调整,以满足不同工况下的需求。
通过对灰铸铁的化学成分标准进行详细了解,可以更好地指导生产实践,提高
铸件的质量和性能。
同时,也有助于对灰铸铁材料的选用和应用进行合理的评估和选择。
希望本文能够对相关行业人士有所帮助,促进灰铸铁材料的合理应用和推广。
GB 976-1967《灰铸铁件 分类及技术条件》标准

GB 976-1967《灰铸铁件分类及技术条件》标准引言灰铸铁是一种常见的铸铁材料,广泛应用于各个工业领域。
为了确保灰铸铁件的质量和性能符合要求,GB 976-1967《灰铸铁件分类及技术条件》标准被制定出来。
本文将对该标准的主要内容进行解读和概述。
1. 精神该标准的主要精神是根据灰铸铁的组织结构、化学成分和机械性能,对灰铸铁件进行分类,并规定了各类灰铸铁件的技术条件。
2. 适用范围该标准适用于所有生产和使用灰铸铁件的企业和单位。
3. 名词术语在本标准中,以下名词术语的定义适用于全文:•灰铸铁:指以石墨为基本组织的铸铁。
•灰铸铁件:指由灰铸铁材料制成的各种形状的铸件。
•组织:指灰铸铁中的石墨颗粒和基体的排列、形态等特征。
4. 分类根据灰铸铁的化学成分和组织结构,本标准将灰铸铁分为以下几个类别:•一类灰铸铁:化学成分只考虑碳含量,通常含有2.8-4.2%的总碳量。
•二类灰铸铁:化学成分同时考虑碳含量和硅含量,碳含量为1.8-4.2%,硅含量为0.8-2.8%。
•三类灰铸铁:化学成分同时考虑碳含量和硅含量,碳含量为1.8-4.2%,硅含量为1.8-3.2%。
5. 技术条件根据灰铸铁的分类,本标准规定了各类灰铸铁件的技术条件,包括机械性能、化学成分、组织结构等方面的要求。
5.1 一类灰铸铁件的技术条件一类灰铸铁件的技术条件如下:•压力下使用时,其抗拉强度不低于180MPa。
•其余力学性能以及化学成分和组织结构等需要根据具体情况来确定,但应符合相应的标准要求。
5.2 二类灰铸铁件的技术条件二类灰铸铁件的技术条件如下:•压力下使用时,其抗拉强度不低于150MPa。
•其余力学性能以及化学成分和组织结构等需要根据具体情况来确定,但应符合相应的标准要求。
5.3 三类灰铸铁件的技术条件三类灰铸铁件的技术条件如下:•压力下使用时,其抗拉强度不低于140MPa。
•其余力学性能以及化学成分和组织结构等需要根据具体情况来确定,但应符合相应的标准要求。
灰铸铁成分设计的一般原则

灰铸铁成分设计的一般原则
灰铸铁化学成分主要包括碳、硅、锰、硫、磷五大常见元素。
对于一些对组织及性能有特殊要求的铸件,还包括少量的合金元素。
同普通灰铸铁不同的是,为保证石墨球化,球墨铸铁中还须含有微量的残留球化元素。
1、碳及碳当量的选择原则:
碳是球墨铸铁的基本元素,碳高有助于石墨化。
由于石墨呈球状后石墨对机械性能的影响已减小到最低程度,球墨铸铁的含碳量一般较高,在3.5~3.9%之间,碳当量在4.1~4.7%之间。
铸件壁薄、球化元素残留量大或孕育不充分时取上限;反之,取下限。
将碳当量选择在共晶点附近不仅可以改善铁液的流动性,对于球墨铸铁而言,碳当量的提高还会由于提高了铸铁凝固时的石墨化膨胀提高铁液的自补缩能力。
但是,碳含量过高,会引起石墨漂浮。
因此,球墨铸铁中碳当量的上限以不出现石墨漂浮为原则。
2、硅的选择原则:
硅是强石墨化元素。
在球墨铸铁中,硅不仅可以有效地减小白口倾向,增加铁素体量,而且具有细化共晶团,提高石墨球圆整度的作用。
但是,硅提高铸铁的韧脆性转变温度(图1),降低冲击韧性,因此硅含量不宜过高,尤其是当铸铁中锰和磷含量较高时,更需要严格控制硅的含量。
球墨铸铁中终硅量一般在1.4—3.0%。
选定碳当量后,一般采取高碳低硅强化孕育的原则。
硅的下限以不出现自由渗碳体为原则。
化学成分的合理选配(讲义)

化学成分的合理选配1.碳、硅、碳当量灰铸铁的主要成分是铁、碳、硅。
碳和硅对灰铸铁的显微组织及最终的性能起着决定性的影响,下图是由C和Si的不同含量对直径30试棒的组织的影响,我们所要的高强度高碳当量铸铁,其C和Si含量应在Ⅱ区,即珠光体+石墨的灰口铸铁区,生产上多是通过调整和控制碳硅含量来获得所需的铸件牌号和性能。
硅是铸铁件中产生石墨的基础,含硅量越高,亚共晶铸铁越接近共晶点,在按稳定系统结晶条件下,灰铁的石墨量越多,机械性能就越低。
反之,在碳含量减低,远离共晶点时,结晶间距加大,而初生奥氏体越多,使基体骨架更为坚强,在不产生枝晶间石墨条件下,铸铁性能就提高。
硅是强烈的石墨化元素,它的作用要比碳大,硅能使Fe-C合金的共晶点和共析点向上,向左移动,使铸铁件能在比较高的温度下进行共晶和共析转变,从而促进了石墨化。
生产中采用碳当量(CE)来综合考虑碳和硅对铸铁组织和性能的影响,碳当量实际上表示铸铁的实际成分离共晶体的远近,当CE=43%时,表示这种含硅铸铁成分是共晶成分,提高碳当量能使石墨变粗数量增加,抗拉强度,硬度下降,反之。
降低碳当量能减少石墨数量,细化石墨,增加初生奥氏体,从而提高灰铸铁的力学性能。
碳当量:Ce=C+1/3(Si+P)而在欧洲常用共晶度Sc来表示铸铁的实际成分与共晶点的远近,Sc=1,为共晶铸铁,Sc<1与亚共晶铸铁,Sc>1与过共晶铸铁,Sc=C÷(426-0.312Si-0.27P)或简化为Sc=C÷[4.3-1/3(Si+P)]经过大量的实验数据统计,获得铸铁的抗拉强度与CE或Sc的关系为:抗拉强度=10.000(K-2CE)xf1Xf2 (1)其中,K=11.80(直径22试棒)k=11.50(直径30试棒) k=11.00(直径50试棒)CE=碳当量,f1,f2……合金元素因子其计算结果为英寸磅(psi)1psi=0.006894Mpa或抗拉强度=981-785XSc 简化为:抗拉强度=1000-800Sc (2)也可由图查得CE与抗拉强度的关系403020直径为30mm的铸态灰铸铁试棒的抗拉强度与CE关系用公式(1)或公式(2)依碳当量及共晶度计算得出的抗拉强度就是众多数据统计出来的经验式,也可以说反映出了正常的工艺技术水平下得出的机械性能,如果我们的强度低于这个水平,说明我们工艺水平低,而高于这个水平,说明我们的工艺先进,无论是在技术上,管理上,都是一流的,所以可用成熟度来衡量。
- 1、下载文档前请自行甄别文档内容的完整性,平台不提供额外的编辑、内容补充、找答案等附加服务。
- 2、"仅部分预览"的文档,不可在线预览部分如存在完整性等问题,可反馈申请退款(可完整预览的文档不适用该条件!)。
- 3、如文档侵犯您的权益,请联系客服反馈,我们会尽快为您处理(人工客服工作时间:9:00-18:30)。
浅谈机床类灰铸铁件化学成分的选择
梁学亮,魏永强
(陕西秦川机床工具集团有限公司铸造厂技术科,721009)
摘要机床类灰铸铁件有着高于其它灰铸铁件的性能要求,生产中应该在确保配料中废钢比例的基础上,合理选择铁水的化学成分,规范的加料、熔化操作,才能保证生产出符合质量要求的机床类灰铸铁件。
关键词机床类灰铸铁件性能要求废钢比例
机床类灰铸铁件除了要满足国家标准GB/T9497-2010外,还要满足机械行业标准JB/T3997-94,这是因为作为工作母机的机床对其铸件还要有着特殊的要求,这就是:1.较高的抗压强度与抗拉强度;
2.良好的精度稳定性;
3.高的弹性模量;
4.良好的耐磨性;
5.较好的减震性;
6.良好的切削性能;
7.良好的铸造性能;
8.较好的尺寸精度和表面光洁度[1]。
而对于灰铸铁而言,在配料不变、原材料成分稳定、加料称量准确的前提下,化学成分决定铸件的金相组织,金相组织决定铸件的性能,由此可见,机床类灰铸铁件化学成分的选择就尤为重要。
下面就机床类灰铸铁件的配料和化学成分的选择谈一些自己看法。
1.配料
配料可以说是所有合金熔炼的基础。
举一个极端的例子来说明,两种配料,一种是全部用生铁熔化出ωC为3.20%的铁水(在中频电炉熔炼条件下,在春节长假期间,需要给炉内加生铁,连续几天烘炉以防止水冷系统冷却水结冻(北方),这样的情况下,全部用生铁熔化出ωC为3.20%的铁水);还有一种就是完全用普通碳素钢类废钢加增碳剂熔化出ωC为3.20%的铁水,在其它元素含量类似情况下,那一种铁水浇铸出的铸件更好呢?
在灰铸铁熔炼中,废钢在配料中的比例很大程度上决定了铸件的性能。
这里,我提一下炉料的遗传性,在一些资料中,提到炉料的遗传性,更多的谈到新生铁对铁水的不利影响;其实,炉料的遗传性含义应该是很广的,它应该是指所有炉料对铁水、铸件的影响,除了生铁,还有废钢、回炉铁、铁合金、增碳剂、增硫剂、碳化硅等等,都会给铁水带来自己独特的影响。
生产机床类灰铸铁件,尤其是机床类五大件床身、立柱、工作台、主轴箱、滑座时,根据我们的生产经验,配料中废钢的比例不应低于45%,生铁的比例不应高于20%。
如果工厂的回炉铁足够多,能够满足生产平衡,也可以不使用生铁,而采用废钢+回炉铁+加增碳剂的配料方式生产(电炉熔炼)。
2.化学成分的选择
2.1碳
作为铸铁中几乎含量最高的非金属元素,碳对铸铁性能的影响毫无疑问是第一位的。
为了满足上文提到的机床类铸件的8种要求,综合考虑,机床类灰铸铁件碳的选择范围为2.90~3.30%,铸件牌号越高,导轨越厚实,选取范围中的较低值,反之,选取较高值;又以3.10~3.20%作为机床类灰铸铁件碳的最佳选择范围(生产中碳的检测以光谱仪或热分析仪为准,化学分析法因为钻取试样石墨的丢失,测量结果会有较大的偏差)。
2.2硅
硅和碳是同主族元素,因此,在铸铁中的作用比较相似。
灰铸铁中硅的来源主要是炉内加硅铁和出铁及浇注时孕育这两部分。
虽然各厂的情况不尽相同,但是终铁水的硅过低或多高,都会对铸件的性能产生不利的影响,导致不能满足上文提到的8种要求,因此对于机床类灰铸铁件,比较适宜的硅的含量为1.6~1.9%,铸件牌号越高,导轨越厚实,选取范围中的较低值,反之,选取较高值;
2.3锰
锰作为五大元素中唯一的金属元素,在铸铁中起着不可替代的作用。
由于锰有增加并细化珠光体的作用,所以适当提高锰的含量会提高铸件的强度和硬度,在机床类灰铸铁件中,比较适宜的锰的含量为0.8~1.2%,铸件牌号越高,导轨越厚实,,选取范围中的较高值,反之,选取较低值。
2.4硫和磷
硫和磷应该算是铸铁中的控制元素。
随着电炉熔炼的普及,人们对硫的作用有了更深刻地认识,在灰铸铁中,硫的含量并不是越低越好,硫过分低,铁水中的高熔点硫化物偏少,形核核心就少,炉前处理效果就较差,铸件性能可能就比较差。
对于电炉熔炼,硫比较适宜的成分为0.06~0.08%,必要时,采用增硫剂增硫;对于冲天炉熔炼,硫比较适宜的成分为0.06~0.10%.
铸铁中的磷主要来自于炉料,要想控制磷的含量,就必须控制每一种原材料中磷的含量,比如控制锰铁中磷的含量。
由于机床类灰铸铁件都是有致密性要求的铸件,所以磷的含量需低于0.06%[2]。
2.5铬
铬是灰铸铁生产中使用最广泛的合金元素,它是强的碳化物稳定元素,增加白口倾向,稳定渗碳体[2],所以,灰铸铁中加入铬,可以提高铸件的硬度,提高耐磨性[2]。
在机床类灰铸铁中,铬一般的加入量为0.15~0.35%,铸件牌号越高,导轨越厚实,选取范围中的较高值,反之,选取较低值。
如果在炉前加入,铬铁的粒度最好控制在10mm以内,出铁温度不应低于1480℃,确保铬铁的充分吸收。
另外由于铬是较强的碳化物形成元素[3],容易在加工表面形成硬质点,影响加工,所以日本和韩国客户不允许在机床类灰铸铁件中加铬。
2.6铜
铜在铸铁中能稳定珠光体[2]。
在合金元素中,铜应该是比较温和的合金元素,副作用比较小。
在机床类灰铸铁件中,铜一般的加入量为0.3~0.5%。
2.7锡
锡是强的碳化物稳定元素,它能增加碳化物,消除铁素体。
有资料认为,灰铸铁加锡后,石墨组织得到改善,呈中等片状的A型分布,从而使机械性能得到很大的提高。
珠光体数量的增加细化,使铸铁的工作表面的耐磨性提高。
在机床类灰铸铁件,锡的加入量一般为0.02~0.05%。
2.8锑
锑是强烈促进形成珠光体元素,促进珠光体生成的能力是锡的2倍[2],从这一点看,可以说锑是提高铸件硬度的“特效药”,但是必须谨慎使用,由于锑没有细化晶粒和组织的作用,所以加工后加锑铸件的表面光洁度较差,虽然硬度可能并不低;而且加工后与加工前比较,硬度下降比较明显,甚至会达到20~30HBS。
在机床类灰铸铁件,锑的加入量一般为0.02~0.04%。
3.结论
机床类灰铸铁件有着更高的性能要求,为生产出合格的铸件,合理的配料是基础,配料中必须确保足够的废钢比例;合适的成分选择是关键,除了五大元素,适当辅以必要的合金元素;稳定、准确的加料,规范的熔化操作是保障。
也只有这样,才能生产出成分稳定、性能合格、符合质量要求的机床类灰铸铁件。
[1] 马敬仲数控机床的高速发展与机床铸件标准铸造行业系列会议—机床铸件篇论文集2007
[2] 张伯明铸造手册.铸铁第3版机械工业出版社2011
[3] 陆文华铸铁及其熔炼机械工业出版社1981。