SMT制程不良原因及改善措施精选文档
SMT不良品整改报告

SMT不良品整改报告第一篇:SMT不良品整改报告不良品统计分析报告篇四:smt不良品控制篇五:不合格品处理流程不合格品处理流程一、原材料来料不良处理方案1.原材料经外协厂依据mil-std-105e 一般检验水准ⅱ级aql(0.4 0.65)一次抽样检验标准进行检验,iqc检验不良的,由外协厂iqc开具来料异常报告,反馈至我司品质,品质进行对存在异常的原材料进行确认。
2.确认完成后,一般确认的结果分为四种:可接受,可特采,不可接受,需进步确认。
2.1 我司品管确认可接受的原材料,需要在外协厂 iqc提供的异常报告中写明可具体情况,并签字确认,外协工厂根据我司给的确认结果进行接受。
2.2 我司品管确认可特采使用的原材料,需在外协厂 iqc的异常报告中写明可特采接受的依据或原因,并与外协工厂的品质一起进行特采的结果确认的实施。
对于我司确认可特采的原材料,外协厂存在异议的,按以下执行:2.2.1若所执行的特采没有造成外协厂的工时浪费、不良严重增加等不良状况,可直接要求外协厂配合执行特采的动作。
2.2.2若所执行的特采会造成外协厂的工时浪费、不良严重增加等不良状况,但仍需继续执行特采动作的,可允许外协工厂申请工时浪费或人力浪费的费用和因此类不良造成的相关物料的损耗。
2.2.3特采动作执行的过程中,由品质、工程并要求外协工厂一起跟进紧密跟进特采执行的全过程,防止问题的发生或扩大。
2.3我司品管确认不可接受的产品,确认不合格的主要责任方后,可按三种方式处理:退货,供方返工,外协厂协助返工。
2.3.1退货的原材料,由我司品管确认后,邮件或书面形式通知生管安排,由生管安排原材料所在的仓库或原材料的管理者将此不合格品退还供方,由供方安排处理。
2.3.2经确认要求供方进行返工的不合格品,由品管通知采购安排人员至外协厂进行返工,生管跟进返工进度。
2.3.3特殊情况下,需要外协厂安排返工的,由我司生管与外协厂相关管理进行协商安排返工,外协厂可要求申请返工费用,如责任在供方的话,此返工费用需要供方承担。
SMT不良分析及改善措施
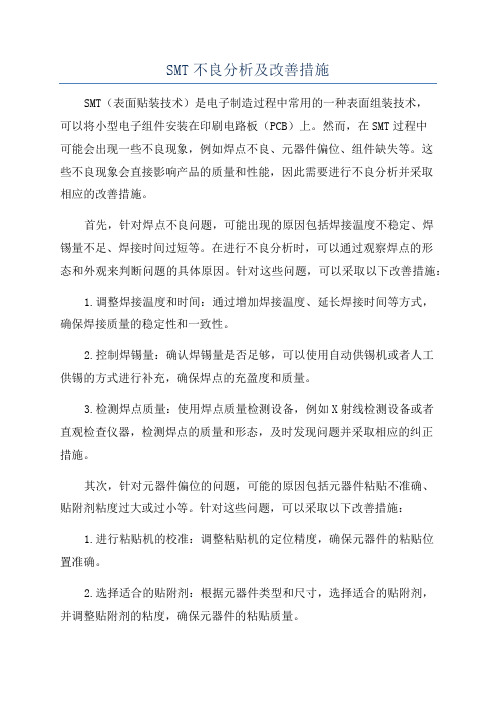
SMT不良分析及改善措施SMT(表面贴装技术)是电子制造过程中常用的一种表面组装技术,可以将小型电子组件安装在印刷电路板(PCB)上。
然而,在SMT过程中可能会出现一些不良现象,例如焊点不良、元器件偏位、组件缺失等。
这些不良现象会直接影响产品的质量和性能,因此需要进行不良分析并采取相应的改善措施。
首先,针对焊点不良问题,可能出现的原因包括焊接温度不稳定、焊锡量不足、焊接时间过短等。
在进行不良分析时,可以通过观察焊点的形态和外观来判断问题的具体原因。
针对这些问题,可以采取以下改善措施:1.调整焊接温度和时间:通过增加焊接温度、延长焊接时间等方式,确保焊接质量的稳定性和一致性。
2.控制焊锡量:确认焊锡量是否足够,可以使用自动供锡机或者人工供锡的方式进行补充,确保焊点的充盈度和质量。
3.检测焊点质量:使用焊点质量检测设备,例如X射线检测设备或者直观检查仪器,检测焊点的质量和形态,及时发现问题并采取相应的纠正措施。
其次,针对元器件偏位的问题,可能的原因包括元器件粘贴不准确、贴附剂粘度过大或过小等。
针对这些问题,可以采取以下改善措施:1.进行粘贴机的校准:调整粘贴机的定位精度,确保元器件的粘贴位置准确。
2.选择适合的贴附剂:根据元器件类型和尺寸,选择适合的贴附剂,并调整贴附剂的粘度,确保元器件的粘贴质量。
3.进行视觉系统的检测:使用视觉系统检测元器件的粘贴质量,如果发现问题,及时进行修正。
最后,针对组件缺失的问题,主要原因可能是元器件的供应链问题,例如供应商发货错误或者内部库存管理不善。
针对这些问题,可以采取以下改善措施:1.加强供应商管理:与供应商建立良好的合作关系,加强供应链的沟通和管理,确保元器件的质量和数量。
2.设立内部库存管理系统:建立完善的库存管理系统,确保元器件的采购、入库、出库等流程的可控性和准确性。
3.进行组件跟踪和检测:使用条码或者RFID等技术,对每个组件进行跟踪和检测,确保组件的精确性和完整性。
SMT不良产生原因及对策

SMT不良产生原因及对策SMT(Super Multi-vision Test)不良产生原因及对策是电子制造行业中一个重要的话题。
在电子制造过程中,SMT是一种常用的组装技术,它涉及到大量的元件的高速表面安装。
然而,在实践中,SMT不良很常见,它可能会导致产品质量下降、生产效率降低以及成本增加。
因此,了解不良产生的原因,并采取相应的对策,对于提高SMT生产的质量和效率至关重要。
1.材料问题:SMT使用的元件和焊料可能存在质量问题。
元件可能存在焊盘偏移、引脚损坏、尺寸不一致等问题。
焊料可能存在含波点、气孔等质量问题。
2.设备问题:SMT设备的故障或不当使用也可能引起不良。
设备的加热、输送、贴装等环节可能存在问题,导致元件无法准确地安装在PCB上。
3.操作问题:操作人员操作不当、技术不到位也是不良产生的原因之一、操作人员可能存在操作失误、程序设置错误、参数调整不当等问题。
为了解决SMT不良的问题,可以采取以下对策:1.强化质量管理:确保元件和焊料的质量。
从可靠的供应商购买元件和焊料,并对其进行严格的质量检查。
对于质量问题严重的供应商,需要采取相应的措施,如更换供应商。
2.维护和保养设备:定期对SMT设备进行维护和保养,以确保其正常运行。
培训操作人员,让他们掌握设备的正确使用方法,并确保操作人员具备相关的技术能力。
3.检查和修正操作问题:建立操作规程,并进行培训,确保操作人员按照规程操作。
同时,建立检查机制,及时发现和纠正操作问题。
定期举行会议,分享操作问题和经验,以便全员学习和提高。
4.强化数据分析和改进活动:建立良好的数据收集和分析体系,及时发现生产过程中的问题,并采取改进措施。
定期评估数据,评估改进措施的效果,及时调整和完善。
5.推行持续改进:将持续改进的理念贯穿于整个SMT生产过程中。
不断寻找不良产生的原因,通过改进工艺流程、优化设备和培训操作人员等方式,降低不良的发生率。
总结起来,SMT不良产生的原因有材料问题、设备问题和操作问题等。
SMT制程不良原因及改善对策

短路
产生原因
1、钢网与PCB板间距过大导致锡膏印刷过 厚短路; 2、元件贴装高度设置过低将锡膏挤压导 致短路; 3、回焊炉升温过快导致; 4、元件贴装偏移导致; 5、钢网开孔不佳(厚度过厚,引脚开孔 过长,开孔过大); 6、锡膏无法承受元件重量; 7、钢网或刮刀变形造成锡膏印刷过厚; 8、锡膏活性较强; 9、空贴点位封贴胶纸卷起造成周边元件 锡膏印刷过厚; 10、回流焊震动过大或不水平; 11、钢网底部粘锡; 12、QFP吸咀晃动贴装偏移造成短路。
1、PCB 板上有异物; 2、胶量过多; 3、红胶使用时间过久; 4、锡膏中有异物; 5、炉温设置过高或反面元件过重; 6、机器贴装高度过高。
改善对策
1、印刷前清洗干净; 2、调整印刷机或点胶机; 3、更换新红胶; 4、印刷过程避免异物掉过去; 5、调整炉温或用纸皮垫着过炉; 6、调整贴装高度。
错件
改善对策
1、调整回焊炉温度或链条速度; 2、调整回焊度回焊区温度; 3、更换新锡膏。
偏移
产生原因
1、印刷偏移; 2、机器夹板不紧造成贴偏; 3、机器贴装座标偏移; 4、过炉时链条抖动导致偏移; 5、MARK点误识别导致打偏; 6、NOZZLE中心偏移,补偿值偏移; 7、吸咀反白元件误识别; 8、机器X轴或Y轴丝杆磨损导致贴装 偏移; 9、机器头部滑块磨损导致贴偏; 10、驱动箱不良或信号线松动; 11、783或驱动箱温度过高; 12、MPA3吸咀定位锁磨损导致吸咀 晃动造成贴装偏移。
直立
产生原因
1、铜铂两边大小不一产生拉力不均; 2、预热升温速率太快; 3、机器贴装偏移; 4、锡膏印刷厚度不均; 5、回焊炉内温度分布不均; 6、锡膏印刷偏移; 7、机器轨道夹板不紧导致贴装偏移; 8、机器头部晃动; 9、锡膏活性过强; 10、炉温设置不当; 11、铜铂间距过大; 12、MARK点误照造成元悠扬打偏; 13、料架不良,元悠扬吸着不稳打偏; 14、原材料不良; 15、钢网开孔不良; 16、吸咀磨损严重; 17、机器厚度检测器误测。
SMT制程不良原因及改善对策

SMT制程不良原因及改善对策SMT制程(Surface Mount Technology)是一种常用的电子组装技术,广泛应用于电子产品的制造过程中。
然而,由于各种原因所引起的不良现象在SMT制程中时有发生。
本文将讨论SMT制程不良原因以及改善对策。
1.焊接不良:焊接不良可以导致焊点虚焊、焊接断裂等问题。
常见的原因包括焊接温度不够、焊接时间不足、焊接设备不稳定等。
改善对策包括提高焊接设备的质量和稳定性、增加焊接温度和时间的控制精度等。
2.贴装不良:贴装不良可以导致元件偏移、元件漏贴等问题。
常见的原因包括贴装位置错误、贴装头磨损、胶垫损坏等。
改善对策包括提高贴装机的精度和稳定性、定期更换贴装头和胶垫等。
3.元件损坏:元件在SMT制程中容易受到机械损伤、电静电等因素的影响而受损。
改善对策包括提供合适的防护措施,如使用防静电设备、增加元件存储和运输的保护等。
4.焊盘不良:焊盘不良可以导致焊点接触不良、导致电路连通性问题。
常见的原因包括锡膏质量不佳、焊盘形状不准确等。
改善对策包括使用高质量的锡膏、提高焊盘生产过程的精度等。
5.引脚弯曲:引脚弯曲会导致元件无法正确插入或连接。
常见的原因包括元件存储和运输过程中引脚受到碰撞、搬运过程中的不当操作等。
改善对策包括提供合适的存储和运输保护措施、培训操作人员正确操作等。
改善SMT制程不良有很多对策,下面列举了其中一些常见的:1.提高设备的质量和稳定性:定期对设备进行维护和保养,确保其正常运行和精度稳定。
采用高质量的设备和工具,可大大降低不良率。
2.优化工艺参数:根据产品要求和设备特性,合理的调整焊接温度、焊接时间等工艺参数,以确保焊接效果和质量。
3.加强员工培训:提供必要的培训和指导,使操作人员熟悉SMT制程的原理和操作技巧,减少人为失误和操作不当导致的不良。
4.严格品质管理:建立完善的品质管理体系,包括设备校验、材料检测、过程控制等环节,确保产品质量稳定。
5.提供合适的存储和运输保护:对元件进行正确的存储和运输保护,避免机械损伤、静电损伤等因素导致的元件损坏。
SMT不良产生原因及解决办法[参考]
![SMT不良产生原因及解决办法[参考]](https://img.taocdn.com/s3/m/beb9436f65ce05087732139d.png)
Administrative Proceduresd管理办法Surface mount technology(SMT)不良发生原因及对策零件反向发生的原因:1:人工手贴贴反2:来料有单个反向3;机器FEEDER坏或FEEDER振荡过大(导致物料反向)振荡飞达4:PCB板上标明不清楚(导致作业员难以判别)5:机器程式视点错6:作业员上料反向(IC之类)7:核对首件人员大意,不能及时发现问题8:炉后QC也未能及时发现问题对策: 1:对作业员进行训练,使其可以正确的区分元器件方向2:对来料加强检测3:修理FEEDER及调整振荡FEEDER的振荡力度(并要求作业员对此物料进行方向查看)4:在出产傍边要是遇到难以判别元器件方向的。
必定要等工程部确认之后才可以批量出产,也可以SKIP5:工程人员要仔细核对出产程式,并要求对首件进行全检(特别要留意有极性的元件)6:作业员每次换料之后要求IPQC核对物料(包含元件的方向)并要求作业员每2小时有必要核对一次物料 7:核对首件人员必定要仔细,最好是2个或以上的人员进行核对。
(假如有专门的IPQC的话也可以要求每2小时再做一次首件)8:QC查看时必定要用放大镜仔细查看(对元件数量多的板尽量运用套版)少件(缺件)发生的原因:1:印刷机印刷偏位2:钢网孔被杂物或其它东西给堵塞(焊盘没锡而导致飞件) 3:锡膏放置时刻太久(元器件不上锡而导致元件飞件)4:机器Z轴高度反常5:机器NOZZLE上有残留的锡膏或胶水(此刻机器每次都可以辨认但物料放不下来导致少件)6:机器气压过低(机器在辨认元件之后气压低导致物料掉下) 7:置件后零件被NOZZLE吹气吹开8:机器NOZZLE类型用错9:PCB板的曲折度已超支(贴片后元件弹掉)10:元件厚度差异过大11:机器零件参数设置过错12:FEEDER中心方位偏移13:机器贴装时未顶顶针14:炉前总检磕碰坠落对策: 1:调整印刷机(要求印刷员对每一PCS印刷好的进行查看)2:要及时的清洗钢网(一般5-10PCS清洗一次)3:依照(锡膏贮存作业指导书)作业,锡膏在常温下放置必定不能超越24小时4:校对机器Z轴(不能使机器NOZZLE放置零件时Z轴离PCB板过高。
SMT制程不良原因及改善措施分析

14、机器贴装高度设置不当; 15、锡膏较薄导致少锡空焊; 16、锡膏印刷脱膜不良。 17、锡膏使用时间过长,活性剂挥发掉; 18、机器反光板孔过大误识别造成; 19、原材料设计不良; 20、料架中心偏移; 21、机器吹气过大将锡膏吹跑; 22、元件氧化; 23、PCB贴装元件过长时间没过炉,导致活性 剂挥发; 24、机器Q1.Q2轴皮带磨损造成贴装角度 偏信移过炉后空焊; 25、流拉过程中板边元件锡膏被擦掉造成 空焊; 26、钢网孔堵塞漏刷锡膏造成空焊。
产生原因
1、真空泵碳片不良真空不够造成缺件; 2、吸咀堵塞或吸咀不良; 3、元件厚度检测不当或检测器不良; 4、贴装高度设置不当; 5、吸咀吹气过大或不吹气; 6、吸咀真空设定不当(适用于MPA); 7、异形元件贴装速度过快; 8、头部气管破烈; 9、气阀密封圈磨损; 10、回焊炉轨道边上有异物擦掉板上元 件; 11、头部上下不顺畅; 12、贴装过程中故障死机丢失步骤; 13、轨道松动,支撑PIN高你不同; 14、锡膏印刷后放置时间过久导致地件无 法粘上。
产生原因
改善对策
1、更换活性较强的锡膏; 2、开设精确的钢网; 3、将来板不良反馈于供应商或钢网将焊 盘间距开为0.5mm; 4、调整刮刀压力; 5、将元件使用前作检视并修整; 6、调整升温速度90-120秒; 7、用助焊剂清洗PCB; 8、对PCB进行烘烤; 9、调整元件贴装座标; 10、调整印刷机; 11、松掉X、Y Table轨道螺丝进行调整; 12、重新校正MARK点或更换MARK点; 13、将网孔向相反方向锉大;
SMT制程不良原因及改善对策

PAD 离轨道边小 于3mm.
PAD氧化
未及时收板,PCB在回焊 炉中碰撞
零件过大过重
零件脚弯
人为手抹锡膏
零件厚度不均
备料时料带过紧
零件氧化
手放散料
异形零件
空气流通速度过快
手推撞板
焊盘上有异物
室温过高 锡膏印刷后硬化
PCB印刷后露置 空气中过久
人为手拨 缺锡
手摆料
PAD间距与组 件长度不符
零件与PAD不符
PCB
通风不畅
室内过于潮湿
温度高
手推撞板
零件
手碰零件
旧
超过
手放散料 缺乏教育训练
新工上线 缺乏责任感
反 破过 向 损周
期
锡 不 搅 使用 锡粉径 膏 均 拌 时间 粒过大
锡 膏
将锡膏加到钢网开口处
锡膏厚 短路
手印锡膏
有异 含 松 物 量香
锡 有锡 膏 水膏
手抹锡膏
印 手印台
零件间距离太近
稀 份内
钢网贴纸未贴好 手拨零件
(3) WHERE——何处?在哪里做?从 哪里入手?
(4) WHEN——何时?什么时间完成? 什么时机最适宜?
(5) WHO——谁?由谁来承担?谁来 完成?谁负责?
(6) HOW ——怎么做?如何提高效率? 如何实施?方法怎样?
(7) HOW MUCH——多少?做到什么 程度?数量如何?质量水平如何?费用产 出如何?
发明者用五个以w开头的英语单词和两 个以H开头的英语单词进行设问,发现解 决问题的线索,寻找发明 5W2H分析法思 路,进行设计构思,从而搞出新的发明项 目,这就叫做5W2H法。
(1) WHY——为什么?为什么要这么做? 理由何在?原因是什么?造成这样的结果 为什么?
SMT制程不良原因及改善对策

发明者用五个以w开头的英语单词和两 个以H开头的英语单词进行设问,发现解 决问题的线索,寻找发明 5W2H分析法思 路,进行设计构思,从而搞出新的发明项 目,这就叫做5W2H法。
(1) WHY——为什么?为什么要这么做? 理由何在?原因是什么?造成这样的结果 为什么?
(2) WHAT——是什么?目的是什么? 做什么工作?
13、PCB铜铂上有穿孔;
12、重新校正MARK点或更换MARK点;
13、将网孔向相反方向锉大;
空焊
14、机器贴装高度设置不当;
14、重新设置机器贴装高度;
15、锡膏较薄导致少锡空焊;
15、在网网下垫胶纸或调整钢网与PCB
16、锡膏印刷脱膜不良。
间距;
17、锡膏使用时间过长,活性剂挥发掉; 16、开精密的激光钢钢,调整印刷
(3) WHERE——何处?在哪里做?从 哪里入手?
(4) WHEN——何时?什么时间完成? 什么时机最适宜?
(5) WHO——谁?由谁来承担?谁来 完成?谁负责?
(6) HOW ——怎么做?如何提高效率? 如何实施?方法怎样?
(7) HOW MUCH——多少?做到什么 程度?数量如何?质量水平如何?费用产 出如何?
水平 角度
无尘布使用次
轨道 参数
钢网 钢网
开口 钢网
数过多
零件管制
内有 设定 排风 异物 不当 不通
张力 材质
规格 厚度
钢网
锡膏选
回焊炉
择不当
锡膏的管制 新旧锡膏混用
机器的保养
未依作业标 准书操作
温度设定 预热
不当
不足
轨道流板不畅撞板 手放零件方法不当
smt不良分析及改善措施
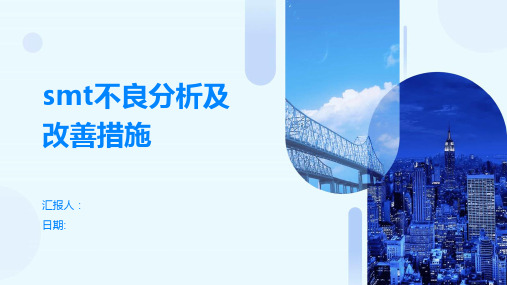
清洁保养
02
定期对设备表面进行清洁保养,保持设备整洁,防止灰尘、异
物等对设备造成损害。
润滑保养
03
按照设备制造商的推荐,定期对设备的运动部件进行润滑保养
,以减少磨损工艺文件,确保每个生产步骤都符合规范和标 准。
人员培训
对操作人员进行专业培训,确保他们熟悉设备的操作和维护,能 够及时发现并解决潜在问题。
总结词
PCB板的设计不合理可能会导致元件脱落、短路等问题。
详细描述
如果PCB板的线路设计不合理,可能会导致元件无法准确吸附在指定位置;如果 PCB板的焊盘设计不合理,则可能会导致短路或虚焊。因此,需要对PCB板的设 计进行严格审核和测试。
案例四:温度和湿度控制不当
总结词
温度和湿度控制不当可能会导致元件引脚氧化、焊接不良等问题。
工艺不良
温度异常
SMT生产线温度异常波动 ,导致零件贴装偏差、焊 接不良等
湿度异常
SMT生产线湿度异常波动 ,导致零件受潮、焊接不 良等
大气污染
SMT生产线大气污染严重 ,导致零件表面污染、焊 接不良等
管理不良
计划管理不良
生产计划不合理、生产安排不科 学等导致生产效率低下、产品质
量不稳定等不良现象
零件材质不良
零件材质不达标,如PCB 板材质不均、零件镀层不 均匀等
零件质量不良
零件本身存在质量问题, 如气泡、划痕等
设备不良
贴片机不良
贴片机精度下降、机械故障等导 致贴装位置偏差、零件损坏等不
良现象
印刷机不良
印刷机精度下降、机械故障等导致 印刷不均匀、印刷错误等不良现象
检测设备不良
检测设备精度下降、机械故障等导 致检测不准确、误判等不良现象
SMT制程常见异常分析

SMT制程常见异常分析SMT制程(表面贴装技术)是一种在电子元件制造中常用的制程技术,用于将电子元件贴装在印刷电路板(PCB)上。
然而,在SMT制程中,常会出现一些异常情况,如焊接不良、元件丢失等问题。
本文将针对SMT制程常见的异常进行分析。
1.焊接不良:焊接不良是SMT制程中常见的问题之一、焊接不良可能由于锡膏的质量问题、焊垫的尺寸偏差、焊接设备的操作不当等原因引起。
常见的焊接不良有焊接剪切、焊锡球、云母等问题。
焊接不良会导致元件与PCB之间的电连接不良,影响产品的性能和可靠性。
2.元件丢失:元件丢失是SMT制程常见的问题之一、元件丢失可能由于操作不当、元件自身缺陷、供应链问题等原因引起。
元件丢失会导致产品的功能性能下降,严重的情况下可能导致产品不能正常工作。
3.印刷问题:印刷问题是SMT制程中常见的问题之一、印刷问题可能由于锡膏的质量问题、印刷设备的操作不当、PCB的表面不平整等原因引起。
常见的印刷问题有锡膏剪切、印刷偏移、印刷污染等问题。
印刷问题会导致焊接质量不良,影响产品的性能和可靠性。
4.质量控制问题:质量控制问题是SMT制程中常见的问题之一、质量控制问题可能由于生产过程中缺乏足够的质量控制措施、操作工人技术水平不足、设备维护不良等原因引起。
质量控制问题会导致产品的性能和可靠性不稳定,严重的情况下可能导致产品不合格。
针对SMT制程常见的异常,可以采取以下措施进行分析和解决:1.异常分析:对于出现的异常情况,首先要进行详细的分析,排查出具体的原因。
可以通过观察异常的形态特征、分析生产过程中的操作记录、检查原材料的质量等方式进行分析。
2.数据收集:在SMT制程中可以采集相关的数据,如焊接温度、湿度、气压等参数,以及生产过程中的记录。
这些数据可以用于分析异常情况的原因,帮助找出潜在的问题。
3.过程优化:针对分析结果,可以进行制程的优化。
例如,对于焊接不良问题,可以优化焊接设备的参数,选择质量更好的焊接材料,加强操作工人的培训等。
smt不良分析及改善措施

材料问题
原材料缺陷:如PCB板、电子元器件等原材料存 在缺陷,将直接影响SMT产品的品质。
使用过期材料:使用过期的原材料进行生产,可 能导致产品性能不稳定,产生不良品。
储存不当:原材料在储存过程中未按照要求进行 保管,可能导致性能受损,进而影响SMT产品质 量。
针对以上原因,可以采取相应的改善措施,如加 强员工培训、规范操作流程、定期维护设备、严 格把控原材料质量等,以降低SMT不良品率,提 高产品质量和生产效率。
03
SMT不良改善措施
人员培训和管理
提高技能水平
定期举办技术培训课程,提升员工在SMT操作、维护、质检等方面 的技能水平,确保员工熟悉并掌握设备操作规程和质量标准。
严格考核与奖惩制度
建立员工绩效考核体系,对操作规范、良品率等方面进行考核,奖 励优秀员工,对操作不规范、产品质量差的员工进行惩罚和再培训 。
强化质量意识
通过定期的质量教育活动,增强员工的质量意识,使其充分认识到产 品质量对企业和个人的重要性。
设备维护和管理
制定维护计划
根据设备使用情况和维护要求,制定合理的设备维护计划,确保 设备按时进行保养、检修,减少设备故障。
监控设备运行状况
通过设备自带的监测系统或额外安装传感器等方式,实时监测设备 运行状况,及时发现异常,避免故障扩大。
• 焊接不良:包括冷焊、虚焊、 焊盘脱落等问题,主要由于焊 接温度、时间等参数设置不当 或焊接材料质量差引起。
• 基板不良:包括基板变形、裂 纹、污染等,可能由基板材料 、设计或生产工艺导致。
SMT不良现象对生产的影响
01
02
03
生产效率下降
SMT不良现象会增加检修 、返工等工作量,降低生 产效率。
SMT制程不良原因及改善FOXCONN

錫膏拉尖(狗耳朵):鋼板開孔不光滑 , 鋼板開孔尺寸過小 , 脫模速度不合理, PCB焊點受污染 , 錫膏品質異常 , 鋼板 擦拭不幹淨 少錫:板子上錫膏量不足
⑥元器件與錫膏接觸壓力過大
解決方法:
①選用相對粘度較高的錫膏,一般來說,含量在 85—87%之間橋連現象較多,至少合金含量要在90% 以上。 ②調整合適的溫度曲線 ③在回流焊之前檢查錫膏與器件接觸點是否合適 ④調整鋼網開孔比例(減少10%)與鋼網厚度 ⑤調整貼片時的壓力和角度
四 常見印刷不良的診斷及處理
因素二:鋼板(範本)的製作及開口
a. 鋼板的開口
我們一般根據印製板上的焊盤來製作鋼板(範本),所 以鋼板的開口就是焊盤的大小。在印刷錫膏時,容易把錫 膏印刷到阻焊層上,從而在再流焊時產生錫珠。因此,我 們可以這樣來製作鋼板,把鋼板的開口比焊盤的實際尺寸 減小10%,另外,可以更改開口的外形來達到理想的效果。
其他外界因素的影響:
一般錫膏印刷時的最佳溫度為25℃± 3 ℃ ,濕度為相 對濕度40%-60%,溫度過高,使錫膏的黏度降低,容易 產生“塌落”,濕度過高,錫膏容易吸收水分,容易發 生飛濺,這都是引起錫珠的原因。另外,印製板暴露在 空氣中較長的時間會吸收水分,並發生焊盤氧化,可焊 性變差。
二 立碑問題分析及處理
b. 鋼板的厚度
錫膏在印製板上的印刷厚度。錫膏印刷後的厚度是漏板 印刷的一個重要參數,通常在0.13mm-0.17mm之間。錫膏過 厚會造成錫膏的“塌落”,促進錫珠的產生。
smthome_制程不良及改善对策

影響性 1.造成電路上焊接不良,不易檢測。 2.嚴重時電路無法導通,電氣功能失效。 造成原因 1.不正確之取、放PWB。 2.設計時產生不當之焊接機械應力。 3.剪腳動作錯誤。 4.剪腳過長。 5.錫少。
補救處置 1.PWB取、放接不能同時抓取零件,且須 輕取、輕放。 2.變更設計。 3.剪腳時不可扭彎拉扯。 4.加工時先控制線腳長度,插件避免零件 傾倒。 5.調整錫爐或重新補焊。
漏焊
特點
NG
NG
零件線腳四週未與焊錫熔接及包覆。 允收標準 無此現象即為允收,若發現即需二次 補焊。
影響性 電路無法導通,電氣功能無法顯現, 偶爾出現焊接不良,電氣測試無法檢測。 造成原因 1.助焊劑發泡不均勻,泡沫顆粒太大。 2.助焊劑未能完全活化。 3.零件設計過於密集,導致錫波陰影效 應。 4.PWB變形。 5.錫波過低或有攪流現象。 6.零件腳受污染。 7.PWB氧化、受污染或防焊漆沾附。
補救處置 1.增加預熱溫度、降低過爐速度、提高錫 槽溫度來增加零件之受熱及吃錫時間。 2.裁短線腳。 3.調高溫度或更換導熱面積較大之烙鐵 頭。
பைடு நூலகம்
錫洞
特點
NG
NG
於焊點外表上產生肉眼清晰可見之貫 穿孔洞者。 允收標準 無此現象即為允收,若發現即需二次 補焊。
影響性 1.電路無法導通。 2.焊點強度不足。 造成原因 1.零件或PWB之焊墊銲錫性不良。 2.焊墊受防焊漆沾附。 3.線腳與孔徑之搭配比率過大。 4.錫爐之錫波不穩定或輸送帶震動。 5.因預熱溫度過高而使助焊劑無法活化。 6.導通孔內壁受污染或線腳度錫不完整。 7.AI零件過緊,線腳緊偏一邊。
補救處置 1.要求供應商改善材料焊性。 2.刮除焊墊上之防焊漆。 3.縮小孔徑。 4.清洗錫槽、修護輸送帶。 5.降低預熱溫度。 6.退回廠商處理。 7.修正AI程式,使線腳落於導通孔中央。
【SMT】制程宝典--SMT常见不良原因分析与改善对策

作业
方法
印刷后锡膏被人碰到.
要求作业员小心作业.
教导并监督作业员小心作业.
贴片位移,炉前作业员用手拨正时形成短路.
用防焊胶纸粘起零件,让机器重打.
让机器打正,昼量不用手拨.
因调机(机器故障)时间过长,达??分钟,此板印刷后等待贴片时间达??分钟,Flux活化剂有所挥发,贴片时的压力造成锡膏瘫蹋,因pitch为0.5mm,造成短路.
IC脚弯? (附上图片)
1.更换另一盘料.
2.记录厂牌,Data Code,保留不良样品,知会QE、IQC.
1.上料前检查. 3.通知QE,IQC,要求供货商改善.
第二章:空焊
原因分析
临时对策
永久对策
环境
?月?日?点的车间温度(或湿度)超标,已达到??.
1.马上通知工务组改善.
2.E-MAIL给管理部及品保部.
临时对策
永久对策
环境
?月?日?点的车间温度(或湿度)超标,已达到??.
1.马上通知工务组改善.
2.E-MAIL给管理部及品保部.
1.随时注意车间温度(或湿度)并作好记录,如发现超标立即通知工务组.
2.E-MAIL给管理部及品保部.
锡膏
锡膏太稀.
1.刮去上层的一部份flux.
2换另一瓶新锡膏.
1.与锡膏厂商联系,要求改善锡膏品质, 2.换别的厂牌的锡膏.
Fine Pitch IC PAD位于板边,印刷时太靠近夹轨. (附上图片)
调宽印刷机轨道,由原来的??mm改为??mm.
反馈给PE、QE,与PCB客户协商改善方案.
锡膏厚度过高.(附上数据)
- 1、下载文档前请自行甄别文档内容的完整性,平台不提供额外的编辑、内容补充、找答案等附加服务。
- 2、"仅部分预览"的文档,不可在线预览部分如存在完整性等问题,可反馈申请退款(可完整预览的文档不适用该条件!)。
- 3、如文档侵犯您的权益,请联系客服反馈,我们会尽快为您处理(人工客服工作时间:9:00-18:30)。
产;
? 26、清洗钢网并用风枪吹钢网。
3
短路
? 产生原因
? 1、钢网与 PCB板间距过大导致锡膏印刷过 厚短路;
? 2、元件贴装高度设置过低将锡膏挤压导 致短路;
? 3、回焊炉升温过快导致; ? 4、元件贴装偏移导致; ? 5、钢网开孔不佳(厚度过厚,引脚开孔
过长,开孔过大); ? 6、锡膏无法承受元件重量; ? 7、钢网或刮刀变形造成锡膏印刷过厚; ? 8、锡膏活性较强; ? 9、空贴点位封贴胶纸卷起造成周边元件
锡膏印刷过厚; ? 10、回流焊震动过大或不水平; ? 11、钢网底部粘锡; ? 12、QFP吸咀晃动贴装偏移造成短路。
? 不良改善对策
? 1、调整钢网与 PCB 间距0.2mm-1mm ; ? 2、调整机器贴装高度,泛用机一般调
整到元悠扬与吸咀接触到为宜(吸 咀下将时); ? 3、调整回流焊升温速度 90-120sec ; ? 4、调整机器贴装座标; ? 5、重开精密钢网,厚度一般为 0.12mm-
0.15mm ; ? 6、选用粘性好的锡膏; ? 7、更换钢网或刮刀; ? 8、更换较弱的锡膏; ? 9、重新用粘性较好的胶纸或锡铂纸贴; ? 10、调整水平,修量回焊炉; ? 11、清洗钢网,加大钢网清洗频率; ? 12、更换 QFP吸咀。
4
直立
? 产生原因
? 1、铜铂两边大小不一产生拉力不均; ? 2、预热升温速率太快; ? 3、机器贴装偏移; ? 4、锡膏印刷厚度不均; ? 5、回焊炉内温度分布不均; ? 6、锡膏印刷偏移; ? 7、机器轨道夹板不紧导致贴装偏移; ? 8、机器头部晃动; ? 9、锡膏活性过强; ? 10、炉温设置不当; ? 11、铜铂间距过大; ? 12、MARK点误照造成元悠扬打偏; ? 13、料架不良,元悠扬吸着不稳打偏; ? 14、原材料不良; ? 15、钢网开孔不良; ? 16、吸咀磨损严重; ? 17、机器厚度检测器误测。
? 1、更换活性较强的锡膏; ? 2、开设精确的钢网; ? 3、将来板不良反馈于供应商或钢网将焊
盘间距开为0.5mm; ? 4、调整刮刀压力; ? 5、将元件使用前作检视并修整; ? 6、调整升温速度90-120秒;
? 9、机器贴装偏移;
? 7、用助焊剂清洗PCB;
? 10、锡膏印刷偏移;
? 8、对PCB进行烘烤;
? 11、机器夹板轨道松动造成贴装偏移; ? 9、调整元件贴装座标;
?
12 、 MARK 点误照造成元件打偏,导致空焊;
?
10、调整印刷机;
? 13、PCB铜铂上有穿孔;
? 11、松掉X、Y Table轨道螺丝进行调整;
? 12、重新校正MARK点或更换MARK点;
? 13、将网孔向相反方向锉大;
2
5
缺件
? 产生原因
? 1、真空泵碳片不良真空不够造成缺件; ? 2、吸咀堵塞或吸咀不良; ? 3、元件厚度检测不当或检测器不良; ? 4、贴装高度设置不当; ? 5、吸咀吹气过大或不吹气; ? 6、吸咀真空设定不当(适用于 MPA); ? 7、异形元件贴装速度过快; ? 8、头部气管破烈; ? 9、气阀密封圈磨损; ? 10、回焊炉轨道边上有异物擦掉板上元
? 改善对策
? 1、开钢网时将焊盘两端开成一样; ? 2、调整预热升温速率; ? 3、调整机器贴装偏移; ? 4、调整印刷机; ? 5、调整回焊炉温度; ? 6、调整印刷机; ? 7、重新调整夹板轨道; ? 8、调整机器头部; ? 9、更换活性较低的锡膏; ? 10、调整回焊炉温度; ? 11、开钢网时将焊盘内切外延; ? 12、重新识别 MARK点或更换 MARK点; ? 13、更换或维修料架; ? 14、更换 OK材料; ? 15、重新开设精密钢网; ? 16、更换 OK吸咀; ? 17、修理调整厚度检测器。
空焊
? 14、机器贴装高度设置不当;
? 14、重新设置机器贴装高度;
? 15、锡膏较薄导致少锡空焊;
? 15、在网网下垫胶纸或调整钢网与 PCB
? 16、锡膏印刷脱膜不性剂挥发掉;
? 16、开精密的激光钢钢,调整印刷
? 18、机器反光板孔过大误识别造成;
机;
? 19、原材料设计不良;
? 17、用新锡膏与旧锡膏混合使用;
? 20、料架中心偏移;
? 18、更换合适的反光板;
? 21、机器吹气过大将锡膏吹跑;
? 19、反馈 IQC联络客户;
? 22、元件氧化;
? 20、校正料架中心;
? 23、PCB贴装元件过长时间没过炉,导致活性 ? 21、将贴片吹气调整为 0.2mm/cm 2;
件; ? 11、头部上下不顺畅; ? 12、贴装过程中故障死机丢失步骤; ? 13、轨道松动,支撑 PIN 高你不同; ? 14、锡膏印刷后放置时间过久导致地件无
法粘上。
? 改善对策
? 1、更换真空泵碳片,或真空泵; ? 2、更换或保养吸膈; ? 3、修改元悠扬厚度误差或检修厚度检测
器; ? 4、修改机器贴装高度; ? 5、一般设为 0.1-0.2kgf/cm 2; ? 6、重新设定真空参数,一般设为 6以下; ? 7、调整异形元件贴装速度; ? 8、更换头部气管; ? 9、保养气阀并更换密封圈; ? 10、打开炉盖清洁轨道; ? 11、拆下头部进行保养; ? 12、机器故障的板做重点标示; ? 13、锁紧轨道,选用相同的支撑 PIN; ? 14、将印刷好的 PCB 及时清理下去。
SMT制程 不良原因及改善措施
制作:神 山 讲师:李日并 1
SMT制程不良原因及改善对策
空焊
? 产生原因
? 改善对策
? 1、锡膏活性较弱; ? 2、钢网开孔不佳; ? 3、铜铂间距过大或大铜贴小元件; ? 4、刮刀压力太大; ? 5、元件脚平整度不佳(翘脚、变形) ? 6、回焊炉预热区升温太快; ? 7、PCB铜铂太脏或者氧化; ? 8、PCB板含有水份;
剂挥发;
? 22、吏换 OK之材料;
? 24、机器 Q1.Q2 轴皮带磨损造成贴装角度
? 23、及时将PCB‘A过炉,生产过程中
偏信移过炉后空焊;
避免堆积;
? 25、流拉过程中板边元件锡膏被擦掉造成 ? 24、更换 Q1或Q2皮带并调整松紧度;
空焊;
? 25、将轨道磨掉,或将 PCB转方向生
? 26、钢网孔堵塞漏刷锡膏造成空焊。