20 硫酸
304耐硫酸腐蚀对照表

304耐硫酸腐蚀对照表
一、实验材料
1. 304不锈钢
二、实验条件
1. 硫酸浓度:20%,40%,60%,80%
2. 温度:常温,50℃,80℃
3. 腐蚀时间:24小时,48小时,72小时,96小时
三、实验结果
1. 腐蚀速率:以304不锈钢在不同条件下的失重率表示
2. 腐蚀类型:化学腐蚀、电化学腐蚀等
3. 腐蚀程度:轻微、中等、严重
四、对照实验
1. 将304不锈钢分别置于不同浓度、温度和时间的硫酸中,观察其耐腐蚀性能的变化。
2. 比较相同条件下,304不锈钢与其他金属材料的耐腐蚀性能差异。
3. 分析硫酸浓度、温度和时间对304不锈钢耐腐蚀性能的影响。
五、结论
根据实验结果,得出以下结论:
1. 随着硫酸浓度的增加,304不锈钢的腐蚀速率逐渐加快,腐蚀程度加重。
2. 随着温度的升高,304不锈钢的腐蚀速率也加快,腐蚀程度加重。
3. 随着时间的延长,304不锈钢的腐蚀速率和腐蚀程度也逐渐加重。
4. 通过对照实验,可以发现304不锈钢在硫酸中的耐腐蚀性能与其他金属材料相比具有一定的优势,但也存在一定的局限性。
因此,在实际应用中,应充分考虑各种因素对304不锈钢耐腐蚀性能的影响,并采取相应的防护措施。
10-20 % 硫酸 250℃ 用什么材料

10%~20% 稀硫酸,250度用什么材料?[讨论]国内石墨材质的设备使用温度一般达不到这么高,因此硫酸输送泵的材质一般选择:不锈钢(SUS316 、SUS316L) :温度40 ℃以下,浓度20% 左右;904L钢:适于温度40~60 ℃、浓度20~75% ;温度80 ℃、浓度60% 以下;高硅铸铁(STSi15R) :室温至90 ℃之间各种浓度;纯铅、硬铅:室温的各种温度;S-05 钢(0Cr13Ni7Si4) 90 ℃以下的浓硫酸,高温浓硫酸(120~150 ℃);普通碳钢室温70% 以上的浓硫酸;铸铁:温度为室温的浓硫酸;蒙乃尔、金属镍、因可耐尔:中温中等浓度的硫酸钛钼合金(Ti-32Mo ):沸点]以下、60% 的硫酸和50 ℃以下、98% 的硫酸;哈氏合金B 、D :100 ℃以下、75% 的硫酸;哈氏合金C :100 ℃左右的各种温度镍铸铁(STNiCr202) :室温60~90% 的硫酸。
用钽材或者是铌材都可以的。
就我个人认为也应该选用内称复合材料,比如楼上所说内称玻璃钢、石墨等,毕竟酸度高、温度高一般金属材质是经不起长期使用的,而且投资也高,现在复合材料制作工艺好应该没有问题。
但是四氟的可能不行。
是的,钽和铌是可以的,但造价不是一般的昂贵.钛、锆、铌、钽金属在硫酸中的应用Randy Scheel,P.E.Wah Chang摘要根据硫酸浓度和温度的变化,总结了活性金属钛、锆,难熔金属铌、钽在不同浓度和不同温度硫酸中的耐蚀性。
钛仅被用于低浓度硫酸中,铌可用于低于沸点的大部分浓度范围的硫酸中,钽可用于所有浓度范围且温度高于沸点的硫酸中,钽40铌合金可用于所有浓度范围的硫酸中,但使用温度低于钽,高于铌。
锆可用于浓度低于70%的硫酸中,使用温度至沸点或沸点以上。
用于硫酸的最佳金属材料的选择应考虑操作条件,寿命周期中的维修成本及停车损失。
设计者还须考虑温度、浓度,杂质等可能造成不利于金属材料耐蚀性的变化,综合分析后方可作出最后选择使用的是那种金属材料。
20%硫酸亚铁 溶液 计算

20%的硫酸亚铁溶液是指每100mL水溶液中含有20g硫酸亚铁(FeSO4·7H2O)。
如果要计算一定体积的20%硫酸亚铁溶液中含有多少克硫酸亚铁,可以按照以下步骤进行:
1. 确定要计算的溶液体积,例如500mL。
2. 计算这个体积的溶液中含有的硫酸亚铁质量,公式为:质量 = 体积 ×浓度。
其中,
浓度可以用百分数表示,即20%可以写成0.2。
因此,计算公式为:质量 = 500mL ×
0.2 = 100g。
因此,500mL的20%硫酸亚铁溶液中含有100g硫酸亚铁。
需要注意的是,硫酸亚铁溶液在储存、使用过程中需要注意安全,避免接触皮肤和吸
入气体等操作不当造成伤害。
20%硫酸亚铁密度
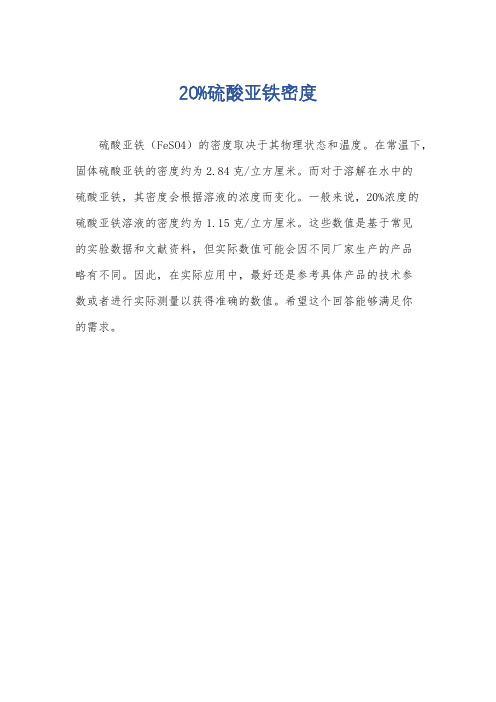
20%硫酸亚铁密度
硫酸亚铁(FeSO4)的密度取决于其物理状态和温度。
在常温下,固体硫酸亚铁的密度约为2.84克/立方厘米。
而对于溶解在水中的
硫酸亚铁,其密度会根据溶液的浓度而变化。
一般来说,20%浓度的
硫酸亚铁溶液的密度约为1.15克/立方厘米。
这些数值是基于常见
的实验数据和文献资料,但实际数值可能会因不同厂家生产的产品
略有不同。
因此,在实际应用中,最好还是参考具体产品的技术参
数或者进行实际测量以获得准确的数值。
希望这个回答能够满足你
的需求。
不同温度下硫酸密度对照表

不同温度下硫酸密度对照表
不同温度下硫酸密度对照表
不同温度下硫酸密度对照表
不同温度下硫酸密度对照表
不同温度下硫酸密度对照表
不同温度下硫酸密度对照表
不同温度下硫酸密度对照表
不同温度下硫酸密度对照表
不同温度下硫酸密度对照表
不同温度下硫酸密度对照表
不同温度下硫酸密度对照表
不同温度下硫酸密度对照表
不同温度下硫酸密度对照表
不同温度下硫酸密度对照表
不同温度下硫酸密度对照表
不同温度下硫酸密度对照表
不同温度下硫酸密度对照表
不同温度下硫酸密度对照表。
- 1、下载文档前请自行甄别文档内容的完整性,平台不提供额外的编辑、内容补充、找答案等附加服务。
- 2、"仅部分预览"的文档,不可在线预览部分如存在完整性等问题,可反馈申请退款(可完整预览的文档不适用该条件!)。
- 3、如文档侵犯您的权益,请联系客服反馈,我们会尽快为您处理(人工客服工作时间:9:00-18:30)。
4.1.2.4 焙烧工艺条件
焙烧温度:850~950℃。
炉底压力:9-12MPa。
炉气含SO2:10-14%。
沸腾区风速:0.3-3.5m•s-1。
实际加入空气量=1.2理论空气用量。
气体在沸腾炉内的停留时间≈10s。
4.1.3 炉气的净化与干燥
SO2
焙 烧 炉 气
矿 尘
堵塞管道,覆盖催 化剂表面降低活性 SO3与水蒸气形成酸雾,腐蚀 管道设备,降低催化剂的活性
第 4章 无机大宗化学品
4.1 硫酸 Vitriolic acid
4.1.1 概述 4.1.2 从硫铁矿制二氧化硫炉气 4.1.3 炉气的净化与干燥 4.1.4 二氧化硫的催化氧化 4.1.5 三氧化硫的吸收 4.1.6 三废治理与综合利用
4.1.1 概述
硫酸是重要的基本化学工业原料。在化肥、冶金、
内结疤,焙烧反而不能顺利进行。通常温度范
围为850950C。
减小硫铁矿粒度(0.24-0.7mm) 。可以减小扩散 阻力,增加接触面积,对第三阶段速度增加有 利。 增加空气与矿粒的相对运动 。
提高入炉空气氧含量。
4.1.2.2 沸腾焙烧与焙烧炉 1. 沸腾焙烧炉的结构
下部:沸腾区,耐火砖较厚
4.1.5 三氧化硫的吸收
4.1.5.1 吸收原理
SO2催化氧化成SO3后,送入吸收工序用发烟
硫酸或浓硫酸吸收,吸收过程可写为: nSO3(g) + H2O(l) = H2SO4(l) + (n-1)SO3(l) n>1时生成发烟硫酸; n=1时生成无水硫酸; n<1时生成含水硫酸。
4.1.5.2 浓硫酸吸收过程的影响因素
国防、有机合成、石油炼制等工业都有广
泛用途。
硫酸的性质 硫酸与水的二组分体系最高恒沸点组成为98.4%。 硫酸浓度可大于100%,称为发烟硫酸,其中含 溶解在浓硫酸中的游离SO3。
生产方法 塔式法:直接用SO2,H2O,O2反应生成硫酸。
接触法:SO2→SO3 +H2O→硫酸 含硫原料
催化剂 生成总费用
折旧费
二次转化流程——8-9%
3. 最终转化率 最终转化率↑,S的利用率↑,原料消耗↓,环境
污染减少。最终转化率与工艺流程和生产条件
有关。通常有一最佳值,超过此值生产成本会
显著上升。
一次转化流程——97.5-98% 二次转化流程——99.5%
工艺流程及设备 转化流程和反应器设计的基本原则:按最佳温 度分配各段反应,并充分利用反应热。 换热方 式不同 二氧化硫转化器
3. 沸腾焙烧炉的特点
生产强度大;硫的烧出率高; 产生的炉气SO2浓度高;适用的原料范围广;
传热系数高;结构简单、维修方便
不足: 炉尘量大,炉尘占总烧渣的60%-70%,除尘净 化系统负荷大。
需将硫铁矿粉碎至较小粒度,需高压鼓风机,
动力消耗大。
4.1.2.3 焙烧前矿石原料的预处理
As2O3 ,SeO2在气体中的饱和浓度 温度 ℃ 50 70 100 125 150 As2O3饱和浓度 mg/Nm3 0.016 0.310 4.200 37.000 280.0 SeO2 饱和浓度 mg/Nm3 0.044 0.880 1.000 82.000 530.0
4.1.3.3 酸雾的形成与清除
SO3
水 分 砷和硒
催化剂的毒物
4.1.3.1 炉气除尘
排 气
方法:机械除尘、电除尘、文丘里除尘。 1. 机械除尘
集尘器除尘、自然沉降除尘、惯性除尘。 旋风分离器除尘 除尘效率高。
2. 电除尘
静电除尘器除尘效 率高,达99%以上, 可使含尘量降至 0.2g/Nm3的绝对值。
4.1.3.2 砷和硒的清除 As2O3 ,SeO2常用水或稀硫酸洗涤炉气来清除。
制备含SO2炉气 炉气净化 转化 吸收
硫酸
生产硫酸的原料
硫铁矿:主要成份是FeS2。磁硫铁矿:主要成份 为Fe7S8。含S量越高,锻烧时放热越多。两种矿 含S量相同时,磁硫铁矿锻烧放热量比普通硫铁矿 高30%左右。自然开采的硫铁矿都含有很多杂质, 使矿呈灰、褐、黄铜等不同颜色。通常含硫量只 有30%~50%。 硫磺:天然硫磺生产硫酸最好,但我国矿少。 其它原料:硫酸盐、冶炼烟气、含硫工业废料
目前,国内广泛使用的是S101和S105
钒催化剂毒物 砷的氧化物
硒的氧化物
毒物 氟化物
酸雾
1、钒催化剂吸附 硒在温度较低时 As 2O3,堵塞催化 HF+SiO 2→SiF4 对钒催化剂有毒 腐蚀钢设备; 剂活性表面,降低 破坏载体,使催 害,但加热后 腐蚀的粉尘落在 活性; 化剂粉碎。 (400-500 ℃)可以 催化剂表面,使 2、在500℃以上 复原。 →VF 其 其活性降低; 5,O VF+V O 能与 As 2 5 2 3生 沸点低 (112.2 ℃) 成 V O •As O , 积累的 Fe SO 2 5 2 25 4 造成钒的损失。 易挥发物质,造成 使催化剂结块。 钒的损失。
间接换热式 实质:反应- 换热反复过程 内部间接换热 外部间接换热 转化器内部结构简单
转化器结构紧凑、阻 优点 力小、热损失小 转化器结构复杂、体 缺点 积大、维修不便
连接管线长、阻力 大、热损失大
冷激式 省去换热器,催化剂用量增加(原因是混合后SO2 浓度降低),所以一般只在1,2段采用冷激式。 冷激方式有炉气式冷激、空气冷激。
1. 吸收酸浓度 酸浓度低:SO3与水冷凝成酸雾,被尾气带出。 酸浓度=98.3%: 25℃,若气体干 燥,吸收率达 99.95%。 酸浓度高: SO3 与大气中的水蒸 气形成酸雾。
100 吸 收 率 % 60℃ 80 ℃ 90 ℃ 100 ℃ 95 98.3 吸收酸浓度/%
98
2. 吸收酸温度
多固 段定 换床 反 热应 式器
外部间接换热
间接换热式
内部间接换热 多段冷激式
1. 二氧化硫转化器
转化器:多段式(3-5 段),绝热
转化器内T-x图。
T-x的关系由热力学
原理求反应热计算。
转化器设计的主要原则 (1)满足最佳温度要求,以提高催化剂利用率; (2)生产能力大,可以省料、省地、省投资; (3)压降小,可省能; (4)换热面积足够大,保证热量平衡; (5)催化剂装填系数大,体积不变时提高生产能力; (6)便于安装检修更换催化剂。
2. 硫铁矿焙烧的焙烧速度 非均相反应,平衡常数很大,进行完全。所以
对生产能力起关键作用的是焙烧速度。
焙烧反应的反应速率与温度的关系如图。
lgk
I:化学反应动 力学控制 III:氧的扩散控制
I II 560 727 III 1/T 977
460
提高焙烧速率的途径
提高操作温度。但不宜太高,温度太高会使炉
1. 酸雾的形成 炉气中少量SO3与水反应生成硫酸,温度较低 时,炉气中大多数SO3都转化成硫酸蒸汽。当 气相中硫酸蒸汽压大于其饱和蒸汽压时,硫酸 蒸汽就会冷凝成雾。 2. 酸雾的清除 雾滴直径很小,很难除去,一般用电除雾器。 为保证除雾效果,电除雾器也要采取增大雾滴 直径的措施。工业:设置冷却塔,既降低温度 又通过增湿来增大雾滴直径。
三塔二电流程
优点: 1、操作稳定,易控制 2、酸可循环使用 3、S的利用率高 4、砷硒也可回收 5、排污量少
热浓酸洗流程
用较高温度的浓硫酸洗涤炉气 优 点 1、流程简单 2、吸收SO3不形成酸雾, S利用率高
3、排污量小
缺点
对砷、氟净化度不高
4.1.4 二氧化硫的催化氧化
活性组分
钒 催 化 剂
2. 转化流程
转化次 数 一次转化
工艺流程
四段转化 间接换热流程
两次转化 (两转两吸流程)
一次转化流程 反应量少,需要移走的热量少,使转化器内部结 构简单。 两次转化流程
(1)反应速度快,最终转化率高; (2)可用SO2浓度较高的炉气; (3)减轻尾气污染和尾气处理负荷; (4)催化剂用量减少; (5)需增加一换热器:一次吸收后需要再加热到 420℃左右才能进行转化反应;动力消耗增加。
粉碎
二级粉碎,先用腭式压碎机粗碎,再用辊式压碎 机细碎,要求粒度<4mm。
配料
原则:贫富搭配,高砷矿与低砷矿搭配,含煤与 不含煤的矿搭配。 沸腾焙烧用矿指标: S>20% ,As<0.05%,C<1.0%,Pb<0.1%, F<0.05%,H2O<6.0%
干燥
使含水量多的矿料达到上述含水量指标。
4.1.5.3 生产浓硫酸的吸收流程
普遍采用一次吸收流程 转化气从塔底送入,浓 硫酸从塔顶喷淋。进塔 气温度140~160℃,喷淋 酸温60-75℃,出塔酸温 用喷淋量控制,使出塔 酸温<60℃。 吸收酸要冷却和循环使 用。
4.1.6 三废治理与综合利用
尾气 SO2、SO3、酸雾
三 废
吸收原理: T低,利于吸收。
温度过低,增加酸冷却器面积,低温热不能有效 利用。所以通常的吸收温度控制在60 ~ 75℃。 3. 进塔气温 酸雾生成:进塔气温太低生成酸雾机会多;例: 转化气中SO37%,水0.1g,露点112℃
进塔气温> 112℃能防止酸雾生成。