模具类型
模具的知识点总结

模具的知识点总结一、模具的基本概念1. 模具的定义:模具是用于生产制品的工艺装置,是一种工业生产中常用的辅助工具。
2. 模具的作用:模具是将原材料经过一定的加工和成型工序,制成具有一定形状和尺寸的制品的工具。
二、模具的分类1. 按成品类型分类:模具可分为塑料模具、压铸模具、橡胶模具、冲压模具等。
2. 按加工方式分类:模具可分为冷冲模、热冲模、复合模、硬模、软模等。
3. 按使用领域分类:模具可分为汽车模具、家电模具、日用品模具等。
三、模具的制造工艺1. 模具设计:模具设计是根据产品的要求和工艺特点,确定模具的结构形式、尺寸精度、加工工艺等内容。
2. 模具加工:模具加工包括模具零件的粗加工、精加工、装配以及热处理等工序。
3. 模具调试:模具调试是指将制造好的模具装配到设备上,进行成型工艺试验,验证模具的可用性和性能。
四、模具的材料1. 模具的零部件通常采用优质合金钢和工具钢制造。
2. 塑料模具的主要材料为45#钢、P20钢、718钢等。
3. 压铸模具的主要材料为H13钢、8407钢等。
4. 橡胶模具的主要材料为S50C钢、SKD61钢等。
五、模具的设计原则1. 模具设计应根据产品的使用要求,确定模具的结构和精度等技术参数。
2. 模具设计应根据材料特性和成本要求,合理选择材料和加工工艺。
3. 模具设计应遵循产品开发的原则,确保模具的可靠性和稳定性。
六、模具的使用与维护1. 模具使用过程中,应定期对模具进行检查和保养,确保模具的精度和可靠性。
2. 模具使用过程中,应注意控制模具的使用次数和工艺参数,减少模具的磨损。
3. 模具使用过程中,应按规定使用润滑剂,保证模具的正常工作。
总结:模具作为工业生产中不可或缺的一部分,对于提高产品质量和生产效率有着重要的作用。
通过对模具的相关知识点进行总结,可以更加深入地了解模具的制造工艺和使用原则,对于提高模具的设计和制造水平有一定的指导作用。
希望通过本文的介绍,能够对模具制造领域有所了解,为读者提供参考和借鉴的价值。
冲压模具的基本类型

冲压模具的基本类型冲压模具是现代工业生产中常用的一种工具,用于将金属板材或条材加工成所需形状的零件。
根据不同的加工需求和工艺要求,冲压模具可以分为以下几种基本类型。
一、单工位模具单工位模具是最简单、最基本的冲压模具类型。
它只有一个工作站,用于完成一次冲压加工操作。
单工位模具结构简单,制造成本较低,适用于简单形状的零件加工。
二、连续模具连续模具是由多个工作站组成的复杂模具。
每个工作站都有不同的功能,可以完成不同的冲压加工操作。
工件在连续模具中依次通过各个工作站,最终完成整个冲压加工过程。
连续模具具有高效生产的特点,适用于批量生产大量相似形状的零件。
三、复合模具复合模具是由多个单工位模具组合而成的模具系统。
每个单工位模具都有自己的功能,可以独立完成一道工序的冲压加工。
通过组合不同的单工位模具,可以实现复杂零件的加工。
复合模具具有灵活多变的特点,适用于加工形状复杂、工序繁多的零件。
四、多工位模具多工位模具是由多个工作站组成的模具,每个工作站都可以独立完成一道工序的冲压加工。
不同工作站之间通过传送装置或转盘进行工件的转移。
多工位模具具有高效率、高精度的特点,适用于大批量生产复杂形状的零件。
五、复进模具复进模具是一种特殊的模具类型,它可以在一次进给中完成多道工序的冲压加工。
复进模具通常由多个工作站组成,每个工作站都有不同的冲压功能。
工件在一次进给中依次通过各个工作站,完成多道工序的加工。
复进模具具有高效生产、节约时间的特点,适用于批量生产多道工序的零件。
六、特殊模具除了以上几种基本类型的冲压模具外,还有一些特殊的模具类型,如拉伸模具、弯曲模具、成形模具等。
这些特殊模具根据不同的加工需求和工艺要求,具有特定的结构和功能,可以完成特定形状的零件加工。
冲压模具的基本类型包括单工位模具、连续模具、复合模具、多工位模具、复进模具和特殊模具。
不同类型的模具适用于不同的加工需求,可以实现各种形状、各种工序的零件加工。
冲压模具在现代工业生产中起着重要的作用,为各行各业的发展提供了强有力的支持。
模具名词三语对照表
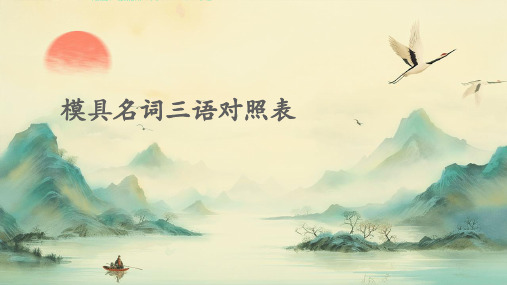
排气系统设计
排气系统
排气系统是指模具中用于排除型腔内 气体的通道和机构。
排气系统的作用
排气系统的作用是排除型腔内的气体, 避免产品出现气孔、鼓包等问题,提 高产品质量。
排气系统的设计原则
排气系统的设计应遵循结构简单、易 于维护、不影响产品外观等原则。
排气系统的类型
根据产品结构和模具结构,排气系统 可分为自然排气和强制排气两种类型。
分模面设计
01
02
03
04
分模面
模具设计中的分模面是指将模 具分成动模和定模两个部分的
面。
分模面设计原则
分模面设计应遵循便于模具加 工、降低模具复杂度、保证产
品精度等原则。
分模面的类型
根据产品结构和模具结构,分 模面可分为水平分模面、垂直 分模面、倾斜分模面等类型。
分模面的选择
选择合适的分模面可以简化模 具结构,提高模具强度和寿命 ,同时保证产品顺利脱模。
模具名词三语对照表
• 模具类型 • 模具部件 • 模具材料 • 模具设计
01
模具类型
注塑模具
注塑模具:注射成型模,德文:Spritzgussform
英文:Injection Mould
注塑模具主要用于热塑性塑料制品的成型,也可用于热固性塑料制品的 成型,而结构上又具备可调镶件、斜导柱、顶针、司筒、分流器、定位 环、冷却水道等结构。
冲压模具主要用于金属薄板零件的成型,如汽 车覆盖件、家电零件等。冲压模具的结构包括 凹模、凸模、压边圈、定位销等部分。
挤出模具
挤出模具:挤出成型模,德文:Extrusionform
英文:Extrusion Mould 挤出模具主要用于塑料制品的连续成型,如塑料管材、塑料薄膜等。挤出 模具的结构包括机头、口模、芯棒、加热系统等部分。
模具知识点总结大全

模具知识点总结大全一、模具概述1. 模具的定义:模具是用来制造各种工业产品的零件和部件的专用工具,它包括冲模、压模、注塑模、挤压模、泡沫模等各种类型。
2. 模具的分类:按照生产工艺的不同,模具可以分为冲压模具、塑料模具、压铸模具、橡胶模具等多种类型。
3. 模具的重要性:模具在工业生产中起着至关重要的作用,它直接影响着产品的质量、成本和产能。
二、模具的结构与原理1. 模具的结构:模具通常由模具座、上模、下模、导柱、导套、顶杆、顶模、底模、顶针、顶杆、导套等部件组成。
2. 模具的工作原理:模具在生产过程中,通过上下模板的闭合和分离,实现对工件的成形、加工、修整等功能。
三、模具的制造技术1. 模具设计:模具设计是模具制造的关键环节,需要考虑到零件的尺寸、形状、壁厚、材料、生产工艺等多个方面因素。
2. 模具制造工艺:模具制造包括模具材料选择、模具结构设计、数控加工、热处理、装配调试等多个环节。
3. 模具加工设备:模具加工设备包括车床、铣床、电火花、磨床、铣镗床、线切割等多种设备。
四、模具的运用与维护1. 模具生产管理:模具生产管理包括模具投入使用、模具维护保养、模具修磨、模具更换、模具存储等多个方面。
2. 模具的维护保养:模具的维护保养包括模具润滑、模具清洁、模具修复、模具存放等环节。
3. 模具故障与排除:模具在使用过程中可能会出现各种故障,需要及时排除,以保证生产的顺利进行。
五、模具行业的发展趋势1. 模具制造技术的发展:随着工业制造技术的进步,模具加工技术不断提升,数控加工、快速制造等技术的应用将会更加广泛。
2. 模具材料的发展:新型的合金材料、陶瓷材料、高分子材料等将逐渐应用到模具制造中,提高模具的使用寿命和制造精度。
3. 智能化制造趋势:智能制造技术将会在模具行业得到广泛应用,包括智能设计、智能制造、智能检测等方面。
4. 环保可持续发展:环保材料、绿色制造、循环利用等理念将逐渐渗透到模具制造过程中,促进模具行业的可持续发展。
模具的分类方式
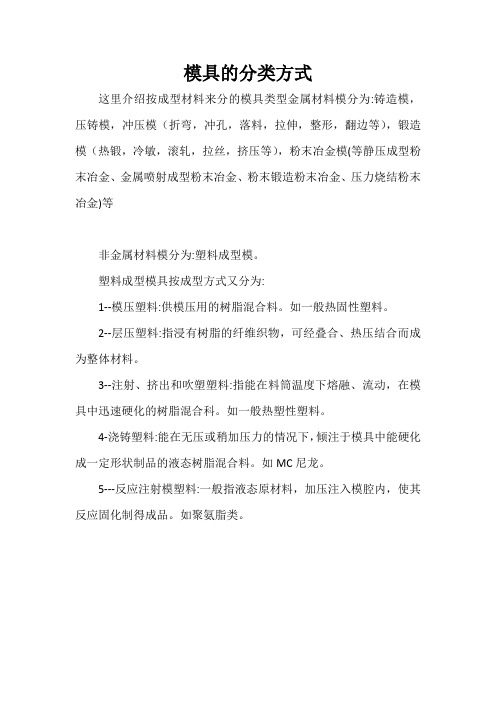
模具的分类方式
这里介绍按成型材料来分的模具类型金属材料模分为:铸造模,压铸模,冲压模(折弯,冲孔,落料,拉伸,整形,翻边等),锻造模(热锻,冷敏,滚轧,拉丝,挤压等),粉末冶金模(等静压成型粉末冶金、金属喷射成型粉末冶金、粉末锻造粉末冶金、压力烧结粉末冶金)等
非金属材料模分为:塑料成型模。
塑料成型模具按成型方式又分为:
1--模压塑料:供模压用的树脂混合料。
如一般热固性塑料。
2--层压塑料:指浸有树脂的纤维织物,可经叠合、热压结合而成为整体材料。
3--注射、挤出和吹塑塑料:指能在料筒温度下熔融、流动,在模具中迅速硬化的树脂混合科。
如一般热塑性塑料。
4-浇铸塑料:能在无压或稍加压力的情况下,倾注于模具中能硬化成一定形状制品的液态树脂混合料。
如MC尼龙。
5---反应注射模塑料:一般指液态原材料,加压注入模腔内,使其反应固化制得成品。
如聚氨脂类。
模具成型分类

模具成型分类
模具成型分类
一、模具成型类型
1、撞击式成型
撞击式成型又称锻成型,是由撞击力作用在加热至一定温度的金属穿过模具内表面,形成零件外形与空间结构的一种成型方法。
它是一种非常广泛使用的成型方法,此外,还有分段锻、多段锻、螺旋锻等。
2、热压成型
热压成型是指将金属加热到一定温度后,用冷压机在阻隔圈模具表面上施加压力,使金属变形而成零件外形的一种成型方法。
3、挤压成型
挤压成型是指通过油压机和模具以及一定的温度,将金属块料高压挤压成型,形成各种形状和尺寸的零件外形的一种成型方法。
4、模铸成型
模铸成型是指将金属块料向模具加热,然后将金属块料填充入模具内,使金属变形而成零件外形的一种成型方法。
5、量铸成型
量铸成型是指通过量铸机和相应模具,将金属块料高温压力加热,使金属流动而变形而成零件外形的一种成型方法。
6、冷冲压成型
冷冲压成型是指用冲压机在非加热条件下,将金属块料填入冲压
模具中,用冲头将其变形而成零件外形的一种成型方法。
二、模具成型之间的区别
1、用料条件不同
撞击式成型中,金属块料需要加热到一定温度,而冷冲压成型则不需要加热。
2、变形原理不同
撞击式成型是靠撞击力对金属块料进行变形,而热压成型和冷冲压成型是分别靠热压机和冲压机进行变形。
3、成型机械不同
撞击式成型用的是锻压机,而热压成型用的是热压机,模铸成型用的是模铸机,量铸成型用的是量铸机,冷冲压成型用的是冲压机。
4、成型精度不同
撞击式成型的成型精度最高,而冷冲压成型的成型精度最低。
模具使用说明书

模具使用说明书模具使用说明书1.概述本文档旨在提供模具的详细使用说明,帮助用户正确、安全地使用模具。
在使用模具之前,请用户仔细阅读本说明书并按照指示进行操作。
2.模具简介2.1 模具类型:(例如,塑料模具、金属模具等)2.2 模具材质:(例如,钢、铝等)2.3 模具尺寸:(包括长度、宽度、高度等)2.4 模具重量:(以公斤为单位)3.安全注意事项3.1 使用模具前,确保操作人员具备相关的技术知识和操作经验。
3.2 在使用模具时,严禁戴手套或其他可能导致手部被夹伤的物品。
3.3 遵循模具的最大负荷限制,不要超过其承载能力。
3.4 使用模具前,检查模具的外观是否有损坏,并确保模具没有松动或松脱的部分。
3.5 使用模具时,必须戴上适当的个人防护设备,如护目镜、手套等。
3.6 当模具出现异常噪音或其他异常情况时,立即停止使用,并联系专业技术人员进行检修。
4.模具安装步骤4.1 准备工作:确保安装场地清洁整齐,并放置正确的工具和所需材料。
4.2 模具准备:仔细检查模具的各个部分,确保模具没有损坏或松动。
4.3 安装步骤:4.3.1 将模具放置在合适的位置上。
4.3.2 使用正确的工具和螺丝将模具固定在位置上。
4.3.3 检查模具是否安装牢固,没有松动或晃动的情况。
4.4 完成安装后,对模具进行功能测试,确保模具正常工作。
5.模具使用指南5.1 操作前准备5.1.1 清洁模具:使用合适的清洁剂和工具对模具进行清洁,确保模具表面干净。
5.1.2 润滑模具:根据模具的要求,在适当的部位涂抹适量的润滑剂。
5.2 操作步骤5.2.1 根据要加工的材料选择合适的模具。
5.2.2 将材料放置在模具内,并确保材料的位置正确。
5.2.3 关闭模具,并按照操作要求启动模具。
5.2.4 等待加工完成后,打开模具,取出加工好的产品。
5.3 操作注意事项5.3.1 确保操作人员遵守操作规程,按照正确的操作流程进行操作。
5.3.2 在操作模具时,注意材料的加工温度和压力要求,避免超过模具的限制范围。
模具类别和分类方法
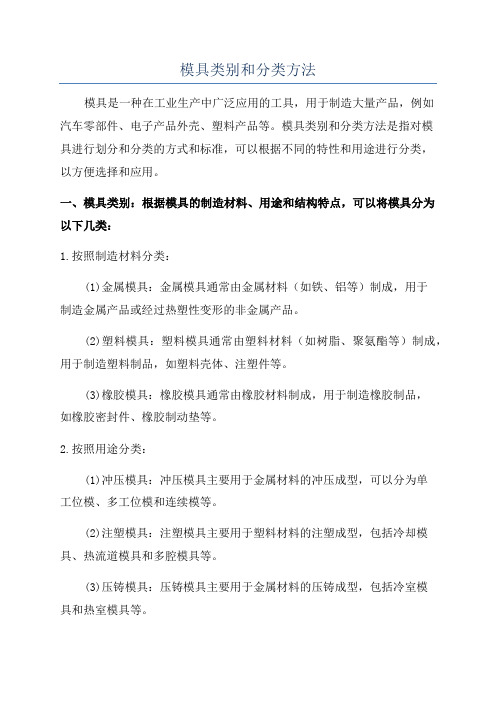
模具类别和分类方法模具是一种在工业生产中广泛应用的工具,用于制造大量产品,例如汽车零部件、电子产品外壳、塑料产品等。
模具类别和分类方法是指对模具进行划分和分类的方式和标准,可以根据不同的特性和用途进行分类,以方便选择和应用。
一、模具类别:根据模具的制造材料、用途和结构特点,可以将模具分为以下几类:1.按照制造材料分类:(1)金属模具:金属模具通常由金属材料(如铁、铝等)制成,用于制造金属产品或经过热塑性变形的非金属产品。
(2)塑料模具:塑料模具通常由塑料材料(如树脂、聚氨酯等)制成,用于制造塑料制品,如塑料壳体、注塑件等。
(3)橡胶模具:橡胶模具通常由橡胶材料制成,用于制造橡胶制品,如橡胶密封件、橡胶制动垫等。
2.按照用途分类:(1)冲压模具:冲压模具主要用于金属材料的冲压成型,可以分为单工位模、多工位模和连续模等。
(2)注塑模具:注塑模具主要用于塑料材料的注塑成型,包括冷却模具、热流道模具和多腔模具等。
(3)压铸模具:压铸模具主要用于金属材料的压铸成型,包括冷室模具和热室模具等。
3.按照结构特点分类:(1)单件模具:单件模具是指由一个模具部件组成的模具,适用于生产单一型号的产品。
(2)组合模具:组合模具是将多个模具部件组合在一起,适用于生产多种型号的产品。
(3)复合模具:复合模具是将两种或以上不同类型的模具组合在一起,适用于生产结构复杂的产品。
二、模具分类方法:1.按照应用行业分类:模具可以根据应用行业的不同进行分类,如汽车模具、电子模具、家电模具等。
这种分类方法可以根据模具所应用的行业领域来确定使用的材料和制造工艺。
2.按照加工工艺分类:模具可以根据加工工艺的不同进行分类,如冲压模具、注塑模具、压铸模具等。
这种分类方法可以根据模具所使用的加工工艺来确定其结构特点和制造要求。
3.按照产品形状分类:模具可以根据产品形状的不同进行分类,如平面模具、曲面模具、异型模具等。
这种分类方法可以根据模具所制造的产品形状来确定其结构设计和制造工艺。
模具结构基础知识1
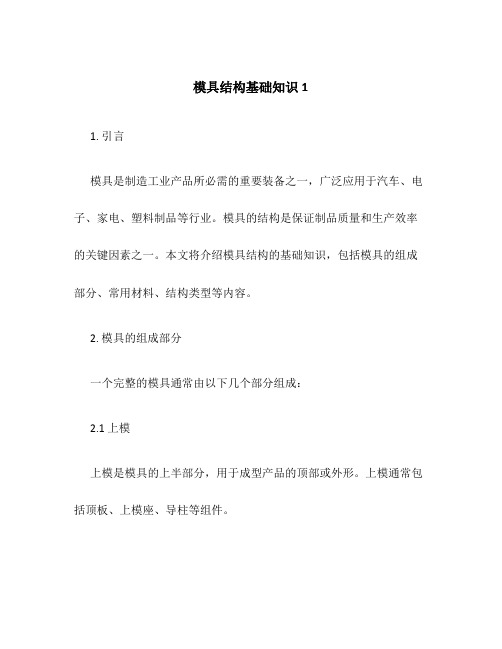
模具结构基础知识11. 引言模具是制造工业产品所必需的重要装备之一,广泛应用于汽车、电子、家电、塑料制品等行业。
模具的结构是保证制品质量和生产效率的关键因素之一。
本文将介绍模具结构的基础知识,包括模具的组成部分、常用材料、结构类型等内容。
2. 模具的组成部分一个完整的模具通常由以下几个部分组成:2.1 上模上模是模具的上半部分,用于成型产品的顶部或外形。
上模通常包括顶板、上模座、导柱等组件。
2.2 下模下模是模具的下半部分,用于成型产品的底部或内形。
下模通常包括下模座、下模板、导柱等组件。
2.3 滑块模滑块模也称为副模或侧模,用于成型产品的侧面或突起部分。
滑块模通常包括滑块、导柱套和定位销等组件。
2.4 斜顶模斜顶模用于成型带有斜侧面的产品。
斜顶模通常包括斜顶、导柱套、斜顶片等组件。
2.5 拉伸模拉伸模用于成型带有拉伸形状的产品。
拉伸模通常包括拉伸块、导柱、拉伸销等组件。
模具材料的选择直接影响到模具的使用寿命和成品质量。
常用的模具材料包括:3.1 铝合金铝合金具有良好的热传导性能和机械性能,适用于制作小型模具和大批量生产的模具。
3.2 铜合金铜合金因其良好的导热性和耐磨性被广泛应用于模具制造,尤其适用于高速冲压模具和大体积模具。
3.3 铁合金铁合金包括低碳钢、合金钢、工具钢等。
它们具有高硬度、高强度和耐磨性,适用于制作高精度模具和耐用性要求较高的模具。
塑料模具材料包括PVC、PE、PP等。
它们具有良好的耐腐蚀性和可塑性,适用于制作塑料制品模具。
4. 模具结构类型模具结构的选择取决于产品的形状、尺寸和材料等因素。
常见的模具结构类型包括:4.1 单模结构单模结构是最简单的模具结构,适用于产品形状简单、工艺要求低的情况。
4.2 组合模结构组合模结构由多个模块组合而成,适用于产品形状复杂、工艺要求高的情况。
4.3 多腔模结构多腔模结构是指在一个模具中设置多个腔室,可以同时成型多个产品。
多腔模结构适用于批量生产相同产品的情况。
模具分种几类型

冲压模具的形式很多,冲模也依工作性质,模具构造,模具材料三方面来分类。
一般可按以下几个主要特征分类:1〃根据工艺性质分类a.冲裁模沿封闭或敞开的轮廓线使材料产生分离的模具。
如落料模、冲孔模、切断模、切口模、切边模、剖切模等。
b.弯曲模使板料毛坯或其他坯料沿着直线(弯曲线)产生弯曲变形,从而获得一定角度和形状的工件的模具。
c.拉深模是把板料毛坯制成开口空心件,或使空心件进一步改变形状和尺寸的模具。
d.成形模是将毛坯或半成品工件按图击、凹模的形状直接复制成形,而材料本身仅产生局部塑性变形的模具。
如胀形模、缩口模、扩口模、起伏成形模、翻边模、整形模等。
2〃根据工序组合程度分类a.单工序模在压力机的一次行程中,只完成一道冲压工序的模具。
b.复合模只有一个工位,在压力机的一次行程中,在同一工位上同时完成两道或两道以上冲压工序的模具。
c.级进模(也称连续模)在毛坯的送进方向上,具有两个或更多的工位,在压力机的一次行程中,在不同的工位上逐次完成两道或两道以上冲压工序的模具。
3、依产品的加工方法分类依产品加工方法的不同,可将模具分成冲剪模具、弯曲模具、抽制模具、成形模具和压缩模具等五大类。
a. 冲剪模具:是以剪切作用完成工作的,常用的形式有剪断冲模、下料冲模、冲孔冲模、修边冲模、整缘冲模、拉孔冲模和冲切模具。
b.弯曲模具:是将平整的毛胚弯成一个角度的形状,视零件的形状、精度及生产量的多寡,乃有多种不同形式的模具,如普通弯曲冲模、击轮弯曲冲模、卷边冲模、圆弧弯曲冲模、折弯冲缝冲模与扭曲冲模等。
c.抽制模具:抽制模具是将平面毛胚制成有底无缝容器。
d.成形模具:指用各种局部变形的方法来改变毛胚的形状,其形式有击张成形冲模、卷缘成形冲模、颈缩成形冲模、孔击缘成形冲模、圆缘成形冲模。
e.压缩模具:是利用强大的压力,使金属毛胚流动变形,成为所需的形状,其种类有挤制冲模、压花冲模、压印冲模、端压冲模。
各种模具分类方法
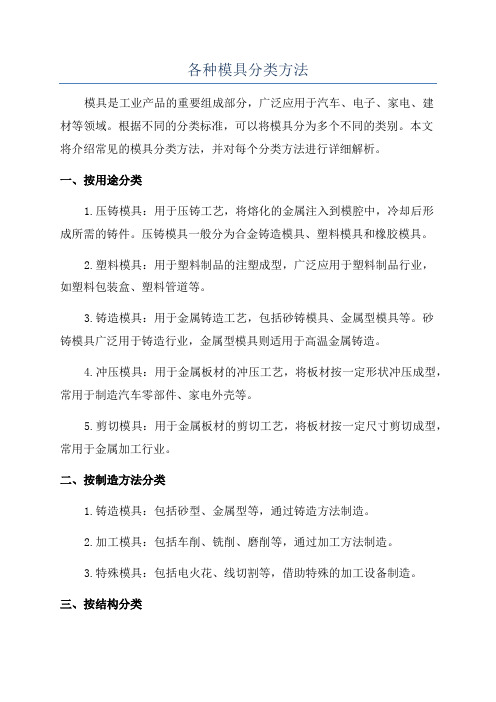
各种模具分类方法模具是工业产品的重要组成部分,广泛应用于汽车、电子、家电、建材等领域。
根据不同的分类标准,可以将模具分为多个不同的类别。
本文将介绍常见的模具分类方法,并对每个分类方法进行详细解析。
一、按用途分类1.压铸模具:用于压铸工艺,将熔化的金属注入到模腔中,冷却后形成所需的铸件。
压铸模具一般分为合金铸造模具、塑料模具和橡胶模具。
2.塑料模具:用于塑料制品的注塑成型,广泛应用于塑料制品行业,如塑料包装盒、塑料管道等。
3.铸造模具:用于金属铸造工艺,包括砂铸模具、金属型模具等。
砂铸模具广泛用于铸造行业,金属型模具则适用于高温金属铸造。
4.冲压模具:用于金属板材的冲压工艺,将板材按一定形状冲压成型,常用于制造汽车零部件、家电外壳等。
5.剪切模具:用于金属板材的剪切工艺,将板材按一定尺寸剪切成型,常用于金属加工行业。
二、按制造方法分类1.铸造模具:包括砂型、金属型等,通过铸造方法制造。
2.加工模具:包括车削、铣削、磨削等,通过加工方法制造。
3.特殊模具:包括电火花、线切割等,借助特殊的加工设备制造。
三、按结构分类1.单一模具:为一次加工过程制造的模具,形状简单,制造成本低,常见的有冲压模具。
2.组合模具:由多个模具组合而成,可实现多道工序连续加工,适合复杂零件的生产。
3.成套模具:包含多种类型的模具组合,适用于多种工件的生产,如汽车模具、家电模具等。
四、按材料分类1.金属模具:制造模具主体材料为金属,如铝合金、钢材等。
金属模具具有高强度、耐磨、耐腐蚀等优点。
2.非金属模具:制造模具主体材料为非金属材料,如陶瓷、塑料等。
非金属模具具有重量轻、耐温高等特点。
五、按形状分类1.平面模具:用于制造平面零件,如零件盖板等。
2.空心模具:用于制造中空零件,如管道、容器等。
3.弯曲模具:用于制造弯曲形状的零件,如曲轴等。
4.复杂模具:用于制造复杂形状的零件,如汽车车身等。
六、按制造精度分类1.普通模具:制造精度要求较低的模具,适用于一般工业产品的制造。
模具结构基础知识
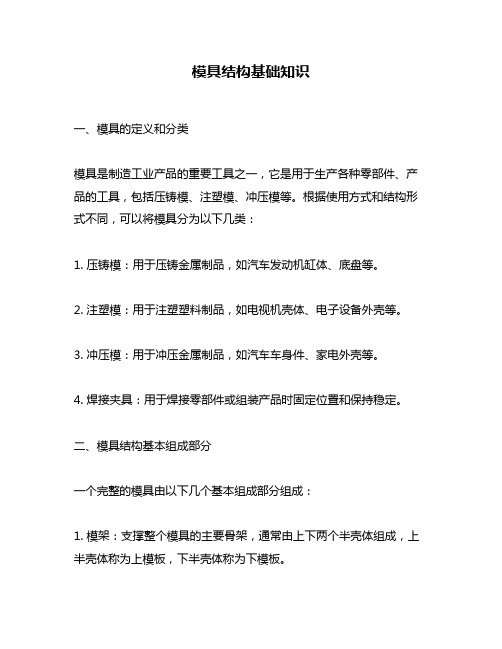
模具结构基础知识一、模具的定义和分类模具是制造工业产品的重要工具之一,它是用于生产各种零部件、产品的工具,包括压铸模、注塑模、冲压模等。
根据使用方式和结构形式不同,可以将模具分为以下几类:1. 压铸模:用于压铸金属制品,如汽车发动机缸体、底盘等。
2. 注塑模:用于注塑塑料制品,如电视机壳体、电子设备外壳等。
3. 冲压模:用于冲压金属制品,如汽车车身件、家电外壳等。
4. 焊接夹具:用于焊接零部件或组装产品时固定位置和保持稳定。
二、模具结构基本组成部分一个完整的模具由以下几个基本组成部分组成:1. 模架:支撑整个模具的主要骨架,通常由上下两个半壳体组成,上半壳体称为上模板,下半壳体称为下模板。
2. 模腔:用于成形产品的空间,在上下两个半壳体中间形成。
根据不同的产品形状和尺寸需求,可以设计出不同形状和尺寸的模腔。
3. 模仁:用于成形产品的核心部分,通常安装在上模板上,与模腔配合使用。
4. 引导柱和导套:引导柱是固定在上下两个半壳体中间,用于保持模具的位置和稳定性;导套则是安装在引导柱上,用于保持引导柱与半壳体之间的间隙,以便半壳体之间的移动。
5. 凸模和凹模:凸模是安装在下模板上的零件,用于成形产品表面;凹模则是安装在上模板上的零件,用于成形产品内部和底部。
6. 夹具和顶针:夹具是用于固定原材料或成品,保持其位置稳定;顶针则是用于将成品从模腔中顶出来。
三、常见的模具结构类型1. 平面式结构:适合制造平面形状、简单结构的产品。
由一个平面型下模板和一个平面型上模板组成。
2. 拉伸式结构:适合制造长条状、管状等拉伸型产品。
由一个拉伸型下模板和一个拉伸型上模板组成。
3. 斜侧式结构:适合制造斜侧形状、倾斜角度较大的产品。
由一个斜侧型下模板和一个斜侧型上模板组成。
4. 旋转式结构:适合制造圆柱形、球形等旋转型产品。
由一个圆柱型下模板和一个圆柱型上模板组成。
四、常见的模具材料1. 铝合金:轻质、导热性能好,适用于制造小批量生产的零件或产品。
注塑模具基础知识介绍

注塑模具是一种常见的工业制造工具,广泛应用于塑料制品的生产过程中。
它是将塑料加热熔化后注入模具中,并通过冷却硬化成型的过程。
注塑模具具有高效、精确、重复性好等特点,被广泛应用于汽车、电子、家电、医疗器械等领域。
本文将介绍注塑模具的基础知识,包括模具的类型、结构、设计原则、材料选择等内容。
正文内容:一、注塑模具的类型1.依据产品形状分类平面模具:用于生产平面形状的产品,如盖板、面板等。
长条模具:用于生产长条形状的产品,如管道、线槽等。
箱式模具:用于生产具有一定体积的产品,如箱子、容器等。
2.依据模具结构分类单腔模具:只有一个腔体,适用于生产单一产品。
多腔模具:有多个相同的腔体,可以同时生产多个产品。
多组份模具:可以同时注射多种材料,生产复合产品。
二、注塑模具的结构1.注塑模具的基本结构模具座:支撑整个模具的基础部件。
固定板:固定上模板和下模板的部件。
上模板:与固定板连接,上部为模腔所在的部分。
下模板:与固定板连接,下部为产品座标部分。
2.注塑模具的附属结构抽芯装置:用于模具腔体内形状复杂的产品,使产品脱模时不损坏。
取出装置:将注塑成型的产品从模具中取出。
冷却系统:通过冷却系统对模具加热的塑料进行冷却,使其硬化成型。
三、注塑模具的设计原则1.合理性原则产品可制造性:模具设计应符合产品的形状、尺寸、结构要求。
模具结构合理性:模具应具有良好的刚度和稳定性,以保证产品的质量和生产效率。
2.生产性原则降低模具成本:在不影响产品质量和生产效率的前提下,尽量降低模具制造成本。
提高模具寿命:通过合理的设计和材料选择,延长模具的使用寿命。
四、注塑模具的材料选择1.模具材料的要求高硬度:能够承受高压力和摩擦力。
高强度:能够承受高扭矩和冲击力。
耐磨性:能够抵抗长时间的磨损。
2.常用的模具材料冷工具钢:适用于生产大批量的塑料产品。
热工具钢:适用于生产高要求的高温、高压产品。
钨钢:适用于生产高精度、高要求的产品。
五、总结注塑模具是塑料制品生产过程中不可或缺的工具。
玻璃模具设计知识点

玻璃模具设计知识点玻璃模具在玻璃制品的生产中起着至关重要的作用。
一个好的模具设计可以确保玻璃制品的质量和生产效率。
本文将介绍一些关于玻璃模具设计的知识点,希望对读者有所帮助。
一、模具类型在玻璃模具设计中,常见的模具类型有以下几种:1. 铸造模具:铸造模具适用于大批量生产玻璃制品,如瓶子、碟子等。
铸造模具通常由金属材料(如铁、铝等)制成,具有较高的耐磨性和耐高温性。
2. 压模具:压模具适用于制作形状复杂的玻璃制品,如花瓶、酒杯等。
压模具通常由优质的硅胶或聚氨酯材料制成,具有良好的弹性和耐磨性。
3. 手工模具:手工模具适用于制作个性化的玻璃制品,如艺术品、手工玻璃等。
手工模具通常由石膏或木材等材料制成,具有良好的可塑性和可操作性。
二、模具设计要点在进行玻璃模具设计时,需要考虑以下几个要点:1. 正确的模具尺寸:模具尺寸应与最终产品的尺寸相匹配,确保模具制造出的玻璃制品具有正确的形状和尺寸。
2. 模具表面光滑度:模具表面应该光滑平整,以确保玻璃制品的表面质量。
可以通过研磨或采用特殊的涂层来提高模具表面的光滑度。
3. 模具冷却系统:模具制造过程中会产生大量的热量,需要合理设计冷却系统来降低模具温度,防止模具变形或损坏。
4. 模具材料选择:根据具体的生产要求和模具使用环境,选择合适的模具材料。
常用的模具材料有金属、硅胶、聚氨酯等。
三、模具制造流程玻璃模具的制造流程一般包括以下几个步骤:1. 模具设计:根据产品的形状和尺寸要求进行模具设计,确定模具的构造和尺寸。
2. 模具制造:通过数控加工或手工制造方式制造模具。
铸造模具通常需要进行砂型制作和铸造工艺。
3. 模具表面处理:对模具表面进行研磨、打磨或涂层处理,以提高模具表面的光滑度和耐磨性。
4. 模具调试:将制造好的模具安装在玻璃生产线上进行调试,检查模具的适用性和性能。
5. 模具维护:定期清洗和保养模具,以延长模具的使用寿命。
结语玻璃模具设计是玻璃制品生产中不可或缺的环节,一个好的模具设计可以提高生产效率、降低成本,并保证产品的质量。
模具类型介绍

噴嘴的身體(主體) 熱流板的加熱線圈(柔性線圈 或鑽孔﹐然后用加熱棒)
空氣隔熱槽 小導柱﹐比模具導柱小﹐作用是定位和保護 (裝在母模板上時﹐先插入母模板﹐避免碰傷)
-
閥針
夾模槽 熱流板的背板
上固定板
注口襯套 定位環
氣缸 分流板
雙色注塑機:水平直角式博创双色注射机
-
30
雙色注塑機後模運動動作
1.動模板為旋轉 裝置的机構.
2.動模板能作 180度旋轉.
-
31
雙色模頂出機構
-
32
雙色模應用實例:硬膠+硬膠
本產品藍色為普通 ABS+黑色導電ABS
-
33
雙色模應用實例:硬膠+軟膠
硬膠ABS+軟膠TPE
-
34
叠模
一幅两层的疊模通常是由两个单层的模具背对背安装而成,分模面通常依 靠齿轮和齿条机构保持同步打开。两层叠模相比标准模具在生产效率方 面有近乎100%的提升。疊模的层数可以多达十几层,层数主要是受注 塑机的注射容积,容模厚度和开模行程所限。
在結構上﹐上固定板 和母模板之間添加小拉 杆﹐限制上固定板和母 模板之間的運動行程﹔ 在公﹑母模板之間加開 閉器﹐在開模過程中﹐ 保証上固定板和母模板 首先打開﹐行程到位之 后﹐才打開公母模。
-
9
運動過程
第一分型
合模狀態
第二分型
開模狀態
-
10
三板模
▪ 三板模: 在二板模的 基礎上加了一塊活動 的板適 用於中心進料 的多型腔模具
撥塊
開閉器 公模仁
滑塊
公模板 上頂出板 下頂出板
模具设计制造及类型

模具设计制造及类型引言模具是工业制造中非常重要的工具之一,它在产品制造过程中起到了至关重要的作用。
本文将介绍模具设计制造的相关内容,包括模具的基本概念、设计原则、制造工艺以及常见类型。
模具的基本概念模具是用于制造高度一致产品的工具,它能够对原材料进行形状、大小和表面质量的精确控制。
模具可以分为压力模具和注塑模具两类。
压力模具主要用于金属材料的成形加工,而注塑模具则主要用于塑料、橡胶等材料的成形加工。
模具的设计原则模具设计的主要原则是要满足产品的设计要求,保证成形品的尺寸精度、表面质量和生产效率。
以下是模具设计的一些重要原则:1.合理的造型设计:模具的造型设计应该符合产品的要求,保证产品的功能和外观。
2.简化工艺流程:模具的设计应尽量简化工艺流程,减少加工步骤,提高生产效率。
3.合理的材料选择:模具的材料应根据所加工材料的性质和生产要求选择,以保证模具的寿命和使用效果。
模具的制造工艺模具的制造工艺包括模具的加工和装配两个主要过程。
模具的加工模具的加工包括以下几个主要步骤:1.图纸设计:根据产品的设计要求,制作出模具的详细设计图纸。
2.材料准备:根据设计图纸的要求,选择合适的材料,并进行材料的切割和加工。
3.零件加工:将模具的各个零件进行精确加工,包括铣削、车削、磨削等工艺。
4.热处理:对于一些需要提高材料硬度和强度的零件,需要进行热处理工艺。
5.组装调试:将加工好的模具零件进行组装,进行调试和检验。
模具的装配模具的装配是将加工好的模具零件进行组合,形成完整的模具结构。
模具的装配过程需要严格按照设计要求进行,保证模具的精确度和稳定性。
常见模具类型模具的类型根据其用途和工艺不同可分为以下几种:1.压铸模具:用于金属材料的熔铸和压制成形,广泛应用于汽车、机械等行业。
2.塑料注塑模具:用于塑料材料的熔化和注射成形,广泛应用于电子、家电等行业。
3.橡胶模具:用于橡胶材料的热压制造,广泛应用于橡胶制品生产。
4.压力模具:用于金属材料的冲压加工,广泛应用于汽车、家电等行业。
模具的产品模和商品模
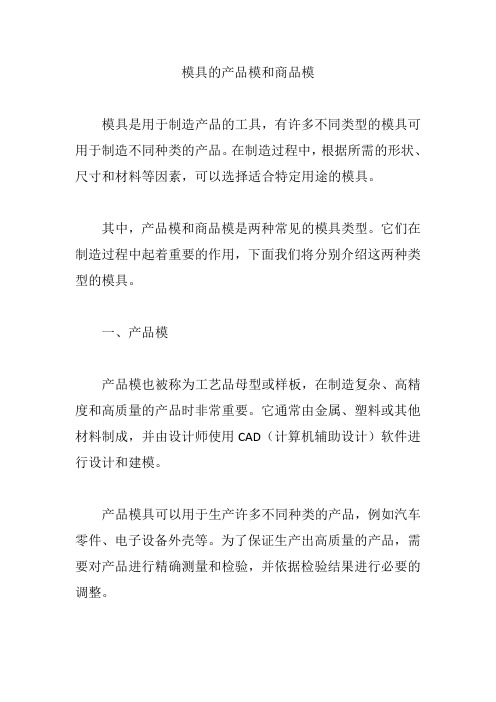
模具的产品模和商品模模具是用于制造产品的工具,有许多不同类型的模具可用于制造不同种类的产品。
在制造过程中,根据所需的形状、尺寸和材料等因素,可以选择适合特定用途的模具。
其中,产品模和商品模是两种常见的模具类型。
它们在制造过程中起着重要的作用,下面我们将分别介绍这两种类型的模具。
一、产品模产品模也被称为工艺品母型或样板,在制造复杂、高精度和高质量的产品时非常重要。
它通常由金属、塑料或其他材料制成,并由设计师使用CAD(计算机辅助设计)软件进行设计和建模。
产品模具可以用于生产许多不同种类的产品,例如汽车零件、电子设备外壳等。
为了保证生产出高质量的产品,需要对产品进行精确测量和检验,并依据检验结果进行必要的调整。
由于其复杂性和高精度要求,一些大型企业会拥有自己专门生产产品模具的工厂。
这种方式可以提供更快速、便捷且成本更低廉地得到标准化组件。
二、商品模商品模又被称为包装印刷模,是用于制造产品包装和标签等的模具。
通常由橡胶、木材或其他材料制成。
商品模具可以用于制造各种形状的包装盒、袋子和容器等。
在商品生产过程中,商品模是必不可少的一部分。
它在生产过程中起着关键作用,需要根据特定的设计要求进行精确制造。
常见的商品模包括印刷机上使用的滚筒和柔性印版等。
与产品模相比,商品模通常需要更频繁更换或更新。
因为随着市场需求和消费趋势发生变化,企业需要更改他们的包装形式或设计风格。
这就需要制造新的商品模以适应不断变化的市场需求。
总结无论是产品模还是商品模,它们都是现代生产中不可或缺的一部分。
它们可以帮助企业快速生产高质量、符合市场需求并且能够满足消费者要求的产品。
随着技术和市场需求不断变化,这两种类型的模具也将继续发展和改进,以适应未来生产环境下可能出现的新挑战。
钣金模具分类

钣金模具分类
钣金模具是制作钣金件所必需的工具之一,随着钣金加工的不断发展,钣金模具也逐渐多样化。
下面,我们来了解一下钣金模具的分类。
1. 折弯模具
折弯模具是最常见的钣金模具,用于将钣金弯曲成所需的形状,例如U形、V形和Z形等。
多数是由上下两模组成,也有单模和复合模式。
折弯模具分为手动操作和自动化操作两种,手动操作通常适用于小批量加工,而自动化操作适用于大批量加工。
2. 切割模具
切割模具用于将钣金材料切割成所需的形状。
常用的模具有拉板刀、激光切割模具和剪切模具等。
根据切割的不同方式,可以分为冲剪模具、摆式模具和激光切割模具等。
3. 成形模具
成形模具是将钣金材料按照所需的形状进行加工的模具。
通常需要先经历多道弯曲、切割和凹凸加工等工序。
成形模具的类型有很多种,如拉伸模具、冲床模具、修整模具和成形机等。
4. 成品模具
成品模具是将钣金加工成成品的模具。
例如,汽车钣金的车门、车身等都是通过成品模具来加工。
成品模具的制造需要考虑到各种适用性要求和复杂的加工工艺。
综上所述,钣金模具的分类有折弯模具、切割模具、成形模具和成品模具。
根据加工的要求和需求来选择相应的模具类型,可以提高工作效率和产品质量。
在使用钣金模具时,要注意使用和维护,以确保模具的寿命和效率。
- 1、下载文档前请自行甄别文档内容的完整性,平台不提供额外的编辑、内容补充、找答案等附加服务。
- 2、"仅部分预览"的文档,不可在线预览部分如存在完整性等问题,可反馈申请退款(可完整预览的文档不适用该条件!)。
- 3、如文档侵犯您的权益,请联系客服反馈,我们会尽快为您处理(人工客服工作时间:9:00-18:30)。
六、模具类型(Mold Types):
两板模(Two-Plate Molds)﹕
两板模是最常用的模具类型,与三板模比较,两板模具有成本低、结构简单及成型周期短的优点。
单模穴两板模
许多单穴模具采用两板模的设计方式,如果你的产品只用一个浇口,不要流道,那么塑料会由竖流道直接流到型腔中。
多模穴与家族模穴两板模
你可以使用两板模在一模多穴和家族模穴模中,但是这种结构中限制进浇的位置,因为在两板模中流道和浇口也位于分模面上,这样他们才能随开模动作一起作业。
在你设计多穴模具之前,你应该分析单个成品(分析类型用Part Only)来决定浇口位置。
如果分模面与浇口在同一线上,那么就能用两板模。
当你设计一模多穴的模具时,到
达流动平衡对你设计流道是重要的。
对于一模多穴而言,使用常用的两板
模结构,使各模穴的流动到达平衡不
大可能,因此你或许要用三板模或者
用热流道的两板模代替。
采用热流道的两板模
它能保证塑料以熔融状态通过竖流道、横流道、浇口,只有到了模穴时才开始冷却、凝固。
当模具打开时,成品(或冷流道)被顶出,当模具再次关闭时,流道中的塑料仍然是热的,因此可以直接充填模穴,此种模具中的流道可能由冷热两部分组成。
采用热流道的两板模可以用来改变成三板模。
在这种模具中,进浇位置必需放在模穴中心,以避免在成品可见侧上留下痕迹,这就意味着流道
必需远离分模面。
(脱模时避免碰
到划伤)
假设你使用热流道模具,流
道不需顶出,因此流道远离分模面也不会引起任何问题。
热流道也适用于小产品的一模多穴模具中,假如有许多小产品,常用的流道系统可能会浪费许多材料,如果它不能回收的话。
热流道的优点:
较少的废料,无需回收
较不明显的浇口痕迹
可以不要切除浇口
缩短成型周期
可较大程度上控制模穴充填和胶体流动
热流道的缺点:
较高的成本
难于改变材料颜色
易于出故障,特别是加热控制系统
对热敏性材料不适用
对高数量、高品质的产品,采用热流道系统利大于弊。
在有些案中,最好的结果也许是采用热流道与冷流道的结合。
三板模(Three-Plate Molds)﹕
三板模的流道系统位于与主分模面平行的拨料板上,开模时拨料板顶出流道及衬套内的废料,在三板模中流道与成品将分开顶出。
当整个流道系统不可能与浇口放于同一平板上时,使用三板模。
这可能因为:
模具包含多穴或家族模穴;
一模一穴较复杂的成品需要多个进浇点;
进浇位置在不便于放流道的地方;
平衡流动要求流道设计在分模面以外的地方。
你也可以用热流道的两板模来解决上面的问题,但是三板模有其优势所在:
三板模的优点三板模的缺点
比热流道易于制造因顶出系统的原困,循环周期较长不易出故障材料浪费较大
对热敏性材料不会有劣化作用需要较大的注射压力
七、流道系统设计:
浇口:
浇口、流道与竖流道是用来将熔胶从喷嘴传输到每个模穴的进浇位置的工具。
下面的图解显示了多模穴两板模的典型流道系统:
浇口连接流道与模穴,当你设计浇口时,你应当把下列因素考虑进去:
产品的表面质量
浇口的切除
所用的材料
顶出部分的体积
在你设计流道系统之前,你应当对每个模穴运行Part Only分析,以找到最好的浇口位置。
对于表面要求严格的产品,浇口应设计窄小一些,以免在外观面留下大的痕迹。
一个小口子也将留下痕迹。
你应当将浇口做短一点,以免浇口处产生大的压力降。
避免浇口与流道的接触角太尖,因为这可以加大系统的压力降。
你应在连接处做一个圆角,这样就不会阻碍胶体的流动。
你的浇口的截面形状取决于流道的截面形状。
流道布置:
流道的设计影响到使用材料的用量以及产品的品质。
假如每个模穴的流动不平衡,过渡保压和滞流就会引起较差的产品品质。
又长又不合理的流道设计,能引起较大的压力降并且需要较大的注射压力。
使用热流道可以解决这些成型问题。
复杂成品的单穴结构及多穴和家族模穴结构的平衡流道是很重要的。
一般来讲应使流道尽可能短,尽可能有较小的射出重量,并提供平衡的流动。
上图是常用的流道系统,它将提供不平均的流动。
当所有的模穴都充填完毕时,部分产品将被过度保压。
假如你做了这样结构的流道,你可能需要作流道平衡处理。
左上图的流道系统将提供较平衡的流动路径,在这个自然平衡的流道系统中,每个产品的流动路径是相同的。
若有可能,MPA自动产生一个平衡的流道系统。
右上图使用了人工平衡的流道系统,它保留了传统的流道结构形式,但是分流道的直径是不同的。
这可以控制流量,以使各模穴以相同的压力同时充填完。
假如你做了一个常用的流道形式,你可以人为的使它平衡。
1.流道的截面形状:
小的流道直径引起流道内的磨擦升热,因此塑料在流道内温比在
料筒中的高,较高的料温可以减小残余应力及翘曲变形的倾向,但是高料温易引起材料的劣化。
为使材料尽量少浪费,并降低所需的料筒温度,应设计小截面的流道。
流道的截面形状影响到塑料在流道中的流动,当热的熔胶碰到冷的模壁时,在流道表面会形成一层凝固层。
当塑料被注入模穴中时,流道的中心保持熔融状态。
流道的形状影响到在内部的熔融塑料的体积。
圆形截面的流道能够最大比例的保持熔融状态的塑料。
有曲线或尖角的截面比矩形截面的流道需要较小的力移除流道废料。
尽管从材料流动及顶出的角度来讲,圆形流道是最好的选择,但是它的造价是最高的。
这其中的原因部分是因为这种流道必需被均匀分成两个半圆,而使这两个半圆精确的配合是很难加工的。
梯形截面流道是较折衷的选择,它常可提供较合理的流动形式和顶出特性,并且比圆形流道的成本低。
假如你想采用一个圆形流道,你还要考虑到将两个半圆流道对齐,以致于流道废料能够被顶出。
如下图,左边的流道对齐得很好,右边的流道错位,只有一个很小的熔化层来约束流动。
竖流道
竖流道是与注射喷嘴接触,延伸进入模具的部分,在单模穴的只
有一个进浇位置的模具中,竖流道与模穴壁相交汇。
竖流道的开口要尽可能小,但是必须完全充满模具。
竖流道上的锥角应该足够大,使它能被容易推出,但不能太大,因为冷却时间和所使用的材料会随着竖流道直径的增加而变大。