自动车床计算公式
车床工作时间计算公式
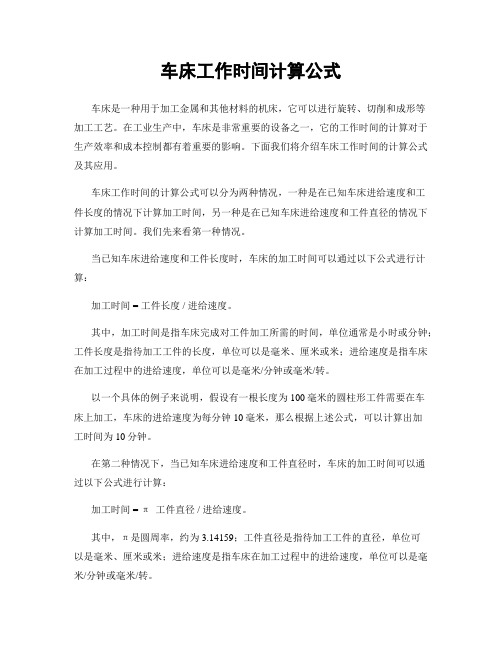
车床工作时间计算公式车床是一种用于加工金属和其他材料的机床,它可以进行旋转、切削和成形等加工工艺。
在工业生产中,车床是非常重要的设备之一,它的工作时间的计算对于生产效率和成本控制都有着重要的影响。
下面我们将介绍车床工作时间的计算公式及其应用。
车床工作时间的计算公式可以分为两种情况,一种是在已知车床进给速度和工件长度的情况下计算加工时间,另一种是在已知车床进给速度和工件直径的情况下计算加工时间。
我们先来看第一种情况。
当已知车床进给速度和工件长度时,车床的加工时间可以通过以下公式进行计算:加工时间 = 工件长度 / 进给速度。
其中,加工时间是指车床完成对工件加工所需的时间,单位通常是小时或分钟;工件长度是指待加工工件的长度,单位可以是毫米、厘米或米;进给速度是指车床在加工过程中的进给速度,单位可以是毫米/分钟或毫米/转。
以一个具体的例子来说明,假设有一根长度为100毫米的圆柱形工件需要在车床上加工,车床的进给速度为每分钟10毫米,那么根据上述公式,可以计算出加工时间为10分钟。
在第二种情况下,当已知车床进给速度和工件直径时,车床的加工时间可以通过以下公式进行计算:加工时间 = π工件直径 / 进给速度。
其中,π是圆周率,约为3.14159;工件直径是指待加工工件的直径,单位可以是毫米、厘米或米;进给速度是指车床在加工过程中的进给速度,单位可以是毫米/分钟或毫米/转。
同样以一个具体的例子来说明,假设有一个直径为50毫米的圆柱形工件需要在车床上加工,车床的进给速度为每分钟5毫米,那么根据上述公式,可以计算出加工时间为31.4159分钟,约合31分钟。
通过上述两种情况的计算公式,我们可以看到车床工作时间的计算是非常简单的,只需要知道工件的长度或直径以及车床的进给速度就可以进行计算。
这些计算公式在工业生产中非常实用,可以帮助生产管理人员合理安排生产计划,提高生产效率,降低生产成本。
除了上述的基本计算公式外,车床工作时间的计算还可以根据具体的加工工艺和车床的性能特点进行更精确的计算。
车床加工报价计算公式

数控车床加工的报价问题是个比较复杂的问题,主要因素有以下几点:首先是加工批量问题,单件和大批量价格可能相差很大了。
第二是工件的复杂程度和公差特别是形位公差,也就是精度等级,这对工件的报价影响也很大。
第三是当地的小时费率,也有很大的关系;还有就是材料了,是易切削程度了,这些因素都影响报价的,所以报价问题是个综合问题。
假定你外径是18mm的话,一个M16的螺杆,长度是20mm,来料加工,材料为不锈钢那你先车外径需要一刀,假定转速为120转/分钟,进给量0.1mm,那么就可以算出一刀的时间是24÷(120×0.1)约为2min(24=工件20+退尾宽度及切刀宽度);第二道工步是车螺扣,M16螺纹是2mm螺距,那么20长就是10圈,加上退尾宽度起码得12圈,按照60转/分钟的话就是0.2分钟,每刀退回按0.2分钟的一半算就是0.1分钟,加起来车螺扣每刀就是0.3分钟,这个螺纹粗车四刀精车一刀算就是0.3×5=1.5分钟。
第三工步是切断,按每转0.1进给量、100转/分钟计算,就是16÷(100×0.1)=1.6分钟以上工时总共为2+1.5+1.6=5.1分钟如果是单件的话,加辅助时间30分钟=35.1分钟批量就按批量大小适当的加一点工时,比如500件的话可以给到6分钟了数控车床加工持续研发、进行产品创新。
下来就是小时费率了,按数控30元/小时计算单件35.1×(30÷60)=17.55元/件批量500件:6×(30÷60)=3元/件材料+加工工时)*1.3*1.08=元/件加工工时要换算成钱.我们这里是这样算的.每个地方都不同1.3是30%的利润.1.08是8%的税。
车床每转进给计算公式(一)

车床每转进给计算公式(一)
车床每转进给
概述
车床每转进给是机床加工过程中一个重要的参数,表示车削工具
在车床上每转动一周所移动的距离。
它是计算和控制车削过程中切削
速度和进给速度的关键参数。
计算公式
车床每转进给可以用以下公式来计算:
车床每转进给(mm/r)= 主轴进给速度(mm/min)/ 主轴转速
(r/min)
其中,主轴进给速度指的是车削工具在车床上每分钟移动的距离,主轴转速则是指主轴每分钟旋转的圈数。
示例
示例1:
假设主轴进给速度为200 mm/min,主轴转速为100 r/min,那么
根据上述公式,可以计算得到
车床每转进给 = 200 mm/min / 100 r/min = 2 mm/r
这意味着车削工具在车床上每转动一周,将移动2毫米的距离。
示例2:
如果主轴进给速度为500 mm/min,主轴转速为250 r/min,那么
车床每转进给 = 500 mm/min / 250 r/min = 2 mm/r
同样地,车削工具在车床上每转动一周,仍然移动2毫米的距离。
结论
通过计算和控制车床每转进给,可以有效地控制车削过程中的切
削速度和进给速度。
根据实际加工需求,合理调整主轴进给速度和主
轴转速,可以获得更高的加工效率和加工质量。
综上所述,车床每转进给作为机床加工过程中的关键参数,其计
算公式可以帮助我们准确地确定车削过程中切削速度和进给速度的关系。
车床线速度计算公式

车床线速度计算公式
1 汽车床线速度计算公式
汽车床线速度计算是机床加工中十分重要的一项内容,其计算方
法可以概括为:线速度=切削前进量/切削时间。
根据机床工作的型号、加工参数、切削角度等,汽车床的线速度的可以用以下的公式计算:线速度(m/min)=200×切削前进(mm)/切削时间(min)×π÷
切削角度
这是一个通用的公式,单位不同的情况下应对单位做相应的转换。
如果被加工件的切削角度为180度,那么这个切削角度在公式中应该
被忽略,"π"可以被换算为3。
计算方法比较简单,但在实际工作中还要考虑到滚刀速度、加工停顿时间等其他因素,进而得出最终改变加
工参数时使用的最优解。
同时,对于汽车床来说,其圆柱性切削角度
越小,线速度越高,因此,还要根据每一次加工的具体情况,加以调整,以达到最优的加工效果。
以上是关于汽车床线速度计算的方法,只有正确算出来汽车床的
线速度,才能确保机床正常运行,加工效果才能达到预期。
数控车床编程教学计算公式

数控车床编程教学计算公式数控车床是一种通过预先编写的程序来控制刀具和工件之间的相对运动,从而实现对工件进行加工的机床。
数控车床编程是数控加工技术中的重要环节,它涉及到各种计算公式的运用。
本文将介绍数控车床编程中常用的计算公式,并对其进行详细解析。
1. 切削速度(Vc)的计算公式。
切削速度是指刀具在加工过程中与工件接触的线速度,它是数控车床加工过程中的重要参数。
切削速度的计算公式为:Vc = π D n。
其中,Vc为切削速度,π为圆周率(取3.14),D为刀具直径,n为主轴转速。
2. 进给速度(F)的计算公式。
进给速度是指刀具在加工过程中沿着工件表面的运动速度,它也是数控车床加工的重要参数。
进给速度的计算公式为:F = f n z。
其中,F为进给速度,f为进给量,n为主轴转速,z为刀具的刃数。
3. 主轴转速(n)的计算公式。
主轴转速是指主轴每分钟的转动次数,它是数控车床加工中的另一个重要参数。
主轴转速的计算公式为:n = (1000 Vc) / (π D)。
其中,n为主轴转速,Vc为切削速度,π为圆周率,D为刀具直径。
4. 切削力(Fc)的计算公式。
切削力是指刀具在加工过程中对工件施加的力,它是衡量刀具加工性能的重要指标。
切削力的计算公式为:Fc = k ap ae。
其中,Fc为切削力,k为切削力系数,ap为切削深度,ae为切削宽度。
5. 切削功率(Pc)的计算公式。
切削功率是指刀具在加工过程中消耗的功率,它是衡量刀具加工效率的重要指标。
切削功率的计算公式为:Pc = Fc Vc。
其中,Pc为切削功率,Fc为切削力,Vc为切削速度。
以上是数控车床编程中常用的计算公式,这些公式在数控车床编程中起着至关重要的作用。
掌握这些计算公式,能够帮助工程师更好地进行数控车床编程,并且能够更加准确地控制加工过程,提高加工效率,降低加工成本。
除了以上介绍的计算公式外,数控车床编程还涉及到其他一些参数的计算,比如切削时间、切削深度、切削宽度等。
车床转矩计算公式

车床转矩计算公式
转矩,即扭矩,公式有:
1、扭矩公式:T=9550P/n,T是扭矩,单位N•m,P是输出功率,单位KW,n 是电机转速,单位r/min。
2、扭矩公式:T=973P/n,T是扭矩,单位Kg•m;P是输出功率,单位KW;n是电机转速,单位r/min。
3、转速公式:n=60f/P(n=转速,f=电源频率,P=磁极对数)。
含义:1kg=9.8N 1千克的物体受到地球的吸引力是9.8牛顿。
含义:9.8N•m 推力点垂直作用在离磨盘中心1米的位置上的力为了9.8N。
扩展资料:
转矩中直接转矩的原理:
在直接转矩控制中,电机定子磁链的幅值通过上述电压的矢量控制而保持为额定值,要改变转矩大小,可以通过控制定、转子磁链之间的夹角来实现。
而夹角可以通过电压空间矢量的控制来调节。
由于转子磁链的转动速度保持不变,因此夹角的调节可以通过调节定子磁链的瞬时转动速度来实现。
假定电机转子逆时针方向旋转,如果实际转矩小于给定值,则选择使定子磁链逆时针方向旋转的电压矢量,这样角度增加,实际转矩增加,一旦实际转矩高与给定值,则选择电压矢量使定子磁链反方向旋转。
从而导致角度降低。
通过这种方式选择电压矢量,定子磁链一直旋转,且其旋转方向由转矩滞环控制器决定。
数控车床常用计算公式

数控车床常用计算公式数控车床是数控系统控制的自动化设备,可以在制造过程中自动完成加工操作。
在数控车床加工中,需要使用一些计算公式来帮助确定加工参数和加工结果。
下面是一些常用的数控车床计算公式。
一、转速和进给速度相关公式:1.主轴转速公式:主轴转速(n)=(切削速度(vc)×1000)÷(π×刀具直径(d))2.进给速度公式:进给速度(f)= 主轴转速(n)× 进给定址(fz)3.进给定址公式:进给定址(fz)=(切削率(s)× 刀具转数(n))÷ 切削深度(h)4.切削速度公式:切削速度(vc)= π×刀具直径(d)×主轴转数(n)÷1000其中,切削率(s)是切削宽度与进给量的比值,切削深度(h)是切削道深度。
二、加工时间相关公式:1.钻孔时间公式:钻孔时间(T1)=钻孔长度(l)÷进给速度(f)2.镗孔时间公式:镗孔时间(T2)=镗孔长度(l)÷进给速度(f)3.攻丝时间公式:攻丝时间(T3)=攻丝长度(l)÷进给速度(f)4.车削时间公式:车削时间(T4)=加工长度(l)÷进给速度(f)其中,加工长度(l)是指加工的工件长度。
三、进给量和切削深度相关公式:1.切削深度公式:切削深度(h)= 可切削余量(ae)+ 刀具半径(r)2.进给量公式:进给量(f)=切削率(s)×刀具宽度(b)其中,可切削余量(ae)是工件加工前与刀具的间隙,刀具半径(r)是刀具直径的一半。
四、加工精度相关公式:1.长度误差公式:长度误差(ΔL)=加工长度(L)-设计长度(L0)2.直线度误差公式:直线度误差(Δd)= 平均残余简化误差(E)× 每20mm测量长度(L)3.圆度误差公式:圆度误差(Δr)= (最大切削直径(Dmax)- 最小切削直径(Dmin))÷ 2其中,设计长度(L0)是工件在设计中规定的长度,平均残余简化误差(E)是多次加工中各测量长度差的平均值。
车床工时计算法
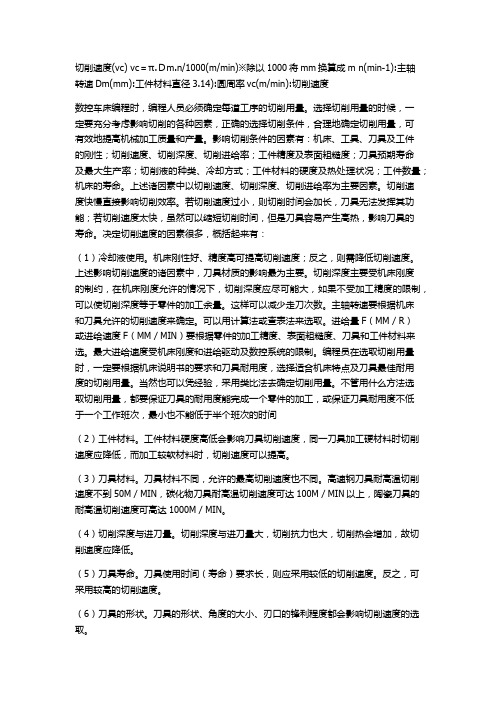
切削速度(vc) vc=π.Dm.n/1000(m/min)※除以1000将mm换算成m n(min-1):主轴转速Dm(mm):工件材料直径3.14):圆周率vc(m/min):切削速度数控车床编程时,编程人员必须确定每道工序的切削用量。
选择切削用量的时候,一定要充分考虑影响切削的各种因素,正确的选择切削条件,合理地确定切削用量,可有效地提高机械加工质量和产量。
影响切削条件的因素有:机床、工具、刀具及工件的刚性;切削速度、切削深度、切削进给率;工件精度及表面粗糙度;刀具预期寿命及最大生产率;切削液的种类、冷却方式;工件材料的硬度及热处理状况;工件数量;机床的寿命。
上述诸因素中以切削速度、切削深度、切削进给率为主要因素。
切削速度快慢直接影响切削效率。
若切削速度过小,则切削时间会加长,刀具无法发挥其功能;若切削速度太快,虽然可以缩短切削时间,但是刀具容易产生高热,影响刀具的寿命。
决定切削速度的因素很多,概括起来有:(1)冷却液使用。
机床刚性好、精度高可提高切削速度;反之,则需降低切削速度。
上述影响切削速度的诸因素中,刀具材质的影响最为主要。
切削深度主要受机床刚度的制约,在机床刚度允许的情况下,切削深度应尽可能大,如果不受加工精度的限制,可以使切削深度等于零件的加工余量。
这样可以减少走刀次数。
主轴转速要根据机床和刀具允许的切削速度来确定。
可以用计算法或查表法来选取。
进给量F(MM/R)或进给速度F(MM/MIN)要根据零件的加工精度、表面粗糙度、刀具和工件材料来选。
最大进给速度受机床刚度和进给驱动及数控系统的限制。
编程员在选取切削用量时,一定要根据机床说明书的要求和刀具耐用度,选择适合机床特点及刀具最佳耐用度的切削用量。
当然也可以凭经验,采用类比法去确定切削用量。
不管用什么方法选取切削用量,都要保证刀具的耐用度能完成一个零件的加工,或保证刀具耐用度不低于一个工作班次,最小也不能低于半个班次的时间(2)工件材料。
CNC常用计算公式

CNC常用计算公式在数控加工中,常用的计算公式有:1.转速计算公式:转速(rpm)= 配置的主轴转速(rpm)/ 刀具直径(mm)* 主轴转鼓数(转/齿)2.进给速度计算公式:进给速度(mm/min)= 进给速度设定值(mm/min)/ 预设倍率3.切削速度计算公式:切削速度(m/min)= π × 刀具直径(mm)× 主轴转速(rpm)/ 10004.主轴转速计算公式:主轴转速(rpm)= 切削速度(m/min)× 1000 / π × 刀具直径(mm)5.驱动轴向力计算公式:驱动轴向力(N)= 刀具直径(mm)× 进给速度(mm/min)× 切削力系数6.切削力计算公式:切削力(N)= 轴向切削力(N)÷ cos(铣削角度)7.铣削力计算公式:铣削力(N)=铣削切削阻力(kB)×轴向力(kN)^铣削阻力指数8.主轴电机功率计算公式:主轴电机功率(kW)=铣削力(N)×铣削力系数(kW/N)9.等分计算公式:切削刀数 = 刀具直径(mm)× π / 距离圆周长度(mm)10.速度比计算公式:速度比=同刃次数/刀具齿数11.加工时间计算公式:加工时间(min)= 切削长度(mm) / 进给速度(mm/min) + 换刀时间(min)12.总加工时间计算公式:总加工时间(min)= 加工时间(min)× 加工个数 + 装夹时间(min)13.检测时间计算公式:检测时间(min)= 检测长度(mm) / 检测速度(mm/min) + 置零时间(min)14.总时间计算公式:。
车床工时计算
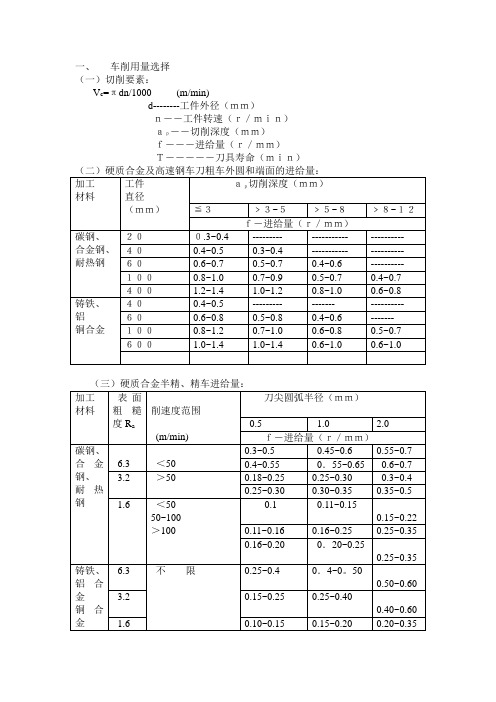
3.2
>50
0.18~0.25
0.25~0.30
0.3~0.4
0.25~0.30
0.30~0.35
0.35~0.5
1.6
<50
50~100
>100
0.1
0.11~0.15
0.15~0.22
0.11~0.16
0.16~0.25
0.25~0.35
0.16~0.20
0.20~0.25
0.25~0.35
≦3
﹥3~5
﹥5~8
﹥8~12
f―进给量(r/mm)
碳钢、
合金钢、
耐热钢
20
0.3~0.4
---------
-----------
----------
40
0.4~0.5
0.3~0.4
-----------
----------
60
0.6~0.7
0.5~0.7
0.4~0.6
----------
100
0.8~1.0
0.112
60
66.9
355
0.280
84.8
450
0.158
84.8
450
0.120
75
65.9
280
0.296
83.6
355
0.172
83.6
355
0.124
95
66.8
224
0.136
83.5
280
0.192
83.6
280
0.136
125
70.6
180
0.316
87.9
224
车床25度倒角计算公式

车床25度倒角计算公式
1、计算公式:倒角长度=(大径-小径)/2/tanα
2、小径=大径-倒角长度×tanα×2
3、大径=小径倒角长度×tanα×2
4、其中的(倒角长度×tanα)计算倒角截面小直角三角形在端面那条边的长度。
5、倒角25°:tan25°约等于0.577,然后计算倒角长度(46.14-38.2)/2/0.577=6.88
6、倒角45°:tan45°,倒角长度(46.14-38.2)/2/1=3.97
7、倒角37°:tan37°,倒角长度(46.14-38.2)/2/0.75=5.29
8、半径差,长度,角度3个条件,只要给了两个,就可以根据上面公式算出另一个。
如果做普车的没给你角度,叫你自己算,要用到反三角函数arctan,自己下个高级计算器,把你得到的数值,输入到arctan中就可以了。
9、如果是最常用的1×45的倒角,倒去部分的每条直角边长度就都是1mm,数控编程时,G01走斜线,Z方向的长度就是1mm,X直径方向因为工件是旋转的,计算时要按2倍算,如工件外径25mm,在外圆上倒角1×45,倒角开始时的坐标就是: X23 Z0,倒角结束时的坐标为 X25 Z-1 ,这个倒角是从工件端面向外圆方向倒角。
如果不是45度倒角,那就要用直角三角函数计算相应坐标。
车床工时计算法

切削速度(vc) vc=π.D1000(m/min)※除以1000将mm换算成m n(min-1):主轴转速Dm(mm):工件材料直径:圆周率vc(m/min):切削速度数控车床编程时,编程人员必须确定每道工序的切削用量。
选择切削用量的时候,一定要充分考虑影响切削的各种因素,正确的选择切削条件,合理地确定切削用量,可有效地提高机械加工质量和产量。
影响切削条件的因素有:机床、工具、刀具及工件的刚性;切削速度、切削深度、切削进给率;工件精度及表面粗糙度;刀具预期寿命及最大生产率;切削液的种类、冷却方式;工件材料的硬度及热处理状况;工件数量;机床的寿命。
上述诸因素中以切削速度、切削深度、切削进给率为主要因素。
切削速度快慢直接影响切削效率。
若切削速度过小,则切削时间会加长,刀具无法发挥其功能;若切削速度太快,虽然可以缩短切削时间,但是刀具容易产生高热,影响刀具的寿命。
决定切削速度的因素很多,概括起来有:(1)冷却液使用。
机床刚性好、精度高可提高切削速度;反之,则需降低切削速度。
上述影响切削速度的诸因素中,刀具材质的影响最为主要。
切削深度主要受机床刚度的制约,在机床刚度允许的情况下,切削深度应尽可能大,如果不受加工精度的限制,可以使切削深度等于零件的加工余量。
这样可以减少走刀次数。
主轴转速要根据机床和刀具允许的切削速度来确定。
可以用计算法或查表法来选取。
进给量F(MM/R)或进给速度F(MM/MIN)要根据零件的加工精度、表面粗糙度、刀具和工件材料来选。
最大进给速度受机床刚度和进给驱动及数控系统的限制。
编程员在选取切削用量时,一定要根据机床说明书的要求和刀具耐用度,选择适合机床特点及刀具最佳耐用度的切削用量。
当然也可以凭经验,采用类比法去确定切削用量。
不管用什么方法选取切削用量,都要保证刀具的耐用度能完成一个零件的加工,或保证刀具耐用度不低于一个工作班次,最小也不能低于半个班次的时间(2)工件材料。
工件材料硬度高低会影响刀具切削速度,同一刀具加工硬材料时切削速度应降低,而加工较软材料时,切削速度可以提高。
车床每转进给计算公式

车床每转进给计算公式
车床每转进给的计算公式为:
每转进给=切削进给速度÷ (主轴转速×主轴进给倍率)
其中,
切削进给速度是指刀具在工件表面上的移动速度,通常用毫米每转(mm/rev)或英寸每转(inch/rev)表示;
主轴转速是指车床主轴每分钟旋转的圈数,通常用转数每分钟(rpm)表示;
主轴进给倍率是指主轴每转带动工件沿轴向移动的距离。
拓展:
车床是一种常见的金属切削机床,常用于加工轴类零件。
控制车床切削进给的公式涉及到切削速度和主轴转速等参数的计算,以确保切削过程中切削进给的准确性和稳定性。
切削速度是刀具切削边缘在工件表面上的移动速度。
切削速度的选择受到材料性质、切削过程要求和刀具材料等因素的影响。
一般来说,不同的材料和加工要求需要选择不同的切削速度,以保证加工质量和切削寿命。
主轴转速是车床主轴旋转的速度,决定了工件表面上切削点的相对位置和切削速度的大小。
主轴转速的选择与材料性质、刀具类型和切削过程要求等因素有关。
合理选择主轴转速可以提高加工效率和加工质量。
主轴进给倍率是主轴每转带动工件沿轴向移动的距离。
主轴进给倍率的选择与切削要求、工件长度和加工条件等因素有关。
较小的主轴进给倍率可以提高加工精度,而较大的主轴进给倍率可以提高加工效率。
在车床加工中,准确计算和控制车床每转进给对于加工精度和加工效率都非常重要。
通过调整切削进给速度、主轴转速和主轴进给倍率等参数,可以实现切削进给的准确控制,以满足不同的加工需求。
车床用料重量计算公式
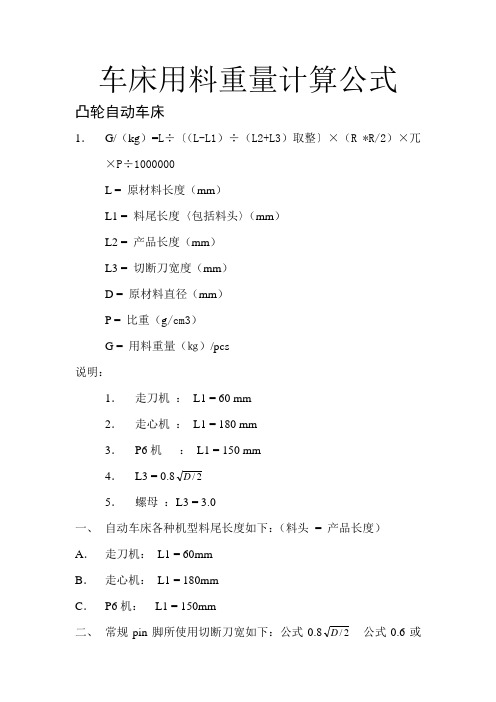
车床用料重量计算公式凸轮自动车床1.G/(kg)=L÷〔(L-L1)÷(L2+L3)取整〕×(R *R/2)×兀×P÷1000000L = 原材料长度(mm)L1 = 料尾长度〈包括料头〉(mm)L2 = 产品长度(mm)L3 = 切断刀宽度(mm)D = 原材料直径(mm)P = 比重(g/cm3)G = 用料重量(㎏)/pcs说明:1.走刀机:L1 = 60 mm2.走心机:L1 = 180 mm3.P6机:L1 = 150 mm4.L3 = 0.82/D5.螺母:L3 = 3.0一、自动车床各种机型料尾长度如下:(料头= 产品长度)A.走刀机:L1 = 60mmB.走心机:L1 = 180mmC.P6机:L1 = 150mm二、常规pin脚所使用切断刀宽如下:公式0.82/D公式0.6或0.82/DCu :φZ-φ4.0使用刀0.8mm-1.6mmCu:φ5.0-φ8.0使用刀宽为1.2mm-2.0mmCu:φ9.0 —φ12.0使用刀宽为2.2mm — 3.0mm三、螺母系列用切断刀宽如下:(一般取3mm)M2.6×0.45以下刀宽厚为2.7mmM3×0.5以下刀宽厚为3.0mmM2×0.45以下刀宽厚为2.5mm例题:1.走心机:如R620为φ4×40.5之规格指令量为20000根据公式算如下:Cu: G(㎏) = 2500÷〔(2500-160 -40.5)÷(40.5+1.0)〕×4×3.14×8.5÷1000000 = 0.0048(再用0.0048*20000) = 96.35kg2. 走刀机: 如R525C为φ5.04×20.8之规格Cu : G(㎏) = 2500÷〔(2500-65-20.8)÷(20.8+1.2)〕×3.14×8.5÷1000000 = 0.003793. P6机如R411为φ4.0×28.0之规格Cu : G(kg) = 2500/〔(2500-180-28.0)/29〕*4*3.14*8.5/1000000=0.00334.如:INSCRT系列产品R457A为φ6.0*7.0规格Cu :G(kg)= 2500/〔(2500-65-7.0)/(7+3)〕*9*3.14*8.5/1000000 = 0.002476.松腾系列R486为φ3.8*12规格Cu:G(kg)= 2500/〔(2500-65-12)/(12+1.5)〕*3.6*3.14*8.6/1000000=0.001357.如不锈钢R198为φ9.0*12.5之规格SUS:G(kg)= 2500/〔(2500-65-12.5)/(12.5+2.7)〕*20*3.14*7.85/1000000 = 0.007758.如铝料T025为φ6.0*6.5之规格AL :G(kg)= 2500/〔(2500-65-6.5)/(12.5+1.8)〕*9*3.14*2.5/1000000 = 0.001※.括号内带下划线的数字为刀宽凸轮自动车床(圆料)1.G = L/〈(L-L1)/(L2+L3)取整>*(D/2)*(D/2)*兀*P/1000000L = 原材料长度(mm)L1 = 料尾长度(包括料头)(mm)L2 = 产品长度(mm)L3 = 切断刀宽度(mm)D = 原材料直径(mm)P = 比重(g/cm3)G = 用料重量(㎏)/pcs2.六角棒材的用料计算公式G = L/<(L-L1)/(L2+L3)取整>*0.866*H*H*兀*P/1000000L = 原材料长度(mm)L1 = 料尾长度(包括料头)(mm)L2 = 产品长度(mm)L3 = 切断刀宽度(mm)D = 原材料直径(mm)P = 比重(g/cm3)G = 用料重量(㎏)/pcs3.方料(四方)G = L/<(L-L1)/(L2+L3)取整>*a*b*p/1000000L = 原材料长度(mm)L1 = 料尾长度(包括料头)(mm)L2 = 产品长度(mm)L3 = 切断刀宽度(mm)a = 边长(mm)b =边长(mm)G = 用料重料(㎏)/PCS说明:A 走刀机:L1 = 60mB 走心机:L1 = 180mC P6机:L1 = 150mD L3 = 0.82/D(1.走心机和P6机加0.2mm 2. 不锈钢再加0.2mm)E. 螺母: L3 = 3.0一、常规PIN脚所使用切断刀宽如下:公式0.82/DCu :φZ-φ4.0使用刀0.8mm-1.6mmCu:φ5.0-φ8.0使用刀宽为1.2mm-2.0mmCu:φ9.0 —φ12.0使用刀宽为2.2mm — 3.0mm二、螺母系列用切断刀宽如下:(一般取3mm)M2.6×0.45以下刀宽厚为2.7mmM3×0.5以下刀宽厚为3.0mmM2×0.45以下刀宽厚为2.5mm。
数控车床常用计算公式

数控车床常用计算公式 Company Document number:WTUT-WT88Y-W8BBGB-BWYTT-19998直径Φ倒角量a 角度θ正切函数tanθ正弦函数sinθ余弦函数cosθ圆弧半径R 乘以号x除以号÷先运算()内结果,再运算【】,再运算全式一、外圆倒斜角计算公式例子:Φ30直径外端倒角°程式:GoX32Z21,倒角起点直径2,倒角起点长度Z=0其中tan60°由数学用表查出3,倒角收点直径X=Φ;G1Z-504,倒角收点长度Z=-a。
二、内圆倒斜角计算公式例子:Φ20孔径外端倒角2x60°程式:GoX18Z21,倒角起点直径2,倒角起点长度Z=3,倒角收点直径X=Φ;G1Z-304,倒角收点长度Z=-a。
三、外圆倒圆角计算公式例子:Φ35直径外端圆角R3程式:GoX36Z21,倒角起点直径X=Φ-2*RX=35-2x3=2,倒角起点长度Z=3,倒角收点直径X=Φ;G1Z-304,倒角收点长度Z=-R。
四、内圆倒圆角计算公式例子;Φ20孔径外端圆角R2程式:G0X18Z21,倒角起点直径X=Φ+2*RX=20+2x2=2,倒角起点长度Z=3,倒角收点直径X=Φ;G1Z-254,倒角收点长度Z=-R。
五、G90、G92数控指令R锥度值的计算:例子:大端Φ35小端Φ32锥体长20牙长16mm让刀3mm加工1、计算图上锥度比例值:(32-35)/20=程式;G0X37Z3(起始端直径-收点端直径)÷锥体长度2、计算G92实际R值(车牙时,起始端至收点端的半径差):2X(16+3)=锥度比例值x1/2x(有效牙长度+让刀位置)3、G92的收刀点直径:35+((20-16))-2X1=锥体收点端直径+锥度比例值x(锥体长度—有效螺纹长度)—2x牙高。
六、球冠的高度计算公式:1、当截面为劣弧时。
球冠高度=R-【R2-(X/2)2)】的方差的平方根2、当截面为优弧时。
车床每转进给计算公式

车床每转进给计算公式
车床每转进给计算公式是根据车床的进给速率和主轴转速来计算的。
进给速率是工件在车削过程中每分钟移动的距离,主要有纵向进给和横向
进给两种。
主轴转速是主轴每分钟转动的圈数。
下面将分别介绍纵向进给
和横向进给的计算公式。
假设车床主轴转速为N,纵向进给速率为f。
纵向进给计算公式如下:每转纵向进给量=f/N
假设车床主轴转速为N,横向进给速率为f。
横向进给计算公式如下:每转横向进给量=f/N
需要注意的是,进给速率和主轴转速之间的单位必须一致,通常为
mm/min或者mm/rev。
如果单位不一致,需要进行单位转换。
此外,如果要计算整个工件的总进给量,可以使用以下公式:
总进给量=每转进给量*工件周长
例如,假设车床主轴转速为1000 rpm,纵向进给速率为0.1 mm/rev,横向进给速率为0.2 mm/rev,工件周长为250 mm,则纵向和横向的每转
进给量分别为:
每转纵向进给量 = 0.1 mm/rev / 1000 rpm = 0.0001 mm/rpm
每转横向进给量 = 0.2 mm/rev / 1000 rpm = 0.0002 mm/rpm
总进给量=每转纵向进给量*工件周长+每转横向进给量*工件周长
= 0.0001 mm/rpm * 250 mm + 0.0002 mm/rpm * 250 mm
= 0.025 mm + 0.05 mm
= 0.075 mm
因此,整个工件的总进给量为0.075 mm。
- 1、下载文档前请自行甄别文档内容的完整性,平台不提供额外的编辑、内容补充、找答案等附加服务。
- 2、"仅部分预览"的文档,不可在线预览部分如存在完整性等问题,可反馈申请退款(可完整预览的文档不适用该条件!)。
- 3、如文档侵犯您的权益,请联系客服反馈,我们会尽快为您处理(人工客服工作时间:9:00-18:30)。
国际标准
一、挤牙丝攻内孔径计算公式:
公式:牙外径-1/2×牙距
例1:公式:M3×0.5=3-(1/2×0.5)=2.75mm M6×1.0=6-(1/2×1.0)=5.5mm
例2:公式:M3×0.5=3-(0.5÷2)=2.75mm M6×1.0=6-(1.0÷2)=5.5mm
二、一般英制丝攻之换算公式:
1英寸=25.4mm(代码)
例1:(1/4-30)
1/4×25.4=6.35(牙径)
25.4÷30=0.846(牙距)
则1/4-30换算成公制牙应为:M6.35×0.846
例2:(3/16-32)
3/16×25.4=4.76(牙径)
25.4÷32=0.79(牙距)
则3/16-32换算成公制牙应为:M4.76×0.79三、一般英制牙换算成公制牙的公式:
分子÷分母×25.4=牙外径(同上)
例1:(3/8-24)
3÷8×25.4=9.525(牙外径)
25.4÷24=1.058(公制牙距)
则3/8-24换算成公制牙应为:M9.525×1.058四、美制牙换算公制牙公式:
例:6-32
6-32 (0.06+0.013)/代码×6=0.138
0.138×25.4=3.505(牙外径)
25.4÷32=0.635(牙距)
那么6-32换算成公制牙应为:M3.505×0.635 1、孔内径计算公式:
牙外径-1/2×牙距则应为:
M3.505-1/2×0.635=3.19
那么6-32他内孔径应为3.19
2、挤压丝攻内孔算法:
下孔径简易计算公式1:
牙外径-(牙距×0.4250.475)/代码=下孔径例1:M6×1.0
M6-(1.0×0.425)=5.575(最大下孔径)
M6-(1.0×0.475)=5.525(最小)
例2:切削丝攻下孔内径简易计算公式:
M6-(1.0×0.85)=5.15(最大)
M6-(1.0×0.95)=5.05(最小)
M6-(牙距×0.860.96)/代码=下孔径
例3:M6×1.0=6-1.0=5.0+0.05=5.05
五、压牙外径计算简易公式:
1.直径-0.01×0.645×牙距(需通规通止规止)
例1:M3×0.5=3-0.01×0.645×0.5=2.58(外径)
例2:M6×1.0=6-0.1×0.645×1.0=5.25(外径)
六、公制牙滚造径计算公式:(饱牙计算)
例1:M3×0.5=3-0.6495×0.5=2.68(车削前外径)
例2:M6×1.0=6-0.6495×1.0=5.35(车削前外径)
七、压花外径深度(外径)
外径÷25.4×花齿距=压花前外径
例:4.1÷25.4×0.8(花距)=0.13 压花深度应为0.13
八、多边形材料之对角换算公式:
1.四角形:对边径×1.414=对角径
2.五角形:对边径×1.2361=对角径
3.六角形:对边直径×1.1547=对角直径
公式2: 1.四角:对边径÷0.71=对角径
2.六角:对边径÷0.866=对角径
九、刀具厚度(切刀):材料外径÷10+0.7参考值
十、锥度的计算公式:
公式1:(大头直径-小头直径)÷(2×锥度的总长)=度数等于查三角函数值
公式2:简易
(大头直径-小头直径)÷28.7÷总长=度数。