▲-PFMEA表格
PFMEA第五版表格
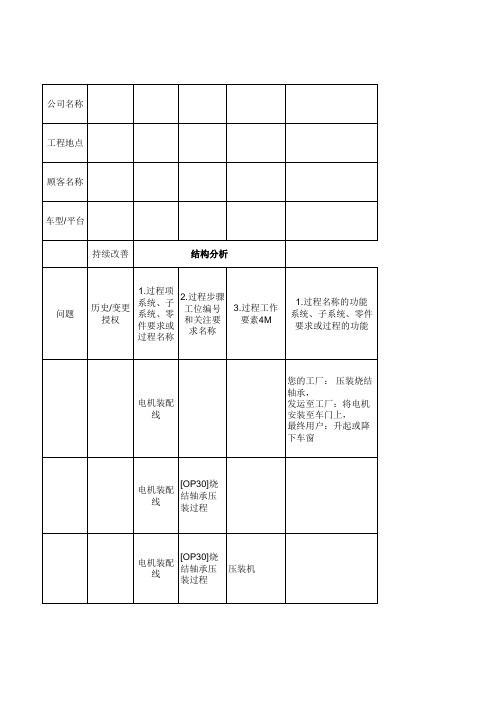
特殊特 性
筛选器 代码
预防措施
探措施
根据规范
MRKJ503
根据数据表调整力的大 小
5
8对电机性 能曲线进
2
M
行完全检
测
带位置控 制传感器 的选择性
压装
带压力监 测的选择 性压装
P
改进措施
责任人
目标完成 日期
状态: 尚未确认/ 决策/执行
已完成 不执行
采取基于 证据的措
施
完成日期
严 重 度
发 生 度
电机装配 线
[OP30]烧 结轴承压 装过程
电机装配 线
[OP30]烧 结轴承压 装过程
压装机
功能分析
项目 开始日期 修订日期 职能团队
失效分析
PFMEA
2.过程步骤的功能 3.过程工作要 1.对于上一较高级别要素和
和产品特性 素的功能和 I或最终用户的失效影响(
(量值为可选项) 过程特性
FE)
不能实现 烧结轴承 的轴向定 位
机器将烧结 轴承压入电 机壳,实现 轴向定位
设备在达 到最终位 置前停止
PFMEA
系统/子系 统/组件/部
件
DFMEA编 号
设计职责
保密等级
风险分析
当前的对失效起因的预 防措施( PC)
频 度 (0 )
FC /FM 的当前探
测措施 (DC)
FC
/F
M 的 AP(行 探 动优先 测 级) 度 (
公司名称
工程地点
顾客名称
车型/平台 持续改善
结构分析
功能分析
问题
历史/变更 授权
1.过程项 系统、子 系统、零 件要求或 过程名称
制程PFMEA分析表格
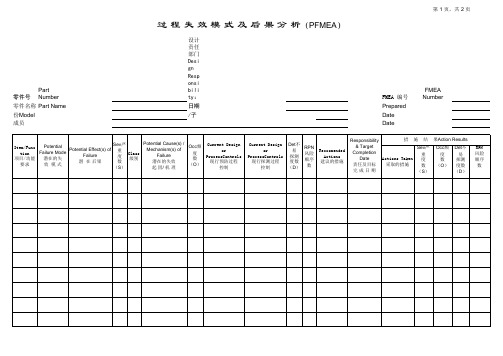
零件号 Part Number 设计责任部门Design Responsibility: 关键日期Key Date: 系统/子系统/部件System/Subsystem/Component FMEA 编号 FMEA Number 零件名称 Part Name 车型/年份Model Year(s)/Vehicle(s) 核心小组成员Core Team Member 编制Prepared by: 编制日期Date (Orig.): 修订日期Date (Rev.):
Det不 RPN 易 风险 探测 顺序 度数 数 (D)
Reccomended Actions 建议的措施
第 2 页,共 2 页
sults RPN 风险 顺序 数
Sev严 Potential Effect(s) of 重 Class Failure 度 级别 潜 在 后果 数 (S)
Potential Cause(s) / Mechanism(s) of Failure 潜在的失效 起 因/ 机 理
Occ频 Current Design or Current Design or 度 ProcessControls现 ProcessControls 数 行预防过程 现行探测过程 (O) 控制 控制
措 施 结 果Action Results Responsibility & Target Sev严 Occ频 Det不 Completion 重 度 易 Date Actions Taken 度 数 探测 采取的措施 责任及目标 数 (O) 度数 完成日期 (S) (D)
Potential Item/Funct Failure Mode ion 项目/功能 潜在的失 要求 效 模式
PFMEA评分表

PFMEA评分表PFMEA评分表》是一种常用的品质管理工具,用于进行潜在失效模式与效应分析(Process Failure Mode and Effects Analysis,简称PFMEA)。
它的目的是识别关键步骤或流程中的潜在失效模式,并评估其对产品或服务质量的影响程度。
PFMEA评分表可以帮助团队全面分析和评估可能发生的失效模式,并制定适当的预防和纠正措施,从而最大程度地降低产品或服务质量风险。
通过对各种失效模式和其效应的评估,可以提前发现潜在问题并采取相应的控制措施,以确保产品或服务质量的稳定和可靠。
在PFMEA评分表中,各个步骤或流程会被列出,并根据其对产品或服务的潜在失效的重要程度进行评分。
评分标准可以根据具体情况进行制定,但通常包括失效模式的严重性、发生频率和检测能力等方面的考量。
评分结果可以帮助团队确定哪些步骤或流程需要重点关注和改进,从而优化生产或服务流程,提高质量稳定性。
综上所述,《PFMEA评分表》是一种重要的品质管理工具,用于识别和评估潜在的失效模式,以确保产品或服务质量的稳定和可靠。
PFMEA评分表是一种用于进行过程故障模式与影响分析的工具。
它由以下几个组成部分构成,并且包含一些必填项。
1.项目信息在评分表的顶部,需要填写一些项目信息,以便对分析的过程进行标识和跟踪。
这些信息可能包括项目名称、项目编号、评分表编制人员等。
2.设计和工艺流程步骤在评分表中,需要列出与该过程相关的设计和工艺流程步骤。
这些步骤可以按照顺序进行排列,并且需要明确指出每个步骤的名称和内容。
3.故障模式与影响分析针对每个设计和工艺流程步骤,需要进行故障模式与影响分析。
这部分需要列出可能的故障模式,并对其进行评估。
评估可以基于指标如严重性、发生频率和可探测性等进行。
4.推理控制计划在评分表中,需要制定推理控制计划,以预防或控制故障模式对产品或过程的影响。
这部分需要明确列出控制措施、控制方式以及执行者。
PFMEA表格
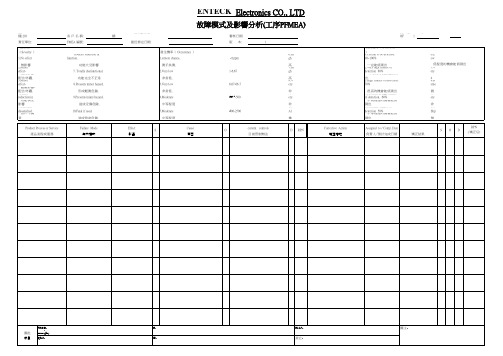
故障模式及影響分析(工序PFMEA)
機 種:203 客 戶 名 稱: FMEA 編號: 首次發行日期: 最近修定日期: 發生機率( Occurrence ) 6.Major reduction in function. 功能大受影響 7. Totally dysfunctional. 功能完全不正常 8.Presents minor hazard. 形成輕微危險. 9.Presents injury hazard. 造成受傷危險. 10.Fatal if used. 造成致命危險. Failure Mode 失效模式 Effect 影響 1.remote chance, 微乎其微. 2.Very low 非常低. 3.Very low 非常低. 4.Moderate 中等程度 5.Moderate 中等程度 Cause 原因 current controls 目前管制辦法 500-2500 66.7-500 6.67-66.7 1-6.67 <1ppm 6.High 高度 7.High 高度 8.Very High 非常高 9.Very High 非常高 10.Almost certain 幾乎是必然會發生 Corrective Action 矯正措施 125000 - 333333 50000- 125000 12500-50000 2500-12500 審核日期: 版 本: 1 偵測能力( Detection ) 1.Certain to be detected. 90~100% 一定能偵測出 2.Very high chance of detection 80% 非常高的機會能偵測出. 3.High chance of detection. 70% 很高的機會能偵測出 4.Moderately high chance of detection. 60% 中高程度的機會能偵測出. 5.Moderate chance of detection 50% 中等程度的機會能偵測出. Assigned to / Comp. Date 負責人/預計完成日期 矯正結果 6.Low chance of detection. 40% 低程度的機會能偵測出 7.Very low chance of detection. 30% 4 8.Remote chance of detection. 20% 微乎其微的機會能偵測出. 9.Very remote chance of detection. 10% 非常微乎其微機會能偵測出. 10.Slips by undetected. 無法偵測. RPN ( 矯正后) 頁 次: 1 OF 1 責任單位: 嚴重性(Severity ) 1.No effect 無影響 2.Minor effect-fit/cosmetics 輕微影響-配合/外觀. 3.Major effect-fit/cosmetics. 嚴重影響-配合/外觀. 4.Minor reduction in Function. 功能稍受影響 5.Customer dissatisfied. 客戶不滿意 Product Process or Service 產品流程或服務
过程分析表(PFMEA)

过程的输入(Input)
1. 2. 3. 4. 5. 6. 7. 8. 顾客要求, 产品图样和规范 过程特殊特性 法律法规 客户抱怨和退回数据资料 纠正或预防措施 过程流程图 类似产品和过程的 FMEA
过程的输出(Output)
过程的名称 Hale Waihona Puke Process)过程 FMEA
1. 过程潜在失效模式的清单 2. 潜在关键特性和重要特性 清单 3. 消除或减少产品失效模式 出现频次的过程措施清单 4. 提供全面的过程控制策略 基础
程序/方法(Procedure)
1. 2. 3. 4. 5. 过程管理工具 保持对项目的关注和跟踪 试验设计 回归分析 因果图
监督方法/测量指标 (Objectives)
1.
2.
内部和外部符合性 风险顺序数改进后的有效性
过程分析表
1. 2.
过程名称:PFMEA
子过程(Subprogram)
工序过程 FMEA
核心过程■
管理过程□
支持性过程□
责任者(Responsibility)
多功能小组:提供 FMEA 数据 资料并主持编写 FMEA 多功能小组:评审/批准 FMEA
资源需求(Resource)
1. 2. 厂房设备。 试验设备。
PFMEA表格(第四版)

措施结果action results R P N
必备条件 requirement
S
O
D
潜在失效模式及后果分析表(PFMEA) RE MODE AND EFFECTS ANALYSIS(PROCESS FMEA)
系统item: 子系统/部件model year(S)/program(s): 核心小组 core team:
级别 classification 项目 process step 功能 function 严重度Severity 潜在失效模式 potential failure mode 潜在失效的后 果potential effect(s) failure 现行过程current process 潜在失效的 起因/机理 频 potential cause(S) 现行过程预防控制 度 现行过程探测控制 controls of failure 数 controls detection prevention 0
FMEA编号 : 过程责任process responsibility 关键日期key date 页码 第 页,共 页 编制人 prepared by: PFMEA 日期(版本) date(Orig)
风险 建议 顺序 措施 探 测 数 recommended action 度 RPN D
责任和目 标完成日 措施实 期 responsibili 施描述 ty&target 及完成 completion 日期
PFMEA表格

外观
有毛刺或锈
加工困难或无法使用
5
没有针对每外包装
无
2
针对每个包装抽样,确保代表性
4
40
无
尺寸
尺寸不合格
产品性能影响
6
测量不够准确
培训合格的检测人员
2
按规定的量具认真检测
5
60
无
20入库贮存
防护到位
生锈
影响加工速度及质量
6
存放环境潮湿
车间保持干燥的环境
2
定期检查库存状况3Biblioteka 36无30阀座测漏
漏油
6
孔片与配件之间未放好
无
2
首检、巡检
4
48
无
130、线圈插片
插入方向正确
左右搞错
影响绕线
5
操作时看错
无
2
首检、巡检
4
40
无
140、线圈绕结
圈数正确
圈数不正确
电阻异常
4
设定错误
无
3
每日班前点检设备设定
4
48
无
150、线圈焊接
无脱焊、虚焊
虚焊、脱焊
不通电
◇
7
焊接电流、脉宽波动
无
2
每日班前点检焊接参数
100%检查
4
56
无
200、总成焊接
无脱焊、虚焊
虚焊、脱焊
顾客难以安装
◇
7
焊接电流、脉宽波动
无
2
每日班前点检焊接参数
3
42
无
无漏气
部分有漏气但未被检出
导致后工序部分产品报废
7
放入时位置不对
制程PFMEA分析表格
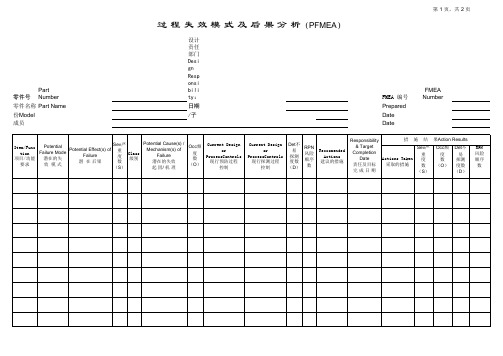
Occ频 度 数
(O)
Current Design or
ProcessControls 现行预防过程 控制
Current Design or
ProcessControls 现行探测过程 控制
Det不
易 探测 度数 (D)
RPN 风险 顺序 数
Reccomended Actions
建议的措施
Responsibility
措 施 结 果Action Results
& Target Completion
Date 责任及目标 完成日期
Actions Taken 采取的措施
Sev严 重 度 数
(S)
Occ频 度 数
(O)
Det不 易 探测 度数
(D)
RPN 风险 顺序
数
Part 零件号 Number
建议的措施
Responsibility
措 施 结 果Action Results
& Target Completion
Date 责任及目标 完成日期
Actions Taken 采取的措施
Sev严 重 度 数
(S)
Occ频 度 数
(O)
Det不 易 探测 度数
(D)
RPN 风险 顺序
数
FMEA Number
Item/Func tion
项目/功能 要求
Potential
Failure Mode 潜在的失 效 模式
Sev严
Potential Effect(s) of Failure
潜 在 后果
重 度 数
Class 级别
过程失效模式及后果分析表(PFMEA)(第五版表格)
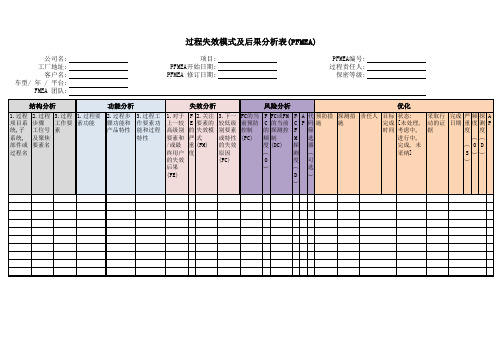
2.过程步 骤功能和 产品特性3.过程工 作要素功 能和过程 特性
1.对于 F 2.关注 3.下一 FC的当 F FC或FM F A 代 预防措 探测措 责任人 目标 状态:
上一较 E 要素的 较低级 前预防 C 的当前 C P 码 施
施
完成 [未处理,
高级别 的 失效模 别要素 控制 的 探测控 F 筛
时间 考虑中,
要素和 严 式
或特性 (PC) 频 制
M选
进行中,
/或最 重 (FM) 的失效
度 (DC) 探 器
完成, 未
()
终用户 度
原因
测
(
采纳]
的失效
(FC)
O
度可
后果
选
)
(FE)
D
采取行 完成 严 频 探 A
动的证 日期 重 度 测 P
据
度度
OD S
() ()
()
()
过程失效模式及后果分析表(PFMEA)
公司名: 工厂地址:
客户名: 车型/ 年 / 平台:
FMEA 团队:
项目: PFMEA开始日期: PFMEA 修订日期:
PFMEA编号: 过程责任人:
保密等级:
结构分析
功能分析
失效分析
风险分析
优化
1.过程 2.过程 3.过程 1.过程要 项目系 步骤 工作要 素功能 统,子 工位号 素 系统, 及聚焦 部件或 要素名 过程名
PFMEA表格

频 度 O
现行过程控制预防
现行过程控制探测
探 测 度 D
R P N
建议措施
责任及目标完成日期
措施结果Biblioteka 采取的措施S0D
R
P
N
铸板
(生板车间)
厚度超差
涂填不均匀
极板变形
极板化成不彻底
影响装配
进而导致电池性能受损,致使客户不满。
5
板栅模具四周边框不一致
2
人工喷膜不均匀
9
作业指导书的规定标准
10
450
1、指定明确有效的喷膜作业指导书
Andy
andrew3天内
1、指定明确有效的喷膜作业指导书
5
2
10
100
2、培养专业、专职的喷膜工
7天内
2、培养专业、专职的喷膜工
模具变形
3
压缩空气压力不稳定或达不到标准压力
4
观测压力表压力值
1
20
导杆磨损拉力不一致
3
定模紧固松弛
2
核心小组:________________________________________________________________________________________________________________________
过程
功能
要求
潜在失效模式
潜在失效后果
严重度S
级别
潜在失效
潜在失效模式及后果分析
(过程FMEA)
FMEA编号:__________
共______页,第______页
__________零部件_______________过程责任:__________________编制人:______________________________
PFMEA第五版表格模板 自己整理(带实例)--2020.2.3
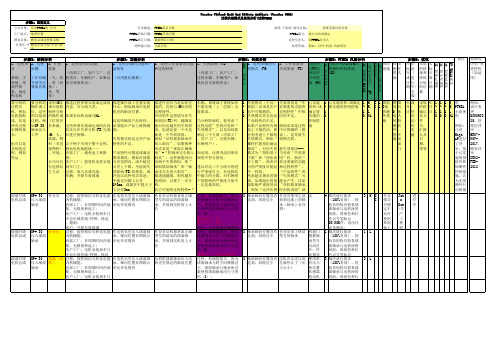
工厂地点: 地理位置
顾客名称: 顾客名或过程族名称 车型年/平 顾客车型年型/平台/款
台: 型
任务描述: PFMEA项目名称 PFMEA开始日期: PFMEA开始日期 PFMEA修订日期: 最新修订日期
跨职能小组: 小组名单
Process Failure Mode and Effects Analysis (Process FMEA) 过程失效模式及效果分析(过程FMEA)
# 批次放行要求
3 H C 作业 Joh 进
电机总成 压入球面
为机械能;
承,轴向位置在图纸公 型号的清洁的球面轴 球面轴承与转子间摩擦过 达到,间距过小 掉到过地上的轴
(100%有效),检
C 指导 n
行
轴承
内部工厂:在周期时间内装 差允许范围内
承,并放到压机的上止 大,球面轴承与轴承座过
承(轴承上有异
验员用检具检查球
书规 Doe 中
配,无报废和返工;
位
紧使得球面轴承内尺寸变
物)
面轴承与电机座的
定不 (生
客户工厂:电机安装到车门Fra bibliotek形(8);
间距,用绿色和红
允许 产
不会出现停线/停顿、拣选
内部工厂:无
色记号笔标记
使用 工
、遏制;
客户工厂:无;
OK/NOK件,再由作
掉到 程
用户:升降车窗玻璃
用户:车窗玻璃升降困难
为无需
0~3mm,或最多不能大于 析。
一定是最高的。
级影响严重度的话 “从料箱拿轴承
额外行
上公差3mm
其它可能的过程特性-“
PFMEA控制程序(含表格)
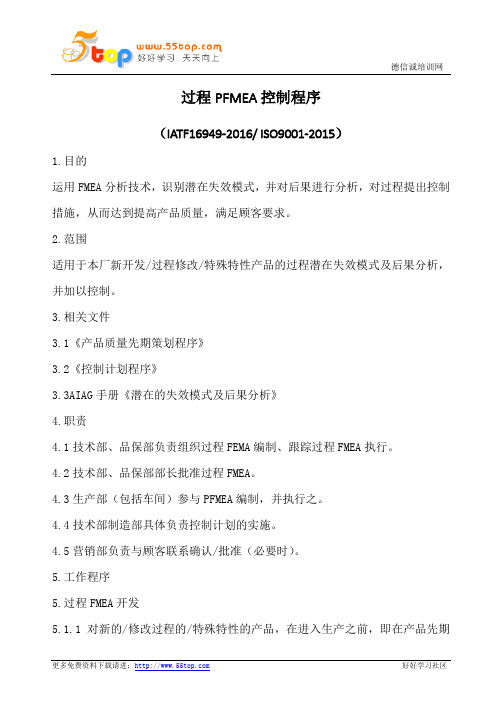
过程PFMEA控制程序(IATF16949-2016/ ISO9001-2015)1.目的运用FMEA分析技术,识别潜在失效模式,并对后果进行分析,对过程提出控制措施,从而达到提高产品质量,满足顾客要求。
2.范围适用于本厂新开发/过程修改/特殊特性产品的过程潜在失效模式及后果分析,并加以控制。
3.相关文件3.1《产品质量先期策划程序》3.2《控制计划程序》3.3AIAG手册《潜在的失效模式及后果分析》4.职责4.1技术部、品保部负责组织过程FEMA编制、跟踪过程FMEA执行。
4.2技术部、品保部部长批准过程FMEA。
4.3生产部(包括车间)参与PFMEA编制,并执行之。
4.4技术部制造部具体负责控制计划的实施。
4.5营销部负责与顾客联系确认/批准(必要时)。
5.工作程序5.过程FMEA开发5.1.1对新的/修改过程的/特殊特性的产品,在进入生产之前,即在产品先期策划过程中,必须进行过程FEMA。
5.1.2技术部组织生产部及相关人员组成PFMEA开发小组,负责PFMEA的开发。
5.1.3技术部提供产品的“过程流程图”,其包括有关产品/过程特性参数。
同时提供相似产品的作用指导书(作参考)。
5.2过程FMEA编制5.2.1PFEMA小组依据产品的“过程流程图”,产品/过程特性参数及作业指导书(参考件)。
针对某一产品的各过程可能会产生的潜在失效模式进行排查并对潜在失效的后果进行分析,填入“潜在失效模式及后果分析“(PFMEA)表中。
5.2.2由潜在失效分析后,分析如失效后果发生时,对该工序或顾客影响后果的严重程度加以评价---严重度(S)。
严重度评估分为“1-10级”,“严重度评估准则”(附录一)。
如果当S>8时,应予以特别注意,采取相应纠正措施,必须指派专人负责并规定完成期限。
5.2.3PAMEA小组紧急着对潜在失效原因/机理进行分析。
发生失效原因/机理可能一个或几个均应分析列出,填入PFMEA表中。
制程PFMEA分析表格

第 1 页,共 1 页
FMEA 编号 FMEA Number 编制Prepared by: 编制日期Date (Orig.): 修订日期Date (Rev.):
Item/Func tion
项目/功能 要求
Potential
Failure Mode 潜在的失 效 模式
Sev严
Potential Effect(s) of Failure
Sev严 重 度 数
(S)
Occ频 度 数
(O)
Det不 易Βιβλιοθήκη 探测 度数(D)RPN 风险 顺序
数
潜 在 后果
重 度 数
Class 级别
(S)
Potential Cause(s) / Mechanism(s) of
Failure 潜在的失效 起 因/ 机 理
Occ频 度 数
(O)
Current Design or
ProcessControls 现行预防过程 控制
Current Design or
零件号 Part Number 零件名称 Part Name 车型/年份Model Year(s)/Vehicle(s) 核心小组成员Core Team Member
过 程 失 效 模 式 及 后 果 分 析(PFMEA)
设计责任部门Design Responsibility: 关键日期Key Date: 系统/子系统/部件System/Subsystem/Component
ProcessControls 现行探测过程 控制
Det不 易 探测 度数
(D)
RPN 风险 顺序 数
Reccomended Actions
建议的措施
Responsibility
PFMEA表格汇总

D
7-10 5-6 2-4
1 7-10 5-6 2-4
1 7-10 5-6 2-4
1 7-10 5-6 2-4
1
措施优先级 AP
H H H H H H H H H H H M H M L L
备注
非常低 非常高
1 8-10
高
6-7
对产品或工厂的 7-8
影响高
中
4-5
对产品或工厂的 4-6
影响中等
低 非常低 非常高
生产线没有停工
缺陷产品会触发重大应对计划的启
100%的产品可能需要在工位上返
外观、声音、震动、粗糙度或触感
4
动;可能不会出现额外的瑕疵产品,
工后才能继续加工
令人感觉非常不舒服。
不需要分拣
缺陷产品会触发次要应对计划的启
部分产品可能需要在工位上返工后
外观、声音、震动、粗糙度或触感
3
动;可能不会出现额外的缺陷产品,
测量可重复性和再现性结果可
5
的半自动化方式),或使用可以探测失效模式或失效
以接受)。
起因的检验设备,例如坐标测量机。
以设备为基础的自动化探测方法,其可以在下游探测
到失效模式,进而避免进一步加工、或系统可以识别
4
已经过实践证明为有效和可靠 差异产品,并允许其在过程中自动前进,直至到达指
的系统(例如工厂在关于相同 定的不合格品卸载去。差异产品将在一个有效的系统
技术控制
预防控制
没有预防控制 预防控制在防止失效起因出现的方面起
到的作用很小。 预防控制在防止失效起因出现的方面可
以起到一定的作用。 预防控制在防止失效起因出现的方面可
以起到有效的作用。
- 1、下载文档前请自行甄别文档内容的完整性,平台不提供额外的编辑、内容补充、找答案等附加服务。
- 2、"仅部分预览"的文档,不可在线预览部分如存在完整性等问题,可反馈申请退款(可完整预览的文档不适用该条件!)。
- 3、如文档侵犯您的权益,请联系客服反馈,我们会尽快为您处理(人工客服工作时间:9:00-18:30)。
中等
现行控制方法找出失效模式的可能性中等
5
中上
现行控制方法找出失效模式的可能性中等偏上
4
高
现行控制方法找出失效模式的可能性高
3
很高
现行控制方法找出失效模式的可能性很高
2
几乎肯定
现行工艺控制方法几乎肯定能找出失效模式,已知相似工艺的可靠的探测控制方法
1
10
有警告的严重危害
失效发生时有警告。可能危害机器、装配操作者或顾客。潜在失效模式严重影响车辆安全运行和/或包含不符合政府法规项,严重程度很高。
9
很高
生产线严重破坏,可能100%的产品得报废,车辆/系统无法运行,丧失基本功能,顾客非常不满。
8
高
生产线破坏较严重,产品需筛选部分(低于100%)报废,车辆能运行,但性能下降,顾客不满意。
过程潜在的失效模式及后果分析(PFMEA)
项目名称:过程责任部门:
车型年/车辆车型:关键日期:
主要参加人:
PFMEA编号:
页码:第页码共页
编制:
PFMEA日期(编制):(修订)
过程
功能要求
潜在的
失效模式
潜在的
失效后果
严重程度数S
级别
潜在失效
原因/机理
频度数O
现行过程
控制预防
现行过程
控制探测
探测度数D
≥0.83
6
1/400
≥1.00
5
1/2000
≥1.17
4
低:很少几次与相似过程有关的失效。
1/15000
≥1.33
3
很低:很少几次与几乎完全相同的过程有关的失效。
1/150000
≥1.50
2
极低:失效不大可能发生。几乎完全相同的过程也未有过失效。
≤1/1500000
≥1.67
1
PFMEA探测度分级评价标准(LQ)
4
轻微
生产线破坏较轻,部分(少于100%)需要在生产线上其它工位返工。装配和涂装或尖响和卡嗒响等项目不符合要求,有一半(50%)顾客发现有缺陷。
3
很轻微
பைடு நூலகம்生产线破坏轻微,部分(少于100%)产品需要在生产线上原工位返工,装配和涂装或尖响和卡塔响等项目不符合要求,很少(25%)顾客发现有缺陷。
2
无
仅对装配或操作者有轻微不方便,对顾客没有影响
探测性
评价准则:在下一个或后续工艺前,或零部件离开制造或装配工位之前,利用过程控制方法找出缺陷存在的可能性
不易探测度数
几乎不可能
没有已知的控制方法能找出失效模式
10
很微小
现行控制方法找出失效模式的可能性很微小
9
微小
现行控制方法找出失效模式的可能性微小
8
很小
现行控制方法找出失效模式的可能性很小
7
小
现行控制方法找出失效模式的可能性小
7
中等
生产线破坏不严重,部分(低于100%)产品报废(不筛选),车辆/系统能运行,但舒适性或方便性项目失效,顾客感觉不舒适。
6
低
生产线破坏不严重,产品需要100%返工,车辆或系统能运行,但有些舒适性或方便面性项目性能下降,顾客有些不满意。
5
很低
生产线破坏不严重,产品经筛选,部分(少于100%)需要返工,装配和涂装或尖响和卡嗒响等项目不符合要求,多数(75%)顾客发现有缺陷。
风险顺序数RPN
建议措施
责任目标
完成日期
措施结果
采取的
措施
严重程度数S
频度数O
探测度数D
风险顺序数RPN
PFMEA严重度评价标准(LQ)
后果
判定准则:后果的严重度
严重度数
无警告的严重危害
失效发生时无警告。可能危害机器、装配操作者或顾客。潜在失效模式严重影响车辆安全运行和/或包含不符合政府法规项,严重程度很高。
1
PFMEA频度分级评价标准(LQ)
失效发生的可能性
可能的失效率
CP
频度数
很高:失效几乎是不可避免的。
≥1/2
<0.33
10
1/3
≥0.33
9
高:一般与以前经常发生失效的过程相似的工艺有关。
1/8
≥0.51
8
1/20
≥0.67
7
中等:一般与以前时有失效发生,但不占主要比例的过程相类似的工艺有关。
1/80