航空零件典型结构加工工艺-薄壁加工
ZL105HB963--2005大型航空铝薄壁筒形零件车削工艺
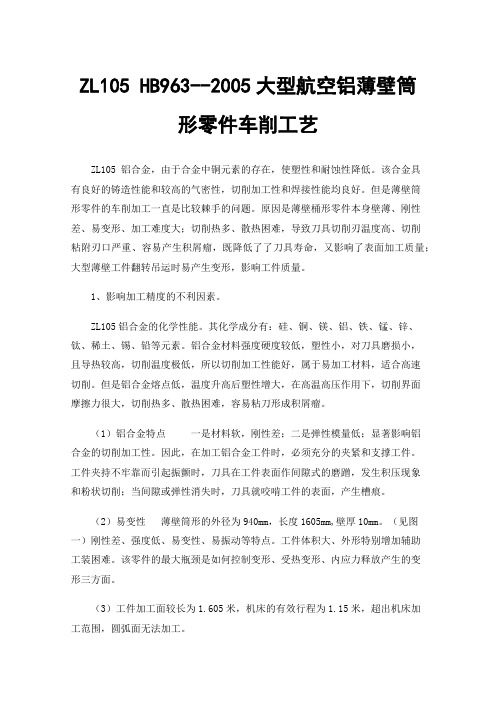
ZL105 HB963--2005大型航空铝薄壁筒形零件车削工艺ZL105 铝合金,由于合金中铜元素的存在,使塑性和耐蚀性降低。
该合金具有良好的铸造性能和较高的气密性,切削加工性和焊接性能均良好。
但是薄壁筒形零件的车削加工一直是比较棘手的问题。
原因是薄壁桶形零件本身壁薄、刚性差、易变形、加工难度大;切削热多、散热困难,导致刀具切削刃温度高、切削粘附刃口严重、容易产生积屑瘤,既降低了了刀具寿命,又影响了表面加工质量;大型薄壁工件翻转吊运时易产生变形,影响工件质量。
1、影响加工精度的不利因素。
ZL105铝合金的化学性能。
其化学成分有:硅、铜、镁、铝、铁、锰、锌、钛、稀土、锡、铅等元素。
铝合金材料强度硬度较低,塑性小,对刀具磨损小,且导热较高,切削温度极低,所以切削加工性能好,属于易加工材料,适合高速切削。
但是铝合金熔点低,温度升高后塑性增大,在高温高压作用下,切削界面摩擦力很大,切削热多、散热困难,容易粘刀形成积屑瘤。
(1)铝合金特点一是材料软,刚性差;二是弹性模量低;显著影响铝合金的切削加工性。
因此,在加工铝合金工件时,必须充分的夹紧和支撑工件。
工件夹持不牢靠而引起振颤时,刀具在工件表面作间隙式的磨蹭,发生积压现象和粉状切削;当间隙或弹性消失时,刀具就咬啃工件的表面,产生槽痕。
(2)易变性薄壁筒形的外径为940mm,长度1605mm,壁厚10mm。
(见图一)刚性差、强度低、易变性、易振动等特点。
工件体积大、外形特别增加辅助工装困难。
该零件的最大瓶颈是如何控制变形、受热变形、内应力释放产生的变形三方面。
(3)工件加工面较长为1.605米,机床的有效行程为1.15米,超出机床加工范围,圆弧面无法加工。
通过对零件结构及材料特性的分析,得知内外圆的精加工以及圆弧面加工是该零件的加工难点,如何有效控制加工变形是解决加工问题的重要措施。
为提高加工效率、保证加工质量,从工艺总体方案,工艺系统刚度、装夹方法、刀具材料及参数、切削参数及冷却方法等方面。
典型薄壁零件数控铣削加工工艺

典型薄壁零件数控铣削加工工艺数控铣削是一种精密加工方法,广泛应用于各种零件的加工过程中。
而对于薄壁零件的加工,由于其结构特点,需要特殊的加工工艺,以确保加工质量和效率。
下面介绍一种典型的薄壁零件数控铣削加工工艺。
1. 设计加工方案首先需要对零件进行结构设计和加工方案设计。
针对薄壁零件,需要注意材料选择、壁厚尺寸和加工顺序等问题。
在设计方案中,需要将零件分解为不同的加工步骤,并分析每个步骤中的工艺要求和工序参数。
2. 材料选择对于薄壁零件的加工,材料选择至关重要。
一般来说,薄壁零件使用的材料应该具有一定的塑性和韧性,以便于加工过程中的变形和切削。
常见的材料包括铝合金、钛合金和不锈钢等。
3. 刀具选择根据加工方案和零件设计要求,选择合适的刀具进行加工。
对于薄壁零件的加工,一般选择刚度较小、切削性能好的刀具。
还需要注意刀具的锋利度和几何参数等,确保切削效果和加工精度。
4. 加工顺序在进行数控铣削加工时,需要合理确定加工顺序。
对于薄壁零件而言,一般应先进行空间徐铣,即去除零件表面的余料和毛刺,然后再进行精确加工和表面处理。
加工顺序应根据零件结构和切削特点进行选择。
5. 加工参数在数控铣削加工过程中,需要合理设置加工参数。
对于薄壁零件而言,刀具进给速度和转速应适当降低,以减少切削力和热变形。
还需要注意切削深度和切削速度等参数,以确保加工质量和表面粗糙度。
6. 加工控制数控铣削加工需要精确的加工控制。
对于薄壁零件而言,需要特别注意切削力和卸刀等问题。
在加工过程中,应及时监控加工状态和切削力,以避免加工过程中的变形和划伤。
7. 加工精度检测加工完成后,需要进行加工精度的检测。
对于薄壁零件而言,主要检测加工尺寸、平行度和表面粗糙度等指标。
根据检测结果,可以进行调整和改善,以提高加工质量。
薄壁零件的数控铣削加工需要在材料选择、刀具选择、加工顺序、加工参数、加工控制和加工精度检测等方面进行精心设计和操作。
只有合理选择工艺和控制加工过程,才能确保薄壁零件的加工质量和效率。
航空钣金薄壁结构件液压成型工艺
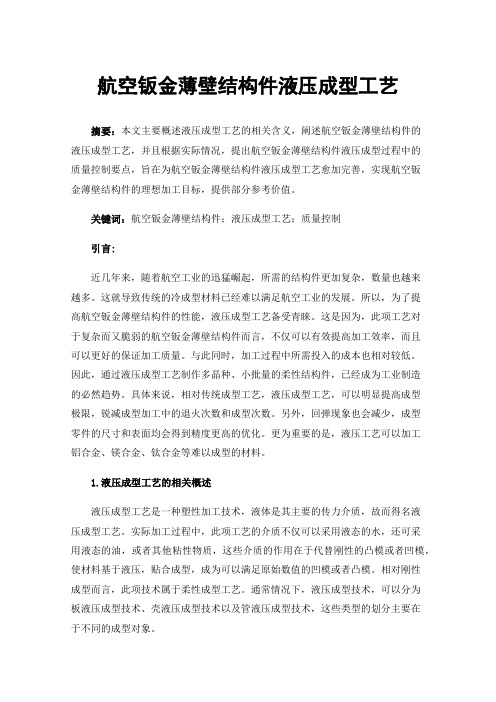
航空钣金薄壁结构件液压成型工艺摘要:本文主要概述液压成型工艺的相关含义,阐述航空钣金薄壁结构件的液压成型工艺,并且根据实际情况,提出航空钣金薄壁结构件液压成型过程中的质量控制要点,旨在为航空钣金薄壁结构件液压成型工艺愈加完善,实现航空钣金薄壁结构件的理想加工目标,提供部分参考价值。
关键词:航空钣金薄壁结构件;液压成型工艺;质量控制引言:近几年来,随着航空工业的迅猛崛起,所需的结构件更加复杂,数量也越来越多。
这就导致传统的冷成型材料已经难以满足航空工业的发展。
所以,为了提高航空钣金薄壁结构件的性能,液压成型工艺备受青睐。
这是因为,此项工艺对于复杂而又脆弱的航空钣金薄壁结构件而言,不仅可以有效提高加工效率,而且可以更好的保证加工质量。
与此同时,加工过程中所需投入的成本也相对较低。
因此,通过液压成型工艺制作多晶种、小批量的柔性结构件,已经成为工业制造的必然趋势。
具体来说,相对传统成型工艺,液压成型工艺,可以明显提高成型极限,锐减成型加工中的退火次数和成型次数。
另外,回弹现象也会减少,成型零件的尺寸和表面均会得到精度更高的优化。
更为重要的是,液压工艺可以加工铝合金、镁合金、钛合金等难以成型的材料。
1.液压成型工艺的相关概述液压成型工艺是一种塑性加工技术,液体是其主要的传力介质,故而得名液压成型工艺。
实际加工过程中,此项工艺的介质不仅可以采用液态的水,还可采用液态的油,或者其他粘性物质,这些介质的作用在于代替刚性的凸模或者凹模,使材料基于液压,贴合成型,成为可以满足原始数值的凹模或者凸模。
相对刚性成型而言,此项技术属于柔性成型工艺。
通常情况下,液压成型技术,可以分为板液压成型技术、壳液压成型技术以及管液压成型技术,这些类型的划分主要在于不同的成型对象。
液压成型工艺的原理是,将液体充满在凹模之中,然后板料在凸模的带动之下,在与凹模交界之时,产生反向液压,然后促使板材成型。
具体来说,基于反向液压,凸模会与板材紧紧贴合。
典型薄壁零件数控铣削加工工艺

典型薄壁零件数控铣削加工工艺摘要:薄壁零件广泛地应用在各工业部门,它具有重量轻,节约材料,结构紧凑等特点。
但薄壁零件很难加工,本文就针对薄壁类零件加工的困境,分析薄壁零件在加工中存在的易变形、零件尺寸精度、位置精度及表面粗糙度不易保证等技术问题,为更好的铣削薄壁零件提供了依据及借鉴。
关键词:薄壁零件;加工工艺;变形;装夹铝合金整体结构件具有薄壁化、轻量化、强度高和耐腐蚀的特点,可有效满足飞行器高速、高机动性对零件的要求。
这类零件目前大量采用数控铣削的加工方法生产,但由于薄壁结构形状复杂,相对刚度较低,故加工工艺性差。
一般加工此类零件时,为保证工艺精度,一般采用在最后精加工之后,进行无进给光切几次,这样无疑增加了工时,降低了生产效率,还容易因刀具后刀面与工件间的积屑瘤造成加工表面粗糙。
下面就以铣削加工时产生变形的原因和控制方法进行了研究。
1.产生变形的原因薄壁件由于本身结构相对复杂,壁薄,质量较小,同时精度要求高,刚度和强度也有一定要求,这导致其易受切削力和切削振动及装夹力、切削热的影响。
在选择毛坯时,尽量选用消除了内应力的原材料。
2.工件的装夹条件刚性较差的薄壁结构件,装夹是引起加工变形较重要的一个因素。
薄壁件的数控铣削中,装夹方案的优劣,将直接影响加工的精度、表面品质、劳动生产率和生产成本。
在制定薄壁零件装夹方案时,应首先根据零件的结构特点和加工技术要求,进行加工过程的受力和变形分析与计算,找出最易变形的薄弱部位;同时要特别注重定位与夹紧方式、夹紧力的选择,使工件所受综合作用力和力矩尽可能小,从而提高零件工艺刚度,减小零件的装夹变形及切削振动,最终达到提高工件几何精度的目的。
2.1加工残余应力零件在加工过程中,由于刀具对已加工面的挤压、刀具前刀面与切屑、后刀面与已加工表面之间的摩擦等综合作用,使零件表层内部产生新的加工残余应力。
残余应力是一个不稳定的应力状态,当零件受到外力作用时,外力与残余应力相互作用,使其某些局部呈现塑性变形,截面内的应力重新分配,当外力作用去除后,整个零件由于内部残余应力的作用发生变形,这种切削过程中残余应力的重新分布引起的工件变形,对加工质量产生重要影响。
典型薄壁零件数控铣削加工工艺

典型薄壁零件数控铣削加工工艺
典型薄壁零件数控铣削加工工艺是指在数控铣床上对薄壁零件进行加工的一种工艺。
薄壁零件是指壁厚相对较薄的零件,通常壁厚在0.5mm至4mm之间。
薄壁零件的加工对加工工艺要求较高,因为薄壁零件的刚性较差,容易产生形变和变形。
在加工过程中需要考虑如何处理薄壁零件的刚性问题,以保证加工质量。
首先需要注意的是薄壁零件的夹紧方式。
由于薄壁零件的刚性较差,夹紧时容易导致零件变形或变形,因此需要选用合适的夹具来夹紧薄壁零件。
一般情况下,可以使用弹簧夹具或软质夹具来夹紧薄壁零件,以减少对零件的变形。
其次需要注意的是刀具的选择。
由于薄壁零件的刚性较差,加工时很容易产生振动和共振现象,因此需要选择合适的刀具来加工。
一般情况下,可以选择刚度较高的刀具,以减少振动和共振的产生。
加工过程中需要注意控制进给速度和切削速度。
由于薄壁零件的刚性较差,加工时进给速度和切削速度过高会导致零件变形或变形,因此需要适当降低进给速度和切削速度,以保证加工质量。
还需要注意切削冷却液的选择和使用。
切削冷却液可以有效降低切削温度,减少切削力和切削热,从而减少对零件的影响。
在加工薄壁零件时,可以选择适当的切削冷却液,使其能够有效地冷却切削工具和工件。
需要注意加工工艺的优化。
在加工薄壁零件时,可以通过优化加工工艺参数,如刀具切削用量、刀具切削轨迹、加工顺序等,以提高加工效率和加工质量。
典型薄壁零件数控铣削加工工艺需要注意薄壁零件的夹紧方式、刀具的选择、进给速度和切削速度的控制、切削冷却液的选择和使用以及加工工艺的优化,以确保加工质量。
典型薄壁零件数控铣削加工工艺

典型薄壁零件数控铣削加工工艺【摘要】本文针对典型薄壁零件的数控铣削加工工艺进行了全面分析和总结。
首先介绍了薄壁零件的特点及加工要求,包括对形状精度、表面质量和结构稳定性等方面的要求。
然后详细阐述了数控铣削加工工艺流程,包括铣削顺序、切削参数和进给速度等内容。
接着就刀具选择与加工参数进行了探讨,指导读者在实际加工过程中如何选择合适的工具和设定参数。
随后分析了薄壁零件加工中常见的问题,并提出了解决方案。
对优化薄壁零件数控铣削加工工艺进行了探讨,包括加工效率和质量的提升策略。
结论部分总结了本文的研究成果,并展望了未来发展趋势。
通过本文的阐述,读者可以深入了解薄壁零件加工过程中的关键技术,为相关领域的工程师和研究人员提供了有益参考。
【关键词】薄壁零件、数控铣削、加工工艺、刀具选择、加工参数、常见问题、优化、总结、未来发展趋势、展望。
1. 引言1.1 典型薄壁零件数控铣削加工工艺薄壁零件数控铣削加工工艺是一种用于加工形状复杂、壁薄的零件的精密加工技术。
随着现代制造业的发展,对零件精度和质量的要求越来越高,薄壁零件的加工难度也相应增加。
在传统加工方法下,薄壁零件容易受到变形、扭曲等问题影响,而数控铣削技术的出现为解决这些难题提供了有效途径。
典型薄壁零件数控铣削加工工艺包括薄壁零件特点及加工要求、数控铣削加工工艺流程、刀具选择与加工参数、薄壁零件加工中的常见问题以及优化薄壁零件数控铣削加工工艺。
通过合理选择刀具和加工参数,结合先进的数控技术,可以有效提高薄壁零件的加工精度和质量,同时减少加工过程中产生的浪费和损耗。
本文将重点探讨典型薄壁零件数控铣削加工工艺的特点、加工流程、技术要点以及发展趋势,以期为相关领域的从业者提供参考和借鉴。
通过不断优化工艺,提高加工效率和质量,为推动薄壁零件加工技术的发展作出积极贡献。
2. 正文2.1 薄壁零件特点及加工要求薄壁零件是指在其最小截面的厚度很薄的零件,通常用于航空、汽车、电子等领域。
典型薄壁回转体零件加工分析及工装设计
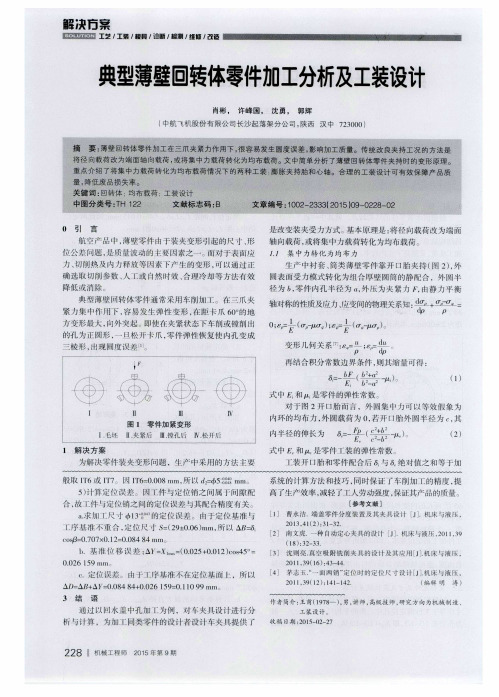
[ 3 ] 沈则亮 . 真空吸 附铣削 夹具 的设 计及 其应用 [ J ] . 机床 j 液压 ,
2 0 1 1 . 3 9 ( 1 6 ) : 4 3 — 4 4 .
c 一 定 位误 差 。 f } { 于工 序基准 不 在定 位 基 而上 ,所 以
AD= AB+ △Y= 0. 0 8 4 8 4 + 0 . 0 2 6】 5 9 = 0 . 1 1 0 9 9 mm
是改变装夹受力方式 。 基本原理是 : 将径向载荷改为端面
轴 向载 荷 , 或将 集 中力 载荷 转化 为均 布载 荷 。
j . i 集 电 力转化 为均 布 力
航空 产 品 中 , 薄壁 零件 由于装 夹 变形 引起 的 尺寸 、 形 位公 差 问题 , 是 质 量波 动的 主要 因素之 一 。 而对 于表 面成 力、 切削热 及内 力释 放等 素下 产生 的变形 , 可 以通过 正 确选 取 切 削参 数 、 人工 或 F { 然时 效 、 合 理冷 却 等 方法有 效
a
球 加] 尺寸 1 3 的定 位误 差 。 南于 定位 基准 与
1 序基 准 重 合 , 定位 尺 寸 S = ( 2 9  ̄ 0 . 0 6 ) m m, 所 以 AB - -  ̄ ,
c o 奶= 0 . 7 0 7 x 0 . 1 2 பைடு நூலகம்0 . 0 8 4 8 4 n l m。
P d D
+
P
:
0 ;
1(
) ;
i 1 o r
) 。
再结 合积 分 常数边 界 条件 , 则其 缩量 可得 :
6 F 一
凸 一
(
r , 一 “
) 。
薄壁深腔零件的机械加工工艺探讨
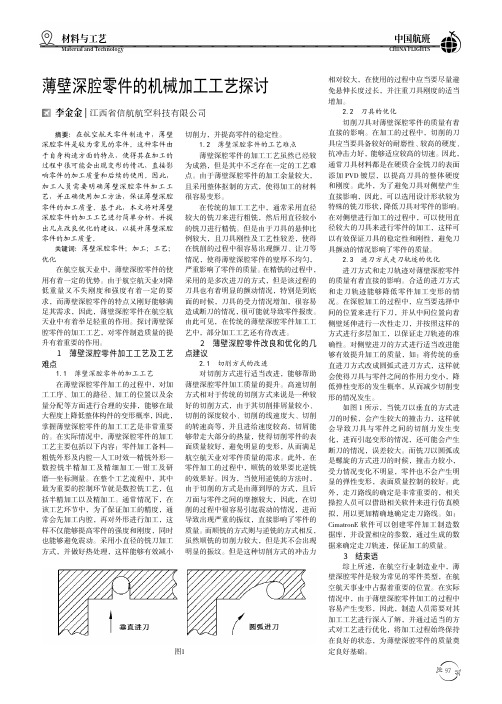
97中国航班材料与工艺Material and TechnologyCHINA FLIGHTS 薄壁深腔零件的机械加工工艺探讨 李金金|江西省信航航空科技有限公司摘要:在航空航天零件制造中,薄壁深腔零件是较为常见的零件。
这种零件由于自身构造方面的特点,使得其在加工的过程中很可能会出现变形的情况,直接影响零件的加工质量和后续的使用。
因此,加工人员需要明确薄壁深腔零件加工工艺,并正确使用加工方法,保证薄壁深腔零件的加工质量。
基于此,本文将对薄壁深腔零件的加工工艺进行简单分析,并提出几点改良优化的建议,以提升薄壁深腔零件的加工质量。
关键词:薄壁深腔零件;加工;工艺;优化在航空航天业中,薄壁深腔零件的使用有着一定的优势。
由于航空航天业对降低重量又不失刚度和强度有着一定的要求,而薄壁深腔零件的特点又刚好能够满足其需求,因此,薄壁深腔零件在航空航天业中有着举足轻重的作用。
探讨薄壁深腔零件的加工工艺,对零件制造质量的提升有着重要的作用。
1 薄壁深腔零件加工工艺及工艺难点1.1 薄壁深腔零件的加工工艺在薄壁深腔零件加工的过程中,对加工工序、加工的路径、加工的位置以及余量分配等方面进行合理的安排,能够在最大程度上降低整体构件的变形概率,因此,掌握薄壁深腔零件的加工工艺是非常重要的。
在实际情况中,薄壁深腔零件的加工工艺主要包括以下内容:零件加工备料—粗铣外形及内腔—人工时效—精铣外形—数控铣半精加工及精细加工—钳工及研磨—坐标测量。
在整个工艺流程中,其中最为重要的控制环节就是数控铣工艺,包括半精加工以及精加工。
通常情况下,在该工艺环节中,为了保证加工的精度,通常会先加工内腔,再对外形进行加工,这样不仅能够提高零件的强度和刚度,同时也能够避免震动。
采用小直径的铣刀加工方式,并做好热处理,这样能够有效减小切削力,并提高零件的稳定性。
1.2 薄壁深腔零件的工艺难点薄壁深腔零件的加工工艺虽然已经较为成熟,但是其中不乏存在一定的工艺难点。
- 1、下载文档前请自行甄别文档内容的完整性,平台不提供额外的编辑、内容补充、找答案等附加服务。
- 2、"仅部分预览"的文档,不可在线预览部分如存在完整性等问题,可反馈申请退款(可完整预览的文档不适用该条件!)。
- 3、如文档侵犯您的权益,请联系客服反馈,我们会尽快为您处理(人工客服工作时间:9:00-18:30)。
所以钛合金切削要点为低线速度,薄切削层厚度
第25页
3 钛合金薄壁
钛合金薄壁
钛合金薄壁特征加工特点: 1)壁薄腔深(框梁类零件),切屑排除困难,影响冷却润滑效果 2)刚性差,极易产生切削振动,影响加工效率和表面质量 3)切削中让刀严重,影响加工精度,易产生接刀痕 4)易产生加工变形,其毛坯大都为锻造毛坯,加工中随残余应力的
5刃不等齿距: 减震,高进给
加长刃长:一刀切
偏心铲背:增强 刃口强度
加大芯厚:高刚 性不让刀
加大螺旋角:提 高表面粗糙度
第38页
谢 谢!
第39页
释放极易产生加工变形,影响零件精度
钛合金薄壁特征加工要点: a ) 细分工序减小变形,一般为粗→半精→精,甚至可以多次半精,必
要时每个半精后辅以修基准面 b ) 精光一刀消除接痕和让刀
第26页
3 钛合金薄壁
工艺方案
粗加工:粗加工留余量3mm单边
缘条、筋条加工 –框梁类零件
半精加工:如右图分层加工每个框格,给精加 工留余量约0.5~0.2mm;零件变形大时可以多留 余量多次半精,必要时每个半精后辅以修基准面
第5页
1 薄壁特征
例2— 平尾对接肋和缘条: 特点为独立立筋–这类立筋两头不靠,长度长,高度与壁厚比值大,
因此强度更低,极易发生振动和变形
立筋
第6页
1 薄壁特征
例3— 壁板:壁板外表面结构较为简单,一般为少量下陷、槽、孔、 台阶等;壁板内表面较为复杂,通常有槽、斜面、下陷、台阶、结构 孔等结构
3 钛合金薄壁
刀具
方肩铣刀-MEB190系列 用途:半精侧壁、腹板 特点: • 切削力小-大前角大后角,刃口锋利 • 真90°侧壁-曲线刃设计 • R0.4~R3底角-适应各种底角需求
第34页
3 钛合金薄壁
刀具
超薄壁立筋专用铣刀-需要订制 用途:超薄壁侧铣专用
倒锥:减小接触长度
有效刃长≥层深+1mm
缘条、筋条加工 –独立立筋
第13页
2 铝合金薄壁
两种精加工推荐的走刀方案:
缘条、筋条加工 –独立立筋
• 两侧水平交替走刀: – 两侧走刀高度成水平状,每次走刀均有不错的
刚性支撑,同时编程较简单
• 两侧阶梯交替走刀: – 两侧走刀高度呈阶梯状,能为每次走刀提供更
大的刚性支撑,编程略麻烦
第14页
2 铝合金薄壁
第11页
2 铝合金薄壁
特点:两头不靠,刚性低易振动 走刀、编程限制少
独立立筋
缘条、筋条加工 –独立立筋
第12页
2 铝合金薄壁
工艺要点:
• 粗精均采用高速铣
• 粗加工:给精加工留单边余量3~5mm
• 精加工:a. 先将筋高、端头加工到位
b. 分层铣削,层深约1.5~3mm; 两侧交替走刀; 厚度尺寸直接加工到位
c. 选择更小直径的铣刀,切削力会小一些
d. 选用特制的薄壁专用铣刀加工
第28页
3 钛合金薄壁 增加加强筋或工艺凸台
缘条、筋条加工 –框梁类零件
第29页
3 钛合金薄壁
特点 – 两头不靠,刚性更弱 – 没有框格,走刀限制少
缘条、筋条加工 –单独立筋
工艺方案:
• 粗加工:大进给或R铣刀粗加工,留余量3mm单边
第7页
2 铝合金薄壁
铝合金薄壁
材料特点:航空铝合金结构件通常7系列超硬铝合金,例如7075、 7050等牌号,硬度约HB160切削性良好,非常适合采用高速铣加工
航空铝合金薄壁件毛坯通常为预拉伸板,这类材料经过拉伸处理消除 了材料残余内应力,具有加工后变形量小的特点
铝合金薄壁件加工要点: a)高速铣分层切削 b ) 立筋精加工前厚度余量要留够 c ) 腹板精加工第二面时采用真空吸附夹具
光洁度,减少加工过程振动 • 良好的润滑和排屑-油槽与中心螺
旋内冷设计
注意:1)腹板悬空状态慎用,因为齿数多切削力比普通刀具大 2)最大切深通常不超过R角深度,建议0.5mm
第24页
3 钛合金薄壁
钛合金材料
钛合金材料切削特点: 1)导热系数低,切削热集中在刃口,影响刀具寿命 2)弹性模量小,切削回弹严重,导致刀具后刀面磨损加剧,并易引
• 半精加工:分层加工如下图,给精加工留余量约0.5~0.2mm;零件 变形量大时可以多次半精
第30页
3 钛合金薄壁
• 精加工:如下图分层铣削,类似半精加工走刀 方式但不留余量,最后光刀消除接刀纹路和让刀
缘条、筋条加工 –单独立筋
• 层深根据切削时有无振动情况来调整,高度与壁厚比值越大,层深越 小
贴实 - 真空吸附
悬空 – 工艺凸台
Байду номын сангаас
第16页
2 铝合金薄壁
腹板加工 –贴实状态
贴实状态:利用真空夹具吸附住腹板或专用夹具支撑腹板的方式装夹 零件,腹板与夹具贴合,支撑性好,可以用比较大的切削参数正常加 工
加工工艺: 粗加工:高速铣,腹板留余量约3mm 精加工:高速铣,分两次加工到位
要点:
1) 腹板第二面精加工尽量采用真空夹具夹持,吸附前工艺凸台先压紧
2) 如腹板面较大专用夹具支撑效果不佳时可以修低定位凸台高度 0.03~0.05mm,增加支撑效果
第17页
3 铝合金薄壁
真空吸附夹具
原理:真空吸盘将工件下 方密封区域内的空气排出 ,从而在零件上下表面形 成压强差,在大气压和静 磨擦力作用下将零件压紧 在夹具上
优点: 1)减少干涉,便于编程 2)夹持刚性和稳定性好 3)装夹方便
应用:在航空领域多用于铝合金铣削粗精加工,因为减振和减小零件 变形的优点特别适合于铝合金薄壁件的加工 通常采用小切深轴向分层或者小切宽径向分层方式切削
第9页
2 铝合金薄壁
缘条、筋条两端通常相 互联接
缘条、筋条加工 –框梁类零件
多为封闭的框格 -加工时通常一个框格 一个框格的加工到位
第10页
2 铝合金薄壁
• 腹板上有孔时:第一面粗加工保留孔处 腹板不加工用作第二面加工时的支撑; 第二面精加工完腹板后再铣开窗口
留作支撑
压紧孔
• 辅助支撑:用填充材料填充底面框格后 加工
• 细分层加工:减小切深减小切削力
第20页
2 铝合金薄壁
刀具
铝合金高速方肩铣-MEH系列
• 用途:粗铣、大腹板贴实状态精铣 • 高线速度-可达2000m/min • 编程方便-大的下刀角度 • 配置齐全-刀尖R0.2~R5.0
刀具
常规缩径立铣刀— SA300-RN3系列 – 用途:筋条及腹板的通用高速粗、半精、精铣 – 与薄壁更短的接触长度,减小振动风险 – 粗精加工一体,减少刀具库存 – 周刃减震刃带设计,切削更稳定
缩径
第23页
2 铝合金薄壁
刀具
铝合金腹板精铣刀-非标定制
• 用途:腹板高速高效精铣 • 高效走刀-6刃有效 • 高光洁度-不等长度修光刃,提高
筋条
腹板
缘条
第3页
1 薄壁特征
薄壁加工的难点
振动:薄壁刚性差易引发零件振动,影响工件的 尺寸精度、表面粗糙度和刀具寿命
受力变形:薄壁受力后变形导致尺寸精度难以保 证
受热变形:薄壁更易受切削热传递后发生受热变 形,导致薄壁形位误差;且会导致整个零件应力 变化造成零件变形
第4页
1 薄壁特征
例1— 框、梁类薄壁结构件:框、梁类薄壁特征较类似,除了缘条、 筋条、腹板结构外,还有凸台、下陷、异形孔等结构
R角:根据零 件底角要求
刃口及角度:钛合金专用
不等齿距:减小振动
第35页
3 钛合金薄壁
刀具
钛合金专用缩径铣刀-ST210系列 用途:半精铣侧壁、腹板;精铣侧壁、腹板
阶梯芯厚:容屑 槽大,刚性高
不等螺旋角:减振
锋利刃口:减小 切削力
缩径:防干涉,减 小接触长度
第36页
3 钛合金薄壁
刀具
钛合金专用合金铣刀- ST300系列
注意:1)需要装刀后总体做动平衡,达到G6.3 2)常换刀片螺钉,通常要求每次更换刀片时就更换 3)每次装刀检察跳动和刀片安装情况
第21页
2 铝合金薄壁
刀具
超薄壁立筋专用铣刀-需要订制
倒锥:减小接触长度
有效刃长≥层深+1mm
R角:根据底 角R确定
特制刃口和角度:铝合金专用
第22页
2 铝合金薄壁
第8页
2 铝合金薄壁
高速铣
高速铣:采用高线速度(铝合金通常vc>1000m/min)、高进给、低 切削用量的方式铣削零件
优点:– 90%的切削热被切屑带走,更小的热变形 – 降低切削力30%,薄壁不易振动、受力变形 – 更高的金属去除率 – 更好的表面质量
需求:高转速高功率的机床;刀具需动平衡G6.3以上
用途:钛合金侧壁及腹板粗、半精、精铣;摆线铣
• 不等齿距设计,优异的抗震性能 • 独特排屑槽设计,大容屑空间,排屑顺畅,
粗精一体 • 锥度中心内冷孔设计,优异冷却效果及排屑
性能,可以使用更高的线速度 • 刀具刃数5刃-更快的走刀,更高的效率
第37页
3 钛合金薄壁
刀具
侧壁精铣刀具:ST210-RL5系列 用途:钛合金侧壁精铣,摆线铣,特别适用于最后精光侧面
腹板加工
腹板上特征繁多:薄壁、下陷,凸台、各种孔、沟槽等
孔 下陷
薄壁
第15页
2 铝合金薄壁
腹板加工
腹板通常有悬空和贴实两种状态 – 框、梁类零件精铣第一面时腹板通常为悬空状态 – 框、梁类零件精铣第二面时腹板通常为贴实状态(真空吸附或专用
夹具) – 壁板两面加工为贴实状态(真空吸附) – 部分异形件采用工艺凸台装夹,腹板两面加工都是悬空状态