轻卡转向节外半轴锤上模锻造工艺设计及模具设计说明书
锻造工艺与模具设计-锤上模锻

锻造工艺与模具设计-锤上模锻引言锤上模锻是一种传统的金属锻造工艺,它使用锤子和模具将金属加热至一定温度后进行锤击,使其塑性发生变化,并通过模具的形状来塑造金属的最终形态。
本文将介绍锤上模锻的工艺流程以及模具设计的要点和注意事项。
锤上模锻的工艺流程锤上模锻的工艺流程通常包括以下几个步骤:1.材料准备:选择适当的金属材料,并对其进行预处理,如去除表面氧化物、清除杂质等。
2.加热:将金属材料加热至适当的温度,以增加其塑性。
加热温度通常根据材料的种类和要求的锻造效果来确定。
3.锤击:在金属材料达到适当温度后,使用锤子对其进行锤击。
锤击力度和频率需根据材料的塑性和形状来调整,以达到锻造工件的要求。
4.模具设计:根据锻造工件的形状和尺寸要求,设计制作适用的模具。
模具应具有足够的强度和刚度,以承受锤击的力量,并能形成金属的预期形状。
5.成品处理:锻造完成后,对锻造工件进行必要的处理,如退火、淬火、表面处理等,以提高其性能和外观质量。
模具设计的要点和注意事项1. 模具材料的选择模具材料应具有足够的硬度和强度,以抵抗锤击力量的作用。
常用的模具材料有合金工具钢、高速钢等。
在选择模具材料时,还需要考虑其热膨胀系数和导热性能,以确保模具在高温条件下能保持形状稳定性。
2. 模具结构设计模具的结构设计应考虑到工件的形状和尺寸要求,以及锤击的力量和频率。
模具应具有足够的强度和刚度,以承受锤击的力量,并能准确地形成金属的预期形状。
同时,模具的结构应合理,方便装卸和调整,以提高生产效率。
3. 模具表面处理模具的表面处理对于形成工件的表面质量和精度非常重要。
常用的表面处理方法包括电火花加工、抛光、渗碳等。
表面处理可以改善模具的耐磨性和抗粘附性,以减少模具的磨损和延长使用寿命。
4. 模具的维护与保养模具在锤上模锻过程中会受到较大的冲击和热应力,因此需要定期进行维护和保养,以确保其性能和使用寿命。
维护和保养包括清洁、修复损坏、润滑等工作。
轻卡转向节外半轴锤上模锻造工艺设计及模具设计说明书

目录1 设计的前期准备 (1)1.1 零件分析 (1)1.1.1 零件的结构分析 (1)1.1.2零件材料的特性分析 (1)1.1.3锻件的加工要求 (1)1.2工艺方案确定 (1)2锤上模锻件设计 (2)2.1选择分模面 (2)2.2确定模锻件加工余量及公差 (2)2.2.1 锻件的形状复杂系数 (2)2.2.2 锻件的质量 (3)2.2.3 锻件的材质系数 (3)2.2.4 模锻件的精度等级 (3)2.2.5 确定锻件公差和余量 (3)2.2.6 模锻斜度 (3)2.2.7 锻件技术要求 (4)2.3计算锻件基本数据 (4)3 确定锻锤的吨位 (5)4 确定飞边槽及尺寸 (7)5 确定终锻型槽 (8)6 设计预锻型槽 (9)7 绘制计算毛坯图 (10)8 制坯工步的选择 (11)9 确定坯料尺寸 (12)10 制坯型槽设计 (13)10.1滚挤型槽设计 (13)10.2拔长型槽设计 (13)11 锤用锻模设计 (15)11.1钳口尺寸确定 (15)11.2模块尺寸 (15)12 锻前加热锻后冷却及热处理要求的确定 (16)12.1确定加热方式,及锻造温度范围 (16)12.2确定加热时间 (16)12.3确定冷却方式及规范 (16)12.4确定锻后热处理方式及要求 (16)参考文献 (17)1 设计的前期准备1.1 零件分析1.1.1零件的结构分析转向节是汽车底盘上的关键零件,根据车型可分为重型汽车转向节、中型汽车转向节、轻型汽车转向节、微型汽车转向节、客车转向节和轿车转向节六大类;按其形状特征可分为长杆类、中心孔类和套管类三种。
长杆类转向节主要由杆部、法兰和枝权构成。
中心孔类转向节主要由基座,法兰和枝权构成,基座中心带孔。
套管类转向节主要由长杆、套管和法兰构成。
转向节是汽车转向桥上的主要零件,形状比较复杂,其形状兼具有轴类、盘类和叉架类等零件的特点。
转向节既支撑车体重量,又传递转向力矩和承受前轮刹车制动力矩,因此对其机械性能和外形结构要求严格,是汽车上的重要安全零件之一1.1.2零件材料的特性分析该锻件材料为18CrMnTi,是合金结构钢,是工业上应用最广泛的不锈钢,密度为7.85g/cm3。
车辆工程毕业设计157轻卡汽车转向节成形工艺设计说明书

第1章绪论1.1 前言近年来,汽车制造业得到了迅猛发展,汽车性能不断提高。
锻造工艺作为机械制造技术之一,对汽车工业具有重要作用,是生产受力部件成形的重要手段。
随着汽车工业的发展,汽车零部件中对高精度、形状复杂锻件的需求量越来越大,传统的加工工艺已经不能满足汽车零件产品需求。
在这种情况下,锻造新工艺的开发对于新型汽车零件的生产尤为重要,而先进工艺模具设计方法将对提高汽车零件设计水平、缩短零件研制周期和降低成本起着举足轻重的作用,从而大大提高汽车市场的竞争力。
塑性成形是材料加工的主要方法之一,它是利用金属塑性使金属在外力作用下成形的一种加工方法。
塑性成形在工业生产中得到广泛的应用,据统计,在汽车生产中70%以上的零部件都是利用金属塑性加工而成。
随着国内汽车制造业的迅速发展,汽车性能不断提高,汽车零部件中对高精度、形状复杂的锻件需求量越来越大,塑性加工行业迎来一个前所未有的发展机会,也面临着新的挑战。
汽车转向节是汽车前轴与前轮之间的关键零件,工作时不但要承载前轴给它的压力和地面给它的反作用力,还受到控制行使方向的扭力,其服役条件对零件的尺寸精度、表面质量和金属纤维流向都有很高的要求。
国内生产此类锻件仍然存在加工余量大、成形不易充满及模具设计困难等问题,探索该类锻件的合理锻造方法对我国汽车产业发展具有重要意义。
目前汽车转向节锻件主要依靠设计人员的经验不断试模、修模来保证质量,即使经验丰富的设计人员也很难保证一次成形出合格的终锻件,反复的试模、修模不仅浪费大量时间、人力和物力,而且增加生产成本,降低企业在市场中的竞争力。
近年来,随着计算机软硬件技术、金属塑性流动理论和计算机图形学等交叉学科的迅猛发展,有限元数值模拟技术得到了快速发展,以数值模拟等先进方法解决工业生产中的实际问题已成为金属成形技术的发展方向。
采用有限元数值模拟方法,可实现体积成形过程的模拟分析,获得零件的成形规律、以较小的代价,在较短的时间内找到最优的和可行的设计方案,为同类零件成形工艺的研究开发和应用提供技术依据和理论指导。
卡车转向节在锤上锻造工艺及模具设计

卡车转向节在锤上锻造工艺与模具设计单丽梅 颜斌哈尔滨哈飞工业锻造公司150060摘 要: 通过对9吨卡车转向节锻件的工艺分析,制定了合理的工艺方案,设计并改进了锻模,在5吨模锻锤上锻造出了合格的锻件。
关键词:转向节、工艺分析、模具设计一、引言9吨卡车转向节是大型卡车上的锻件,其形状不对称,截面变化剧烈,锻件质量大,形状复杂,成形难度很大,根据市场的需求及我单位的现有设备,我们在5吨模锻锤上对该锻件进行了工艺成形分析与锻模设计研究。
二、转向节锻件工艺分析汽车转向节系汽车前桥总成部分的重要保安件,其结构复杂,锻造工艺复杂系数为复杂级,金属塑性变形难度大,转向节在锻造生产中对工艺和模具设计均有较高的要求。
该锻件经初步估算成形打击力需5.9吨,锻件重量约21公斤,锻件材料40Cr。
如图1图一 转向节锻件图从图上可以看出锻件总长在365mm。
杆部细而长,小端直径Φ48,长211mm;叉口部分宽251mm,且法兰部分型腔深而窄深82.5mm,宽度仅有16mm;由此可见,该锻件关键在于如何保证料的合理分配及型腔的充满。
经计算该锻件原材料应选择Φ120×313,用圆棒料直接锻造成型是很困难的。
因而,需从锻模设计上充分考虑预锻型腔、终锻型腔的金属流动和原材料的预分配。
在工艺成型上要考虑制坯的形状尺寸,坯料在型腔的放置位置,锻造操作时打击力的轻重。
现采用二火成形的工艺方案,先进行自由锻制坯、而后进行预锻、终锻成形。
主要要研究的内容是制坯的形状及尺寸规格、预锻模型腔的设计参数、工艺试验及如何保证材料向锻件头部及深处流动。
工艺过程为:下料→加热→自由锻锻制坯→预锻→ 终锻→热切边→调质处理→ 吹砂。
三、 制坯工艺尺寸的确定从图1的锻件图上及以上的分析,考虑到杆部细而长,需将杆部制出,法兰处深而窄用料较多,叉口部位的距离较宽,料的分配比较困难,很难保证所有的角部充满,在试造初期我们将坯料制成如图2(a)所示,经过几次试造,用此坯料锻出的锻件法兰盘四角和叉口部位外侧很难充满。
转向节(工艺)毕业设计说明书

第1章零件分析1.1 转向节的功用转向节(俗称羊角)是汽车转向桥上的主要零件之一。
转向节与前梁组装后构成铰链装置,利用该铰链装置使车轮可以偏转一定角度,从而实现汽车的转向行驶。
转向节是车轮和方向盘之间的联系纽带,通过方向盘的旋转,带动连杆,即开始调整车轮的高度,而车轮通过两个轴承与转向节配合,使他们连接在一起。
转向节锥孔与转向节臂配合,并和转向横拉杆连接。
转向节法兰面通过四个螺钉和制动盘连接在一起。
转向节的功用是承受汽车前部载荷,支承并带动前轮转向。
在汽车的行驶状态下受到多变的冲击载荷。
转向节零件实体建模如图:1.2 转向节的结构特点与技术要求转向节(见下图)形式比较复杂,其结构兼具有轴类、盘类、叉架类等各种零件的特点。
根据其功用与结构特点,主要技术要求如下:1.轴颈部分转向节轴颈部分精度要求高的部位有:与轴承配合的两个支承轴颈,分别为Φ25和Φ40以及端面。
两支承轴颈对轴线的同轴度不大于Φ0.01mm,端面对轴线的垂直度不大于0.03mm。
圆角R5处是应力集中部位,Φ74轴颈端面易磨损,因此要求有高的强度和硬度。
在此区域采用高频淬火,淬火深度3-6mm,硬度为HRC53-58。
2.法兰面部分法兰面上有均匀分布的4-Φ12mm的孔,法兰面背面有因锻造拨模角为斜面,为使孔端面与法兰面很好贴合,每个孔均锪有Φ15mm的沉孔。
3.叉架部分转向节的上下耳和法兰面构成叉架体,精度要求高的部分有:注销孔为断续长孔,尺寸要求为Φ30mm,最大实体同轴度不大于Φ0.02mm,与轴线的位置度不大于Φ0.3mm。
锥孔大径为Φ28mm,锥度1:8。
第2章转向节的材料与毛坯制造2.1 转向节的材料与毛坯制造转向节的材料选取为40Cr,它是含碳量为0.37~0.45%的全多结构钢,并经调质淬火处理,以提高强度及抗冲击能力,使其具有较高的综合机械性能。
由于汽车在行驶过程中要经常转弯,故转向节在工作过程中要频繁的承受正反两个方向的冲击载荷,转向节毛坯一般采用锻造,锻造后的毛坯要求金属纤维的方向沿着轴颈轴线方向并与外形轮廓想适应,并且具有较高的抗拉、抗弯和抗扭的强度,以提高零件的强度。
锻造工艺与模具设计-锤上模锻

带连皮的模锻件,不需绘出连皮的形状和尺寸。产品 图的主要轮廓线要用点划线在模锻件图上表示,便于表示 各部分的加工余量。
锻造工艺与模具设计-锤上模锻
6.3.6 锻件图和锻件技术条件
锻件图(冷)是在零件图基础上,加上余量、余块 或其它特殊留量后绘制的图,图中锻件外形用 粗实线表示,零件外形用双点划线表示。 锻件的公称尺寸与公差注在尺寸线的上面,而 零件的尺寸注在尺寸线的下面的括号内。
α大到一定值时,可自动脱模,但α太大将会增大 金属的消耗量和余量。
但是,为了便于出模,高度较小的锻件可采用较
大的斜度,这时,多消耗的金属量不大。如:
H<50mm,查到3°改为5°;H<30mm,查的3°
、5°一律改为7°。
锻造工艺与模具设计-锤上模锻
(2) 同一锻件上内模锻斜度要比外模锻斜度大。 (大小原则)原因在于锻件冷却时,外壁趋向离开模 壁,而内壁正相反。
锻造工艺与模具设计-锤上模锻
1、热锻件图设计
热锻件图是将冷锻件图的所有尺寸计入收缩 率而绘制的。钢锻件的收缩率取1.2%-1.5%; 钛合金锻件取0.5%-0.7%;铝合金锻件取 0.8%-1.0%;铜合金锻件取1.0%-1.3%;镁合 金锻件取0.8%左右。 加放收缩率时,对无坐标中心的圆角半径不 加放收缩率;对于细长的杆类锻件、薄的锻 件、冷却快或打击次数较多而终锻温度较低 的锻件,收缩率取小值;带大头的长杆类锻 件,可根据具体情况将较大的头部和较细杆 部取不同的收缩率。
状越复杂,见表6-2:
级别 代号 形状复杂系数值S 形状复杂程度
Ⅰ S1
0.63~1
简单
Ⅱ S2
0.32~0.63
一般
Ⅲ S3
0.16~0.32
转向节外半轴锻压说明书(DOC)

目录1 设计的前期准备 (1)1.1零件分析 (1)1.1.1 零件的结构分析 (1)1.1.2 零件材料的特性分析 (1)1.2工艺方案确定 (1)2 锤上模锻件设计 (2)2.1选择分模面 (2)2.2确定模锻件加工余量及公差 (2)2.2.1 锻件的形状复杂系数 (2)2.2.2 锻件的质量 (3)2.2.3 锻件的材质系数 (3)2.2.4 模锻件的精度等级 (3)2.2.5 确定锻件公差和余量 (3)2.2.6 模锻斜度 (3)2.2.7 锻件技术要求 (3)2.3计算锻件基本数据 (4)3 确定锻锤的吨位 (I)4 确定飞边槽及尺寸 (II)5 确定终锻型槽 ...................................................................................................................... I II6 绘制计算毛坯图 .................................................................................................................. I V7 制坯工步的选择 (V)8 确定坯料尺寸 ...................................................................................................................... V I9 制坯型槽设计 (VII)9.1滚挤型槽设计 (VII)9.2拔长型槽设计 (VIII)10 锤用锻模设计 .................................................................................................................... I X 10.1钳口尺寸的确定 ........................................................................................................ I X10.2模块尺寸的确定 ........................................................................................................ I X11 锻前加热锻后冷却及热处理要求的确定 (X)11.1确定加热方式,及锻造温度范围 (X)11.2确定加热时间 (X)11.3确定冷却方式及规范 (X)11.4确定锻后热处理方式及要求 (X)参考文献 .................................................................................................................................. X I1 设计的前期准备1.1 零件分析1.1.1 零件的结构分析转向节是汽车转向桥上的主要零件,形状比较复杂,其形状兼具有轴类、盘类和叉架类等零件的特点。
汽车转向节锻造说明书
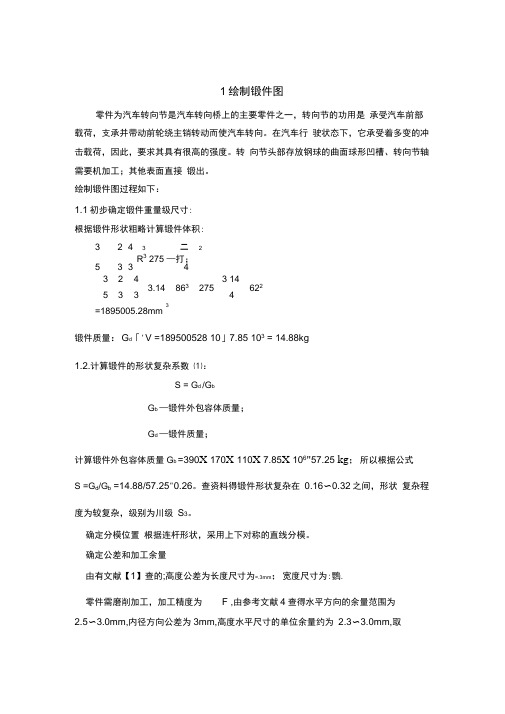
1绘制锻件图零件为汽车转向节是汽车转向桥上的主要零件之一,转向节的功用是承受汽车前部载荷,支承并带动前轮绕主销转动而使汽车转向。
在汽车行驶状态下,它承受着多变的冲击载荷,因此,要求其具有很高的强度。
转向节头部存放钢球的曲面球形凹槽、转向节轴需要机加工;其他表面直接锻出。
绘制锻件图过程如下:1.1初步确定锻件重量级尺寸:根据锻件形状粗略计算锻件体积:3 24 3二2R3 275 —打;5 3 3 43 24 3 143.14 863275 6225 3 3 43=1895005.28mm锻件质量:G d「'V =189500528 10」7.85 103= 14.88kg1.2.计算锻件的形状复杂系数⑴:S = G d /G bG b —锻件外包容体质量;G d —锻件质量;计算锻件外包容体质量G b =390X 170X 110X 7.85X 106"57.25 kg;所以根据公式S =G d/G b=14.88/57.25"0.26。
查资料得锻件形状复杂在0.16〜0.32之间,形状复杂程度为较复杂,级别为川级S3。
确定分模位置根据连杆形状,采用上下对称的直线分模。
确定公差和加工余量由有文献【1】查的;高度公差为长度尺寸为=.3mm;宽度尺寸为:鸚.零件需磨削加工,加工精度为 F ,由参考文献4查得水平方向的余量范围为2.5〜3.0mm,内径方向公差为3mm,高度水平尺寸的单位余量约为2.3〜3.0mm,取3mm。
1.3模锻斜度零件图上的技术条件已注明模锻斜度为5。
1.4圆角半径无零件圆角处取3mm,零件内圆角取R=(2〜3)r,其余圆角取3〜5mm。
1.5技术要求a图上未标注的模锻斜度为5 ;b图上未标注的圆角半径为R=3〜5mm;c允许的错移量为1.4mm;d允许的残留毛边量为1.4mm;e允许的表面缺陷深度为0.5mm;f锻件热处理:正火;g锻件表面清理:为便于检查淬火裂纹,采用喷砂或喷丸。
起重机连杆锤上模锻工艺及模具设计-课程设计说明书

目录引言 (2)1 锤锻工艺设计 (3)1.1热锻件图 (3)1.1.1分模面 (3)1.1.2余量及公差 (3)1.1.3拔模斜度 (4)1.1.4圆角半径 (4)1.1.5冲孔连皮 (4)1.1.6技术条件 (4)1.2锻件的主要参数 (4)1.3 设备吨位 (5)1.4计算毛坯图 (5)1.5制坯工步 (7)1.6坯料尺寸 (8)1.7模锻工艺流程 (8)2锻锤模具设计 (10)2.1 终锻模膛设计 (10)2.1.1 飞边槽设计 (10)2.1.2 钳口设计 (10)2.1.3 终锻模膛 (10)2.2 预锻模膛设计 (11)2.3 拔长模膛设计 (13)2.4滚压模膛设计 (14)2.5模膛排布 (15)2.5.1 排布顺序 (15)2.5.2 模膛壁厚 (15)2.5.3 模膛宽度方向排布 (15)2.5.4 模膛长度方向排布 (15)2.6模块设计 (15)2.7 锁扣设计 (16)2.8燕尾设计 (16)2.9模具校核 (16)2.10模具 (16)参考文献 (18)引言连杆是连杆机构中两端分别与主动和从动构件铰接以传递运动和力的杆件。
连杆是机器的主要运动件之一,它受载情况复杂,是较难设汁的重要零件之一。
连杆的工作条件要求连杆具有较高的强度和抗疲劳性能;又要求具有足够的钢性和韧性。
连杆是长轴类锻件中有代表性的锻件之一。
起重机连杆是起重机发动机的主要零件之一,工作时在高速下运转,工作条件比较繁重。
连杆的形状比较复杂,既有和曲轴相连的大头部,又有工字形断面的杆部,还有通过活塞销与活塞相连的小头部。
起重机连杆绝大多数都不需要机械加工,所以对连杆锻件的尺寸要求比较严格。
本次专业课程设计以起重机连杆为例,介绍它的锤锻工艺制订以及锻模设计的内容和步骤。
本次专业课程设计摒弃了传统的锤锻工艺设计手段,针对传统的手工计算、绘图和分析的方法将有很大的误差和设计时间周期长并且费时费力等缺点,应用了计算机辅助设计(CAD)技术,通过大型三维CAD软件UG进行零件的造型、工艺计算及工艺分析,提高了设计效率以及计算的准确性。
汽车转向节的锻模设计

汽车转向节的锻模设计摘要一辆汽车由多个部分组成,其中的汽车转向节是汽车上的关键零件,它既要承载车体重量,又需要承受前轮刹车的制动力矩并传递转向力矩,所以需要对其外形结构和机械性能有严格要求。
随着汽车行业的快速发展,汽车的需求量增大,对汽车转向节的需求量也同时增加。
由于其外形结构非常特殊,以传统的加工工艺方式已不能满足其强度和精度要求,因此锻造加工成为了制造汽车转向节的最优加工方式。
关键词:转向节预锻终锻1绪论1.1目的及意义汽车转向节是汽车转向控制系统的重要零部件,它承担着传递转向力矩的重要作用,作为汽车的主要安保部件之一,它既承担着车辆的制动力矩,同时还支撑着汽车的总体重量。
在汽车正常行驶途中,汽车转向节时常承担着重复的冲击载荷,所以它必须在满足高强度的机械性能和高标准的配置要求的同时,还要求有强大的抗疲劳能力[1]。
作为车辆的主要驱动元件,汽车转向节能保证车辆在复杂多变的情况下能够保持行驶稳定性,但由于其造型复杂,在生产过程中不易成型,而且对零部件的品质要求也相当高,因此过去的传统生产方式和制造方法已不能满足如今汽车现代化和大批量生产的要求。
不同的汽车型号它们的转向节也会稍有差异,因此现今市场上的转向节型号繁多,实现汽车转向节生产方式的优化是解决汽车批量生产的重要课题[2]。
以锻造加工为主的汽车转向节生产方式,满足了优化转向节锻造技术、降低材料的损耗率、节约工时以及减少成本的要求,同时对汽车转向节的合理锻造方法进行探索研究以及对锻造新工艺的开发具有重要意义,因此对锻模进行高端的技术设计和研究是非常关键的。
现今机器工业中生产毛坯的主要途径之一便是锻造,其优势就是它可以改变各种金属材质原有的组合,使其力学性能与物理性能获得了较大的改善,同时锻造还可以增加各种金属资源使用率以节省各种金属资源,并且锻造还可以直接获得金属零部件的外形,对于部分零部件来说锻造完成后甚至能进行使用。
锻造工艺能挤压锻件中的气孔并其疏松组织,粉碎粗大的颗粒使之变成细小颗粒,并形成沿着零件轮廓合理分布的纤维组织。
转向节臂锻件复合锻造工艺及模具设计

作特性。由于摩擦压力机行程速度较模锻锤慢,模具
3.2弯曲的回弹
受力条件较好,其承击面~般为锤上模锻的1/3即
对复杂弯轴类锻件而言,弯曲成形至关重要,弯 可。在本项目的设计中,对于预锻模、终锻模、校正模
曲回弹在冷冲弯曲工艺中是个突出的技术问题,不 均采用了镶块式模具结构(图2)。可较大幅度地降
同材质、板厚、相对弯曲半径R/r、弯曲件的形状、模 具尺寸及间隙等都将影响弯曲回弹值的大小。在热
积F=Fd+2KFI时,飞边槽充满系数K取0.4~0.6即 可,根据锻件形状尺寸,难于充填的部分取大值,易 于充填的部分取小值;⑧辊锻制坯各道次间的延伸
直方向的弯曲成形是成功的。 4模具合理结构与设计
系数的计算与选取,要避免辊锻过程道次之间或辊
摩擦压力机具有模锻锤和热模锻压力机双重工
锻后的毛坯出现折叠。
设计要点及模具的合理结构与设计。经实际生产验证:工艺方案先进合理、生产过程稳定可靠、经济效益显
著。这一工艺设计方法对其他复杂弯轴类锻件有参考意义。
关键词:机械制造;复合锻造;转向节臂;模具;汽车
中图分类号:TG316.1十4
文献标识码:B
1前言 左转向节臂是典型的复杂弯轴类锻件(图1),
复杂弯轴类锻件的最佳成形法,一直是锻造业致力 研究的问题。近年来,我国轻轿车生产迅速发展,生 产批量越来越大,整机制造水平越来越高,对复杂弯 轴类锻件而言,不仅形状复杂,而且锻件尺寸精度、 表面质量等方面的要求也越加严格,故探索轻轿车 复杂弯轴类锻件的合理锻造方法,显得尤为重要。根 据轻轿车生产实际需求,在试验研究的基础上,我们 采用了辊锻制坯~摩擦压力机模锻复合工艺替代传 统的锤上模锻,生产了轻型车左转向节臂,轿车左、 右下控制臂等5种复杂弯轴类锻件,其锻件技术水
第十一章 锤上模锻工艺及模具设计

2、圆角半径的取法: 较大的圆角半径有利于金属充满型腔、提高锻件质量和模具寿命。
外圆角半径r =余量+c。 内圆角半径R应比外圆角半径r大,一般可取:
R=(2~3)r
五、冲孔连皮
定义: 具有通孔的零件,在模锻时不能直接锻出通孔,仅能冲出一个具有一定
厚度的盲孔即孔内还留有一定厚度的金属层,称为冲孔连皮。
型式Ⅱ:切边时须将锻件翻转或者整个型腔都设在下模的情况时采用。
型式Ⅲ:用于锻件尺寸大而形状较复杂,在算料时不太准确,采用这种 飞边型式,飞边仓部能容纳更多的金属。
型式Ⅳ:为了更大的增加金属外流的阻力,迫使金属更好地充满深而复 杂的型腔,多用于型腔的局部地方。
型式Ⅴ :主要用于提高模具使用寿命,并便于将锻件放在切边凹模 的细颈上的情况。
维方向。
锻件分模位置一般都选择在具有最大轮廓线的地方。此外,还应考 虑下列要求:
(1)保证锻件能从型腔中取出,锻件的侧表面上不得有内凹的形状;
(2)分模的位置要尽量使型腔的深度最小和宽度最大,使金属容易 充满型腔。
(3)容易发现锻件的错移,分模面应尽量使上、下两部分对称,避 免分模面选择在端面上;
图11-17 a)预锻 b)终锻
图11-18 预锻型腔水平面上拐角处的圆角型式
(2)型槽的宽与高: 预锻型槽的高度应比终锻型槽的大2~5mm,宽度则比终锻型
腔小1~2mm;横断面面积比终锻型腔稍大些。 预锻型槽不设飞边槽。
(3)模锻斜度:与终锻型槽的相同
图11-19 预锻与终锻的尺寸关系
(4)特殊剖面 锻件个别部位需特殊设计时,以剖面的形式画出。下面介绍 几种特殊剖面 。
1)叉形劈开部分:劈开台的形式有两种(图11-20)。
轻卡转向节锻造工艺与模具设计
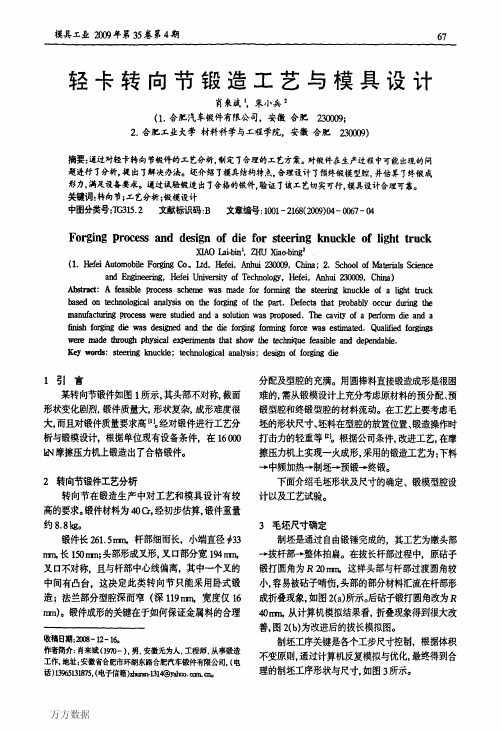
finish forging die was designed and the die forging forming force was estimated.Qualified forgings
were made through physical experiments that show the tedmique feasible and dependable.
轮廓及圆角进一步清晰,多余材料从飞边挤出,锻 件各部分尺寸达到锻件图要求nlo
(1)按热锻件图制造,收缩率取1.5%。 (2)在上、下模型槽底部设置钳口(与预锻型槽 钳口相同),以方便锻件从模具中取出。
4.3飞边槽设计 在进行飞边槽设计时.由于飞边槽桥部材料流
动较剧烈。磨损加快,在选择飞边槽桥部参数时,
4.1预锻型腔设计 预锻的主要目的是在终锻前进一步分配材料,
确保材料无缺陷流动。易于充填模膛。减少材料流 向飞边槽的损失,减小终锻模膛磨损,提高终锻模 寿命.取得所希望的材料流线和便于控制锻件的力
学性能,保证终锻时锻件成型饱满,无折叠、裂纹等 缺陷【3】o
预锻要解决的主要问题是满足法兰盘处充满所 需的料和叉口部位料的合理分配,要解决这一问题, 既要考虑预锻时材料能充分向法兰盘深处流动.又 要使叉El部位的料不被抽走,保证终锻时法兰盘处 的料足够充满型腔。
相似文献(8条)
1.期刊论文 单丽梅.颜斌.SHAN Li-mei.YAN Bin 卡车转向节锻造工艺与模具设计 -模具工业2008,34(1)
通过对卡车转向节锻件的工艺分析,制定了合理的工艺方案.对锻件生产过程中可能出现的缺陷进行了分析,提出了解决办法.介绍了模具结构特点,合 理设计了预锻模型腔,使坯料得到充分的预分配,保证了终锻的成型,从而减少终锻成型力,解决了设备吨位不足问题,锻造出的锻件质量良好.
轻卡汽车转向节成形工艺设计
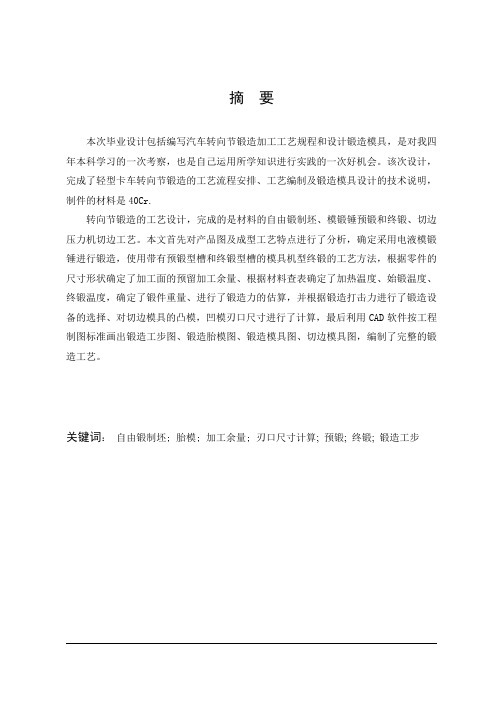
摘要本次毕业设计包括编写汽车转向节锻造加工工艺规程和设计锻造模具,是对我四年本科学习的一次考察,也是自己运用所学知识进行实践的一次好机会。
该次设计,完成了轻型卡车转向节锻造的工艺流程安排、工艺编制及锻造模具设计的技术说明,制件的材料是40Cr.转向节锻造的工艺设计,完成的是材料的自由锻制坯、模锻锤预锻和终锻、切边压力机切边工艺。
本文首先对产品图及成型工艺特点进行了分析,确定采用电液模锻锤进行锻造,使用带有预锻型槽和终锻型槽的模具机型终锻的工艺方法,根据零件的尺寸形状确定了加工面的预留加工余量、根据材料查表确定了加热温度、始锻温度、终锻温度,确定了锻件重量、进行了锻造力的估算,并根据锻造打击力进行了锻造设备的选择、对切边模具的凸模,凹模刃口尺寸进行了计算,最后利用CAD软件按工程制图标准画出锻造工步图、锻造胎模图、锻造模具图、切边模具图,编制了完整的锻造工艺。
关键词:自由锻制坯; 胎模; 加工余量; 刃口尺寸计算; 预锻; 终锻; 锻造工步ABSTRACTThe graduation design including compilation automotive steering knuckle forging process planning and design for forging die of undergraduate study four years, but also his trip knowledge learned a good oppotunity to carry on the practice. The Times design, completed the light trucks steering knuckle forging process arrangement, process Compilation and forging die design technical specification, the product's material is 40Cr.Steering knuckle forging process design, complete is material of free forging blocking, forging hammer forging and eventually gets forging, trimming press trimming process. This paper firstly product image and molding process characteristics are analyzed, sure to use electro-hydraulic forging hammer forging, use with pretensioners on forging type slots and end the mould forging type slot machine forging process method, end according to determine the size of parts machining surface shape to reserve machining allowance, according to materials look-up table determined the heating temperature, temperature, final forging beginning temperature of forging, determines the weight of the forging of forgings, according to the estimate, and force the forging stroke forging equipment choice, the punch molds for trimming blade, concave die size, finally, using the calculated according to the engineering drawing standards CAD tools software draw forging tool graph, forging die step womb graph, forging die figure, trimming mould figure, compiled the complete forging process.Keywords:Free Forging Blocking; Tire Mold; Machining Allowance; The Blade Size Calculation; Forging; Eventually Gets Forging; Forging Work Steps目录摘要 (Ⅰ)Abstract (Ⅱ)第1章绪论 (1)1.1前言 (1)1.2转向节国内外研究现状 (1)1.3选题的目的和意思 (4)1.4研究内容 (5)1.4.1研究的基本内容 (5)1.4.2拟解决的主要问题 (5)第2章转向节工作原理 (6)2.1转向节工作原理功能 (6)2.2本章小结 (6)第3章转向节的工艺设计 (9)3.1转向节锻件的工艺分析 (9)3.1.1锻件的零件图设计 (9)3.1.2锻件工艺流程的设计 (10)3.1.3锻件工艺难点和锻造工艺方案制定 (10)3.2锻件图的设计与锻件毛坯尺寸的计算 (11)3.2.1锻造工步的设计 (11)3.2.2冷锻件图的设计 (12)3.2.3热锻件图的设计 (18)3.2.4锻件毛坯尺寸的计算 (18)3.3本章小结 (20)第4章转向节的模具设计 (21)4.1自由锻制坯工具的设计 (21)4.1.1摔轴颈摔模的设计 (21)4.1.2劈料胎模的设计 (22)4.2锻造打击力的估算和设备的选用 (23)4.3锻造模具、切边模具及锻造工艺编制 (24)4.3.1模具压力中心的确定 (24)4.3.2锻造模具设计 (25)4.3.3切边模具的设计 (27)4.3.4锻造工艺的编制 (29)4.4锻造模具的制造 (29)4.4.1锻造模具的模块加工 (30)4.4.2模膛的制造 (30)4.5本章小结 (30)结论 (31)参考文献 (32)致谢 (33)附录 (34)第1章绪论1.1 前言近年来,汽车制造业得到了迅猛发展,汽车性能不断提高。
锤上模锻说明书3

锤上模锻说明书3热锻模设计——传动叉锻造工艺及模具设计摘要传动叉一般用于汽车传动轴的端部。
它的主要作用:一是传递扭矩,使汽车获得前进的动力,鉴于它是重要的受力零件,所以要求他要有很好的力学性能。
因此必须选用锻造的方法来生产制造。
通过对零件的分析,首先确定工艺方案,确定冷锻件的尺寸,通过计算锻件基本数据,确定锻锤吨位,绘制计算毛坯图,选择制坯工步,完成各制坯型腔,锻模结构以及切边模的设计。
通过本次毕业设计我们可以学习模具设计的一般方法,了解和掌握常用模具整体设计、零部件的设计过程和计算方法,培养正确的设计思想和分析问题、解决问题的能力,特别是总体设计和计算的能力;综合运用热锻模课程和其它有关选修课程的理论及生产实践的知识去分析和解决模具设计问题,使所学专业知识得到进一步巩固和深化;通过计算和绘图,学会运用标准、规范、手册、图册和查阅有关技术资料等,培养模具设计的基本技能;同时掌握锻造工艺,熟悉各种锻造设备,掌握计算机操作以及相关软件的应用,并具有机械设计及制造等综合知识。
关键词:力学性能,锻造,工艺,锻模结构,锻造设备HOT FORGING DIE DESIGN—TRANSMISSION FORKFORGING PROCESS ANG DIE DESIGNAbstractTransmission fork is generally used for the end of automobile transmission shaft. Its main functions: one is the transmission of torque, giving the car forward momentum, given that it is important to stress parts, so he must have good mechanical properties. Methods must therefore choose forging to manufacture. Through to the ponents analysis, first determine the process scheme, determine the cold forging size, by calculating the forging basic data, determine the hammer tonnage calculation, drawing a blank map, select performing step, plete the blank cavity, die structure and design of trimming die. Through the graduation design, we can learn the general method of mould design, design process and calculation method to understand and grasp the mon mould overall design, spare parts, training the correct design and analysis problem, problem-solving ability, especially the ability of overall design and calculation; curriculum integrated use of hot forging die and other elective courses related to the theory and practice of knowledge to analyze and solve problems in the mold design, professional knowledge has been further consolidated anddeepened; through calculating and drawing, learn to use the standard, specifications, manuals, books and access to relevant technical information, training of basic skills mold design; at the same time to master theforging process, familiar with all kinds of forging equipment, application master puter operation and related software, and has a prehensive knowledge of mechanical design and manufacturing etc.Keywords: mechanical property, forge technology, Die structure, forging equipment目录1. 冷锻件分析及工艺方案确定 ...................................................... ......................................................... .. (1)1.1 冷锻件图分析....................................................... ......................................................... .................. 1 1.2 工艺方案的确定....................................................... ......................................................... .............. 22. 锤上模锻件设......................................................... (3)2.1 选择分模面 ...................................................... ......................................................... ...................... 3 2.2 确定锻件复杂系数及锻造公差 ...................................................... (3)2.2.1初步确定锻件重量及尺寸 ...................................................... .............................................. 3 2.2.2复杂系数....................................................... ......................................................... ................ 3 2.2.3选择锻件材质系数M及公差 ...................................................... ........................................ 4 2.3 确定锻件模锻斜度 ...................................................... ......................................................... ........... 4 2.4 确定锻件圆角半......................................................... ........... 4 3. 锤上模锻工艺设计....................................................... ......................................................... .. (5)3.1 根据冷锻件图计算锻件基本数据 ...................................................... ............................................ 5 3.2 确定模锻锤的吨位 ...................................................... ......................................................... ........... 5 3.3 选择飞边槽 ...................................................... ......................................................... ...................... 5 3.4 绘制计算毛坯图....................................................... ......................................................... .. (6)3.4.1所选取截面位置 ...................................................... .............................................................. 6 3.4.2所取各截面形状 ...................................................... ......................................................... ..... 6 3.4.3各截面参数 ...................................................... ......................................................... ............. 7 3.4.4绘制计算毛坯的截面图 ...................................................... .. (8)3.4.5复杂形状的简化 ...................................................... ......................................................... ... 10 3.5 计算繁重系数,选择制坯工步 ...................................................... .............................................. 10 4. 热锻件图的设计 ...................................................... ......................................................... .......................11 5. 制坯型腔的设计 ...................................................... ......................................................... . (12)5.1 坯料长度计算....................................................... ......................................................... ................ 12 5.2 拔长型腔尺寸的确定 ...................................................... ......................................................... .. (12)5.2.1坎高 ...................................................... ......................................................... ...................... 13 5.2.2坎长的确定 ...................................................... ......................................................... .. (13)5.2.3型槽其他参数的确定 ...................................................... . (13)5.3 滚挤型腔尺寸的确定 ...................................................... ......................................................... .. (14)5.3.1滚挤模膛高度设计 ...................................................... ........................................................14 5.3.2滚挤模膛宽度设计 ...................................................... ........................................................15 5.4 滚挤模膛钳口、毛刺槽尺寸 ...................................................... .................................................. 15 6. 预锻型腔的设计 ...................................................... ......................................................... .. (16)6.1 预锻型腔各圆角设计 ...................................................... ......................................................... ..... 16 6.2 型腔的宽和高 ...................................................... ......................................................... ................. 16 6.3 模锻斜度 ...................................................... .................................................................................. 16 6.4 叉形劈开部分 ...................................................... ......................................................... ................. 16 6.5 钳口的设计 ...................................................... ......................................................... ..................... 16 7. 锻模的结构 ...................................................... ......................................................... . (18)7.1 终锻模膛与预锻模膛间的壁厚 ...................................................... .............................................. 18 7.2 模膛至外壁或锁扣的壁厚 ...................................................... (18)7.3 锻模承击面 ...................................................... ......................................................... ..................... 18 7.4 模块尺寸确定 ............................................................................................................... .. (18)7.4.1燕尾和键槽尺寸 ...................................................... ......................................................... ... 18 7.4.2模块的高度 ...................................................... ......................................................... ........... 19 7.5 模块允许质量 ...................................................... ......................................................... ................. 19 7.6 模块规格标准化 ...................................................... ......................................................... ............. 19 7.7 检验角和检验面 ...................................................... ......................................................... ............. 20 7.8 燕尾及键槽 ...................................................... ......................................................... ..................... 20 7.10模膛的尺寸公差和表面粗糙度 ......................................................力计算及压力机吨位选择 ...................................................... ........................................................248.1 切边压力机吨位选择 ...................................................... ......................................................... ..... 24 8.2 切边凹模设计 ...................................................... ......................................................... ................. 24 8.3 凸模与凹模间隙的选择 ...................................................... ..........................................................25 8.4 脱飞边器 ...................................................... ......................................................... ......................... 26 8.5 切边凸模的固定 ...................................................... ......................................................... ............. 26 8.6 切边凹模的固定 ................................................................... 27 9. 锻造工艺卡片 ...................................................... ......................................................... ........................... 28 总结 ...................................................... ......................................................... ................................................ 29 致谢 ...................................................... ......................................................... (31)参考文献 ...................................................... ......................................................... ....................................... 33 附录 ...................................................... ......................................................... .. (35)。
轻卡汽车转向节成形工艺设计-任务书

四、设计(论文)进度安排
资料收集,整理,完成开题报告第1~2周
论文的撰写,完成中期检查第3~9周
毕业论文提交第9~13周
毕业论文修改完善第13~16周
毕业论文答辩第17周
五、主要参考资料
1 汪泽波.汽车转向节成形工艺有限元模拟研究[D].合肥,合肥工业大学
2 陈小斌.汽车转向节锤上锻造工艺[J].锻压机械
3 张德春,孙吉宝.STEYR转向节模锻成形工艺研究[J].锻压技术
六、备注
指导教师签字:
年 月 日
教研室主任签字:
年 月 日
毕业设计(论文)任务书
学生姓名
系部
汽车工程系
专业、班级
指导教师姓名
职称
实验师
从事
专业
汽车服务
是否外聘
□是■否
题目名称
轻卡汽车转向节成形工艺设计
一、设计(论文)目的、意义
汽车转向节是汽车转向系统的关键零件,随着国内汽车产业飞速发展,该类锻件市场前景极为广阔,然而目前国内生产此类锻件仍然存在加工余量大、成形不易充满及模具设计困难等问题,所以探索该类锻件成形工艺具有十分重要的意义。传统的生产方式是自由锻成形,成形过程需要两次加热,能源浪费而且污染严重,质量也不易控制。为了响应国家节能减排的政策,提高生产效率和产品质量,将生产工艺进行改进,利用现有设备实现一火成形。为了减少研发成本,通过计算机模拟各工步的成形过程,确定成形工艺,得到一套切实可行的生产工艺及合理的模具结构。
二、设计(论文)内容、技术要求(研究方法)
主要内容:
1汽车转向节分类及结构分析
2汽车转向节成形工艺的研究现状与成形工艺分析
3汽车ห้องสมุดไป่ตู้向节模具的设计
锤上模锻轴课程设计

锤上模锻轴课程设计一、课程目标知识目标:1. 学生能理解并掌握锤上模锻轴的基本概念、工艺流程及在工程中的应用。
2. 学生能描述锤上模锻轴的主要参数及其对锻件质量的影响。
3. 学生能解释锤上模锻轴过程中金属流动、应力与应变的基本规律。
技能目标:1. 学生能运用所学知识,分析并解决实际锤上模锻轴过程中的问题。
2. 学生能通过观察、实验等方法,对锤上模锻轴过程进行初步的工艺设计和优化。
3. 学生能运用相关软件或工具,进行简单的锤上模锻轴模拟和计算。
情感态度价值观目标:1. 培养学生对机械制造及金属加工工艺的兴趣,激发其探索精神和创新能力。
2. 增强学生的团队合作意识,使其在讨论、实践过程中学会倾听、交流、协作。
3. 培养学生严谨、细致、负责的工作态度,提高其工程素养。
课程性质:本课程为机械制造及自动化专业的高年级课程,旨在帮助学生深入了解锤上模锻轴的工艺原理和应用,提高学生的实际操作能力和工程素养。
学生特点:学生已具备一定的机械基础知识和实践能力,具有较强的学习兴趣和探索精神。
教学要求:结合学生特点,注重理论与实践相结合,强化实际操作训练,提高学生的综合应用能力。
通过本课程的学习,使学生能够达到上述课程目标,为将来的工程实践打下坚实基础。
二、教学内容1. 锤上模锻轴基本概念:介绍锤上模锻轴的定义、分类及特点,使学生了解其在金属加工领域的重要地位。
2. 锤上模锻轴工艺流程:详细讲解锤上模锻轴的工艺步骤,包括原材料准备、加热、锻造、冷却和后续处理等环节。
3. 锤上模锻轴主要参数:分析并讲解锻件尺寸、形状、变形程度、锻造速度等参数对锻件质量的影响。
4. 金属流动、应力与应变规律:探讨锤上模锻轴过程中金属流动、应力与应变的基本规律,分析其对锻件质量的影响。
5. 锤上模锻轴设备与工具:介绍锤上模锻轴所使用的设备、工具及其特点,为学生实际操作提供指导。
6. 锤上模锻轴工艺设计与优化:讲解如何根据锻件要求进行工艺设计,以及如何运用优化方法提高锻件质量。
销轴锤上模锻模具设计
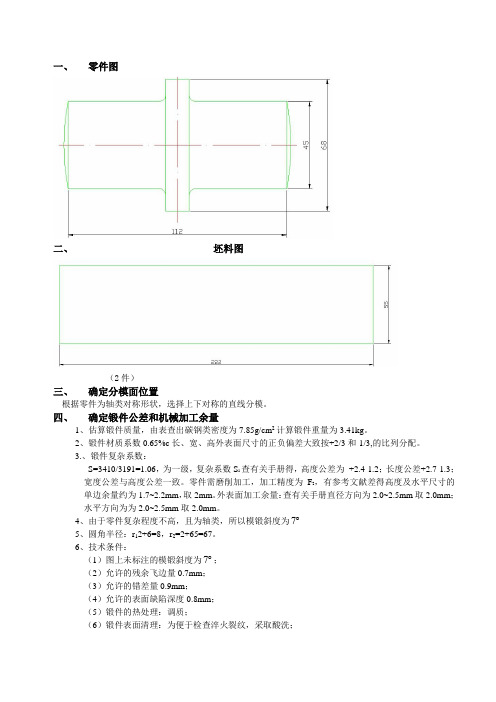
一、零件图二、坯料图(2件)三、确定分模面位置根据零件为轴类对称形状,选择上下对称的直线分模。
四、确定锻件公差和机械加工余量1、估算锻件质量,由表查出碳钢类密度为7.85g/cm2计算锻件重量为3.41kg。
2、锻件材质系数0.65%c长、宽、高外表面尺寸的正负偏差大致按+2/3和-1/3,的比列分配。
3.、锻件复杂系数:S=3410/3191=1.06,为一级,复杂系数S1查有关手册得,高度公差为+2.4-1.2;长度公差+2.7-1.3;宽度公差与高度公差一致。
零件需磨削加工,加工精度为F2,有参考文献差得高度及水平尺寸的单边余量约为1.7~2.2mm,取2mm。
外表面加工余量:查有关手册直径方向为2.0~2.5mm取2.0mm;水平方向为为2.0~2.5mm取2.0mm。
4、由于零件复杂程度不高,且为轴类,所以模锻斜度为︒75、圆角半径:r12+6=8,r2=2+65=67。
6、技术条件:(1)图上未标注的模锻斜度为︒7;(2)允许的残余飞边量0.7mm;(3)允许的错差量0.9mm;(4)允许的表面缺陷深度0.8mm;(5)锻件的热处理:调质;(6)锻件表面清理:为便于检查淬火裂纹,采取酸洗;(7)直线度和平面度公差0.8;;(8)中心距尺寸公差:4.07、根据余量和公差绘制锻件图:五、计算锻件的主要参数(1)锻件在平面上的投影面积为5810平方毫米;(2)锻件周边长度为386mm;(3)锻件体积为241680立方毫米;(4)短剑质量为3.41kg。
六、确定锻锤吨位总变形面积为锻件在平面图上的投影面积与毛边面积之和,按1t~2t锤毛边槽尺寸考虑,假定毛边乔部宽度为23mm,总面积F=5810+386*23=14688mm2按双作用模锻锤吨位确定的经验公式G=(3.5~6.3)k*F确定段位吨位因销轴生产量大,需生产效率高故去交大的系数6.3取k=1,于是:G=6.3*1*146.8=924.84 选用1t锤。
- 1、下载文档前请自行甄别文档内容的完整性,平台不提供额外的编辑、内容补充、找答案等附加服务。
- 2、"仅部分预览"的文档,不可在线预览部分如存在完整性等问题,可反馈申请退款(可完整预览的文档不适用该条件!)。
- 3、如文档侵犯您的权益,请联系客服反馈,我们会尽快为您处理(人工客服工作时间:9:00-18:30)。
目录1 设计的前期准备 (1)1.1 零件分析 (1)1.1.1 零件的结构分析 (1)1.1.2零件材料的特性分析 (1)1.1.3 锻件的加工要求 (1)1.2工艺方案确定 (1)2 锤上模锻件设计 (2)2.1选择分模面 (2)2.2确定模锻件加工余量及公差 (2)2.2.1 锻件的形状复杂系数 (2)2.2.2 锻件的质量 (3)2.2.3 锻件的材质系数 (3)2.2.4 模锻件的精度等级 (3)2.2.5 确定锻件公差和余量 (3)2.2.6 模锻斜度 (3)2.2.7 锻件技术要求 (4)2.3计算锻件基本数据 (4)3 确定锻锤的吨位 (5)4 确定飞边槽及尺寸 (6)5 确定终锻型槽 (7)6 设计预锻型槽 (7)7 绘制计算毛坯图 (7)8 制坯工步的选择 (8)9 确定坯料尺寸 (8)10 制坯型槽设计 (9)10.1滚挤型槽设计 (9)10.2拔长型槽设计 (10)11 锤用锻模设计 (10)11.1钳口尺寸确定 (11)11.2模块尺寸 (11)12 锻前加热锻后冷却及热处理要求的确定 (11)12.1确定加热方式,及锻造温度范围 (11)12.2确定加热时间 (12)12.3确定冷却方式及规范 (12)12.4确定锻后热处理方式及要求 (12)参考文献 (13)1 设计的前期准备1.1 零件分析1.1.1零件的结构分析转向节是汽车底盘上的关键零件,根据车型可分为重型汽车转向节、中型汽车转向节、轻型汽车转向节、微型汽车转向节、客车转向节和轿车转向节六大类;按其形状特征可分为长杆类、中心孔类和套管类三种。
长杆类转向节主要由杆部、法兰和枝权构成。
中心孔类转向节主要由基座,法兰和枝权构成,基座中心带孔。
套管类转向节主要由长杆、套管和法兰构成。
转向节是汽车转向桥上的主要零件,形状比较复杂,其形状兼具有轴类、盘类和叉架类等零件的特点。
转向节既支撑车体重量,又传递转向力矩和承受前轮刹车制动力矩,因此对其机械性能和外形结构要求严格,是汽车上的重要安全零件之一1.1.2零件材料的特性分析该锻件材料为18CrMnTi,是合金结构钢,是工业上应用最广泛的不锈钢,密度为7.85g/cm3。
18CrMnTi的预锻温度为1200℃,终锻温度为800℃。
1.1.3 锻件的加工要求模锻斜度7°,精度为普通级。
1.2 工艺方案确定根据零件的形状以及要求大批量生产,因此选用锤上模锻。
2 锤上模锻件设计2.1 选择分模面分模面是指模锻件在可分的模腔中成型时,组成模具型腔的各模块的分合面。
锻件分模位置合适与否,关系到锻件成形、锻件出模、材料利用率等一系列问题。
为了提高锻件质量合生产过程的稳定性,并使锻模结构尽量简单,防止上下模错移,分模面尽可能采用直线状,如图2.1分模面的位置所示。
图2.1 分模面的位置2.2 确定模锻件加工余量及公差2.2.1 锻件的形状复杂系数锻件的形状复杂系数S 时锻件质量或体积(G d ,V d )与其外廓包容体的质量或体积(G b ,V b )的比值,即:V V G G bd b d S == (2.1) 其中 V d ——锻件体积;V b ——外廓包容体的体积;G d ——锻件质量;G b ——外廓包容体的体积。
经估算:31863640mm V d =34855230mm V b =38.048552301863640===Vb Vd S查锻件形状复杂程度等级表[1]得该锻件形状复杂程度级别为S2级,形状复杂程度为一般。
2.2.2 锻件的质量锻件的质量可以根据锻件图的名义尺寸进行计算,即:v m ρ= (2.2)其中 ρ——材料密度,取7.85 g/cm 3V ——锻件体积,取1863640mm 3经计算,Kg m 63.14==ρν2.2.3 锻件的材质系数材质系数按锻压的难易程度划分两个等级,材质系数不同,公差不同。
该锻件的材料为18CrMnTi ,属于M 1。
2.2.4 模锻件的精度等级模锻件的公差一般为三级,普通级、半精度级和精度级,此锻件采用普通级。
2.2.5 确定锻件公差和余量根据锻件的名义尺寸、质量、精度等级、形状复杂系数以及锻件材质诸因素查找锻压手册确定长、宽和高度方向的尺寸公差。
查手册[1]得厚度方向公差 3.2mm mm 1.21.1+-,长度公差按各段长度分别查表,宽度公差3.2mm mm 1.21.1+-。
查手册[1]得高度方向单边余量为 2.0~2.5mm,取 2.5mm ,长度方向上余量为2.0~2.7,取2.5mm. 宽度方向上余量为2.0~2.5mm,取2.5mm 。
2.2.6 模锻斜度便于模锻件从型槽中取出,必须将型槽壁部做成一定的斜度,即模锻斜度。
它可以是锻件侧壁附加的斜度,也可以是侧壁的自然斜度。
模锻斜度有内斜度β和外斜度α。
当锻件冷缩时,锻件外侧趋向离开模壁,而内侧抱住模具型槽中凸出部分不易取出。
本设计中内外斜度均采用7°。
2.2.7 锻件技术要求1.图上未标注的模锻外斜度7°;2.图上未标注的圆角半径R=2mm;3.允许的错移量1.4mm;4.残留的毛边量1.4mm;5.允许的表面缺陷深度0.5mm;6.热处理表面渗碳0.9~1.3mm.7.热处理后喷丸或抛丸。
2.3计算锻件基本数据1.锻件在平面上的投影面积32371mm2;2.锻件的周边长度1007mm;3.锻件体积1863640mm3;4.锻件质量14.63kg。
3 确定锻锤的吨位模锻锤吨位选择恰当,既能获得优质锻件,又能节省能量,保证正常生产,并能保证模具有一定的寿命。
模锻过程是一个短暂的动态变化过程,受到诸多因素的制约,要获得准确的理论解是很困难的。
因此,生产中,为方便起见,多用经验公式或近似解的理论公式确定设备吨位。
有时,甚至采用更为简易的办法,即参照类似锻件的生产经验,通过类似来选择设备吨位。
经验公式法(1)按锻件在分模面上的投影面积、锻件的复杂程度和变形抗力确定模锻锤的吨位:件F G αβ= (3.1)式中 α——合金变形抗力系数;β——锻件复杂程度系数;件F ——不包括毛边的模锻件在分模面上的投影面积(钛合金包括毛边桥部在内)mm 2。
锻锤的选用一般用经验公式进行计算:经查表[1]:α=1.2~1.5,取1.5β=0.07F 件=32371 mm 2t Kg G 9.48.48794647507.05.1≈=⨯⨯=由计算结果可知,选用5吨锻锤。
(2)按锻件在分模面上的投影面积和材料性质确定模锻锤吨位:双动模锻锤G=(3.5~6.3)kF (3.2)式中G , G 1——锻落下部分质量(kg);E ——无毡座锤的打击能量(J);F ——锻件本体和毛边(按仓部的50%计算)在水平面上的投影面积(cm 2);K ——材料系数,查表4-10。
[2]按毛边槽尺寸考虑,假定毛边桥宽度为35mm,总面积=663.56cm 2,因大批量生产,取系数为5,k=1.0。
G=5×1.0×663..56=3318.25kg≈3.4t 综合考虑,安全起见选用5吨锤。
4 确定飞边槽及尺寸毛边槽的形式和尺寸对锻件质量影响很大,有六种形式。
1.飞边槽的作用:1)增加金属流出模膛的阻力,迫使金属充满模膛。
2)容纳多余金属。
3)锻造时飞边起缓冲作用,减弱上下模的直接撞击,防止模具的压塌与开裂。
2.飞边槽尺寸的确定:计算法计算法是采用经验公式计算毛边槽桥部高度,即()h0.015F mm=件式中F件——锻件在分模面上的投影面积32371mm2=()=2.7mmh0.015F mm件h h1 圆角R1 b b1 Fmax2.7 5 2.5 14 36 268图3.1飞边槽的形状5 确定终锻型槽终锻形槽及热锻件图见装配图的画法。
转向节材料为18CrMnTi;考虑收缩率取1.5%,绘制的锻件图如锻件图。
6 设计预锻型槽由于锻件较复杂,需要设置预锻型槽。
在头部开设坯料台(见锻模图)mmH h mmB A 5.26535.0)7.0~4.0(156025.025.0=⨯===⨯==7 绘制计算毛坯图根据转向节的形状特点,选取14个截面,分别计算锻F ,毛F ,计F 列于表3,并在坐标纸上绘出连杆的截面图和直径图。
为设计滚挤型槽方便,计算毛坯图按热锻件尺寸计算。
截面图所得面积即为计算毛坯体积,得3计1920481mm V =平均截面积为2总计均5.51763711920481mm L V F ===平均直径为mm F d 3.815.517613.113.1均均===表7.1 转向节外半轴计算毛坯的计算数据8 制坯工步的选择计算毛坯为一头一杆,则计算繁重系数如下39.13.817.112均max ===d d a 56.43.81371===dL β 计L 为计算毛坯杆部长度,β越大则轴向流动越困难。
查制坯工步应用范围表,制坯工艺方案为拔长-闭式滚挤。
9 确定坯料尺寸拔长加滚挤联合制坯,F 坯=(0.75-0.9)F max式中F max 为冷锻件图计算毛坯最大截面积取系数为0.85,则F 坯=22.880395.01974485.0mm =⨯mm F d .3101.8803913.113.1坯坯===选择坯料直径为Φ100的圆柱坯。
坯料体积:mm F V L 3.24310014.3191023142坯坯坯=⨯⨯==,取244。
考虑到钳口夹头长度取坯料长度244+100=344mm 。
33计坯1910231)%5.21(015.11948768)1(mm V V =+=+=δ10 制坯型槽设计10.1滚挤型槽设计(1)采用闭式滚挤,型槽高度,计算结果列于表1中,坯料的截面积为8659.8和锻件的截面积相比需要增加的部分K 取1.13,需要减小的部分K 取0.8,其余截面不变化。
按各截面的高度绘出滚挤型槽纵剖面外形,然后用圆弧或直线光滑连接,并适当简化。
(2) 型槽宽度为:坯料经过拔长mmd B 160~140)6.1~4.1(坯==取B=160mm 。
(3) 滚挤模腔的尾部与钳口 钳口形状可见图图3 修正后的闭式滚挤型槽外形设计尺寸按下式确定 mm30取,)2~1(1551.02662.0坯坯h m mm d R mmd h ==+==+=查参考文献[1]表4-26,尾部小槽的尺寸为mm r mm c mm a 10,30,8===。
10.2拔长型槽设计(1)拔长坎高度mm L V K a 1.5224993619585.0杆杆1=⨯== 取52mm ; (2) 拔长坎长度mmd K C 1301003.1坯3=⨯=;(3) 圆角半径mmR R mmC R 32510 2.5301325.025.01===⨯==;(4) 型槽宽度B=K 4d 坯 =1.4X100=140mm ;(5) 拔长膛深度mm a h .6122.36122杆=⨯== ,取123mm ; (6) 拔长型槽长度mm L L 25910249)10~5(杆=+=+=。