总装油漆数据
钢结构油漆用量计算

钢结构油漆用量计算主次钢结构都是根据防腐的要求来打砂油漆的,油漆的用量很大程度和干膜厚度有关的,与施工方法和涂装系统也有关系(喷涂要比手工刷的损耗率),以下数据是理论涂布率(仅供参考),实际用量乘上1.5-1.8的系数:75微米厚度的,大约8.5平方米/升;125微米厚度的,大约6.5平方米/升;200微米厚度的,大约4平方米/升。
一般是使用容积单位来衡量的。
油漆说明书里有个理论涂布率,就是涂1平方米100um(或者是50um等等自己可以换算)用多少L油漆。
比如这个数是X% 那么油漆用量=x%*25000*油漆厚度/100这个结果之后你再乘以一个损耗系数,比如1.3一般这个与施工的设备有关系。
在钢结构上焊缝的净重量是钢构件的1.5~2%左右。
然后根据这个来提焊条,由于是净重量所以焊条重量有些增加,加上留下的焊条头,和药皮的重量,一般需要焊条重量的是1.8~2.2倍。
点击☞工程资料免费下载钢结构工程油漆用量﹑损耗系数估算方法油漆的理论涂布率和实际涂布率计算公式在完全光滑平整且无毛孔的玻璃表面,倒上一升油漆,形成规定的干膜厚度后所覆盖的面积,就叫该油漆的理论涂布率。
理论涂布率=固体体积含量*10/干膜厚度(微米)(米²/升)实际工程施工时,因施工工件表面形状,要求的漆膜厚度,施工方法,工人技术,施工环境条件,天气等等各种因素的影响,油漆的实际使用量一定大于以施工面积除以理论涂布率计算出来的“理论使用量”。
油漆实际使用量/理论使用量(该比值定义为“损耗系数”CF。
)工程油漆实际用量 = 施工面积/实际涂布率=施工面积*CF/理论涂布率= 理论使用量× CF“损耗系数”CF分析及估算:工件表面粗糙度造成的油漆损耗在经过喷射处理的表面涂漆时,钢板波峰处的膜厚要小于波谷处的膜厚,为满足波峰处的防腐厚度要求(避免点蚀),波谷的坑洼中所“藏”的油漆就相当于被损耗了,此即“钢板粗糙度消耗损失”。
钢结构油漆用量计算
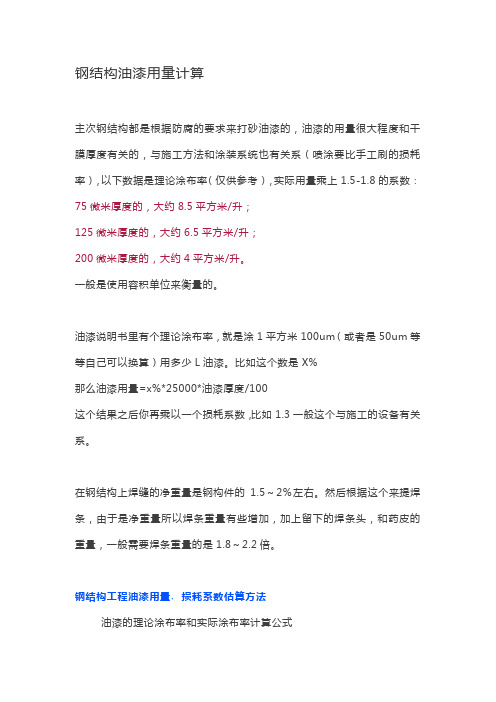
钢结构油漆用量计算主次钢结构都是根据防腐的要求来打砂油漆的,油漆的用量很大程度和干膜厚度有关的,与施工方法和涂装系统也有关系(喷涂要比手工刷的损耗率),以下数据是理论涂布率(仅供参考),实际用量乘上1.5-1.8的系数:75微米厚度的,大约8.5平方米/升;125微米厚度的,大约6.5平方米/升;200微米厚度的,大约4平方米/升。
一般是使用容积单位来衡量的。
油漆说明书里有个理论涂布率,就是涂1平方米100um(或者是50um等等自己可以换算)用多少L油漆。
比如这个数是X%那么油漆用量=x%*25000*油漆厚度/100这个结果之后你再乘以一个损耗系数,比如1.3一般这个与施工的设备有关系。
在钢结构上焊缝的净重量是钢构件的1.5~2%左右。
然后根据这个来提焊条,由于是净重量所以焊条重量有些增加,加上留下的焊条头,和药皮的重量,一般需要焊条重量的是1.8~2.2倍。
钢结构工程油漆用量﹑损耗系数估算方法油漆的理论涂布率和实际涂布率计算公式在完全光滑平整且无毛孔的玻璃表面,倒上一升油漆,形成规定的干膜厚度后所覆盖的面积,就叫该油漆的理论涂布率。
理论涂布率=固体体积含量*10/干膜厚度(微米)(米²/升)实际工程施工时,因施工工件表面形状,要求的漆膜厚度,施工方法,工人技术,施工环境条件,天气等等各种因素的影响,油漆的实际使用量一定大于以施工面积除以理论涂布率计算出来的“理论使用量”。
油漆实际使用量/理论使用量(该比值定义为“损耗系数”CF。
)工程油漆实际用量 = 施工面积/实际涂布率=施工面积*CF/理论涂布率= 理论使用量× CF“损耗系数”CF分析及估算:工件表面粗糙度造成的油漆损耗在经过喷射处理的表面涂漆时,钢板波峰处的膜厚要小于波谷处的膜厚,为满足波峰处的防腐厚度要求(避免点蚀),波谷的坑洼中所“藏”的油漆就相当于被损耗了,此即“钢板粗糙度消耗损失”。
下表给出不同的喷射方式引起漆料损失(以干膜厚度表示):漆膜厚度分布不均匀造成的油漆损耗施工后漆膜验收时膜厚达到或超过规定膜后,技术服务代表,监理或业主会按正常合格签字,但对未达到规定膜厚部分将被要求补涂,因此必将造成“超厚”损耗。
中华人民共和国汽车行业标准汽车油漆涂层QC-T484-1999

中华人民共和国汽车行业标准汽车油漆涂层本标准适用于汽车油漆涂层,不适用于汽车电器和仪表产品的油漆涂层。
1 油漆涂层代号的规定按汽车零部件的使用条件和涂漆质量要求的不同。
油漆涂层分10个组和若干等级。
按表1的规定。
表12 技术要求2.1油漆涂层的主要质量指标,按油漆涂层代号的组别和级别规定于表2。
QC/T 484-1999 代替JB/Z 111-662.2整车的漆膜应完整,不允许有露底(包括焊缝、封闭内腔)和碰伤的表面。
在总装的过程中,应加强对车身及覆盖件的油漆涂层的保护。
在总装后车架、底盘等应补漆。
2.3汽车零部件油漆涂层的颜色,本标准不做统一规定。
由各企业根据零部件的用途和用户的要求确定。
3 标注根据汽车各零部件的使用条件、涂层质量要求,选择油漆涂层的代号和等级。
例如:高级轿车车身装饰性涂层,在产品图纸上的标注如下:漆以TQ2甲QC/T484-1999。
4 检验4.1油漆涂层质量指标的检验方法,按下述规定:4.1.1漆膜外观:与标准版目测比较。
4.1.2漆膜光泽:按GB/T1764-1979《漆膜光泽度测定法》测定。
4.1.3漆膜厚度:按GB/T1764-1979《漆膜厚度测定发》测定。
4.1.4冲击强度:按GB/T764-1979《漆膜耐冲击测定法》测定。
4.1.5弹性:按GB/T1731-1979《漆膜柔韧性测定法》测定。
4.1.6硬度:按GB/T1730-1979《漆膜硬度测定发(摆杆法)测定》。
4.1.7耐碱性:采用以下两种检验方法测定:a)把涂漆的样板,浸入泥土80±2℃的碳酸氢钠水溶液中,经过是10min后,检查漆膜被溶解的状况;b)把涂漆的样板,浸在55±1℃含0.1 NaOH水溶液中,经过10min后,检查漆膜被溶解的情况。
4.1.9耐酸性:将0.1NH3SO4溶液,滴在被试样板上,在20℃下经过24h后观察漆膜变化情况4.1.10耐水性:将样板浸在50±1℃的恒温水浴中,观察漆膜变化情况,加温在50±1℃保持8h,然后停止加热,在保温的设备中自然冷却16h为一个周期。
油漆参数
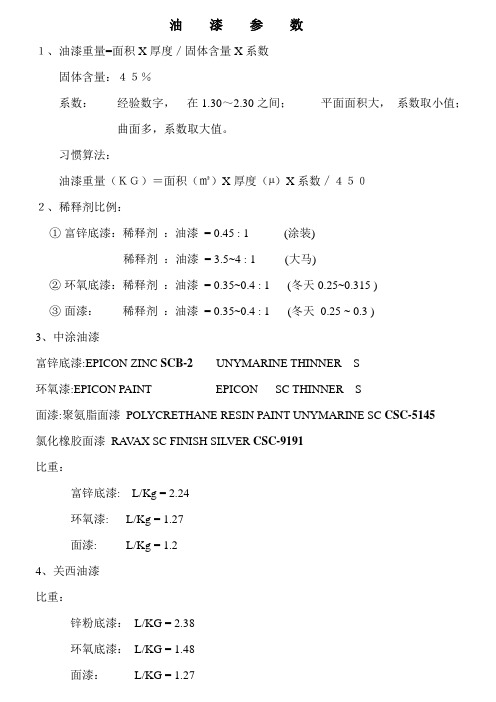
油漆参数1、油漆重量=面积X厚度/固体含量X系数固体含量:45%系数:经验数字,在1.30~2.30之间;平面面积大,系数取小值;曲面多,系数取大值。
习惯算法:油漆重量(KG)=面积(㎡)X厚度(µ)X系数/4502、稀释剂比例:①富锌底漆:稀释剂:油漆= 0.45 : 1 (涂装)稀释剂:油漆= 3.5~4 : 1 (大马)②环氧底漆:稀释剂:油漆= 0.35~0.4 : 1 (冬天0.25~0.315 )③面漆:稀释剂:油漆= 0.35~0.4 : 1 (冬天0.25 ~ 0.3 )3、中涂油漆富锌底漆:EPICON ZINC SCB-2 UNYMARINE THINNER S环氧漆:EPICON PAINT EPICON SC THINNER S面漆:聚氨脂面漆POLYCRETHANE RESIN PAINT UNYMARINE SC CSC-5145氯化橡胶面漆RA V AX SC FINISH SILVER CSC-9191比重:富锌底漆: L/Kg = 2.24环氧漆: L/Kg = 1.27面漆: L/Kg = 1.24、关西油漆比重:锌粉底漆:L/KG = 2.38环氧底漆:L/KG = 1.48面漆:L/KG = 1.275、各个油漆厂商产品固化物含量:汉堡KCC 中涂关西锌粉漆:49%45%53%80%环氧漆:41%51%46%80%聚氨酯漆:52%53%45%62%醇酸瓷漆:34% 40%丙烯酸漆:42% 42% 58%清漆:29.5% 30%氯化橡胶漆:40%UT6581: 68%6、各种油漆喷涂面积(40’H参考):汉堡KCC 中涂关西锌粉漆(大马):39.2m2/L 24.8m2/L 28.1m2/L 31.1m2/L锌粉漆(涂装):5m2/L 3.6m2/L环氧漆: 4.82m2/L 5.25m2/L 6.16m2/L 5.1m2/L聚氨酯漆: 4.15m2/L 5.8m2/L 6.2m2/L 2.53m2/L(门板) 氯化橡胶漆: 4.35m2/L 4.93m2/L丙烯酸漆: 3.35m2/L。
钢结构油漆涂布率参考

0.10
0.10 0.05 0.09 0.11 0.13 0.23 0.14 0.34 0.25
溶剂型乙基硅酸底漆 水性无机富锌底漆 水性环氧富锌底漆 有机硅锌粉底漆 环氧铁红底漆 环氧磷酸锌底漆 环氧三聚磷酸铝底漆 环氧云母氧化铁涂料 环氧防锈涂料 环氧红丹底漆 环氧通用底漆 环氧铝粉耐油漆 单组份快干型环氧底漆 环氧脂铁红、锌黄底漆 环氧脂中涂漆 环氧瓷釉面漆 环氧云铁中间漆 环氧厚膜型面漆 冬用型高固体表面处理环氧漆 环氧厚膜型中涂漆 环氧耐酸碱面漆 环氧树脂面漆 水性环氧云铁防锈漆、中涂漆 水性环氧防腐底漆 水性环氧防腐面漆 可覆涂聚氨脂面漆 聚氨酯面漆(芳香型) 高耐候性聚氨酯面漆(脂肪族) 单组份聚氨酯涂料底漆 单组份聚氨酯涂料面漆 聚氨酯底漆 聚氨酯中涂漆 氟碳涂料(面漆) 氟碳烘干面漆 氟碳烘干底漆 氟碳罩光清漆 氟碳防锈中间漆 水性氟碳涂料
0.16 0.23 0.33 0.10 0.16 0.24 0.19 0.20 0.18 0.12 0.12 0.21 0.22 0.18 0.21 0.20 0.24 0.26 0.13
0.1米) 理论涂布率M2/Kg 重量Kg/M2 丙烯酸工程面漆 40-60 7.5 0.13 丙烯酸铁红底漆 50-80 7.4(50) 0.14 丙烯酸云母氧化铁中涂漆 50 6.5 0.15 丙烯酸塑胶底漆 50 8.8 0.11 水性丙烯酸底漆 35 5.9 0.17 水性丙烯酸防腐面漆 50-75 5.9 0.17 新型防锈底漆 35 10 0.10 C051醇酸灰云母氧化铁防锈漆、面漆 50 6.2 0.16 醇酸红丹防锈漆 50 5.7 0.18 醇酸面漆 50 7.3 0.14 醇酸铁红防锈漆 50 8.03 0.12 醇酸磷酸锌防锈底漆 50 6.7 0.15 醇酸铝粉石墨面漆 40-60 7.5 0.13 醇酸耐油漆 35 10 0.10 乙烯改性醇酸面漆 40 9.1 0.11 有机硅改性醇酸面漆 40 8.3 0.12 耐候型醇酸磁漆 50 7.3 0.14 丙烯酸改性醇酸面漆 50-60 7.0-9.1 触变性醇酸漆(厚浆型) 100-120 3.86-5.34(底) 4.76-5.05(面) 氯化橡胶中间漆、面漆 50 7.5 0.13 氯化橡胶厚膜底漆 80 3.98 0.25 丙烯酸改性氯化橡胶面漆 50 9 0.11 氯化橡胶底漆 35 9 0.11 氯化橡胶云铁防锈漆 70 4.1 0.24 氯化橡胶云铁中间漆 70 4.1 0.24 氯化橡胶铝粉防锈漆 40 8.7 0.11 高氯化聚乙烯底漆 高氯化聚乙烯防腐中间漆 高氯化聚乙烯云铁防锈漆 高氯化聚乙烯面漆 高氯化聚乙烯铝粉厚膜防腐漆 高氯化聚乙烯厚膜防腐面漆 氯磺化聚乙烯底漆 氯磺化聚乙烯清漆 氯磺化聚乙烯防水涂料 氯磺化聚乙烯面漆 氯磺化聚乙烯银粉面漆 磷化底漆 无机硅酸锌车间底漆 环氧铁红车间底漆 环氧富锌车间底漆 单组份环氧富锌底漆 环氧富锌防锈底漆 环氧富锌底漆 环氧树脂锌粉底漆 35-40 45-50 45-50 35-40 30 55-60 30 20 25-30 30-40 25 6 15-20 25 20 40 35 75 75 8.0-10 4.2-6 5.1-5.4 9.0-10 10 4.2-5.1 10.2 13 10.0-12 8.8-6.7 10.3 20 10.67 8.7 8 4.4 7.1 2.96 4
钢结构油漆用量计算
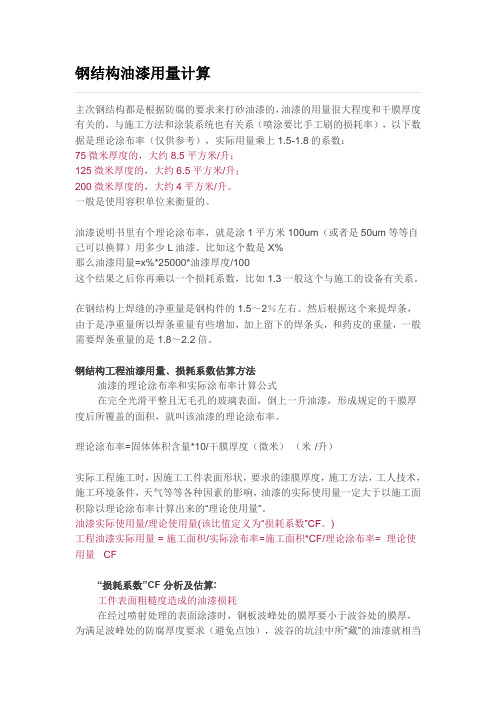
钢结构油漆用量计算主次钢结构都是根据防腐的要求来打砂油漆的,油漆的用量很大程度和干膜厚度有关的,与施工方法和涂装系统也有关系(喷涂要比手工刷的损耗率),以下数据是理论涂布率(仅供参考),实际用量乘上1.5-1.8的系数:75微米厚度的,大约8.5平方米/升;125微米厚度的,大约6.5平方米/升;200微米厚度的,大约4平方米/升。
一般是使用容积单位来衡量的。
油漆说明书里有个理论涂布率,就是涂1平方米100um(或者是50um等等自己可以换算)用多少L油漆。
比如这个数是X%那么油漆用量=x%*25000*油漆厚度/100这个结果之后你再乘以一个损耗系数,比如1.3一般这个与施工的设备有关系。
在钢结构上焊缝的净重量是钢构件的1.5~2%左右。
然后根据这个来提焊条,由于是净重量所以焊条重量有些增加,加上留下的焊条头,和药皮的重量,一般需要焊条重量的是1.8~2.2倍。
钢结构工程油漆用量﹑损耗系数估算方法油漆的理论涂布率和实际涂布率计算公式在完全光滑平整且无毛孔的玻璃表面,倒上一升油漆,形成规定的干膜厚度后所覆盖的面积,就叫该油漆的理论涂布率。
理论涂布率=固体体积含量*10/干膜厚度(微米)(米²/升)实际工程施工时,因施工工件表面形状,要求的漆膜厚度,施工方法,工人技术,施工环境条件,天气等等各种因素的影响,油漆的实际使用量一定大于以施工面积除以理论涂布率计算出来的“理论使用量”。
油漆实际使用量/理论使用量(该比值定义为“损耗系数”CF。
)工程油漆实际用量 = 施工面积/实际涂布率=施工面积*CF/理论涂布率= 理论使用量× CF“损耗系数”CF分析及估算:工件表面粗糙度造成的油漆损耗在经过喷射处理的表面涂漆时,钢板波峰处的膜厚要小于波谷处的膜厚,为满足波峰处的防腐厚度要求(避免点蚀),波谷的坑洼中所“藏”的油漆就相当失(以干膜厚度表示):漆膜厚度分布不均匀造成的油漆损耗施工后漆膜验收时膜厚达到或超过规定膜后,技术服务代表,监理或业主会按正常合格签字,但对未达到规定膜厚部分将被要求补涂,因此必将造成“超厚”损耗。
油漆的浓度或浓度标准范围

油漆的浓度或浓度标准范围油漆的浓度或浓度标准范围是指油漆中溶剂的含量和颜料的分散程度。
这些指标对于油漆的质量和施工效果有重要影响。
下面将介绍一些常见的油漆浓度标准范围。
1. 溶剂含量:油漆中的溶剂主要是用来调整油漆的流动性和干燥速度。
溶剂含量过高会导致油漆干燥时间过长,涂膜易出现开裂和脱落;溶剂含量过低则会影响油漆的流动性和施工效果。
一般来说,溶剂含量的标准范围为20%~40%。
2. 颜料分散程度:颜料是油漆中提供颜色和遮盖力的成分,颜料分散程度的好坏直接影响到油漆的质量。
颜料分散不均匀会使涂膜颜色不均匀,出现斑驳现象。
油漆制造商通常会进行颜料分散测试,常见的标准是通过目测或使用光谱仪评估颜料的分散程度,一般要求颜料分散度达到90%以上。
3. 固体含量:固体含量是指油漆中固体颗粒的质量占总油漆质量的比例。
固体颗粒主要包括颜料和填料,固体含量的高低会直接影响到油漆的厚度和涂膜的密实性。
固体含量一般为30%~60%,不同类型的油漆固体含量有所不同。
4. 膜厚度:膜厚度是指涂膜在干燥后的厚度,膜厚度对于油漆的保护和装饰效果起着重要作用。
不同的涂装对象和环境要求会有不同的膜厚要求,常见的膜厚要求为30~100μm。
5. 干燥时间:油漆的干燥时间是指涂膜从湿态到完全干燥所需的时间。
干燥时间的长短会影响到涂膜的施工效率和质量。
油漆生产商通常会在油漆参数表中提供干燥时间的范围,供施工人员参考。
综上所述,油漆的浓度或浓度标准范围包括溶剂含量、颜料分散程度、固体含量、膜厚度和干燥时间等指标。
这些指标的选择和控制对于油漆质量和施工效果至关重要,通过合理调整这些指标可以使油漆满足特定的使用要求。
施工人员在选择和使用油漆时应根据具体的需要,参考相关标准范围以获得最佳的涂装效果。
涂装常用计算公式
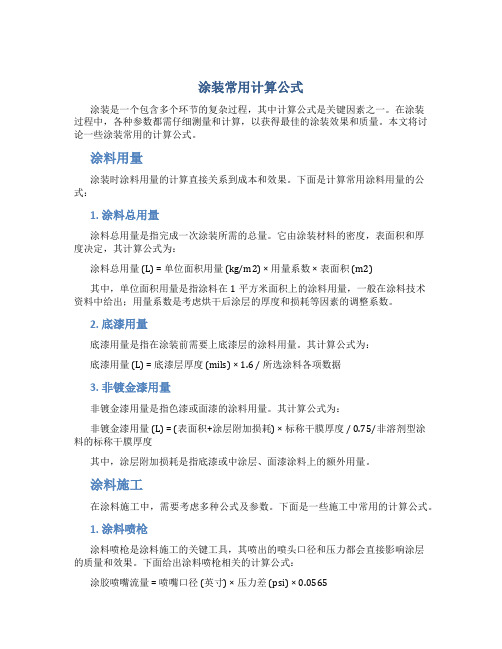
涂装常用计算公式涂装是一个包含多个环节的复杂过程,其中计算公式是关键因素之一。
在涂装过程中,各种参数都需仔细测量和计算,以获得最佳的涂装效果和质量。
本文将讨论一些涂装常用的计算公式。
涂料用量涂装时涂料用量的计算直接关系到成本和效果。
下面是计算常用涂料用量的公式:1. 涂料总用量涂料总用量是指完成一次涂装所需的总量。
它由涂装材料的密度,表面积和厚度决定,其计算公式为:涂料总用量 (L) = 单位面积用量 (kg/m2) × 用量系数 × 表面积 (m2)其中,单位面积用量是指涂料在1平方米面积上的涂料用量,一般在涂料技术资料中给出;用量系数是考虑烘干后涂层的厚度和损耗等因素的调整系数。
2. 底漆用量底漆用量是指在涂装前需要上底漆层的涂料用量。
其计算公式为:底漆用量 (L) = 底漆层厚度 (mils) × 1.6 / 所选涂料各项数据3. 非镀金漆用量非镀金漆用量是指色漆或面漆的涂料用量。
其计算公式为:非镀金漆用量 (L) = (表面积+涂层附加损耗) × 标称干膜厚度 / 0.75/非溶剂型涂料的标称干膜厚度其中,涂层附加损耗是指底漆或中涂层、面漆涂料上的额外用量。
涂料施工在涂料施工中,需要考虑多种公式及参数。
下面是一些施工中常用的计算公式。
1. 涂料喷枪涂料喷枪是涂料施工的关键工具,其喷出的喷头口径和压力都会直接影响涂层的质量和效果。
下面给出涂料喷枪相关的计算公式:涂胶喷嘴流量 = 喷嘴口径 (英寸) × 压力差 (psi) × 0.0565涂胶施工速度 = 60 / 喷嘴速率其中,涂胶喷嘴流量是指喷嘴每分钟涂胶量,单位为gpm(每分钟加仑),喷嘴速率是指喷嘴每秒钟喷出的涂胶量,单位为cm3/s。
2. 施工温度及湿度温度和湿度是影响涂层干燥和硬化的主要因素,下面给出一些涂料施工中常用的计算公式:相对湿度 (RH) = (实际水汽压 / 饱和水汽压) × 100%饱和水汽压 = 0.6108 × exp [17.27 × (温度 / (温度 + 237.3))]涂胶干燥时间 (min) = 并成时间 / 干膜厚度 × 干燥修正系数 × 酱/湿度调整系数其中,涂胶干燥时间是指涂胶完成后开始干燥所需的时间,其单位为分钟;并成时间是指涂层硬化完全所需时间,其单位为小时。
喷漆使用的数字

喷漆使用的数字
1. 颜色编码:喷漆通常以颜色编码的方式进行标识。
每种颜色都有一个独特的编码或编号,以便用户能够准确选择所需的颜色。
这些数字编码通常与颜色标准相关联,例如 RAL 颜色标准或 PANTONE 颜色系统。
2. 涂层厚度:为了确保喷漆的质量和耐久性,了解涂层的厚度是至关重要的。
数字可以用来表示涂层的厚度,通常以微米(μm)或密耳(mil)为单位。
这些数字帮助用户确定需要涂覆的层数以及每层的厚度。
3. 干燥时间:不同类型的喷漆在涂覆后需要一定的时间来干燥。
数字可以表示喷漆的干燥时间,以分钟、小时或天数为单位。
这些数字帮助用户了解何时可以进行下一步操作或处理。
4. 比例和稀释:在喷漆混合或稀释过程中,数字可以表示喷漆与稀释剂或其他添加剂的比例。
这些数字确保用户获得正确的混合比例,以获得所需的喷漆性能。
5. 产品型号和批次:每个喷漆产品通常都有一个独特的型号或批次号码。
这些数字有助于追踪和识别特定的产品,包括其生产日期、生产地点和其他相关信息。
6. 安全数据:喷漆产品可能包含有关安全使用的重要信息,如易燃性、毒性等级等。
数字可以表示这些安全数据,帮助用户了解如何正确处理和使用喷漆。
总之,数字在喷漆使用中起到了关键的作用,提供了准确的信息和指导,以确保用户获得所需的颜色、涂层质量和性能。
油漆涂层厚度及涂布率情况

油漆涂层厚度及涂布率情况
1.醇酸漆涂层厚度40μm左右,涂布率7-8m2/L。
2.氯化橡胶漆涂层厚度50μm左右,涂布率5-6m2/L。
3.环氧漆涂层厚度75μm左右,涂布率6-7m2/L。
4.聚安酯漆涂层厚度50μm左右,涂布率7m2/L。
七、各类油漆调漆水使用方法及用量
1.要特别注意各类油漆调漆水不能混用,更不能用错。
2.醇酸漆调漆水使用量为0~5%,存放时间不同使用调漆水的量是不同的,通常存放时间长的漆用量稍大一些。
3.氯化橡胶漆调漆水使用量为4~8%,不能多用。
4.环氧漆调漆水使用量为8~12%,气温低时多加些,气温高时少加些。
5.聚安酯漆调漆水使用量为5%。
调制或涂饰聚氨酯漆时,不能与水、酸、碱、醇类接触。
尤其是硬化剂贮存与开封用后要封紧,防止潮气进入。
总之,各种调漆水都不能过量,过多会使油漆分子分离,降低覆盖率,产生缝隙,易渗水后生锈。
总装漆面控制方案
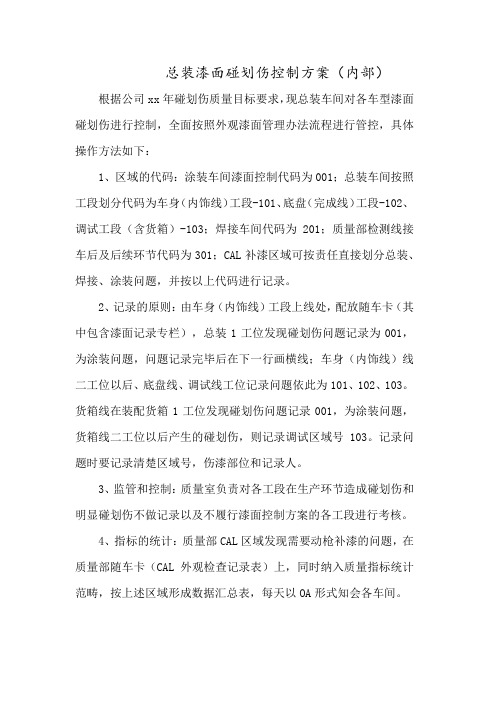
总装漆面碰划伤控制方案(内部)根据公司xx年碰划伤质量目标要求,现总装车间对各车型漆面碰划伤进行控制,全面按照外观漆面管理办法流程进行管控,具体操作方法如下:
1、区域的代码:涂装车间漆面控制代码为001;总装车间按照工段划分代码为车身(内饰线)工段-101、底盘(完成线)工段-10
2、调试工段(含货箱)-103;焊接车间代码为201;质量部检测线接车后及后续环节代码为301;CAL补漆区域可按责任直接划分总装、焊接、涂装问题,并按以上代码进行记录。
2、记录的原则:由车身(内饰线)工段上线处,配放随车卡(其中包含漆面记录专栏),总装1工位发现碰划伤问题记录为001,为涂装问题,问题记录完毕后在下一行画横线;车身(内饰线)线二工位以后、底盘线、调试线工位记录问题依此为101、102、103。
货箱线在装配货箱1工位发现碰划伤问题记录001,为涂装问题,货箱线二工位以后产生的碰划伤,则记录调试区域号103。
记录问题时要记录清楚区域号,伤漆部位和记录人。
3、监管和控制:质量室负责对各工段在生产环节造成碰划伤和明显碰划伤不做记录以及不履行漆面控制方案的各工段进行考核。
4、指标的统计:质量部CAL区域发现需要动枪补漆的问题,在质量部随车卡(CAL外观检查记录表)上,同时纳入质量指标统计范畴,按上述区域形成数据汇总表,每天以OA形式知会各车间。
油漆参数资料
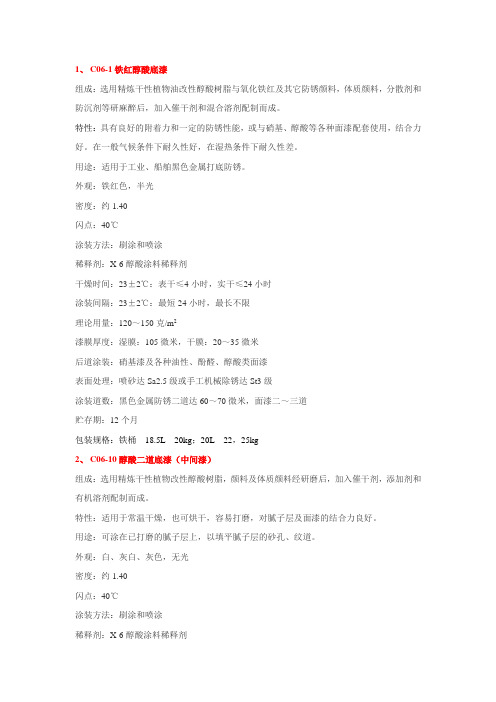
1、C06-1铁红醇酸底漆组成:选用精炼干性植物油改性醇酸树脂与氧化铁红及其它防锈颜料,体质颜料,分散剂和防沉剂等研麻醉后,加入催干剂和混合溶剂配制而成。
特性:具有良好的附着力和一定的防锈性能,或与硝基、醇酸等各种面漆配套使用,结合力好。
在一般气候条件下耐久性好,在湿热条件下耐久性差。
用途:适用于工业、船舶黑色金属打底防锈。
外观:铁红色,半光密度:约1.40闪点:40℃涂装方法:刷涂和喷涂稀释剂:X-6醇酸涂料稀释剂干燥时间:23±2℃:表干≤4小时,实干≤24小时涂装间隔:23±2℃:最短24小时,最长不限理论用量:120~150克/m2漆膜厚度:湿膜:105微米,干膜:20~35微米后道涂装:硝基漆及各种油性、酚醛、醇酸类面漆表面处理:喷砂达Sa2.5级或手工机械除锈达St3级涂装道数:黑色金属防锈二道达60~70微米,面漆二~三道贮存期:12个月包装规格:铁桶18.5L20kg;20L22,25kg2、C06-10醇酸二道底漆(中间漆)组成:选用精炼干性植物改性醇酸树脂,颜料及体质颜料经研磨后,加入催干剂,添加剂和有机溶剂配制而成。
特性:适用于常温干燥,也可烘干,容易打磨,对腻子层及面漆的结合力良好。
用途:可涂在已打磨的腻子层上,以填平腻子层的砂孔、纹道。
外观:白、灰白、灰色,无光密度:约1.40闪点:40℃涂装方法:刷涂和喷涂稀释剂:X-6醇酸涂料稀释剂干燥时间:23±2℃:表干≤3小时,实干≤24小时,烘干150±2℃:≤1小时涂装间隔:23±2℃:最短24小时,最长不限理论用量:130~150克/ m2漆膜厚度:湿膜:110微米,干膜:35微米表面处理:前道漆应完全干燥,除尽油漆上所有的油污和杂物。
前道涂装:醇酸、酚醛类防锈底漆后道涂装:硝基、油性、酚醛、醇酸类面漆或浅色面漆贮存期:12个月包装规格:铁桶18.5L20kg;20L22,25kg3、C06-11快干醇酸铁红底漆组成:由快干醇酸树脂、氧化铁红、防锈颜填料、催干剂、助剂、有机溶剂等组成。
油漆参数

氯磺化聚乙烯防腐工程面漆(单组份)组成该漆是由特种树脂、防锈颜料、填料等组成的单组份防腐面漆。
主要特性具有常温干燥、良好的耐候性、耐水性、及耐化学品性等。
用途广泛应用于化工设备、钢结构、煤气柜、冷水塔、海洋石油钻井等防腐面漆用。
技术指标干燥时间(25℃)表干≤0.5h实干≤24h附着力≤2级冲击强度≥50㎝柔韧性≤1㎜施工参数涂层厚度干膜厚度 30μm湿膜厚度 50μm理论用量 150g/㎡复涂间隔时间最短8小时最长不限前道配套底漆氯磺化聚乙烯防腐底漆、环氧云铁灰厚浆底漆涂装方法无气喷涂稀释剂 LJ专用稀释剂稀释量 0-5%(以油漆重量记)喷嘴口径 0.4-0.5mm喷涂压力 15-20Mpa(约150-200kg/cm2)刷涂、滚涂稀释剂 LJ专用稀释剂稀释量 0-5%(以油漆重量记)清洗剂 LJ专用稀释剂安全措施 B、D类详细解释参见《安全卫生操作标志》通风量 1kg油漆或稀释剂油漆 a.达到爆炸极限下限(LEL)的10% 58m3b.达到安全卫生标准(TLV) 2800m3稀释剂 a.达到LEL的10% 170m3b.达到安全卫生标准(TLV) 8000m3储藏期限 12个月(室内通风干冷处)注意事项·被涂物表面必须清洁、干燥·施工时所用的工具必须保证干燥清洁·必须使用配套的专用稀释剂兑稀,禁止与其他品种涂料拼合使用。
喷涂粘度根据施工现场条件而定。
备注为正确使用本厂产品,请仔细阅读《使用指南》声明本资料提供的信息完全基于我们在实验室和实践中所取得的知识,担忧漆的使用通常都是在我们的控制之外,除了油漆本身质量,我们不能担保任何东西。
我们保留不提前通知而修改所提供数据的权利。
氯磺化聚乙烯防腐底漆(单组份)组成该漆是由特种树脂、防锈颜料等组成的单组份重防腐涂料。
主要特性具有良好的附着力、柔韧性、耐化学品性,应用面广、施工方便。
用途广泛应用于化工设备、钢结构、煤气柜、冷水塔等防腐底漆用。
低档及国产油漆技术指标
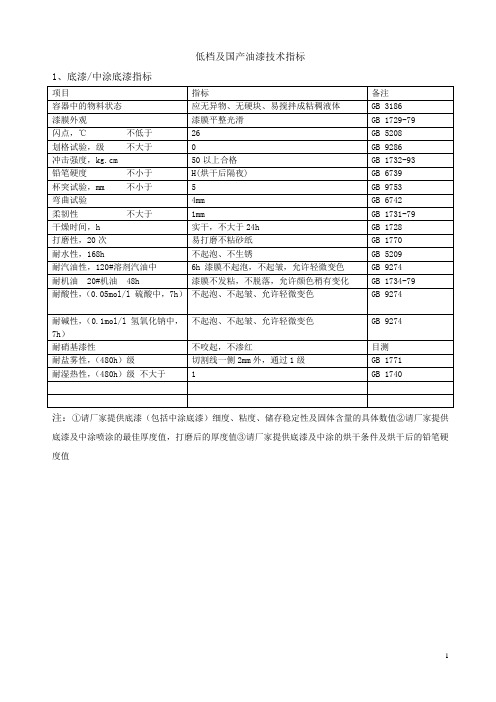
低档及国产油漆技术指标
1、底漆/中涂底漆指标
注:①请厂家提供底漆(包括中涂底漆)细度、粘度、储存稳定性及固体含量的具体数值②请厂家提供底漆及中涂喷涂的最佳厚度值,打磨后的厚度值③请厂家提供底漆及中涂的烘干条件及烘干后的铅笔硬度值
2、面漆指标
注:①请厂家提供面漆细度、粘度、储存稳定性、固体含量的具体数值②请厂家提供各色色漆的遮盖力数据(或单位面积的油漆用量)③请厂家提供各色色漆的喷涂厚度值及烘干后的铅笔硬度值
3、清漆技术指标
注:①请厂家提供清漆细度、粘度、储存稳定性及固体含量的具体数值②请厂家提供清漆的喷涂厚度值、烘干条件及烘干后的铅笔硬度值
1、所喷面漆的所有车辆在中国所有路况正常使用年限达5年时能保留70%以上的新车光泽度要求。
2、质量保证期在正常使用下不低于5年(要求5年之内漆面不能有起泡、粉化、生锈、开裂等常见油漆问题)。
在此期间,若因乙方产品质量问题引起购车用户对甲方的所有索赔,乙方负全部责任。
3、产品应该符合国家的环保要求。
油漆成品检验标准

木饰面:1、尺寸1.1、长度、宽度误差±0.3mm;1.2、对角线长度≥1400mm误差±2.0mm ;对角线长度<1400mm≥700mm误差±1mm;对角线长度<700mm误差±0.5mm;1.3、位差度:在相邻的板面前后、左右、上下节点错位量误差±0.5mm;1.4、木饰面平整度:取任意表面用1m靠尺测量其误差应小于0.3mm;1.5、木饰面工艺槽宽度、深度误差±0.3mm,角度误差±2°;镶嵌金属条、玻璃等物件时,镶嵌物件拼接处高低误差±0.1mm;2、漆面质量2.1、同一立面或同一空间的木饰面和配套产品色泽不应有明显色差要接近色板且光泽度要一致符合要求,漆面干燥后不得有下陷;2.2、不允许流挂、橘皮、积油、针孔、气泡、漏喷(少漆)缺陷;2.3、不允许鼓泡、划/压/碰伤、白化、颗粒、钉眼凹陷、钉眼异色明显缺陷;2.4、工艺槽:工艺槽宽度≤3mm的可以做混油,>3mm槽内贴皮,特殊要求除外。
工艺槽内颜色、表面质量同大面相同;2.5、饰面槽口及边缘不允许崩缺、粗糙、槽内积油等缺陷;活动柜、固定柜1、尺寸1.1、长度、宽度误差±0.5mm,对角线长度误差±1.0mm,其它按图纸误差±0.5mm;1.2、翘曲度:a、部件对角线长度≤700mm,翘曲度≤0.5mm;b、700mm<部件对角线长度≤1400mm,翘曲度≤1mm;c、部件对角线长度>1400mm,翘曲度≤2mm;1.3、孔位:垂直度、水平度、孔距偏差<±0.2mm;1.4、单独组装柜体长度、宽度、高度误差<±1mm,对角线误差<2mm;1.5、抽屉缝隙≤2.0mm,门缝隙2mm~3mm。
2、漆面质量2.1、整体产品和成套产品不能有明显的色差,且光泽度符合客户确认色板一致;2.2、不允许流挂、橘皮、积油、针孔、气泡、漏喷(少漆)缺陷;2.3、不允许鼓泡、划/压/碰伤、白化、颗粒、钉眼凹陷、钉眼异色明显缺陷;2.4、针对2.2、2.3条款缺陷对可见面不允许出现,不可见面允许轻微出现;门扇/门套1、尺寸1.1、门框:长度、宽度公差-0.0mm/+1.5mm,翘曲度<1.5mm/m;1.2、门扇:长度、宽度公差+0.0mm/-1.0mm,厚度公差-1.0mm/+0.5mm,翘曲度:1.5mm/m,对角线长度小于3mm,五金孔位误差±1mm,平整度小于1mm(1m靠尺);2、漆面质量2.1、整体产品和成套产品不能有明显的色差,且光泽度符合客户确认色板一致;2.2、不允许流挂、橘皮、积油、针孔、气泡、漏喷(少漆)缺陷;2.3、不允许鼓泡、划/压/碰伤、白化、颗粒、钉眼凹陷、钉眼异色明显缺陷;2.4、针对2.2、2.3条款缺陷对可见面不允许出现,不可见面允许轻微出现;。
828丙烯酸聚氨酯罩光清漆

828丙烯酸聚氨酯罩光清漆产品简介多元醇树脂与多异氰酸酯组成的聚氨酯清漆产品特性■良好的保色、保光性■漆膜丰满、坚固、耐磨损■极好的耐化学品和耐油性能■良好的施工性能■干燥迅速基本数据颜色透明光泽高光、半光、哑光混合比率主漆:固化剂=5:1(重量比)固体份38% (混合料)涂装膜厚干膜:20 µm/道湿膜:75 µm/道耗漆量理论值0.07 kg/m/220 µm(由于实际施工时的涂装环境、涂装方法、涂装技术、表面状况及结构、形状的不同,损耗率也就会有很大的不同)储存储存温度-10℃——40℃储存期限 1 年闪点21 ℃施工数据施工方法无气喷涂、空气喷涂、刷涂及辊涂喷嘴尺寸0.017-0.023无气喷涂出口压力100-150 kg/cm2稀释量0-10%稀释剂丙烯酸聚氨酯稀释剂施工温度5℃——40℃干燥时间~涂装间隔自燃干燥≤1小时(20℃)20 µm强制干燥90℃*30分20 µm重涂间隔16小时以上(20℃)涂装粘度(秒NK2#20℃)12-20秒熟化时间15分钟/20℃可使时间6小时(20℃)-4小时(35℃)表面处理●喷砂处理将钢铁表面除锈到SIS Sa2.5级后与面漆配套涂装●底漆表面应清洁,无污物●注意施工时与底漆的涂装间隔施工环境在温度持续低于5℃、湿度大于85%的场合或通风不良的情况下避免施工,钢板的温度高于露点温度3℃以上在夏天,阳光暴晒下时,重涂应该在5天内完成,超过5天打磨表面保证附着力保养期20℃七天以上容量主漆18Kg 固化剂3.6Kg安全事项●避免油漆接触皮肤和眼睛●如果油漆接触到皮肤,应用温水以及适当清洗剂清洗,如果油漆接触到眼睛,应用大量水冲洗并立即就医●保证良好的通风●涂料中含有可燃物质,请远离火花禁止在临近地区吸烟●火灾时,使用二氧化碳气体、泡沫、和粉末灭火机●作业前,请参阅《安全卫生注意事项》说明以上数据是根据实验和施工经验所得,鉴于产品使用条件非我方所能控制,产品使用众多影响因素,因此我们只对产品品质作出保证。
- 1、下载文档前请自行甄别文档内容的完整性,平台不提供额外的编辑、内容补充、找答案等附加服务。
- 2、"仅部分预览"的文档,不可在线预览部分如存在完整性等问题,可反馈申请退款(可完整预览的文档不适用该条件!)。
- 3、如文档侵犯您的权益,请联系客服反馈,我们会尽快为您处理(人工客服工作时间:9:00-18:30)。
2
2 63 48 40 64 61 82 68 82 13 68 164 240 2 35
955
50线含混装线
956C 国内 精品线
956CT20 956GT21
精品线
956CT20 956GT21
精品线
标准动臂 摇臂 标准拉杆 前车架 标准动臂 加长动臂
9 8 5 87 24 22 13 7 75 7 59 33 37 13 5 34
30B-Ⅱ
混装线
标准摇臂 加长摇臂 标准拉杆 加长拉杆 前车架 标准动臂 加长动臂 摇臂 标准拉杆 加长拉杆
3B-Ⅲ混装线Fra bibliotek二0一二年四月油漆车间(部件)结转数
机 型
车间
名
称
3月结转数
前车架 标准动臂 加长动臂 快换动臂 石材叉动臂 摇臂 50E-3
50线含精品线
271 159 109 3 121 120 97
标准拉杆 加长拉杆 石材叉拉杆 快换架 木材叉 石材叉 杂物叉 门架 前车架 标准动臂 加长动臂 摇臂 标准拉杆 加长拉杆 前车架 标准动臂 加长动臂 摇臂 标准拉杆 加长拉杆 前车架956C 前车架956G