新版FMEA-失效模式与影响分析实战训练(1)
FMEA-失效模式与效应分析(1)
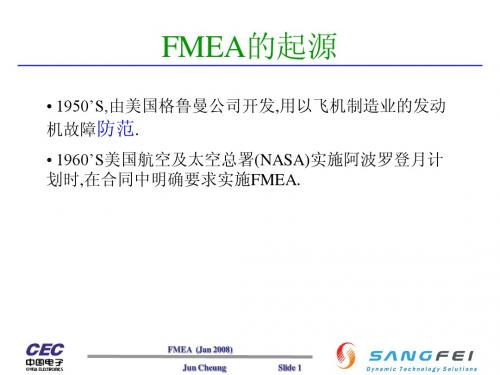
FMEA (Jan 2008) Jun Cheung Slide 17
Continued
C Process Function Potential Failure Mode Potential Effect(s) of Failure S e v l a s s Potential Cause(s) Mechanism(s) of Failure O c c u r Current Process Control Prevention Detection D e t e c R. P. N. Recommend Action(s) Responsibility & Target Complete Date Actions Taken Action Results S e v O c c D e t R. P. N.
1
2
3
4
5
6
7
8
9
1
2
3
4
5
6
7
8
9
10
11
12
13
14
15
16
17
18
以FPC安装为例 Process and Function: XXXX-XXX-SSS安装FPC
FMEA (Jan 2008) Jun Cheung Slide 9
Item 2: Potential Failure Mode
C Process Function Potential Failure Mode Potential Effect(s) of Failure S e v l a s s Potential Cause(s) Mechanism(s) of Failure O c c u r Current Process Control Prevention Detection D e t e c R. P. N. Recommend Action(s) Responsibility & Target Complete Date Actions Taken Action Results S e v O c c D e t R. P. N.
FMEA失效模式和效果分析培训教材
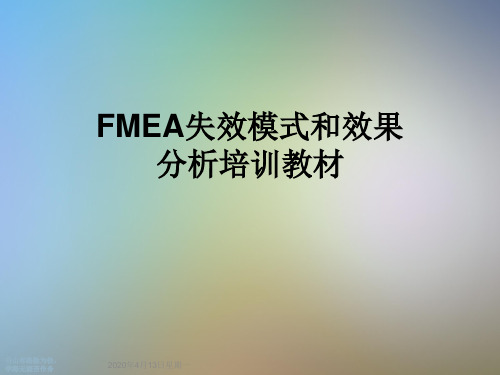
product/process and the effects of that failure 识别和评估一个产品或过程的潜在失效模式及其影响; 2. List down the actions which could eliminate or reduce the chance of the potential failure occurring 确定能排除或减少潜在失效发生的机率的措施; 3. Document all the elements for review and action 文件化整个过程。
•Taken from “The Certified Quality Engineer Handbook” ASQ
书山有路勤为径, 学海无涯苦作舟
Definition of FMEA FMEA定义 (II)
FMEA : Failure Mode and Effects Analysis FMEA:失效模式和效果分析
书山有路勤为径, 学海无涯苦作舟
Definition of FMEA FMEA定义
•An FMEA can be described as a systematic group of activities intended to : •FMEA 是一系列系统化的活动,其目的是 : 1. Identify and evaluate the potential failure modes of a
FMEA培训教材(失效模式和后果分析)

AUTHORITY CONSULTING
失效模式和后果分析(FMEA)
课程目的
AUTHORITY CONSULTING
掌握FMEA的概 念和运用时机 发现,评价产品/过程中 潜在的失效及其后果 找到能够避免或减少这 些潜在失效发生的措施 书面总结上述过程
Fቤተ መጻሕፍቲ ባይዱEA发展简史
AUTHORITY CONSULTING
Failure Model And Effect Analysis
FMEA应用的主要行业 -- 航空业 ——复杂的体系,产品和过程, 小批量生产 -- 汽车业——复杂的体系,产品和过程,大 批量生产 -- 其它行业
FMEA发展简史
AUTHORITY CONSULTING
正式使用FMEA技术是美国六十年代的阿波 罗登月计划.
AUTHORITY CONSULTING
新设计, 新设计,新技术或新过程 设计FMEA 对现有设计或过程的修改 将现有的设计或过程用于 新的环境, 新的环境,场所或应用 过程FMEA
FMEA实施说明
概念提 出和批 准
FMEA介绍-APQP过程图
项目批准 样件 试生产 投产
AUTHORITY CONSULTING
策划
DFME A
产品设计和开发
PFME A
过程设计和开发 产品与过程确认 生产
计划和确定 项目 产品设计和开 发验证 过程设计和开 发验证 产品和过程确认
FMEA介绍-总原则
AUTHORITY CONSULTING
总原则:每一个设计或过程功能/模式,对"失效的结果"分 总原则:每一个设计或过程功能/模式, 失效的结果" 析应能量化失效模式没有纠正导致的风险
过程失效模式及影响分析(过程FMEA)
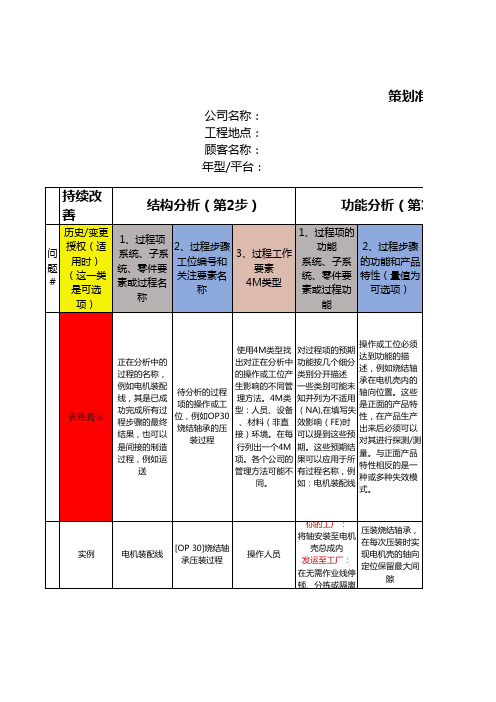
探测度 (D)
AP
特 殊 特 性
筛选器 代码 (选 填)
预防 控制
负
探测 措施
责 人 姓
目标 完成 时间
名
初始状态-过去经过验证 的控制和/或将要采用的
控制
1-10
H、M、L 、NA
CC
LL
为降低频 度所需的 附加措施
为改善 探测所 需的附 加措施
姓名
根据规范MRKL5039对
电机性能曲线进行100%
更多。量值/规格为 、过程项、最终用户)
可选,请查看过程文 建议在三个考虑方面旁
档。例如:压力、机 列出严重度评级,并使
器温度、冲洗液浓度 用最高的严重度评级。
、速度等。在过程进 例如,最终用的某个方面
行中可对过程特性进 可能并不总是获得最高
行测量。
的严重度评级。
1-10
失效模式 在“过程工作要
在产品 素的功能和过程
公司名称: 工程地点: 顾客名称: 年型/平台:
策划准备(第一步)
持续改 善
结构分析(第2步)
功能分析(第3步)
历史/变更
问 题 #
授权(适 用时) (这一类 是可选
项)
1、过程项 系统、子系 统、零件要 素或过程名
称
2、过程步骤 工位编号和 关注要素名
称
3、过程工作 要素
4M类型
1、过程项的 功能
跨职能团队:
分析(第3步)
失效分析(第4步)
失效影响的严重度 (S)
3、过程工作要 1、对于上一高层级
素的功能和过程 要素或最终用户的
特性
失效影响(FE)
2、关注 要素的 失效模
式 (FM)
过程FMEA失效模式及后果分析PPT培训课件

评估失效模式的 后果
确定失效模式的 严重程度…
制定预防和探测 措施
食品加工过程,包括原料 采购、加工、包装和储存 等环节。
例如,原料可能存在农药 残留、微生物污染等问题 ;加工过程中可能出现烘 烤不均匀、切割尺寸不对 等;包装过程中可能出现 标签错误、密封不严等。
例如,农药残留可能导致 消费者健康问题;烘烤不 均匀可能导致食品口感和 质量下降;标签错误可能 导致消费者对产品的误解 。
THANKS FOR WATCHING
感谢您的观看
跟踪实施效果
对改进措施的实施情况进行跟 踪和效果评估,持续改进。
02 过程FMEA的实施过程
确定分析范围和边界
确定分析对象
明确过程FMEA的分析对象,如产品、服务或系统 等,并定义其边界和范围。
确定分析阶段
确定失效模式可能发生的阶段,如设计、制造、 运输、安装等。
确定分析重点
根据分析对象和阶段,确定失效模式分析的重点 和关注点。
如何制定有效的改进措施和行动计划?
制定改进措施和行动计划是FMEA分析的最终目的。
根据风险优先级,选择具有最大潜在改进的失效模式进行改进。这可能包括设计更改、工艺改进、过 程控制强化等。制定行动计划时,应明确责任人、完成时间和检查点,以确保改进措施的有效实施。
如何持续改进FMEA分析?
持续改进FMEA分析可以提高其有效性和可靠性。
明确分析的对象,包括产品、系统、过程等,并对其进行 定义和描述。
列出所有可能的失效模式
全面考虑可能出现的失效模式,并对其进行分类和归纳。
评估失效模式的后果
分析失效模式可能导致的影响和后果,包括对产品、系统 、过程的影响以及对顾客的影响。
确定失效模式的严重程度、发生频率…
FMEA失效模式及后果分析手册精选全文

可编辑修改精选全文完整版FM E A 失效模式及后果分析手册FMEA (Failue Mode &Effect Analgsis ) Failue :失效、失败、不良 Mode :模式Effect :后果、效应、影响 Analgsis :分析一、FMEA 思维逻辑方法:D ’FMEA —→分析着重点BOM 表的零件及组装件P ’FMEA —→分析着重点OPC/AC 的零件加工及组装的工艺流程PRN 高风险优先系数 重点管理原则控制重点少数,不重要大多数列为次要管理 轻重缓急,事半功倍类比量产品(模块化) 工艺流程 过程参数/工艺条件 质量特性类比量产品 质量不良履历失败经验产品病历卡预设未来新产品投产后可能/潜在的会出现类似的不良事前 分析原因 整改措施(鱼刺图)先期产品质量策划结果控制计划(欧美) QC 工程表(台/日)新产品投产施工的要求监视和测量(首中末件检查)开发新产品例:有20项不良,前3项不良占70%,对策能解决50%的不良,70%*50%=35%后17项不良占30%,对策能解决100%的不良,30%*100%=30%①质量管理AC 柏拉图分析②物料管理MC 物料ABC法避免待料停工目的降低库存量的成本二、在何种情况下应进行FMEA分析:新产品开发阶段1、RP N≥1002、严重度/发生度/难检度(任一项)≥7;3、严重度≥7,发生度≥3;4、发生度≥5,难检度≥4量产阶段秉持持续改善的精神三、FMEA建立与更新时机1、新产品开发时;2、设计变更时(材质变更,BOM变更);3、工程变更;4、检验方法变更(检验设备/项目/频度)5、定期审查更新(建议每季度修订,至少也要每半年)四、FMEA分析表作成说明35%>30%重效果大,轻效果小活性化文件随时更新有效版本的识别(以修订日期)1、增加零件编号与名称:与BOM 表一致(D ’FMEA 分析,着眼在构成零件及组装件);2、增加工序编号与名称:与OPC/AC 表一致(P ’FMEA 分析,着眼在加工与组装工艺流程,D ’FMEA 可省略)3、功能与要求:已含外观、颜色、尺寸及ES TEST 功能质量要求;4、潜在失效模式:类比量产品质量不良履历(历史档)→产量履历→失效分析累积5、潜在失效效应(后果):万一不良时会造成的后果,如影响安全性/功能性/一般性,必须站在广义的客户中思考,包含: ● 下工程● 直接客户:下购销合同者/客户:如代理商 ● 最终客户:user/消费者6、严重度:参照对照表予以评估,复合型≥7;功能性4~6;一般性<4;7、分类(等级)class :与CC/SC 管制特性计划清单一致,包含符号识别,如FORD ▽,通用,依客户指定或本司对等的符合标注。
fmea培训资料最新版(141页)

FMEA培训资料最新版(141页)FMEA(失效模式和影响分析)是一种系统的、结构化的方法,用于识别和评估产品或过程中的潜在失效模式,以及这些失效模式对最终用户的影响。
FMEA培训资料旨在帮助参与者了解FMEA的基本概念、方法和工具,以便在实际工作中应用FMEA来提高产品或过程的质量和可靠性。
一、FMEA概述FMEA是一种预防性的质量工具,它通过系统性地识别和分析潜在的失效模式,以及这些失效模式对产品或过程的影响,来降低失效风险。
FMEA通常分为两个阶段:设计FMEA(DFMEA)和过程FMEA (PFMEA)。
DFMEA关注于产品设计和开发阶段,而PFMEA关注于制造和装配过程。
二、FMEA的基本步骤1. 定义项目范围:确定要分析的系统和子系统的范围。
2. 建立团队:组建一个跨职能的团队,包括设计、工程、制造和质量等部门的代表。
3. 识别失效模式:团队成员共同识别潜在的失效模式,并记录下来。
4. 分析失效影响:评估每个失效模式对最终用户的影响,包括安全性、成本、性能和可维护性等方面。
5. 评估失效严重性:根据失效影响的严重程度,对每个失效模式进行评分。
6. 评估失效发生概率:根据失效模式的已知历史数据或专家经验,评估每个失效模式的发生概率。
7. 评估检测难度:评估检测每个失效模式的难度,包括检测方法的有效性和成本。
8. 计算风险优先级数(RPN):将严重性、发生概率和检测难度相乘,得到每个失效模式的风险优先级数。
9. 采取预防措施:根据RPN,制定和实施预防措施,以降低失效风险。
10. 跟踪和更新:定期跟踪和更新FMEA,以确保其持续有效。
三、FMEA工具和模板FMEA工具和模板可以帮助团队更有效地进行FMEA分析。
常用的FMEA工具包括:1. FMEA表格:用于记录失效模式、影响、严重性、发生概率、检测难度和RPN等信息。
2. FMEA软件:提供自动化的FMEA分析功能,包括数据输入、计算和分析报告。
失效模式与影响分析(FMEA) 讲义
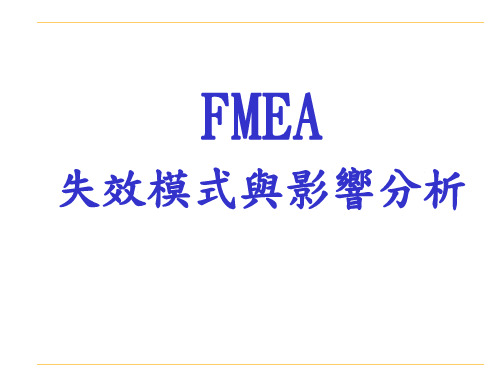
探測度评价基准参考表
检出率 几乎无法检出
非常微小 微小 非常低 低 中度 中高 高 非常高
几乎一定
等级 10 9 8 7 6 5 4 3 2 1
检出机会 <= 80.0%
> 80.0% > 82.5% > 85.0% > 87.5% > 90.0% > 92.5% > 95.0% > 97.5% > 99.5%
FMEA
失效模式與影響分析
Content
一.FMEA概論 二.FMEA作業流程 三.SOD的確定及判定準測 四.FMEA案例解析 五.FMEA實施注意事項
一.FMEA概論
定義
FMEA( Failure Mode and Effect Analysis) 是指在設計
或過程實施階段對構成的子系統﹑零件,以及構成的各 工序逐一進行分析,找出所有潛在的失效模式并分析出 可能的后果,從而預先采取必要的防范措施以提高產品 的品質和可靠性,提升過程的能力及穩定性等,并將全 過程形成文件的一種系統化的活動.
模后 式果
功能 要求
功能、特 性或要求 是什么?
后果是 什么?
会是什么问题? -无功能 -部分功能/功能 过强/功能降级 -功能间歇 -非预期功能
严级 潜
重别 在
度
失
S
效
起
因
机
理
有多
糟糕
?
起因是 什么?
频 现行 探 R 建
度 控制 测 P 议
O
预 防
探 测
度 D
N
措 施
责任 及目 标完 成日 期
潜在失效模式与后果分析(FMEA)培训

表面加工规范错误 维修保养说明错误
演算法不适当
维修保养说明不适当
16. 发生率(O):在设计的寿命中某一特定失效起 因/机理发生的可能性。描述发生率的级别数重在 其含义,而不是具体的数值。通过设计更改更改 来预防或控制该失效模式的起因/机理是降低发生 率级别数的唯一途径。
确定等级需考虑: 维修历史情况 部件是否全新设计 环境有无变化 用途有何变化 是否采取了预防性控制措施 针对用途,是否作了工程分析(如可靠度)来估计
构成零件
组件 功能件 子系统 系统
人、环境等
零件故障
对组件 的影响
FMEA的分析层次
对功能 件的影响
对子系 统的影响
对系统 的影响
对人和环境 等的影响
图1-1 FMEA的影响分析层次
设计FMEA的一个关系方块图(分析中所考虑的项目)
也可用其他形式的方块图
开关
3
2
灯泡总成
灯罩
4
4
1
极板
电池
弹簧
5
5
连接方法:1.不连接(滑动配合) 2.铆接 3.螺纹连接 4.卡扣连接 5.压紧装接
• “系统”的概念
1、“系统”。系统是指具有全部功能并可达成要求的任务 的产品,如汽车、轮船、飞机等可以称为机械系统;电脑、 卫星、移动电话等可称为电子系统。
2、子系统。子系统是系统的构成部分,能达成系统的部分 功能,如汽车的动力系统、电脑的显示系统等。
3、构成件。构成件是构成子系统和系统的单元,可分为功 能件、组件和零件。
没有特定的RPN值要求强制措施
1、小组的焦点应该定位于严重度最高等级的失效模式,当严重 度等级为9或10时,必须强制确保风险通过存在的设计控制 或建议措施来陈述
新版潜在失效模式及后果分析(FMEA)1

例举本次分析的产品失效模式:
31
➢ 步骤四:失效分析
失效链 FMEA中对失效的分析包括三个不同方面 ▲失效影响(FE) ▲失效模式(FM) ▲失效起因(FC)
30
➢ 步骤四:失效分析
失效 系统和子系统的失效模式描述是功能损失或退化。 功能的失效由功能推导而来。潜在失效模式包括但不限于以下 种: • 功能丧失(即无法操作、突然失效) • 功能退化(即性能随 间损失) • 功能间歇(即操作随机开始 停止 开始) • 部分功能丧失(即性能损失) • 非预期功能(即在错误的时间操作、意外的方向、不相等的性能) • 功能超范围(即超出可接受极限的操作) • 功能延迟(即非预期时间间隔后的操作) 例如:当向左打方向盘时,车辆向右转,这是非预期功能;
FMEA的定义和分类
FMEA的术语定义
• 失效(failure): 是指产品丧失规定功能的状态,又可译为故障。 失效与故障在含义上略有差别,失效是对不可修复产品而言;故障 是对可修复产品而言的。这里的失效含有这两方面的含义。
* 潜在失效模式(failure mode): 是指可以发生,但不一定非 得发生的失效模式,这时工程技术人员对设计、制造和装配过程中 认识到或感觉到的可能存在的隐患。
24
➢ 步骤二:结构分析
3.系统结构可视化:
灯泡
3
总成
4
D
极板
5
E
+ 零件
A.灯 罩
B.电 池
C.开 关
D.灯泡总成
E.电 极
03802-FMEA失效模式与影响分析培训资料.pdf
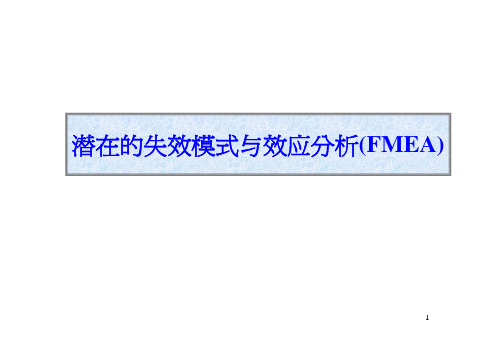
潜在的失效模式与效应分析(FMEA)1FMEA F:Failure 失效、失败→ 定义:达不到预期的功能或目的Fail to reach Scope. Objective. Purpose.Failure Mode (cause) Effect Analysis 2谈Failure ,先谈定义要层别得够细,否则收集的资料会很混淆在规定条件下不能完成其规定的功能,或参数不能保持在规定范围内,或操作者失误,造成产品功能失效,及因应环境力变化导致功能丧失。
FMEA Failure Mode (cause) Effect Analysis M:Mode在所有失效中,出现最多的(众数)例:2, 3, 3, 3, 4, 5, 5, 6, 7在组织有限的资源下,从失效最多的状况、最高的频率开始着手,此即Failure Mode3FMEA E:Effect 影响Effect谈三种:在有限resource 的状况下,从失效最多的状况开始着手,此即Failure ModeFailure Mode (cause) Effect Analysis 41.L ocal effect 2.Next high level effect 3.E nd effect(对本身的立即影响)(对同一Level 的影响,也可能对Next high level effect)(对产品用户的影响)(对end product 的user 影响,产品跑到user 身上,use 时才发现)D ownstream I nternal effect D ownstream E xternal effectFMEA 之沿革GrummanAircraft Company1950FMEA 飞机主操纵系统失效分析Boeing & Martin MariettaAerospace Company1957工程手册中正式列出FMEA 程序5Nation Aeronautics andSpace Administration (NASA)1960 FMEA 成功地应用于航天计划Defense DepartmentInternational ElectricalCommission (IEC)Chrysler, FordGM, ASQ, AIAG 1974出版Mil-STD-1629FMECA 1980出版Mil-STD-1629A FMECA 1985出版IEC812 FMEA 1993出版FMEA 手册1995出版FMEA 手册2001出版FMEA 手册FMEA定义及分析方式FMEA是一种工程技術用以定义、确认及消除在系统上、设计、制程及服务还没有到达顾客前已知的或潜在的失效、问题等。
失效模式与影响分析(FMEA)相关培训(医院)
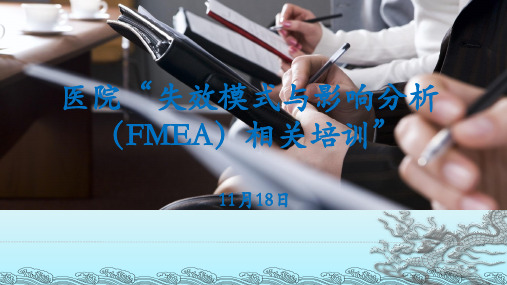
医院“失效模式与影响分析(FMEA)相关培训”11月18日主要内容(目录)一、东莞仁康医院迎接“2021年东莞市民营医院医疗服务质量现场评价工作”的通知(一) 失效模式与影响分析(FMEA )相关培训 一 (二) (三) 失效模式与影响分析的概念解读失效模式与影响分析的应用未做失效模式与影响分析的案例第七章共6节36条(616项)监测指标,用于对二级综合医院的日常运行、医疗质量与安全指标的监测与评审后的追踪评价。
《三级医院评审标准(2020年版)》第二部共设74 节240 条监测指标。
本部分在评审综合得分中的权重不低于60%。
工作模式转变为现场检查、主观定性、集中检查日常行为、客观指标、定量评价国家下发《医疗机构临床路径管理指导原则》截止2017-09-12临床路径累计印发数量达到1212个。
下发《单病种质量管理与控制技术方案(2020年版)》单病种质量监测信息项51项。
《病案管理质量控制指标(2021年版)、各类医疗质量控制指标等医疗质量管理办法发布时间: 2016-10-14 第10号 《医疗质量管理办法》已于2016年7月26日经国家卫生计生委委主任会议讨论通过,现予公布,自2016年11月1日起施行.主任:李斌 2016年9月25日 第四十七条 本办法下列用语的含义: (一)医疗质量:指在现有医疗技术水平及能力、条件下,医疗机构及其医务人员在临床诊断及治疗过程中,按照职业道德及诊疗规范要求,给予患者医疗照顾的程度。
(二)医疗质量管理:指按照医疗质量形成的规律和有关法律、法规要求,运用现代科学管理方法,对医疗服务要素、过程和结果进行管理与控制,以实现医疗质量系统改进、持续改进的过程。
(三)医疗质量安全核心制度:指医疗机构及其医务人员在诊疗活动中应当严格遵守的相关制度,主要包括:首诊负责制度、三级查房制度、会诊制度、分级护理制度、值班和交接班制度、疑难病例讨论制度、急危重患者抢救制度、术前讨论制度、死亡病例讨论制度、查对制度、手术安全核查制度、手术分级管理制度、新技术和新项目准入制度、危急值报告制度、病历管理制度、抗菌药物分级管理制度、临床用血审核制度、信息安全管理制度等。
设计失效模式与影响分析(DFMEA)应用与实操(李健老师课程部分课后测试)

设计失效模式与影响分析(DFMEA)应用与实操(李健老师课程部分课后测试)多选题1、在哪些情况下可以使用DFMEA()(10 分)A:新设计,新技术B:对现有设计修改D:将现有的设计用于新的环境,场所和应用2、FMEA的特征有哪些()(10 分)A:适时性B:团队性C:持续性D:传承性E:全面性F:针对性3、FMEA实施过程常见的问题有哪些()(10 分)A:SOD未与实际过程结合,动态调整B:客诉、不合格发生后FMEA未及时更新C:过程变更时,FMEA与CP不能同步更新D:FMEA只做为质量策划的资料保存E:失效模式未转化为知识管理及培训需求F:FMEA输出未能与SPC、CP与作业指导结合4、DFMEA团队的核心成员包括()(10 分)A:设计发布工程师;主任工程师C:制造工程师;接口工程师D:认证工程师;供应商FMEA工程师5、原因分析工具包括哪些()(10 分)A:鱼骨图B:Statistical统计图形C:DMAIC-Minitab统计分析D:8DE:5Why分析法6、下列关于风险分析过程中“频度”的说法,正确的是()(10 分)A:频度是指某一特定的起因/机理在设计寿命内出现的可能性C:评价准则表将频度分为非常低、低、中等、高和非常高。
D:通过设计变更或设计过程变更来预防或控制失效模式的起因/机理是可能影响频度降低的唯一的途径。
7、在评估DFMEA时,对现有的过程控制需要检查哪些情况()(10 分)A:确定预防/探测方法B:实际的控制和计划的控制是否吻合C:联系主要的变差来源或主要原因D:过度使用最终确认的分析方法判断题1、界面功能矩阵揭示了子系统,装配,部件,和零件之间的关系以及研究对象和相临系统和环境之间的界面关系。
(10 分)正确2、设计优化的主要目的是通过改进设计来制定降低风险和增加顾客满意度。
(10 分)正确3、在优化改进时,采取任何措施的目的都是以下列顺序来降低定级:S严重度→O频度→D探测度。
失效模式分析FMEA教育训练

PPT文档演模板
Eson Precision Engineer失i效n模g式分C析FoME.A,教L育训t练d 21
FMEA的益處
DFMEA: ------有助於設計測試和開發程序; -----從顧客角度評價失效; -----允許跟蹤和文件化降低風險的措施; -----將來分析和設計的極好參考; -----設計FMEA過程的文件化.
------系統組裝工程師及TEAM負責系統組裝FMEA, 並將此給PDT/PMT/QIT;
------設計工程師及TEAM負責設計FMEA,並將此給PDT/PMT/QIT; ------制程工程師及TEAM負責制程FMEA,並將此給PDT/PMT/QIT; ------設備工程師及TEAM負責設備FMEA,並將此給PDT/PMT/QIT; ------各段制作FMEA工程師必定是PDT/PMT/QIT成員.
▪ 利用表格進行工程分析
▪ 在設計階段早期發現問題
▪ 及早謀求解決措施
▪根據以往經驗與教訓對一些環節的分析
簡而言之:就是用工程方法預防失效或錯誤的發生,防患於未然.
PPT文档演模板
Eson Precision Engineer失i效n模g式分C析FoME.A,教L育训t练d 16
FMEA及時性
它是一個“事前的行為”而不是“事后行為” -------減輕事后修改的危機
1.安全失效 2.機能失效 3.管制失效 〈感覺、外觀〉
MODE
EFFECT
失效模式分析FMEA教育训练
FMEA作業展開
任務確認
決定 分析層級
系統、
子系統、
零件
經驗累積
提出 對策方案
RPN評價 選定對象
PPT文档演模板
FMEA-FMEA失效模式分析 精品001
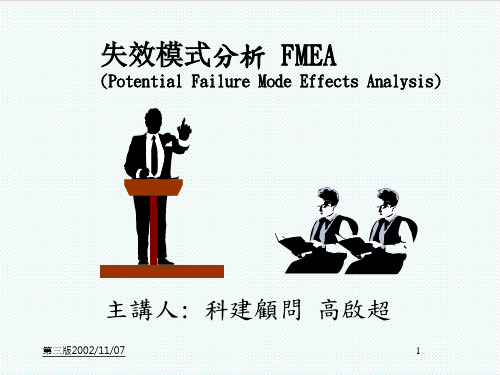
FMECA國際標準 (IEC812),即參考MIL-STD-1629A 加以部份修改而成。
第三版2002/11/07
7
FMEA之特徵
1.是一項以失效為討論重點的支援性與輔助性的可靠度 技術。
2.用表格方式進行工程分析,使產品在設計與製程規劃時 ,早期發現缺陷及影響程度以便及早提出解決之道。
沒有
沒有影響。
1
第三版2002/11/07
17
設計FMEA填寫說明
(13)等級 這個欄位用來區分任何對零件、子系統、或系統將要求附
加於製程管制的特性(如:關鍵的、主要的、重要的。 任何項目被認為是要求的特殊製程管制,將被以適當的特
徵或符號列入設計FMEA的分等欄位,並將於建議行動欄位被提 出。
每一個於設計FMEA列出的項目,將在製程FMEA的特殊 製程管制中被列出。
可能的話,最先使用第(1)種管制;其次,才使用第(2)種管制; 最後,才使用第(3)種管制。
第三版2002/11/07
22
設計FMEA填寫說明
(17)難檢度
查出失效 完全不確定
非常些微 些微
非常低的 低的
適中的 適度高的
高的 非常高的 幾乎確定
標準:查出可能會因設計管制的缺失 設計管制無法查出潛在原因/設備裝置和後 面相關的的失效模式;或根本沒設計管制。 非常些微機會可以查出在潛在原因/設備裝 置和後面相關的失效模式。 些微的機會可以查出潛在原因/設備裝置和 後面相關的失效模式。 非常低的機會可以查出潛在原因/設備裝置 和後面相關的失效模式。 較低的機會可以查出潛在原因/設備裝置和 後面相關的失效模式。 適中的機會可以查出潛在原因/設備裝置和 後面相關的失效模式。 適度高的機會可以查出潛在原因/設備裝置 和後面相關的失效模式。 較高的機會可以查出潛在原因/設備裝置和 後面相關的失效模式。 非常高的機會可以查出潛在原因/設備裝置 和後面相關的失效模式。 設計管制幾乎可以確定查出潛在原因/設備 裝置和後面相關的失效模式。
- 1、下载文档前请自行甄别文档内容的完整性,平台不提供额外的编辑、内容补充、找答案等附加服务。
- 2、"仅部分预览"的文档,不可在线预览部分如存在完整性等问题,可反馈申请退款(可完整预览的文档不适用该条件!)。
- 3、如文档侵犯您的权益,请联系客服反馈,我们会尽快为您处理(人工客服工作时间:9:00-18:30)。
新版FMEA-失效模式与影响分析实战训练
●课程背景
德国汽车工业协会(VDA QMC)在德国柏林召开股东会议,并正式宣布新版AIAG-VDA FMEA标准发布!这是一个历史性时刻,历经了长时间汽车行业专家的反复研讨和修订,第一版的AIAG-VDA标准终于正式发布!本次培训将根据最新发布的AIAG-VDA FMEA 要求,系统地讲解新版FMEA的背景,重要变化点以及企业如何应对等,并对新的AIAG-VDA FMEA七步法进行详细讲解,帮助企业迅速掌握新版FMEA的使用。
FMEA是1960 年代美国太空计划所发展出来的一套手法,为了预先发现产品或流程的任何潜在可能缺点,并依照其影响效应,进行评估与针对某些高风险系数之项目,预先采取相关的预防措施避免可能产生的损失与影响。
近年来广为企业界做为内部预防改善与外部对供货商要求的工具,是从事产品设计及流(制)程规划相关人员不得不熟悉的一套运用工具。
FMEA是系统化的工程设计辅助工具,主要利用表格方式协助进行工程分析,使其在工程设计时早期发现潜在缺陷及其影响程度,及早谋求解决之道,避免失效之发生或降低影响,提高系统之可靠度。
因此尽早了解与推动失效分析技术,是业界进军国际市场必备的条件之一!
●培训对象
研发总监、经理、工程师;质量总监、质量经理、质量主管、质量工程师、质量技术员;技术总监、经理、工程师、技术员;产吕流程总监、经理、工程师、技术员;生产经理、生产主管以及所有工程师(PE,ME,QA,SQE等)。
●培训时间
2-3天
●课程收获
1.了解最新版FMEA的背景及主要变化点
2.理解和掌握新版FMEA的七步法
3.预先考虑正常的用户使用和制造过程中会出现的失效
4.有助于降低成本提升效益,预防不良品的发生
5.建立产品可靠度保证系统,具备整体的概念
6.认识失效的类型及其影响
7.熟悉并运用失效模式与效应分析手法预防产品设计与制程规划可能发生的不良现象
8.累积公司相关不良模式与效应处理之工程之知识库,不断改进产品可靠性
课程大纲
第一章FMEA的发展过程
一.了解FMEA
二.FMEA定义
三.FMEA的目的
四.什么时候用FMEA
五.新版FMEA的主要变化
1.七步法代替以前的“填表法”
2.全新的SOD评分标准
3.全新的措施优先级AP取代RPN
4.增加了优化措施的状态跟踪
5.监视及系统响应的补充FMEA(FMEA-MSR)
6.全新的表格等
第二章FMEA简介
一.FMEA的时间顺序
二.FMEA集体的努力
三.成功的FMEA小组
四.FMEA小组的守则
五.FMEA小组决定的标准/模式
第三章执行新版PFMEA和实例
一.执行新版PFMEA的步骤
二.流程图的介绍与分析
三.特殊特性矩阵图的分析与练习
四.新版PFMEA模板和样例
五.新版PFMEA第一步:策划和准备
1.目的
2.PFMEA项目确定和边界
3.PFMEA项目计划
4.确定基础PFMEA
5.过程FMEA表头和练习
1)公司名称
2)制造地点
3)顾客名称
4)年型/项目
5)项目
6)PFMEA开始日期
7)PFMEA修订日期
8)跨职能团队
9)PFMEA ID编号
10)过程职责
11)保密级别
六.新版PFMEA第二步:结构分析
1.结构分析的目的
2.结构树的分析与练习
3.过程项
4.过程步骤
5.过程工作要素
6.结构分析实例
七.新版PFMEA第三步:功能分析
1.功能分析的目的。