分子动力学模拟位错和界面的相互作用
分子动力学模拟原理及其在材料科学中的应用

分子动力学模拟原理及其在材料科学中的应用概述:分子动力学模拟(Molecular Dynamics Simulation,简称MD)是一种基于牛顿经典运动方程的计算模拟方法,通过对原子或分子的位置、速度和受力进行迭代计算,模拟物质的宏观行为和微观结构。
该方法广泛应用于材料科学领域,用于研究原子尺度下的材料特性和反应行为,帮助解决许多实验无法观察到的现象。
模拟原理:分子动力学模拟基于牛顿第二定律和经典力场理论进行计算。
它将原子或分子看作质点,根据相互作用力和势能函数,使用数值积分方法求解运动方程,模拟物质内粒子的运动和相互作用。
在模拟过程中,需要考虑分子间相互作用力、键角势、位阻效应、偶极矩等因素,并通过热力学和统计学方法进行分析。
应用领域:1. 材料力学性能的研究:通过分子动力学模拟,可以研究材料的力学性能,如材料的弹性模量、屈服强度、断裂韧性等。
研究材料在不同应力和温度条件下的变化规律,可为材料设计和改性提供理论依据。
2. 材料缺陷与断裂行为:分子动力学模拟可以对材料中的缺陷进行研究,如晶体缺陷、位错、晶界等。
通过模拟分子在缺陷附近的行为,可以理解和预测材料的缺陷对材料性能的影响,同时也能研究材料的断裂行为和断裂韧性。
3. 界面和表面性质研究:分子动力学模拟可用于研究材料中的界面和表面性质。
通过模拟原子在界面和表面处的行为,可以研究材料的表面能、界面结合能、界面扩散等因素,为材料的表面改性和界面控制提供理论支持。
4. 物质相变和相分离研究:分子动力学模拟可以模拟材料的相变和相分离行为,如晶体生长、相分离、固溶体形成等。
通过模拟不同条件下材料相变的过程和机制,可以预测材料的相变温度、相变速率等重要参数,从而指导材料的合成和工艺。
5. 反应动力学研究:分子动力学模拟可用于研究材料中的化学反应和催化反应机制。
通过模拟反应物在反应中的行为,可以研究反应物之间的相互作用、反应速率、反应通道等,为理解和优化化学反应提供理论依据。
分子动力学模拟在材料科学中的应用

分子动力学模拟在材料科学中的应用导言分子动力学模拟是一种基于牛顿力学和统计力学原理的计算模拟方法,通过模拟分子之间的相互作用,预测材料的物理性质和化学反应,广泛应用于材料科学领域。
本文将重点阐述分子动力学模拟在材料科学中的应用。
材料表面与界面的分子动力学模拟在材料科学中,表面和界面现象是重要的研究对象。
分子动力学模拟可以用于研究材料表面和界面的结构、动力学行为及相互作用。
例如,分子动力学模拟可以用于研究金属表面的化学反应,从而预测附加原子的类型和吸附位置。
此外,分子动力学模拟还可以研究液体与固体的相互作用,从而预测液体的界面张力、界面浓度等性质。
这些应用在表面科学和材料科学中具有重要的意义。
材料力学性能的分子动力学模拟除了表面和界面现象,分子动力学模拟还可以用于研究材料的力学性能。
例如,分子动力学模拟可以用于研究材料的力学强度和材料的形成和断裂。
此外,分子动力学模拟还可以用于预测材料的塑性和断裂机制。
这些应用在材料科学中具有重要的意义,可以帮助材料科学家设计更加坚固的材料。
材料电子结构的分子动力学模拟另一个分子动力学模拟在材料科学中的应用是研究材料的电子结构。
分子动力学模拟可以研究材料的电子结构,例如,材料的电导率和带隙。
分子动力学模拟还可以用于研究材料的光学性质,例如材料的吸收光谱和透射光谱。
这些应用在材料科学中具有重要的意义,可以帮助材料科学家设计更好的电子材料和光学材料。
材料热力学性质的分子动力学模拟最后,分子动力学模拟还可以用于研究材料的热力学性质。
分子动力学模拟可以用于研究材料的热膨胀系数、热导率和比热容等性质。
这些应用在材料科学中十分重要,可以有助于材料科学家优化材料的热学性能。
结论在本文中,我们探讨了分子动力学模拟在材料科学中的几个重要应用。
这些应用在材料科学领域中具有广泛的应用前景,并在材料科学领域中发挥着重要作用。
随着计算机科学技术的发展和分子动力学模拟方法的不断改进,我们相信分子动力学模拟在材料科学中的应用将会越来越广泛。
不同温度下bcc-Fe中螺位错滑移及其与^(12)[111]位错环相互作用行为
![不同温度下bcc-Fe中螺位错滑移及其与^(12)[111]位错环相互作用行为](https://img.taocdn.com/s3/m/d2877531a200a6c30c22590102020740bf1ecd4c.png)
11¯1不同温度下bcc-Fe 中螺位错滑移及其与½[]位错环相互作用行为*王瑾† 贺新福 曹晗 贾丽霞 豆艳坤 杨文(中国原子能科学研究院, 反应堆工程技术研究部, 北京 102413)(2020 年10 月8日收到; 2020 年11 月9日收到修改稿)11¯1¯211¯110¯211采用分子动力学方法模拟研究了不同温度下bcc-Fe 中螺位错滑移行为和螺位错与½[ ]位错环相互作用机制. 结果表明, 螺位错在低温2 K 剪切应力下主要沿( )面滑移; 随温度逐渐升高到823 K, 它容易发生交滑移, 该交滑移在( )和( )面之间交替进行, 因此随温度升高, 临界剪切应力逐渐降低. 当螺位错滑移靠近位错环时, 不同温度下螺位错与位错环相互作用机制不同: 低温2 K 时, 螺位错与位错环之间存在斥力作用, 当螺位错滑移靠近位错环过程中, 螺位错发生交滑移, 切应力比无位错环时有所降低; 中温300 K 和600 K 时, 螺位错与位错环间斥力对螺位错的滑移影响减弱, 螺位错会滑移通过位错环并与之形成螺旋结构, 阻碍螺位错继续滑移, 切应力有所升高; 高温823 K 时, 螺位错因热激活更易发生交滑移, 位错环也会滑移, 两者在整个剪切过程中不接触, 剪切应力最低.关键词:bcc-Fe, 螺位错, 位错环, 分子动力学PACS :87.10.Tf, 87.15.A– DOI: 10.7498/aps.70.202016591 引 言在聚变反应堆中, 核结构材料将遭受恶劣的工作环境(高温、高压和高通量的中子辐照), 由此材料会发生级联碰撞和He 辐照损伤, 经长时间服役,出现肿胀、硬化和脆化等性能恶化[1−3]. 低活化铁素体/马氏体钢(reduced activation ferritic/mar-tensitic steels, RAFM)作为典型的体心立方(bcc)结构Fe 基材料, 因具有抗高热负荷性能, 抗高能粒子辐照性能和较好力学性能成为未来聚变堆候选结构材料. 然而目前RAFM 钢的发展瓶颈为辐照脆化和高温强度不足. 辐照硬化脆化主要归因于位错环、富 Cr 析出物、He 泡等辐照缺陷阻碍位错运动[4−25]. Hardie 等[4]发现 Fe-Cr 合金在辐照下会产生富Cr 析出相, 随后, 文献[5−7]采用分子¯11111¯1动力学方法对富Cr 析出物与位错的相互作用机制及硬化机理进行了研究, 模拟发现富Cr 析出物会阻碍位错运动, 引起剪切应力增大, 且不同析出物尺寸、Cr 含量和切过位置均会对硬化效果产生不同影响. 与之类似, He 泡[8−10]和位错环[11−15]也会阻碍位错滑移进而产生硬化. Terentyev 等[11]发现½[ ]位错环与刃位错之间存在排斥作用, 而当位错环上富集Cr 时则由排斥转为吸引. Rong 等[12]发现½[111]位错环迁移能很低, 容易被刃位错拖拽并随之一起滑移. ½[ ]位错环与刃位错的相互作用与温度(300—900 K)相关[13]: 当温度较高时, 位错环被刃位错拖拽一起运动; 当温度较低时, 位错环会被刃位错线拖拽一段距离后从位错上分离出来. 可见, 温度会影响位错环与刃位错的相互作用机制. 近年来, Liu 和 Biner [14]模拟研究了100—300 K 下½[111]位错环对螺位错滑移行为* 国家自然科学基金(批准号: U1867217)和国家重点研发计划(批准号: 2018YFE0308104)资助的课题.† 通信作者. E-mail: wangjin118114@© 2021 中国物理学会 Chinese Physical Society⟨111⟩11¯1的影响, 结果表明, 当½[111]位错环较小时, 环会发生旋转, 先被螺位错吸收随后又释放出位错环; 当½[111]位错环较大时, 先形成[100]位错片段, 最后½[111]位错环完全转变成[100]位错环.然而高温下½ 位错环对螺位错滑移行为的研究还相对较少. 相对于刃位错而言, 螺位错因较低可移动性, 对材料的塑性变形行为具有更为重要的影响[24,25]. 因此为了充分地理解螺位错在bcc-Fe 结构材料中所扮演的角色, 本文模拟研究了不同温度下螺位错的滑移行为和½[ ]位错环对螺位错滑移的影响, 并详细探讨了温度对位错环和螺位错之间相互作用的影响机制.2 原子模型与方法11¯111¯1112¯11011¯1¯11011¯111¯111¯1为了探究螺位错滑移行为及其与½[ ]位错环相互作用机制, 构建了如图1所示的两种初始构型. 图1(a)是螺位错模型, 图1(b)是含½[ ]位错环的螺位错模型. 这两个模型中x , y , z 轴取向分别为: [ ], [ ], [ ]. 模型尺寸是40.56 nm ×30.28 nm × 14.34 nm (晶格常数a 0 = 2.8553 Å),共包含1528242个原子. 螺位错滑移面法向为[ ], 位错线方向为 [ ], 柏氏矢量方向为 [ ].图1(b)中½[ ]位错环位于螺位错滑移面上, 位错环直径1.5 nm, 距离螺位错12 nm. 建立好模型后, 对上述模型进行能量最小化处理得到稳定构型, 随后进行模拟.采用分子动力学程序Lammps [26]进行模拟,Fe 原子间相互作用势函数的选取来自于文献[27].在整个模拟过程中, x 和y 方向采用自由边界条件,z 方向采用周期性边界条件[15]. 首先, 对初始构型进行能量最小化处理, 得到稳定构型; 随后, 采用NPT 系综, 对模型在一定温度2, 300, 600和823 K 下进行弛豫, 保持温度稳定; 最后, 采用NVT 系综, 对弛豫后的构型进行剪切变形, 沿着z 方向施加应变率为3.0 × 108 s –1, 时间步长为1 fs.⟨111⟩在模拟分析中采用开源可视化工具OVITO (open visualization tool) [28], 用公共近邻分析法CNA (common neighbor analysis)分析原子结构的转变, 位错提取算法DXA (dislocation extraction algorithm)分析不同柏氏矢量的位错. Fe 原子均用蓝色球形原子表示, 错排原子用白色球形原子表示, ½ 位错用绿色线条表示.3 模拟结果与讨论3.1 切应力-应变曲线11¯1图2为不同温度下螺位错及其与½[ ]位错环模型切应力-应变曲线, 图3(a)—(f)分别为2 K 下螺位错在剪切过程中不同应变量下z 截面构型图, 为了便于分析, 模型中均删除bcc 结构的Fe 原子, 仅剩余错排原子(包括界面原子、间隙原子和位错结构原子). 由图2可知, 当温度为2 K 时, 螺位错切应力-应变曲线包含4个阶段, 分别为I, II, III 和IV. 阶段I 为弹性变形阶段, 该阶段内螺位错未发生移动, 模型仅发生弹性变形, 应力Screw dislocation[112]½[111]dislocation loop- [111]- [110]-(a)(b)11¯1图 1 (a)螺位错模型和(b)含½[ ]位错环的螺位错模型11¯1Fig. 1. (a) Model of screw dislocation; (b) model of screw dislocation with ½[ ] dislocation loop./G P a11¯1图 2 不同温度下螺位错及其与½[ ]位错环模型切应力-应变曲线11¯1Fig. 2. Shear stress-strain (t -e ) curves of screw dislocationmodel with and without ½[ ] loop under different tem-peratures.¯21111¯1随应变量增加而线性增加, 应变区间和应力区间分别为e = 0—0.03和t = 0—0.98 GPa, 当e = 0时, 构型如图3(a)所示, 螺位错未滑移, 稳定存在于基体中, 图3(a)右上角为位错结构放大图. 阶段II 为位错滑移启动阶段, 该阶段内应力仍随应变量增大而增大, 但由于位错已准备启动滑移, 因此曲线斜率比阶段I 稍有降低, 应变区间和应力区间分别为e = 0.03—0.048和t = 0.98—1.45 GPa,当e = 0.03时, 螺位错结构发生变化, 准备启动滑移(图3(b)); 当e = 0.048时, 螺位错以扭结对形核[29]并开始滑移(图3(c)). 阶段III 为稳定滑移阶段, 如图3(d)和图3(e)所示, 位错以扭结对形式沿着( )面[15]稳定滑移, 应变区间e = 0.048—0.068, 该阶段内应力出现平台, 平台应力值为1.45 GPa, 不随应变量增大发生变化, 位错划过后在基体内残留下空位, 这些空位以聚集的错排原子显示(图3(e)), 是与文献[30]结论相似. 阶段IV 为位错划出模型阶段, 当e = 0.075时, 位错已经划出模型, 基体中仅剩下残余空位, 模型构型如图3(f)所示, 图3(f)右上角为临近右边界模型x 截面局部放大图, 可见残余空位线性排列, 该阶段剪切应力引起弹性变形, 应力随应变量增加线性增加, 应变区间和应力区间分别为e = 0.068—0.075和t = 1.45—1.52 GPa. 随着温度升高和½[ ]位错环插入, 切应力-应变曲线与单根螺位错模型存在明显不同(见图2), 这表明温度和位错环的存在会显著影响螺位错滑移行为, 下文3.2节和3.3节将详细阐明该滑移行为的差异.3.2 温度对螺位错滑移行为的影响¯211¯110由图2可知, 随温度升高, 螺位错切应力-应变曲线与2 K 时明显不同, 均不存在应力平台阶段. 图4(a)和图4(d), 图4(b)和图4(e), 图4(c)和图4(f)分别为300, 600和823 K 下螺位错在应变量e = 0.03和0.045下的z 截面构型图. 当e =0.03时, 螺位错因温度升高均已发生了滑移, 如图4(a)—(c)所示, 模型基体(尤其是螺位错附近)产生大量错排原子, 600和823 K 下错排原子数目明显比300 K 多, 图右上角为螺位错及其附近原子结构放大图, 这些错排原子会促进螺位错滑移, 因此温度越高, 螺位错滑移应力越低(与图3(b)和图2相对应); 当e = 0.045时, 螺位错均已滑移出模型, 如图4(d)—(f)所示, 详细观察发现, 位错划过后在基体内会残留些许空位, 这些空位排布可用来近似表征位错的滑移痕迹. 与2 K 下模型对比发现, 300, 600和823 K 下位错滑移痕迹存在不同, 这主要归因于螺位错的交滑移行为. 已有研究表明, 螺位错典型滑移面为{112}和{110}[15], 在本文中, 当温度从2 K 升高到823 K 时, 由于温度热激活作用[13−15], 它会沿着( )和( )面发生交替滑移, 因此模型临界剪切应力逐渐降低, 与图2中e = 0—0.045时的切应力-应变曲线变化相对应;(d)(e)(f)Screw dislocationReading to slideKink -pairSliding along (211) plane-Remained vacanciesRemained vacanciesScrew dislocation图 3 随应变量增加的螺位错模型构型图 (a) e = 0; (b) e = 0.03; (c) e = 0.048; (d) e = 0.058; (e) e = 0.068; (f) e = 0.075Fig. 3. Configurations of screw dislocation model with increasing strain: (a) e = 0; (b) e = 0.03; (c) e = 0.048; (d) e = 0.058;(e) e = 0.068; (f) e = 0.075.当e > 0.045时, 300, 600和823 K 下位错均已滑移出模型, 由于交滑移的发生, 位错滑移出模型时距离底端边界的位置明显比2 K 时有所升高(823 K 较为明显), 而应变量有所降低, 这表明温度越高, 位错滑移速度越快, 交滑移越明显.11¯13.3 螺位错与½[ ]位错环相互作用11¯1¯211¯110¯110¯211当模型中存在位错环时, 不同温度下位错环对螺位错滑移行为产生不同影响. 图5(a)—(c)分别为2 K 下含½[ ]位错环的螺位错模型在不同应变量下z 截面构型图. 当e = 0.015时, 螺位错未发生滑移, 螺位错和位错环z 截面结构如图5(a)所示, y 截面结构和位错环结构放大图如右上角所示; 当e = 0.03时, 螺位错准备发生滑移, 位错环发生旋转[31](图5(b)); 当e = 0.06时, 螺位错未滑移通过位错环, 而是从位错环上面滑过并在模型右界面上划出, 位错环完整保留在基体内, 螺位错滑移轨迹上留下残余空位缺陷(图5(c)). 与不含位错环模型相比, 该模型中螺位错滑移轨迹存在不同,这主要是由于当螺位错滑移靠近位错环时, 两者之间的排斥作用[11]导致螺位错在( )面上滑移受阻, 它会沿着( )面滑移, 之后在( )和( )面之间发生交滑移, 因此螺位错滑移出模型时距离底端边界的位置明显升高, 模型切应力明显降低,与图2中切应力-应变曲线相对应.随着温度升高到300 K 和600 K 时, 螺位错¯21111¯1会滑移通过位错环并与位错环发生交互作用, 模型在不同应变量下z 截面构型如图6(a)—(c)和图6(d)—(f)所示. 当e = 0.015时, 由于温度升高,位错环容易翻转, 螺位错也在热激活作用下已经发生了滑移(图6(a)和图6(d)), 此时螺位错与位错环间距离明显比图5(a)近; 当e = 0.03时, 螺位错沿着( )面滑到位错环处, 与之相互作用形成螺旋(helix turn)[14](图6(b)和图6(e)), 该结构阻碍螺位错继续滑动, 因此切应力有所升高(图2); 之后, 螺旋只能沿着螺位错线柏氏矢量方向发生滑移, 当e = 0.045时, 新的½[ ]位错环从螺位错中分离出来(图6(c)和图6(f)), 该新位错环与螺位错柏氏矢量方向一致, 但沿着Z 轴向上滑移了一定距离, 这与文献[14]研究结论一致. 可见, 当温度为300和600 K 时, 螺位错在剪切运动过程中,会与位错环发生交互作用: 一方面, 位错环会阻碍螺位错运动, 起到硬化效果; 另一方面, 螺位错成为位错环快速滑移运动的通道, 促使位错环发生滑移.随着温度进一步升高到823 K, 模型在不同应变量下z 截面构型如图7(a)—(c)所示. 当e =0.015时, 由于温度很高, 位错环更容易发生翻转,螺位错也更容易发生交滑移(图7(a)); 当e = 0.03时, 螺位错继续交滑移, 位错环也因热激活继续翻转, 它们之间没有接触(图7(b)); 当e = 0.045时,位错环沿Z 轴向下滑移了一段距离, 同时螺位错也滑移接近模型右边界(图7(c)). 由此可知, 823 K(d)(e)(f)Remained vacancies Remained vacanciesRemained vacanciesDisorder atoms Moredisorder atomsScrew dislocationhas slidedScrew dislocationhas slidedSlip traceSlip traceSlip traceScrew dislocation has slided图 4 不同温度下螺位错模型在e = 0.03 (a), (b), (c)和0.045 (d), (e), (f)时的构型图 (a), (d) 300 K; (b), (e) 600 K; (c), (f) 823 K Fig. 4. Configurations of screw dislocation model when e = 0.03 (a), (b), (c) and 0.045 (d), (e), (f) under different temperatures:(a), (d) 300 K; (b), (e) 600 K; (c), (f) 823 K.下螺位错始终未滑移通过位错环, 这与2 K 下位错滑移过程相似, 但不同的是, 由于此时温度较高,位错滑移速度增加, 同时螺位错更易发生交滑移,因此螺位错滑移出模型的应变量和切应力与2 K 下模型要低.综上所述, 当模型中存在位错环时, 不同温度下螺位错与位错环相互作用机制可分为三方面: 低温2 K 时, 螺位错与位错环之间存在斥力作用, 当螺位错滑移靠近位错环时, 螺位错发生交滑移, 未通过位错环, 因此位错环没有产生阻碍作用, 剪切应力比纯螺位错模型要低; 中温300和600 K 时,位错环容易翻转, 螺位错与位错环间斥力对螺位错Remained vacanciesDislocation loopDislocation loop Dislocation loopScrew dislocation图 5 2 K 下随应变量增加含位错环的螺位错模型构型图 (a) e = 0.015; (b) e = 0.03; (c) e = 0.06Fig. 5. Configurations of screw dislocation model with dislocation loop with increasing strain at 2 K: (a) e = 0.015; (b) e = 0.03;(c) e = 0.06.(a)(b)(c)(d)(e)(f)Dislocation loopflippedDislocation loopflippedScrew dislocation has slided Screw dislocationhas slidedHelix turnHelix turnNew dislocation loopSliding alongaxisNew dislocation loopSliding alongaxis图 6 不同温度下含位错环的螺位错模型在 e = 0.015 (a), (d), 0.03 (b), (e)和0.045 (c), (f)时构型图 (a), (b), (c) 300 K;(d), (e), (f) 600 KFig. 6. Configurations of screw dislocation model with dislocation loop when e = 0.015 (a), (d), 0.03 (b), (e), and 0.045 (c), (f) un-der different temperatures: (a), (b), (c) 300 K; (d), (e), (f) 600 K.(a)(b)(c)Dislocation loop has flippedScrew dislocationhas slidedGo on flippingInitial dislocation loop Sliding along axis图 7 823 K 下随应变量增加含位错环的螺位错模型构型图 (a) e = 0.015; (b) e = 0.03; (c) e = 0.045Fig. 7. Configurations of screw dislocation model with dislocation loop with increasing strain at 823 K: (a) e = 0.015; (b) e = 0.03;(c) e = 0.045.滑移影响减弱, 两者靠近时螺位错滑移通过位错环, 螺位错继续滑移受位错环所阻碍, 因此剪切应力有所升高; 高温823 K 时, 斥力影响更弱, 位错环更容易翻转和滑移, 螺位错也更容易发生交滑移, 该温度下螺位错交滑移行为占主导, 在整个滑移过程中始终未通过位错环, 因此位错环没有产生阻碍作用, 剪切应力与纯螺位错模型差距不大.4 结 论在前人研究螺位错滑移行为的基础上, 本文进一步揭示了不同温度下螺位错的滑移行为, 详细探讨了位错环缺陷与螺位错的相互作用机制, 结论归结如下:¯211¯110¯2111) 当温度为2 K 时, 单根螺位错在剪切应力下沿着( )面滑移, 临界剪切应力为1.45 GPa;随温度逐渐升高到823 K, 切应力逐渐降低, 螺位错易在( )和( )面发生交滑移, 其中823 K 下交滑移行为较明显.2) 低温2 K 时, 螺位错易发生交滑移, 螺位错在整个滑移运动过程中未通过位错环, 切应力低于纯螺位错模型.3) 中温300 K 和600 K 时, 螺位错滑移通过位错环, 并与之相互作用形成螺旋结构, 阻碍螺位错继续滑移, 切应力高于纯螺位错模型.4) 高温823 K 时, 螺位错更易发生交滑移, 位错环也更容易翻转和滑移, 螺位错在整个滑移运动过程中始终未通过位错环, 切应力与纯螺位错模型差距不大.⟨111⟩⟨100⟩该研究对服役过程中核结构材料的塑性变形行为有一定理论指导意义, 但是由于结构材料基体内不仅存在 位错环, 还有 位错环, 而且不同类型位错环拥有不同柏氏矢量, 因此本文只是研究了位错环一隅, 为了完整全面地阐明位错环与螺位错相互作用机制, 还需进一步研究.参考文献U llmaier H 1984 Nucl. Fusion 24 1039[1]S okolov M A, Tanigawa H, Odette G R, Shiba K, Klueh R L2007 J. Nucl. Mater. 367 68[2]D ai Y, Long B, Tong Z F 2008 J. Nucl. Mater. 377 115[3]H ardie C D, Williams C A, Xu S, Roberts S G 2013 J. Nucl.Mater. 439 33[4]S uganuma K, Kayano H 1983 J. Nucl. Mater. 118 234[5]T erentyev D, Haghighat S M H, Schaublin R 2010 J. Appl.Phys. 107 55[6]J ia L X, He X F, Dou Y K, Wu S, Wang D J, Yang Wen2017 Nuclear Power Engineering 38 115 (in Chinese) [贾丽霞,贺新福, 豆艳坤, 吴石, 王东杰, 杨文 2017 核动力工程 38 115][7]W ang Y X, Xu Q, Yoshiie T, Pan Z Y 2008 J. Nucl. Mater.376 133[8]O setsky Y N, Stoller R E 2015 J. Nucl. Mater. 465 448[9]Y ang L, Zhu Z Q, Peng S M, Long X G, Zhou X S, Zu X T,Heinisch H L, Kurtz R J, Gao F 2013 J. Nucl. Mater. 441 6[10]T erentyev D, Bergner F, Osetsky Y 2013 Acta Mater. 61 1444[11]R ong Z, Osetsky Y N, Bacon D J 2005 Philos. Mag. 85 1473[12]J ia L X, He X F, Dou Y K, Wang D J, Wu S, Cao H, YangW 2019 Nucl. Instrum. Methods Phys. Res. 456 103[13]L iu X Y, Biner S B 2008 Scripta Mater. 59 51[14]H ale L M, Zimmerman J A, Weinberger C R 2014 Comput.Mater. Sci. 90 106[15]Y ang L, Gao F, Kurtz R J, Zu X T 2015 Acta Mater. 82 275[16]Z hang L, Fu C C, Hayward E, Lu G H 2015 J. Nucl. Mater.459 247[17]M artinez E, Schwen D, Caro A 2015 Acta Mater. 84 208[18]Z hurkin E E, Terentyev D, Hou M, Malerba L, Bonny G 2011J. Nucl. Mater. 417 1082[19]W akai E, Hishinuma A, Kato Y, Yano H, Takaki S, Abiko K1995 J. Phys. IV France 5 C7-277[20]X u H X, Stoller R E, Osetsky Y N, Terentyev D 2013 Phys.Rev. Lett. 110 265503[21]T erentyev D, Bacon D J, Osetsky Y N 2010 Philos. Mag. 901019[22]P ascale E T, Shehadeh M A 2018 Int. J. Plasticity 9 2[23]S ong G, Lee S W 2019 Comput. Mater. Sci. 168 172[24]X ia Z Y, Zhang Z J, Yan J X, Yang J B, Zhang Z F 2020Comput. Mater. Sci. 174 109503[25]L AMMPS Molecular Dynamics Simulator http://lammps./ [2020-10-7][26]C aro A, Hetherly J, Stukowski A, Caro M, Martinez E,Srivilliputhur S, Zepeda-Ruiz L, Nastasi M 2011 J. Nucl.Mater. 418 261[27]S tukowski A 2010 Modell. Simul. Mater. Sci. Eng. 18 015012[28]G ordon P A, Neeraj T, Li Y, Li J 2010 Modell. Simul. Mater.Sci. Eng. 18 085008[29]J aime M, Wei C, Vasily V B 2004 Nature Mater. 3 158[30]B acon D J, Osetsky Y N, Rong Z 2006 Philos. Mag. 86 3921[31]11¯1Screw dislocation slip and its interaction with ½[]dislocation loop in bcc-Fe at different temperatures *Wang Jin † He Xin -Fu Cao Han Jia Li -Xia Dou Yan -Kun Yang Wen(Reactor Engineering Technology Research Department , China Institute of Atomic Energy , Beijing 102413, China )( Received 8 October 2020; revised manuscript received 9 November 2020 )Abstract11¯1¯211¯110¯211Reduced activation ferritic/martensitic (RAFM) steel, as a typical body centered cubic (bcc) iron based structure material, has become a candidate material for future fusion reactor. Nano-scale prismatic interstitial dislocation loops formed in irradiated RAFM have been studied for many years because of their significant influences on the mechanical properties (e.g. irradiation embrittlement, hardening, creep, etc.). Compared with edge dislocation, screw dislocation has very important influence on plastic deformation behavior because of its low mobility. Thus, the mechanism of interaction between screw dislocation and interstitial dislocation loops has become an intense research topic of interest. In this study, the slip behavior of screw dislocation and the mechanisms of interaction between screw dislocation and ½[ ] dislocation loop in bcc-Fe at different temperatures are investigated by molecular dynamics simulation. The results show that the screw dislocation mainly slides along the ( ) plane at a low temperature of 2 K under the increase of shear stress. With the temperature increasing to 823 K, it is prone to cross slip, and then the cross slip occurs alternately in the ( ) plane and the ( ) plane. Therefore, with the increase of temperature, the critical shear stress decreases gradually. When the screw dislocation slips close to the dislocation loop, the mechanism of interaction between screw dislocation and dislocation loop is different at different temperature: at low temperature of 2 K, there is repulsive force between screw dislocation and dislocation loop, when screw dislocation slip approaches to the dislocation loop, the cross slip of screw dislocation can occur, and shear stress is lower than that from the model without dislocation loop; at medium temperatures of 300 K and 600 K, the influence of repulsive force on the cross slip of screw dislocation can be weakened, and screw dislocation will slip through the dislocation loop then form the new structure named helix turn, which further hinders screw dislocation slipping and results in the increase of shear stress; at a high temperature of 823 K, the screw dislocation is more likely to cross slip due to the thermal activation, and the slip of dislocation loop is also easier to occur, but the screw dislocation and the dislocation loop do not contact each other in the whole shearing process, therefore the shear stress is lowest.Keywords: bcc-Fe, screw dislocation, dislocation loop, molecular dynamicsPACS: 87.10.Tf, 87.15.A – DOI: 10.7498/aps.70.20201659* Project supported by the National Natural Science Foundation of China (Grant No. U1867217) and the National Key Research and Development Program of China (Grant No. 2018YFE0308104).† Corresponding author. E-mail: wangjin118114@。
分子动力学模拟原理及其在材料科学中的应用

分子动力学模拟原理及其在材料科学中的应用概述:分子动力学模拟是一种计算方法,通过模拟与描述分子间相互作用的运动方程来预测材料的物理、化学性质以及其在材料科学中的应用。
本文将介绍分子动力学模拟的原理以及在材料科学领域中的重要应用。
原理:分子动力学模拟的原理基于牛顿运动定律,即“质点上力等于质点质量乘以加速度”。
通过计算各个原子之间的相互作用力,可以预测系统在一定时间内的运动轨迹。
主要步骤包括选取分子的初速度、计算原子之间的相互作用力、更新原子位置和速度等。
分子动力学模拟的应用:1. 原子尺度材料研究:分子动力学模拟可以帮助研究人员深入了解材料的微观结构和性质,探索在原子尺度上材料的行为。
通过模拟纳米材料的力学性能、热传导、光学性质等,可以揭示材料内部的原子运动与相互作用规律,为新材料的设计和合成提供理论基础。
2. 材料性能优化:分子动力学模拟可以模拟和预测材料的性能,如强度、硬度、热膨胀系数等。
通过改变材料的组成、形状和处理条件,可以进一步优化材料的性能。
这些模拟结果可以指导实验设计和优化材料制备工艺,提高材料的性能和功能。
3. 催化材料设计:催化材料的设计和合成对于化学反应的效率和选择性有着重要影响。
通过分子动力学模拟,可以研究催化剂在反应过程中的结构演化、吸附性能和表面反应机理等。
这些模拟结果为催化剂的设计和合成提供了理论指导,有助于提高催化反应的效率和选择性。
4. 药物设计与研发:分子动力学模拟可以模拟和预测药物与生物分子之间的相互作用,为药物设计和研发提供理论基础。
通过模拟药物和靶标蛋白的相互作用过程,可以预测药物的亲和力和选择性,优化药物的结构和性能,提高药物的疗效和安全性。
5. 界面和表面科学:界面和表面的性质对材料的各种性能起着决定性作用。
通过分子动力学模拟,可以模拟和预测不同材料之间的相互作用、界面结构和界面性能。
这有助于理解和改善材料的界面性能,如阻尼、界面强化和附着性能。
结论:分子动力学模拟是材料科学中一种重要的计算方法,可以揭示材料的微观结构和性质,指导材料设计和优化。
分子动力学模拟(二)

分子动力学模拟(二)引言概述:分子动力学模拟是一种通过模拟分子之间相互作用力和相对位置的方法,来研究系统在不同条件下的动力学行为的技术。
本文将继续探讨分子动力学模拟的应用领域并深入介绍其在材料科学、生物医学和化学等领域的具体应用。
一、材料科学中的分子动力学模拟1. 分子结构与性质的研究1.1 分子间相互作用力的模拟与计算1.2 晶体缺陷与物理性质的关联1.3 材料相变的模拟及驱动机制的研究1.4 纳米材料的热力学性质模拟1.5 材料表面与界面的模拟研究2. 材料设计与优化2.1 基于分子动力学模拟的材料设计方法2.2 优化材料的结构与性能2.3 基于计算的高通量材料筛选2.4 分子动力学模拟在材料工程中的应用案例2.5 材料仿真与实验的结合二、生物医学中的分子动力学模拟1. 蛋白质结构与功能的研究1.1 蛋白质折叠和构象转变的模拟1.2 水溶液中蛋白质的动力学行为1.3 药物与蛋白质的相互作用模拟1.4 多肽和蛋白质的动态模拟1.5 分子动力学模拟在药物设计中的应用2. 病毒与细胞相互作用的模拟2.1 病毒与宿主细胞的相互识别与结合2.2 病毒感染过程的动态模拟2.3 细胞信号传导的分子动力学模拟2.4 细胞内各组分的动态行为模拟2.5 分子动力学模拟在生物药物研发中的应用三、化学中的分子动力学模拟1. 化学反应的机理研究1.1 反应路径与转变态的模拟1.2 温度和压力对反应速率的影响1.3 催化反应的模拟与优化1.4 化学反应中的动态效应模拟1.5 化学反应机理的解析与预测2. 溶液中的分子行为模拟2.1 溶剂效应的模拟与计算2.2 溶液中的分子运动与扩散2.3 溶液界面的分子动力学模拟2.4 溶液中的化学平衡与反应行为2.5 分子动力学模拟在化学合成与设计中的应用总结:分子动力学模拟在材料科学、生物医学和化学等领域具有广泛的应用前景。
通过模拟分子间交互作用力和相对位置的变化,可以深入研究分子系统的动力学行为,为材料设计、药物研发和化学反应机理的解析提供重要参考。
形成冶金复合材料界面的分子动力学模拟

形成冶金复合材料界面的分子动力学模拟在材料科学领域,冶金复合材料是一种非常有潜力的材料,它由两种或更多种不同的金属材料组成,通过热加工、机械加工、等离子弧焊、激光熔覆等工艺制备而成。
冶金复合材料因其物理性能优异,广泛应用于航空、汽车、机械等领域。
其中,界面的形成和性质对材料的整体性能有着至关重要的作用。
本文将介绍一种用分子动力学模拟研究冶金复合材料界面形成的方法。
一、分子动力学模拟简介分子动力学(Molecular Dynamics,MD)是一种分子模拟方法,主要用于研究分子间相互作用、分子的运动及其对宏观状态的影响。
分子动力学方法基于牛顿运动定律和哈密顿原理,通过数值模拟方法,将需要研究的分子体系建模并用数学方法求解其运动方程,从而得到分子的动态行为及性质。
二、冶金复合材料界面的分子动力学模拟冶金复合材料的界面是由两个或多个不同材料界面相互作用而形成的。
在分子动力学模拟中,可以通过建立一个真实的原子模型来研究界面形成的过程。
具体而言,包括以下步骤:(1)原子模型的构建冶金复合材料的材料选择和界面形态决定了原子模型的构建方式。
在构建原子模型时,首先需要选择用于模拟的原子种类和材料组成比例,然后通过分子动力学软件进行模型构建并设置参数,包括粒子间相互作用力和初速度等。
(2)原子模型的能量计算在模拟过程中,需要计算原子模型各个时刻的能量,以表征各个原子之间的相互作用。
因此,需要对原子间的相互作用力进行计算,从而得到体系的总势能。
通常采用Lennard-Jones 势函数来描述相互作用力。
(3)界面的形成过程模拟界面的形成主要是由于两种不同材料之间的扩散和相互作用引起的。
在分子动力学模拟中,可以通过模拟两种不同材料之间的相互作用,分析物质的扩散、界面的热力学稳定性及其界面形态变化等物理过程。
三、分子动力学模拟在冶金复合材料界面研究中的应用目前,分子动力学模拟在冶金复合材料界面的研究中已经得到广泛应用。
bcc-Fe中间隙型位错环与表面及裂纹相互作用的分子动力学研究
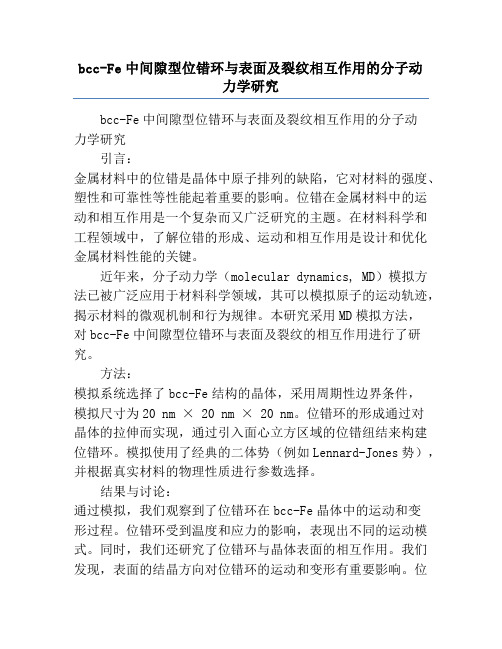
bcc-Fe中间隙型位错环与表面及裂纹相互作用的分子动力学研究bcc-Fe中间隙型位错环与表面及裂纹相互作用的分子动力学研究引言:金属材料中的位错是晶体中原子排列的缺陷,它对材料的强度、塑性和可靠性等性能起着重要的影响。
位错在金属材料中的运动和相互作用是一个复杂而又广泛研究的主题。
在材料科学和工程领域中,了解位错的形成、运动和相互作用是设计和优化金属材料性能的关键。
近年来,分子动力学(molecular dynamics, MD)模拟方法已被广泛应用于材料科学领域,其可以模拟原子的运动轨迹,揭示材料的微观机制和行为规律。
本研究采用MD模拟方法,对bcc-Fe中间隙型位错环与表面及裂纹的相互作用进行了研究。
方法:模拟系统选择了bcc-Fe结构的晶体,采用周期性边界条件,模拟尺寸为20 nm × 20 nm × 20 nm。
位错环的形成通过对晶体的拉伸而实现,通过引入面心立方区域的位错纽结来构建位错环。
模拟使用了经典的二体势(例如Lennard-Jones势),并根据真实材料的物理性质进行参数选择。
结果与讨论:通过模拟,我们观察到了位错环在bcc-Fe晶体中的运动和变形过程。
位错环受到温度和应力的影响,表现出不同的运动模式。
同时,我们还研究了位错环与晶体表面的相互作用。
我们发现,表面的结晶方向对位错环的运动和变形有重要影响。
位错环在<100>晶面上的运动速度更快,并且产生了较大的位错切应力。
另外,我们也研究了位错环与裂纹之间的相互作用。
裂纹是金属材料中常见的缺陷形式,它对材料的强度和韧性起着重要的影响。
模拟结果显示,位错环可以在裂纹端部聚集,并通过与裂纹之间的相互作用影响裂纹的扩展行为。
当位错环与裂纹相互作用时,位错环的运动会改变裂纹尖端的应力分布,从而影响裂纹的扩展速率和路径。
结论:通过分子动力学模拟,我们研究了bcc-Fe中间隙型位错环与表面及裂纹的相互作用。
研究结果表明,位错环对晶体表面和裂纹的运动和行为起着重要的调控作用。
分子力学和动力学的分子动力学模拟

分子力学和动力学的分子动力学模拟分子动力学模拟是一种计算模拟方法,可用于研究复杂的分子系统。
在这种模拟中,系统的各种物理和化学性质均可在数学上描述出来,并使用计算机模拟出来。
分子动力学模拟主要应用于材料科学、化学、物理、生物等多个领域,并取得了很多成果。
一、分子力学分子力学是研究分子结构、构象和力学性质的一种数学模拟方法。
分子力学的研究基于牛顿力学,即研究每个分子内部原子的相对位置和相互作用力,以计算出分子体系的各种性质。
分子力学模拟主要用于预测分子结构、构象和分子性质等内容。
在分子力学模拟中,主要采用原子模型或粒子模型,使用数学方法建立分子体系的力学模型,并通过计算机模拟分子结构的形态变化和各种性质的变化。
分子动力学模拟可以计算物质的各种力学性质,如粘度、流动性质、热扩散系数等。
二、分子动力学分子动力学是关于分子的运动学和力学的序列计算的数值模拟方法。
在分子动力学模拟中,通过对分子的空间位置、速度、加速度等物理量进行计算,以模拟分子的运动轨迹和相互作用,从而得到分子系统的各种性质。
分子动力学模拟是研究异质分子体系中原子或分子间相互作用的力学运动方式的一种计算方法。
在这种模拟中,分子被理解为是由原子和键组成的,它们之间相互作用的方式和运动规律都可以通过计算机模拟得到。
三、分子动力学模拟方法分子动力学模拟的基本思想是:根据外部场的作用,计算某一时刻的力,进而计算某一时刻的速度和位置信息。
模拟过程中,需要采用一定的算法和公式,并完善计算过程的细节,使计算结果更加准确。
分子动力学模拟方法主要有三大部分:模拟系统构建部分、力场计算部分和数值模拟部分。
在模拟系统构建部分,需要对模拟的分子体系进行构建和压缩,并对体系进行初始化。
在力场计算部分,需要选择恰当的势函数,并计算各个位点上的受力情况。
在数值模拟部分,需要选择恰当的时间步长,使用恰当的算法进行计算,并输出各个周期的动力学数据。
四、分子动力学模拟技术应用分子动力学模拟技术广泛应用于新材料的研究、生物化学、纳米材料、生物医药等领域。
分子动力学模拟在材料科学中的应用

分子动力学模拟在材料科学中的应用在材料科学领域,研究材料的性能、结构和行为对于推动科技进步和创新至关重要。
分子动力学模拟作为一种强大的研究工具,正发挥着越来越重要的作用。
它为我们深入理解材料的微观世界提供了独特的视角,帮助科学家们在原子和分子水平上揭示材料的奥秘。
分子动力学模拟的基本原理是基于经典力学,通过对大量粒子的运动方程进行数值求解,来模拟材料在一定条件下的动态演化过程。
在这个过程中,每个粒子都被视为具有一定质量和相互作用的质点,它们的运动受到牛顿运动定律的支配。
通过计算粒子之间的相互作用力,如化学键、范德华力等,进而得到粒子的加速度和速度,从而预测它们在不同时间步长下的位置和状态。
那么,分子动力学模拟在材料科学中有哪些具体的应用呢?首先,它在研究材料的力学性能方面表现出色。
比如,通过模拟可以预测材料的强度、硬度、韧性等力学参数。
以金属材料为例,我们可以模拟金属晶体中的原子排列和运动,研究位错的产生、运动和相互作用,从而深入理解金属的塑性变形机制。
这对于设计和开发具有优异力学性能的新型金属材料具有重要的指导意义。
其次,在研究材料的热学性能方面,分子动力学模拟也发挥着关键作用。
它可以帮助我们了解材料的热导率、比热容等热学参数。
例如,对于纳米材料,由于其尺寸效应,热学性能往往与宏观材料有很大的不同。
通过分子动力学模拟,我们能够揭示纳米材料中热传递的微观机制,为设计高效的纳米热电器件和热管理材料提供理论依据。
再者,分子动力学模拟在研究材料的扩散和相变过程中也具有不可替代的优势。
比如,在研究合金中的元素扩散时,我们可以直观地观察到原子的迁移路径和扩散速率,从而优化合金的成分和工艺。
在相变研究中,如从固态到液态的相变,或者从一种晶体结构到另一种晶体结构的相变,模拟能够清晰地展示相变过程中的原子重排和结构变化,帮助我们深入理解相变的热力学和动力学机制。
此外,分子动力学模拟还在研究材料的表面和界面特性方面有着广泛的应用。
分子动力学模拟h原子与si的表面相互作用

分子动力学模拟h原子与si的表面相互作用分子动力学模拟可以用来研究分子之间的相互作用,包括分子与表面之间的相互作用。
下面是一种可能的模拟方法:
选择合适的分子力场,例如经典的Lennard-Jones势函数,来描述H 原子与Si表面之间的相互作用。
定义系统边界和温度,以及H原子和Si表面的初始位置和速度。
使用分子动力学算法,如Verlet算法或Leapfrog算法,计算系统在时间上的演化,包括原子的位移和速度的更新。
在模拟过程中,考虑表面的周期性边界条件,以便原子可以在表面上自由运动,并周期性地穿过表面。
在模拟过程中,记录H原子与Si表面之间的相互作用能量和力,以及H原子在表面上的轨迹和速度分布等信息。
根据模拟结果,分析H原子在Si表面上的扩散和吸附行为,以及表面结构对原子的影响。
通过对模拟参数的调整,比如温度和表面结构的改变,来研究不同条
件下H原子与Si表面之间的相互作用。
基于分子动力学模拟的材料界面性质研究
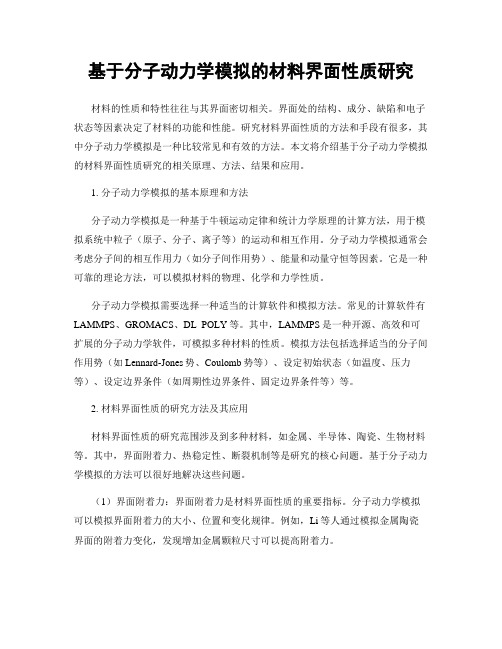
基于分子动力学模拟的材料界面性质研究材料的性质和特性往往与其界面密切相关。
界面处的结构、成分、缺陷和电子状态等因素决定了材料的功能和性能。
研究材料界面性质的方法和手段有很多,其中分子动力学模拟是一种比较常见和有效的方法。
本文将介绍基于分子动力学模拟的材料界面性质研究的相关原理、方法、结果和应用。
1. 分子动力学模拟的基本原理和方法分子动力学模拟是一种基于牛顿运动定律和统计力学原理的计算方法,用于模拟系统中粒子(原子、分子、离子等)的运动和相互作用。
分子动力学模拟通常会考虑分子间的相互作用力(如分子间作用势)、能量和动量守恒等因素。
它是一种可靠的理论方法,可以模拟材料的物理、化学和力学性质。
分子动力学模拟需要选择一种适当的计算软件和模拟方法。
常见的计算软件有LAMMPS、GROMACS、DL_POLY等。
其中,LAMMPS是一种开源、高效和可扩展的分子动力学软件,可模拟多种材料的性质。
模拟方法包括选择适当的分子间作用势(如Lennard-Jones势、Coulomb势等)、设定初始状态(如温度、压力等)、设定边界条件(如周期性边界条件、固定边界条件等)等。
2. 材料界面性质的研究方法及其应用材料界面性质的研究范围涉及到多种材料,如金属、半导体、陶瓷、生物材料等。
其中,界面附着力、热稳定性、断裂机制等是研究的核心问题。
基于分子动力学模拟的方法可以很好地解决这些问题。
(1)界面附着力:界面附着力是材料界面性质的重要指标。
分子动力学模拟可以模拟界面附着力的大小、位置和变化规律。
例如,Li等人通过模拟金属陶瓷界面的附着力变化,发现增加金属颗粒尺寸可以提高附着力。
(2)热稳定性:材料界面的热稳定性是材料长期使用和稳定性的基础。
分子动力学模拟可以模拟材料界面的热稳定性,如陶瓷金属界面的热稳定性。
例如,Chu等人模拟了SiC/Ti界面的界面稳定性,发现在高温环境下,会出现TiC/TiSi2相的形成和失稳。
(3)断裂机制:材料界面的断裂机制是材料强度和韧性的主要决定因素之一。
共聚物材料界面相互作用的分子动力学模拟研究
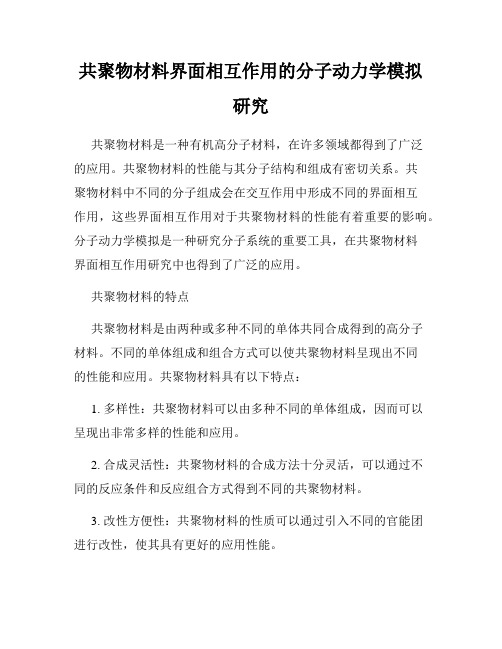
共聚物材料界面相互作用的分子动力学模拟研究共聚物材料是一种有机高分子材料,在许多领域都得到了广泛的应用。
共聚物材料的性能与其分子结构和组成有密切关系。
共聚物材料中不同的分子组成会在交互作用中形成不同的界面相互作用,这些界面相互作用对于共聚物材料的性能有着重要的影响。
分子动力学模拟是一种研究分子系统的重要工具,在共聚物材料界面相互作用研究中也得到了广泛的应用。
共聚物材料的特点共聚物材料是由两种或多种不同的单体共同合成得到的高分子材料。
不同的单体组成和组合方式可以使共聚物材料呈现出不同的性能和应用。
共聚物材料具有以下特点:1. 多样性:共聚物材料可以由多种不同的单体组成,因而可以呈现出非常多样的性能和应用。
2. 合成灵活性:共聚物材料的合成方法十分灵活,可以通过不同的反应条件和反应组合方式得到不同的共聚物材料。
3. 改性方便性:共聚物材料的性质可以通过引入不同的官能团进行改性,使其具有更好的应用性能。
4. 优良物理性能:共聚物材料的物理性能往往比普通高分子材料更加出色,包括机械性能、光学性能、电学性能等。
共聚物材料界面相互作用的研究意义共聚物材料中不同的分子组成会在交互作用中形成不同的界面相互作用,这些界面相互作用对于共聚物材料的性能有着重要的影响。
例如,PEO(Polyethylene oxide)和PS(Polystyrene)等在配合体系中会出现相分离现象。
这是因为在PEO和PS之间存在相互作用,引起了相分离现象。
如果能够深入理解PEO和PS之间的相互作用,可以有针对性地进行改性,提高其应用性能。
此外,共聚物材料的应用涵盖了许多领域,包括医药、化学、电子、材料等。
了解共聚物材料界面相互作用对于这些领域的研究和开发都有着十分重要的意义。
分子动力学模拟在研究共聚物材料界面相互作用中的应用分子动力学模拟是一种研究分子系统的重要工具,因其可以模拟分子间相互作用和运动行为等,能够提供对分子系统的深入了解。
分子动力学模拟在材料结晶机制解析中的应用

分子动力学模拟在材料结晶机制解析中的应用材料结晶是一种重要的材料加工方法,通过控制材料的晶体生长来实现材料的制备和性能优化。
随着计算机技术和模拟方法的发展,分子动力学模拟逐渐成为研究材料结晶机制的重要工具。
分子动力学模拟是一种计算模拟方法,通过数值计算分子间相互作用力和位移,模拟物质在尺度时间上的运动。
它能够在原子层面上模拟材料的性质和行为,揭示材料的微观结构和动力学过程。
在材料结晶研究中,分子动力学模拟可以提供详细的原子信息和运动轨迹,帮助揭示材料的结晶机制。
首先,分子动力学模拟可以帮助理解材料的晶体生长行为。
晶体生长是指材料从液体或气相中形成有序排列的晶体结构的过程。
通过分子动力学模拟,我们可以模拟液体或气相中的原子或分子的运动,观察其在时间和空间上的演变。
通过分子动力学模拟,我们可以研究晶体生长的影响因素,如温度、浓度、溶液成分等,进一步理解晶体生长的机制和规律。
其次,分子动力学模拟可以揭示材料的晶体核形成和演化过程。
材料的结晶始于晶体核的形成,核的数量和质量决定了晶体生长的速率和质量。
通过分子动力学模拟,我们可以模拟原子或分子在凝聚态中的聚集行为,观察晶体核的形成和演化过程。
通过研究核的形态、大小和稳定性,我们可以深入理解晶体核的形成规律和控制方法。
此外,分子动力学模拟还可以研究材料的晶体生长形貌和界面性质。
材料的晶体生长形貌对材料的性能和应用具有重要影响。
通过分子动力学模拟,我们可以模拟晶体生长的过程,观察晶体的形状、尺寸和晶面的取向。
同时,分子动力学模拟还可以研究晶体与溶液或气相界面的相互作用,揭示界面的结构和性质。
这些信息对于优化晶体生长条件、控制晶体生长形貌和改变晶界性质具有重要意义。
最后,分子动力学模拟可以预测材料的结晶方式和相变行为。
结晶方式是指物质由无序态向有序晶体结构的转变路径。
通过分子动力学模拟,我们可以预测物质的结晶方式和相变行为,如晶体的多少相和相变温度。
这对于理解材料的相变机制和优化相变材料的制备工艺具有重要意义。
材料界面的分子动力学模拟

材料界面的分子动力学模拟材料科学是一个与我们的日常生活息息相关的领域,无论是我们使用的电子设备、汽车、航空航天器还是建筑物,都离不开材料科学的贡献。
在材料界面的研究中,分子动力学模拟是一种非常重要的方法。
一、分子动力学模拟的基本原理分子动力学模拟是一种计算方法,它可以对材料系统中原子的运动进行模拟,通过计算分子之间的相互作用力和各个原子的运动轨迹,预测材料的物理性质和化学反应行为。
这种模拟方法的基本原理是牛顿力学定律,即物体受到的力等于该物体质量乘以其加速度,力和加速度之间存在着直接的关系。
根据这个理论,分子动力学模拟可以通过计算分子之间的作用力,来预测系统中原子的运动轨迹和材料的各种性质。
二、分子动力学模拟在材料界面研究中的应用在材料界面研究中,分子动力学模拟被广泛应用,来研究材料的力学性能、化学行为以及微观结构。
1. 材料的力学性能材料在力学性能方面的研究主要包括材料的强度、硬度、韧性等方面,这些性能与材料内部的结构和原子之间的相互作用密切相关。
分子动力学模拟可以通过计算材料中原子之间的相互作用,来预测材料的力学性能,并提供一些改善材料性能的策略。
2. 材料的化学行为材料的化学行为是材料科学研究的另一个重要方面,涉及到材料的反应机理、反应速率和热力学性质。
分子动力学模拟可以模拟材料中化学反应的过程,来研究材料的化学行为,并提供可靠的数据支持。
3. 材料的微观结构材料的微观结构是材料性质的基础,也是制备高性能材料的重要前提。
分子动力学模拟可以帮助研究人员观察材料的微观结构,包括原子的排列方式、晶格结构和界面等方面,理解材料的性质和行为。
三、分子动力学模拟的发展趋势随着信息技术的快速发展,分子动力学模拟已经成为材料研究中不可或缺的工具之一。
现代计算机技术的进步为分子动力学模拟的应用提供了更大的空间,未来分子动力学模拟将有望实现更高的分辨率和更完备的模拟方法。
1. 人工智能与分子动力学模拟的结合人工智能已经在材料科学领域得到广泛应用,将人工智能技术与分子动力学模拟相结合,可以进一步提高模拟精度和效率。
α-Ti中位错运动及相互作用的分子动力学模拟的开题报告
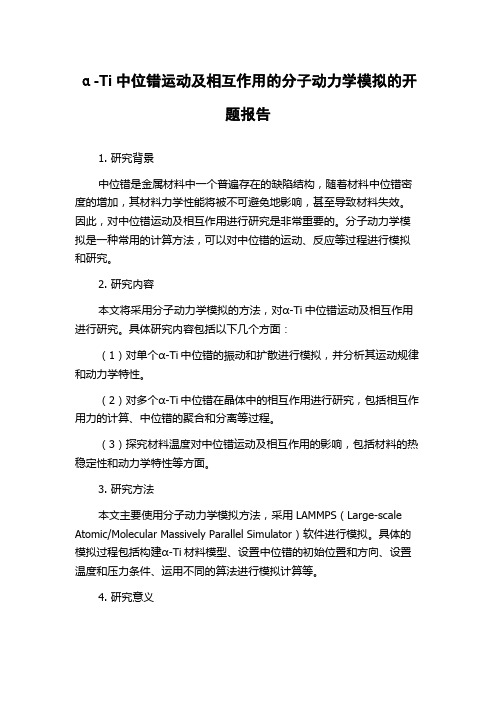
α-Ti中位错运动及相互作用的分子动力学模拟的开
题报告
1. 研究背景
中位错是金属材料中一个普遍存在的缺陷结构,随着材料中位错密度的增加,其材料力学性能将被不可避免地影响,甚至导致材料失效。
因此,对中位错运动及相互作用进行研究是非常重要的。
分子动力学模拟是一种常用的计算方法,可以对中位错的运动、反应等过程进行模拟和研究。
2. 研究内容
本文将采用分子动力学模拟的方法,对α-Ti中位错运动及相互作用进行研究。
具体研究内容包括以下几个方面:
(1)对单个α-Ti中位错的振动和扩散进行模拟,并分析其运动规律和动力学特性。
(2)对多个α-Ti中位错在晶体中的相互作用进行研究,包括相互作用力的计算、中位错的聚合和分离等过程。
(3)探究材料温度对中位错运动及相互作用的影响,包括材料的热稳定性和动力学特性等方面。
3. 研究方法
本文主要使用分子动力学模拟方法,采用LAMMPS(Large-scale Atomic/Molecular Massively Parallel Simulator)软件进行模拟。
具体的模拟过程包括构建α-Ti材料模型、设置中位错的初始位置和方向、设置温度和压力条件、运用不同的算法进行模拟计算等。
4. 研究意义
本文的研究将对α-Ti中位错的运动和相互作用规律进行深入探究,有助于进一步理解中位错参与材料力学性能的机理,为材料设计和制备提供一定的理论基础。
si晶体中点缺陷和位错交互作用的分子动力学研究

si晶体中点缺陷和位错交互作用的分子动力学研究
Si 作为宽带隙半导体,其被广泛应用于电子电路中,但是晶体中的缺陷也会降低其性能。
研究Si晶体中点缺陷和位错的作用对于改善器件性能具有重要意义。
在过去几十年中,以分子动力学(MD)作为最有效的手段来研究点缺陷和位错交互作用,其结果表明引起Si晶体中ionicity缺陷吸附氧原子。
在Si晶体中,点缺陷会影响它们周围的原子结构,影响力学性质;位错可以大幅度地改变它们周围的原子结构,并对晶体的性质产生关键作用。
分子动力学方法在研究点缺陷和位错交互作用时具有很大的优势,它能够准确地反映晶体原子结构和力学性质的变化。
近期的研究表明,分子动力学模拟可以解释不同类型的位错及其作用对点缺陷的影响。
在轰击缺陷周围的晶格原子时,不同类型的位错可以改变缺陷的能量状态,有助于氧离子的吸附和氧原子的排除。
另一方面,利用分子动力学方法研究缺陷与位错之间的作用也是重要的。
结果表明,位错可以介导半导体中点缺陷的活性、变化速率和作用力学性质的变化。
例如,它们可以控制缺陷表面上氧原子的吸附能,并可能改变缺陷的热力学性质。
有趣的是,位错不受缺陷的影响,但却可以影响晶体中的缺陷。
综上所述,分子动力学是研究Si晶体中点缺陷和位错作用的有效方法。
它可以准确描述缺陷和位错与晶体原子结构之间的相互作用,以及它们之间相互影响的力学性质,为改善器件性能提供了有益的信息。
未来,分子动力学研究将继续深入了解缺陷-位错交互作用,以提高半导体元件的性能。
位错能量的算法

位错能量的算法位错能量的算法是一种用于计算材料中位错能量的方法。
位错是材料中晶体结构中的一种缺陷,它是晶体中原子排列顺序的偏离。
位错能量是位错的形成和移动所需的能量,它对材料的力学性质和变形行为起着重要作用。
了解和计算位错能量可以帮助人们更好地理解材料的力学行为和变形机制,对材料设计和性能改进具有重要意义。
位错能量的计算可以通过原子尺度模拟方法进行。
通常,人们使用分子动力学模拟或离子力学模拟来模拟材料中的位错和位错运动。
这些模拟方法可以根据原子间相互作用力场和位错的移动规律,计算出位错形成和移动所需的能量。
具体而言,分子动力学模拟通过求解牛顿运动方程,模拟材料中原子的运动和相互作用,从而得到位错的能量。
离子力学模拟则是通过构建原子间相互作用势能函数,通过优化位错的结构和能量,来计算位错能量。
在位错能量的计算中,需要考虑位错的类型和形态。
不同类型的位错具有不同的结构和能量,因此计算方法也有所不同。
常见的位错类型包括位错线、位错环和位错面。
位错线是晶体中原子排列顺序的偏移线,位错环是位错线的闭合形式,位错面则是晶体中原子排列顺序的偏移面。
这些位错类型的能量计算方法可以根据其结构特征进行选择和优化。
位错能量的计算结果可以用来预测材料的变形行为和力学性能。
位错能量越高,材料的抗变形性能越好;位错能量越低,材料的变形性能越差。
因此,通过计算位错能量,人们可以评估材料的变形能力和强度,为材料设计和应用提供指导和参考。
除了计算位错能量,人们还可以通过实验方法来测量位错能量。
常用的实验方法包括透射电子显微镜和原子力显微镜等。
透射电子显微镜可以通过电子束的透射和散射来观察和测量材料中的位错结构和能量。
原子力显微镜则是通过探针和样品之间的相互作用力,来测量位错的结构和能量。
实验方法可以与计算方法相互验证,提高位错能量的计算和测量的准确性和可靠性。
位错能量的算法是一种用于计算材料中位错能量的方法。
通过计算位错能量,可以帮助人们更好地理解材料的力学行为和变形机制,为材料设计和性能改进提供指导和参考。
lammps案例
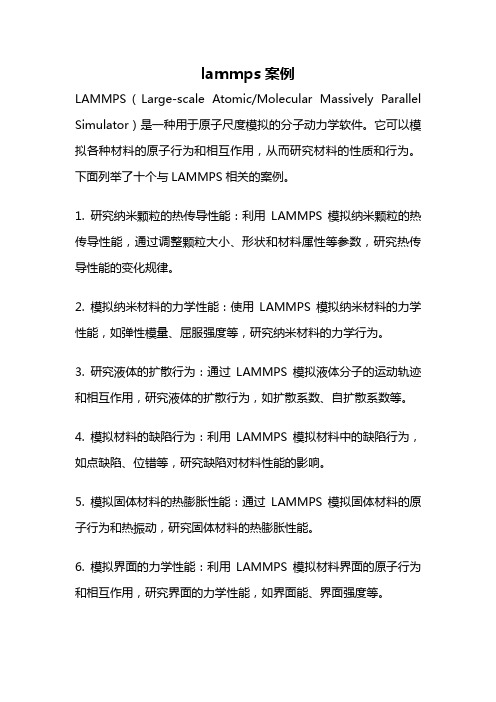
lammps案例LAMMPS(Large-scale Atomic/Molecular Massively Parallel Simulator)是一种用于原子尺度模拟的分子动力学软件。
它可以模拟各种材料的原子行为和相互作用,从而研究材料的性质和行为。
下面列举了十个与LAMMPS相关的案例。
1. 研究纳米颗粒的热传导性能:利用LAMMPS模拟纳米颗粒的热传导性能,通过调整颗粒大小、形状和材料属性等参数,研究热传导性能的变化规律。
2. 模拟纳米材料的力学性能:使用LAMMPS模拟纳米材料的力学性能,如弹性模量、屈服强度等,研究纳米材料的力学行为。
3. 研究液体的扩散行为:通过LAMMPS模拟液体分子的运动轨迹和相互作用,研究液体的扩散行为,如扩散系数、自扩散系数等。
4. 模拟材料的缺陷行为:利用LAMMPS模拟材料中的缺陷行为,如点缺陷、位错等,研究缺陷对材料性能的影响。
5. 模拟固体材料的热膨胀性能:通过LAMMPS模拟固体材料的原子行为和热振动,研究固体材料的热膨胀性能。
6. 模拟界面的力学性能:利用LAMMPS模拟材料界面的原子行为和相互作用,研究界面的力学性能,如界面能、界面强度等。
7. 研究材料的相变行为:通过LAMMPS模拟材料的原子行为和相互作用,研究材料的相变行为,如熔化、凝固等。
8. 模拟电子输运行为:利用LAMMPS模拟材料中电子的输运行为,研究电子的迁移率、电导率等。
9. 研究纳米材料的自组装行为:通过LAMMPS模拟纳米材料的原子行为和相互作用,研究纳米材料的自组装行为,如纳米颗粒的聚集、纳米管的形成等。
10. 模拟材料的化学反应:利用LAMMPS模拟材料中的原子行为和相互作用,研究材料的化学反应行为,如材料的氧化、还原等。
通过以上案例,可以看出LAMMPS在材料科学、物理化学等领域中的广泛应用。
它的高度可定制性和可扩展性使得研究者可以根据自己的需求进行模拟和分析,从而深入理解材料的性质和行为。
- 1、下载文档前请自行甄别文档内容的完整性,平台不提供额外的编辑、内容补充、找答案等附加服务。
- 2、"仅部分预览"的文档,不可在线预览部分如存在完整性等问题,可反馈申请退款(可完整预览的文档不适用该条件!)。
- 3、如文档侵犯您的权益,请联系客服反馈,我们会尽快为您处理(人工客服工作时间:9:00-18:30)。
学校代码 10530 学 号 200910081121 分 类 号 密 级硕 士 学 位 论 文分子动力学模拟位错和界面的相互作用学 位 申 请 人 周银库指 导 教 师 陈尚达 副教授学 院 名 称 材料与光电物理学院学 科 专 业 材料科学与工程研 究 方 向 金属薄膜的力学性能二零一二年五月Molecular dynamics simulations of interaction between dislocations and interfacesCandidate Yinku ZhouSupervisor Shangda Chen (Associate Professor)College Faculty of Materials, Optoelectronics and PhysicsProgram Material Science and EngineeringSpecialization Mechanical Properties of metal filmDegree Engineering MasterUniversity Xiangtan UniversityDate May, 2012湘潭大学学位论文原创性声明本人郑重声明:所呈交的论文是本人在导师的指导下独立进行研究所取得的研究成果。
除了文中特别加以标注引用的内容外,本论文不包含任何其他个人或集体已经发表或撰写的成果作品。
对本文的研究做出重要贡献的个人和集体,均已在文中以明确方式标明。
本人完全意识到本声明的法律后果由本人承担。
作者签名:日期:年月日学位论文版权使用授权书本学位论文作者完全了解学校有关保留、使用学位论文的规定,同意学校保留并向国家有关部门或机构送交论文的复印件和电子版,允许论文被查阅和借阅。
本人授权湘潭大学可以将本学位论文的全部或部分内容编入有关数据库进行检索,可以采用影印、缩印或扫描等复制手段保存和汇编本学位论文。
涉密论文按学校规定处理。
作者签名:日期:年月日导师签名:日期:年月日摘要纳米尺度的金属多层膜在屈服应力、塑性、抗腐蚀性能等方面具有特殊的性能。
目前它已被广泛应用于航空航天、机械制造、电子技术、光学工程及计算机工程等各个领域。
而在薄膜材料的应用过程中,薄膜的使用寿命和可靠性是人们普遍关注的焦点问题。
界面的结合性能是影响多层膜寿命和可靠性的关键指标,而位错和界面的相互作用机理决定着界面的结合性能,即位错和界面的相互作用机理在薄膜的使用寿命和可靠性方面扮演着关键角色。
因此对位错和界面的相互作用机理的研究就显得特别有价值和意义。
随着高性能计算机的发展,原子模拟已成为材料性能预测与设计方面一种有效的方法。
本文用三维分子动力学方法研究了位错和界面的相互作用机理,具体如下:首先,用分子动力学方法研究了侧向拉伸载荷下位错从bcc-Fe/Ni界面的形核和发射过程。
弛豫后,在Fe(0 0 1)/Ni(0 0 1)和Fe(0 0 1)/Ni(1 1 1)界面观察到无序的失配位错网络,Fe(0 0 1)/Ni(1 1 0)界面观察到长方形的失配位错网络。
研究了晶体取向对Fe/Ni 双层膜拉伸性能的影响。
不同取向的对比发现Fe(0 0 1)/Ni(1 1 0)系统的屈服强度最低。
和Fe薄膜进行了对比,发现Fe/Ni双层膜系统的塑性高于Fe薄膜的,而屈服强度低于Fe薄膜的。
模拟结果显示,界面是位错的发射源,滑移位错从界面的失配位错线形核和发射。
同时界面也会阻碍位错运动,随着拉伸的进行,Fe层中越来越多的位错被塞积在界面处,当到达到临界值时,迫使位错穿过Fe/Ni界面,从Fe层到Ni层。
在Fe基体中位错主要在{1 0 1}面滑移,而在Ni中主要在{1 1 1}面滑移。
其次,用分子动力学模拟了单轴拉伸载荷下不同扭转角的Cu(001)/Ni(001)界面的结合性能。
模拟结果显示,当扭转角小于15.124度时,界面形成方格状的失配位错网络,界面失配位错网络的密度随着扭转角的增加而增加。
当扭转角大于15.124度时,在界面形成面缺陷。
模拟发现界面构型对Cu/Ni系统的界面强度有着非常显著的影响。
随着扭转角的增加屈服应力首先减小,直到扭转角为5.906度的最小值,然后增加,当其达到扭转角为15.124度的最大值后,又开始减小,最后当扭转角约大于20度,屈服应力几乎趋于一稳定的值。
关键词:分子动力学;界面;滑移位错;失配位错IABSTRACTNanoscale multilayered composites often possess extraordinary mechanical properties in terms of yield stress, ductility, and wear resistant. Now it has been widely used in aerospace, mechanical manufacturing, electronics, optical engineering and computer engineering fields. In the applied process of the thin film materials, people commonly focus on the reliability and service life of the thin films. The binding property between the thin film and the substrate is a key indicator of metallic multilayers’the reliability and service life, the interaction mechanisms between dislocations and interfaces dominate the binding properties of the interfaces. Therefore, the interaction mechanism between dislocations and interfaces plays a vital role in the field of the reliability and service life of the thin films.So it is an interesting and valuable thing to understand the interaction mechanisms between dislocations and interfaces. With the development of high-performance computer, atomic simulations have become an effective method in the field of material properties forecast and design. In the present work, we have studied the interaction between dislocations and interfaces with 3D Molecular Dynamic Simulations.Firstly, molecular dynamics simulations were carried out to investigate the nucleation and emission of dislocations from an interface in a bcc-Fe/Ni bilayer subjected to transverse loading. After relaxation, disordered types of dislocations were observed at both Fe(0 0 1)/Ni(0 0 1) and Fe(0 0 1)/Ni(1 1 1) interfaces, and rectangular dislocations types at Fe(0 0 1)/Ni(1 1 0) interface. The orientation effect on the mechanical properties of a Fe/Ni bilayer system was investigated. The yield stress of the Fe(0 0 1)/Ni(1 1 0) system abtained is lowest. We also found that the yield stress of pure iron nanofilm was higher than that of a Fe/Ni bilayer system, and the ductility was lower than that of a Fe/Ni bilayer system for given temperature and strain rate. The simulation results obtained also show that the misfit dislocations at Fe/Ni interface acted as a source to nucleation and emission of glide dislocations. Glide dislocations nucleation and emission from misfit dislocation line at Fe/Ni interface. The existence of misfit dislocations and the lattice mismatch can also act as barriers to dislocation motion and transmission across the interface. More dislocations in Fe have been arrested at the Fe/Ni interface, which provides sufficient stress for dislocations to transmit from Fe to Ni. Glide dislocations mainly occurred on {1 0 1} plane in Fe layer of FeNi bilayer, and {1 1 1} plane in Ni layer.Secondly, molecular dynamics simulations were carried out to study the mechanicalIIproperties of Cu(001)/Ni(001) interface boundaries with different twist angles subjected to uniaxial loading. The results obtained revealed that square misfit dislocations networks can be observed when the twist angle was lower than 15.124︒, and the density of misfit dislocations increased with increasing twist angle. Face defects were formed when the twist angle was higher than 15.124︒. It has been found that the interface configuration had a significant effect on the interface strength of the Cu/Ni system. The yield stress was found to decrease first with increasing twist angle and it reached its lowest value at 5.906︒ twist angle. Subsequently, it increased with increasing twist angle till it reached its highest value at 15.124︒ of the latter; it then decreased again and finally became almost constant when the twist angle was larger than approximately 20︒ .Key Words: Molecular Dynamics; Interface; Glide dislocation; Misfit dislocationIII目录第1章引言 (1)1.1 薄膜概述 (1)1.2 界面概述 (1)1.3晶体位错相关理论概述 (4)1.4晶体界面的分子动力学研究现状 (6)1.5本文的研究思路、目的及意义 (7)第2章分子动力学方法 (9)2.1 引言 (9)2.2基本原理 (10)2.2.1 积分方法 (10)2.2.2 原子间的相互作用势 (11)2.3 边界条件 (13)2.4 温度、压力控制方法 (14)2.4.1 控温方法 (14)2.4.2 控压方法 (15)2.5 分析方法 (16)2.5.1 中心对称参数(centrosymmetry parameter) (16)2.5.2 径向分布函数 (17)2.6 模拟软件与可视化 (17)2.7 小结 (18)第3章 Fe/Ni双层膜系统中位错和界面的相互作用 (19)3.1 模拟方法 (19)3.2 结果及讨论 (20)3.2.1 弛豫后沿厚度方向的势能分布 (20)3.2.2初始界面失配位错结构 (21)3.2.3 晶体取向的影响 (22)3.2.4 bcc-Fe薄膜的变形机理 (23)3.2.5 bcc-Fe层的滑移位错 (24)3.2.6 Fe/Ni双层膜的变形机理 (26)3.2.7 Ni层厚度的影响 (29)3.2.8 温度的影响 (30)IV3.2.9 应变率的影响 (30)3.3 小结 (31)第4章 Cu(001)/Ni(001)扭转界面的结合强度 (33)4.1 模拟模型和方法 (33)4.2 结果与讨论 (35)4.2.1 初始失配位错构型 (35)4.2.2 Cu(001)/Ni(001)系统的变形机理 (36)4.2.3 Cu层中滑移位错的变形机理 (37)4.3 小结 (39)第5章总结与展望 (41)5.1 工作总结 (41)5.2 工作展望 (41)参考文献 (43)致谢 (48)个人简历、攻读硕士学位期间发表的论文 (49)V湘潭大学硕士毕业论文第1章引言1.1 薄膜概述薄膜材料通常是指在二维方向上的尺度比另一维方向大很多,在其基体材料上通过化学或物理等方法制备另外一层材料,以达到某种特定功能,如提高断裂韧性、增加塑性、增加使用寿命, 以及美观度等等。