CXSL32-20资料下载
乐鑫信息科技 ESP32

ESP32S2WROOM ESP32S2WROOMI技术规格书2.4GHz WiFi(802.11b/g/n)模组内置ESP32S2系列芯片(版本0),Xtensa ®单核32位LX7微处理器4MB flash37个GPIO ,丰富的外设板载PCB 天线或外部天线连接器ESP32S2WROOMI版本1.3乐鑫信息科技版权©2022不推荐用于新设计(NR ND )1模组概述1.1特性CPU和片上存储器•内置ESP32-S2芯片,Xtensa®单核32位LX7微处理器,支持高达240MHz的时钟频率•128KB ROM•320KB SRAM•16KB RTC SRAMWiFi•802.11b/g/n•802.11n模式下数据速率高达150Mbps•帧聚合(TX/RX A-MPDU,RX A-MSDU)•0.4µs保护间隔•工作信道中心频率范围:2412~2484MHz外设•GPIO、SPI、UART、I2C、I2S、LCD接口、Camera接口、IR、脉冲计数器、LED PWM、TWAI®(兼容ISO11898-1,即CAN规范2.0)、全速USBOTG、ADC、DAC、触摸传感器、温度传感器模组集成元件•40MHz集成晶振•4MB SPI flash天线选型•板载PCB天线(ESP32-S2-WROOM)•通过连接器连接外部天线(ESP32-S2-WROOM-I)工作条件•工作电压/供电电压:3.0~3.6V•工作环境温度:–40~85°C认证•RF认证:见ESP32-S2-WROOM和ESP32-S2-WROOM-I 证书•环保认证:RoHS/REACH测试•HTOL/HTSL/uHAST/TCT/ESD1.2描述ESP32-S2-WROOM和ESP32-S2-WROOM-I是通用型Wi-Fi MCU模组,功能强大,具有丰富的外设接口,可用于可穿戴电子设备、智能家居等场景。
LC320WXE-SBV2_Ver1.0

SPECIFICATION FOR
APPROVAL
LC320WXE
( ) Preliminary Specification ( ● ) Final Specification
Title
BUYER MODEL
HAIER
32.0” WXGA TFT LCD
SUPPLIER
Operating Ambient Humidity
Storage Humidity
VLCD
VOP TOP TST HOP HST
Value
Min
Max
-0.3
+14.0
600
1300
0
+50
-20
+60
10
90
10
90
A-3/14 Changed pallet ass’y spec.
A-5/14 Changed name in the LCM label spec. (SBV1→SBV2)
A-6/14
Changed pallet label spec. and name in the pallet label (SBV1→SBV2)
CN2, 3Pin, 10 Lamps/@65 mA CN3, 3Pin, 10 Lamps/@65 mA
Back light Assembly (10EEFL)
31.51 inches(800.4mm) diagonal 760.0 mm(H) x 450.0 mm(V) x 36.0 mm(D) (Typ.) 510.75㎛ x 170.25㎛ x RGB 1366 horiz. by 768 vert. pixels RGB horizontal stripe arrangement 8bit, 16,7 M colors 350 cd/m2 (Center 1 point) (Typ.) Viewing angle free ( R/L 178(Min.), U/D 178(Min.)) Total 73.7Watt (Typ.) (Logic=3.7 W, Back Light= 70W @ with Inverter) 4,000g(Typ.) Transmissive mode, normally black Hard coating(3H), anti-glare treatment of the front polarizer (Haze 13%)
Sophos APX 320X 操作指南说明书

Operating Instructions APX 320XForewardWe are pleased to welcome you as a new Sophos APX Series customer.Sophos APX Series access points are high performance wireless products using the latest 802.11ac Wave 2 technology for a best-in-class user experience. The APX Series models can be easily managed in Sophos Central, our cloud-based security management platform. All you need to do is set up a Sophos Central account and plug in the device anywhere in your network. The access point will find the cloud-based controller automatically and become operable within seconds.These operating instructions will help you set up your Sophos Central account, install and configure your Sophos APX Series access point and also provide detailed technical specifications. In addition, please also see the following documents that contain useful information on safety, regulatory compliance, and configuration options:ÌSophos APX Series Safety Instructions and Regulatory InformationÌSophos APX 320X Quick Start GuideThe instructions must be read carefully prior to using the device and should be kept in a safe place. You can download all user manuals and additional documentation from the Sophos Knowledgebase under /en-us/support/knowledgebase.aspx or from /get-started-ap.Security symbolsThe following symbol and its meaning appears in the Quick Start Guide, Safety Instructions and in these Operating Instructions.Caution and Important Note. If these notes are not correctly observed:ÌThis is dangerous to life and the environmentÌThe access point may be damagedÌThe functions of the access point will be no longer guaranteedÌSophos shall not be liable for damages arising from afailure to comply with the Safety InstructionsDesigned useThe access point must be installed pursuant to the current installation notes. Otherwise failure-free and safe operation cannot be guaranteed. The EU declaration of conformity is available upon request from the following address:Sophos Technology GmbHGustav-Stresemann-Ring 165189 WiesbadenGermanyOperating elements and connections N type connector for 2.4/5 GHz antenna (Radio 1)N type connector for 2.4/5 GHz antenna(Radio 0)N type connector for 2.4/5 GHz antenna (Radio 1)N type connector for 2.4/5 GHz antenna(Radio 0)Forge posts for mounting plate connection Gore vent LED RJ45 connector/Reset button Grounding wireconnectorComponent descriptionsLEDs* Your AP should recover from this state after a maximum of 5 minutes.Connection and configurationYour access point can be managed by a wireless controller located in Sophos Central. The initial connection of your access point to your network and the wireless controller is described in the APX Quick Start Guide which was shipped with your device or is available under /get-started-ap.For the access point to communicate with Sophos Central servers the following ports will need to be open on your firewall:Ì443 (HTTPS)Ì80 (HTTP)Ì123 (NTP)After successful connection you can start your initial configuration.Setting up your access point in Sophos CentralYou will need a Sophos Central account to manage your access points from Sophos Central. Please go to https:// to sign in under your account or create a new account.After signing in select Wireless from the popup screen or click on Wireless in the left navigation to get started.Follow the Onboarding Wizard to register your access point.For more information, please see the Sophos Central Admin Help.Setting up your access point in XG FirewallPlease note: APX 320X is not supported on XG or XGS Firewalls.Reboot and resetYour access point can be rebooted with the installed configuration or reset to the factory default configuration depending on how long you press and hold the reset button. Reboot with current image and configuration1. Press reset button.2. Release reset button.3. AP reboots (LED will go off, then will turn to solid green).Reboot with current image and clear configuration1. Press and hold reset button.2. AP reboots (LED will go off and then switch to green briefly).3. LED will turn solid red for 5 sec. You can still cancel the configuration clearanceprocess by releasing the reset button before the LED starts blinking.4. LED will blink red (configuration will be cleared).5. Release reset button.6. AP reboots with factory default settings.Technical specifications* Not available in the countries listed here: https:///support/s/article/KB-000039850 ** For the countries listed here: https:///support/s/article/KB-000039850Radiation patterns2.4 GHz BandH-plane V-plane—2400 (MHz) —2450 (MHz) —2500 (MHz)5 GHz BandH-plane V-plane—4900 (MHz) —5150 (MHz) —5350 (MHz)—5475 (MHz)—5725 (MHz)—5875 (MHz)Optional Sector / Directional AntennasTechnical specifications120° Sector AntennaFrequency range2400~2500 MHz5150~5850 MHzPort V-pol. / H-pol.V-pol. / H-pol.Antenna Gain10.6~10.8 dBi) / 10.0~11.4 dBi 12.5~13.1 dBi / 11.6~12.9 dBi HPBW / Horizontal76~77 deg / 63~66 deg40~61 deg / 52~76 deg HPBW / Vertical24~25 deg / 26~28 deg11~13 deg / 11~13 deg Isolation20 dBImpedance50 OhmsConnector N JackDimensions320 x 200 x 20.5 mm (12.6 x 7.87 x 0.81 inches)(Height x Width x Depth)30° Directional AntennaFrequency range2400~2500 MHz5150~5850 MHzPort V-pol. / H-pol.V-pol. / H-pol.Antenna Gain11.6~11.8 dBi) / 11.6~12.0 dBi 10.6~11.0 dBi / 10.4~11.5 dBi HPBW / Horizontal36~37 deg / 35~36 deg33~35 deg / 26~36 deg HPBW / Vertical34~35 deg / 36~38 deg32~39 deg / 30~41 deg Isolation20 dBImpedance50 OhmsConnector N JackDimensions320 x 200 x 20.5 mm (12.6 x 7.87 x 0.81 inches)(Height x Width x Depth)Radiation patterns Sector Antenna – Horizontal Polarization 2.4 GHz BandH-plane V-plane—2400 (MHz) —2450 (MHz) —2500 (MHz)5 GHz BandH-plane V-plane—4900 (MHz) —5150 (MHz) —5350 (MHz)—5475 (MHz)—5725 (MHz)—5875 (MHz)Radiation patterns Sector Antenna – Vertical Polarization 2.4 GHz BandH-plane V-plane—2400 (MHz) —2450 (MHz) —2500 (MHz)5 GHz BandH-plane V-plane—4900 (MHz) —5150 (MHz) —5350 (MHz)—5475 (MHz)—5725 (MHz)—5875 (MHz)H-plane V-plane—2400 (MHz) —2450 (MHz) —2500 (MHz)5 GHz BandH-plane V-plane—4900 (MHz) —5150 (MHz) —5350 (MHz)—5475 (MHz)—5725 (MHz)—5875 (MHz)H-plane V-plane—2400 (MHz) —2450 (MHz) —2500 (MHz)5 GHz BandH-plane V-plane—4900 (MHz) —5150 (MHz) —5350 (MHz)—5475 (MHz)—5725 (MHz)—5875 (MHz)Mounting instructionsThere are various mounting options available allowing you to hang your access point on the wall or mount it on a pole. Both options require the use of the mounting bracket which is shipped with your access point. The following sections provide detailed instructions on each of these options.Mounting bracketMounting holesVertical orientation mounting clamp slots Horizontal orientation mounting clamp slotsMountingattachment slotsMount plateattachment screwWall mount1. Use the mounting bracket to mark the screw mounting positions on the wall.2. Attach the access point to the bracket by hanging the 4 forge postsinto the attachment slots of the bracket and pressing it down.3. Tighten the attachment screw to fix the access point to the bracket.1.3.Tighten the attachment screwPole mount1. Attach the two metal clamps to the back of the mounting bracket using thevertical or horizontal mounting slots (according to the desired orientation).2. Hold the bracket against the pole and tighten the metal clamps.3. Attach the access point to the bracket by hanging the 4 forge postsinto the attachment slots of the bracket and pressing it down.4. Tighten the attachment screw to fix the access point to the bracket1. 2.3. 4.Sector / Directional Antenna Mounting Instructions1. Attach the articulating mount to the back of the Sector /Directional antenna using four of the supplied M6 nuts.2. Fix the T-form bracket to the pole by using the two supplied stainless steel hoseclamps.Please note: The clamps can be used for poles of 35-80 mm (1.5-3 inches) diameter.3. Fix the articulating mount to the T-form bracket by using thesupplied M8x40 bolts, nut, spring washer and washer.4.Direct the antenna upward or downward (max. angle is 27°) and fix it into place.1.27°27°Use a No. 12 hexagonal wrench to lock the M8 nut.4.M8x40 ScrewBoltsT-form BracketWasherSpring WasherM8 Nut3.2.Connect the Sector / Directional Antenna to the Access Point Connect the antenna to your APX 320X access point by using the supplied cables. You can use your sector/directional antenna either in combination with the standard omni-directional antennas or with another sector/ directional antenna.Choose the appropriate connection for the scenario which best fits your use case - as shown in the table below.NOTE: If you use the sector/directional antenna with the APX 320X in some countries, the use of Radio-1 may not be possible. Regulatory restrictions in some countries prohibit the use of low band 5 GHz channels which do not support DFS in outdoor environments. Therefore, Radio-1 cannot be configured when used in the countries listed here: https:// /support/s/article/KB-000039850. In those countries, this model will function as a single radio device (2.4 OR 5 GHz), your antennas should be connected to Radio-0 only, and concurrent use of the sector/directional and omni-directional antennas is not possible.a. b. c.Configure Sector / Directional Antenna Software SettingsOnce the external antenna is connected, please select the corresponding antenna settings in your Sophos Central Wireless admin account. Once selected and the configuration synched, the AP reboots and the correct power values will be set. WARNING: Failure to configure the correct antenna settings may place the AP outsideof regulatory limits. The administrator is responsible for ensuring this configuration is correct.Operating Instructions APX 320X© Copyright 2020-22. Sophos Ltd. All rights reserved.United Kingdom and Worldwide Sales Tel: +44 (0)8447 671131Email: ****************North American SalesToll Free: 1-866-866-2802Email: ******************Australia and New Zealand Sales Tel: +61 2 9409 9100Email: ****************.au Asia SalesTel: +65 62244168Email: ********************。
SX32中文资料

Maximum Recurrent Peak Reverse Voltage Maximum RMS Voltage Maximum DC Blocking Voltage Maximum Average Forward Rectified Current at T L (See figure 1) Peak Forward Surge Current 8.3ms single half sine-wave superimposed on rated load (JEDEC method) Maximum Instantaneous Forward Voltage at 3.0A (Note 1) Maximum DC Reverse Current (Note 1) Ta= 25°C
3.0 2.5 2.0 1.5 1.0 0.5 0 50 60 70 80 90 100 110 120 130 140 150
O
10
SINGLE PHASE HALF WAVE 60Hz RESISTIVE OR INDUCTIVE LOAD P.C.B MOUNTED ON 0.55 X 0.55" ( 14 X 14mm ) COPPER PAD AREAS
SYMBOLS
SX32 20.0 14.0 20.0
SX33 30.0 21.0 30.0
SX34 40.0 28.0 40.0
SX35 50.0 35.0 50.0 3.0
SX36 60.0 42.0 60.0
SX38 80.0 56.0 80.0
SX39 UNITS 90.0 71.0 90.0 V V V A
INSTANTANEOUS REVERSE CURRENT, MILAMPERES
EMC存储 CX3-20 详细安装文档

地震局项目CX3-20安装报告项目编号:王版本记录日期版本号作者备注07/03/30 V1.0王坤初稿07/03/18 V1.2王坤修订稿07/03/24 V2.0王坤提交稿目录一、工作步骤及流程 (1)二、物理连接图 (2)三、初始化CX3-20盘阵 (3)四、磁盘阵列配置 (6)五、盘阵划分步骤 (9)六、主机端软件安装 (11)七、主机连接盘阵 (13)一、工作步骤及流程序号工作条目工作内容备注1确认安装环境确认客户机房电源、机架准备到位。
2开箱验货根据到货清单验货,请客户盖章确认。
3磁盘阵列和光纤交换机上架,物理联线根据设备联接图,联接控制器、扩展柜和SPS。
4设备初始化,配置控制器IP 将两个控制器和笔记本联入LAN,使用NavisphereStorage System Initializaiotn配置控制器IP。
5抓取EIP信息使用CAP2软件抓取盘阵信息,将生成的.zip文件mail腾冲(tengchong@)。
6配置磁盘阵列,和客户确认盘阵划分方案激活写cache、accesslogis和flareos等,盘阵配置基本方案是每个柜子划分为一个RadiGroup, Raid类型为Raid5,要划分热备盘。
7将Flare升级到Release24使8激活光纤交换机的扩展端口每台光纤交换机需激活8个端口。
9填写ccpf文档相关部分将有关盘阵划分部分mail相关人员10连接主机和光纤交换机,划分zoning.光纤线两端要标标签,zoning划分方式使用wwn方式。
11在主机端安装PowerPath等软件在要连接的主机端安装powerpath和Navisphere agent&cli等软件,请注意Powerpath版本(推荐4.5版本)。
12在盘阵建立StorageGroup在主机端扫描盘阵,确认PowerPath设备。
确认powerpath设备确认powerpath设备和每个Lun所对应的路径数目的正确性。
CSU32P20 用户手册说明书

CSU32P20用户手册带12-bit ADC的8位RISC OTP MCUREV 1.7版本历史目录版本历史 (2)目录 (3)1产品概述 (6)1.1功能描述 (6)1.2主要特性 (6)1.3选型表 (7)1.4PIN配置 (8)1.4.1SOP8/DIP8/MSOP8 PIN配置 (8)1.4.2MSOP10 PIN配置 (8)1.4.3SOP14/DIP14/TSSOP14 PIN配置 (9)1.4.4SOP16/TSSOP16/DIP16 PIN配置 (9)1.5引脚说明 (10)1.6CSU32P20与CSU8RP3119B/3117B/3115B/CSU8RP3215资源差异 (11)2标准功能 (12)2.1CPU核 (12)2.1.1存储器 (14)2.1.2状态寄存器 (16)2.1.3SFR (17)2.2时钟系统 (19)2.2.1概述 (19)2.2.2时钟框图 (19)2.2.3寄存器 (19)2.2.4内部高速RC时钟 (20)2.2.5内部低速wdt时钟 (20)2.3复位系统 (21)2.3.1上电复位 (23)2.3.2看门狗复位 (23)2.3.3窗看门狗复位 (23)2.3.4掉电复位 (23)2.3.5外部硬件复位 (24)2.3.6非法指令复位 (24)2.3.7EMC复位 (24)2.3.8寄存器说明 (24)2.4中断 (26)2.4.1中断概述 (26)2.4.2中断使能寄存器 (27)2.4.3中断标志寄存器 (29)2.4.4外部中断0 (31)2.4.5外部中断1 (31)2.4.6AD中断溢出 (34)2.4.7定时器0溢出中断 (34)2.4.8定时/计数器2溢出中断 (34)2.4.9定时/计数器3溢出中断 (34)2.4.10PUSH和POP处理 (34)2.5定时器0 (36)2.5.2定时器0寄存器列表 (36)2.5.3定时功能 (38)2.6I/O PORT (39)2.6.1GPIO上下拉电阻 (39)2.6.2PT1口 (39)2.6.3PT3口 (44)2.6.4PT5口 (47)3增强功能 (50)3.1H ALT和S LEEP模式 (50)3.2看门狗(WDT) (52)3.2.1看门狗定时器寄存器表 (52)3.2.2WDT定时器功能 (53)3.3窗看门狗(WWDT) (55)3.3.1WWDT特性 (55)3.3.2WWDT功能描述 (55)3.3.3寄存器描述 (57)3.4定时/计数器2 (59)3.4.1定时/计数器2概述 (59)3.4.2寄存器描述 (59)3.4.3定时/计数器功能 (63)3.4.4蜂鸣器 (63)3.4.5PWM (64)3.5定时/计数器3 (66)3.5.1寄存器描述 (66)3.5.2定时/计数器功能 (71)3.5.3蜂鸣器 (71)3.5.4PWM (72)3.5.5互补式PWM输出 (73)3.6模数转换器(ADC) (75)3.6.1寄存器描述 (75)3.6.2输入电压和SRAD输出数据的关系 (79)3.6.3转换时间 (79)3.6.4ADC采样时间 (81)3.6.5AD失调电压校正 (82)3.6.6数字比较器 (83)3.6.7内部测量VDD的电压 (84)3.75*8软件LCD (86)3.7.1寄存器描述 (86)3.7.2软件LCD实现方法 (86)3.8数据查表 (87)3.8.1读操作 (87)3.8.2寄存器描述 (87)3.9输入逻辑电平电压配置 (89)3.9.1寄存器描述 (89)3.10输出电流配置 (90)3.10.1寄存器描述 (90)3.11烧录模块 (91)3.12代码选项 (92)3.12.1OPTIION (92)4MCU指令集 (94)5典型应用 (112)5.1移动电源 (112)5.2其他应用 (112)6电气特性 (113)6.1极限值 (113)6.2直流特性(VDD=5V,T A=25ºC,如无其他说明则都是此条件) (113)6.3ADC特性(VDD=5V,T A=25ºC,如无其他说明则都是此条件) (114)6.432MH Z IRC时钟频率特性 (116)6.516MH Z IRC时钟频率特性 (116)6.68MH Z IRC时钟频率特性 (117)6.7WDT时钟频率特性 (117)6.8 2.0V掉电复位温度特性 (118)6.9 2.4V低电压复位温度特性 (118)6.10内部参考电压1.4V电压和温度特性 (119)6.11内部参考电压2.0V电压和温度特性 (119)6.12内部参考电压3.0V电压和温度特性 (120)6.13内部参考电压4.0V电压和温度特性 (120)6.14可靠性 (120)6.14.1ESD特性 (120)6.14.2Latch up (120)7封装图 (122)7.1SOP-8PIN (122)7.2DIP-8PIN (124)7.3MSOP-8PIN (126)7.4MSOP-10PIN (127)7.5SOP-14PIN (128)7.6DIP-14PIN (129)7.7TSSOP-14PIN (130)7.8SOP-16PIN (131)7.9TSSOP-16PIN (132)7.10DIP-16PIN (133)8单片机产品命名规则 (134)8.1产品型号说明 (134)8.2命名举例说明 (135)8.3产品印字说明 (135)9订货信息 (136)10附录 (137)10.1使用CSU32P20替换CSU3115B/CSU3117B/CSU3119B方法说明 (137)1产品概述1.1功能描述CSU32P20是一款带12-bit ADC的8位CMOS单芯片RISC MCU,内置2K×16位OTP程序存储器,104字节SRAM。
LD32传感器系列数据手册说明书
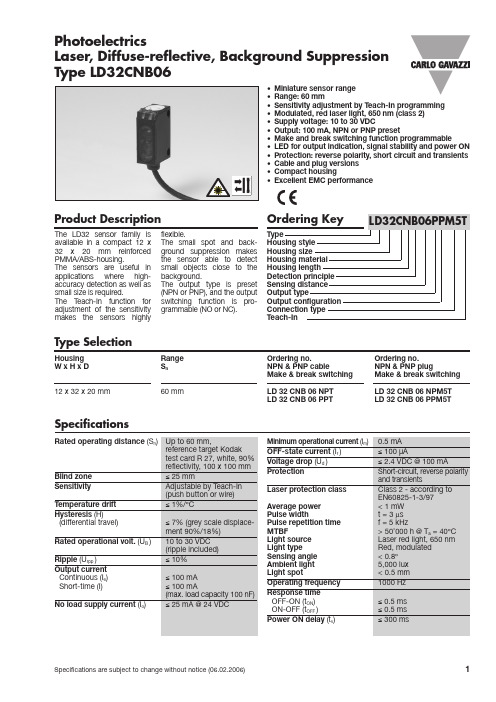
Product DescriptionThe LD32 sensor family is available in a compact 12 x 32 x 20 mm reinforced PMMA/ABS-housing.The sensors are useful in applications where high-accuracy detection as well as small size is required.The T each-In function for adjustment of the sensitivity makes the sensors highlyflexible.The small spot and back-ground suppression makes the sensor able to detect small objects close to the background.The output type is preset (NPN or PNP), and the output switching function is pro-grammable (NO or NC).•Miniature sensor range •Range: 60 mm•Sensitivity adjustment by Teach-In programming •Modulated, red laser light, 650 nm (class 2)•Supply voltage: 10 to 30 VDC•Output: 100 mA, NPN or PNP preset•Make and break switching function programmable•LED for output indication, signal stability and power ON •Protection: reverse polarity, short circuit and transients •Cable and plug versions •Compact housing•Excellent EMC performancePhotoelectricsLaser, Diffuse-reflective, Background SuppressionType LD32CNB06Type SelectionHousing Range Ordering no.Ordering no.W x H x D S n NPN & PNP cableNPN & PNP plugMake & break switching Make & break switching 12 x 32 x 20 mm60 mmLD 32 CNB 06 NPT LD 32 CNB 06 NPM5T LD 32 CNB 06 PPTLD 32 CNB 06 PPM5TSpecificationsOperation DiagramInstallation HintsRelief of cable strain Protection of the sensing face Switch mounted on mobile carrier To avoid interference from inductive voltage/current peaks, separate the prox. switch pow-er cables from any other power cables, e.g.motor, contactor or solenoid cablesIncorrectCorrectThe cable should not be pulled A proximity switch should not serve asmechanical stopAny repetitive flexing of thecable should be avoidedLD32CNB06Specifications (cont.)Wiring Diagramstv = Power ON delayDelivery Contents•Photoelectric switch: LD 32 CNB 06 ...•Installation instruction•Packaging:Cardboard boxAccessoriesLD32CNB06DimensionsFor further information refer to “Accessories”1.Press the button for 13 s.2.Release the button: the green LED flashes.3. While the green LED flashes, the output is invertedeach time the button is pressed. This is indicated by the yellow LED.When the button is not pressed for 10 s, the current output function is stored.The sensor is now ready for operation.Default setting 1.No object in the detection area:3 s, until both LED’s flash simultaneously.2.NB!The Teach Input (2 WH) will work similarly to the push button, active High.AdjustmentSensitivity adjustment, with static object 1.Line up the sensor with the object. Yellow LED andgreen LED are ON.2.Press the button for 3 s until both LED’s flashsimultaneously (the first switching point is stored).3. Place the object outside the detection area.4. Press the button for 1 s.a)The green LED flashes and stays ON: thesecond switching point is stored, and the sensor is ready to operate.b)Both LED’s flash simultaneously: the sensorcannot detect the object, no switching points are stored.1.Line up the sensor with the object. Yellow LED andgreen LED are ON.2.Press the button for 3 s until both LED’s flashsimultaneously (the first switching point is stored).3. Leave the object in the detection area, press thebutton for 1 s. The green LED flashes and stays on: the second switching point is stored, and the sensor is ready to operate.Sensitivity adjustment, with a running process 1.Line up the sensor with the object. Green LED is ON.At this stage the status of the yellow LED can be ignored.2.The running process must be the only “object” withinthe detection area. Press the button for 3 s until both LED’s flash simultaneously.3.Press the button for at least the duration of one pro-cess cycle.a)The green LED flashes and stays ON: bothswitching points have been stored, and the sen-sor is ready to operate.b)Both LED’s flash simultaneously: the sensor cannot detect the object, no switching points are stored.LD32CNB063 s 1 cycle 13 s 3 s 1 s。
XCF32P中文资料
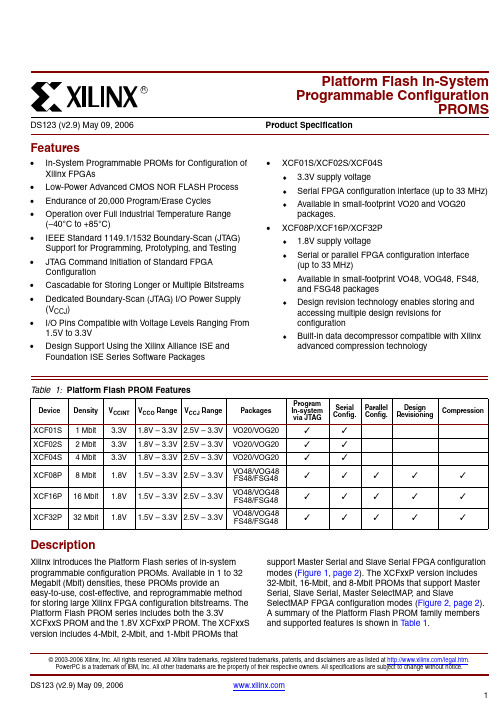
the PROMs DATA (D0-D7) pins. New data is available a short access time after each rising clock edge. The data is clocked into the FPGA on the following rising edge of the CCLK. A free-running oscillator can be used in the Slave Parallel /Slave SelecMAP mode.
• I/O Pins Compatible with Voltage Levels Ranging From 1.5V to 3.3V
• Design Support Using the Xilinx Alliance ISE and Foundation ISE Series Software Packages
D[1:7] (Parallel Mode)
CF
REV_SEL [1:0]
Figure 2: XCFxxP Platform Flash PROM Block Diagram
ds123_19_122105
When the FPGA is in Master Serial mode, it generates a configuration clock that drives the PROM. With CF High, a short access time after CE and OE are enabled, data is available on the PROM DATA (D0) pin that is connected to the FPGA DIN pin. New data is available a short access time after each rising clock edge. The FPGA generates the appropriate number of clock pulses to complete the configuration.
SLSC-12201 32通道数字输入 输出模块说明书

SPECIFICA TIONSSLSC-1220132 Channel, 5 V to 33 V, Digital Input/OutputSLSC module design specification version 1.0SLSC compatibility level1Rear I/O compatibility category[01] (digital input/output up to 32 channels) Recommended RTI RTI-12301Front I/O CharacteristicsNote The 32 front I/O channels are organized into two banks consisting of twoports with eight channels per port. Port0 and Port1 are in Bank0; Port2 and Port3 arein Bank1. At least one Vsup must be present and routed to the banks. Each bank canbe powered by either Vsup_0 or Vsup_1.Note The mapping between the 32 rear I/O channels and the 32 front I/O channelsis one-to-one. DIO0 maps to P0.0, and DIO31 maps to P3.7.Number of channels32 bidirectional channelsOvervoltage protection±60 VSynchronization jitter±12.5 nsExternal supply voltage (Vsup) 5 V DC to 33 V DCUndervoltage lockout at 4 VPower-on configuration Software configurable (factory default issinking digital input)Table 1. Feature Configurability (Continued)Digital InputInput type Sinking or sourcingInput voltage range0 V to 5 V0 V to 33 VThreshold voltage settling time20 msMinimum pulse width100 nsMaximum signal frequency100 kHzPropagation delay200 nsSourcing input pull-up resistor24 kΩDigital OutputOutput type Sourcing, sinking, or push-pull Continuous output current50 mA maximumOutput impedance sourcing30 ΩOutput impedance sinking20 ΩShort circuit protection10 channels simultaneous fault Minimum pulse width100 nsMaximum signal frequency100 kHzPropagation delay300 nsRise/fall time25 ns (push-pull configuration) Maximum load capacitance 1 nF maximum2| | SLSC-12201 SpecificationsRear I/O CharacteristicsConnector XJ3 connects to an NI digital input/digital output device supporting 5 V TTL or 3.3 V LVTTL signaling.Power RequirementsPower consumption from backplane 4.1 W maximum5.7 W maximumPower consumption from Vsup under noloadMinimum Vsup power supply outputcurrent capability 1.0A+50mA×BBB BBBBℎBBBThermal dissipation< 50 WPhysical CharacteristicsSLSC slots1Dimensions175 mm × 31 mm × 336 mm (6.89 in. × 1.19in. × 13.21 in.)Weight581 g (20.5 oz)Front I/O connectors2x 44-pin high-density D-SUBRear I/O connectors1x 110-pin Hard Metric type A. 1x 8-bladeUniversal Power Module (UPM), capable ofimplementing Fully Compatible Rear I/O Safety VoltagesMeasurement category OIsolationChannel-to-channel NoneChannel-to-earth ground NoneCaution Do not connect the SLSC-12201 to signals or use for measurementswithin Measurement Categories II, III, or IV.Note Measurement Categories CAT I and CAT O are equivalent. These test andmeasurement circuits are for other circuits not intended for direct connection to theSLSC-12201 Specifications| © National Instruments| 3MAINS building installations of Measurement Categories CAT II, CAT III, orCAT IV.Caution Do not operate the SLSC-12201 in a manner not specified in thisdocument. Product misuse can result in a hazard. You can compromise the safetyprotection built into the product if the product is damaged in any way. If the productis damaged, return it to NI for repair.SafetyThis product is designed to meet the requirements of the following electrical equipment safety standards for measurement, control, and laboratory use:•IEC 61010-1, EN 61010-1•UL 61010-1, CSA C22.2 No. 61010-1Note For UL and other safety certifications, refer to the product label or the OnlineProduct Certification section.Electromagnetic CompatibilityThis product meets the requirements of the following EMC standards for electrical equipment for measurement, control, and laboratory use:•EN 61326-1 (IEC 61326-1): Class A emissions; Basic immunity•EN 55011 (CISPR 11): Group 1, Class A emissions•EN 55022 (CISPR 22): Class A emissions•EN 55024 (CISPR 24): Immunity•AS/NZS CISPR 11: Group 1, Class A emissions•AS/NZS CISPR 22: Class A emissions•FCC 47 CFR Part 15B: Class A emissions•ICES-001: Class A emissionsNote In the United States (per FCC 47 CFR), Class A equipment is intended foruse in commercial, light-industrial, and heavy-industrial locations. In Europe,Canada, Australia and New Zealand (per CISPR 11) Class A equipment is intendedfor use only in heavy-industrial locations.Note Group 1 equipment (per CISPR 11) is any industrial, scientific, or medicalequipment that does not intentionally generate radio frequency energy for thetreatment of material or inspection/analysis purposes.Note For EMC declarations and certifications, and additional information, refer tothe Online Product Certification section.4| | SLSC-12201 SpecificationsCE ComplianceThis product meets the essential requirements of applicable European Directives, as follows:•2014/35/EU; Low-V oltage Directive (safety)•2014/30/EU; Electromagnetic Compatibility Directive (EMC)EnvironmentalModule operating temperature0 °C to 85 °C1 (Tested in accordance withIEC 60068-2-1 and IEC 60068-2-2)Storage temperature range-40 °C to 85 °C (Tested in accordance withIEC 60068-2-1 and IEC 60068-2-2.) Relative humidity range, operating10% to 90%, noncondensing (Tested inaccordance with IEC-60068-2-78.)Relative humidity range, storage5% to 95%, noncondensing (Tested inaccordance with IEC-60068-2-78.)Pollution degree2Maximum altitude2,000 m (800 mbar)(at 25 °C ambient) Indoor use only.Shock and VibrationOperating shock30 g peak, half-sine, 11 ms pulse (Tested inaccordance with IEC-60068-2-27. MeetsMIL-PRF-28800F Class 2 limits) Operating vibration, random 5 to 500 Hz, 0.3 g rms (Tested in accordancewith IEC-60068-2-64)Non-operating vibration, random 5 to 500 Hz, 2.4 g rms (Tested in accordancewith IEC-60068-2-64. Non-operating testprofile exceeds the requirements ofMIL-PRF-28800F Class 3.) 1The chassis internal ambient temperature may reach 85 °C with all slots at the maximum allowedpower dissipation.SLSC-12201 Specifications| © National Instruments| 5Online Product CertificationRefer to the product Declaration of Conformity (DoC) for additional regulatory compliance information. To obtain product certifications and the DoC for this product, visit / certification, search by model number or product line, and click the appropriate link in the Certification column.Worldwide Support and ServicesThe NI website is your complete resource for technical support. At /support, you have access to everything from troubleshooting and application development self-help resources to email and phone assistance from NI Application Engineers.Visit /services for NI Factory Installation Services, repairs, extended warranty, and other services.Visit /register to register your NI product. Product registration facilitates technical support and ensures that you receive important information updates from NI.A Declaration of Conformity (DoC) is our claim of compliance with the Council of the European Communities using the manufacturer’s declaration of conformity. This system affords the user protection for electromagnetic compatibility (EMC) and product safety. You can obtain the DoC for your product by visiting /certification. If your product supports calibration, you can obtain the calibration certificate for your product at /calibration.NI corporate headquarters is located at 11500 North Mopac Expressway, Austin, Texas, 78759-3504. NI also has offices located around the world. For telephone support in the United States, create your service request at /support or dial 1 866 ASK MYNI (275 6964). For telephone support outside the United States, visit the Worldwide Offices section of / niglobal to access the branch office websites, which provide up-to-date contact information, support phone numbers, email addresses, and current events.Information is subject to change without notice. Refer to the NI T rademarks and Logo Guidelines at /trademarks for information on NI trademarks. Other product and company names mentioned herein are trademarks or trade names of their respective companies. For patents covering NI products/technology, refer to the appropriate location: Help»Patents in your software, the patents.txt file on your media, or the National Instruments Patent Notice at /patents. Y ou can find information about end-user license agreements (EULAs) and third-party legal notices in the readme file for your NI product. Refer to the Export Compliance Information at /legal/export-compliance for the NI global trade compliance policy and how to obtain relevant HTS codes, ECCNs, and other import/export data. NI MAKES NO EXPRESS OR IMPLIED WARRANTIES AS TO THE ACCURACY OF THE INFORMATION CONT AINED HEREIN AND SHALL NOT BE LIABLE FOR ANY ERRORS. U.S. Government Customers: The data contained in this manual was developed at private expense and is subject to the applicable limited rights and restricted data rights as set forth in FAR 52.227-14, DFAR 252.227-7014, and DFAR 252.227-7015.© 2017 National Instruments. All rights reserved.377037A-01July 20, 2017。
扫描纸 ScanSnap 用户指南说明书

Specifications are subject to change without notice.Be sure to carefully read all safety precautions prior to using this product and use this device as instructed.For more ScanSnap related information, visit our website at :Do not place this device in wet, moist, steamy, dusty or oily areas. Using this product under such conditions may result in electrical shock, fire or damage to this product.Safety Precautions*1 Available only when connecting to a computer. *2 Scanning speeds may vary due to the system environment used.*3 Scans will be made in "Best mode" if shorter sides are less than 105 mm and in "Better mode" if not. *4 A3 scans are possible with use of A3 carrier sheets. *5 Available in all modes except for "Excellent mode". *6 Indicated specifications apply when using ScanSnap Home. *7 Maximum capacity varies, depending upon paper weight. *8 Some computers do not recognize the ScanSnap when it is connected to a USB 3.2 Gen1/3.0 port. In this case, please use a USB 2.0 cable. *9 Availability of 5 GHz Wi-Fi may vary depending on region. *10 Access Point Connect Mode requires a Wi-Fi access point or router. *11 5 GHz Wi-Fi is not available with Direct Connect Mode. *12 Excluding the stacker and other external attachments.*1 The ScanSnap device may not work if the connected computer does not meet these requirements. *2 The ScanSnap device also operates with Apple Silicon-based Mac computers. Please visit the ScanSnap website for latest support information. *3 Scanning speeds may drop if the recommended CPU, memory capacity and USB 1.1 requirements are not met. *Compatibility may differ depending on software versions. Please visit the ScanSnap website for latest information on driver and application support. *The system requirements may change depending on the support policies of the above system and third-party software.*1 ScanSnap scanners do not run with Windows® 10 ARM-based PCs.*2 Operate Windows in desktop mode. *3 The ScanSnap device may not work if the connected computer does not meet these requirements. *4 Scanning speeds may drop if the recommended CPU, memory capacity and USB 1.1 requirements are not met. *5 Indicated disk capacity requirements apply when downloading ScanSnap Home. *6 .NET Framework 4.7 or later must be installed. If it is not installed, it is installed with ScanSnap Home. Up to 4.5 GB of disk space is required for the installation.*Please refer to the ScanSnap website for the latest support information of the driver and applications. Compatibility may differ depending on the software's version. *The system requirements may change depending on the support policies of the above system and third-party software.iX1600 (White/Black)Product name Scanner type Scanning color modeScanning speed *(A4 portrait)Document sizeADF (Automatic Document Feeder)/Manual Feed, Duplex Color, Grayscale, Monochrome,Automatic (Color/Grayscale/Monochrome * detection)Color CIS x 2 (Front x 1, Back x 1)3 Color LED (Red/Green/Blue)Image sensor Light source600 dpiOptical resolutionSimplex/Duplex: 40 ppmSimplex/Duplex: 40 ppm(Color/Grayscale: 150 dpi, Monochrome: 300 dpi)Simplex/Duplex: 40 ppm(Color/Grayscale: 200 dpi, Monochrome: 400 dpi)Simplex/Duplex: 40 ppm(Color/Grayscale: 300 dpi, Monochrome: 600 dpi)Simplex/Duplex: 10 ppm(Color/Grayscale: 600 dpi, Monochrome: 1,200 dpi)Auto mode (Default)*Normal modeBetter mode Best mode Operating systemsHardware requirements *Intel Celeron 1.8 GHz (2core) or higher(Recommended: Intel Core™ i5 2.5 GHz or higher)2 GB or more (Recommended: 4 GB or more)1,024 x 768 pixels or more3.8 GB or more of free hard disk spaceCPU *Memory capacity *Display resolution Disk capacity **Excellent mode *Minimum: 50.8 x 50.8 mm (2 x 2 in.)Maximum: 216 x 360 mm (8.5 x 14.17 in.) A3, B4,279 x 432 mm (11 x 17 in.)3,000 mm (863 mm in 32-bit) Smart Device: 863 mm (Duplex), 1,726 mm (Simplex)40 to 209 g/m (11 to 56 lb)A8 size or less: 128 to 209 g/m (34 to 56 lb)Cards: 0.76 mm or less (Compliant with the ISO7810 ID-1 type)(Includes embossed cards in landscape orientation)Normal scan *Manual scan Long paper scanning *Paper weight (Thickness)50 sheets (A4, 80 g/m or 20 lb)ADF capacity *InterfaceWi-Fi InterfaceUSB 3.2 Gen1x1 / USB 2.0 / USB 1.1(Connector Type: Type-B)*IEEE802.11a/b/g/nFrequency band: 2.4 GHz *USBWi-FiAccess Point Connect Mode (Infrastructure mode)*Direct Connect Mode (Ad-hoc mode)*4.3 in. color TFT touch screen AC 100 to 240 V , 50/60 Hz 17 W or less 1.5 W or less 1.6 W or lessOperating Sleep mode(USB connected)Sleep mode(Wi-Fi connected)LCDPower requirementPowerconsumptionOverlap detection (Ultrasonic sensor), Length detection ScanSnap Home (ScanSnap specific driver) •Windows : Does not support TWAIN/ISIS™ •macOS: Does not support TWAINMultifeed detection DriverT emperature: 5 to 35 °C (41 to 95 °F)Relative humidity: 20 to 80% (Non-condensing) Operation environment 292 x 161 x 152 mm (11.5 x 6.3 x 6.0 in.) 3.4 kg (7.5 lb)Dimensions (W x D x H)*Device weightENERGY STAR /RoHSEnvironmental compliance General SpecificationsScanSnap iX1600 System Requirements•Windows®Operating systemsHardwarerequirements *Intel Core i5 1.4 GHz or higher(Recommended: Core i5 2.5 GHz or higher)2 GB or more (Recommended: 8 GB or more)1,024 x 768 pixels or more2.0 GB or more of free hard disk spaceCPU **Memory capacity * Display resolution Disk capacity•Mac*1 ScanSnap Home installation requires a computer and Internet. Activation is also necessary for software use. Please visit the company website for download information. https:///g-support/en. *2 ScanSnap Manager V7.1 and later is required. *3 Please refer to the included license certificate to download the software. *4 Kofax Power PDF is not included with the iX1400.Kofax Power PDF Standard **Kofax Power PDF Standard for Mac **ScanSnap Home * ScanSnap Manager *Windows MacABBYY FineReader for ScanSnap™•Software*1 Although ScanSnap Carrier Sheets have a listed lifespan of 500 scans, the lifespan may vary with usage. ScanSnap Carrier sheets are intended to scan paper documents with weights of 127 g/m or less. They also support the scanning of folded documents that are as large as 216 x 297 mm.Carrier Sheets *DescriptionPhoto Carrier Sheets ScanSnap BagPart number RemarksPA03360-0013 PA03770-0015PA03951-0651Contains 5 sheets supporting photographs and various document sizesFor ScanSnap iX1600, iX1400, iX1500, iX500, iX100, S1100i ScanSnap Home Additional License (1 License)PA43404-B043 1 additional license for ScanSnap HomeContains 3 sheets supporting photographs(E-size, L-size, King-size), postcards, and business cards Stores the ScanSnap iX1600, iX1400, iX1500, iX500 and accessoriesOptions*1 These recommended lifetimes are for 80 g/m (20 lb) A4 sized documents. Therefore, appropriate replacement lifetimes may vary for other document types.Roller Set Description Cleaner F1Cleaning Wipe Part number RemarksPA03656-0001PA03950-0352PA03950-0419Lifetime: Every 200,000 sheets or one year *(For ScanSnap iX1600, iX1400, iX1500 or iX500)100 ml bottleFor use on the Brake roller and Pick roller 24 packetsFor use on the Brake roller and Pick roller Cleaning PaperCA99501-001210 sheetsUse this non-woven sheet with Cleaner F1Consumables*It is recommended to use original or approved accessories for consumables, options and cleaning kits, specially designed for your device. Device failures, troubles and damages arising from use of OEM or 3rd Party accessories may render your warranty invalid and incur charges for repair even during the warranty period.©2021 PFU Limited Printed in some country 2021.01 U-208 SZX 50SPFU Limited, a Fujitsu company, has determined that this product meets the ENERGY STAR ® guidelines for energy efficiency. ENERGY STAR ® is a registered trademark of the United States.This scanner is designed to digitize materials that can be reproduced lawfully, in accordance with applicable copyright regulations and other laws. ScanSnap users are responsible for how they use this scanner. It is imperative that ScanSnap users comply with all applicable local rules and laws, including, without limitation, copyright laws when using this scanner.*ABBYY™ FineReader™ Engine © ABBYY. OCR by ABBYY. ABBYY and FineReader are trademarks of ABBYY Software, Ltd. which may be registered in some jurisdictions. *Intel, Pentium, and Intel Core are trademarks or registered trademarks of Intel Corporation or its subsidiaries in the U.S. and/or other countries. *ISIS™ is a trademark of Open Text. *Mac, macOS, and the Mac logo are trademarks of Apple Inc. *Kofax and Power PDF are trademarks or registered trademarks of Kofax Limited in the United States and other countries. *ScanSnap, the ScanSnap logo and ScanSnap Home are registered trademarks or trademarks of PFU Limited in Japan. *Other company names and product names are the trademarks or registered trademarks of the respective companies.Accessories•Safety Precautions •AC Cable •AC Adapter •USB Cable •Receipt GuideUltimate efficiencyand flexibility.Windows®11 (64-bit), Windows 10 (32-bit / 64-bit)**, Windows 8.1 (32-bit / 64-bit)*, Windows 7 (32-bit / 64-bit)macOS High Sierra 10.13 or laterEase into a whole new world of digitalization and unlocking seamless flow of information ScanSnap Home – All-in-one software to optimize your productivityEase into a whole new world of digitalization and unlocking se ScanSnap Home – All-in-one software to optimize your p ScanSnap iX1600 –Evolved flagship model of the ScanSnap seriesA software specially designed for ScanSnap scanners,assisting users to easily manage, edit, and utilize various types of scanned data.Combining all your favorite functions,it allows users to organize your documents,receipts, business cards, photos and much more all in one application.A brand new experience to digitize, augment, organize, and share information to fuel your business growth and innovation with the fastest model in the ScanSnap Series.Able to load up 50 sheets at a time and scan at a speedy 40 pages per minute, the iX1600 produces superior, high-quality images. Simply open the document chute, and ScanSnap is ready to go. Fast start-up and stable feeding performance provide you with a peace of mind while you carry out your tasks.Name files fasterFind files easilyScanSnap Home uses the text, found onyour scanned documents to identify file names.Accuracy is heightened with increased use.Finding documents can never be easier. ScanSnap Home comes with functions tore-organize and perform searches on document types using folders, tags, and keywords.Optimized user experience Scan anywhere, whenever you want - Connects via Wi-Fi. Works without a computer. - Scans on any smart device or popular cloud service 1, desktop or document management application.Intuitive and ideal for team sharingThe iX1600 comes equipped with a 4.3-inch touch screen, providing an easy to use interface with simple icons and intuitive user experience. Keeping documents in order is a breeze, whether at the office or home. Select which device youwould like to scan to, and share between multiplemembers and devices anytime.1 Available services vary by region.g seamless flow of informationur productivity DocumentsQuickly find that recipe or meeting agenda that you stored last week with easy tagging features.ReceiptsKeep track of your spending habits eachmonth so that you can check back whenever you desire.Easy to install, configure and start.Just for anyone - Personal, SOHO, Remote Office/Work from home,Small businesses, New to ScanSnap, New to scanning.Available in black and white, choose the color you want based on your preference.Business CardsScanSnap Home’s intelligent auto correction makes managing business card contacts a simple and seamless process with less manual work for you. Organize your contacts with powerful search features.SatisfactionCan be used in conjunction with ScanSnap Manager software.Stress-free usabilityScan receipts and much moreScan larger-sized documents, like A3 documents, envelopes, and much more, with Manual Scan Mode 2. Effortlessly scan small documents with the Receipt Guide. No need to be concerned about fixing receipts and business cards that tend to curl or skew.Reliable and intelligentWith professional grade feeding technology and ultrasonic sensors, iX1600 handles multi-page documents with ease and can additionally detect and alert the user of multi-feeding errors. A host of intelligent automatic image processing functions enables users to scan confidently without adjusting settings.Ease into a whole new world of digitalization and unlocking seamless flow of information ScanSnap Home – All-in-one software to optimize your productivity Brake Roller2 Manual Scan Mode is available when using ScanSnap Home.。
MICROCHIP PIC32MX5XX 6XX 7XX 数据手册
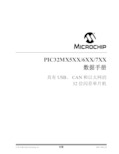
PIC32MX5XX/6XX/7XX数据手册具有USB、CAN和以太网的32位闪存单片机 2010 Microchip Technology Inc.初稿DS61156B_CNDS61156B_CN 第2页初稿2010 Microchip Technology Inc.提供本文档的中文版本仅为了便于理解。
请勿忽视文档中包含的英文部分,因为其中提供了有关Microchip 产品性能和使用情况的有用信息。
Microchip Technology Inc.及其分公司和相关公司、各级主管与员工及事务代理机构对译文中可能存在的任何差错不承担任何责任。
建议参考Microchip Technology Inc.的英文原版文档。
本出版物中所述的器件应用信息及其他类似内容仅为您提供便利,它们可能由更新之信息所替代。
确保应用符合技术规范,是您自身应负的责任。
Microchip 对这些信息不作任何明示或暗示、书面或口头、法定或其他形式的声明或担保,包括但不限于针对其使用情况、质量、性能、适销性或特定用途的适用性的声明或担保。
Microchip 对因这些信息及使用这些信息而引起的后果不承担任何责任。
如果将Microchip 器件用于生命维持和/或生命安全应用,一切风险由买方自负。
买方同意在由此引发任何一切伤害、索赔、诉讼或费用时,会维护和保障Microchip 免于承担法律责任,并加以赔偿。
在Microchip 知识产权保护下,不得暗中或以其他方式转让任何许可证。
商标Microchip 的名称和徽标组合、Microchip 徽标、dsPIC 、K EE L OQ 、K EE L OQ 徽标、MPLAB 、PIC 、PICmicro 、PICSTART 、PIC 32徽标、rfPIC 和 UNI/O 均为Microchip Technology Inc .在美国和其他国家或地区的注册商标。
FilterLab 、Hampshire 、HI-TECH C 、Linear ActiveThermistor 、MXDEV 、MXLAB 、SEEVAL 和The Embedded Control Solutions Company 均为Microchip Technology Inc .在美国的注册商标。
Super32使用手册(V5.2.2)

使用手册
适用 Super32 控制器
Super32 使用手册
安控自动化产品,您成功的选择
尊敬的用户:
欢迎您使用安控公司为您提供的自动化产品及使用手册。 经过多年,在产品品质、技术应用、服务支持等方面不断进取和踏实积 累,安控公司成功推出的 Rock E 系列 PLC 和 SuperE 系列 RTU 两大系列 产品,已在自动化行业各领域中得到很好地应用。经受了各种现场应用环 境的考验,得到了专家及广大用户的一致认可。 如果您是初次使用我们的产品,请您在购买和使用 ECHO 产品时,仔细阅 读使用手册。这样您会更加了解产品的各项性能,合理配置硬件和软件资 源,真正使我们的产品成为您工程项目实施中最成功的选择。 自动化产品使用手册包括:
《Rock E40 使用手册》 《Super E40 使用手册》 《Super32 使用手册》 《Rock32 使用手册》 《OpenPCS 编程手册》 《OpenPCS 编程手册附录》 《ESet 配置手册》
我们将不断地升级使用手册,为您陆续提供现场应用程序和文档。当您遇 到疑难问题时,可以随时与我们技术支持(010)62971668—6520~6526 取 得联系,我们将在第一时间及时响应,帮助您解决问题。您也可登录公司 网站,在“技术资源”栏目查询有关资料,取得应用帮助。
产品介绍 介绍产品组成、参数设置、性能指标等内容。
产品选型 介绍产品可选配置、选型方法等内容。
安装使用 介绍产品安装、程序开发、应用方法等内容。
技术服务 介绍技术支持、销售服务等内容。
适用读者
阅读《Super32 使用手册》应具有一定的 RTU/PLC 知识,手册是针对产品 开发工程师、电气工程师及安装人员等编写。
max3232技术资料下载datasheet下载中文pdf下载

PACKAGING INFORMATIONOrderable Device Status(1)PackageType PackageDrawingPins PackageQtyEco Plan(2)Lead/Ball Finish MSL Peak Temp(3)MAX3232CD ACTIVE SOIC D1640Green(RoHS&no Sb/Br)CU NIPDAU Level-1-260C-UNLIMMAX3232CDB ACTIVE SSOP DB1680Green(RoHS&no Sb/Br)CU NIPDAU Level-1-260C-UNLIMMAX3232CDBE4ACTIVE SSOP DB1680Green(RoHS&no Sb/Br)CU NIPDAU Level-1-260C-UNLIMMAX3232CDBG4ACTIVE SSOP DB1680Green(RoHS&no Sb/Br)CU NIPDAU Level-1-260C-UNLIMMAX3232CDBR ACTIVE SSOP DB162000Green(RoHS&no Sb/Br)CU NIPDAU Level-1-260C-UNLIMMAX3232CDBRE4ACTIVE SSOP DB162000Green(RoHS&no Sb/Br)CU NIPDAU Level-1-260C-UNLIMMAX3232CDBRG4ACTIVE SSOP DB162000Green(RoHS&no Sb/Br)CU NIPDAU Level-1-260C-UNLIMMAX3232CDE4ACTIVE SOIC D1640Green(RoHS&no Sb/Br)CU NIPDAU Level-1-260C-UNLIMMAX3232CDG4ACTIVE SOIC D1640Green(RoHS&no Sb/Br)CU NIPDAU Level-1-260C-UNLIMMAX3232CDR ACTIVE SOIC D162500Green(RoHS&no Sb/Br)CU NIPDAU Level-1-260C-UNLIMMAX3232CDRE4ACTIVE SOIC D162500Green(RoHS&no Sb/Br)CU NIPDAU Level-1-260C-UNLIMMAX3232CDRG4ACTIVE SOIC D162500Green(RoHS&no Sb/Br)CU NIPDAU Level-1-260C-UNLIMMAX3232CDW ACTIVE SOIC DW1640Green(RoHS&no Sb/Br)CU NIPDAU Level-1-260C-UNLIMMAX3232CDWG4ACTIVE SOIC DW1640Green(RoHS&no Sb/Br)CU NIPDAU Level-1-260C-UNLIMMAX3232CDWR ACTIVE SOIC DW162000Green(RoHS&no Sb/Br)CU NIPDAU Level-1-260C-UNLIMMAX3232CDWRG4ACTIVE SOIC DW162000Green(RoHS&no Sb/Br)CU NIPDAU Level-1-260C-UNLIMMAX3232CPW ACTIVE TSSOP PW1690Green(RoHS&no Sb/Br)CU NIPDAU Level-1-260C-UNLIMMAX3232CPWE4ACTIVE TSSOP PW1690Green(RoHS&no Sb/Br)CU NIPDAU Level-1-260C-UNLIMMAX3232CPWG4ACTIVE TSSOP PW1690Green(RoHS&no Sb/Br)CU NIPDAU Level-1-260C-UNLIMMAX3232CPWR ACTIVE TSSOP PW162000Green(RoHS&no Sb/Br)CU NIPDAU Level-1-260C-UNLIMMAX3232CPWRE4ACTIVE TSSOP PW162000Green(RoHS&no Sb/Br)CU NIPDAU Level-1-260C-UNLIMMAX3232CPWRG4ACTIVE TSSOP PW162000Green(RoHS&no Sb/Br)CU NIPDAU Level-1-260C-UNLIMMAX3232ID ACTIVE SOIC D1640Green(RoHS&no Sb/Br)CU NIPDAU Level-1-260C-UNLIMMAX3232IDB ACTIVE SSOP DB1680Green(RoHS&no Sb/Br)CU NIPDAU Level-1-260C-UNLIMMAX3232IDBE4ACTIVE SSOP DB1680Green(RoHS&no Sb/Br)CU NIPDAU Level-1-260C-UNLIMOrderable Device Status(1)PackageType PackageDrawingPins PackageQtyEco Plan(2)Lead/Ball Finish MSL Peak Temp(3)MAX3232IDBG4ACTIVE SSOP DB1680Green(RoHS&no Sb/Br)CU NIPDAU Level-1-260C-UNLIMMAX3232IDBR ACTIVE SSOP DB162000Green(RoHS&no Sb/Br)CU NIPDAU Level-1-260C-UNLIMMAX3232IDBRE4ACTIVE SSOP DB162000Green(RoHS&no Sb/Br)CU NIPDAU Level-1-260C-UNLIMMAX3232IDBRG4ACTIVE SSOP DB162000Green(RoHS&no Sb/Br)CU NIPDAU Level-1-260C-UNLIMMAX3232IDE4ACTIVE SOIC D1640Green(RoHS&no Sb/Br)CU NIPDAU Level-1-260C-UNLIMMAX3232IDG4ACTIVE SOIC D1640Green(RoHS&no Sb/Br)CU NIPDAU Level-1-260C-UNLIMMAX3232IDR ACTIVE SOIC D162500Green(RoHS&no Sb/Br)CU NIPDAU Level-1-260C-UNLIMMAX3232IDRE4ACTIVE SOIC D162500Green(RoHS&no Sb/Br)CU NIPDAU Level-1-260C-UNLIMMAX3232IDRG4ACTIVE SOIC D162500Green(RoHS&no Sb/Br)CU NIPDAU Level-1-260C-UNLIMMAX3232IDW ACTIVE SOIC DW1640Green(RoHS&no Sb/Br)CU NIPDAU Level-1-260C-UNLIMMAX3232IDWE4ACTIVE SOIC DW1640Green(RoHS&no Sb/Br)CU NIPDAU Level-1-260C-UNLIMMAX3232IDWG4ACTIVE SOIC DW1640Green(RoHS&no Sb/Br)CU NIPDAU Level-1-260C-UNLIMMAX3232IDWR ACTIVE SOIC DW162000Green(RoHS&no Sb/Br)CU NIPDAU Level-1-260C-UNLIMMAX3232IDWRE4ACTIVE SOIC DW162000Green(RoHS&no Sb/Br)CU NIPDAU Level-1-260C-UNLIMMAX3232IDWRG4ACTIVE SOIC DW162000Green(RoHS&no Sb/Br)CU NIPDAU Level-1-260C-UNLIMMAX3232IPW ACTIVE TSSOP PW1690Green(RoHS&no Sb/Br)CU NIPDAU Level-1-260C-UNLIMMAX3232IPWE4ACTIVE TSSOP PW1690Green(RoHS&no Sb/Br)CU NIPDAU Level-1-260C-UNLIMMAX3232IPWG4ACTIVE TSSOP PW1690Green(RoHS&no Sb/Br)CU NIPDAU Level-1-260C-UNLIMMAX3232IPWR ACTIVE TSSOP PW162000Green(RoHS&no Sb/Br)CU NIPDAU Level-1-260C-UNLIMMAX3232IPWRE4ACTIVE TSSOP PW162000Green(RoHS&no Sb/Br)CU NIPDAU Level-1-260C-UNLIMMAX3232IPWRG4ACTIVE TSSOP PW162000Green(RoHS&no Sb/Br)CU NIPDAU Level-1-260C-UNLIM(1)The marketing status values are defined as follows:ACTIVE:Product device recommended for new designs.LIFEBUY:TI has announced that the device will be discontinued,and a lifetime-buy period is in effect.NRND:Not recommended for new designs.Device is in production to support existing customers,but TI does not recommend using this part in a new design.PREVIEW:Device has been announced but is not in production.Samples may or may not be available.OBSOLETE:TI has discontinued the production of the device.(2)Eco Plan-The planned eco-friendly classification:Pb-Free(RoHS),Pb-Free(RoHS Exempt),or Green(RoHS&no Sb/Br)-please check /productcontent for the latest availability information and additional product content details.TBD:The Pb-Free/Green conversion plan has not been defined.Pb-Free(RoHS):TI's terms"Lead-Free"or"Pb-Free"mean semiconductor products that are compatible with the current RoHS requirements for all6substances,including the requirement that lead not exceed0.1%by weight in homogeneous materials.Where designed to be soldered at high temperatures,TI Pb-Free products are suitable for use in specified lead-free processes.Pb-Free(RoHS Exempt):This component has a RoHS exemption for either1)lead-based flip-chip solder bumps used between the die and package,or2)lead-based die adhesive used between the die and leadframe.The component is otherwise considered Pb-Free(RoHS compatible)as defined above.Green(RoHS&no Sb/Br):TI defines"Green"to mean Pb-Free(RoHS compatible),and free of Bromine(Br)and Antimony(Sb)based flame retardants(Br or Sb do not exceed0.1%by weight in homogeneous material)(3)MSL,Peak Temp.--The Moisture Sensitivity Level rating according to the JEDEC industry standard classifications,and peak solder temperature.Important Information and Disclaimer:The information provided on this page represents TI's knowledge and belief as of the date that it is provided.TI bases its knowledge and belief on information provided by third parties,and makes no representation or warranty as to the accuracy of such information.Efforts are underway to better integrate information from third parties.TI has taken and continues to take reasonable steps to provide representative and accurate information but may not have conducted destructive testing or chemical analysis on incoming materials and chemicals.TI and TI suppliers consider certain information to be proprietary,and thus CAS numbers and other limited information may not be available for release.In no event shall TI's liability arising out of such information exceed the total purchase price of the TI part(s)at issue in this document sold by TI to Customer on an annual basis.OTHER QUALIFIED VERSIONS OF MAX3232:•Enhanced Product:MAX3232-EPNOTE:Qualified Version Definitions:•Enhanced Product-Supports Defense,Aerospace and Medical ApplicationsTAPE AND REEL INFORMATION*All dimensions are nominal Device Package Type Package DrawingPinsSPQ Reel Diameter (mm)Reel Width W1(mm)A0(mm)B0(mm)K0(mm)P1(mm)W (mm)Pin1Quadrant MAX3232CDBR SSOPDB 162000330.016.48.2 6.6 2.512.016.0Q1MAX3232CDR SOICD 162500330.016.4 6.510.3 2.18.016.0Q1MAX3232CDWR SOICDW 162000330.016.410.7510.7 2.712.016.0Q1MAX3232CPWR TSSOPPW 162000330.012.4 6.9 5.6 1.68.012.0Q1MAX3232IDBR SSOPDB 162000330.016.48.2 6.6 2.512.016.0Q1MAX3232IDR SOICD 162500330.016.4 6.510.3 2.18.016.0Q1MAX3232IDWR SOICDW 162000330.016.410.7510.7 2.712.016.0Q1MAX3232IPWR TSSOP PW 162000330.012.4 6.9 5.6 1.68.012.0Q1*All dimensions are nominalDevice Package Type Package Drawing Pins SPQ Length(mm)Width(mm)Height(mm) MAX3232CDBR SSOP DB162000346.0346.033.0 MAX3232CDR SOIC D162500333.2345.928.6 MAX3232CDWR SOIC DW162000346.0346.033.0 MAX3232CPWR TSSOP PW162000346.0346.029.0 MAX3232IDBR SSOP DB162000346.0346.033.0 MAX3232IDR SOIC D162500333.2345.928.6 MAX3232IDWR SOIC DW162000346.0346.033.0MAX3232IPWR TSSOP PW162000346.0346.029.0IMPORTANT NOTICETexas Instruments Incorporated and its subsidiaries(TI)reserve the right to make corrections,modifications,enhancements,improvements, and other changes to its products and services at any time and to discontinue any product or service without notice.Customers should obtain the latest relevant information before placing orders and should verify that such information is current and complete.All products are sold subject to TI’s terms and conditions of sale supplied at the time of order acknowledgment.TI warrants performance of its hardware products to the specifications applicable at the time of sale in accordance with TI’s standard warranty.Testing and other quality control techniques are used to the extent TI deems necessary to support this warranty.Except where mandated by government requirements,testing of all parameters of each product is not necessarily performed.TI assumes no liability for applications assistance or customer product design.Customers are responsible for their products and applications using TI components.To minimize the risks associated with customer products and applications,customers should provide adequate design and operating safeguards.TI does not warrant or represent that any license,either express or implied,is granted under any TI patent right,copyright,mask work right, or other TI intellectual property right relating to any combination,machine,or process in which TI products or services are rmation published by TI regarding third-party products or services does not constitute a license from TI to use such products or services or a warranty or endorsement e of such information may require a license from a third party under the patents or other intellectual property of the third party,or a license from TI under the patents or other intellectual property of TI.Reproduction of TI information in TI data books or data sheets is permissible only if reproduction is without alteration and is accompanied by all associated warranties,conditions,limitations,and notices.Reproduction of this information with alteration is an unfair and deceptive business practice.TI is not responsible or liable for such altered rmation of third parties may be subject to additional restrictions.Resale of TI products or services with statements different from or beyond the parameters stated by TI for that product or service voids all express and any implied warranties for the associated TI product or service and is an unfair and deceptive business practice.TI is not responsible or liable for any such statements.TI products are not authorized for use in safety-critical applications(such as life support)where a failure of the TI product would reasonably be expected to cause severe personal injury or death,unless officers of the parties have executed an agreement specifically governing such use.Buyers represent that they have all necessary expertise in the safety and regulatory ramifications of their applications,and acknowledge and agree that they are solely responsible for all legal,regulatory and safety-related requirements concerning their products and any use of TI products in such safety-critical applications,notwithstanding any applications-related information or support that may be provided by TI.Further,Buyers must fully indemnify TI and its representatives against any damages arising out of the use of TI products in such safety-critical applications.TI products are neither designed nor intended for use in military/aerospace applications or environments unless the TI products are specifically designated by TI as military-grade or"enhanced plastic."Only products designated by TI as military-grade meet military specifications.Buyers acknowledge and agree that any such use of TI products which TI has not designated as military-grade is solely at the Buyer's risk,and that they are solely responsible for compliance with all legal and regulatory requirements in connection with such use. TI products are neither designed nor intended for use in automotive applications or environments unless the specific TI products are designated by TI as compliant with ISO/TS16949requirements.Buyers acknowledge and agree that,if they use any non-designated products in automotive applications,TI will not be responsible for any failure to meet such requirements.Following are URLs where you can obtain information on other Texas Instruments products and application solutions:Products ApplicationsAmplifiers Audio /audioData Converters Automotive /automotiveDLP®Products Communications and /communicationsTelecomDSP Computers and /computersPeripheralsClocks and Timers /clocks Consumer Electronics /consumer-appsInterface Energy /energyLogic Industrial /industrialPower Mgmt Medical /medicalMicrocontrollers Security /securityRFID Space,Avionics&/space-avionics-defenseDefenseRF/IF and ZigBee®Solutions /lprf Video and Imaging /videoWireless /wireless-appsMailing Address:Texas Instruments,Post Office Box655303,Dallas,Texas75265Copyright©2010,Texas Instruments Incorporated。
55-CXS -SMX66EN Dual Rod Cylinder 55-CXS(J) Series
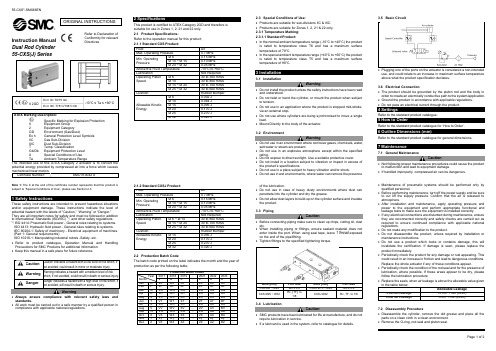
Instruction ManualDual Rod Cylinder 55-CXS(J) SeriesII 2 potential energy provided by compressed air into a force which causes Note 1: The X at the end of the certificate number represents that this product is subject to “Special Conditions of Use”, please see Section 2.3.1 Safety InstructionsThese safety instructions are intended to prevent hazardous situations and/or equipment damage. These instructions indicate the level of potential hazard with t he labels of “Caution,” “Warning” or “Danger.” They are all important notes for safety and must be followed in addition to International Standards (ISO/IEC) *1), and other safety regulations. *1)ISO 4414: Pneumatic fluid power - General rules relating to systems. ISO 4413: Hydraulic fluid power - General rules relating to systems.IEC 60204-1: Safety of machinery - Electrical equipment of machines. (Part 1: General requirements)ISO 10218-1: Manipulating industrial robots -Safety. etc.∙ Refer to product catalogue, Operation Manual and Handling Precautions for SMC Products for additional information. ∙ Keep this manual in a safe place for future reference.not avoided, will result in death or serious injury.Warning∙ Always ensure compliance with relevant safety laws and standards.∙ All work must be carried out in a safe manner by a qualified person incompliance with applicable national regulations.2 SpecificationsThis product is certified to ATEX Category 2GD and therefore is suitable for use in Zones 1, 2, 21 and 22 only. 2.1 Product Specifications:Refer to the operation manual for this product;2.1.2 Standard CXSJ Product: 2.2 Production Batch Code:The batch code printed on the label indicates the month and the year of production as per the following table;2.3 Special Conditions of Use:∙ Products are suitable for sub-divisions IIC & IIIC. ∙ Products are suitable for Zones 1, 2, 21 & 22 only. 2.3.1 Temperature Marking: 2.3.1.1 Standard Product:∙ In the normal ambient temperature range (-10°C to +40°C) the product is rated to temperature class T6 and has a maximum surface temperature of 78°C.∙ In the special ambient temperature range (+40°C to +60°C) the product is rated to temperature class T5 and has a maximum surface temperature of 98°C.3 Installation3.1 InstallationWarning∙ Do not install the product unless the safety instructions have been read and understood.∙ Do not twist or bend the cylinder, or mount the product when subject to tension.∙ Do not use in an application where the product is stopped mid-stroke, via an external stop.∙ Do not use where cylinders are being synchronised to move a single load.∙ Mount Directly to the body of the actuator.3.2 EnvironmentWarning∙ Do not use in an environment where corrosive gases, chemicals, water, salt water or steam are present.∙ Do not use in an explosive atmosphere except within the specified rating.∙ Do not expose to direct sunlight. Use a suitable protective cover.∙ Do not install in a location subject to vibration or impact in excess of the product’s specifications .∙ Do not use in a place subject to heavy vibration and/or shock.∙ Do not use in wet environments, where water can remove the presence of the lubrication.∙ Do not use in case of heavy dusty environments where dust can penetrate into the cylinder and dry the grease.∙ Do not allow dust layers to build up on the cylinder surface and insulate the product.3.3 PipingCaution∙ Before connecting piping make sure to clean up chips, cutting oil, dust etc.∙ When installing piping or fittings, ensure sealant material does not enter inside the port. When using seal tape, leave 1 thread exposed on the end of the pipe/fitting.∙ Tighten fittings to the specified tightening torque.Bore [mm] Port Size Bore [mm] Port Size 3.4 LubricationCaution∙ SMC products have been lubricated for life at manufacture, and do not require lubrication in service.∙ If a lubricant is used in the system, refer to catalogue for details.3.5 Basic Circuit∙ Plugging one of the ports on the actuator is considered a non-intended use, and could relate to an increase in maximum surface temperature above what the product specification declares.3.6 Electrical Connection∙ The product should be grounded by the piston rod and the body in order to create an electrically conductive path to the system/application. ∙ Ground the product in accordance with applicable regulations. ∙ Do not pass an electrical current through the product.4 SettingsRefer to the standard product catalogue.5 How to OrderRefer to the standard product catalogue for ‘How to Order’.6 Outline Dimensions (mm)Refer to the standard product catalogue for general dimensions.7 Maintenance7.1 General MaintenanceCaution∙ Not following proper maintenance procedures could cause the product to malfunction and lead to equipment damage.∙ If handled improperly, compressed air can be dangerous.∙ Maintenance of pneumatic systems should be performed only by qualified personnel.∙ Before performing maintenance, turn off the power supply and be sure to cut off the supply pressure. Confirm that the air is released to atmosphere.∙ After installation and maintenance, apply operating pressure and power to the equipment and perform appropriate functional and leakage tests to make sure the equipment is installed correctly.∙ If any electrical connections are disturbed during maintenance, ensure they are reconnected correctly and safety checks are carried out as required to ensure continued compliance with applicable national regulations.∙ Do not make any modification to the product.∙ Do not disassemble the product, unless required by installation or maintenance instructions.∙ Do not use a product which looks or contains damage, this will invalidate the certification. If damage is seen, please replace the product immediately.∙ Periodically check the product for any damage or rust appearing. This could result in an increase in friction and lead to dangerous conditions. Replace the whole actuator if any of these conditions appear.∙ Periodically check the condition of the rod seal and for the presence of lubrication, where possible. If these areas appear to be dry, please follow the lubrication procedure.∙ Replace the seals, when air leakage is above the allowable value given 7.2 Disassembly Procedure∙ Disassemble the cylinder, remove the old grease and place all the parts on a clean cloth in a clean environment. ∙ Remove the O-ring, rod seal and piston seal.ORIGINAL INSTRUCTIONSRefer to Declaration of Conformity for relevant DirectivesNote 1: CXSJM and CXSJL are similar construction just more compact.7.3 Seal Replacement Part NumbersWarningOnly use SMC seal kits as listed in the table below;Caution∙ A wear ring is not fitted to double rod cylinders.7.4 Lubrication Procedure∙Apply lubricant to:• The rod seal• The rod seal groove on the rod cover.• The piston outer su rface and piston seal groove.• The piston rod surface and cylinder tube internal surface.∙Lubricate the parts with the grease packs provided with the seal kit.7.5 Reassembly Procedure∙Reassembly should be completed in the following order;• Head Cover Assembly (In case of CXSJ),• Snap Ring on the Head Cover Side,• Piston Rod Assembly,• Rod Cover Assembly / Ball Pushing Assembly,• Snap ring on the Rod Cover side,• Plate.∙When assembling the plate, supply air to the cylinder till it is extended.• Tighten the hexagon socket head cap bolt first, and then thehexagon socket head set screw.∙Use the following torque for tightening the hexagon socket head capbolt and hexagon socket head set screw.∙Before re-installing the cylinder back into the machine, check forsmooth movement and check for air leakage.8 Limitations of Use8.1 Limited warranty and Disclaimer/Compliance RequirementsRefer to Handling Precautions for SMC Products located on .8.2 Obligations of the end-user∙Ensure the product is used within the specification outlined.∙Ensure that the maintenance periods are suitable for the application.∙Ensure any cleaning processes to remove dust layers are made withthe atmosphere in mind (e.g. using a damp cloth to avoid static buildup).∙Ensure that the application does not introduce additional hazards bymounting, loading, impacts or other methods.∙Ensure that there is sufficient ventilation and air circulation around theproduct.∙If the product is subject to direct heat sources in the application, theyshould be shielded so that the actuator temperature stays within thestated operating range.Caution∙SMC products are not intended for use as instruments for legalmetrology.Measurement instruments that SMC manufactures or sells have notbeen qualified by type approval tests relevant to the metrology(measurement) laws of each country.Danger∙Do not exceed any of the specifications listed in Section 2 of thisdocument as this will be deemed improper use.∙Air equipment has an air leakage during operation within certain limits.Do not use this equipment when the air itself introduces additionalhazards and could lead to an explosion.∙Use only ATEX certified auto switches. These should be orderedseparately.∙Do not use this product in the presence of strong magnetic fields thatcould generate a surface temperature higher than the productspecification.∙Avoid applications where the piston rod end and the adjoining part inthe application can create a possible ignition source.∙Do not install or use these actuators where there is the possibility forthe piston rod to impact foreign objects.∙In the event of damage or failure of any parts located in the vicinitywhere this product has been installed, it is the responsibility of the userto determine whether or not this has compromised the safety andcondition of this product and/or the application.∙External impact on the cylinder body could result in a spark and/orcylinder damage. Avoid any application where foreign objects can hitor impact the cylinder. In such situations the application should installa suitable guard to prevent this occurrence.∙Do not use this equipment where vibration could lead to failure.9 ContactsRefer to Declaration of Conformity and for contacts.URL : http// (Global) http// (Europe)'SMC Corporation, Akihabara UDX15F, 4-14-1, Sotokanda, Chiyoda-ku, Tokyo 1010021Specifications are subject to change without prior notice from the manufacturer.© 2018 SMC Corporation All Rights Reserved.Template DKP50047-F-085H。
X20(c)DO6322数据手册 V3.23说明书

X20(c)DO63221 General informationThe module is equipped with 6 outputs for 1 or 2-wire connections. The X20 6-pin terminal block can be used for universal 1-line wiring. 2-line wiring can be implemented using the 12-pin terminal block. The module is designed for source output wiring.•6 digital outputs•Source connection•2-wire connections•GND for signal supply•Integrated output protection•1-wire connection type with 6-pin terminal block•OSP mode2 Coated modulesCoated modules are X20 modules with a protective coating for the electronics component. This coating protects X20c modules from condensation and corrosive gases.The modules' electronics are fully compatible with the corresponding X20 modules.For simplification purposes, only images and module IDs of uncoated modules are used in this data sheet.The coating has been certified according to the following standards:•Condensation: BMW GS 95011-4, 2x 1 cycle•Corrosive gas: EN 60068-2-60, Method 4, exposure 21 days3 Order dataTable 1: X20DO6322, X20cDO6322 - Order data4 Technical dataTable 2: X20DO6322, X20cDO6322 - Technical dataTable 2: X20DO6322, X20cDO6322 - Technical data1)Number of outputs x R DS(on) x Nominal output current 2 (A calculation example can be found on the B&R website in the download area for the module.)2)At loads ≤ 1 kΩ5 Status LEDsFor a description of the various operating modes, see section "Additional information - Diagnostic LEDs" of theX20 system user's manual.6 Pinout1X 20 D O 632223456r e7 Connection exampleCaution!If the module is operated outside of specifications, the output current can increase above the maximum permissible nominal current. This applies to individual channels and also to the summation current for the module.Therefore sufficient cable cross sections or external safety measures must be used.8 OSP hardware requirementsIn order to best use OSP mode, make sure when creating the application that the output module and CPU have separate power supplies.9 Output circuit diagram10 Switching inductive loadsEnvironmental temperature: 60°C, all outputs with the same load500.11101001000Coil inductance100 mH1 H10 H100 H10 mHCoil resistance[Ω]100Max. switching cycles / second(with 90% duty cycle)28.8 V 24.0 VSwitching voltage:Information:If the maximum number of operating cycles per second is exceeded, an external inverse diode must be used.Operating conditions outside of the area in the diagram are not permitted!11 Register description11.1 General data pointsIn addition to the registers listed in the register description, the module also has other more general data points. These registers are not specific to the module but contain general information such as serial number and hardware version.These general data points are listed in section "Additional information - General data points" of the X20 system user's manual.11.2 Function model 0 - StandardFixed modules require their data points to be in a specific order in the X2X frame. Cyclic access occurs according to a predefined offset, not based on the register address.Acyclic access continues to be based on the register numbers.11.3 Function model 1 - OSPFixed modules require their data points to be in a specific order in the X2X frame. Cyclic access occurs according to a predefined offset, not based on the register address.Acyclic access continues to be based on the register numbers.11.4 Function model 254 - Bus Controller1)The offset specifies where the register is within the CAN object.11.4.1 CAN I/O bus controllerThe module occupies 1 digital logical slot on CAN I/O.11.5 Digital outputsThe output status is transferred to the output channels with a fixed offset (<60 µs) in relation to the network cycle (SyncOut).11.5.1 Switching state of digital outputs 1 to 6Name:DigitalOutputDigitalOutput01 to DigitalOutput06The switching state of digital outputs 1 to 6 are stored in this register.Function model 0 - Standard only:The "Packed outputs" setting in the Automation Studio I/O configuration is used to determine whether all of this registers' bits should be set up individually as data points in the Automation Studio I/O mapping ("DigitalOutput01" through "DigitalOutput0x") or whether this register should be displayed as an individual USINT data point ("Digi-talOutput").Bit structure:11.6 Monitoring status of the digital outputsOn the module, the output states of the outputs are compared to the target states. The control of the output driver is used for the target state.A change in the output state resets monitoring for that output. The status of each individual channel can be read.A change in the monitoring status generates an error message.11.6.1 Status of digital outputs 1 to 6Name:StatusInput01StatusDigitalOutput01 to StatusDigitalOutput06The status of digital outputs 1 to 6 is mapped in this register.Function model 0 - Standard only:The "Packed outputs" setting in the Automation Studio I/O configuration is used to determine whether all of this registers' bits should be set up individually as data points in the Automation Studio I/O mapping ("StatusDigitalOut-put01" through "StatusDigitalOutput0x") or whether this register should be displayed as an individual USINT data point ("StatusInput01").Bit structure:11.7 "OSP" function modelIn the "OSP" function model (Operator Set Predefined), the user defines an analog value or digital pattern. This OSP value is output as soon as communication between the module and master is interrupted.FunctionalityThe user can choose between 2 OSP modes:•Retain last valid value•Replace with static valueIn the first case, the module retains the last value as validly recognized output state.When selecting the mode, "Replace with static value" a plausible output value must be entered in the corresponding value register. If an OSP event occurs, this value will be output instead of the value currently requested by the task.11.7.1 Activating the OSP output in the moduleName:OSPValidThis data point offers the possibility to start module output and request OSP operation during running operation.Bit structure:There is one OSPValid bit on the module, which is managed by the user task. It must be set when the enabled channels are started. As long as the OSPValid bit remains set in the module, the module behaves the same as the "Standard" function model.If an OSP event occurs (e.g. communication between the module and master CPU interrupted) then the OSPValid bit will be reset on the module. The module enters OSP mode and the output occurs in the register "OSPMode" on page 9 according to the configuration.The following applies:The OSP replacement value remains even after the communication channel has recovered. OSP mode is only exited when a set OSPValid bit is transferred.When the master CPU is restarted, the OSPValid bit is re-initialized on the master CPU. It must once more be set by the application and transferred via the bus.When temporary communication errors occur between the module and master CPU (e.g. due to EMC),a few bus cycles will pass without refreshing the cyclic registers. The OSPValid bit is reset internally inthe module - the bit in the CPU however remains set. Upon the next successful transfer, the OSPValid bit in the module is set again and the module returns to normal operation.The ModulOK bit can be evaluated if the task in the master CPU needs to know which output mode the module is currently in.Warning!If the OSPValid bit is reset to "0" on the module, then the output state no longer depends on the responsible task in the master CPU. However, output still occurs according to the configuration of the OSP replacement value.11.7.2 Setting the OSP modeName:CfgOSPModeThis register essentially controls a channel's behavior when OSP is being used.11.7.3 Define the OSP digital output valueName:CfgOSPValueThis register contains the digital output value, which is output in "Replace with static value" mode during OSP operation.Bit structure:Warning!The "OSPValue" is not accepted by the module until the "OSPValid" bit has been set in the module.11.8 Minimum cycle timeThe minimum cycle time defines how far the bus cycle can be reduced without communication errors occurring. Note that very fast cycles decrease the idle time available for handling monitoring, diagnostics and acyclic com-mands.11.9 Minimum I/O update timeThe minimum I/O update time defines how far the bus cycle can be reduced while still allowing an I/O update to take place in each cycle.。
凝固化剂 CoolTherm SC-320 新型型号说明书

USA SAFETY DATA SHEET1. CHEMICAL PRODUCT AND COMPANY IDENTIFICATIONProduct name:CoolTherm SC-320 THK RESINProduct Use/Class: Encapsulant, Part AReference: Our thermal management products are now named CoolTherm (Registered Trademark). Some of our Gelease, Circalok and Thermoset products are included under this new brand.LORD Corporation111 LORD DriveCary, NC 27511-7923 USATelephone: 814 868-3180Non-Transportation Emergency: 814 763-2345Chemtrec 24 Hr Transportation Emergency No.800 424-9300 (Outside Continental U.S. 703 527-3887)EFFECTIVE DATE: 12/18/20202. HAZARDS IDENTIFICATIONGHS CLASSIFICATION:Serious eye damage/eye irritation Category 2BHazardous to the aquatic environment - acute hazard Category 2Hazardous to the aquatic environment - chronic hazard Category 2GHS LABEL ELEMENTS:Symbol(s)Signal WordW ARNINGHazard StatementsCauses eye irritation.Toxic to aquatic life.Toxic to aquatic life with long lasting effects.Precautionary StatementsPreventionWash thoroughly after handling.Avoid release to the environment.ResponseIF IN EYES: Rinse cautiously with water for several minutes. Remove contact lenses, if present and easy to do.Continue rinsing.If eye irritation persists: Get medical advice/attention.Collect spillage.StorageRefer to Section 7 of this SDS.Disposal:Dispose of contents/container in accordance with waste/disposal laws and regulations of your country or particular locality.Other Hazards:300001008445This product contains component(s) which have the following warnings; however based on the GHS classification criteria of your country or locale, the product mixture may be outside the respective category(s).Acute: May be harmful if swallowed. Ingestion is not an expected route of entry in industrial or commercial uses.Do not breathe sanding dust.May cause mild skin irritation.Chronic: This product contains methylpolysiloxanes which can generate formaldehyde at approximately 300degrees F (150 C) and above, in atmospheres which contain oxygen. Formaldehyde is a skin and respiratorysensitizer, eye and throat irritant, acute toxicant, and known cancer hazard. Workplace exposure to formaldehyde is regulated by OSHA Standard 29 CFR 1910.1048.withheld.FIRST AID - EYE CONTACT: Flush eyes immediately with large amount of water for at least 15 minutes holding eyelids open while flushing. Get prompt medical attention.FIRST AID - SKIN CONTACT: Flush contaminated skin with large amounts of water while removing contaminated clothing. Wash affected skin areas with soap and water. Get medical attention if symptoms occur.FIRST AID - INHALATION: This material is not likely to be hazardous by inhalation. However, if exposed to excessive levels of vapor or mist, remove to fresh air, give oxygen if breathing is difficult, and get immediate medical attention. FIRST AID - INGESTION: If swallowed, do not induce vomiting. Call a physician or poison control center immediately for further instructions. Never give anything by mouth if victim is rapidly losing consciousness, unconscious or convulsing.SUITABLE EXTINGUISHING MEDIA: Carbon Dioxide, Dry Chemical, Foam, Water FogUNSUITABLE EXTINGUISHING MEDIA: Not determined for this product.SPECIFIC HAZARDS POSSIBLY ARISING FROM THE CHEMICAL: Keep containers tightly closed. Closed containers may rupture when exposed to extreme heat. Use water spray to keep fire exposed containers cool. During a fire, irritating and/or toxic gases and particulate may be generated by thermal decomposition or combustion.SPECIAL PROTECTIVE EQUIPMENT AND PRECAUTIONS FOR FIRE-FIGHTERS: Wear full firefighting protective clothing, including self-contained breathing apparatus (SCBA). If water is used, fog nozzles are preferable.PERSONAL PRECAUTIONS, PROTECTIVE EQUIPMENT AND EMERGENCY PROCEDURES: Avoid breathing vapors. Avoid contact.ENVIRONMENTAL PRECAUTIONS: Do not contaminate bodies of water, waterways, or ditches, with chemical or used container.METHODS AND MATERIALS FOR CONTAINMENT AND CLEANUP: Notify appropriate authorities if necessary. Contain and remove with inert absorbent material. Avoid contact. Keep non-essential personnel away from spill area. Before attempting cleanup, refer to hazard caution information in other sections of the SDS form.HANDLING: Keep closure tight and container upright to prevent leakage. Avoid skin and eye contact. Wash thoroughly after handling. Do not handle until all safety precautions have been read and understood. Empty containers should not be re-used. Use with adequate ventilation. Avoid breathing sanding dust from this product.STORAGE: Avoid excessive heat. Avoid moisture contamination. Store only in well-ventilated areas. Keep container closed when not in use.INCOMPATIBILITY: Strong acids, bases, and strong oxidizers.Engineering controls: Provide adequate general ventilation where this product is used.PERSONAL PROTECTION MEASURES/EQUIPMENT:RESPIRATORY PROTECTION: Respiratory protection is not required under normal working conditions where adequate ventilation is present. Note: If the exposure limit for formaldehyde is exceeded, a formaldehyde-specific, formaldehyde/organic vapor combination, or airline respirator may be required.SKIN PROTECTION: Use neoprene, nitrile, or rubber gloves to prevent skin contact.EYE PROTECTION: Use safety eyewear including safety glasses with side shields and chemical goggles where splashing may occur.OTHER PROTECTIVE EQUIPMENT: Remove and wash contaminated clothing before reuse.HYGIENIC PRACTICES: Wash hands before eating, smoking, or using toilet facility. Do not smoke in anychemical handling or storage area. Food or beverages should not be consumed anywhere this product is handled or stored. Wash thoroughly after handling.Typical values, not to be used for specification purposes.ODOR: Odorless VAPOR PRESSURE: N.D.APPEARANCE: Pink VAPOR DENSITY: Heavier than Air PHYSICAL STATE: Liquid LOWER EXPLOSIVE LIMIT: Not ApplicableUPPER EXPLOSIVE LIMIT: Not ApplicableFLASH POINT:≥ 201 °F, 93 °CSetaflash Closed CupBOILING RANGE: N.A.EVAPORATION RATE: Slower than n-butyl-acetate AUTOIGNITION TEMPERATURE:N.D.DENSITY: 3.03 g/cm3 (25.23 lb/gal) DECOMPOSITION TEMPERATURE:N.D. VISCOSITY, DYNAMIC: ≥50,000 mPa.s @ 25 °C ODOR THRESHOLD: N.D.VISCOSITY, KINEMATIC: ≥16,502 mm2/s @ 25 °CSOLUBILITY IN H2O: Insoluble VOLATILE BY WEIGHT: 0.00 %pH: N.A.VOLATILE BY VOLUME: 0.00 %FREEZE POINT: N.D. VOC CALCULATED: 0 lb/gal, 0 g/lN.D.COEFFICIENT OF WATER/OILDISTRIBUTION:LEGEND: N.A. - Not Applicable, N.E. - Not Established, N.D. - Not DeterminedHAZARDOUS POLYMERIZATION: Hazardous polymerization will not occur under normal conditions. STABILITY: Product is stable under normal storage conditions.CONDITIONS TO AVOID: Moisture.; High temperatures.INCOMPATIBILITY: Strong acids, bases, and strong oxidizers.HAZARDOUS DECOMPOSITION PRODUCTS: Carbon monoxide, carbon dioxide, Oxides of silicon, Metal oxides, Organic acid vapors, FormaldehydeEXPOSURE PATH: Refer to section 2 of this SDS.SYMPTOMS:Refer to section 2 of this SDS.TOXICITY MEASURES:Germ cell mutagenicity: No classification proposedCarcinogenicity: No classification proposedReproductive toxicity: No classification proposedPERSISTENCE AND DEGRADABILITY:Not determined for this product.BIOACCUMULATIVE: Not determined for this product.MOBILITY IN SOIL: Not determined for this product.OTHER ADVERSE EFFECTS: Not determined for this product.DISPOSAL METHOD: Disposal should be done in accordance with Federal (40CFR Part 261), state and local environmental control regulations. If waste is determined to be hazardous, use licensed hazardous waste transporter and disposal facility.US DOT RoadProper Shipping Name: Environmentally hazardous substances, liquid, n.o.s.Hazard Class: 9SECONDARY HAZARD: NoneUN/NA Number: 3082Packing Group: IIIEmergency Response Guide Number: 171For US DOT non-bulk road shipments this material may be classified as NOT REGULATED. For the mostaccurate shipping information, refer to your transportation/compliance department regarding changes inpackage size, mode of shipment or other regulatory descriptors.IATA CargoPROPER SHIPPING NAME: Environmentally hazardous substance, liquid, n.o.s.Hazard Class: 9HAZARD CLASS: NoneUN NUMBER: 3082PACKING GROUP: IIIEMS: 9LIMDGPROPER SHIPPING NAME: Environmentally hazardous substance, liquid, n.o.s.Hazard Class: 9HAZARD CLASS: NoneUN NUMBER: 3082PACKING GROUP: IIIEMS: F-AThe listed transportation classification applies to non-bulk shipments. It does not address regulatory variations due to changes in package size, mode of shipment or other regulatory descriptors. For the most accurate shipping information, refer to your transportation/compliance department.U.S. FEDERAL REGULATIONS: AS FOLLOWS:SARA SECTION 313This product contains the following substances subject to the reporting requirements of Section 313 of Title III of the Superfund Amendment and Reauthorization Act of 1986 and 40 CFR part 372.:Chemical Name CAS Number Weight % Less ThanZinc oxide1314-13-225.0%TOXIC SUBSTANCES CONTROL ACT:INVENTORY STATUSThe chemical substances in this product are on the TSCA Section 8 Inventory.EXPORT NOTIFICATIONThis product contains the following chemical substances subject to the reporting requirements of TSCA 12(B) if exported from the United States:NoneUnder HazCom 2012 it is optional to continue using the HMIS rating system. It is important to ensure employees have been trained to recognize the different numeric ratings associated with the HazCom 2012 and HMIS schemes.HMIS RATINGS - HEALTH: 1* FLAMMABILITY: 1 PHYSICAL HAZARD: 0* - Indicates a chronic hazard; see Section 2Revision: Company Logo, Section 2Effective Date: 12/18/2020The information contained herein is, to the best of our knowledge and belief, accurate. However, since the conditions of handling and use are beyond our control, we make no guarantee of results, and assume no liability for damages incurred by use of this material. It is the responsibility of the user to comply with all applicable federal, state and local laws and regulations.。
Siemens SCALANCE X204-2 产品数据手册说明书

Product data sheet6GK5204-2BB10-2AA3 Product-type designation SCALANCE X204-2SCALANCE X204-2, MANAGED IE SWITCH,4 X 10/100MBIT/S RJ45 PORTS,2 X 100MBIT/S MULTIMODE BFOC,LED DIAGNOSTICS,ERROR SIGNAL CONTACT WITH SET BUTTON,REDUNDANT POWER SUPPLY,PROFINET-IO DEVICE, NETWORK MANAGEMENT,INTEGRATED REDUNDANCY MANAGER,INCL. ELECTRONIC MANUAL ON CD,C-PLUG OPTIONALTransfer rate / 110 Mbit/sTransfer rate / 2100 Mbit/sNumber of electrical/optical connections• for network components or terminal equipment / maximum6Number of electrical connections• for network components and terminal equipment4• for signaling contact1• for power supply1• for redundant power supply1Design of the electrical connection• for network components and terminal equipment RJ45 port• for signaling contact2-pole terminal block• for power supply4-pole terminal blockNumber of optical interfaces / for optical waveguide / at 100 Mbit/s2Design of optical interface / for optical waveguide / at 100 Mbit/s BFOC sockets (multimode up to 5 km)Connectable optical power relative to 1 mW• of the transmitter output-19 … -14 dBOptical sensitivity relative to 1 mW / of the receiver input / minimum-34 dBAttenuation / of fiber-optic cable transmission link / minimum0 dBnecessaryRange / at the optical interface / depending on the optical fiber used0 … 5 kmdesign of the removable storage / C-PLUG YesOperating voltage / of signaling contacts / at DC / rated value24 VOperating current / of signaling contacts / at DC / maximum0.1 AType of / supply voltage DCSupply voltage / external24 V• minimum18 V• maximum32 VProduct component / fusing at power supply input YesType of fusing / at input for supply voltage0,6 A / 60 VConsumed current / maximum0.265 AActive power loss / at 24 V / for DC 6.36 WAmbient temperature• during operating-40 … +60 °C• during storage-40 … +70 °C• during transport-40 … +70 °CRelative humidity / at 25 °C / without condensation / during operating95 %/ maximumProtection class IP IP30Design compactWidth60 mmHeight125 mmDepth124 mmNet weight0.78 kgMounting type• 35 mm DIN rail mounting Yes• wall mounting Yes• S7-300 rail mounting Yes50Cascading in the case of a redundant ring / at reconfiguration time of<\~0.3\~sCascading in cases of star structuring Any (depending only on signal propagation time) Product function• CLI Yes• web-based management Yes • MIB support Yes • TRAPs via email Yes • Configuration with STEP 7Yes • Port mirroring Yes • for IRT / PROFINET IO switch No • PROFINET IO diagnosis Yes • switch-managed Yes Protocol / is supported• Telnet Yes • HTTP Yes • HTTPS Yes • TFTP Yes • FTP Yes • BOOTP No • SNMP v1Yes • SNMP v2Yes • SNMP v3Yes • DCP Yes • LLDP Yes Identification & maintenance function• I&M0 - device-specific information Yes • I&M1 – higher level designation/location designation YesProduct function• Port diagnostics Yes • Statistics Packet Size Yes • Statistics packet type Yes • Error statistics YesProduct function / DHCP client YesProduct function• Ring redundancy Yes • Redundancy manager Yes • Standby redundancy No • High Speed Redundancy Protocol (HRP)Yes • Media Redundancy Protocol (MRP)Yes • Parallel Redundancy Protocol (PRP)No• Passive listening YesProtocol / is supported / PRP YesProtocol / is supported / SSH YesProduct function / SICLOCK support YesProtocol / is supported• NTP No• SNTP YesStandard• for EMC / from FM FM3611: Class 1, Division 2, Group A, B, C, D / T4, CL.1, Zone 2,GP. IIC, T4• for hazardous zone EN 60079-0: 2006, EN60079-15: 2005, II 3 (2) G Ex nA [op is] IICT4, KEMA 07 ATEX 0145 X• for safety / of CSA and UL UL 60950-1, CSA C22.2 No. 60950-1• for hazardous area / of CSA and UL ANSI / ISA 12.12.01, CSA C22.2 No. 213-M1987, CL. 1 / Div. 2 / GP.A, B, C, D T4, CL. 1 / Zone 2 / GP. IIC, T4• for emitted interference EN 61000-6-4:2001 (Class A)• for interference immunity EN 61000-6-4:2001Verification of suitability EN 61000-6-4:2001• CE mark Yes• C-Tick Yes• KC approval Yes• Railway application in accordance with EN 50155No• Railway application in accordance with EN 50124-1NoMarine classification association• American Bureau of Shipping Europe Ltd. (ABS)Yes• Bureau Veritas (BV)Yes• Det Norske Veritas (DNV)Yes• Germanische Lloyd (GL)Yes• Lloyds Register of Shipping (LRS)Yes• Nippon Kaiji Kyokai (NK)Yes• Polski Rejestr Statkow (PRS)YesInternet-Link• to website: Industry Mall /industrial-controls/mall• to website: Industrial communication /simatic-net• to website: Information and Download Center /automation/net/catalog• to website: Image database /bilddb• to website: CAx Download Manager /cax• to website: Industry Online Support Security information Siemens provides products and solutions with industrial securityfunctions that support the secure operation of plants, solutions,machines, equipment and/or networks. They are importantcomponents in a holistic industrial security concept. With this inmind, Siemens’ products and solutions undergo continuousdevelopment. Siemens recommends strongly that you regularlycheck for product updates. For the secure operation of Siemensproducts and solutions, it is necessary to take suitable preventiveaction(e.g. cell protection concept) and integrate each componentinto a holistic, state-of-the-art industrial security concept. Third-partyproducts that may be in use should also be considered. For moreinformation about industrial security, visit/industrialsecurity. To stay informed aboutproduct updates as they occur, sign up for a product-specificnewsletter. For more information, visit. Version 3.4 – 14.11.2013-Siemens AG, I IA L CG, Nurembergletzte Änderung:Jun 16, 2014。
X24320PIG-1.8资料

元器件交易网This X24320 device has been acquired by IC MICROSYSTEMS from Xicor, Inc.ICmicTMIC MICROSYSTEMS32KX24320400KHz 2-Wire Serial E PROM with Block Lock2 TM4K x 8 BitFEATURES•Save Critical Data with ProgrammableBlock Lock Protection 2 —Block Lock (0, 1/4, 1/2, or all of E PROM Array) —Software Write ProtectionDESCRIPTION 2 The X24320 is a CMOS Serial E PROM, internally organized 4K x 8. The device features a serial interface and software protocol allowing operation on a simple two wire bus. The bus operates at 400 KHz all the way down to 1.8V. Three device select inputs (S0–S2) allow up to eight devices to share a common two wire bus. A Write Protect Register at the highest address location, FFFFh, provides three write protection features: Software Write Protect, Block Lock Protect, and Programmable Hardware Write Protect. The Software Write Protect feature prevents any nonvolatile writes to the device until the WEL bit in the Write Protect Register is set. The Block Lock Protection feature gives the user four array block protect options, set by programming two bits in the Write Protect Register. The Programmable Hardware Write Protect feature allows the user to install the device with WP tied to VCC, write to and Block Lock the desired portions of the memory array in circuit, and then enable the In Circuit Programmable ROM Mode by programming the WPEN bit HIGH in the Write Protect Register. After this, the Block Locked portions of the array, including the Write Protect Register itself, are permanently protected from being erased.•In Circuit Programmable ROM Mode •400KHz 2-Wire Serial Interface—Programmable Hardware Write Protect—Schmitt Trigger Input Noise Suppression —Output Slope Control for Ground BounceNoise Elimination •Longer Battery Life With Lower Power —Active Read Current Less Than 1mA —Active Write Current Less Than 3mA —Standby Current Less Than 1µA •1.8V to 3.6V, 2.5V to 5.5V and 4.5V to 5.5V Power Supply Versions •32 Word Page Write Mode —Minimizes Total Write Time Per Word•Internally Organized 4K x 8 •Bidirectional Data Transfer Protocol •Self-Timed Write Cycle—Typical Write Cycle Time of 5ms •High Reliability —Endurance: 100,000 Cycles —Data Retention: 100 Years•8-Lead SOIC •14-Lead TSSOP •8-Lead PDIPFUNCTIONAL DIAGRAMSERIAL E PROM DATA AND ADDRESS (SDA)2DATA REGISTER Y DECODE LOGICCOMMAND DECODE AND CONTROLSERIAL E PROM ARRAY2SCLPAGE DECODE4K x 8 1K x 8LOGICBLOCK LOCK AND WRITE PROTECT CONTROL LOGICLOGIC1K x 8WRITE PROTECTS2 S1 S0DEVICE SELECTLOGICREGISTER2K x 8WPWRITE VOLTAGE CONTROL7035 FM 01©Xicor, 1995, 1996 Patents Pending 7035-1.2 4/25/97 T0/C2/D0 SH1Characteristics subject to change without notice元器件交易网X24320Xicor E PROMs are designed and tested for applications requiring extended endurance. Inherent data2PIN NAMES SymbolS0, S1, S2 SDA SCL WP VSS VCC NCretention is greater than 100 years.PIN DESCRIPTIONS Serial Clock (SCL)DescriptionDevice Select Inputs Serial Data Serial Clock Write Protect Ground Supply Voltage No Connect7035 FM T01The SCL input is used to clock all data into and out of the device.Serial Data (SDA) SDA is a bidirectional pin used to transfer data into and out of the device. It is an open drain output and may be wire-ORed with any number of open drain or open collector outputs. An open drain output requires the use of a pull-up resistor. For selecting typical values, refer to the Pullup resistor selection graph at the end of this data sheet. Device Select (S0, S1, S2) The device select inputs (S0, S1, S2) are used to set the first three bits of the 8-bit slave address. This allows up to eight devices to share a common bus. These inputs can be static or actively driven. If used statically they must be tied to VSS or VCC as appropriate. If actively driven, they must be driven with CMOS levels (driven to VCC or VSS). Write Protect (WP) The Write Protect input controls the Hardware Write Protect feature. When held LOW, Hardware Write Protection is disabled. When this input is held HIGH, and the WPEN bit in the Write Protect Register is set HIGH, the Write Protect Register is protected, preventing changes to the Block Lock Protection andPIN CONFIGURATIONNot to scale 8-Lead DIP/SOICS 0S1 2 3 4 * .244” X243208 7 6 5V* .197”1 2CC WPSV SSSCL SDA14-Lead TSSOPS 01 NC S1 2 3 4 5 6 7 .252”14 13 12 X24320 11 10 9 8V CC WP.200”NC NCV SS S 2NC NCNC SCL SDAWPEN bits.* SOIC Measurement7035 FM 022元器件交易网X24320Clock and Data Conventions Data states on the SDA line can change only during SCL LOW. SDA state changes during SCL HIGH are reserved for indicating start and stop conditions. Refer to Figures 1 and 2. Start Condition All commands are preceded by the start condition, which is a HIGH to LOW transition of SDA when SCL is HIGH. The device continuously monitors the SDA and SCL lines for the start condition and will not respond to any command until this condition has been met.DEVICE OPERATION The device supports a bidirectional bus oriented protocol. The protocol defines any device that sends data onto the bus as a transmitter, and the receiving device as the receiver. The device controlling the transfer is a master and the device being controlled is the slave. The master will always initiate data transfersand provide the clock for both transmit and receive operations. Therefore, the device will beconsidered a slave in all applications.Figure 1. Data ValiditySCLSDA DATA STABLE DATA CHANGE7035 FM 03Figure 2. Definition of Start and StopSCLSDA START BIT STOP BIT7035 FM 043元器件交易网X24320Stop ConditionAll communications must be terminated by a stop condition, which is a LOW to HIGH transition of SDA when SCL is HIGH. The stop condition is also used to place the device into the standby power mode after a read sequence. A stop condition can only be issued after the transmitting device has released the bus. Acknowledge Acknowledge is a software convention used to indicate successful data transfer. The transmitting device, either master or slave, will release the bus after trans- mitting eight bits. During the ninth clock cycle the receiver will pull the SDA line LOW to acknowledge that it received the eight bits of data. Refer to Figure 3. The device will respond with an acknowledge after recognition of a start condition and its slave address. If both the device and a write operation have been selected, the device will respond with an acknowledge after the receipt of each subsequent 8-bit word. In the read mode the device will transmit eight bits of data, release the SDA line and monitor the line for an acknowledge. If an acknowledge is detected and no stop condition is generated by the master, the device will continue to transmit data. If an acknowledge is not detected, the device will terminate further data transmissions. The master must then issue a stop condition return the device to the standby power mode and place the device into a known state. toFigure 3. Acknowledge Response From ReceiverSCL FROM MASTER189DATA OUTPUT FROMTRANSMITTERDATA OUTPUT FROM RECEIVERSTARTACKNOWLEDGE7035 FM 054元器件交易网X24320DEVICE ADDRESSING Following a start condition, the master must output the address of the slave it is accessing. The first four bits of the Slave Address Byte are the device type identifier bits. These must equal “1010”. The next 3 bits are the device select bits S0, S1, and S2. This allows up to 8 devices to share a single bus. These bits arecompared to the S0, S1, and S2 device select input pins. The last bit of the Slave Address Byte defines thedevice select input pins. If the compare is not successful, no acknowledge is output during the ninth clock cycle and the device returns to the standby mode. The word address is either supplied by the master or obtained from an internal counter, depending on the operation. The master must supply the two Word Address Bytes as shown in figure 4. The internal organization of the E array is 128 pages by 32 bytes per page. The page address is partially contained in the Word Address Byte 1 and partially in bits 7 through 5 of the Word Address Byte 0. The byte address is contained in bits 4 through 0 of the Word Address Byte 0. See figure 4.2operation to be performed. When the R/W bit is a one, then a read operation is selected. When it is zero thena write operation is selected. Refer to figure 4. After loading the Slave Address Byte from the SDA bus, the device compares the device type bits with the value “1010” and the device select bits with the status of theFigure 4. Device AddressingDEVICE TYPE IDENTIFIERDEVICE SELECT1010S 2S 1S 0R/WSLAVE ADDRESS BYTEHIGH ORDER WORD ADDRESS0000A11A10A9A8X24320 WORD ADDRESS BYTE 1LOW ORDER WORD ADDRESSA7A6A5A4A3A2A1A0WORD ADDRESS BYTE 0D7D6D5D4D3D2D1D0DATA BYTE7035 FM 065元器件交易网X24320WRITE OPERATIONS Byte Write For a write operation, the device requires the Slave Address Byte, the Word Address Byte 1, and the Word Address Byte 0, which gives the master access to any one of the words in the array. Upon receipt of the Word Address Byte 0, the device responds with an acknowledge, and waits for the first eight bits of data. After receiving the 8 bits of the data byte, the device again responds with an acknowledge. The master then terminates the transfer by generating a stop condition, at which time the device begins the internal write cycle to the nonvolatile memory. While the internal write cycle is in progress the device inputs are disabled and the device will not respond to any requests from the master. The SDA pin is at high impedance. See figure 5. Page Write The device is capable of a thirty-two byte page write operation. It is initiated in the same manner as the byte write operation; but instead of terminating the write operation after the first data word is transferred, the master can transmit up to thirty-one more words. The device will respond with an acknowledge after the receipt of each word, and then the byte address is internally incremented by one. The page address remains constant. When the counter reaches the end of the page, it “rolls over” and goes back to the first byte of the current page. This means that the master can write 32 words to the page beginning at any byte. If the master begins writing at byte 16, and loads 32 words, then the first 16 words are written to bytes 16 through 31, and the last 16 words are written to bytes 0 through 15. Afterwards, the address counter would point to byte 16. If the master writes more than 32 words, then the previously loaded data is overwritten by the new data, one byte at a time. The master terminates the data byte loading by issuing a stop condition, which causes the device to begin the nonvolatile write cycle. As with the byte write operation, all inputs are disabled until completion of the internal write cycle. Refer to figure 6 for the address, acknowledge, and data transfer sequence.Figure 5. Byte Write SequenceS TSIGNALS FROM THE MASTERA RSLAVE ADDRESSWORD ADDRESS BYTE 1WORD ADDRESS BYTE 0DATAS TO PT SDA BUSSIGNALS FROM THE SLAVES10100A C A C A C A CPKKKK7035 FM 07Figure 6. Page Write Sequence(0=n=31)SIGNALS FROM THE MASTER S TA RSLAVE ADDRESSWORD ADDRESS BYTE 1WORD ADDRESS BYTE 0DATA (0)DATA (n)S TO PT SDA BUSSIGNALS FROM THE SLAVES 10100A C A C A C A C A CPKKKKK7035 FM 086元器件交易网X24320Acknowledge Polling The maximum write cycle time can be significantly reduced using Acknowledge Polling. To initiateREAD OPERATIONSRead operations are initiated in the same manner as write operations with the exception that the R/W bit of the Slave Address Byte is set to one. There are three basic read operations: Current Address Reads, Random Reads, and Sequential Reads. Current Address Read Internally, the device contains an address counter that maintains the address of the last word read or written incremented by one. After a read operation from the last address in the array, the counter will “roll over” to the first address in the array. After a write operation to the last address in a given page, the counter will “roll over” to the first address on the same page. Upon receipt of the Slave Address Byte with the R/W bit set to one, the device issues an acknowledge and then transmits the eight bits of the Data Byte. The master terminates the read operation when it does not respond with an acknowledge during the ninth clock and then issues a stop condition. Refer to figure 8 for the address acknowledge, and data transfer sequence.Acknowledge Polling, the master issues a start condition followed by the Slave Address Byte for a write or read operation. If the device is still busy with the internal write cycle, then no ACK will be returned. If thedevice has completed the internal write operation, an ACK will be returned and the host can then proceedwith the read or write operation. Refer to figure 7 . Figure 7. Acknowledge Polling SequenceBYTE LOAD COMPLETED BY ISSUING STOP.ENTER ACK POLLINGISSUE STARTISSUE SLAVE ADDRESS BYTEISSUE STOP(READ OR WRITE)ACK RETURNED?NOIt should be noted that the ninth clock cycle of the read operation is not a “don’t care " .” To terminate a read operation, the master must either issue a stop condition during the ninth cycle or hold SDA HIGH during the ninth clock cycle and then issue a stop condition.YESHIGH VOLTAGE CYCLE COMPLETE. CONTINUENOFigure 8. Current Address Read SequenceSIGNALS FROM THE MASTERS TSEQUENCE?YES SDA BUSCONTINUE NORMAL READ OR WRITEA RSLAVE ADDRESSS TO PT S 1 01 0 1A CP DATA7035 FM 10ISSUE STOPCOMMAND SEQUENCESIGNALS FROM THE SLAVEKPROCEED7035 FM 097元器件交易网X24320Random Read Random read operation allows the master to access any memory location in the array. Prior to issuing the Slave Address Byte with the R/W bit set to one, the master must first perform a “Dummy” write operation. The master issues the start condition and the Slave Address Byte with the R/W bit low, receives an acknowledge, then issues the Word Address Byte 1, receives another acknowledge, then issues the Word Address Byte 0. After the device acknowledges receipt of the Word Address Byte 0, the master issues another start condition and the Slave Address Byte with the R/W bit set to one. This is followed by an acknowledge and then eight bits of data from the device. The master terminates the read operation by not responding with an acknowledge and then issuing a stop condition. Refer to figure 9 for the address, acknowledge, and data transfer sequence. The device will perform a similar operation called “Set Current Address” if a stop is issued instead of the second start shown in figure 9. The device will go into standby mode after the stop and all bus activity will be ignored until a start is detected. The effect of this operation is that the new address is loaded into the address counter, but no data is output by the device. The next Current Address Read operation will read from the newly loaded address. Sequential Read Sequential reads can be initiated as either a current address read or random read. The first Data Byte is transmitted as with the other modes; however, the master now responds with an acknowledge, indicating it requires additional data. The device continues to output data for each acknowledge received. The master terminates the read operation by not with an acknowledge and then issuing a stop condition. respondingThe data output is sequential, with the data from address n followed by the data from address n + 1. The address counter for read operations increments through all byte addresses, allowing the entire memory contents to be read during one operation. At the end of the address space the counter “rolls over ” to address 0000h and the device continues to output data for each acknowledge received. Refer to figure 10 for the acknowledge and data transfer sequence.Figure 9. Random Read SequenceSIGNALS FROM THE MASTER S T S TA RSLAVE ADDRESSWORD ADDRESS BYTE 1WORD ADDRESS BYTE 0A RSLAVE ADDRESSS TO PT SDA BUSSIGNALS FROM THE SLAVET 0A C A C A CS1 0 1 0S1A CPKKKKDATA7035 FM 11Figure 10. Sequential Read SequenceSIGNALS FROM THE MASTER SLAVE ADDRESS A C A C A CS TO PK 1A CKKSDA BUSSIGNALS FROM THE SLAVESPKDATA (1)DATA (2)DATA (n–1)DATA (n)(n is any integer greater than 1)7035 FM 128元器件交易网X24320WRITE PROTECT REGISTER (WPR) Writing to the Write Protect RegisterThe Write Protect Register can only be modified by performing a “ByteWrite” operation directly to the address FFFFh as described below. The Data Byte must contain zeroes where indicated in the procedural descriptions below; otherwise the operation will not be performed. Only one Data Byte is allowed for each register write operation. The part will not acknowledge any data bytes after the first byte is entered. The user then has to issue a stop to initiate the nonvolatile write cycle that writes BL0, BL1, and WPEN to the nonvolatile bits. A stop must also be issued after volatile register write operations to put the device into Standby. The state of the Write Protect Register can be read by performing a random byte read at FFFFh at any time. The part will reset itself after the first byte is read. The master should supply a stop condition to be consistent with the protocol, but a stop is not required to end this operation. After the read, the address counter contains WPEN: Write Protect Enable Bit (Nonvolatile) The Write Protect (WP) pin and the Write Protect Enable (WPEN) bit in the Write Protect Register control the Programmable Hardware Write Protection feature. Hardware Write Protection is enabled when the WP pin is HIGH and the WPEN bit is HIGH, and disabled when either the WP pin is LOW or the WPEN bit is LOW. Figure 12 defines the write protect status for each combination of WPEN and WP. When the chip is Hardware Write Protected, nonvolatile writes are disabled to the Write Protect Register, including the Block Lock Protect bits and the WPEN bit itself, as well as to the Block Lock protected sections in the memory array. Only the sections of the memory array that are not Block Lock protected, and the volatile bits WEL and RWEL, can be written. In Circuit Programmable ROM Mode Note that when the WPEN bit is write protected, it cannot be changed back to a LOW state; so write protection is enabled as long as the WP pin is held HIGH. Thus an In Circuit Programmable ROM function can be implemented by hardwiring the WP pin to VCC, writing to and Block Locking the desired portion of the array to be ROM, and then programming the WPEN bit HIGH. 0 0 Unused Bit Positions Bits 0, 5 & 6 are not used. All writes to the WPR must have zeros in these bit positions. The data byte output during a WPR read will contain zeros in these bits. Writing to the WEL and RWEL bits WEL and RWEL are volatile latches that power up in the LOW (disabled) state. While the WEL bit is LOW, writes to any address other than FFFFh will be ignored (no acknowledge will be issued after the Data Byte). The WEL bit is set by writing 00000010 to address FFFFh. Once set, WEL remains HIGH until either it is reset to 0 (by writing 00000000 to FFFFh) or until the part powers up again. Writes to WEL and RWEL do not cause a nonvolatile write cycle, so the device is ready for the next operation immediately after the stop condition. The RWEL bit controls writes to the Block Lock Protect bits, BL0 and BL1, and the WPEN bit. If RWEL is 0 then no writes can be performed on BL0, BL1, or WPEN. RWEL is reset when the device powers up or after any nonvolatile write, including writes to the Block Lock Protect bits, WPEN bit, or any bytes in the memory array. When RWEL is set, WEL cannot be0000h. Write Protect Register: WPR (ADDR = FFFFh)7 WPEN 6 0 5 0 4 BL1 3 BL0 2 1RWEL WELWEL: Write Enable Latch (Volatile) 0 = Write Enable Latch reset, writes disabled.1 = Write Enable Latch set, writes enabled.RWEL: Register Write Enable Latch (Volatile) 0 = Register Write Enable Latch reset, writes to the Write Protect Register disabled. 1 = Register Write Enable Latch set, writes to the Write Protect Register enabled.BL0, BL1: Block Lock Protect Bits (Nonvolatile) TheBlock Lock Protect Bits, BL0 and BL1, determine which blocks of the array are protected. A write to a protected block of memory is ignored, but will receive an acknowledge. The master must issue a stop to put the part into standby, just as it would for a valid write; but the stop will not initiate an internal nonvolatile write cycle. See figure 11.9元器件交易网X24320reset, nor can RWEL and WEL be reset in one write operation. RWEL can be reset by writing 00000010 toFFFFh; but this is the same operation as in step 3 described below, and will result in programing BL0, step 2. RWEL is reset to zero in step 3 so that user is required to perform steps 2 and 3 to make another change. RWEL must be 0 in step 3. If the RWEL bit in the data byte for step 3 is a one, then no changes are made to the Write Protect Register and the device remains at step 2. The WP pin must be LOW or the WPEN bit must be LOW before a nonvolatile register write operation is initiated. Otherwise, the write operation will abort and the device will go into standby mode after the master issues the stop condition in step 3. Step 3 is a nonvolatile write operation, requiring tWC to complete (acknowledge polling may be used to reduce this time requirement). It should be noted that step 3 MUST end with a stop condition. If a start condition is issued during or at the end of step 3 (instead of a stop condition) the device will abort the nonvolatile register write and remain at step 2. If the operation is aborted with a start condition, the master must issue a stop to put the device into standby mode.BL1, and WPEN.Writing to the BL and WPEN Bits A 3 step sequence is required to change the nonvola- tile Block Lock Protect or Write Protect Enable bits:1) Set WEL=1, Write 00000010 to address FFFFh (Volatile Write Cycle.) 2) Set RWEL=1, Write 00000110 to address FFFFh (Volatile Write Cycle.) 3) Set BL1, BL0, and/or WPEN bits, Write u00xy010 to address FFFFh, where u=WPEN, x=BL1, and y=BL0.(Nonvolatile Write Cycle.) The three step sequence was created to make it diffi cult to change the contents of the Write Protect Register accidentally. If WEL was set to one by aprevious register write operation, the user may start atABSOLUTE MAXIMUM RATINGS*Figure 11. Block Lock Protect Bits and Protected Addresses BL1 0 0 1 1 BL0 0 1 0 1 Protected AddressesNone C00h - FFFh 800h - FFFh 000h - FFFhArray Location No Protect Upper 1/4 Upper 1/2 Full Array7003 FRM T02Figure 12. WP Pin and WPEN Bit Functionality WP 0 X 1 WPEN X 0 1Memory Array Not Lock Block ProtectedMemory Array Block Lock ProtectedBlock Lock Bits Unprotected Unprotected ProtectedWPEN BitWritable Writable WritableProtected Protected ProtectedUnprotected Unprotected Protected7003 FRM T0310元器件交易网X24320Temperature under Bias X24320 ....................................... –65°C to +135°CStorage Temperature ........................ –65°C to +150°C Voltage on any Pin with Respect to VSS .................................... –1V to +7V D.C. Output Current ..............................................5mA Lead Temperature (Soldering, .............................. 300°C 10 seconds)*COMMENT Stresses above those listed under “Absolute Maximum Ratings” may cause permanent damage to the device. This is a stress rating only and the functional operation of the device at these or any other conditions above those indicated in the operational sections of this specification is not implied. Exposure to absolute maximum rating conditions for extended periods may affect device reliability.RECOMMENDED OPERATING CONDITIONS TemperatureCommercial IndustrialSupply VoltageX24320 X24320–2. 5 X24320–1. 8Limits4.5V to 5.5V 2.5V to 5.5V 1.8V to 3.6V7003 FRM T05Min.0°C –40°CMax.+70°C +85°C7003 FRM T04D.C. OPERATING CHARACTERISTICS Limits SymbolICC1 ICC2 ISB1 (1)ParameterVCC Supply Current (Read) VCC Supply Current (Write) VCC Standby CurrentMin.Max.1 3 5UnitsmA mA ∝ATest ConditionsSCL = VCC X 0.1/VCC X 0.9 Levels @ 400KHz, SDA = Open, All OtherInputs = VSS or VCC – 0.3VSCL = SDA = VCC, All Other Inputs = VSS or VCC – 0.3V,VCC = 5V ± 10% ISB2 (1) VCC Standby Current 1 ∝ASCL = SDA = VCC, All Other Inputs = VSS or VCC – 0.3V,VCC = 2.5V ILI ILO VlL (2) VIH (2) VOL Vhys (3) Input Leakage Current Output Leakage Current Input LOW Voltage Input HIGH Voltage Output LOW VoltageHysteresis of Schmitt Trigger Inputs10 10 –0.5 VCC x 0.7 VCC x 0.3 VCC + 0.5 0.4 VCC x 0.05∝A ∝A V V V VVIN = VSS to VCCVOUT = VSS to VCCIOL = 3mA7003 FRM T06CAPACITANCE TA = +25°C, f = 1MHz, VCC = 5VSymbolCI/O (3) CIN (3)ParameterInput/Output Capacitance (SDA) Input Capacitance (S0, S1, S2, SCL, WP)Max.8 6UnitspF pFTest ConditionsVI/O = 0V VIN = 0V7003 FRM T07Notes: (1)Must perform a stop command prior to measurement. (2)VIL min. and VIH max. are for reference only and are not 100% tested. (3)This parameter is periodically sampled and not 100% tested.11元器件交易网X24320A.C. CONDITIONS OF TESTInput Pulse LevelsInput Rise and Fall Times Input and Output Timing LevelsEQUIVALENT A.C. LOAD CIRCUITVCC x 0.1 to VCC x 0.9 10ns VCC X 0.57003 FRM T085V 1.53KΟ OUTPUT 100pF7035 FM 13A.C. OPERATING CHARACTERISTICS (Over the recommended operating conditions, unless otherwise specified.) Read & Write Cycle LimitsSymbolfSCL tI tAA tBUF tHD:STA tLOW tHIGH tSU:STA tHD:DAT tSU:DAT tR tF tSU:STO tDH tOFParameterSCL Clock FrequencyNoise Suppression Time Constant at SCL, SDA InputsMin.0 50 0.1 1.2 0.6 1.2 0.6Max.400UnitsKHz nsSCL LOW to SDA Data Out ValidTime the Bus Must Be Free Before a New Transmission Can Start0.9∝s ∝s ∝s ∝s ∝s ∝s ∝s nsStart Condition Hold Time Clock LOW Period Clock HIGH PeriodStart Condition Setup Time a Repeated Start Condition) (for0.6 0 100 300 300 0.6 50 20+0.1Cb (5) 300Data In Hold Time Data In Setup Time SDA and SCL Rise Time SDA and SCL Fall Time Stop Condition Setup Time Data Out Hold Time Output Fall Timens ns ∝s ns7003 FRM T09POWER-UP TIMING SymboltPUR tPUW(4)ParameterPower-up to Read Operation Power-up to Write OperationMax.1 5Unitsms ms7003 FRM T10Notes: (4)tPUR and tPUW are the delays required from the time VCC is stable until the specified operation can be initiated. These parameters are periodically sampled and not 100% tested.12。
ICP DAS ISO-AD32数据采集系统硬件手册说明书

ISO-AD32Hardware Manual ICP DAS Industrial Computer Products Data Acquisition SystemWarrantyAll products manufactured by ICP DAS are warranted against defective materials for a period of one year from the date of delivery to the original purchaser.WarningICP DAS assume no liability for damages consequent to the use of this product. ICP DAS reserves the right to change this manual at any time without notice. The information furnished by ICP DAS is believed to be accurate and reliable. However, no responsibility is assumed by ICP DAS for its use, nor for any infringements of patents or other rights of third parties resulting from its use.CopyrightCopyright 1997 by ICP DAS. All rights are reserved.TrademarkThe names used for identification only may be registered trademarks of their respective companies.Table of Contents1. INTRODUCTION (4)1.1G ENERAL D ESCRIPTION (4)1.2T HE B LOCK D IAGRAMS (5)1.3 F EATURES (6)1.4 S PECIFICATIONS (7)1.5 P RODUCT C HECK L IST (8)2. HARDWARE CONFIGURATION (9)2.1 B OARD L AYOUT (9)2.2 JP1 : S INGLE-ENDED/D IFFERENTIAL A NALOG I NPUT T YPE S ELECT (10)2.3 JP2 : IRQ C HANNEL S ELECTION (10)2.4 JP5 : W AIT S TATE (11)2.5 VR S (11)2.6 I/O B ASE A DDRESS S ETTING (12)2.7 CN1 C ONNECTORS (13)2.8 D AUGHTER B OARDS (15)2.8.1 DB1825 (15)2.8.2 DB37 (15)2.8.3 DN37 (15)3. FUNCTION OPERATION (16)3.1 AD C ONVERSION O PERATION (16)3.1.1 The Configuration Code Table (16)3.1.2 Analog Input Type Selection (17)3.1.3 The Input Signal Range (18)3.1.4 The AD Conversion Mode (21)3.1.5 The Channel Scan Circular_Scan_Queue (22)3.1.6 Trigger Methods : (23)3.2D IAGNOSTIC P ROGRAM (24)3.3 C ALIBRATION (24)3.4 A NALOG S IGNAL C ONNECTION (25)1. Introduction1.1 General DescriptionThe ISO-AD32H/L ( H for high gain / L for low gain ) is a bus-type isolated 12-bit A/D board for PC/AT compatible computers. The isolation inputs can operate with up to 500Vrms of common-mode voltage.The ISO-AD32H/L features a 200KHz 12-bit analog-to-digital converter, on board 1 K byte FIFO buffer, 32 singled-ended or 16 differential analog input channels. The analog input allows auto-channel/gain scan. This board support gap-free A/D conversion at 200KHz sampling rates for single channel or 100KHz sampling rates for channel scan.The “Hands-Off“ design permits all board parameters (channel selection, gain, input type, operating mode) to be performed in software. Once installed, you will never have to take care it again.The board’s innovative design improve several drawbacks of the conventional isolated A/D card. Such as :1. The speed is faster; up to 200KHz2. The sampling rate can be programmable3. On board FIFO buffer support gap-free A/D conversion and work well under NT and95 environment.4. High channel count input can be implemented in half size .1.2 The Block DiagramsThe block diagram of ISO-AD32 series is shown below :Fig 1 : The block diagram of ISO_AD32.The X86 send one command to command queue through ISA bus. The embedded controller will auto read and execute this command. The results of this command will store in the data FIFO, therefore the X86 can read back and analysis the results through ISA bus.The X86 site and the embedded controller is fully isolated. Therefore the noise from external device will be isolated from X86, this will improve the X86 reliability.The X86 only need to send out command and the embedded controller will handle the control details. The features of command set system are given as following:(1) : reduce X86 load(2) : easy programming1.3 FeaturesThe general features of ISO-AD32 series are given as follows:32 single-ended or 16 differential input channels, 500VDC photo-isolation protection Maximum 200K 12-bit sampling rateBuilt-in 1K byte FIFOSingle -ended or differential input, can be jumper selectableAuto-channel / gain scanCommand set programmingGap-free A/D conversion1.4 SpecificationsAnalog Input SpecificationsChannels : 32 single-ended/ 16 differentialResolution : 12 bitsConversion rate : 200KS/s max.Input impedance : 10,000 MΩ║6pFOver voltage protection : +/-35VAccuracy : 0.01% of reading +/- 1 bitLinearity : +/- 1 bitOn chip sample & holdZero drift : +/-25ppm/°C of FS max.ISO-AD32H Input RangeBipolar : +/-10V,+/-5V,+/-1V,+/-0.5V,+/-0.1V,+/-0.05V,+/-0.01V,+/-0.005V Unipolar : 0~10V,0~1V,0~0.1V,0~0.01VThroughput Gain Bipolar(V) Unipolar(V)1/0.5 ±5 / ±10 0~10 125k/s10/5 ±0.5 / ±1 0~1 80k/s100/50 ±0.05 / ±0.1 0~0.1 10k/s1000/500 ±0.005 / ±0.01 0~0.01 1k/sISO-AD32L Input RangeBipolar : +/-10V,+/-5V,+/-2.5V,+/-1.25V,+/-0.0625Unipolar : 0~10V,0~5V,0~2.5V,0~1.25VGain Bipolar(V) Unipolar(V) Throughput0.5 ±10 X 200K/s1 ±5 0~10 200K/s2 ±02.5 0~5 200K/s4 ±1.25 0~2.5 200K/s8 ±0.625 0~1.25 200k/sPower Requirements: +5V @850mA max.General EnvironmentalOperating temp 0-50°CStorage temp -20°C to 70°CHumility 0 to 90% non-condensingDimensions 173 mm x 122 mm1.5 Product Check ListIn addition to this manual, the package includes the following items:ISO_AD32 multifunction card.One company floppy diskette or CD.One DOS software user’s manual.Attention !If any of these items is missing or damaged, please contact your local field agent. Save the shipping materials and carton in case you want to ship or store the product in the future.2. Hardware Configuration 2.1 Board Layout2.3JP2 : IRQ Channel SelectionIRQ3IRQ4IRQ5IRQ6IRQ7IRQ9IRQ10IRQ11IRQ12IRQ14IRQ15NC (default)2.5 VRsV1 : AD offset adjustmentVR2 : AD gain adjustmentVR3 : -5V adjustmentVR4 : PGA offset adjustmentThe detail calibration steps are given in “DOS software manual” Sec. 4.1.4.2.6 I/O Base Address SettingThe ISO-AD32 occupies 8 consecutive locations in I/O address space from BASE to BASE+7. The default setting is 0x220 as following :ON1 2 3 4 5 6A8A7A6A5A4NCBase Addr A8A7A6A5A4200On On On On On210On On On On Off220On On On Off On230On On On Off Off250On On Off On Off::::::300Off On On On On::::::3F0Off Off Off Off Off2.7 CN1 ConnectorsPin assignment for single-ended analog inputName Pin Name PinAI161 AI0 202 AI1 21AI17AI183 AI2 22AI194 AI3 23AI205 AI4 24AI216 AI5 25AI227 AI6 26AI238 AI7 27AI249 AI8 28AI2510 AI9 29AI2611 AI10 30AI2712 AI11 31AI2813 AI12 3214 AI13 33AI29AI3015 AI14 34AI3116 AI15 3517 Analog Common 36 Analog GND18 Digital +5V output 37 Digital GND19 External Trigger InputPin assignment for differential analog inputName Pin Name PinAI0-1 AI0+ 202 AI1+ 21AI1-AI2-3 AI2+ 22AI3-4 AI3+ 23AI4-5 AI4+ 24AI5-6 AI5+ 25AI6-7 AI6+ 26AI7-8 AI7+ 27AI8-9 AI8+ 28AI9-10 AI9+ 29AI10-11 AI10+ 30AI11-12 AI11+ 31AI12-13 AI12+ 3214 AI13+ 33AI13-AI14-15 AI14+ 34AI15-16 AI15+ 3517 Analog Cmmon 36 Analog GND18 Digital +5V output 37 Digital GND19 External Trigger Input37pin cableconnection 1 : by 37 pin cableconnectconnection direct2.8.3 DN37The DN-37 is a daughter board for 37 pins DIN Rail Mounting. It is designed for easy wire connection.37pin cable3. Function Operation3.1 AD Conversion OperationThe user do not need to know about the detail control of AD operations, the embedded controller will handle the details.3.1.1 The Configuration Code Table3.1.2 Analog Input Type SelectionThe analog input signal can be single-ended or differential. If select single-ended, there can be 32 channels max. If select differential, there can be only 16 channels max. But some signal can not be connected as single-ended input, such as thermocouple couple sensor. Refer to Sec 3.7 for analog signal input type selection.The embedded control can read back the JP1 setting. If the software tell the embedded controller to perform single-ended operation and the JP1 in the wrong setting, the embedded controller will return a error code. Refer to software manual for details.3.1.2.1 Unipolar/BipolarIf the analog input signal is unipolar, you can measure this signal with bipolar setting (this will reduce resolution only). If the analog input is bipolar, you must select bipolar configuration code to measure this signal.3.1.3 The Input Signal RangeIf the input range of analog signal is +/- 1V, you can measure this signal wih +/-10V, +/- 5V, +/-2.5V and +/- 1.25V configuration code setting. The only difference is the resolution. The resolution of +/- 2.5V is 4 times higher than in +/- 10V setting. Select the correct configuration code will get the best resolution.3.1.3.1 The Gain FactorThe analog input signal will be amplified by gain factor. If the user wish to compute the real value, the AD data must divided with the gain factor. The general real value computation functions is given as follows:double AD32L_ComputeRealValueBipolar(WORD wAdConfig, WORD wAdHex){WORD wZERO=2048;double dfMAX, dfVal;switch (wAdConfig){case 0x00 : dMAX=5.0; break;case 0x10 : dMAX=2.5; break;case 0x20 : dfMAX=1.25; break;case 0x30 : dfMAX=0.625; break;case 0x80 : dfMAX=10.0; break;case 0x90 : dfMAX=5.0; break;case 0xA0 : dfMAX=2.5; break;case 0xB0 : dfMAX=1.25; break;default : return(ConfigCodeError);;}dfVal=(((double)(wAdHex)-wZERO)/2048.0)*dfMAX;return(dfVal);}{WORD wZERO=0;double dfMAX, dfVal;switch (wAdConfig){case 0x00 : dMAX=10.0; break;case 0x10 : dMAX=5.0; break;case 0x20 : dfMAX=2.5; break;case 0x30 : dfMAX=1.25; break;default : return(ConfigCodeError);;}dfVal=(((double)(wAdHex)-wZERO)/2048.0)*dfMAX;return(dfVal);}double AD32H_ComputeRealValueBipolar(WORD wAdConfig, WORD wAdHex) {WORD wZERO=2048;double dfMAX, dfVal;switch (wAdConfig){case 0x00 : dMAX=5.0; break;case 0x10 : dMAX=0.5; break;case 0x20 : dfMAX=0.05; break;case 0x30 : dfMAX=0.005; break;case 0x80 : dfMAX=10.0; break;case 0x90 : dfMAX=1.0; break;case 0xA0 : dfMAX=0.1; break;case 0xB0 : dfMAX=0.01; break;default : return(ConfigCodeError);;}dfVal=(((double)(wAdHex)-wZERO)/2048.0)*dfMAX;return(dfVal);}{WORD wZERO=0;double dfMAX, dfVal;switch (wAdConfig){case 0x00 : dMAX=10.0; break;case 0x10 : dMAX=1.0; break;case 0x20 : dfMAX=0.1; break;case 0x30 : dfMAX=0.01; break;default : return(ConfigCodeError);;}dfVal=(((double)(wAdHex)-wZERO)/2048.0)*dfMAX;return(dfVal);}3.1.3.2 The Settling TimeIf the channel number or gain factor is change, the hardware need extra time for signal ready. This is called the settling time. This limitation will apply both to the Fixed-channel mode and MagicScan mode AD conversions. So the user must take care to avoid the settling error. Refer to “DOS software manual” Sec. 3.6.3.1.3.3 How to Delay the Settling TimeThe software driver can auto delay the settling time. Refer to “DOS software manual” Sec. 3.6 for fixed-channel AD conversion.It is no need to delay the settling time in the channel-scan mode AD conversion3.1.4 The AD Conversion ModeThe AD operation can be fixed-channel mode or channel-scan mode. In the fixed-channel mode, the AD operation will fix at one channel until the change channel command is received. Refer to “DOS software manual” Sec3.6, Sec. 3.7, Sec. 3.9, Sec. 3.10 for details.In the channel scan mode, the embedded controller will auto scan and change gain. The scan sequence and gain for each channel can be programmable. Refer to the software manual for details. Refer to “DOS software manual” Sec3.16, Sec. 3.17, Sec. 3.18 for details.3.1.5 The Channel Scan Circular_Scan_QueueThe channel scan controller equips with a circular queue for scan sequence control. The scan sequence is one by one and repeatable with the limitation of maximum 32 channels. So the following scan sequence are all validate :two channel scan, scan sequence=010101One channel scantwo channel scan, scan sequence=101010two channel scan, scan sequence=000000Three channel scan : 123123123Three channel scan : 251251251Three channel scan : 252252252Three channel scan : 2222222223.1.6 Trigger Methods :The trigger methods are giving as following:(1) Internal trigger = software trigger + pacer trigger(2) External trigger = post-trigger + middle-trigger + pre-triggerFig 1-2: Trigger methods of ISO-AD32.The software trigger is the easy way and isn’t suitable for input wave form reconstruction. The pacer trigger provide a programmable pacer for fixed time interval AD sampling, therefore it is suitable for input wave form reconstruction.The external trigger must used with pacer timer. This pacer timer is same as the internal pacer trigger timer. Both the internal pacer trigger and external trigger use the same pacer timer. The external trigger can be post-trigger, middle trigger or pre-trigger software programmable.The user can select one of these trigger. Refer to software manual for details.3.2 Diagnostic Program Refer to “ISO-AD32 DOS software manual” Chapter 4 for details.3.3 CalibrationRefer to “ISO-AD32 DOS software manual” Sec 4.1.4 for details.3.4 Analog Signal ConnectionThe ISO_AD32 can measure single-ended or differential type analog input signal. Some analog signal can be measured in both of single-end or differential mode but some only can be measured in one of the single-ended or differential mode. The user must decide which mode is suitable for measurement.In general, there are 3 different analog signal connection method as shown in Fig1 to Fig3. The Fig1 is suitable for grounding source analog input signals. The Fig2 can measure more channels than in the Fig1 but only suitable for large analog input signals. The Fig3 is suitable for thermocouple and the Fig4 is suitable for floating source analog input signals.Note : In Fig3, the maximum common mode voltage between the analog input source and the AGND is 70Vp-p, so the user must make sure that the input signal is under specification first. If the common mode voltage is over 70Vp-p, the input multiplexer will be damaged forever.The simple way to select the input signal connection configuration is as below.1. Grounding source input signal select Fig12. Thermocouple input signal select Fig33. Floating source input signal select Fig44. If Vin > 0.1V and gain<=10 and need more channelsselect Fig2If the user can not make sure the characteristic of input signal, the test steps are given as below:1. Step1 : try Fig1 and record the measurement result2. Step2 : try Fig4 and record the measurement result3. Step3 : try Fig2 and record the measurement result4. Compare the measurement result of step1,step2,step3 andselect the best oneSignal ShieldingSignal shielding connections in Fig1 to Fig4 are all the sameUse single-point connection to frame ground (not AGND or DGND)Appendix A : The DB-1825 user manualA.1 : PCB layout for connecting to ISO_AD32: for differential input (R=0 ohm)Pin assignment of D1 same as CN1 of ISO-AD32Pin assignment of D2 same as CN1 of DB-889DA.2 : PCB layout for connecting to PCI-1802: for differential input (R=0 ohm)Pin assignment of D1 same as CON3 of PCI-1802Pin assignment of D2 same as CN1 of DB-889DA.3 : connection to ISO-AD32A.5 : connection to PCI-1802 and multiple DB-889D(16 channels differential) ISO-AD32 Hardware Manual(Ver.1.0, Feb/1998, IPH-012-10) ---- 31。