PowerFeed10M_CN
31012709_Liebert NX 30kVA和40kVA UPS_V1.0_3.4用户手册

1.若长时间存储或放置不使用,必须将本产品置于干燥、洁净和规定温度范围的环境中。 2.本产品应在适当的工作环境中使用(详见本产品手册环境要求章节)。 3.禁止在以下工作环境中使用本产品:
超出本产品技术指标规定的高温、低温或潮湿场所 有导电粉尘、腐蚀性气体、盐雾或可燃性气体的场所 有振动、易受撞的场所 靠近热源或有强电磁场干扰的场所
1.1 特点.........................................................................................................................................................................................1 1.2 设计思想.................................................................................................................................................................................1
一般安全
与其它类型的大功率设备一样,UPS 及电池开关盒/电池柜内部带有高压。但由于带高压的元器件只有打开前门(有锁)才可 能接触到,所以接触高压的可能性已降到最小。本设备符合 IP20 标准,内部还有其它的安全屏蔽。 如果遵照一般规范并按照本书所建议的步骤进行设备的操作,将不会存在任何危险。
用户可维护器件
目录
第一章 概述 ........................................................................................................................................................................ 1
AIMS Power 10,000瓦直流到交流电源逆变器 (V 2.0) 使用说明书
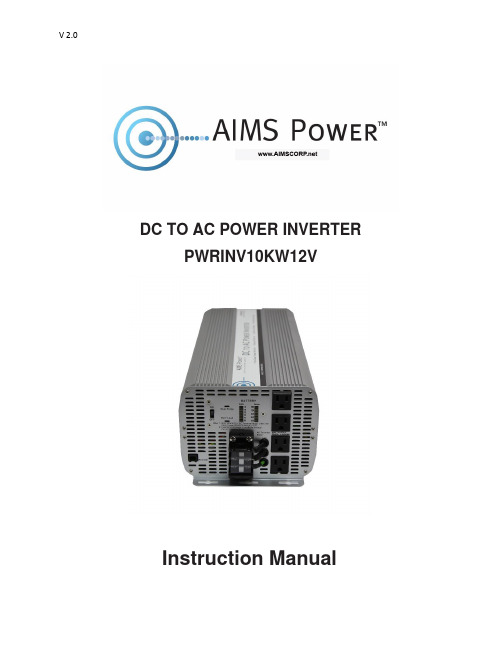
DC TO AC POWER INVERTER PWRINV10KW12VInstruction ManualIntroductionThe AIMS Power 10,000 watt inverter is the most technology advanced mobile DC to AC power inverter available. AIMS also offers the 8,000 Watt 12V or 12,000 Watt 24V.This inverter is used in a wide range of applications including back up power for remotehomes, off-grid systems, RVs, boats, commercial vehicles and mobile businesses. The10,000 watt inverter will operate most pumps, motors, lights, heaters, compressorbased appliances and hand tools.To get the most out of the power inverter, it must be installed and used properly. Readthe instructions in this manual before installing and using this product. Follow all safetyprecautions.FUNCTIONSFRONT VIEWA. On/Off switch: Leave in the OFF position during installation.B. Over temperature indicator: Lights when inverter protects itself against overheating. Invertershuts down while indicator is on. Inverter will restart automatically and indicator will turn off when the inverter cools.C. Over load indicator: Lights when inverter shuts down because of overload. Indicator will turn offand inverter will restart when overload is removed.D. Bar meters: Displays battery voltage and current. Current should be in the green zone forcontinuous operation. The inverter will operate for several minutes when the current is in the yellow zone. Operation with battery voltage or current in the red zone of a meter will result in protective shutdown of inverter.E. AC outlets: Maximum recommended output per outlet is 1500W.F. Remote port: Used with remote switch to turn inverter ON/OFF (sold separately).G. AC terminal block: Hard wire block providing inverter's full power.E: AC outletsD: Bar metersB: Over temperature indicatorA: On/Off switch C: Over load indicatorG: AC terminal Block F: Remote portREAR VIEWA: Fan: Do not obstruct, allow at least 12 inches for air flow.B: Battery terminals: Connect to 12V, or 24V, or 36V, or 48V (depending on inverter model) battery(s) or other DC power source. "+" is positive & " - " is negative. Reverse polarity connection will blow internal fuse and may damage inverter permanently. Make sure you check your input voltage and do not REVERSE POLARITY! This will void the warranty.C: Chassis ground lug: Connect to earth ground or to vehicle chassis using #8 AWG wire. Warning! Operation of the inverter without a proper ground connection may result in an electrical safety hazard.QUICK HOOK-UP AND TESTINGIf you would like to quickly hook-up the power inverter and check its performance before moving forward with your installation, please follow these guidelines:1. Unpack and inspect the power inverter, check to see that the power switch is in the OFF position.2. Before you connect the battery cables, make sure the power switch is in the off position. Connect Red (+) battery cable to Red (+) inverter terminal. Connect Black (-) battery cable to Black (-) inverter terminal. Connect Red (+) battery cable to Red (+) battery terminal. Connect Black (-) battery cable to Black (-) battery terminal. Alligator clamp cables may be used but only to connect to the battery. Do not use clamps on inverter terminals. Alligator clamps are not a permanent solution. You may see a spark during connection. Do not reverse the polarity. This may damage the inverter and void warranty. Caution! Loosely tightened connectors result in excessive voltage drop and may cause overheated wires and melted insulation. Reverse polarity connection will blow a fuse in inverter and may permanently damage the inverter. Damage caused by reverse polarity connection is not covered by our warranty. Warning! You may observe a spark when you make this connection since current may flow to charge capacitors in the power inverter. Do not make this connection in the presence of flammable fumes, as explosion or fire may result.A: FanB: Battery terminal (+)B: Battery terminal (-)C: Chassis grounding3. Set the power switch to the on position. Check the meters and indicators on the front panelof the inverter. The voltage bar graph should indicate 11 to 14 volts depending on the voltageof the power source. If it does not, check your power source and the connections to inverter.The other indicators should be off.4. Set power inverter switch to the OFF position, the indicator l ights may blink and theinternal alarm may sound momentarily. This is normal. Plug the test load into the ACreceptacle on the front panel of the inverter. Leave the test load switch off.5. Set power inverter switch to the ON position and turn the test load on, the inverter shouldsupply power to the load. If you plan to measure the true output R.M.S. voltage of inverter, ameter such as FLUKE 87A, BACKMAN 4410 or TRIPLETT 4200 must be used.INSTALLATION1. Where to installThe power inverter should be installed in a location that meets the following requirements:a. Dry - Do not allow water to drip or splash onto the inverter.b. Cool - Ambient air temperature should be between 0°C and 40°C, the cooler the better when operating in this rangec. Ventilation - Allow at least one inch of clearance around the inverter for air flow. Ensure the ventilation openings on the rear and bottom of the unit are not obstructed.d. Safety - Do not install the inverter in the same compartment as batteries or in any compartment capable of storing flammable liquids such as gasoline.2. CablesDC to AC inverters require high amperage/low voltage DC power to low amperage/high voltage AC power. To operate properly, connect inverter DC input terminals direct to battery with heaviest wire available see below:12 Volt Model: 2x set of 4/0 AWG (2 red + 2 black) and quantity 2- ANL500KIT-500 Amp fuse kits for positive (red) cablesBattery Cables InstallationWhen connecting the AC inverter to the battery terminals, it is important to connect the "+" wire to the "+" terminal and the wire to the "-" wire to the “-“ terminal. Do NOT reverse the polarity. It will void the warranty. Make sure you connect negative to negative and positive to positive.Red (+) * 2Black (-) * 2REDBLACKCaution!DO NOT allow the wires to cross or touch each other. Install the cables facing away from each other and screw tightly. When connecting the battery cables to the terminals of the inverter, make sure they do not touch the case.3. GroundingThe power inverter has a lug on the rear panel marked "chassis ground" This is to connect the chassis of the power inverter to the ground.The ground terminals in the AC outlets on the front panel of the inverter are also connected to the ground lug.The chassis ground lug must be connected to a grounding point, which will vary depending on where the power inverter is installed. In a vehicle, connect the chassis ground to the chassis of the vehicle. In a boat, connect to the boat's grounding systems in a fixed location, connect the chassis ground lug to an earth point, which will vary depending on where the power inverter is installed.The neutral (common)conductor of the power inverter AC output circuit is connected to the chassis ground. Therefore, when the chassis is connected to ground, the neutral conductor will also be grounded.This conforms to national electrical code requirements that separately derived AC sources (such as inverters and generators) have their neutral tied to ground in the same way that the neutral conductor from the utility line is tied to ground at the AC breaker panel.Caution! The Negative DC input of the power inverter is connected to the chassis. DO not install the power inverter in a positive ground DC system. A positive ground DC system has the positive terminal of the battery connected to the chassis of the vehicle or to the grounding point.Warning! Do not operate the power inverter without connecting it to ground. Electrical shock hazard may result.OPERATIONTo operate the power inverter, turn it on using the ON/OFF switch on the front panel. The power inverter is now ready to deliver AC power to your loads. If you are operating several loads from the power inverter, turn on separately after the inverter has been turned on. This will ensure that the power inverter does not deliver starting currents to all of the loads at once.1. Controls and indicatorsThe ON/OFF switch turns the control circuit in the power inverter on and off. It does not disconnect power from the power inverter.When the switch is in the OFF position, the power inverter draws no current from battery. When the switch is in the ON position but with no load, the power inverter draws less than 450 mA.2. Battery voltage indicatorThe battery voltage bar graph indicates the voltage at the input terminals of the power inverter. At low input current, this voltage is very close to the battery voltage. At high input current, this voltage will be lower than the battery voltage because of the voltage drop across the cable and connections.Ideally, the voltage should remain in the green area of the bar graph. If the voltage goes into the red area at top or bottom of the graph, inverter may shut-down.3. Battery current indicatorThe battery current bar graph indicates the current drawn from the battery by the power inverter, it will not indicate current by other loads also connected to the battery. The indicator only displays DC volts and amps.For long term operation, the current should be in the green area of the bar graph. Short term operation is possible with current in the orange area. If the current rises to the red area, the inverter will reduce its output voltage to protect itself.To measure AC current, use a TRUE RMS MULTI METER.4. Over temp indicatorThe over temp indicator indicates that the power inverter has shut itself down because it has become overheated. The power inverter may overheat because it has been operated at power levels above its rating, or because it has been installed in a location which does not allow it to dissipate heat properly.5. Over load indicatorThe over load indicator indicates that the power inverter has shut itself down because its output circuit has been short circuited or drastically overloaded. Switch the ON/OFF to OFF, correct the fault condition, and then switch the ON/OFF back to ON.THINGS TO CONSIDER REGARDING THE LOADThe 10,000W inverter will operate most AC loads within its power rating. When determining whether a microwave oven can be operated by the 10,000W inverter, remember that the power commonly advertised for microwave ovens is the cooking power (the power delivered to the food) not the power actually consumed by the microwave oven. The microwave oven will consume 40% to 100% more than its advertised cooking power. Check the rating sticker on the back of the oven to determine its actual power draw. The 10,000W inverter will operate small microwave ovens (0.2 to 0.3 cubic foot capacity) that draw is about 1700 watts.Some induction motors used in refrigerators, freezers, pumps, and other motor operated equipment require very high surge currents to start. The power inverter may not be able to start some of these appliances even though their rated current draw is within the rating of the power inverter.If a motor refuses to start, observe the battery voltage indicator while trying to start the motor. If the battery voltage indicator drops below 10.5V DC while inverter is attempting to start the motor, this may be why the motor won't start.Make sure that the battery connections are good and that the battery is fully charged. If the connections are good and the battery to is charged, but the voltage still drops below 11 volts, you may need a larger battery or larger battery bank.(*2 for 24V *3 for 36V *4 for 48V)INPUT VOLTAGEThe power inverter will operate from input voltage ranging from 10V-16V. If the voltage drops below input range, an audible low battery warning will sound and the voltage indicator will be in the lower red zone. The power inverter will shut down if the input voltage drops below 10V +/- .5V. This protects your battery from being over discharged.The power inverter will also shut down if the input voltage exceeds 17V +\-.5V. This protects the inverter against excessive input voltage.The voltage indicator will be in the upper red zone. Although the power inverter incorporates protection against over voltage, the inverter is at risk of permanent damage if the input voltage is allowed to exceed 17V +\-.5V.TROUBLESHOOTINGmon problemsa. Buzz in audio systems:Some inexpensive stereo systems and radios will emit a buzzing noise from their loudspeakers when operated from the power inverter. This is because the power supply in the device does not adequately filter the modified sine wave produced by the power inverter. The only solution is to use a sound system that incorporates a higher quality power supply.b. Television interference:Operation of the power inverter can interfere with television reception on some channels. If this situation occurs, the following steps may help to alleviate the problem.-Make sure that the chassis ground lug on the back of the power inverter is solidly connected to the ground system of your vehicle, boat or home.-Do not operate high power loads with the power inverter while watching television.-Move the television as far away from the power inverter as possible.-Keep the cables between the battery and the power inverter as short as possible and twist them together with about 2 to 3 twists per foot. This minimizes radiated interference from the cables.SPECIFICATIONSAIMS Corp., Inc. dba AIMS Power Warranty Instructions:This product is designed using the most modern digital technology and under very strict quality control and testing guidelines. If, however you feel this product is not performing as it should, please contact us:**************************(775)359-6703We will do our best to resolve your concerns. If the product needs repair or replacement, make sure to keep your receipt/invoice, as that will need to be sent back along with the package and RMA# prepaid to AIMS. You have a full 1 year warranty from date of purchase.This warranty is valid worldwide with the exception that freight and duty charges incurred outside the contiguous 48 United States will be prepaid by customer.Except as provided above, AIMS Power makes no warranty of any kind, express or implied, including without limitation the implied warranties of merchantability and fitness for a particular purpose. In no event shall AIMS be liable for indirect, special or consequential damages. This warranty only applies to AIMS Power branded products. All other name brand products are warranted by and according to their respective manufacturer. Please do not attempt to return non-AIMS Power branded products to AIMS Power.For additional products such as:-Modified sine wave inverters-Pure sine wave inverters-Low Frequency Inverters-Solar Charge Controllers-Micro Grid Tied Inverters-Inverter Chargers and Automatic transfer switches-Converters DC-DC-Custom cut cables-Batteries-Solar Panels & RacksPlease visit our web site: Tofindoutwheretobuyanyofourproducts,youmayalsoe-mail:************************ (775)359-6703.。
搭载 TotalFORCE 控制技术的 PowerFlex 变频器 编程手册说明书

搭载 TotalFORCE 控制技术的 PowerFlex 变频器固件版本 10.xxx本产品的参数及故障和报警代码参⻅此 PDF 文件随附的电子表格。
如需访问这些电子表格,保存此 PDF 文件并在您的设备上(而非浏览器)打开。
然后,单击此处打开“附件”窗格(⻅左侧)即可访问每个电子表格。
2罗克⻙尔⾃动化出版物 750-PM101A-ZH-P - 2021 年2 月搭载 TotalFORCE 控制技术的 PowerFlex 变频器 编程手册重要⽤⼾须知在安装、配置、操作或维护本产品之前,请阅读本文档以及“其他资源”章节所列的文档,了解关于安装、配置和操作该设备的信息。
除了所有适用的条例、法律和标准的要求之外,用⼾还必须熟悉安装和接线说明。
包括安装、调整、投⼊运⾏、使用、装配、拆卸和维护等在内操作必须由经过适当培训的人员根据适用的操作守则来执⾏。
如果未遵照制造商所指定的方式使用该设备,将可能导致该设备提供的保护失效。
任何情况下,对于因使用或操作本设备造成的任何间接或连带损失,罗克⻙尔⾃动化有限公司概不负责。
本手册中包含的示例和图表仅用于说明。
由于任何具体安装都涉及众多变数和要求,罗克⻙尔⾃动化有限公司对于依据这些示例和图表所进⾏的实际应用不承担任何责任和义务。
对于因使用本手册中所述信息、电路、设备或软件而引起的专利问题,罗克⻙尔⾃动化有限公司不承担任何责任。
未经罗克⻙尔⾃动化有限公司的书⾯许可,不得复制本手册的全部或部分内容。
在整本手册中,我们在必要的地方使用了以下注释,来提醒您留意安全注意事项。
标签也可能位于设备表⾯或内部,提供具体的预防措施。
警告:标识在危险环境下可能导致爆炸,进而导致人员伤亡、物品损坏或经济损失的操作或情况。
注意:标识可能导致人员伤亡、物品损坏或经济损失的操作或情况。
注意符号可帮助您确定危险情况,避免发生危险,并了解可能的后果。
重要信息标识对成功应用和了解本产品有重要作用的信息。
MAX774ISDN铃声电源供应器评估套件(EV套件)使用说明书

For free samples & the latest literature: , or phone 1-800-998-8800.For small orders, phone 408-737-7600 ext. 3468._______________General DescriptionThe MAX774 ISDN ring-tone power-supply (IRG) evalua-tion kit (EV kit) provides the high voltages required for implementing a plain old telephone system (POTS) inter-face on ISDN modems and line cards. It is a fully assem-bled and tested board that provides a tightly regulated, -24V output for powering off-hook voice communication and a -70V output for on-hook, ring-tone generation.The EV kit is designed for applications that implement the telephone interface using subscriber line interface circuit (SLIC) ICs, such as the AM79R79 from AMD and comparable products from Lucent, Harris, and other vendors. Its design feeds back the -24V output, achiev-ing tight regulation for clean voice-signal transmission.An economical, off-the-shelf, surface-mount transformer reduces system cost and size. Compact design con-serves board area. High efficiency and reduced quies-cent current make this design the optimal solution for green PC and portable designs.The MAX774 IRG EV kit can also be used to evaluate the MAX775/MAX776. It has a layout that allows modifi-cation for -48V output operation as well as adaptation____________________________Featureso +3V to +16.5V Operating Rangeo Tightly Regulated, -24V Output for Off-Hook Voice Communication o -70V Output Supports a Five-Ringer-Equivalent Load (V IN > 10.5V)o Compact Construction o Proven PC Board Design o Uses Off-the-Shelf Components o Up to 84% Efficiency o 5µA Shutdown Current o Fully Assembled and TestedEvaluates: MAX774/MAX775/MAX776MAX774 ISDN, Ring-Tone, Power-Supply Evaluation Kit________________________________________________________________Maxim Integrated Products119-1287; Rev 0; 9/97______________Ordering InformationE v a l u a t e s : M A X 774/M A X 775/M A X 776MAX774 ISDN, Ring-Tone,Power-Supply Evaluation Kit 2____________________________________________________________________________________________________________________________Quick Start The MAX774 IRG evaluation kit (EV kit) is fully assem-bled and tested. Follow these steps to verify board operation. Do not turn on the power supply until all connections are completed.1)Connect a 12V, 2A power-supply ground terminal to a GND pad on the MAX774 IRG EV kit. 2)Monitor the input current by connecting the power supply's positive terminal to the EV kit’s VIN input through a current meter. 3)Attach a voltmeter across the EV kit’s VIN and GND inputs to monitor input voltage.4)Connect voltmeters to each of the EV kit’s outputs labeled -70V and -24V.5)Connect the SHDN pad to GND.6)Turn on the power supply and slowly increase the voltage to 12V. 7)Monitor the outputs for correct voltage and check the input for typical supply current (20mA at 12V)._______________Detailed DescriptionThe MAX774 IRG EV kit provides the high voltages required for implementing a plain old telephone system (POTS) interface on ISDN modems and other telephone line cards. These boards typically employ ICs such as the AM79R79 Ringing Subscriber Line Interface Circuit (SLIC) from AMD. These ICs generate an analog tele-phone interface by providing both off-hook and on-hook signal transmission, ring-tone generation, and ring-trip detection. Ringing SLIC ICs typically require two high-voltage power-supply inputs. The first is atightly regulated voltage around -24V or -48V for off-hook signal transmission. The second is a loosely regu-lated -70V for ring-tone generation. Servicing a typical five-ringer equivalent load requires a current around 100mA or more from the -70V supply, depending on the SLIC IC and the ring-generation scheme.The MAX774 IRG EV kit can service a SLIC with a five-phone ringer equivalent load (approximately 9W) from a 12V ±10% input. It operates down to 3V, and pro-vides 2.4W from 3.3V and 3.9W from 5V. Use of an inexpensive off-the-shelf transformer, such as the Versa-Pac™ model VP2-0216, provides both high-volt-age outputs from a single inverting DC-DC controller,reducing board area and component costs. Selection of a transformer with multifilar winding enhances cross regulation by improving voltage coupling between the outputs and reducing spiking from leakage inductance.The two outputs are implemented by connecting three pairs of transformer windings in series. The -24V output is obtained by connecting a diode (D1) and output filter capacitor (C9) to the first pair of windings. Feeding back this output achieves tight regulation. The -70V output is derived from the third pair of windings. Loose regulation of this output is obtained by the turns ratio with the -24V output.Circuit OperationThe EV kit schematic (Figure 1) and the MAX774 block diagram in the MAX774/MAX775/MAX776 data sheet show how the circuit works. When the -24V output drops out of regulation, the error comparator in the MAX774 initiates a switching cycle. The P-channel MOSFET (P1) turns on, allowing current to ramp up through the transformer’s lower windings (between the 1/3 tap and ground) and store energy in a magnetic field. When the current through the sense resistor crosses the trip threshold (210mV / 68m Ω= 3.09A), the MOSFET turns off and interrupts the current flow, caus-ing the magnetic field in the transformer to collapse.The transformer forces current through the output diodes, transferring the stored energy to the output fil-ter capacitors. The output filter capacitors smooth the power and voltage delivered to the load. The MAX774waits until it senses the output dropping below the reg-ulation trip point before initiating another cycle. The -24V output is precisely regulated by connecting a volt-age divider, R1 and R2, as shown in Figure 1. The MAX774 regulates the FB pin, keeping it at 0V. The -70V output is regulated using the turns ratios between the -24V and -70V output.Versa-Pac is a trademark of Coiltronics Corp.Output Filter CapacitorsThe positive pin of the filter capacitor for the -70V out-put is connected to the -24V output rather than ground to simplify board layout, enhance stability, allow the use of a lower-cost lower-voltage capacitor, and improve cross-regulation. Ripple on the -24V output is about 200mV and can be reduced further using a capacitor with lower ESR. The Sanyo MV-GX series is recom-mended.__________Applications InformationThis section is intended to aid in transferring the EV kit design to a finished product.Transformer SelectionChoose a transformer with an inductance around 10µH to 15µH per winding, with a saturation-current rating greater than 3A. The MAX774 IRG EV kit uses Coiltronics’ Versa-Pac model VP2-0216. This economi-cal, off-the-shelf transformer uses two trifilar windings for superior coupling and improved regulation of the-70V output. Dale’s LPE6855-100MB and LPE6562-100MB also work, but have different footprints and pinouts and require almost double preloading.If lower output power is desired, increase the current-sense-resistor value and transformer inductance propor-tionally. For example, when reducing power capability to one-half of the current design, double the current-sense resistor to around 130m Ωand the transformer induc-tance per winding to around 20µH to 33µH.Cross RegulationThe -70V output is derived from the -24V output by stacking pairs of windings in an autotransformer config-uration. Cross regulation between the two outputs, how-ever, has limitations. In the on-hook and ringing case,when the -24V output is lightly loaded with the -70V out-put heavily loaded, the -70V output droops. In the off-hook case with the -24V output heavily loaded and the -70V output lightly loaded, the -70V output rises. These effects occur in all transformer-based flyback solutions when the outputs are dissimilarly loaded.Evaluates: MAX774/MAX775/MAX776MAX774 ISDN, Ring-Tone, Power-Supply Evaluation Kit_______________________________________________________________________________________3Figure 1. MAX774 IRG EV Kit SchematicE v a l u a t e s : M A X 774/M A X 775/M A X 776PreloadingUse preloading at the outputs to keep the -70V output in regulation. For designs servicing a five-ringer equiva-lent load, use the following preloads. For the off-hook case, only a couple hundred microamperes are neces-sary to hold down the -70V output. This can be achieved using either a 330k Ωresistor (R4, Figure 1) or zener diode (Figure 2b). For the on-hook case, draw approximately 5.5mA from the -24V output to hold up the -70V output. This 5.5mA can be drawn continuously using two 8.2k Ωresistors (R5 and R6), or intermittently using a transistor to gate the preload while the phone is ringing (Figure 2c). The transistor can be controlled using a microcontroller input/output line, or it can be decoded from the control signals of the AM79R79.To optimize performance or efficiency in applications servicing a different ringer-equivalent load, use the pre-loading curves for guidance (Figure 3 and 4). UseFigure 3 to determine the minimum preloading needed on the -24V output for adequate regulation of the -70V output while the SLIC IC is ringing phones (on-hook case). For example, approximately 50mA is required for a two-phone load. First, follow the vertical line from the -70V output axis up to curve A or B. Next, follow the hor-izontal lines to the corresponding point on the -24V Output Minimum Load axis, in this case 2.5mA using curve A. Preload the -24V output with this current using a resistor R = V / I or 24V / 2.5mA = 9.6k Ω. Round down to the nearest standard value (9.1k Ω). The power rating of the resistor must exceed V 2 / R = 24V 2 / 9.1k Ω=63mW.Use Figure 4 to determine the preloading needed to hold down the -70V output when the -24V output is heavily loaded during off-hook communication. This preloading is intended to protect the AM79R79. The VBAT1 pin of this SLIC IC has a -75V operational range and a -80V absolute maximum rating. If a zener diode is used for preloading, set the zener voltage rating suf-ficiently above the regulation set point to prevent unnecessary current draw.Efficiency, Quiescent Current,and PreloadingThe MAX774 is a pulse-frequency-modulation (PFM)controller designed primarily for use in portable appli-cations. It improves efficiency and reduces quiescent current by switching only as needed to service the load. Prior to preloading, this circuit’s efficiency can be up to 84%, and quiescent current is around 170µA.Resistor preloading reduces efficiency and increasesMAX774 ISDN, Ring-Tone,Power-Supply Evaluation Kit 4_______________________________________________________________________________________Figure 2. Fixed and Switchable Preloading SchemesFigure 3. Cross Regulation for -24V Output Preload Selection (on-hook case)quiescent current. Switchable preloading on the -24V output (Figure 2c), combined with zener clamping of the -70V output (Figure 2b) can be used to reduce cir-cuit current consumption.Current Limiting and Overload ProtectionNeither this EV kit nor competing solutions have a prac-tical level of current protection at the outputs. Use the current-limiting features built into the AM79R79 SLIC IC as described in the data sheet for that product. Using PolySwitch™ resettable fuses at the outputs adds pro-tection to the system at little expense (Figure 5). With a PolySwitch, use faster models such as the surface-mount SMD series.The MAX774 uses an internal current-sense compara-tor that provides pulse-by-pulse input current limiting.However, like competing flyback solutions, this trans-lates to power (and not current) limiting at the output.As the output voltage pulls down during overload, the output current can become high (essentially P IN(MAX)/V OUT ) until inefficiency and parasitic resistance in the circuit dominate. Since the circuit is designed for 9W (min) output to service a five-phone load, short-circuit currents can reach several amperes.Stability and Feedback CompensationThe MAX774 IRG EV kit has been compensated and tested for a full range of loads. When implementing the circuit, ensure stability by following the EV kit board and component list (see PC Board Layout section). Use NPO or COG ceramic capacitors for C1 and C2.Connect the ground terminal of the -70V filter capacitor to the -24V output rather than to ground. (This also improves transient response and simplifies layout.)The MAX774 uses a PFM control scheme that adjusts the pulse rate to regulate power and voltage to the load. Pulse spacing decreases with increasing load. As the pulses begin touching each other, the circuit transi-tions into continuous-conduction mode. Stable transi-tion into continuous conduction occurs through pulse grouping, with gaps less than two cycles wide between groups, and output ripple no larger than the single-cycle voltage ripple at light loads (Figure 6).Poor PC board layout or improper compensation can cause instability by corrupting the feedback signals.Instability is identified by either grouped pulses, large gaps between groups, or output ripple larger than the single-cycle voltage ripple (Figure 7). It can cause increased audio interference. Test for instability with aEvaluates: MAX774/MAX775/MAX776MAX774 ISDN, Ring-Tone, Power-Supply Evaluation Kit_______________________________________________________________________________________5Figure 4. Cross Regulation for -70V Output Preload Selection (off-hook case)Figure 5. Overload Protection Using Raychem PolySwitch Resettable FusesPolySwitch is a trademark of Raychem Corp.M A X 774I R G E V F I G 065µs/divV OUT1 = -23.6V, V OUT2 = -70V, I OUT2 = -30mA, V IN = 9VA: MOSFET DRAIN, 20V/divB: V OUT1, 100mV/div, AC COUPLED C: TRANSFORMER CURRENT, 1A/divFigure 6. Normal Light-Load Switching WaveformsE v a l u a t e s : M A X 774/M A X 775/M A X 7769V input by applying a 5mA to 10mA load on the -24V output and then sweeping the -70V output to full-load. If instability occurs due to errors in the design if a pro-duction board, try removing C7 and C8.If the feedback resistors are changed, adjust the com-pensation capacitors. In general, M x C1 x R1 = C2 x R2with C2 around 1nF provides the best results, where M ranges from 0.5 to 1.PC Board LayoutUse of the tested PC board design is strongly recom-mended. Components can be placed closer together to conserve space. Observe the following guidelines in PC board design:1)Place the current-sense resistor (R3) within 0.2in.(5mm) of the MAX774, directly between the V+ and CS pins. The V+ and reference-bypass capacitors (C3 and C4) must be placed as close as possible to their respective pins. Figure 8 shows the recom-mended layout and routing for these components. 2)Place the voltage-feedback resistors (R1 and R2)and compensation capacitors (C1 and C2) within 0.2in. (5mm) of the MAX774’s FB pin. Keep high-current traces and noisy signals, such as EXT, away from FB. On multilayer boards, if inner ground or power planes are thinly separated from the top-side copper, use small cutouts in the ground plane under the FB node to reduce stray capacitance and capacitive coupling. 3)Make high-power traces, highlighted in the EV kit schematic (Figure 1), as short and as wide as possi-ble. Make the supply-current loop (formed by C5,C6, R3, P1, and L1) and output current loops (L1,D1, and C9 for the -24V output; L1, D2, C9, and C10for the -70V output) as tight as possible to reduce radiated noise. 4)Route transformer L1’s ground pins (C5, C6, and C10) to a common ground point in a star ground configuration using top-side copper fill as a pseudo-ground plane. On multilayer boards, use the star ground as described, and connect it to the inner ground plane using vias. Build up separate star grounds for the power components and controller IC (Figure 9), and then couple them together through the back side of the board using several vias.5)For reduced noise and improved heat dissipation,keep the extra copper on the PC board’s compo-nent and solder sides, rather than etching it away,and connect it to ground for use as a pseudo-ground plane.DC-DC Converter Placementand Audio InterferencePrevent interference through careful board and system design. Place the DC-DC converter and high-speed CMOS logic on a corner of the PC board, away from sensitive analog circuitry such as audio-signal pream-plifier stages (Figure 10). In very compact designs, use localized shielding around sensitive analog stages. Use a separate ground plane for analog circuitry. Where necessary, reduce supply ripple to sensitive analog stages by using LC Pi filters or specialized, low-dropout linear regulators. Tiny, inexpensive linear regulators,such as the SOT23 MAX8863 and µMAX MAX8865, are designed specifically for this purpose. These solutions are commonly used in cellular phones and other portable communications devices.MAX774 ISDN, Ring-Tone,Power-Supply Evaluation Kit 6_______________________________________________________________________________________M A X 774I R G E V F I G 07250µs/divV OUT1 = -23.6V, V OUT2 = -70V, I OUT2 = -30mA, V IN = 9V A: MOSFET DRAIN, 20V/divB: V OUT1, 100mV/div, AC COUPLED C: TRANSFORMER CURRENT, 1A/divC2 REMOVEDFigure 7. Unstable Switching Waveforms from Improper Compensation or Board DesignFigure 8. Recommended Placement and Routing of R3, C3,and C4Modification for -48V and -70V OutputsThe MAX774 IRG EV kit board design allows leeway for adapting the circuit for -48V and -70V outputs. Perform the following steps for implementation:1)Cut the trace from the transformer’s 1/3 tap to theoutput diode, and then solder a wire jumper from the transformer’s 2/3 tap to the diode (D2) (Figure 11).2)Swap output filter capacitors C9 with C10. Be sure toconnect them with the correct polarity. This exchange ensures that the output filter capacitors have voltage ratings exceeding their respective outputs.3)Replace voltage-feedback resistor R2 with a 31.6k Ωresistor.4)Replace compensation capacitor C1 with a 330pFceramic capacitor.5)Change R5 and R6 to 16k Ωresistors.Evaluates: MAX774/MAX775/MAX776MAX774 ISDN, Ring-Tone, Power-Supply Evaluation Kit_______________________________________________________________________________________7SWITCHING DC-DCCONVERTERSSHIELDING (IF NEEDED)DIGITAL LOGIC= LC Pi FILTERS OR LDO LINEAR REGULATORFigure 10. Place the DC-DC converter and CMOS logic away from sensitive analog circuitry.PLACE POWER COMPONENTS CLOSE TOGETHER;MAKE POWER TRACES SHORT AND WIDE.LEAVE THE EXTRA FRONT- AND BACK-SIDE COPPER ON THE BOARD AS A PSEUDO-GROUND PLANE.PLACE GROUND PINS OF POWER COMPONENTS CLOSE TOGETHER AND ORIENT TO CONVERGE, FORMING A STAR GROUND.PLACE VOLTAGE-FEEDBACK COMPONENTS AS CLOSE TO THE FB PIN AS POSSIBLE.PLACE BYPASS CAPACITORS CLOSE TO THE REF AND V+ PINS; ORIENT AS SHOWN.TIE THE IC GROUND AND POWER STAR GROUND TOGETHER USING VIAS AND A WIDE BACK-SIDE GROUND TRACE. ON MULTILAYER BOARDS, TIE INTERIOR GROUND PLANES TO THE POWER STAR GROUND.PLACE CURRENT-SENSE RESISTOR R3 WITHIN 0.2IN. OF CS AND V+ PINS.Figure 9. Key Layout FeaturesE v a l u a t e s : M A X 774/M A X 775/M A X 776MAX774 ISDN, Ring-Tone, Power-Supply Evaluation Kit Maxim cannot assume responsibility for use of any circuitry other than circuitry entirely embodied in a Maxim product. No circuit patent licenses are implied. Maxim reserves the right to change the circuitry and specifications without notice at any time.8_____________________Maxim Integrated Products, 120 San Gabriel Drive, Sunnyvale, CA 94086 408-737-7600©1997 Maxim Integrated ProductsPrinted USAis a registered trademark of Maxim Integrated Products.Modification for European ApplicationsApplications targeted for Europe may require a lower voltage on the -70V output to meet European safety regulations. In such cases, modify the circuit for -48V and -70V outputs as described previously, then change the feedback resistor R2 to reduce output voltages to -43V and -65V. Add a clamping zener to preload the high-voltage output. Since the MAX774 regulates the FB pin to 0V, R2 will be:R2 = (V REF / V OUT ) x R1where V REF = 1.5V.Adjust C1 so that R1C1 = R2C2. Verify correct com-pensation by examining stability over all loading combi-nations, especially with the -43V output lightly loaded and the -65V output moderately and heavily loaded.Suggested values are R1 = 1M Ω, C1 = 330pF, R2 =34.8k Ω, C2 = 1000pF.RECONNECT TRACE HERECUT TRACE HEREFigure 11. PC Board Changes for -48V and -70V OperationFigure 12. MAX774 IRG EV Kit Component Placement Guide (Top Silkscreen)Figure 13. MAX774 IRG EV Kit PC Board Layout—Component SideFigure 14. MAX774 IRG EV Kit PC Board Layout—Solder Side1.0"1.0" 1.0"。
回馈式源载系统 IT6000B系列 用户手册说明书

回馈式源载系统IT6000B系列用户手册型号:IT6000B系列版本:V1.3/06,2020声明©Itech Electronic,Co.,Ltd. 2020根据国际版权法,未经Itech Electronic,Co.,Ltd.事先允许和书面同意,不得以任何形式(包括电子存储和检索或翻译为其他国家或地区语言)复制本手册中的任何内容。
手册部件号商标声明Pentium是Intel Corporation 在美国的注册商标。
Microsoft、Visual Studio、Windows和MS Windows是Microsoft Corporation在美国和/或其他国家/地区的商标。
担保本文档中包含的材料“按现状”提供,在将来版本中如有更改,恕不另行通知。
此外,在适用法律允许的最大范围内,ITECH不承诺与本手册及其包含的任何信息相关的任何明示或暗含的保证,包括但不限于对适销和适用于某种特定用途的暗含保证。
ITECH对提供、使用或应用本文档及其包含的任何信息所引起的错误或偶发或间接损失概不负责。
如ITECH与用户之间存在其他书面协议含有与本文档材料中所包含条款冲突的保证条款,以其他书面协议中的条款为准。
技术许可本文档中描述的硬件和/或软件仅在得到许可的情况下提供并且只能根据许可进行使用或复制。
限制性权限声明美国政府限制性权限。
授权美国政府使用的软件和技术数据权限仅包括那些定制提供给最终用户的权限。
ITECH在软件和技术数据中提供本定制商业许可时遵循FAR12.211(技术数据)和12.212(计算机软件)以及用于国防的DFARS252.227-7015(技术数据-商业制品)和DFARS227.7202-3(商业计算机软件或计算机软件文档中的权限)。
安全声明“小心”标志表示有危险。
它要求在执行操作步骤时必须加以注意,如果不正确地执行或不遵守操作步骤,则可能导致产品损坏或重要数据丢失。
在没有完全理解指定的条件且不满足这些条件的情况下,请勿继续执行小心标志所指示的任何不当操作。
POWER FEED 10S操作手册说明书
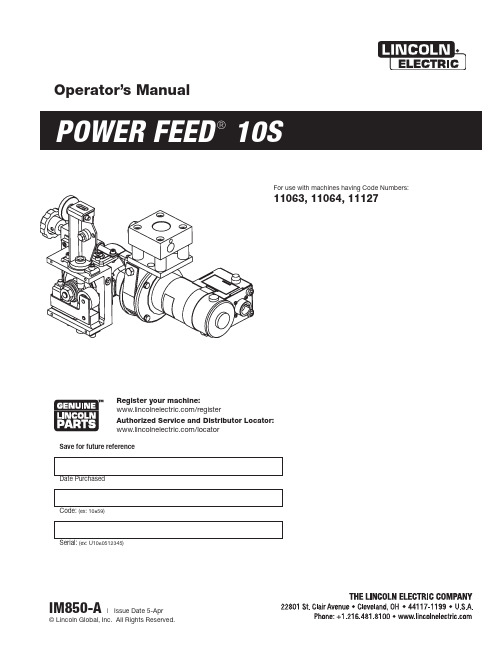
Operator’s ManualSave for future reference Date PurchasedCode: (ex: 10859)Serial: (ex: U1060512345)For use with machines having Code Numbers: 11063, 11064, 11127Register your machine:/registerAuthorized Service and Distributor Locator: /locatorMar ‘95for selecting a QUALITY product by Lincoln Electric. We want you to take pride in operating this Lincoln Electric Company product ••• as much pride as we have in bringing this product to you!vvPRODUCT SUMMARYThe Power Feed 10S series of Automatic Wire Drives are designed for hard automation, submerged arc welding. The heavy-duty gearbox and feed plate have many years of proven reliability while a new perma-nent magnet motor has been added.The Power Feed 10S wire drives consist of a high torque motor and gearbox assembly with a heavy-duty feed plate housing knurled drive rolls for positive, accurate wire feeding of heavy welding wire. The Power Feed 10S has many axes of rotation for ease of fixturing and locating.RECOMMENDED PROCESSES• The Power Feed 10S series of wire drives are best suited for submerged arc welding.PROCESS LIMITATIONS• MIG welding• Robotic applicationsEQUIPMENT LIMITATIONSThe Power Feed 10S series of wire drives cannot be used with the NA3, NA-4, or NA-5 series of Lincoln Automatics.COMMON EQUIPMENT PACKAGESBasic Package:K2344-1Power Wave 1000 AC/DCK2362-1PF-10A ControllerK2312-1PF-10SF Wire DriveBasic Package with optional kits:K2311-1PF-10SM Motor Retrofit KitK2370-1PF-10S Wire Drive (includes CrossSeam Adjuster and Automatic FluxHopper with hardware to connect toTC-3 Travel Carriage)K2282-1System Interface (Phase Generator)DESIGN FEATURES•Closed-loop speed control.• Knurled drive rolls.• Heavy cast aluminum gearbox housing and feed plate assembly.• Wire straightener.• 32Vdc permanent magnet, high torque motor.• Conversion kit included to change speed range.• Voltage sense leads included for precision welding performance.LOCATION OF COMPONENTSCAUTIONPOWER WAVE AC/DC 1000AMP SUBARC SYSTEM CONNECTIONS(See Figure A.1)1- Work cable connection3- 14 pin wire feeder control cable4- 5 pin Arclink control cable to user interface7- Electrode cable connectionMOUNTING DIMENSIONSThe PF-10S can be mounted by using the four 3/8-16 tapped holes or the two 0.562 through holes. See mounting hole locations (Figure A.2).FIGURE A.1 FIGURE A.2Due to the Power Wave AC/DC”s ability to produce either a DC positive, DC negative or AC output the elec-trode and work connections do not need to be reversed for the different polarities. Additionally no DIP switch changes are required to switch between the different polarities. All of this is controlled internally by the Power Wave AC/DC. The following directions apply to all polar-ities:Connect a work lead of sufficient size (Per Table A.1) and length between the "work" stud (located beneath the spring loaded output cover on the front of the machine) and the work. For convenience, the work lead can be routed behind the left strain relief (under the spring loaded output cover), along the channels, and out the back of the machine. Be sure the connection to the work makes tight metal-to-metal electrical contact. The work piece connection must be firm and secure. Excessive voltage drops caused by poor work piece connections often result in unsatisfactory welding per-formance. To avoid interference problems with other equipment and to achieve the best possible operation, route all cables directly to the work and wire feeder. Avoid excessive lengths and do not coil excess cable. Connect the electrode cable to the "ELECTRODE" stud on the power source (located behind the cover plate on the lower left side). For convenience, the cable can be routed through the oval hole in the left cable tray before being connected to the output terminals. Connect the other end of the electrode cable to the nozzle. Be sure the connection makes tight metal-to-metal electrical contact. The electrode cable should be sized according to the specifications given in Table A.1.TABLE A.1 - Output Cable Guidelines ArrayWhen using inverter type power sources like the Power Wave, use the largest welding (electrode and work) cables that are practical. When pulsing, thepulse current can reach very high levels. Voltagedrops can become excessive, leading to poor weldingnection often result in unsatisfactory pulse weld-ing performance.WELDING WITH MULTIPLE ARCSSpecial care must be taken when more than one arc is welding simultaneously on a single part. Arc blow and arc interference may occur or be magnified. Each power source requires a work lead from the work stud to the welding fixture. Do not combine all of the work leads into one lead. Always weld in a direction away from the work leads. Connect all of the work sense leads from each power source to the work piece at the end of the weld, such that they are out of the path of the weld current.For the best results when pulse welding, set the wire size and wire feed speed the same for all the arcs. When these parameters are identical, the pulsing fre-quency will be the same, helping to stabilize the arcs.If the voltage sensing is enabled but the sense leads are missing, improperly connected, or if the electrode polarity switch is improperly configured extremely high welding outputs may occur.In extremely sensitive applications requiring voltage sense leads, it may be necessary to route cables that contain the sense leads away from the electrode and work welding cables. For more information regarding the placement of voltage sense leads, see the section entitled "Welding with Multiple Independent Power Waves."GEAR RATIO CONVERSION KITS (SEE INSTRUCTIONS INCLUDED WITH CON-VERSION KIT)1. Remove the 2 hex head screws and the 2 slot headscrews holding the Motor to the Wire Drive Gearbox assembly.2. Remove existing Adapter Plate and MotorAssembly.3. Take the two long screws removed in step 1 andscrew one into each of the tapped holes located on the face of fiber input helical gear. Insert the screws through the full thickness of the gear, and using a screwdriver wedged between the screws to prevent rotation, remove the hex nut that holds the gear to the shaft. Remove plain washer.4. Pull the gear from the shaft using the screws as apulling device.5. Be certain woodruff key is properly located on theshaft. Screw the adapter plate and motor assembly mounting screws into the new fiber input helical gear from the stenciled side and place the gear on the shaft. Replace plain washer, tighten the hex nut, and remove the adapter plate and motor assembly mounting screws from the gear.6. Support the pinion properly and, with the propersize punch, drive the roll pin that holds the pinion out of the shaft. Pull the pinion off. Remove the Ring Magnet from the pinion gear and snap it onto the new pinion gear. Before installing the new pin-ion gear with the Ring Magnet onto the motor shaft, ensure that the flat washer is located at the bottom of the shaft. Install the new pinion and replace the roll pin.7. Cover the teeth of the motor pinion and the inputgear with a non-fluid molydisulfide type grease such as Non-Fluid Oil Corporation’s A-29 Special/MS Lubricant. This grease can be scooped from the cavity of the gear case.8. Reassemble the motor on the gearbox; make surethe gears mesh properly and the adapter plate locating bead is in its cavity. Replace and tighten the four screws removed in step 1.9. See the power source manual on how to config-ure the power source DIP switches for the new gear ratio.K2311-1 MOTOR CONVERSION KIT (FOR 142:1 NA STYLE WIRE DRIVES)--This conver-tion kit converts old NA style wire drives.1. Remove the 2 hex head screws and the 2 slot head screws holding the Motor to the Wire Drive Gearbox assembly.2. Remove existing Adapter Plate and Motor Assembly.3. The Conversion Kit Motor is shipped configured for a 142:1 gear ratio. The existing gearbox must be con-figured for a 142:1 gear ratio for the Conversion Kit to assemble correctly. If both assemblies are not con-figured for the same gear ratio, this must be done before continuing. (See Gear Ratio Conversion Kit instructions.)4. Cover the teeth of the new Motor pinion gear with a non-fluid molydisulfide type grease such as Non-Fluid Oil Corporation’s A-29 Special/MS Lubricant. This grease can be scooped from the cavity of the gear case First Chamber.5. Reassemble the new Adapter Plate and Motor Assembly on the Wire Drive Gearbox; making sure the gears mesh properly and the Adapter Plate locat-ing bead is in its cavity. Replace and tighten the 4 screws removed in step 1.SAFETY PRECAUTIONS ELECTRIC SHOCK can kill.• Only Qualified personnel shouldperform this maintenance.•Turn the input power OFF at thedisconnect switch or fuse boxbefore working on this equipment.•Do not touch electrically hot parts.ROUTINE MAINTENANCE• Check weld cables, control cables and gas hoses for cuts.• Clean and tighten all weld terminals.•Inspect and clean drive rolls and inner wire guide and replace if worn.PERIODIC MAINTENANCE• Every six months check the motor brushes. Replace them if they are less than 1/4" long.•Every year inspect the gearbox and coat the gear teeth with a moly-disulfide filled grease. DO NOT use graphite grease.CALIBRATION SPECIFICATIONAll calibration is factory set on the Power Feed 10S.To verify the wire feed speed:• Press the INCH DOWN switch and adjust the wire feed speed to 100 in/min (2.54m/min).• Measure the actual wire feed speed with a calibrated wire feed speed tachometer.• The measured wire feed speed should be within ±2% of the set value.SENSE LEAD FUSEThere should never be any current flowing through the sense leads!There is a fuse located in the sense lead circuit that is mounted in the wire drive Connection Box which protects the sense lead circuit from weld current due to incorrect configuration. If this fuse ever opens, check the sense lead configuration to ensure proper connections. The fuse must be replaced with a comparable fuse with a rating of less than 1 amp before welding. The fuse being open or missing would have the same effect on the welding as having a disconnected sense lead.This Troubleshooting Guide is provided to help you locate and repair possible machine malfunctions.Simply follow the three-step procedure listed below.Step 1.LOCATE PROBLEM (SYMPTOM).Look under the column labeled “PROBLEM (SYMP-TOMS)”. This column describes possible symptoms that the machine may exhibit. Find the listing that best describes the symptom that the machine isexhibiting.Step 2.POSSIBLE CAUSE.The second column labeled “POSSIBLE CAUSE ” lists the obvious external possibilities that may contribute to the machine symptom.Step 3.RECOMMENDED COURSE OF ACTIONThis column provides a course of action for the Possible Cause, generally it states to contact your local Lincoln Authorized Field Service Facility.If you do not understand or are unable to perform the Recommended Course of Action safely, contact your local Lincoln Authorized Field Service Facility.HOW TO USE TROUBLESHOOTING GUIDEService and Repair should only be performed by Lincoln Electric Factory Trained Personnel.Unauthorized repairs performed on this equipment may result in danger to the technician and machine operator and will invalidate your factory warranty. For your safety and to avoid Electrical Shock, please observe all safety notes and precautions detailed throughout this manual.__________________________________________________________________________L 12119JapaneseChineseKoreanArabicREAD AND UNDERSTAND THE MANUFACTURER’S INSTRUCTION FOR THIS EQUIPMENT AND THE CONSUMABLES TO BE USED AND FOLLOW YOUR EMPLOYER’S SAFETY PRACTICES.SE RECOMIENDA LEER Y ENTENDER LAS INSTRUCCIONES DEL FABRICANTE PARA EL USO DE ESTE EQUIPO Y LOS CONSUMIBLES QUE VA A UTILIZAR, SIGA LAS MEDIDAS DE SEGURIDAD DE SU SUPERVISOR.LISEZ ET COMPRENEZ LES INSTRUCTIONS DU FABRICANT EN CE QUI REGARDE CET EQUIPMENT ET LES PRODUITS A ETRE EMPLOYES ET SUIVEZ LES PROCEDURES DE SECURITE DE VOTRE EMPLOYEUR.LESEN SIE UND BEFOLGEN SIE DIE BETRIEBSANLEITUNG DER ANLAGE UND DEN ELEKTRODENEINSATZ DES HER-STELLERS. DIE UNFALLVERHÜTUNGSVORSCHRIFTEN DES ARBEITGEBERS SIND EBENFALLS ZU BEACHTEN.JapaneseChineseKoreanArabicLEIA E COMPREENDA AS INSTRUÇÕES DO FABRICANTE PARA ESTE EQUIPAMENTO E AS PARTES DE USO, E SIGA AS PRÁTICAS DE SEGURANÇA DO EMPREGADOR.。
PMM人工电源网络商品说明书

The AMN - Artificial Mains Network, also known as LISN - Line Impedance Stabilization Network is the ancillary device intended for repeatable and accurate measurement of the disturbance voltage that an EUT (Equipment Under T est) may inject into the power line or mains.This is obtained by providing well known impedance value and phase response across the frequency range of the test.L1-150M and L1-150M1 are a single-path LISN (Line Impedance Stabilization Network) designed to be easily used for conducted disturbances measurements according to different standards for Automotive and ISM (Industrial, Scientific, Medical) applications.Selecting the standard is as fast as the turn of a rotary switch located on the rear panel.PMM Artificial Mains Networks provide robust and stable m echanical construction, high quality electric components, easy and perfect grounding, solid input and output power connections. They can be used in conjunction with any EMI receiver or spectrum analyzer and offer features required for safe, repeatable and accurate measurements.Multi-standard Single-path LISNProvided Features•Powering the EUT•EUT termination to a standardizedimpedance respect to the reference ground •Coupling the measuring receiver to the disturbance generated by the EUT•Decoupling the measuring receiver from unwanted RF signals from the power lineMain Features•L1-150M: 100 kHz to 200 MHz frequency range •L1-150M1: 10 kHz to 400 MHz frequency range •Multi standard design •150 A max output current •Suitable also for DC lines•Large baseplate for optimal grounding •Robust, compact construction •Screw terminals for safe wiring•Meets the requirements of several standards including CISPR 16-1-2, CISPR 25, ISO 11452-2/4/5,ISO 7637-2, MIL-STD-461F, DO-160, ED-14GProvided by: (800)404-ATECAdvanced Test Equipment Rentals®Frequency range Continuous rated output currentMax. output current @ 45 °C Max. permissible operating voltagesEUT supply frequency range Equivalent circuit RF output connector EUT connectionLine input connection Ground connectionOperating temperature Storage temperature Dimensions (W x H x D)WeightReceiversLISNRFI Filters• 7010/00: EMI receiver 150 kHz to 1 GHz • 7010/01: EMI receiver 9 kHz to 1 GHz • 7010/02: EMI receiver 9 kHz to 30 MHz • 7010/03: EMI receiver 9 kHz to 3 GHz • 9010: EMI receiver 10 Hz to 30 MHz • 9010F: EMI receiver 10 Hz to 30 MHz• 9010/03P: EMI receiver 10 Hz to 300 MHz • 9010/30P: EMI receiver 10 Hz to 3 GHz •9010/60P: EMI receiver 10 Hz to 6 GHz• L2-16B: single phase AMN, 16 A • L3-32: 4 lines, 3-phase AMN, 32 A • L3-64: 4 lines, 3-phase AMN, 63 A• L3-64/690: 4 lines, 3-phase AMN, 63 A • L3-100: 4 lines, 3-phase AMN, 100 A • L3-500: 4 lines, 3-phase AMN, 500 A • L1-500: single phase AMN, 500 A•L2-D: Delta LISN for telecom, 2 A, 150 Ω• FIL-L2-16F: single phase RFI filter, 16 A • FIL-L2-24M: single phase RFI filter, 24 A • FIL-L3-32M: 3-phase+neutral RFI filter, 32 A •FIL-L3-70M: 3-phase+neutral RFI filter, 70 A100 kHz to 200 MHz L1-150M, L1-150M1Multi-standard Single-path LISNOrdering Information:L1-150M - L1-150M1 Artificial NetworkIncludes: Operating Manual, RF Cable, N-BNC adapter, Calibration CertificateOptional accessories:SBRF4: RF switching boxAutomatic (in conjunction with PMM receivers) andmanual switching of up to four single-path AMN. Internal 50 Ohm terminations and switchable 150 kHz high-pass filter. Low insertion loss.Max. operating frequency: 108 MHz.L 1150-F E N -40704 - S p e c i fi c a t i o n s s u b j e c t t o c h a n g e s w i t h o u t p r i o r n o t i c eSPECIFICATIONSRelated Products•Electrical safety and presence of ground protection relays do require the installation of properly rated insulating transformer(s) between mains power line and AMN line inputs.•High mains noise may require the installation of properly rated mains filters to reduce the level of unwanted signals.Sales Office:Via Leonardo da Vinci, 21/2320090 Segrate (Milano) - ITALY Phone: +39 02 2699871Fax: +39 02 26998700E-Mail:**************************Internet: www.narda-sts.itHeadquarter:Via Benessea, 29/B17035 Cisano sul Neva (SV) - ITALY Phone: +39 0182 58641Fax: +39 0182 586400L1-150ML1-150M110 kHz to 400 MHz100 A150 A 600 Vdc 300 Vac DC to 440 Hz (5 μH+0/1 Ω)//50 Ω N female, 50 Ω Screw terminal M10 Screw terminal M10 2x Screw terminal M10-10 to +45 °C -25 to +70 °C 230 x 105 x 410 mm5 kg。
联想网御安全网关Power V 作业指导书

联想网御安全网关Power V作业指导书江苏国瑞信安科技有限公司二零一一年七月目录第1章如何开始 (1)1.1 登录管理界面 (1)1.1.1 登录方法 (1)1.1.2 管理认证 (2)1.1.3 登录过程 (3)1.1.4 网御安全网关Power V的一般配置过程 (4)1.1.5 退出登录 (4)第2章系统配置 (5)2.1 日期时间 (5)2.2 系统参数 (6)2.3 系统更新 (6)2.3.1 模块升级 (6)2.3.2 导入导出 (7)2.4 管理配置 (9)2.4.1 管理主机 (9)2.4.2 管理员账号 (10)2.4.3 管理证书 (11)2.5 报告设置 (12)2.5.1 日志服务器 (12)2.5.2 报警邮箱设置 (12)第3章策略配置 (14)3.1 安全选项 (14)3.1.1 包过滤策略 (14)3.1.2 IP/MAC检查 (15)3.1.3 允许所有非IP协议 (15)3.2 安全规则 (16)3.2.1 包过滤规则 (17)3.2.2 NA T规则 (18)3.2.3 地址列表、服务列表 (19)3.3 地址绑定 (20)3.4 带宽管理 (23)3.5 黑名单 (24)3.6 连接管理 (25)3.6.1 基本参数 (25)3.6.2 连接规则 (25)3.6.3 连接状态 (27)第4章网络配置 (29)4.1.1 物理设备 (29)4.1.2 VLAN设备 (30)4.1.3 桥接设备 (31)第5章绿色上网 (33)5.1 URL过滤策略 (33)5.2 绿色上网规则 (35)第6章系统监控 (35)6.1 网络设备 (35)6.2 HA状态 (37)6.3 资源状态 (38)6.4 日志信息 (39)6.4.1 日志查看 (39)6.4.2 包过滤日志报表 (40)6.4.3 P2P报表 (41)6.4.4 深度过滤报表 (41)6.5 用户信息 (42)6.6 连接状态 (42)6.7 连接统计 (44)6.8 深度过滤 (44)6.9 带宽监控 (45)6.10 网络调试工具 (45)6.11 路由监控 (46)6.12 动态路由监控 (47)第1章如何开始1.1 登录管理界面1.1.1 登录方法安全网关共有四种管理方式:1)Web界面管理2)串口命令行管理3)远程SSH登录管理4)PPP拨号接入管理。
NDC说明书

探头类型: TM710e
出版参考: 105/14686-07SA 版本 1
版权说明
在使用手册中阐述的仪器包括有一个或多个计算机程序,这些计算机程序属 NDC 红外技术公司机密并受版权保护。NDC 红外技术公司只允许在正常使用产品时,使用这些程序,而不许可将其用于其它情况。严禁设备买方或他人以任何形式将 上述程序的原件、拷贝或经编辑、转换而成的程序副本挪为它用。本手册内容未经版权所有者允许不得部份摘录或全部引 用。 NDC 对本手册不作任何保证。 对于本手册中包含的错误或因使用本手册中信息导致的结果性损害或附带性损害, NDC 概不负责。 © NDC Infrared Engineering 2008 保留所有权利 NDC 美国、英国和中国办事处。 请访问 了解办事处的详细信息。 隶属于 Spectris 集团
4
4.1 4.2 4.2.1 4.2.2 4.2.3 4.3 4.4 4.5 4.6 4.7 4.7.1 4.7.2 4.7.3 4.7.4 4.8 4.8.1 4.8.2 4.9 4.10 4.10.1 4.10.2 4.10.3 4.10.3.1 4.10.3.2
安装
4-1
简要安装说明 .......................................................................................................................................4-1 恶劣和危险环境 ....................................................................................................................................4-2 Atex 认证 .............................................................................................................................................4-2 安装注意事项 .......................................................................................................................................4-2 设备安装 ..............................................................................................................................................4-2 地点要求 ..............................................................................................................................................4-3 EMC 预防措施 .....................................................................................................................................4-3 开箱......................................................................................................................................................4-4 存储......................................................................................................................................................4-4 安装探头 ..............................................................................................................................................4-4 定位......................................................................................................................................................4-4 安装......................................................................................................................................................4-5 安装空气净化装置 ................................................................................................................................4-5 连接水冷却 ...........................................................................................................................................4-6 安装外围设备 .......................................................................................................................................4-6 外壳安装 ..............................................................................................................................................4-6 仪表板装置 ...........................................................................................................................................4-7 24V 电源装置 ......................................................................................................................................4-8 系统连接 ..............................................................................................................................................4-9 以太网电缆 ...........................................................................................................................................4-9 电缆屏蔽终端 .....................................................................................................................................4-10 电源配件 ............................................................................................................................................4-10 以太网供电.....................................................................................................................................4-10 独立电源 ........................................................................................................................................4-11
UP2210使用手册_4.5_CH

祝贺您选择了我们的 UP-2210 在线式电能质量监测仪!如果您对我们的仪表有任何问题,请 直接联系我们或向我们的本地代表处询问。
顺颂商祺! 瑞典联合电力公司
Unipower AB
Copyright (c) UNIPOWER AB Alingsås, Sweden 2006 E-mail: mail@unipower.se Internet: www.unipower.se
UP-2210 型在线式电能质量监测仪,由瑞典联合电力公司(Unipower AB Sweden)研制生 产,具有 4 路 0-275V 差分电压输入通道和 4 路 0-6A 差分电流输入通道。可以测量几乎所有 的电力参数和电能质量参数,它可同时具有 RS232、RS485、以太网、内置调制解调器、外置 调制解调器通讯方式。它采用 32 位 DSP 数字信号处理技术,高精度、多功能,全电子化,无 任何可动部件(如硬盘、风扇等),特别适合安装在现场,完全能够满足电能质量在线监测 的所有要求。
山特webpower卡使用手册
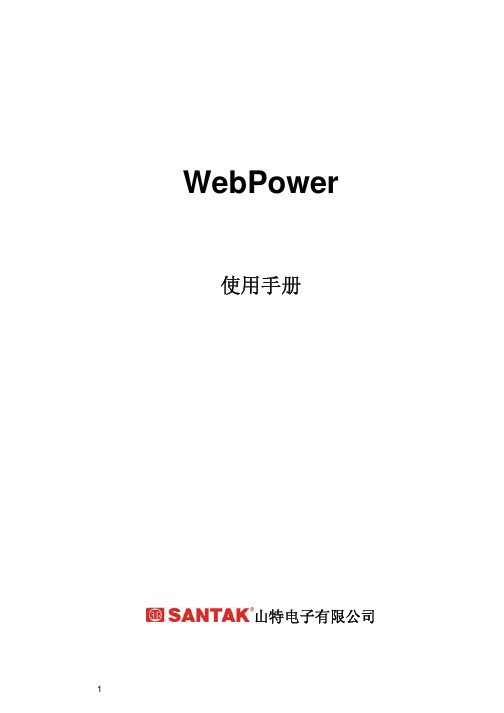
联邦电信委员会(Federal Communications Commission ,FCC)
此仪器已经交过测试并且符合联邦电信委员会第15章有关等级B的数字仪器相关限制。当仪器用作商 业用途时,这些限制的目的是为有害的干扰提供合理的保护。
CE公告
此设备遵守了欧盟(European Community)的EMC规定,并且符合或超过了下列的技术标准: • EN 55022:1998 ⎯ ‘有关信息科技仪器之无线干扰特性的限制与方法。’ 此仪器符合了CISPR的等
Pro的一半。
图ڌ1-1 WebPower Pro/mini USHA ͉و
4
Webpower 使用手册
WebPower 的资源
WebPower的光盘片包含了快速安装手册、使用者手册、MIB档案和WebPower 对不同操作系统(OS)的关机软件,你可以自行设定这些关机软件。
1. WebPower快速安装手册提供了如何利用 Windows OS 工作站来安装和设 定WebPower的细节 。
ୋ̬ ஷ过Java监છWebPower/UPS ________________________________ 55
Java 监䕦ኜ __________________________________________________________ 55 UPSٙ䢮行记录监䕦ኜ _________________________________________________ 57 UPSʘ扩࢝䢮行记录监䕦ኜ ______________________________________________ 58
2. WebPower 使用者手册提供更为详细的WebPower 安装和设定信息。 3. WebPower提供线上说明的功能,以便提供管理WebPower更明确的指示。
Powerful多媒体安装项目器说明书

Powerful multimedia installation projector equipped to take on the mostdemanding integration projectsRemote control(Included accessory)OptionsInstallation ProjectorPA621U / PA521U / PA671W / PA571W / PA721X / PA621XCable cover NP04CVOption lensNP11FL NP30ZL NP12ZL NP13ZL NP14ZL NP15ZLWireless LAN unitNP02LM1NP02LM2NP02LM3Replacement lampNP26LPCabinet dimensions *Stated projection distances are standard values.For a stack installation, the recommended projection distances will be different.*The values in the tables are design values and may vary.Throw distance and screen sizePA621U/PA521U (Aspect ratio 16:10)30"40"60"80"100"120"150"200"240"300"400"500"-0.71.01.41.72.12.6-----0.7 - 0.91.0 - 1.31.5 - 1.92.0 - 2.62.5 - 3.33.0 - 3.93.8 - 4.95.1 - 6.66.1 - 7.97.6 - 9.910.2 - 13.212.7 - 16.5--1.0 - 1.31.4 - 1.81.7 - 2.22.0 - 2.72.6 - 3.43.4 - 4.54.1 - 5.45.2 - 6.86.9 - 9.0 8.7 - 11.3-1.2 - 2.51.9 - 3.82.5 - 5.13.2 - 6.33.8 - 7.64.8 - 9.5 6.4 - 12.77.6 - 15.3 9.6 - 19.112.8 - 25.516.0 - 31.9--3.7 - 6.05.0 - 8.0 6.3 - 10.1 7.5 - 12.1 9.4 - 15.212.6 - 20.315.2 - 24.419.0 - 30.525.4 - 40.731.8 - 50.9--5.9 - 9.0 7.9 - 12.1 9.9 - 15.111.9 - 18.214.9 - 22.820.0 - 30.524.0 - 36.630.1 - 45.840.1 - 61.150.2 - 76.4PA721X/PA621X (Aspect ratio 4:3)30"40"60"80"100"120"150"200"240"300"400"500"(0.61x0.46m)(0.81x0.61m)(1.22x0.91m)(1.63x1.22m)(2.03x1.52m)(2.44x1.83m)(3.05x2.29m)(4.06x3.05m)(4.88x3.66m)(6.10x4.57m)(8.13x6.10m)(10.16x7.62m)-0.6 1.0 1.3 1.62.02.5-----0.7 - 0.90.9 - 1.21.4 - 1.91.9 - 2.52.4 - 3.22.9 -3.83.7 -4.84.9 - 6.45.9 - 7.77.4 - 9.6 9.8 - 12.812.3 - 16.0--1.0 - 1.31.3 - 1.71.6 - 2.12.0 - 2.62.5 - 3.23.3 - 4.34.0 - 5.25.0 - 6.56.7 - 8.7 8.4 - 10.9-1.2 - 2.41.8 - 3.72.4 - 4.93.0 - 6.13.7 - 7.44.6 - 9.2 6.1 - 12.3 7.4 - 14.8 9.2 - 18.512.3 - 24.715.4 - 30.8--3.6 - 5.84.8 - 7.86.0 - 9.7 7.3 - 11.7 9.1 - 14.712.2 - 19.614.7 - 23.618.4 - 29.524.6 - 39.430.7 - 49.2--5.7 - 8.7 7.6 - 11.6 9.6 - 14.611.5 - 17.614.4 - 22.019.3 - 29.423.2 - 35.329.1 - 44.238.8 - 59.048.6 - 73.8PA671W/PA571W (Aspect ratio 16:10)WUXGA typeXGA typeWXGA type30"40"60"80"100"120"150"200"240"300"400"500"(0.65x0.40m)(0.86x0.54m)(1.29x0.81m)(1.72x1.08m)(2.15x1.35m)(2.59x1.62m)(3.23x2.02m)(4.31x2.69m)(5.17x3.23m)(6.46x4.04m)(8.62x5.39m)(10.77x6.73m)(0.65x0.40m)(0.86x0.54m)(1.29x0.81m)(1.72x1.08m)(2.15x1.35m)(2.59x1.62m)(3.23x2.02m)(4.31x2.69m)(5.17x3.23m)(6.46x4.04m)(8.62x5.39m)(10.77x6.73m)-0.71.01.41.72.1 2.6-----0.7 - 1.01.0 - 1.31.5 - 2.02.0 - 2.62.5 - 3.33.0 - 4.03.8 - 5.05.1 - 6.66.1 - 8.0 7.7 - 10.010.2 - 13.312.8 - 16.7--1.0 - 1.31.4 - 1.81.7 - 2.22.0 - 2.72.6 - 3.43.4 - 4.54.1 - 5.45.2 - 6.86.9 - 9.0 8.7 - 11.3-1.2 - 2.5 1.9 - 3.8 2.5 - 5.1 3.2 - 6.4 3.9 - 7.7 4.8- 9.6 6.4 - 12.8 7.7 - 15.4 9.6 - 19.2 12.8 - 25.7 16.0 - 32.1-- 3.7 - 6.0 5.0 - 8.1 6.3 - 10.1 7.6 - 12.2 9.5 - 15.3 12.7 - 20.4 15.3 - 24.5 19.1 - 30.7 25.5 - 40.9 31.9 - 51.2NP13ZL NP14ZLNP15ZL--5.9 - 9.1 7.9 - 12.1 9.9 - 15.212.0 - 18.315.0 - 22.920.1 - 30.624.1 - 36.830.2 - 46.040.4 - 61.450.5 - 76.9· The projector can be unplugged during its cool down period after it is turned off.Parts of the projector will become heated during operation.Use caution when picking up the projector immediately after it has been operating.· Use caution when putting the projector in the soft case immediately after the projector has been operating. The projector cabinet is hot.Cat.No. WLPJ-1411-0013NMicrosoft is a registered trademark or trademark of Microsoft Corporation in the United States and/or other countries.HDMI, the HDMI Logo and High-Definition Multimedia Interface are trademarks or registered trademarks of HDMI Licensing LLC.DisplayPort and DisplayPort Certified Logo are trademarks of the Video Electronics Standards Association, registered in the U.S. and other countries.CRESTRON and CRESTRON ROOMVIEW are trademarks or registered trademarks of Crestron Electronics, Inc.Trademark PJLink is a trademark applied for trademark right in the United States of America and other countries.VESA is a trademark of a nonprofit organization, Video Electronics Standard Association.All other trademarks are the property of their respective owners.The images in this brochure are samples./ap/162359368142499Lens centreLens centreUnit: mmThree primary colour liquid crystal shutter projection1,024,000 (1,280 dots × 800 lines)Manual (zoom range depends on lens)Manual Manual40" to 500" (throw distance depends on lens)10-bit colour processing (approx. 1.07 billion colors)Built-in 10 W monaural speaker33 dB / 39 dBAnalog: 15 kHz, 24 to 100 kHz (24 kHz or greater for RGB inputs), conforms to VESA standards / Digital: 15 kHz, 24 to 153 kHz, conforms to VESA standards Analog: 48 Hz, 50 to 85 Hz, 100, 120 Hz conforms to VESA standards / Digital: 24, 25, 30, 48 Hz, 50 to 85 Hz, 100, 120 Hz conforms to VESA standardsAnalog: 1,920 × 1,200 (with Advanced AccuBlend) / Digital: 4,096 × 2,160 (with Advanced AccuBlend)Mini D-Sub 15-pin × 1, 5BNC x 1Stereo mini jack × 2Stereo mini jack × 1 (selected from Computer / BNC / HDMI)TypeA 19 pin(HDMI connector) with HDCP(V1.4) x 2YesTypeA 19 pin(HDMI connector) with HDCP(V1.4) x 1YesDisplayPort 20 pin connecter x 1Yes BNC × 1Stereo mini jack x 1 ,shared with 5BNC, BNC (CV), BNC (Y/C)BNC × 2Stereo mini jack x 1 ,shared with 5BNC, BNC (CV), BNC (Y/C)D-Sub 9-pin × 1USB type A × 1RJ-45 × 1, (Supports 10BASE-T/100BASE-TX)IEEE 802.11b/g/n (Optional)Stereo mini jack × 15 V / 10 mA, synchronized signal output for 3D useOperating temperature: 5 to 40°C (*5), Operating humidity: 20 to 80 % (with no condensation)Storage temperature: -10 to 50°C, Storage humidity: 20 to 80 % (with no condensation)Operating altitude: 0 to 3,650 m (1,700 to 3,650 m: Set [FAN MODE] to [HIGH ALUTITUDE])100-240 V AC, 50/60 Hz377 W (100-130 V) / 362 W (200-240 V)0.11 W (100-130 V) / 0.16 W (200-240 V)4.7 W (100-130 V) / 4.9 W (200-240 V)499 × 142 × 359 mm (Net dimensions not including protruding parts)591 × 259 × 491 mm (Gross dimensions)8.4 kg (not including lens) 11.2 kg (Gross weight)2,304,000 (1,920 dots × 1,200 lines)350 W AC 6,200 lm 6,000:1483 W (100-130 V)460 W (200-240 V)5.5 A-2.2 A330 W AC 5,200 lm 5,000:1463 W (100-130 V) 440 W (200-240 V)5.1 A-2.2 A350 W AC 6,700 lm 6,000:1483 W (100-130 V)460 W (200-240 V)5.5 A-2.2 A330 W AC 5,700 lm 5,000:1463 W (100-130 V) 440 W (200-240 V)5.1 A-2.2 A350 W AC 7,200 lm 6,000:1483 W (100-130 V)460 W (200-240 V)5.5 A-2.2 A330 W AC 6,200 lm 5,000:1463 W (100-130 V) 440 W (200-240 V)5.1 A-2.2 A0.79" (with MLA) × 3 (aspect ratio: 4:3)786,432 (1,024 dots × 768 lines)MethodSpecifications of main partsLight output (*3) (*4)Contrast ratio (*3) (all white/all black)Screen size(throw distance) Colour reproducibility Audio outputQuietness (ECO mode ON/ECO mode OFF)Scan rateMax. display resolution (horizontal × vertical)Input/output connectorsUsage environmentPower supplyPower consumptionRated input current Dimensions (W x H x D)WeightSize Pixels(*1) Zoom Focus Lens shiftingECO OFFHorizontal VerticalVideo input Audio input Audio outputVideo input Audio input Video output Audio output Video input Audio input Video input Audio input Video input Audio inputECO mode off ECO mode on STANDBY (NORMAL) STANDBY(Network STANDBY)Liquid crystal panel Projection lensesLamp wattage (*2)Computer/ComponentHDMI Input Terminals HDMI Output Terminal DisplayPort BNC (CV) BNC (Y/C)PC control connector USB port Ethernet port Wireless LAN (USB)Remote connector 3D SYNC output terminal 0.76" (with MLA) × 3 (aspect ratio: 16:10)*1 : Effective pixels are more than 99.99 %. *2 : 264W when ECO mode is on.*3 : This is the light output value (lumens) when the [PRESET] mode is set to [HIGH-BRIGHT].The light output values will drop to 80 % when [ON] is selected for [ECO MODE]. If any other mode is selected as the [PRESET] mode, the light output value may drop slightly. *4 : Compliance with ISO21118-2005*5 : 35 to 40°C – “Forced ECO mode” (PA621U/PA521U will shift to the ECO-mode in stages starting from 33 °C.) • These specifications and the product’s design are subject to change without notice.Model name of the wireless LAN unit varies depending on the country where the unit is used (or to be used).NP02LM1 : NP02LM2 :NP02LM3 : United States, Canada, Mexico,Taiwan, Brazil, ColombiaEurope, United Arab Emirates,Saudi Arabia, Oman, South Africa, Turkey, Ukraine, Egypt,Israel, Australia,New Zealand,Japan, Thailand, China, Hong Kong, Singapore, South Korea,Sri Lanka, Pakistan, Vietnam,India, Indonesia, Philippines,Peru, Chile, Argentina, EcuadorRussiaTerminalsTilt-free and portrait mode supportThis 10 bit video processor represents an enormous leap in video processing, with true flagship performance in noise reduction,de-interlacing and scaling.Equipped with NEC 4,096 x 2,160 scaler NV1301 and the 3rd SweetVision TM circuitWide selection of inputs and outputsRemote control / monitoringECO modeLarge maintenance-free filterEnergy saving design with a standby power consumption of 0.16 W (200-240 V)This function seamlessly blends multipleprojected images to display a single high-resolution image.Built-in edge blendingMulti-display capabilities and Tiling technologies are integrated into the new PA series. This projector is also equipped with multiple digital input & HDMI output terminals that can connect multiple projectors in a digital daisy chain. These cutting-edge functions produce a beautiful high-resolution image, including a 4K/2K high-resolution display using 4 PA621U/521U projectors and various Picture in Picture/Picture by picture configurations.The projector uses large two-layer filters. Since they are highly effective at repelling dust, as long as the filter is replaced with new ones when changing the lamp, there is no need for regular cleaning.ECO mode that curbs electricity consumption and extends the lamp replacement time to a maximum of 4,000 hours.The projector is equipped with a wide range of input/output terminals and compatible with a variety of image sources, which lets you connect HDMI, DisplayPort, computer (analogue), 5-core BNC, video, and wired LAN (RJ-45)/wireless LAN* sources.Image Express Utility / Wireless Image Utility*Using Image Express Utility Lite contained on the supplied NEC Projector CD-ROM provides wired and wireless* data and audio transmission via peer-to-peer networking or over a network.Wireless Image Utility can send images directly from your iOS devices such as an Apple iPad, iPhone and iPod touch, which enables you to send the real-time images taken with its internal camera, web pages accessed or cloud files in combination with a file sharing application to the projector.Multiscreen functionThis feature allows the projectors to boost an image’s brightness up to 28,800 ANSI lm (PA721X), which is ideal for large screens and environments with strong ambient light. It also prevents the complete loss of an image, which can happen when using only one projector.Stacking capabilitiesGeometric correction*1 Value with XGA. *2 Brightness value when the lamp mode is set to "ECO OFF Mode" and the preset mode is "High-bright mode".*The lens shift mechanism does not work when using NP11FL.*As you maximise the tilt direction of the lens shift, the area surrounding t h e s c re e n m a y g e t d a r k e r a n d shadows may appear.Lens shifting range (with NP12ZL/NP13ZL/NP14ZL/NP15ZL)1V1H0.5 V(PA721X/PA621X/PA621U/521U)0.6 V(PA671W/PA571W)0.1V0.1H0.1HHeight of projected imageWidth of projected image0.3H*0.3H**The lenses are not included with this unit.HDBaseT models* are also available. *PA622U / PA522U / PA672W / PA572W / PA722X / PA622XLens specifications-0.8 : 140-1505,400 ANSI lm 4,600 ANSI lm 4,700 ANSI lm 4,000 ANSI lm 4,200 ANSI lm 3,500 ANSI lm 1.2 kg1.31.19-1.56 : 130-5005,600 ANSI lm 4,800 ANSI lm 5,000 ANSI lm 4,200 ANSI lm 4,600 ANSI lm 3,800 ANSI lm 1.2 kg1.30.81-1.06 : 152-5006,800 ANSI lm 5,900 ANSI lm 6,400 ANSI lm 5,400 ANSI lm 5,900 ANSI lm 4,900 ANSI lm 1.2 kg2.01.50-3.02 : 140-5007,200 ANSI lm 6,200 ANSI lm 6,700 ANSI lm 5,700 ANSI lm 6,200 ANSI lm 5,200 ANSI lm 0.84 kg1.62.97-4.79 : 160-5005,800 ANSI lm 5,000 ANSI lm 5,100 ANSI lm 4,300 ANSI lm 4,700 ANSI lm 4,000 ANSI lm 1.0 kg1.524.70-7.20 : 160-5005,600 ANSI lm 4,800 ANSI lm5,000 ANSI lm 4,200 ANSI lm 4,600 ANSI lm 3,800 ANSI lm1.0 kgManual (Focus only)Manual Fixed Short Throw Lens Zoom LensSix types of optional lenses available for flexible installationEnjoy greater installation flexibility with a complete line of optional bayonet style lenses (6) for quick and easy exchange. Lens throw distances range from 0.6 to 76.9 m.Lens shift function for easily adjusting the position of the projected imageThe projector is equipped with a lens shift that allows you to adjust the projected image horizontally or vertically. You can easily adjust the position of the projection just by turning the lens shift dials, without having to move the projector unit itself. Furthermore, the projector is also equipped with a centre lens design for easy alignment.4K Ultra HD support( 4,096 x 2,160 / 3,840 x 2,160 )12 bit gamma correction Advance colour correction(6-axis saturation and hue adjustment / skin tone) Video and film cadence detection (multi cadence)Seamless switching Active single 3D video supportRemote control ID Program timer with real time clock / OFF Timer Silent design of 33dB in ECO mode Built-in 10 W monaural speakerPIN security / Control panel lock / Security bar / Security slot Simple access pointNaViSet Administrator 2 AMX BEACONCRESTRON ROOMVIEW TM with emergency function PC Control Utility 4.0 for Windows PC Control Utility 5.0 for MACPJLink HTTP server Virtual remotePer-pixel motion adaptive de-interlacing Detail enhancementSuper resolution correction (3rd SweetVison TM )3D random, mosquito and block noise reductionPA571WPA621XPA521UPA671WPA721XPA621U6200ANSI lumens WUXGA 8.4kg6700ANSI lumens WXGA 8.4kg7200ANSI lumensXGA 8.4kg 5200ANSI lumens WUXGA 8.4kg5700ANSI lumens WXGA 8.4kg6200ANSI lumensXGA8.4kgLens shift dials* For the PA621U/PA521U, horizontal lens shift range is 0.15H at over 150"** These value are with the NP12ZL/NP13ZL/NP14ZL/NP15ZLBrightness using NP13ZL. Weight does not include lensThis feature corrects horizontal and vertical keystone distortion or adjusts the image when projecting onto an unique shaped screen.The projector can be rotated freely (360°) to point up or down depending on the installation requirements and can be installed on its side to create a portrait image.HDMI 1 INUSB PortEthernet(RJ-45)DisplayPort INCOMPUTER INAUDIO OUT (Stereo mini)PC CONTROL (D-Sub 9 pin)BNC AUDIO IN (Stereo mini)HDMI OUTHDMI 2 INBNC INCOMPUTER AUDIO IN (Stereo mini)3D SYNC (Mini DIN 4 pin)1920192019201200Daisy chain Daisy chain*Requires optional wireless LAN moduleREMOTE (Stereo mini)。
百兆以太网ICIP101G规格书

百兆以太⽹ICIP101G规格书Single Port 10/100 MII/RMII/TP/FiberFast Ethernet Transceiver(85nm/Extreme Low PW, PWMT ? and EMIMT ?)Features General Descriptionz 10/100Mbps IEEE 802.3/802.3u compliant Fast Ethernet transceiverz Supports 100Base-TX/FX Media Interface z Supports MII/ RMII Interfacez Supports Auto MDI/MDIX function z Power Management Tool- APS, auto power saving while Link-off - 802.3az, protocol based power saving - WOL+, light traffic power saving - PWD, force-off power saving- Supports MII with LPI for RX and TX - Supports RMII with LPI for RXz Supports Base Line Wander compensation z Supports Interrupt functionz Built in synchronization FIFO to support jumbo frame size up to 12KB in MII mode (10KB in RMII 100Mbps mode)z Supports MDC and MDIO to communicate with the MACz EMI Management Tool - F/W based control- 4 levels for mapping the difference layoutlength on the PCBz Single 3.3V power supply z Built-in Vcore regulatorz DSP-based PHY Transceiver technology z System Debug Assistant Tool - 16 bit RX counter- 9 bit RXError/CRC counter - Isolate MII/RMII - RX to TX Loopback - Loopback MII/RMIIz Using either 25MHz crystal/oscillator or 50MHz oscillator REF_CLK as clock sourcez Built-in 49.9ohm resistors for simplifying BOMz Flexible LED display z Process: 85nmzPackage and operation temperatureIP101G: dice, 0~70℃IP101GA: 48LQFP , 0~70℃ IP101GR: 32QFN, 0~70℃ IP101GRI: 32QFN, -40~85℃IP101G is an IEEE 802.3/802.3u compliant single-port Fast Ethernet Transceiver for both 100Mbps and 10Mbps operations. It supports Auto MDI/MDIX function to simplify the network installation and reduce the system maintenance cost. To improve the system performance, IP101G provides a hardware interrupt pin to indicate the link, speed and duplex status change.IP101G provides Media Independent Interface (MII) or Reduced Media Independent Interface (RMII) to connect with different types of 10/100Mbps Media Access Controller (MAC). IP101G is designed to use category 5 unshielded twisted-pair cable or Fiber-Optic cables connecting to other LAN devices. A PECL interface is supported to connect with an external 100Base-FXfiber optical transceiver. Except good performance, reliability, rich power saving method and extreme low operating current, IP101G provides a serial tool for system designers to complete their projects easily. They are System Debug Assistant Tool and EMI Management Tool.IP101G is fabricated with advanced CMOS (85nm) technology and design is based onIC Plus’s 5th Ethernet-PHY architecture, this feature makes IP101G consumes very low power. Such as in the full load operation (100Mbps_FDX), it only takes below 0.15W. IP101GA / IP101GR&IP101GRI are available in 48LQFP/32QFN, lead-free package.* EMIMT: Patent under apply.Application■ NAS■ Network Printers and Servers ■ IP Set-Top Box ■IP/Smart TV■ Game console■ IP and Video Phone ■ PoE■Telecom Fiber deviceTable Of ContentsTable Of Contents (2)List of Figures (4)List of Tables (5)Revision History (6)Features comparison between IP101G and IP101A/IP101AH (7)Transmit and Receive Data Path Block Diagram (8)1Pin diagram (9)2Dice pad information (11)3Pin description (12)3.1IP101GA pin description (12)3.2IP101GR/GRI pin description (16)4Register Descriptions (19)4.1Register Page mode Control Register (20)4.2MII Registers (20)4.3MMD Control Register (30)4.4MMD Data Register (31)4.5RX Counter Register (34)4.6LED Pin Control Register (35)4.7WOL+ Control Register (36)4.8UTP PHY Specific Control Register (39)4.9Digital IO Pin Control Register (39)5Function Description (41)5.1Major Functional Block Description (41)5.1.1Transmission Description (41)5.1.2MII and Management Control Interface (42)5.1.3RMII Interface (43)5.1.4Flexible Clock Source (45)5.1.5Auto-Negotiation and Related Information (45) 5.1.6Auto-MDIX function (46)5.2PHY Address Configuration (46)5.3Power Management Tool (47)5.3.1Auto Power Saving Mode (47)5.3.2IEEE802.3az EEE (Energy Efficient Ethernet) (48) 5.3.3Force power down (48)5.3.4WOL+ operation mode (48)5.4LED Mode Configuration (52)5.5LED Blink Timing (52)5.6Repeater Mode (52)5.7Interrupt (52)5.8Miscellaneous (52)5.9Serial Management Interface (53)5.10Fiber Mode Setting (54)5.11Jumbo Frame (54)6Layout Guideline (55)6.1General Layout Guideline (55)6.2Twisted Pair recommendation (55)7Electrical Characteristics (56)7.1Absolute Maximum Rating (56)7.2DC Characteristics (56)7.3Crystal Specifications (57)7.4AC Timing (58)7.4.1Reset, Pin Latched-in, Clock and Power Source (58) 7.4.2MII Timing (59)7.4.3RMII Timing (60)7.4.4SMI Timing (61)7.5Thermal Data (61)8Order Information (62)9Physical Dimensions (63)9.148-PIN LQFP (63)9.232-PIN QFN (64)List of FiguresFigure 1 Flow chart of IP101G (8)Figure 2 IP101GA 48 Pin Diagram (9)Figure 3 IP101GR/GRI 32 Pin Diagram (10)Figure 4 IP101G dice pad information (11)Figure 5 LPI transition (43)Figure 6 IP101G/GA/GR/GRI MII Mode with LPI transition Block Diagram (43) Figure 7 IP101G/GA/GR/GRI MII Mode without LPI transition Block Diagram (43) Figure 8 IP101G RMII Mode with internal clock Block Diagram (44)Figure 9 IP101G RMII Mode with external clock Block Diagram (44)Figure 10 IP101G RMII Clock Application Circuit (45)Figure 11 IP101G link speed and EEE ability programming guide (46)Figure 12 PHY Address Configuration (47)Figure 13 Magic Packet Format (49)Figure 14 Sleep or wake up automatically programming guide (50)Figure 15 MAC control sleep or wake up programming guide (51)Figure 16 MDC/MDIO Format (53)Figure 17 IP101G Fiber Mode Setting (54)Figure 18 Reset, Pin Latched-In, Clock and Power Source Timing Requirements (58) Figure 19 MII Transmit Timing Requirements (59)Figure 20 MII Receive Timing Specifications (59)Figure 21 RMII Transmit Timing Requirements (60)Figure 22 RMII Receive Timing Specifications (60)Figure 23 SMI Timing Requirements (61)Figure 24 48-PIN LQFP Dimension (63)Figure 25 32-PIN QFN Dimension (64)List of TablesTable 1 Features comparison between IP101G and IP101A/IP101AH (7)Table 2 Register Map (19)Table 3 Flexible Clock Source Setting (45)Table 4 PHY Address Configuration (47)Table 5 WOL+ operation mode (49)Table 6 LED Mode 1 Function (52)Table 7 LED Mode 2 Function (52)Table 8 LED Blink Timing (52)Table 9 SMI Format (53)Table 10 DC Characteristics (56)Table 11 I/O Electrical Characteristics (56)Table 12 Pin Latched-in Configuration Resistor (57)Table 13 Crystal Specifications (57)Table 14 Reset, Pin Latched-in, Clock and Power Source Timing Requirements (58) Table 15 MII Transmit Timing Requirements (59)Table 16 MII Receive Timing Specifications (59)Table 17 RMII Transmit Timing Requirements (60)Table 18 RMII Receive Timing Specifications (60)Table 19 SMI Timing Requirements (61)Table 20 Thermal Data (61)Table 21 Part Number and Package (62)Revision HistoryRevision # Change DescriptionIP101G-DS-R01 Initial release.IP101G-DS-R01-20120622 Add 30 seconds into the definition for register WOL_PLUS_TIMER_SEL. IP101G-DS-R01-20120629 Add the symbol SC (Self Clear) for PHY MII register 0.15 Reset and 0.9Restart Auto-Negotiation.IP101G-DS-R01-20120709 1) Add LED mode 2 in the pin description and function description.2) Correct the table of LED Blink Timing.3) Add more description of PHY Address Configuration and IEEE 802.3az.4) Add ESD reliability of Absolute Maximum Rating.5) Correct the typo of function description for Auto Power Saving Mode.6) Change register P16R16[10] description from HEART_BEAT_EN toReserved.IP101G-DS-R01-20120719 Correct the table of Register Map for page selection.IP101G-DS-R01-20120726 1) Add more description of Register RX2TX_LPBK P1R23[13] for Rx to Txloopback test.2) Add more description on Fiber Mode Setting and latched-in pin signalson AC Timing.3) Add IP101AH into the table of features comparison.IP101G-DS-R01-20120808 1) Correct the I/O type of IP101GA pin description to O(Ouput) for pin24RXER.2) Change the pin name from DVDD33_IO to VDDIO.IP101G-DS-R01-20120821 1) Change the default value of register P16R27 from 0x0022 to 0x0012.2) Remove I/O Slew Rate Control Register.3) Change the register location RMII_WITH_ER from P16R29[0] toP16R29[7].IP101G-DS-R01-20120927 1) Add more description of low power idle (LPI) state in MII and RMIImodes.2) Correct the typo of Physical Dimensions.IP101G-DS-R01-20121101 Change the LED blink timing from “On 80ms -> Off (20~40)ms” to “On 26ms-> Off 78ms”.IP101G-DS-R01-20121113 Add more function description to support Jumbo Frame.IP101G-DS-R01-20121127 Change the LED mode function as same as IP101A.IP101G-DS-R01-20121224 Add the notice that does not let these PHY address pins floating for thelatched-in settings after the power is ready.IP101G-DS-R01-20130206 Change the AC timing Tclk_MII_rdy in Table 14 from 10ms Min. to 10ms Max. IP101G-DS-R01-20130312 1) Add more Min. and Max value on the AC Timing table.2) Add thermal data on the Table 20.IP101G-DS-R01-20130507 Add LED Pin Driving Control RegisterIP101G-DS-R01-20130621 Add GRI 2.5V I/O power supplyDisclaimerThis document probably contains the inaccurate data or typographic error. In order to keep this document correct, IC Plus reserves the right to change or improve the content of this document.Features comparison between IP101G and IP101A/IP101AHTable 1 Features comparison between IP101G and IP101A/IP101AHProduct Name IP101GR IP101G IP101GA IP101A IP101AH Package Type 32pin QFN Dice 48pin LQFP48pin LQFP REGOUT(1) Output Voltage and location 1.0V, pin28 1.0V, pad5and pad111.0V, pin82.5V, pin32REGIN Input Voltage and location NA(2) 1.0V,pad23and pad26NA 2.5V,pin8RMII mode setting Pin4 Pad18 Pin1 Pin1 and pin44Fiber mode setting: Fiber FXSD signal: Pin19Pin1Pad39Pad13Pin22Pin43NA Pin24 and pin48Pin37Number of LED 2 4 4 5LED mode 1 and 2 1 and 2LED Blink Timing On 26ms -> Off 78ms On 26ms -> Off 78msPHY address number(3) Single: 0 ~ 1Multi: 2 ~ 31Single: 0 ~ 7Multi: 8 ~ 31Single: 0 ~ 31Center-tap of transformer Do not connect to any power 2.5V input powerBuilt-in 49.9ohm resistors Yes NoPowerconsumption ~150mW ~480mW Process 85nm0.25µmIEEE 802.3az Yes No10Base TX amplitude ~1.75V (10Base-Te) ~2.5V(10Base-T) WOL+ (Wake On LAN Plus) Yes NoAnalog OFF Yes No16 bit RX counter Yes No9 bit RXER/CRC counter Yes NoRX to TX Loopback Yes NoLoopback MII/RMII Yes YesSNI mode No YesNote 1: Regulator voltage output is for internal use only. Do not supply to any other device.Note 2: Not available for this function. The 1.0V is supplied by the regulator that built-in the chip. Note 3: Do not let these PHY address pins floating for the latched-in settings after the power is ready.Transmit and Receive Data Path Block DiagramFigure 1 Flow chart of IP101G1Pin diagramRXER CRS/LEDMODRXDV/CRS_DV/FX_HEN X1X2RXD2RXD3RXCLK/50M_CLKO DGNDRXD0NCRESET_N IP101GA (LQFP-48)242322212019181716NC NC TXER/FXSDNC Those pins in "blue "are different from IP101A. NC Note:RXD1INTRNC DGNDNC LED3/PHY_AD3VDDIOFigure 2 IP101GA 48 Pin DiagramIP101GR/GRI (VQFN-32)(GND on bottom of chip)RXD3TXCLK/50M_CLKI RXCLK/50M_CLKO LED0/PHY_AD0LED3/PHY_AD3161514131211109 RESET_NISET REGOUT MDI_TN MDI_TP MDI_RP MDI_RN RXD2AVDD33 Figure 3 IP101GR/GRI 32 Pin Diagram2Dice pad informationIC LogoPad 1Pad 44Pad 11Pad 45Pad 24Pad 31Pad 12Pad 22Pad 23REGINPHYAD_LED028PHYAD_LED129VSS30PHYAD_LED231PHYAD_LED332VDDIO 33RX_CLK REGOUT 34VSSIO RESET_N 35RXD[3]TXER_FXSD 36RXD[2]VSSIO 37RXD[1]15X138RXD[0]16X239RXDV_FIBMOD 17INTR40CRS18COL_RMII 41RXER_INTR 19TX_EN 4220TXD[3]21TXD[2]22TXD[1]23REGINFigure 4 IP101G dice pad information3 Pin descriptionType DescriptionType DescriptionLI Latched Input in power up or reset PD Internal Pull-Down 104K ? I/O Bi-directional input and outputPUInternal Pull-Up 222K ?I Input Hi-Z High impedanceO Output P Power OD Open Drain3.1 IP101GA pin descriptionIP101GAPin no. LabelType Reset StateDescriptionSerial Management Interface Pins 25 MDC I Hi-Z Management Data Interface Clock: This pin provides a clock reference to MDIO. The clock rate can be up to 2.5MHz.26 MDIO I/O (PU) I (PU)Management Data interface Input/Output:Thefunction of this pin is to transfer management informationbetween PHY and MAC.MII/RMII Pins2 TXEN I (PD) I (PD)Transmit Enable or Signal Detect.43 TXER/FXSD I (PD) I (PD)Transmit Error or FXSD:This is a dual-function pin which is determined by themedia type selection. If RXDV/CRS_DV/FX_HEN islatched as “0 (default)” upon reset, the TP interface isselected and its function as TXER. If the fiber interface is selected, this pin’s function as FXSD.FXSD:0: Fiber link down; 1: Fiber link upTransmit Enable:TXEN TXER Description 1 1 Transmission errorpropagation.0 1 Combine TXD[3:0] that equalto 0001 for request PHY to enter LPI mode.1 0 0 0Normal operationThis pin TXER must be either floating or connecting to GND in RMII mode.7 TXCLK/50M_CLKI I/O Hi-Z Transmit Clock output or 50M clock input:In MII mode, this pin provides a continuous 25MHz clock at 100Base-TX and 2.5MHz at 10Base-T . In RMII mode, a 50Mhz clock should input to this pin for the timing reference of the internal circuit. 3,4,5,6 TXD[3:0] I Hi-Z Transmit Data Input:IP101GAPin no.LabelType ResetDescriptionStateIn MII mode, TXD[3:0] is synchronous to TXCLK.In RMII mode, TXD[1:0] is synchronous to 50M_CLKI.22 RXDV/CRS_DV/ FX_HEN O/LI (PD) I (PD)Receive Data Valid or Media Type Selection:FX_HENThe input state is latched upon reset to determine whether TP or fiber interface is selected. If it is at logic “0” (default) state upon reset, the TP interface is selected; otherwise the fiber interface is selected. RXDV/CRS_DVIn MII mode, this pin indicates the Receive Data Valid function.In RMII mode, this pin indicates the Carrier Sense and Receive Data Valid function.16 RXCLK/ 50M_CLKO O Hi-Z Receive Clock:In MII mode, this pin provides 25MHz for 100BT or2.5MHz for 10BT.In RMII mode, this pin output a 50 MHz clock for the timing reference of MAC side.18,19, 20,21 RXD[3:0] O Hi-Z Receive Data: In MII mode, RXD[3:0] is synchronous to RXCLK.In RMII mode, RXD[1:0] is synchronous to 50M_CLKI.24 RXER O Hi-Z Receive error:RXDV RXER Description1 1 Decoding error of thereceived signal0 1 Combine RXD[3:0] equal to0001 indicates PHY isreceiving LPI.1 0 0 0Normal operationThis pin RXER is an optional input for MAC/CPU device.1 COL/RMII O/LI (PD) I (PD)Collision Detected:During the normal operation, thispin outputs a high status signal it means collision isdetected.RMII Mode Selection: During the power on reset, thispin status is latched to determine what kind MAC interface will be used. Logic “1” is for RMII mode and logic “0” is for MII mode.23 CRS/LEDMOD O/LI (PD) I (PD)Carrier Sense: When signal output from this pin is highindicates the transmission or reception is in process andat low status means the line is in idle state.LEDMOD: During power on reset, this pin status is latched to determine which either LED mode 1 or 2is selected, please refer to the LED pins description.Cable Transmission Interface 34,33 MDI_TP MDI_TN I/O I/O Hi-Z Transmit Output Pair: Differential pair shared by100Base-TX and 10Base-T modes. When configured as100Base-TX, output is an MLT-3 encoded waveform. When configured as 10Base-T , the output is ManchesterIP101GAPin no. Label Type Reset DescriptionStatecode.31,30 MDI_RPMDI_RN I/OI/OHi-Z Receive Input Pair: Differential pair shared by 100Base-TX and 10Base-T modes.Clock and Miscellaneous Pins47 X2 O O 25MHz Crystal Output: Connects to crystal to providethe 25MHz output. It must be left open when X1 is drivenwith an external 25MHz oscillator.46 X1 I I 25MHz Crystal Input: Connects to crystal to provide the25MHz crystal input. If a 25MHz oscillator is used,connect X1 to the oscillator’s output. If a 50MHz clock isapplied to pin7 TXCLK/50M_CLKI, X1 must beconnected to GND or AGND33.42 RESET_N I I(PU)RESET_N: Enable a low status signal will reset the chip. For a complete reset function. 25MHz clock (x1) must be active for a minimum of 10 clock cycles before the rising edge of RESET_N. Chip will be able to operate after 2.5ms delay of the rising edge of RESET_N. The 2.5ms extension is to ensure the stability of system power.28 ISET I I Bandgap Circuit Resistor: This pin should beconnected to GND via a 6.19K? (1%) resistor to definethe standard current of the internal circuit.48 INTR OD Hi-Z Interrupt: Programmable Interrupt Output, this is anopen drain output, and an external pulled-up resistor isneeded for normal mode operation. Another operationmode is Rx to Tx loopback debugging test (reflect onRegister P1R23[13] RX2TX_LPBK) when connect INTRpin to GND.9 LED0/PHY_AD0 O/LI Hi-Z LED 0 and PHY Address [0]LED 0LED mode1 2LED0Link Link/ACT(blinking)10 LED1/PHY_AD1 O/LI Hi-Z LED 1 and PHY Address [1]LED1LED mode1 2LED1Duplex Duplex /COL (blinking)12 LED2/PHY_AD2 O/LI Hi-Z LED 2 and PHY Address [2]LED2LED mode1 2LED210M Link /ACT10M Link13 LED3/PHY_AD3 O/LI(PD) Hi-Z LED 3 and PHY Address [3]LED3LED mode1 2LED3100M Link /ACT 100M Link27 TEST_ON I I Test Enable: Set this pin to high to enable Test mode.IP101GAPin no. Label Type Reset DescriptionState(PD) (PD)For normal operation, this pin doesn’t need to be connected.Power and Ground32 NC -- -- It’s a NC pin.8 REGOUT P P Regulator Power Output: This is a regulator power output. A 10uF and 0.1uF should be connected to this pinto filter the power noise.14 VDDIO P P Digital Power input:Either 3.3V or 2.5V for I/O power supply.36 AVDD33 P P 3.3V Analog power input: This is a 3.3V power supply for analog circuitry, and it should be decoupled carefully.35 AGND33 P P Ground.29 AGND1V P P Ground45,11,17 DGND P P Ground.3.2 IP101GR/GRI pin descriptionIP101GR/GRIPin no. Label Type ResetStateDescriptionSerial Management Interface Pins22 MDC I Hi-Z Management Data Interface Clock: This pin provides a clock reference to MDIO. The clock rate can be up to2.5MHz.23 MDIO I/O(PU)I(PU)Management Data interface Input/Output:Thefunction of this pin is to transfer management informationbetween PHY and MAC.MII/RMII Pins5 TXEN I(PD)I(PD)Transmit Enable or Signal Detect.1 TXER/FXSD I(PD)I(PD)Transmit Error or FXSD:This is a dual-function pin which is determined by the media type selection. If RXDV/CRS_DV/FX_HEN is latched as “0 (default)” upon reset, the TP interface is selected and its function as TXER. If the fiber interface is selected, this pin’s function as FXSD.FXSD:0: Fiber link down; 1: Fiber link upTransmit Enable:TXEN TXER Description1 1 Transmissionerrorpropagation.0 1 CombineTXD[3:0]thatequalto 0001 for request PHY toenter LPI mode.1 00 0Normal operationThis pin TXER must be either floating or connecting toGND in RMII mode.10 TXCLK/50M_CLKI I/O Hi-Z Transmit Clock output or 50M clock input: In MII mode,this pin provides a continuous 25MHz clockat 100Base-TX and 2.5MHz at 10Base-T.In RMII mode, a 50Mhz clock should input to this pin forthe timing reference of the internal circuit.6,7,8,9 TXD[3:0] I Hi-Z Transmit Data Input:In MII mode, TXD[3:0] is synchronous to TXCLK.In RMII mode, TXD[1:0] is synchronous to 50M_CLKI.19 RXDV/CRS_DV/FX_HEN O/LI(PD)I(PD)Receive Data Valid or Media Type Selection:FX_HENThe input state is latched upon reset to determinewhether TP or fiber interface is selected. If it is at logic“0” (default) state upon reset, the TP interface isselected; otherwise the fiber interface is selected.RXDV/CRS_DVIn MII mode, this pin indicates the Receive Data ValidIP101GR/GRIPin no.LabelType ResetDescriptionStatefunction.In RMII mode, this pin indicates the Carrier Sense and Receive Data Valid function.14 RXCLK/ 50M_CLKO O Hi-Z Receive Clock:In MII mode, this pin provides 25MHz for 100BT or2.5MHz for 10BT.In RMII mode, this pin output a 50 MHz clock for the timing reference of MAC side.15,16, 17,18 RXD[3:0] O Hi-Z Receive Data: In MII mode, RXD[3:0] is synchronous to RXCLK. In RMII mode, RXD[1:0] is synchronous to 50M_CLKI.21 RXER/INTR_32 O/ODHi-Z The multiplex function of this pin is set by the registerSEL_INTR32, page 16,29[2]. The default function is RXER.Receive error:RXDV RXER Description 1 1 Decoding error of thereceived signal0 1 Combine RXD[3:0] equal to0001 indicates PHY is receiving LPI.1 0 0 0Normal operationThis pin RXER is an optional input for MAC/CPU device.Interrupt: Programmable Interrupt Output, this is an open drain output, and an external pulled-up resistor is needed.4 COL/RMII O/LI (PD) I (PD)Collision Detected:During the normal operation, thispin outputs a high status signal it means collision isdetected.RMII Mode Selection: During the power on reset, thispin status is latched to determine what kind MAC interface will be used. Logic “1” is for RMII mode and logic “0” is for MII mode.20 CRS/LEDMOD O/LI (PD) I (PD)Carrier Sense:When signal output from this pin is highindicates the transmission or reception is in process andat low status means the line is in idle state.LEDMOD: During power on reset, this pin status is latched to determine which either LED mode 1 or 2is selected, please refer to the LED pins description.Cable Transmission Interface 30,29 MDI_TP MDI_TN I/O I/O Hi-Z Transmit Output Pair: Differential pair shared by100Base-TX and 10Base-T modes. When configured as100Base-TX, output is an MLT-3 encoded waveform. When configured as 10Base-T , the output is Manchester code.27,26 MDI_RP MDI_RN I/O I/O Hi-Z Receive Input Pair: Differential pair shared by100Base-TX and 10Base-T modes.Clock and Miscellaneous PinsIP101GR/GRIPin no. Label Type Reset DescriptionState3 X2 O O 25MHz Crystal Output: Connects to crystal to providethe 25MHz output. It must be left open when X1 is drivenwith an external 25MHz oscillator.2 X1 I I 25MHz Crystal Input: Connects to crystal to provide the25MHz crystal input. If a 25MHz oscillator is used,connect X1 to the oscillator’s output. If a 50MHz clock isapplied to pin10 TXCLK/50M_CLKI, X1 must beconnected to GND.32 RESET_N I I(PU)RESET_N: Enable a low status signal will reset the chip. For a complete reset function. 25MHz clock (x1) must be active for a minimum of 10 clock cycles before the rising edge of RESET_N. Chip will be able to operate after 2.5ms delay of the rising edge of RESET_N. The 2.5ms extension is to ensure the stability of system power.25 ISET I I Bandgap Circuit Resistor: This pin should beconnected to GND via a 6.19K? (1%) resistor to definethe standard current of the internal circuit.11 LED0/PHY_AD0 O/LI Hi-Z LED 0 and PHY Address [0]LED 0LED mode1 2LED0Link Link/ACT(blinking)12 LED3/PHY_AD3 O/LI(PD) Hi-Z LED 3 and PHY Address [3]LED3LED mode1 2LED3100M Link /ACT 100M Link24 TEST_ON I(PD)I(PD)Test Enable: Set this pin to high to enable Test mode.For normal operation, this pin doesn’t need to beconnected.Power and Ground28 REGOUT P P Regulator Power Output: This is a regulator power output. A 10uF and 0.1uF should be connected to this pinto filter the power noise.13 VDDIO P P Digital Power input:IP101GR/GRI: Either 3.3V or 2.5V for I/O power supply.31 AVDD33 P P 3.3V Analog power input: This is a 3.3V power supply for analog circuitry, and it should be decoupled carefully.Bottom PAD GND PPGround.4 Register DescriptionsTable 2 Register MapPage Register Description Default NoteRegister 0x0010X 20 PageControlRegister 0x3100-- 0 ControlRegister 0x7849-- 1 Status-- 2 PHY Identifier 1 Register 0x0243-- 3 PHY Identifier 2 Register 0x0C54Advertisement Register 0x01E1-- 4 Auto-Negotiation-- 5 Auto-Negotiation Link Partner Ability Register 0x0000-- 6 Auto-Negotiation Expansion Register 0x0004-- 7 Auto-Negotiation Next Page Transmit Register 0x2001-- 8 Auto-Negotiation Link Partner Next Page Register 0x0000-- 13 MMD Access Control Register 0x0000-- 14 MMD Access Address Data Register 0x000016 16 PHY Specific Control Register 0x000216 17 PHY Interrupt Ctrl/Status Register 0x0F0016 18 PHY Status Monitoring Register 0x020816 26 Digital IO Pin Driving Control Register 0x124916 27 Digital IO Pin Driving Control Register 0x001216 28 LED Pin Driving Control Register 0x000116 29 Digital I/O Specific Control Register 0x008216 30 PHY MDI/MDIX Control and Specific Status Register 0x0000 -- MMD 3.0 PCS Control 1 Register 0x0000-- MMD 3.1 PCS Status 1 Register 0x0000-- MMD 3.20 EEE Capability Register 0x0002-- MMD 3.22 EEE Wake Error Count Register 0x0000-- MMD 7.60 EEE Advertisement Register 0x0002-- MMD 7.61 EEE Link Partner Ability Register 0x00001 17 PHY Specific Control Register 0x00001 18 RX CRC Error Counter Register 0x00001 22 Linear Regulator Output Control Register 0x20201 23 UTP PHY Specific Control Register 0x80002 18 RX Packet Counter Register 0x00003 16 LED Mode Control Register 0x00004 16 WOL+ Control Register 0x5F404 22 Digital IO Pin Driving Control Register 0x40005 16 PHY WOL+ MAC Address Register 0x00008 17 RX Counter Control Register 0x7000。
powerWave455M_CN
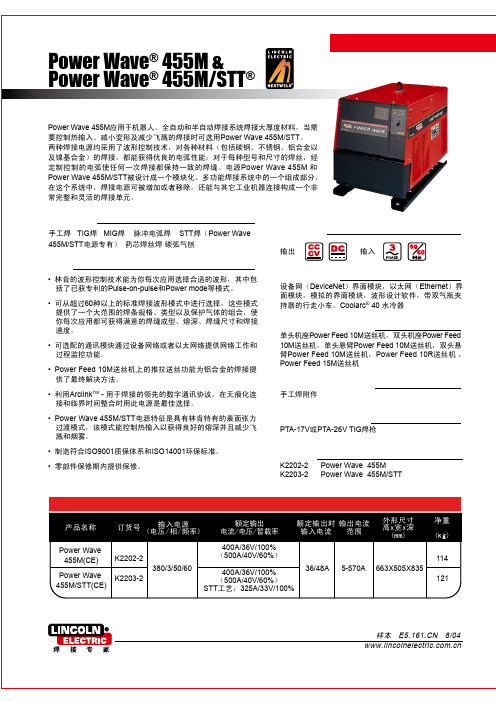
• 制造符合ISO9001质保体系和ISO14001环保标准。
• 零部件保修期内提供保修。
使用说明
输出
输入
推荐Байду номын сангаас配件
设备网(DeviceNet)界面模块,以太网(Ethernet)界 面模块,模拟的界面模块,波形设计软件,带双气瓶夹 持器的行走小车,Coolarc® 40 水冷器
送丝机选配件推荐
单头机座Power Feed 10M送丝机,双头机座Power Feed 10M送丝机,单头悬臂Power Feed 10M送丝机,双头悬 臂Power Feed 10M送丝机,Power Feed 10R送丝机 , Power Feed 15M送丝机
• 可选配的通讯模块通过设备网络或者以太网络提供网络工作和 过程监控功能。
• Power Feed 10M送丝机上的推拉送丝功能为铝合金的焊接提 供了最终解决方法。
• 利用ArclinkTM - 用于焊接的领先的数字通讯协议,在无痕化连 接和临界时间整合时用此电源是最佳选择。
• Power Wave 455M/STT电源特征是具有林肯特有的表面张力 过渡模式,该模式能控制热输入以获得良好的熔深并且减少飞 溅和烟雾。
[4]
Power Wave 455M & Power Wave 455M/STT
简单的模块化扩充
以太网(Ethernet)模块外观 留给机器人送丝驱动模块的位置
Power Wave 455M和Power Wave 455M/STT电源前面板
Keysight Technologies Advanced Power System (APS)
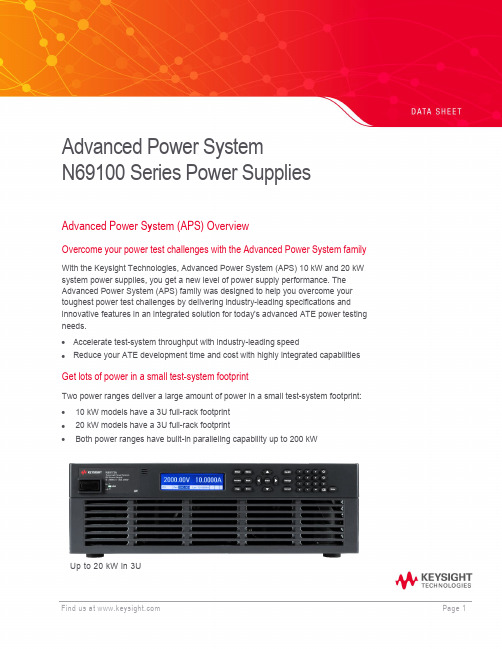
Advanced Power SystemN69100 Series Power SuppliesAdvanced Power System (APS) OverviewOvercome your power test challenges with the Advanced Power System family With the Keysight Technologies, Advanced Power System (APS) 10 kW and 20 kW system power supplies, you get a new level of power supply performance. The Advanced Power System (APS) family was designed to help you overcome your toughest power test challenges by delivering industry-leading specifications and innovative features in an integrated solution for today's advanced ATE power testing needs.•Accelerate test-system throughput with industry-leading speed•Reduce your ATE development time and cost with highly integrated capabilities Get lots of power in a small test-system footprintTwo power ranges deliver a large amount of power in a small test-system footprint: • 10 kW models have a 3U full-rack footprint• 20 kW models have a 3U full-rack footprint• Both power ranges have built-in paralleling capability up to 200 kWUp to 20 kW in 3UChoose the APS model with the voltage and current you needThe N69100 Series DC power supply family offers three voltage and current combinations at the 10 kW power range and two voltage and current combinations at the 20 kW power range.N69143A 20 V, 800 A N69172A 1000V, 60 AN69145A 80 V, 250 A N69173A 2000 V, 30 AN69146A 160 V, 125 AAutoranging output – does the job of multiple power suppliesThe N69100 power supplies’ autoranging output characteristic makes it much more flexible than rectangular, or traditional, output characteristic power supplies because they expand the power curve, giving the user more voltage and current combinations in one power supply. Power supplies with rectangular output characteristics provide full power at only one voltage and current combination. The N691900 is like having many rectangular power supplies in one.Figure 1. Autoranging output characteristic of the 10kW N69145A APSFigure 2. Rectangular output characteristic of a traditional 10kW supplyEmulate high-power batteryWith their battery emulation feature, the N69100 Series allows you to test your devices under the same power conditions that exist in actual use. Emulating the battery is key when characterizing battery operating life and detecting early product failures. Through programable resistance up to 277 Ω (model dependent), the N69100 DC sources simulate the effects of internal resistance of the battery, enabling them to emulate the operation of batteries in different charge states.Accelerate test throughput with industry-leading specificationsShaving seconds or even milliseconds off a test time can lead to significant savings for high-volume manufacturers, making throughput gains a never-ending quest for test system designers. The N69100 is a valuable tool for increasing throughput. It provides fast output speed, sub-millisecond command-processing time (≤ 1 ms), and output list that can help you achieve significant throughput gains in your testing.Make accurate advanced measurements with the APSThe N69100 provides simultaneous voltage and current measurement capabilities that deliver high accuracy and resolution. Make measurements using average mode, where the N69100 delivers accurate voltage and current measurements.In addition, the N69100 Advanced Power System offer built-in power, peak power, amp-hour, and watt-hour calculations. These measurements help simplify your power efficiency and storage calculations.Avoid damage to your DUTWhen you are testing costly DUTs, integrating power protection measures into the test system is critical. Using instrumentation with built-in or integrated protection features provides a huge benefit when DUT protection is required. With protection measures implemented in hardware rather than test system software, error conditions can be detected and handled much faster, reducing the likelihood of the DUT sustaining major damage. The N69100 provides built-in over-voltage, over-current, and over-temperature protection.Generate voltage and current transientsDUTs that are operated in rugged environments, such as automotive electronics and avionics, can often experience transient behavior from the power source, such as voltage dropouts or surges. To ensure your DUT can stand up to these real-world transients, you must simulate worst-case power transient conditions in the test process. The N69100 provide three different functionalities for simulating either voltage or current transients for testing:Step: One-time event that steps the output voltage or current up or down in response to a triggered event.Constant dwell arbitrary waveforms: An arbitrary waveform generator (ARB) allows you to generate complex user-defined voltage or current waveforms of up to 65,535 data points. One dwell setting applies for the entire ARB, from 10.24 μs to 0.30 seconds.List: A list can consist of up to 512 steps. Each step in the list can have a unique dwell time associated with it, which specifies the time in seconds that the list will remain at that step before moving on to the next step. Lists can also be trigger-paced, in which case the list advances one step for each trigger received. List is not supported in primary/secondary mode (except on the N69172A/73A APS).Properly powering on and off your DUTIf you work with DUTs that have multiple power supply inputs, you often need to properly sequence on or off each power supply at strictly repeatable times to prevent current surges and latch-up conditions. In addition to sequencing on or off each supply, you may need to set the ramp rate of each supply at turn-on or turn-off to a particular rate. These requirements add significant complexity to an ATE test system, both in hardware and software. The N69100 provides built-in sequencing capability across N69100 supplies or with Keysight’s popular N6700 modular system power supplies or N6900/N7900 Advanced Power System. Also, the N69100 provide adjustable slew rate control at turn-on or turn-off. These built-in capabilities provide a clean low-complexity way to properly power-on or off your DUT during test.Add power flexibility to your test system by paralleling multiple suppliesParalleling multiple power supplies together is a great way to add power flexibility to your test system. The downside of paralleling power supplies together is typically you cannot get all the supplies to operate in the desired constant voltage (CV) or constant current (CC)mode. For instance, when trying to operate in CV mode with two parallel supplies, one will typically source the bulk of the current and operate in CC mode and the other supply will source only a fraction of the current and operate in CV mode. This condition can highly degrade certain power supply performance specifications such as transient response. With theN69100 you do not have to worry about this since it has built-in paralleling capability that ensures each supply equally shares the load current, so they all remain in the desired mode, whether it is CV or CC. The N69100 can be operated in primary/secondary mode which enables paralleled units to be configured and programmed to look like “one” big power supply of up to 200 kW of total power; no need to program each supply individually. The N69100 Series advanced power system gives you the flexibility to easily parallel up to 20 of the 10 kW models and up to 10 of the 20 kW models. Models with identical voltage ratings can be put in parallel for greater output current. List is not supported in primary/secondary mode on the 10 kW N69143A - N69146A (but is supported on the 20 kW N69172A and N69173A APS).Figure 3. Parallel operation for more powerSimplify system connectionThe N69100 Advanced Power System comes standard with GPIB, Ethernet/LAN, USB 2.0 giving you the flexibility to use your I/O interface of choice today and safeguard your test setup for the future. There is no need to worry whether you are choosing the right interface when they all come standard. The N69100 is compliant to 1.5 LXI Device Specification 2016 and includes a built-in Web interface. This means you can control the N69100 remotely using a Web browser and a LAN connection.AC inputThe N69100 series includes five models that use 3-phase, 400/480 VAC inputs. The 10 kW N69143A - N69146A ac mains connections are: L1, L2, L3, PE. While the 20kW N69172A and N69173A ac mains connections are: L1, L2, L3, N, PE (requires a neutral connection).Digital control portOn the rear panel of every N69100 power supply is a digital control port that consists of seven user configurable I/O pins that provide access to various control functions.Figure 4. Digital control port on rear panelTable 1. Digital control port descriptionPin function Available configuration pinsDigital I/O and digital in Pins 1 through 7External trigger in/out Pins 1 through 7Fault out Pins 1 through 2Inhibit in Pins 3Output couple Pins 4 through 7Common (connected to ground) Pins 8Rack mount kitsThe 10 kW N69100 APS are easily rack mounted using the RP7909A rack mount slide kit. This kit provides all the necessary hardware to rack mount a N69143A - N69146A in a 19-inch EIA rack cabinet. This rack mount slide kit includes slide rails, and flange mounts (without ears).The 20 kW N69172A and N69173A can easily be rack mounted using the 1CP108A rack mount flange and front handle kit with the E3663AC basic rail kit for system II Keysight instrument racks. The 1CP108A with the E3663AC can also be used to rack mount any one of the N69100 APS models.BV9200B PathWave BenchVue Advanced Power Control and Analysis SoftwareThe BV9200B and BV9201B PathWave BenchVue Advanced Power Control and Analysis Software gives you fast and easy access to the advanced sourcing and measurement functionality of your N69100 Advanced Power System without any programming. The BV9201B will allow user to control a single instrument, while the BV9200B will allow users to control up to four instruments at once. They are flexible tools for any application and allows you to control any of the N69100 Series’ 5 models (List not supported in primary/secondary mode on the N69143A - N69146A). The software can also control other Keysight power supplies including the popular N6700 modules, N6705 DC Power Analyzer, and the N7900 Advanced Power Supplies.•Control and analyze data from up to four N69100 Advanced Power System•Easily create complex waveforms to stimulate or load down a DUT by inputting a formula, choosing from built-in, or importing waveform data.•Enhanced control and analysis of data with familiar PC controls and large display.•Data log measurements directly to a PC.•Perform statistical analysis (CCDF) of power consumption.•Integrate software functions into users programming environment via API (automation programming interface)Figure 5. BV9201B connected to a N69143A APSSpecificationsUnless otherwise noted, specifications are warranted over the ambient temperature range of 0 to 40°C aftera 30-minute warm-up period. Specifications apply at the output terminals, with the local sensing.For more detailed specifications refer to the N69100 user's manual at:/find/N69100APS-docDC RatingsVoltage source: 0 to 20 V 0 to 80V 0 to 160V 0 to 1000 V 0 to 2000 V Current source: 0 to 800 A 0 to 250A 0 to 125A 0 to 60 A 0 to 30 A Current sink @-80 A -25A -12.5 A -6 A -3 A 10%:Power: 10 kW 10 kW 10 kW 20 kW 20 kW Output ripple and noise30 mV 80 mV 200 mV 1.5 V 3 VCV peak-to-peak1:CV rms2: 3 mV 8 mV 20 mV 200 mV 400 mV Load regulationVoltage3: 1 mV 3 mV 6 mV 50 mV 100 mV Current: 50 mA 25 mA 13 mA 8 mA 4 mA Voltage programming & measurement accuracy40.02% + 4 mV 0.02% + 13 mV 0.02% + 26 mV 0.04% + 120 mV 0.04% + 240 mV Current programming & measurement accuracy40.09% + 370 mA 0.06% + 115 mA 0.06% + 58 mA 0.09% + 23 mA 0.09% + 12 mA Transient response5Recovery Time: 900 µs 900 µs 900 µs 900 µs 900 µs Settling band: 0.2 V 0.8 V 1.6 V 10 V 20 V1 From 20 Hz to 20 MHz (-3dB bandwidth) with resistive load, terminals ungrounded, or either terminal grounded2 From 20 Hz to 10 MHz (-3dB bandwidth) with resistive load, terminals ungrounded, or either terminal grounded3 Also applies when remote sensing with a ≤1 V drop per load lead4 Percent of value + offset; at 25°C ±5°C after a 30-minute warm-up; measurement NPLC=1; valid for 1 year5 Time to recover to within the settling band following a step change from 40% to 90% and 90% to 40% of full load at Comp0 with a 40 μscurrent rise and fall timeSupplemental CharacteristicsSupplemental characteristics are not warranted but are descriptions of performance determined either by design or by type testing. Supplemental characteristics are typical unless otherwise noted.Output ripple and noise (from 20 Hz to 20 kHz)CC rms: 200 mA 70 mA 50 mA 30 mA 15 mA Voltage programmingRange: 20 mV to 20.4 V 80 mV to 81.6 V 160 mV to 163.2 V 1 V to 1020 V 2 V to 2040 V Resolution: 3.06 mV 12.8 mV 25.6 mV 160 mV 320 mV Current programmingRange: 0 to 816 A 0 to 255 A 0 to 127.5 A 0 to 61.2 A 0 to 30.6 A Resolution: 248 mA 80 mA 40 mA 19.2 mA 9.6 mA Resistance programmingRange: 0 to 0.049 Ω0 to 0.625 Ω0 to 2.5 Ω0 to 69 Ω0 to 277 ΩResolution: 0.4 µΩ 4.8 µΩ19.6 µΩ0.55 mΩ 2.2 mΩAccuracy: 0.05% + 2 µΩ0.05% + 16 µΩ0.05% + 50 µΩ0.06% + 0.55 mΩ0.06% + 2.2 mΩVoltage up/down programming, comp 0110 ms 10 ms 10 ms 10 ms 10 ms Rise/fall time 10%to 90% of step:50 ms 50 ms 50 ms 50 ms 50 ms Settling time to0.1% of step:Voltage up/down programming, comp 11Rise/fall time 10%20 ms 20 ms 20 ms 20 ms 20 msto 90% of step:100 ms 100 ms 100 ms 100 ms 100 ms Settling time to0.1% of step:Voltage up/down programming, comp 2140 ms40 ms40 ms40 ms40 ms Rise/fall time 10%to 90% of step:200 ms200 ms200 ms200 ms200 ms Settling time to0.1% of step:Current up/down programming, comp 022.5 ms 2.5 ms 2.5 ms 2.5 ms 2.5 ms Rise/fall time 10%to 90% of step:Settling time to 1%5 ms 5 ms 5 ms 5 ms 5 msof step:1 With no load and a step change from 0.1% to 100% of voltage rating; bandwidth frequency = 100 kHz2 With AC short and a step >10% of output voltage rating; bandwidth frequency = 100 kHzCommon Characteristics - All ModelsCommand processing time ≤ 1 ms from receipt of command to start of output change. Applies tosimple setting commands over theC omputer interfacesLXI 1.5 LXI Device Specification 2016LAN 10 Mb, 100 Mb, 1 Gb LANUSB USB 2.0 (USB-TMC488 protocol)GPIB SCPI - 1993, IEEE 488.2 compliant interfaceConstant dwell ARBsNumber of points Up to 65,535Dwell range One dwell setting applies for the entire ARB, from 10.24 µs to 0.30secondsDwell resolution Values are rounded to the nearest 10.24-microsecond increment Regulatory complianceEMC Complies with European EMC Directive for test and measurementproductsComplies with Australian standard and carries C-Tick markThis ISM device complies with Canadian ICES-001Cet appareil ISM est conforme à la norme NMB-001 du Canada Safety Complies with European Low Voltage Directive and carries the CEmark.Conforms to US and Canadian safety regulations.Output terminal isolationFor all 20 VDC models No output terminal may be more than ± 60 VDC from any otherterminal or chassis ground.For all 80 and 160 VDC models No output terminal may be more than ± 240 VDC from any otherterminal or chassis ground.For 1 kV DC models No output terminal may be more than ±1000 VDC from any otherterminal or chassis ground.For 2 kV DC models No output terminal may be more than ±2000 VDC from any otherterminal or chassis ground.Common Characteristics - All Models continuedAC inputConnections L1, L2, L3, PE; does not require a neutral connection (N69143A - N69146A)L1, L2, L3, N, PE; requires a neutral connection (N69172A, N69173A)Phase and range 3 phase; 400 VAC ± 15% and 480 VAC ± 10% (N69143A, N69145A, N69146A)3 phase; 380 - 480 VAC ±10% (N69172A, N69173A)Input VA N69143A, N69145A, N69146A: 11.5 kVAN69172A, N69173A: 23 kVAInput current per phase400 VAC input N69143A, N69145A, N69146A: 17.3 AN69172A, N69173A: 36 AEfficiency at full powerN69143A, N69145A, N69146A: 85%N69172A, N69173A: 90%Power factor0.99 at nominal input and rated powerTypical weightN69143A, N69145A, N69146A: 70 lbs. (31.8 kg)N69172A, N69173A: 82 lbs. (37.3 kg)Output QuadrantsFigure 6. N69100 output characteristicModel + V1 + V2 + V3 + I1 + I2 - I2 P1 Sinking resistance N69143A 20 V 12.5 V 0.5 V 500 A 800 A 80 A 10 kW 625 μΩN69145A 80 V 40 V 0.75 V 125 A 250 A 25 A 10 kW 3 mΩN69146A 160 V 80 V 1.5 V 62.5 A 125 A 12.5 A 10 kW 12 mΩN69172A 1000 V 333 V 7.5 V 20 A 60 A 6 A 20 kW 83.3 mΩN69173A 2000 V 666 V 6 V 10 A 30 A 3 A 20 kW 333 mΩOrdering InformationAvailable models400/480 VAC modelsN69143A Advanced Power System - DC Power Supply 20 V, 800 A, 10 kW, 400/480 VACN69145A Advanced Power System - DC Power Supply 80 V, 250 A, 10 kW, 400/480 VACN69146A Advanced Power System - DC Power Supply 160 V, 125 A, 10 kW, 400/480 VACN69172A Advanced Power System - DC Power Supply 1000 V, 60 A, 20 kW, 400/480 VACN69173A Advanced Power System - DC Power Supply 2000 V, 30 A, 20 kW, 400/480 VACLine cords and terminations (plugs)Due to the number of different line cords and terminations around the world, the N69100 power supplies do not come with line cords or terminations. Users will need to supply their own dependent on the local laws and codes of the country/region where the power supply will be used.OptionOption UK6 Commercial calibration with test results dataAccessoriesBV9200B BenchVue Advanced Power Control and Analysis - 4 instrument connectionBV9201B BenchVue Advanced Power Control and Analysis - single instrument connectionRP7909A Rack Mount Slide Kit for N69143A - N69146A Advanced Power System1CP108A* Rack Mount Flange and Handle kit (N69172A/73A and all N69100 models)E3663AC Basic Rail Kit for System II Keysight Instrument Racks*requires rail kitLearn more at: For more information on Keysight Technologies’ products, applications or services,please contact your local Keysight office. The complete list is available at:/find/contactus。
intel m10 电源管理用户指南说明书

Intel® MAX® 10电源管理用户指南本翻译版本仅供参考,如果本翻译版本与其英文版本存在差异,则以英文版本为准。
某些翻译版本尚未更新对应到最新的英文版本,请参考英文版本以获取最新信息。
在线版本ID: 683400内容内容1. MAX® 10电源管理概述 (3)2. MAX 10电源管理功能和体系结构 (4)2.1. 电源器件选项 (4)2.1.1. 单电源器件 (4)2.1.2. 双电源器件 (4)2.1.3. MAX 10电源器件选项对比 (5)2.1.4. 电源设计 (5)2.2. 上电复位电路 (6)2.2.1. POR电路监控和未监控电源 (7)2.2.2. 即时启动支持 (8)2.3. 电源管理控制器方案 (8)2.3.1. 电源管理控制器体系结构 (8)2.4. 热插拔 (10)2.4.1. 热插拔规范 (10)2.4.2. 热插拔功能的实现 (11)3. 电源管理控制器参考设计 (12)3.1. 时钟控制模块 (13)3.2. I/O缓冲器 (13)3.3. 内部振荡器 (13)3.4. 电源管理控制器 (13)3.4.1. Entering状态 (14)3.4.2. 睡眠状态 (14)3.4.3. Exiting状态 (14)3.4.4. 唤醒状态 (14)3.5. 进入或退出睡眠模式 (14)3.5.1. 进入睡眠模式 (14)3.5.2. 退出睡眠模式 (15)3.5.3. 时序参数 (15)3.6. 硬件实现和电流测量 (16)A. MAX 10 Power Management User Guide存档 (18)B. MAX 10电源管理用户指南附加信息 (19)B.1. MAX 10电源管理用户指南文档修订历史 (19)1. MAX® 10电源管理概述MAX® 10器件提供下列电源器件选项:•单电源供电器件—需要1个3.0 V或3.3 V外部电源,以提供最大便利性和电路板简洁性。
高压电源XMPF10N5 24安全和安装说明书

High Voltage Power SupplyXMPF10N5/24SAFETY AND INSTALLATIONINSTRUCTIONSDocument Number: 81234-4.SAFETYDANGERHIGH VOLTAGERISK OF ELECTROCUTIONObserve extreme caution when working with this equipmentHigh voltage power supplies must always be connected to protective earthDo not touch connections unless equipment is turned off and the capacitance of both the load and power supply are groundedAllow adequate time for discharge of internal capacitance of the power supplyDo not ground yourself or work under wet or damp conditionsServicing SafetyMaintenance may require removing the Instrument cover with the power onServicing should only be done by qualified personnel aware of the hazardsIf in doubt, return to supplier for servicingChange HistoryContents1Unit Description (4)2Safety (4)3Installation (4)4Regulatory Specifications (5)5Environmental conditions (5)6Mechanical (6)7Input and Output Connections (7)1 Unit DescriptionThe XMPF10N5/24 unit consists of one chassis containing the high voltage power supply.The dimensions are 170mm x 70mm x 30mmThe unit is designed for operation from 24Vdc ± 10%. The maximum rated input current is 500mA.The unit provides an HV Cathode output rated at -10kV, 5W. With a floating filament intended to drive an X-ray tube with a grounded anode, rated at 0V to 3.5Vac referenced to the Cathode Output, 0.42A max.All control and monitoring is accomplished via a 15 way ‘D’ connector which also provides input power to the unit.2 SafetyThe HV output of the unit is hazardous and the conditions of this manual must be complied with to maintain safety. Operating the unit in a manner not specified in this manual may impair the protection against electric shock provided by the unit.The unit is contained in an earthed case, the system protective earth shall be provided to the chassis. The case of the unit shall be properly bonded to the main protective earth termination in the end product.The unit has been evaluated for use in a Pollution Degree 2, Installation Category II environment. Consideration should be given to conducting the following tests with the unit installed in the end product:•Dielectric Voltage Withstand Test, between live parts of the unit and the end product chassis.•Permissible Limits Tests with the unit installed in the end product.•Temperatures on power electronic components, transformer windings and accessible surfaces. There is no relevance to a risk assessment carried out as part of the CE testing on the HV unit. It is recommended that a full assessment is carried out in the end application.This symbol on the unit means “read the manual before powering the equipment”.This symbol on the unit means “Caution; risk of electric shock”.3 Installation3.1 Initial InspectionInspect the package exterior for evidence of damage due to handling in transit. Notify the carrier and Spellman immediately if damage is evident. Do not destroy or remove any of the packing material used in a damaged shipment.After unpacking, inspect the panel and chassis for visible damage.Note: Failure to comply with the above could compromise the safe operation of the unit and invalidate the warranty.3.2 Mechanical InstallationThe unit should only be used in a Pollution Degree 2 Installation Category II environment.The input and output connectors are not intended for field connections and should only be connected to internal wiring in the end product. The unit is intended for use as a component and no surface of the unit should be accessible in the end product.3.3 Electrical InstallationThe unit must be terminated safely before operation. Hazardous voltages will be exposed if the connector is removed whilst the unit is enabled.The 24Vdc input shall be provided by a double insulated, or SELV, UL recognised power supply.Circuits connected to the unit shall be provided with rated insulation to IEC/UL61010-1.The unit must be switched off for at least one minute before disconnecting any of the connectors.4 Regulatory SpecificationsThe unit is designed to meet the requirements of EN 61010-1, UL 61010-1 and CAN/CSA-22.2 No. 61010-1. Please consult the factory for further approval information.As the unit is designed for incorporation within the user’s system it is not tested against any specific EMC standards. The user will need to take sensible EMC precautions when designing the unit in and verify the overall system EMC performance against any relevant standards.5 Environmental conditions5.1 OperatingProtection: The power supply will be designed to meet IP40 and will bereasonably protected against dust.Temperature: +5o C to +40o C.Relative Humidity: 20% to 80% (no condensation)5.2 StorageTemperature: -40o C to +70o C.Relative humidity: 5% to 95%Absolute humidity: maximum 25 gm-³Maximum storage period: >0.25 year (at above conditions)Long term storage: >3 year (special packaging required)6 Mechanical6.1 XMP10 Mechanical outline: 170mm x 70mm x 30mmThe mass of the module is nominally 2kg.M4 Earth stud7 Input and Output Connections7.1 Monitoring and Control7.1.1 Filament (direct program)If required, the filament can be programmed directly. In this case the emission current is notcontrolled it will be fixed by the filament setting. This requires removal of an internal link and should be requested when the unit is ordered so that it can be configured at the factory.7.1.2 HV enableThis is a digital input which controls the output. Driving this input low (< 0.8V) will cause the filament current to increase from its pre heat level to the value set by the pre-set maximum filament current adjustment. The HV converter then starts up and reaches full output approximately 4.5 seconds after the HV enable is driven low. Disconnecting or driving this input high (>2.4V ) will cause the filament to return to its pre heat value and the HV output is disabled. The maximum input voltage of this input is 12V.7.1.3 Cathode voltage program outputA 10V internal reference voltage and 12 turn 5kΩ potentiometer is provided that can be used to pre-set the cathode voltage. Connecting this output to the cathode voltage program input will allow thevoltage of the cathode to be pre-set using the internal potentiometer.7.1.4 Cathode voltage program input0 – 10V input corresponding to 0 – 10kV on the cathode output.Accuracy ±2% of full scale.Z in =470kΩ7.1.5 Cathode voltage monitor0 – 10V output corresponding to 0 – 10kV on the cathode output.Accuracy ±2% of full scale.Z out = 2k2Ω7.1.6 Emission current monitor0 – 10V output corresponding to 0 – 500uA emission current.Accuracy ±3% of full scale.Z out = 2k2Ω7.1.7 Filament current monitor0 – 10V output corresponding to 0 – 500mA filament current.Accuracy ±5% of full scale.Z out = 2k2Ω7.1.8 Emission current program input0 – 10V input corresponding to 0 – 500uA emission current.Accuracy ±3% of full scale.Z in= 10MΩ7.1.9 Emission current program outputA 10V internal reference voltage and 12 turn 10kΩ potentiometer is provided that can be used to pre-set the emission current. Connecting this output to the emission current program input will allow the emission current to be pre-set using the internal potentiometer.7.1.10 Pre-set maximum filament current set value.A 10V internal reference voltage and 12 turn 10KΩ potentiometer is provided that can be used topre-set the maximum filament current. This is brought out to a pin so that it can be measured.0 – 10V output corresponding to 0 – 500mA filament current.7.2 The low voltage signal connections are made by a 15 way ‘D’ connector; the pin out is shown below.The filament current limit is set via an internal pre-set accessible through the case.If external cathode voltage control is not required link pins 7 and 8.If external emission current control is not required link pins 12 and 13.7.3 Output:The HV output is a flying lead consisting of 2 Reynolds 18kV rated FEP insulated wire, 1.02mm overall diameter. Conductors 19/40AWG. Overall length 500mm. The two wires are sleeved together.。
ANTEC NE650M 电源用户手册说明书

NE650M POWER SUPPLY USER’S MANUALNE650MGet economical power today with the NeoECO Modular Series, Antec's high-efficiency power supply solution. Featuring hybrid modular cable management, 80 PLUS® BRONZE certification, a quiet 120mm DBB fan, Japanese heavy-duty capaitors and universal input with active power factor correction (PFC), the NeoECO Modular series gives you a cooler, quieter system all powered by Continuous Power. The NeoECO Modular series also features industrial safety protection, including short circuit and over voltage protection, for stable and reliable power no matter what.STANDARDS AND FEATURESThe connectors and power specifications of the NE650M PSU are all compatible with ATX12V v2.4 & EPS12V v2.92 specifications. This power supply also features Active Power Factor Correction (PFC), which improves the power factor value of the power supply by altering the input current wave shape, helping to power transmission across the grid.SYSTEM PROTECTIONA variety of industrial-grade safety circuitry will help protect your computer. Sometimes the PSU will “latch” into a protected state. You will need to power off the PSU and clear the fault before it will function again. There are no user-replaceable fuses in your NE650M.80 PLUS® CERTIFICATION80 PLUS® certification is the most widely recognizedindependent standard in power supply efficiency. An80 PLUS® BRONZE certified power supply uses lessenergy and generates less heat to stay cooler, runquieter and last longer. The NE650M has been 80PLUS® BRONZE certified to be at least 82% efficient ata wide range of operating loads; this will lower youroperating costs and help protect the environment.POWER OUTPUTTo see the output capacity and regulation for each different voltage, see table 1. TABLE 1Output Voltage Load Max.Regulation Ripple & Noise +12V₁50A± 5%< 120 mV+3.3V20A± 5%< 50 mV+5V17A± 5%< 50 mV-12V0.3A± 5%< 120 mV+5Vsb 2.5A± 5%< 50 mVTABLE 2Cable QuantityConnectorsDescription1X 124(20+4)-pin Motherboard1X 18(4+4)-pin ATX12V/EPS12V2X 28(6+2)-pin PCI-E2X 3SATA1X 3Molex1X 2MolexX 1FDDINSTALLATIONInstall the PSU into either the top or bottom of your case with the four screws provided. Refer to your case manual if you are unsure where the power supply should be installed.Connect the 24-pin main power connector to your motherboard.Connect the 8-pin or 4+4-pin connector for the CPU. If your motherboard has an 8-pin socket with a cover on some of the openings, we recommend that you remove the cover and use the 8-pinconnector.Note: Please also refer to your motherboards manual for any special instructions.Connect the AC power cord to the power supply AC inlet. Be sure to use the heavy-duty cord suppliedwith your PSU.PCI-E graphics cards use different amounts of power. For some, a single 6-pin connector is sufficient, making the hardwired connector the preferred choice. More powerful cards use multiple connectors, including the advanced 8-pin PCI-E connector. The 8-pin PCI-E connector on the PSU can be used aseither a 6- or 8-pin connector.Hard drives, optical drives (CD/DVD/BluRay™) and other accessories will use either the older 4-pin Molex connector or the newer 15-pin SATA connector. 4-pin Molex connectors have two black, one yellow and one red wire. The SATA connector has an additional orange power wire.When you have all the connections secured, turn the switch on the PSU to the “|” position.Technical Support:/supportUSA & Canada1-800-22ANTEC*******************Europe+31-(0)-10-462-2060*******************Asia+886 (0)800-060-696 *******************Visit us on Facebook for contests, information & supportUSA & Canada /AntecIncEurope /AntecEuropeUK /AntecUKAustralia & New Zealand /AntecAUIndia /AntecIndiaIsrael /AntecIsraelPhilippines /AntecPHSingapore /AntecSGSweden /AntecSwedenAntec, Inc.47681 Lakeview Blvd., Fremont, CA 94538 / USATel: 510-770-1200 - Fax: 510-770-1288© 2017 Antec, Inc. All rights reserved.Specifications are subject to change without prior notice. Actual product(s) and accessories may differ from illustrations. Omissions and printing errors excepted. Content of delivery might differ in different countries or areas. Some trademarks may be claimed as the property of others.Reproduction in whole or in part without written permission is prohibited.。
动态功率共享安装指南说明书
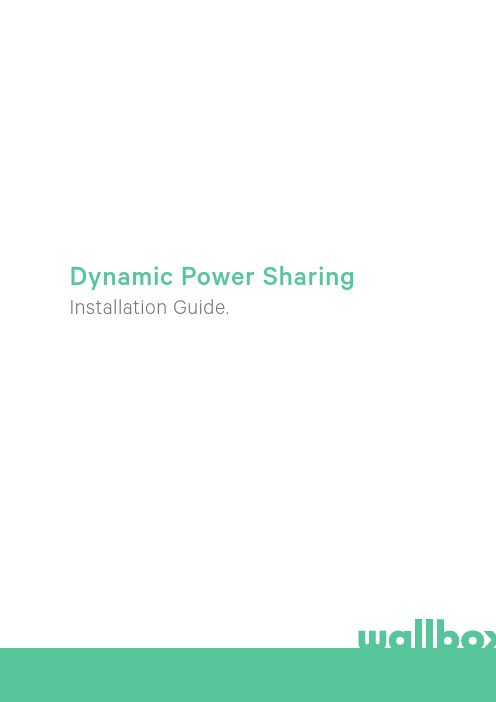
Dynamic Power Sharing Installation Guide.1 Introduction2 Important notes3 Required material and tools4 Summary of characteristics5 Installation5.1. Installation of the charging network5.2 Installation of the energy meter6 Configuration6.1 Master/Slave setup and powering on6.2 Network configuration6.3 Status notification6.3.1 Network not configured6.3.1 Master paired6.3.1 Master not paired6.3.1 Slave paired6.3.1 Slave not paired6.3.1 In queue7 TroubleshootingANNEX A3 6 8 10 12 13 16 17 18 18 20 20 21 21 22 22 23 24 27Index1 Introduction1 IntroductionThe addition of charging points in a building implies an increase of the overall power demand. This usually results in having to increase the overall available power, which is an expensive option and sometimes not the most efficient.The Dynamic Power Sharing (DPS) monitors a building’s demand and compares it to its maximum allowable value. When it is lower than the maximum, it can supply all the remaining available power to reach the maximum to the charging network. Contrarily, if the building’s demand is equal or greater than its maximum permitted value, no power will be supplied to the charging stations. It can be seen that just by taking advantage of periods where there is low demand from the building side, the charging network’s demand can be satisfied without having to increase the installation’s overall power. To accomplish this smart energy distribution system, the Power Sharing Smart functionality has been enhanced to create Dynamic Power Sharing.BENEFITSThe Dynamic Power Sharing has a set of benefits that extend to multiple levels and actors. Benefits for the building owner• Protection over blackouts: The Dynamic Power Sharing will prevent that the operating of the charging station leads to a blackout.• Savings up to 40% of current capacity costs: In cases where there is a power limitation the optimization in the use of this power leads to real capacity savings.• Reduction in installation costs: Since the Power Sharing provides savings regarding installation costs, the Dynamic Power Sharing offers the same savings.Benefits for the end users• Service available: This configuration allows to increase the number of chargers installed in a building. Taking advantage of periods where the building demand is low, the Dynamic Power Sharing allows for a bigger number of chargers to charge.• Reduction in price: The capacity and installation costs savings from the building owner can also lead to money savings for the user.• Reduction in charging time compared to ordinary solutions: The variability in the available power for charging can lead to a bigger power supplied to all chargers, which will result in a reduction of the time of charge.SYSTEM COMPONENTSDynamic Power Sharing uses an external energy meter installed after the mains breaker to know the power available for the charging network at every moment and dynamically distribute it across the chargers in a smart way.One DPS-ready charging network consists in one Master charger and up to 24 Slave chargers. The energy meter is connected to the Master charger and transmits measurements of the actual power consumption of all the electrical loads downstream. The Master charger automatically adjusts the total power that is left for charging EVs and distributes it among the Slave chargers and itself.Wallbox Master Charging installationCommunication Fig. 12 Important notes2 Important notes• This feature is supported by the following Wallbox chargers: Commander, Commander 2, Copper C, Copper S, Copper SB, Pulsar Plus, Pulsar (only as slave).• A Wallbox Pro license is required to activate Dynamic Power Sharing on your charger. The charger must be installed following the instructions of the product Installation Guide that is delivered with the charger as well as of this guide.• Only energy meters that are delivered by Wallbox are compatible with this feature.• Only qualified technicians are allowed to perform the installation as it is described in this document.• Before the installation of Dynamic Power Sharing, the charger must be powered off and its cover removed. After, the charger must be properly closed as defined in the Installation Guide.3 Required material and tools3 Required material and toolsOne energy meter Two or more Wallbox chargersUTP and STP cable myWallbox account• Access to the main fuse box is necessary for the installation of the energy meter.• Cable between Master charger and Energy Meter: an STP Class 5E cable, 2 twisted pair, is recommended. The length depends on the customer setup, while a maximum of 500 m can be installed. • Cable between chargers: UTP Cat 5E, 1 twisted pair, is recommended. A total maximum length of 250 m can be installed.4 Summary of characteristics4 Summary of characteristicsQuantity of Master chargers (all models except Pulsar)Quantity of Slave chargers (all models) Quantity of Energy meters (only the models supplied by Wallbox are supported) Communication protocol between chargers Communication protocol between Master charger and power meterMaximum total length of charging network Maximum length between Master charger and energy meterTerminating chargersConfigurable maximum phase current Configurable installation maximum current 11-241CANModbus RTU250 m500 m2 (at the ends of the charging network) Charging network MCB rated current Installation main switch rated current5 Installation5 InstallationThe installation of a charging network with Dynamic Power Sharing can be split in two parts:• Installation of the charging network• Installation of the meterExisting installationIn case the charging network is already installed in non-Power Sharing Smart configuration, power off and carefully open all chargers before continuing with next steps. In case of a Power Sharing Smart charging network, power off and carefully open only the Master charger before continuing with steps in section 5.2. For safety opening, follow the instructions in section “Opening the device” into the product Installation Guide.New installationIn case of a new installation, first carefully read this manual for determining the cabling requirements of the installation. Once cabling and charger positions are clear, proceed by installing the chargers at the selected locations according to the product Installation Guide and the indications provided in the following sections.5.1 Installation of the charging networkPositioning in the system (T/NT chargers)When installing the Wallbox in a Dynamic Power Sharing network, the location is important to be taken into account.The Master charger communicates with the Slave chargers through a cabling system that connects the chargers in a chain: one charger is connected to the next one.The chargers at the ends of the communication chain must be configured as Terminating (T) chargers while the chargers in between the ends must be configured as Non-terminating (NT).Each charger includes an electric element that defines whether it is T or NT:• Commander 2, Pulsar Plus and Copper*: Defined by the position of the corresponding switch on the control circuit.• Commander or Pulsar: Pre-defined factory setting. A specific Part Number must be specified when ordering the unit. Indicated with a -P- in the Part Number (ex. WBXX-X-X-X-P-XXX-X).*In this document, Copper C, Copper S and Copper SB are referred as CopperCopper T/NT Switch Pulsar PlusT/NT SwitchCommander 2 T/NT Switch5.2 Cabling installation• The communication cable consists of two lines: CAN-low (CAN-L) and CAN-high (CAN-H).• We recommend to use the following cable-type: Ethernet Class 5E no shield, 1 twisted pair.• The total maximum length of the cabling between the ends of the network is 250 m. 5.1 Installation of the charging networkCopper, Commander 2 and Pulsar Plus have two slots for input and output cabling so the conjunction is done inside the charger.TNTNTTCopper T connection Copper NT connectionPulsar Plus or Commander 2 NT connection Pulsar Plus or Commander 2T connectionCAN-HCAN-LCAN-LCAN-HCAN-LCAN-HCAN-HCAN-LCABLING COPPER, COMMANDER 2 AND PULSAR PLUS5.1 Installation of the charging networkCABLING COMMANDER AND PULSARCommander and Pulsar only have one slot so the conjunction is done with a connection strip.Commander connection PulsarconnectionCAN-LCAN-HCAN-HCAN-L5.2 Installation of the energy meterLocation of the energy meterAs shown in Fig. 1, the energy meter (labeled as “Wallbox Meter”) must be installed at the main branch after the main switch of the electrical installation and before the split in branches. Install the energy meter to the mains according to its Installation Guide.Cabling of the energy meterAfter the energy meter has been installed according to its Installation Guide on the correct position, it must be connected to the Master charger of the charging network.The Annex “A” describes the cabling setup to the currently supported energy meters.6 Configuration6 Configuration6.1 Master/Slave setup and powering onEach Dynamic Power Sharing network consists of 1 Master charger and up to 24 Slave chargers. The role of a charger within the network can be configured according to the following table:MasterSlaveCopperPulsarCommander 2Pulsar Plus Commander Charger Any combinations are possible.The master can be set at any position within the group (T or NT).The role of each charger must be configured using the rotary switch before powering the charger on (see product Installation Guide for position of the rotary switch)::Once the role of all chargers is set with the rotary switch, the system can be powered on.The Master charger will automatically detect the Slave chargers as well as the energy meter.0Configuration 0Slave 8 or 9MasterAny otherStand-alone (see Installation Guide)Position 6.2 Network ConfigurationOnce the system has been powered on, Dynamic Power Sharing functionality must be configured on the Master charger only. This can be done using either the Wallbox App or the touchscreen in Commander and Commander 2.The chargers will stay in Unconfigured status while the Master is not properly configured (see section “Status notification”).A myWallbox account with Wallbox Pro license is needed in order to configure this functionality. For more information see the corresponding product User Guide.The Dynamic Power Sharing requires four parameters to be configured on the Master charger:In Commander, access the configuration menu through Settings -> System -> Dynamic Power Sharing.1. NUMBER OF CHARGERS IN THE POWER SHARING SYSTEM •This number must include the master charging station.2. MAXIMUM CURRENT PER PHASE • This value refers to the maximum current that can be supplied to the charging network.•Typically this value is the rated current of the MCB that protects the chargers branch.3. MINIMUM CURRENT PER CHARGER • While the standards define a minimum current of 6 A (default value), some cars need to have a minimum current of 10 A.•Default value is 6 A4. MAINS BREAKER MAXIMUM CURRENT •This value refers to the maximum current that can be supplied to the electrical installation to which the charging network belongs. Typically this value is the rated current of the mainscircuit breaker that protects the electrical installation.CommanderCommander 2In Commander 2, access through Menu -> Settings -> Dynamic Power Sharing.In the Wallbox App, once connected and synchronized with the charger, access throughConfiguration Menu -> Dynamic Power Sharing.All master chargersOnce the role of all chargers is set with the rotary switch, the system can be powered on.The Master charger will automatically detect the Slave chargers as well as the energy meter.6.3 Status notification6.3.1 Network not configuredThis is the initial status after power on the setup.CommanderCommander 2All chargers6.3.2 Master pairedThe network has been successfully set. All chargers are connected with the master.6.3.3 Master not pairedThe number of chargers in the configuration does not match the number of chargers that are connectedand detected by the Master. Review sections 2 and 3 to make sure all steps are being understood.CommanderCommander 2All master chargersAll master chargersCommanderCommander 26.3.5 Slave not pairedThe slave is not successfully connected with the master on the DPS network.This state is reached after 30 seconds without successful communication.In this state, the charger status indicator (Halo or RGB LED) will blink fast in Ready, Connected and Charging state. Remember that in this state the slave can only charge at 6 A.6.3.4 Slave pairedSlave connected with the master. The installation has been successful.CommanderCommander 2All chargersAll chargersCommanderCommander 2Pulsar / Pulsar PlusREADY slave not paired CONNECTEDslave not pairedCHARGINGslave not paired6.3.6 In queueNot enough power available for this charger.• If the power has already been reduced to the minimum, the newly plugged cars will go into this state.• Once the system has enough power available (e.g. a car has been fully charged) it will start charging.•In this state, the charger status indicator (Halo or RGB LED) will blinkAll chargersCommanderCommander 2Pulsar / Pulsar Plus7 Troubleshooting7 TroubleshootingUpgrading from older Power Sharing versionsAs Power Sharing is a functionality that is working across our charging stations, and not only on a single one, all chargers must work the same way.Therefore, when upgrading from an older version of Power Sharing Smart, you need to update the Software of all of the chargers in the network. Our User Guides explain the update process. Charger(s) have a red LED/HALO/screen• After the start up, this is the default colour on a Power Sharing Smart net. If it lasts more than around 30 seconds, then check that the net is configured properly. If not, set the net configuration and wait from 5 to 30 seconds.• Make sure that the amount of chargers in the configuration include the Master.• Make sure that the maximum current per phase is set properly and that is higher than the minimum to be assigned.Charger(s) have a blinking green LED/HALO or Commander / Commander 2 shows the message “Slave not paired with the power sharing network” on the Power Sharing menu• Poor contact on the CAN communication cables. Check that all the communication cables are properly connected on the chargers (see section 2).• Wrong resistor value between CAN communication lines. Power off all the chargers and measure the electrical resistance between CAN-H and CAN-L, it must be around 60 Ohms. If not, please check again section 5.Resistor’s value between communication lines is different than 60 Ohms• If it is higher is because there’s only one charger with the terminal resistors. If it is lower is because there are more than 2 charger with terminal resistors.• Make sure that the two ends of the line have the “T” switch (if there’s the switch) selected or that the resistors are on the corresponding chargers (see section 5).• If the resistor value is not around 60 Ohm but the configuration is correct, a charger may be faulted.• To ease the searching of the faulty unit remove the CAN cables of the chargers and check the resistor value in each one with, if possible, the switch in T position.• The T chargers should have a 120 Ohm resistance between lines while the NT should have an open line.The Master charger does not detect the energy meterThe Master charger automatically detects the energy meter if both devices are correctly connected and powered on. When the communication with the energy meter has been established, a thunder icon is displayed on the screen of Commander, Commander 2 and Copper, and an icon “RxTx” is displayed on the screen of power meters EM112 and EM340.• Check that the RS485 cable is properly connected to both devices according to indications in Annex A.• Check that the RS485 switch on the Master if it is a Pulsar Plus or Commander 2.Erratic behaviour• Poor contact on the communication cables. Check that all the CAN communication cables are properly connected on the chargers and the RS485 communication cable is properly connected between the Master and the energy meter.• Wrong configuration on the Master.• Wrong resistor value between communication lines. Power off all the chargers and measure the Ohm resistor between CAN-H and CAN-L, it must be around 60 Ohms. If not, please check again section 2.Charger keeps waiting for current even though there’s no other car• The current assignation may last up to 30 seconds.• Make sure that there are no schedules programmed.• Check that the master and slaves are all paired. If not the maximum current per phase will be diminished 6 A per charger not paired.ANNEXANNEX A.1 Carlo Gavazzi EM340 / EM112The energy meter Carlo Gavazzi EM 340 is used for a 3-phase installation and the model EM112 for a 1-phase installation.Fig. A1.1: Cabling in specified energy metersFig. A1.2 Power lines installation on an EM112 without neutral line and/or line-to-line voltage below 260V.In the event that the supply scheme does not include a neutral line connection and/or the line-to-line voltage is below 260V, please connect the Carlo Gavazzi EM112 energy meter as shown in Fig. A1.2:In the following page Fig. A1.3, Fig. A1.4, Fig. A1.5 and Fig. A1.6 show where to connect the cabling to the Wallbox.Depending on the model, the Wallbox may label RS485A for D+ and RS485B for D-.Fig. A1.1 shows the cabling between the energy meter and the Wallbox. Please mind the required short-circuit between the pins T and A- of the energy meter.For installing the EM112 or EM340 in supply schemes with neutral line, follow the instructions of the manufacturer's manual delivered with the energy meter.ANNEX A.1 Carlo Gavazzi EM340 / EM112Fig. A1.3: Cabling in a Commander Wallbox GNDD-D+Fig. A1.4: Cabling Installation in a Copper WallboxGNDD-D+Fig. A1.6 Cabling Installation in a Wallbox Commander 2Fig. A1.5 Cabling Installation in a Wallbox Pulsar Plus D-D+GNDD-D+GNDANNEX A.2 Temco SPM1-100-ACThe energy meter Temco SPM1-100-AC is used for a 1-phase installation with up to 100 A.The Temco power meter needs to be clipped to the mains power cable (schematic location shown in Fig. 1), with the current flowing in the direction as shown in Fig A2.1.Only the phase-cable must be drawn through the clamp. The neutral-cable must not be drawn through.Fig. A2.1: Energy Meter connection diagramm123456Fig. A2.2: Cabling in Temco energy meterFig. A2.2 shows the cabling between the energy meter and the Wallbox. The numbers are refering to the Fig. A2.1. Before turning on the system it is important to check again that the connection of “GND” and “12 V” has been done correctly.In the following page Fig. A2.3, Fig. A2.4, Fig. A2.5 and Fig. A2.6 show where to connect the cabling tothe Wallbox.ANNEX A.2 Temco SPM1-100-ACFig. A2.4: Cabling Installation in a Copper WallboxGNDD-D+12VFig. A2.5 Cabling Installation in a Wallbox Pulsar Plus D-D+GND12V Fig. A2.6 Cabling Installation in a Wallbox Commander 2D-D+GND12V Fig. A2.3: Cabling in a Commander WallboxGND12VD-D+ANNEX A.3Fig. A3.1 Setting the RS485 switch to “T”Fig. A3.2 Setting the RS485 switch to “T”In the cover of your Pulsar Plus remember to set the RS485 switch to “T”In the cover of your Commander 2 remember to set the RS485 switch to “T”。
- 1、下载文档前请自行甄别文档内容的完整性,平台不提供额外的编辑、内容补充、找答案等附加服务。
- 2、"仅部分预览"的文档,不可在线预览部分如存在完整性等问题,可反馈申请退款(可完整预览的文档不适用该条件!)。
- 3、如文档侵犯您的权益,请联系客服反馈,我们会尽快为您处理(人工客服工作时间:9:00-18:30)。
后面板 1、面板入口——删除或改变DIP设置。 2、保护气体管子入口——工业标准5/8—18CGA线路连接。 3、卷筒焊枪/推拉焊枪连接器,用于连接PythonCobraMAX和Prince XL焊枪。 4、用于TIG焊接的遥控/脚踏电流控制开关连接器(可选)。 5、Arclink控制线缆连接器。 6、水冷装置连接器(可选)。
MIG焊 脉冲MIG焊 STT焊 药芯焊丝焊 手工焊 TIG焊 碳弧气刨
● 在焊接钢铁、不锈钢、铝和其它材料时能获得国际水平 的优良的电弧性能。
● 波形控制技术特点是配置了已获专利的Pulse-on-pulse 和Power Mode模式,利用Pulse-on-Pulse模式能产生类 似TIG焊的焊缝外观;利用Power Mode模式在低电流焊 接时仍能获得稳定的电弧。
[2]
四驱动滚轮 分开的焊丝导向装置 铜连接器
4驱动滚轮系统
Power Feed 10M
近观
主要调节装置
按下选择程序
单头机座Power Feed™ 10M送丝机中提到的双重程 序/记忆面板选配件。 双重程序/记忆面板在双头机座Power Feed™ 10M送 丝机中是标准配件,在单头机座Power Feed™ 10M 送丝机中是选配件。该面板具有三个功能:焊接方法
当用MIG焊接方法焊接铝时,Pulse-on-pulse利用改变脉冲波形形状的 次序获得类似TIG焊接焊缝外形和极佳的焊缝性能。Pulse-on-pulse同 时控制弧长和热输入,因此很容易获得良好的熔深。
更多信息请看Nextweld文献#NX-2.10
Pulse-on-pulse应用在3mm铝焊接中
高速: 0.6~1.6 0.9~2.0
低速: 0.6~2.4 0.9~3.0
外形尺寸 高x宽x深
(mm)
净重 (kg)
470X343X775 28.1
508X504X781 40.8
样本 8/04
MSP4操作界面面板
新的MSP4操作界面面板能够对模式选择、 电弧控制、焊接顺序和通过红外(IR)端 口进行锁定限制控制。
CO2 Ar (MIX) Ar (MIX) Ar (MIX) CO2, Ar/CO 2 CO2, Ar/CO 2
0.030 0.035 0.045 0.052
---
10 20 24
94 11 21 25
95 12 22 26
---
14 19 28
109 109 125 125
110 110 126 126
中提供极好的保护。 ● 零部件在保修期内提供保修。 ● 制造符合ISO9001质保体系和ISO14001环保标准。
[3]
Power Feed 10M
近观
什么是NEXTWELD ? NEXTWELD是林肯的技术、程序与产品一体化,构成一个全面的、灵活的、容易应用的焊接体系,从而 提高效率和减少生产成本,波形控制技术和数字通讯为NEXTWELD的创新技术的应用例如Pulse-on-pulse、 Power mode、STT和Arclink技术等奠定了基础。用NEXTWELD以获得理想的电弧控制、高效率/可靠性和 完整的综合体系。
波形控制技术 驾驭优良的焊接性能 林肯的波形控制技术控制和决定了输出波形(或焊接方式),使它适合所有的 应用场合、材料和焊接位置。此外,你可以让我们的应用工程部门为您增加或 定制标准的波形程序,或者应用林肯的波形设计软件自己建立或定制波形程序。
更多信息请看Nextweld文献#NX-1.10
林肯Nextweld的创新方法 采用Power Feed 10M送丝机和Power Wave焊接电源进行焊接时,应用波形控制技术可获得林肯创新方法所带来的优点。
● 通过在操作者附近安置控制装置调节焊接过程和送丝机 的参数,提高工作效率。
● 装有大数字显示屏幕的操作面板使人一目了然,方便设 置焊接参数。
● 具有推拉功能,在焊接铝时能产生优良的性能。 ● 零部件保修期内提供保修。
输出
输入
焊丝盘支架,MSP4面板,与Arclink/Linc-net调节装置和电 源电缆组装在一起的8英尺输入电缆,高速传动齿轮,焊枪 连接电缆。
ALUMINUM
0.035 3/64
GMAW
Ar 148 71
4043 PULSE
Ar 149 72
PULSE-ON-PULSE Ar 98 99
1/16
0.035 3/64 1/16
73
GMAW
Ar 151 75 77
74 5356 PULSE
Ar 152 76 78
100
PULSE-ON-PULSE Ar 101 102 103
产品名称
订货号 输入电源 额定输出 送丝速度范围 电流/暂载率 (米/分钟)
焊丝尺寸范围 (米/分钟) 实芯 药芯
Power Feed™ 10M 送丝机(单头机座)
K2230-1
Power Feed™ 10M 送丝机(双头机座) K2234-1
40伏直流
600安/60% 500安/100%
高速:2.0~30.5 低速:1.27~20.3
● Arclink™——用于焊接的领先的数字通讯协议,使该送 丝机与电源连接后成为完整的、严格时间控制的综合体 系的最佳选择。
● 在许多焊接应用中,可调用预置的电压值进行同步恒压 MIG焊接。也可根据需要进行必要的调整。
● 脉冲MIG焊——低飞溅、低热量输入以及适合全位置焊 接——使任何一个操作者都能成为一个更加出色的焊工。
STAINLESS
GMAW GMAW PULSE PULSE PULSE STT STT II
Ar (Mix) Ar/He/CO2
Ar/CO2 Ar/O2 Ar/He/CO2 Ar/He/CO2 Ar/He/CO2
0.030 0.035 0.045 61 31 41
63 33 43
66 36 46
62 32 42
在Power Wave 焊接电源 中,焊接模式提供进入多 种焊接波形程序的简单通 路。
电弧调节装置就是大家所 知的电弧电感调节或波形 控制。在大多数焊接模式 中,它允许操作者调整电 弧特性从“软”到“硬”之间 变化 。
一目了然的大数字显示屏
启动选配件 可以设置提前供气时间、 送丝速度、开启时间
收弧选配件 可以设置收弧时间、回烧 时间和滞后供气时间。
红外端口(IR) 利用掌上电脑操作系统进行无线机器配置以 及错误诊断,不需要任何线缆连接。 我们的Palm操作系统应用软件使林肯的装有 红外端口的机器具有特定形式并能进行故障 检验。 对“Lock out”操作员权限进行自定义设置或者 限制进入设置的通路,以保护系统、校准行 为和保证提供可靠的结果。
Power Feed™ 10M
当您需要一种通用的、多功能的工业送丝机焊接多种 材料时,Power Feed™ 10M送丝机正好可以满足您的需求。 Power Feed™ 10M送丝机可用在汽车制造、造船、压力容 器/厚钢板、石油、气体和管道建筑行业中,尤其是对工件 质量要求极高的情况下。新的MSP4操作界面面板特点是 自动配置Palm操作系统界面的红外端口,可实现控制装置 与焊接系统之间的无线连接,快速、方便、过程控制精确。
23 4 5 6
质量和可靠性 ● 坚固的钢铁外壳,精确耐用的控制器,优良的仪表显示器。 ● 适合操作的环境温度范围(-10℃~+40℃)和适合储藏的温
度范围(-40℃~+40℃)。 ● 抗电子干扰设计。 ● 符合CSA/CE标准:C22.2No60,UL551,EN60974-5,
EN50199。 ● 满足IP21S等级。 ● PC板是板状封闭的,用环氧树脂粘合,在恶劣的工作环境
---
34 44
109 109 125
110 110 126
METAL CORE
0.045 0.052 1/16
GMAW Ar/CO2 81 83 85
PULSE Ar/CO2 82
84
86
M 20240 VM
焊接波形程序列表,方便地印制在Power Feed™ 10M送丝机的控制箱面板上,使标准的波形程序 选择更加容易。Power FeedTM 10M送丝机内置大量的预设焊接波形程序,适用于多种材料的焊接 (包括铁、不锈钢、铝、镍基合金和硅青铜),并能实现良好的电弧控制。针对其它的一些材料、 接头形式、焊接方法、保护气体或者其它方面的变化,有些顾客需要一些相应的解决方案,林肯电 气能为这些客户添加或者设计相应的波形程序。此外,林肯的波形设计软件,允许你根据自己的需 要建立和定制相应的波形程序。
Arclink/Linc-net加长控制电缆,焊接电源电缆,同轴焊接电 源电缆,送丝机焊枪连接座,送丝轮和送丝导管组件,Magnum 焊枪和电缆组件,推拉焊枪,推拉焊枪连接组件,双重程序 开关,Arclink“T”型连接器组件,脚踏电流控制开关连接器组 件,焊丝校直器,锭子适配器,转子适配器,线圈适配器, 焊丝保护套,适合林肯焊丝导入的引入套筒,气流调整器, 供水线路组件,Magnum流动传感器,支撑小脚轮组件—— 轻载荷,6000系列焊机悬臂。
GENERAL
GMAW STD. CV
5
CV GMAW POWER MODE
40
FCAW STD. CV
6
STICK SOFT (7018)
1
STICK CRISP (6010)
2
CC
TIG TOUCH START 3
GOUGE
---
9
STEEL
GMAW GMAW PULSE (CRISP) PULSE (SOFT) STT (NO TAILOUT) STT II