薄壁圆管件端部缺口及孔的冲裁模设计
冲裁及冲裁模设计
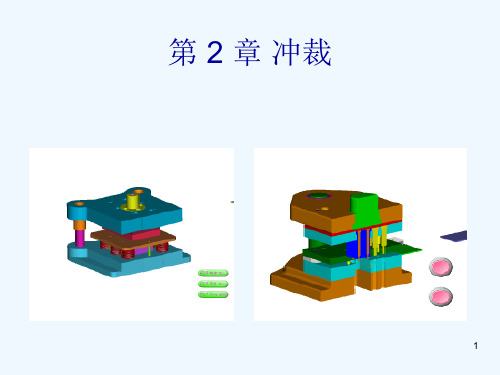
第 2 章 冲裁
2 -2 冲裁模具间隙
2.2.1 间隙对冲裁件质量的影响
冲裁件的质量:断面质量、尺寸精度 a 间隙对断面质量的影响 小间隙、合理间隙、大间隙情况下的剪切过程 断面特征值与间隙的关系图。
17
第 2 章 冲裁
2-2 冲裁模间隙
间隙对断面质量的影响
18
第 2 章 力、变形和冲裁件正常的断面状况 a)冲孔件 b)落料件
第 2 章 冲裁
2 -2 冲裁模具间隙
间隙的概念 模具凸凹模刃口缝隙间的距离。 单边间隙c、双边间隙z。 间隙对冲裁件的质量、模具寿命、冲裁力都有很大 的影响,是冲裁工艺和模具设计中的最重要的工艺参数。 2.2.1 间隙对冲裁件质量的影响 2.2.2 间隙对冲裁力的影响 2.2.3 间隙对模具寿命的影响 2.2.4 间隙的确定
12
第 2 章 冲裁
2-1 冲裁变形机理
2.1.5 断面特征
1)圆角带:冲裁过程中,纤维的弯曲与拉伸形成, 软材料圆角大。 2)光亮带:塑剪变形时,由于相对移动,凸凹模侧 压力将毛料压平形成的光亮垂直断面。
3)断裂带:刃口微裂纹受拉应力不断扩展形成的撕 裂面,导致断面粗糙并有斜度。 4)毛刺:由微裂纹位置与冲裁间隙等引起,是金属 拉断而形成的金属刺残留在冲裁件上
板 坯
F v 1
F v 2
F h 2
F h 2
F v 2
凹 模
板坯受力简图 Diagram of sheet metal under load
10
第 2 章 冲裁
2-1 冲裁变形机理
2.1.3 裂纹的形成与发展 裂纹产生的条件:当变形区的应变达到极限塑性应变值时, 就产生微裂纹 裂纹扩展的方向:沿着最大剪切应变速度的方向扩展 裂纹的成长过程:裂纹首先在低应力区产生,由于变形过 程中最大剪切应变的速度方向发生变化,使得新的裂纹不断产 生,旧裂纹的扩展不断停止,然后在旧裂纹的前端附近重新产 生新的裂纹,不断产生的微裂纹的根部汇成了一条主裂纹 极限塑性应变值除和材质外,还和应力状态、变形历史(损 伤程度)有关。
圆形板件冲孔模设计说明书
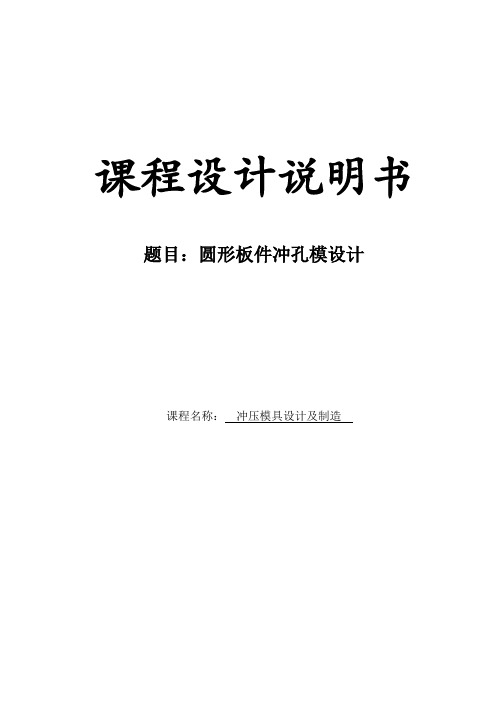
课程设计说明书题目:圆形板件冲孔模设计课程名称:冲压模具设计及制造目录一、课程设计目的 (1)二、工件简图 (2)三、工艺分析 (2)3.1工件材料 (2)2.2工件结构形状 (2)2.3工件尺寸精度 (3)2.4工艺方案选择 (3)四、工艺计算 (5)4.1冲裁力的计算 (5)4.2工作零件刃口尺寸计算 (5)4.3凹模结构厚度H计算 (6)4.4选定标准模架 (7)4.5凸模长度计算 (7)4.6橡胶计算 (7)五、设备选择 (8)六、装配图及零件图绘制 (8)七、参考文献 (9)一、课程设计目的冲压工艺设计主要包括冲压件的工艺性分析和冲压工艺方案的确定两个方面的内容。
良好的工艺性和合理的工艺方案,可以用最小的材料消耗,最少的工序数量和工时,稳定地获得符合要求的优质产品,并使模具结构简单,模具寿命高,因而可以减少劳动量和冲裁成本。
冲裁件的工艺性是指冲裁件对冲裁工艺的适应性,一般情况下,对冲裁件工艺性影响较大的是制件的结构形状、精度要求、形位公差及技术要求等。
冲压件的工艺性合理与否,影响到冲压件的质量、模具寿命、材料消耗、生产效率等,设计中应尽可能提高其工艺性。
课程设计是将大学课本上所学的课程知识、理论联系实际,提高分析、解决问题的能力的一种形式。
通过对具体产品的分析、计算,设计出一套合理的模具,使我们对于模具设计的理念更加深刻,也巩固了课上所学的专业知识,对以后工作奠定了基础,工艺与模具设计能力是材料成型及控制工程专业学生所必备的工程技术能力。
课程设计是教学大纲的必修课,也是锻炼学生加强工艺与模具设计能力的的重要教学环节。
二、工件简图材料为Q235钢,板厚为t=1.5mm,生产批量:大批量。
三、工艺分析3.1工件材料由图分析知:Q235为钢优质金属材料,具有良好的塑性,及压力加工性能。
适合冲裁加工。
3.2工件结构形状工件结构形状相对简单,只有一个圆孔。
料厚为1.5mm满足许用壁厚要求(孔与孔之间、孔与边缘之间的壁厚),可以冲裁加工。
冲裁模具设计方案
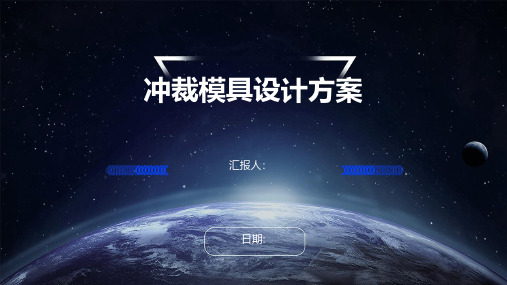
凹模定位板01020304夹板紧固螺栓顶杆弹簧分析图纸选择模具类型设计模具结构030201选择材料和热处理工艺进行试模粗加工热处理备料精加工抛光总装试模冲裁适用于加工各种形状的薄板零件,具有加工精度高、生产效率高、成本低等优点。
但冲裁过程中会产生废料,模具磨损也较快。
冲裁原理及工艺特点工艺特点冲裁原理间隙选择间隙计算冲裁间隙的选择与计算排样设计搭边值选择冲裁件的排样与搭边确定模具类型模具结构形式模具类型与结构形式根据产品形状和尺寸,设计凸模的结构和尺寸,考虑凸模强度、刚度和使用寿命。
凹模设计根据产品形状和尺寸,设计凹模的结构和尺寸,考虑凹模的加工精度和使用寿命。
根据产品要求,设计定位销的结构和尺寸,确保定位销能够准确固定产品位置。
挡料装置设计根据产品要求,设计挡料装置的结构和尺寸,确保挡料装置能够准确控制产品送料位置。
定位销设计VS模具的夹持与固定装置夹持器设计固定座设计模具材料选择模具结构设计模具强度计算模具强度校核模具刚度定义根据冲裁件的材料、厚度和精度要求,确定模具的刚度要求。
模具刚度校核标准模具刚度优化模具刚度校核03模具稳定性优化01模具稳定性定义02模具稳定性校核标准模具的稳定性分析为保证模具的使用寿命,需要选择具有足够硬度的材料,以便抵抗磨损和保持其形状。
模具材料的硬度模具材料的韧性模具材料的抗疲劳性模具材料的耐腐蚀性为了使模具能够承受冲击和弯曲,需要选择具有足够韧性的材料。
由于模具在长期使用中会受到循环应力的作用,因此需要选择具有较好抗疲劳性能的材料。
对于需要接触腐蚀性材料的模具,应选择具有较好耐腐蚀性的材料。
模具材料的选择原则碳素工具钢低合金工具钢高碳高铬工具钢不锈钢常用模具材料及其特性退火淬火正火回火01030204模具材料的热处理工艺复杂零件的冲裁模具设计通常适用于生产批量较大、对精度要求较高的场合。
在设计时,需考虑以下因素1. 材料:选择适合冲裁的材料,如不锈钢、高强度钢等。
薄壁零件冲床机构设计(公式WORD手写)

一、 设计任务书1、 设计题目:薄壁零件冲床的设计2、 设计背景:(1) 工作原理: 薄壁零件冲床的组成框图如图1所示。
图1 薄壁零件冲床的组成框图工作原理如图2a 所示。
在冲制薄壁零件时,上模(冲头)以较大的速度接近坯料,然后以匀速进行拉延成形工作,接着上模继续下行将成品推出型腔,最后快速返回。
上模退出下模后,送料机构从侧面将坯料送至待加工位置,完成一个工作循环。
图2 薄壁零件冲制工作原理图(2) 设计条件与要求 动力源为电动机,上模做上下往复直线运动,其大致运动规律如图2b 所示,要求有快速下沉、匀速工作进给和快速返回的特征。
上模工作段的长度L=40~100mm,对应曲柄转角φ=60º~90º;上模行程长度必须大于工作段长度的两倍以上,行程速比系数K ≥1.5。
上模到达工作段之前,送料机构已将坯料送至待加工位置(下模上方),如图2a 所示。
送料距离L=60~250mm 。
要求机构具有良好的传力特性,特别是工作段的压力角α应尽可能小,一般取许用压力角[α]=50º。
生产率为每分钟70件。
按平均功率选用电动机。
需要5台冲床。
室内工作,载荷有轻微冲击,动力源为三相交流电动机。
使传动装置原动机薄壁零件冲制执行系统(3)执行机构的选择工作机应采用往复移动机构。
可选择的有:连杆机构、凸轮机构、齿轮齿条机构、螺旋机构。
本设计是要将旋转运动转换为往复运动,所以连杆机构、凸轮机构、齿轮齿条机构均可,凸轮机构能够较容易获得理想的运动规律,而齿轮齿条机构加工复杂、成本高,所以不采用。
同时由于不考虑送料机构,同时考虑到凸轮尺寸以及运动规律实现的可行性,结合前辈的经验和自己的思考,最终决定一种方案。
简图如下:1>改进方案2> 传统方案(4) 方案评价传统方案和改进方案都满足设计要求,但是和传统方案相比,改进方案中由于利用的杠杆原理,工件端传递力矩和运动规律更简单的通过两平行杠杆传递到传动机构端,同时压力角更易计算,而且传动更平稳。
如何设计一套圆管双头冲孔与翻孔模具
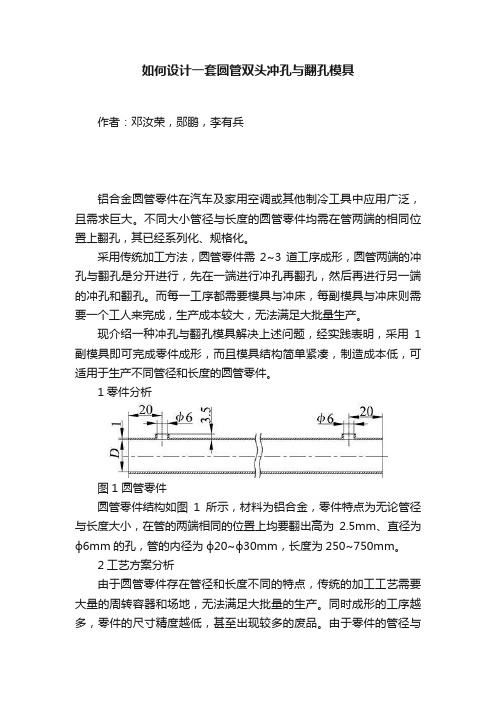
如何设计一套圆管双头冲孔与翻孔模具作者:邓汝荣,郧鹏,李有兵铝合金圆管零件在汽车及家用空调或其他制冷工具中应用广泛,且需求巨大。
不同大小管径与长度的圆管零件均需在管两端的相同位置上翻孔,其已经系列化、规格化。
采用传统加工方法,圆管零件需2~3道工序成形,圆管两端的冲孔与翻孔是分开进行,先在一端进行冲孔再翻孔,然后再进行另一端的冲孔和翻孔。
而每一工序都需要模具与冲床,每副模具与冲床则需要一个工人来完成,生产成本较大,无法满足大批量生产。
现介绍一种冲孔与翻孔模具解决上述问题,经实践表明,采用1副模具即可完成零件成形,而且模具结构简单紧凑,制造成本低,可适用于生产不同管径和长度的圆管零件。
1零件分析图1 圆管零件圆管零件结构如图1所示,材料为铝合金,零件特点为无论管径与长度大小,在管的两端相同的位置上均要翻出高为2.5mm、直径为ϕ6mm的孔,管的内径为ϕ20~ϕ30mm,长度为250~750mm。
2工艺方案分析由于圆管零件存在管径和长度不同的特点,传统的加工工艺需要大量的周转容器和场地,无法满足大批量的生产。
同时成形的工序越多,零件的尺寸精度越低,甚至出现较多的废品。
由于零件的管径与长度不同,需要不同的模具与之相适应,模具通用性低、互换性差,需要的模具数量多,生产成本大,不便于管理。
面对零件批量大、劳动力成本不断上涨的市场环境,传统的加工方法已不适应当前生产。
通过对不同的管径和长度系列的模具进行优化后,采用1副模具则可生产任何规格的圆管零件,大幅度减少了模具制造成本,提高了生产效率,并提高了零件的成形尺寸精度。
3成形过程与工作原理图2 模具结构1.连接螺母2.推板3.限位安全块4.压板5.上模板6.模柄7.凸模固定板8.冲孔凸模9.上卸料板 10.导柱导套 11.导向杆 12.右导向杆支承块 13.螺钉 14.限位块 15.底座 16.锁紧块 17.凸凹模固定板 18.下卸料板 19.弹簧 20.螺钉 21.螺钉 22.弹簧 23.托料板 24.螺钉 25.下模板 26.凸凹模 27.气缸 28.左导向杆支承块 29.螺钉 30.调节块 31.弹簧1模具结构如图2所示。
冲裁模的结构设计(doc 7页)
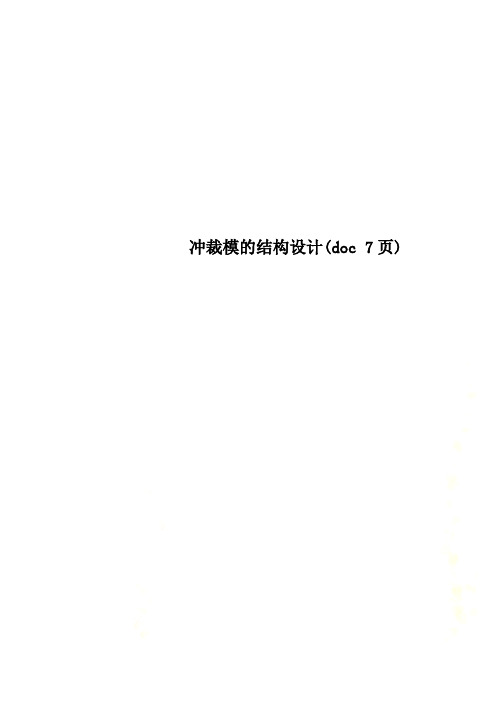
冲裁模的结构设计(doc 7页)冲裁模的结构设计冲裁模是冲裁工序所用的模具。
冲裁模的结构型式很多,为研究方便,对冲裁模可按不同的特征进行分类。
1.按工序性质可分为落料模、冲孔模、切断模、切口模、切边模、剖切模等;2.按工序组合方式可分为单工序模、复合模和级进模;3.按上、下模的导向方式可分为无导向的开式模和有导向的导板模、导柱模、导筒模等。
4.按凸、凹模的材料可分为硬质合金冲模、钢皮冲模、锌基合金冲模、聚氨脂冲模等;5.按凸、凹模的结构和布置方法可分为整体模和镶拼模,正装模和倒装模。
6.按自动化程度可分为手工操作模、半自动模、自动模。
分类的方法还比较多,上述的各种分类方法从不同的角度反映了模具结构的不同特点。
下面以工序组合方式,分别分析各类冲裁模的结构及其特点。
单工序冲裁模单工序冲裁模指在压力机一次行程内只完成一个冲压工序的冲裁模,如落料模、冲孔模、切断模、切口模、切边模等。
(一)落料模落料模常见有三种形式:1.无导向的敞开式落料模,其特点是上、下模无导向,结构简单,制造容易,冲裁间隙由冲床滑块的导向精度决定。
可用边角余料冲裁。
常用于料厚而精度要求低的小批量冲件的生产。
2.导板式落料模,是将凸模与导板间(又是固定卸料板)选用H7/h6的间隙配合,且该间隙小于冲裁间隙。
回程时不允许凸模离开导板,以保证对凸模的导向作用。
它与敞开式模相比,精度较高,模具寿命长,但制造要复杂一些常用于料厚大于 0.3mm 的简单冲压件(图1)。
图 4 超短凸模的小孔冲模复合冲裁模图 5 复合模的基本结构在压力机的一次工作行程中,在模具同一部位同时完成数道冲压工序的模具,称为复合冲裁模。
复合模的设计难点是如何在同一工作位置上合理地布置好几对凸、凹模。
图 5是落料冲孔复合模的基本结构。
在模具的一方是落料凹模,中间装着冲孔凸模;而另一方是凸凹模,外形是落料的凸模,内孔是冲孔的凹模。
若落料凹模装在上模上,称为倒装复合模;反之,称为顺装复合模。
冲裁模(冲压模具)课程设计说明书
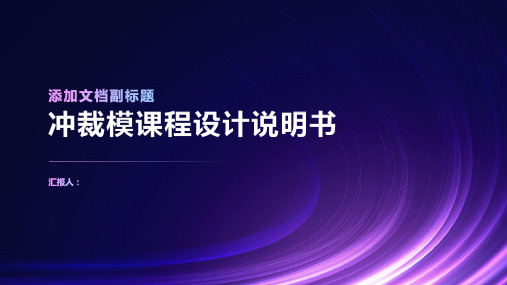
模具设计的具体步骤
确定冲裁模的类型和尺寸 设计冲裁模的轮廓和结构 确定冲裁模的冲压力和冲压速度
设计冲裁模的模具材料和热处理工艺 设计冲裁模的冷却系统和润滑系统 设计冲裁模的模具寿命和维护保养方法
冲裁模的制造工艺
冲裁模的设计:根据产品要求进行设计,包括尺寸、形状、材料等 冲裁模的制造:采用数控机床进行加工,保证精度和效率 冲裁模的装配:将各个部件组装成完整的冲裁模 冲裁模的调试:在装配完成后进行调试,确保其性能和精度达到要求
采用环保材料和工艺, 减少对环境的影响
提高冲裁模的自动化 程度,降低人工成本
提高模具寿命的方法和途径
优化模具设计: 合理选择材料、 结构、尺寸等, 提高模具的强度 和耐磨性
提高加工精度: 采用先进的加工 技术和设备,提 高模具的加工精 度,减少误差
加强维护保养: 定期检查、清洗、 润滑模具,及时 发现并处理模具 的磨损和损坏
冲裁模的使用和维护
冲裁模的使用 步骤:安装、 调试、运行、
停机
冲裁模的维护 方法:定期检 查、清洁、润 滑、更换易损
件
冲裁模的安全 操作:遵守操 作规程,注意
安全防护
冲裁模的常见 故障及处理方 法:如卡模、 漏油、噪音等, 需及时处理, 确保生产安全
常见问题的处理和解决方法
冲裁模调试过程中, 如果出现模具损坏, 应及时更换或修复。
设计前的准备工作
确定冲裁模的用途和功能 收集冲裁模的设计要求和技术参数 确定冲裁模的材料和尺寸 准备冲裁模的设计图纸和工具
模具设计的基本流程
确定冲裁 模的设计 要求
设计冲裁 模的尺寸 和形状
确定冲裁 模的材料 和加工工 艺
设计冲裁 模的装配 和调试方 法
薄壁圆管方孔冲模设计

《模具工业》 !""# $ % & $ ! 总 !’"
薄 壁 圆 管 方 孔 冲 模 设 计
南京工业职业技术学院 ( 江苏南京 !#""#) * 匡余华 + 摘要 , 介绍了薄壁圆管的一种冲孔方法, 还介绍了这种方法的模具结构特点和设计要点。 关键词 圆管 浮动模芯 凹模 凸模
! !"#$%&’$ " # $%&’()*’+,*-. /’0$%1 2%+ +%3-1 0$*-(45&& )*)’6 456 *-0+%13,’1 7 #-1 0$’ 60+3,03+’ ,$5+5,0’+*60*,6 5-1 /5*- 1’6*.- )%*-06 %2 0$’ 1*’ *- 0$*6 /’0$%1 4’+’ 6050’1 7 ()* +,%-# +%3-1 )*)’ 8 2&%50*-. ,%+’ 8 /50+*9 8 )3-,$
图! # $ 支承板 ( $ 导柱
模具结构 , $ 弹簧 + $ 凸模 ’ $ 定位套 ) $ 模芯 图, 凸 模
!、 * $ 卸料板 - $ 凹模
,
模具结构特点 . # / 模芯采用浮动结构,有效地解决了一般圆
. ’ / 弹簧的选择。由于凸模的行程大, 弹簧的压 缩量大于 ,";; , 故在选择弹簧时应注意。 . ( / 装配要求。该模具相对运动零件较多, 装配 时要注意相互间的位置关系,如模芯在滑动时与凸 模的垂直度要求。 . - / 该模具的工作行程较大, 在选择冲床时应注 意冲裁力不超过机床的压力曲线冲裁力, 减少了空 心圆管冲裁变形。 ’ 模具设计要点
冲裁模设计过程
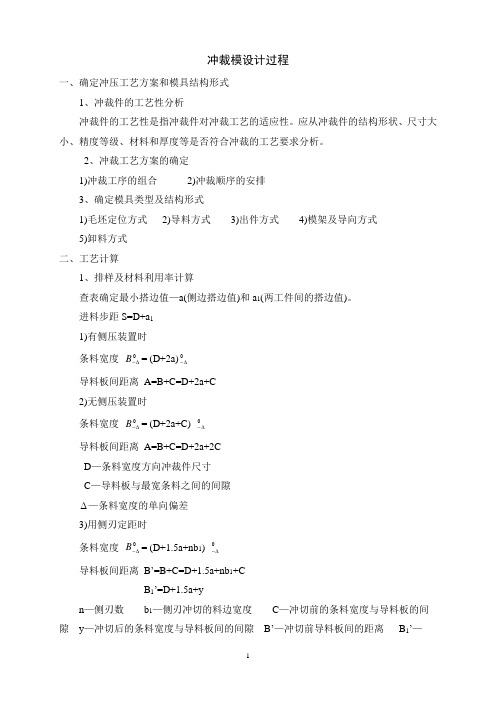
冲裁模设计过程一、确定冲压工艺方案和模具结构形式1、冲裁件的工艺性分析冲裁件的工艺性是指冲裁件对冲裁工艺的适应性。
应从冲裁件的结构形状、尺寸大小、精度等级、材料和厚度等是否符合冲裁的工艺要求分析。
2、冲裁工艺方案的确定1)冲裁工序的组合 2)冲裁顺序的安排3、确定模具类型及结构形式1)毛坯定位方式 2)导料方式 3)出件方式 4)模架及导向方式5)卸料方式二、工艺计算1、排样及材料利用率计算查表确定最小搭边值—a(侧边搭边值)和a 1(两工件间的搭边值)。
进料步距S=D+a 11)有侧压装置时条料宽度 0∆-B = (D+2a)0∆-导料板间距离 A=B+C=D+2a+C2)无侧压装置时条料宽度 0∆-B = (D+2a+C) 0∆-导料板间距离 A=B+C=D+2a+2CD —条料宽度方向冲裁件尺寸C —导料板与最宽条料之间的间隙∆—条料宽度的单向偏差3)用侧刃定距时条料宽度 0∆-B = (D+1.5a+nb 1) 0∆-导料板间距离 B ’=B+C=D+1.5a+nb 1+CB 1’=D+1.5a+yn —侧刃数 b 1—侧刃冲切的料边宽度 C —冲切前的条料宽度与导料板的间隙 y —冲切后的条料宽度与导料板间的间隙 B ’—冲切前导料板间的距离 B 1’—冲切后导料板间的距离计算材料利用率 η=0A A ⨯100% A 0—一个步距的条料面积 A —制件的总面积画出排样图。
2、冲裁模刃口尺寸计算查表知凸凹模的最大间隙Z max 和最小间隙Z min计算Z max -Z min 的值查公差表确定工件的尺寸公差∆,确定x 的值(注:工件尺寸公差与冲模刃口尺寸的制造偏差原则上都应按“入体”原则标注为单向公差,但对于磨损后无变化的尺寸,一般标注双向偏差)1)按凸模与凹模图样分别加工法落料 以凹模为基准,间隙取在凸模上。
D A =(D max -x ∆)A δ+0D T =( D A -Z min )0T δ-= (D max -x ∆- Z min ) 0T δ-(T δ、A δ—凸、凹模制造公差)校核:|A δ|+|T δ|≤Z max -Z min 若不能满足间隙公差条件,则取:T δ≤0.4 (Z max -Z min ) A δ≤0.6(Z max -Z min )冲孔 以凸模为基准,间隙取在凹模上d T =(d min + x ∆)0T δ-d A ==( d T +Z min ) A δ+0=(d min + x ∆+Z min ) A δ+0校核:|A δ|+|T δ|≤Z max -Z min 若不能满足间隙公差条件,则取:T δ≤0.4 (Z max -Z min ) A δ≤0.6(Z max -Z min )孔心距:L d =L±81∆ 2)凸模与凹模配作法对于冲制薄材料的冲模,或冲制复杂形状工件的冲模,或单件生产的冲模,常常采用凸模与凹模配作的加工方法。
薄壁圆管冲孔模具设计

薄壁圆管冲孔模具设计1薄壁圆管冲孔模具设计初步构思按工艺流程先冲压翻边孔,并以翻边孔内插入定位销定位保证翻边孔和圆孔两孔间的中心距及角度尺寸公差。
在薄壁圆管圆弧外壁上冲孔,凸、凹模接触的零件工作面是圆弧面,因此凹模只能设计在圆管内腔,所以将凹模设计成镶嵌在仿形圆管内腔的芯棒上,刃口部位圆弧与芯棒外径圆弧重合,芯棒外径与圆管内径间隙单边0.2mm,方便装、卸工件;由于管壳将凹模包在圆管内,所以冲孔的落料只能在取下工件后排出;在取下工件前落料需在芯棒落料孔内暂时存放;上述是冲孔模具结构的初步构思,具体的模具零件结构、尺寸公差、零件的加工工艺性及装配工艺性还需从模具整体细致的设计。
构思冲压步骤:上料装卡管壳,将冲压完翻边孔的半成品管壳,插入芯棒,翻边孔端向外,将定位销插入翻边孔及芯棒定位孔,工件固定;凸模下行至冲压行程下限,冲孔完成;落料停留在芯棒落料孔内;凸模回程至行程上限,拔出定位销,取下工件,落料从落料孔排出。
2薄壁圆管冲孔模具设计分析按上述模具构思详细分析后进行冲孔模具零件的细节设计2.1凹模设计凹模设计成镶嵌在仿形圆管内腔的芯棒上;因此凹模外径Ф26±0.01mm与芯棒Ф26孔按过度配合设计;Ф14.1(0,-0.02)mm尺寸为凹模刃口,Ф15mm沉孔为冲压落料孔;R25.8mm 圆弧与芯棒外径圆弧一致,可采用将凹模镶嵌入芯棒后磨削芯棒外圆至凹模与芯棒圆弧完全重合;凹模刃口磨损后可通过底部多次增加垫片重新磨削开刃来增加凹模使用寿命。
2.2芯棒设计工件装卡胎具:芯棒外径Ф51.6mm按管壳内径尺寸间隙单边0.2mm设计,方便装、卸工件;芯棒根部50mm长度设计外径Ф52±0.01mm与底座Ф52mm圆孔过渡配合,防止冲压过程中芯棒前后窜动导致凸模及凹模报废;镶嵌固定凹模:Ф26±0.01mm沉孔为凹模镶嵌孔,与凹模外径按过渡配合装配;Ф16mm孔为冲压落料孔,暂时存放冲压圆孔的落料;60±0.01mm 尺寸扁与底座沉台外形过渡配合,避免芯棒在冲压过程中发生转动导致凸模及凹模报废;定位销孔定位管壳工件,Ф12mm销孔为定位管壳翻边孔的定位销孔,管壳插入芯棒后翻边孔与销孔对正,插入定位销,工件固定。
薄壁圆管端部豁口冲压模具设计
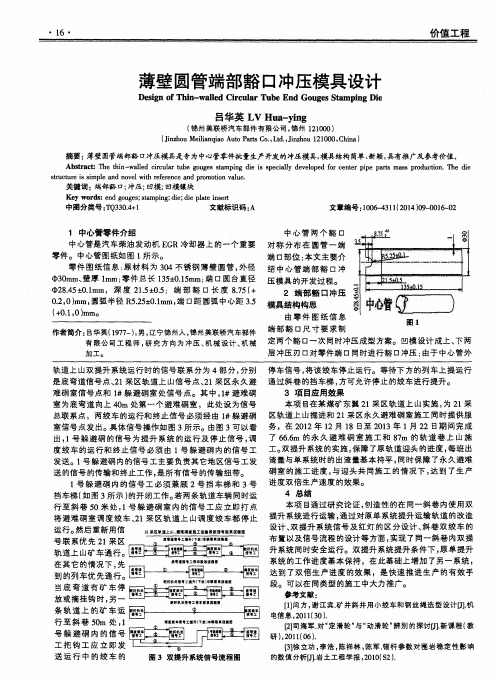
通过对原单系统提升运输轨道 的改造 将避难 硐室调 度绞 车、 2 1 采 区轨道 上 山调 度绞 车都 停止 提升 系统进行运输 , 设计 、 双提升 系统信号及 红灯的 区分设计、 斜巷 双绞车 的 运行。 然后重新用信 2 l 采 区 轨 道 上 山 、 避 堆 硐 童 施 工 运 输 舅 l 统 信 号 联 系 流 程 田 布 置以及信号 流程 的设计 等方面 , 实现 了同一斜巷 内双提 升系统 同时安 全运行 。双提升 系统提升条件下 , 原 单提升 系统的工作 进度基本保持 ,在 此基础上增加 了另一系统 , 达到 了双倍 生产进度 的效果 ,是 快速推进 生产 的有效手 段。可以在 同类型的施工中大力推广。
0 . 2 , 0 ) m m, 圆弧半径 R 5 . 2 5  ̄ 0 . 1 m m, 端 口距 圆弧 中心距 3 . 5 模具结构构思 ( + 0 . 1 , 0 ) m mo 由 零 件 图 纸 信 息 端 部豁 口尺寸 要 求制
作者简介 : 吕华英( 1 9 7 7 一 ) , 男, 辽宁锦州人 , 锦州美联桥汽 车部件
室为底弯道 向上 4 0 m 处第一个 避难硐 室 ,此处设 为信 号 总联系点 ,两绞 车的运行和终止信号 必须经 由 1 #躲避硐 室信号点发 出。具体信号操作如 图 3 所 示。由图 3可 以看 出, 1 号躲 避硐 的信号 为提 升系统 的运行 及停 止信号 , 调 度绞 车的运行和 终止信号 必须 由 1 号 躲避硐 内的信 号工
q ) 3 0 m m、 壁厚 l m m; 零件总长 1 3 5 + 0 . 1 5 r n m; 端 口 圆 台 直 径 压模具 的开发过程。 2 8 . 4 5 ± O . 1 m m,深 度 2 1 . 5 ± 0 . 5 :端 部 豁 口长 度 8 . 7 5( + 2 端 部豁 口冲压
圆管接头模具设计方案

圆管接头模具设计方案第一章绪论1.1课题研究背景介绍圆管接头是用于家用管道连接用塑料件,其需求量巨大,易清洁、耐磨、耐腐蚀老化、强度高、使用寿命长等特点。
选用材料为热塑性塑料pp,采用注射成型。
注射成型是将塑料经过料筒加热之后,通过注射机将熔融的塑料注射到具有一定形状的型腔之,而达到成型目的。
它具有成型周期短,能一次成型形状复杂、尺寸精度的塑料制品。
其生产率高,易实现自动化生产。
在设计过程中,我先对塑件的原材料进行分析,了解它的成型工艺性能、主要用途等,然后根据塑件的形状结构,结合pp 的性能,初步选取注射机。
本模具利用CAD 软件对模具进行计算分析,参考模具设计有关资料,最后选出了顶杆等装置,让模具在精度、可行性以及脱模等方面有了较为突出的优势。
设计当中,利用CAD软件进行辅助,不仅加快了模具设计的速度,更是让模具设计更为合理,并预先知道其可行性。
在多种模具结构中选取最优的一种[1]。
最后利用CAD绘图软件对模具的图纸进行清晰的表达,使模具结构让人一目了然。
通过计算与对模具结构的分析,分别设计出模具的成型零部件、浇注系统、推出机构、冷却系统等。
本模具通过计算与综合考虑,在节约模具成本、缩短生产周期、提高模具寿命、实现中批量生产等方面取得了较大的成就。
由于本人水平有限,模具设计与制造知识不够完善,所以设计中难免出现或多或少错误,在此希望读者在阅读时加以批评指正第二章拟定模具结构形式2.1确定型腔数量及排列方式2.1.1塑件成型工艺性分析该塑件是圆管接头,如下图所示,塑件壁厚属薄壁塑件,生产批量很大,材料为PP(收缩率在0.4%~0.8%围),在本设计中选用的收缩率为0.5 %。
成型工艺很好,可以注射成型[ 2]。
该产品主要用于圆管接头,要求表面光滑、无明显的浇口痕迹,故采用点式浇口。
如图1 所示:图 1 圆管接头2.1.2PP 材料分析PP 材料是一种由聚丙烯制的的热塑性塑料,具有良好综合力学性能。
冲裁工艺与模具设计-冲裁模设计步骤及实例
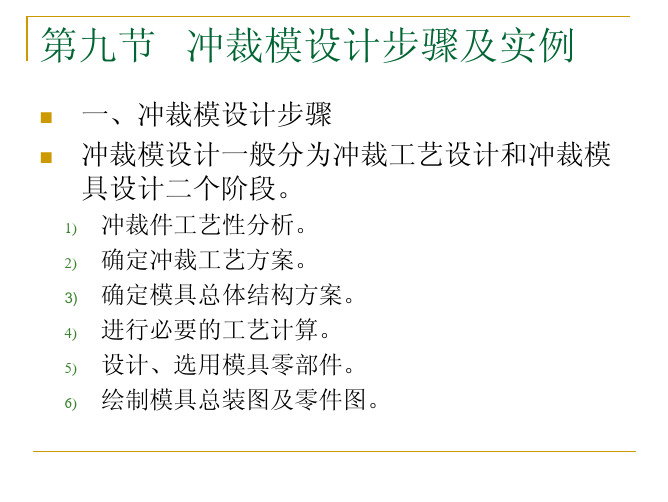
高模具寿命,建议将所有90°清角改为R=1的圆角。 3. 尺寸精度:零件图上所有尺寸均未标注公差,属自由尺寸,可
按IT14级确定工件尺寸的公差。经查公差表,各尺寸公差为: 58-0.74、38-0.62、30-0.52、16-0.44、14±0.22、17±0.22、
Ф3.5+0.3 结论:可以冲裁
《冲压工艺及模具设计》
第2(章1冲)裁模具工类艺型及冲裁模设计
模具类型主要是指单工序模、复合模、级进模三种。有些单件试 制或小批量生产的情况下,也采用简易模或组合模。
模具类型应根据生产批量、冲件形状与尺寸、冲件质量要求、材 料性质与厚度、冲压设备与制模条件、操作与安全等因素确定。
(2)操作与定位方式
△ ------条料下料时的下偏差值 C -------条料与导料板之间的间隙
《冲压工艺及模具设计》
第2章 冲裁工艺及冲裁模设计
表 2.5.3剪料公差△及条料与导料板之间隙δ(mm)
《冲压工艺及模具设计》
第2章 冲裁工艺及冲裁模设计
2.计算总冲压力 由于冲模采用刚性卸料装置和自然漏料方式,故
总的冲压力为: P总冲压力=P冲裁力+P推件力 P冲裁力=P1+P2 式中 P1--------落料时的冲裁力
《冲压工艺及模具设计》
第2章 冲裁工艺及冲裁模设计
薄壁圆管端部豁口冲压模具设计

薄壁圆管端部豁口冲压模具设计吕华英【摘要】The thin-walled circular tube gouges stamping die is specially developed for center pipe parts mass production. The die structure is simple and novel with reference and promotion value.%薄壁圆管端部豁口冲压模具是专为中心管零件批量生产开发的冲压模具,模具结构简单、新颖,具有推广及参考价值。
【期刊名称】《价值工程》【年(卷),期】2014(000)009【总页数】2页(P16-17)【关键词】端部豁口;冲压;凹模;凹模镶块【作者】吕华英【作者单位】锦州美联桥汽车部件有限公司,锦州121000【正文语种】中文【中图分类】TQ330.4+11 中心管零件介绍中心管是汽车柴油发动机EGR 冷却器上的一个重要零件。
中心管图纸如图1 所示。
零件图纸信息:原材料为304 不锈钢薄壁圆管,外径Ф30mm、壁厚1mm;零件总长135±0.15mm;端口圆台直径Ф28.45±0.1mm,深度21.5±0.5;端部豁口长度8.75(+0.2,0)mm,圆弧半径R5.25±0.1mm,端口距圆弧中心距3.5(+0.1,0)mm。
中心管两个豁口对称分布在圆管一端端口部位;本文主要介绍中心管端部豁口冲压模具的开发过程。
2 端部豁口冲压模具结构构思由零件图纸信息端部豁口尺寸要求制定两个豁口一次同时冲压成型方案。
凹模设计成上、下两层冲压刃口对零件端口同时进行豁口冲压;由于中心管外径为Ф30mm,凹模需设计成穿入管内径的悬臂式芯棒结构;凸模与凹模冲压刃口配对设计,也设计成上、下两层刃口;冲压过程中,上层豁口冲压落料需停留在凸模上、下两层刃口中间缺口处,含在凹模芯棒刃口型腔内,随着凸模向上排料动作排出;两个豁口一次同时冲压成型的方案增加了模具的设计难度,需采用特殊的模具结构才能够满足模具设计要求。
圆管接头模具设计

圆管接头模具设计⽬录前⾔ (2)⼀:塑件的⼯艺性分析 (3)1、塑件的分析 (3)2、PP的性能分析 (3)3 : PP的注射成型⼯艺及参数 (4)⼆: 拟定模具的结构形式 (4)1:分型⾯位置确定 (4)2: 型腔数量和排列⽅式的确定 (5)3: 注射机型号的确定 (5)三: 浇注系统的确定 (6)1: 主流道的设计 (6)2: 分流道的设计 (7)3:浇⼝的设计 (8)4: 校核主流道的剪切速率 (9)5: 冷料⽳的设计及计算 (9)四: 成型零件的结构设计及计算 (10)1: 成型零件的结构设计 (10)2: 成型零件钢材的使⽤ (10)3: 成型零件钢材的选⽤ (10)4:成型零件尺⼨及动模垫板厚度的计算 (12)五: 模架的设计 (13)1、各模板尺⼨的确定 (13)六:排⽓槽的设计 (13)七:脱模推出机构的设计 (13)1: 推出⽅式的确定 (14)2: 脱模⼒的计算 (14)3: 校核推出机构作⽤在塑件上的单位应变⼒ (14)⼋.冷却系统的设计 (15)1、冷却介质 (15)2、冷却系统的简单计算 (15)九、导向与定位结构的设计 (16)⼗、总装配图和零件的绘制 (16)前⾔:随着中国当前的经济形势的⾼速发展,在“实现中华民族的伟⼤复兴”⼝号的倡引下,中国的制造业也蓬勃发展;⽽模具技术已成为衡量⼀个国家制造业⽔平的重要标志之⼀,模具⼯业能促进⼯业产品⽣产的发展和质量提⾼,并能获得极⼤的经济效益,因⽽引起了各国的⾼度重视和赞赏。
在⽇本,模具被誉为“进⼊富裕的原动⼒”,德国则冠之为“⾦属加⼯业的帝王”,在罗马尼亚则更为直接:“模具就是黄⾦”。
可见模具⼯业在国民经济中重要地位。
我国对模具⼯业的发展也⼗分重视,早在1989年3⽉颁布的《关于当前国家产业政策要点的决定》中,就把模具技术的发展作为机械⾏业的⾸要任务。
近年来,塑料模具的产量和⽔平发展⼗分迅速,⾼效率、⾃动化、⼤型、长寿命、精密模具在模具产量中所战⽐例越来越⼤。
圆形零件侧壁冲孔模具结构设计
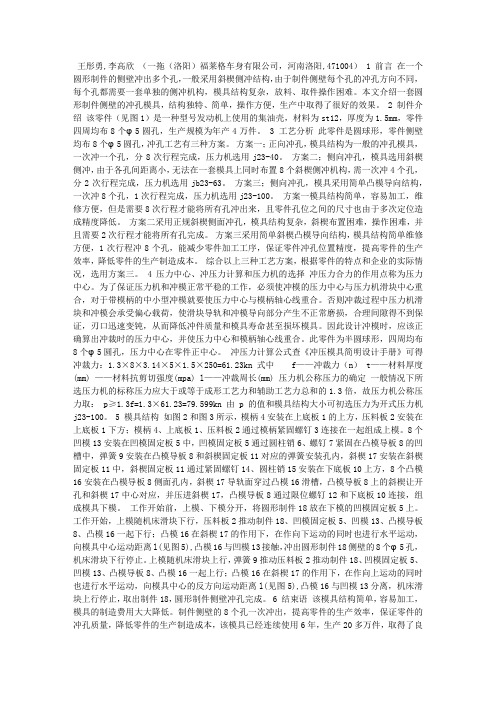
王彤勇,李高欣(一拖(洛阳)福莱格车身有限公司,河南洛阳,471004) 1 前言在一个圆形制件的侧壁冲出多个孔,一般采用斜楔侧冲结构,由于制件侧壁每个孔的冲孔方向不同,每个孔都需要一套单独的侧冲机构,模具结构复杂,放料、取件操作困难。
本文介绍一套圆形制件侧壁的冲孔模具,结构独特、简单,操作方便,生产中取得了很好的效果。
2 制件介绍该零件(见图1)是一种型号发动机上使用的集油壳,材料为st12,厚度为1.5mm,零件四周均布8个φ5圆孔,生产规模为年产4万件。
3 工艺分析此零件是圆球形,零件侧壁均布8个φ5圆孔,冲孔工艺有三种方案。
方案一;正向冲孔,模具结构为一般的冲孔模具,一次冲一个孔,分8次行程完成,压力机选用j23-40。
方案二;侧向冲孔,模具选用斜楔侧冲,由于各孔间距离小,无法在一套模具上同时布置8个斜楔侧冲机构,需一次冲4个孔,分2次行程完成,压力机选用jb23-63。
方案三;侧向冲孔,模具采用简单凸模导向结构,一次冲8个孔,1次行程完成,压力机选用j23-100。
方案一模具结构简单,容易加工,维修方便,但是需要8次行程才能将所有孔冲出来,且零件孔位之间的尺寸也由于多次定位造成精度降低。
方案二采用正规斜楔侧面冲孔,模具结构复杂,斜楔布置困难,操作困难,并且需要2次行程才能将所有孔完成。
方案三采用简单斜楔凸模导向结构,模具结构简单维修方便,1次行程冲8个孔,能减少零件加工工序,保证零件冲孔位置精度,提高零件的生产效率,降低零件的生产制造成本。
综合以上三种工艺方案,根据零件的特点和企业的实际情况,选用方案三。
4 压力中心、冲压力计算和压力机的选择冲压力合力的作用点称为压力中心。
为了保证压力机和冲模正常平稳的工作,必须使冲模的压力中心与压力机滑块中心重合,对于带模柄的中小型冲模就要使压力中心与模柄轴心线重合。
否则冲裁过程中压力机滑块和冲模会承受偏心载荷,使滑块导轨和冲模导向部分产生不正常磨损,合理间隙得不到保证,刃口迅速变钝,从而降低冲件质量和模具寿命甚至损坏模具。