FMEA案例
fmea案例
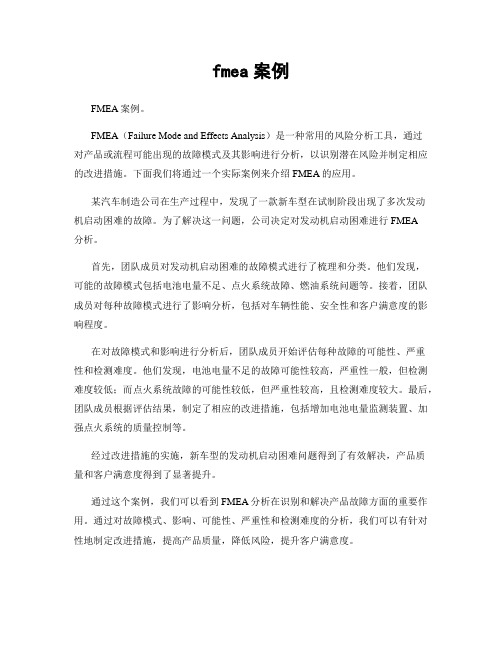
fmea案例FMEA案例。
FMEA(Failure Mode and Effects Analysis)是一种常用的风险分析工具,通过对产品或流程可能出现的故障模式及其影响进行分析,以识别潜在风险并制定相应的改进措施。
下面我们将通过一个实际案例来介绍FMEA的应用。
某汽车制造公司在生产过程中,发现了一款新车型在试制阶段出现了多次发动机启动困难的故障。
为了解决这一问题,公司决定对发动机启动困难进行FMEA分析。
首先,团队成员对发动机启动困难的故障模式进行了梳理和分类。
他们发现,可能的故障模式包括电池电量不足、点火系统故障、燃油系统问题等。
接着,团队成员对每种故障模式进行了影响分析,包括对车辆性能、安全性和客户满意度的影响程度。
在对故障模式和影响进行分析后,团队成员开始评估每种故障的可能性、严重性和检测难度。
他们发现,电池电量不足的故障可能性较高,严重性一般,但检测难度较低;而点火系统故障的可能性较低,但严重性较高,且检测难度较大。
最后,团队成员根据评估结果,制定了相应的改进措施,包括增加电池电量监测装置、加强点火系统的质量控制等。
经过改进措施的实施,新车型的发动机启动困难问题得到了有效解决,产品质量和客户满意度得到了显著提升。
通过这个案例,我们可以看到FMEA分析在识别和解决产品故障方面的重要作用。
通过对故障模式、影响、可能性、严重性和检测难度的分析,我们可以有针对性地制定改进措施,提高产品质量,降低风险,提升客户满意度。
总之,FMEA是一种简单而有效的风险分析工具,可以帮助我们识别和解决潜在风险,提高产品质量,降低成本,增强竞争力。
在实际工作中,我们应该充分发挥FMEA的作用,不断完善和改进产品和流程,为企业的可持续发展提供有力支持。
fmea失效模式分析案例
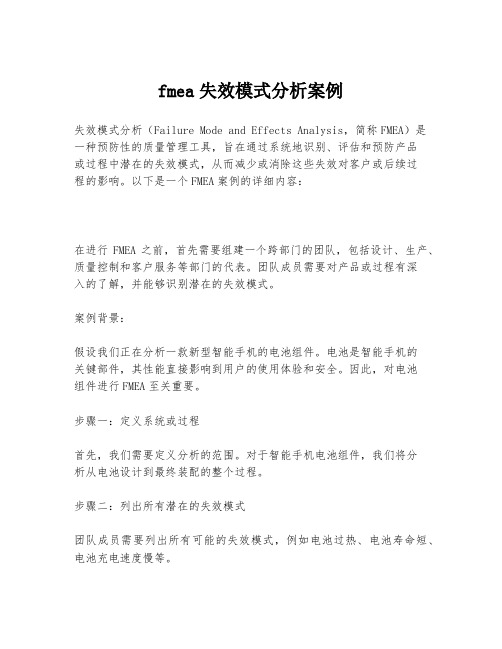
fmea失效模式分析案例失效模式分析(Failure Mode and Effects Analysis,简称FMEA)是一种预防性的质量管理工具,旨在通过系统地识别、评估和预防产品或过程中潜在的失效模式,从而减少或消除这些失效对客户或后续过程的影响。
以下是一个FMEA案例的详细内容:在进行FMEA之前,首先需要组建一个跨部门的团队,包括设计、生产、质量控制和客户服务等部门的代表。
团队成员需要对产品或过程有深入的了解,并能够识别潜在的失效模式。
案例背景:假设我们正在分析一款新型智能手机的电池组件。
电池是智能手机的关键部件,其性能直接影响到用户的使用体验和安全。
因此,对电池组件进行FMEA至关重要。
步骤一:定义系统或过程首先,我们需要定义分析的范围。
对于智能手机电池组件,我们将分析从电池设计到最终装配的整个过程。
步骤二:列出所有潜在的失效模式团队成员需要列出所有可能的失效模式,例如电池过热、电池寿命短、电池充电速度慢等。
步骤三:确定失效模式的潜在原因对于每个失效模式,团队需要确定可能导致该失效的原因。
例如,电池过热可能是由于电池设计不当、材料选择错误或制造过程中的缺陷。
步骤四:评估失效模式的严重性使用1到10的评分系统,团队需要评估每个失效模式的严重性。
评分越高,表示失效对客户或后续过程的影响越大。
步骤五:确定失效模式的潜在后果团队需要确定每个失效模式可能导致的后果。
例如,电池过热可能导致设备损坏或用户受伤。
步骤六:评估当前控制措施的有效性团队需要评估现有的控制措施是否能够有效预防或检测到潜在的失效模式。
例如,是否有严格的质量控制流程来检测电池的过热问题。
步骤七:计算风险优先数(RPN)风险优先数是通过将严重性(S)、发生概率(O)和检测难度(D)的评分相乘得到的。
RPN越高,表示该失效模式的风险越大。
步骤八:制定改进措施对于高RPN值的失效模式,团队需要制定改进措施。
这些措施可能包括重新设计电池、改进制造工艺或加强质量控制。
新版fmea案例

新版fmea案例在一家汽车零部件制造厂中,由于近期发生了多起产品质量问题,导致公司遭受了较大的经济损失和声誉受损,高层管理层意识到必须采取有效的措施来改善产品的质量。
因此,他们决定引入新版FMEA(失效模式与影响分析)方法来提前预防可能的失效模式,并采取相应的措施来减轻损失。
以下是一种新版FMEA方法的案例:首先,公司成立了一个由不同岗位的员工组成的跨部门团队,负责进行新版FMEA分析。
该团队包括设计人员、生产技术人员、品质控制人员以及售后服务人员。
他们共同制定了一个详细的工作计划,包括收集相关数据、分析失效模式和确定相应的控制措施。
团队首先收集了各个部门的历史数据,包括产品质量记录、客户投诉和售后服务的问题反馈。
通过对这些数据的分析,他们确定了几个重要的失效模式,包括产品组装不良、材料使用不当和设备故障等。
接下来,团队进行了详细的失效模式和影响分析。
他们根据每个失效模式的可能性、严重性和检测能力来对它们进行评估。
例如,对于产品组装不良这个失效模式,他们评估了造成客户事故的可能性、产品质量的影响程度以及生产线检测装置的能力。
在评估每个失效模式之后,团队开始制定相应的控制措施。
他们首先关注一些高风险的失效模式,采取主动的控制措施来减轻损失。
例如,对于产品组装不良的失效模式,他们决定增加更为严格的产品组装过程控制和检测步骤,以确保每个产品组装质量的稳定性。
同时,团队还制定了一系列培训计划,以提高员工的技能和意识。
他们认识到单纯的控制措施是不够的,员工的专业技能和操作规范同样重要。
因此,他们组织了一系列培训课程,包括质量控制、产品组装和设备维护等内容,以提高员工的整体素质。
最后,团队设立了一个监控机制,定期对已经实施的控制措施进行检查和评估。
他们收集相关的数据,并根据事故和客户投诉的情况调整控制措施。
这种迭代的过程使得FMEA分析更加灵活和有效。
通过引入新版FMEA方法,该厂成功地改进了产品质量并减少了损失。
经典FMEA案例
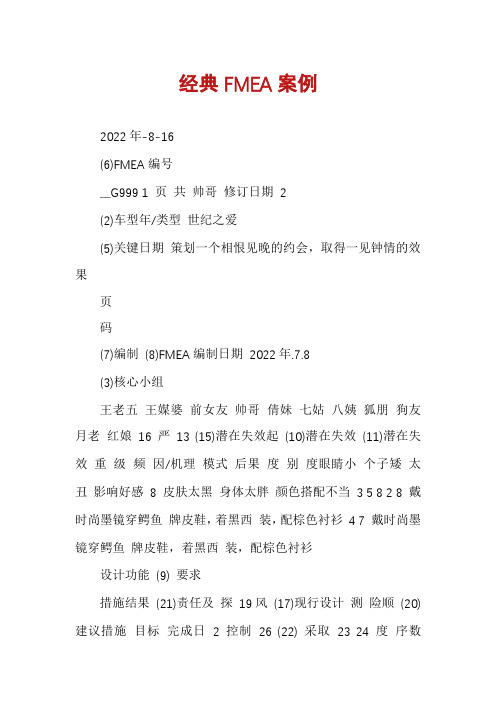
经典FMEA案例2022年-8-16(6)FMEA编号__G999 1 页共帅哥修订日期2(2)车型年/类型世纪之爱(5)关键日期策划一个相恨见晚的约会,取得一见钟情的效果页码(7)编制(8)FMEA编制日期2022年.7.8(3)核心小组王老五王媒婆前女友帅哥倩妹七姑八姨狐朋狗友月老红娘16 严13 (15)潜在失效起(10)潜在失效(11)潜在失效重级频因/机理模式后果度别度眼睛小个子矮太丑影响好感8 皮肤太黑身体太胖颜色搭配不当3 5 8 2 8 戴时尚墨镜穿鳄鱼牌皮鞋,着黑西装,配棕色衬衫4 7 戴时尚墨镜穿鳄鱼牌皮鞋,着黑西装,配棕色衬衫设计功能(9) 要求措施结果(21)责任及探19风(17)现行设计测险顺(20)建议措施目标完成日 2 控制26 (22) 采取23 24 度序数期5 S O RPN 的措施D3 8 6 6 6 5 5 96 448 144 240 穿步步高牌皮鞋,补钙增高涂迷你型奶油增白霜执行束身包扎,进行瘦身运动王老五/8月15 日前王老五/8月15 日前王老五/8月15 日前王老五/8月16 日前240 穿休闲棕色西服50 200 None 时尚的国际名牌西服风度翩翩的仪表不符合身份衣着不得体影响形象5 衣着不够档次帅哥/8月15日前借给王老五倩妹/8月10日前报告审美观王老五/8月15 日前执行调整王老五/8月10 日前52550不符合对方的审美观不良的习气如扣鼻子/模耳朵太紧张没有幽默感影响约会气氛 5 不符合对方的欣赏水平不良的口头禅8 CC 内容安排不当77根据倩妹/8月10 245 日前提供的审美观及时调整服装368 克服坏习惯120 None 210 制定5套应急方案256 72 克服坏习惯举止不良影响第一印象89 8 7 8 3尽量控制/别人提醒帅哥/倩妹左右护驾解围倩妹卧底为王老五作参谋尽量控制/别人提醒时尚笑话4 3 6 4 3帅哥/倩妹/王媒制定15套应婆8月10日前急方案王老五/8月10 日前71428谈吐幽默有品位影响好感/第一印俗气.乏味.无聊象展现失败表达方式不当约会D-FMEA(1)项目名称王老五的第999次约会(4)过程责任部门王媒婆2022年-8-16(6)FMEA编号__G999 2 页共帅哥修订日期2(2)车型年/类型世纪之爱(5)关键日期策划一个相恨见晚的约会,取得一见钟情的效果页码(7)编制(8)FMEA编制日期2022年.7.8(3)核心小组王老五王媒婆前女友帅哥倩妹七姑八姨狐朋狗友月老红娘16 严13 (15)潜在失效起现行设计(10)潜在失效(11)潜在失效重级频因/机理预防模式后果度别度才学疏浅,肚里没货设计功能(9) 要求措施结果(21)责任及探19风(17)现行设计测险顺(20)建议措施目标完成日2 控制26 (22) 采23 24 度序数期5 取的措施S O D RPN借题发挥,展现所10 长自吹自擂7 210 多阅读名著,提高修养水平王老五/8月15 日前帅哥/倩妹/王媒婆8月10日前王老五/8月15 日前父母/8月15日前3非凡的文化品位体现不出高尚的品位不能增进好感7表达方式不当6295 第三方宣传造势互动性交谈,以245 对方为中心,灵活进行。
第三版FMEA设计案例(ppt 68页)

12.01.2020
36
潜在失效模式
所谓潜在失效模式是指部件、子系统或系统有可能会 未达到或不能实现项目/功能栏中所描述的预期功能的 情况。
对于特定的项目及其功能,列出每一个潜在的失效模 式。
要考虑非正常使用条件下的失效模式。
无警告的 无预兆;影响安全或违反政府规章
10
严重危害
有警告的 有预兆;影响安全或违反政府规章
9
严重危害
很高 车辆(系统)不能运行,丧失基本功能
8
高 车辆(系统)能运行,性能下降,顾客
7
中等 车辆(系统)能运行,舒适性下降,顾客不舒服
6
低 车辆(系统)能运行,舒适性下降,顾客轻微不舒服
5
很低 配合、外观等项目不符合要求,大多数顾客能发现缺陷
FMEA能够减少或消除因修改而带來更大损失的机会。
适当的应用FMEA是一个相互作用的过程,永无止境。
12.01.2020
8
FMEA的实施注意事項
12.01.2020
9
那些原因可能 分析 現行預計的过程 分析 对顾客或下
造成这个失效模式
可能产生的失效模式
工序的影响
采取可行的对策
评审、验证并将更改 加入到其它文件
12.01.2020
34
核心小組:
列出有权限参与或执行這 項工作負責人姓名和单位 (建义將所有小組成員名字、 单位、电话号码、地址等 另行列表)。
12.01.2020
35
项目/功能
填入被分析项目的名称和其它相关信息。 用尽可能简明的文字来说明被分析项目满足设计
意图的功能,如:
新版fmea案例
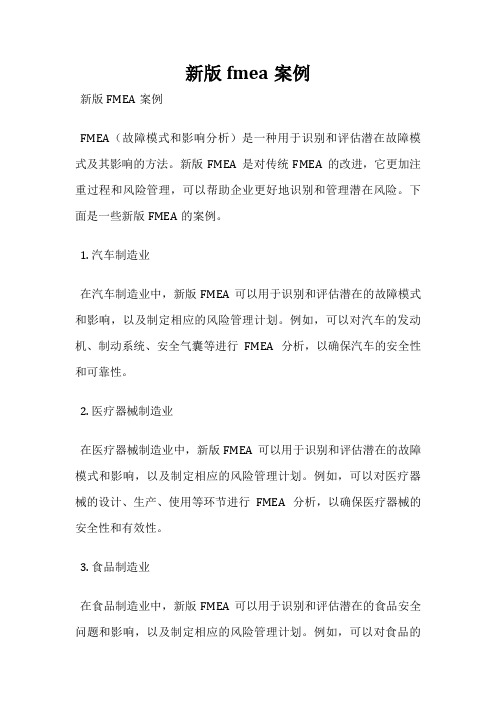
新版fmea案例新版FMEA案例FMEA(故障模式和影响分析)是一种用于识别和评估潜在故障模式及其影响的方法。
新版FMEA是对传统FMEA的改进,它更加注重过程和风险管理,可以帮助企业更好地识别和管理潜在风险。
下面是一些新版FMEA的案例。
1. 汽车制造业在汽车制造业中,新版FMEA可以用于识别和评估潜在的故障模式和影响,以及制定相应的风险管理计划。
例如,可以对汽车的发动机、制动系统、安全气囊等进行FMEA分析,以确保汽车的安全性和可靠性。
2. 医疗器械制造业在医疗器械制造业中,新版FMEA可以用于识别和评估潜在的故障模式和影响,以及制定相应的风险管理计划。
例如,可以对医疗器械的设计、生产、使用等环节进行FMEA分析,以确保医疗器械的安全性和有效性。
3. 食品制造业在食品制造业中,新版FMEA可以用于识别和评估潜在的食品安全问题和影响,以及制定相应的风险管理计划。
例如,可以对食品的生产、加工、储存、运输等环节进行FMEA分析,以确保食品的安全性和质量。
4. 航空航天制造业在航空航天制造业中,新版FMEA可以用于识别和评估潜在的故障模式和影响,以及制定相应的风险管理计划。
例如,可以对飞机的设计、生产、维护、使用等环节进行FMEA分析,以确保飞机的安全性和可靠性。
5. 电子制造业在电子制造业中,新版FMEA可以用于识别和评估潜在的故障模式和影响,以及制定相应的风险管理计划。
例如,可以对电子产品的设计、生产、测试、维护等环节进行FMEA分析,以确保电子产品的安全性和可靠性。
6. 石油化工制造业在石油化工制造业中,新版FMEA可以用于识别和评估潜在的安全问题和影响,以及制定相应的风险管理计划。
例如,可以对石油化工产品的生产、储存、运输、使用等环节进行FMEA分析,以确保石油化工产品的安全性和环保性。
7. 金属制造业在金属制造业中,新版FMEA可以用于识别和评估潜在的故障模式和影响,以及制定相应的风险管理计划。
FMEA案例范文
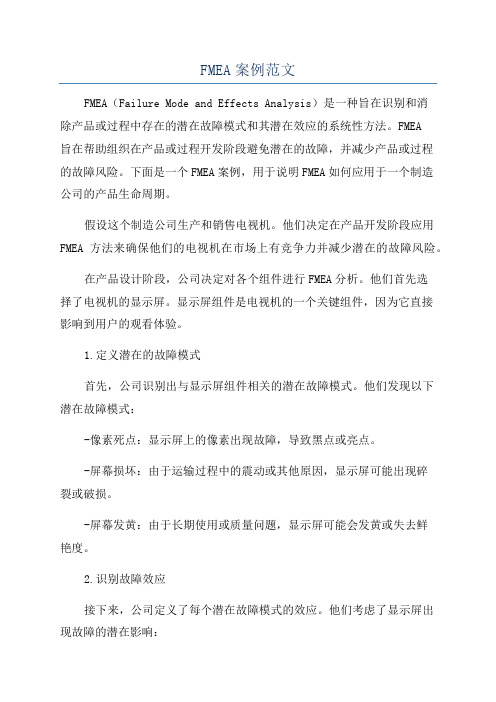
FMEA案例范文FMEA(Failure Mode and Effects Analysis)是一种旨在识别和消除产品或过程中存在的潜在故障模式和其潜在效应的系统性方法。
FMEA旨在帮助组织在产品或过程开发阶段避免潜在的故障,并减少产品或过程的故障风险。
下面是一个FMEA案例,用于说明FMEA如何应用于一个制造公司的产品生命周期。
假设这个制造公司生产和销售电视机。
他们决定在产品开发阶段应用FMEA方法来确保他们的电视机在市场上有竞争力并减少潜在的故障风险。
在产品设计阶段,公司决定对各个组件进行FMEA分析。
他们首先选择了电视机的显示屏。
显示屏组件是电视机的一个关键组件,因为它直接影响到用户的观看体验。
1.定义潜在的故障模式首先,公司识别出与显示屏组件相关的潜在故障模式。
他们发现以下潜在故障模式:-像素死点:显示屏上的像素出现故障,导致黑点或亮点。
-屏幕损坏:由于运输过程中的震动或其他原因,显示屏可能出现碎裂或破损。
-屏幕发黄:由于长期使用或质量问题,显示屏可能会发黄或失去鲜艳度。
2.识别故障效应接下来,公司定义了每个潜在故障模式的效应。
他们考虑了显示屏出现故障的潜在影响:-像素死点:用户在观看电视节目或电影时会被黑点或亮点分散注意力,影响观看体验。
-屏幕损坏:显示屏碎裂或破损可能导致显示效果变差,甚至无法使用。
-屏幕发黄:显示屏发黄或失去鲜艳度会影响图像质量,用户无法获得高质量的观看体验。
3.评估潜在原因和控制措施公司评估了每个潜在故障模式的可能原因,并制定相应的控制措施以减少潜在故障模式的出现概率:-像素死点的可能原因:制造过程中的材料问题,控制措施是选择高质量的材料,进行严格的质量控制。
-屏幕损坏的可能原因:运输过程中的震动,控制措施是加强包装和运输过程中的保护。
-屏幕发黄的可能原因:长期使用,控制措施是使用高品质的材料和组件,以及进行适当的维护和保养。
4.评估风险严重性和优先级公司为每个潜在故障模式评估了风险严重性和优先级,以指导其在产品设计过程中的决策:-像素死点的风险严重性:中等,由于像素死点会影响观看体验,但不会导致电视机无法使用。
fmea失效模式分析案例
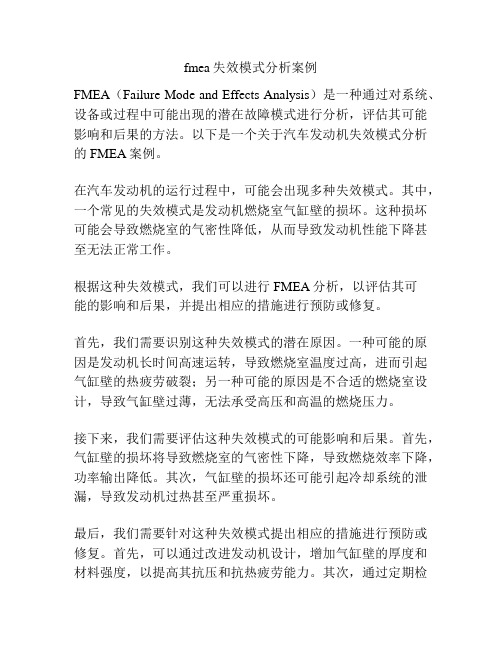
fmea失效模式分析案例FMEA(Failure Mode and Effects Analysis)是一种通过对系统、设备或过程中可能出现的潜在故障模式进行分析,评估其可能影响和后果的方法。
以下是一个关于汽车发动机失效模式分析的FMEA案例。
在汽车发动机的运行过程中,可能会出现多种失效模式。
其中,一个常见的失效模式是发动机燃烧室气缸壁的损坏。
这种损坏可能会导致燃烧室的气密性降低,从而导致发动机性能下降甚至无法正常工作。
根据这种失效模式,我们可以进行FMEA分析,以评估其可能的影响和后果,并提出相应的措施进行预防或修复。
首先,我们需要识别这种失效模式的潜在原因。
一种可能的原因是发动机长时间高速运转,导致燃烧室温度过高,进而引起气缸壁的热疲劳破裂;另一种可能的原因是不合适的燃烧室设计,导致气缸壁过薄,无法承受高压和高温的燃烧压力。
接下来,我们需要评估这种失效模式的可能影响和后果。
首先,气缸壁的损坏将导致燃烧室的气密性下降,导致燃烧效率下降,功率输出降低。
其次,气缸壁的损坏还可能引起冷却系统的泄漏,导致发动机过热甚至严重损坏。
最后,我们需要针对这种失效模式提出相应的措施进行预防或修复。
首先,可以通过改进发动机设计,增加气缸壁的厚度和材料强度,以提高其抗压和抗热疲劳能力。
其次,通过定期检查和维护发动机,及时发现和修复燃烧室气缸壁的损坏。
此外,还可以加强发动机冷却系统的设计,以确保发动机在高温环境下的正常运行。
通过对发动机燃烧室气缸壁损坏失效模式的FMEA分析,我们可以更全面地了解这种失效模式的潜在原因、可能的影响和后果,进而采取相应的措施进行预防或修复,以提高发动机的可靠性和性能。
同时,FMEA分析也可以为其他失效模式的分析提供参考,以实现对系统、设备或过程的全面考虑和持续改进。
fmea失效模式分析案例2篇

fmea失效模式分析案例2篇FMEA失效模式分析案例1:医院输液泵故障一、问题描述在医院使用的输液泵在使用过程中会发生故障,导致输液不正常,对患者造成影响。
二、分析步骤1. 列出可能的失效模式在使用过程中,输液泵可能出现以下失效模式:电源失效、软件出现错误、泵头堵塞、压力不足等。
2. 确定失效后果对于每个可能的失效模式,我们需要确定其产生的影响。
对于输液泵来说,可能导致输液不正常,导致患者的治疗效果受到影响,甚至危及生命。
3. 确定失效频率每个失效模式的出现频率不同,需要根据历史数据、专家评估等方式确定流失频率。
当然,针对不同的失效模式,可能需要采用不同的数据分析方法。
4. 确定探测方式为了及早发现输液泵的故障,需要确定哪些探测方式能够有效捕捉故障信号。
输液泵可能会出现一系列的故障信号,例如声音变化、滴速变慢等,需要通过多种探测方式来进行监测。
5. 确定纠正措施对于每个失效模式,需要确定针对性的纠正措施。
例如,对于电源失效,可以采取备用电源等方法来降低影响;对于软件错误,可以通过更新软件来解决;对于堵塞等问题,可以采取人工处理等方式来纠正。
6. 重新评估并持续改进在确定措施后,需要对整个过程进行重新评估,确保采取的措施有效。
同时,需要建立持续改进机制,不断优化输液泵的故障分析和纠正措施。
三、结论在输液泵的使用过程中,我们需要进行FMEA分析,以有效预防输液泵的故障。
通过对可能失效模式的分析,确定出可能的探测方式和纠正措施,并利用持续改进机制来优化管理。
这样可以最大限度地保证患者安全和治疗效果。
FMEA失效模式分析案例2:汽车刹车系统故障一、问题描述在汽车驾驶过程中,刹车系统出现故障造成车辆无法正常刹车,导致事故发生。
二、分析步骤1. 列出可能的失效模式在汽车刹车系统中,可能出现以下失效模式:制动液泄漏、制动片摩擦力不足、制动鼓磨损、制动蹄变形等。
2. 确定失效后果对于每个失效模式,我们需要进行分析,确定其对车辆行驶的影响。
fmea失效模式分析案例

fmea失效模式分析案例FMEA失效模式分析案例。
在产品设计和制造过程中,我们经常会遇到各种潜在的失效模式和效应分析(FMEA)的问题。
FMEA是一种系统性的方法,用于识别和评估产品或过程中可能出现的失效模式,以及这些失效模式对系统性能的影响。
本文将通过一个实际案例来介绍FMEA的应用和分析过程。
案例背景:某汽车制造公司在新车型的设计阶段进行FMEA分析,以识别潜在的设计缺陷和改进方案。
在这个案例中,我们将以发动机的设计和制造过程为例进行FMEA 分析。
失效模式识别:首先,我们需要识别可能的失效模式。
在发动机设计和制造过程中,可能的失效模式包括但不限于,磨损、材料疲劳、润滑系统故障、燃烧不完全等。
针对每一种失效模式,我们需要评估其可能性、严重性和检测难度。
可能性评估:针对每种失效模式,我们需要评估其发生的可能性。
例如,对于磨损这一失效模式,可能性评估可以考虑材料选择、工艺控制、使用环境等因素。
严重性评估:每种失效模式对系统性能的影响程度不同,我们需要评估其严重性。
例如,发动机磨损可能导致性能下降,甚至损坏其他部件,因此其严重性较高。
检测难度评估:对于每种失效模式,我们需要评估其在设计和制造过程中的检测难度。
例如,润滑系统故障可能需要通过传感器监测和故障诊断来进行检测。
改进方案:在评估了可能性、严重性和检测难度之后,我们需要制定相应的改进方案。
例如,针对发动机磨损这一失效模式,可以考虑改进材料选择、优化润滑系统设计等方案。
实施和监控:最后,我们需要实施改进方案,并持续监控失效模式的发生情况。
通过持续的FMEA分析,可以及时发现和解决潜在的问题,确保产品质量和性能。
结论:通过FMEA失效模式分析,我们可以识别潜在的失效模式,评估其可能性、严重性和检测难度,并制定相应的改进方案。
这有助于提高产品的质量和可靠性,减少故障率和维修成本,提升客户满意度。
总之,FMEA是一种非常有效的方法,可以帮助我们识别和解决产品或过程中可能出现的失效模式,提高产品质量和性能,降低成本和风险。
fmea失效分析案例
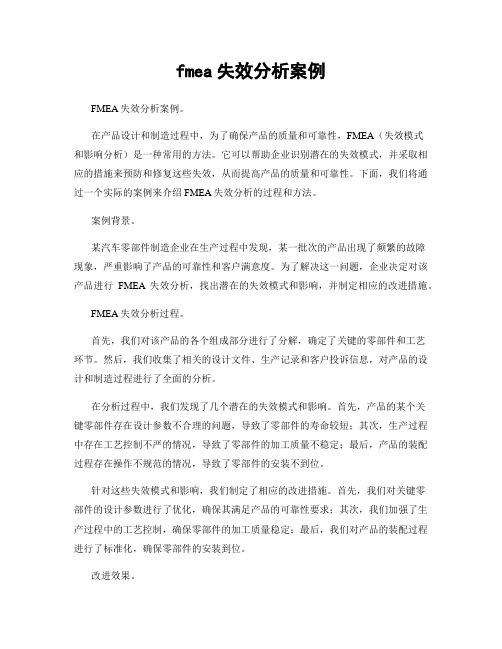
fmea失效分析案例FMEA失效分析案例。
在产品设计和制造过程中,为了确保产品的质量和可靠性,FMEA(失效模式和影响分析)是一种常用的方法。
它可以帮助企业识别潜在的失效模式,并采取相应的措施来预防和修复这些失效,从而提高产品的质量和可靠性。
下面,我们将通过一个实际的案例来介绍FMEA失效分析的过程和方法。
案例背景。
某汽车零部件制造企业在生产过程中发现,某一批次的产品出现了频繁的故障现象,严重影响了产品的可靠性和客户满意度。
为了解决这一问题,企业决定对该产品进行FMEA失效分析,找出潜在的失效模式和影响,并制定相应的改进措施。
FMEA失效分析过程。
首先,我们对该产品的各个组成部分进行了分解,确定了关键的零部件和工艺环节。
然后,我们收集了相关的设计文件、生产记录和客户投诉信息,对产品的设计和制造过程进行了全面的分析。
在分析过程中,我们发现了几个潜在的失效模式和影响。
首先,产品的某个关键零部件存在设计参数不合理的问题,导致了零部件的寿命较短;其次,生产过程中存在工艺控制不严的情况,导致了零部件的加工质量不稳定;最后,产品的装配过程存在操作不规范的情况,导致了零部件的安装不到位。
针对这些失效模式和影响,我们制定了相应的改进措施。
首先,我们对关键零部件的设计参数进行了优化,确保其满足产品的可靠性要求;其次,我们加强了生产过程中的工艺控制,确保零部件的加工质量稳定;最后,我们对产品的装配过程进行了标准化,确保零部件的安装到位。
改进效果。
经过改进措施的实施,我们再次对产品进行了测试和验证,发现产品的可靠性和稳定性得到了显著提高。
故障率明显下降,客户投诉现象得到了有效控制,企业的产品质量和客户满意度得到了提升。
结论。
通过本次FMEA失效分析案例,我们深刻认识到了FMEA在产品设计和制造过程中的重要性和价值。
只有通过对潜在的失效模式和影响进行全面的分析和评估,才能及时采取相应的措施,确保产品的质量和可靠性。
我们将继续深入推进FMEA方法在企业的应用,不断提升产品质量和客户满意度。
新版fmea七步法案例
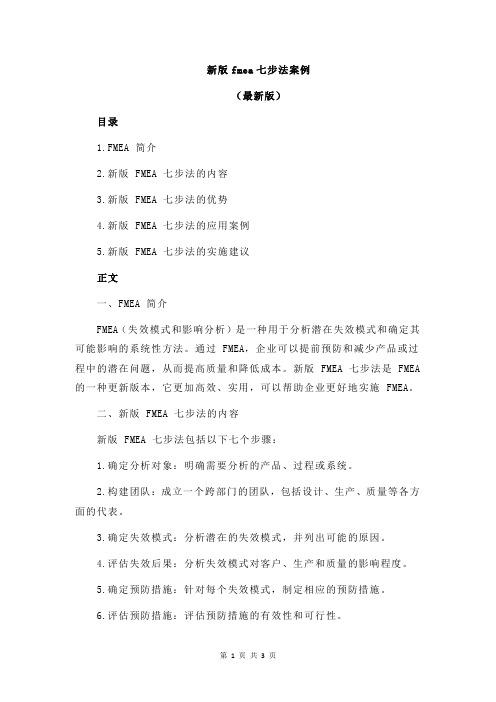
新版fmea七步法案例(最新版)目录1.FMEA 简介2.新版 FMEA 七步法的内容3.新版 FMEA 七步法的优势4.新版 FMEA 七步法的应用案例5.新版 FMEA 七步法的实施建议正文一、FMEA 简介FMEA(失效模式和影响分析)是一种用于分析潜在失效模式和确定其可能影响的系统性方法。
通过 FMEA,企业可以提前预防和减少产品或过程中的潜在问题,从而提高质量和降低成本。
新版 FMEA 七步法是 FMEA 的一种更新版本,它更加高效、实用,可以帮助企业更好地实施 FMEA。
二、新版 FMEA 七步法的内容新版 FMEA 七步法包括以下七个步骤:1.确定分析对象:明确需要分析的产品、过程或系统。
2.构建团队:成立一个跨部门的团队,包括设计、生产、质量等各方面的代表。
3.确定失效模式:分析潜在的失效模式,并列出可能的原因。
4.评估失效后果:分析失效模式对客户、生产和质量的影响程度。
5.确定预防措施:针对每个失效模式,制定相应的预防措施。
6.评估预防措施:评估预防措施的有效性和可行性。
7.实施和跟踪:实施预防措施,并定期跟踪和更新 FMEA 分析。
三、新版 FMEA 七步法的优势新版 FMEA 七步法相较于传统 FMEA 方法,具有以下优势:1.更系统化:新版 FMEA 七步法将 FMEA 分析过程分解为七个明确的步骤,使得分析更加系统化。
2.高效:新版 FMEA 七步法强调团队协作,可以提高分析效率。
3.实用:新版 FMEA 七步法注重实际应用,使得分析结果更具针对性和可操作性。
四、新版 FMEA 七步法的应用案例假设某企业要分析一款新产品的可靠性,他们可以采用新版 FMEA 七步法进行分析:1.确定分析对象:新产品的可靠性。
2.构建团队:由设计、生产、质量等部门的代表组成。
3.确定失效模式:分析新产品可能出现的失效模式,如无法启动、电池寿命短等。
4.评估失效后果:分析失效模式对客户使用、生产和质量的影响。
fmea失效模式分析案例
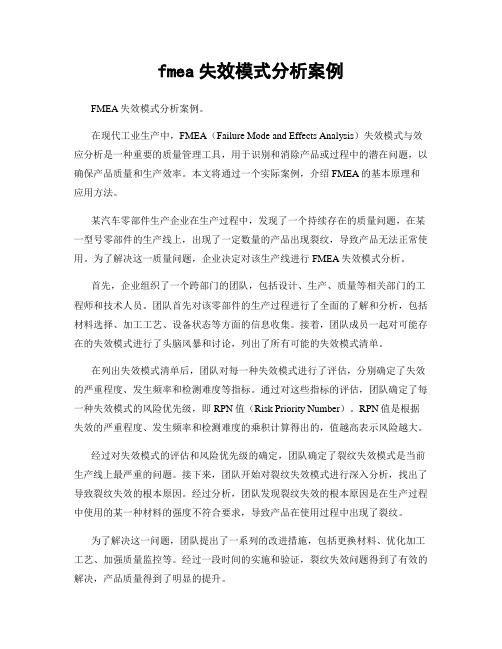
fmea失效模式分析案例FMEA失效模式分析案例。
在现代工业生产中,FMEA(Failure Mode and Effects Analysis)失效模式与效应分析是一种重要的质量管理工具,用于识别和消除产品或过程中的潜在问题,以确保产品质量和生产效率。
本文将通过一个实际案例,介绍FMEA的基本原理和应用方法。
某汽车零部件生产企业在生产过程中,发现了一个持续存在的质量问题,在某一型号零部件的生产线上,出现了一定数量的产品出现裂纹,导致产品无法正常使用。
为了解决这一质量问题,企业决定对该生产线进行FMEA失效模式分析。
首先,企业组织了一个跨部门的团队,包括设计、生产、质量等相关部门的工程师和技术人员。
团队首先对该零部件的生产过程进行了全面的了解和分析,包括材料选择、加工工艺、设备状态等方面的信息收集。
接着,团队成员一起对可能存在的失效模式进行了头脑风暴和讨论,列出了所有可能的失效模式清单。
在列出失效模式清单后,团队对每一种失效模式进行了评估,分别确定了失效的严重程度、发生频率和检测难度等指标。
通过对这些指标的评估,团队确定了每一种失效模式的风险优先级,即RPN值(Risk Priority Number)。
RPN值是根据失效的严重程度、发生频率和检测难度的乘积计算得出的,值越高表示风险越大。
经过对失效模式的评估和风险优先级的确定,团队确定了裂纹失效模式是当前生产线上最严重的问题。
接下来,团队开始对裂纹失效模式进行深入分析,找出了导致裂纹失效的根本原因。
经过分析,团队发现裂纹失效的根本原因是在生产过程中使用的某一种材料的强度不符合要求,导致产品在使用过程中出现了裂纹。
为了解决这一问题,团队提出了一系列的改进措施,包括更换材料、优化加工工艺、加强质量监控等。
经过一段时间的实施和验证,裂纹失效问题得到了有效的解决,产品质量得到了明显的提升。
通过这个案例,我们可以看到FMEA失效模式分析的应用对于解决生产过程中的质量问题具有重要的作用。
FMEA第五版教材中的潜在失效模式分析实战案例分享

FMEA第五版教材中的潜在失效模式分析实战案例分享近年来,潜在失效模式分析(Failure Mode and Effects Analysis,简称FMEA)在各行业中得到了广泛应用。
作为一种系统性、科学性的分析方法,FMEA帮助企业识别产品或流程中潜在的失效模式,并找出可能导致失效的原因,进而采取相应的措施进行风险管理。
本文将通过教材中的实战案例分享,来介绍FMEA第五版教材中关于潜在失效模式分析的具体应用。
案例一:汽车制造业中的传动轴失效模式分析在汽车制造业中,传动轴是汽车动力传输的重要组成部分。
在FMEA第五版教材中的案例中,以一家汽车制造企业为例,对传动轴进行了失效模式分析。
首先,团队成员收集了大量关于传动轴的信息,包括设计图纸、材料信息、工艺参数等。
然后,通过分析失效模式的可能性和后果,确定了传动轴的失效模式,如碎裂、断裂等。
接下来,团队进一步分析了失效原因,如材料质量、工艺参数等,并评估了每种失效原因对传动轴失效的影响程度。
最后,团队提出了相应的风险控制措施,如提高材料强度、优化工艺参数等,以预防或减少失效的发生。
案例二:医疗设备中的电路板失效模式分析在医疗设备制造领域中,电路板是设备正常运行的关键组成部分。
本案例中,以一家医疗设备制造企业为例,团队运用FMEA方法对电路板进行了失效模式分析。
团队首先收集了电路板的相关信息,包括设计规范、元器件参数、焊接工艺等。
然后,他们通过分析电路板失效的可能性和后果,确定了失效模式,如短路、开路等。
接下来,团队分析了失效的潜在原因,如元器件损坏、焊接接触不良等,并评估了每种原因对失效的影响程度。
最后,团队提出了相应的控制措施,比如加强元器件检测质量、优化焊接工艺等,以提高电路板的可靠性和稳定性。
通过以上两个案例的分享,我们可以看出FMEA方法在实践中的应用价值。
通过分析失效模式和潜在原因,企业可以及早发现隐藏的问题,采取相应的预防措施,以降低风险和提高产品或流程的质量。
fmea成功案例

fmea成功案例FMEA(故障模式与影响分析)是一种系统性的方法,用于识别和评估潜在故障模式及其对系统性能的影响。
下面是一些FMEA成功案例的示例。
1. 汽车生产线的FMEA:在汽车生产线上,FMEA被广泛应用于识别和预防潜在的故障模式,以确保高质量和高效率的生产。
通过对每个工作站和关键步骤进行FMEA分析,制造商能够及早发现潜在问题,并采取相应的纠正措施,从而避免生产线停机和产品质量问题。
2. 医疗器械设计的FMEA:在医疗器械设计过程中,FMEA被用于识别和评估潜在的设计缺陷和安全风险。
通过分析每个组件和子系统的潜在故障模式及其对患者安全和治疗效果的影响,设计团队能够及早发现并解决潜在问题,确保医疗器械的安全性和可靠性。
3. 航空航天领域的FMEA:在航空航天领域,FMEA被广泛应用于识别和评估潜在的故障模式,以确保飞机和航天器的安全和可靠性。
通过对每个关键系统和组件进行FMEA分析,工程师能够识别出潜在的故障模式,并采取相应的措施来预防或减轻其对系统性能的影响。
4. 制药行业的FMEA:在制药行业,FMEA被用于识别和评估潜在的制造过程中的风险和质量问题。
通过对每个关键步骤和操作进行FMEA分析,制药公司能够及早发现潜在问题,并采取相应的措施来确保产品质量和符合法规要求。
5. 电子产品设计的FMEA:在电子产品设计过程中,FMEA被用于识别和评估潜在的设计缺陷和可靠性问题。
通过对每个关键功能和组件进行FMEA分析,设计团队能够及早发现潜在问题,并采取相应的措施来提高产品的可靠性和性能。
6. 银行业的FMEA:在银行业,FMEA被用于识别和评估潜在的操作风险和安全问题。
通过对每个关键业务流程和操作进行FMEA分析,银行能够及早发现潜在风险,并采取相应的措施来预防或减轻其对业务运营的影响。
7. 石油和化工行业的FMEA:在石油和化工行业,FMEA被广泛应用于识别和评估潜在的安全和环境风险。
通过对每个关键工艺步骤和设备进行FMEA分析,公司能够及早发现潜在问题,并采取相应的措施来预防事故和减轻对环境的影响。
实用文档某知名品牌企业经典FMEA案例完整版(一)

实用文档某知名品牌企业经典FMEA案例完整版(一)实用文档某知名品牌企业经典FMEA案例完整版FMEA全称为故障模式及影响分析(Failure Mode and Effects Analysis),是一种在设计或改进系统、过程和产品中,识别潜在故障和缺陷,以及对它们进行排除或减小影响的系统性方法。
FMEA在品质管理、产品设计和工业工程领域具有广泛的应用。
本文将分享某知名品牌企业的经典FMEA案例完整版,希望能对大家有所启发。
案例背景:某家制造汽车零部件的企业在进行新产品开发时,出现过多的故障和退货问题,导致生产进度延误、产品质量下降、成本增加等问题。
为了解决这一问题,企业采用了FMEA方法进行了全面分析,下面详细介绍具体步骤。
第一步:构建FMEA团队由于FMEA要求对产品的每个设计和制造阶段都进行全面分析,故要构建一个具有多专业背景的团队,包括:设计、制造、采购、生产、品质控制等各部门人员。
第二步:定义分析对象该企业对汽车变速箱附件系统进行分析,包括传动轴、联轴器、轴承、节温器等几个部分。
第三步:制定方案团队制定FMEA分析方案,明确分析项目、分析子目标、分析流程、分析参数、分析人员等,确保分析的全面性和可操作性。
第四步:收集数据在分析之前,需要给每个部件定义一些常规的故障模式,这些故障模式可能是来自Wiki、历史数据、TRIZ解决方案等。
此外,还需收集制造过程中的全部参数,这些参数包括:物理参数、材料参数、人员技能参数、工具、设备、工艺等。
第五步:分析风险以传动轴为例,各部门人员根据自己的经验和知识,确定可能存在的故障模式,并将其分类到FM(故障模式)、CO(原因)和SE(效果)三个方面。
通过求解等级风险值,对各子目标进行排序,找出风险最高的故障点进行改进。
第六步:提出改进方案分析了存在风险的故障点之后,团队需要提出针对性的改进方案,并将其汇总到FMEA报告中,以便后续跟踪和实施。
本案例中,制造车轴和齿轮方面则是各类TO DO列表,逐一排查并修改,以最终减少零件故障,最终提高生产效益,降低成本,改进生产流程并提高产品质量的目的。
新版fmea七步法案例
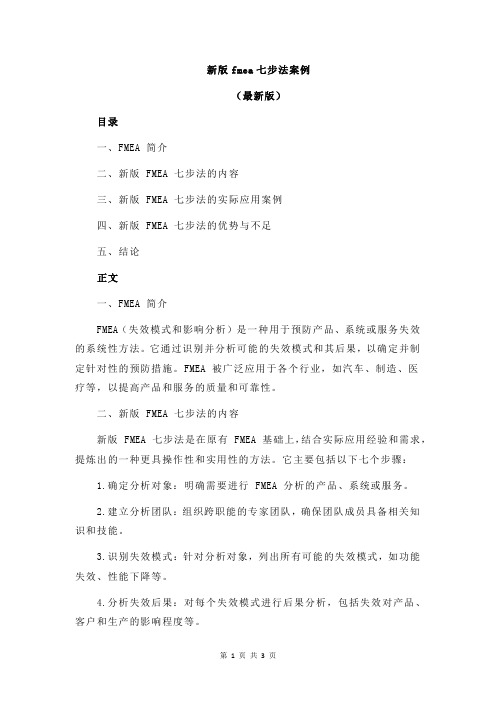
新版fmea七步法案例(最新版)目录一、FMEA 简介二、新版 FMEA 七步法的内容三、新版 FMEA 七步法的实际应用案例四、新版 FMEA 七步法的优势与不足五、结论正文一、FMEA 简介FMEA(失效模式和影响分析)是一种用于预防产品、系统或服务失效的系统性方法。
它通过识别并分析可能的失效模式和其后果,以确定并制定针对性的预防措施。
FMEA 被广泛应用于各个行业,如汽车、制造、医疗等,以提高产品和服务的质量和可靠性。
二、新版 FMEA 七步法的内容新版 FMEA 七步法是在原有 FMEA 基础上,结合实际应用经验和需求,提炼出的一种更具操作性和实用性的方法。
它主要包括以下七个步骤:1.确定分析对象:明确需要进行 FMEA 分析的产品、系统或服务。
2.建立分析团队:组织跨职能的专家团队,确保团队成员具备相关知识和技能。
3.识别失效模式:针对分析对象,列出所有可能的失效模式,如功能失效、性能下降等。
4.分析失效后果:对每个失效模式进行后果分析,包括失效对产品、客户和生产的影响程度等。
5.评估失效风险:根据失效后果的严重程度和发生概率,评估每个失效模式的风险等级。
6.制定预防措施:针对高风险的失效模式,制定相应的预防措施,确保问题得到有效解决。
7.实施和监控:将预防措施纳入产品设计、生产和维护过程中,并持续监控实施效果。
三、新版 FMEA 七步法的实际应用案例以某汽车制造企业为例,该企业采用新版 FMEA 七步法对一款新车型进行失效分析。
通过该方法,企业成功识别并预防了潜在的失效模式,提高了产品的质量和可靠性。
四、新版 FMEA 七步法的优势与不足新版 FMEA 七步法的优势主要体现在以下几个方面:1.操作性强:七步法结构清晰,易于理解和操作,降低了 FMEA 实施的难度。
2.实用性高:新版 FMEA 七步法更注重实际应用,能够有效解决企业在产品设计、生产和维护过程中遇到的问题。
3.系统性优:新版 FMEA 七步法从失效模式识别到预防措施制定,再到实施和监控,形成了一个完整的闭环管理体系。
- 1、下载文档前请自行甄别文档内容的完整性,平台不提供额外的编辑、内容补充、找答案等附加服务。
- 2、"仅部分预览"的文档,不可在线预览部分如存在完整性等问题,可反馈申请退款(可完整预览的文档不适用该条件!)。
- 3、如文档侵犯您的权益,请联系客服反馈,我们会尽快为您处理(人工客服工作时间:9:00-18:30)。
磁体B/H值
○
●
○
磁隙宽度
○
●
○
●
磁芯直径
●
○
●
外形尺寸
○
音圈
与磁场共同作用,将电信号转换为机械震动
直流阻抗
●
○
骨架材料
○
●
●
●
直径
●
●
高度
○
●
承受电流
●
●
以下略
案例(续):
DFMEA小组开始着手开发DFMEA。小组成员经过讨论,完成了产品的DFMEA工作。在评价严重度(S),频度数(O),探测度时,采用了客户所要求的判断准则。
部件设计责任编制人
车型年/车辆类型关键日期FEMA日期(编制)(修订)
核心小组
项目
功能
潜在
失效模式
潜在
失效后果
严重度S
级别
潜在失效
起因/机理
频度O
现行
设计控制
探测度D
R
P
N
建议措施
责任及
目标完成
日期
措施结果
-预防
-探测
采取的措施
S
O
D
R
P
N
案例分析:
DFMEA表格的第一栏内容(项目/要求)来自什么地方?为了明确表格中第一栏的内容,在开始做DFMEA前,应做哪些准备工作?
SPL偏低,声音小,音响系统声道不均衡
5
▼
供应商提供的磁体达不到要求
7
要求供应商每批次提供测试报告
进料时测试
生产完成后,100%人工检听
5
175
依照PPAP对供应商进行过程批准
特别是:
要求供应商CPK达到1.33
引进MALISSA检测系统进行100%测试
2006-10-30:SQE小组,确定批准要求并完成供应商手册。2008-10-01,供应商满足手册要求
⑨
顾客质量批准/日期(如需要)
⒀
供方/工厂
⑤
供方代码⑥
其它批准/日期(如需要)
⒁
其它批准/日期(如需要)
⒁
零件/过
程编号
⒂
过程名称/操作描述 ⒃
机器、装置
夹具、工装
⒄
特性
特殊特
性分类
(21)
方法
反应控制
(26)
编号
⒅
产品⒆
过程⒇
产品/过程规范/公差(22)
评价/测
量技术
(23)
样本(24)
控制方法
(25)
子系统(PFMEA)共页,第页
部件设计责任编制人
车型年/车辆类型关键日期FEMA日期(编制)(修订)
核心小组
工序
作用
潜在
失效模式
潜在
失效后果
严重度S
级别
潜在失效
起因/机理
频度O
现行
过程控制
探测度D
R
P
N
建议措施
责任及
目标完成
日期
措施结果
-预防
-探测
采取的措施
S
O
D
R
P
N
磁体采购
所采购磁体满足要求
饱和充磁B/H值低于要求下限
以下是部分的结果:
设计FMEA的标准表
系统潜在失效模式及后果FMEA编号
子系统(设计FMEA)共页,第页
部件设计责任编制人
车型年/车辆类型关键日期FEMA日期(编制)(修订)
核心小组
项目
功能
潜在
失效模式
潜在
失效后果
严重度S
级别
潜在失效
起因/机理
频度O
现行
设计控制
探测度D
R
P
N
建议措施
责任及
目标完成
日期
案例:
某音响制造公司为某汽车制造商设计制造一车用扬声器。以下是汽车制造商提出的(部分)要求:
安装尺寸▼:外形图标注,为4’扬声器。
可靠性要求:3年无故障▼。
阻抗:8.0±0.8 OHM at 400Hz
注:其中带▼为特殊特性。
公司可确定,扬声器用于低档XX型轿车。对音质要求不高。
公司经过可行性论证,正式立项,并成立了项目小组。为保证产品设计能满足客户要求,项目小组组建DFMEA小组,小组组长由产品设计工程师张三担任,成员有:
案例(续):为了保证产品设计意图完整地贯彻到生产过程中,项目小组接着组建了PFMEA小组。小组组长由参加过DFMEA开发的工艺工程师王五担任,小组成员有原DFMEA小组的产品设计工程师张三和品质工程师赵六,SQE钱七,以及计划将来进行该产品生产的生产车间主任贾师傅。
PFMEA小组首先利用特性矩阵,将产品关键特性对应到生产过程的中,以下是关键特性矩阵的部分内容:
9
很高
车辆/项目不能运行(丧失基本功能)
8
高
车辆/项目可运行,但性能下降,顾客非常不满意
7
中等
车辆/项目可运行,但舒适性/方便性项目不能运行,顾客不满意。
6
低
车辆/项目可运行,但舒适性/方便性项目的性能下降,顾客有些不满意。
5
很低
配合和外观/尖响和卡嗒响等到项目不舒服。大多数顾客(75%以上)能感觉到有缺陷。
尤全
10-30前投入使用
5
2
2
20
过程FMEA的标准表
系统潜在失效模式及后果FMEA编号
子系统(PFMEA)共页,第页
部件设计责任编制人
车型年/车辆类型关键日期FEMA日期(编制)(修订)
核心小组
工序
作用
潜在
失效模式
潜在
失效后果
严重度S
级别
潜在失效
起因/机理
频度O
现行
设计控制
探测度D
R
P
N
建议措施
责任及
电容厂的品质人员,检查了库存产品的状况,发现发往A客户的产品同样存在毛刺,但检查以往的记录,A顾客从来没有就此问题提出任何投诉。
案例讨论:
以往生产的发往A客户的产品,是否可能存在类似的问题?为什么以往A顾客没有投诉?
如果您负责此缺陷的整改,您为确定产生此问题的根源,还应该检查哪些文件或记录?
案例(续):
措施结果
-预防
-探测
采取的措施
S
O
D
R
P
N
磁路系统:
提供驱动震动的恒定磁场,与音圈配合
磁场强度过低
SPL偏低,声音小
5
▼
磁体型号选择不当
磁隙设计过宽
磁心直径小
6
2
3
磁路设计指南/模拟计算
磁隙B值测量以及
样件测试
2
2
2
60
20
30
设计FMEA的标准表
系统潜在失效模式及后果FMEA编号
子系统(设计FMEA)共页,第页
产品设计工程师:张三、李四
产品工艺工程师:王五
品质工程师:赵六
SQE:钱七
FMEA小组首先明确客户对产品的要求如下:
外部:
扬声器主要技术参数:
阻抗:8.0±0.8 OHM at 400Hz
特性灵敏度级:88±2dB
f0:120±15Hz
额定功率:8W
长期最大功率:20W
安装尺寸:见外形图
使用寿命: 3000 Hours
以下是小组开发的控制计划,控制计划和FMEA有什么联系?
总结:
客户的要求是如何一步一步转换到对生产过程的控制的?
控制计划第页共页
样件试生产生产
①
控制计划编号②
主要联系人/电话
⑦
日期(编制)
⑩
日期(修订)
⑾
零件名称/最新更改等级
③
核心小组
⑧
顾客工程批准/日期(如需要)
⑿
零件名称/描述
④
供方/工厂批准/日期
-预防
-探测
采取的措施
S
O
D
R
P
N
充磁
使磁体磁饱和
磁体充磁不饱和
SPL偏低,使用者感觉明显
轻微失真
5
2
▼
充磁时间不够
充磁机的充磁电流不够
8
2
SETUP检查
设备定期保养
最终100%检查
4
160
40
在充磁机加装时间控制装置
并使用MALISSA检测系统进行100%测试
2006-6-22
Pat
尤全
10-30前投入使用
工厂的流程为:
进料――裁线/去线头绝缘层――压合――包装――出货
其中,裁线/去绝缘层由自动裁线的设备完成,压合由半自动冲压机完成。
请根据上述信息,开发PFMEA和控制计划。
案例提示:
ROHS的要求是如何通过FMEA传递到过程中去的?
过程中是否可能涉及操作工人的安全?
还有可能导致客户不满的其他问题吗?
目标完成
日期
措施结果
-预防
-探测
采取的措施
S
O
D
R
P
N
绕线
在骨架上绕制规定匝数线圈
绕线匝数不够
阻抗偏小,失真增加,且顾客使用时和功放不匹配,影响使用
工作电流增大,影响产品寿命
SPL偏高,造成左右声道不均衡
2
7
5
▼
▼
绕线机设定错误
绕线机控制系统出现错误
2
2
SETUP检查
计数器定期校准
检查表
生产完成后,100%人工检听
容量