连铸结晶器温度场及热变形的数值模拟
连铸结晶器内热一力耦合数值模拟及研究
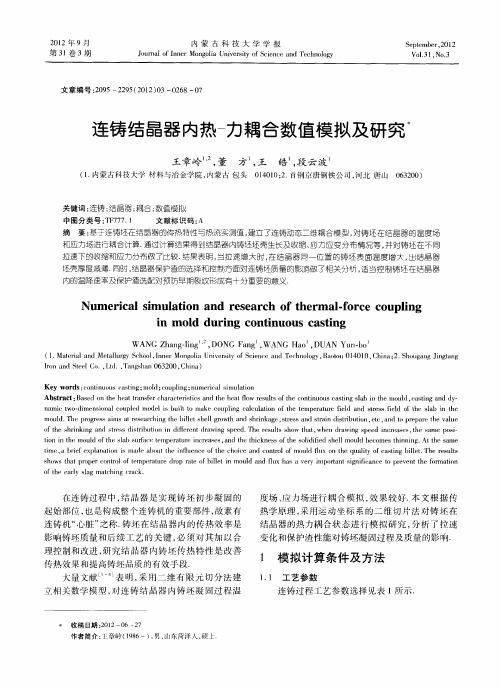
报一
‰
Nu e i a i u a i n a d r s a c ft e m a -o c o p i g m rc lsm l to n e e r h o h r lf r e c u l n i o d d r n o tn o s c si n m l u i gc n iu u a t ng
s o ha o rc nto ftmp r t r r p r t fble n mo l n ux h sa v r nlut n infc n e t e e h om ain h ws t tprpe o r lo e e a u e d o ae o ilti ud a d f a e y i p ra tsg i a c opr v ntt e f r t l i o o"h a 1 lg m ac i g ( a k tte e iY sa t h n : c . r
1 1 工艺 参数 .
连铸过 程工 艺参 数选择 见表 1 所示 .
¥ 收 稿 日期 :0 2—0 2 21 6— 7
作者简介 : 王章岭 (9 6一) 男 , 18 , 山东菏泽人 , 硕上
王章岭 , : 等 连铸结 晶器 内热一 力耦合数值模拟及研究 表 1 连铸工艺参数
o he s rn i g a te s dsrbu in n dier n a ng s e d. e r s t h w h t whe r wig s e d i r a e te s ne po t ft h i k n nd sr s iti to i f e tdrwi p e Th e ulss o t a , t n d a n p e nce s s,h a l s— to n t ul ft e sa)s rH et mp r t ej c e s s. n het ikn s ft e s ld fe h l mo l ) e me hinig. hes me in i hemo d o h lt u ̄ e e e aur n r a e a d t h c e so h o ii d s e l ud 1 o st n n Att a i e
连铸过程原理及数值模拟

连铸过程原理及数值模拟连铸是一种重要的金属成形工艺,广泛应用于钢铁、铝合金等金属材料的生产和加工中。
连铸过程原理及数值模拟是研究连铸工艺的关键内容,通过对连铸过程的原理分析和数值模拟,可以优化连铸工艺参数,提高产品质量和生产效率。
连铸过程是将熔融金属直接注入到连续运动的铸坯中,通过冷却和凝固过程,将熔融金属转化为固态铸坯。
连铸的基本原理是利用连续运动的铸坯带走热量,使熔融金属迅速凝固,形成连续的固态铸坯。
在连铸过程中,主要包括液相区、液固两相区和固相区三个区域。
在液相区,熔融金属通过连续浇注,填充到铸坯的空腔中。
熔融金属的温度高于固相线,处于液态状态。
随着熔融金属的注入,液相区的长度逐渐增加。
在液固两相区,熔融金属和正在凝固的铸坯同时存在。
由于熔融金属的温度高于固相线,所以熔融金属仍然保持液态。
而铸坯由于受到液相的热量传递,开始逐渐凝固。
在这个区域中,液相区的长度逐渐减小,凝固铸坯的长度逐渐增加。
在固相区,整个铸坯都已经完全凝固。
熔融金属已经完全转化为固态,形成连续的固态铸坯。
在这个区域中,液相区的长度为零,凝固铸坯的长度为整个连铸过程的长度。
为了研究连铸过程的细节和优化连铸工艺参数,数值模拟成为一种重要的方法。
数值模拟是通过数学模型和计算机仿真技术,对连铸过程进行模拟和分析。
数值模拟可以准确地计算连铸过程中的温度场、流场和凝固结构等关键参数,为工艺优化提供科学依据。
在连铸过程的数值模拟中,需要考虑多个物理过程的相互作用。
首先是流体力学过程,包括熔融金属的流动和铸坯带走热量的过程。
其次是热传导过程,包括熔融金属的冷却和凝固过程。
最后是凝固结构演化过程,包括铸坯的晶粒生长和偏析等现象。
为了建立连铸过程的数值模型,需要考虑材料的物理性质、流体力学和热传导方程等方面的参数。
同时,还需要考虑边界条件和初始条件等参数。
通过数值模拟,可以预测连铸过程中的温度分布、流速分布和凝固结构等重要参数,为工艺优化提供指导。
热型连铸凝固过程微观组织形成的数值模拟
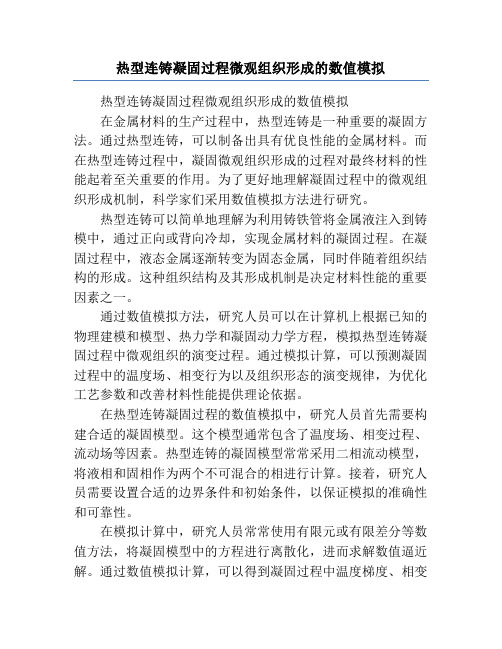
热型连铸凝固过程微观组织形成的数值模拟热型连铸凝固过程微观组织形成的数值模拟在金属材料的生产过程中,热型连铸是一种重要的凝固方法。
通过热型连铸,可以制备出具有优良性能的金属材料。
而在热型连铸过程中,凝固微观组织形成的过程对最终材料的性能起着至关重要的作用。
为了更好地理解凝固过程中的微观组织形成机制,科学家们采用数值模拟方法进行研究。
热型连铸可以简单地理解为利用铸铁管将金属液注入到铸模中,通过正向或背向冷却,实现金属材料的凝固过程。
在凝固过程中,液态金属逐渐转变为固态金属,同时伴随着组织结构的形成。
这种组织结构及其形成机制是决定材料性能的重要因素之一。
通过数值模拟方法,研究人员可以在计算机上根据已知的物理建模和模型、热力学和凝固动力学方程,模拟热型连铸凝固过程中微观组织的演变过程。
通过模拟计算,可以预测凝固过程中的温度场、相变行为以及组织形态的演变规律,为优化工艺参数和改善材料性能提供理论依据。
在热型连铸凝固过程的数值模拟中,研究人员首先需要构建合适的凝固模型。
这个模型通常包含了温度场、相变过程、流动场等因素。
热型连铸的凝固模型常常采用二相流动模型,将液相和固相作为两个不可混合的相进行计算。
接着,研究人员需要设置合适的边界条件和初始条件,以保证模拟的准确性和可靠性。
在模拟计算中,研究人员常常使用有限元或有限差分等数值方法,将凝固模型中的方程进行离散化,进而求解数值逼近解。
通过数值模拟计算,可以得到凝固过程中温度梯度、相变速率以及组织演变规律等信息。
这些信息对于工艺优化和材料性能的改善起到了重要的指导作用。
为了更好地验证数值模拟结果的准确性,研究人员通常会进行实验验证。
实验验证常常包括金属样品的制备、显微组织的观察和性能测试等步骤。
通过与实验结果的对比,可以验证数值模拟的准确性,并进一步改进模型和计算方法。
通过热型连铸凝固过程微观组织形成的数值模拟,研究人员可以更好地理解材料凝固过程中组织形成的机制,为优化工艺参数和改善材料性能提供科学依据。
CSP连铸结晶器内三维流场与温度场的数值模拟
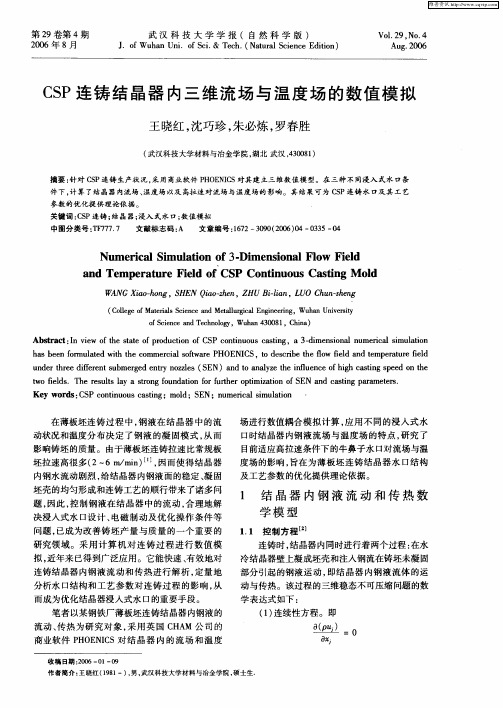
参数 的优化提供理论依据 。
关键词 :S C P连铸 ; 结晶器; 浸入 式水 1 ; 5 数值模拟 / 中图分类号 : 7 . T 77 文献标 志码 : A 文章编号 :6 2— o o 2o )4— 35— 4 17 3 9 (06 0 0 3 0
Nu e i a i u a i n o . m e so a l w ed m rc lS m lto f3 Di n i n lF o Fil a d Te p r t r il fCS n i u u si g M od n m e a u e F ed o P Co t o s Ca tn l n
题, 因此 , 控制钢液在结晶器中的流动 , 合理地解
决浸 入式 水 口设计 、 电磁 制 动 及 优 化操 作 条 件 等 问题 , 已成为改 善 铸 坯产 量 与质 量 的一 个 重 要 的 研究 领 域 。采 用 计 算 机 对 连 铸 过 程 进 行 数值 模 拟, 近年来 已得 到广 泛应 用 。它能快 速 、 效地对 有 连铸 结 晶器 内钢 液 流动 和 传 热 进行 解 析 , 量 地 定 分 析水 口结构 和 工 艺参 数 对 连 铸 过程 的影 响 , 从
维普资讯
第2 9卷第 4期 20 0 6年 8月
武 汉 科 技 大 学 学 报 (自 然 科 学 版 )
J f h nU i f c. T c . N trl c neE io ) .o a n.o i& eh ( a a Si c dt n Wu S u e i
u d r he iee t u megde t oz s( E n e tredf rn b re nr n z e S N)adt aayetei u n e f ihc t gsedo e s y l n l z f ec g a i pe nt on h n l oh s n h
《板坯连铸结晶器内三维流热固耦合数值模拟研究》

《板坯连铸结晶器内三维流热固耦合数值模拟研究》篇一一、引言随着现代工业的快速发展,板坯连铸作为冶金工业中的重要工艺之一,其技术进步对钢铁产业的可持续发展起着决定性作用。
在板坯连铸过程中,结晶器作为关键设备之一,其内部流场和温度场的分布对铸坯的质量具有重要影响。
为了更准确地描述和优化这一过程,本研究采用了三维流热固耦合数值模拟方法对板坯连铸结晶器内的流动与传热行为进行研究。
二、研究背景与意义传统的板坯连铸过程通常依靠实验观察和经验模型来分析和预测。
然而,这种方法既费时又成本高昂,且难以准确反映结晶器内部复杂的流场和温度场分布。
因此,采用数值模拟方法进行深入研究显得尤为重要。
三维流热固耦合数值模拟技术能够有效地模拟结晶器内的流动、传热和固相变化等复杂过程,为优化连铸工艺、提高铸坯质量提供理论依据。
三、研究方法与模型建立本研究采用三维流热固耦合数值模拟方法,建立了板坯连铸结晶器内的物理和数学模型。
模型考虑了结晶器内部的流动、传热、相变以及材料性质等复杂因素。
通过建立合理的网格系统和边界条件,确保了模拟结果的准确性和可靠性。
四、结果与分析4.1 流场分析通过对结晶器内流场的模拟,我们得到了板坯连铸过程中流体的速度、流向和涡旋等详细信息。
分析表明,结晶器内的流场分布受到多种因素的影响,如浇注速度、结晶器形状和尺寸等。
优化这些参数可以有效改善流场的分布,从而提高铸坯的质量。
4.2 温度场分析模拟结果显示,结晶器内的温度场分布受到流体流动、热量传递和相变等多种因素的影响。
通过对温度场的分析,我们可以了解铸坯在凝固过程中的温度变化规律,为优化连铸工艺提供依据。
4.3 三维流热固耦合模拟结果将流场和温度场的结果进行耦合分析,我们可以得到结晶器内流体流动与传热的相互作用关系。
这有助于我们更全面地了解板坯连铸过程中的物理现象,为优化工艺参数提供有力支持。
五、讨论与展望本研究通过三维流热固耦合数值模拟方法对板坯连铸结晶器内的流动与传热行为进行了深入研究。
连铸结晶器温度场及热变形的数值模拟

d fr a o n ra e . T e rt fc o i g w tr h r a n u n e o h e e au e f l d t e a e o t n ic e s h ae o o l ae a g e ti e c n t e tmp rt r ed a h r l m i s n s l f i n m
Nu e ia i u a in o e o ma i n a d tm p r t r m rc lSm lto n d f r t n e e a u e o
i l fc ntnu u a tn u d fed o o i o sc si g m o l
K ANG i L ,W A n g n , HE J—h n NG E —a g i e g c
r t n atn p e n t e tmp r t r ed a d d fr t n o l e n e t ae . T e r s s ae a d c i g s e d o h e e u e f l n e o mai f mod w r i v si td h et s a i o e g e s o e h tw e a t g s e d i c e s s h mp r tr n eo ai n as n r a e . W h n t e m伽 l h w d t a h n c si p e n r a e .te t n e e au e a d d fr t l o ic s s m o e e h d
维普资讯
第 5卷 第 3期
20 0 6年 9月
材
料
与 台 金
学
报
Vo. . 15 No 3 S pt e .20 6 0
宽板坯连铸结晶器流场和温度场的数值模拟

宽板坯连铸结晶器流场和温度场的数值模拟
随着工业生产技术的不断发展,连铸技术已经成为宽板坯的主要生产方式,特别是在钢铁行业中,大量的钢铁产品均采用连铸工艺生产。
宽板坯连铸技术的核心是结晶器,结晶器的流场和温度场是宽板坯质量的关键因素,因此对流场和温度场进行数值模拟研究是必要的。
数值模拟能够对结晶器内部的流场和温度场进行快速、准确的计算,揭示了结晶器内的流场和温度场在宽板坯生产中的重要作用。
本文通过对结晶器内流场和温度场的数值模拟分析,提出了一种优化结晶器设计的方法。
首先,本文基于Navier-Stokes方程和热传导方程,建立了数学模型,考虑结晶器内部的流动载荷、热辐射、传导热和对流换热等因素。
其次,利用Fluent软件进行流场和温度场计算,得到了流场和温度场的数值解。
通过对数值模拟结果的分析,发现结晶器内部的流动较为复杂,主要存在四个涡旋,其中两个涡旋在底部,两个涡旋在上部。
涡旋的存在使得物料在结晶器内部获得了良好的混合,进一步提高了结晶器内物料的质量。
另外,结晶器内部的温度场也十分关键。
通过数值模拟结果可以看出,结晶器内部温度分布不均匀,底部温度较高,而顶部温度较低。
这是由于底部邻近铸坯熔池温度较高,导致底部结晶器的温度较高;而顶部的散热较快,导致顶部结晶器的温度较低。
最后,通过对数值模拟结果的分析得出,改变结晶器底部的形状,减少对流热损失,可以提高结晶器内部的温度分布均匀性,进而提高宽板坯的质量,同时也可以减少不必要的生产成本。
铸件凝固过程中热应力场及热裂的数值模拟研究分析.
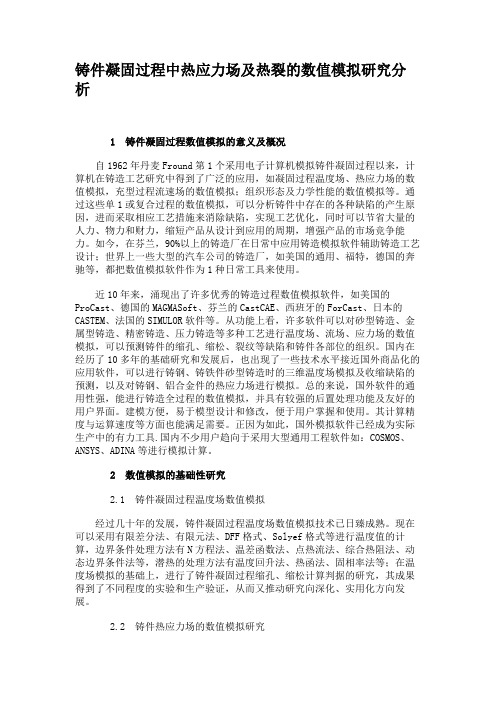
铸件凝固过程中热应力场及热裂的数值模拟研究分析1 铸件凝固过程数值模拟的意义及概况自1962年丹麦Fround第1个采用电子计算机模拟铸件凝固过程以来,计算机在铸造工艺研究中得到了广泛的应用,如凝固过程温度场、热应力场的数值模拟,充型过程流速场的数值模拟;组织形态及力学性能的数值模拟等。
通过这些单1或复合过程的数值模拟,可以分析铸件中存在的各种缺陷的产生原因,进而采取相应工艺措施来消除缺陷,实现工艺优化,同时可以节省大量的人力、物力和财力,缩短产品从设计到应用的周期,增强产品的市场竞争能力。
如今,在芬兰,90%以上的铸造厂在日常中应用铸造模拟软件辅助铸造工艺设计;世界上一些大型的汽车公司的铸造厂,如美国的通用、福特,德国的奔驰等,都把数值模拟软件作为1种日常工具来使用。
近10年来,涌现出了许多优秀的铸造过程数值模拟软件,如美国的ProCast、德国的MAGMASoft、芬兰的CastCAE、西班牙的ForCast、日本的CASTEM、法国的SIMULOR软件等。
从功能上看,许多软件可以对砂型铸造、金属型铸造、精密铸造、压力铸造等多种工艺进行温度场、流场、应力场的数值模拟,可以预测铸件的缩孔、缩松、裂纹等缺陷和铸件各部位的组织。
国内在经历了10多年的基础研究和发展后,也出现了一些技术水平接近国外商品化的应用软件,可以进行铸钢、铸铁件砂型铸造时的三维温度场模拟及收缩缺陷的预测,以及对铸钢、铝合金件的热应力场进行模拟。
总的来说,国外软件的通用性强,能进行铸造全过程的数值模拟,并具有较强的后置处理功能及友好的用户界面。
建模方便,易于模型设计和修改,便于用户掌握和使用。
其计算精度与运算速度等方面也能满足需要。
正因为如此,国外模拟软件已经成为实际生产中的有力工具.国内不少用户趋向于采用大型通用工程软件如:COSMOS、ANSYS、ADINA等进行模拟计算。
2 数值模拟的基础性研究2.1 铸件凝固过程温度场数值模拟经过几十年的发展,铸件凝固过程温度场数值模拟技术已日臻成熟。
板坯连铸结晶器流场物理与数学模拟研究

板坯连铸结晶器流场物理与数学模拟研究
1 连铸结晶器流场物理模拟
连铸结晶器流场物理模拟是研究连铸坯料结晶过程的一种重要手段,是利用数值模拟的方法,来模拟连铸拉管内坯料的运动及结晶发展状态。
模型的实际内容主要包括连铸坯料的宏观流场状态以及坯料中结晶物的运动规律等行为。
通过模拟,可以更客观准确的描述连铸结晶器内坯料的物理行为,从而深入了解坯料在结晶器内的运动规律及行为,为分析和优化结晶器厂内运行状况提供更全面及客观的评价依据。
2 连铸结晶器流场数学模拟
连铸结晶器流场的数学模拟是指通过构建连铸拉管内的坯料流场数学模型,以及采用恰当的结晶行为模型,通过数值计算模拟分析出连铸坯料结晶过程的流场行为。
数学模拟可以非常客观准确的描述在连铸拉管内坯料结晶时存在的热平衡性、液态结晶性及流场的发展变化规律,而且还能考虑到基于个体的细致行为,如晶粒大小、组分等及结晶动力学过程。
数学模拟可以作为理解坯料的运动过程的重要工具,帮助研究人员更深入了解结晶器内坯料的流场状态,有助于研究连铸结晶器内坯料的性能及实际运行情况。
3 结论
连铸结晶器流场物理模拟和数学模拟是目前研究连铸结晶器流场状态的有力手段,它们可以通过客观的数据和事实,来解释连铸坯料
的结晶过程及其运动规律,从而帮助研究人员更深入地探索问题本质及潜在机理,以此寻求更好的解决方案。
目前,已经有许多研究者采用这两种模拟方法,研究了连铸结晶器流场性质及变化规律,同时也得出了不少有益的结论与研究成果,但由于连铸结晶器流场特性复杂且简单模型化研究还存在不足,所以仍然需要持续深入探讨和研究才能进一步提高连铸结晶器的运行效率和能源使用效率。
165mm×165mm方坯连铸结晶器安全性的数值模拟分析
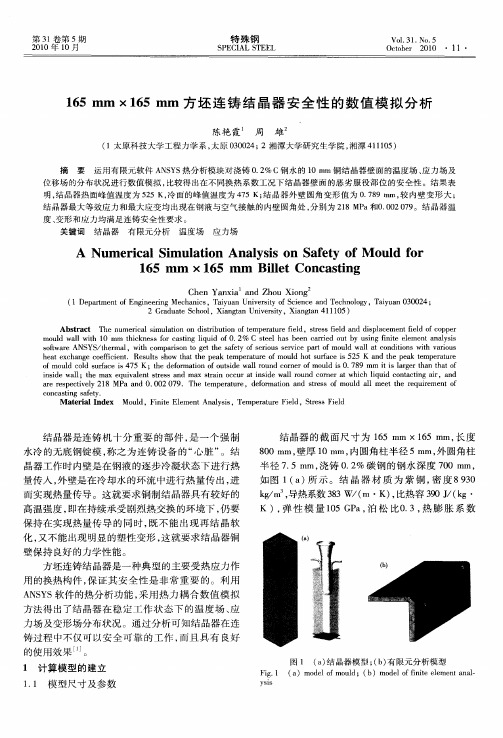
( e at n o n ie r gMe h nc , a u nU i r t o ce c n e h o g , ay a 3 0 4 1D p r me t f gn ei c a i T i a nv s y f in ea dT c n l y T iu n0 0 2 ; Eo a y i n S f t f M o l o Nu r c lS m a i n An l ss o a e y o u d f r 1 5 m m ×1 5 m m le n a tn 6 6 Bi t Co c si g l
c nc si g s f t o a tn aey.
第 3 卷 第 5期 1
21 0 0年 1 O月
特殊 钢
S PECI AL TEEL S
V0 . . 1 31 No. 5
Oco e 2 1 th r 0 0
・1 ・ 1
1 5 mm ×1 5 mm 方 坯 连 铸 结 晶 器 安 全 性 的 数 值 模 拟 分 析 6 6
s f r ot e ANS /t e ma .wih c mpa io o g tt e s ft fs ro evie p r fm o l Wala o diinswih v ro wa YS h r 1 t o rs n t e h ae y o e iuss r c a to ud l tc n to t a ius he te c a e c e fce t Re u t ho t a h e k tm p r t e o o d h ts f c s5 a h e k tmpe au e a x h ng o f in . i s ls s w h tte p a e e aur fm ul o ura e i 25 K nd t e p a e rtr
Q345大方坯连铸过程表面温度变化的数值模拟

图1结晶器出口铸坯断面温度场图2二冷段出口铸坯断面温度场圈3一矫点铸坯断面温度场图4切割点铸坯断面温度场段出口两者相同。
3一套攀翘芸描搿1.o倍、1.2倍、1.4倍的工况条仟珀月、里一……Q345大方坯连铸过程表面温度变化的数值模拟作者:丁秀青, 李大鹏, 李宏, 张炯明, 王恭亮, 梁玫作者单位:丁秀青,李大鹏,李宏(北京科技大学,冶金与生态工程学院,北京100083), 张炯明(北京科技大学,冶金与生态工程学院,北京,100083), 王恭亮,梁玫(石家庄钢铁有限公司,河北,石家庄,050031)刊名:炼钢英文刊名:STEELMAKING年,卷(期):2009,25(5)1.姜立东,李建军.包钢大方坯连铸机结晶器凝固传热的数值模拟[J].包头钢铁学院学报,2000,(2):134-137.2.张炯明,张立,杨会涛,等.板坯结晶器钢水凝固的数值模拟[J].北京科技大学学报,2004,(2):130-134.3.贾洪明,李惊鸿,李晓伟,等.厚板坯连铸凝固过程数值模拟[J].炼钢,2007,23(2):27-30.4.蔡开科,程士富.连续铸钢原理与工艺(第一版)[M].北京:冶金工业出版社,1994.5.王恩刚,杨泽宽,陈海耿,等.结晶器内连铸坯凝固过程的有限无数值模拟[J].东北大学学报,1996,17(4):384-387.6.李峰,张炯明.板坯动态二冷配水系统的开发与应用[J].中国冶金,2008,18(3):11-13.7.曹广畴.现代板坯连铸[M].北京:冶金工业出版社,1994.8.刘青,田乃媛,王英群,等.矩形坯连铸凝固传热的数学模型[J].钢铁,1997,32(2):28-32.9.Louhenkilpi S,Laitinen E,Niemincn R.Real-time simulation of heat transfer in continuouscasting[J].Metallurgical Transactions B,1993,24(4):685-691.10.E A Mizikar.Mathematical heat transfer model for solidification of continuously cast steelslabs[J].Trans.TMSAIME,1967,239:1747-1753.本文链接:/Periodical_lg200905012.aspx。
连铸凝固传热过程的数值模拟
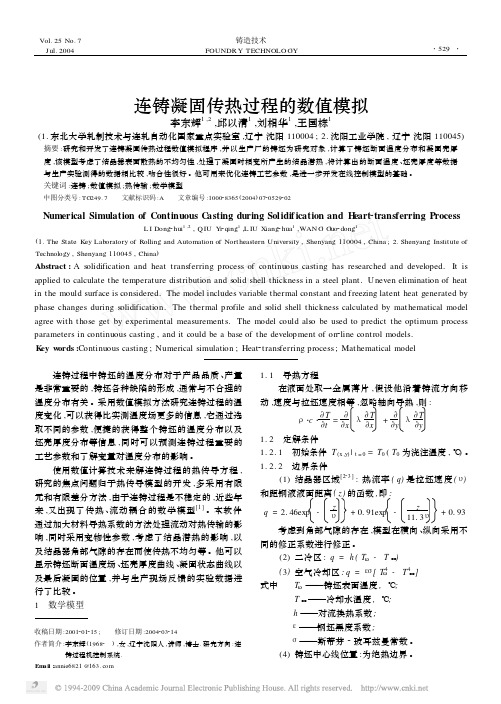
收稿日期:2001201215; 修订日期:2004203214作者简介:李东辉(19682 ),女,辽宁沈阳人,讲师,博士.研究方向:连铸过程机控制系统.Em ail :annie6821@连铸凝固传热过程的数值模拟李东辉1,2,邱以清1,刘相华1,王国栋1(1.东北大学轧制技术与连轧自动化国家重点实验室,辽宁沈阳110004;2.沈阳工业学院,辽宁沈阳110045)摘要:研究和开发了连铸凝固传热过程数值模拟程序,并以生产厂的铸坯为研究对象,计算了铸坯断面温度分布和凝固壳厚度,该模型考虑了结晶器表面散热的不均匀性,处理了凝固时相变所产生的结晶潜热,将计算出的断面温度、坯壳厚度等数据与生产实验测得的数据相比较,吻合性很好。
他可用来优化连铸工艺参数,是进一步开发在线控制模型的基础。
关键词:连铸;数值模拟;热传输;数学模型中图分类号:TG249.7 文献标识码:A 文章编号:100028365(2004)0720529202Numerical Simulation of Continuous C asting during Solidif ication and H eart 2transferring ProcessL I Dong 2hui 1,2,Q IU Y i 2qing 1,L IU Xiang 2hua 1,WAN G Guo 2dong 1(1.The State K ey Laboratory of Rolling and Automation of Northeastern University ,Shenyang 110004,China ;2.Shenyang Institute of Technology ,Shenyang 110045,China )Abstract :A solidification and heat transferring process of continuous casting has researched and developed.It is applied to calculate the temperature distribution and solid shell thickness in a steel plant.Uneven elimination of heat in the mould surface is considered.The model includes variable thermal constant and freezing latent heat generated by phase changes during solidification.The thermal profile and solid shell thickness calculated by mathematical model agree with those get by experimental measurements.The model could also be used to predict the optimum process parameters in continuous casting ,and it could be a base of the development of on 2line control models.K ey w ords :Continuous casting ;Numerical simulation ;Heat 2transferring process ;Mathematical model 连铸过程中铸坯的温度分布对于产品品质、产量是非常重要的,铸坯各种缺陷的形成,通常与不合理的温度分布有关。
宽板坯连铸结晶器流场和温度场的数值模拟
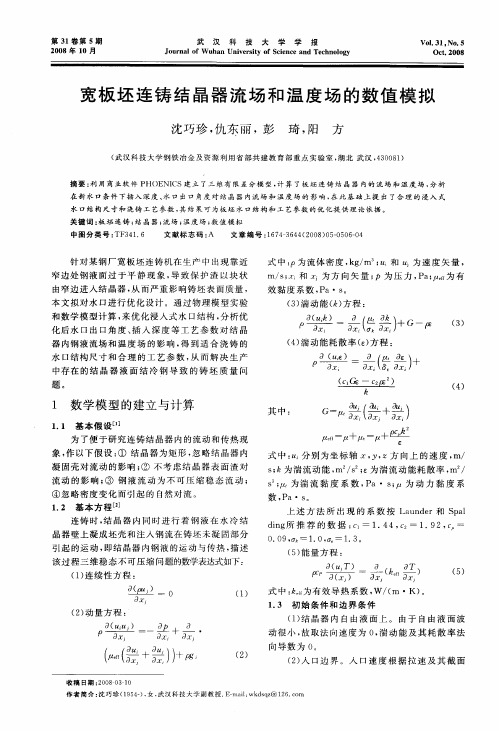
m/ ; 和 z 为方 向矢 量 ; s . P为 压 力 , a 为有 P;
效 黏 度 系 数 , a・ 。 P S
本 文拟对 水 口进行 优化设 计 。通 过物理 模 型实验
和 数学模 型计 算 , 来优 化 浸入式 水 口结 构 , 析优 分 化后 水 口出 口角 度 、 入 深 度 等工 艺 参 数 对结 晶 插 器 内钢液 流场 和 温度 场 的 影 响 , 到 适 合 浇铸 的 得 水 口结 构尺寸 和 合理 的工 艺参 数 , 而 解 决 生产 从
面积 给出 , 浇铸温 度 为 T 一15 0℃。 。 4
( ) 称 面 。对 称 面上 的 边 界 条件 与液 面 处 3对
收 稿 日期 : 0 80 0 2 0 — 31
作者 简 介 : 巧 珍 ( 9 4)女 , 汉 科技 大学 副 教 授 . — i: dq@ 1 6 Cr 沈 1 5一 , 武 E malwk sz 2 .O n
20 0 8年 第 5期
沈 巧珍 。 : 等 宽板 坯 连 铸 结 晶 器 流 场 和 温 度 场 的 数 值 模 拟
( ) 量方 程 : 2动
1 D
,
一 一矗 + . 十 ’
一 一
动很小 , 故取 法 向速度 为 0 湍 动 能及 其 耗 散 率法 ,
( 0+ a) P z ) g u u + , ,
d
向导数 为 0 。
() 2 ( ) 口边 界 2入
。
入 口速度 根 据 拉 速 及 其截 面
针对 某钢 厂宽板 坯连铸 机在 生产 中出现 靠近 窄边 处钢 液面 过 于平 静 现 象 , 导致 保 护 渣 以块 状 由窄边进 入结 晶器 , 而严 重影 响铸坯 表 面质量 , 从
宽厚板连铸过程温度场数值模拟

影响, 必须很 好地 加 以控制 .为 了尽 可 能地 减 少铸
坯 内部缺 陷 , 在二 冷 区对铸 坯 进 行 均 匀 而有 效 的 冷
DO NG a g F n ,W A NG h n — n ,L in c a ,CHE a — u Z a gl g IJa —h o i N Xio h i ( t i n ea ug ho, ne o gl n es f c neadT cnlg , at 10 0 C ia Ma r l dM t lr S ol InrM no aU i r t o i c n eh o y B o u0 4 1 , h ) e aa l yc i v i y Se o o n
21 02年 3月 第 3 卷第 1期 1
内 蒙 古 科 技 大 学 学 报
J u n lo n rMo g l i est fS i n e a d T c n lg o r a fI e n oi Un v ri o ce c n e h oo y n a y
M ac 2 2 r h, 01
Vo . 1 No 1 1 , . 3
文章 编 号 :0 5— 25 2 1 ) 1 0 4— 5 29 2 9 (0 2 O —0 1 0
宽厚 板 连 铸 过 程 温 度场 数值 模 拟
董 方, 王章岭 , 李建超 , 陈晓辉
( 内蒙古科技大学 材料与冶金学院 , 内蒙古 包头 04 1 ) 100
本 文通过 利用 A S S软件 采 用 运 动 坐标 系 的 NY 二维切 片法 , 拟计 算 了宽厚 板 连铸 过 程 的温 度 3模 J 场和应 力应变 状态 分 布 , 分析 了连铸 过 程 中板 坯 的 几 个关 键部位 温度 变化 和应 力应 变 状 况 , 实 际生 为 产 中铸 坯在进 人矫直 段避免 高温 脆性 区提供 参考 依
R9m连铸机小方坯结晶器流场和温度场的数值模拟

度 00 62k /m・) 导热 系数 3 ( K)热 膨胀 . g( s ; 0 4W/m・ ;
系数 0 0 K 。 . 01 ~ 0 21 基 本假设 .
A otl i 人耦合 计算 了结 晶器 内流场 、 buae 等 b 温度 场 以
及溶 质 的输运 行 为 , 算得 到 的结 果与试 验 测量 数 计
生 凝 固坯 壳厚 度 降低 。伴 随着 水 口浸入 深 度 的增 加, 内外 弧侧环 流 区均逐 渐增 大 。较 浅 的浸入 深度 导致 环 流区未 获得很 好 的发展 , 钢水 向上 回流速度 快 , 晶器 中钢 液 面易受 强烈 扰 动 , 成卷 渣 。 浸 结 造
收敛 标准要 求 , 各节 点质量残差 控制在 R S 0 。 M <1~
况, 分析 了不 同条件下 的结晶器 内流场 、 面波动 、 液 温度 分布及坯 壳厚度 。结 果表明 , 较小尺寸和浸入 深度 的水 口作用 在 下, 钢液对外弧壁面 的冲刷作用 明显 , 易降低 结晶器寿命 。随着水 口内径 和浸入深度 的增大 , 钢液面扰动减弱 , 易于防止卷
渣 。试验 条件下 , 采用 3 n 0I n内径水 口、0 10mm浸入深度较为合理。 关键词 : 小方 坯结晶器 ; 浸人式水 日; 流场 ; 温度场 ; 数值模拟
徐 永斌 , 马春武 , 幸 伟, 徐海伦
( 中冶南方T程技术有 限公 司 技术研究 院, 湖北 武汉 4 0 2 ) 3 2 3 摘 要 : 用 A S SC X 1 .软件 , 采 N Y F 21 对结晶器浸入式水 口的尺 寸和浸入深度进行建模 , 研究 了相应 的流场 和温度场分布情
23 数值求解 .
考 虑铸 坯 流 场 和 温度 场 分 布 的 对称 性 , 1 以 / 2 结 晶器 为模型 , 利用 A S SC X1.软件计算 。收 N Y F 21
圆坯连铸结晶器-铸坯温度场与浓度场数值模拟
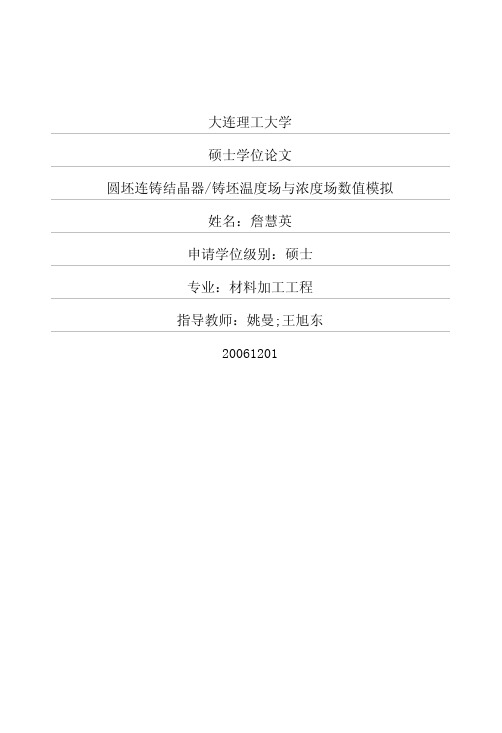
大连理工大学硕士学位论文圆坯连铸结晶器/铸坯温度场与浓度场数值模拟姓名:詹慧英申请学位级别:硕士专业:材料加工工程指导教师:姚曼;王旭东20061201圆坯连铸结晶器,铸坯温度场与浓度场数值模拟3结晶器/铸坯温度场与浓度场数值建模3.1引言连铸过程是一个复杂的物理化学过程,其内在规律不能完全由实测得到,应用数学模型对连铸过程进行模拟是一种有效的方法。
结晶器是连铸机核心设备之一,结晶器内钢液的凝固伴随着传热、传质、流动等复杂过程现象,充分了解结晶器内钢液的凝固过程有利于获得优质的铸坯,因此,针对结晶器与铸坯温度场和铸坯浓度场的数值计算。
具有很好的理论意义和实用价值。
目前我国已经建设了多台圆坯连铸机,而现有多数文献的报道常集中在板坯和方坯方面[13,14,55,弱J,对圆坯结晶器内铸坯凝壳规律研究不多,对于浓度场的研究更是鲜有报道。
针对此种情况,本章基于结晶器温度、热流实测数据,建立了圆坯连铸结晶器的三维传热模型,利用有限差分法对模型进行离散化处理,计算圆坯/结晶器的温度场和铸坯凝固过程结晶器内的热流分布,并根据已有的实测数据验证模型的正确性。
在准确计算结晶器与铸坯温度场的基础上,建立铸坯凝固过程中的溶质扩散模型,计算铸坯的固相率、浓度场和坯壳厚度分布。
本研究对预测铸坯质量和防止漏钢具有一定的参考意义。
3.2模型的提出本文主要研究圆坯连铸过程,根据圆坯形状的对称性特点,在圆柱坐标系内建立传热模型,整个模型区域的网格剖分图如图3.1所示,结晶器、保护渣的网格单元与铸坯基本相同。
图3.1模型计算区域网格示意图Fig.3.1Thediagramofnodeincomputaliondomain大连理工大学硕士学位论文随着距离弯月面越远铸坯温度越低;半径越大,温度越低,下降的速度越快。
图4.3(b)显示的是在不同高度处铸坯温度沿圆坯半径方向的变化。
由图可知,距离中心到60ram处铸坯温度保持在~个较为恒定的值,随着半径的增大温度逐渐降低;距离弯月面越远铸坯温度越低。
板坯连铸结晶器铜板温度场的数值仿真
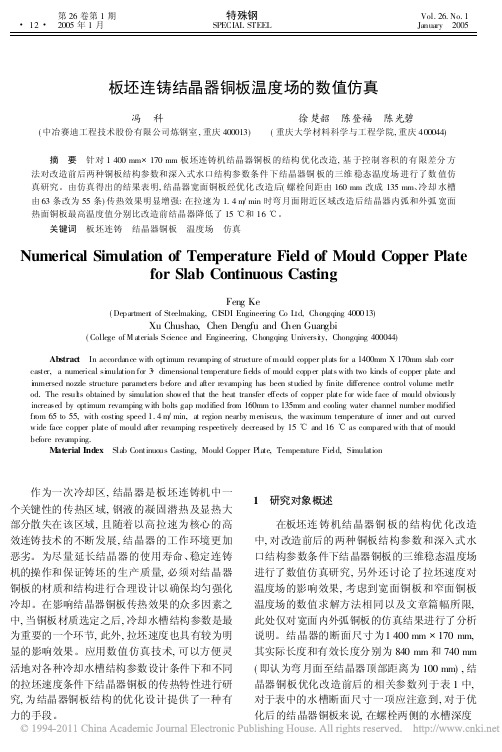
板坯连铸结晶器铜板温度场的数值仿真冯 科徐楚韶 陈登福 陈光碧(中冶赛迪工程技术股份有限公司炼钢室,重庆400013) (重庆大学材料科学与工程学院,重庆400044)摘 要 针对1400mm 170mm 板坯连铸机结晶器铜板的结构优化改造,基于控制容积的有限差分方法对改造前后两种铜板结构参数和深入式水口结构参数条件下结晶器铜板的三维稳态温度场进行了数值仿真研究。
由仿真得出的结果表明,结晶器宽面铜板经优化改造后(螺栓间距由160mm 改成135mm 、冷却水槽由63条改为55条)传热效果明显增强:在拉速为1.4m min 时弯月面附近区域改造后结晶器内弧和外弧宽面热面铜板最高温度值分别比改造前结晶器降低了15 和16 。
关键词 板坯连铸 结晶器铜板 温度场 仿真Numerical Simulation of Temperature Field of Mould Copper Platefor Slab Continuous CastingFeng Ke(Departmen t of Steelmaking,CISDI Engineering Co Ltd,Chongqing 400013)Xu Chushao,Chen Dengfu and C hen Guangbi(College of M aterials Science and Engineering,Chongqing Universi ty,Chongqing 400044)Abstract In accordance with op timum revamping of structure of mould copper plats for a 1400mm X 170mm slab con caster,a numerical si mulation for 3 dimensional temperature fields of mould copper plats with two kinds of copper plate and i mmersed nozzle structure parameters before and after revamping has been studied by finite difference control volume meth od.The resul ts obtained by simulation showed that the heat transfer effects of copper plate for wide face of mould obviously increased by optimum revamping with bolts gap modified from 160mm to 135mm and cooling water channel number modified from 65to 55,with costi ng speed 1.4m min,at region nearby meniscus,the waximum temperature of inner and out curved wide face copper plate of mould after revamping respeetively decreased by 15 and 16 as compared with that of mould before revamping.M aterial Index Slab Continuous Casting,Mould Copper Plate,Temperature Field,Si mulation作为一次冷却区,结晶器是板坯连铸机中一个关键性的传热区域,钢液的凝固潜热及显热大部分散失在该区域,且随着以高拉速为核心的高效连铸技术的不断发展,结晶器的工作环境更加恶劣。
连铸机数值模拟要点
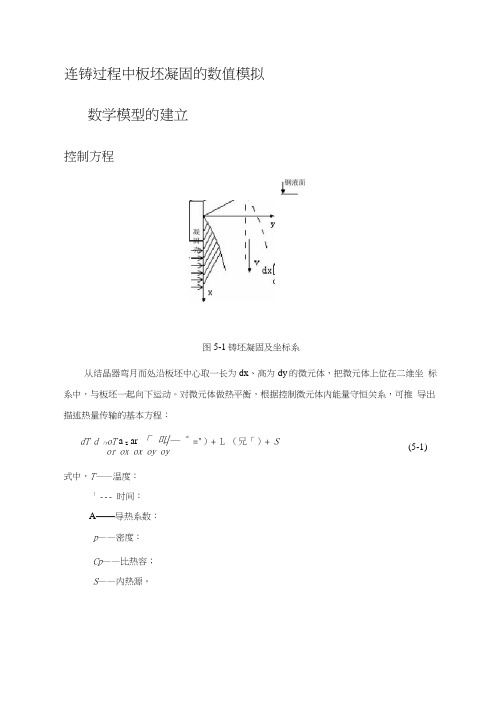
连铸过程中板坯凝固的数值模拟数学模型的建立控制方程图5-1铸坯凝固及坐标系从结晶器弯月而处沿板坯中心取一长为dx、髙为dy的微元体,把微元体上位在二维坐标系中,与板坯一起向下运动。
对微元体做热平衡,根据控制微元体内能量守恒关系,可推导出描述热量传输的基本方程:dT d /y oT a z ar 「叫—= =")+ L (兄「)+ S(5-1) or ox ox oy oy式中,T——温度:1 --- 时间:A——导热系数:p——密度:Cp——比热容;S——内热源。
定解条件(1) 初始条件:T = T C (浇注温度) (2) 边界条件:结晶器:在结晶器冷却区,结晶器器壁的热流密度是拉坯速度和距钢水液而距离的函数,这一函 数是由savage 和pritchard 提岀并由Davies 实验确左。
q = 2.64exp(~—) + 0.91 exp(-—-—) + 0・93MW / nrv 11.3v式中:q 一一热流密度:v -------拉速:z ——距钢水液面距离。
二冷区:q = h(T b -T f )(w/m 2)式中:h ——对流换热系数:T h ——板坯表而温度: T f 一一冷却水温度:空冷区:q =刃[(耳 + 273 )4 -(7;)+273)4] (W/m 2)(5-4)式中,8——物体黑度;CT 一一韦斯蒂芬-波尔兹曼常数: T.——外部环境温度。
本项目中涉及的板坯无空冷区O内热源项的消除与凝固潜热的等效对于同一铸件液相的内能疋丄大于固相的内能E"因此当合金凝固由液相转变为固相 时,必然要产生^E = E L _E S 的内能变化,这个内能变化量(通常用厶表示)成为凝(5-2)(5-3)固潜热。
潜热释放是凝固过程区别于一般导热过程的显著特点。
由于潜热释放,会明显降低铸件的冷却和凝固速度,傅立叶方程由于潜热的释放,实际变成了具有内热源的温度场,如图5-1 所示。
结晶器内钢液流动、温度分布及凝固过程的数值模拟 - Copy
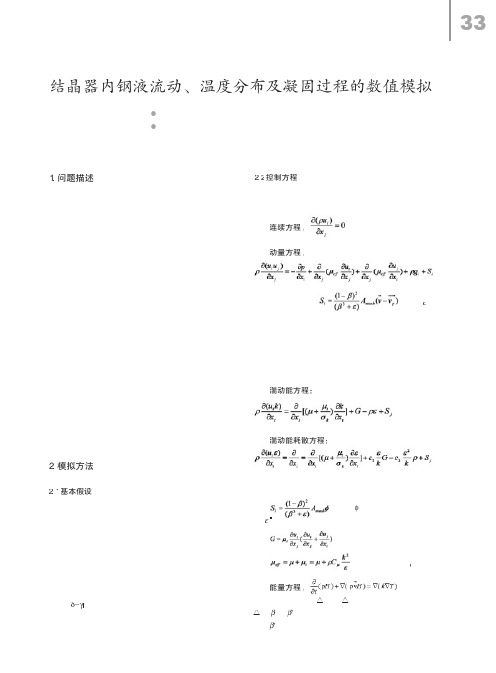
本文针对两种不同水口类型的结晶器进行了流
高性能计算应用
场、温度场和凝固进行了模拟。结果表明:钢液从 水口出口处喷出,其撞击到结晶器侧壁的冲击位置 与水口类型相关,沿水口出流方向,钢水分离形成 上下两股,并分别发展成两个回流;对于相同断面 不同类型的水口,在圆形水口(SEN1)附近,温度 分布比较均匀,流场混合充分,在计算区域的出口 处凝固要好于方形水口(SEN2)。模拟结果对于优 化设计连铸机具有帮助意义。
2)对称面 在对称面上,所有变量的垂直地读均设为零,
,u = 0;
,v = 0。
3)出口
在计算区域的出口处利用充分发展的条件,所
有变量(速度、湍流量、温度)的垂直梯度均为零。
4)壁面
结晶器内壁包括浸入式水口壁面附近的粘性边
界层中,湍流计算一般采用低雷诺数的
模型或
壁面函数法。采用
模型方法,壁面无需进行特
H=βL,β为液相的体积分数,有如下的定义:
β=0,当T < Tsolidus
34
《高性能计算发展与应用》 2008年第三期 总第二十四期
β=1,当T > Tsolidus
β
,当Tsolidus < T < Tliquidus
2.3 数值方法及网格 本文采用有限体积法对控制方程进行离散,交
35
36
《高性能计算发展与应用》 2008年第三期 总第二十四期
计算区域的出口处液相分数等于0.5的等值线右端所 示。在结晶器窄面附近,相同断面来说,SEN1的凝 固率要大于SEN2。而在离结晶器窄面较远的位置, SEN1和SEN2基本上都是充分发展流动,因而两种水 口凝固相差不大。
(Uin)根据不可压缩流体进出口质量守恒原理计算 得到,假定入口速度均匀,u = 0,v = 0,w = Uin,k = 0.01Uin2,ε = k1.5/Rnoz,h = CpTin,湍动能以及湍流耗散 率根据经验公式来选取。入口速度通过拉速换算。 在此计算过程中,两种水口类型选取相同的拉速。
宽板坯连铸结晶器三维流场与温度场的数值模拟的开题报告

宽板坯连铸结晶器三维流场与温度场的数值模拟的开题报告一、选题背景和意义宽板坯连铸技术目前已在钢铁工业的生产中广泛应用。
连铸过程中,结晶器的性能直接影响铸坯的质量和表面质量。
因此,研究宽板坯连铸结晶器内部的流场与温度场,对提高宽板坯连铸的生产效率和质量具有重要的意义。
目前,结晶器内部流场与温度场的研究主要依赖于实验方法,但实验成本高、周期长,而且实验过程存在难以控制的因素。
因此,采用数值模拟方法,结合计算机技术,可以有效地研究结晶器内部流场与温度场。
二、研究内容和方法本文主要研究宽板坯连铸结晶器内部的流场与温度场,依据宽板坯连铸结晶器的结构特点,建立三维流场模型和温度场模型。
对结晶器内部的流动和传热过程进行模拟,得到流体运动状态和液相/固相相变过程的温度分布规律,并分析钢坯内部组织结构的变化。
本文计划采用计算流体力学(CFD)方法,结合有限元法(FEM)对宽板坯连铸结晶器内部的流场与温度场进行数值模拟。
具体操作分为以下几个步骤:1. 根据实际情况建立宽板坯连铸结晶器模型,并确定模拟的范围和边界条件。
2. 进行网格划分,将结晶器模型离散化,生成计算网格。
3. 根据有限元法和控制方程建立数学模型,并进行求解。
4. 根据计算结果分析流场和温度场内部的变化规律,展开数值仿真计算。
三、研究目标和预期成果1. 建立宽板坯连铸结晶器的三维流场和温度场数学模型。
2. 对结晶器内部的流动和传热过程进行数值模拟,得到流体运动状态和液相/固相相变过程的温度分布规律,并分析钢坯内部组织结构的变化。
3. 在数值模拟的基础上,对结晶器内部的结构参数和工艺参数进行优化和分析,提高铸坯的质量和表面质量。
预期成果:基于数值模拟技术对宽板坯连铸结晶器结构参数和工艺参数进行优化和分析,提高铸坯的品质和表面质量。
四、工作计划和进度安排本研究计划分为以下四个阶段:1. 研究阶段一(前期准备阶段)、制定计划和开题报告、收集文献资料,2022年9月-11月完成。
- 1、下载文档前请自行甄别文档内容的完整性,平台不提供额外的编辑、内容补充、找答案等附加服务。
- 2、"仅部分预览"的文档,不可在线预览部分如存在完整性等问题,可反馈申请退款(可完整预览的文档不适用该条件!)。
- 3、如文档侵犯您的权益,请联系客服反馈,我们会尽快为您处理(人工客服工作时间:9:00-18:30)。
第5卷第3期材 料 与 冶 金 学 报Vol 15No 13 收稿日期:2006-03-27 基金项目:国家自然科学基金资助项目(No .50274023);国家高新技术研究发展计划项目(No .2001AA337040). 作者简介:康丽(1977-),女,山西晋中人,东北大学博士研究生,E -mail:kangli_erni@sina .com.王恩刚(1962-),男,辽宁沈阳人,东北大学教授,博士生导师。
赫冀成(1943-),男,辽宁瓦房店人,东北大学教授,博士生导师.2006年9月Journal ofMaterials and MetallurgySep t .2006连铸结晶器温度场及热变形的数值模拟康 丽,王恩刚,赫冀成(东北大学 材料电磁过程研究教育部重点实验室,辽宁沈阳110004)摘 要:利用MARC 有限元软件建立了圆坯结晶器的三维温度场与应力场耦合的热弹性模型,并在此基础上研究了结晶器厚度、冷却水流速以及拉坯速度对结晶器温度场和铜管变形的影响规律.模拟结果表明:拉速提高时,结晶器的温度和变形量都增大,但影响不显著;结晶器厚度增大时,铜管冷面温度降低,热面温度升高,同时变形增大;冷却水流速对铜管温度分布和变形量有较大影响,增大冷却水流速,铜管温度和变形量均下降.关键词:连铸;结晶器;温度场;变形;MARC中图分类号:TF 777 文献标识码:A 文章编号:167126620(2006)0320190205Nu m er i ca l S i m ul a ti on on deforma ti on and tem pera turef i eld of con ti n uous ca sti ng m ouldK ANG L i,WANG En 2gang,HE J i 2cheng(The Key of Laborat ory of Electr omagnetic Pr ocessing of Materials (M inistry of Educati on ),Northeastern University,Shenyang 110004,China 1)Abstract:A 3-D model was devel oped f or the coup ling of te mperature field and stress field in r ound -billet continuous casting mold by means of M arc s oft w are 1The influences of mould thickness,cooling water rate and casting s peed on the te mperature field and def or mati on of mold were investigated 1The results showed that when casting s peed increases,the temperature and defor mati on als o increases 1W hen the mould thickness increases,the te mperature of cold face decreases,that of the hot face increases,and the mold def or mati on increases 1The rate of cooling water has great influence on the te mperature field and ther mal def or mati on 1I ncreasing the cooling water rate will decrease both the temperature and defor mati on of the mould 1Key words:continuous casting;mould;te mperature field;def or mati on;Marc 钢水在结晶器中冷却凝固形成坯壳是连铸的重要环节.其中的传热过程对铸坯质量具有至关重要的影响.但是在结晶器的传热过程中,由于结晶器铜管的受热膨胀和铸坯的冷却收缩,不可避免地会在坯壳与铜管之间产生气隙[1],这将极大地降低结晶器的传热效果.因此研究掌握结晶器的温度场和应力场的变化规律具有重要的意义.多年来,众多冶金工作者对这一问题进行了研究.郭佳[2]等将三维温度场分析简化为二维,忽略了结晶器拉坯方向的传热,建立了板坯结晶器铜板二维非稳态传热数学模型,研究了铜板的温度场分布;杨甲申[3]等考虑了结晶器铜板内侧面镀层对温度场的影响,将铜板温度场简化为无内部热源的平面稳态温度场来进行计算;还有的研究者对热应力应变分析采用平面应变或者平面应力分析[4,5];计算中不考虑温度场和应力场的耦合关系,将温度场的计算结果作为应力场分析的边界条件[6].纵观以上研究,由于三维模型建模的困难,研究者基于各种假设,多将实际问题作了简化.事实上铜板的热应力分析属于材料非线性问题,温度改变的同时,铜板材料的热力学参数也在发生变化,分开考虑必然会带来一定的误差.为更全面地模拟结晶器铜管的温度场和变形,本文采用大型有限元软件MARC 建立了研究连铸结晶器的三维温度场和应力场耦合的热弹性模型,并在此基础上分析了铜管厚度、冷却水流速、拉坯速度等因素对温度和热变形的影响,为结晶器的优化设计提供了理论依据.1 数学模型计算结晶器为<178mm 连铸圆坯水冷结晶器,长度780mm.建立连铸结晶器铜管变形和温度场数值模型时作如下假定:(1)冷却水属于强制对流,冷却水与钢制外水套之间传热忽略不计;(2)假定结晶器铜管的导热系数为各向同性,其密度、导热系数和比热视为常数,计算中只考虑热膨胀系数随温度的变化;(3)结晶器振动和钢水的波动对传热影响不计;(4)结晶器应力计算满足小变形理论.111 结晶器铜管变形和温度场耦合计算方法对体积为V,边界为S 的连续介质,根据热力学第一定律可写出能量守恒方程[7]:∫VρV i9V i 9t d V +∫Vρ5U5t d V =∫Vρ(珚Q +b i v id V +∫S(ρi v i -H )d S (1)其中,ρ是密度,v 1是速度场,U 是给定内能,珚Q 是给定体积热流,b i 是给定体积力,P i 是单位面积上的边界力,H 是边界S 上的单位面积的热流强度.当上式对物体中任一部分体积都成立时,根据柯西第一定理,引入柯西应力分量σij ,压力可用柯西应力表示为:P i =n i σij(2)其中,n i 表示表面S 的单位外法线向量.对同一体积为V,边界为S 的连续介质,可建立积分形式的力平衡方程:∫Vρ(b i -5v i5t )d V =∫SP i d S (3)将力平衡方程引入能量守恒方程,可得热-应力耦合的能量守恒方程:∫V{ρ(珚Q -5U 5t )+σij 5v i5x i}d V =∫SH d s (4)其中,上式左端第二项的被积函数对应于单位体积的变形功率.依据虚功原理,可建立结构位移u i 所需满足的下式:∫Vσij5δu i x i d V =∫V ρb i δu i d V -∫Vρ5v i5t δu i d V (5) 进一步假设可忽略惯性项的影响,则式(5)右端第二项可去掉.并且假设物体的能量方程和力平衡方程都是建立在当前的构型上;因此,可用弱耦合的增量非线性有限元法处理热-应力耦合问题.在每个增量步开始时,由当前位移增量修正域V 和边界S,并且在增量步内交替迭代力平衡方程和能量守恒方程.收敛后,在同一增量步中,更新温度值,评价材料力学性质和热应变,迭代求解力平衡方程,收敛后,进行下一增量步的分析,直到所需的增量步结束.112 边界条件(1)钢水与铜管交界面,施加于结晶器的热流量q m ,本文根据圆坯生产现场实测数据,对常采用的热流公式[8]进行修正.在MARC 具体实施上编写F ORCE M 子程序在结晶器内壁施加随空间位置变化的热流量.式中L 为距结晶器顶端的距离,m;V 为拉速,m /s .-k5t5r=q m(6)q m =112×(2680-315×L /V )k W /m 2(7) (2)结晶器与冷却水接触面,不考虑冷却水的沸腾换热,换热系数视为常数.-k5t 5r=αw (t -t w )(8) (3)结晶器铜管内侧、上侧和下侧未接触钢水处,按辐射条件处理,具体处理时将热辐射等效成一种对流放热系数随温度变化的非线性对流边界条件.q f =h (T S )(T S -T ∞)(9)其中等效的非线性对流放热系数h (T S )为:h (T S )=σε(T 2S +T 2∞)(T S +T ∞)(10) (4)固定位移边界条件,结晶器上端固定下端允许自由膨胀.即约束结晶器上端平面上的节点使u =v =w =0(11)2 有限元计算利用大型有限元软件MARC2003,采用单元191第3期 康 丽等:连铸结晶器温度场及热变形的数值模拟类型为3D -S OL I D 六面体7号单元,同时计算温度场和应力场,共划分节点28440个,六面体单元23400个.计算中涉及的物性参数如表1~表3所示.表1 计算中采用的物性参数Ta b l e 1 p hysi ca l p r op e rty p a ram e te rs物性参数取值密度/kg ・m-38940比热/J ・(kg ・℃)-1700导热系数/J ・(m ・s ・℃)-1380弹性模量/GPa110计算拉速/m ・m in-1116泊松比0136冷却水温度/℃进口出口3540结晶器换热系数J ・(m 2・s ・℃)-1热面与钢液辐射换热系数[9]上下侧与空气辐射换热系数[9]与冷却水的对流换热系数111×10-6111×10-6321102表2 铜的热膨胀系数Ta b l e 2 The the r m a l exp a n s i o n co effi c i e n to f the copp e r m o u l d温度/℃1571127227327427527热膨胀系数/10-61512151716151716181318191914表3 铜管的屈服应力Tab l e 3 The yi e l d s tre ss o f the copp e r m o u l d温度/℃25100200300400屈服应力/M Pa187138183149166169141117119143 计算结果与分析应用上面提出的三维温度场和应力场耦合的热弹性模型,计算了当拉速为116m /m in,冷却水流速为10m /s 时结晶器壁的温度分布与径向变形量.311 结晶器壁温度分布图1为计算出的结晶器冷热面的温度分布,从图中可以看出,铜管冷热面温度变化趋势一致,在结晶器上部由于铜管未与钢液接触,温度相对较低.铜管最高温度出现在距上口位置约150mm 处,约位于弯月面偏下50mm 处,这是因为铜管自由表面高度处与上部存在较大温度梯度,发生热量传递使温度最高值向下移动.当前计算条件下,结晶器热面温度峰值为19714℃,低于铜的软化温度;结晶器冷面温度峰值为11018℃,低于水的形核沸腾温度.图1 沿拉速方向结晶器冷热面径向温度分布F i g.1 The tem p e ra tu re d is tri bu ti o n a l o ng ca s ti ng d irec ti o n312 结晶器壁热变形分析由于非均匀温度场的存在,结晶器壁将发生变形.如图2所示,冷热面变形趋势一致,相同高度上,冷面变形量大于热面变形量.这是因为结晶器冷面与冷却水存在强烈的对流换热现象,温度梯度大,热变形比较大.与温度分布相对应,铜壁最大变形量也不出现在自由表面处,而是向下偏移了一定距离.值得注意的是热变形使结晶器沿高度方向产生不同的锥度.在结晶器内壁上部产生的负锥度,大小约为212%/m ,这部分负锥度加大了铸坯与铜管之间的气隙,增加了界面热阻.在结晶器铜管下部产生的倒锥度约为0125%/m ,小291材料与冶金学报 第5卷于结晶器的设计锥度.图2 沿拉速方向结晶器冷热面径向变形分布F i g.2 The defo r m a ti o n d is tri bu ti o n a l o ng ca s ti ng d irec ti o n313 连铸参数对铜管温度场和变形的影响31311拉速的影响表4列出了冷却水流速为10m /s,不同拉速下结晶器冷热面的温度最大值,随着拉速的提高,铜管的冷热面温度均有升高,当拉速从116m /m in 升高到210m /m in 时,温度升高了113~218℃,即平均拉速每提高012m /m in,温度升高0165~114℃,可见拉速对结晶器温度场的影响较小,在提高拉速时应该考虑使结晶器温度低于它的软化温度.表4 不同拉速下结晶器铜管温度与变形量峰值Ta b l e 4 The p e ak va l ue s o f the m o u l d tem p e ra tu re anddefo r m a ti o n unde r d i ffe ren t ca s ti ng sp ee d s拉速m m in -1温度/℃ 冷面 热面 变形/mm 冷面 热面 116110181971401201201176711811115198190120420118012101121120012012060011809 对铜管的变形来说,随着拉速的提高,冷热面变形量均变大.当拉速由116m /m in 提高到210m /m in 时,热面变形量增加了约0101mm.虽然变形量很小,而且整个结晶器长度方向上,加工锥度上下尺寸差也仅在几个毫米的数量级,但在拉坯过程中,即使是这么小的变形量也会对传热产生影响.31312 结晶器壁厚度的影响表5列出了冷却水流速10m /s,拉速116m /s 时,不同壁厚条件下铜管温度和变形量的峰值.计算发现,随着壁厚的增加,在结晶器热面上温度升高,冷面上温度降低,即结晶器壁沿径向的温度梯度增大了.这是由于壁厚增加,结晶器热阻增大所致.同时结晶器壁的变形也增大了.因此,在保证强度的前提下,结晶器壁不宜太厚.表5 不同壁厚条件下铜管温度和变形量峰值Tab l e 5 The p e a k va l ue s o f the m o u l d tem p e ra tu re a nddefo r m a ti o n unde r d i ffe ren t m o u l d th i ckne s s壁厚mm温度/℃ 冷面 热面 变形/mm 冷面 热面 13110181971401201201176717107102161501221501178221104132361901241601179231313 冷却水流速的影响由表6知,保持拉坯速度116m /m in 不变,随着冷却水流速从6m /s 增加到12m /s,结晶器壁温度平均降低了约45℃.因为水流速度增加,换热系数h 增大,铜管与冷却水的热交换增强了.数值计算结果显示,冷却水流速对结晶器的温度场影响较大,适当增加冷却水流速有利于结晶器的换热.当前计算条件下,冷却水流速低于9m /s 时,结晶器冷面温度将达到120℃,可能导致冷却水形核沸腾.间歇沸腾将使温度场周期性变化,对传热不利.国外学者较早发现了这个问题,Sa marasekera 和B ri m acombe 率先建立了考虑冷却水沸腾的结晶器温度场模型[10~12].由于冷却水形核沸腾,在结晶器铜管冷面局部区域经常发现水垢,使结晶器传热能力下降,结晶器变形增加,大大降低了结晶器铜管的寿命.如表6所示,随着冷却水流速的提高,结晶器壁温度下降的同时变形量也减小了,弯月面处形391第3期 康 丽等:连铸结晶器温度场及热变形的数值模拟成的负锥度变小,气隙减小,有利铸坯的凝固.表6 不同冷却水流速下铜管温度和变形量峰值Ta b l e6 The p e ak va l ue s o f the m o u l d tem p e ra tu re and de f o r m a ti o n unde r d i ffe re n t coo li ng w a te r ra te s冷却水流速m s-1温度/℃ 冷面 热面 变形/mm 冷面 热面 6147122331401271601232191181220416012145011883101101819714012012011767121021218910011861011635 4 结 论利用MARC软件建立了连铸结晶器铜管的三维温度场与应力场耦合的热弹性数值分析模型,研究了结晶器厚度、冷却水流速以及拉坯速度对结晶器壁温度和变形的影响规律.模拟结果表明:(1)随着拉速的提高,结晶器壁的温度和变形量随之增大,平均拉速每提高012m/m in,温度升高0165~114℃.(2)随着结晶器壁厚度增大,结晶器铜管冷面温度降低,热面温度升高,沿径向的温度梯度增大.同时结晶器壁的变形也增大.因此,在保证强度的前提下,结晶器壁不宜太厚.(3)冷却水流速对结晶器壁温度分布和变形均有较大的影响,增大冷却水流速,铜管温度和变形量都有所下降,有利于铸坯凝固换热.当铜壁厚度为13mm,拉坯速度为116m/m in,冷却水流速度大于9m/s时,满足工作要求.参考文献:[1]王恩刚,杨泽宽,陈海耿,等.气隙对连铸坯凝固影响的有限元数值模拟[J].钢铁,1996,31(11):22-26.[2]郭佳,蔡开科.板坯连铸结晶器铜板温度场研究[J].炼钢,1994,6:27-31.[3]杨甲申,赵敏,张继强.连铸机结晶器铜板温度场分析[J].重型机械,2003,6:12-14.[4]崔小朝,刘才.结晶器铜管变形和临界压力分析[J].燕山大学学报,1999,23(4):327-330.[5]杜素周,张丙奇,张少军,等.漏斗结晶器热应力的研究[J].重型机械,2003,3:17-19.[6]王宝峰,谢延敏,麻永林.小方坯高速连铸时结晶器应力场有限元模拟[J].包头钢铁学院院报,2003,22(3):201-207.[7]黄筑平.连续介质力学基础[M].北京:高等教育出版社,2003.141-143.[8]刘新,赵连刚,张富强.拉速条件下板坯连铸结晶器铜板温度场研究[J].重型机械,2000,6:13-15.[9]Kelly J E,M ichalek K P,O’Connor T G,et al.I nitialDevel opment of ther mal and stress fields in continuously caststeel billets[J].Metallurgical Transacti ons A,1988,19A(10):2589-2600.[10]Sa marasekera I V,Anders on D L,B ri m acombe J K.Thether mal dist orti on of continuous-casting billet molds[J].Metallurgical Transacti ons B,1982,13B:91-104.[11]Sa marasekera I V,B ri m acombe J K.The influence of moldbehavi or on the p r oducti on of continuously cast steel billets[J].Metallurgical Transacti ons B,1982,13B:105-106. [12]Sa marasekera I V,B ri m acombe J K.The ther mal field incontinuous casting moulds[J].Canadian MetallurgicalQuarterly,1979,18:251-266.491材料与冶金学报 第5卷。