VLRR
sqe工作月度总结报告
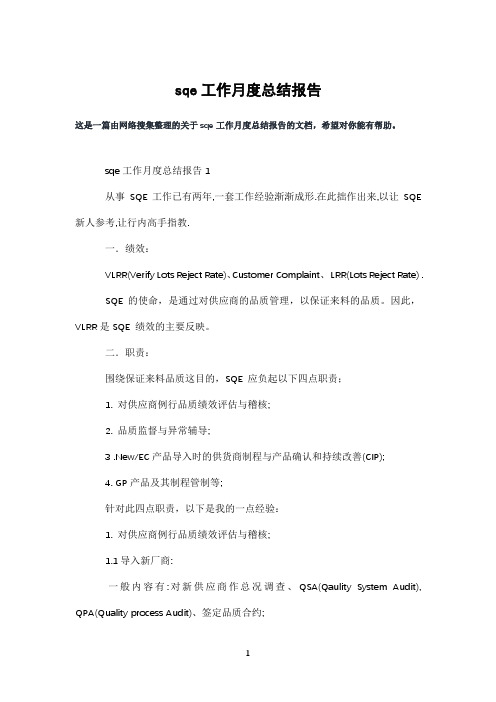
sqe工作月度总结报告这是一篇由网络搜集整理的关于sqe工作月度总结报告的文档,希望对你能有帮助。
sqe工作月度总结报告1从事SQE工作已有两年,一套工作经验渐渐成形.在此拙作出来,以让SQE 新人参考,让行内高手指教.一.绩效:VLRR(Verify Lots Reject Rate)、Customer Complaint、LRR(Lots Reject Rate) .SQE 的使命,是通过对供应商的品质管理,以保证来料的品质。
因此,VLRR是SQE 绩效的主要反映。
二.职责:围绕保证来料品质这目的,SQE 应负起以下四点职责;1. 对供应商例行品质绩效评估与稽核;2. 品质监督与异常辅导;3 .New/EC产品导入时的供货商制程与产品确认和持续改善(CIP);4. GP产品及其制程管制等;针对此四点职责,以下是我的一点经验:1. 对供应商例行品质绩效评估与稽核;1.1导入新厂商:一般内容有:对新供应商作总况调查、QSA(Qaulity System Audit), QPA(Quality process Audit)、签定品质合约;1.2供应商例行品质绩效评, 每月评分与制程稽核QPA;每月评分三要素TQR: Technology. Quality. Response;每月一评,评分结果分A/B/C/D等级。
1.3 制程稽核(QPA)每季度末由SQE制定下季度的稽核计划.制程稽核方式:针对不同的站别, including Receiving Inspection、Warehouse、MRB、P/L、Secondary Operations、OQC、Packing and Stock and so on.总结起来,重点项目由人、机、料、法、环五项构成,具体事项按公司QPA List点检。
人:1. 培训 2. Comply WI/SOP ;机:3 设备/校验。
4 治具/测量;料:5. 物料分区. 6 保存期/保存方式;法:7 可追溯性; 8. SPC, 自检, CLCA检讨;环:9 安全防护. 10 湿/温度;QSA 通常每年一评。
品质指标名词解释

Quality Index Defination 品质指标名词解释1.0 目的統一、規范本公司常用的品質指標的定義,包括中英文解釋、定義、公式、及其報告的格式。
以下按照從廠外到廠內(COPIS)的順序,把常見的品質指標加以說明,其中包括:CIT、AFR、DOA&客戶端LRR、客戶端VLRR、COQ、TAT、FPY (直通率)、制程不良率、制程來料不良率、MQA 判退率、CAR結案率、SCAR結案率、IQA LRR(進料批退率)、IQA VLRR(廠商來料批退率)2.0 範圍MSIS all QA Dept.3.0 組織與權責MSIS由Function QA定義制定; 由MSIS all QA Dept. 實施並執行。
4.0 流程圖無5.0 作業內容、規定、注意事項5.1 CIT5.1.1 CIT中英文對照中文:客訴追蹤報告English: Customer Incidents Tracking log5.1.2 CIT定義CIT是為了有效地、系統地對客戶端發生的品質異常進行追蹤紀錄,而由CQS制作並更新維護的追蹤報告。
(daily report)CIT單位:件數。
CIT Qty:即客訴發生的件數。
CIT的定義范圍如下,共12條:5.1.2.1板子/零件燒毀5.1.2.2批量性不良(包括集中性高不良)5.1.2.3會引起重工的(包括廠內和廠外sorting & rework)5.1.2.4造成廠內hold貨的客訴問題(即影響到廠內出貨)5.1.2.5造成客戶端停線/退貨的客訴問題5.1.2.6 Workmanship issue和制程問題需100%提報(此問題可highlight給廠內改善)5.1.2.7屬MSI的廠商來料不良的客訴問題5.1.2.8 Design 問題5.1.2.9客人Audit重大缺失項5.1.2.10客人發正式的異常通知單或者要求回復正式的改善報告5.1.2.11屬CID的問題也需要報告CIT(不會影響客訴減半的KPI)5.1.2.12廠商直接出貨到客人端以及外包產品,在客戶端出現問題均需要提報CITCIT Website address:首頁-2007>系統整合>未結案系統> Customer Incidents Tracking Log5.1.3 CIT公式Weekly CIT Qty:當周提報的CIT Qty累加之和。
sqe工作经验谈
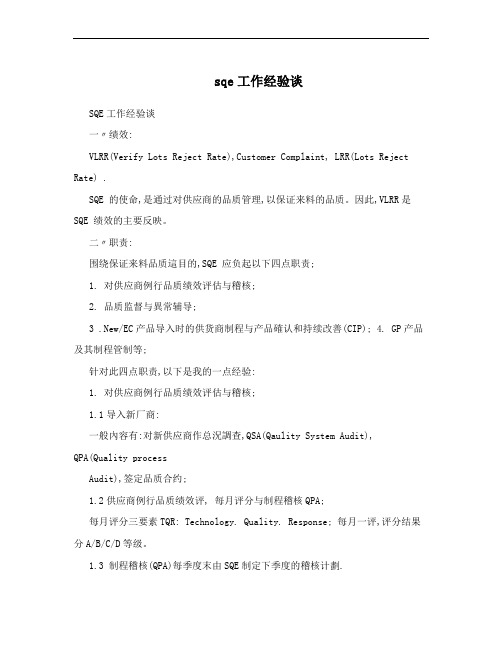
sqe工作经验谈SQE工作经验谈一〃绩效:VLRR(Verify Lots Reject Rate),Customer Complaint, LRR(Lots Reject Rate) .SQE 的使命,是通过对供应商的品质管理,以保证来料的品质。
因此,VLRR是SQE 绩效的主要反映。
二〃职责:围绕保证来料品质這目的,SQE 应负起以下四点职责;1. 对供应商例行品质绩效评估与稽核;2. 品质监督与異常辅导;3 .New/EC产品导入时的供货商制程与产品確认和持续改善(CIP); 4. GP产品及其制程管制等;针对此四点职责,以下是我的一点经验:1. 对供应商例行品质绩效评估与稽核;1.1导入新厂商:一般內容有:对新供应商作总況調查,QSA(Qaulity System Audit),QPA(Quality processAudit),签定品质合约;1.2供应商例行品质绩效评, 每月评分与制程稽核QPA;每月评分三要素TQR: Technology. Quality. Response; 每月一评,评分结果分A/B/C/D等级。
1.3 制程稽核(QPA)每季度末由SQE制定下季度的稽核计劃.制程稽核方式:针对不同的站別, including ReceivingInspection,Warehouse,MRB,P/L,Secondary Operations,OQC,Packing and Stock and so on. 总结起来,重点项目由人,机,料,法,环五项構成,具体事项按公司QPA List点检。
人:1. 培訓 2. Comply WI/SOP ;机:3 设备/校验。
4 治具/测量;料:5. 物料分区. 6 保存期/保存方式;法:7 可追溯性; 8. SPC, 自检, CLCA检讨;环:9 安全防护. 10 湿/温度;QSA 通常每年一评。
依ISO9000, 针对厂商的品质系統,对管理职责,資源管理,产品實現,量測分析与改進等四大塊進行audit. 具体事项可按公司QSA List点检.2 . 品质监督与異常辅导;以VLRR and LRR 及customer complaint数据为基础,对厂商品质異常, 通过review 其FMEA,8D/5C report, 及review 改善的結果等,以监督其品质改善狀況. 通过驻厂的Production Line Walking audit, check 品质異常改善措施的實施狀況,并提出相關的改善要求,以輔導厂商品质的維持与改善.3 .New/EC产品导入时的供应商制程与产品確认和持续改善(CIP);对新产品的導入,或EC产品的首次投产,均須到厂商的产線,对其制程的狀況和产品的合格狀況進行確認,并Review TVR/FAI/CPK 等相關数据。
SQE 知识
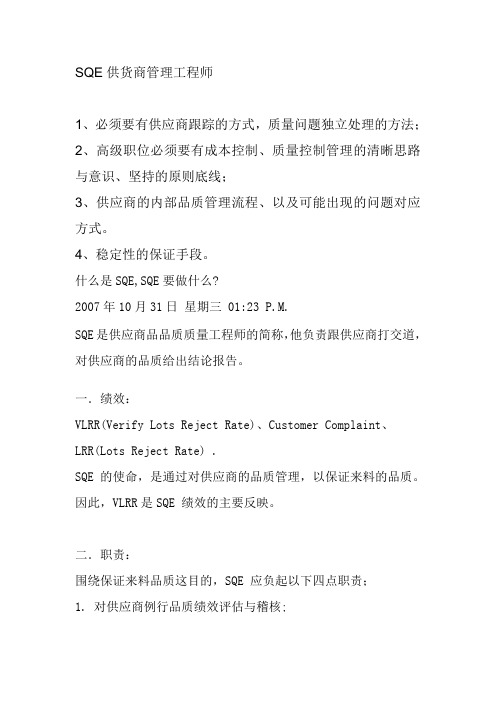
SQE供货商管理工程师1、必须要有供应商跟踪的方式,质量问题独立处理的方法;2、高级职位必须要有成本控制、质量控制管理的清晰思路与意识、坚持的原则底线;3、供应商的内部品质管理流程、以及可能出现的问题对应方式。
4、稳定性的保证手段。
什么是SQE,SQE要做什么?2007年10月31日星期三 01:23 P.M.SQE是供应商品品质质量工程师的简称,他负责跟供应商打交道,对供应商的品质给出结论报告。
一.绩效:VLRR(Verify Lots Reject Rate)、Customer Complaint、LRR(Lots Reject Rate) .SQE 的使命,是通过对供应商的品质管理,以保证来料的品质。
因此,VLRR是SQE 绩效的主要反映。
二.职责:围绕保证来料品质这目的,SQE 应负起以下四点职责;1. 对供应商例行品质绩效评估与稽核;2. 品质监督与异常辅导;3 .New/EC产品导入时的供货商制程与产品确认和持续改善(CIP);4. GP产品及其制程管制等;针对此四点职责,以下是我的一点经验:1. 对供应商例行品质绩效评估与稽核;1.1导入新厂商:一般内容有:对新供应商作总况调查、QSA(Qaulity System Audit), QPA(Quality process Audit)、签定品质合约;1.2供应商例行品质绩效评, 每月评分与制程稽核QPA;每月评分三要素TQR: Technology. Quality. Response;每月一评,评分结果分A/B/C/D等级。
1.3 制程稽核(QPA)每季度末由SQE制定下季度的稽核计划. 制程稽核方式:针对不同的站别, including Receiving Inspection、Warehouse、MRB、P/L、Secondary Operations、OQC、Packing and Stock and so on.总结起来,重点项目由人、机、料、法、环五项构成,具体事项按公司QPA List点检。
SQE 基础知识

品管人员角色定位、岗位素质要求
优秀SQE需要掌握的知识
19
MSA(Measurement System Analysis)使 用数理统计和图表的方法对测量系统的分 辨率和误差进行分析,以评估测量系统的 分辨率和误差对于被测量的参数来说是否 合适,并确定测量系统误差的主要成分。
20
DOE(实验设计Design Of Experiments,) 在质量控制的整个过程中扮演了非常重要的角 色,它是我们产品质量提高,工艺流程改善的重要 保证。实验设计已广泛运用了从航天业到一般生产 制造业的产品质量改善、工艺流程优化甚至已运用 到医学界。通过对产品质量,工艺参数的量化分析 ,寻找关键因素,控制与其相关的因素。根据实际 需求,判别与选择不同的实验设计种类,设计实验 步骤,发现如何控制各种影响因素,以最少的投入 ,换取最大的收益,从而使产品质量得以提升,工 艺流程最优化
25
品质的定义、本质,理解SQM
品质定义
·品质是一种以最经济的手段,制造出市场上最有 用的产品——戴明
·品质是一种合用性,而所谓“合用性”是指产品 在使用期间能满足使用者的需要——裘兰
26
·品质不是最好的,它只是在某些消费条件下的 最好,这些条件指的是产品价格(隐含品质成 本),以及实际用途。——费根堡
21
谢宁DOE 实验设计(DOE)方法一直在发展、丰富和 完善,美国人多里安·谢宁(Dorian Shainin)总结了七种新的DOE应用技术: 多变图技术、零件搜索技术 、成对比较 技术 、变量搜索技术 、完全析因技术 、 改进效果检查及实验设计的回归分析。
22
没有戴明,美国就不会有质量哲学; 没有朱兰,美国就不会有质量的方向; 没有谢宁,美国就无从解决质量问题。 这句名言总结了美国最伟大的三位质 量大师的贡献。
英文简称

供应商品质状况品质术语IFIR:初期(30天内)的市场不良率VRR:确认的批退率(主要指进料的批退率)LRR:生产线不良率VLRR:确认的生产线不良率DPPM:每百万的不良数量Lot Reject Rate:批退率On Time Delivery:及时交货Field Service …:市场服务生产厂常用英文缩写-特为新进厂菜鸟准备:Control Plan 管制计划Correction 纠正Cost Down 降低成本CS: Customer Sevice 客户中心Data 数据Data Collection 数据收集Description 描述Device 装置Digital 数字Do 执行DOE: Design of Experiments 实验设计Environmental 环境Equipment 设备FMEA: Failure Mode and Effect Analysis 失效模式与效果分析FA: Failure Analysis 坏品分析FQA: Final Quality Assurance 最终品质保证FQC: Final Quality control 最终品质控制GS: Gauge System 量测系统Grade 等级Inductance 电感Improvement 改善Inspection 检验IPQC: In Process Quality Control 制程品质控制IQC: Incoming Quality Control 来料品质控制JD: Job Description 岗位描述ISO: International Organization for Standardization 国际标准组织LCL: Lower Control limit 管制下限LQC: Line Quality Control 生产线品质控制LSL: Lower Size Limit 规格下限Materials 物料Measurement 量测MSA: Measurement System Analysis 量测系统分析Occurrence 发生率Operation Instruction 作业指导书Organization 组织Parameter 参数Parts 零件Pulse 脉冲Policy 方针Procedure 流程Process 过程Product 产品Production 生产Program 方案Projects 项目QA: Quality Assurance 品质保证QC: Quality Control 品质控制QE: Quality Engineering 品质工程QFD: Quality Function Design 品质机能展开Quality 质量Quality manual 品质手册Quality policy 品质政策Range 全距Record 记录Reflow 回流Reject 拒收Repair 返修Repeatability 再现性Reproducibility 再生性Requirement 要求Residual 误差Response 响应Responsibilities 职责Review 评审Rework 返工Rolled yield 直通率Sample 样本,抽样Scrap 报废SOP: Standard Operation Procedure 标准作业书SPC: Statistical Process Control 统计制程管制Specification 规格SQA: Source(Supplier) Quality Assurance 供应商品质保证Taguchi-Method 田口方法TQC: Total Quality Control 全面品质控制TQM: Total Quality Management 全面品质管理Traceability 追溯UCL: Upper Control Limit 管制上限USL: Upper Size Limit 规格上限Validation 确认Variable 计量值Verification 验证Version 版本QCC: Quality Control Circle 品质圈/QC小组PDCA: Plan Do Check Action 计划执行检查总结Consumer electronics 消费性电子产品Communication 通讯类产品Core Value 核心价值Confidence & Decision 信心和决心Corporate Cul t ure 公司文化Integration 融合Responsibility/Liability 责任QC: Quality Control 品质管理人员FQC: Final Quality Control 终点品质管制人员IPQC: In process Quality Control 制程中的品质管制人员OQC: Output Quality Control 最终出货品质管制人员IQC: Incoming Quality Control 进料品质管制人员TQC: Total quality Control 全面质量管理PQC: Passage Quality Control 段检人员QA: Quality Assurance 质量保证人员OQA: Output Quality Assurance 出货质量保证人员QE: Quality Engineering 品质工程人员FAI: First Article Inspection 新品首件检查FAA: First Article Assurance 首件确认CI: Capability Index 能力指数SSQA: Standardized Supplier Quality Audit 合格供应商品质评估FMEA: Failure Model Effectiveness Analysis 失效模式分析AQL: Acceptable Quality Level 运作类允收品质水准S/S: Sample Size (抽样检验的)样本数量ACC: Accept 允收REE: Reject 拒收CR: Critical 极严重的MAJ: Major 主要的MIN: Minor 轻微的Q/R/S: Quality/Reliability/Service 品质/可靠度/服务P/N: Part Number 料号L/N: Lot Number 批号AOD: Accept On Deviation 在公差范围内UAI: Use As It 可用FPIR: First Piece Inspection Report 首件检查报告PPM: Percent Per Million 百万分之一SPC: Statistical Process Control 统计制程管制SQC: Statistical Quality Control 统计品质管制GRR: Gauge Reproducibility & Repeatability 量具之再制性及重测性判断量可靠与否DIM: Dimension 尺寸DIA: Diameter 直径QIT: Quality Improvement Team 品质改善小组ZD: Zero Defect 零缺点QI: Quality Improvement 品质改善QP: Quality Policy 目标方针TQM: Total Quality Management 全面品质管理RMA: Return Material Audit 退料认可7QCTools: 7 Quality Control Tools 品管七大手法通用件类ECN: Engineering Change Notice 工程变更通知(供应商)ECO: Engineering Change Order 工程改动要求(客户)PCN: Process Change Notice 工序改动通知PMP: Product Management Plan 生产管制计划SIP: Standard Inspection Procedure 制程检验标准程序SOP: Standard Operation Procedure 制造作业规范IS: Inspection Specification 成品检验规范BOM: Bill Of Material 物料清单PS: Package Specification 包装规范SPEC: Specification 规格DWG: Drawing 图面系统文件类ES: Engineering Standard 工程标准IWS: International Workman Standard 工艺标准ISO: International Standardization Organization 国际标准化组织GS: General Specification 一般规格部门类PMC: Production & Material Control 生产和物料控制PCC: Product control center 生产管制中心PPC: Production Plan Control 生产计划控制MC: Material Control 物料控制DCC: Document Control Center 资料控制中心QE: Quality Engineering 品质工程部QA: Quality Assurance 品质保证处QC: Quality Control 品质管制(课)PD: Product Department 生产部LAB: Laboratory 实验室IE: Industrial Engineering 工业工程R&D: Research & Design 研发部。
生产厂常用英文缩写-特为新进厂菜鸟准备
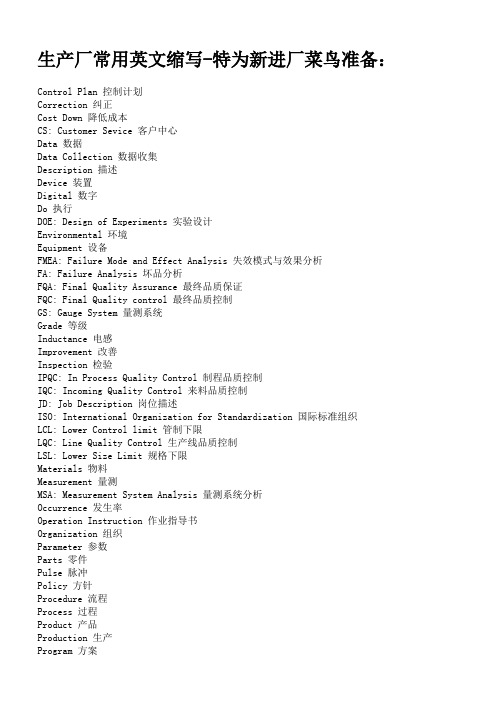
生产厂常用英文缩写-特为新进厂菜鸟准备:Control Plan 控制计划Correction 纠正Cost Down 降低成本CS: Customer Sevice 客户中心Data 数据Data Collection 数据收集Description 描述Device 装置Digital 数字Do 执行DOE: Design of Experiments 实验设计Environmental 环境Equipment 设备FMEA: Failure Mode and Effect Analysis 失效模式与效果分析FA: Failure Analysis 坏品分析FQA: Final Quality Assurance 最终品质保证FQC: Final Quality control 最终品质控制GS: Gauge System 量测系统Grade 等级Inductance 电感Improvement 改善Inspection 检验IPQC: In Process Quality Control 制程品质控制IQC: Incoming Quality Control 来料品质控制JD: Job Description 岗位描述ISO: International Organization for Standardization 国际标准组织LCL: Lower Control limit 管制下限LQC: Line Quality Control 生产线品质控制LSL: Lower Size Limit 规格下限Materials 物料Measurement 量测MSA: Measurement System Analysis 量测系统分析Occurrence 发生率Operation Instruction 作业指导书Organization 组织Parameter 参数Parts 零件Pulse 脉冲Policy 方针Procedure 流程Process 过程Product 产品Production 生产Program 方案Projects 项目QA: Quality Assurance 品质保证QC: Quality Control 品质控制QE: Quality Engineering 品质工程QFD: Quality Function Design 品质机能展开Quality 质量Quality manual 品质手册Quality policy 品质政策Range 全距Record 记录Reflow 回流Reject 拒收Repair 返修Repeatability 再现性Reproducibility 再生性Requirement 要求Residual 误差Response 响应Responsibilities 职责Review 评审Rework 返工Rolled yield 直通率Sample 样本,抽样Scrap 报废SOP: Standard Operation Procedure 标准作业书SPC: Statistical Process Control 统计制程管制Specification 规格SQA: Source(Supplier) Quality Assurance 供应商品质保证Taguchi-Method 田口方法TQC: Total Quality Control 全面品质控制TQM: Total Quality Management 全面品质管理Traceability 追溯UCL: Upper Control Limit 管制上限USL: Upper Size Limit 规格上限Validation 确认Variable 计量值Verification 验证Version 版本QCC: Quality Control Circle 品质圈/QC小组PDCA: Plan Do Check Action 计划执行检查总结Consumer electronics 消费性电子产品Communication 通讯类产品Core Value 核心价值Confidence & Decision 信心和决心Corporate Culture 公司文化Integration 融合Responsibility/Liability 责任QC: Quality Control 品质管理人员FQC: Final Quality Control 终点品质管制人员IPQC: In process Quality Control 制程中的品质管制人员OQC: Output Quality Control 最终出货品质管制人员IQC: Incoming Quality Control 进料品质管制人员TQC: Total quality Control 全面质量管理PQC: Passage Quality Control 段检人员QA: Quality Assurance 质量保证人员OQA: Output Quality Assurance 出货质量保证人员QE: Quality Engineering 品质工程人员FAI: First Article Inspection 新品首件检查FAA: First Article Assurance 首件确认CI: Capability Index 能力指数SSQA: Standardized Supplier Quality Audit 合格供应商品质评估FMEA: Failure Model Effectiveness Analysis 失效模式分析AQL: Acceptable Quality Level 运作类允收品质水准S/S: Sample Size (抽样检验的)样本数量ACC: Accept 允收REE: Reject 拒收CR: Critical 极严重的MAJ: Major 主要的MIN: Minor 轻微的Q/R/S: Quality/Reliability/Service 品质/可靠度/服务P/N: Part Number 料号L/N: Lot Number 批号AOD: Accept On Deviation 在公差范围内UAI: Use As It 可用FPIR: First Piece Inspection Report 首件检查报告PPM: Percent Per Million 百万分之一SPC: Statistical Process Control 统计制程管制SQC: Statistical Quality Control 统计品质管制GRR: Gauge Reproducibility & Repeatability 量具之再制性及重测性判断量可靠与否DIM: Dimension 尺寸DIA: Diameter 直径QIT: Quality Improvement Team 品质改善小组ZD: Zero Defect 零缺点QI: Quality Improvement 品质改善QP: Quality Policy 目标方针TQM: Total Quality Management 全面品质管理RMA: Return Material Audit 退料认可7QCTools: 7 Quality Control Tools 品管七大手法通用件类ECN: Engineering Change Notice 工程变更通知(供应商)ECO: Engineering Change Order 工程改动要求(客户)PCN: Process Change Notice 工序改动通知PMP: Product Management Plan 生产管制计划SIP: Standard Inspection Procedure 制程检验标准程序SOP: Standard Operation Procedure 制造作业规范IS: Inspection Specification 成品检验规范BOM: Bill Of Material 物料清单PS: Package Specification 包装规范SPEC: Specification 规格DWG: Drawing 图面系统文件类ES: Engineering Standard 工程标准IWS: International Workman Standard 工艺标准ISO: International Standardization Organization 国际标准化组织GS: General Specification 一般规格部门类PMC: Production & Material Control 生产和物料控制PCC: Product control center 生产管制中心PPC: Production Plan Control 生产计划控制MC: Material Control 物料控制DCC: Document Control Center 资料控制中心QE: Quality Engineering 品质工程部QA: Quality Assurance 品质保证处QC: Quality Control 品质管制(课)PD: Product Department 生产部LAB: Laboratory 实验室IE: Industrial Engineering 工业工程R&D: Research & Design 研发部供应商品质状况品质术语IFIR:初期(30天内)的市场不良率VRR:确认的批退率(主要指进料的批退率)LRR:生产线不良率VLRR:确认的生产线不良率DPPM:每百万的不良数量Lot Reject Rate:批退率On Time Delivery:及时交货Field Service …:市场服务。
14691名词解释

Dell 名詞說明
1.英文縮寫:CLCA 2.英文全文:Close Loop Corrective Action 3.中 文:循環改善行動
4.定義說明: 當產品或製程發生不良時必須建立的改善行動,一般使 用8D的標準來執行。
Page :3
Dell 名詞說明
1.英文縮寫:FAI 2.英文全文:First Article Inspection 3.中 文:首件檢查
4.定義說明:
4.1 流程/程序/標準的文件建立。
4.2 生產材料與維修材料有效性的管理及防止使用錯誤 的材料。 4.3 維修人員的技能/訓練及維修設備來支援不良解析。 4.4 現場堆放WIP之數量管控。
4.5 維修材料及半成品先進先出。
Page :6
4.6 維修站資料的回饋及驅動製程持續改善。 4.7 不良分析及矯正行動的有效性。 4.8 原先有問題,後來判定無問題,這部分資料要收 集分析及管控。
4.定義說明: 當On-line SPC量測值超出管制界限(±3σ= UCL/LCL =OOC)時,應持續觀察監控製程品位,是否有異常發生?
Page :10
Dell 名詞說明
1.英文縮寫:OOS 2.英文全文:Out of specification 3.中 文:量測值超出產品規格
4.定義說明: 當On-line SPC量測值超出產品規格(USL/LSL=OOS)時, 應即追查發生源、找出根因、擬定對策、對策實施,使
Dell 名詞說明
1.英文縮寫:IFIR 2.英文全文:Initial Field Incident Rate 3.中 文:初期市場批退率
4.定義說明: The percentage of commodity replaced within the first 30 days from product invoice date (in DPPM).
品质管理术语解释

LRR:生产线不良率 :LOT REJECT RATE
VLRR:确认的生产线不良率:Verified Line Reject Rate
DPPM:每百万的不良数量
CPK:Complex Pro代企业用于表示制程能力的指标
Ca: 制程准确度。 Cp: 制程精密度。
Cpk, Ca, Cp三者的关系: Cpk = Cp * ( 1 - |Ca|),Cpk是Ca及Cp两者的中和反应,Ca反应的是位置关系(集中趋势),Cp反应的是散布关系(离散趋势)
SPC: Statistical Process Control的简称统计过程控制
cpk:CPK:Complex Process Capability index 的缩写,是现代企业用于表示制程能力的指标。 制程能力是过程性能的允许最大变化范围与过程的正常偏差的比值。 制程能力研究在於确认这些特性符合规格的程度,以保证制程成品不符规格的不良率在要求的水准之上,作为制程持续改善的依据。 当我们的产品通过了GageR&R的测试之后,我们即可开始Cpk值的测试。 CPK值越大表示品质越佳。 Cpk——过程能力指数 CPK= Min[ (USL- Mu)/3s, (Mu - LSL)/3s] Cpk应用讲议 1. Cpk的中文定义为:制程能力指数,是某个工程或制程水准的量化反应,也是工程评估的一类指标。 2. 同Cpk息息相关的两个参数:Ca , Cp. Ca: 制程准确度。 Cp: 制程精密度。 3. Cpk, Ca, Cp三者的关系: Cpk = Cp * ( 1 - |Ca|),Cpk是Ca及Cp两者的中和反应,Ca反应的是位置关系(集中趋势),Cp反应的是散布关系(离散趋势) 4. 当选择制程站别Cpk来作管控时,应以成本做考量的首要因素,还有是其品质特性对后制程的影响度。 5. 计算取样数据至少应有20~25组数据,方具有一定代表性。 6. 计算Cpk除收集取样数据外,还应知晓该品质特性的规格上下限(USL,LSL),才可顺利计算其值。 7. 首先可用Excel的“STDEV”函数自动计算所取样数据的标准差(σ),再计算出规格公差(T),及规格中心值(U). 规格公差T=规格上限-规格下限;规格中心值U=(规格上限+规格下限)/2; 8. 依据公式:Ca=(X-U)/(T/2) , 计算出制程准确度:Ca值 (X为所有取样数据的平均值) 9. 依据公式:Cp =T/6σ , 计算出制程精密度:Cp值 10. 依据公式:Cpk=Cp(1-|Ca|) , 计算出制程能力指数:Cpk值 11. Cpk的评级标准:(可据此标准对计算出之制程能力指数做相应对策) A++级 Cpk≥2.0 特优 可考虑成本的降低 A+ 级 2.0 > Cpk ≥ 1.67 优 应当保持之 A 级 1.67 > Cpk ≥ 1.33 良 能力良好,状态稳定,但应尽力提升为A+级 B 级 1.33 > Cpk ≥ 1.0 一般 状态一般,制程因素稍有变异即有产生不良的危险,应利用各种资源及方法将其提升为 A级 C 级 1.0 > Cpk ≥ 0.67 差 制程不良较多,必须提升其能力 D 级 0.67 > Cpk 不可接受 其能力太差,应考虑重新整改设计制程。 CPK与PPK都是表示制程能力的参数,现代计算中多采用Minitab软件来实现,方便快捷
品质管理常见名词解释

品质指标名词解释1、CIT——Customer Incidents Tracking log,客诉追踪报告l CIT定义:CIT是为了有效地、系统地对客户端发生的质量异常进行追踪记录,而由CQS制作并更新维护的追踪报告。
(daily report)l CIT单位:件数。
CIT Qty:即客诉发生的件数。
l CIT的定义范围如下,共12条:1.1板子/零件烧毁1.2批量性不良(包括集中性高不良)1.3会引起重工的(包括厂内和厂外sorting & rework)1.4造成厂内hold货的客诉问题(即影响到厂内出货)1.5造成客户端停线/退货的客诉问题1.6 Workmanship issue和制程问题需100%提报(此问题可highlight给厂内改善)1.7属厂商来料不良的客诉问题1.8 Design 问题1.9客人Audit重大缺失项1.10客人发正式的异常通知单或者要求回复正式的改善报告1.11属CID的问题也需要报告CIT1.12厂商直接出货到客人端以及外包产品,在客户端出现问题均需要提报CITl CIT公式Weekly CIT Qty:当周提报的CIT Qty累加之和。
Monthly CIT Qty:当月提报的CIT Qty累加之和。
Yearly CIT Qty:整年度提报的CIT Qty累加之和。
2、AFR——Accumulated Failure Rate,累积不良率l AFR定义:AFR即产品在客户端的不良回归到产品制造月份的累积不良率。
从AFR 报告里面可以侦测到产品在客户端都发生了哪些不良以及这些不良在产品的整个生命周期发生的时机为何;还可以使用AFR对厂内外的良率做比对、分析和并寻求改善产品质量和信赖度的方向。
(weekly report)l AFR 单位:DPPM(每百万的不良数)l AFR公式3个月的AFR=(从生产当月算起3个月的所有返修数量/当月的生产总数)*10^66个月的AFR=(从生产当月算起6个月的所有返修数量/当月的生产总数)*10^61年的AFR=(从生产当月算起12个月的所有返修数量/当月的生产总数)*10^62年的AFR=(从生产当月算起24个月的所有返修数量/当月的生产总数)*10^63年的AFR=(从生产当月算起36个月的所有返修数量/当月的生产总数)*10^63、DOA&(客户端)LRR——Dead On Arrival,到货即损;(Customer) Line Reject Rate,(客户端)在线不良率l 定义:DOA&(客户端)LRR即客人收到货品后在进料检验时或在线投入使用时发现的不良,是工厂端为了监控产品到客户端的最及时的不良率报告。
品质管理常见名词解释

品质指标名词解释1、CIT——Customer Incidents Tracking log,客诉追踪报告l CIT定义:CIT是为了有效地、系统地对客户端发生的质量异常进行追踪记录,而由CQS制作并更新维护的追踪报告。
(daily report)l CIT单位:件数。
CIT Qty:即客诉发生的件数。
l CIT的定义范围如下,共12条:1.1板子/零件烧毁1.2批量性不良(包括集中性高不良)1.3会引起重工的(包括厂内和厂外sorting & rework)1.4造成厂内hold货的客诉问题(即影响到厂内出货)1.5造成客户端停线/退货的客诉问题1.6 Workmanship issue和制程问题需100%提报(此问题可highlight给厂内改善)1.7属厂商来料不良的客诉问题1.8 Design 问题1.9客人Audit重大缺失项1.10客人发正式的异常通知单或者要求回复正式的改善报告1.11属CID的问题也需要报告CIT1.12厂商直接出货到客人端以及外包产品,在客户端出现问题均需要提报CITl CIT公式Weekly CIT Qty:当周提报的CIT Qty累加之和。
Monthly CIT Qty:当月提报的CIT Qty累加之和。
Yearly CIT Qty:整年度提报的CIT Qty累加之和。
2、AFR——Accumulated Failure Rate,累积不良率l AFR定义:AFR即产品在客户端的不良回归到产品制造月份的累积不良率。
从AFR 报告里面可以侦测到产品在客户端都发生了哪些不良以及这些不良在产品的整个生命周期发生的时机为何;还可以使用AFR对厂内外的良率做比对、分析和并寻求改善产品质量和信赖度的方向。
(weekly report)l AFR 单位:DPPM(每百万的不良数)l AFR公式3个月的AFR=(从生产当月算起3个月的所有返修数量/当月的生产总数)*10^66个月的AFR=(从生产当月算起6个月的所有返修数量/当月的生产总数)*10^61年的AFR=(从生产当月算起12个月的所有返修数量/当月的生产总数)*10^62年的AFR=(从生产当月算起24个月的所有返修数量/当月的生产总数)*10^63年的AFR=(从生产当月算起36个月的所有返修数量/当月的生产总数)*10^63、DOA&(客户端)LRR——Dead On Arrival,到货即损;(Customer) Line Reject Rate,(客户端)在线不良率l 定义:DOA&(客户端)LRR即客人收到货品后在进料检验时或在线投入使用时发现的不良,是工厂端为了监控产品到客户端的最及时的不良率报告。
品质管理常见名词解释

品质管理常见名词解释 This manuscript was revised on November 28, 2020品质指标名词解释1、CIT——Customer Incidents Tracking log,客诉追踪报告l CIT定义:CIT是为了有效地、系统地对客户端发生的质量异常进行追踪记录,而由CQS制作并更新维护的追踪报告。
(daily report)l CIT单位:件数。
CIT Qty:即客诉发生的件数。
l CIT的定义范围如下,共12条:板子/零件烧毁批量性不良(包括集中性高不良)会引起重工的 (包括厂内和厂外sorting & rework)造成厂内hold货的客诉问题 (即影响到厂内出货)造成客户端停线/退货的客诉问题Workmanship issue和制程问题需100%提报 (此问题可highlight给厂内改善)属厂商来料不良的客诉问题Design 问题客人Audit重大缺失项客人发正式的异常通知单或者要求回复正式的改善报告属CID的问题也需要报告CIT厂商直接出货到客人端以及外包产品,在客户端出现问题均需要提报CITl CIT公式Weekly CIT Qty:当周提报的CIT Qty累加之和。
Monthly CIT Qty:当月提报的CIT Qty累加之和。
Yearly CIT Qty:整年度提报的CIT Qty累加之和。
2、AFR——Accumulated Failure Rate,累积不良率l AFR定义:AFR即产品在客户端的不良回归到产品制造月份的累积不良率。
从AFR报告里面可以侦测到产品在客户端都发生了哪些不良以及这些不良在产品的整个生命周期发生的时机为何;还可以使用AFR对厂内外的良率做比对、分析和并寻求改善产品质量和信赖度的方向。
(weekly report)l AFR 单位:DPPM(每百万的不良数)l AFR公式3个月的AFR=(从生产当月算起3个月的所有返修数量/当月的生产总数)*10^66个月的AFR=(从生产当月算起6个月的所有返修数量/当月的生产总数)*10^61年的AFR=(从生产当月算起12个月的所有返修数量/当月的生产总数)*10^62年的AFR=(从生产当月算起24个月的所有返修数量/当月的生产总数)*10^63年的AFR=(从生产当月算起36个月的所有返修数量/当月的生产总数)*10^63、DOA&(客户端)LRR——Dead On Arrival,到货即损;(Customer) Line Reject Rate,(客户端)在线不良率l 定义:DOA&(客户端)LRR即客人收到货品后在进料检验时或在线投入使用时发现的不良,是工厂端为了监控产品到客户端的最及时的不良率报告。
质量管理常用词汇缩写
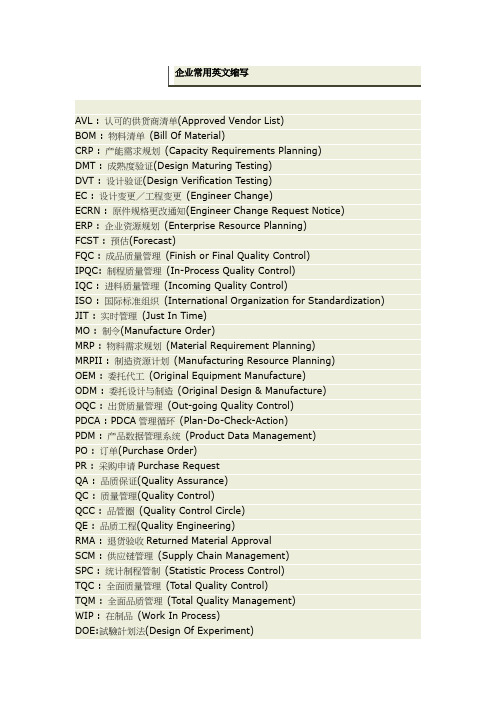
企业常用英文缩写AVL : 认可的供货商清单(Approved Vendor List)BOM : 物料清单(Bill Of Material)CRP : 产能需求规划(Capacity Requirements Planning)DMT : 成熟度验证(Design Maturing Testing)DVT : 设计验证(Design Verification Testing)EC : 设计变更/工程变更(Engineer Change)ECRN : 原件规格更改通知(Engineer Change Request Notice)ERP : 企业资源规划(Enterprise Resource Planning)FCST : 预估(Forecast)FQC : 成品质量管理(Finish or Final Quality Control)IPQC: 制程质量管理(In-Process Quality Control)IQC : 进料质量管理(Incoming Quality Control)ISO : 国际标准组织(International Organization for Standardization) JIT : 实时管理(Just In Time)MO : 制令(Manufacture Order)MRP : 物料需求规划(Material Requirement Planning)MRPII : 制造资源计划(Manufacturing Resource Planning)OEM : 委托代工(Original Equipment Manufacture)ODM : 委托设计与制造(Original Design & Manufacture)OQC : 出货质量管理(Out-going Quality Control)PDCA : PDCA管理循环(Plan-Do-Check-Action)PDM : 产品数据管理系统(Product Data Management)PO : 订单(Purchase Order)PR : 采购申请Purchase RequestQA : 品质保证(Quality Assurance)QC : 质量管理(Quality Control)QCC : 品管圈(Quality Control Circle)QE : 品质工程(Quality Engineering)RMA : 退货验收Returned Material ApprovalSCM : 供应链管理(Supply Chain Management)SPC : 统计制程管制(Statistic Process Control)TQC : 全面质量管理(Total Quality Control)TQM : 全面品质管理(Total Quality Management)WIP : 在制品(Work In Process)DOE:試驗計划法(Design Of Experiment)。
SQE工作职责
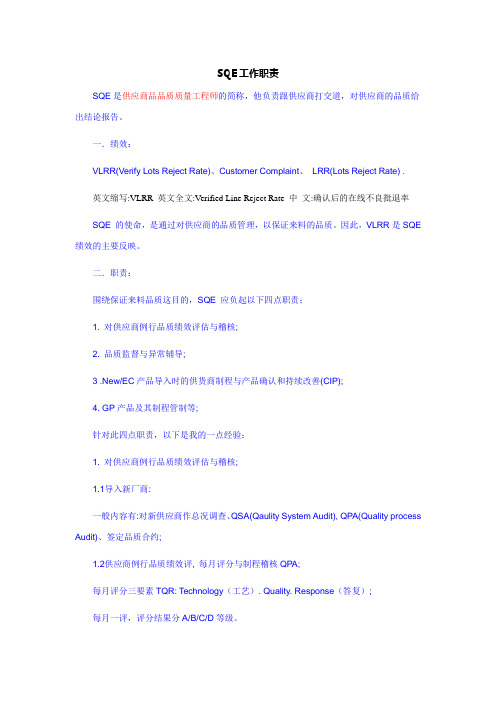
SQE工作职责SQE是供应商品品质质量工程师的简称,他负责跟供应商打交道,对供应商的品质给出结论报告。
一.绩效:VLRR(Verify Lots Reject Rate)、Customer Complaint、LRR(Lots Reject Rate) .英文缩写:VLRR 英文全文:Verified Line Reject Rate 中文:确认后的在线不良批退率SQE 的使命,是通过对供应商的品质管理,以保证来料的品质。
因此,VLRR是SQE 绩效的主要反映。
二.职责:围绕保证来料品质这目的,SQE 应负起以下四点职责;1. 对供应商例行品质绩效评估与稽核;2. 品质监督与异常辅导;3 .New/EC产品导入时的供货商制程与产品确认和持续改善(CIP);4. GP产品及其制程管制等;针对此四点职责,以下是我的一点经验:1. 对供应商例行品质绩效评估与稽核;1.1导入新厂商:一般内容有:对新供应商作总况调查、QSA(Qaulity System Audit), QPA(Quality process Audit)、签定品质合约;1.2供应商例行品质绩效评, 每月评分与制程稽核QPA;每月评分三要素TQR: Technology(工艺). Quality. Response(答复);每月一评,评分结果分A/B/C/D等级。
1.3 制程稽核(QPA)每季度末由SQE制定下季度的稽核计划.制程稽核方式:针对不同的站别, including Receiving Inspection(包括接收检验)、Warehouse(仓库)、MRB、P/L、Secondary Operations (二次加工)、OQC、Packing and Stock and so on(包装存储等).注:以上为直译MRB: Material Review Board (美国)材料审查委员会,产线上的物料经检测不合格的退MRB 然后再做决定是RTV(退给供应商)还是RTC(退给客户)还是SCRAP(报废),由MRB出货给V或C或相应的报废品接收商,同时MRB还需同产线及采购做好协调沟通以做好不良品的库存控制总结起来,重点项目由人、机、料、法、环五项构成,具体事项按公司QPA List点检。
SQE的基本岗位职责是什么
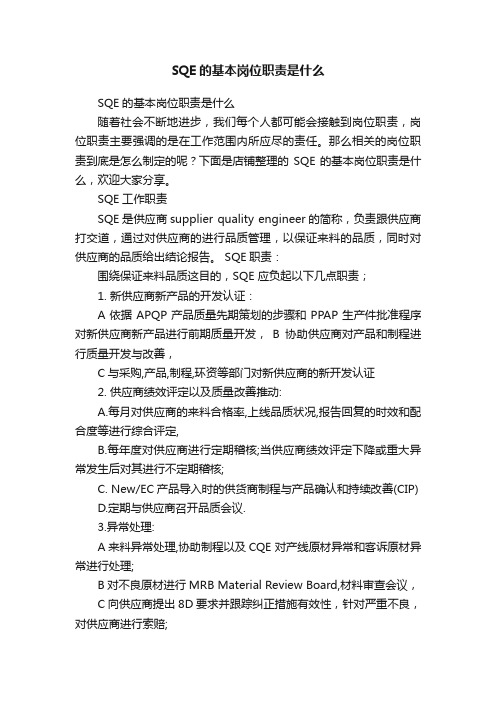
SQE的基本岗位职责是什么SQE的基本岗位职责是什么随着社会不断地进步,我们每个人都可能会接触到岗位职责,岗位职责主要强调的是在工作范围内所应尽的责任。
那么相关的岗位职责到底是怎么制定的呢?下面是店铺整理的SQE的基本岗位职责是什么,欢迎大家分享。
SQE工作职责SQE是供应商supplier quality engineer的简称,负责跟供应商打交道,通过对供应商的进行品质管理,以保证来料的品质,同时对供应商的品质给出结论报告。
SQE职责:围绕保证来料品质这目的,SQE 应负起以下几点职责;1. 新供应商新产品的开发认证:A依据APQP产品质量先期策划的步骤和PPAP生产件批准程序对新供应商新产品进行前期质量开发,B协助供应商对产品和制程进行质量开发与改善,C与采购,产品,制程,环资等部门对新供应商的新开发认证2. 供应商绩效评定以及质量改善推动:A.每月对供应商的来料合格率,上线品质状况,报告回复的时效和配合度等进行综合评定,B.每年度对供应商进行定期稽核;当供应商绩效评定下降或重大异常发生后对其进行不定期稽核;C. New/EC产品导入时的供货商制程与产品确认和持续改善(CIP)D.定期与供应商召开品质会议.3.异常处理:A来料异常处理,协助制程以及CQE 对产线原材异常和客诉原材异常进行处理;B对不良原材进行MRB Material Review Board,材料审查会议,C向供应商提出8D要求并跟踪纠正措施有效性,针对严重不良,对供应商进行索赔;4.GP产品(GP绿色和平组织和国际品牌联盟IBF),和包装废弃材料的再生资源利用及其制程管制等5.对检验人员进行培训和来料检验标准SIP制作更新A对检验人员等进行检验手法,环境和标准方面的培训B对检验标准的修订制作和宣导SQE常用专业术语:1、APQP产品质量先期策划的步骤:项目的计划与确定、产品设计与开发、过程设计与开发、产品和过程的确认、反馈与纠正APQP(Advanced Product Quality Planning)即产品质量先期策划,是一种结构化的方法,用来确定和制定确保某产品使顾客满意所需的步骤。
SQE的基本岗位职责是什么 (2)

SQE的基本岗位职责是什么SQE工作职责SQE是供应商supplier quality engineer的简称,负责跟供应商打交道,通过对供应商的进行品质管理,以保证来料的品质,同时对供应商的品质给出结论报告。
SQE职责:围绕保证来料品质这目的,SQE 应负起以下几点职责;1. 新供应商新产品的开发认证:A根据APQP产品质量先期策划的步骤和PPAP生产件批准程序对新供应商新产品进行前期质量开发, B帮助供应商对产品和制程进行质量开发与改善,C与选购,产品,制程,环资等部门对新供应商的新开发认证2. 供应商绩效评定以及质量改善推动:A.每月对供应商的来料合格率,上线品质状况,报告回复的时效和协作度等进行综合评定,B.每年度对供应商进行定期稽核;当供应商绩效评定下降或重大异样发生后对其进行不定期稽核;C. New/EC产品导入时的供货商制程与产品确认和持续改善(CIP)D.定期与供应商召开品质会议.3.异样处理:A来料异样处理,帮助制程以及CQE 对产线原材异样和客诉原材异样进行处理;B对不良原材进行MRB Material Review Board,材料审查会议, C向供应商提出8D要求并跟踪订正措施有效性,针对严峻不良,对供应商进行索赔;4.GP产品〔GP绿色和平组织和国际品牌联盟IBF〕,和包装废弃材料的再生资源利用及其制程管制等5.对检验人员进行培训和来料检验标准SIP制作更新A对检验人员等进行检验手法,环境和标准方面的培训B对检验标准的修订制作和宣导SQE常用专业术语:1、APQP产品质量先期策划的步骤:项目的打算与确定、产品设计与开发、过程设计与开发、产品和过程确实认、反馈与订正APQP〔Advanced Product Quality Planning〕即产品质量先期策划,是一种结构化的方法,用来确定和制定确保某产品使顾客满足所需的步骤。
产品质量策划的目标是促进与所涉及的每一个人的联系,以确保所要求的步骤按时完成。
品质管理常见名词解释
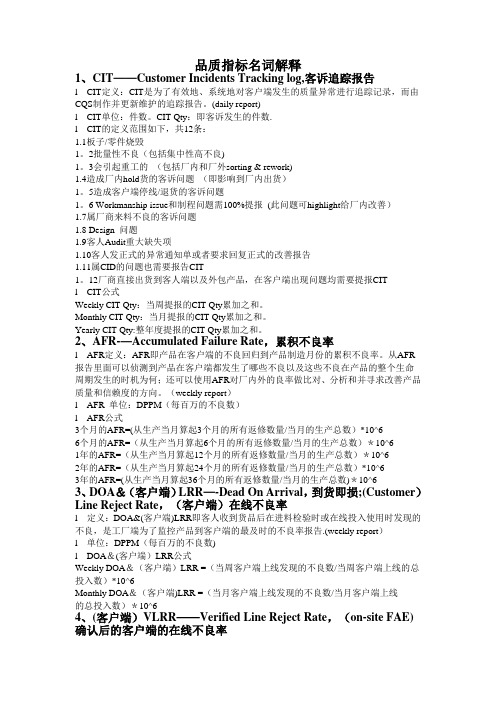
品质指标名词解释1、CIT——Customer Incidents Tracking log,客诉追踪报告l CIT定义:CIT是为了有效地、系统地对客户端发生的质量异常进行追踪记录,而由CQS制作并更新维护的追踪报告。
(daily report)l CIT单位:件数。
CIT Qty:即客诉发生的件数.l CIT的定义范围如下,共12条:1.1板子/零件烧毁1。
2批量性不良(包括集中性高不良)1。
3会引起重工的(包括厂内和厂外sorting & rework)1.4造成厂内hold货的客诉问题(即影响到厂内出货)1。
5造成客户端停线/退货的客诉问题1。
6 Workmanship issue和制程问题需100%提报(此问题可highlight给厂内改善)1.7属厂商来料不良的客诉问题1.8 Design 问题1.9客人Audit重大缺失项1.10客人发正式的异常通知单或者要求回复正式的改善报告1.11属CID的问题也需要报告CIT1。
12厂商直接出货到客人端以及外包产品,在客户端出现问题均需要提报CITl CIT公式Weekly CIT Qty:当周提报的CIT Qty累加之和。
Monthly CIT Qty:当月提报的CIT Qty累加之和。
Yearly CIT Qty:整年度提报的CIT Qty累加之和。
2、AFR-—Accumulated Failure Rate,累积不良率l AFR定义:AFR即产品在客户端的不良回归到产品制造月份的累积不良率。
从AFR报告里面可以侦测到产品在客户端都发生了哪些不良以及这些不良在产品的整个生命周期发生的时机为何;还可以使用AFR对厂内外的良率做比对、分析和并寻求改善产品质量和信赖度的方向。
(weekly report)l AFR 单位:DPPM(每百万的不良数)l AFR公式3个月的AFR=(从生产当月算起3个月的所有返修数量/当月的生产总数)*10^66个月的AFR=(从生产当月算起6个月的所有返修数量/当月的生产总数)*10^61年的AFR=(从生产当月算起12个月的所有返修数量/当月的生产总数)*10^62年的AFR=(从生产当月算起24个月的所有返修数量/当月的生产总数)*10^63年的AFR=(从生产当月算起36个月的所有返修数量/当月的生产总数)*10^63、DOA&(客户端)LRR—-Dead On Arrival,到货即损;(Customer)Line Reject Rate,(客户端)在线不良率l 定义:DOA&(客户端)LRR即客人收到货品后在进料检验时或在线投入使用时发现的不良,是工厂端为了监控产品到客户端的最及时的不良率报告.(weekly report)l 单位:DPPM(每百万的不良数)l DOA&(客户端)LRR公式Weekly DOA&(客户端)LRR =(当周客户端上线发现的不良数/当周客户端上线的总投入数)*10^6Monthly DOA&(客户端)LRR =(当月客户端上线发现的不良数/当月客户端上线的总投入数)*10^64、(客户端)VLRR——Verified Line Reject Rate,(on-site FAE)确认后的客户端的在线不良率l (客户端)VLRR定义:(客户端)VLRR是经过本公司的人员(如on—site FAE)确认过的属于MSI责任的客户端的在线不良率.(weekly report)l 单位:DPPM(每百万的不良数)l (客户端)VLRR公式Weekly (客户端)VLRR=(当周确认后的属MSI责任的客户端的在线不良数量/当周客户端总投入数量)*10^6Monthly (客户端)VLRR=(当月确认后的属MSI责任的客户端的在线不良数量/当月客户端总投入数量)*10^65、COQ——Cost of Quality,质量成本(或失败成本)l COQ 定义:COQ是为确保客户得到高质量产品所耗之成本及为改善各种错误所投入的财力之总和。
- 1、下载文档前请自行甄别文档内容的完整性,平台不提供额外的编辑、内容补充、找答案等附加服务。
- 2、"仅部分预览"的文档,不可在线预览部分如存在完整性等问题,可反馈申请退款(可完整预览的文档不适用该条件!)。
- 3、如文档侵犯您的权益,请联系客服反馈,我们会尽快为您处理(人工客服工作时间:9:00-18:30)。
模拟试验
Lead broken实验模拟
实验sample: T260XW02 VQ 半成品. COF型号为Raydium 92122.
实验方式:手持PCB,做不同方向的拉扯或弯折实验.
水平拉扯PCB实验 实验步骤如下: 1.画检确认sample OK,同时OM下确认X1 COF OLB溢 胶边缘的导线无弯折痕迹. 2.贴着平面水平往后拉扯PCB,直到Cell在玻璃平台上移 动,重复3次,OM下确认. 实验结果: OM下未确认到COF Lead明显变化
Cell在CST中位移与时间T相关性---减少手动对位Cell
S
T
M
f
V
根据动量定理可以得到:
FT=MV—〉FT*T=MS
M和S固定,F和T成反比,时间越短,人员
对CST施加的力越大,根据作用力和反作用
力可以推导出,施加在CELL下表面的力也 会越大。这个力大于摩擦力,CELL更容易 发生偏移。
时间T越短,CST速度V越快,当CST突然停 止时,CELL还会向前移动一小段距离。根 据可以得到: S=V*V/2a—〉S=MV*V/2f
549 491
改善 255DPPM
Feb Input
Mar Dppm
390 Apr
pcs 700,000 600,000 500,000 400,000 300,000 200,000 100,000 0
Remark:Q1 COF Lead Broken VLRR 78DPPM (Target 90 DPPM)
手指接触Film材,往上抬cell
Lead broken实验模拟
Process制程中review <COF 受到90度引力>的机会 3个站点存在high risk. 一.P/T 站 不良品送修或外观检验时.需将panel从平台上拿起.存在90度受力risk.
NG动作:手指接触COF
对策: 在机台上先将PCB180度翻折,然后才可 以将panel拿起.
1E4/3前调整完毕。
CST里防滑垫改善---减少手动对位Cell
CST里每个支撑杆上都贴有防滑垫,如下图所示:
防滑垫起到防滑作用,对防止CELL 在CST里发生位移起到一定的作用。
根据CST的设计,目前贴附的防滑垫存在可以导致COF Peeling的Risk,如下图所示:
PCB 板边缘与防滑垫边缘相切
MGV车高度调整---减少手动对位Cell
产线发现MGV车高度有偏低现象:
CST
MA CST P
MGV
MGV车高度偏低直接导致在由JI转移CST 至MA CST P时,出现异常。需要向上搬 动CST才可以将CST推进。
2ETotal 5辆MGV高度已经校正OK。(调 整MGV车螺杆高度及换掉NG螺杆)
其中a固定,为摩擦力f给与Cell的加速度。 可以得到,V越小,S越小,f越大,S越小。
结论:通过增加时间T及增加f即可缩短S。 即Cell位移越小。
1E&2EJI和MA CST P差异:
1E为马达带动,2E马达未使用:
1E JI CST P
1E MA CST P
1E MA CST P
1E JI&M拉CST时,因滚轮速度固定的影响,无法 快速将CST拉动。
手持PCB弯折实验: 分两种方式:手指不接触COF和手指接触COF(见下页). 手指不接触COF 实验动作分2块:拉起cell和不拉起cell 1.手持PCB弯折30-45度, 同时拉起cell,重复3次,OM下确 认. 2. 单纯弯折180度3次(不拉起Cell ),OM下确认. 实验结果: 1.第一个动作后,OM确认COF有轻微弯折 2.第二个动作后,无任何变化.
Robot在取片时,PCB板与防滑 垫相干涉,造成COF Peeling
CST里防滑垫改善---减少手动对位Cell
在靠近PCB板附近的防滑垫周围再贴附1PCS防滑垫,如下图所示:
额外贴附的防滑垫
PCB板平躺在防滑垫上
增加的防滑垫托起PCB板,且防滑垫高度一致,PCB板放置于防滑垫上 不会存在之前的干涉现象。 4/10—4/11日 2E和1E 皆贴附完成。
当向上调整到一定高度,不好执行此种动 作时,拇指和食指捏住AB角或AD角,食 指在上,拇指在下。调整CELL位置时, 切勿不要将PCB板反折到CELL下面。
Lead broken实验模拟
三.重合不良调整 1.review基本动作无lead broken risk.
PCB瞬间下落拍打B/L动作(无risk)
SOP:S02JE-09-056已经定义
Lead broken实验模拟
二.CST点位调整 当panel在CST点位不当,调整点位需抬起 cell, COF存在90度受力risk. SOP添加CST 中Cell位置调整作业手法。
T26/T32 SOP定义一致
拇指和食指捏住AB角或AD角,中指托住 PCB板。禁止手指抵触COF。
而2E不同,2E所有马达已经卸掉,人员可以很随意的推拉CST。因人员个体差异CST的行进速 度无法进行定义。
MA设备预计于4/16日开始在2E4#开始验证,
2E根据设备的安排预计于WK918周全部导入。
AUO Proprietary & Confidential
MA Process VLRR Report
AUO Proprietary & Confidential
COF Lead Broken MA Trend Chart
dppm
700 650 600 550 500 450 400 350 300 250 200 150 100
645 Jan
Lead Broken&Peeling Trend Chart
手持PCB动作
Cell侧 ACF溢胶边缘
PCB侧
已有轻微弯折痕迹
Lead broken实验模拟
手指接触COF 实验步骤: 手持PCB,手指接触COF,并往上抬起cell. 方式及步骤解析如右.. 实验结果: 此步骤1次后,COF lead上有折断痕迹, 参考如下图片.
溢胶边缘固定COF
手指往上给COF引力
第二种:
拇指和食指捏住BC角和CD角, :
拇指托住C边,食指托住B边或D边。 已经加入重点回训项目中
CST 中CELL点位调整:---减少手动对位Cell
A a
Y1 Cell X=50mm
Cell X=50mm
Y1
b=35
a位置Y1COF与托杆相齐
A位置Y1COF与托杆距离b
取中间值 5(mm)<b<25(mm)
2.重合不良时调整动作
重合不良时,需将cell拎起,然后调整位置,存 在COF 90度受力机会.
PCB组装动作(无risk)
如左图: 手指抵触COF拎起cell的动作是不允许的.
SOP定义不许提PCB侧来调节Cell,需制 造严格执行。
作业手法
Cell&B/L对位不良时调整作业手法
调整动作手法如下两种: 第一种: