1350kVA电煅炉的热平衡
一种炼锌电炉均衡加热结构

一种炼锌电炉均衡加热结构一、引言炼锌电炉是炼锌工业中的核心设备,其运行效率和稳定性对整个炼锌过程具有重要影响。
传统的炼锌电炉在加热过程中,由于各部分加热元件的功率分布不均,往往会导致炉内温度分布不均,进而影响锌的熔炼效果和能耗。
为了解决这一问题,我们提出了一种炼锌电炉均衡加热结构。
二、均衡加热结构的设计均衡加热结构的设计核心在于优化加热元件的布局和功率分布,使炉内温度场更加均匀。
具体设计如下:1、加热元件布局设计:采用分区布置的方式,将炉膛分为多个加热区,每个加热区设置一定数量的加热元件。
根据炉膛内温度场的模拟结果,调整加热元件的位置和数量,以实现温度的均匀分布。
2、功率分配设计:根据各加热区的热负荷需求,为每个加热区配备不同功率的加热元件。
通过合理分配功率,确保各加热区温度能够快速、稳定地达到工艺要求。
3、智能控制系统设计:采用先进的智能控制系统,实时监测炉内温度、压力等参数,并根据实际情况动态调整加热元件的工作状态,实现对炉内温度的精确控制。
三、均衡加热结构的优点与传统的炼锌电炉相比,均衡加热结构具有以下优点:1、温度均匀:通过优化加热元件布局和功率分配,使炉内温度场更加均匀,提高了锌的熔炼效果。
2、能耗低:由于温度场均匀,减少了能源浪费,降低了生产成本。
3、设备寿命长:均衡加热结构减少了设备局部过热现象,降低了设备损坏的风险,延长了设备使用寿命。
4、环保节能:该结构能够有效降低能耗,符合当前绿色环保的产业发展趋势。
四、结论通过上述分析,我们可以得出结论:均衡加热结构在炼锌电炉中具有良好的应用前景。
该结构通过优化加热元件布局、功率分配和智能控制系统设计,实现了炉内温度的均匀分布,提高了锌的熔炼效果和设备运行效率。
同时,该结构还具有能耗低、设备寿命长、环保节能等优点,为炼锌工业的可持续发展提供了有力支持。
在实际应用中,我们建议进一步研究和改进均衡加热结构的设计,以提高其在不同工况下的适应性和稳定性。
转炉炼钢物料平衡和热平衡计算模板-

转炉炼钢物料平衡和热平衡计算模板- 第二章、转炉物料平衡和热平衡计算1、低磷生铁吹炼(单渣法)一、原始数据(一)铁水成分及温度表2-1-1成分 C Si Mn P S 温度 ?% 4.36 o.57 0. 62 0.07 0.05 1300 (二)原材料成分表2-1-2烧合计成分% CaO SiO MgO AlO S P CaF FeO FeO HO C 2232232减 % 种类100 91(08 1(66 1(54 1(22 0(06 4(44 石灰100 1(00 5(61 0(52 1(10 0(07 29(4 61(8 0(50 矿石100 6(00 0(58 1(78 0(09 0(55 89(00 2(00 萤石10 8 53(04 0(48 34(94 0(74 白云石100 1(40 2(60 85(00 11(00 炉衬(三)冶炼钢种及成分表2-1-3成分 C Si Mn P S % 0.12—0.20 0.20—0.55 1.20—1.60 ?0.045 ?0.045 (四)平均比热表2-1-4项目固态平均比热kcal/kg.? 熔化潜热kcal/kg 液态或气态平均比热kcal/kg.?生铁 0.178 52 0.20 钢 0.167 65 0.20 炉渣 50 0.298 烟尘 0.238 50 矿石炉气:CO 0.349 CO 0.558 2SO 0.555 2O 0.356 2N 0.346 2HO 0.439 2(五)冷却剂用废钢做冷却剂,其成分与冶炼钢种中限相同。
(六)反应热效应1反应热效应通常采用25?为参考温度,比较常用的反应数据见表2-1-5 (七)根据国内转炉实测数据选取1、渣中铁珠量为渣量的2.5%;2、金属中[C]假定85%氧化成CO,15%氧化成CO; 23、喷溅铁损为铁水量的0.3%;4、取炉气平均温度1450?,自由氧含量0.5%,烟尘量为铁水量的1.8%,其中FeO=75%,Fe0=22%; 235、炉衬侵蚀量为铁水量的0.15%;6、氧气成分为98.9% O,1.5% N。
工业电炉三相整流电力调整器功能

工业电炉三相整流电力调整器功能工业电炉是一种利用电能进行加热的设备,广泛应用于冶金、化工、轻工等行业。
而在电炉的工作过程中,为了保证电炉的稳定运行和高效工作,需要使用到三相整流电力调整器。
本文将就三相整流电力调整器的功能进行详细介绍。
一、稳定输出电力工业电炉的加热过程需要稳定的电力供应,而三相整流电力调整器能够将输入的交流电转换为稳定的直流电,并根据电炉的工作需要进行调整,以保证输出电力的稳定性。
通过对电流和电压的调整,三相整流电力调整器能够确保电炉在不同工作状态下都能获得稳定的电力供应。
二、调节电炉温度电炉的加热温度对于工业生产过程非常重要,而三相整流电力调整器可以通过调节输出电力的大小来控制电炉的加热温度。
通过改变电炉的电流和电压,三相整流电力调整器可以精确地控制电炉的加热温度,以满足不同工艺要求和产品质量的需要。
三、保护电炉设备在电炉的工作过程中,由于电流和电压的变化,可能会对电炉设备造成损坏。
而三相整流电力调整器能够实时监测电流和电压的波动情况,并根据需要进行调整,以保护电炉设备的安全运行。
当电流和电压超出安全范围时,三相整流电力调整器会自动进行调整,避免设备损坏和事故发生。
四、提高电炉效率通过使用三相整流电力调整器,可以提高电炉的效率,降低能源消耗。
三相整流电力调整器能够根据电炉的工作需求调整电流和电压的大小,以提高电炉的加热效率。
通过合理调节电力输出,可以减少能源的浪费,提高生产效率和经济效益。
五、提升电炉控制精度三相整流电力调整器具有较高的控制精度,可以使电炉的加热温度控制更加精确。
通过对电流和电压的精确调节,可以实现电炉温度的精确控制,提高产品质量的稳定性和一致性。
六、降低电炉噪音和电磁干扰电炉在加热过程中会产生噪音和电磁干扰,而三相整流电力调整器可以通过控制电流和电压的波动,降低电炉的噪音和电磁干扰。
通过使用三相整流电力调整器,可以改善电炉的工作环境,提高工作人员的舒适度和生产效率。
电井炉热平衡计算

电井炉热平衡计算及工艺参数确定徐效谦(东北特殊钢集团大连钢丝制品公司)钢丝热处理过程必须满足两个基本条件:必须提供足够的热量,把钢丝加热到预定的温度;必须对单位时间内提供的热量实行有效地控制,使钢丝保温一段时间,完成组织结构的转变后,再以一定的冷却速度,冷却到指定温度出炉。
因此,热能的供给方式和控制水平,就代表热处理炉的水平。
苏州市东升电炉厂生产的RJQ-280-9型强对流气体保护井式退火炉采用全纤维砌筑,炉体保温条件较好,热惯性小,升温和降温速度比较快。
为防止钢丝氧化、脱碳,炉内配置内胆,形成密封罐体,热处理全过程通氮气或氨分解气体保护。
内胆中有一层导流桶,内胆底部装两级强对流风机,风机鼓起的气流沿导流桶与内胆间的风道直达炉顶,然后从炉中心部位回流到风机页片中。
由于气体从四周向中心有规律的循环流动,炉温均匀性有根本性的改善。
该炉投产后彻底扭转了钢丝制品公司成品钢丝抗拉强同批差偏大的被动局面。
强对流气体保护井式退火炉设计装炉量为8~16t,最高使用温度为850℃。
采用电阻带加热,加热功率280kW。
因供热速度有限,不同退火温度,不同装炉量热处理升热时间差别较大,因此需要通过热平衡计算为退火工艺的制订提供依据。
1热平衡计算方法(1)计算加热钢丝或台架等热量消耗的基本公式为:Q=m(C1t1-C0t0) (1)式中m—钢丝或台架等重量,kgC1—加热到预定温度时的平均比热,kcal / kg.℃C0—装炉时的平均比热,kcal /kg.℃t1—预定加热温度,℃t0—钢丝或台架等原始温度,℃Q—热量消耗,kcal(2)炉体表面散热计算公式Q=qF (2)式中:q—散热系数,kcal/ m2·hF—炉体外表面积,m2公式(2)中的散热系数(q)是与炉体外表面温度相关的经验数据,从表1中可以查出相应数值。
(3)热量消秏耗换算成单位时间的电耗—功率N=860Q(3)式中:τ0—钢丝加热到预定温度的时间,h(4) 总电耗N总=K(N1+N2+N3+……+N n) (4)式中:K—安全系数公式(4)中的安全系数主要考虑电压波动、电热元件接线孔和热电偶观察孔等造成的热量损失。
发电厂生产过程锅炉热平衡及启动

发电厂生产过程锅炉热平衡及启动1. 引言发电厂是将燃料燃烧产生的热能转化为电能的重要设施,其中的锅炉是发电厂的核心设备之一。
在发电厂的生产过程中,锅炉热平衡以及启动是非常关键的环节。
本文将介绍发电厂锅炉热平衡的原理及其控制方法,并详细讨论锅炉的启动过程。
2. 发电厂锅炉热平衡锅炉热平衡是指锅炉内燃料的热能与产生的蒸汽的热能之间的平衡关系。
保持锅炉热平衡对于提高发电厂的能效和安全运行至关重要。
一般来说,锅炉热平衡可以通过以下两个方面的控制来实现:2.1 燃料供给控制燃料供给控制是指调整燃料的供给量,以使得燃烧产生的热能与所需的蒸汽热能之间达到平衡。
燃料的供给量可以通过控制燃料进料速度或燃料的燃烧速度来实现。
一般来说,当锅炉内的燃料供给过多时,会导致过热,而供给不足则会导致蒸汽产量减少。
因此,控制燃料供给量对于保持锅炉热平衡非常重要。
2.2 蒸汽流量控制蒸汽流量控制是指调整蒸汽流量,使得蒸汽的热能与所需的热能之间达到平衡。
蒸汽流量可以通过控制汽水循环系统内的阀门开度和泵的转速来实现。
一般来说,当蒸汽流量过大时,会导致过热,而流量过小则会导致蒸汽产量不足。
因此,控制蒸汽流量对于保持锅炉热平衡也是非常重要的。
3. 锅炉的启动过程锅炉的启动是指将冷态的锅炉逐渐升温并达到正常工作温度的过程。
锅炉启动过程通常包括以下几个步骤:3.1 预热在锅炉的冷态启动过程中,首先通过预热的方式将锅炉内的水加热至一定温度。
预热可以通过使用辅助燃料或者余热回收系统来实现。
预热的目的是为了提供足够的热能来加热锅炉内的水,同时也可以预防冷态下锅炉内的管道和部件因突然加热而发生损坏。
3.2 点火在锅炉预热完成后,通过点火的方式引燃燃料,并使燃料快速燃烧,产生高温高压的气体。
点火时需要注意控制燃料供给量和燃烧速度,以避免过热或者过燃的情况发生。
3.3 升温点火后,锅炉会逐渐升温,直至达到正常工作温度。
在升温过程中,需要不断调整燃料供给量和蒸汽流量,以保持锅炉的热平衡。
铸造车间感应电炉的选型

铸造车间感应电炉的选型摘要:阐述了中频电炉在现代化铸造车间中日趋广泛的应用。
讨论了感应电炉选型时需要着重考虑的各种因素:电炉容量及功率大小与工艺需求的关系,电源类型、电源与电炉的配置等与工艺需求的关系。
着重对目前感应电炉选型时比较容易混淆的电炉熔化率与生产率的关系展开了深入的讨论,并引入了功率利用系数K的概念。
此外,对选型时需要考虑的系统功能完整性、安全性、先进性、经济性以及对环保的适应性也作了详细的论述关键词:铸造车间,感应电炉,选型;1.中频感应电炉在现代化铸造车间中得到日趋广泛的应用随着固态中频电源技术的快速发展,其变换效率已逐步提高到目前的96~97%,它的操作安全性已完全能满足生产的需要,而它的投资成本却逐年下降到已低于工频电源,再考虑到它在使用上的众多优点,使得它自上世纪的80年代后期起在欧、美等发达国家得到广泛应用,基本上替代了传统的工频感应电炉。
自90年代中期起,随着我国电子技术的飞速发展,大功率的国产固态中频电源也已得到成功的开发、生产和应用。
因此,传统的工频感应电炉在我国已逐渐从销售市场上消失,铸造车间内现有的工频感应电炉也在技术改造中逐步被中频感应电炉替代。
由于中频电源的成本低、控制方便、占地小、可以与计算机控制管理系统连接等优势(见下表1),甚至连使用工业频率(50Hz)的有心感应电炉的传统的工频电源自90年代中期起在国外也开始被固态中频电源替代(输出50~200Hz)。
国内第一台配置固态中频电源的有心感应电炉(50Hz)也已经于去年问世,该电炉还配置有计算机熔化过程自动控制管理系统,对炉况、炉衬烧结、功率输入及熔化温度可实行全自动控制和检测。
表1中频与工频无心感应电炉的性能比较(以铸铁为例)由表2可见,电炉的工作频率愈高,其允许功率密度值愈高。
目前,国外制造的中频感应熔化炉的功率密度通常配置到600~800 kW/t,,小容量熔化炉的功率密度配置可高达1000 kW/t 。
电炉普通铁合金冶炼过程中热平衡分析与调控

电炉普通铁合金冶炼过程中热平衡分析与调控热平衡是电炉普通铁合金冶炼过程中关键的参数之一。
合理控制冶炼过程的热平衡可以确保铁合金的质量,提高冶炼效率和能源利用率。
本文将通过对电炉普通铁合金冶炼过程中热平衡进行分析,并探讨如何调控热平衡,从而提高铁合金的生产效益。
在电炉普通铁合金冶炼过程中,热平衡是指冶炼系统中热量的输入和输出之间的平衡状态。
一个良好的热平衡状态可以使铁合金的冶炼温度稳定,并确保合金中的合金元素得到充分的溶解和分散。
同时,热平衡还与冶炼炉体的寿命、电能消耗和环境排放等因素密切相关,因此在铁合金冶炼过程中,必须特别重视热平衡的分析和调控。
首先,进行热平衡分析时,需要考虑到炉体和冶炼过程中的热损失,这是影响热平衡的重要因素之一。
冶炼炉体的外壳和衬里的材料导热系数、厚度和温度梯度等因素都会影响热损失的大小。
此外,冶炼过程中的废气和废热也是热平衡分析的重要内容,合理回收和利用废气和废热可以减少热损失,提高热平衡。
其次,调控热平衡主要涉及到热量的输入和输出的平衡。
冶炼过程中,热量的输入主要来自电能和燃料燃烧产生的热能。
电能通过电极和炉料的电阻加热产生热能,可以通过调节电极的电流强度和电极位置来控制热量的输入。
而燃料燃烧产生的热能主要由燃料的燃烧效率和燃烧温度决定,通过控制燃料的供给量和氧气的流量来调节燃烧产生的热量。
除了热量的输入之外,还需要考虑热量的输出,即冶炼过程中冶炼系统中的热损失。
通过合理设计冶炼设备的外壳和衬里材料、加强冶炼炉体的保温措施等方式可以减少热损失。
此外,还可以通过回收和利用废气和废热来降低热损失,以提高热平衡水平。
在具体的调控操作中,还需要根据冶炼过程的实际情况和要求来确定合理的热量输入和输出。
例如,在铁合金冶炼过程中,合金元素的溶解温度是一个重要的参数。
通过调节电极电流强度和电极位置等参数,可以控制炉内的温度分布,从而确保合金元素得到充分的溶解。
同时,要特别注意电极与炉料的接触情况,保证电极与炉料的紧密接触,以减少电阻和电热效应的损失。
大型锻件锻造加热规范

水压机锻件锻造加热规范一表1是常用锻钢的锻造温度范围,表2是常用锻钢的分组。
对表1,表2中未列入的钢种,按化学成份相近的钢号确定。
二表3是热锻钢锻造加热规范。
热锻钢是指表面温度≥550'C的钢锭或钢坯。
对于温度在400至550℃之间者,应先按下表规定均热后,再按热锻钢加热。
表面温度低于400℃,截面大于1000mm的热锻钢,由车间技术组或现场值班人员临时制定专用加热曲线。
注:钢锭表面温度采用高温计或红外线测温仪测量。
测量部位在钢锭冒口线以下100mm左右的凹面上。
三、表4至衰6是各组冷锻钢锻造加热规范冷锻钢是指在常温下存放的钢锭或钢坯,对于放在露天跨的冷锻钢,冬季(当年11月至下年2月)入炉加热前,需先吊至车间内避风处放2至3天后再入炉加热。
l. 表列升温时间是总加热时间组成部份(总加热时间=升温时间+保温时间)。
对于热锻钢加热,在保证总加热时间的前提下,升温时间可根据实际加热情况缩短,但保温时间则应相应增长。
2.当具备采用高温计(或红外线测温仪)测定料温的条件时,对于热锻钢加热的升温时间及冷锻钢加热经750℃保温后的升温时间的确定,可按实际升温时间计。
实际升温时间是指从开始升温到采用高温计测定料温的确达到始锻温度止这一段加热时间。
保温时间仍按表列值要求。
3. 采用“WHF’法锻造时转子及与转子质量要求相当(主要是指超声波探伤要求)的重要锻件,保温时间按表列值的2倍计,其余锻件按表列值的1.5倍计,采用“JTS”法锻造时保温时间均按表列值的1.2倍计。
4.进行镦粗的Ⅰ、Ⅱ、Ⅲ组钢,,保温时间应按表列值增加30%.对于压钳口工序,各组钢的保温时间均可按表列值减少30-40%。
5、热锻钢的再加热,返炉时其表面温度≥1100℃时,,保温时间可按表列值减少40—50%,若表面温度在1000-1100℃时,保温时间可按表刮值减少30-40%。
当需要执行此规定时,锻坯返炉的表面温度,由车间现场值班人员和中间检查人员共同确认。
钢铁行业蓄热式工业炉窑热平衡测试与计算方法

钢铁行业蓄热式工业炉窑热平衡测试与计算
方法
钢铁行业蓄热式工业炉窑热平衡测试与计算方法是一种关键的技术,它可以帮助钢铁行业的生产过程更加高效和可靠。
这种热平衡测
试方法能够检测工业炉窑中热量的平衡,以及对燃料的使用情况进行
计算。
在进行热平衡测试时,需要将炉膛中的温度、热辐射和火焰气流
等各种参数进行测试和分析,从而确定炉窑的热平衡情况和燃烧效率。
这项技术的主要流程包括数据采集、数据处理和计算,通过这些步骤
可以获取可靠的热平衡数据以及燃烧效率等参数。
同时,该技术还具有很高的自动化水平,可以实现全面自动化的
数据采集和处理,大大提高了测试的精度和效率,减少了人为误差的
发生。
这项技术的使用,能够帮助钢铁行业的企业节约能源成本,提
高生产效率,同时还能够改善环境保护的工作。
总而言之,钢铁行业蓄热式工业炉窑热平衡测试与计算方法是一
项非常重要的技术,它能够为钢铁行业的企业提供可靠的数据和有效
的解决方案,帮助行业实现更高效的生产和更加可持续的发展。
金属冶炼中的热平衡控制

通过建立数学模型来描述金属冶炼过程中的热平衡状态,可以对各种工艺参数 进行模拟和优化。通过不断调整模型参数,可以找到最优的工艺条件,提高金 属的产量和质量,同时降低能耗和减少环境污染。
04
热平衡控制的实践案例
钢铁冶炼中的热平衡控制
总结词
钢铁冶炼中的热平衡控制是实现高效、低耗、环保生产的关键。
02
热平衡控制的重要性
热平衡对冶炼过程的影响
温度控制
热平衡是维持冶炼过程温度稳定的关键因素,温度过高或过低都可 能影响金属的熔炼效果和产品质量。
化学反应速率
热平衡对冶炼过程中的化学反应速率有重要影响,通过控制温度和 热量分布,可以优化化学反应过程,提高金属的提取率和纯度。
熔融状态保持
在金属冶炼过程中,需要保持金属处于熔融状态,热平衡是维持这一 状态的重要条件,有助于实现金属的连续熔炼和提取。
目的
金属冶炼的主要目的是满足工业 生产和人类生活的需求,提供各 种金属材料,如钢铁、铜、铝、 锌等。
金属冶炼的流程与技术
选矿
通过物理或化学方法,将矿石 中的有用成分与无用成分分离 。
熔炼
将烧结矿或直接将矿石在高温 下熔化,提取金属。
采矿
从地下或地表开采矿石,为冶 炼提供原材料。
烧结
将矿石粉或精矿制成烧结矿, 提高其冶金性能。
热平衡对金属质量的影响
金属纯度
金属组织和性能
通过控制热平衡,可以降低杂质元素 的含量,提高金属的纯度。
热平衡对金属的组织和性能有显著影 响,通过优化热平衡条件,可以获得 更优异的金属性能。
金属结晶
热平衡对金属结晶过程有重要影响, 合理的温度控制可以获得更均匀、更 细小的晶粒结构,提高金属的力学性 能。
锅炉热平衡资料
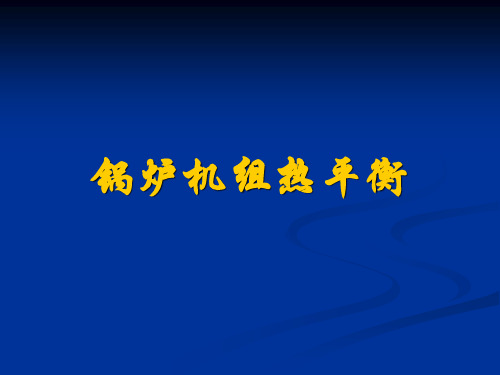
100 q1 q2 q3 q4 q5 q6
锅炉热平衡示意图
热平衡方程式各项意义
Qr Q1 Q2 Q3 Q4 Q5 Q6 Qr 1kg燃料的锅炉输入热量, kJ / kg; Q1 锅炉的有效利用热量,kJ / kg; Q2 排烟损失的热量,kJ / kg; Q3 化学不完全燃烧损失的热量,kJ / kg; Q4 机械不完全燃烧损失的热量,kJ / kg; Q5 散热损失的热量,kJ / kg; Q6 灰渣物理热损失的热量,kJ / kg
负荷 炉温 q4
化学不完全燃烧热损失
原因:由于烟气中含有可燃气体造成的热损失,燃
煤锅炉主要热损失之一,通常仅次于排烟热损失。
影响q3的因素
炉内过量空气系数
炉温 燃烧速度慢 q3 氧供应不足 q3
燃料挥发分含量
挥发分含量高 q3
炉温以及炉内空气动力工况
炉温 燃烧速度慢 q3 炉膛有死角或燃料在炉内停留时间短 q3
研究锅炉热平衡的意义
研究锅炉热平衡的意义,就在于弄清燃料中的 热量有多少被有效利用,有多少变成热损失,依据 热损失分别表现在那些方面和大小如何,以便判断 锅炉设计和运行水平,进而寻求提高锅炉经济性的 有效途径。锅炉设备在运行中应定期进行热平衡试 验(通常称热效率试验),以查明影响锅炉效率的 主要因素,作为改进锅炉的依据。
煤锅炉主要热损失之一,通常仅次于排烟热损失。
影响q4的因素
燃烧方式:层燃炉、沸腾炉较大,旋风炉较小,煤 粉炉介于两者之间。 燃料性质:煤中灰分和水分越多,挥发份含量越少, q4 越大 煤粉细度:煤粉越粗,q4越大
过量空气系数 炉温 ,不利于燃烧,q4
不利于燃料完全燃烧,q4
钢铁行业蓄热式工业炉窑热平衡测试及计算方法编制说明

钢铁行业蓄热式工业炉窑热平衡测试及计算方法编制说明《钢铁行业蓄热式工业炉窑热平衡测试与计算方法》行业标准编制说明一工作简况1任务来源根据工信部工信厅科[2010]74号“关于印发2010年第一批行业标准制修订计划的通知”中规定,由中钢集团鞍山热能研究院有限公司负责组织制定《钢铁行业蓄热式工业炉窑热平衡测试及计算方法》行业标准。
本项是根据国家节能减排精神和钢铁行业结构调研的要求,2010年初由中国钢铁工业协会联合中钢集团鞍山热能研究院有限提出有关蓄热式工业炉窑热平衡测试与计算方法的标准项目并提交上级主管部门立项。
2 工作过程2.1开展的阶段工作立项批准后,由中钢集团鞍山热能研究院有限公司、冶金工业信息标准研究院牵头组织专家走访有关生产、设计、使用、施工、测试等单位,了解国内蓄热式工业炉窑应用情况,同时收集国外有关技术资料及应用情况,并成立了标准起草小组,这些工作都为制定标准打下基础。
2010年7月召开标准工作组第一次工作会,讨论标准初稿,并确定工作分工;(修改)2.2国内外情况调研从国内外蓄热式燃烧技术发展看,早在1858年出现了蓄热式回收余热装置,1950’S 考贝尔和西门子发明了炼铁炉和炼钢炉的蓄热室,而后广泛应用于热风炉和焦炉等回收烟气余热来预热空气,但由于体积庞大,蓄热体厚,换向时间长,预热温度波动大,热回收率低,无法推广应用。
直到80年代,英国燃气公司(British Gas)开发了蓄热式烧嘴,同时期,在欧洲出现的一种以陶瓷球为载体介体的蓄热式回收废热系统,1984年英国Hotwork和British Gas 公司推出的紧凑型蓄热室,均使得燃烧空气预热温度可以在工业生产条件下,稳定地达到1000℃,称为RCB型烧嘴(Regenerative Ceramic Burner),主要特点是将燃烧器与蓄热室余热回收装置结合一体,介质预热温度比金属换热器高许多。
1984年首次应用于Avesta Sheffild公司的不锈钢退火炉,1988年在Rotherham Engineering Steel公司的大方坯步进梁式炉上全面应用。
金属冶炼中的热力学平衡与非平衡状态

在非平衡状态下,有色金属冶炼过程中可能会出现金属损失、分离效果不佳等问题,导致资源的浪费。为了提高金属提取率和资源利用率,需要深入研究热力学平衡和非平衡状态的影响因素,并采取相应的措施进行优化和控制。
总结词
总结词:新兴金属冶炼涉及到一些新兴领域和高新技术产业。
感谢您的观看
THANKS
02
选择适宜的添加剂
选择适当的添加剂可以改变反应体系的热力学性质,促进热力学平衡的形成。
03
非平衡状态在金属冶炼中的影响
指系统各部分之间热力学相互作用的状态,与平衡状态相对。
非平衡状态
系统内部各部分之间没有宏观的能量和物质交换,系统达到稳定状态。
热力学平衡
系统内部各部分之间存在宏观的能量和物质交换,系统处于不稳定状态。
非平衡状态则是指系统偏离热力学平衡状态的情况,此时反应速率不为零,物质和能量在不断转移和变化。
在金属冶炼过程中,热力学平衡和非平衡状态相互作用,共同决定着冶炼过程和产物的性质。
优化策略一
优化策略二
优化策略三
根据热力学平衡原理,选择合适的反应条件(如温度、压力、组分浓度)以促进所需反应的正向进行,提高金属的提取率和纯度。
金属冶炼中的热力学平衡与非平衡状态
contents
目录
金属冶炼的基本原理热力学平衡在金属冶炼中的应用非平衡状态在金属冶炼中的影响热力学平衡与非平衡状态在金属冶炼中的关系案例分析
01
金属冶炼的基本原理
氧化焙烧
通过添加氧化剂(如空气或纯氧),将矿石中的有价金属氧化成高价态,使其更容易与脉石分离。
矿石准备
将矿石破碎、磨细成粉,以便进行后续的化学或物理处理。
还原熔炼
在高温下,通过加入还原剂(如碳或氢气),将高价态的有价金属还原成金属单质或合金。
冶金炉热平衡

冶金炉热平衡1、热平衡原则(1)热平衡是以热力学第一定律为基础,遵循能量守恒原理,研究系统能量进出平衡关系,反映能量消耗、有效利用和能量损失之间的平衡⑵冶金热平衡是指冶金炉体系热量收、支平衡,能量消耗和有效利用、能量损失之间的平衡关系。
是冶金炉热工常用的分析方法。
⑶热平衡结果,可用热平衡方程、热平衡表及热流图表示。
2.冶金炉热平衡计算的目的:(1)通过现场测试,编制热平衡表,分析炉子的热工作,判断热量的利用是否合理,找出提高热效率的途径;(2)在设计加热炉时,通过计算编制热平衡表,从热平衡关系中找出燃料消耗等未知量。
将热收入和热支出与现有加热炉进行比较,以帮助设计师判断设计方案的优缺点。
3.冶金炉热平衡的主要内容3.1热平衡区域划定在热平衡计算中,热量的收集和消耗项目是根据所选的热平衡系统确定的,因此必须首先划定热平衡系统的区域,进入该区域的热量应视为热收集器。
相反,这是热量消耗。
热平衡区域的划分视需要而定,通常有炉膛区域、预热区域及全炉区域。
有时,可将炉子某一特定区域作为热平衡计算所划定的区域,例如可以将炉膛沿炉长方向划定几个区域分别作区域热平衡计算。
不同指定区域的热量收入和热量支出项目不同。
例如:某炉由炉膛及空气换热器两部分组成,如图所示。
图13.17热平衡区划分图13.18全炉热平衡模型炉膛区域热平衡式为:qdw+qα=qs+qcp+qω其中热量收入项qdw---燃料的燃烧热qα——预热空气带来的物理热热量支出项qs---加热炉料的有效热QCP——烟气带走的热量Qω——炉内各种热损失换热器域热平衡式为:qcp=qp+qα+qcω其中热量收入项qcp---炉堂烟气所带入的热热耗QP——空气预热的物理热qα---换热器各项热损失qcω——烟气带走的热量和整个炉膛的热平衡为:qdw=qs+qp+(qω+qcω)其中:(q)ω+qcω)——整个炉膛的热损失不难看出炉膛热平衡与全炉热平衡的差别。
由于区域不同,对炉膛来说qα是热收入;但对全炉来说,热收入不包括qα,是其内部的循环热量,因为供给炉子的是冷空气,qα是来自换热器从炉膛烟气回收的热,而不是另外供给的热。
锻造炉的热平衡与热失控预警技术

锻造炉的热平衡与热失控预警技术锻造炉是一种常见的工业设备,用于加热和塑造金属材料。
在锻造炉的运行过程中,热平衡的维持和热失控的预警都是至关重要的。
热平衡可以确保锻造炉的稳定运行,而热失控的预警则能有效避免事故的发生。
本文将详细介绍锻造炉的热平衡原理和热失控预警技术。
一、锻造炉的热平衡原理热平衡是指锻造炉内部各部件的温度保持在合适的范围内,确保锻造过程的稳定进行。
锻造炉的热平衡原理主要与炉内的热传导和热辐射有关。
1. 热传导:锻造炉内部的热传导主要通过材料之间的热量传递来实现。
金属材料是良好的导热体,在锻造炉的加热过程中,热量会通过钢材、炉衬等材料不断传递和吸收,以实现热平衡。
2. 热辐射:锻造炉内的高温会产生辐射热,即热辐射。
通过调整锻造炉内的辐射热能的吸收和辐射,可以实现热平衡。
辐射热会被锻造炉内的材料吸收并转化为热能,通过炉内空气的对流和传导释放出去。
为了实现锻造炉的热平衡,我们需要关注以下几个方面:1. 温度控制:通过精确控制加热器的温度、热工作介质的流量和温度来调整锻造炉的加热过程,以达到所需的加热效果。
2. 材料选择:选择合适的材料作为锻造炉的炉衬、加热元件等部件,以确保良好的导热和热辐射性能。
3. 假设参数:对于复杂的锻造炉系统,我们可以借助计算机仿真的方法,根据实际工艺参数和炉内的材料特性,建立数学模型,通过模拟计算,预测和控制炉内的热平衡情况。
二、锻造炉的热失控预警技术热失控是指锻造炉内部温度失去控制,导致过热、燃烧或其他危险情况的发生。
为了避免热失控造成的事故,需要采取相应的热失控预警技术。
1. 温度监测:通过在锻造炉的关键位置安装温度传感器,实时监测锻造炉内的温度变化。
当温度超出设定的安全范围时,即可发出预警信号,提醒操作员及时采取措施。
2. 烟气监测:锻造炉的失控往往伴随着烟气的产生。
通过安装烟雾传感器和氧气传感器,可以监测炉内的烟气浓度和氧气含量。
当烟气浓度或氧气含量异常上升时,即可发出预警信号。
热电平衡量计算
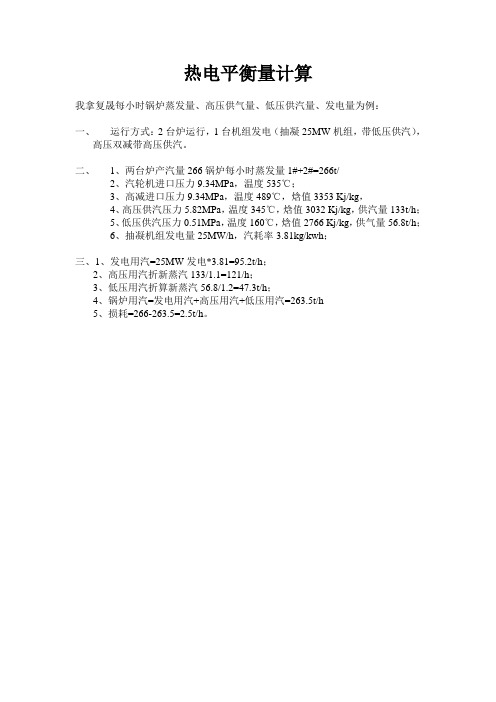
热电平衡量计算
我拿复晟每小时锅炉蒸发量、高压供气量、低压供汽量、发电量为例:
一、运行方式:2台炉运行,1台机组发电(抽凝25MW机组,带低压供汽),
高压双减带高压供汽。
二、1、两台炉产汽量266锅炉每小时蒸发量1#+2#=266t/
2、汽轮机进口压力9.34MPa,温度535℃;
3、高减进口压力9.34MPa,温度489℃,焓值3353 Kj/kg,
4、高压供汽压力5.82MPa,温度345℃,焓值3032 Kj/kg,供汽量133t/h;
5、低压供汽压力0.51MPa,温度160℃,焓值2766 Kj/kg,供气量56.8t/h;
6、抽凝机组发电量25MW/h,汽耗率3.81kg/kwh;
三、1、发电用汽=25MW发电*3.81=95.2t/h;
2、高压用汽折新蒸汽133/1.1=121/h;
3、低压用汽折算新蒸汽56.8/1.2=47.3t/h;
4、锅炉用汽=发电用汽+高压用汽+低压用汽=263.5t/h
5、损耗=266-263.5=2.5t/h。
- 1、下载文档前请自行甄别文档内容的完整性,平台不提供额外的编辑、内容补充、找答案等附加服务。
- 2、"仅部分预览"的文档,不可在线预览部分如存在完整性等问题,可反馈申请退款(可完整预览的文档不适用该条件!)。
- 3、如文档侵犯您的权益,请联系客服反馈,我们会尽快为您处理(人工客服工作时间:9:00-18:30)。
1350kVA 电煅炉的热平衡马历乔,陈杰,王柏钢,张桂兰,向左良(兰州炭素股份有限公司,甘肃兰州730084)HEA T BALANCE OF THE 1350kV A ELECTRIC CALCINERM A Li qiao,CHEN Jie,WANG Bai gang,ZHANG Gui lan,XIANG Zuo liang(Lanzhou Carbon Co LTD,Lanzhou,Gansu,730084,China)无烟煤在用于炭素制品生产之前必须经过煅烧,以除去其中的挥发分,并使无烟煤的电阻率降低。
研究表明,在用于高炉和铝电解槽砌筑时,就炉衬寿命而言,电煅无烟煤炭块优于煤气煅烧的无烟煤炭块,这是由于电煅无烟煤与煤气煅烧的无烟煤相比,平均煅烧温度高,有较低的电阻率和气化反应率,较高的真密度、抗碱金属侵蚀性和导热性[1]。
最近几年,随着国内炼铝工业的飞速发展,阴极炭块需求量猛增,一些中小型炭素厂相继建成了电煅烧炉,如今,电煅烧已成为炭块生产中的关键技术。
电煅烧炉要消耗大量宝贵的电能,通常生产1t 电煅无烟煤大约要消耗550~1150kW h 的电能[2],并产生大量的废热,于是,节能及废热的回收和利用就成为关注企业经济效益人士所研究的课题。
热平衡的测算是节能及废热利用研究的基础工作,国外曾有人进行过电煅烧炉热平衡的测算[2],而在国内,类似的工作尚未有报道,本文对兰州炭素股份有限公司1350kVA 电煅炉的热平衡进行了测算,并提出了节能及废热利用方面的一些建议。
1 电煅烧炉内的物料平衡在热平衡的测算之前应了解电煅炉内的物料平衡。
电煅炉内的基本物料平衡方程为:m 前=m 后+m 挥式中:m 前 煅前无烟煤流量,kg/s;m 后 煅后无烟煤流量,kg/s;m 挥 煅烧产生的挥发物流量,kg/s 。
经实测得到m 前=17t/d =0.1968kg/s,挥发物产率(即烧损率)为14.85%。
因此:m 挥=0.1968!0.1485=0.0292kg /s m 后=0.1968-0.0292=0.1676kg /s 。
2 1350kVA 电煅炉热平衡测算就电煅炉本身而言,其基本热平衡方程为:Q 电=Q 径+Q 挥+Q 无+Q 余式中:Q 电 电气给热(输入功率),kW;Q 径 电煅炉径向散热,kW;Q 挥 挥发物带走的热量,kW;Q 无 煅后无烟煤带走的热量,kW;Q 余 其余部分,即电气损失,夹持器冷却和吸热反应吸收的热量,kW 。
2.1 电气给热(输入功率)电煅烧炉正常运行时变压器功率为680kW,因此电气给热Q 电=680kW,如果以煅后无烟煤为基准时,电气给热变换单位,此时Q ∀电=680/(0.1676!3600/1000)=1127kW h/t(煅煤)。
2.2 电煅炉径向散热[3]经测定,炉皮温度t s =208.3#,周围主体空气温度t b =10#,电煅炉特征高度H =6.025m,因此作者简介:马历乔 男 1969年10月生,1992年毕业于北京化工大学化工学院化学工程专业,主要从事炭素工艺研究收稿日期:2001-03-20编辑 朱海哲2001年第5期总第116期CARBON TECHNIQUES炭 素 技 术2001∃5SUM116取定性温度t=(208.3+10)/2=109.2#,此时空气的体积膨胀系数 =1/(109.2+273)= 2.616! 10-3K-1,导热系数 =0.033W/m K,比热C P= 1.009!103J/kg K,粘度=22.6!10-6Pa.s,运动粘度!=/∀=22.6!10-6 0.9124=24.27! 10-6m2/s,普朗特准数P!=C P/ =1.009!103!22.6!10-6/0.033=0.691,格拉霍夫准数G!= g#tH3/!2=2.616!9.81!(208.3-10)!6.0253/ (24.77!10-6)2=1.814!1012,因此,自然对流给热系数∃对=0.135! /H!(P! G!)1/3=0.135!0.033/6.025!(0.691!1.814!1012)1/3=7.97W/m2 K钢板的黑度取%=0.8,辐射常数C0=5.669W/ m2 K4,则辐射给热系数∃辐=%C0{[(t s+273)/100]4-[(t b+273)/ 100]4}/(t s-t b)=0.8!5.669!{[(208.3+273)/100]4 -[(10+273)/100]4}/(208.3-10)=10.81W/m2 K 总给热系数∃=∃对+∃辐=7.97+10.81=18.78W/m2 K电煅炉外径d= 2.298m,因此,径向散热Q径=&d H ∃ #t=3.14!2.298!6.025!18.78!(208.3-10)=161.9kW以煅后无烟煤为基准时Q∀径=161.9/(0.1676!3600 1000)=268kW h/t(煅煤)2.3 挥发物带走的热量经测定挥发物气体的体积分数为H2:73.5%, CO:23.5%,CH4:3.0%,换算成质量分数为:H2: 17.2%,CO:77.1%,CH4:5.7%。
烟道温度为1000#,挥发物产生温度(平均)为700#。
由文献[4]查得H2,CO,CH4的比热与温度的关系式并经过计算得到700~1000#之间混合气体的平均比热C P= 4.385!103J/kg K。
因此,挥发物带走的热量:Q挥=C P #t m挥=38.41kW以煅后无烟煤为基准时Q∀挥=38.41/(0.1676!3600/1000)=64kW h/t(煅煤)2.4 煅后无烟煤带走的热量离开煅烧带时煅后无烟煤的平均温度为1400 #,由文献[5]中的数据经计算得无烟煤在25~1400#时的平均比热C P=1.732!103J/kg K,因此,煅后无烟煤带走的热量Q无=C P #t m后=1.732!103!(1400-25) !0.1676=399.14kW以煅后无烟煤为基准时Q∀无=399.14/(0.1676!3600/1000)=662kW h/t(煅煤)2.5 其他热损失(电气损失,夹持器冷却和吸热反应吸收的热量)由差值可求得电气损失,夹持器冷却和吸热反应吸收的热量总和Q余=Q电-Q径-Q挥-Q无=680-161.9-38.41-399.14=80.55kW 以煅后无烟煤为基准时Q∀余=80.55/(0.1676!3600 1000)=134kW h t(煅煤)3 结果讨论根据上述测算结果可得1350kVA电煅炉的热平衡如表1所示,表1还列出了法国Savie公司电煅炉的热平衡状况[2]。
从表1可看出,兰炭1350kVA电煅炉的吨煤能耗与Savie公司传统炉一样多,是Sav ie公司新式炉的2倍,而且与Savie公司传统炉相比,兰炭1350 kVA电煅炉的径向热损失要大得多,在同样条件下,必然造成炉内更大的温度梯度,影响煅后无烟煤质量。
兰炭1350kVA电煅炉无烟煤带走的热量比Savie公司传统炉少,是由于径向散热快,无烟煤在高温下保持时间短,部分热量来不及带出煅烧区就散失掉了。
Savie公司新式炉的吨煤能耗非常低,仅为传统炉的一半,这是由于新式炉对炉内物流和热流进行了特殊的调整。
它是用一台风机将炉内气体抽出,然后经冷却和洗涤后(废热回收)再从炉底返回炉表1 电煅炉热平衡表kW h/t(煅煤)兰炭1350kVA电煅炉Savie公司传统炉Savie公司新式炉入热:电气给热11271150550出热:径向散热268134165挥发物带走644281无烟煤带走662836202其他热损失13413810347第5期 马历乔 1350kVA电煅炉的热平衡内,冷却气体通过已高温煅烧的无烟煤,经热交换使出炉无烟煤冷却,循环气体与无烟煤流向相反,当气体在炉内上升时,因含氢量高,很易扩散,在中心热区和四周冷却区增加了径向热传导,提高了温度分布均匀性,当气体进一步达到煅烧炉上部时,进入炉内的生无烟煤被气体干燥和预热。
Savie 公司的这种设计实际上是回收了煅后无烟煤带出的热量,使热量重新回到炉内,使能耗大大降低,而且提高了煅烧均匀性,省去了煅后无烟煤冷却设备,一举多得,很值得学习。
参考文献:[1]WIL L IAM S M M.Electrically calcined anthracite forpotling[J].L ight M etals ,1972:163.[2]BERN ARD J C,et al.Electr ical calcination of anthracites:anew technolo gy[J].L ight M etals,1987:581.[3]陈敏恒,等编.化工原理(上册)[M ].北京:化学工业出版社,1988:205.[4]罗义贤编.物理化学[M ].北京:冶金工业出版社,1990:294.[5]张家埭编.碳材料工程基础[M ].北京:冶金工业出版社,1992月第一版:17.炭素专利公开号:CN 1277148A 公开日:2000-12-20申请人:李铁真 共同申请人:株式会社日进纳米技术发明人:李铁真柳在银发明名称:通过在扩散炉中热处理气相净化碳纳米管的方法利用酸性气体的热解气相净化碳纳米管。
该碳纳米管的净化方法包括:在具有适于热处理的炉管的扩散炉中,利用热分解的酸性气体净化碳纳米管。
酸性气体包括盐酸气或硝酸气,并可以与例如氢等稀释气体一起向炉管内供应。
公开号:CN 1278021A 公开日:2000-12-27申请人:李铁真 共同申请人:株式会社日进纳米技术发明人:李铁真柳在银发明名称:低温热化学气相沉积设备及利用该设备合成碳纳米管的方法一种低温热CV D 设备和利用设备合成碳纳米管的方法,是将该设备中的反应管分成在空间上邻接气体输入部分、用于热分解输入气体的第一区,和空间上邻接排气部分、用于利用前述的分解气体合成碳纳米管第二区,并且,保持两区的温度,使第二区的温度低于第一区的温度。
将具有第一金属催化膜的第一基片用腐蚀气腐蚀,形成纳米级催化颗粒,利用上述设备热分解碳源气,在其温度低于第一区的第二区中,从催化颗粒上合成碳纳米管。
公开号:CN 1275528A 公开日:2000-12-06申请人:喻承庚发明人:喻承庚发明名称:一种活性炭生产工艺本发明涉及一种工业材料的制备与处理,尤其涉及一种活性炭生产工艺。
其工艺过程为原料准备 装钵 炭化 烟气活化 水蒸汽活化 风选 酸洗 烘干 球磨 成品包装;炭化工艺采用焖烧的方法;烟气活化是用炭化过程中产生的烟气来活化已被炭化的原料;水蒸汽活化是用水蒸汽对原料进行活化。