M45x QuadCopterController Solution Introduction(SC)
迈克罗斯 47007-0005450 远程控制器用户指南说明书

For countries outside the European Union:
If you wish to discard these items, please contact your local authorities or dealer and ask for the correct method of disposal.
• If you must operate this unit while driving, do not take your eyes off the road or an accident could result.
• If any of the following problems occur, immediately stop using this unit and consult your dealer from whom you purchased this unit: – smoke coming from the unit. – abnormal odors or smells. – a foreign object has entered the unit. – liquid has been spilled on or into the unit. If you continue to use the unit when it is not operating properly, damage could result in an accident or fire.
Notes
• Depending on the car stereo, there may not be some buttons with the same names as those on this unit.
Mellanox ConnectX-4 高性能低延迟网络适配器产品指南说明书

Mellanox ConnectX-4 AdaptersProduct GuideConnectX-4 from Mellanox is a family of high-performance and low-latency Ethernet and InfiniBand adapters. The ConnectX-4 Lx EN adapters are available in 40 Gb and 25 Gb Ethernet speeds and the ConnectX-4 Virtual Protocol Interconnect (VPI) adapters support either InfiniBand or Ethernet.These adapters address virtualized infrastructure challenges, delivering best-in-class performance to various demanding markets and applications. Providing true hardware-based I/O isolation with unmatched scalability and efficiency, achieving the most cost-effective and flexible solution for Web 2.0, Cloud, data analytics, database, and storage platforms.The following figure shows the Mellanox ConnectX-4 2x100GbE/EDR IB QSFP28 VPI Adapter (the standard heat sink has been removed in this photo).Figure 1. Mellanox ConnectX-4 2x100GbE/EDR IB QSFP28 VPI Adapter (heatsink removed)Did you know?Virtual Protocol Interconnect (VPI) enables standard networking, clustering, storage, and management protocols to seamlessly operate over any converged network by leveraging a consolidated software stack. Each port can operate on InfiniBand, Ethernet, or Data Center Bridging (DCB) fabrics, and supports Ethernet over InfiniBand (EoIB) as well as RDMA over Converged Ethernet (RoCE). VPI simplifies I/O system design and makes it easier for IT managers to deploy infrastructure that meets the challenges of a dynamic data center.Click here to check for updatesFigure 2. ThinkSystem Mellanox ConnectX-4 Lx 10/25GbE SFP28 2-port OCP Ethernet Adapter Supported transceivers and cablesThis section lists the supported transceivers and cables:25 Gb Ethernet adapters25 Gb Ethernet adaptersThe following table lists the supported transceivers.Table 3. TransceiversPart number Feature code Description10Gb Transceivers46C34475053SFP+ SR Transceiver4TC7A78615BNDR ThinkSystem Accelink 10G SR SFP+ Ethernet transceiver4TC7A90142BWG5SFP+ 10G LR Transceiver PRC only (for China only)25Gb Transceivers4M27A67041BFH2Lenovo 25Gb SR SFP28 Ethernet Transceiver7G17A03537AV1B Lenovo Dual Rate 10G/25G SR SFP28 Transceiver4TC7A88638BYBJ ThinkSystem Finisar Dual Rate 10G/25G SR SFP28 TransceiverThe following table lists the supported cables.Table 4. Supported DAC cables - 25 Gb EthernetPart number Feature code Description25 GbE SFP28 DAC cables7Z57A03557AV1W Lenovo 1m Passive 25G SFP28 DAC Cable7Z57A03558AV1X Lenovo 3m Passive 25G SFP28 DAC Cable7Z57A03559AV1Y Lenovo 5m Passive 25G SFP28 DAC CableLC-LC OM3 Fiber Optic Cables (these cables require a transceiver)00MN499ASR5Lenovo 0.5m LC-LC OM3 MMF Cable00MN502ASR6Lenovo 1m LC-LC OM3 MMF Cable00MN505ASR7Lenovo 3m LC-LC OM3 MMF Cable00MN508ASR8Lenovo 5m LC-LC OM3 MMF Cable00MN511ASR9Lenovo 10m LC-LC OM3 MMF Cable00MN514ASRA Lenovo 15m LC-LC OM3 MMF Cable00MN517ASRB Lenovo 25m LC-LC OM3 MMF Cable00MN520ASRC Lenovo 30m LC-LC OM3 MMF Cable25Gb transceivers: When installed in this 25Gb Ethernet adapter, 25Gb transceivers are designed to operate at either 25 Gb/s or 10 Gb/s speeds as listed in the description of the transceiver, however the speed also depends on the negotiation with the connected switch. In most configurations, this negotiation is automatic, however in some configurations you may have to manually set the link speed or FEC mode.In addition, the 25Gb adapters also can share a connection to a 100 Gb switch using a 4:1 breakout cable. Supported breakout cables (fiber optic and AOC) are listed in the following table.Table 5. Breakout cables for connectivity to a 100Gb switchPart number Feature code DescriptionMTP-4xLC OM3 MMF Breakout Cable00FM412A5UA Lenovo 1m MPO-4xLC OM3 MMF Breakout Cable00FM413A5UB Lenovo 3m MPO-4xLC OM3 MMF Breakout Cable00FM414A5UC Lenovo 5m MPO-4xLC OM3 MMF Breakout Cable100G Breakout OM4 MPO Cables (these cables require a transceiver)7Z57A03573AV2B Lenovo 1m MPO to 4x LC Breakout OM4 MMF Cable7Z57A03574AV2C Lenovo 3m MPO to 4x LC Breakout OM4 MMF Cable7Z57A03575AV2D Lenovo 5m MPO to 4x LC Breakout OM4 MMF CableQSFP28 100Gb Ethernet Breakout Active Optical Cables7Z57A03552AV1S Lenovo 5m 100G to 4x25G Breakout Active Optical Cable7Z57A03554AV1U Lenovo 15m 100G to 4x25G Breakout Active Optical CableQSFP28 100G-to-4x25G Ethernet Breakout Cables7Z57A03564AV22Lenovo 1m 100G QSFP28 to 4x25G SFP28 Breakout DAC Cable 4Z57A85043BS32Lenovo 1.5m 100G to 4x25G Breakout SFP28 Breakout DAC Cable 4Z57A85044BS33Lenovo 2m 100G to 4x25G Breakout SFP28 Breakout DAC Cable 7Z57A03565AV23Lenovo 3m 100G QSFP28 to 4x25G SFP28 Breakout DAC Cable 7Z57A03566AV24Lenovo 5m 100G QSFP28 to 4x25G SFP28 Breakout DAC CableIn addition, the 25Gb adapters also support the following 10 GbE AOC/DAC cables.Table 6. Supported optical transceivers and DAC cables - 10 Gb EthernetPart number Feature code DescriptionSFP+ 10Gb Active Optical Cables00YL634ATYX Lenovo 1m SFP+ to SFP+ Active Optical Cable00YL637ATYY Lenovo 3m SFP+ to SFP+ Active Optical Cable00YL640ATYZ Lenovo 5m SFP+ to SFP+ Active Optical Cable00YL643ATZ0Lenovo 7m SFP+ to SFP+ Active Optical Cable00YL646ATZ1Lenovo 15m SFP+ to SFP+ Active Optical Cable00YL649ATZ2Lenovo 20m SFP+ to SFP+ Active Optical Cable10Gb SFP+ Passive DAC cables00D6288A3RG0.5m Passive DAC SFP+ Cable90Y9427A1PH1m Passive DAC SFP+ Cable00AY764A51N 1.5m Passive DAC SFP+ Cable00AY765A51P2m Passive DAC SFP+ Cable90Y9430A1PJ3m Passive DAC SFP+ Cable90Y9433A1PK5m Passive DAC SFP+ Cable00D6151A3RH7m Passive DAC SFP+ Cable10Gb SFP+ Active DAC cables00VX111AT2R Lenovo 1m Active DAC SFP+ Cables00VX114AT2S Lenovo 3m Active DAC SFP+ Cables00VX117AT2T Lenovo 5m Active DAC SFP+ CablesThe following figure shows the Mellanox ConnectX-4 Lx ML2 1x25GbE SFP28 Adapter.Figure 3. Mellanox ConnectX-4 Lx 10/25GbE SFP28 1-port ML2 Adapter (heatsink removed)FeaturesThe ConnectX-4 family of adapters offer a number of performance features, including the following: ConnectX-4 Lx Ethernet adaptersThe ConnectX-4 Lx adapters discussed in this product guide offer a high performance Ethernetadapter solution for Ethernet speeds up to 40 Gb/s, enabling seamless networking, clustering, or storage. The Lx adapters reduce application runtime, and offer the flexibility and scalability to make infrastructure run as efficiently and productively as possible.ConnectX-4 100 Gb Ethernet / EDR InfiniBandConnectX-4 with Virtual Protocol Interconnect (VPI) offers the highest throughput VPI adapter,supporting EDR 100Gb/s InfiniBand and 100Gb/s Ethernet and enabling any standard networking, clustering, or storage to operate seamlessly over any converged network leveraging a consolidated software stack.I/O VirtualizationFigure 4. Mellanox ConnectX-4 Lx 1x40GbE QSFP+ Adapter (heatsink removed) Technical specificationsPCIe 3.0 host interface:ConnectX-4 Lx Ethernet adapters: PCIe 3.0 x8 interfaceConnectX-4 EDR InfiniBand / 100 Gb Ethernet adapter: PCIe 3.0 x16 interface Support for MSI/MSI-X mechanismsExternal connectors:25 Gb PCIe and ML2 adapters: SFP2840 Gb and 100 Gb adapters: QSFP28Server support - ThinkSystemThe following tables list the ThinkSystem servers that are compatible. Table 7. Server support - ThinkSystem (Part 1 of 3)PartNumber Description Edge1S IntelV2AMD V3Intel V3ConnectX-4 Lx 25 Gb Ethernet adapters01GR250Mellanox ConnectX-4 Lx 10/25GbESFP28 2-port PCIe EthernetAdapterN N N N N N N N N N N N N N N N N N N4XC7A08249ThinkSystem Mellanox ConnectX-4Lx 10/25GbE SFP28 2-port PCIeEthernet AdapterY N N N N N N N N N N N N N N N N N N4XC7A08246ThinkSystem Mellanox ConnectX-4Lx 10/25GbE SFP28 2-port OCPEthernet AdapterN N N N N N N N N N N N N N N N N N N7ZT7A00507ThinkSystem Mellanox ConnectX-4Lx 10/25GbE SFP28 2-Port ML2Ethernet Adapter N N N N N N N N N N N N N N N N N N N SE35(7Z46/7D1X)SE35V2(7DA9)SE36V2(7DAM)SE45(7D8T)SE455V3(7DBY)ST5V2(7D8K/7D8J)ST25V2(7D8G/7D8F)SR25V2(7D7R/7D7Q)SR635V3(7D9H/7D9G)SR655V3(7D9F/7D9E)SR645V3(7D9D/7D9C)SR665V3(7D9B/7D9A)SR675V3(7D9Q/7D9R)ST65V3(7D7B/7D7A)SR63V3(7D72/7D73)SR65V3(7D75/7D76)SR85V3(7D97/7D96)SR86V3(7D94/7D93)SR95V3(7DC5/7DC4)PartNumber Description Dense V32S Intel V2AMD V1Dense V24SV28SConnectX-4 Lx 25 Gb Ethernet adapters01GR250Mellanox ConnectX-4 Lx10/25GbE SFP28 2-port PCIeEthernet AdapterN N N N N N N N N N N N N N N N N N N Y4XC7A08249ThinkSystem MellanoxConnectX-4 Lx 10/25GbESFP28 2-port PCIe EthernetAdapterN N N N N Y Y N Y Y N Y Y Y N N N N N N4XC7A08246ThinkSystem MellanoxConnectX-4 Lx 10/25GbESFP28 2-port OCP EthernetAdapterN N N N N Y Y N Y Y N Y Y N N N N N N N7ZT7A00507ThinkSystem MellanoxConnectX-4 Lx 10/25GbESFP28 2-Port ML2 EthernetAdapter N N N N N N N N N N N N N N N N N N N Y SD665V3(7D9P)SD665-NV3(7DAZ)SD65V3(7D7M)SD65-IV3(7D7L)ST65V2(7Z75/7Z74)SR63V2(7Z7/7Z71)SR65V2(7Z72/7Z73)SR67V2(7Z22/7Z23)SR635(7Y98/7Y99)SR655(7Y/7Z1)SR655ClientOSSR645(7D2Y/7D2X)SR665(7D2W/7D2V)SD63V2(7D1K)SD65V2(7D1M)SD65-NV2(7D1N)SN55V2(7Z69)SR85V2(7D31/7D32)SR86V2(7Z59/7Z6)SR95(7X11/7X12)PartNumber Description4S V11S Intel V12S Intel V1Dense V1ConnectX-4 Lx 25 Gb Ethernet adapters01GR250Mellanox ConnectX-4 Lx 10/25GbESFP28 2-port PCIe EthernetAdapterY Y Y N N N Y Y N N N N Y Y N N N N N4XC7A08249ThinkSystem Mellanox ConnectX-4Lx 10/25GbE SFP28 2-port PCIeEthernet AdapterN N N N N N N N N N N N N N N N N N N4XC7A08246ThinkSystem Mellanox ConnectX-4Lx 10/25GbE SFP28 2-port OCPEthernet AdapterN N N N N N N N N N N N N N N N N N N7ZT7A00507ThinkSystem Mellanox ConnectX-4Lx 10/25GbE SFP28 2-Port ML2Ethernet AdapterY Y Y N N N N N N N N N Y Y N N N N N SR85(7X18/7X19)SR85P(7D2F/2D2G)SR86(7X69/7X7)ST5(7Y48/7Y5)ST25(7Y45/7Y46)SR15(7Y54)SR25(7Y52/7Y51)ST55(7X9/7X1)SR53(7X7/7X8)SR55(7X3/7X4)SR57(7Y2/7Y3)SR59(7X98/7X99)SR63(7X1/7X2)SR65(7X5/7X6)SR67(7Y36/7Y37)SD53(7X21)SD65(7X58)SN55(7X16)SN85(7X15)Server support - System xThe following tables list the System x and dense servers that are compatible.Support for System x and dense servers with Xeon E5 v4 and E3 v5 processorsTable 10. Support for System x and dense servers with Xeon E5 v4 and E3 v5 processorsPartnumber DescriptionConnectX-4 Lx Ethernet adapters01GR250Mellanox ConnectX-4 Lx 10/25GbE SFP28 2-port PCIeAdapterN N Y Y Y Y N N00MN990Mellanox ConnectX-4 Lx 10/25GbE SFP28 1-port ML2AdapterN N Y Y Y Y N N7ZT7A00507Mellanox ConnectX-4 Lx 10/25GbE SFP28 2-Port ML2AdapterN N N N N N N N 00MM950Mellanox ConnectX-4 Lx 1x40GbE QSFP+ Adapter N N Y Y Y Y N N ConnectX-4 VPI InfiniBand adapters7XC7A05524Mellanox ConnectX 4 PCIe FDR 1 Port QSFP VPI Adapter N N N N N N N N 7ZT7A00500Mellanox ConnectX-4 PCIe FDR 2-Port QSFP VPI Adapter N N N N N N N N00MM960Mellanox ConnectX-4 2x100GbE/EDR IB QSFP28 VPI Adapter N N Y Y Y Y N N x325M6(3943)x325M6(3633)x355M5(8869)x365M5(8871)x385X6/x395X6(6241,E7v4)nx36M5(5465,E5-26v4)sd35(5493)nx36M5WCT(5467,v4)Support for System x and dense servers with Intel E5 v3 and E3 v3 processors Table 11. Support for servers with Intel Xeon v3 processorsPart number DescriptionConnectX-4 Lx Ethernet adapters01GR250Mellanox ConnectX-4 Lx 10/25GbE SFP28 2-port PCIe Adapter N N N Y Y Y Y 00MN990Mellanox ConnectX-4 Lx 10/25GbE SFP28 1-port ML2 Adapter N N N Y Y Y Y 7ZT7A00507Mellanox ConnectX-4 Lx 10/25GbE SFP28 2-Port ML2 Adapter N N N N N N N 00MM950Mellanox ConnectX-4 Lx 1x40GbE QSFP+ AdapterN N N Y Y Y Y ConnectX-4 VPI InfiniBand adapters7ZT7A00500ThinkSystem Mellanox ConnectX-4 PCIe FDR 2-Port QSFP VPIAdapter N N N N N N N 00MM960Mellanox ConnectX-4 2x100GbE/EDR IB QSFP28 VPI AdapterNNNYYYYx 3100 M 5 (5457)x 3250 M 5 (5458)x 3500 M 5 (5464)x 3550 M 5 (5463)x 3650 M 5 (5462)x 3850 X 6/x 3950 X 6 (6241, E 7 v 3)n x 360 M 5 (5465)Support for System x servers with Intel Xeon v2 processors Table 12. Support for servers with Intel Xeon v2 processorsPart number DescriptionConnectX-4 Lx Ethernet adapters01GR250Mellanox ConnectX-4 Lx 10/25GbE SFP28 2-port PCIe AdapterN N N N N N N Y 00MN990Mellanox ConnectX-4 Lx 10/25GbE SFP28 1-port ML2AdapterN N N N N N N Y 7ZT7A00507Mellanox ConnectX-4 Lx 10/25GbE SFP28 2-Port ML2Adapter N N N N N N N N 00MM950Mellanox ConnectX-4 Lx 1x40GbE QSFP+ AdapterN N N N N N N Y ConnectX-4 VPI InfiniBand adapters7ZT7A00500ThinkSystem Mellanox ConnectX-4 PCIe FDR 2-Port QSFPVPI Adapter N N N N N N N N 00MM960Mellanox ConnectX-4 2x100GbE/EDR IB QSFP28 VPI AdapterNNNNNNNY The following figure shows the Mellanox ConnectX-4 Lx 2x25GbE SFP28 Adapter.x 3300 M 4 (7382)x 3500 M 4 (7383, E 5-2600 v 2)x 3550 M 4 (7914, E 5-2600 v 2)x 3630 M 4 (7158, E 5-2400 v 2)x 3650 M 4 (7915, E 5-2600 v 2)x 3650 M 4 B D (5466)x 3750 M 4 (8753)x 3850 X 6/x 3950 X 6 (6241, E 7 v 2)Figure 5. Mellanox ConnectX-4 Lx 10/25GbE SFP28 2-port PCIe Ethernet Adapter (heatsink removed) Operating system supportThe Mellanox ConnectX-4 adapters support the following operating systems:Mellanox ConnectX-4 Lx 10/25GbE SFP28 2-port PCIe Ethernet Adapter, 01GR250ThinkSystem Mellanox ConnectX-4 Lx 10/25GbE 2-port PCIe Ethernet Adapter, 4XC7A08249ThinkSystem Mellanox ConnectX-4 Lx 10/25GbE SFP28 2-port OCP Ethernet Adapter, 4XC7A08246 Mellanox ConnectX-4 Lx 10/25GbE SFP28 1-port ML2 Adapter, 00MN990ThinkSystem Mellanox ConnectX-4 Lx 10/25GbE SFP28 2-Port ML2 Ethernet Adapter, 7ZT7A00507 Mellanox ConnectX-4 Lx 1x40GbE QSFP+ Adapter, 00MM950ThinkSystem Mellanox ConnectX-4 PCIe FDR 1-Port QSFP VPI Adapter, 7XC7A05524ThinkSystem Mellanox ConnectX-4 PCIe FDR 2-Port QSFP VPI Adapter, 7ZT7A00500Mellanox ConnectX-4 2x100GbE/EDR IB QSFP28 VPI Adapter, 00MM960Table 13. Operating system support for Mellanox ConnectX-4 Lx 2x25GbE PCIe Adapter, 01GR250 (Part 1of 2)Operating systemsMicrosoft Windows Server 2012N N N N N N N N N N N N N N N N Y Y Microsoft Windows Server 2012 R2N N N N N N N N N Y Y Y Y Y Y Y Y Y Microsoft Windows Server 2016Y Y Y Y Y Y Y Y Y Y Y Y Y Y Y Y Y Y Microsoft Windows Server 2019Y Y Y Y Y Y Y Y Y Y Y Y Y Y Y Y N Y Microsoft Windows Server 2022Y Y Y Y Y Y Y Y Y Y Y Y Y Y Y Y N N Microsoft Windows Server version 1709N N N N N N N N N Y Y Y Y Y Y Y Y Y Microsoft Windows Server version 1803N N N N N N N N N Y Y Y Y Y Y N N N Red Hat Enterprise Linux 6.10N N N N N N N N N Y Y Y Y Y Y Y Y Y Red Hat Enterprise Linux 6.9N N N N N N N N N Y Y Y Y Y Y Y Y Y Red Hat Enterprise Linux 7.3N N N N N N N N N Y Y Y Y N Y Y Y Y Red Hat Enterprise Linux 7.4N N N N N N N N N Y Y Y Y Y Y Y Y Y Red Hat Enterprise Linux 7.5Y N N N N N N N N Y Y Y Y Y Y Y Y Y Red Hat Enterprise Linux 7.6N Y Y Y Y Y Y Y Y Y Y Y Y Y Y Y Y Y Red Hat Enterprise Linux 7.7Y Y Y Y Y Y Y Y Y Y Y Y Y Y Y Y Y Y Red Hat Enterprise Linux 7.8Y Y Y Y Y Y Y Y Y Y Y Y Y Y Y Y Y Y Red Hat Enterprise Linux 7.9Y Y Y Y Y Y Y Y Y Y Y Y Y Y Y Y Y Y Red Hat Enterprise Linux 8.0Y Y Y Y Y Y Y Y Y Y Y Y Y Y Y Y N Y Red Hat Enterprise Linux 8.1Y Y Y Y Y Y Y Y Y Y Y Y Y Y Y Y N Y Red Hat Enterprise Linux 8.2Y Y Y Y Y Y Y Y Y Y Y Y Y Y Y Y N Y Red Hat Enterprise Linux 8.3Y Y Y Y Y Y Y Y Y Y Y Y Y Y Y Y N Y Red Hat Enterprise Linux 8.4Y Y Y Y Y Y Y Y Y Y Y Y Y Y Y Y N N Red Hat Enterprise Linux 8.5Y Y Y Y Y Y Y Y Y Y Y Y Y Y Y Y N N Red Hat Enterprise Linux 8.6Y Y Y Y Y Y Y Y Y Y Y Y Y Y Y Y N N Red Hat Enterprise Linux 8.7Y Y Y Y Y Y Y Y Y Y Y Y Y Y Y Y N N Red Hat Enterprise Linux 8.8Y Y Y Y Y Y Y Y Y Y Y Y Y Y Y Y N N Red Hat Enterprise Linux 8.9Y Y Y Y Y Y Y Y Y N N N N N N N N N Red Hat Enterprise Linux 9.0Y Y Y Y Y Y Y Y Y Y Y Y Y Y Y Y N N Red Hat Enterprise Linux 9.1Y Y Y Y Y Y Y Y Y Y Y Y Y Y Y Y N N Red Hat Enterprise Linux 9.2Y Y Y Y Y Y Y Y Y Y Y Y Y Y Y Y N N Red Hat Enterprise Linux 9.3Y Y Y Y Y Y Y Y Y N N N N N N N N N SUSE Linux Enterprise Server 11 SP4N N N N N N N N N Y Y Y Y Y Y YYY S R 250S D 530 (X e o n G e n 2)S R 630 (X e o n G e n 2)S R 650 (X e o n G e n 2)S R 850 (X e o n G e n 2)S R 850P (X e o n G e n 2)S R 860 (X e o n G e n 2)S R 950 (X e o n G e n 2)S T 550 (X e o n G e n 2)S D 530 (X e o n G e n 1)S R 630 (X e o n G e n 1)S R 650 (X e o n G e n 1)S R 850 (X e o n G e n 1)S R 860 (X e o n G e n 1)S R 950 (X e o n G e n 1)S T 550 (X e o n G e n 1)x 3850/3950 X 6 (6241, E 7 v 3)x 3850/3950 X 6 (6241, E 7 v 4)11SUSE Linux Enterprise Server 12 SP2N N N N N N N N N Y Y Y Y N Y Y Y Y SUSE Linux Enterprise Server 12 SP3Y N N N N Y N N N Y Y Y Y Y Y Y Y Y SUSE Linux Enterprise Server 12 SP4N Y Y Y Y Y Y Y Y Y Y Y Y Y Y Y Y Y SUSE Linux Enterprise Server 12 SP5Y Y Y Y Y Y Y Y Y Y Y Y Y Y Y Y Y Y SUSE Linux Enterprise Server 15Y Y Y Y Y Y Y Y Y Y Y Y Y Y Y Y Y Y SUSE Linux Enterprise Server 15 SP1Y Y Y Y Y Y Y Y Y Y Y Y Y Y Y Y Y Y SUSE Linux Enterprise Server 15 SP2Y Y Y Y Y Y Y Y Y Y Y Y Y Y Y Y Y Y SUSE Linux Enterprise Server 15 SP3Y Y Y Y Y Y Y Y Y Y Y Y Y Y Y Y N N SUSE Linux Enterprise Server 15 SP4Y Y Y Y Y Y Y Y Y Y Y Y Y Y Y Y N N SUSE Linux Enterprise Server 15 SP5Y Y Y Y Y Y Y Y Y Y Y Y Y Y Y Y N N Ubuntu 22.04 LTSY Y Y Y Y Y Y Y Y Y Y Y Y Y Y Y N N VMware vSphere Hypervisor (ESXi) 5.5N N N N N N N N N N N N N N N N Y N VMware vSphere Hypervisor (ESXi) 6.0 U3N N N N N N N N N Y Y Y Y Y Y Y Y Y VMware vSphere Hypervisor (ESXi) 6.5N N N N N N N N N Y Y Y Y N Y Y N Y VMware vSphere Hypervisor (ESXi) 6.5 U1N N N N N N N N N Y Y Y Y Y Y Y N Y VMware vSphere Hypervisor (ESXi) 6.5 U2Y Y Y Y Y Y Y Y Y Y Y Y Y Y Y Y N Y VMware vSphere Hypervisor (ESXi) 6.5 U3Y Y Y Y Y Y Y Y Y Y Y Y Y Y Y Y N Y VMware vSphere Hypervisor (ESXi) 6.7Y N N N N N N N N Y Y Y Y Y Y Y N Y VMware vSphere Hypervisor (ESXi) 6.7 U1N Y Y Y Y Y Y Y Y Y Y Y Y Y Y Y N Y VMware vSphere Hypervisor (ESXi) 6.7 U2Y Y Y Y Y Y Y Y Y Y Y Y Y Y Y Y N Y VMware vSphere Hypervisor (ESXi) 6.7 U3Y Y Y Y Y Y Y Y Y Y Y Y Y Y Y Y N Y VMware vSphere Hypervisor (ESXi) 7.0Y Y Y Y Y Y Y Y Y Y Y Y Y Y Y Y N N VMware vSphere Hypervisor (ESXi) 7.0 U1Y Y Y Y Y Y Y Y Y Y Y Y Y Y Y Y N N VMware vSphere Hypervisor (ESXi) 7.0 U2Y Y Y Y Y Y Y Y Y Y Y Y Y Y Y Y N N VMware vSphere Hypervisor (ESXi) 7.0 U3Y Y Y Y Y Y Y Y Y Y Y Y Y Y Y Y N N VMware vSphere Hypervisor (ESXi) 8.0Y Y Y Y Y Y Y Y Y Y Y Y Y Y Y Y N N VMware vSphere Hypervisor (ESXi) 8.0 U1Y Y Y Y Y Y Y Y Y Y Y Y Y Y Y Y N N VMware vSphere Hypervisor (ESXi) 8.0 U2Y Y Y Y Y Y Y Y Y Y Y Y Y Y Y YNN Operating systems[in box driver support only]S R 250S D 530 (X e o n G e n 2)S R 630 (X e o n G e n 2)S R 650 (X e o n G e n 2)S R 850 (X e o n G e n 2)S R 850P (X e o n G e n 2)S R 860 (X e o n G e n 2)S R 950 (X e o n G e n 2)S T 550 (X e o n G e n 2)S D 530 (X e o n G e n 1)S R 630 (X e o n G e n 1)S R 650 (X e o n G e n 1)S R 850 (X e o n G e n 1)S R 860 (X e o n G e n 1)S R 950 (X e o n G e n 1)S T 550 (X e o n G e n 1)x 3850/3950 X 6 (6241, E 7 v 3)x 3850/3950 X 6 (6241, E 7 v 4)1Table 14. Operating system support for Mellanox ConnectX-4 Lx 2x25GbE PCIe Adapter, 01GR250 (Part 2of 2)Operating systemsMicrosoft Windows Server 2012Y N Y Y Y Microsoft Windows Server 2012 R2Y N Y Y Y Microsoft Windows Server 2016Y Y Y Y Y Microsoft Windows Server 2019N N Y N Y Microsoft Windows Server 2022N N N N N Microsoft Windows Server version 1709Y Y Y Y Y Microsoft Windows Server version 1803N N Y N Y Red Hat Enterprise Linux 6.10Y Y Y Y Y Red Hat Enterprise Linux 6.9Y Y Y Y Y Red Hat Enterprise Linux 7.3Y Y Y Y Y Red Hat Enterprise Linux 7.4Y Y Y Y Y Red Hat Enterprise Linux 7.5Y Y Y Y Y Red Hat Enterprise Linux 7.6Y Y Y Y Y Red Hat Enterprise Linux 7.7Y Y Y Y Y Red Hat Enterprise Linux 7.8Y Y Y Y Y Red Hat Enterprise Linux 7.9Y Y Y Y Y Red Hat Enterprise Linux 8.0N N N N N Red Hat Enterprise Linux 8.1N N N N N Red Hat Enterprise Linux 8.2N N N N N Red Hat Enterprise Linux 8.3N N N N N Red Hat Enterprise Linux 8.4N N N N N Red Hat Enterprise Linux 8.5N N N N N Red Hat Enterprise Linux 8.6N N N N N Red Hat Enterprise Linux 8.7N N N N N Red Hat Enterprise Linux 8.8N N N N N Red Hat Enterprise Linux 8.9N N N N N Red Hat Enterprise Linux 9.0N N N N N Red Hat Enterprise Linux 9.1N N N N N Red Hat Enterprise Linux 9.2N N N N N Red Hat Enterprise Linux 9.3N N N N N SUSE Linux Enterprise Server 11 SP4Y N Y Y Y SUSE Linux Enterprise Server 12 SP2Y Y Y Y Y SUSE Linux Enterprise Server 12 SP3Y Y Y Y Y SUSE Linux Enterprise Server 12 SP4Y Y Y Y Y SUSE Linux Enterprise Server 12 SP5Y Y Y Y Yn x 360 M 5 (5465)x 3550 M 5 (5463)x 3550 M 5 (8869)x 3650 M 5 (5462)x 3650 M 5 (8871)SUSE Linux Enterprise Server 15Y N Y N Y SUSE Linux Enterprise Server 15 SP1Y N Y N Y SUSE Linux Enterprise Server 15 SP2Y N Y N Y SUSE Linux Enterprise Server 15 SP3N N N N N SUSE Linux Enterprise Server 15 SP4N N N N N SUSE Linux Enterprise Server 15 SP5N N N N N Ubuntu 22.04 LTSN N N N N VMware vSphere Hypervisor (ESXi) 5.5Y N Y Y Y VMware vSphere Hypervisor (ESXi) 6.0 U3Y N Y Y Y VMware vSphere Hypervisor (ESXi) 6.5Y Y Y Y Y VMware vSphere Hypervisor (ESXi) 6.5 U1Y Y Y Y Y VMware vSphere Hypervisor (ESXi) 6.5 U2Y Y Y Y Y VMware vSphere Hypervisor (ESXi) 6.5 U3Y Y Y Y Y VMware vSphere Hypervisor (ESXi) 6.7Y N Y N Y VMware vSphere Hypervisor (ESXi) 6.7 U1Y N Y N Y VMware vSphere Hypervisor (ESXi) 6.7 U2Y N Y N Y VMware vSphere Hypervisor (ESXi) 6.7 U3Y N Y N Y VMware vSphere Hypervisor (ESXi) 7.0N N N N N VMware vSphere Hypervisor (ESXi) 7.0 U1N N N N N VMware vSphere Hypervisor (ESXi) 7.0 U2N N N N N VMware vSphere Hypervisor (ESXi) 7.0 U3N N N N N VMware vSphere Hypervisor (ESXi) 8.0N N N N N VMware vSphere Hypervisor (ESXi) 8.0 U1N N N N N VMware vSphere Hypervisor (ESXi) 8.0 U2N N N N NOperating systemsTable 15. Operating system support for ThinkSystem Mellanox ConnectX-4 Lx 10/25GbE SFP28 2-port PCIe Ethernet Adapter, 4XC7A08249Operating systems Microsoft Windows 10N N N N N N Y N Microsoft Windows 11N N N N N N Y N Microsoft Windows Server 2016Y Y Y Y Y Y Y Y Microsoft Windows Server 2019Y Y Y Y Y Y Y Y Microsoft Windows Server 2022Y Y Y YYYYY Red Hat Enterprise Linux 7.6Y N N N Y Y Y Y Red Hat Enterprise Linux 7.7Y N N N Y Y Y Y n x 360 M 5 (5465)x 3550 M 5 (5463)x 3550 M 5 (8869)x 3650 M 5 (5462)x 3650 M 5 (8871)S E 350S D 630 V 2S R 630 V 2S R 650 V 2S R 635S R 645S R 655S R 665211111111Red Hat Enterprise Linux 7.8Y N N N Y Y Y Y Red Hat Enterprise Linux 7.9Y Y Y Y Y Y Y Y Red Hat Enterprise Linux 8.0N N N N Y NY NRed Hat Enterprise Linux 8.1Y N N N Y Y Y Y Red Hat Enterprise Linux 8.2Y Y Y Y Y Y Y Y Red Hat Enterprise Linux 8.3Y Y Y Y Y Y Y Y Red Hat Enterprise Linux 8.4Y Y Y Y Y Y Y Y Red Hat Enterprise Linux 8.5Y Y Y Y Y Y Y Y Red Hat Enterprise Linux 8.6Y Y Y Y Y Y Y Y Red Hat Enterprise Linux 8.7Y Y Y Y Y Y Y Y Red Hat Enterprise Linux 8.8Y Y Y Y Y Y Y Y Red Hat Enterprise Linux 8.9N Y Y Y Y Y Y Y Red Hat Enterprise Linux 9.0Y Y Y Y Y Y Y Y Red Hat Enterprise Linux 9.1Y Y Y Y Y Y Y Y Red Hat Enterprise Linux 9.2Y Y Y Y Y Y Y Y Red Hat Enterprise Linux 9.3N Y Y Y Y Y Y Y SUSE Linux Enterprise Server 12 SP4N N N N Y N Y N SUSE Linux Enterprise Server 12 SP5N Y Y Y Y Y Y Y SUSE Linux Enterprise Server 15Y N N N N N N N SUSE Linux Enterprise Server 15 SP1Y N N N Y Y Y Y SUSE Linux Enterprise Server 15 SP2Y Y Y Y Y Y Y Y SUSE Linux Enterprise Server 15 SP3Y Y Y Y Y Y Y Y SUSE Linux Enterprise Server 15 SP4Y Y Y Y Y Y Y Y SUSE Linux Enterprise Server 15 SP5Y Y Y Y Y Y Y Y Ubuntu 18.04.5 LTS N Y Y Y N N N N Ubuntu 18.04.6 LTS Y N N N N N N N Ubuntu 20.04 LTS N N Y Y N N N N Ubuntu 20.04.5 LTS Y N N N N N N N Ubuntu 22.04 LTSY Y Y Y Y Y Y Y VMware vSphere Hypervisor (ESXi) 6.5 U2Y N N N N N N N VMware vSphere Hypervisor (ESXi) 6.7 U2Y N N N N N N N VMware vSphere Hypervisor (ESXi) 6.7 U3Y Y Y YYY Y Y VMware vSphere Hypervisor (ESXi) 7.0Y N N N Y Y Y Y VMware vSphere Hypervisor (ESXi) 7.0 U1Y N N N Y Y Y Y VMware vSphere Hypervisor (ESXi) 7.0 U2Y Y Y Y Y Y Y Y VMware vSphere Hypervisor (ESXi) 7.0 U3Y Y Y Y Y Y Y Y VMware vSphere Hypervisor (ESXi) 8.0Y Y Y Y Y Y Y Y VMware vSphere Hypervisor (ESXi) 8.0 U1Y Y Y Y Y Y Y Y VMware vSphere Hypervisor (ESXi) 8.0 U2Y Y Y YYYYYOperating systems S E 350S D 630 V 2S R 630 V 2S R 650 V 2S R 635S R 645S R 655S R 6651111111111111111111111111111111。
Shure MX405 MX410 MX415鹅颈话筒及配件用户指南

MX405 MX410 MX415 Gooseneck Microphones and AccessoriesThe Shure miniature gooseneck microphones, MX405, MX410 and MX415, user guide.Version: 5 (2019-J)Table of ContentsMX405 MX410 MX415Gooseneck Microphones and Accessories 3General Description3 Features 3 Model Variations 3 Snap-Fit Windscreen 8 Interchangeable Cartridges 9 MX400SMP Surface Mount Preamp9 Accessories 10 Installation11MX400SMP Pin Assignments 12 DIP Switches 12 LED Logic 13 MX400DP Desktop Base14 Installation 15 Cable 15 MX400DP DIP Switches 16 Local Mute Control 17 Logic Mute Control (Automatic Mixing) 18 Specifications19 Certifications25•••••MX405 MX410 MX415Gooseneck Microphones and Accessories General DescriptionShure MX405, MX410, and MX415 miniature gooseneck microphones are suitable for boardrooms and other sites where aesthetics are important. Permanently mount them at conference tables or lecterns using the MX400SMP surface mount, or use the MX400DP moveable desktop base, which includes a configurable mute button with logic output. Also compatible with the MX890 wireless desktop base and the ULXD8 wireless base.FeaturesLow profile, aesthetic designChoice of bi-color indicator or light ringWide dynamic range and smooth frequency responseRF filtering with CommShield technology Logic input for external LED controlModel VariationsThese gooseneck microphones are available in different lengths with a cardioid, supercardioid, or mini-shotgun cartridge and either a bi-color LED status indicator or a light ring. The 10 and 15 inch models are also available with a dualflex neck.®Gooseneck Microphones5" Cardioid Gooseneck Microphone MX405LP/C 5" Supercardioid Gooseneck Microphone MX405LP/S 5" Mini-shotgun Gooseneck Microphone MX405LP/MS 5" Gooseneck with Red Top LED (no cartridge)MX405RLP/N 10" Cardioid Gooseneck Microphone MX410LP/C 10" Supercardioid Gooseneck Microphone MX410LP/S 10" Gooseneck with Red Top LED (no cartridge)MX410RLP/N 10" Cardioid Dualflex Gooseneck Microphone MX410LPDF/C 10" Supercardioid Dualflex Gooseneck Microphone MX410LPDF/S 10" Dualflex Gooseneck with Red Top LED (no cartridge)MX410RLPDF/N 10" Cardioid Dualflex Gooseneck Microphone with Red Top LED MX410RLPDF/C 10" Supercardioid Dualflex Gooseneck Microphone with Red Top LED MX410RLPDF/S 15" Cardioid Gooseneck Microphone MX415LP/C 15" Supercardioid Gooseneck Microphone MX415LP/S•••15" Gooseneck with Red Top LED (no cartridge)MX415RLP/N 15" Cardioid Dualflex Gooseneck Microphone MX415LPDF/C 15" Supercardioid Dualflex Gooseneck Microphone MX415LPDF/S 15" Dualflex Gooseneck with Red Top LED (no cartridge)MX415RLPDF/N 15" Cardioid Dualflex Gooseneck Microphone with Red Top LED MX415RLPDF/C 15" Supercardioid Dualflex Gooseneck Microphone with Red Top LED MX415RLPDF/S 5" White Gooseneck Microphone (no cartridge)MX405WLP/N 5" White Gooseneck Microphone with Red Top LED (no cartridge)MX405WRLP/N 10" White Gooseneck Microphone (no cartridge)MX410WLP/N 10" White Gooseneck Microphone with Red Top LED (no cartridge)MX410WRLP/N 15" White Gooseneck Microphone (no cartridge)MX415WLP/N 15" White Gooseneck Microphone with Red Top LED (no cartridge)MX415WRLP/N 10" White Dualflex Gooseneck Microphone (no cartridge)MX410WLPDF/N 10" White Dualflex Gooseneck Microphone with Red Top LED (no cartridge)MX410WRLPDF/N 15" White Dualflex Gooseneck Microphone (no cartridge)MX415WLPDF/N 15" White Dualflex Gooseneck Microphone with Red Top LED (no cartridge)MX415WRLPDF/NCoverage and PlacementCardioid: One microphone for one or two people.Supercardioid: One microphone for each person.Mini-shotgun:One microphone for each person.CardioidSupercardioid•••Mini-shotgunMic PlacementSnap-Fit WindscreenSnap into the groove below the cartridge.To remove, spread the gap with a screwdriver or thumbnail.Provides 30 dB of "pop" protection.Interchangeable CartridgesMicroflex microphones use interchangeable cartridges that allow you to choose the polar pattern for different installations.Cartridge Polar PatternsMX400SMP Surface Mount PreampPermanent mount for conference tables or lecterns. Includes LED logic input.AccessoriesFurnished AccessoriesMX400SMP Surface Mount KitInstallationNote: Over tightening the wing nut reduces shock isolation.Caution: To prevent bending pins, line up key with notch and seat connector fully before twisting to lock.MX400SMP Pin Assignments5-Pin XLRDIP SwitchesSet DIP Switch 1 up to engage the low cut filter, which attenuates frequencies by 6 dB per octave below 150 Hz.Switch Down (default)Up1Full frequency response Low cut filter2LED steady LED flashesLED LogicTo operate the LED indicator, use the included 5-pin XLR connector to wire the microphone to an automatic mixer or other logic device.Note: Connect the LED IN to the gate output to illuminate the LED when the channel is gated on.Do not use the relay ports on Crestron and AMX devices. Use the I/O logic ports instead.The LED logic may not function when connecting to devices that do not have internal "pull-up resistor" logic circuits, such as ClearOne DSP products. External pullup resistor circuits can be added for each microphone. Visit /FAQ for detailed instructions.Logic ConnectionConnection to device with internal "pull-up resistor" logic circuitMX405, 410, 415Logic LOW (0 V)Logic HIGH (+5 V)MX405, 410, 415Green RedMX405R, 410R, 415RLogic LOW (0 V)Logic HIGH (+5V)Red Off/flashingMX400DP Desktop BaseThe MX400DP moveable desktop base includes a configurable mute button with logic output.MX400DP Desktop BaseInstallationCaution: To prevent bending pins, line up key with notch and seat connector fully before twisting to lock.CableThe 20 ft. attached cable is terminated with a 3-pin XLR connector. For logic applications, open the XLR connector to access the three unterminated logic conductors.Wire Color FunctionRed Audio +Black Audio −White SWITCH OUTOrange LED INGreen Logic GroundShield Mic Common GroundMX400DP Pin Assignments3-Pin XLRMX400DP DIP SwitchesCaution: Failure to reinstall the setscrew will reduce RF immunity.Switch Down (default)Up1Momentary Toggle2Push-to-Mute Push-to-Talk 3Local Mute Logic ControlSwitch Down (default)Up4Full Frequency Range Low Cut Filter (attenuates 6 dB per octave below 150 Hz)5LED Steady LED FlashesLocal Mute ControlThe microphone ships configured for local (manual) mute control (DIP Switch 3 down). In this mode, the PUSH button on the microphone mutes the audio signal at the microphone. Audio is not sent to the audio outputs when muted.In this configuration, the LED color reflects the microphone state, as controlled by the user with the PUSHbutton.Microphone StatusMX405, 410, 415MX405R, 410R, 415RActive Green RedMuted Red Off/flashingButton ConfigurationFor local mute control operation, use DIP Switches 1 and 2 to configure the button behavior.Button Behavior SWITCH OUT Logic Signal DIP Switch Setting Momentary: push-to-mute (as shipped).When pushed, SWITCH OUT (red wire) fallsto 0 V. When released, SWITCH OUT returns to +5 V.Momentary: push-to-talkButton Behavior SWITCH OUT Logic Signal DIP Switch SettingToggle: Push and release to toggle the microphone on or off. Mic is active whenpowered on.Push and release sets SWITCH OUT to 0 V.Push again to toggle back to +5 V.Toggle: Push and release to toggle the microphone on or off. Mic is mute whenpowered onLogic Mute Control (Automatic Mixing)Set DIP Switch 3 up to configure the microphone for logic control applications where audio from the microphone is muted by an external device, such as an automatic mixer. In this mode, the local mute function of the PUSH button is bypassed (the microphone always sends audio) and the LED does not respond directly from pushing the button.As required by the installation specifications, wire the SWITCH OUT conductor in the microphone cable to the automatic mixer or other TTL logic device. When the talker presses the button on the microphone, it changes the voltage level at the SWITCH OUT conductor, which signals the device to mute audio for that channel or perform some other function.To control the LED on the microphone, wire the LED IN conductor to the gate output on the automatic mixer (or any TTL logic device).Button ConfigurationFor logic control operation, DIP Switch 1 determines the button behavior (DIP Switch 2 has no effect).Button Behavior DIP Switch SettingMomentary: When pushed, SWITCH OUT (red wire) falls to 0 V. When released,SWITCH OUT returns to +5 V.Toggle: Push and release sets SWITCH OUT to 0 V. Push again to toggle back to +5 V.••Controlling the LED Using Logic LED INWhen configured for logic mute control, connect the LED IN conductors to an external switch, relay, or a TTL gate (gate out) on an automatic mixer. The MX400DB contains an internal pull-up resistor circuit.The LED illuminates green/red when the MX396 LED IN is grounded (orange wire connected to the green wire).The LED illuminates red/off when LED IN is lifted (orange wire is NOT connected to the green wire).SpecificationsTypeElectret CondenserFrequency Response50–17000 HzPolar PatternMX405/C, MX410/C, MX415/C Cardioid MX405/S, MX410/S, MX415/S Supercardioid MX405/MSMini-shotgunOutput Impedance170 ΩOutput ConfigurationActive BalancedSensitivity@ 1 kHz, open circuit voltageCardioid −35 dBV/Pa (18 mV)Supercardioid −34 dBV/Pa (21 mV)Mini-shotgun -33 dBV/Pa (22 mV)1 Pa=94 dB SPLMaximum SPL1 kHz at 1% THD, 1 kΩ loadCardioid 121 dB Supercardioid 120 dB Mini-shotgun121 dBSelf NoiseA-weightedCardioid 28 dB SPLSupercardioid27 dB SPLMini-shotgun26 dB SPL Signal-to-Noise RatioRef. 94 dB SPL at 1 kHzCardioid66 dB Supercardioid68 dB Mini-shotgun68 dB Dynamic Range1 kΩ load, @ 1 kHz93 dBCommon Mode Rejection10 to 100,000 kHz45 dB, minimumClipping Levelat 1% THD−8 dBV (0.4 V)Polarity3-pin XLR Positive sound pressure on diaphragm produces positive voltage on pin 2 relative to pin 3 of output XLR connector5-pin XLR Positive sound pressure on diaphragm produces positive voltage on pin 4 relative to pin 2 of output XLR connectorWeightMX4050.054 kg (0.119 lbs)MX4100.068 kg (0.150 lbs)MX4150.07 kg (0.154 lbs)MX400DP0.516 kg (1.138 lbs)MX400SMP0.125 kg (0.275 lbs)Logic ConnectionsLEDINActive low (≤1.0V), TTL compatible. Absolute maximum voltage: 0.7V to 50V.LOGIC OUT Active low (≤1.0V), sinks up to 20mA, TTL compatible. Absolute maximum voltage: 0.7V to 50V (up to 50V through 3kΩ).Mute Switch Attenuation -50 dB minimumCableMX400DP6.1 m (20 ft) attached cable with shielded audio pair terminated at a 3pin male XLR and three unterminated conductors for logic controlEnvironmental ConditionsOperating Temperature–18–57°C (0–135°F)Storage Temperature–29–74°C (–20–165°F)Relative Humidity0–95%Power RequirementsPhantom Power48–52 V DC, 8.0 mACertificationsThis product meets the Essential Requirements of all relevant European directives and is eligible for CE marking. The CE Declaration of Conformity can be obtained from: /europe/complianceAuthorized European representative:Shure Europe GmbHHeadquarters Europe, Middle East & AfricaDepartment: EMEA ApprovalJakob-Dieffenbacher-Str. 1275031 Eppingen, GermanyPhone: +49-7262-92 49 0Fax: +49-7262-92 49 11 4Email:*************。
Kinetix 5100 I O 终端扩展模块安装指南说明书

Installation InstructionsOriginal InstructionsKinetix 5100 I/O Terminal Expansion BlockCatalog Number 2198-TBIOThe I/O terminal expansion block lets you wire I/O directly to the Kinetix® 5100 drive without the use of an extension cable and a separate terminal block. The I/O terminal expansion block securely mounts to the drive with its own mounting screws and simplifies I/O wiring. This publication provides installation and wiring instructions for the Kinetix 5100 I/O terminal expansion block. For further installation instructions on the Kinetix 5100 drive, refer to the Kinetix 5100 Single-axis EtherNet/IP Servo Drive User Manual, publication 2198-UM004.Before You BeginThe I/O terminal expansion block is attached to the I/O terminal on the front of the drive. When used the expansion block requires additional cabinet height and width.Front view of Kinetix 5100 drive.2198-E1004-ERS Kinetix 5100 drive is shown.Partial top view of Kinetix 5100 drive show additional clearance required for I/O terminal expansion block.PadDimensions are in mm (in.).2Rockwell Automation Publication 2198-IN020A-EN-P - August 2019Kinetix 5100 I/O Terminal Expansion BlockInstall the I/O Terminal Expansion BlockFollow these steps to install your I/O terminal expansion block.1.Wire the I/O terminal expansion block, by using the pinout table on page 3. The terminal block accepts the following.2.T o obtain a high-frequency bond between the cable shield and the expansion block and for stress relief, firmly attach the cable to the expansion block by using a tie wrap (you supply).3.Attach expansion block to the I/O connector on the front of the Kinetix 5100 drive by using a screwdriver and torque to 0.2 N•m (1.77 lb•in).Attribute 2198-TBIOWire gauge 1.5…0.05 mm 2 (16…30 AWG)Strip length 6…7 mm (0.24…0.27 in.)Torque value20 N•cm (1.77 lb•in)Tie WrapExposed copper pad is under cable shield.Route wires such that it limits stress on cable.Rockwell Automation Publication 2198-IN020A-EN-P - August 20193Kinetix 5100 I/O Terminal Expansion BlockWire the I/O Terminal Expansion BlockUse the following pinout table to wire the I/O from your system.I/O Terminal Expansion Block PinoutIOD PinDescriptionSignal1Digital output 4+OUTPUT4+2Digital output 3-OUTPUT3-3Digital output 3+OUTPUT3+4Digital output 2-OUTPUT2-5Digital output 2+OUTPUT2+6Digital output 1-OUTPUT1-7Digital output1+OUTPUT1+8Digital input 4INPUT49Digital input 1INPUT110Digital input 2INPUT211Common for digital inputs, connected to +24 or 0V DC DCOM 12Analog input signal ground AGND 13Analog input signal ground AGND 14Reserved (1)(1)The reserved pins are not present on I/O terminal expansion block.—15Analog monitor output 2AOUT216Analog monitor output 1AOUT117Reserved (1)—18Analog torque input COMMAND119Analog input signal ground AGND 20Reserved (1)—21Buffered encoder output Ch A+AMOUT+22Buffered encoder output Ch A-AMOUT-23Buffered encoder output Ch B-BMOUT-24Buffered encoder output Ch Z-ZMOUT-25Buffered encoder output Ch B+BMOUT+Allen-Bradley, Kinetix, Rockwell Automation, and Rockwell Software are trademarks of Rockwell Automation, Inc.Trademarks not belonging to Rockwell Automation are property of their respective companies.Rockwell Otomasyon Ticaret A.Ş., Kar Plaza İş Merkezi E Blok Kat:6 34752 İçerenköy, İstanbul, T el: +90 (216) 5698400Rockwell Automation maintains current product environmental information on its website at/rockwellautomation/about-us/sustainability-ethics/product-environmental-compliance.page .Publication 2198-IN020A-EN-P - August 2019Copyright © 2019 Rockwell Automation, Inc. All rights reserved. Printed in the U.S.A.Additional ResourcesThese documents contain additional information concerning related products from Rockwell Automation.Y ou can view or download publications at /global/literature-library/overview.page .Rockwell Automation SupportFor technical support, visit /support/overview.page .ResourceDescriptionKinetix Servo Drives Specifications Technical Data, publication KNX-TD003Product specifications for Kinetix Integrated Motion over the EtherNet/IP network, Integrated Motion over Sercos interface, EtherNet/IP networking, and component servo drive families.Kinetix 5100 Single-axis EtherNet/IP Servo Drive User Manual, publication 2198-UM004.Provides information on how to install, configure, start up, and troubleshoot your Kinetix 5100 servo drive system.Industrial Automation Wiring and Grounding Guidelines, publication 1770-4.1Provides general guidelines for installing a Rockwell Automation industrial system.Product Certifications website: rok.auto/certificationsProvides declarations of conformity, certificates, and other certification details.。
Red Lion Model CL40 一体化操作器终端说明书
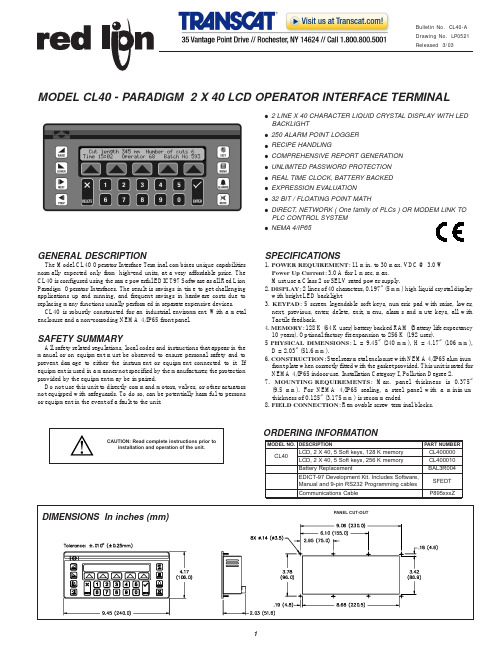
!2 LINE X 40 CHARACTER LIQUID CRYSTAL DISPLAY WITH LED BACKLIGHT!250 ALARM POINT LOGGER !RECIPE HANDLING!COMPREHENSIVE REPORT GENERATION !UNLIMITED PASSWORD PROTECTION !REAL TIME CLOCK, BATTERY BACKED !EXPRESSION EVALUATION !32 BIT / FLOATING POINT MATH!DIRECT, NETWORK ( One family of PLCs ) OR MODEM LINK TO PLC CONTROL SYSTEM !NEMA 4/IP65MODEL CL40 - PARADIGM 2 X 40 LCD OPERATOR INTERFACE TERMINALGENERAL DESCRIPTIONThe Model CL40 Operator Interface Terminal combines unique capabilities normally expected only from high-end units, at a very affordable price. The CL40 is configured using the same powerful EDICT97 Software as all Red Lion Paradigm Operator Interfaces. The result is savings in time to get challenging applications up and running, and frequent savings in hardware costs due to replacing many functions usually performed in separate expensive devices.CL40 is robustly constructed for an industrial environment. With a metal enclosure and a non-corroding NEMA 4/IP65 front panel.SAFETY SUMMARYAll safety related regulations, local codes and instructions that appear in the manual or on equipment must be observed to ensure personal safety and to prevent damage to either the instrument or equipment connected to it. If equipment is used in a manner not specified by the manufacturer, the protection provided by the equipment may be impaired.Do not use this unit to directly command motors, valves, or other actuators not equipped with safeguards. To do so, can be potentially harmful to persons or equipment in the event of a fault to the unit.SPECIFICATIONS1. POWER REQUIREMENT :**********************Power Up Current : 3.0 A for 1 msec. max.Must use a Class 2 or SELV rated power supply.2. DISPLAY : 2 lines of 40 characters, 0.197" (5 mm) high liquid crystal display with bright LED backlight3. KEYPAD : 5 screen legendable soft keys, numeric pad with raise, lower,next, previous, enter, delete, exit, menu, alarms and mute keys, all with Tactile feedback.4. MEMORY : 128 K (64 K user) battery backed RAM (Battery life expectancy 10 years). Optional factory fit expansion to 256 K (192 user).5 PHYSICAL DIMENSIONS : L = 9.45" (240 mm), H = 4.17" (106 mm), D = 2.03" (51.6 mm).6. CONSTRUCTION : Steel rear metal enclosure with NEMA 4/IP65 aluminum front plate when correctly fitted with the gasket provided. This unit is rated for NEMA 4/IP65 indoor use. Installation Category I, Pollution Degree 2.7. MOUNTING REQUIREMENTS : Max. panel thickness is 0.375"(9.5 mm). For NEMA 4/IP65 sealing, a steel panel with a minimum thickness of 0.125" (3.175 mm)is recommended8. FIELD CONNECTION : Removable screw terminal blocks.Bulletin No. CL40-A Drawing No. LP0521Released 3/03PROGRAMMABILITYEvent Driven Configuration ToolEdict 97, an extremely powerful Windows 95/3.11 based software program, provides for the intuitive configuration of every aspect of the operator interface’s behavior. The requirement for time consuming PLC ladder logic is drastically reduced by the unique event driven approach of EDICT 97. The capability of this program, in conjunction with the PLC and the Paradigm operator interface unit, ensures a great deal of advanced functionality for your system. This powerful PLC/Paradigm system provides many of the capabilities and features normally associated with the more complicated and costly PC/SCADA systems. Display pages are easily generated, including PLC and internal variables, text strings, or bar charts. All dynamic elements are also available as alarms, recipes, triggers, and reports, for the run time software. After completion of the programming, the program is directly downloaded to the operator interface from your PC, without any compiling or saving requirement. When you require a change in your program, EDICT 97 loads only the change, not the entire program, saving valuable on-line time. DYNAMIC DISPLAY PAGE ELEMENTSEach display page has provisions to show static and dynamic information, including data variables, text messages, time, and date.Data Variables can be either PLC derived or internally generated, either in data entry or display only mode. The Paradigm unit has an extremely powerful math capability, allowing the operator to manipulate the variables to meet the specific application’s demands. If required, the display can be formatted to BCD, binary, hex, floating point, and string. Upper and lower limits of data entry variables are fully supported and able to be password protected.Text Message Animation enables several different types of animated text froma local or global message table to be displayed. The message displayed isdependent on the condition of the particular controlling expression. The controlling expression may be a PLC bit level, a timer value, preset counter condition, or any one of a wide variety of message triggers.Time and Date in the Paradigm unit has the capability to display in any combination of year, month, day, hours, minutes, and seconds.Bar Graphs in horizontal format are easily attached to data variables. The partial or full length bar graph displays can be scaled and offset to optimize the required display effect.SECURITYThe password protection scheme provides the ultimate in tamper-proof capability. Access can be limited on a unit, page, recipe, or even individual data entries.ALARMSThe Paradigm unit can monitor and log from 100 to 500 alarms, depending on model. Such triggers as a simple bit level transition, a PLC coil activation, or a complex application algorithm can activate an alarm. The alarms can be time and date stamped, with an automatic screen display and/or downloading to a printer for hard copy recording purposes.REAL TIME SCHEDULEReal time schedule allows for repetitive or one time task to take place in the system. Typically a schedule action similar to...At 1:55 PM on Monday, Wednesday, and Friday, print the production report...is required in the application. In conjunction with the recipe capabilities, a downloading of a special recipe can be requested by the real time schedule feature.USER PROGRAMSThis feature offers the user the ability to incorporate custom application requirements via a powerful program language. For example, a program designated “Calculate V olume” which determines the amount of fluid in a round tank at specific temperatures could be created. This program would be triggered to run and display each time the page denoted as “V olume Now” is requested.The ability to customize to your application’s specialized needs is easily solved with the user program capability.KEYBOARD EDITINGAll the interface keys can be programmed to perform virtually unlimited functions with each key, having multiple actions assigned to three types of key events: key pressed, key held down (auto repeat), and key released. Typical key actions would be Go to page, set value, load recipe, view alarms, print report, and many more.COMMUNICATIONSWith over 70 communication drivers available, the Paradigm operator interface offers a wide range of connectivity including: PLCs, Variable Speed Drives, Temperature Controllers, Bar Code Readers, etc. Utilizing real PLC data references, the automatic comms configuration optimizes the system’s communication performance. In the event that your specific driver does not appear on the Paradigm drivers list, let us know, as this list is always being expanded to meet our customers’ needs.9. CERTIFICATIONS AND COMPLIANCES:ELECTRICAL SAFETYEN 61010-1, IEC 1010-1Safety requirements for electrical equipment for measurement, control,and Laboratory use, Part 1ELECTROMAGNETIC COMPATIBILITYNote:1. Self-recoverable loss of performance during EMI disturbance at 10 Vrms:Communications error may occur during EMI disturbance.For operation without loss of performance:I/O cables are routed in metal conduit connected to earth ground.10. ENVIRONMENTAL CONDITIONS:Operating Temperature: 0 to 40°CStorage Temperature: -20 to 80°COperating and Storage Humidity: 80% max. relative humidity (non-condensing) from 0°C to 40°C.Altitude: Up to 2000 meters11. WEIGHT: 2.1 lb. (0.95 Kg)INPUT/OUTPUT COMMUNICATIONS SPECS1. SERIAL PORTS: Data Format and Baud Rates for each port is individuallysoftware programmable up to 19200 baud.Port 1: Programming Port - RS-232 on an RJ-11 jackPort 2:RS-232 Port on a Plug-In Screw Terminal BlockPort 3: RS-485 Port on a Plug-In Screw Terminal Block(Up to 29 Units can be connected and individually addressed.) Note:LED Indicators show communications status on Ports 2 & 32. COMMUNICATION MODES: Any of the three ports can be used tocommunicate with Serial Devices.Model - (CL400000) only one of Ports 1, 2, and 3 may be configured.Exception Red Lion Controls Instrument, simple ASCII Printer, PC Link Network, Program Through, External Keyboards, and Roll-Your-OwnProtocols can be used with other protocols on all Ports.Model - (CL400010) may communicate in Master mode with a different device protocol on each port (See Note &Exception).However, only one of the Ports 2 and 3 may be configured, if either is selected as a Slave Protocol.Note: Ports 2 and 3 may be configured as different device protocols in Master mode and Port 1 may be used simultaneously in Slave mode fora third device protocol.Exception: If Allen Bradley DH485 is selected on either Port 2 or 3, only Port 1 will be available for a separate device protocol.Immunity to EN 50082-2Electrostatic discharge EN 61000-4-2Level 2; 4 Kv contactLevel 3; 8 Kv air Electromagnetic RF fields EN 61000-4-3Level 3; 10 V/m80 MHz - 1 GHz Fast transients (burst)EN 61000-4-4Level 4; 2 Kv I/OLevel 3; 2 Kv power RF conducted interference EN 61000-4-6Level 3; 10 V/rms 1150 KHz - 80 MHz Emissions to EN 50081-1RF interference EN 55022Enclosure class BHARDWARE INFORMATIONThis bulletin contains a variety of information related to the installation and operation of the Operator Interface supplied. Ideally, you should read this document thoroughly before attempting to use the equipment. For information about the software aspects of the terminal, please consult other documentation. CONTENTS OF PACKAGEThe Operator Interface is supplied in a packaging box containing the following...!The interface terminal itself.!A NEMA 4/IP65 rated mounting gasket.!A bag containing panel hardware.!This hardware bulletin.!If any of these items is missing, please contact your supplier immediately.POWER SUPPLY REQUIREMENTSThe Operator Interface requires an 11 to 30 VDC power supply rated at 3.0 W unless otherwise stated on the label.!The terminal may take as little as 100 mA in certain circumstances, so be sure that the chosen power supply can operate correctly with this load.Large switch-mode supplies tend to need a certain minimum load before they will operate correctly.In any case, it is very important that the power supply is mounted correctly if the unit is to operate reliably. A very high proportion of reported problems are caused by incorrect power supply installation, so please take care to observe the following points...!The power supply must be mounted close to the unit, with usually not more than 6 feet of cable between the supply and the Operator Interface.Ideally, as short a length as is possible should be used.!The wire used to connect the Operator Interface’s power supply should be of at least 22 gage wire. If a longer cable run is used, you should useheavier gage wire. The routing of the cable should be kept away fromlarge contactors, inverters and other devices which may generatesignificant electrical noise.BATTERY BACKUP ISSUESThe Operator Interface is supplied with a Lithium Battery designed to maintain the internal memory and real-time clock during power outages. Assuming the operator interface terminal is powered up for 50% of the time, this battery should last over 4 years. A “Battery Low” system variable is available so that the programmer can choose specific action(s) to occur when the battery voltage drops below its nominal voltage.It is possible to replace the battery without losing the contents of the Operator Interface’s memory, but this does not reduce the importance of ensuring that a copy of the terminal’s configuration is kept readily at hand to allow the terminal to be re-loaded in the case of mishaps. Please remember that although an image of the database contents can be uploaded, this file is not editable, so the importance of keeping a copy on disk cannot be over stressed. CHANGING THE BATTERYTo change the internal battery, follow these steps...!Remove the power and PLC communications connector from the unit.!Remove the four screws from the rear-cover and remove the cover.!If you wish to avoid losing the terminal’s configuration, reconnect the power connector and re-apply power. Note that this will require the panel to be powered-up and, as such, only suitably qualified staff should carry out this procedure.!The battery is located in a holder on the main circuit board. This should be clearly visible. Remove the battery from its holder.!Place the new battery in the holder. The terminal’s power supply can now be disconnected, if you re-applied power in the step above.!Replace the lid, screws and connector by following the above procedure in reverse. You may like to make a note of the date the battery wasreplaced to allow planned maintenance to be carried out.!If you did not keep the unit powered-up during battery replacement, hold down the EXIT and MUTE keys on the keyboard and cycle power.Release the keys and follow the menu guides to clear the memory. Theunit is now ready for a configuration database to be reloaded.Please note that the old battery must be disposed of in a manner which complies with your local waste regulations. Also, the battery must not be disposed of in fire or in a manner whereby it may be damaged and its contents come into contact with human skin.INSTALLATION & CONNECTIONS The unit meets NEMA 4/IP65 requirements for indoor use, when properly installed. The units are intended to be mounted into an enclosed panel. Installation EnvironmentThe unit should be installed in a location that does not exceed the maximum operating temperature and provides good air circulation. Placing the unit near devices that generate excessive heat should be avoided.Continuous exposure to direct sunlight may accelerate the aging process of the bezel. The bezel should be cleaned only with a soft cloth and neutral soap product. Do NOT use solvents.Do not use tools of any kind (screwdrivers, pens, pencils, etc.) to operate the keypad of the unit.CONNECTING TO A PLCThe Operator Interface is designed to operate with a PLC. A serial communication connection must be made between the operator interface terminal and PLC, and the details of this connection vary according to which PLC is used.The following section lists the connection details for the PLC to be used . PLC TYPEDetails on how to connect to most PLCs are available on request from RLC. CONNECTING TO AN IBM®PC/ATThe Operator Interface is programmed via software running on an IBM PC/AT or a compatible computer. The connection between the PC/AT and the operator interface terminal is made via a custom cable provided with the EDICT Developer’s Kit. The cable is designed for a 9-way serial port. Please contact your supplier if you require a 25-way version.PROGRAMMING PORT PIN OUTThe Operator Interface’s programming port is sometimes used to connect other RS-232 devices, such as printers. The following illustration and table gives the pin-out of this port to enable such connections to be made.connecting, the pin name at the programming port is connected to the opposite of that pin name at the destination device.MOUNTING INSTRUCTIONSThe Operator Interfaces are designed for through-panel mounting. A neoprene gasket is provided, to enable sealing to NEMA 4/IP65 specification. The panel cut-out diagram for the model supplied is provided. All mounting holes should be drilled for 0.14" (3.5 mm) clearance. Care should be taken to remove any loose material from the mounting hole to avoid such metal falling into the Operator Interface itself during installation.TROUBLESHOOTINGFor further technical assistance, contact technical support at the appropriate company numbers listed.© 2003, RED LION CONTROLS, ALL RIGHTS RESERVED.Information in this document is subject to change without notice and does not represent a commitment by Red Lion Controls. Software, which includes any database supplied therewith, described in this document may be furnished subject to a license agreement or a nondisclosure agreement. It is against the Law to copy the software except as specifically allowed in the license or nondisclosure agreement. No part of this document may be reproduced in any form or by any means, electronic or mechanical, including photocopying and recording, for any purpose, without the express written permission of Red Lion Controls.PowerPoint and Windows are registered trademarks of Microsoft Corporation. Other product and company names mentioned herein may be the trademarks of their respective owners.DisclaimerRed Lion Controls, hereinafter referred to as RLC, will under no circumstances be responsible for direct, indirect, special, incidental or consequential damages, death or personal injury arising from the use or misuse of all or part of this documentation or the products and software described herein. Notwithstanding the above, RLC does not exclude any liability for death or personal injury caused by its negligence.RLC does not warrant any of its software products to be free from error or to be fit for any particular purpose. Neither is the software guaranteed to provide operation without interruption. The customer's sole remedy in case of failure is the refund of the purchase price of the software.The customer, in applying the products and software described herein, accepts that the products are wholly or partly programmable electronic systems that are inherently complex and which cannot thus be guaranteed to be free of errors. In doing so, the customer accepts the responsibility to ensure that the products are correctly programmed, configured, installed, commissioned, operated and maintained by competent and suitably trained staff and according to any instructions or safety instructions provided and as dictated by good engineering practices.This documentation, and the software and products described herein, is subject to continuous development and improvement. All information is given in good faith, but RLC shall not be liable for any omissions or errors herein or within the software herein described.。
MULTIGIG RT 2-R 多功能高速接口连接器说明书

IntroducingMULTIGIG RT 2-RRuggedized Connectors for VPX applicationspart configUrationssee TE drawings for guide module and pin options.see TE drawings for guide module and pin options.part configUrations see TE drawings for guide module and pin options.Notes (Reference VITa 46.10; Observation 3-6):Note 1: 16 column shell, 15 columns of contactsNote 2: 16 column shell, 7 columns of contacts present (plus contacts i9-16)Note 3: 16 column shell, 16 columns of contactsNote 4: 16 column shell, 8 columns of contacts present (plus contacts i1-8)associated VpX solUtionsMEZaLOK Mezzanine Connectors (Compliant to VITa 61)• U tilizes the proven, reliable MIL-55302 Mini-Box contact interface, with fourpoints of contact• B ackwards compatible with XMC board footprint• Accommodates 10mm, 12mm, 15mm and 18mm stack heights• Solder ball SMT attach in SnPb and RoHS options• 114 (6 x 19) positions and 60 (6 x 10) positions• Protected “stub-proof” socket contacts w/superior signal integrity• Exceptional solder joint reliability (1000+ cycles thermal shock)MULTI-BEaM XLE Power Connectors (Compliant to VITa 62)• 20A and 50A power contacts, plus signal contacts• 3-beam high-conductivity-copper contact design allows for a greater angularmisalignment between mating connectors and offers a lower mating force• Slim guide sockets reduce the overall PCB footprint• Vented housing allows for better heat dissipation• Hot-plug capableOptic Connectors (Compliant to VITa 66)• L ight weight• High bandwidth• EMI immunity• 3 fiber optic interface types available:- 66.1 has two MT ribbon ferrules up to 24 fibers each- 66.2 four ARINC 801 termini- 66.3 one expanded beam lensed insert with four fibersRF Modules (Compliant to VITa 67)• E xcellent channel-to-channel isolation and RF performance to 65 GHz• M odular design permits application specific configuration with high RFcontact count• F loat mounted jack maintains positive RF ground• .240 center-to-center spacing• 4 and 8 position modules are designed to meet the requirements ofVITA 67.1 and VITA 67.2MULTIGIG RT 2-R ConnectorsdescriptionTE’s MULTIGIG RT 2-R ruggedized, light weight, high speed board-to-board interconnect is compliant to VITA 46 standard. This connector systemfeatures the modularity and flexibility of the MULTIGIG RT 2 connector, with a new quad-redundant contact structure designed for high vibration levels.applicationsRugged embedded computing applications: - Ground Defense - Missile Defense - Electronic Systems / C4ISR - Space - Commercial and Military AerospacematerialsContacts: High performance copper alloy, plated 50 µin Au over50 µin Ni in mating area, tin-lead on compliant pin tails Housings:High temperature thermoplasticRugged Guide Hardware: Aluminum or passivated stainless steelmechanicalOperating Temperature: -55 to +105˚CMating Force: 0.75 N [2.70 ozf] maximum per contact, same as standardMULTIGIG RT 2 backplane connectorstandards & specificationsCompliant to VITA 46 (VPX)Product Specification: 108-2072Application Specification: 114-13056Qualification Test Report:501-544physical or other properties Tested to HALT (Highly accelerated life test) vibration levels(0.2G 2/Hz) per VITA 72Connector modules available for 3U and 6U VPX slot profiles,including rear transition modulesReliable press-fit termination, requiring only flat rock toolingLightest weight VPX connector system: mated set of connectors and guide hardware for typical module and backplane slots: 3U - 62.66g (2.21 oz); 6U - 140.26g (4.95 oz)KEy FEaTUREsQuad-redundant contact system supports high lev-els of shock/vibration Compliant to VITA 46 for Open VPX applications Supports Ethernet, Fibre Channel, InfiniBand appli-cations, PCIe and Serial RapidIO high speed protocolsModular, lightweight connector system Robust “pinless” interface Differential, single-ended and powerRuggedized guide hardware availableSupports 0.8 inch card slot pitchesVITA 46 compliance enables upgrade in existingVPX applications Can be combined with high power modules (VITA 62), RF modules (VITA 67) and Optical modules (VITA 66)FOR MORE INFORMaTIONTechnical supportInternet: /ADMamericas: +1 800 522-6752asia Pacific: +86 400 820 6015Europe:Austria: +43 1 905 601 228Baltic Regions: +46 8 5072 5000Benelux: +31 73 6246 999France: +33 1 34 20 86 86Germany: +49 6251-133 1999Italy: +39 011-401 2632Nordic: +46 8 5072 5000Spain/Portugal: +34 93-2910366Switzerland: +41 52 633 66 26United Kingdom: +44 800 267 666Czech Republic: +420 800 701 462Poland: +48 800 702 309Hungary: +36 809 874 04Russia: +7495 790 790 2Follow us on Twitter for all the latest product news@TEConnectivity, and on Facebook, TEConnectivity./aDM© 2013 Tyco Electronics Corporation. All Rights Reserved.1773466-4 ADM/RRD 2.5M 01/2013MEZALOK, MULTI-BEAM XL, MULTIGIG RT, TE Connectivity and the TE connectivity (logo) are trademarks of the TE Connectivity Ltd. family of companies.Other products, logos, and company names mentioned herein may be trademarks of their respective owners. InfiniBand is a trademark of the InfiniBand Trade Association.While TE has made every reasonable effort to ensure the accuracy of the information herein, nothing herein constitutes any guarantee that such information is error-free, or any other representation, warranty or guarantee that the information is accurate, correct, reliable current. The TE entity issuing this publication reserves the right to make any adjustments to the information contained herein at any time without notice. All implied warranties regarding the information contained herein, including, but not limited to, any implied warranties of merchantability or fitness for a particular purpose are expressly disclaimed. The dimensions herein are for reference purposes only and are subject to change without notice. Specifications are subject to change without notice. Consult TE for the latest dimensions and design specifications.。
TPS40055同步降压控制器

ORDERING INFORMATIONIMPORTANT NOTICETexas Instruments Incorporated and its subsidiaries (TI) reserve the right to make corrections, modifications, enhancements, improvements, and other changes to its products and services at any time and to discontinue any product or service without notice. Customers should obtain the latest relevant information before placing orders and should verify that such information is current and complete. All products are sold subject to TI’s terms and conditions of sale supplied at the time of order acknowledgment.TI warrants performance of its hardware products to the specifications applicable at the time of sale in accordance with TI’s standard warranty. T esting and other quality control techniques are used to the extent TI deems necessary to support this warranty. Except where mandated by government requirements, testing of all parameters of each product is not necessarily performed.TI assumes no liability for applications assistance or customer product design. Customers are responsible for their products and applications using TI components. T o minimize the risks associated with customer products and applications, customers should provide adequate design and operating safeguards.TI does not warrant or represent that any license, either express or implied, is granted under any TI patent right, copyright, mask work right, or other TI intellectual property right relating to any combination, machine, or process in which TI products or services are used. Information published by TI regarding third-party products or services does not constitute a license from TI to use such products or services or a warranty or endorsement thereof. Use of such information may require a license from a third party under the patents or other intellectual property of the third party, or a license from TI under the patents or other intellectual property of TI.Reproduction of information in TI data books or data sheets is permissible only if reproduction is without alteration and is accompanied by all associated warranties, conditions, limitations, and notices. Reproduction of this information with alteration is an unfair and deceptive business practice. TI is not responsible or liable for such altered documentation.Resale of TI products or services with statements different from or beyond the parameters stated by TI for that product or service voids all express and any implied warranties for the associated TI product or service and is an unfair and deceptive business practice. TI is not responsible or liable for any such statements. Following are URLs where you can obtain information on other Texas Instruments products and application solutions:Products ApplicationsAmplifiers Audio /audioData Converters Automotive /automotiveDSP Broadband /broadbandInterface Digital Control /digitalcontrolLogic Military /militaryPower Mgmt Optical Networking /opticalnetwork Microcontrollers Security /securityTelephony /telephonyVideo & Imaging /videoWireless /wirelessMailing Address:Texas InstrumentsPost Office Box 655303 Dallas, Texas 75265Copyright 2004, Texas Instruments Incorporated。
RoboClaw ST 2x45A 双通道驱动型电机控制器数据表说明书

RoboClaw ST 2x45A, 34VDC Dual Channel Brushed DC Motor ControllerData Sheet Version 2.3Feature Overview:• 45 Amps Continuous Per Channel• 60 Amps Peak Per Channel• Screw Terminal Inputs• Channel Bridging Supported• Dual Quadrature Decoding• 9.8 million PPS Decoding• Multimode Interface• TTL Serial• USB Port• Analog Interface• R/C Input Control• Limit, Home and E-Stops• Up to 34VDC Operation• Cooling Fan With Automatic Control• 3.3v Compliant Control Outputs• 5v Tolerant Control Inputs• Programmable Current Limiting• Programmable Voltage Clamping• Closed and Open Loop Operation• Auto Tuning PID Feature• Mixed Control Modes• Data Logging• Diagnostic LEDs• Field Firmware Updates• Regulated 5VDC, 3A User Available Output• Over Voltage and Under Voltage Protection• Easy Tuning, Monitor and Setup with PC utilityDevice OverviewThe RoboClaw is an intelligent, high performance motor controller designed to control dual brushed DC motors. It can be controlled from USB, RC radio, PWM, TTL serial, analog and microcontrollers such as an Arduino or Raspberry Pi.RoboClaw automatically supports 3.3V or 5V logic levels, travel limit switches, home switches, emergency stop switches, power supplies, braking systems and contactors. A built-in switching mode BEC supplies 5VDC at up to 3 Amps for powering user devices. In addition power supplies can be utilized by enabling the built in voltage clamping control feature.A wide variety of feedback sensors are supported. This includes quadrature encoders, potentiometers and absoluteencoders which can be easily configured using the available auto tune function. With sensors, two brushed DCmotors can be controlled in closed loop mode allowing precise control over position and speed. With the ability to use potentiometers, servo systems can be created and controlled from any of RoboClaw’s interface modes.For greater control, built-in commands are available for controlling acceleration, deceleration, distance, speed, current sense, voltage limits and more. In addition, RC and analog modes can be configured by user defined settings to control acceleration and deceleration rates.RoboClaw incorporates multiple protection features including temperature, current, over voltage and under voltage limits.The protection features are self monitoring and protect RoboClaw from damage in any operating condition. User definable settings such as maximum current limit, maximum and minimum battery voltages are provided for more refined control.RoboClaw’s regenerative capabilities will charge a supply battery during slow down or breaking. It’s advance circuitry can change direction during full throttle without damage! RoboClaw also incorporates a LiPo cutoff mode to prevent battery damage.Multimode InterfaceRoboClaw’s I/O are voltage protected and can handle up to 5VDC. The I/O only output a high of 3.3V. This allows RoboClaw to be interfaced to 5V or 3V logic easily with no translation circuits required. RoboClaw can be connected directly to a Raspberry Pi or Arduino. All of RoboClaw’s inputs are internally pulled-up to prevent false triggers. Inputs can also be configured using the Motion Studio application.User Regulated Power OutputRoboClaw provides regulated power (BEC) for user devices. A high efficiency switching regulator supplies 5VDC at up to3 Amps. This voltage can be used to power external sensors, encoders, MCUs and other electronics. The regulated userpower is automatically current limited and thermally protected.Main BatteryThe peak operational input voltage depending on the model can be up to 34VDC, 60VDC or 80VDC. The modelsmaximum input voltage can not be exceeded. If the maximum voltage is exceed the motors will be disabled. Fully charged batteries maximum voltage must be taken into account when in use. RoboClaw is a regenerative motor controller. During regeneration, voltages can peak over the maximum rated voltage in which RoboClaw is designed to handle these over voltage spikes by braking the motors.Logic BatteryRoboClaw accepts a logic battery. The logic battery is also known as a backup battery. The user regulated power output (BEC) is by default powered from the main battery, unless a logic battery is detected. The logic battery source is coupled to the main battery through an on board automatic switch. If the main battery voltage drops below the logic battery input level, the logic circuit and user regulated power output will be drawn from the logic battery.SoftwareRoboClaw can be easily configured using the Motion Studio software tool. The Windows based application enables users to quickly configure RoboClaw. The software can be used during run time to monitor and control several operational parameters. Motion studio is available from the website. It can also be found in the Downloads section of the Basicmicro website or listed under the Download tabs on the production page.User ManualThis data sheet only covers model specific information and basic wiring. To properly setup and use RoboClaw refer to the RoboClaw User Manual available for download from .CoolingRoboClaw will generate heat. The maximum current ratings can only be achieved and maintained with adequate heat dissipation. The motor controller should be mounted so that sufficient airflow is provided. Which will dissipate the heat away from the motor controller during operation. Some models of RoboClaw include a built-in automatic cooling fan controller, which can be used to help maintain continuous currents under extreme conditions.Emergency StopThe motor controller should be wired using an external contactor, relay or high amperage mechanical switch to control the main power input. A second power source should be used to power the logic section in situations where the main power will be under heavy load. Voltage drops can occur from constant full load or high speed direction changes. Voltage drop can cause logic brown outs if only a main battery is used without a logic battery.USBThe motor controllers USB port should be used for configuration and debugging. The USB protocol is not designed for electrically noisy environments. The USB port will likely disconnect and not automatically recover during operation in electrically noisy environments. To recover from a dropped USB port, the motor controllers USB cable may require being unplugged and re-plugged in. The TTL serial control should be the preferred method of control in electrically noisy environments.Firmware UpdatesFirmware updates will be made available to add new features or resolve any technical issue. Before using RoboClaw for the first time it is recommended to update to the latest firmware. Download and install Motion Studio. Refer to the RoboClaw User Manual or Application Notes for additional information on updating the RoboClaw firmware.Hardware Overview:Control InterfaceThe RoboClaw ST uses standard screw terminals (2.54mm) spacing. The table below list the pins and their respectivefunctions. All pins are 5V tolerant and output 3.3V for compatibility with processor such as Raspberry Pi and Arduino. R/C pulse input, Analog and TTL can be generated from any microcontroller such as a Arduino or Raspberry Pi. The R/C Pulse input pins can also be driven by any standard R/C radio receiver . There are several user configurable options available. Toconfigure RoboClaw, install Motion Studio and connect it to an available USB port.Logic Battery (LB IN)The logic circuit of RoboClaw can be powered from a secondary battery wired to LB IN. A logic battery will prevent brownouts when the main battery is low or under heavy load. The positive (+) terminal is located at the board edge and ground (-) is the inside pin closest to the heatsink.Encoder Inputs (1A / 1B / 2A / 2B)The encoders inputs are labeled 1B, 1A, 2B and 2A. 1B and 1A are the inputs for encoder 1. 2B and 2A are the inputs for encoder 2 which also correspond to motor channel 1 and motor channel 2. Quadrature encoder inputs are typically labeled 1A, 1B, 2A and 2B. Quadrature encoders are directional. When connecting encoders make sure the leading channel for the direction of rotation is connected to A. If one encoder is backwards to the other you will have one internal counter counting up and the other counting down. Use Motion Studio to determine the encoders direction relative to the motors rotation. Encoder channels A and B can be swapped in software using Motion Studio to avoid re-wiring the encoder or motor.Control Inputs (S1 / S2 / S3 / S4 /S5)S1, S2, S3, S4 and S5 are configured for standard servo style headers I/O (except on ST models), +5V and GND. S1 and S2 are the control inputs for serial, analog and RC modes. S3 can be used as a flip switch input, when in RC or Analog modes. In serial mode S3, S4 and S5 can be used as emergency stops inputs or as voltage clamping control outputs.When configured as E-Stop inputs, they are active when pulled low. All I/O have internal pull-ups to prevent accidental triggers when left floating. S4 and S5 can be configured as home switch and limit switch inputs. The pins closest to the board edge are the I/0s, center pin is the +5V and the inside pins are ground. Some RC receivers have their own supply and will conflict with the RoboClaw’s 5v logic supply. It may be necessary to remove the +5V pin from the RC receivers cable in those situations.Cooling Fan ControlThe cooling fan control will automatically turn on and off a fan based on RoboClaws temperature. The fan will turn on when the board temperature reaches 45°C and will automatically turn off when the board temperature falls below 35°C.The fan control circuit can power a 5VDC fan at up to 230mA. A wide range of fans can be used. The CFM rating of the fan will determine how effective the fan is at cooling. A tested fan is available from DigiKey under part number:259-1577-ND. However any fan can be used provided it meets the electrical specifications outlined above.Main Battery Screw TerminalsThe main power input can be from 6VDC to 34VDC on a standard RoboClaw and 10.5VDC to 60VDC or 80VDC on an HV (High Voltage) RoboClaw. The connections are marked + and - on the main screw terminal. The plus (+) symbol marks the positive terminal and the negative (-) marks the negative terminal. The main battery wires should be as short as possible.Do not reverse main battery wires or damage will occur.DisconnectThe main battery should include a quick disconnect in case of a run away situation and power needs to be cut. The switch must be rated to handle the maximum current and voltage from the battery. Total current will vary depending on the type of motors used. A common solution would be an inexpensive contactor which can be sourced from sites like Ebay.A power diode rated for approximately 2 to 10 Amps should be placed across the switch/contactor to provide a return tothe battery when power is disconnected. The diode will provide the regenerative power a place to go even if the switch is open.Motor Screw TerminalsThe motor screw terminals are marked with M1A / M1B for channel 1 and M2A / M2B for channel 2. For a typical differential drive robot the wiring of one motor should be reversed from the other. The motor and battery wires should be as short as possible. Long wires can increase the inductance and therefore increase potentially harmful voltage spikes.Control ModesRoboClaw has 4 main functional control modes explained below. Each mode has several configuration options. The modes can be configured using Motion Studio or the built-in buttons. Refer to the RoboClaw User Manual for installation and setup instructions.RCUsing RC mode RoboClaw can be controlled from any hobby RC radio system. RC input mode also allows low powered microcontrollers such as a Basic Stamp to control RoboClaw. Servo pulse inputs are used to control the direction and speed. Very similar to how a regular servo is controlled. Encoders are supported in RC mode, refer to the RoboClaw user manual for setup instructions.AnalogAnalog mode uses an analog signal from 0V to 2V to control the speed and direction of each motor. RoboClaw can be controlled using a potentiometer or filtered PWM from a microcontroller. Analog mode is ideal for interfacing RoboClaw with joystick positioning systems or other non microcontroller interfacing hardware. Encoders are supported in Analog mode, refer to the RoboClaw user manual for setup instructions.Simple SerialIn simple serial mode RoboClaw expects TTL level RS-232 serial data to control direction and speed of each motor.Simple serial is typically used to control RoboClaw from a microcontroller or PC. If using a PC, a MAX232 or an equivalent level converter circuit must be used since RoboClaw only works with TTL level inputs. Simple serial includes a slave select mode which allows multiple RoboClaws to be controlled from a signal RS-232 port (PC or microcontroller). Simple serial is a one way format, RoboClaw can only receive data. Encoders are not supported in Simple Serial mode.Packet SerialIn packet serial mode RoboClaw expects TTL level RS-232 serial data to control direction and speed of each motor. Packet serial is typically used to control RoboClaw from a microcontroller or PC. If using a PC a MAX232 or an equivalent level converter circuit must be used since RoboClaw only works with TTL level input. In packet serial mode each RoboClaw is assigned a unique address. There are 8 addresses available. This means up to 8 RoboClaws can be on the same serial port. Encoders are supported in Packet Serial mode, refer to the RoboClaw user manual for setup instructions.USB ControlUSB can be used in any mode. When RoboClaw is in packet serial mode and another device, such as an Arduino, is connected commands from the USB and Arduino will be executed and can potentially override one another. However if RoboClaw is not in packet serial mode, motor movement commands will be overiden by Analog or RC pulse input. USB packet serial commands can then only be used to read status information and set configuration settings.There are several wiring configurations for RoboClaw. Each configuration will have unique wiring requirements to ensure safe and reliable operation. The diagram below illustrates a very basic wiring configuration used in a small motor system where safety concerns are minimal. This is the most basic wiring configuration possible. All uses of RoboClaw should include some kind of main battery shut off switch, even when safety concerns are minimal. Never underestimate a system with movement when an uncontrolled situation arises.In addition, RoboClaw is a regenerative motor controller. If the motors are moved when the system is off, it could cause potential erratic behavior due to the regenerative voltages powering the system. The regenerative voltages can cause problems if a power supply is used for main power. A voltage clamping circuit is recommended to dump the excessive voltages. See the RoboClaw user manual or Application Notes for voltage clamping setup and wiring diagrams.R/C ModeThe below wiring diagram is very basic and for use with R/C mode. R/C mode can be used when pairing RoboClaw with a standard R/C receiver. R/C mode can also be used with a microcontroller and using servo pulses to control RoboClaw. The RoboClaw supplies power to the R/C system. If the R/C receiver used, has its own power the 5V pin on the 3 pin header must be remove otherwise it will interfere with RoboClaw’s BEC.In all system with movement, safety is a concern. This concern is amplified when dealing with higher voltages. The wiring diagram below illustrates a properly wired system. An external main power cut off is required (SW1). The external cut off can consist of a high amperage mechanical switch or a contactor.When the RoboClaw is switched off or a fuse is blown, a high current diode (D1) is required to create a return path to the battery for potential regenerative voltages. In addition a pre-charge resistor (R1) is required to reduce the high inrush currents to charge the on board capacitors. A pre-charge resistor (R1) should be around 1K, 1/2Watt for a 60VDC motor controller which will give a pre-charge time of about 15 seconds. A lower resistances can be used with lower voltages to decrease the pre-charge time.Closed Loop ModeA wide range of sensors are supported for closed loop operation. RoboClaw supports dual quadrature encoders (up to9.8 million PPS), absolute encoders, potentiometers and hall effect sensors. The wiring diagram below is an exampleof closed loop mode using quadrature encoders. Quadrature encoders are directional. RoboClaw’s internal counters will increment for clockwise rotation (CW) and decrement for counter clockwise rotation (CCW). When wiring encoders A andB channels it is important they are wired to match the direction of the motor. If the encoder is wired in reverse it cancause a run away condition. All motor and encoder combinations will need to be tuned (see the RoboClaw user manual).Logic BatteryAn optional logic battery is supported. Under heavy loads the main power can suffer voltage drops, causing potential logic brown outs which may result in uncontrolled behavior . A separate power source for the motor controllers logic circuit, will remedy potential problems from main power voltage drops. The logic battery maximum input voltage is34VDC with a minimum input voltage of 6VDC. The 5V regulated user output is supplied by the secondary logic battery if supplied. The mAh of the logic battery should be determined based on the load of attached devices powered by the regulated 5V user output.R1D1Bridging ChannelsRoboClaws dual channels can be bridge to run as one channel, effectively doubling its current capability for one motor.Damage will result if RoboClaw is not set to bridged channel mode before wiring. Download and install Motion Studio.Connect the motor controller to the computer using an available USB port. Run Motion Studio and in general settings check the option to combine channels. Then click “Write Settings” in the device menu. When operating in bridged mode the total peak current output is combined from both channels. Each channel will indicate the amount of current being drawn for that channel. The peak current run time is dependant on heat build up. Adequate cooling must be maintained.For more information see the RoboClaw user manual.Bridged Channel WiringWhen bridged channel mode is active the internal driver scheme for the output stage is modified. The output leads must be wired correctly or damage will result. One side of the motor is connected to M1A and M2B. The other side of the motor is then connected to M1B and to M2A.DimensionsNotes:1. Peak current is automatically reduced to the typical current limit as temperature approaches 85°C.2. Current is limited by maximum temperature. Starting at 85°C, the current limit is reduced on a slope with a maximumtemperature of 100°C, which will reduce the current to 0 amps. Current ratings are based on ambient temperature of 25°C.3. RS232 format is 8Bit, No Parity and 1 Stop bit.4. Condensing humidity will damage the motor controller.WarrantyBasicmicro warranties its products against defects in material and workmanship for a period of 1 year. If a defect is discovered, Basicmicro will, at our sole discretion, repair, replace, or refund the purchase price of the product in question.*******************************.Noreturnswillbeacceptedwithouttheproperauthorization.Copyrights and TrademarksCopyright© 2015 by Basicmicro, Inc. All rights reserved. All referenced trademarks mentioned are registered trademarks of their respective holders.DisclaimerBasicmicro cannot be held responsible for any incidental or consequential damages resulting from use of products manufactured or sold by Basicmicro or its distributors. No products from Basicmicro should be used in any medical devices and/or medical situations. No product should be used in any life support situations.ContactsEmail:********************Techsupport:**********************Web: Discussion ListA web based discussion board is maintained at Technical Support*******************************************************************,byopeningasupportticketontheIon Motion Control website or by calling 800-535-9161 during normal operating hours. All email will be answered within 48 hours.。
Infoprint 250 導入と計画の手引き 第 7 章ホスト
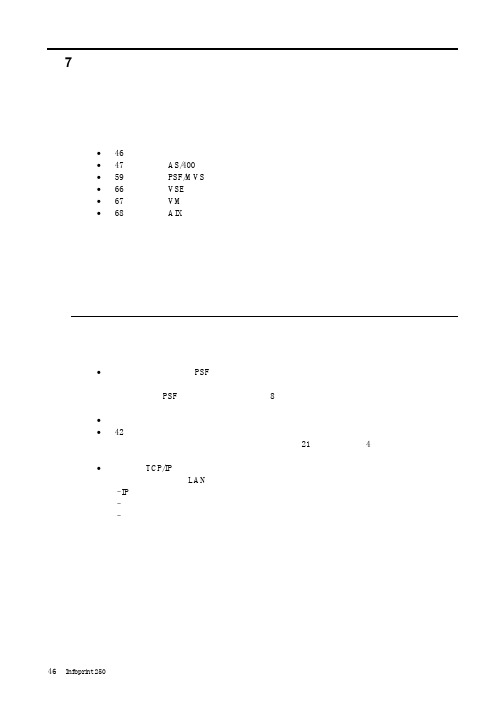
SUBNETMASK
255.255.255.128
Type of service...............: TOS
*NORMAL
Maximum transmission unit.....: MTU
*LIND
Autostart.....................:
AUTOSTART
*YES
: xx.xxx.xxx.xxx
: xx.xxx.xxx.xxx
*
(
)
IEEE802.3
60 1500
: xxxx
48 Infoprint 250
31. AS/400
IP
MTU
1
1
IPDS TCP
CRTPSFCFG (V3R2)
WRKAFP2 (V3R1 & V3R6)
RMTLOCNAME RMTSYS
MODEL
0
Advanced function printing............:
AFP
*YES
AFP attachment........................:
AFPATTACH
*APPC
Online at IPL.........................:
ONLINE
FORMFEED
*CONT
Separator drawer......................:
SEPDRAWER
*FILE
Separator program.....................:
SEPPGM
*NONE
Library.............................:
Atlas Copco Optimizer 4.0 中央控制器说明书

Central controller Optimizer 4.0It's all about efficiency,reliability andconnectivityOptimizer 4.0, the name says it all... This new device optimizes the operationof your compressed air and blower system while set pressure and flow arebeing met. It maximizes energy savings and keeps the units in good runningcondition with a proactive approach to maintenance through onlinemonitoring. The central controller is ready for Industry 4.0, or the Internet ofThings, and is designed for smart factories.Optimizer 4.0EfficiencyThe Optimizer 4.0 compliments the already efficient AtlasCopco compressors and blowers. Multiple unitsinstallation run with optimum pressure or flow band whileprioritizing machines that will have more efficientcombination. Realize the full energy saving potential ofVSD (Variable Speed Drive) units. This centralcontroller regulates the VSD to cope with varying demand,while avoiding fixed speed machines to run unloadwhenever possible.Reliability and uptimeAside from efficiency, our customers also demand reliablesolutions with the highest availability. When you combinemultiple units with the Optimizer 4.0, the load will bedistributed evenly among your compressors and blowers,hence equalizing their running hours. Therefore, planningand operation of the preventive maintenance can bedone accordingly.Compressors and blowers operating with Atlas Copco’scentral controller will have less load/unload cycles andwill operate at the lowest possible pressure/flow toextended the lifetime of your machines.ConnectivityManagement of facilities nowadays always involve remotemonitoring and control. In the 4th Industrial Revolution(Industry 4.0), machines should be able to sendinformation which can be analyzed by the system and thepeople who manage the units. This is only possible if yourmachines are connected. The Optimizer 4.0 is the solutionto connect your compressors, blowers and dryers to bemonitored and analyzed through Local Area Network(LAN) or via a cloud-based monitoring system. There arevarious ways to be connected and to monitor theperformance of your air system.3Applications controlled by a pressure or flow setpoint can easily be integrated in theOptimizer 4.0. As multiple machines and airnets can be connected, the Optimizer 4.0 is also capable to regulate based on pressure and flow simultaneously.1. Setpoint controlHaving a central controller reduces the average pressure band.It also reduces the operating pressure of your machines.• By reducing the pressure by 1 bar (or 14.5 psi), your energy usage lowers by 7%.• By reducing the pressure by 1 bar (or 14.5 psi) decreases air leakages by 13%.Multiple embedded functions in the Optimizer 4.0 in which pressure, capacity and speed can be regulated.LegendA =Net pressureB =Average pressureC =Min. system pressurePressure setpointOptimizer 4.0The Optimizer 4.0 efficiently controls up to three air flows • With or without a flow meter an accurate regulation is obtained.Easy implementation for each application:• One flow signal to the Optimizer 4.0.• Embedded flow bands ensure that the flow is always within the demand, reducing the energy cost related to excess air flow.• Minimizing the fluctuation of the air flow during a change in demand.• Reduced pressure results in energy savings.Multiple embedded functions in the Optimizer 4.0 in which flow, capacity and speed can be regulated.LegendA =Energy consumptionB =Air demand 1 =Energy loss 2 =Air demandFlow controlThe Optimizer 4.0 is equipped with multiple control modes that adapt to your compressed air & flow demands. Different control modes can also be applied to different group of compressors & blowers within a profile. Hence, there is group management.2. Control modes1. Multiple VSD'sRunning units will be at most optimum point.2. Turbos combined with VSDCentrifugal Turbos will work with VSD in harmony avoiding blow-off (load-sharing can also be applied).3. Global optimizationDemand profile can vary depending on time of the day or week, Optimizer 4.0 selects the most efficient combination of available machines LegendA =Flow (l/s)B =TimeC =SER (J/l)Energy saving mode5• Equalizes the running hours of the machines by giving them the same priority which can be modified based on unit of time preferred.• Reduces maintenance interventions to one single visit for all your machines• Planning & administration are more manageableEqual wear mode3. There is even more...Maximizing energy-saving potential even with non-Atlas Copco machines, made possible by an Interface Module for fixed screw compressor and Interface Box for variable speed drive and turbo compressors.Optimize your entire compressed air systemISO50001 is a systematic approach on how to achievecontinual improvement on energy usage by establishing the baseline, monitoring it and create another opportunity to improve the energy performance.The features of the Optimizer 4.0 supports this EnergyManagement System with its ability to determine the base,reduce energy consumption and continuously monitor the performance of the compressed air & blower system, which can also be gathered and able to generate report.Legend1. Define & Plan2. Implement3. Monitor & Continuous ImprovementSupports the working principle of EnergyManagement SystemOptimizer 4.0The air demand in WWT is changing over-time, resulting in a higher risk of energy losses due to slower PLC interaction.• Flexibility: Simple integration of new blowers • One single flow demand calculated by the WWT PLC system, no need for multiple calculations and complex tuning• Flow split based on the energy efficiency of the blower, the blowers are running at their most optimum point• Increased process and blower reliability, it’s not your local PLC system’s responsibility anymore. The Optimizer 4.0 takes care of the uptime!• Improved TCO: Reduced maintenance cost of the blowers and more energy savings• Reduced pressure, resulting in savingsWastewater treatment7In the food and beverage industry multiple blowers are used to aerate different fermentation processes. Fermenters require very accurate flow control to ensure the correct chemical reaction.• The Optimizer 4.0 has all the operating data of the screw and turbo blowers, ensuring that the blowers are running at the highest efficiency for each requested flow• Improved TCO: Reduced maintenance cost of the blowers and more energy savings• Accurate air flow regulation thanks to the knowledge of the blower’s behavior• Reduced pressure, resulting in savings• Flexibility: Easy integration of new blowers• Increased process and blower reliability, it’s not your local PLC system’s responsibility anymore. The Optimizer 4.0 takes care of the uptime! FermentationOne of the most critical facilities in the Electronics industry is compressed air. Loss of compressed air or huge dip in set pressure can lead to costly production loss. Hence most electronics companies have an integrated monitoring system that can provide data analysis and an easy to trace parameters’ history.• With Optimizer 4.0, you can easily gather information from the whole compressed air system through the Optimizer 4.0.• It can serve as communication gateway depending on customers required protocol• Electronics application requires huge compressed dry air. Hence they need more energy to produce compressed and dry air, a central controller with smart control algorithm can lower down the power consumption.Electronics Optimizer 4.0Due to huge application of compressed air in various processes such as Engine & Vehicle Assembly, Stamping, Painting Process, and other pneumatic tools application, Automotive Factories usually have multiple turbo units and several VSD compressors.• Optimizer 4.0 can manage the whole compressed air system and adapt to the demand of automotive assembly process.• It can store and generate report able to help plant managers plan their next steps to align their factories compressed air requirement.• The central controller also help in planning their maintenance with utilization information & machine data trend, leading to a more reliable system.AutomotiveThe food & Beverage industry has one of the most stringent quality air requirements. They consume a lot of compressed air for their different applications in their process, packaging, conveying and clean-in-process.• Having an Optimizer 4.0 also helps to monitor all critical parameters like dew-point, compressed air temperature and other measurement points that can be integrated and be monitored in the user interface via Analog inputs.• The compressed air profile in Food & Beverage usually varies depending on the products produced and time of the day, with multiple compressor and VSD units, Optimizer 4,0 will select the most efficient combination adapting to the factory's demand.Food & beverage9AIRnet/ProcessThis sections serves as the main screen of theOptimizer 4.0. It provides the overview of the wholesystem’s status and shows key parameters.Set Pressure or FlowSystem pressure or flow in a glanceEvolution of actual pressure or flow in a given timeframe.Calculated FlowIndicates utilized capacity & how much is stillavailable. In case a machine is not able to operate,the equivalent capacity in”red” bar will be shownto indicate action is required.Integrated MachinesOverview of all connected machines & their status(loaded, unloaded, % capacity & IGV positions). Allconnected units’ parameters are shown (pressure,calculated flow, power, speed, and othermeasurement points). Possible to integrate andisolate machines.Pinned ValueAside from Pressure & Flow, other criticalparameters can be shown in the main screen as“Pinned Value". It can be any parameter in thesystem that is already available in the Optimizer orany digital input from customer’s measurementpoint (actual flow, dew-point, ambienttemperature).Optimizer 4.0NotificationsNotification signs on the “Events” tab to inform the end-user.Description of machine’s cause of alarm (e.g. service required, warning, shutdown).Specific cause of the alarm in the Event Snapshot. HistoryTrace back the occurred events (level & type of machines) based on the selected period.EventsKey ParametersOverview of an Airnet / process pressure & flow in agraphCreate your own trend graph based on selectedparameters & time period.Energy DataMonitor power consumption trend of an Airnet/process or an individual machineAnalyze how efficient the system with an SpecificEnergy Requirement trend (power vs. flow) &compare it with the factory’s production output.Trends11REMOTEVIEWMonitoring & controlling is no longer confinedinside the compressor room. REMOTEVIEW mirrorsthe Optimizer 4.0 user-interface to any monitoringdevice through a Local Area Network (LAN).Remote control of the Optimizer 4.0 itself is alsopossible. You are able to change pressure/flowsetpoint, integrate & isolate units and select theoptimization profile that can done with sufficientaccess rights.Optimizer 4.0Get rid of high cost of system monitoring integration and have your own Atlas Copco-designed local visualization screen for machine parameters, compressed air & flow demand, power consumption and other notifications that can be viewed remotely via Local Area Network.Energy & VolumeCapture specific energy requirement and compare it in a specified period. Generating report is made easy whether with an Excel file or PDF format. UsageHow are the machines’ performance in terms of utilization?The “Usage” section provides information on how much individual machines are utilized. You can manage the maintenance planning of the entire system. The data can be used to justify additional compressors or blowers.This is all available in an optional SMARTVIEW feature.SMARTVIEWGet insights and access to compressed air & blowerequipment, anytime of the day or anywhere youare through Atlas Copco’s cloud-based monitoringsystem, SMARTLINK. A customized report onenergy efficiency is always ready to bedownloaded. Early warning notifications to replacemaintenance parts on time and avoid unnecessarybreakdown and production loss. Aside from thecustomer’s access, SMARTLINK is monitored in keystrategic areas around the globe by a dedicatedAtlas Copco specialists.SMARTLINK13The Optimizer 4.0 is a communication gateway. Depending on the communication protocol, Modbus TCP, Ethernet IP or OPC-UA, compressors and blowers data can be communicated to the facility site’s SCADA system. SMART2SCADA is an optional software upgrade and no extra hardware is needed.SMART2SCADA Optimizer 4.015Optimizer 4.0 can further increase the efficiency of the operation of the whole system by operating the integrated machines in their most optimum points possible. Dryer parameters can also be monitored. Key machineparameters and data trends can be generated and have an easily downloaded via Smartview options. Optimizer 4.0 can also be the data uploader to Atlas Copco’sSmartlink. This central controller also serves as a gateway to customer’s Scada / DCS system depending on the communication protocol.With the Atlas Copco local controller, it can easily be connected to the Optimizer 4.0 central controller.Performance curve of each model is known to Optimizer 4.0, enabling it to operate integrated machines as efficient as possible with energy saving mode, having a balanced running hours with equal wear mode, or prioritizing units to run with forced sequence. Aside from overview of the whole system, individual unit’s paramaters can also be viewed . These collected data from the Elektronikon are converted into graphical representation of a selected measurement or parameter.Aside from the new touch and feel, Atlas Copco’sElektronikon has also built-in Smartbox. Being connected,provides you an overview of the compressed air usage,status of all machines and plan the preventivemaintenance of all equipment. Smartlink connectivity also provides assistance from Atlas Copco on managing the whole compressed air or blower system.On the Optimizer 4.0, Air Dryer performance can be monitored, the status and the real-time dew-pointmeasurement reading. If the pressure dewpoint or quality of air is critical to the customer’s operations, it can be the “pinned value” that can also be shown on the main screen.Provides buffer and pressure & flow stability. It is also recommended to place the pressure transmitter in the pressure vessel to avoid pressure pulsations. The correct size of buffer, also provides enough time cushion for the Optimizer to make decisions.Another component to comply to the quality airrequirements is the air filter. But in due time, these filters can also need maintenance to avoid any contamination or contribute to huge pressure drop if clogged. Pressure differential signals can also be monitored in the Optimizer screen through 4-20mA analog inputs.Pipe installation is one of the most critical component in the compressed air system. For energy efficiency, it should be properly sized to avoid big pressure drop and ideally free from leakages. For critical applications, pipe should be clean and free from corrosion. Pressure sensors & flow meters can be installed in the distribution pipe and monitor it in the Optimizer 4.0 through 4-20mA digital input. Atlas Copco’s unique Airnet pipes is ideal for general and critical applications, part of our smart AIRsolution.1.Central controller2.Elektronikon Mk5 Touch3.Integrated Smartlink4.Air Dryer5.Air Receiver6.Air Filter7.AIRnetOptimizer 4.0smart AIR solutionsOnly a complete solution is an energy efficient system. smart AIR solutions combine compressors, blowers and boosters with quality air solutionsfully optimized to operate together in the most efficient and reliable way. Our smart AIR solutions apply for all our customers and include not onlythe products but also our services.17Operational capabilitiesMaximum number of connected machines60Maximum Load-unload, VSD & Turbo units30Dryers (monitoring)30Set-point control Pressure/FlowMaximum of airnets / processes3*Control modes**Energy Saving / Equal Wear / Forced Sequence* For compressor applications, multiple airnets are available through Optimization Plan.** Can implement within groups or between groups.ConnectivityStandard analog Inputs*8Standard digital input*4Standard digital output*4Data logging Minimum 30 days of measured or calculated data. Minimum 2 years for energy dataLocal / Remote ConnectivityEmbedded webserver view of user interface on any device in LAN via REMOTEVIEW (standard) Remote monitoring, data gathering, generating printable trend graphs via SMARTVIEW (optional) Online cloud-based monitoring via SMARTLINK (optional)Remote Commands via Fieldbus Modbus TCP / Ethernet IP via Optional SMART2SCADA software (no extra hardware needed) Modbus RTU / Profibus via optional Mk5 Gateway* Can be expandedHardwareDisplay size12"Screen Capacitive touch Amount of ethernet ports4Cubicle protection IP 54 Dimensions (LxWxH)600x600x210mm or (24x24x8 inch) Weight32kg (70lbs)Optimizer 4.0Notes19Atlas Copco AB(publ) SE-105 23 Stockholm, Sweden Phone: +46 8 743 80 00Reg. no: 556014-2720 2936741©219,AtlasCopcoAirpowerNV,Belgium.Allrightsreserved.Designsandspecificationsaresubjecttochangewithoutnoticeorobligation.Readallsafetyinstructionsinthemanualbeforeusage.。
Tracer UC400 程序可控传感器支架控制器说明书
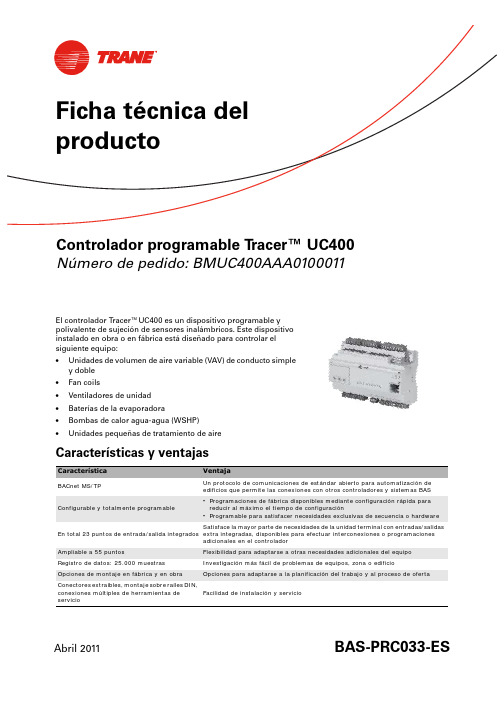
Controlador programable T racer™ UC400Número de pedido: BMUC400AAA0100011BAS-PRC033-ESEl controlador Tracer™UC400 es un dispositivo programable ypolivalente de sujeción de sensores inalámbricos. Este dispositivoinstalado en obra o en fábrica está diseñado para controlar elsiguiente equipo:•Unidades de volumen de aire variable (VAV) de conducto simple y doble •Fan coils •Ventiladores de unidad •Baterías de la evaporadora •Bombas de calor agua-agua (WSHP)•Unidades pequeñas de tratamiento de aireCaracterísticas y ventajas Característica Ventaja BACnet MS/TPUn protocolo de comunicaciones de estándar abierto para automatización de edificios que permite las conexiones con otros controladores y sistemas BASConfigurable y totalmente programable•Programaciones de fábrica disponibles mediante configuración rápida parareducir al máximo el tiempo de configuración•Programable para satisfacer necesidades exclusivas de secuencia o hardware En total 23 puntos de entrada/salida integradosSatisface la mayor parte de necesidades de la unidad terminal con entradas/salidas extra integradas, disponibles para efectuar interconexiones o programacionesadicionales en el controladorAmpliable a 55 puntos Flexibilidad para adaptarse a otras necesidades adicionales del equipoRegistro de datos: 25.000 muestras Investigación más fácil de problemas de equipos, zona o edificioOpciones de montaje en fábrica y en obra Opciones para adaptarse a la planificación del trabajo y al proceso de ofertaConectores extraíbles, montaje sobre raíles DIN, conexiones múltiples de herramientas deservicioFacilidad de instalación y servicioEspecificaciones del controlador y conformidad normativaDimensiones del controlador AlmacenamientoTemperatura:De -48 °F a 203 °F (de -55 °C a 95 °C)Humedad relativa:Entre el 5% y el 95% (sin condensación)FuncionamientoTemperatura:De -40 °F a 158 °F (de -40 °C a 70 °C)Humedad:Entre el 5% y el 95% (sin condensación)Alimentación:20,4 a 27,6 V CA (24 V CA, ±15% nominal) 50 a 60 Hz 24 VA (24 VA más cargas de salida binaria para un máximo de 12 VA por salida binaria)Peso de montaje del controlador:La superficie de montaje debe soportar: 0,364 kg (0,80 lb)Clasificación medioambiental (carcasa):NEMA 1Altitud:1981 m como máximo (6500 pies)Instalación:UL 840: Categoría 3Contaminación UL 840: Grado 2Cableado/transformadorCable de cobre de 16 AWG (recomendado)•Transformador de potencia 20,4 a 27,6 V CA (24 V CA, ±15% nominal) incluido en la lista UL, clase 2•El transformador deberá estar dimensionado para suministrar una alimentación correcta al controlador UC400 (12 VA) y a las salidas (máximo 12 VA por salida binaria)Conformidad normativa•UL916 PAZX- Equipos de gestión de energía abierta •UL94-5V Inflamabilidad •Marca de la CE •FCC parte 15, apartado B, límite clase B •AS/NZS CISPR 22:2006•VCCI V-3/2008.04•ICES-003, edición 4:2004•Comunicaciones BACnet MS/TP , admite protocolo BACnet de ASHRAE 135-2004 y cumple con la acreditación del laboratorio de pruebas BACnet (BTL) como dispositivo de perfil controlador específico de aplicación (ASC)Conexiones del dispositivoT able 1.Conexiones del dispositivo Conexión Cantidad TiposRango Notas *Entrada analógica (AI1 a AI5)5TemperaturaTermistor de 10 k Ω Punto de consignade 0 Ω a 1000 ΩResistivo de 200 Ω a 20.000ΩUsado normalmente para el interruptor de velocidad del ventiladorEntrada universal (UI1 y UI2)2Lineal0 a 20 mA Estas entradas pueden configurarse como entradas del termistor , entradas de 0 a 10 V CC o entradas de 4 a 20 mA. Lineal0 a 10 V CC Resistivo* Véase conexión de entrada analógica para los rangos y tipos indicados anteriormente BinarioColector abierto de estado sólido Impulso Colector abierto de estado sólido El tiempo mínimo de permanencia es de 10 milisegundos (ms) conectado y 10 milisegundos desconectado.Entrada binaria (a)(BI1 a BI3)(a)Entradas binarias, salidas binarias y TRIAC: por motivos de seguridad, no mezcle voltajes de clase 1 y clase 2 en un cerramiento o en un controlador sin una barrera física entre estas unidades.3Detectar 24 V CAEl controlador UC400 proporciona los 24 V CA requeridos para activar las entradas binarias si se utilizan las conexiones recomendadas.Salida binaria (a)(BO1 a BO3)3Relé2,88 A a 24 V CA auxiliar (Para más valores nominales de potencia, véase el Manual de instalación, funcionamiento y mantenimiento de Tracer UC400 [BAS-SVX20]).La alimentación debe cablearse hasta la salida binaria. Todas las salidas están aisladas entre sí y con respecto a tierra o alimentación. Los rangos se indican por contacto .Salida binaria (a)(BO4 a BO9)6TRIAC 0,5 A máximo a 24 a 277 V CA, resistivo y auxiliar (Para más valores nominales de potencia, véase el Manual de instalación, funcionamiento y mantenimiento de Tracer UC400 [BAS-SVX20]).Utilización para TRIAC de modulación. El usuario decide si se cierra el lado de alta (aplicando voltaje a la carga conectada a tierra) o el lado de baja (proporcionando tierra a la carga de alimentación). Los rangos se indican por contacto y la alimentación proviene del circuito de ALIMENTACIÓN DE TRIAC .Salida analógica/entrada binaria (AO1/BI4 y AO2/BI5)2Salida lineal 0 a 20 mALas terminaciones deben configurarse como salidas analógicas o como entradas binarias.Salida lineal 0 a 10 V CCEntrada binaria:Contacto seco Entradas de presión (PI1 y PI2)2 3 cables 0 a 5 en H 2O Entradas de presión suministradas con 5 voltios de alimentación. Diseñado para transductores de presión Kavlico™.Total global de los puntos 23Trane optimiza el rendimiento de edificios de oficinas y residenciales en todo el mundo. Trane es una empresa de Ingersoll Rand, líder en creación y mantenimiento de entornos energéticamente ef icientes, conf ortables y seguros, y of rece una amplia gama de dispositivos de control y sistemas de calef acción, ventilación y aire acondicionado avanzados, mantenimiento integral de edificios y piezas de repuesto.Si desea obtener más información, visite .Debido a la política de continua mejora de sus productos y de sus datos correspondientes, Trane se reserva el derecho de modificar las especificaciones y el diseño sin previo aviso.© 2010 Trane Reservados todos los derechos BAS-PRC033-ES Abril de 2011Producido con un papel que utiliza menos árboles y productos químicos y menos energía, con prácticas de impresión respetuosas con el medio ambiente que producen menos residuos.。
海尔商业空调中央控制器系统说明书
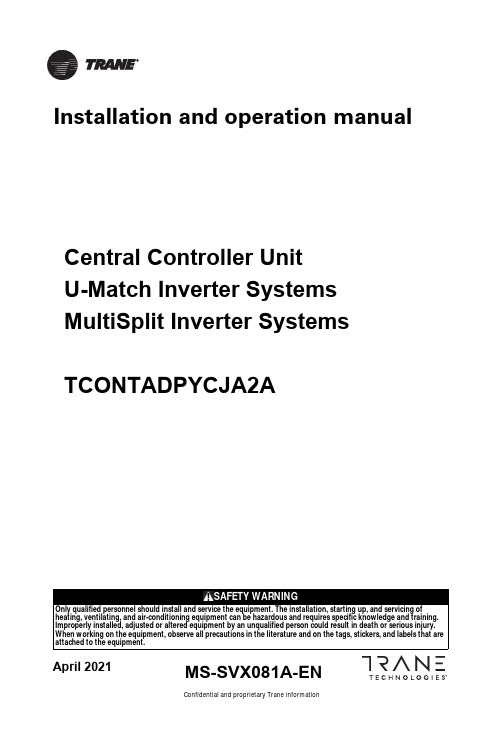
Central Controller U nit UMatch Inverter Systems MultiSplit Inverter SystemsTCONTADPYCJA2AConfidential and proprietary Trane informationA pril 2021Installation and operation manualMS-SVX081A-ENUser manuals and installation manuals for remote control detector TCONTADPYCJA2AFunctions IntroductionRemote control detector(short form:Detector)is essential equipment of remote monitor system of Haier commercial A/C.By connecting the interface in indoot units or outdoor units,this detector can reach functions of remote an central control◆Communication function1.with air conditioning communication:①. YCJ-A002 can at most connect two same model units by six-pin fixed screw. It canrealize double switching function. It can control air conditioning to work in different ways according to the requirement of detector, at the same time query the airconditioner's operation information and fault information.munication with RS-485:①. Communication with the central controllerBM1 dip switch as (1: OFF, 2: OFF)Communicate with the central controller via RS-485 interface bus (A, B). It receives commands from central controller according to the units address what is set by detector dip switch. And to realize internal control or query request, and answer the reception status and air conditioning operation information and fault information.②Communication with the central controllerBM1 dip switch as (1: ON, 2: OFF)Communicate with the central controller by RS-485 bus port. According to the detector within the dip switch setting address, Receive commands from the central controller. Have internal control or query request, and answer the reception status and air conditioning operation informationand fault information.③Communicate with remote devices. Detector has RS-485 port, and the protocol is Modbus RTU, users can use the private network and open protocol to create remote control program, no need other accessories.The BM1 dip switch as (1: OFF, 2: ON).④communication with the central control systemD ip switch BM1 (1: ON,2: ON)Communicate with the central control system by RS-485 bus port(A, B). it receives12commands from central controller according to the units address what is set by detector dip switch. And to realize internal control or query request, and answer the reception status and air conditioning operation information and fault information.In order to improve the reliability of air conditioning, the detector has double switching function, set SW1 to single unit mode, detector controls the A unit according to the command from the host equipment. Set SW1 to double switching mode, it can realize double switching function.Double switching function realization: under normal condition, the detector control one unit ON and another unit OFF, when reach the switch time, detector wake up the OFF state unit and the ON state unit will still work half an hour and then OFF.If any air conditioner has failure, switch time will stop, the detector automatically wake up another unit, and let the failure unit OFF, then upload the failure information. After the failure restore, automatically change to the double switching function; if air-conditioner operate for some time and cannot reach setting temperature, switch time will stop, the detector automatically wake up another air conditioner, double units operate until reaching the setting temperature, then automatically turn off that air conditioner, and automatically restore the double switching function. Factory default switch time is 12 hoursDetector has three lights, yellow light is for RS-485 communication , red and green lights are for the air conditioner communication, When the communication is normal, lights in accordance with the frequency of 0.5s flashing, when have failure, lights in according with the frequency of 1s flashing, stop 2s flashingThrough the RS-485 bus to build a central control network, In order to reduce the impact of unified operation of air conditioning on the power grid, the detector set the delay start function, the delay time is automatically generated by the detector【1】【2】BM10:OFF 1:ON numbe485communication mode details00①TCONTCCMYCZG1/TCONTCCMYCZ256 single unit10②/01③Modbus rtu standard protocol 11④BMS system◆Dual switch function◆Address setting function◆Operation status displasy function◆Delay control functionThe detector with 8-bit dip switch (SW1), the highest bit D8 bit, for setting the single mode or double-switch mode,(D7, D6, D5, D4, D3, D2, D1) is used to set the number (central control network or double switch time when select the dual switch mode)◆Double switching function instructions◆use central controller for central control functionSystem OverviewDetector connects with the two same model units through six-pin fixed screw. Set the dip switch to double switching model. Only use the double switching function, the system does not need connect the other components; double switching time can be chosen 8,10,12,14 hours by dip switch setting.the specific settings and the corresponding time see dip switch list12V 、COM 、GND ports of detector connect with air conditioner. Dip switch set to singlemode, the specific settings and the corresponding address see dip switch list, The system also needs to connect withcentral controller, Each detector connect with central Controller by 2-pin fix screw(A,B).DetectorsIndoor Unit Indoor UnitOutdoor Unit Outdoor Unit4◆Status check◆When servicing, be sure to power off the power supplyMaintenanceDimension drawing•When select the single unit mode and control A unit, when A unit failure occurs, the detector will query fault information and upload it, when select double switch mode,detectorcontrolA unit and B unit, if one of air conditioner is faulty, the detector will query the fault information and upload it•Detector operating status and running lamp display: When operation properly, running lamp for 0.5 seconds off 0.5 secondsfor a cycle to indicate,When have the fault to flash 1 second, stop 2 seconds to cycle to indicate, yellow lamp for the central control of communication status indication, red light for the air conditioner A unit communication Status indication, green lamp for air conditioning B unit communication status indication•Wipe clean with a soft cloth and be careful not to touch the electrical parts.•Do not use gasoline, thinner, decontamination powder, chemical wipes, etc. to avoid damage to electrical parts.•Check whether the wiring with the central control and air conditioning is normal, there is no broken wire or the existence of loosening of the connection.Interface Description:1-air conditioning A communication port,three-core shielded communication wire connection, wire length is not more than 10meter2-air conditioning B communication port,three-core shielded communication wire connection, wire length is not more than 10meter3 - dial switch is used for centralized control interface of detector detector Communication Associationand dual switching functionIOS device to achieve remote control.Installation and commissioning◆installation and wiring of the basic requirements:Use a screw driver to install detector, screw spacing see the right figure.Keep the detector on a wall or other reliable location to ensure that there is no water and other creatures that may cause failure to enter.1.Central control network design planning principles:(1) Detector, in order to maintain the appropriate response speed and communication reliability, the number of detectors in one central system should not exceed 64 pieces (2)A/C should be ready for network ,bu sure to be installed and us according to instructions(3) Detector installation position does not leave the air conditioner too far; do not exceed the wiring length(4) Detector address number in strict accordance with the order from small to large allocation(5) Detector power from the indoor unit, 12V, need have distance with the high voltage cable .and the shieldlayer needs earth one side(6) Central control bus wire length limit less than 1000 meters(7) both ends of the bus in the A bus and B bus were connected between the 100 ohm metal film precision resistance (depending on the scene to match)(8) bus shielded wire single point grounding, the proposed layout in the middle of the communication bus location, and centralized controller similar(9) Central controller installation location in principle arranged in the middle of the communication bus position, and the communication bus shield ground similar2.Detector and air conditioning connection: Detector through the air conditioning interface six screws fixed terminal (12V、COM1、GND、12V、COM2、GND) ,andup to two air-conditioning (A, B) for wired communication; detector and air conditioning connection with the uniform wiring, one end of the wiring terminal with plug connect to air conditioning indoor PCB remote control terminal. If the detector does not operation properly during commissioning, it can be check by change the wiring polarity + - . Also can be based on the running lamp show the operation status of the air conditioning and communication interface to determine whether the normal.3.After the communication bus wiring is completed, connect the detector and the communication bus: the connection method of hand by hand type, all A ports in the same Bus, all B ports on another bus, the communication bus shielding line in the communication bus in a single point of grounding, communication bus total length Limited to less than 1000 meters.◆According to the host equipment to select RS-485 interface protocol by dip switch BM1:Detector built a variety of different protocols to correspond to different host equipment, the use of four different protocols corresponding to four different conditions:1.The host equipment is a centralcontroller, central controller can choose to select the device type for single unit, in order to be able to deal with different system structure, the detector has two built-in protocols that communicate with the central controller.5①central controller, select the communication mode for the single unit, then dip switch: BM1: 1: OFF; 2: OFF.The system diagram is as follows:67②the host equipment for the third party communication equipment, the detector provides the standard Modbusrtu protocol, BM1 dip switch: 1: ON; 2: OFF, The communication between the detector and the air conditioner is consistent with the other 3. When the detector is used as a third-party protocol converter, it should be specificAccess to the requirements of third-party host device connection; the basic functions are as follows:The address of the address set by SW1 changes to the slave address in the Modbus RTU communicationSerial port9600,8,n ,1130B modbusrtu query01 control 05/15WORD name Unit Range Remarks 01 function code 0Indoor units on/off Read operation to obtain the current switchunit status 0: off 1: onWrite operation to change the switch state 0: off 1: on03 function code query 03 control 06/16 0I n t e r n a l s e t t i n g temperature ℃16-30Read operation Get current setting temperature, write operationChange set temperature1within the machine running mode 1--5Read operation to obtain the current operating mode: 1 - cooling 2 - heating 3 - dehumidification4 – Fan only5 - automatic Write operation to change the operating mode: 1 - cooling 2 - heating 3 - dehumidification 4 – Fan only 5 - automatic2Fan speed 1--4Read operation to obtain the current fan speed: 1 - low speed 2 – middle speed 3 - high speed4 – Automatic speedWrite operation to change the fan speed: 1 - low speed 2 – middle speed 3 - high speed 4 -Automatic speed3i n d o o r c o n t r o lmode1--4 1 is not locked; 2 empty - query back to 1, issued to write 1; 3 query back to 1,Issued to write 1; 4 - lock 04 function code read only 0indoortemp ℃301℃1Fault code 0-256within the indoor fault code 0-256 value of 0 that no error ,2machine numberThe number of internal indoor This address exists , query back 08◆Power test :◆RS485 interface dip switch instructions1.Power test: After the equipment is connected, the power test①first verify the detector and air conditioner communication status, the red lightshould be light 0.5 seconds off 0.5 seconds as a cycle to indicate, If the indicator does not light or flashes for 1 second and stops for 2 seconds, it should check whether the communication wire of the air conditioner and detector are the connection is correct and the air conditioner is powered up until the indicator flashes normally.②check 485 communication indicator (yellow lamp), should be light 0.5 seconds off 0.5seconds as a cycle to indicate, if the instructions If the lamp does not light or flashes for 1 second and stops for 2 seconds, it should check whether the BM1 protocol is correct; the communication wire is connectedWhether it is correct; whether there is a device with a repeated address, etc., until the indicator flashes normally2.The detector and the host equipment communication, if the host equipment to normal monitoring and control of air conditioners, the completion of debugging.Performance parameters and accessoriesDetector built a variety of different protocols to correspond to different equipment, the use of four different protocols corresponding to four different conditions:1.The host equipment is a centralcontroller, central controller can choose to select the device type for single unit , in order to be able to deal with different the system structure, the detector has two built-in protocols that communicate with the central controller.①central controller, select the communication mode for the unit, then dip switch BM1:1: OFF; 2: OFF.performance parameter DC12VPower consumption Power consumption is less than 3W Detector code number 0151800130BAccessoriesair conditioning communication 3 core shielded wire, special number 0010452854, color white, yellow, and redPerformance parameter9S W 1(1m e a n O N ,0 m e a n O F F )B M 1c o d e1:O F F ;2:O F F1:O N ;2:O F F 1:O F F ;2:O N 1:0N ;2:O N[1][2][3][4][5][6][7][8]D e fi n i t i o n : u n i t a r y a i r c o n d i t i o n e D e fi n i t i o n :V R F D e fi n i t i o n :M o d b u s R T U D e fi n i t i o n :B M S G a t e a d d r U n i t a d d r 1---0000D u a l m o d e a d d r =1D u a l m o d e a d d r =1-1D u a l m o d e s l a v e I D =1D u a l m o d e 3101---0001D u a l m o d e a d d r =2D u a l m o d e a d d r =2-2D u a l m o d e s l a v e I D =2D u a l m o d e 311—— —— —— —— —— —— 1---1110D u a l m o d e a d d r =15D u a l m o d e a d d r =15-15D u a l m o d e s l a v e I D =15D u a l m o d e 31141---1111D u a l m o d e a d d r =16D u a l m o d e a d d r =16-16D u a l m o d e s l a v e I D =16D u a l m o d e 3115-0000000S i n g l e m o d e a d d r =1S i n g l e m o d e a d d r =1-1S i n g l e m o d e s l a v e I D =1S i n g l e m o d e 310-0000001S i n g l e m o d e a d d r =2S i n g l e m o d e a d d r =2-2S i n g l e m o d e s l a v e I D =2S i n g l e m o d e 311—— —— —— —— —— —— -0100110S i n g l e m o d e a d d r =39S i n g l e m o d e a d d r =39-39S i n g l e m o d e s l a v e I D =39S i n g l e m o d e 3138-0100111S i n g l e m o d e a d d r =40S i n g l e m o d e a d d r =40-40S i n g l e m o d e s l a v e I D =40S i n g l e m o d e 3139-0101000S i n g l e m o d e a d d r =41S i n g l e m o d e a d d r =41-41S i n g l e m o d e s l a v e I D =41S i n g l e m o d e 300-0101001S i n g l e m o d e a d d r =42S i n g l e m o d e a d d r =42-42S i n g l e m o d e s l a v e I D =42S i n g l e m o d e 301—— —— —— —— —— —— -1001110S i n g l e m o d e a d d r =79S i n g l e m o d e a d d r =79-79S i n g l e m o d e s l a v e I D =79S i n g l e m o d e 3038-1001111S i n g l e m o d e a d d r =80S i n g l e m o d e a d d r =80-80S i n g l e m o d e s l a v e I D =80S i n g l e m o d e 3039-1010000S i n g l e m o d e a d d r =81S i n g l e m o d e a d d r =81-81S i n g l e m o d e s l a v e I D =81S i n g l e m o d e 290-1010001S i n g l e m o d e a d d r =82S i n g l e m o d e a d d r =82-82S i n g l e m o d e s l a v e I D =82S i n g l e m o d e 291—— —— —— —— —— —— -1110110S i n g l e m o d e a d d r =119S i n g l e m o d e a d d r =119-119S i n g l e m o d e s l a v e I D =119S i n g l e m o d e 2938-1110111S i n g l e m o d e a d d r =120S i n g l e m o d e a d d r =120-120S i n g l e m o d e s l a v e I D =120S i n g l e m o d e 2939-1111000S i n g l e m o d e a d d r =121S i n g l e m o d e a d d r =121-121S i n g l e m o d e s l a v e I D =121S i n g l e m o d e 280-1111001S i n g l e m o d e a d d r =122S i n g l e m o d e a d d r =122-122S i n g l e m o d e s l a v e I D =122S i n g l e m o d e 281—— —— —— —— —— —— -1111110S i n g l e m o d e a d d r =127S i n g l e m o d e a d d r =127-127S i n g l e m o d e s l a v e I D =127S i n g l e m o d e 286-1111111S i n g l e m o d e a d d r =128S i n g l e m o d e a d d r =128-128S i n g l e m o d e s l a v e I D =128S i n g l e m o d e 287◆ Address setting functionSW01Definition[1][2][3][4][5][6][7][8]0———————Single mode 1———————Double Switch mode —00—————Double Switch time 8 hours —01—————Double Switch time 10 hours —10—————Double Switch time 12 hours —11—————Double Switch time 24 hours———0————Dual operation at ambient temperature of 34℃———1————Dual operation at ambient temperature of 32℃1———0000Double Switch mode and ad-dress=11———0001Double Switch mode and ad-dress=2———1———1110Double Switch mode and ad-dress=151———1111Double Switch mode and ad-dress=1600000000Single mode and address=100000001Single mode and address=2———01111110Single mode and address=12701111110Single mode and address=12810Trane - by Trane Technologies (NYSE: TT), a global climate innovator - creates comfortable, energy efficient indoor environments for commercial and residential applications. For more information, please visit or .Trane has a policy of continuous product and product data improvement and reserves the right to change design and specifications without notice. We are committed to using environmentally conscious print practices.©2020 TraneConfidential and proprietary Trane information。
Cambridge Technology ScanMaster

Frequently Asked Questions about Cambridge Technology ScanMaster™ Controller SolutionsContents1 Introduction (2)2 How do I choose a laser adapter? (2)3 What additional features does the SMC Auxiliary I/O board provide, and when wouldI typically use one? (3)4 Can you compare some of the common APIs and which Cambridge Technologycontrollers they support? (4)5 What is ScanScript? Is it available through SMD and all types of APIs? (5)6 What are the differences between J1 (Power) and J3 (24V)? How do you choosebetween them? (5)7 How many scan heads can a single SMC control? (5)8 What is the current status of MOTF function? (5)9 What features does SMC currently support that SC500 and EC1000 do not? (5)10 Is it possible to get tightly synchronized control of two SMC cards with four scanheads? (5)11 How do I set up the Start Mark signal on SMC? (6)12 How do I set up 5V Digital inputs on SMC? (6)13 SMD gives me the following error when I try to run a job: “SMC does not have thelicense to run this job. (200212.)” How do I get a license? (7)14 I installed the software and can see SMC on the network via ping, but the CTIsoftware doesn’t see the SMC device. What may be the problem? (8)1 IntroductionThis technical bulletin addresses some of the recent questions about how to integrate Cambridge Technology ScanMaster™ Controller Solutions into their laser systems.2 How do I choose a laser adapter?There are several popular commercial laser adapters to choose from depending on the type of laser you have and what your needs are.Table 1 - Laser adapters for popular commercial lasersManufacturer Model AdapterCoherent Avia_355-X LSR-03Coherent Coherent-C70 LSR-05Coherent Diamond E-400 LSR-05IPG YLM LSR-01IPG YLP LSR-01IPG YLR LSR-04IPG YLS LSR-01SPI G3 LSR-02SPI G4 LSR-02Synrad Ti60 LSR-03VGEN LSR-01LSR-01 – Provides IPG YLP 25 pin compatible connector.LSR-02 – Provides connector used by SPI Lasers on their G3 and G4 models.LSR-03 – A LSR-01 connector with BNC style LaserMod out signal.LSR-04 – 24V compatible, provides customizable connections via Phoenix style connections and a TTL BNC modulation signal.See the SMC hardware reference manual for details.3 What additional features does the SMC Auxiliary I/O boardprovide, and when would I typically use one?Use the SMC Auxiliary I/O board when you need extended Input/Output (see below) or a second XY2- 100 connection. The Auxiliary I/O board includes Phoenix Contact industrial automation connectors for easy PLC connections.•XY2-100 25 pin connections•Second XY2-100 port•DB9 COM port (COM3)•16 new AUX inputs (0-15)•16 new AUX outputs (0-15)•Phoenix connectors for easy wiring•RS485 Phoenix connection•5V or 24V I/O operationFigure 1 - SMC Auxiliary I/O boardUse the SMC Auxiliary I/O board when you need the extended I/O (see above) or a second XY2-100 connection. The board also provides Phoenix Contact industrial automation connectors for easy PLC connections.4 Can you compare some of the common APIs and whichCambridge Technology controllers they support?Table 2 - Comparison of APIs supported by Cambridge Technology controllersAPI Description Similarities &Differences Limitations ControllerScanMaster API (SMAPI) The common API forall CambridgeTechnologycontrollers and therecommended API. Itallows you toincorporate complexshape rendering, suchas barcodes, text,hatching, etc. intoyour applications.Built on top of theXML API, it addsmuch morefunctionality, includingscripting and complexshape support.Actively supported,including bug fixesand enhancements.Requires VisualStudio® but is themost functionalchoice.Requires .NET 4.0Runtime.All CambridgeTechnologycontrollersRecommendedselection.XML API XML API is a commonAPI forEC1000/SM1000 andSMC controllers. Itallows vector orientedlow level control ofmarking operation. Similar in scope toSMAPI for vectormarking but withoutbasic support for highlevel shapes.Actively supported,including bug fixesand enhancements.Jobs are representedas ASCII text in XMLformat. Less powerfulfunctionality thanSMAPI. Error codeswith some description.No line numbers witherrors.EC1000/SM1000or SMCUniversal API An earlier API used Similar in capability to Less functional than SC500 with the SC500 Visual XML API. SMAPI. Bug fixesStudio VC++ only. Notenvironment. recommended for newdevelopment.Remote API An ASCII based APIallowing the remotecontrol managementof controllers and theirjobs. To be used with PLCbased controlsystems.EC1000/SM1000or SMC5 What is ScanScript? Is it available through SMD and all typesof APIs?ScanScript is a domain-specific scripting language designed to support many intricate scenarios in the laser scanning industry. This lightweight yet powerful scripting language consists of several libraries of dedicated algorithms to perform laser scanning functions such as marking job flow control, process automation through I/O and much more. ScanScript is extensively used by SMD to extend its capabilities in automation situations. It is not available from the XML API.6 What are the differences between J1 (Power) and J3 (24V)?How do you choose between them?J1 is the standard power connection for SMC (differential voltage between V+ and V- must be in the range of 15–48V). J3 input is optional and is designed to conveniently supply digital I/O optical isolators on the expansion I/O board.7 How many scan heads can a single SMC control?The SMC can control two heads. Current design is limited to using the same job, one laser, but with different correction tables for each head.8 What is the current status of MOTF function?MOTF job setup is done in ScanScript. SMC supports either X or Y tracking.9 What features does SMC currently support that SC500 andEC1000 do not?SMC has ScanPack mode, supports more I/O options, and has faster processing, more working memory, and more onboard storage capacity for holding larger and more jobs than both SC500 and EC1000.10 Is it possible to get tightly synchronized control of two SMCcards with four scan heads?Yes, it’s possible to get tightly synchronized control of two SMC cards with four scan heads. The user needs to control the two SMC controllers via a programmable PLC controller so they both get the same start signal.11 How do I set up the Start Mark signal on SMC?The easiest method to set up the Start Mark signal on the SMC is to connect a switch between pin 3 (start signal input) and pin 4 (GND). You can use the following code in SMD ScanScript to have your program wait for the start signal.Report("Waiting for the StartMark")count = 1while true doif (Io.ReadPin(Pin.Din.StartMark)==true) thenReport("Accepted the part Start Marking")ScanAll()Laser.WaitForEnd()Report("Marked" ..count)count = count + 1Sleep(1000) --for a short job you may need some time to release the switchelse--Keep the part on conveyor or start systemSleep(10)endend12 How do I set up 5V Digital inputs on SMC?The following diagram shows the setup to attach a button/switch to an SMC Digital I/O board input for 5V. Operation and switch on UserIn1.Figure 2 -Connection DescriptionAny 5V Out to GPICOM Provides 5V TTL operationOne end of switch to GPI0(Gen. purpose in#0=UserIn1) Provide switch operation I/O to UserIn1One end of switch to GND Provide Ground ref. to switch13 SMD gives me the following error when I try to run a job:“SMC does not have the license to run this job. (200212.)”How do I get a license?Customer Service will need two items of information to send you a license file:1. The sales order number from your controller purchase.2. The internal license key number from the controller:a. For SMC or EC1000, run the corresponding firmware loader application for the controller youare using (see section 4.2 - Running the Firmware Loader).b. For the SMC, you can also access the key using the configuration editor (see step 4 - Selectdevice configuration).Once the Firmware loader is running and the appropriate controller selected, note the license key number that is found in the lower left corner. Send this number along with the original Sales Order number to Cambridge Technology Technical Support. You will receive a license file in via e-mail.14 I installed the software and can see SMC on the network viaping, but the CTI software doesn’t see the SMC device. What may be the problem?Because the Cambridge Technology controllers are network-based devices, Cambridge Technology applications must have permission to go through the Windows Firewall to work properly. If your firewall is blocking the broadcast monitor, it will not show any devices present.For example, most Cambridge Technology applications need to sense the presence of controllers that periodically broadcast system information on the network. If the broadcast packets are blocked from reaching the applications by the Windows Firewall, they will not be aware of them and hence, not be able to connect to them.Please enable Firewall access to the Home/Work, and Public network categories for all Cambridge software products. It may also be necessary to enable the Domain category at some sites.You can access the firewall settings by:Start→Control Panel→System and Security→Windows Firewall→Allowed Programs。
TI 控制模式快速参考指南说明书

Control-mode quick reference guideOverviewTI is active in the development of leading-edge controlcircuits to help engineers address specific designchallenges. Since no control mode is optimal for everyapplication, various control modes for non-isolated step-down controllers and converters are referenced with theiradvantages and how to learn more about each mode.The TI portfolio contains 15 types of control architecturesfor non-isolated TPS- and LM-series switching DC/DCconverters and controllers.Voltage modeInternally-compensatedadvanced currentmode (ACM)Direct connection tothe output capacitor(D-CAP™)Voltage mode with voltage feed-forward Hysteretic controlmodeD-CAP+™controlmodePeak current mode Constant on-time D-CAP2™ controlmodeAverage currentmodeConstant on-timewith emulated ripplemodeD-CAP3™ controlmodeEmulated currentmodeDCS-Control™:Direct control withseamless transitioninto power-savemodeD-CAP4™controlmodeVoltage modePulse-width modulation (latch output) is accomplished by comparing a voltage error signal (V E) from the output voltage and reference voltage to a constant saw-tooth-ramp waveform. The ramp is initiated by a clock signal from an oscillator. Good noise-margin performance is attained with a fixed ramp amplitude (V R). Voltage regulation is independent of the output current. Voltage mode uses type-3 compensation addressing a double-pole power stage to support a wide range of output filter combinations for externally compensated devices.When to use: When a fixed, predictable switching frequency is desired. Also useful when wide output-load variations are possible.Popular devices: TPS54610, TPS40040, LM22670Learn more:Switching Power Supply Topology Voltage Mode vs. Current ModeCLOCKVVLATCHEROUTPUTVoltage mode with voltage feed-forward Similar to voltage mode, but ramp generator varies the PWM ramp slope with the input voltage at a constant ramp magnitude and delivers an instantaneous response to input voltage variations. The PWM does not have to wait for loop delays to change the duty cycle.When to use: When a fixed, predictable switching frequency is desired. Also useful when wide variationsof input voltage and output load are possible.Popular devices:TPS40057, TPS40170, TPS56121 Learn more:Effect of Programmable UVLO on Maximum Duty Cycle Achievable With the TPS4005x and TPS4006x Family of Synchronous Buck ControllersVt>t and D>DVtD=tPeak current modePulse-width modulation (latch output) is accomplished by comparing a voltage error signal (V E) and a ramp waveform (V S) derived from the output current. The ramp is initiated by the clock signal. This mode offers fastresponse to output current changes. However, it can be susceptible to noise sensitivity at low duty cycles due to leading-edge current spike. It uses type-2 compensation addressing a single-pole power stage for externally compensated devices.When to use: When a fixed, predictable switching frequency is needed with a lower parts count than the externally-compensated, double-pole voltage mode.Peak current mode uses a single zero compensator,which is easier to design than voltage mode’s double-zero compensator.Popular devices: TPS54620, TPS62913, LM5140-Q1Learn more: Understanding and Applying Current-Mode ControlTheoryCLOCKV EV SLATCH OUTPUTAverage current modeAverage current mode addresses noise immunity issues, peak-to-average current errors, and slope compensation needs of peak current mode. Average current mode introduces a high gain integrating current error amplifier into the current loop. The voltage across a current sense resistor represents the actual inductor current. The difference, or current error, is amplified and compared to a large amplitude saw-tooth (oscillator ramp) at the PWM comparator inputs. The gain of the current loop effectively sets the slope compensation without restricting the minimum on-time or minimum-off time. Current sensing is usually inside the regulator, but can be external.When to use: Effectively control currents other than inductor current, allowing a much broader range of topological application.Popular devices: TPS546D24S , TPS546B24SLearn more: Average Current Mode Control of Switching Power SuppliesEmulated current modeSimilar to current mode, but employs a gated sample and hold circuit to capture current information emulated by measuring inductor voltage to estimate the ramp current. Eliminates the leading-edge spike issue of the traditional peak-current mode by allowing smaller duty cycles. Provides a clean current waveform when operating near the minimum on-time.When to use: When low duty cycle is neededversus traditional current mode, without current noise susceptibility.Popular devices: LM5116, LM5119Learn more: Emulated Current Mode Control for Buck Regulators Using Sample and Hold TechniqueInternally-compensated advanced currentmode (ACM)Internally-compensated ACM is a ripple-based, peak-current-mode control scheme that uses an internally generated ramp to represent the inductor current. This control mode provides a balance between the fast transient response of non-linear control modes (D-CAP™, constant on-time, and so forth) and the broad capacitor stability of other externally-compensated, fixed-frequency control modes (voltage mode, current mode). Internally-compensated advanced current mode provides a fixed, predictable frequency and a simplified compensation selection to reduce external components.When to use: When fixed frequency and/or stack ability is needed with good output capacitor tolerance and a simplified compensation selection.Popular devices: TPS543B22 , TPS543C20A , TPS543620Learn more: Internally Compensated Advanced Current Mode(ACM)Hysteretic control modeThe simplest control scheme. The PWM (SW) on-time (T ON ) is terminated when the feedback voltage is greater than a reference-high threshold and the off-time (T OFF ) is terminated when the feedback voltage is less than a reference-low threshold. No compensation components are required. The PWM switching frequency is not controlled and varies with load current and delivers higher efficiency at lighter loads.When to use: When fast transient response is required. There is no clock-signal time delay to initiate the ramp. A certain amount of ripple is required at the output from the output capacitor’s ESR.Popular devices: LM3475, LM3485Learn more: LM3485 Hysteretic PFET Buck Controller Data SheetI OUTV REF (HIGH)V OUT GNDV IN V REF (LOW)Constant on-timeA slight variation to hysteretic control minimizing frequency shift, but with a single voltage-threshold level, yet achieving fast transient response. The on-time is terminated by a one-shot on-timer and is proportional to the input voltage. The off-time is terminated when the feedback voltage falls below the reference-low threshold.When to use: When fast transient response is required and a fixed or predictable switching frequency is not required. A certain amount of ripple is required at the output from the output capacitor ESR.Popular devices: LM5017, LM2696, TPS54A20Learn more: Controlling Output Ripple and Achieving ESR Independence in Constant On-Time (COT) Regulator DesignsI OUTV OUTGNDV V IN V REFConstant on-time with emulated ripple modeA variation of the COT regulator that senses a portion of the low-side MOSFET’s off-time current and injects it into the error comparator to emulate ripple. This control mode has the same fast transient response and fewer external component advantages of COT.When to use: When employing low-ESR ceramic capacitors or when an external ripple injection circuit is undesirable.Popular devices:LM3100, LM3150Learn more:Emulated ripple technique advances hysteretic switch-mode suppliesDCS-Control™: Direct control with seamless transition into power-save modeCombines the advantages of hysteretic control for a fast transient response without compensation components, and the advantages of voltage-mode control for high DC accuracy with a seamless transition from PWM to power saving mode (PSM).When to use: When light-load efficiency is needed with small, low-ESR ceramic capacitors.Popular devices:TPS62872,TPS628303, TPS62903, TPS82130Learn more:High-efficiency, low-ripple DCS-Control™ offers seamless PWM/power-save transitionsFBDirect connection to the output capacitor (D-CAP™)Similar to COT control except a one-shot timer generates an on-time pulse that is proportional to the input voltage and the output voltage. When the falling feedback voltage equals the reference voltage, a new PWM on-pulse is generated. Fast response to load changes is achieved with a high-speed comparator in the control loop. D-CAP™ minimizes frequency shift compared to hysteretic control.When to use: When a fast transient response is required and POSCAP or medium-ESR output capacitors are used. No loop-compensation calculation or components are needed.Popular devices:TPS51116, TPS53219A, TPS53355Learn more:Adaptive Constant On-Time (D-CAP™) Control Study in Notebook ApplicationsT OND-CAP+™D-CAP+ adds an error amplifier to D-CAP that compares V FB to V REF for better output voltage accuracy and a current sense amplifier to sense the current directly, instead of relying on output ESR to act as the sense element. D-CAP+ is a true voltage-controlled current source without a clock limitation like most variants of current mode control. D-CAP+ is used where true current sensing is required, such as multi-phase and droop-compensation (load-line) applications with one output voltage. Current sensing may be accomplished either inside or outside of the power IC depending on the device.When to use: When high accurate current sensingis needed for load-line or multi-phase controller applicationsPopular devices:TPS53661, TPS53667, TPS548C26Update Learn more:D-CAP+™ Control for Multi-phase, Step-Down Voltage Regulators for Powering MicroprocessorsD-CAP2™A slight variation of D-CAP with the same transient and external component advantages as D-CAP . This control mode supports ceramic output capacitance without external circuitry. A signal from an internal ripple-injection circuit is fed directly into the comparator, thus reducing the need for output voltage ripple from the capacitor’s ESR. The ramp is emulated by the output inductor.When to use: When desiring fast transient response with low-ESR ceramic output capacitors.Popular devices: TPS563202, TPS563210Learn more:D-CAP2™ Frequency Response ModelD-CAP3™A variation of D-CAP2™ with the same transient and external component advantages. A sample-and-hold circuit is built-in to the converter to remove an offset voltage created by D-CAP2’s emulated ramp circuit,improving the voltage reference accuracy. Well suited for powering low-core-voltage FPGAs, ASICs and DSPs.When to use: When a tighter reference voltage accuracy and a fast transient response are desirable when using ceramic output capacitors.Popular devices: TPS565247 , TPS56C231, TPS548B28, TPS563206Learn more: Accuracy-Enhanced Ramp-Generation Design forD-CAP3 ModulationD-CAP4™D-CAP4 includes the advantages as D-CAP3, but desensitizes the loop gain to the output voltage in order to improve the transient response at higher output voltages. The ramp injection principle is the same as D-CAP3, except the ramp common mode and amplitude are independent of the output voltage. The ramp common mode is inversely proportional to (1-D), keeping ramp amplitude constant, so there is less need to adjust the ramp for different output voltages.When to use: When fast transient response time is needed with higher output voltages, like 3.3 V or 5 V .Popular devices:TPS54KB20Important Notice: The products and services of Texas Instruments Incorporated and its subsidiaries described herein are sold subject to TI’s standard terms and conditions of sale. Customers are advised to obtain the most current and complete information about TI products and services before placing orders. TI assumes no liability for applications assistance, customer’s applications or product designs, software performance, or infringement of patents. The publication of information regarding any other company’s products or services does not constitute TI’s approval, warranty or endorsement thereof.All trademarks are the property of their respective owners.IMPORTANT NOTICE AND DISCLAIMERTI PROVIDES TECHNICAL AND RELIABILITY DATA (INCLUDING DATA SHEETS), DESIGN RESOURCES (INCLUDING REFERENCE DESIGNS), APPLICATION OR OTHER DESIGN ADVICE, WEB TOOLS, SAFETY INFORMATION, AND OTHER RESOURCES “AS IS” AND WITH ALL FAULTS, AND DISCLAIMS ALL WARRANTIES, EXPRESS AND IMPLIED, INCLUDING WITHOUT LIMITATION ANY IMPLIED WARRANTIES OF MERCHANTABILITY, FITNESS FOR A PARTICULAR PURPOSE OR NON-INFRINGEMENT OF THIRD PARTY INTELLECTUAL PROPERTY RIGHTS.These resources are intended for skilled developers designing with TI products. You are solely responsible for (1) selecting the appropriate TI products for your application, (2) designing, validating and testing your application, and (3) ensuring your application meets applicable standards, and any other safety, security, regulatory or other requirements.These resources are subject to change without notice. TI grants you permission to use these resources only for development of an application that uses the TI products described in the resource. Other reproduction and display of these resources is prohibited. No license is granted to any other TI intellectual property right or to any third party intellectual property right. TI disclaims responsibility for, and you will fully indemnify TI and its representatives against, any claims, damages, costs, losses, and liabilities arising out of your use of these resources.TI’s products are provided subject to TI’s Terms of Sale or other applicable terms available either on or provided in conjunction with such TI products. TI’s provision of these resources does not expand or otherwise alter TI’s applicable warranties or warranty disclaimers for TI products.TI objects to and rejects any additional or different terms you may have proposed.Mailing Address: Texas Instruments, Post Office Box 655303, Dallas, Texas 75265Copyright © 2023, Texas Instruments Incorporated。
威世 2805 4 象限 pwm 运动控制器 用户手册说明书

4-Quadrant PWMFor combination with:Brushless DC-ServomotorsMotion ControllerGeneral information 1) Can be changed over the RS232 port (factory setting: command velocity is analog).2)Preset value. Can be changed over the RS232 port.Note: The Motion Controller is supplied with detailed operating instruction manual for easy installation and start-up.The MCBL 2805 was designed for Faulhaber brushless DC-Servomotors with linear hall sensors. This means that, even without an external encoder, low speed and positioning with a resolution up to 1/1000th of a revolution is possible. The motion controller is based on a power-ful 16-Bit micro controller with excellent fi ltering quality. Maximum Power:Velocity Control: High performance speed synchronization andthe lowest possible torque variance even in the most demanding of applications. A PI-controller makes sure that the command position is accurately achieved. Velocity Profi les: Ramping, triangular, trapezoidal, and more complex combined motion profi les are available to the user.Positioning Mode: Positioning with high resolution including limit switches and zero referencing.Additional Modes: For example, Stepper Motor Mode, to synchro-nize multiple motors.Torque Controlling: Achieved through current limiting. Saving and Running Program Sequences: For stand-alonep ositioning applications and to relieve the host PC.Modern Technology in Miniature Format:High effi ciency Amplifi er with high range PWM frequencies Power MOSFETS with low input resistanceUnique temperature supervision of the power MOSFETS Powerful 16-bit micro controller RS232 InterfaceOn-board memory (EEPROM)Inputs and Outputs:Command Value Input: For inputing command speed values in digital or analog form. This input can also interpret a reference mark signal. Depending on the mode, a frequency signal or an incremental encoder can be connected at this input.Fault Output (Open Collector): This output can also be programmed as a direction of rotation input, a digital input, or a reference mark input. RS232 Interface: For connecting a host PC and controlling program sequences.An additional digital input.The inputs are suitable for controlling program sequences.Specifi cations subject to change without notice1628 T 012 B K11551628 T 024 B K11552036 U 024 B K11552444 S 024 B K11553056 K 012 B K11553056 K 024 B K11553564 K 024 B K1155OptionsFaulhaber offers the optional Multiplexer Board to operate mul-tiple motion controllers from one host PC.To accomodate the customers specialized needs we offer factory preconfi guring of modes and parameters to fi t the application. The Faulhaber Motion Manager is available for download from the internet at or upon request.Adapters for IE2 – xx Encoders allow for simple attatchment to mounting railings.Ordering informationThis Motion Controller is exclusively d esigned for the control of the following motors and can be ordered with motor or on its own.K1155 indicates motor with linear Hall sensors for implementation with MCBL 2805.Note: the no-load speed is approx. 20% lower when used in combination with the MCBL 2805.ProgrammingA complete ASCII command set is available for programming and operating the motion controllers. All that is necessary is a terminal program such as the ‘hyperterminal’ provided with the Windows operating system. The Faulhaber Motion Manager program is available for users of Windows 95/98/ME and NT, 2000, XP . This program makes confi guration and operation easy and allows the user to perform an online graphic analysis of the performance of the drive.Additional Modes Stepper Motor Mode Gearing ModeAnalog Voltage Positioning Mode External EncoderVoltage Regulator ModeSpecifi cations subject to change without notice。
FlexLogix 控制器(Controller)15.6版本说明书
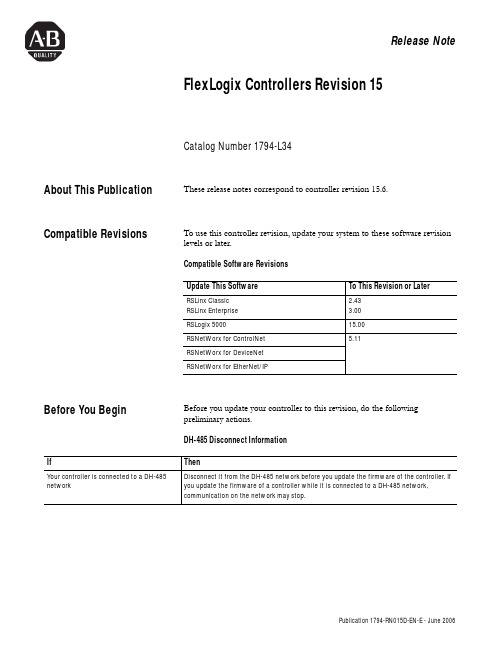
Publication 1794-RN015D-EN-E - June 2006Release NoteFlexLogix Controllers Revision 15Catalog Number 1794-L34About This Publication These release notes correspond to controller revision 15.6.Compatible RevisionsTo use this controller revision, update your system to these software revision levels or later.Compatible Software Revisions Before You BeginBefore you update your controller to this revision, do the following preliminary actions.DH-485 Disconnect InformationUpdate This Software To This Revision or Later RSLinx Classic RSLinx Enterprise 2.43 3.00RSLogix 500015.00RSNetWorx for ControlNet 5.11RSNetWorx for DeviceNet RSNetWorx for EtherNet/IPIfThenYour controller is connected to a DH-485 networkDisconnect it from the DH-485 network before you update the firmware of the controller. If you update the firmware of a controller while it is connected to a DH-485 network, communication on the network may stop.2 FlexLogix Controllers Revision 15Known Anomaly in Revisions 15.0, 15.3, 15.4, 15.5, and 15.6Revisions 15.0, 15.3, 15.4, 15.5, and 15.6 of FlexLogix controllers have this known anomaly.Known Anomaly Description in Revisions 15.0, 15.3, 15.4, 15.5, and 15.6Corrected Anomaly in Revision 15.6Revision 15.6 of FlexLogix controllers corrects this anomaly. Corrected Anomaly Description in Revision 15.6The information in this section contains previous release notes.Corrected Anomaly in Revision 15.5Revision 15.5 of FlexLogix controllers corrects this anomaly. Corrected Anomaly Description in Revision 15.5Anomaly DescriptionLimitsInv and SelectLimitInv are swapped.In the High/Low Limit (HLL) instruction:•LimitsInv parameter is set when the SelectLimit is invalid.•SelectLimitInv parameter is set when the HighLimit and LowLimit parameters areinvalid.Lgx00055977 Anomaly DescriptionThe 1794-L34 controllers experience a non-recoverable major fault in approximately 3... 4 months of continuous operation. The 1794-L34 controllers experience a non-recoverable major fault in approximately 3 (4)months of continuous operation. Continuous operation is defined as the controller being powered up; the mode of the controller (program, run, remote) does not matter. This was caused by a background diagnostic test completion.Lgx00066633Anomaly DescriptionSometimes I/O modules on the local rails would not be sent the proper configuration data.If a module that uses a direct connection on the local rails of a 1794-L34 FlexLogix controller was removed or inserted under power (RIUP) or had its power removed and then reapplied, the module may not have its configuration data passed to it when the controller reopens the connection.When this happened, no indication was given that the module did not receive the configuration. The only way to tell was that the input and output values were not correct.Lgx00061814Publication 1794-RN015D-EN-E - June 2006FlexLogix Controllers Revision 15 3Corrected Anomalies in Revision 15.4Revision 15.4 of FlexLogix controllers corrects these anomalies. Corrected Anomalies Description in Revision 15.4Anomaly DescriptionThe Batch recipe became inoperative.If two PXRQ instructions that had been triggered on the same phase were received by thebatch server before the first PXRQ completes, the Batch recipe became inoperative.Lgx00056918RSLogix 5000 software reported that POINT I/O connections were not scheduled even though they were scheduled and working on the network. After associating the RSNetWorx for ControlNet file in RSLogix 5000 software and scheduling the network, RSLogix 5000 software displayed an error while trying to save the configuration. The error stated that the POINT I/O connections were not scheduled even though they clearly were and working properly on the network.If you made changes to the program that didn’t involve ControlNet changes, and then downloaded, you had to reschedule the ControlNet network. The work around was to remove the association before you saved. Revision 15.4 removes the need for this work around.Lgx00058517PXRQ Instruction sometimes stayed in process and did not complete.When executing phase request messages to a batch server, the PXRQ instruction would sometimes stay in process (IP bit set) and never complete. The same scenario could have occurred if you took ownership of a phase from Logix5000 software while a PXRQ instruction was in process. The only recovery method was to transition from program to run or to cycle power to the controller.Lgx00058484, 58631, 59317, 58390, 57760Executing PXRQ instruction through manual phase control could have caused loss of controller communication.If the batch server was running and a PXRQ instruction was executed by manual control within Logix5000 software, the controller could have lost communication. The recovery method was to cycle power to the controller.Lgx00058151An Attempt to Abort a Phase Request (PXRQ) caused all PXRQ's not to function.If the abort bit was set in a PXRQ instruction with the IP or WA bit set, all remaining PXRQ's in the phase would stop operating correctly. Recovery from this situation required that you download the program again or to cycle power to the controller.Lgx00058678Publication 1794-RN015D-EN-E - June 20064 FlexLogix Controllers Revision 15Corrected Anomalies in Revision 15.3Revision 15.3 of FlexLogix controllers corrects these anomalies. Corrected Anomalies Description in Revision 15.3Anomaly DescriptionLarge write MSG instructions.This revision of FlexLogix firmware adds more stringent range checks when reading to orwriting from tags. Message packets are now limited to 240 bytes. This could cause someMSG instructions that worked in previous firmware revisions to not work in revision 15firmware.For example, use a CIP Generic MSG instruction to perform a Get Attribute Single service.The attribute is 4 bytes in. Assume the destination tag is an INT data type (2 bytes). Inrevision 13 firmware, the MSG instruction places the first 2 bytes of the attribute in thedestination tag. In revision 15 firmware, the MSG instruction errors because thedestination tag is not large enough. To correct this error, change the destination tag to aDINT data type.Lgx00052504The file search compare (FSC) instruction caused a nonrecoverable fault.The FSC instruction caused an nonrecoverable fault if both these conditions occurred.•A major fault was declared from within the expression of an FSC instruction.•The user fault routine cleared the fault.When the user fault routine attempted to recover, information previously saved was not properly restored, which resulted in corrupted system registers and a nonrecoverable fault.Lgx00055522Programmatic change of MSG instruction status bits could cause the MSG instruction to appear remain active (EN Set).If you programmatically reset the DN or ER bits of a MSG instruction due to the asynchronous nature of the MSG instruction, the MSG instruction could appear to remain active (EN set). In fact, the MSG instruction was not active. The MSG instruction required manual intervention to trigger it to execute again. Revision 15 removes the need for manual intervention to trigger the MSG instruction to execute again.Lgx00053112Publication 1794-RN015D-EN-E - June 2006Publication 1794-RN015D-EN-E - June 2006FlexLogix Controllers Revision 15 5An SFC instruction could execute the wrongstep.If you had an SFC instruction with nested simultaneous branches, the controller could begin execution at an unexpected step. Following the convergence of a nested simultaneousbranch, if the SFC looped back to the initial step of the parent branch, instead of executing that step, the SFC could jump to a step of another path in the nested simultaneous branch.Execution starts at Step_000. When Tran_000 becomes true, Step_001, Step_002 and Step_003 should become active. However, because the nested simultaneous branch in the left path converged and looped back to its parent step (Step_001), the active steps were actually Step_005, Step_002, and Step_003.Lgx00054247Quick power cycling or removing and reinserting local input modules could cause controller to fault When cycling power to or removing and reinserting input modules that use directconnections, a momentary window existed where the module could lose its connection to the controller and reestablish the connection, and the module connection was neverproperly closed. This only occurred on the local rails. To clear the fault, you had to power cycle the controller and redownload the program.Lgx00054979Anomaly Description6 FlexLogix Controllers Revision 15Restrictions in Revision 15.4FlexLogix controllers do not support the FLEX I/O or FLEX Ex HART modules on the local rail. They can only be used on the ControlNet network with a FLEX I/O ControlNet adapter and a FlexLogix communication card. Also, all FLEX Ex modules must be used on the local rail and cannot be used with a 1794-FLA module.If you simultaneously applied power to a 1794-VHSC and a controller, the controller might not turn on.In applications that used the 1794-L34 controller, revision 12.x or later, and a 1794-VHSC module, if the controller and I/O modules were powered up at the same time, occasionally the controller would not cycle power. In this case, the 1794-VHSC module displayed a solid red on its status indicators.In addition to using FlexLogix firmware revision 15.03, you must update your 1794-VHSC firmware to firmware revision F to correct this anomaly. You must return the 1794-VHSC module to Rockwell Automation for a firmware upgrade. The firmware cannot be upgraded in the field.Lgx00052295Anomaly DescriptionPublication 1794-RN015D-EN-E - June 2006Publication 1794-RN015D-EN-E - June 2006FlexLogix Controllers Revision 15 7Restriction in Revision 15.3Revision 15.3 of FlexLogix controllers has this restriction.Restriction Description in Revision 15.3RestrictionDescriptionIn a tag of a user-defined data type, aninstruction may write past the end of an array.If you write too much data to an array that is within a user-defined data type, some instructions write beyond the array and into other members of the tag.The following instructions write beyond the array into other members of the tag:This restriction also applies to all previous revisions.To prevent writing beyond the limits of the destination array, make sure the length operand of the instruction is less than or equal to the number of elements in the array.Lgx00033747If the length is greater than the numberof elements in the destination array……the instruction stops at the end of the array.Example 1: InstructionStops at the End of the ArrayIf the length is greater than the number of elements in the destination array……the instruction writes data beyond the end of the array into other members of the tag. Regardless of the length specified for the instruction, it stops writing if it reaches the end of the tag.Example 2: Instruction Writes Beyond the Array BSL BSR COP CPS DDTFBC FFL FFU FLL GSVLFL LFU SQL SRT SSV8 FlexLogix Controllers Revision 15Enhancements to Revision 15.3Revision 15.3 of FlexLogix controllers adds these enhancements:•The PhaseManager option provides a state model for your equipment. Itincludes:–equipment phase to run the state model.–PHASE data type.–equipment phase instructions (relay ladder and structured text only) Enhancement Descriptions to Revision 15.3•In function block diagram instructions, DeltaT for periodic timing in a periodic task now includes fractional values.If You Want To Use This InstructionSignal a phase that the state routine is complete so go to the next state Equipment Phase State Complete (PSC) Change the state or substate of a phase Equipment Phase Command (PCMD) Signal a failure for a phase Equipment Phase Failure (PFL)Clear the failure code of a phase Equipment Phase Clear Failure (PCLF) Initiate communication with RSBizWare Batch software Equipment Phase External Request (PXRQ) Clear the NewInputParameters bit of a phase Equipment Phase New Parameters (PRNP) Set up breakpoints within the logic of a phase Equipment Phase Pause (PPD)Take ownership of a phase to either:•prevent another program or RSBizWare Batch software from commandinga phase.•make sure another program or RSBizWare Batch software does notalready own a phase.Attach to Equipment Phase (PATT)Relinquish ownership of a phase Detach from Equipment Phase (PDET) Override a command Equipment Phase Override Command (POVR)Publication 1794-RN015D-EN-E - June 2006FlexLogix Controllers Revision 15 9Additional Memory Requirements Revision 15.0 or later may require more memory than previous revisions (for example, 10.x, 11.x). To estimate the additional memory that your project may require, use the following table.Estimate Additional Memory RequirementsIf You Have This Firmware Revision (add all that apply)Then Add The Following Memory Requirements to Your Project Which Comes From ThisType of Memory(1) Component Increase PerInstanceI/O(base)Data and Logic(expansion)15.x or earlier Tag that uses the COORDINATE SYSTEM data type60 bytes4 13.x or earlier Program12 bytes4Task 4 bytes4User-defined data type 4 bytes4I/O module16 bytes4(8 bytes)4 (8 bytes)Produced or consumed tag8 bytes412.x or earlier I/O module with a comm format = Rack Optimization90 bytes4I/O module with a comm format = something other thanRack Optimization (that is, direct connection)144 bytes4 Bridge module with a comm format = None160 bytes4Bridge module with a comm format = Rack Optimization220 bytes411.x or earlier User-defined data type.•Number of user-defined data types in the controllerorganizer > Data Types folder > User-defined folder•Not the use of that data type in tags128 bytes4Indirect address (using a tag as the subscript for an array inan instruction, for example, Array_A[Tag_B]). This memorychange applies only if the array:•uses a structure as its data type•does not use one of these data types: CONTROL,COUNTER, PID, or TIMER•has only one dimension (for example, UDT_1[5])(-60 bytes)410.x or earlier Program12 bytes4Routine16 bytes49.x or earlier Tag that uses the MESSAGE data type376 bytes47.x or earlier Project1050 bytes4Tag0.55 bytes4Message that transfers more than 500 bytes of data andtargets a controller in the same chassis.This memory is allocated only when the MSG instruction isenabled. To estimate, count the number of these messagesthat are enabled and/or cached at one time.2000 bytes4Publication 1794-RN015D-EN-E - June 2006Publication 1794-RN015D-EN-E - June 200610 FlexLogix Controllers Revision 15Connect Power SuppliesIf you use a 1794-PS13 power supply, connect the power supply to the controller before applying ac power to the power supply. This is also the recommended installation procedure for any third-party power supply you might use.Additional ResourcesYou can view or download publications at. To order paper copies of technical documentation, contact your local Rockwell Automation distributor or sales representative.Allen-Bradley, Rockwell Automation, FlexLogix, RSLinx Classic, RSLogix 5000, RSNetWorx for ControlNet, RSNetWorx for DeviceNet, RSNetWorx for EtherNet/IP , Logix5000, FLEX Ex, PhaseManager, RSBizWare Batch, POINT I/O, and FLEX I/O are trademarks of Rockwell Automation, Inc.Trademarks not belonging to Rockwell Automation are property of their respective companies.6.x or earlierBase tag 24 bytes 4Alias tag 16 bytes4Produced or consumed tagData type Bytes per tag DINT 412 bytes 4REAL412 bytes 43 x bytes per tag 43 x bytes per tag 46.x Routine 68 bytes 45.x or earlierRoutine116 bytes4(1)In the FlexLogix controllers, the I/O and expansion memory types are merged into a single merged pool.If You Have This Firmware Revision (add all that apply)Then Add The Following Memory Requirements to Your Project Which Comes From This Type of Memory (1)Component Increase Per Instance I/O (base)Data and Logic (expansion)FlexLogix Controllers Revision 15 11 Publication 1794-RN015D-EN-E - June 2006Publication 1794-RN015D-EN-E - June 2006 PN 953014-81Supersedes Publication 1794-RN015C-EN-E - April 2006Copyright © 2006 Rockwell Automation, Inc. All rights reserved. Printed in the U.S.A.Rockwell Automation SupportRockwell Automation provides technical information on the web to assist you in using its products. At , you can find technical manuals, a knowledge base of FAQs, technical and application notes, sample code and links to software service packs, and a MySupport feature that you can customize to make the best use of these tools.For an additional level of technical phone support for installation, configuration, and troubleshooting, we offer TechConnect Support programs. For more information, contact your local distributor or Rockwell Automation representative, or visit .Installation AssistanceIf you experience a problem with a hardware module within the first 24 hours of installation, please review the information that's contained in this manual. You can also contact a special Customer Support number for initial help in getting your module up and running.New Product Satisfaction ReturnRockwell tests all of its products to ensure that they are fully operational when shipped from the manufacturing facility. However, if your product is not functioning, it may need to be returned.United States1.440.646.3223Monday – Friday, 8am – 5pm EST Outside United States Please contact your local Rockwell Automation representative for any technical support issues.United StatesContact your distributor. You must provide a Customer Support case number (see phone number above to obtain one) to your distributor in order to complete the return process.Outside United StatesPlease contact your local Rockwell Automation representative for return procedure.。
英国微晶控制DA0405调光轨道式模块安装手册2023 - (无logo)
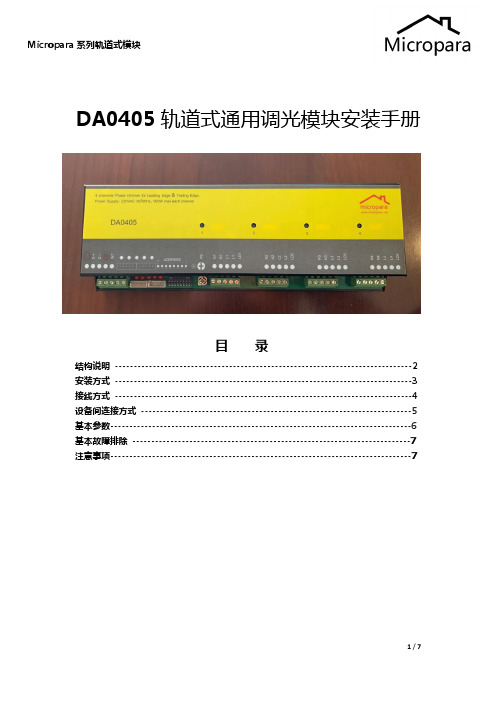
DA0405轨道式通用调光模块安装手册目录结构说明------------------------------------------------------------------------------2 安装方式------------------------------------------------------------------------------3 接线方式------------------------------------------------------------------------------4 设备间连接方式-----------------------------------------------------------------------5 基本参数-------------------------------------------------------------------------------6 基本故障排除-------------------------------------------------------------------------7 注意事项-------------------------------------------------------------------------------71. 结构说明红色: (12V 0V)对应两端子,由成套厂提供12V直流电,给模块供电白色: (D+,D-)对应两端子, 是模块的网络通讯端子,由调试人员负责白色: INT 对应端子,是报警信号输入(如:来自火灾系统的信号、应急照明信号等),强制输出亮模块的地址码,其中1-6用于模块的地址0~63, 1是低位,拨上(ON)为1,拨下为0, 二进制。
其中7-8用于输出回路合并的设置,详细咨询微晶公司模块的接地端子,与上级配电箱的接地线相连。
维尔斯韦尔 Pro Micro 40 缩放工具技术说明书
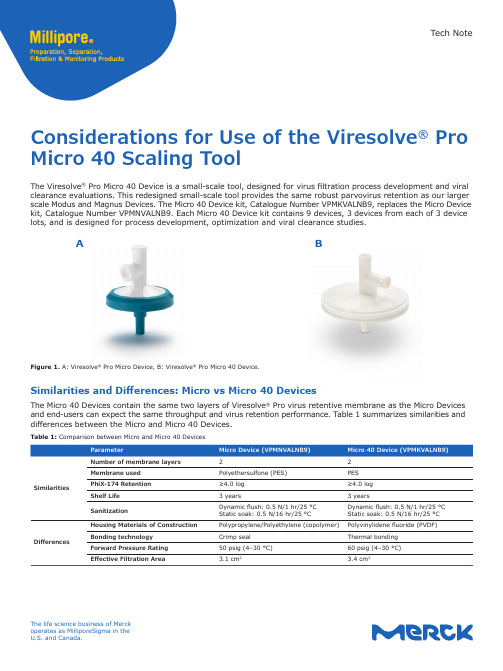
Tech NoteConsiderations for Use of the Viresolve® Pro Micro 40 Scaling ToolThe Viresolve® Pro Micro 40 Device is a small-scale tool, designed for virus filtration process development and viral clearance evaluations. This redesigned small-scale tool provides the same robust parvovirus retention as our larger scale Modus and Magnus Devices. The Micro 40 Device kit, Catalogue Number VPMKVALNB9, replaces the Micro Device kit, Catalogue Number VPMNVALNB9. Each Micro 40 Device kit contains 9 devices, 3 devices from each of 3 device lots, and is designed for process development, optimization and viral clearance studies.Figure 1. A: Viresolve® Pro Micro Device, B: Viresolve® Pro Micro 40 Device.A BSimilarities and Differences: Micro vs Micro 40 DevicesThe Micro 40 Devices contain the same two layers of Viresolve® Pro virus retentive membrane as the Micro Devices and end-users can expect the same throughput and virus retention performance. Table 1 summarizes similarities and differences between the Micro and Micro 40 Devices.Table 1: Comparison between Micro and Micro 40 DevicesParameter Micro Device (VPMNVALNB9)Micro 40 Device (VPMKVALNB9)Similarities Number of membrane layers22Membrane used Polyethersulfone (PES)PESPhiX-174 Retention ≥4.0 log≥4.0 logShelf Life 3 years 3 yearsSanitization Dynamic flush: 0.5 N/1 hr/25 °CStatic soak: 0.5 N/16 hr/25 °CDynamic flush: 0.5 N/1 hr/25 °CStatic soak: 0.5 N/16 hr/25 °CDifferences Housing Materials of Construction Polypropylene/Polyethylene (copolymer)Polyvinylidene fluoride (PVDF) Bonding technology Crimp seal Thermal bondingForward Pressure Rating 50 psig (4–30 °C)60 psig (4–30 °C)Effective Filtration Area 3.1 cm2 3.4 cm2The life science business of Merck operates as MilliporeSigma in the U.S. and Canada.The upgrade in device format results in benefits to the end-user, outlined in Table 2.Table 2: Benefits of upgrade for the end-user Housing Materials of Construction PVDF housing materials are aligned with those of Modus and Magnus Devices and enable extractable and leachable (E&L) studies at small scale.Bonding technology Thermal bonding technology in the Micro 40 Devices now matches that of larger device scales, improving robustness of virus retention under elevated pressure conditions.Forward Pressure RatingThermal bonding resulted in an increase to forward pressure specification enabling end-users to realize the benefits of higher flux and faster processing time.Throughput and Flux Performance with Micro 40 DevicesThe effective filtration area of the Micro 40 Device is 3.4 cm 2 corresponding to an increase of ~10% as compared to the Micro Device with an area of 3.1 cm 2. As the filter membrane has not changed, end-users should expect the same volumetric throughput or filter capacity from the Micro 40 Devices when normalized for filtration area. Figure 2shows the similarity in throughput and flux performance from Viresolve ®Pro Micro and Micro 40 Devices with a human IgG fluid stream.When coupled with the Viresolve ® Pro Shield or Viresolve ® Pro Shield H prefilters, the increased filtration area of the Viresolve ® Pro Micro 40 means there is no longer a 1:1 ratio between prefilter and virus filter in small-scale studies. Filter throughput is estimated during small-scale process development studies to determine throughput targets for viral clearance evaluations. Filter throughput achieved during viral clearance evaluations is then used to establish filtration area requirements for the process. In small-scale process development and clearance studies, the lower prefilter to Viresolve ® Pro Device filtration area ratio results in the prefilter being undersized and adds an additional safety factor for consideration in calculations of filtration area requirements.Virus Retention with Micro 40 DevicesAs the filter membrane is the same, the change in device format does not impact the virus retention performance. Figure 3 shows virus retention from filtrate pool samples collected from Viresolve ® Pro Micro and Micro 40 Devices challenged with PhiX-174 in an IgG solution.Figure 2. Throughput and normalized flux of Viresolve ® Pro Micro and Micro 40 Devices in an IgG fluid stream. Flux was normalized to buffer flux at 30 psi.T h r o u g h p u t (L /m 2)Time (minutes)Micro 40 Devices (n=5)Micro Devices (n=5)N o r m a l i z e d F l u x (%)Throughput (L/m 2)Micro 40 Devices (n=5)8.07.06.05.04.03.02.01.000%10%20%30%40%50%60%70%80%90%100%P h i X -174 P o o l L R VFlux Decay (J/Jo)Figure 3. PhiX-174 retention in Viresolve ® Pro Micro and Micro 40 devices.SummaryOur experience manufacturing the Viresolve ® Pro Solution enabled us to make improvements in the small-scale device manufacturing process. These improvements resulted in the Micro 40 Device which is more representative of process-scale devices while providing the same reliable throughput and viral retention performance. Key benefits include:• The materials of construction and bonding technology of small-scale devices now match the larger scale devices.• E&L studies can be performed on the small-scale device.• Forward pressure specification of the Micro 40 Devices has been increased to 60 psig, enabling validation of processes that require higher flux and lower processing times.© 2021 Merck KGaA, Darmstadt, Germany and/or its affiliates. All Rights Reserved. Merck, the vibrant M, Millipore, and Viresolve are trademarks of Merck KGaA, Darmstadt, Germany or its affiliates. All other trademarks are the property of their respective owners. Detailed information on trademarks is available via publicly accessible resources.MK_TN8481EN Ver. 1.03814312/2021 Merck KGaAFrankfurter Strasse 25064293 Darmstadt, GermanyTo place an order or receive technical assistance Please visit /contactPSFor additional information, please visit 。
罗克韦尔自动化 440R-UM007C-EN-P MSR45E 安全继电器扩展模块 用户手册说明书

MSR45E Safety Relay Extension ModuleBulletin Number 440R2Rockwell Automation Publication 440R-UM007C-EN-P - January 2023MSR45E Safety Relay Extension Module User ManualImportant User InformationRead this document and the documents listed in the additional resources section about installation, configuration, and operation of this equipment before you install, configure, operate, or maintain this product. Users are required to familiarize themselves with installation and wiring instructions in addition to requirements of all applicable codes, laws, and standards.Activities including installation, adjustments, putting into service, use, assembly, disassembly, and maintenance are required to be carried out by suitably trained personnel in accordance with applicable code of practice.If this equipment is used in a manner not specified by the manufacturer, the protection provided by the equipment may be impaired.In no event will Rockwell Automation, Inc. be responsible or liable for indirect or consequential damages resulting from the use or application of this equipment.The examples and diagrams in this manual are included solely for illustrative purposes. Because of the many variables and requirements associated with any particular installation, Rockwell Automation, Inc. cannot assume responsibility or liability for actual use based on the examples and diagrams.No patent liability is assumed by Rockwell Automation, Inc. with respect to use of information, circuits, equipment, or software described in this manual.Reproduction of the contents of this manual, in whole or in part, without written permission of Rockwell Automation, Inc., is prohibited.Throughout this manual, when necessary, we use notes to make you aware of safety considerations.These labels may also be on or inside the equipment to provide specific precautions.The following icon may appear in the text of this document.WARNING: Identifies information about practices or circumstances that can cause an explosion in a hazardous environment, which may lead to personal injury or death, property damage, or economic loss.ATTENTION: Identifies information about practices or circumstances that can lead to personal injury or death, property damage, or economic loss. Attentions help you identify a hazard, avoid a hazard, and recognize the consequence.IMPORTANT Identifies information that is critical for successful application and understanding of the product.SHOCK HAZARD: Labels may be on or inside the equipment, for example, a drive or motor, to alert people that dangerous voltage may be present.BURN HAZARD: Labels may be on or inside the equipment, for example, a drive or motor, to alert people that surfaces may reach dangerous temperatures.ARC FLASH HAZARD: Labels may be on or inside the equipment, for example, a motor control center, to alert people to potential Arc Flash. Arc Flash will cause severe injury or death. Wear proper Personal Protective Equipment (PPE). Follow ALL Regulatory requirements for safe work practices and for Personal Protective Equipment (PPE).Identifies information that is useful and can help to make a process easier to do or easier to understand.Table of ContentsAbout This Publication . . . . . . . . . . . . . . . . . . . . . . . . . . . . . . . . . . . . . . . . . . . 5Summary of Changes. . . . . . . . . . . . . . . . . . . . . . . . . . . . . . . . . . . . . . . . . . . . . 5Additional Resources. . . . . . . . . . . . . . . . . . . . . . . . . . . . . . . . . . . . . . . . . . . . . 5Chapter 1Introduction General Description. . . . . . . . . . . . . . . . . . . . . . . . . . . . . . . . . . . . . . . . . . . . . . 7Special Features . . . . . . . . . . . . . . . . . . . . . . . . . . . . . . . . . . . . . . . . . . . . . . . . . 7Typical Applications. . . . . . . . . . . . . . . . . . . . . . . . . . . . . . . . . . . . . . . . . . . . . . 8Application Restrictions. . . . . . . . . . . . . . . . . . . . . . . . . . . . . . . . . . . . . . . 8Chapter 2System Configuration Terminal Connection Diagrams . . . . . . . . . . . . . . . . . . . . . . . . . . . . . . . . . . . 9Connecting Hardware. . . . . . . . . . . . . . . . . . . . . . . . . . . . . . . . . . . . . . . . . . . 10Status Indicator Display Elements. . . . . . . . . . . . . . . . . . . . . . . . . . . . . . . . 11Arc-limiting Graphs. . . . . . . . . . . . . . . . . . . . . . . . . . . . . . . . . . . . . . . . . . . . . 11Chapter 3Maintenance Service. . . . . . . . . . . . . . . . . . . . . . . . . . . . . . . . . . . . . . . . . . . . . . . . . . . . . . . . . 13Inspection. . . . . . . . . . . . . . . . . . . . . . . . . . . . . . . . . . . . . . . . . . . . . . . . . . . . . . 13Decommission. . . . . . . . . . . . . . . . . . . . . . . . . . . . . . . . . . . . . . . . . . . . . . . . . . 13Appendix ASpecifications Technical Specifications . . . . . . . . . . . . . . . . . . . . . . . . . . . . . . . . . . . . . . . . . 15Catalog Numbers . . . . . . . . . . . . . . . . . . . . . . . . . . . . . . . . . . . . . . . . . . . . . . . 16Product Labels. . . . . . . . . . . . . . . . . . . . . . . . . . . . . . . . . . . . . . . . . . . . . . . . . . 17Approximate Dimensions. . . . . . . . . . . . . . . . . . . . . . . . . . . . . . . . . . . . . . . . 17Declaration of Conformity . . . . . . . . . . . . . . . . . . . . . . . . . . . . . . . . . . . . . . . 17CE Conformity . . . . . . . . . . . . . . . . . . . . . . . . . . . . . . . . . . . . . . . . . . . . . . 17UKCA Conformity . . . . . . . . . . . . . . . . . . . . . . . . . . . . . . . . . . . . . . . . . . . 18Appendix BAccessories Additional Components . . . . . . . . . . . . . . . . . . . . . . . . . . . . . . . . . . . . . . . . . 19Rockwell Automation Publication 440R-UM007C-EN-P - January 20233Table of Contents4Rockwell Automation Publication 440R-UM007C-EN-P - January 2023Rockwell Automation Publication 440R-UM007C-EN-P - January 20235PrefaceAbout This Publication This manual covers the connection and configuration of the Guardmaster® MSR45E Safety Relay Extension Module.Summary of Changes This publication contains the following new or updated information. This list includes substantive updates only and is not intended to reflect all changes.Additional ResourcesThese documents contain additional information concerning related products from Rockwell Automation.You can view or download publications at rok.auto/literature.ATTENTION: MSR42 safety module, MSR41 safety module, or MSR45E extension module units can only achieve their function as a safety controller module if the instructions and additional documentation that are given in this instruction manual are exactly followed. You must also consult the valid laws and regulations at the time of installation. Serious injury or death can occur if you do not follow these instructions carefully. The installer or system integrator is fully responsible for a safe integration of this product. Use this instruction manual with the MSR42 safety module, MSR41 safety module, or MSR45E extension module. This instruction must be accessible together with the other machine documentation during its entire lifecycle for all personnel responsible for assembly, installation, operation, and maintenance.TopicPage Corrected Figure 812Updated Figure 917Updated Declaration of Conformity 17Resource DescriptionSystem Security Design Guidelines Reference Manual, SECURE-RM001Provides guidance on how to conduct security assessments, implement Rockwell Automation products in a secure system, harden the control system, manage user access, and dispose of equipment.UL Standards Listing for Industrial Control Products, publication CMPNTS-SR002Assists original equipment manufacturers (OEMs) with construction of panels, to help confirm that they conform to the requirements of Underwriters Laboratories.Industrial Components Preventive Maintenance, Enclosures, and Contact Ratings Specifications, publication IC-TD002Provides a quick reference tool for Allen-Bradley industrial automation controls and assemblies.Safety Guidelines for the Application, Installation, and Maintenance of Solid-state Control, publication SGI-1.1Designed to harmonize with NEMA Standards Publication No. ICS 1.1-1987 and provides general guidelines for the application, installation, and maintenance of solid-state control in the form of individual devices or packaged assemblies incorporating solid-state components.Industrial Automation Wiring and Grounding Guidelines, publication 1770-4.1Provides general guidelines for installing a Rockwell Automation industrial system.Product Certifications website, rok.auto/certifications .Provides declarations of conformity, certificates, and other certification details.PrefaceNotes:6Rockwell Automation Publication 440R-UM007C-EN-P - January 2023Rockwell Automation Publication 440R-UM007C-EN-P - January 20237Chapter 1Introduction General DescriptionThe MSR4x is a family of compact safety control modules. This main controlling module allows the connection and the control of the compact Allen-Bradley® GuardShield™ Micro400 Safety Light Curtain systems. Depending on the configuration, other safety components can also be connected and monitored simultaneously.Figure 1 - MSR42 Safety Module and Safety Components The MSR41 safety module or MSR42 safety module offer two safety PNP outputs (OSSD). Additional safety relay extension modules can be applied for applications that require more outputs (MSR41 safety modules or MSR42 safety modules) and/or dry contacts (MSR45E extension modules) to switch loads. You can daisy-chain up to three extension modules, which the base module controls.We also offer models in special configurations, which are described in Terminal Connection Diagrams on page 9.Special Features The characteristics of the MSR41 safety module and MSR42 safety module:•Category 4, PLe according to EN ISO 13849-1•Type 4 according to EN 61496-1/-2•SIL 3 according to IEC 61508•SIL CL 3 according to EN 62061•Short response timesIMPORTANT The MSR45E extension module is not a standalone safety relay module. You can only use the unit with either an MSR41 safety module or MSR42 safety module.Safety Light Curtain Main Safety ModuleExtension ModuleChapter 1 Introduction•Up to three extension modules per main safety module•Adjustable stop delay time•Different safety components suitable for connection (MSR42 safetymodule only)Typical Applications Typical MSR41 and MSR42 safety module applications are:•Presses•Robotic cells with automatic insertion•Assembly lines•Indexing tables•Conveyor systems•Automatic storage facilitiesApplication RestrictionsMSR4x modules are not intended for application in explosive (EX) or inradioactive environments.8Rockwell Automation Publication 440R-UM007C-EN-P - January 2023Chapter 2 System ConfigurationTerminal Connection DiagramsFigure2…Figure4 on page10 show the safety output contact configuration of the available MSR45E extension modules. The control and expansion module housings snap together. Use a ribbon cable to electronically link the devices.Figure 2 - MSR45E Extension Module (Cat. No. 440-P4NANS)Figure 3 - MSR45E (3C 3NO) Extension Module (Cat. No. 445L-104860)Rockwell Automation Publication 440R-UM007C-EN-P - January 2023910Rockwell Automation Publication 440R-UM007C-EN-P - January 2023Chapter 2 System Configuration Figure 4 - MSR45E (3C 2NO 1NC) Extension Module (Cat. No. 445L-105938)Connecting HardwareFigure 5 and Figure 6 on page 11 show a main module and extension modules.Figure 5 - Ribbon Cable for One Extension Module ATTENTION: Only use the normally closed contacts (NC) of an extension module for status feedback from the machine controller. NC contacts cannot be used for any safety function. Integration with the safety circuit of a machine is not allowed.!Cat. No. 440R-ACABL1Chapter 2 System ConfigurationFigure 6 - Ribbon Cable for Two Extension ModulesStatus Indicator Display ElementsTable 1 shows information about the two final switching device (FSD) status indicators that are integrated into the MSR45E extension module.Arc-limiting GraphsFigure 7 and Figure 8 on page 12 show arc-limiting graphs and lifespan curves for MSR45E extension modules with secure-off switching, no standing arc, and a maximum of one operating cycle. Each figure is a set of characteristic curves for DC and AC applications.Figure 7 - 2C Relay Expansion ModuleCat. No. 440R-ACABL2Table 1 - Status Indicator DescriptionColor StatusGreen Corresponding contacts of the module are closed (active)Red Corresponding contacts of the module are opened (not active, NC contact)OffNo power at the main module or no internal bus (no ribbon cable connection)Arc-limiting Graph (DC)Electrical Service LifeVoltage (DC)Switching Current (A)C u r r e n t (A )S w i t c h i n g C y c l e s x 10001 = Inductive Load L/R = 40 ms2 = Resistive LoadChapter 2 System ConfigurationFigure 8 - 3C Relay Expansion ModuleArc-limiting Graph (DC)Electrical Service LifeVoltage (DC)Switching Current (A)C u r r e n t (A )S w i t c h i n g C y c l e s x 10001 = Inductive Load L/R = 40 ms2 = Resistive LoadChapter 3MaintenanceService MSR45E extension modules have no serviceable components. Inspection Qualified and trained personnel must periodically test the MSR45E extensionmodule, in accordance with valid regulations, to discover prohibitedmanipulations or unauthorized modifications.Decommission Only remove the MSR45E extension module when the machine or theequipment is shut down completely and can no longer operate without tools.Dismantle a controller if disposal is necessary. The separated materials can berecycled according to state-of-the-art technology and the correspondingregulations of the country where the unit is used.Chapter 3 Maintenance Notes:Appendix ASpecificationsTechnical SpecificationsTable 2 - Technical SpecificationsAttribute ValueProbability of a dangerous failure per hour PFH 6.0 E-9 1/h: MSR42 safety module, MSR45E extension module, and Micro400 safety light curtain9.0 E-10 1/h: MSR42 safety module and MSR41 safety module3.0 E-10 1/h: MSR45E extension module4.0 E-9 1/h: Micro400 safety light curtainPerformance Level PL PLe, Cat. 4 (EN ISO 13849-1) Safety Integrity Level SIL CL 3 (IEC 61508/IEC 62061)Approvals CE Marked for all applicable EU directives, UKCA marked for all applicable regulations, cULus Listed, TÜV Certifiedrok.auto/certificationsGeneralNominal working mode Continuous processTemperature •Environmental: 0…55 °C (32…131 °F)•Operating: 0…55 °C (32…131 °F)•Storage: -25…+70 °C (-13…+158 °F)Enclosure rating (EN 60529)•Housing:IP20•Terminals: IP20Conductor connection, max 6-pin, terminal stripWire cross section: 2.5 mm2 (14 AWG) stranded, spring clamping technology, Minimum 12 mm (0.47 in.) ferrule or wire lengthMounting Quick mount: 35 mm (1.38 in.) top hat rail (EN 50022)Weight Net: 150 g (0.33 lb)Housing dimensions 111 mm x 22.5 mm x 125 mm (4.37 in. x 0.89 in. x 4.92 in.) (including plugs), seeApproximate Dimensions on page17Housing material PolyamideVibration (EN60068-2-6)•Amplitude: 0.35 mm (0.1 in.)•Frequency: 10…55 HzShock resistant (EN 60068-2-29)•Acceleration: 100 ms-2•Impulse length: 16 ms•Number of shocks: 1000 per directionInstallation position No restrictionsShippingPackaging 280 mm x 200 mm x 70 mm (11.02 in. x 7.87 in. x 2.76 in.) Shipping weight Net + 220 g (8.66 in.)OutputsNumber of expansion modules, max 3 per main moduleNumber of contacts 2NO, 3NO, or 2NO/1NCAdditional response time t(em) withU N Protective mode, max≤ 6 msContact type Force guided relay (EN 50205)Contact material AgSN02 + 0.2 µm AU platedSwitching capacity •Min: 0.06VA•Max: 250V AC 8 A, [AC1] = 2000VA•DC 13 (EN 60947-5-1, 0.1 Hz, 24V): 6 A DC/24 V •AC 15 (EN 60947-5-1, 0.1 Hz, 220V):–2NO: 3 A AC/230V–3NO or 2NO/1NC: 3 A AC/120V •Allowed 2C or 3C: 900 switching /h, maxAppendix A SpecificationsCatalog Numbers Switching current•Min: 10 mA•Max8ASwitching voltage, max•2NO:AC250V;DC300V•3NO or 2NO/1NC: AC 120V; DC 170VOutput nominal voltage DC: See Arc-limiting Graphs on page112C•Continuous current I th: 8 A (1 contact)•With simultaneous switching (1 extension module): 6 A (≥ 2 contacts)•With simultaneous switching (2 or more extension modules): 4 A (≥ 2 contacts)Switching capacity According to DC 13 (EN 60947-5-1, 0.1 Hz, 24V)6 A DC/24 VElectronic lifespanAccording to AC 15 at 2 A, 230V AC2C or 3C: 105 operating cycles (EN 60947-5-1),see Arc-limiting Graphs on page11Mechanical lifespan 106Switch on delay after switching on the powersupply< 3 sSwitch off delay after switching off the powersupply< 40 msTable 2 - Technical Specifications (Continued)AttributeValueTable 3 - Catalog NumbersCat. No. (1)(1)All series.Description440R-P221AGSMSR41 On/Off Safety Module•Mounting: 35 mm (1.34 in.) DIN Rail•Size: 22.5 mm (0.98 in.)440R-P226AGS-NNR MSR42 Start/Restart Safety Module•Mounting: 35 mm (1.34 in.) DIN Rail•Size: 22.5 mm (0.98 in.)445L-104794-B xxx (2)(2)x = Customer configurable options that do not impact the standards or directives cited in Declaration of Conformity onpage17.440-P4NANS MSR45E 2C Safety Relay Extension Module (optional)•Input voltage: Supplied by MSR41 safety module or MSR42 safety module•Reset: Determined by MSR41 safety module or MSR42 safety module•Outputs:Two NO445L-1xxxx (2)Appendix A SpecificationsProduct LabelsThe necessary safety information is on the product label, which is on every MSR45E extension module.Figure 9 - Example Product LabelApproximate DimensionsFigure 10 - MSR42 Safety Module and MSR45E Extension Module [mm (in.)]Declaration of ConformityCE ConformityRockwell Automation declares that the products that are shown in this document conform with the Essential Health and Safety Requirements (EHSRs) of the European Machinery Directive (2006/42/EC) and the EMC Directive (2014/30/EU).•EN 61496-1:2012 Safety of machinery – Electro-sensitive protective equipment – Part 1: General requirements and tests•IEC 61496-2:2013 Safety of machinery – Electro-sensitive protectiveequipment – Part 2: Particular requirements for equipment using active opto-electronic protective devices (AOPDs)•EN ISO 13849-1:2015 Safety of machinery – Safety-related parts of control systems – Part 1: General principles for design•EN 61508 Parts 1-7:2010 Functional safety of electrical/electronic/programmable electronic safety-related systems111(4.37)95(3.74)110(4.33)125(4.92)22.5(0.86)Appendix A Specifications•EN 954-1:1997 Safety of machinery – Safety-related parts of controlsystems – Part 1: General principles for design•EN 50178:1997 Electronic equipment for use in power installations•EN 62061:2005 Safety of machinery – Functional safety of safety-relatedelectrical, electronic, and programmable electronic control systems•EN 60204-1:2006 Safety of machinery – Electrical equipment of machines– General requirements•EN 61000-6-4:2007 Electromagnetic compatibility (EMC) – Part 6-4:Generic standards – Emission standard for industrial environments(Class A)•EN 61000-6-2:2005 Electromagnetic Compatibility (EMC) – Part 6-2:Generic standards – Immunity for industrial environmentsFor a comprehensive CE certificate visit: rok.auto/certifications.UKCA ConformityRockwell Automation declares that the products that are shown in thisdocument are in compliance with the Supply of Machinery (Safety)Regulations (2008 No. 1597) and Electromagnetic Compatibility Regulations(2016 No. 1091).•EN 61496-1:2013 Safety of machinery – Electro-sensitive protectiveequipment – Part 1: General requirements and tests•IEC 61496-2:2013 Safety of machinery – Electro-sensitive protectiveequipment – Part 2:•Particular requirements for equipment using active opto-electronicprotective devices (AOPDs)•EN ISO 13849-1:2015 Safety of machinery – Safety-related parts of controlsystems – Part 1: General principles for design•EN 61508 Parts 1-7:2010 Functional safety of electrical/electronic/programmable electronic safety-related systems•EN 62061:2005 Safety of machinery – Functional safety of safety-relatedelectrical, electronic, and programmable electronic control systems•EN 60204-1:2006 Safety of machinery – Electrical equipment of machines– General requirements•EN 61000-6-4:2007 Electromagnetic compatibility (EMC) – Part 6-4:Generic standards – Emission standard for industrial environments(Class A)•EN 61000-6-2:2005 Electromagnetic Compatibility (EMC) – Part 6-2:Generic standards – Immunity for industrial environmentsFor a comprehensive UKCA certificate visit: rok.auto/certifications.Appendix BAccessoriesAdditional ComponentsTable 4 - Catalog NumbersCat. No. Description440R-ACABL1 Ribbon cable – two modules440R-ACABL2 Ribbon cable – three modules440R-ACABL3 Ribbon cable – four modules440R-ATERM1P Terminal block kit for MSR41 safety module replacement440R-ATERM2P Terminal block kit for MSR42 safety module replacement440R-ATERM2C Terminal block kit for MSR45E extension moduleAppendix B Accessories Notes:Appendix B Accessories Notes:Rockwell Automation Publication 440R-UM007C-EN-P - January 202321Appendix B AccessoriesNotes:22Rockwell Automation Publication 440R-UM007C-EN-P - January 2023MSR45E Safety Relay Extension Module User Manual Rockwell Automation Publication 440R-UM007C-EN-P - January 202323CSA 107 179Publication 440R-UM007C-EN-P - January 202310000172479 Ver 03Supersedes Publication 440R-UM007B-EN-P - August 2022 Copyright © 2023 Rockwell Automation, Inc. All rights reserved. Printed in the U.S.A.Rockwell Automation SupportUse these resources to access support information.Documentation FeedbackYour comments help us serve your documentation needs better. If you have any suggestions on how to improve our content, complete the form at rok.auto/docfeedback .Waste Electrical and Electronic Equipment (WEEE)Rockwell Automation maintains current product environmental compliance information on its website at rok.auto/pec .Technical Support Center Find help with how-to videos, FAQs, chat, user forums, and product notification updates.rok.auto/support KnowledgebaseAccess Knowledgebase articles.rok.auto/knowledgebase Local Technical Support Phone NumbersLocate the telephone number for your country.rok.auto/phonesupport Literature LibraryFind installation instructions, manuals, brochures, and technical data publications.rok.auto/literature Product Compatibility and Download Center (PCDC)Download firmware, associated files (such as AOP, EDS, and DTM), and access product release notes.rok.auto/pcdcAt the end of life, this equipment should be collected separately from any unsorted municipal waste.Rockwell Otomasyon Ticaret A.Ş. Kar Plaza İş Merkezi E Blok Kat:6 34752, İçerenköy, İstanbul, Tel: +90 (216) 5698400 EEE Yönetmeliğine UygundurAllen-Bradley, expanding human possibility, GuardMaster, Guardshield, and Rockwell Automation are trademarks of Rockwell Automation, Inc.Trademarks not belonging to Rockwell Automation are property of their respective companies.。
- 1、下载文档前请自行甄别文档内容的完整性,平台不提供额外的编辑、内容补充、找答案等附加服务。
- 2、"仅部分预览"的文档,不可在线预览部分如存在完整性等问题,可反馈申请退款(可完整预览的文档不适用该条件!)。
- 3、如文档侵犯您的权益,请联系客服反馈,我们会尽快为您处理(人工客服工作时间:9:00-18:30)。
• •
支持USB 2.0 FS OTG 支持LPM USB 2.0 FS Device
•
可调整电压外设
• • • •
系统时钟错误检测 双看门狗 内存奇偶检查(SRAM parity check) 硬件循环冗余校验(CRC)
•
PWM内含144 MHz的快速电机控制 定时器, 分辨率 < 7ns
16
M451系列框图
M452 特色 CortexR-M4 支持 USB OTG之微控制器
• • • 72MHz /90 DMIPS 内存 zero-wait state 带FPU、DSP、MPU
• • • 2.5V ~ 5.5V 宽工作电压 -40℃ ~ +105 ℃宽工作温度 高抗干扰, ESD8KV, EFT 4KV
ARM Cortex® _M4
(DSP & FPU)
LDROM 4 KB (Mask ROM 16 KB) 数据闪存共享APROM 内存 32/16 KB (16/8 KB带奇偶较验)
PDMA
12/8-ch
72 MHz
USB LDO 3.3V
Bridge
AHB Bus APB Bus
时钟控制
HS Osc. 22.1184 MHz PLL
罗盘校准 3轴全回转 软磁干扰与硬磁干扰消除 1.5度的精确度 Gyro 校准 Gyro 中心校准 (drift cancel) Gyro 比例校准. 2 度/每小时精密度
校准工具
校准工具
ACC 校准 快速方式 (Z轴即可) 全面方式 (六轴皆校准) 罗盘校准 User Free Rotation Sample points display Calibration quality indicator
稳定飞控系统
ESC 1~4
UART
B.T. module
PWM
Motor Driver
Parameters
SSV RC
PID Control
Stabilizer
RC Driver Sensor Driver
SPI Sensors
I2C
Euler Angle
Sensor DataFra bibliotekApplication Interface Nuvoton AHRS Core Sensor Calibration 10 DOF Sensor Fusion Quaternion 400Hz
新唐飞控系统
Nuvoton M452
Nuvoton N79E814
SSV 2.4G RF
新唐飞控系统
ESC0 ESC1 ESC2 ESC3 SSV 2.4GRF
PWM
SSV 2.4GRF SPI
51
ADC
M4
SPI
I2C
ACC
GYRO
MAG
BARO
Stick/Butto n
新唐飞控系统
新唐 N79E814 .(51 基础上) SSV 2.4G 射频. 0 dBm. (1mW) 250Kbps 位传输. 支持美国手控制方式(mode 2/3) 支持4通道微调. 片上参数存贮. 2 按键方式切换 空旷地带控制距离可达100米.
稳定飞控系统
10 轴传感器融合. 基于四元数姿态稳定系统演算法. 支持 2 阶 PID 控制. 支持传感器校准. 超过 400Hz AHRS Refresh Rate. 陀螺仪增稳.
存贮器
APROM 256/128/72/40 KB
电源控制
LDO 1.8V POR, LVR, BOR VREF 2.048V/2.56V/
3.072V/4.096V
定时器/ PWM
32-bit 定时器X 4 RTC (VBAT) 双看门狗 PWM 144MHz,12 通道
模拟接口
12位 ADC 16通道 12位 DAC 比较器 X 2 USB PHY
N78E814A 特色 用于遥控器
1. 2. 3. 4. 5. 6. 7. 增强型8位51微控制器 (4T 方式) 内嵌8K EPROM , 256 Byte RAM TSSOP28 / TSSOP20 / SOP20 /SOP16 Package PWM up to 4 channel 10-bit ADC up to 8 channel Internal RC 22.1184MHz SPI X 1 , I2C X 1
USB 2.0 OTG/Device
*框图中(4+1) 含意是4 UART + ISO-7816 UART Flash 256/128 KB 型号支持Touch key
M452 特色 用于飞控板
1. 2. 3. 4. 5. 6. 7. 8. CPU Speed up to 72Mhz DSP , FPU MASK ROM for USB ISP ROM / RAM up to 256K/16K PWM up to 12 channel 12-bit ADC up to 16 channel Internal RC 22.1184MHz UART X 4 , SPI X 3 , I2C X 2 , USB 2.0 OTG/ Device 9. 连接 GPS , 2.4G RF , 9 轴感应器 , 压力感应 器 , 红外感应器 , 超声波感应器 10.
PID 控制工具
PID 控制工具
2 阶 PID 控制 Level PID Roll Pitch Yaw Rate PID Roll Pitch Yaw 定高 PID 控制
传感器校准
ACC 校准 快速 Z 校准 全面校准 (6 个方向) 1度的精确度
新唐 32 bit cortex-M4 微控器. 支持高速 ESC(400Hz). 支持 Quad-X 250mm frame. 支持 SSV 2.4G 射频接收发射器 . 支持低电池侦测. 支持低 R.C 信号侦测. 支持片上Flash(自校参数). 支持飞行动态 PID 调适.
2.4G RC Transceiver System
连接性 / GPIO
通用I/O SPI X 3/2 I2S X 2/1
连接性
串口 X (4+1)* I2C X 2 Touch Key x 16*
LS Osc. 10 kHz
时钟监控
外扩总线接口
CAN VAI
外部高速晶振 4~24 MHz
外部低速晶振 32.768 kHz
外部中断
ISO-7816-3