918080-Advanced Placement Program -Intro to 2nd FTC
6181 X危险地点工业计算机系列说明书

6181X Hazardous Location Industrial ComputersIndustrial computers with extreme designThe Allen-Bradley® 6181X line of industrial computers compliments theRockwell Automation® XT extreme environment system portfolio with theability not only to operate efficiently in hazardous locations but actuallyimprove the working experience for operators in these harsh environments.Features shared by all models:Additional Projected Capacitive (PCAP) features available:The latest 6181X model features an integrated display with PCAP multi-touchfunctionality, delivering the familiar experience of a simple and responsivesmartphone screen. Plus, added functionality for hazardous locations:• Intel Dual Core i3, 2.1 GHzprocessor• 8 GB RAM (16 GB System Max)• 128 GB solid-state hard drive• Windows 7* or Windows 10operating system• 2 Gigabit Ethernet ports• Display port and DVI-D port• External CompactFlash Type II cardslot (supports up to 16 GB)• Dry to damp screen operation• Multi-touch settings for thick or thin gloves• Sunlight readable (1300-nit LCD display)• ThinManager Compatible PlusDesigned for extreme environments and hazardous locations6181X Integrated Display, resistive touch6181X Integrated Display,PCAP multi-touch6181X Integrated Display with addedsun shield accessory (sold seperately)6181X Non-Display*Windows 7 operating system not available in PCAP modelFirst, choose your preferred set-up. Choose a non-display computer to build a two-piece solution. Or choose one of our 12-inch touch screen integrated display models for an integrated experience. Computers can be mounted in the same enclosure with a Logix-XT Controller without requiring additional heating or cooling equipment.For integrated display solutions, you may choose a resistive touch screen or a more intuitive, advanced projected capacitive (PCAP) model.Finally, add accessories. Sun shield attachments offer added protection from UV and infrared radiation. PC riser cards add versatility. For added flexibility in the field, memory, CompactFlash drives, and solid-state drives (SSD) can be easily upgraded.Industries and applicationsHeat, cold, dust and hazardous gas challenge equipment and - even worse - threaten production. Our 6181X computers are suited for high performance under these conditions, especially necessary in these industries: Flexible optionsSpecifications➊➋➌➍➎➏➐➑➒➓• Chemical and Pharmaceutical • Energy and Power Generation • Mining and Metals• Water and Wastewater • Oil and GasHazardous location certifications and ratingsAllen-Bradley, Rockwell Automation and Rockwell Software are trademarks of Rockwell Automation, Inc.Trademarks not belonging to Rockwell Automation are property of their respective companies.Publication 6181X-PP001F-EN-P – April 2020 | Copyright © 2020 Rockwell Automation, Inc. All Rights Reserved. Printed in USA.。
Red Hat Enterprise Linux 8.6 Supplement for Gen9.0

Legal and notice information© Copyright 2015- 2017 Hewlett Packard Enterprise Development LP Document H istory:Released DescriptionJune 2022 Final VersionTable of ContentsOverview (4)Update recommendation (4)Alignment (4)Summary of Changes (4)Important Notes (4)Release Summary (4)Prerequisites (5)Running SUM on Linux (5)Deployment Instructions (6)Component Release Notes (6)Content Notes (8)RHEL8.6 Supplement for Gen9 SPP Contents (8)OverviewA Service Pack for ProLiant (SPP) Supplement is a software bundle. It may include support for anew operating system update excluded in SPP but functions with the SPP components. TheSupplement will provide support for functionality that is required outside a normal SPP release cycle allowing HPE to deliver support, so customers do not have to wait on a complete SPP’s availability.Each SPP Supplement’s version number will match the version of its corresponding SPP.Supplement Release Notes will be available and will include information on the components in thebundle. If the Supplement’s contents include Linux components, the components will also beavailable on the Linux Software Delivery Repository (SDR).Once released, the functionality of the SPP Supplement contents is included in the next availableSPP.Hot Fixes associated with an SPP may work with an SPP Supplement. Please review the Hot Fix to verify if it has support for the operating system that is supported in the Supplement. For moreinformation on SPP Hot Fixes, please see the SPP Release Notes located on the SPP InformationLibrary page.This is the Red Hat Enterprise Linux (RHEL) 8.6 Supplement for Gen9.0 Post Production ServicePack for ProLiant 2022.03.0.For more information on which servers are supported with RHEL 8.6, please visit our OS SupportSite at: SPP OS Support Guide.RHEL8.6 Supplement for Gen9.0 SPP version 2022.03.0 Bundle containing software components Filename: supspp-2022.03.rhel8.6.en.tar.gzUpdate recommendationOptional - Users should update to this version if their system is affected by one of the documented fixes or if there is a desire to utilize any of the enhanced functionality provided by this version.AlignmentGen9 Service Pack for ProLiant 2022.03.0Summary of ChangesImportant NotesWhen the terms, Supplement, Service Pack for ProLiant or SPP are used throughout this document,they refer to all the deliverables in the Table in the Overview Section unless explicitly stated.Before deploying any components to a system, be sure that a recent backup of the system isavailable in the event the deployment procedure fails.Release SummaryThe summary of this Red Hat Enterprise Linux (RHEL) 8.6 Supplement for Service Pack for ProLiantrelease is:Added support for Red Hat Enterprise Linux 8.5This Supplement corresponds with SPP 2022.03.0. Drivers either found in SPP 2022.03.0 or deliveredwith the RHEL 8.4 distribution can be used.However, the drivers found in the initial release (SPP2022.03.0) may not contain all the HPE value added features that are available in the Supplement. These features will be added in a future SPP release.All components delivered in this Supplement to the Service Pack for ProLiant (SPP) are tested together and meet the dependencies of the other components in the Service Pack for ProLiant.Systems using software and firmware components delivered with the following products should be able to easily migrate to the components in this supplement:Service Pack for ProLiant 2022.03.02021.10.02021.05.02020.09.2Note: The users may see the “thawing” state in the systemd message console because the systemd doesn’t set the default value correctly, especially after a restart or reload services.PrerequisitesRunning SUM on LinuxBefore deploying software updates on a target system, be sure that a recent backup of the target system is available in the event the deployment procedure fails.To successfully deploy SUM on remote target systems based on a Linux operating system, the following must be available:•libcrypt.so•libcrypt.so.1•/usr/lib/libqlsdm.so•/usr/lib64/libqlsdm-x86_64.so•/lib/cim/libqlsdm.so•/usr/lib/libemsdm.so•/usr/lib64/libemsdm.so•/lib/cim/libemsdm.so•/usr/lib/bfahbaapi.so•/usr/lib64/bfahbaapi.so•/lib/cim/bfahbaapi.so•linux-vdso.so.1•/lib64/libcrypt.so.1•/lib64/libpthread.so.0•/lib64/libz.so.1•/lib64/libdl.so.2•/lib64/librt.so.1•/usr/lib64/libstdc++.so.6•/lib64/libm.so.6•/lib64/libgcc_s.so.1•/lib64/libc.so.6•/ lib64/ld-linux-x86-64.so.2Deployment InstructionsThe Supplement is designed for use after the operating system is installed. This enables the updating ofdrivers, and the installation of HPE utilities (such as Health and iLO drivers), and agents (Server, NIC,and Storage).Using the SPP Supplement and its corresponding SPP on a supported Linux operating system. Enablesthe choice of either standard Linux installation tools (YUM/Zypper) or HPE management tools(SUM/OneView) to do the following:•Use the software and firmware provided in the Supplement and the SPP.•Use the firmware provided in the SPP and get the software from the Software DeliveryRepository at https:///SDR.•Use the firmware and software utilities provided in the SPP and get the drivers from the operating system distro.When appropriate for any given deployment, components can be combined into a single ISO using SUMcustom baseline or applied as separate packages.To upload selected components to the iLO Repository and create an install set, select Save Components as an Install set on iLO Repository. SUM automatically creates a default name and description, but you can edit the name and description for the install set. You can use this install set to roll back the server components at a future time. The name and description are limited to 63 characters, and the only special charactersallowed are - and _.Component Release NotesDriver - Storage ControllerSoftware - System ManagementDriver - Storage Controller Top HPE ProLiant Smart Array Controller (64-bit) Driver for Red Hat Enterprise Linux 8 (64-bit)Version: 3.4.20-211(Recommended)Filename: kmod-hpsa-3.4.20-211.rhel8u4.x86_psig; kmod-hpsa-3.4.20-211.rhel8u4.x86_64.rpm; kmod-hpsa-3.4.20-211.rhel8u5.x86_psig; kmod-hpsa-3.4.20-211.rhel8u5.x86_64.rpmEnhancementsAdded RHEL8.5 supportSoftware - System Management Top HPE ProLiant Agentless Management Service for Red Hat Enterprise Linux 8 ServerVersion: 2.10.5(Optional)Filename: hp-ams-2.10.5-888.1.rhel8.x86_psig; hp-ams-2.10.5-888.1.rhel8.x86_64.rpmPrerequisiteso hp-ams supported on HPE ProLiant Gen8 and Gen9 Servers.o hp-ams provides information to the HPE iLO 4 service providing SNMP support.o SNMP PASS-THRU on the HPE iLO 4 MUST be disabled, and SNMP should be configured on the HPE iLO 4. The HPE iLO 4 may need to be reset after changing these settings.o Requirements:▪Minimum HPE iLO 4 Firmware Version = 1.05▪Minimum supported OS Versions = Red Hat Enterprise Linux 5.6, Red Hat Enterprise Linux 6.0,SuSE Linux Enterprise Server 10 SP4, SuSE Linux Enterprise Server 11 SP1FixesFixed the following items:o Addressed issue where the NIC port status or IML record when NIC port link status changes from "Unknown"to "OK". Updated the SNMP trap to make iLO/IML record the correct link port status.HPE SNMP Agents for Red Hat Enterprise Linux 8 ServerVersion: 10.9.4(Optional)Filename: hp-snmp-agents-10.94-689.8.rhel8.x86_psig; hp-snmp-agents-10.94-689.8.rhel8.x86_64.rpm PrerequisitesThe hp-health and hp-snmp-agents run as 32 bit applications in the x86_64 environment. The Linux kernel 32 bit compatibility must be enabled (usual default for Linux) and the 32 bit compatibility libraries must be present.To get the list of all dependency files for hp-snmp-agents type:rpm –qp –-requires hp-snmp-agents-<version>.rpmFixesFixed the following items:o The hp-snmp-agent may show "NAME="SLES"" as OS description for all the SLES15 and subversion.o The user may see the incorrect status for the connected NIC ports due to missing the ifconfig system command in SLES15 and subversion.o The user may see interface information is missing on the SMH page due to the hp-snmp-agent for SLES 15 missing the systemd rpm during the package build.HPE System Health Application and Command Line Utilities for Red Hat Enterprise Linux 8 ServerVersion: 10.9.3(Optional)Filename: hp-health-10.93-307.4.rhel8.x86_psig; hp-health-10.93-307.4.rhel8.x86_64.rpmPrerequisitesThe hp-health and hp-snmp-agents run as 32 bit applications in the x86_64 environment. The Linux kernel 32 bit compatibility must be enabled (usual default for Linux) and the 32 bit compatibility libraries must be present.To get the list of all dependency files for hp-health, type:rpm –qp –requires hp-health-< version >.rpmFixesFixed the following items:o The hpasmcli utility may show DIMM status as "N/A" due to the SMBIOS data entry not correctly initializing the DIMM information.HPE System Management Homepage Templates for LinuxVersion: 10.8.1(Optional)Filename: hp-smh-templates-10.8.1-1487.3.noarch.rpmPrerequisitesThe hp-smh-templates RPM install will fail, if all dependencies are not installed. The administrator can verify the list of dependencies required by running this command. If the repositories being used by yum or zypper, includes these dependencies, the installation tool will automatically retrieve them. However if they are not present, the user must manually install them prior to proceeding with the RPM install.To get the list of all dependency files for hp-smh-templates type:rpm –qp –-requires hp-smh-templates-<version>.rpmFixesInitial support for Red Hat Enterprise Linux 8 ServerContent NotesRHEL8.6 Supplement for Gen9 SPP ContentsThis table lists all of the software and firmware on this RHEL8.6 Supplement for Gen9 SPP. For more information on this deliverable go to /servers/spp/download.ProductCategory Component Title Version Release Date FilenameApplication - System Management Integrated Smart UpdateTools for Linux x64 2.9.1.021 October2021sut-2.9.1-22.linux.x86_64.rpmDriver - Storage Controller HPE ProLiant Smart ArrayController (64-bit) Driverfor Red Hat EnterpriseLinux 8 (64-bit)3.4.20-218 06 May 2022kmod-hpsa-3.4.20-218.rhel8u5.x86_64.rpmkmod-hpsa-3.4.20-218.rhel8u6.x86_64.rpmDriver - Storage Controller HPE Dynamic Smart ArrayB140i SATA RAIDController Driver for Red1.2.10-211 06 May 2022 kmod-hpdsa-1.2.10-211.rhel8u6.x86_64.rpmHat Enterprise Linux 8 (64-bit)kmod-hpdsa-1.2.10-211.rhel8u5.x86_64.rpmDriver - Storage Controller HPE ProLiant Smart ArrayController (64-bit) Driverfor Red Hat EnterpriseLinux 8 (64-bit)3.4.20-211 03 December2021kmod-hpsa-3.4.20-211.rhel8u5.x86_64.rpmkmod-hpsa-3.4.20-211.rhel8u4.x86_64.rpmSoftware - Driver Update HPE Dynamic Smart ArrayB140i SATA RAIDController Driver for RedHat Enterprise Linux 8(64-bit)1.2.10-211 07 May 2022Software - System Management HPE SNMP Agents for RedHat Enterprise Linux 8Server10.9.4 28 August2021hp-snmp-agents-10.94-689.8.rhel8.x86_64.rpmSoftware - System Management HPE System ManagementHomepage Templates forLinux10.8.1 15 February2019hp-smh-templates-10.8.1-1487.3.noarch.rpmSoftware - System Management HPE ProLiant AgentlessManagement Service forRed Hat Enterprise Linux8 Server2.10.503 January2022hp-ams-2.10.5-888.1.rhel8.x86_64.rpmSoftware - System Management HPE System HealthApplication and CommandLine Utilities for Red HatEnterprise Linux 8 Server10.9.3 10 April 2021 hp-health-10.93-307.4.rhel8.x86_64.rpmSoftware - Lights-Out Management HPE Lights-Out OnlineConfiguration Utility forLinux (AMD64/EM64T)5.7.0-0 03 January2022hponcfg-5.7.0-0.x86_64.rpmThere are 10 items in this table.© Copyright 2021 Hewlett Packard Enterprise Development LP。
FFGGG

PART IBACKGROUNDThis compliance program provides guidance to FDA field and center staffs for the inspections and administrative/enforcement activities related to the Quality System (QS) regulation (21 CFR Part 820), the Medical Device Reporting (MDR) regulation (21 CFR Part 803), the Medical Device Tracking regulation (21 CFR Part 821), the Corrections and Removals regulation (21 CFR Part 806), and the Registration and Listing regulation (21 CFR Part 807). This compliance program supersedes the program of the same name which was issued on October 1, 2000.This compliance program encompasses five regulations for inspecting medical device firms. Under the QS regulation, manufacturers are expected to control their devices from design stage through post-market surveillance. Manufacturing processes, such as sterilization, are required to be implemented under appropriate controls. The MDR, Tracking, and Corrections and Removals regulations involve activities with which manufacturers and importers are required to comply after the devices aredistributed. This compliance program provides specific guidance for each. It also requires coverage for the Registration & Listing regulation.A. THE QUALITY SYSTEM (QS) REGULATIONManufacturers establish and follow quality systems to help ensure that their productsconsistently meet applicable requirements and specifications. The quality systems for FDA-regulated products (food, drugs, biologics, and devices) are known as CGMP's. CGMPrequirements for devices in part 820 (21 CFR part 820) were first authorized by section 520(f) of the Federal Food, Drug, and Cosmetic Act (the act) (21 U.S.C. 360j(f)), which was among theauthorities added to the act by the Medical Device Amendments of 1976. Under section 520(f) of the act, FDA issued a final rule in the Federal Register of July 21, 1978 (43 FR 31 508),prescribing CGMP requirements for the methods used in, and the facilities and controls used for the manufacture, packing, storage, and installation of medical devices. This regulation became effective on December 18, 1978.The Safe Medical Devices Act of 1990 (the SMDA), enacted on November 28, 1990, amended section 520(f) of the act, providing FDA with the authority to add preproduction design controls to the CGMP regulation. This change in law was based on findings that a significant proportion of device recalls were attributed to faulty design of product. The SMDA also added new section 803 to the act (21 U.S.C. 383) which, among other things, encourages FDA to work with foreign countries toward mutual recognition of CGMP requirements. FDA undertook the revision of the CGMP regulation to add the design controls authorized by the SMDA to the CGMP regulation, as well as because the agency believed that it would be beneficial to the public and the medical device industry for the CGMP regulation to be consistent, to the extent possible, with therequirements for quality systems contained in applicable international standards. FDA published the revised CGMP requirements in the final rule entitled “Quality System Regulation” in theFederal Register of October 7, 1996 (61 FR 52602). This regulation became effective on June 1, 1997 and remains in effect.B.THE MDR REGULATIONThe first Medical Device Reporting (MDR) regulation became final on December 13, 1984. As aresult of changes mandated by the Safe Medical Devices Act (SMDA) of 1990, and the MedicalDevice Amendments of 1992, the 1984 MDR regulations (21 CFR 803 & 807) were revised andpublished on December 11, 1995. The FDA Modernization Act of 1997 made additional changes and a revised MDR regulation was proposed in May 1998. The final revised MDR regulation was published in the Federal Register on January 26, 2000. The latest version of MDR regulationincludes reporting requirements for manufacturers, user facilities, and importers. MDR reporting for medical device distributors (except importers) was revoked by the FDA Modernization Act of 1997.Distributors are, however, still required to maintain complaint records, per 21 CFR 803.18(d)(1-3).21 CFR Part 803 requires manufacturers of medical devices, including in vitro diagnostic devices, toreport to FDA whenever the manufacturer or importer receives or otherwise becomes aware ofinformation that reasonably suggests that one of its marketed devices:1.may have caused or contributed to a death or serious injury or,2. has malfunctioned and that the device or any other device marketed by the manufacturer orimporter would be likely to cause or contribute to a death or serious injury if the malfunctionwere to recur.NOTE: Importers (initial distributors) of medical devices are subject to 21 CFR Part 803 published in the Federal Register on January 26, 2000, and effective March 27, 2000.C. THE MEDICAL DEVICE TRACKING REGULATIONUnder the authority of section 519(e) of the Act, the agency may issue a written tracking “order” that tells a manufacturer to implement a tracking program that meets the requirements of 21 CFR Part821. Devices subject to tracking may include those that are permanently implanted or lifesustaining/life supporting devices that are used outside a device user facility. These devices areconsidered reasonably likely to cause serious adverse health consequences if they fail. Theregulation is intended to ensure that in the event of a recall or safety alert, a tracked device can betraced by the manufacturer from the device manufacturing facility to the end user or patient.D. THE CORRECTIONS AND REMOVAL REGULATIONThe Corrections and Removal regulation requires manufacturers, and importers to report promptly to FDA any corrections or removals of devices being undertaken to reduce risk to health.E.THE REGISTRATION AND LISTING REGULATIONThe Registration and Listing regulation requires manufacturers and foreign exporters to register and list their devices; and importers to register. (See Part III)。
Linux LPC18XX BSP (Board Support Package) Guide fo

Linux LPC18XXBSP (Board Support Package) Guide for the Hitex LPC1850 Eval BoardRelease 1.10.1Table of Contents1.OVERVIEW (3)2.PRODUCT CONTENTS (3)2.1.S HIPPABLE H ARDWARE I TEMS (3)2.2.D OWNLOADABLE H ARDWARE M ATERIALS (3)2.3.D OWNLOADABLE S OFTWARE M ATERIALS (3)2.4.D OWNLOADABLE D OCUMENTATION M ATERIALS (3)3.SOFTWARE FUNCTIONALITY (4)3.1.S UPPORTED F EATURES (4)3.2.N EW AND C HANGED F EATURES (5)3.3.K NOWN P ROBLEMS &L IMITATIONS (5)4.HARDWARE SETUP (5)4.1.H ARDWARE I NTERFACES (5)4.2.J UMPERS (5)4.3.B OARD C ONNECTIONS (5)5.LPC1850 EVAL BOARD LINUX SOFTWARE SET-UP (6)5.1.U-B OOT I NSTALLATION (6)5.2.U-B OOT E NVIRONMENT (7)5.3.E THERNET MAC A DDRESS (8)5.4.N ETWORK C ONFIGURATION (8)5.5.L OADING L INUX I MAGES (8)5.6.U-B OOT B UILD (10)6.FURTHER MATERIALS (10)7.SUPPORT (10)1. OverviewThis document is a Linux LPC18XX BSP (Board Support Package) Guide for the HitexLPC1850 Eval board, Release 1.10.1.The BSP provides a software development environment for evaluation and development of Linux on the Cortex-M3 processor core of the NXP LPC18XX microcontroller using the Hitex LPC1850 Eval board as a hardware platform.2. Product ContentsThis product includes the following components.2.1. Shippable Hardware ItemsThe following hardware items are shipped to customers of this product:1.None - THIS IS A SOFTWARE-ONLY PACKAGE. Please purchase the LPC1850 Eval boardfrom Hitex or its distributors.2.2. Downloadable Hardware MaterialsThe following hardware materials are available for download from Emcraft's web site to customers of this product:1.None - Please obtain hardware materials pertinent to the LPC1850 Eval board directlyfrom Hitex.2.3. Downloadable Software MaterialsThe following software materials are available for download from Emcraft's web site to customers of this product:1.u-boot.bin - prebuilt U-Boot file in the format suitable for installation into embeddedFlash of Cortex-M3 on the LPC1850 Eval board;working.uImage - prebuilt Linux image ready to be loaded to the LPC1850 Evalboard;3.linux-LPC18XX-1.10.1.tar.bz2 - Linux LPC18XX software development environment,including:a)U-Boot firmware;b)Linux kernel;c)busybox and other target components;d)Linux-hosted cross-development environment;e)Framework for developing multiple projects (embedded applications) from a singleinstallation, including sample projects allowing to kick-start software development for Linux LPC18XX.2.4. Downloadable Documentation MaterialsThe following documentation materials are available for download from Emcraft's web site to customers of this product:1.linux-cortexm-um-1.10.1.pdf - Linux Cortex-M User's Manual;2.linux-LPC1850-EVAL-bspg-1.10.1.pdf - Linux LPC18XX BSP (Board Support Package)Guide for the Hitex LPC1850 Eval Board (this document).3. Software Functionality3.1. Supported FeaturesThe following list summarizes the features and capabilities of Linux LPC18XX, Release1.10.1:∙U-Boot firmware:o U-Boot v2010.03;o Target initialization from power-on / reset;o Runs from the internal eNVM and internal SRAM (no external memory required for standalone operation);o Serial console;o Ethernet driver for loading images to the target;o Serial driver for loading images to the target;o Device driver for built-in Flash (eNVM) and self-upgrade capability;o Device driver for storing environment and Linux images in external Flash;o Autoboot feature, allowing boot of OS images from Flash or other storage with no operator intervention;o Persistent environment in Flash for customization of target operation;o Sophisticated command interface for maintenance and development of the target. ∙Linux:o uClinux kernel v2.6.33;o Boot from compressed and uncompressed images;o Ability to run critical kernel code from integrated Flash of LPC18XX;o Serial device driver and Linux console;o Ethernet device driver and networking (ping, NFS, Telnet, FTP, ntpd, etc.);o busybox v1.17;o POSIX pthreads;o Hardened exception handling; an exception triggered by a process affects only the offending process;o Loadable kernel modules;o Secure shell (ssh) daemon;o Web server;o MTD-based Flash partitioning and persistent JFFS2 Flash file system for external Flash.∙Development tools:o ARMv7-optimized GNU toolchain from CodeSourcery (2010q1) is used for development of U-Boot, Linux and user-space applications (toolchain must bedownloaded separately from the CodeSourcery web site);o Cross GDB for debugging user-space applications;o mkimage tool used by the Linux kernel build process to create a Linux image bootable by U-Boot.∙Development environment:o Linux-hosted cross-development environment;o Development of multiple projects (embedded applications) from a single installation;o hello sample project ("Hello, world!" single-process configuration);o networking sample project (basic shell, networking and Flash management tools demonstration);o developer sample project (template project that can be used to jump-start development of custom user-space applications and loadable kernel modules).3.2. New and Changed FeaturesThis section lists new and changed features of this release:1.Improve boot-up time of network-enabled configurations in Linux Cortex-M3/M4.ID: RT 85493.3.3. Known Problems & LimitationsThis section lists known problems and limitations of this release:1.CONFIG_KERNEL_IN_ENVM requires disabling CONFIG_ARM_UNWINDand CONFIG_EARLY_PRINTK.ID: RT 74683.Workaround: When enabling CONFIG_KERNEL_IN_ENVM in the kernel, disableCONFIG_ARM_UNWIND and CONFIG_EARLY_PRINTK.4. Hardware SetupThis section explains how to set up the Hitex LPC1850 Eval board.4.1. Hardware InterfacesFor a description of the hardware interfaces provided by the LPC1850 Eval board, refer to detailed technical documentation and other associated materials available from Hitex.4.2. JumpersThe following jumpers must be configured on the LPC1850 Eval board:Jumper Configuration NotesJP5 2-3 closed Ethernet: MII modeJP14 2-3 closed Ethernet: MII modeJP15 open Ethernet: MII modeJP23 open Disable write protection of NOR flashSV1 only 5-6 and 7-8 closed Connect USART0 to the DB9 port "UART" SV3 all closed Connect Ethernet signalsSV6 all closed Connect Ethernet signalsSV12 all open Disconnect signals optionally shared withEthernetSV13 all open Disconnect signals optionally shared withEthernet4.3. Board ConnectionsTo power the LPC1850 Eval board up, simply connect it to a PC / notebook by plugging a USB-B cable into the X2 USB-B connector on the LPC1850 Eval board. As soon as theconnection to the PC has been made, the various on-boards LEDs should lit up, indicating that the board is up and running.To provide a serial interface to a PC / notebook plug a RS-232 cable to the X1 "UART" connector on the board. On the PC side, the serial link provides a serial console device to the LPC1850 Eval. The software installed on the board is configured for a 115.2 K terminal. On the Linux host, the serial console is available using a /dev/ttyS n device.To provide network connectivity to the board, connect it into your LAN by plugging a standard Ethernet cable into the 10/100 Ethernet connector. The board is pre-configured with an IP address of 192.168.0.2.5. LPC1850 Eval Board Linux Software Set-up5.1. U-Boot InstallationTo install U-boot onto the Hitex LPC1850 Eval, follow the step-wise procedure documented below:1.Configure the boot select jumpers according to the table below for booting from USB0:Jumper ConfigurationBOOT1 1-2 closedBOOT2 2-3 closedBOOT3 1-2 closedBOOT4 2-3 closed2.Connect the UART port of the LPC1850 Eval board to a host.3.Run a terminal program (e.g. HyperTerminal on Windows, or kermit on Linux) and createa serial connection to the LPC1850 Eval board with the following COM-port settings:115200 8N1.4.Connect the LPC1850 Eval board to a Linux host by plugging a USB-B cable into the X2USB-B connector on the LPC1850 Eval board.5.Install the free tool dfu-util on the Linux host either from your Linux distributionpackages or by building it from sources. The sources of dfu-util are available fordownload at /.6.Boot U-Boot on the LPC1850 Eval board by running dfu-util on the Linux host.dfu-util -R -D u-boot.bin7.Start a TFTP server in the local network of the LPC1850 Eval board and make the u-boot.bin image available on this TFTP server.8.Set the U-Boot environment variables serverip and ipaddr to the IP address of theTFTP server and the desired IP address of the LPC1850 Eval board, respectively.LPC1850-EVAL> setenv serverip 192.168.0.10LPC1850-EVAL> setenv ipaddr 192.168.0.18LPC1850-EVAL>9.Download the u-boot.bin image into the on-board RAM.LPC1850-EVAL> tftp lpc18xx/u-boot.binpleted.LPC18XX_MAC: link UP (100/Full)Using LPC18XX_MAC deviceTFTP from server 192.168.0.10; our IP address is 192.168.0.18Filename 'lpc18xx/u-boot.bin'.Load address: 0x28000000Loading: #######doneBytes transferred = 93200 (16c10 hex)LPC1850-EVAL>10.Write the u-boot.bin image into the beginning of the on-board NOR flash.LPC1850-EVAL> era 1c000000 +${filesize}....................... doneErased 23 sectorsLPC1850-EVAL> cp.b ${fileaddr} 1c000000 ${filesize}Copy to Flash... doneLPC1850-EVAL>11.Reconfigure the boot select jumpers according to the table below for booting from NORflash:Jumper ConfigurationBOOT1 1-2 closedBOOT2 1-2 closedBOOT3 2-3 closedBOOT4 2-3 closed12.Reset the LPC1850 Eval board and see the U-Boot start-up banner in the terminalprogram.5.2. U-Boot EnvironmentWhen the LPC1850 Eval board is reset, the Linux bootstrap will proceed to boot the U-Boot firmware from the external NOR Flash printing the following output to the serial console:U-Boot 2010.03-linux-cortexm-1.10.1 (June 11 2013 - 19:43:46)CPU : LPC18xx series (Cortex-M3)Freqs: SYSTICK=180MHz,CCLK=180MHzBoard: Hitex LPC1850 Eval rev 1DRAM: 8 MBFlash: 4 MB*** Warning - bad CRC, using default environmentIn: serialOut: serialErr: serialNet: LPC18XX_MACHit any key to stop autoboot: 0LPC1850-EVAL>U-boot makes use of the so-called environment variables to define various aspects of the system functionality. Parameters defined by the U-boot environment variables include: target IP address, target MAC address, address in RAM where a Linux bootable images will be loaded, and many more. To examine the current settings of the environment variables, run printenv from the U-Boot command interface.The reason for the warning about the "bad CRC" is that U-Boot is configured to store its environment variables in the external Flash. However, this being the first time when you boot Linux LPC18XX on the development board, obviously there is no U-Boot environment programmed to the external Flash. U-Boot goes to the external Flash, fails to find its environment there, prints the warning message and resorts to using the default environment integrated into the U-Boot image at build time.U-Boot provides a command called saveenv that stores the up-to-date run-time environment to the persistent storage, which will be the external Flash for the U-Boot configuration used on the LPC1850 Eval board. You need to call saveenv any time when you want to copy current settings of the environment variables to the persistent storage in Flash.This is how you can write the current U-Boot environment to the external Flash:LPC1850-EVAL> saveenvSaving Environment to Flash......LPC1850-EVAL>Reset the LPC1850 Eval board and check that there is no warning about the bad CRC in the boot-up messages. This is expected since now U-Boot successfully finds its environment in the external Flash:LPC1850-EVAL> resetresetting ...U-Boot 2010.03-linux-cortexm-1.10.1 (June 11 2013 - 19:43:45)...Hit any key to stop autoboot: 0LPC1850-EVAL>5.3. Ethernet MAC AddressIn Linux LPC18XX, the MAC address of the Ethernet interface is defined by the ethaddr U-Boot environment variable. The value of the MAC address can be examined from the U-Boot command line monitor as follows:LPC1850-EVAL> printenv ethaddrethaddr=C0:B1:3C:88:88:88LPC1850-EVAL>The default U-Boot environment for the LPC1850 Eval board sets ethaddr to a fixed MAC address. This address should work for you in a general case, however if you have more than two LPC1850 Eval boards in your LAN, use of the same address on multiple boards may result in packet collisions in your LAN and overall may render your LAN mal-functioning.If you have more than one LPC1850 Eval boards in your LAN, you have to assign a unique MAC address to each board.The MAC address can be changed by modifying the ethaddr variable as follows:LPC1850-EVAL> setenv ethaddr C0:B1:3C:88:88:89Don't forget to store your update in the persistent storage using saveenv so it is remembered across resets and power cycles.5.4. Network ConfigurationYou will have to update the network configuration of your board to match settings of your local environment.Typically, all you have to allow loading images over network from a TFTP server is update the U-Boot environment variables ipaddr (the board IP address) and serverip (the IP address of the TFTP server). Here is how it is done.Update ipaddr and serverip:LPC1850-EVAL> setenv ipaddr 192.168.0.2LPC1850-EVAL> setenv serverip 192.168.0.1and then save the updated environment to the external Flash so that your changes are persistent across resets/power cycles.5.5. Loading Linux ImagesAt this point, you are able to load Linux bootable images to the board over TFTP and either boot them directly or install them to the external Flash to allow booting Linux from Flash on power-up/reset.On the host, activate the Linux LPC18XX development environment and build the networking project:-bash-3.2$ . ACTIVATE.sh-bash-3.2$ cd projects/networking/-bash-3.2$ make...-bash-3.2$Copy the Linux bootable image to the TFTP download directory:-bash-3.2$ cp networking.uImage /tftpboot/vlad/-bash-3.2$To load the image directly, use the netboot U-Boot macro:LPC1850-EVAL> setenv image vlad/networking.uImageLPC1850-EVAL> run netboot...TFTP from server 172.17.0.1; our IP address is 172.17.5.100Filename 'vlad/networking.uImage'....Loading: ###############################################################################################################################################doneBytes transferred = 2084704 (1fcf60 hex)...Image Name: Linux-2.6.33-arm1Image Type: ARM Linux Kernel Image (uncompressed)...Verifying Checksum ... OKLoading Kernel Image ... OKOKStarting kernel ...Linuxversion2.6.33-arm1(******************.com)(gccversion4.4.1(SourceryG++Lite 2010q1-189) ) #1 Tue June 11 15:43:44 MSK 2013...To load the image into the Flash, use the U-Boot update macro:LPC1850-EVAL> setenv image vlad/networking.uImageLPC1850-EVAL> run update...TFTP from server 172.17.0.1; our IP address is 172.17.5.100Filename 'vlad/networking.uImage'....Loading: ###############################################################################################################################################doneBytes transferred = 2084704 (1fcf60 hex) ................................ doneUn-Protected 32 sectors................................ doneErased 32 sectorsCopy to Flash... doneLPC1850-EVAL>Reset the board and verify that the newly programmed image boots on the target in the autoboot mode:LPC1850-EVAL> resetresetting ...U-Boot 2010.03-linux-cortexm-1.10.1 (June 11 2013 - 17:19:37)...Starting kernel ......init started: BusyBox v1.17.0 (June 11 2013 - 17:19:37)~ #5.6. U-Boot BuildThe BSP distribution comes with U-Boot pre-built for the LPC1850 Eval board. If however you need to re-build U-Boot for your board, please follow the instructions below:1.Install the Linux LPC18XX distribution to the development host, as described in the LinuxCortex-M User's Manual.2.From the top of the Linux LPC18XX installation, activate the Linux LPC18XX cross-compile environment by running . ACTIVATE.sh.3.Go to the U-Boot source directory (cd u-boot/).4.Run the following commands:[psl@pvr u-boot]$ make lpc1850-eval_configConfiguring for lpc1850-eval board...[psl@pvr u-boot]$ make -s6. Further MaterialsRefer to Linux Cortex-M User's Manua l for detailed information on the software architecture of the Linux LPC18XX distribution.Visit Emcraft Systems' web site at to obtain additional materials related to Linux LPC18XX.7. SupportWe appreciate your review of our product and welcome any and all feedback. Comments can be sent directly by email to:*****************************The following level of support is included with your purchase of this product:∙Email support for installation, configuration and basic use scenarios of the product during3 months since the product purchase;∙Free upgrade to new releases of the downloadable materials included in the product during 3 months since the product purchase.If you require support beyond of what is described above, we will be happy to provide it using resources of our contract development team. Please contact us for details.。
NI Academic Installation Guide
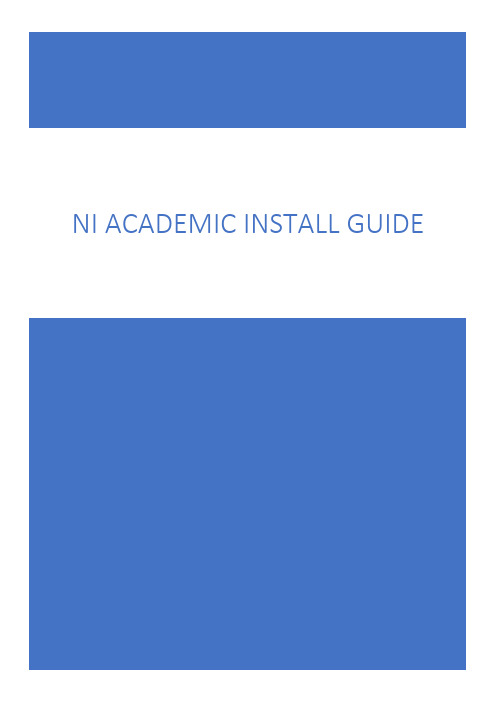
NI ACADEMIC INSTALL GUIDEAcademic Installation GuideThis guide is designed to make getting up and running with your NI software quick and easy.ContentsAcademic Installation Guide 0Choosing Which Installer to Use (1)Running the Installer (2)Choosing Which Software to Download and Install (5)Which Software Should I Select to Install? (6)Starting the Download (8)Adding More Software at a Later Date (12)Multiple Versions of LabVIEW on the Same Computer (13)Where to Go Next (13)Learn How to Use NI Software (13)Get Support (13)Server-Based Licensing for IT Admins (13)Choosing Which Installer to UseThe website at /academic/download hosts several different installers for NI software, from which you can select based on your requirements. You can choose between three installer options:•The NI Software Platform Bundle contains most of the NI Software Portfolio and allows you to select the exact software items you wish to download and install. This is the installer we recommend using if you have purchased the LabVIEW Academic Site License. This document contains guidance on which software items you should choose for common scenarios. To use this installer, follow the steps beginning on page 2.•The Circuit Design Suite Education Edition installer includes Multisim TM and Ultiboard TM software, which are both included in the Multisim TM Academic Site License.•The Specific NI Software Installers contain only the subset of NI software needed to support a particular focus area (i.e. using a specific hardware product or specific OS), thus simplifying the options presented to users.Each installer has a choice of different versions by year or by release, so you can use the exact same software on your own computer that you run in your lab class, research lab, or department library. Running the same version of software helps prevent incompatibilities between code transferred among different computers.Running the InstallerOnce you have downloaded one of the installers, navigate to the file in Windows Explorer, right-click, and select “Run as Administrator.” You then see this window:Press “Start.”You may receive a Windows security warning after pressing “Start” that asks if you would like this application to make changes to your computer. Ensure that the warning detects “Verified publisher: National Instruments Corporation.” Say “Yes” or “Allow.”Save and close any open files, exit other applications, and select “Next.”Selecting “I want to i nstall software now” download s and installs the software you choose in later steps. Selecting “I want to d ownload software only” download s only the installation files so that you can install later. Choose which one is best for you and select “Next.”IT Admins: The “I want to download software only” option is useful if you want to create your own installation media. Active subscriptions to any Teaching Academic Site License receive a physical shipment of installation media once per year immediately after the NIWeek conference. If you want to order extra installation media, contact NI at/contact-us.The “I have s erial numbers…” option shows only the software products you can activate using those serial numbers (also known as activation keys). The “I want to e valuate…” option shows the full list of NI software, but be awarethat you may download software you cannot later activate with your license. For a list of the software activated by NI academic site licenses, view this white paper.Choose the best option for you and select “Next.”If you chose to active by serial number in the previous step, enter the serial number(s) and select “Add Serial Number” and then “Next.”IT Admins: The University chose between two options to activate software when they purchased an Academic Site License: a serial number or a license file. If you have the serial number, you can enter it here. If you are using a license file on a license server, then press “Back” and choose “Evaluate Products Only” from the previous page of the installer.Students: If you purchased your own copy of LabVIEW, enter the serial number here. The serial number may be printed on the packaging of the LabVIEW CD/DVD or sent in an email by the company that sold you LabVIEW. If you are using the Student Install (part of a university’s Academic Site License) to get free access, you need to retrieve the Student Install serial number from your IT administrator. This is different from the main campus serial number. Each year, you will need to get the new Student Install serial number from your IT admin.Choosing Which Software to Download and InstallIn this step, choose the software you want to download and install. You should see a software list like the one below with a few default options already selected.The installer uses a tree hierarchy to organize different software items into folders. You can use the + and – symbols to expand sections of the tree.To select a software item for download and installation, click the icon to the left of the software item’s name. You can then choose to “Install” or “Do not i nstall” from the drop-down menu that appears. You can perform the same operation on an entire folder of software items by clicking on the folder icon.Which Software Should I Select?Choosing the right software to install can be confusing if you are not sure what you need. You can download and install everything, but that may lead to a very large download. This section of the guide recommends the minimum software items you should install for certain scenarios and explains how to find these items in the different folders on the tree.Installing more software items means your LabVIEW software contains more features, tools, APIs, code blocks, examples, and help documentation to use in your projects.Choosing Software Based on Your Hardware*NI-ELVISmx is for the myDAQ and NI ELVIS II/II+ only. For use with the NI ELVIS III, install the NI ELVIS III Software Bundle under Specific NI Software Installers.Choosing Software Based on Your Engineering Topic*NI-ELVISmx is for the myDAQ and NI ELVIS II/II+ only. For use with the NI ELVIS III, install the NI ELVIS III Software Bundle under Specific NI Software Installers.Starting the DownloadCheck for any important messages or updates to the software you have chosen before installing. This step requires an active Internet connection. Select “Next.”If the software you chose has no notifications, select “Next.” If warnings appear, follow the on-screen advice.Choose the destination folder for your software. If you are unfamiliar with this step, use the default directories that appear automatically. Select “Next.”Agree to the licenses for the software you have chosen. Review the agreements, select “I accept,” and click “Next.”You can choose to disable Windows Fast Startup, which can cause hardware connection issues on tablet and laptop computers. Select “Next.”If you are installing for the first time, select “Create a new Account.” This requires an Internet connection. Use your university/school email address to create an account on . Afterward, or if you already have an account, enter your login credentials here.IT Admins: If you are installing on behalf of a staff member, select “I am not the end user.” When end user s start the software for the first time, they are prompted to create their own accounts. Creating accounts, especially when using university email addresses, significantly streamlines the process of getting technical support for your NI software and licenses.Review the download size for the software you have chosen. You can pause the download at any time if you need to continue it later.If you selected to install software you will automatically progresses to the software installation. Do not let your computer sleep, hibernate, shut down, or interfere with the installation stage.A new window opens during the installation stage. Do not close any of the download or installation windows. They close automatically when finished.You may see this type of window once for each software item you chose. After all the software items have finished installing the installer generates an installation report which you can review before selecting “Next or “Finish.”Adding More Software LaterYou can add more NI software to a computer later. Simply relaunch the installer file and select new software items to download and install. Visit /academic/download to download the most recent version of the installer.Multiple Versions of LabVIEW on the Same ComputerNI introduces new versions of LabVIEW in major and minor releases. Major release examples are LabVIEW 2016 and LabVIEW 2017. A minor release example is a service pack denoted as LabVIEW 2017 SP1.Major releases work side by side on the same computer, so you can have LabVIEW 2016 and LabVIEW 2017 installed and working at the same time if you need. However, you should always use the same version of LabVIEW across all your work (homework, laboratory class, research lab computer, colleagues’ computers) to avoid incompatibilities when transferring code from one computer to the next. If you do receive code that does not open in your version of LabVIEW because the code has been made on a newer version, you need to ask the author to use the “Save for Previous Version” feature and send you the new files.Installing a minor release (SP1 or patch) upgrades any existing software on the PC. Incompatibilities with code do not normally occur between an SP1 version of software and a non-SP1 version.Where to Go NextLearn How to Use NI SoftwareNeed to quickly get familiar with the fundamentals of LabVIEW? LabVIEW 101 is a collection of short videos that guide a student through an introduction to LabVIEW.Want a more formal training structure? Take the official NI education courses online. All users of an active Academic Site License have access to self-paced online training courses. Talk to your IT admins to see if they have set up email-domain level access for your institution.Instructor-led courses are available for in-person and online learning. Academic customers can take these multiday courses at a huge discount. Contact NI to learn the closest course location.Get SupportStaff members at academic institutions are encouraged to contact NI by phone and email to get answers to their NI software and hardware questions. Begin a service request online using your serial number.For students, the NI community provides a great place to exchange ideas and collaborate on challenges.Server-Based Licensing for IT AdminsYou may now be ready to start setting up your license server, or you may need to connect that server to the computers on which you have installed NI software. NI Volume License Manager (VLM) is powerful server-based licensing software that is included with an Academic Site License.To learn how VLM software can help you, check out “Getting Started with NI VLM” under Academic Site License Administrator Resources.。
博世 安全系统-法拉登VIVIDIO应用程序 步骤配置 说明书

From Nuremberg BT-VS/MKP-XPT Product Management 20.04.2023Release LetterProduct: VIDEOJET decoder 7000 VJD-7513Version: Firmware 10.40.0055This letter contains latest information about the above-mentioned product.1. GeneralThis firmware release 10.40.0055 is a feature release based on FW 10.31.0005.Changes since last release FW 10.31.0005 are marked in blue.VIDEOJET decoder 7000 uses robust, fan-less technology designed for ambitious environmental conditions while providing maximum performance on minimum space in a nicely designed industrial housing.VIDEOJET decoder 7000 displays video from Standard Definition (SD), High Definition (HD), 4K Ultra High Definition (UHD), and Megapixel (MP) cameras and encoders using H.265, H.264 or MPEG-4 encoding at up to 60 frames per second over IP networks.VIDEOJET decoder 7000 is the successor of VIDEOJET decoder 8000 (VJD-8000, VJD-8000-N). It is using the same housing but comes with different video output interfaces and provides improved performance and functionality.Notes:•Firmware update may take several minutes due to a large cumulative Microsoft patch.•This firmware includes OpenSSL.From NurembergBT-VS/MKP-XPT Product Management 20.04.20232. Applicable products•VIDEOJET decoder 7000, VJD-75133. New Features•SRTP for encrypted multicast traffic is supported. This allows fully secured communication with and video streaming from CPP13 and CPP14 cameras in multicast environments.•SNMPv3 trap service has been added, including the support of SNMP-related RCP+ commands for configuration.• A JPEG snapshot is now possible from each of the displays, including JPEG quality settings parameter.•Display order can be re-arranged in case Windows display detection differs from mechanical order.•The default layout is depending on the display number to simplify the identification of display order. The number of video windows per display increases as square of the display number.•The web interface of the decoder has been updated to the latest style guide and re-structured to ease usage for installation, licensing, and integration purposes.o The new web pages provide links to documentation and include a live preview.o Maintenance log file creation and download is supported by a workflow mechanism.o A keyboard emulator supports initial setup for IP Matrix even without keyboard connected.From NurembergBT-VS/MKP-XPT Product Management 20.04.20234. Changes•The Video SDK as one of the core components for the decoder firmware has been updated to latest version 6.40, providing a great number of improvements and fixes, mainly aroundONVIF and RTSP support, increasing the overall robustness.•An issue is fixed for banner upload when banners are activated.•An issue is fixed for zooming out in client dewarping mode of panoramic camera streams.•An issue is fixed where client dewarping was not working on line 1 of a panoramic camera in onboard dewarping mode. Onboard dewarping is only available for lines 2 and higher, line 1 always provides the full warped image circle.•An issue with DNS server configuration is fixed.•An issue is fixed where CPP13 and CPP14 cameras were not correctly connected in camera sequences.•Maintenance log file download is improved, supported by the new web interface structure.•An issue is fixed where daylight saving time was incorrectly reflected in time zone offset calculation.5. System RequirementsFor configuration purposes:•Configuration Manager 7.61 or newerFor operation purposes:•Bosch Video Management System 12.0 or higherNote that not all features may be supported by BVMS yet.Please refer to BVMS release notes.From NurembergBT-VS/MKP-XPT Product Management 20.04.20236. Restrictions; Known Issues•Connecting encrypted streams without proper signalling may result in crashing the software decoder instance, resulting in black video displayed.•Alarms will not be signaled with a red border around the cameo if connection was established using CONNECT_PRIMITIVE.•Using CONNECT_PRIMITIVE via TCP is not possible.•CONNECT_PRIMITIVE does not support "first available" feature.•Audio may remain audible despite layout change to other than single view.•RCP+ command CONF_ALARM_CONNECT_TO_IP is not supported.•Alarm connection does not support audio, nor does it include metadata.•Maximum password length is 19 characters.•With “Reconnect last devices” active camera connections are stored and automatically reconnected after reboot. To avoid deadlock in case of an overload situation the automaticreconnect will be deactivated after the decoder was forced into reboot for ten times within 10 minutes.•Monitors may be swapped after update. Swap back is possible using Configuration Manager.•IP Matrix pre-requisites for multi-decoder clustering:o Fixed IP addresses must be assigned; DHCP configuration is not functional.o Passwords for service level must be same on all clustered decoders.o Passwords for user level must be same on all clustered decoders.•After removing a slave decoder from the IP Matrix master, both decoders must be restarted.•Camera sequences are paused when picture-in-picture mode is activated.•Time related settings may appear in Configuration Manager only with delay or after a reboot.•Monitors connected to the Display Port via USB-C may not always be detected during booting.In this case, unplug and reconnect the adapter or cable to the monitor. If only one monitor isused it is recommended to connect to the direct HDMI output.•Log file download stability may be affected by workload of decoder. As a workaround, the download may need to be repeated, or the workload of the decoder may need to be reduced (disconnect all camera streams).•Time zone configuration is only supported via TIME_ZONE_STRING.•The KBD-DIGITAL keyboard is locked automatically during start-up of the decoder, or with re-connect. It will be unlocked after entering the PIN but the lock screen will remain until the next action on the keyboard.•Certificates used with the decoder must not have any Windows policies defined.•DNS resolution is not implemented yet, thus time server entry only works with IP addresses.•Dewarping zoom does not work correctly for panoramic cameras in on-board dewarping mode for camera line 1.•Overload messages and traps may appear too sensitive in cases where display refresh rates are lower than video stream frame rates.From NurembergBT-VS/MKP-XPT Product Management 20.04.20237. Previous Revisions7.1. New Features with 10.31.0005•Support for HOST_NAME to get and set the device’s hostname; only supported in extended configuration mode.•Support for DNS_SERVER_IP_STRING to get and set primary and secondary DNS server IPv4 addresses.7.2. Changes with 10.31.0005•Optimized transparent data processing time to allow adequate transparent data pass-through for serial PTZ keyboard.•An issue is fixed to apply e-PTZ presets correctly in camera sequences.•Feature loss due to suppressing encrypted UDP multicast connections for Bosch IP cameras with firmware 8 and higher, and fall back to TCP, tunneled via HTTPS control connection.(This feature will be added again with FW 10.40.)From NurembergBT-VS/MKP-XPT Product Management 20.04.20237.3. New Features with 10.30.0005•The default setting for Automatic IPv4 address assignment is set to “DHCP plus Link-Local”.Though this might seem a small change, it may have an impact:The former default IP address 192.168.0.200 will virtually become obsolete.Instead, the camera will assign itself an auto-IP address out of the range 169.254.1.0 to169.254.254.255 as long as there is no other IP address assigned by a DHCP server.(https:///wiki/Link-local_address)The advantage is that there are no more duplicate IP addresses, which is consideredprohibited in a network.•Network authentication 802.1x with EAP/TLS has been added.Please note that the server certificate needs to get the usages ‘Trust’ and ‘EAP_TLS_Trusted’ assigned.The client certificate will get the necessary usages assigned automatically.•The possibility of large banner overlays has been introduced.o Banners can be uploaded as images that can be displayed over three areas: top, center and bottom. The images are scaled to fill the area and cropped wherenecessary.o Banners can be sequenced with a configurable dwell time.o Configuration Manager 7.60 is supporting this with upload and banner sequence configuration, including banner previews.•Set and recall prepositions for moving cameras (AUTODOME, MIC) as well as for ONVIF PTZ cameras via keyboard has been added to the IP Matrix functionality.•Images can be uploaded to the decoder for two purposes, using Configuration Manager. The images shall be in JPG format and must be named as follows:o‘monitor background’ image, shown as background of an empty video window: ‘Logo.jpg’o‘’no camera’ image, shown on connection failure: ‘NoCamLogo.jpg’7.4. Changes with 10.30.0005•An issue was fixed where uploading a new video loss image did not break the software seal.From NurembergBT-VS/MKP-XPT Product Management 20.04.20237.5. Changes with 10.23.0002• A security vulnerability has been fixed where a crafted configuration packet sent by an authenticated administrative user can be used to execute arbitrary commands in systemcontext (CVE-2021-23862).For more details refer to our Security Advisory BOSCH-SA-043434-BT, published at ourSecurity Advisory web pagehttps:///xc/en/support/product-security/security-advisories.htmlor visit our PSIRT website at https://.7.6. New Features with 10.22.0038•APIPA (link-local address, Auto-IP) is used instead of a default IP address when DHCP is on and no DHCP server responded.•Transparent data pass-through for serial PTZ keyboard (SERIAL_PORT_APP_VAL and TRANSFER_TRNSPARENT_DATA) has been added.•Support of RCP+ via CGI (including WRITE commands) has been added.•HTTP digest authentication is supported for RCP+ via CGI.•Display orientation can be changed per line via RCP+.•RCP+ WRITE command MONITOR_NAME now supported for custom monitor names.•Updated RCP+ documentation is now available via the VIDEOJET decoder webpage.•Download of screen and tile snapshots via snap.jpg is now supported (requires at least user privileges).•Firmware update on-screen countdown dialog now shows a heartbeat whenever a single update step takes longer.•Support of CONNECT_URL read queries to get current video connection details, including current digital and dewarping zoom settings, has been added.•Support of various digital and dewarping zoom persistence modes(DIGITAL_ZOOM_PERSISTENCE_MODE) has been added.•Support of SYSTEM_DATETIME_V2 to read/write UTC system time has been added.•Support for new Sentinel RMS licenses has been added. Legacy licenses can now also be based on new installation code (lock code from Sentinel RMS).From NurembergBT-VS/MKP-XPT Product Management 20.04.20237.7. Changes with 10.22.0038•IP Matrix initialization is now working also for camera lines larger than 1.•RCP+ response for query on connected cameras is now working correctly.•URL extension for camera configuration in IP Matrix is no longer truncated.•An issue with an unexpected application restart has been fixed.•The DECODER_GROUP command is no longer supported when decoder IP address is not static. This disables the whole IP matrix configuration pages in Configuration Manager until a static IP is configured in the decoder’s network settings.•Improvements were made for log export via webpage and via Configuration Manager.•KBD-DIGITAL keyboard PIN is now used immediately without application restart.•KBD-DIGITAL keyboard PIN is now required whenever keyboard is attached and at application start.•Display orientation is now working for further monitor types.•Support of further USB to serial COM port adapters for KBD-DIGITAL keyboard connectivity.o Current: Prolific PL2303 [hardware ID USB\VID_067B&PID_2303]o New: Prolific PL2303GT [hardware ID USB\VID_067B&PID_23C3]o New: ATEN UC232A [hardware ID USB\VID_0557&PID_2008]o New: Unitek Y-108 [hardware ID FTDIBUS\VID_0403+PID_6001]o CableCreation CD0489 (PL2303) [hardware ID USB\VID_067B&PID_2303] is compatible to the already supported Prolific PL2303 adapter.Please note that the KBD-DIGITAL keyboard connectivity requires continuous maintenance, since new or not listed USB-to-serial COM port adapters typically require the installation of a suitable driver on the VIDEOJET decoder and an adaption of the hardware ID filter in thekeyboard detection software module. Newer USB adapters may require a firmware update to become supported.From NurembergBT-VS/MKP-XPT Product Management 20.04.20237.8. New Features with 10.01.0036Security• A protected configuration mode has been implemented, allowing too enable SSD encryption (BitLocker) and too disable USB ports, e.g. for installation of the decoder in public areas.•The configuration of the decoder can be protected by Software Sealing, similar to IP cameras.•The latest Microsoft Windows security updates have been included.Miscellaneous• A dewarped cutout from panoramic cameras can be defined with PTZ coordinates.• A new way to control and integrate the decoder into a management system has been added by a JSON RPC API. This allows to send commands and retrieve status information via JSON remote procedure calls. The API documentation is added to the distribution package.• A video output capture service (VOCS) has been implemented which could be activated via a license, applicable per display output. This service captures the memory of the video outputand encodes it into a camera-like video stream, which can be recorded via Video StreamingGateway (VSG) onto iSCSI storage.• A time server can be added to synchronize the decoder.•Decoder log file can be downloaded via Configuration Manager. This is especially recommended when download of the log file is not working correctly via web browser.7.9. Changes with 10.01.0036•Upload of background image and connection loss image to the decoder and reverting them to default is now also possible with service password set. The former restriction is obsolete.•Various minor bug fixes.From NurembergBT-VS/MKP-XPT Product Management 20.04.20237.10. New Features with 9.60.0017IP Matrix enhancements•KBD-DIGITAL is supported in addition to KBD-UNIVERSAL XF.This keyboard requires a serial-to-USB adapter to connect to the decoder.Both keyboards can be mixed in a clustered multi-decoder IP Matrix, one keyboard perdecoder.•Playback from local recording is supported.Permission is configured via Configuration Manager for the whole IP Matrix, valid for all users.•Buttons for next and previous camera have been added to the KBD-UXF functions.•Audio can be switched on or off via keyboard.•Camera channels can be extended via license up to 64 cameras per decoder unit.Note:IP Matrix manual is now separated intoo One configuration manual for IP Matrixo One operation manual for IP Matrix using KBD-UXFo One operation manual for IP Matrix using KBD-DIGITALSecurity•The latest Microsoft Windows security updates have been included.Miscellaneous•Background image and connection loss image can be uploaded to the decoder, replacing the default images. Reverting them to default is done by uploading an empty image.Note: Upload is only possible in conjunction with an empty service password.7.11. Changes with 9.60.0017•Temperature control margin increased to improve maximum performance at the specified maximum temperature, covering component tolerances, and to ensure that all productsadhere fully to their specification.•Various minor bug fixes.Security SystemsFromNuremberg BT-VS/MKP-XPT Product Management 20.04.202311BOSCH and the symbol are registered trademarks of Robert Bosch GmbH, Germany 7.12. Features with initial release 9.51• VIDEOJET decoder 7000 displays video from Standard Definition (SD), High Definition (HD),4K Ultra High Definition (UHD), and Megapixel (MP) cameras and encoders using H.264 or MPEG -4 encoding at up to 60 frames per second over IP networks.• VIDEOJET decoder 7000 provides an HDMI and a DisplayPort (via USB-C connector) output, both capable of driving up to 4K UHD displays simultaneously.• Display settings are automatically discovered and set for optimal display performance. • Monitor layouts can be switched independently for each display.• Upright monitors (portrait mode) are supported.• Video window (cameo) aspect ratio can be set to 16:9, 9:16, 3:4, or 1:1.• Active camera connections and layout are stored and automatically reconnected after reboot if configured. To avoid deadlock in case of an overload situation the automatic reconnect will be deactivated after VIDEOJET decoder 7000 was forced into reboot for 3 times within 10 minutes.• Video smoothing can be configured.• RTSP connections are supported, enabling connectivity to 3rd party and ONVIF cameras. • Discovery port is configurable.• Cameo distance is configurable.• VIDEOJET decoder 7000 supports IP Matrix application as built-in feature.• VIDEOJET decoder 7000 is able to display VCA metadata.• VIDEOJET decoder 7000 provides bi-directional G.711 audio for the video stream shown in single view on the first monitor.• Configuration is done using the Configuration Manager.• The number of decoders presented in capabilities is configurable to regulate the consumption of VMS licenses. Default value is 30.• System access is password-protected with two levels.• The system firmware can be upgraded remotely.• System API is compatible to predecessor VIDEOJET decoder 8000 for easy plug-and-play integration.• Operating temperature iso 0 °C to +50 °C (+32 °F to +122 °F) ambient temperature, with airflow o 0 °C to +40 °C (+32 °F to +104 °F) ambient temperature, still airFor detailed functional description of inherited firmware features, please refer to the VIDEOJET decoder 8000 firmware 9.51 release notes.For detailed technical specification, please refer to the datasheet.。
ARTISAN TECHNOLOGY GROUP - 品牌、产品名、型号说明书

GETTING STARTED GUIDENI PXIe-4080/4081/40821.8 MS/s Digital MultimeterNote Before you begin, install and configure your chassis and controller.This document explains how to install, configure, and test the NI 4080/4081/4082. TheNI 4080/4081/4082 is a digital multimeter that ships with NI-DMM, which you use to program the device.To access NI 4080/4081/4082 documentation, navigate to Start»All Programs»National Instruments»NI-DMM Documentation.Caution The protection provided by this device may be impaired if the device isused in a manner not specified in this document.ContentsElectromagnetic Compatibility Guidelines (2)Verifying the System Requirements (2)Unpacking the Kit (2)Preparing the Environment (3)Safety (3)Kit Contents (4)Other Equipment (4)Installing the Software (4)Installing the NI 4080/4081/4082 (5)Hardware Front Panel Connectors (6)Connecting Signals (7)Requirements for Cables and Probes (10)Configuring the NI 4080/4081/4082 in MAX (11)Programming the NI 4080/4081/4082 (11)NI-DMM Examples (13)Troubleshooting (14)What Should I Do if the NI 4080/4081/4082 Doesn't Appear in MAX? (14)What Should I Do if the Module Fails the Self-Test? (15)Where to Go Next (15)Worldwide Support and Services (15)Electromagnetic Compatibility GuidelinesThis product was tested and complies with the regulatory requirements and limits for electromagnetic compatibility (EMC) stated in the product specifications. These requirements and limits provide reasonable protection against harmful interference when the product is operated in the intended operational electromagnetic environment.This product is intended for use in industrial locations. However, harmful interference may occur in some installations, when the product is connected to a peripheral device or test object, or if the product is used in residential or commercial areas. To minimize interference with radio and television reception and prevent unacceptable performance degradation, install and use this product in strict accordance with the instructions in the product documentation. Furthermore, any changes or modifications to the product not expressly approved by National Instruments could void your authority to operate it under your local regulatory rules.Verifying the System RequirementsTo use the NI 4080/4081/4082, your system must meet certain requirements. For more information about minimum system requirements, recommended system, and supported application development environments (ADEs), refer to the readme, which is available on the software media or online at /updates.Unpacking the KitCaution To prevent electrostatic discharge (ESD) from damaging the device,ground yourself using a grounding strap or by holding a grounded object, such asyour computer chassis.1.Touch the antistatic package to a metal part of the computer chassis.2.Remove the device from the package and inspect the device for loose components or anyother sign of damage.Caution Never touch the exposed pins of connectors.Note Do not install a device if it appears damaged in any way.3.Unpack any other items and documentation from the kit.Store the device in the antistatic package when the device is not in use.2| | NI PXIe-4080/4081/4082 Getting Started GuidePreparing the EnvironmentEnsure that the environment you are using the NI 4080/4081/4082 in meets the following specifications.Operating EnvironmentAmbient temperature range0 °C to 55 °C (Tested in accordance withIEC 60068-2-1 and IEC 60068-2-2. MeetsMIL-PRF-28800F Class 3 low temperaturelimit and MIL-PRF-28800F Class 2 hightemperature limit.)Relative humidity range10% to 90%, noncondensing (Tested inaccordance with IEC 60068-2-56.)Storage ambient temperature range-40 °C to 70 °C (Tested in accordancewith IEC 60068-2-1 and IEC 60068-2-2.) Maximum altitude2,000 m (800 mbar) (at 25 °C ambienttemperature)Pollution Degree2Indoor use only.Note Refer to the device specifications on /manuals for completespecifications.SafetyCaution Always refer to the specifications document for your device beforeconnecting signals. Failure to observe the specified maximum signal ratings cancause shock, a fire hazard, or damage to the devices connected to theNI 4080/4081/4082. NI is not liable for any damage or injuries resulting fromincorrect signal connections.NI PXIe-4080/4081/4082 Getting Started Guide| © National Instruments| 3Kit ContentsFigure 1.NI 4080/4081/4082 Kit Contents1.NI PXIe-4080/4081/4082 Device2.Test probes3.Driver Software DVD4.NI PXIe-4080/4081/4082 Getting Started Guide (this document)5.Maintain Forced-Air Cooling Note to Users Other EquipmentThere are several required items not included in your device kit that you need to install or operate the NI 4080/4081/4082.•1/8 in. flathead screwdriver• A PXI Express chassis with a controller and the chassis documentation Installing the SoftwareYou must be an Administrator to install NI software on your computer.1.Install an ADE, such as LabVIEW or LabWindows ™/CVI ™.2.Insert the driver software media into your computer. The installer should open automatically.If the installation window does not appear, navigate to the drive, double-click it, and double-click autorun.exe .3.Follow the instructions in the installation prompts.Note Windows users may see access and security messages duringinstallation. Accept the prompts to complete the installation.4 | | NI PXIe-4080/4081/4082 Getting Started Guide4.When the installer completes, select Restart in the dialog box that prompts you to restart,shut down, or restart later.Installing the NI 4080/4081/4082Caution To prevent damage to the NI 4080/4081/4082 caused by ESD orcontamination, handle the module using the edges or the metal bracket.1.Ensure the AC power source is connected to the chassis before installing the module.The AC power cord grounds the chassis and protects it from electrical damage while you install the module.2.Power off the chassis.3.Inspect the slot pins on the chassis backplane for any bends or damage prior toinstallation. Do not install a module if the backplane is damaged.4.Remove the black plastic covers from all the captive screws on the module front panel.5.Identify a supported slot in the chassis. The following figure shows the symbols thatindicate the slot types.Figure 2. Chassis Compatibility Symbols1.PXI Express System Controller Slot2.PXI Peripheral Slot3.PXI Express Hybrid Peripheral Slot4.PXI Express System Timing Slot5.PXI Express Peripheral SlotNI 4080/4081/4082 modules can be placed in PXI Express peripheral slots, PXI Express hybrid peripheral slots, or PXI Express system timing slots.6.Touch any metal part of the chassis to discharge static electricity.7.Ensure that the ejector handle is in the downward (unlatched) position.8.Place the module edges into the module guides at the top and bottom of the chassis. Slidethe module into the slot until it is fully inserted.NI PXIe-4080/4081/4082 Getting Started Guide| © National Instruments| 5Figure 3. Module Installation1.Chassis2.Hardware Module3.Ejector Handle in Downward (Unlatched) Positiontch the module in place by pulling up on the ejector handle.10.Secure the module front panel to the chassis using the front-panel mounting screws.Note Tightening the top and bottom mounting screws increases mechanical stability and also electrically connects the front panel to the chassis, which canimprove the signal quality and electromagnetic performance.11.Cover all empty slots using EMC filler panels or fill using slot blockers to maximizecooling air flow, depending on your application.12.Power on the chassis.Hardware Front Panel ConnectorsRefer to the following figure for the NI 4080/4081/4082 front panels. The front panels have four shrouded banana plug connectors.6 | | NI PXIe-4080/4081/4082 Getting Started GuideConnecting SignalsThe following figures show how to connect signals to the DMM front panel connectors for common measurements.For more information about these common measurements, refer to the NI Digital Multimeters Help at /manuals .Caution Always refer to the device specifications before connecting signals.Failure to observe the specified maximum signal ratings can cause shock, a fireNI PXIe-4080/4081/4082 Getting Started Guide | © National Instruments | 7hazard, or damage to the devices connected to the DMM. NI is not liable for anydamage or injuries resulting from incorrect signal connections.Figure 4. DC and AC VoltageorFigure 5. DC and AC Current8| | NI PXIe-4080/4081/4082 Getting Started GuideFigure 6. 2-Wire and 4-Wire ResistanceNote4-wire resistance measurements use both pairs of terminals. Use the configuration to measure low resistances accurately by eliminating the effects of lead resistance.Figure 7. Capacitance and InductanceNI PXIe-4080/4081/4082 Getting Started Guide| © National Instruments| 9Figure 8. Voltage Drop Across a DiodeRequirements for Cables and ProbesThe DMM shipping kit contains a pair of test probes with safety banana plugs. These probesmeet international safety requirements, including UL 3111 and IEC-1010-1, for the full rangeof applications supported by the DMM.Caution Before using any probes or accessories, ensure that they meet applicablesafety requirements for the signal levels you may encounter.Connect the test probes to the banana plug connectors on the DMM front panel using safetybanana plugs. The shrouds around the banana plugs prevent you from contacting potentiallyhazardous voltages connected to the test probes. You can also connect the cable to standard,unshrouded banana plug probes or accessories. Use unshrouded probes or accessories onlywhen the voltages are less than 30 Vrms and 42 Vpk, or 60 VDC.Caution (NI 4081 users) To prevent possible safety hazards, the maximum voltagebetween any of the inputs and the ground of the PXI Express chassis is 500 VDC or500 Vrms (sine wave), except between the HI terminal and ground, where themaximum voltage is 1,000 VDC or700 Vrms (sine wave). The maximum current theNI 4081 can measure through the current inputs is ±3 ADC or 3 Arms.Caution (NI 4080/4082 users) To prevent possible safety hazards, the maximumvoltage between any of the inputs and the ground of the computer is 300 VDC or300 Vrms. The maximum current the NI 4080/4082 can measure through the currentinputs is ±1 ADC or 1 Arms.10 | | NI PXIe-4080/4081/4082 Getting Started GuideConfiguring the NI 4080/4081/4082 in MAXUse Measurement & Automation Explorer (MAX) to configure your NI hardware. MAX informs other programs about which NI hardware products are in the system and how they are configured. MAX is automatically installed with NI-DMM.unch MAX.2.In the configuration tree, expand Devices and Interfaces to see the list of installed NIhardware.Installed modules appear under the name of their associated chassis.3.Expand your Chassis tree item.MAX lists all modules installed in the chassis. Your default names may vary.Note If you do not see your module listed, press <F5> to refresh the list ofinstalled modules. If the module is still not listed, power off the system, ensurethe module is correctly installed, and restart.4.Record the identifier MAX assigns to the hardware. Use this identifier whenprogramming the NI 4080/4081/4082.5.Self-test the hardware by selecting the item in the configuration tree and clicking Self-Test in the MAX toolbar.The MAX self-test performs a basic verification of hardware resources.Programming the NI 4080/4081/4082You can acquire data interactively using the NI-DMM Soft Front Panel (SFP), or you can use the NI-DMM instrument driver to program your device in the supported ADE of your choice.NI PXIe-4080/4081/4082 Getting Started Guide| © National Instruments| 11Table 1. NI-DMM Programming Options12| | NI PXIe-4080/4081/4082 Getting Started GuideTable 1. NI-DMM Programming Options (Continued)NI-DMM ExamplesThe NI Example Finder is a utility available for some ADEs that organizes examples into categories and allows you to easily browse and search installed examples. You can see descriptions and compatible hardware models for each example, or see all the examples compatible with one particular hardware model.To locate examples, refer to the following table.NI PXIe-4080/4081/4082 Getting Started Guide| © National Instruments| 13Table 2. Locating NI-DMM ExamplesT roubleshootingIf an issue persists after you complete a troubleshooting procedure, contact NI technical support or visit /support.What Should I Do if the NI 4080/4081/4082 Doesn't Appear in MAX?1.In the MAX configuration tree, expand Devices and Interfaces.2.Expand the Chassis tree to see the list of installed hardware, and press <F5> to refreshthe list.3.If the module is still not listed, power off the system, ensure that all hardware is correctlyinstalled, and restart the system.4.Navigate to the Device Manager.Operating System DescriptionWindows 7Select Start»Control Panel»Device Manager.5.If you are using a PXI or PXI Express controller, verify that a National Instrumentsentry appears in the System Devices list. Reinstall NI-DMM and the module if errorconditions appear in the list. If you are using an MXI controller, right-click PCI-to-PCI Bridge, and select Properties from the shortcut menu to verify that the bridge is enabled. 14| | NI PXIe-4080/4081/4082 Getting Started GuideWhat Should I Do if the Module Fails the Self-T est?1.Restart the system.unch MAX, and perform the self-test again.3.Power off the chassis.4.Reinstall the failed module in a different slot.5.Power on the chassis.6.Perform the self-test again.Where to Go NextRefer to the following figure for information about other product tasks and associated resources for those tasks.Worldwide Support and ServicesThe NI website is your complete resource for technical support. At /support, you have access to everything from troubleshooting and application development self-help resources to email and phone assistance from NI Application Engineers.NI PXIe-4080/4081/4082 Getting Started Guide| © National Instruments| 15Visit /services for NI Factory Installation Services, repairs, extended warranty, and other services.Visit /register to register your NI product. Product registration facilitates technical support and ensures that you receive important information updates from NI.A Declaration of Conformity (DoC) is our claim of compliance with the Council of the European Communities using the manufacturer’s declaration of conformity. This system affords the user protection for electromagnetic compatibility (EMC) and product safety. You can obtain the DoC for your product by visiting /certification. If your product supports calibration, you can obtain the calibration certificate for your product at /calibration.NI corporate headquarters is located at 11500 North Mopac Expressway, Austin, Texas, 78759-3504. NI also has offices located around the world. For telephone support in the United States, create your service request at /support or dial 1 866 ASK MYNI (275 6964). For telephone support outside the United States, visit the Worldwide Offices section of / niglobal to access the branch office websites, which provide up-to-date contact information, support phone numbers, email addresses, and current events.Refer to the NI Trademarks and Logo Guidelines at /trademarks for information on NI trademarks. Other product and company names mentioned herein are trademarks or trade names of their respective companies. For patents covering NI products/technology, refer to the appropriate location: Help»Patents in your software, the patents.txt file on your media, or the National Instruments Patent Notice at /patents. Y ou can find information about end-user license agreements (EULAs) and third-party legal notices in the readme file for your NI product. Refer to the Export Compliance Information at /legal/export-compliance for the NI global trade compliance policy and how to obtain relevant HTS codes, ECCNs, and other import/export data. NI MAKES NO EXPRESS OR IMPLIED WARRANTIES AS TO THE ACCURACY OF THE INFORMA TION CONTAINED HEREIN AND SHALL NOT BE LIABLE FOR ANY ERRORS. U.S. Government Customers: The data contained in this manual was developed at private expense and is subject to the applicable limited rights and restricted data rights as set forth in FAR 52.227-14, DFAR 252.227-7014, and DFAR 252.227-7015.© 2015—2016 National Instruments. All rights reserved.。
NI cDAQ
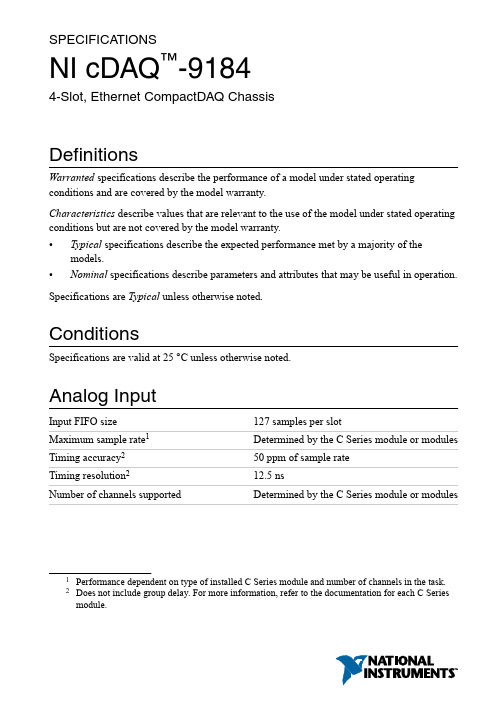
SPECIFICA TIONSNI cDAQ™-91844-Slot, Ethernet CompactDAQ ChassisDefinitionsWarranted specifications describe the performance of a model under stated operating conditions and are covered by the model warranty.Characteristics describe values that are relevant to the use of the model under stated operating conditions but are not covered by the model warranty.•Typical specifications describe the expected performance met by a majority of the models.•Nominal specifications describe parameters and attributes that may be useful in operation. Specifications are Typical unless otherwise noted.ConditionsSpecifications are valid at 25 °C unless otherwise noted.Analog InputInput FIFO size127 samples per slotMaximum sample rate1Determined by the C Series module or modules Timing accuracy250 ppm of sample rateTiming resolution212.5 nsNumber of channels supported Determined by the C Series module or modules 1Performance dependent on type of installed C Series module and number of channels in the task.2Does not include group delay. For more information, refer to the documentation for each C Series module.Analog OutputNumber of channels supportedHardware-timed taskOnboard regeneration16Non-regeneration Determined by the C Series module or modules Non-hardware-timed task Determined by the C Series module or modules Maximum update rateOnboard regeneration 1.6 MS/s (multi-channel, aggregate)Non-regeneration Determined by the C Series module or modules Timing accuracy50 ppm of sample rateTiming resolution12.5 nsOutput FIFO sizeOnboard regeneration8,191 samples shared among channels used Non-regeneration127 samples per slotAO waveform modes Non-periodic waveform,periodic waveform regeneration mode fromonboard memory,periodic waveform regeneration from hostbuffer including dynamic updateDigital Waveform CharacteristicsWaveform acquisition (DI) FIFOParallel modules511 samples per slotSerial modules63 samples per slotWaveform generation (DO) FIFOParallel modules2,047 samples per slotSerial modules63 samples per slotDigital input sample clock frequencyStreaming to application memory System-dependentFinite0 MHz to 10 MHz2| | NI cDAQ-9184 SpecificationsDigital output sample clock frequencyStreaming from application memory System-dependentRegeneration from FIFO0 MHz to 10 MHzFinite0 MHz to 10 MHzTiming accuracy50 ppmGeneral-Purpose Counters/TimersNumber of counters/timers4Resolution32 bitsCounter measurements Edge counting, pulse, semi-period, period,two-edge separation, pulse widthPosition measurements X1, X2, X4 quadrature encoding withChannel Z reloading; two-pulse encoding Output applications Pulse, pulse train with dynamic updates,frequency division, equivalent time sampling Internal base clocks80 MHz, 20 MHz, 100 kHzExternal base clock frequency0 MHz to 20 MHzBase clock accuracy50 ppmOutput frequency0 MHz to 20 MHzInputs Gate, Source, HW_Arm, Aux, A, B, Z,Up_DownRouting options for inputs Any module PFI, analog trigger, many internalsignalsFIFO Dedicated 127-sample FIFOFrequency GeneratorNumber of channels1Base clocks20 MHz, 10 MHz, 100 kHzDivisors 1 to 16 (integers)Base clock accuracy50 ppmOutput Any module PFI terminalNI cDAQ-9184 Specifications| © National Instruments| 3Module PFI CharacteristicsFunctionality Static digital input, static digital output, timinginput, and timing outputTiming output sources3Many analog input, analog output, counter,digital input, and digital output timing signals Timing input frequency0 MHz to 20 MHzTiming output frequency0 MHz to 20 MHzDigital TriggersSource Any module PFI terminalPolarity Software-selectable for most signalsAnalog input function Start Trigger, Reference Trigger,Pause Trigger, Sample Clock,Sample Clock TimebaseAnalog output function Start Trigger, Pause Trigger, Sample Clock,Sample Clock TimebaseCounter/timer function Gate, Source, HW_Arm, Aux, A, B, Z,Up_DownModule I/O StatesAt power-on Module-dependent. Refer to the documentationfor each C Series module.Network InterfaceNetwork protocols TCP/IP, UDPNetwork ports used HTTP:80 (configuration only), TCP:3580;UDP:5353 (configuration only), TCP:5353(configuration only); TCP:31415; UDP:7865(configuration only), UDP:8473 (configurationonly)Network IP configuration DHCP + Link-Local, DHCP, Static,Link-Local3Actual available signals are dependent on type of installed C Series module.4| | NI cDAQ-9184 SpecificationsHigh-performance data streams7Data stream types available Analog input, analog output, digital input,digital output, counter/timer input,counter/timer output, NI-XNET4Default MTU size1500 bytesJumbo frame support Up to 9000 bytesEthernetNetwork interface1000 Base-TX, full-duplex; 1000 Base-TX,half-duplex; 100 Base-TX, full-duplex;100 Base-TX, half-duplex; 10 Base-T,full-duplex; 10 Base-T, half-duplex Communication rates10/100/1000 Mbps, auto-negotiated Maximum cabling distance100 m/segmentPower RequirementsCaution The protection provided by the NI cDAQ-9184 chassis can be impaired ifit is used in a manner not described in the NI cDAQ-9181/9184/9188/9191 UserManual.Note Some C Series modules have additional power requirements. For moreinformation about C Series module power requirements, refer to the documentationfor each C Series module.Note Sleep mode for C Series modules is not supported in the NI cDAQ-9184.V oltage input range9 V to 30 VMaximum power consumption515 W4When a session is active, CAN or LIN (NI-XNET) C Series modules use a total of two data streams regardless of the number of NI-XNET modules in the chassis.5Includes maximum 1 W module load per slot across rated temperature and product variations.NI cDAQ-9184 Specifications| © National Instruments| 5Note The maximum power consumption specification is based on a fully populatedsystem running a high-stress application at elevated ambient temperature and withall C Series modules consuming the maximum allowed power.Power input connector 2 positions 3.5 mm pitch mini-combicon screwterminal with screw flanges, SauroCTMH020F8-0N001Power input mating connector Sauro CTF020V8, Phoenix Contact 1714977,or equivalentPhysical CharacteristicsWeight (unloaded)Approximately 643 g (22.7 oz)Dimensions (unloaded)178.1 mm × 88.1 mm × 64.3 mm(7.01 in. × 3.47 in. × 2.53 in.) Refer to thefollowing figure.Screw-terminal wiringGauge0.5 mm 2 to 2.1 mm2 (20 AWG to 14 AWG)copper conductor wireWire strip length 6 mm (0.24 in.) of insulation stripped from theendTemperature rating85 °CTorque for screw terminals0.20 N · m to 0.25 N · m (1.8 lb · in. to2.2 lb · in.)Wires per screw terminal One wire per screw terminalConnector securementSecurement type Screw flanges providedTorque for screw flanges0.20 N · m to 0.25 N · m (1.8 lb · in. to2.2 lb · in.)If you need to clean the chassis, wipe it with a dry towel.6| | NI cDAQ-9184 SpecificationsFigure 1. NI cDAQ-9184 Dimensions30.6 mm 47.2 mm Safety VoltagesConnect only voltages that are within these limits.V terminal to C terminal30 V maximum, Measurement Category IMeasurement Category I is for measurements performed on circuits not directly connected to the electrical distribution system referred to as MAINS voltage. MAINS is a hazardous liveNI cDAQ-9184 Specifications | © National Instruments | 7electrical supply system that powers equipment. This category is for measurements of voltages from specially protected secondary circuits. Such voltage measurements include signal levels, special equipment, limited-energy parts of equipment, circuits powered by regulatedlow-voltage sources, and electronics.Caution Do not connect the system to signals or use for measurements withinMeasurement Categories II, III, or IV.Note Measurement Categories CAT I and CAT O (Other) are equivalent. These testand measurement circuits are not intended for direct connection to the MAINsbuilding installations of Measurement Categories CAT II, CAT III, or CAT IV.Environmental-20 °C to 55 °C6Operating temperature (IEC 60068-2-1and IEC 60068-2-2)Caution To maintain product performance and accuracy specifications when theambient temperature is between 45 and 55 °C, you must mount the chassishorizontally to a metal panel or surface using the screw holes or the panel mount kit.Measure the ambient temperature at each side of the CompactDAQ system 63.5 mm(2.5 in.) from the side and 25.4 mm (1.0 in.) from the rear cover of the system. Forfurther information about mounting configurations, go to /info and enterthe Info Code cdaqmounting.-40 °C to 85 °CStorage temperature (IEC 60068-2-1 andIEC 60068-2-2)Ingress protection IP 30Operating humidity (IEC 60068-2-56)10% to 90% RH, noncondensingStorage humidity (IEC 60068-2-56)5% to 95% RH, noncondensingPollution Degree (IEC 60664)2Maximum altitude5,000 mIndoor use only.6When operating the NI cDAQ-9184 in temperatures below 0 °C, you must use the PS-15 powersupply or another power supply rated for below 0 °C.8| | NI cDAQ-9184 SpecificationsHazardous LocationsU.S. (UL)Class I, Division 2, Groups A, B, C, D, T4;Class I, Zone 2, AEx nA IIC T4Canada (C-UL)Class I, Division 2, Groups A, B, C, D, T4;Class I, Zone 2, Ex nA IIC T4Europe (ATEX) and International (IECEx)Ex nA IIC T4 GcShock and VibrationTo meet these specifications, you must direct mount the NI cDAQ-9184 system and affix ferrules to the ends of the terminal lines.Operational shock30 g peak, half-sine, 11 ms pulse (Tested inaccordance with IEC 60068-2-27. Test profiledeveloped in accordance withMIL-PRF-28800F.)Random vibrationOperating 5 Hz to 500 Hz, 0.3 g rmsNon-operating 5 Hz to 500 Hz, 2.4 g rms (Tested in accordancewith IEC 60068-2-64. Non-operating testprofile exceeds the requirements ofMIL PRF-28800F, Class 3.)Safety and Hazardous Locations StandardsThis product is designed to meet the requirements of the following electrical equipment safety standards for measurement, control, and laboratory use:•IEC 61010-1, EN 61010-1•UL 61010-1, CSA C22.2 No. 61010-1•EN 60079-0:2012, EN 60079-15:2010•IEC 60079-0: Ed 6, IEC 60079-15; Ed 4•UL 60079-0; Ed 6, UL 60079-15; Ed 4•CSA 60079-0:2011, CSA 60079-15:2012Note For UL and other safety certifications, refer to the product label or the OnlineProduct Certification section.NI cDAQ-9184 Specifications| © National Instruments| 9Electromagnetic CompatibilityThis product meets the requirements of the following EMC standards for electrical equipment for measurement, control, and laboratory use:•EN 61326-1 (IEC 61326-1): Class A emissions; Basic immunity•EN 55011 (CISPR 11): Group 1, Class A emissions•EN 55022 (CISPR 22): Class A emissions•EN 55024 (CISPR 24): Immunity•AS/NZS CISPR 11: Group 1, Class A emissions•AS/NZS CISPR 22: Class A emissions•FCC 47 CFR Part 15B: Class A emissions•ICES-001: Class A emissionsNote In the United States (per FCC 47 CFR), Class A equipment is intended foruse in commercial, light-industrial, and heavy-industrial locations. In Europe,Canada, Australia and New Zealand (per CISPR 11) Class A equipment is intendedfor use only in heavy-industrial locations.Note Group 1 equipment (per CISPR 11) is any industrial, scientific, or medicalequipment that does not intentionally generate radio frequency energy for thetreatment of material or inspection/analysis purposes.Note For EMC declarations and certifications, and additional information, refer tothe Online Product Certification section.CE ComplianceThis product meets the essential requirements of applicable European Directives, as follows:•2014/35/EU; Low-V oltage Directive (safety)•2014/30/EU; Electromagnetic Compatibility Directive (EMC)•2014/34/EU; Potentially Explosive Atmospheres (ATEX)Online Product CertificationRefer to the product Declaration of Conformity (DoC) for additional regulatory compliance information. To obtain product certifications and the DoC for this product, visit / certification, search by model number or product line, and click the appropriate link in the Certification column.10| | NI cDAQ-9184 SpecificationsEnvironmental ManagementNI is committed to designing and manufacturing products in an environmentally responsible manner. NI recognizes that eliminating certain hazardous substances from our products is beneficial to the environment and to NI customers.For additional environmental information, refer to the Minimize Our Environmental Impact web page at /environment. This page contains the environmental regulations and directives with which NI complies, as well as other environmental information not included in this document.Waste Electrical and Electronic Equipment (WEEE) EU Customers At the end of the product life cycle, all NI products must bedisposed of according to local laws and regulations. For more information abouthow to recycle NI products in your region, visit /environment/weee.电子信息产品污染控制管理办法(中国RoHS)中国客户National Instruments符合中国电子信息产品中限制使用某些有害物质指令(RoHS)。
staad foundation advanced v8i 更新内容说明书
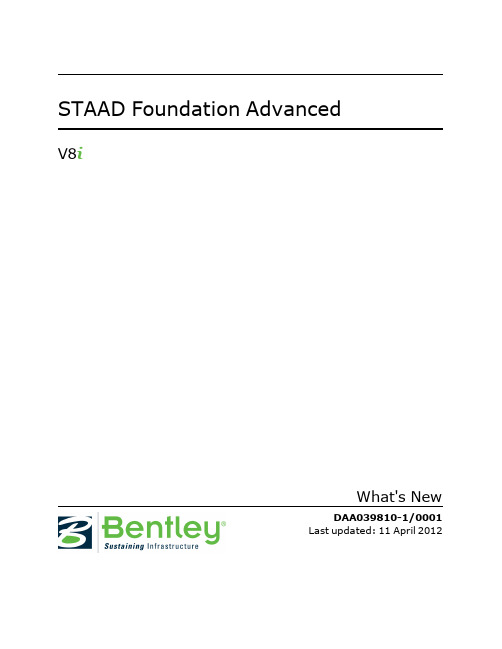
1
2 Anchor Bolt Library
2
3 Isolated Footing Enhanced Drawing
5
4 Concrete Check Options
6
5 Bearing Capacity Type
7
6 Compression Development Length for Isolated Foot-
1.1 To create or update an ISM Repository
1. Click the STAAD Foundation Application button and select Sync ISM from the application menu.
2. Select either:
It consists of following key features l Auto-scaled views l True scale reinforcement along with thickness for congestion detection l Anchor bolt overlay on pedestal reinforcement l Concrete grout, leveling concrete, Project Elevation options l Revised Title Block
Select to…
this…
Update update an existing ISM repository with data Repository form your STAAD Foundation project.
Create
create a new ISM repository from your
特斯拉电动汽车用户手册说明书
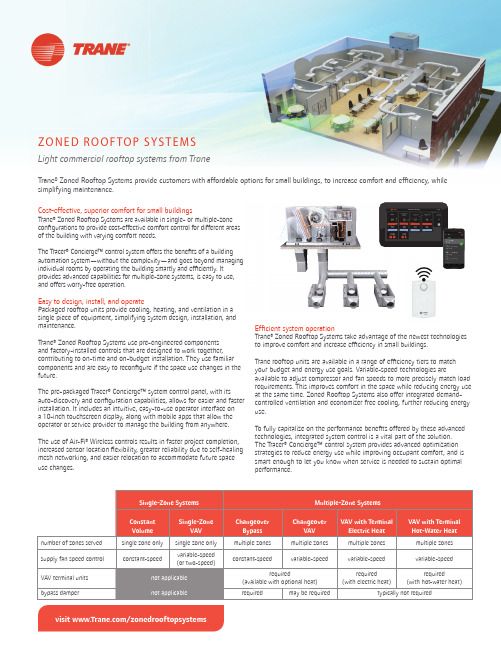
visit /zonedrooftopsystemsEf fi cient system operationTrane® Zoned Rooftop Systems take advantage of the newest technologies to improve comfort and increase ef fi ciency in small buildings.Trane rooftop units are available in a range of ef fi ciency tiers to match your budget and energy use goals. Variable-speed technologies areavailable to adjust compressor and fan speeds to more precisely match load requirements. This improves comfort in the space while reducing energy use at the same time. Zoned Rooftop Systems also offer integrated demand-controlled ventilation and economizer free cooling, further reducing energy use.To fully capitalize on the performance bene fi ts offered by these advanced technologies, integrated system control is a vital part of the solution. The Tracer® Concierge™ control system provides advanced optimization strategies to reduce energy use while improving occupant comfort, and is smart enough to let you know when service is needed to sustain optimal performance.Cost-effective, superior comfort for small buildingsTrane® Zoned Rooftop Systems are available in single- or multiple-zone con fi gurations to provide cost-effective comfort control for different areas of the building with varying comfort needs.The Tracer® Concierge™ control system offers the bene fi ts of a building automation system—without the complexity—and goes beyond managing individual rooms by operating the building smartly and ef fi ciently. It provides advanced capabilities for multiple-zone systems, is easy to use, and offers worry-free operation.Easy to design, install, and operatePackaged rooftop units provide cooling, heating, and ventilation in a single piece of equipment, simplifying system design, installation, and maintenance.Trane® Zoned Rooftop Systems use pre-engineered components and factory-installed controls that are designed to work together, contributing to on-time and on-budget installation. They use familiar components and are easy to recon fi gure if the space use changes in the future.The pre-packaged Tracer® Concierge™ system control panel, with its auto-discovery and con fi guration capabilities, allows for easier and faster installation. It includes an intuitive, easy-to-use operator interface on a 10-inch touchscreen display, along with mobile apps that allow the operator or service provider to manage the building from anywhere.The use of Air-Fi® Wireless controls results in faster project completion, increased sensor location fl exibility, greater reliability due to self-healing mesh networking, and easier relocation to accommodate future space use changes.ZO N E D R O O F TO P S YS T E M SLight commercial rooftop systems from TraneTrane® Zoned Rooftop Systems provide customers with affordable options for small buildings, to increase comfort and ef fi ciency, whilesimplifying maintenance.VAV terminal units (200 to 8000 cfm)• Trane fl ow ring provides unmatched air fl ow measurement accuracy and control • Durable, heavy-gauge air valve cylinder• modulating control• Air-Fi® Wireless communications • Retro fit dampers available for upgrading existing systemsTrane - by Trane Tech nologies (NYSE: TT), a global climate innovator - creates comfortable, energy efficient indoor environments for commercial and residential applications. For more information, please visit or .Trane h as a policy of continuous product and product data improvement and reserves th e righ t to ch ange design and specifications without notice. We are committed to using environmentally conscious print practices.All trademarks referenced are the trademarks of their respective owners.©2020 Trane. All Rights Reserved. ENV-SLB024C-ENNovember 5, 2020•single piece of equipment• able-speed fan control• Three tiers of effi ciency: standard, high, or ultra-high•••Pre-programmed, factory-installed ReliaT el™ DDC controls with wired or Air-Fi® Wireless communicationsAir-Fi® Wireless controls• Eliminates wires between equipment controllers and zone sensors, and between equipment and system controllers, allowing for faster installation, increased location fl exibility, and easier relocation• Self-healing wireless mesh and extended signal range maximize reliability• Supports open communication protocols through conformance with ASHRAE® Standard 135 (BACnet®/ZigBee®)• Up to four sensing functions in one zone sensor: temperature, humidity, occupan-cy, and CO 2• 15-year lifetime batteries。
Oracle Database Administration 2019 认证说明书
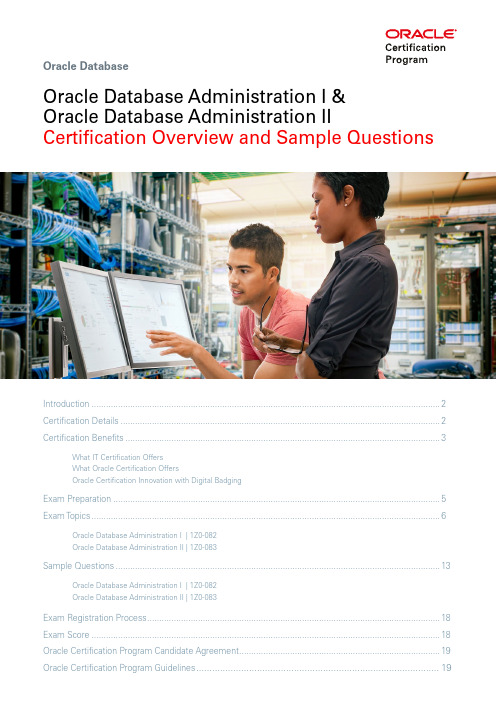
Introduction ................................................................................................................................................2Certification Details ....................................................................................................................................2Certification Benefits . (3)What IT Certification Offers What Oracle Certification OffersOracle Certification Innovation with Digital BadgingExam Preparation .......................................................................................................................................5Exam Topics (6)Oracle Database Administration I | 1Z0-082Oracle Database Administration II | 1Z0-083Sample Questions (13)Oracle Database Administration I | 1Z0-082Oracle Database Administration II | 1Z0-083Exam Registration Process .........................................................................................................................18Exam Score ................................................................................................................................................18Oracle Certification Program Candidate Agreement ...................................................................................19Oracle Certification Program Guidelines .. (19)Oracle Database Administration I & Oracle Database Administration IICertification Overview and Sample QuestionsOracle DatabaseIntroductionPreparing to earn the Oracle Database Administration 2019 Certified Professional certification helps candidates gain the skills and knowledge to install, patch and upgrade Oracle Database and Oracle Grid Infrastructure for a standalone server, create and manage a backup and recovery strategy using Recovery Manager (RMAN), use RMAN for Database duplication and transportation, diagnose failures using RMAN, and manage all aspects of Multitenant container databases, pluggable databases and application containers including creation, cloning, security, transportation and backup and recovery. The Administration I exam and recommended training focus on fundamental Database Administration topics such as understanding the database architecture, managing database instances, managing users, roles and privileges, and managing storage that lay the foundation for a Database Administrator entry-level job role. Additionally, the Admin I exam assumes knowledge of SQL.The Administration II exam and associated recommended training presents advanced topics such as multi-tenancy, backup and recovery, deploying, patching, and upgrading.Certification BenefitsWhat Oracle Certification OffersBy becoming a certified Oracle Database Administrator Professional , you demonstrate the full skill set needed to perform day to day administration of the Oracle Database.Preparing to take the Oracle Database certification exam broadens your knowledge and skills by exposing you to a wide array of important database features, functions and tasks. Oracle Database certification preparation teaches you how to perform complex, hands-on activities through labs, study and practice.Additionally, Oracle certification exams validate your capabilities using real-world, scenario-based questions that assess and challenge your ability to think and perform.What IT Certification OffersRecognitionof having required skillsExperienced a Greater Demandfor Their SkillsReceived Positive Impact onProfessional Imagethrough new skillsOpportunitiesSaid Certification was a Key Factor in Recent Raiseby peers and managementConfidence and RespectJanuary 2018 issue of Certification Magazine’s annual salary survey The kind of longevity suggests that earning and maintaining a certification can keep you moving for-ward in your career, perhaps indefinitely.73%65%71%January 2019 issue of Certification Magazine’s annual salary survey January 2019 issue of Certification Magazine’s annual salary surveyCertification that Signifies Y our Readiness to Perform Earned badges represent recognized skills and capabilitiesDisplay Y our Oracle Certification BadgeY ou‘ve earned it. Get the recognition you deserve.Modern Representation of Skills Tied to Real Time Job Markets View from your profile and apply to jobs that are matched to your skills; based on location, title, employers or salary rangeDisplay Y our AchievementA secure way to display and share your certification achievement • Industry Recognized • Credible • Role Based• Product Focused Across Database, Applications, Cloud, Systems, Middleware and Java• Globally one of the top 10 certifica-tion programs availableOracle Certification Innovation with Digital Badging Use Your Badge to Apply for JobsBenefitsOracle Certification Signifies a Candidate’s Readiness to Perform2019 Oracle Certified Professional Oracle Database AdministratorBoost Y our Professional ImageLearn MoreExam PreparationBy passing these exams, a certified individual proves fluency in and solid understanding of the skills required to be an Oracle Database Administrator.Recommendations to successfully prepare for Oracle Database Administration I | 1Z0-082 and Oracle Database Administration II | 1Z0-083 exams are:Attend Recommended Oracle T rainingThe courses below are currently available and are terrific tools to help you prepare not only for your exams, but also for your job as an Oracle Database Administrator.The new Oracle Database Administration Learning Subscription also helps you prepare for these exams with 24/7 access to continually updated training and hands-on labs and integrated certification.Recommended for 1Z0-082• O racle Database: Administration Workshop • Oracle Database: Introduction to SQL Recommended for 1Z0-083• O racle Database: Deploy, Patch and Upgrade Workshop• O racle Database: Backup and Recovery Workshop • O racle Database: Managing Multitenant Architecture• Oracle Database Administration: Workshop • O racle Database 19c: New Features for Administrators• O racle Database 18c: New Features forAdministrators (for 10g and 11g OCAs and OCPs)• O racle Database 12c R2: New Features for 12c R1 Administrators (12c R1 OCAs and OCPs)• O racle Database 11g: New Features for Administrators (for 10g OCAs and OCPs)The following topics are covered in the Oracle Database: Administration Workshop course.The following topics are covered in theOracle Database: Introduction to SQL course.The following topics are covered in the Oracle Database: Managing Multitenant Architecture Ed 1 course.The following topics are covered in the Oracle Database: Backup and Recovery Workshop course.The following topics are covered in the Oracle Database: Deploy, Patch and Upgrade Workshop course.The following topics are covered in the Oracle Database 19c: New Features for Administrators course.The following topics are covered in the Oracle Database: Administration Workshop course1. Which two statements are true about the Oracle Database server architecture?A. An Oracle Database server process represents the state of a user’s login to an instance.B. An Oracle Database server process is always associated with a session.C. Each server process has its own User Global Area (UGA).D. A connection represents the state of a user’s login to an instance.E. The entire data dictionary is always cached in the large pool.2. W hich two statements are true about the Oracle Database server during and immediatelyafter SHUTDOWN IMMEDIATE?A. New connection requests made to the database instance are refused.B. Uncommitted transactions are rolled back automatically.C. All existing connections to the database instance remain connected until all transactions eitherroll back or commit.D. Uncommitted transactions are allowed to continue to the next COMMIT.E. All existing transactions are aborted immediately.3. Which three statements are true about Oracle database block space management?A. A row can be migrated to a block in a different extent than the extent containing the originalblock.B. An insert statement can result in a migrated row.C. An update statement cannot cause chained rows to occur.D. A row can be migrated to a block in the same extent as the extent containing the originalblock.E. An insert statement can result in a chained row.1 2. 3.4. A n Oracle Database server session has an uncommitted transaction in progress whichupdated 5000 rows in one table.In which two situations does the transaction complete, thereby committing the updates?A. When a DDL statement is executed successfully by same user in a different session.B. When a DDL statement is executed successfully by the user in the same session.C. When a DML statement is executed successfully by same user in a different session.D. When a DML statement is executed successfully by the user in the same session.E. When a DBA issues a successful SHUTDOWN NORMAL statement and the sessionterminates normally.5.Which two statements are true about indexes and their administration in an Oracle database?A. An index can be scanned to satisfy a query without the indexed table being accessed.B. A non-unique index can be converted to a unique index using a Data Definition Language(DDL) command.C. A descending index is a type of bitmapped index.D. An invisible index is maintained when a Data Manipulation Language (DML) command is per-formed on its underlying table.E. An index is always created by scanning the key columns from the underlying table.6. Which two statements are true about sequences in a single instance Oracle database?A. Sequences that start with 1 and increment by 1 can never have gaps.B. A sequence can issue the same number more than once.C. Sequence numbers that are allocated require a COMMIT statement to make the allocationpermanent.D. A sequence can provide numeric values for more than one column or table.E. The data dictionary is always updated each time a sequence number is allocated.4. 5. 6.7. E xamine the description of the SALES table:Name Null? Type---------------------------- -------- --------------PRODUCT_ID NOT NULL NUMBER(10)CUSTOMER_ID NOT NULL NUMBER(10)TIME_ID NOT NULL DATECHANNEL_ID NOT NULL NUMBER(5)PROMO_ID NOT NULL NUMBER(5)QUANTITY_SOLD NOT NULL NUMBER(10,2)PRICE NUMBER(10,2)AMOUNT_SOLD NOT NULL NUMBER(10,2)The SALES table has 55,000 rows.Examine this statement:CREATE TABLE mysales (prod_id, cust_id, quantity_sold, price)ASSELECT product_id, customer_id, quantity_sold, priceFROM salesWHERE 1 = 2;Which two statements are true?A. MYSALES is created with no rows.B. MYSALES will have no constraints defined regardless of which constraints might be de-fined on SALES.C. MYSALES has NOT NULL constraints on any selected columns which had that constraintin the SALES table.D. MYSALES is created with 2 rows.E. MYSALES is created with 1 row.71. Which three are true about an application container?A. It always contains multiple applications.B. Two or more application PDBs in the same application container can share access to tables.C. It can have new application PDBs created by copying PDB$SEED.D. T wo or more application PDBs in the same application container can be given exclusive accessto some tables.E. It always has a new application PDBs created by copying PDB$SEED.F. It always contains a single application.2. RMAN has just been connected to a target database and the recovery catalog database.In which two cases would an automatic partial resynchronization occur between this target database’s control file and the RMAN recovery catalog?A. When any control file metadata for data file backups or image copies is now older thanCONTROL_FILE_RECORD_KEEP_TIME.B. When a new data file is added to a tablespace in a registered target database.C. When a backup of the current SPFILE is created.D. When the target is first registered.E. When any control file metadata for archive log backups or image copies is now older thanCONTROL_FILE_RECORD_KEEP_TIME.3. Which two are true about Oracle Grid Infrastructure for a Standalone Server?A. Oracle Restart can be used without using ASM for databases.B. Oracle Restart can attempt to restart a failed ASM instance automatically.C. It must be installed before Oracle Database software is installed.D. It must be installed after Oracle Database software is installed.E. It allows ASM binaries to be installed without installing Oracle Restart.F. It allows Oracle Restart binaries to be installed without installing ASM.1 2. 3.4. W hich two are true about creating container databases (CDBs) and pluggable databases (PDBs) inOracle 19c and later releases?A. A CDB can be duplicated using the Database Configuration Assistant (DBCA) in silent mode.B. A CDB can be duplicated using Recovery Manager (RMAN) with no configuration requiredbefore starting the duplication.C. A PDB snapshot must be a full copy of a source PDB.D. A PDB snapshot can be a sparse copy of a source PDB.E. A CDB can be duplicated only by using the Database Configuration Assistant (DBCA).5. Which two are true about the Oracle Optimizer?A. It requires system statistics when generating SQL execution plans.B. It always generates an index access operation when a statement filters on an indexed columnwith an equality operator.C. It ignores stale object statistics in the Data Dictionary.D. It can automatically re-optimize execution plans that were detected to be sub-optimal whenexecuting.E. It can re-write a statement internally in order to generate a more optimal plan.4. 5.Exam Registration ProcessOracle exams are delivered through the independent company Pearson VUE. Create a Pearson VUE loginOracle Certification Program Candidate AgreementIn order to take your Oracle certification, you will need to agree to the Oracle Certification Program Candidate Agreement. Please review this document by going here.Oracle Certification Program GuidelinesLearn more about Oracle Certification policies here.This certification overview and sample questions were created in June 2019. The content is subject to change,please always check the web site for the most recent information regarding certifications and related exams: /certification。
Oracle Essbase Integration Services 11.1.1.3 发行版说明

Oracle® Essbase Integration ServicesRelease 11.1.1.3Readme[Skip Navigation Links]About This Service Fix (1)New Features (1)Defects Fixed (1)Known Issues in Release 11.1.1.3 (3)Documentation Updates (6)About This Service FixThis Readme file describes the defects fixed in Oracle® Essbase Integration Services Service Pack11.1.1.3 as well as the known issues in this release.Top of Document New FeaturesCertification MatrixInformation about system requirements for EPM System products is now available in a spreadsheet format in the Oracle Hyperion Enterprise Performance Management System Certification Matrix, posted at /technology/products/bi/hyperion-supported-platforms.html. Systemrequirements are no longer part of the Oracle Hyperion Enterprise Performance Management System Installation Start Here.Supported LanguagesThis release supports non-English languages. The list of supported languages for all EPM System products is included in the Oracle Hyperion Enterprise Performance Management System Certification Matrix, posted at /technology/products/bi/hyperion-supported-platforms.html.Top of Document Defects FixedDefects Fixed in Release 11.1.1.3•Member load. In the batch file created for EIS scheduling for member loads, the path was not updated to include the start command.(8439772)•Console. Creating the fact table by selecting the Menu > Tools option failed.(8403636)•Data load. Batch file executed during data loads falsely reported that load was terminated with errors despite data load being successful.(8412247, 8304235, 8269211)•Console. Integration Services Console was not granting re-access to users after they exited the application because user ID information was not being cached.(8412193, 7714801)•Data and member loads. Data and member loads failed when run from a .cbs script, but Integration Services status indicated the load was successful.(8412254, 8304252, 7721750)Defects Fixed in Release 11.1.1.2These defects are fixed in Integration Services release 11.1.1.2. The defect number follows thedescription of the defect.Drill-Through Template SQL. Incorrect table alias names were generated in the SQL query created by Integration Server.(6584510, 8-631137724)Drill-Through Template SQL. Integration Server terminated abnormally when verifying Drill-Through Template SQL.(6851055)Data Load. When the Default Miscellaneous Member option was enabled for the aggregate storage option, the default members were not added and the data load failed. The data load failure has been addressed; however, you may need to reload any rejected records.(7607685, 7268275)Defects Fixed in Release 11.1.1.1These defects are fixed in Integration Services release 11.1.1.1. The defect number follows thedescription of the defect.Console. When building a cube in Integration Services Release 9.3.1., using a metaoutline that been generated in Release 7.x, a false error condition sometimes prevented users from building the cube.(7138407)Console. When several batch jobs for data loads were run consecutively, and one or more scripts had empty parameters, Integration Services would sometimes shut down, forcing a manual restart.(7212289)Load. In data loads, the displayed total of records loaded and records rejected exceeded the number of records in the outline.(7310328, 7158311)Drill-Through. If users changed passwords, sometimes drill-through report operations would fail because of encryption errors.(7360009, 7393959)Top of DocumentKnown Issues in Release 11.1.1.3The following issues are the noteworthy known issues of this release.ODBC Notes•“Localhost” is not a valid server name. In the Login dialog box, you must specify a computer name or IP address in both the Integration Server frame and the Essbase Server frame.•For UNIX systems, Integration Services installation creates a template odbc.ini. To store information about how to connect to a relational data source, edit the file using your preferrededitor.•To configure a Teradata data source, the TDODBC environment variable must be set manually. Configuration File Entry for DB2 OS/390DB2 OS/390 is supported only as a data source and should not be used as an OLAP Metadata Catalog.If you use IBM DB2 OS/390 as a data source, you must add an entry to the ais.cfg file for each data source name you configured in your DataDirect Wire Protocol driver for DB2. Add an entry to the ais.cfg file in the following format: [DS:dsn:390]. For example, using the sample database, TBC, the following is the entry to the ais.cfg file:[DS:TBC:390]JISX0213 Japanese Character Set Not SupportedThe JISX0213 Japanese character set, which replaces the JISX0208 and JISX0212 Japanese character sets, is supported on Windows Vista.The Oracle Essbase family of products, including Integration Services, does not support the JISX0213 Japanese character set. (6576813, 8-563756229)Windows Server 2003 SP1 May Experience Abnormal ShutdownIf you are using Windows Server 2003 Service Pack 1 with Integration Services, your system may experience an abnormal shutdown. To prevent this, install the update from Microsoft by going to: /kb/923996/Column Names with 0x5C Double-byte Characters May Not DisplayIf column names contain 0x5C double-byte characters, the columns may not display in a table.(6551802, 2-HYPER00071286)MBCS Characters Should Not Be Used in Names of Some Entities Multibyte-character-set characters should not be used in the names of these entities:•OLAP models•Metaoutlines•Data sources•Owners(6550123; 2-HYPER00073848, 73905, 73906, 73910, and 74122)Oracle Database as Unicode Data SourceIf you run Integration Services on Windows and access an Oracle database as an MBCS or Unicode data source using the DataDirect Wire Protocol Driver, characters corresponding to 0x4E88 in UTF-8 encoding may not be processed properly.Time-based Incremental Load LimitationDue to database restrictions in some databases such as Oracle, if the IN clause has more than 1,000 outline members that require updating during time-based incremental loads, SQL statements may not execute. In such cases, we recommend full loads rather than time-based incremental loads.Unable to Validate @ISUDA FunctionsAlthough Oracle Essbase Administration Services validates recently added functions in formulas for the block storage option (BSO), Integration Services may not. We strongly recommend you use Oracle Essbase Administration Services to validate these functions.Japanese EncodingIf you use Japanese encoding, Oracle recommends you use MS932 encoding instead of Shift-JIS.Specifying Ancestors in Template SQL for Drill-Through Operations on Duplicate MembersIn general, Oracle does not recommend using Drill-Template SQL for OLAP metaoutlines that support duplicate member names.If you still choose to use Drill-Through Template SQL for OLAP metaoutlines that support duplicate member names, Oracle suggests you take the following actions in order for Drill-Through Template SQL to function correctly:•Associate database keys for the drill-through-enabled members.To do this, in the General tab of the Member Properties dialog box for each drill-through-enabled member, in the Member Key Column drop-down list, select the appropriate database key columns for the drill-through-enabled members.These actions are valid for drill-through reports defined on any member level, including level zero members.•For drill-through defined on level zero members (leaf nodes), you can also fully identify a duplicate member by specifying all the ancestors for that member in Template SQL.In the following example of Template SQL using the TBC sample, for a drill-through intersectiondefined on Product.SKU, a WHERE clause was added (see bolded text) for the ancestor of SKU in order to fully define the member:SELECT DISTINCT ac."SKU", ac."SKU_ALIAS", ac."CAFFEINATED", ac."OUNCES",ac."PKGTYPE", ac."INTRODATE", aa."SUPPLIERID", ad."SUPPLIER_ALIAS", ad."ADDRESS", ad."CITY", ad."STATE", ad."ZIP", ad."COUNTRY"FROM TBC.SALES aa, TBC.PRODUCTDIM ab, TBC.PRODUCT ac, TBC.SUPPLIER adWHERE aa."PRODUCTID" = ac."PRODUCTID"AND aa."SUPPLIERID" = ad."SUPPLIERID"AND ac."SKU" = ab."SKU"AND ((($$Year-COLUMN$$ IN ( $$Year-VALUE$$))))AND (ab."FAMILY" in ('100'))AND (((ab."FAMILY" in ('100','200','300','400','Diet')) AND ($$Product-COLUMN$$ IN ( $$Product-VALUE$$))))The caveat to the solution given in the above example is that the member is fully defined only for children of Product 100; it is not practical to define Template SQL for every possible ancestor value.(6807790, 1-156SS6)Runtime Filter Condition Limitation for Customized Drill-Through OperationsIf you customize drill-through reports at run time and add a user-defined filter, keep the length of the filter under 8KB; otherwise, some members may not be included in the drill-through report query.(1-147T5F)Users Without Create Access to Essbase Server Cannot Verify Member FormulasTo verify member formulas, users must have Create access to the Essbase Server.(1-82215061)Updating Drill-Through Reports Not Supported for Outlines Containing Duplicate Member NamesRelease 11.1.1 does not support updating drill-through information in an outline containing duplicate member names. For such outlines, you should perform a full member load.Drill-Through Operations Are Not Supported on Unicode Data in Release 11.1.1 Records Rejected During Data Load when Alternate Fact Table SelectedIf the Time dimension is built directly from the fact table, and you select an alternate fact table, the data load may reject those records for which time members are not found in Oracle Essbase. In such cases, be sure that the time dimension is built to span time periods of all fact tables.(1-194924642)SQL Server 2005 Requires Name of New Executable in Sample Creation Scripts to Create TBC Sample Tables and to Load Sample DataThe current batch files and scripts used to create the TBC sample tables and to load the sample data do not function with SQL Server 2005. These files require the executable named SQLCMD.EXE.WORKAROUND: Edit the batch file install_sqlsrv.bat located in the AIS\samples directory, and replace the name of the executable ISQL.EXE with the new executable name SQLCMD.EXE.(8-532792001)Application Naming RestrictionsWhen managing Oracle’s Hyperion Shared Services models and naming applications, you cannot use the forward slash (/), backslash (\), or double quotation (“) characters.(8-514151218)Read-only Permission to External Data Sources for Drill-Through ReportsOracle recommends that your users be granted read-only permission to external data sources for drill-through reports and custom data load SQL.Adding Alternate Hierarchy a Second Time Duplicates ValuesWhen building a shared hierarchy for a block storage database, adding a shared hierarchy a second time may duplicate the values stored on a single element, resulting in incorrect data. This problem occurs when shared members are from the same hierarchy, such as these two hierarchies from theTBC sample database: Diet > 100-20 and 100 > 100-20.WORKAROUND: Use user-defined SQL to edit data load commands.(6584211)Start and Stop Controls for Windows Service on Windows 2003 SP1On Windows 2003 SP1, after installing Integration Services, the EPM System Installer uses Windows services to start and stop the services for Integration Services. Sometimes after stopping the service using Windows Services console, the Integration Server process, olapisvr.exe, continues to run.WORKAROUND: Manually stop the “olapisvr.exe” and “olapisvc.exe” processes by using the Windows Task Manager.(7253757)Long Table and Column Names Truncated in the Drill-Through WizardWhen using the Drill-Through Wizard in Essbase Spreadsheet Add-in, users will only see the first 80 characters of the table or column name.(6536313)System Limitations•Integration Services supports full Unicode functionality only on Oracle relational database servers.•Oracle recommends you use the same language for your Data source names as you use for your applications. (English will work in all cases.)•When creating a drill-through report with an OLAP intersection level based on a user-defined dimension or column, neither of the variables of the form $$dimension-COLUMN$$ or $$dimension-VALUE$$ will be created.•To retain and upgrade Dynamic Time Series settings made in Integration Services prior to release6.5.4, open and save the metaoutline using release 11.1.1. For recursive and alternate hierarchies,we recommend that you verify your settings.•Integration Services does not support user-defined tables created in Sybase or Informix.Top of Document Documentation UpdatesAccessing Hyperion Product DocumentationThe most recent version of each Hyperion product guide is available for download from theDocumentation area of the Oracle Technology Network (OTN) Web site(/technology/index.html). Deployment-related documentation is also availablefrom the Oracle E-Delivery Web site (/EPD/WelcomePage/get_form).Individual product guides are available for download on the Oracle Technology Network (OTN) Web site only.Note: Not all of the documentation for this product has been updated from Release 11.1.1.1 or11.1.1.2. Similarly, the product UI may not have been updated from Release 11.1.1.1 or 11.1.1.2. Oracle Call Interface No Longer SupportedOracle® Essbase Integration Services no longer supports Oracle Call Interface (OCI). References in the documentation to OCI should be disregarded.Top of DocumentCopyright © 2009, Oracle and/or its affiliates. All rights reserved.。
IBM Tivoli Enterprise Portal用户指南说明书

IBM Software Group | Tivoli software
Agenda
The Tivoli Enterprise Portal And Integrated Performance And Availability Automation About Situations And Policies Situation Review Policies – Definition And Deployment Policy Usage Recommendations And Best Practices Summary And Questions
The TEP provides multiple command options
Manual ‘Take Action’, Situations, Policies
Take Action provides for manual command capability
Commands may be predefined
Situations remain the essential starting point Policies add additional function and flexibility Policies run within the TEMS infrastructure
6
IBM Software Group | Tivoli software
Note - Policy automation requires OMEGAMON Dashboard Edition (DE) which is a separately licensable item on z/OS
4
IBM Software Group | Tivoli software
Transition Networks CPSMC18xx-xxx 18-Slot PointSys
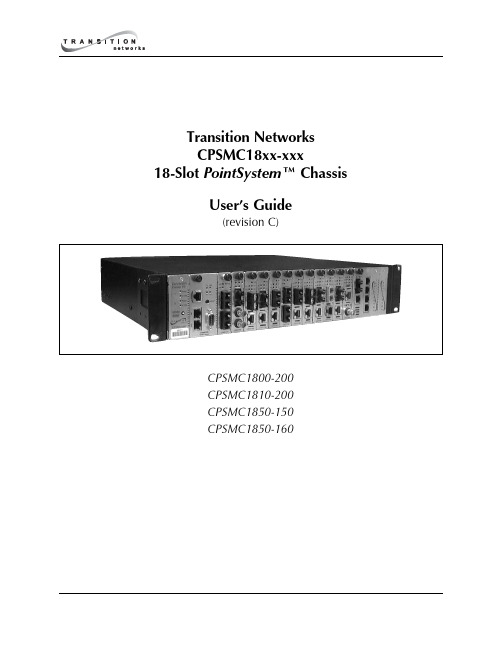
Table of Contents1Introduction . . . . . . . . . . . . . . . . . . . . . . . . . . . . . . . . . . . . . . .51.1Description . . . . . . . . . . . . . . . . . . . . . . . . . . . . . . . . . . . . . . . . . .51.2Unpacking the CPSMC18xx-xxx Equipment . . . . . . . . . . . . . . . . . .72Slide-in-Modules . . . . . . . . . . . . . . . . . . . . . . . . . . . . . . . . . . .82.1Media Converter Slide-in-Modules . . . . . . . . . . . . . . . . . . . . . . . . .82.1.1Chassis Face Plates . . . . . . . . . . . . . . . . . . . . . . . . . . . . . . . . . . .82.1.2Calculating the Power Consumption . . . . . . . . . . . . . . . . . . . . . .82.1.3Installing the Media Converter Slide-in-Modules . . . . . . . . . . . . .92.1.4Replacing the Media Converter Slide-in-Modules . . . . . . . . . . .102.2Management Modules . . . . . . . . . . . . . . . . . . . . . . . . . . . . . . . . .112.2.1Three Types of Management Modules . . . . . . . . . . . . . . . . . . . .112.2.2Installing the Management Modules . . . . . . . . . . . . . . . . . . . . .122.2.3Replacing the Management Modules . . . . . . . . . . . . . . . . . . . . .133Powering the CPSMC18xx-xxx . . . . . . . . . . . . . . . . . . . . . . . .143.1AC Power Supply Module . . . . . . . . . . . . . . . . . . . . . . . . . . . . . .143.2DC Power Supply Module . . . . . . . . . . . . . . . . . . . . . . . . . . . . . .163.3Optional Dual Power Supply Modules . . . . . . . . . . . . . . . . . . . . .183.4Power Supply Module Maintenance . . . . . . . . . . . . . . . . . . . . . .193.4.1Primary/Secondary-Management/Manual Switch . . . . . . . . . . . .193.4.2Installing the Power Supply Module . . . . . . . . . . . . . . . . . . . . . .203.4.3Replacing the Power Supply Module . . . . . . . . . . . . . . . . . . . . .213.4.4Replacing the Power Supply Fuses . . . . . . . . . . . . . . . . . . . . . . .223.5Optional Fan Module . . . . . . . . . . . . . . . . . . . . . . . . . . . . . . . . . .244CPSMC18xx-xxx Chassis . . . . . . . . . . . . . . . . . . . . . . . . . . . .254.1Installing the CPSMC18xx-xxx Chassis . . . . . . . . . . . . . . . . . . . . .254.1.1Table Top Installation . . . . . . . . . . . . . . . . . . . . . . . . . . . . . . . .254.1.2Standard 19-inch Rack Installation . . . . . . . . . . . . . . . . . . . . . . .254.1.3Grounding Lugs . . . . . . . . . . . . . . . . . . . . . . . . . . . . . . . . . . . . .274.2Telco Option . . . . . . . . . . . . . . . . . . . . . . . . . . . . . . . . . . . . . . . .284.3Cascade Option . . . . . . . . . . . . . . . . . . . . . . . . . . . . . . . . . . . . . .314.4Connecting the Slide-in-Modules to the Network . . . . . . . . . . . . .334.5Operation . . . . . . . . . . . . . . . . . . . . . . . . . . . . . . . . . . . . . . . . . . .335Network Management . . . . . . . . . . . . . . . . . . . . . . . . . . . . . .345.1Hardware Connections . . . . . . . . . . . . . . . . . . . . . . . . . . . . . . . .346Troubleshooting . . . . . . . . . . . . . . . . . . . . . . . . . . . . . . . . . . .36 Technical Specifications . . . . . . . . . . . . . . . . . . . . . . . . . . . . . . . . . . . . .37 Cable Specifications . . . . . . . . . . . . . . . . . . . . . . . . . . . . . . . . . . . . . . . .38 Contact Us . . . . . . . . . . . . . . . . . . . . . . . . . . . . . . . . . . . . . . . . . . . . . . .40 Warranty . . . . . . . . . . . . . . . . . . . . . . . . . . . . . . . . . . . . . . . . . . . . . . . . .41introductionintroductionslide-in-modules1.2Unpacking the CPSMC18xx-xxx EquipmentUse the following list to verify the shipment:ItemPart Number 18-Slot chassis with AC Power SupplyCPSMC1800-20018-Slot chassis with DC Power SupplyCPSMC1810-20018-Slot chassis with AC Power SupplyCPSMC1850-150and two (2) Telco connectors18-Slot chassis with DC Power SupplyCPSMC1850-160and two (2) Telco connectorsPointSystem™Chassis Face Plates (18)CPSFP-200 Power Cord(varies by country)User’s Guide 33185The following items are optional accessories for the C PSMC 18xx-xxx 18-Slot PointSystem™ chassis:ItemPart Number Redundant AC Power Supply ModuleCPSMP-200 (optional)Redundant 48-VDC Power Supply ModuleCPSMP-210 (optional)Redundant Fan ModuleCPSFM-200 (optional)Single-Slot Master Management ModuleCPSMM-120 (optional)Dual-Slot Master Management ModuleCPSMM-200 (optional)FocalPoint™Software DiskA1-7227(included with the management modules)Expansion Management ModuleCPSMM-210 (optional)Management Module Cascade Connector6026 (optional)Telco RJ-21 (male) to RJ-45 Hydra cable21HC45-6 (optional)Telco RJ-21 to RJ-21 (male-to-male) cable21HC21-6 (optional)Rack Mount EarsCPSRE-230 (optional)Selectable media converter slide-in-module(s)(various P/N) - (optional)slide-in-modulesslide-in-modulesslide-in-modulesslide-in-modulesslide-in-modulespower supplypower supplypower supplypower supplypower supplypower supplypower supplypower supplypower supplypower supplychassischassischassischassisFiber Port #2Fiber Port #1CDFTF1001850-1xx are designed for any Transition Networks Slots 7-18 on the CPSMC1850-1xx can accommodate any Transition Networks media converter slide-in-module. However the Telco option will not functionchassisCascading multiple CPSMC18xx-xxx chassisTo cascade two or more CPSMC18xx-xxx chassis:1.Locate one (1) Transition Networks management module cascade cable (withRJ-45 connectors installed at both ends) (P/N 6026) for each set of two (2)chassis to be cascaded.NOTE: Transition Networks management module cascade cables are one (1)meter long. Ensure that the chassis are installed within one (1) meter of eachother.2.At the first chassis in the series: Plug the RJ-45 connector at one end of thecascade cable into the management module’s RJ-45 port labeled “OUT”.3.At the next chassis in the series: Plug the RJ-45 connector at the other end of thecascade cable into the management module’s RJ-45 port labeled “IN”.4.At the same chassis as in step 3: Plug the RJ-45 connector at one end of thecascade cable into the management module’s RJ-45 port labeled “OUT”.5.At the next chassis in the series: Plug the RJ-45 connector at the other end of thecascade cable into the management module’s RJ-45 port labeled “IN”.6.Repeat steps 4 and 5 until all chassis have been connected.chassisnetwork mgmt.network mgmt.6Troubleshooting1.Are any of the power LEDs on any of the slide-in-modules illuminated, AND arethe fans operating?YES•The chassis is receiving power. Proceed to the next step.NO•Check all power supply cables for proper connection.•For AC power: Ensure the AC receptacle on the wall is supplying power.•If the fuse for the AC receptacle on the wall blows repeatedly, have the ACreceptacle inspected by a qualified electrician.•For DC power: Ensure the DC power supply is supplying power.•Check the fans to see if they are operating.•C ontact Technical Support: U.S./C anada: 1-800-260-1312, International:00-1-952-941-7600.2.For the management modules (CPSMM-120, CPSMM-200, CPSMM-210), areANY of the power LEDs NOT illuminated?NO•All management modules are receiving power. Proceed to the next step.YESFor those management modules where the power LED is NOT illuminated:•Ensure the management module is firmly seated in the slot.•Press the RESET button on the management module.•C ontact Technical Support: U.S./C anada: 1-800-260-1312, International:00-1-952-941-7600.3.For the remaining slide-in-modules, are ANY of the power LEDs NOTilluminated?NO•All slide-in-modules are receiving power. Proceed to the next step.YESFor those slide-in-modules where the power LED is NOT illuminated:•Ensure the slide-in-module is firmly seated in the slot.•C ontact Technical Support: U.S./C anada: 1-800-260-1312, International:00-1-952-941-7600.4.To determine if a fault is due to a software problem, consult the troubleshootingsection of the Focal Point™ 2.0 Management Appl ication and CPSMM100Firmware User’s Guide (P/N 33293). This manual is available on the enclosedapplication CD and on-line at .5.To determine if a fault is due to an individual management module or slide-in-troubleshooting module, consult the troubleshooting section of the user’s guide for thatparticular module.6.If none of the solutions listed in this section resolves the problem, contactTechnical Support: U.S./Canada: 1-800-260-1312, International: 00-1-952-941-7600.Cable SpecificationsNull Modem CableThe Null Modem Cable is used for connecting a terminal or terminal emulator tothe management module’s DB-9 connector to access the command-line interface.The table below shows the pin assignments for the DB9 cable.Function Mnemonic PinCarrier Detect CD1Receive Data RXD2Transmit Data TXD3Data Terminal Ready DTR4Signal Ground GND5Data Set Ready DSR6Request To Send RTS7Clear To Send CTS8The table below shows the pin assignments for the RS-232 null modem cable.RJ-45 CableCategory 5:Gauge:24 to 22 AWGAttenuation: 22.0 dB /100m @ 100 MHzMaximum Cable Distance:100 meters• Straight-through OR crossover cable may be used.• Shielded twisted-pair(STP) OR unshielded twisted-pair (UTP) may be used.• Pins 1&2 and 3&6 are the two active pairs in an Ethernet network.(RJ-45 Pin-out: Pin 1 = TD+, Pin 2 = TD-, Pin 3 = RD+, Pin 6 = RD-)• All pin pairs (1&2, 3&6, 4&5, 7&8) are active in a gigabit Ethernet network.• Use only dedicated wire pairs for the active pins:(e.g., blue/white & white/blue, orange/white & white/orange, etc.)• Do not use flat or silver satin wire.COAX CableCoaxial cable media is used for circuits such as DS3, E1 and 10Base-2 Ethernet.The impedance of the coaxial cable is determined by the interface type, forexample:•75 ohm for DS3.•50 ohm for 10Base-2 Ethernet.Special attention should be given to the grounding requirements of coaxial cablecircuits. Installation may require grounding at both cable ends or only one cableend or neither cable end.Cable Shield GroundingMedia converter network cabling my be shielded or unshielded. Shielded cablesMUST be grounded according to the specific requirements of the media and porttype. For example:•Shielded RJ-45 cable used for 100Base-Tx Ethernet MUST be grounded at both cable endpoints via shielded RJ-45 jacks.•Shielded RS-232 cable MUST have the shield grounded at both cable endpoints via shielded RS-232 connectors.•COAX cable used for 10Base-2 Ethernet MUST only be grounded at a single point.The media converters provide a jumper option or other grounding mechanism asrequired. Special attention should be given to the grounding requirements ofcoaxial cable circuits. Installation may require grounding at both cable ends or onlyone cable end or neither cable end. See the individual media converter user’s guidefor cable/port grounding requirements.WarrantyLimited Lifetime WarrantyEffective for products shipped May 1, 1999 and after. Every Transition Networks' labeled product purchased after May 1, 1999 will be free from defects in material and workmanship for its lifetime. This warranty covers the original user only and is not transferable.This warranty does not cover damage from accident, acts of God, neglect, contamination, misuse or abnormal conditions of operation or handling, including over-voltage failures caused by use outside of the product's specified rating, or normal wear and tear of mechanical components. If the user is unsure about the proper means of installing or using the equipment, contact Transition Networks' free technical support services.To establish original ownership and provide date of purchase, please complete and return the registration card accompanying the product or register the product on-line on our product registration page.Transition Networks will, at its option:•Repair the defective product to functional specification at no charge,•Replace the product with an equivalent functional product, or•Refund the purchase price of a defective product.To return a defective product for warranty coverage, contact Transition Networks' technical support department for a return authorization number. Transition's technical support department can be reached through any of the following means: Technical Support is available 24 hours a day at:•800-260-1312 x 200 or 952-941-7600 x 200•fax 952-941-2322•*******************************•live web chat: and click the “Transition Now” link•voice mail 800-260-1312 x 579 or 952-941-7600 x 579•All messages will be answered within one hour.Send the defective product postage and insurance prepaid to the following address: CSI Material Management Centerc/o Transition Networks508 Industrial DriveWaconia, MN 55387 USAAttn: RETURNS DEPT: CRA/RMA # ___________Failure to properly protect the product during shipping may void this warranty. The return authorization number must be written on the outside of the carton to ensure its acceptance. We cannot accept delivery of any equipment that is sent to us without a CRA or RMA number.The customer must pay for the non-compliant product(s) return transportation costs to Transition Networks for evaluation of said product(s) for repair or replacement.Transition Networks will pay for the shipping of the repaired or replaced in-warranty product(s) back to the customer (any and all customs charges, tariffs, or/and taxes are the customer's responsibility).Before making any non-warranty repair, Transition Networks requires a $200.00 charge plus actual shipping costs to and from the customer. If the repair is greater than $200.00, an estimate is issued to the customer for authorization of repair. If no authorization is obtained, or the product is deemed not repairable, Transition Networks will retain the $200.00 service charge and return the product to the customer not repaired. Non-warranted products that are repaired by Transition Networks for a fee will carry a 180-day limited warranty. All warranty claims are subject to the restrictions and conventions set forth by this document.Transition Networks reserves the right to charge for all testing and shipping incurred, if after testing, a return is classified as "No Problem Found."THIS WARRANTY IS YOUR ONLY REMEDY. NO OTHER WARRANTIES, SUCH AS FITNESS FOR A PARTIC ULAR PURPOSE, ARE EXPRESSED OR IMPLIED. TRANSITION NETWORKS IS NOT LIABLE FOR ANY SPEC IAL, INDIREC T, INCIDENTAL OR CONSEQUENTIAL DAMAGES OR LOSSES, INCLUDING LOSS OF DATA, ARISING FROM ANY CAUSE OR THEORY. AUTHORIZED RESELLERS ARE NOT AUTHORIZED TO EXTEND ANY DIFFERENT WARRANTY ON TRANSITION NETWORKS' BEHALF.。
Cisco SCE8000 10GBE平台安装和配置指南(版本3.1.6S)说明书

C H A P T E R2-1Cisco SCE8000 Installation and Configuration Guide, Rel 3.1.6SOL-16478-042Introduction to the Cisco SCE8000 PlatformThis chapter provides an introduction to the Cisco SCE8000 10GBE platform, the Service Control hardware component.•SCE Platform Information, page 2-1•Service Control Module—SCE8000-SCM-E, page 2-3•SIP and SPA Introduction, page 2-4•SCE8000-SIP Status LEDs, page 2-7•1-Port 10 GBE SPA Interface Module, page 2-7•Cisco SCE8000 Optical Bypass Module, page 2-9•Checking the Shipping Container Contents, page 2-14•Cisco SCE8000 Installation Checklist, page 2-15SCE Platform InformationThe Service Control Engine (SCE) platform, which is the hardware component of the Cisco service control solution, is designed to support observation, analysis, and control of Internet and IP traffic (Figure 2-1).Chapter2 Introduction to the Cisco SCE8000 Platform SCE Platform InformationFigure2-1Cisco SCE8000 PlatformTable2-1 summarizes model information for the Cisco SCE8000 platform.T able2-1SCE Platform Model InformationModel number Cisco SCE8000 10 GBELink Type10 Gigabit EthernetNumber of Ports 2 or 4Number of Links 1 or 2The Cisco SCE8000 is a transparent element with 10 GBE links service throughput. It can be installedinline in the network where all traffic passes through it, or in receive-only mode where it receivesreplication of the traffic through SPAN ports or optical splitters.The Cisco SCE8000 supports the following network insertion models:•Single appliance (inline)•Single appliance (receive-only)•MGSCP configurationThe Cisco SCE8000 platform is a 4-slot chassis hosting the following modules:•One or two service control modules (SCE8000-SCM-E) that each contain special-purpose, fast-path chipset, traffic processors, and control processor.•One SPA Interface Processor card (SCE8000-SIP) that holds up to four SPA 10 GBE interface modules.•One optional optical bypass module hosting panel that holds up to two optical bypass modules.In addition, the Cisco SCE8000 chassis contains two power supply modules in a 1+1 configuration, aswell as a fan tray module.Cisco SCE8000 Installation and Configuration Guide, Rel 3.1.6SOL-16478-042-3Cisco SCE8000 Installation and Configuration Guide, Rel 3.1.6SOL-16478-04Chapter 2 Introduction to the Cisco SCE8000 PlatformService Control Module—SCE8000-SCM-EChapter2 Introduction to the Cisco SCE8000 Platform SIP and SPA IntroductionT able2-3SCE8000-SCM-E LED Description (continued)LED DescriptionOptical Bypass•Steady amber—The optic bypass module is directed to pass traffic through theCisco SCE8000.•Unlit—The optic bypass module (if present) connects link fibers directly, andtraffic bypasses the Cisco SCE8000.On a slave SCE8000-SMC_E module (in slot 2), this LED is always off.This functionality is consistent even when the Cisco SCE8000 is powered off.Master Indicates the master service control module•Steady green—Master service control module•Unlit—Slave service control moduleMng interface The Mng interface LEDs indicate the operational status of the Cisco SCE8000out-of-band LAN-based management port, as follows:•Link/ActiveSteady green—Port link is upFlashing green—Activity on the port linkUnlit—Port link is down•SpeedUnlit—Port is set to 10 MbpsSteady green—Port is set to 100 MbpsSteady amber—Port is set to 1000 MbpsOn a slave SCE8000-SMC_E module (in the second slot), this LED is always off.SIP and SPA IntroductionSIPs and SPAs are carrier card and port adapter architectures used to increase modularity, flexibility, anddensity across Cisco routers for network connectivity. This section describes SIPs and SPAs andprovides some guidelines for their use.•SPA Interface Processors, page2-4•Specifying a SIP Subslot Location for a SPA, page2-5•Shared Port Adapters, page2-5•Modular Optics, page2-6•XFP Connections, page2-6SPA Interface ProcessorsThe SIP module supported by the Cisco SCE8000 chassis is the SCE8000-SIP. General characteristicsof a SIP include:• A SIP is a carrier card that inserts into a slot in the chassis like a line card. It provides no network connectivity on its own.Cisco SCE8000 Installation and Configuration Guide, Rel 3.1.6SOL-16478-042-5Cisco SCE8000 Installation and Configuration Guide, Rel 3.1.6SOL-16478-04Chapter 2 Introduction to the Cisco SCE8000 PlatformSIP and SPA Introduction2-6Cisco SCE8000 Installation and Configuration Guide, Rel 3.1.6SOL-16478-04Chapter 2 Introduction to the Cisco SCE8000 PlatformSIP and SPA IntroductionNoteChapter2 Introduction to the Cisco SCE8000 PlatformSCE8000-SIP Status LEDsT able2-4XFP Port Cabling SpecificationsXFP Wavelength (nm)Fiber TypeXFP-10GLR-OC192SR1310SMFXFP-10GER-OC192IR1550SMFXFP-10GZR-OC192LR1550SMFXFP-10G-MM-SR850MMFQualified XFPs include an optical transmitter and receiver pair integrated with clock and data recovery(CDR) integrated circuits. XFPs provide high-speed serial links at 10.3125 Gbps on single-mode fibers.The transmit side recovers and retimes the 10 Gbps serial data and passes it to a laser driver. The laserdriver biases and modulates a laser, enabling data transmission over fiber through an LC connector. Thereceive side recovers and retimes the 10 Gbps optical data stream from a photo detector trans impedanceamplifier and passes it to an output driver.To identify technology type and model, see the label on the XFP. XFP dimensions are:•Height—12.5 mm•Width—18.35 mm•Length—71.1 mmThe XFP operating temperature range is 0°C to 70°C.SCE8000-SIP Status LEDsTable2-5 describes the SCE8000 status LEDs.T able2-5SCE8000-SIP LEDLEDs DescriptionStatus•Green—Operational•Flashing Amber—Electrical bypass in operation•Red—Not initialized or failed•Unlit—No power1-Port 10 GBE SPA Interface ModuleThe SCE8000-SIP:•Is installed in slot 3 of the Cisco SCE8000 chassis.•Hosts up to 4 single-width, single-height 1-port 10 GBE SPA interface modules (Figure2-6).In the Cisco SCE8000, the SPA interface module must be configured with either:•Two 1-port 10 GBE SPAs (in the upper two subslots), or•Four 1-port 10 GBE SPAsCisco SCE8000 Installation and Configuration Guide, Rel 3.1.6S OL-16478-042-8Cisco SCE8000 Installation and Configuration Guide, Rel 3.1.6SOL-16478-04Chapter 2 Introduction to the Cisco SCE8000 Platform1-Port 10 GBE SPA Interface ModuleChapter2 Introduction to the Cisco SCE8000 PlatformCisco SCE8000 Optical Bypass ModuleCisco SCE8000 Optical Bypass Module•Optical Bypass Functionality, page2-9•Optical Bypass Module: OPB-SCE8K, page2-10The Cisco SCE8000 platform optical bypass module preserves the service provider 10 GBE links underall circumstances. Upon power failure, the bypass is automatically activated. It can also be activated bythe Cisco SCE8000 software.The Cisco SCE8000 platform already includes an internal electrical bypass, but we recommended thatyou use the optical bypass module for addressing the following scenarios:•During platform reboot (SW reload)—If the external bypass module is not used, there is a 5-second period (at most) during which the link is forced down (cutoff functionality).•During a power failure—The Cisco SCE8000 has two power supplies. A power failure occurs only if both of them fail.If the Cisco SCE8000 platform must be replaced, it is possible to remove the bypass modules from theSCE8000 chassis without disconnecting them from the network and then reinstall them in the new SCEplatform. Traffic links are preserved even in a case of complete failure and replacement of the CiscoSCE8000 platform. See the “Replacing Optical Bypass Module without Disrupting Traffic on Link”section on page9-26.Optical Bypass FunctionalityThe optical bypass module is connected bump-in-the-wire in the 10-GBE link. It is then connected to theCisco SCE8000 platform with two types of connections:•10GBE optical connections for data link traffic—10 GBE connections from the optical bypass module to one pair of the 10 GBE SPA ports.•Control connection—Connection to the RJ-11 External Bypass connector on the SCE8000-SCM, so the optical bypass is activated if the Cisco SCE8000 platform fails.Optical Bypass Module ConnectivityThe optical bypass module functions as follows (Figure2-7):•Under normal conditions, the bypass module directs traffic to flow through the Cisco SCE8000.•Under failure conditions, the optical bypass shortcuts the interfaces that are connected to the traffic link, and all traffic flows through the optical bypass module, bypassing the SCE platform.Cisco SCE8000 Installation and Configuration Guide, Rel 3.1.6S OL-16478-042-10Cisco SCE8000 Installation and Configuration Guide, Rel 3.1.6SOL-16478-04Chapter 2 Introduction to the Cisco SCE8000 PlatformCisco SCE8000 Optical Bypass ModuleCisco SCE8000 Installation and Configuration Guide, Rel 3.1.6SOL-16478-04Cisco SCE8000 Optical Bypass ModuleOptical Bypass Module SpecificationsFiber Cable TypeThe fiber cable type within the Optical Bypass Module area as follows:•OPB-SCE8K-MM: 50 um core.•OPB-SCE8K-SM: SMF-28Maximum optical path (fiber length of two ports) is 600m.Switching TimeSwitching time is measured from trigger to stable 90% optical output.•Typical switching time: 3 ms •Maximal switching time: 10msFan AssemblyThe system fan assembly, located in the chassis, provides cooling air for the installed modules (Figure 2-9).T able 2-8Optical Bypass Module PortsPort Quantity DescriptionConnect This Port to…10 GBE line port410GBE ports A through DDuplex LC, panel mount adaptor for LC/UPC connectors SPA interfaces on the Cisco SCE8000.Refer to the “Cabling the 10GBE Line Interface Ports: Using the External Optical Bypass Module” section on page 6-10 for information.CTRL1RJ-11 portRJ-11 optical bypass port on the SCE8000-SCM-ET able 2-9Optical Bypass Module LEDsLEDs DescriptionStatusThe Status LED indicates the operational status of the optical bypass module, as follows:•Green—Bypass module has been de-activated (traffic flows through the Cisco SCE8000 platform)•Off—Bypass module is active (traffic does not flow through the Cisco SCE8000 platform)2-12Cisco SCE8000 Installation and Configuration Guide, Rel 3.1.6SOL-16478-04Cisco SCE8000 Optical Bypass Module2-13Cisco SCE8000 Installation and Configuration Guide, Rel 3.1.6SOL-16478-04Cisco SCE8000 Optical Bypass ModuleCisco SCE8000 Installation and Configuration Guide, Rel 3.1.6SOL-16478-04Checking the Shipping Container ContentsPower Supply CoolingPower supplies have built-in fans and are completely self-cooling. Air enters from the right of the fan and exits through the left.Load-SharingWith two power supplies, each power supply concurrently provides approximately half of the required power to the system. If one power supply fails, the second power supply immediately assumes full power to maintain uninterrupted system operation. The second power supply enables load sharing and fault tolerance automatically; no software configuration is required.Checking the Shipping Container ContentsUse the Cisco SCE8000 Component List to check the contents of the Cisco SCE8000 platform shipping container.TipWhen you unpack the Cisco SCE8000, do not discard the shipping container. Flatten the shipping cartons and store them with the pallet. You may need these containers if you move or ship the Cisco SCE8000 in the future.Cisco SCE8000 ComponentsTable 2-10 lists the components of the SCE8000 system.T able 2-10Cisco SCE8000 Component ListComponentDescriptionCisco SCE8000 platform•Cisco SCE8000-SCM-E •Cisco SCE8000-SIP • 2 or 4 SPA Jacket cards • 2 or 4 XFP OpticsXFP optic modules.• 2 Cisco PWR-2700-AC/4 or 2 Cisco PWR-2700-DC/4 •SCE8000-FANCisco SCE8000 10 GBE chassis configured with the following components:•Cisco SCE8000 service control module•Cisco SCE8000 SPA Jacket card Interface Processor •SPA Interface. See below the list of supported SPA models.•See below the list of supported XFP models •Cisco power supply units, AC or DC.Hot swappable, redundant power supply, compatible with Cisco 7604 router.•Redundant fan unit.AccessoriesThe following accessories might arrive in separate shipping containers:Cisco SCE8000 Installation ChecklistT able2-10Cisco SCE8000 Component List (continued)Component DescriptionManagement cables•Gigabit Ethernet cable for connecting to theManagement ports•RS-232 serial cables (DB-9 to RJ-45 and DB-25 toRJ-45) for connecting to a local terminalPower cables Two AC power supply cords, if ordered with AC-input powersupply unitsGrounding kit 69-0815-01•Grounding lug•Two M4 hex-head screws with locking washersOptical Bypass module kit•Optical Bypass Module•Control Cable (2 m)•Control Cable (40 cm)Note We do not ship the entire Cisco SCE8000 documentation set automatically with each system. You must specifically order the documentation as part of the sales order. If you ordered documentation and did notreceive it, we will ship the documents to you within 24 hours. To order documents, contact a customerservice representative.Cisco SCE8000 Installation ChecklistTo assist you with your installation and to provide a historical record of actions performed, photocopythe following Cisco SCE8000 Installation Checklist (Table2-11). Indicate the date each procedure orverification is completed. When the checklist is completed, place it in your site log along with the otherrecords for your Cisco SCE8000 platform.T able2-11Cisco SCE8000 Installation ChecklistTask Verified By DateDate Cisco SCE8000 receivedCisco SCE8000 and all accessories unpackedSafety recommendations and guidelines reviewedTopology verified—Quantity of Cisco SCE8000 platforms, numberof links, and whether inline or receive-onlyInstallation Checklist copiedSite log established and background information enteredSite power voltages verifiedSite environmental specifications verifiedRequired passwords, IP addresses, device names, and so on, neededfor initial configuration available (refer to the “Initial SetupParameters” section on page5-2)Cisco SCE8000 Installation and Configuration Guide, Rel 3.1.6S OL-16478-04Cisco SCE8000 Installation ChecklistT able2-11Cisco SCE8000 Installation Checklist (continued)Task Verified By DateRequired tools availableNetwork connection equipment availableCisco SCE8000 mounted in rackSystem grounding established, if requiredAC/DC power cables connected to AC/DC sources andCisco SCE8000 chassisOptical bypass modules installed (optional)Console port set for 9600 baud, 8 data bits, no parity, and 1 stop bit(9600 8N1)ASCII terminal attached to console portManagement port is operationalNetwork interface cables and devices connectedSystem power turned onSystem boot complete (Status LED is on)10 GBE line ports operationalCorrect hardware configuration displayed after system bannerappearsCisco SCE8000 Installation and Configuration Guide, Rel 3.1.6SOL-16478-04。
ATLAS.ti 8 windows 快速导览 说明书
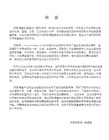
ATLAS.ti 8 Windows 快速导览ATLAS.ti 8 Windows – 快速导览版权所有©2018年ATLAS.ti Scientific Software Development GmbH,柏林。
版权所有。
文件版本:1264.20180813。
更新程序版本:8.1作者: Dr. Susanne Friese (QUARC)制作: /Dr. Thomas G. Ringmayr抄袭或复制本手册或其中任何部分均违反适用法律。
未经ATLAS.ti GmbH书面许可,不得以电子形式、机械手段、复印等任何形式或手段复制或传播本手册的任何部分。
商标:ATLAS.ti是ATLAS.ti Scientific Software Development GmbH的注册商标。
Adobe Acrobat是Adobe Systems Incorporated的商标; 此处引用的Microsoft,Windows,Excel和其他Microsoft产品是Microsoft Corporation在美国和/或其他国家(地区)的商标。
Google Earth是Google Inc.的商标。
本文档中提及的所有其他产品名称,以及任何已注册和未注册的商标仅用于识别目的。
它们仍为其各自所有者的专有财产。
启动屏幕创建新项目,或者打开已有项目。
图1: ATLAS.ti –图2: 导入项目捆绑包对话框你可能熟悉其他当前在用的Windows 软件的功能区。
功能区是一组图形控制元素,通过放置在多个选项卡上的工具栏形式来存在。
它们按照功能而不是对象类型进行分组,这跟旧版ATLAS.ti 的情况一样。
在本版ATLAS. ti 中,选项卡可以用来显示不同的控制组合,从而避免大量并行的工具栏。
这可以极大地改进工作流程,并让用户更容易查看在既定背景下的可以用哪些功能。
ATLAS.ti 功能区ATLAS.ti 的五大核心选项卡:•主页•搜索项目•分析•导入和导出•工具和支持根据你正在使用的功能,其它的背景选项卡将会出现。
Oracle Hospitality Suite8 版本控制说明书
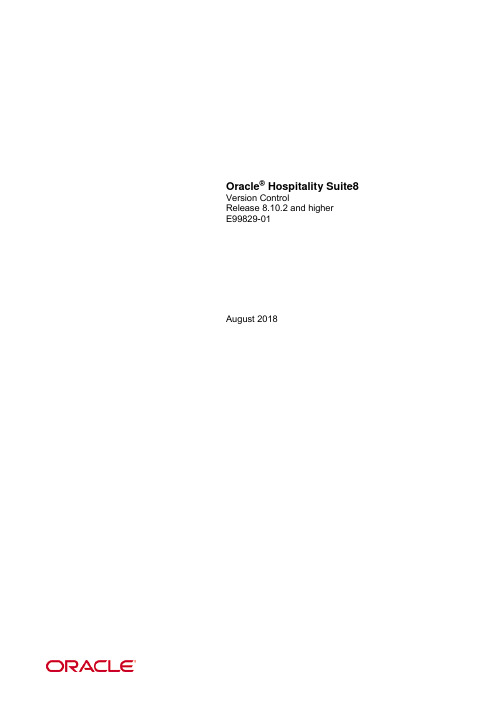
This software or hardware and documentation may provide access to or information on content, products, and services from third parties. Oracle Corporation and its affiliates are not responsible for and expressly disclaim all warranties of any kind with respect to third-party content, products, and services. Oracle Corporation and its affiliates will not be responsible for any loss, costs, or damages incurred due to your access to or use of third-party content, products, or services.
Ruckus ZoneDirector 10.1 Release Notes.pdf_1698096
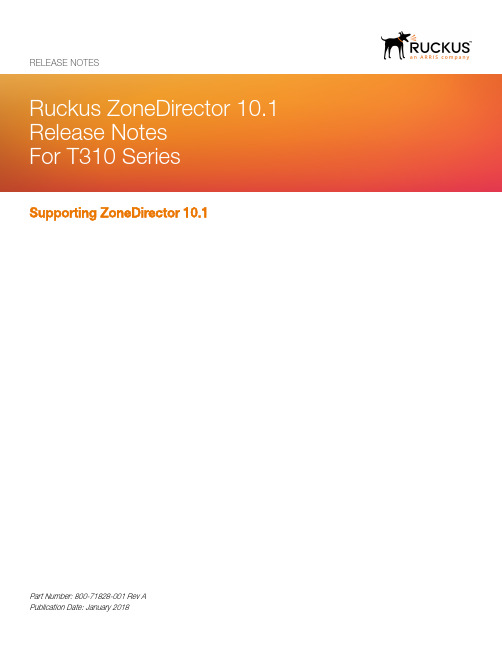
Supporting ZoneDirector 10.1RELEASE NOTESPart Number: 800-71828-001 Rev ACopyright Notice and Proprietary Information© 2018 ARRIS Enterprises, LLC. All rights reserved.No part of this documentation may be used, reproduced, transmitted, or translated, in any form or by any means, electronic, mechanical, manual, optical, or otherwise, without prior written permission of or as expressly provided by under license from ARRIS. Destination Control StatementTechnical data contained in this publication may be subject to the export control laws of the United States of America. Disclosure to nationals of other countries contrary to United States law is prohibited. It is the reader’s responsibility to determine the applicable regulations and to comply with them.DisclaimerTHIS DOCUMENTATION AND ALL INFORMATION CONTAINED HEREIN (“MATERIAL”) IS PROVIDED FOR GENERAL INFORMATION PURPOSES ONLY. ARRIS and RUCKUS WIRELESS, INC. AND THEIR LICENSORS MAKE NO WARRANTY OF ANY KIND, EXPRESS OR IMPLIED, WITH REGARD TO THE MATERIAL, INCLUDING, BUT NOT LIMITED TO, THE IMPLIED WARRANTIES OF MERCHANTABILITY, NON-INFRINGEMENT AND FITNESS FOR A PARTICULAR PURPOSE, OR THAT THE MATERIAL IS ERROR-FREE, ACCURATE OR RELIABLE. ARRIS and RUCKUS RESERVE THE RIGHT TO MAKE CHANGES OR UPDATES TO THE MATERIAL AT ANY TIME. Limitation of LiabilityIN NO EVENT SHALL ARRIS or RUCKUS BE LIABLE FOR ANY DIRECT, INDIRECT, INCIDENTAL, SPECIAL OR CONSEQUENTIAL DAMAGES, OR DAMAGES FOR LOSS OF PROFITS, REVENUE, DATA OR USE, INCURRED BY YOU OR ANY THIRD PARTY, WHETHER IN AN ACTION IN CONTRACT OR TORT, ARISING FROM YOUR ACCESS TO, OR USE OF, THE MATERIAL.TrademarksRuckus Wireless, Ruckus, the bark logo, BeamFlex, ChannelFly, Dynamic PSK, FlexMaster, ICX, Simply Better Wireless, SmartCell, SmartMesh, SmartZone, Unleashed, ZoneDirector and ZoneFlex are trademarks of Ruckus Wireless, Inc. in the United States and in other countries. Other trademarks may belong to third parties.ContentsAbout This Release (4)Supported Platforms and Upgrade Information (4)Supported Platforms (4)Access Points (4)Upgrading to This Version (5)Enhancements and Resolved Issues (6)New Access Points (6)Enhancements and New Features (7)Resolved Issues (8)Caveats, Limitations and Known Issues (9)About This ReleaseThis document provides release information on ZoneDirector release 10.1, including new features, enhancements, known issues, caveats, workarounds, upgrade details and interoperability information for version 10.1.NOTEBy downloading this software and subsequently upgrading the ZoneDirector and/or the AP to version 10.1, please be advised that:•The ZoneDirector will periodically connect to Ruckus and Ruckus will collect the ZoneDirector serial number, software version and build number. Ruckus will transmit a file back to the ZoneDirector and this will be used to display the currentstatus of the ZoneDirector Support Contract.•The AP may send a query to Ruckus containing the AP’s serial number. The purpose is to enable your AP to autonomously connect with a wireless LAN controller operated by your choice of cloud service provider. Ruckus maytransmit back to the AP, the Fully Qualified Domain Name (FQDN) or IP address of the controller that the AP willsubsequently attempt to join.Please be advised that this information may be transferred and stored outside of your country of residence where data protection standards may be different.Supported Platforms and Upgrade InformationSupported PlatformsZoneDirector version 10.1.0.0.1525 supports the following ZoneDirector models:•ZoneDirector 1200•ZoneDirector 3000NOTEZoneDirector 5000 is discontinued as of this release, and cannot be upgraded to version 10.1 or later.Access PointsZoneDirector version 10.1.0.0.1525 supports the following Access Point models:•C110•H320•H500•H510•R300•R310•R500•R510•R600•R610•R700Supported Platforms and Upgrade InformationUpgrading to This Version•R710•R720•T300•T300e•T301n•T301s•T310c*•T310d*•T310n*•T310s*•T610•T610s•T710•T710s•ZF7055•ZF7352•ZF7372•ZF7372-E•ZF7781CM•ZF7782•ZF7782-E•ZF7782-N•ZF7782-S•ZF7982NOTE*This patch release adds support for new APs: T310c, T310d, T310n, T310s.Upgrading to This VersionThis section lists important notes on upgrading ZoneDirector to this version.Officially Supported 10.1 Upgrade PathsThe following release builds can be directly upgraded to this release:•10.1.0.0.1515 (10.1 GA)If you are running an earlier version, you must upgrade to one of the above builds before upgrading to this release.If you do not have a valid Support Entitlement contract, you will be unable to upgrade ZoneDirector to this release. See the Administer > Support page for information on Support Entitlement activation.Enhancements and Resolved IssuesAdding a New AP ModelZoneDirector 10.1 release supports the registration of new AP models that were not yet available when this ZoneDirector version was released.Before starting this procedure, verify that the controller is running release 10.1 (GA) or later.NOTEThis procedure will restart ZoneDirector services. During the upgrade process, service outage will occur as the ZoneDirector will restart automatically to complete the upgrade.Follow these steps to register a new AP model with the controller:1.Contact Ruckus for the AP patch file that will enable the controller to support the new AP model (for example,T310-10.1.0.0.1525.encrypted.patch).2.Get the AP patch file, and then save or move the patch file to a location that you can access from the computer that you are usingto access the controller's web interface.3.Log on to the controller's web interface as Super Admin.4.Go to the Administer > Upgrade page, and then click Choose File under AP Patch Firmware. Select the AP Patch file to upload.5.Click Upgrade .6.The controller adds the T310 series (T310c, T310d, T310n, T310s) to AP release 10.1.0.0.1525. (New AP models are added intoAdminister > Upgrade page under Current Software.)7.After the controller completes upgrading, connect the new AP model to the network. The new AP model registers with thecontroller, and then the controller upgrades the AP firmware to release 10.1.0.0.1525.8.Go to the Access Points page, and then verify that the new AP model you added to the controller is listed under CurrentlyManaged APs.9.Under the Status column, verify that new AP model isn’t Approval Pending. Allow it from the Action column if it is ApprovalPending.You have completed adding a new AP model to the controller.Enhancements and Resolved IssuesThis section lists new features and enhancements that have been added in this release, and any customer-reported issues from previous releases that have been resolved in this release.New Access Points•New Access Point: T310 SeriesThe T310 series (T310c, T310d, T310n, T310s) is a new outdoor dual-band 802.11ac Wave 2 AP designed for flexible installation in a wide variety of outdoor environments.The T310d has an omni antenna, an extended temperature range (-40C to 65C), one 10/100/1000 Ethernet port that supports 802.3af PoE in, optional DC power input, and a USB port for IoT devices, such as a BLE or Zigbee dongle, Z-Wave, etc.The T310c has an omni antenna, with narrower operating temperature range, and no USB port or DC power supply.The T310s is the sector antenna variant of the T310 series, and the T310n is the narrow sector antenna variant.Enhancements and Resolved IssuesEnhancements and New FeaturesEnhancements and New FeaturesThis section lists the new features and enhancements in this release.•New UI – Phase 2This release introduces the second stage of the new redesigned web interface, which highlights network health and trafficstatistics visibility, and includes several enhancements to the overall UI organization and user-friendliness.•Adaptive Band BalancingThis feature enhances the existing Band Balancing feature by allowing client redistribution dynamically after association, ratherthan only once during the initial association.•Additional SMS Service Provider SupportCustomers can now configure a custom SMS service provider for delivering alarms and guest passes, in addition to the existing Twilio and Clickatell SMS provider options.•Client Connection TroubleshootingThis feature is designed to help customers diagnose wireless client connection issues to determine why a client fails to connect to the wireless network.•Multiple Social Media Logins on the Same WLANExisting Social Media login methods (Facebook, Google, LinkedIn and Microsoft) can now be used simultaneously on the same WLAN.•WeChat SupportA new social media WLAN type – WeChat – is now available.•Social Media Login Scale EnhancementEnhanced the scaling capabilities of Social Media WLANs.•Role-Based Application Recognition and ControlApplication Recognition and Control (ARC) features can now be applied to users based on user role, in addition to the existing per-WLAN configuration. Role-based application policies take precedence when both role-based and WLAN-based policies exist.•Source IP/Port-Based Access Control ListsCustomers can now configure ACLs to allow or deny access to wireless clients from an external source IP address or port.•LWAPP Tunnel Performance EnhancementThis enhancement improves the performance of tunneled WLAN traffic by reducing some time-consuming operations in theRuckus GRE tunnel module.•Ability to Export DPSK RecordsThe Dynamic PSK Batch Generation page now provides an additional option to download generated DPSK records.•Recovery SSID EnhancementEnhanced the AP configure and recovery SSIDs to allow remote wireless configuration of newly installed APs and recovery ofisolated mesh APs.•Client Flow Data LoggingThis feature allows ZoneDirector to transmit client session data to a syslog server for use in legal obligation compliance for Hotspot service providers in certain countries, or for emerging Wi-Fi monetization projects, where the ability to export session data could be useful for marketing or for use by a third-party platform.•DTIM, Directed Multicast, and RTS-CTS Configuration OptionsThe following new configuration options are available for configuring advanced wireless settings: DTIM, Directed Multicast/Broadcast Threshold, and Protection Mode.•New SNMP OID SupportSeveral new SNMP OIDs have been introduced for configuring 802.11d and BSS Minrate settings.•Bonjour Fencing EnhancementThis release enhances the functionality of the Bonjour Fencing feature by allowing fencing policies to be deployed on multiple wired devices.•End of Support for ZoneDirector 5000ZoneDirector 5000 is discontinued as of this release, and cannot be upgraded to version 10.1 or later.•Disabled TLSv1.0TLSv1.0 has been disabled in this release due to security concerns, and ZoneDirector now supports only TLSv1.1 and v1.2. For information on security incidents and responses, see https:///security.Resolved Issues•Resolved an issue related to the WPA KRACK vulnerability. For information on security incidents and responses, see https:///security. [AP-6463]This release fixes multiple vulnerabilities (also known as KRACK vulnerabilities) discovered in the four-way handshake stage of the WPA protocol. The Common Vulnerabilities and Exposures (CVE) IDs that this release addresses include:–CVE-2017-13077–CVE-2017-13078–CVE-2017-13079–CVE-2017-13080–CVE-2017-13081–CVE-2017-13082Client devices that have not yet been patched are vulnerable to KRACK attacks. To help protect unpatched client devices from KRACK attacks, Ruckus strongly recommends running the CLI commands below:ruckus# config ruckus(config)# system ruckus(config-sys)# eapol-no-retryUse the following command to disable:ruckus(config-sys)# no eapol-no-retryEnabling the eapol-no-retry feature (disabled by default) prevents the AP from retrying packets in the key exchange process that have been found to be vulnerable to KRACK attacks. Note that enabling this feature may introduce client connectivity delay in high client density environments.For more information about KRACK vulnerabilities, visit the Ruckus Support Resource Center at https:///krack-ruckus-wireless-support-resource-center.•Resolved an issue where the max clients limit was not enforced on Autonomous WLANs when an AP was disconnected fromZoneDirector. [ER-3887]Enhancements and Resolved IssuesResolved IssuesCaveats, Limitations and Known IssuesCaveats, Limitations and Known IssuesThis section lists the caveats, limitations and known issues in this release.•Some new or modified UI pages have not been fully translated into all available UI languages. [ZF-17158, ZF-18280, ZF-18230]•Apple iOS 11.x clients are unable to connect to an 802.1x WLAN using Zero-IT in some situations due to changes in the way iOS11 handles TLS connections. [ZF-18254]•When running the R720 AP in sniffer mode, the Phy type, bandwidth and data rate elements are decoded incorrectly. [ZF-16839]•R720 APs are unable to properly fence Bonjour services when Bonjour Fencing is enabled on the AP. [ZF-18314]•BSS Fast Transition roaming is not working properly for Google Pixel and Sony Z5 clients. [ZF-18319]•Client Fingerprinting does not properly display the Host Name for some clients, including some Android 8.0 and Chrome OS clients. [ZF-18143]•For APs that were upgraded to 10.1 from a previous release, the uniform recovery SSID passphrase will continue to use the previous format until after a factory reset (e.g., "ruckus-<admin password>"), instead of the new passphrase format ("<admin-password>"). [ZF-18625]•Northbound Portal interface may be incompatible with some versions of curl or python. [ZF-18649]•Mac OS clients may fail to be redirected to the intended URL after authentication to a Facebook WLAN. [ZF-18607]•Spectrum Analysis on the 5 GHz radio may fail to run on some outdoor APs in certain situations due to an error that prevents the AP from changing to certain channels correctly. [ZF-18573]•Nexus 5X clients will not connect to dot1x Zero-IT profiles using the Zero-IT Android APP. [ZF-18252]。
广州新穗学校信息中心机房及数字化校园应用系统建设项目
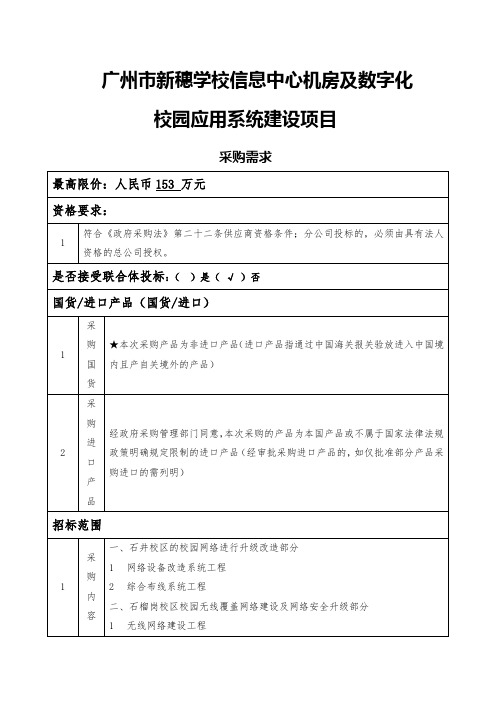
2、石榴岗校区无线网络以及网络安全现状和需求:
(A)目前广州市新穗学校的无线建设目前还处于较为落后的阶段,课堂、机房大
多还是采用有线网络,无线网络也只是通过家用无线路由器简单的Байду номын сангаас于办公室给
老师办公。近年来,中小学希望推进无线校园网络建设,每间普通教室、专用教
室、教室办公室实现无线网络覆盖。无线热点覆盖主要教学场所,为移动学习提
随着互联网的更新换代,加上现有旧系统、硬件的老化性能下降,为实现广州市新穗 学校校园网络高质、高效互联的目标要求,现需要对原有网络进行升级改造,建设一套完 善的信息化网络平台,并实现学校各个信息系统相互融合,满足数据、语音、视讯等多业 务需求。传统基础网络架构设计方法已经无法满足新业务的需求,主要问题体现在以下几 个方面:
(三) 投标人根据招标文件载明的标的采购项目实际情况,拟在中标后将中标项目的 非主体、非关键性工作交由他人完成的,应当在投标文件中载明。
(四) 投标人的投标文件必须提供完整、详细的设备材料清单,包括设备、材料的型 号、数量及主要设备的技术性能指标介绍。投标文件必须提供产品检测报告等资料的复印 件。
(五) 属于《中华人民共和国实施强制性产品认证的产品目录》的产品,交货时不能 提供超出此目录范畴外的替代品,产品还须同时具备国家认监委颁布《中国强制认证》(CCC 认证)。
2015 年接管广州市新穗学校(石井)校区,负责该校区未成年犯的教学管理工作。 学校目前占面积 20158 平方米,可用新征面积 9178 平方米,共 29336 平方米;现有建筑面 积 6562 平方米。至 2014 年 9 月有 8 个班(其中 3 个初二班和 5 个初三班)共 160 个专门
教育(工读)学位。按照市教育局 2004 年规划,新穗学校将建成在全市、全省乃至全国同 类学校中起示范、带动作用的一流专门教育(工读)学校。建成后的新穗学校分义务制教 育阶段专门教育(工读)部和职业教育部两块。 二、建设目标 建设技术先进、性能优良的信息化机房基础设施,构建先进、开放的信息化校园支撑环境; 利用先进的网络技术、通信技术、计算机技术和教育管理理念,构建先进、开放的信息化 系统支撑平台,在此基础上,开发和整合网络基本应用、电子校务系统、教学服务系统以 及综合信息服务系统的多层次应用。项目的实施,将实现学校信息化应用、资源及服务的 高度整合,为采购人的教学、科研、管理与生活提供先进、完善的数字化平台,最终达到 提升采购人教育综合实力的目的。 三、建设范围 1、对广州市新穗学校的石井校区的校园网络进行升级改造,对交换机设备进行升级更换, 提高设备的网络性能,保证网络信息化的高效运行。 2、广州市新穗学校的石榴岗校区校园无线覆盖网络建设及网络安全升级, 全面改造提升 校区的无线网络覆盖,针对安全设备升级,实现学校安全等级保护提升。保障网络可靠运 行。 四、需求描述