机械故障机理
旋转机械故障基本机理与诊断技术

图 陀螺力矩的影响
这一力矩与成正比,相当于弹性力矩。在正进动 (0< </2)的情况下,它使转轴的变形减小, 因而提高了转轴的弹性刚度,即提高了转子的临界 角速度。在反进动( /2 < <)的情况下, 这力矩使转轴的变形增大,从而降低了转轴的刚度, 即降低了转子的临界角速度。故陀螺力矩对转于临 界转速的影响是正进动时,它提高了临界转速;反 进动时,它降低了临界转速。
量信息的基础上,基于机器的故障机理,从中提取 故障特征,进行周密的分析。例如,对于汽轮机、 压缩机等流体旋转机械的异常振动和噪声,其振动 信号从幅值域、频率域和时间域为诊断机器故障提 供了重要的信息,然而它只是机器故障信息的一部 分;而流体机械的负荷变化,以及介质的温度、压 力和流量等,对机器的运行状态有重要的影响,往 往是造成机器发生异常振动和运行失稳的重要因素。
(c)当= n时,A,是共振情况,实际上由于 存在阻尼,振幅A不是无穷大而是较大的有限值, 转轴的振动仍然非常剧烈,以致有可能断裂。 n 称为转轴的“临界角速度”;与其对应的每分钟的 转数则称为“临界转速”,以nc表示 ,即
因
故
研究不平衡响应时如果考虑外阻力的作用, 则复变量式变为
其特解为
Z=|A |ej(t+)
一、概述
旋转机械的种类繁多,有发电机、汽轮机、 离心式压缩机、水泵、通风机以及电动机等,这 类机械的主要功能都是由旋转动作完成的,统称 为机器。旋转机械故障是指机器的功能失常,即 其动态性能劣化,不符合技术要求。例如,机器 运行失稳,机器发生异常振动和噪声,机器的工 作转速、输出功率发生变化,以及介质的温度、 压力、流量异常等。机器发生故障的原因不同, 所产生的信息也不一样,根据机器特有的信息, 可以对机器故障进行诊断。但是,机器发生故障 的原因往往不是单一的因素,特别是对于机械系 统中的旋转机械故障,往往是多种故障因素的耦 合结果,所以对旋转机械进行故障诊断,必须进 行全面的综合分析研究。
转轴裂纹的故障机理与诊断

转轴裂纹的故障机理与诊断石油化工行业的旋转机械一般转速都非常高,载荷也较大,长期运转后,转轴上易出现横向疲动裂纹,导致断轴的严重事故。
相对而言,转轴裂纹的故障概率比其他故障少得多,但因能产生轴裂纹的潜在原因很多,如各种因素造成的应力集中、复杂的受力状态、恶劣的工作条件和环境等,加之裂纹对振动响应不够敏感(深度达1/4直径的裂纹,轴刚度变化仅为10%左右,临界转速的变化也只有5%左右),有可能发展为断轴事故,危害极大。
因此,对轴裂纹诊断知识的学习很有必要。
一、故障机理转轴裂纹对振动的响应与裂纹所处的轴向位置、裂纹深度及受力情况有关。
视裂纹所处部位应力状态的不同,裂纹会呈现出三种不同的形态。
(1)闭裂纹转轴在压应力情况下旋转时,裂纹始终处于闭合状态。
例如,转子重量不大、不平衡离心力较小或不平衡力正好处于裂纹的对侧时就是这种情况。
闭裂纹对转轴振动影响不大,难以察觉。
(2)开裂纹当裂纹区处于拉应力状态时,轴裂纹始终处于张开状态。
开裂纹会造成轴刚度不对称,使振动带有非线性性质,伴有2×、3×、…等高频成分,随着裂纹的扩展,l×、2×、等频率的幅值也随之增大。
(3)开闭裂纹当裂纹区的应力是由自重或其他径向载荷产生时,轴每旋转一周,裂纹就会开闭一次,对振动的影响比较复杂。
理论分析表明,带有裂纹的转子的振动响应可分别按偏心及重力两种影响因素考虑,再作线性叠加。
由于偏心因素的影响,振动峰值会出现在与两个不对称刚度相应的临界转速之间;而重力因素的影响结果,是在转速约为无裂纹转轴的临界转速处时,会出现较大峰值。
裂纹的张开或闭合与裂纹的初始状态、偏心、重力的大小及涡动的速度有关,同时也与裂纹的深度有关。
若转子是同步涡动,裂纹会只保持一种状态,即张开或闭合,这与其初始态有关。
在非同步涡动时,裂纹在一定条件下也可能会一直保持张开或闭合状态,但通常情况下,转轴每旋转一周,裂纹都会有开有闭。
工程机械常见故障与排除
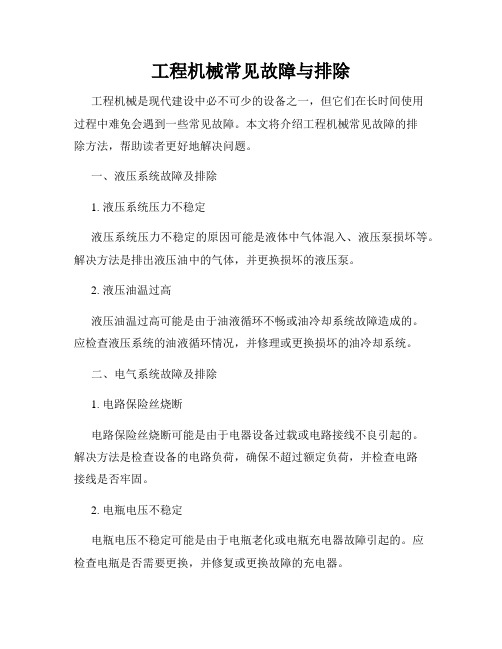
工程机械常见故障与排除工程机械是现代建设中必不可少的设备之一,但它们在长时间使用过程中难免会遇到一些常见故障。
本文将介绍工程机械常见故障的排除方法,帮助读者更好地解决问题。
一、液压系统故障及排除1. 液压系统压力不稳定液压系统压力不稳定的原因可能是液体中气体混入、液压泵损坏等。
解决方法是排出液压油中的气体,并更换损坏的液压泵。
2. 液压油温过高液压油温过高可能是由于油液循环不畅或油冷却系统故障造成的。
应检查液压系统的油液循环情况,并修理或更换损坏的油冷却系统。
二、电气系统故障及排除1. 电路保险丝烧断电路保险丝烧断可能是由于电器设备过载或电路接线不良引起的。
解决方法是检查设备的电路负荷,确保不超过额定负荷,并检查电路接线是否牢固。
2. 电瓶电压不稳定电瓶电压不稳定可能是由于电瓶老化或电瓶充电器故障引起的。
应检查电瓶是否需要更换,并修复或更换故障的充电器。
三、机械部件故障及排除1. 发动机启动困难发动机启动困难可能是由于供油不良或发动机点火系统故障引起的。
解决方法是检查供油系统是否正常,并检修或更换损坏的点火系统组件。
2. 轴承损坏轴承损坏可能是由于润滑不良或长时间使用导致的磨损引起的。
应定期加注润滑油,维护轴承,并及时更换损坏的轴承。
四、润滑系统故障及排除1. 润滑油泄漏润滑油泄漏可能是由于密封件老化或机械部件松动造成的。
应更换老化的密封件,并检查机械部件是否紧固。
2. 润滑系统润滑效果不佳润滑系统润滑效果不佳可能是由于润滑油污染或润滑系统堵塞引起的。
解决方法是定期更换润滑油,并清洗润滑系统。
总结:工程机械常见故障的排除需要根据具体情况进行诊断和处理,以上只是列举了一些常见问题及解决方法。
在实际操作中,应根据设备的具体情况进行维修和保养,确保工程机械的正常运行。
同时,及时保养和维修设备,可以减少故障发生的可能性,延长设备的使用寿命。
齿轮故障机理以及特性分析
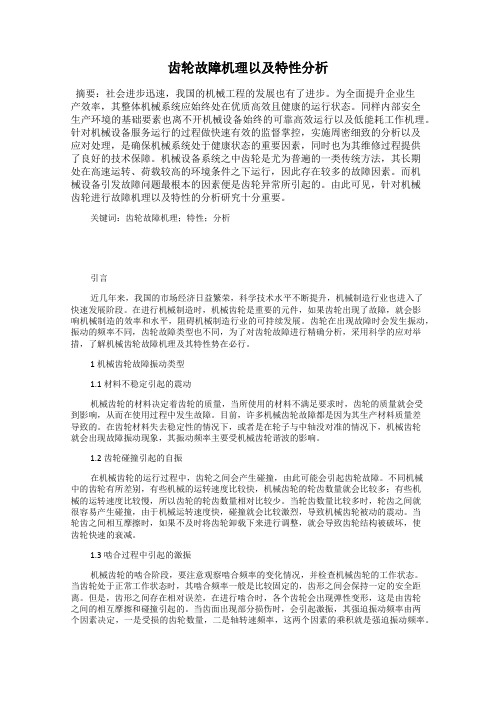
齿轮故障机理以及特性分析摘要:社会进步迅速,我国的机械工程的发展也有了进步。
为全面提升企业生产效率,其整体机械系统应始终处在优质高效且健康的运行状态。
同样内部安全生产环境的基础要素也离不开机械设备始终的可靠高效运行以及低能耗工作机理。
针对机械设备服务运行的过程做快速有效的监督掌控,实施周密细致的分析以及应对处理,是确保机械系统处于健康状态的重要因素,同时也为其维修过程提供了良好的技术保障。
机械设备系统之中齿轮是尤为普遍的一类传统方法,其长期处在高速运转、荷载较高的环境条件之下运行,因此存在较多的故障因素。
而机械设备引发故障问题最根本的因素便是齿轮异常所引起的。
由此可见,针对机械齿轮进行故障机理以及特性的分析研究十分重要。
关键词:齿轮故障机理;特性;分析引言近几年来,我国的市场经济日益繁荣,科学技术水平不断提升,机械制造行业也进入了快速发展阶段。
在进行机械制造时,机械齿轮是重要的元件,如果齿轮出现了故障,就会影响机械制造的效率和水平,阻碍机械制造行业的可持续发展。
齿轮在出现故障时会发生振动,振动的频率不同,齿轮故障类型也不同,为了对齿轮故障进行精确分析,采用科学的应对举措,了解机械齿轮故障机理及其特性势在必行。
1机械齿轮故障振动类型1.1材料不稳定引起的震动机械齿轮的材料决定着齿轮的质量,当所使用的材料不满足要求时,齿轮的质量就会受到影响,从而在使用过程中发生故障。
目前,许多机械齿轮故障都是因为其生产材料质量差导致的。
在齿轮材料失去稳定性的情况下,或者是在轮子与中轴没对准的情况下,机械齿轮就会出现故障振动现象,其振动频率主要受机械齿轮谐波的影响。
1.2齿轮碰撞引起的自振在机械齿轮的运行过程中,齿轮之间会产生碰撞,由此可能会引起齿轮故障。
不同机械中的齿轮有所差别,有些机械的运转速度比较快,机械齿轮的轮齿数量就会比较多;有些机械的运转速度比较慢,所以齿轮的轮齿数量相对比较少。
当轮齿数量比较多时,轮齿之间就很容易产生碰撞,由于机械运转速度快,碰撞就会比较激烈,导致机械齿轮被动的震动。
起重机械常见故障原因分析及处理

起重机械常见故障原因分析及处理摘要:起重机是现代机械化生产的重要传输设备,能够满足大型、重型货物的升降运输需要。
随着国内工业经济的逐渐发展,各种形式的起重机设备得到了广泛运用,显著降低了人工操作的难度。
由于起重机具备体积大、结构多、操作难等特点,其在使用过程中容易出现故障问题,从而引发安全意外事故。
针对这一点,本文首先介绍了起重机械使用过程中的不安全应诉,然后主要分析了起重机安全故障的原因、分析、处理方法以及一些改进措施。
关键词:起重机械;安全故障;改进;起重机械是指用于垂直升降或者垂直升降并水平移动重物的机电设备,其范围规定为额定起重量大于或者等于的升降机;额定起重量大于或者等于1t,且提升高度大于或者等于2m的起重机和承重形式固定的电动葫芦等。
在企业里运用较为平凡的主要有电动葫芦、单梁桥式起重机及双梁桥式起重机。
一般情况下生产型企业运用起重机械主要是在检修的时候辅助使用,且运行环境较恶劣,使用率不高,但是故障率较高,据统计,检修用起重机械每年平均的使用次数约为6次,但是发生故障为次,从而影响检修进度、增加维修费用及成本,且对检修时的安全埋下了极大的隐患。
因此,判断起重机械的故障原因并采取有效的的措施预防其故障的发生就显得尤为重要。
1.起重机械使用过程中存在的不安全因素近几年,国家对特种设备的安全很重视,先后制定了《特种设备安全监察条例》、《起重机械安全监察规定》等多项法规、标准,加强了对起重机械的监察管理工作,有效地控制了事故发生。
但由于种种原因,起重机械仍然存在许多不安全因素,起重机械存在的不安全因素主要有以下几点:人为因素由人为因素引起的起重机械事故较多,主要表现在:(1)起重机械司机的失误。
司机注意力不集中,司机的能力、意识不足,不熟悉所使用的起重机械,不按安全操作规程作业,易导致事故的发生。
(2)起重机械监管的失误。
起重机械进行危险性较大作业时,不设专门监管人员旁站;监管人员责任心不强,疏于监护,造成起重机械与周围物体碰撞。
”机器故障”通常发生在哪些类型的机器或设备上?

”机器故障”通常发生在哪些类型的机器或设备上?近年来,机器的普及和应用范围的扩大,使得机器故障成为我们日常生活中经常会遇到的问题之一。
那么,究竟哪些类型的机器或设备更容易发生故障呢?本文将通过有序列表的方式,从多个角度进行探讨,帮助读者了解机器故障的发生机理及应对措施。
一、电子设备类电子设备类机器广泛应用于各行各业,其故障也是最常见的。
在这个类型中,终端设备例如电视、手机、电脑等是常见的故障源。
由于电子设备的组件众多,而且存在相互连接的关系,因此一旦某个组件发生故障,往往会影响到整个设备的正常功能。
故障原因及处理方法涵盖了电源问题、硬件故障、软件崩溃等多个方面。
二、工业设备类工业设备类机器主要指一些用于生产和制造的设备。
这类机器通常承受较大的工作压力和负荷,因此故障发生的可能性更大。
常见的故障类型包括电机损坏、传动系统故障、控制系统失效等。
在工业设备维护过程中,定期保养和故障预防是最关键的措施,以确保机器的可靠性和稳定性。
三、交通工具类交通工具类机器包括汽车、火车、飞机等,其故障可能导致严重的后果。
机械故障、电气故障以及燃油供应问题是常见的故障类型。
合理的保养和定期检查是降低交通工具故障风险的重要手段。
四、医疗设备类医疗设备的故障可能直接影响到患者的生命安全,因此其可靠性要求极高。
医疗设备故障的原因包括电源故障、传感器故障、软件错误等。
提高设备可靠性、完善维护措施和紧急备用设备是降低医疗设备故障风险的重要举措。
五、办公设备类办公设备类主要包括打印机、复印机、传真机等。
这些设备通常在日常办公中使用频率较高,因此容易发生故障。
常见故障类型包括卡纸、纸张堵塞、墨盒干燥等。
提前维护、及时清洁和采用高质量的耗材是预防故障的有效措施。
综上所述,机器故障的发生范围广泛,涉及电子设备、工业设备、交通工具、医疗设备以及办公设备等多个领域。
针对不同类型的机器故障,我们需要采取不同的应对措施,以确保机器的正常运行和延长使用寿命。
滚动轴承故障机理分析
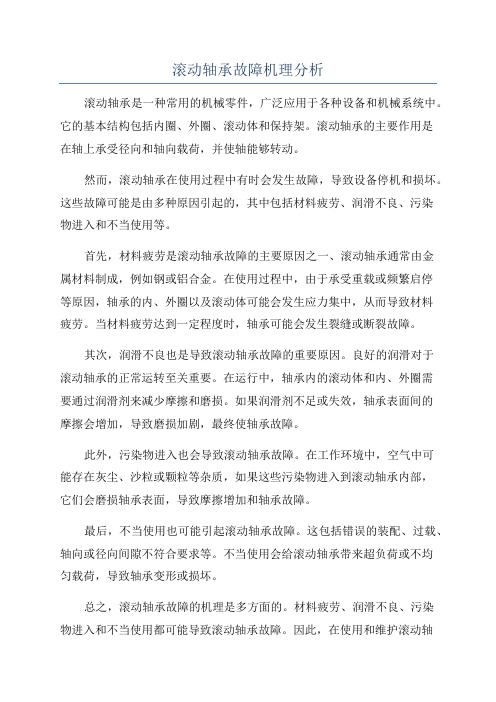
滚动轴承故障机理分析滚动轴承是一种常用的机械零件,广泛应用于各种设备和机械系统中。
它的基本结构包括内圈、外圈、滚动体和保持架。
滚动轴承的主要作用是在轴上承受径向和轴向载荷,并使轴能够转动。
然而,滚动轴承在使用过程中有时会发生故障,导致设备停机和损坏。
这些故障可能是由多种原因引起的,其中包括材料疲劳、润滑不良、污染物进入和不当使用等。
首先,材料疲劳是滚动轴承故障的主要原因之一、滚动轴承通常由金属材料制成,例如钢或铝合金。
在使用过程中,由于承受重载或频繁启停等原因,轴承的内、外圈以及滚动体可能会发生应力集中,从而导致材料疲劳。
当材料疲劳达到一定程度时,轴承可能会发生裂缝或断裂故障。
其次,润滑不良也是导致滚动轴承故障的重要原因。
良好的润滑对于滚动轴承的正常运转至关重要。
在运行中,轴承内的滚动体和内、外圈需要通过润滑剂来减少摩擦和磨损。
如果润滑剂不足或失效,轴承表面间的摩擦会增加,导致磨损加剧,最终使轴承故障。
此外,污染物进入也会导致滚动轴承故障。
在工作环境中,空气中可能存在灰尘、沙粒或颗粒等杂质,如果这些污染物进入到滚动轴承内部,它们会磨损轴承表面,导致摩擦增加和轴承故障。
最后,不当使用也可能引起滚动轴承故障。
这包括错误的装配、过载、轴向或径向间隙不符合要求等。
不当使用会给滚动轴承带来超负荷或不均匀载荷,导致轴承变形或损坏。
总之,滚动轴承故障的机理是多方面的。
材料疲劳、润滑不良、污染物进入和不当使用都可能导致滚动轴承故障。
因此,在使用和维护滚动轴承时,我们应该注意保持良好的润滑、避免污染物进入、正确安装和使用,并定期检查轴承的状态,及时发现并处理潜在的故障问题,以确保设备的正常运转。
机械零部件故障模式原因和机理

故障模式分类 机械零件典型故障模式及机理
按失效的宏观特征,可将零件失效分为四大类。 变形失效 举例:在工程中常见的 断裂失效 失效实例? 磨损失效 腐蚀失效 按失效性质和具体特征,每一类型还可以包括几 个小类,如图所示。 举例说明故障模式及原因,如表所示
5
2.1 机械零部件的故障模式和机理
变形 失效 过量弹性变形失效 过量塑性变形失效 脆性断裂失效 塑性断裂失效 环境介质引起的断裂 (应力腐蚀、氢脆断裂等) 低周疲劳 高周疲劳 机械 零件 失效 断裂 失效 疲劳 断裂 腐蚀疲劳 高温疲劳 热疲劳 冲击断裂 蠕变持久断裂 磨粒磨损 磨损 失效 粘着磨损 氧化磨损 接触疲劳 腐蚀 失效 均匀腐蚀 局部腐蚀
三向等拉伸时的应力状态最硬;单向拉伸、三向不等拉伸 均属“硬性”应力状态;单向压缩、三向不等压缩则属于 “软性”应力状态
26
应力状态
不同加载方式下的软性系数
27
应力状态
不同加载方式下的断裂情况,如表所示 零件材料的强度指标(剪切屈服强度、切断抗力和正断抗 力)与外加载荷所产生的应力状态如何配合,决定零件的断 裂形式。决定断裂形式的力学状态图 如图所示 应力状态对断裂形式的影响:
A
τ α= max σmax
1 2
α=
1 4
B
τ
α =1
α=
C
O
σ
图 决定断裂形式的力学状态图
30
工作环境
环境介质与零件失效
环境介质包括气体、液体、液体金属、射线辐照、固体 磨料和润滑剂等
介质 气体:大气、盐雾气氛、水蒸气、气液二相流 (CO,CO2)、含 H2S 气氛 液体:Cl 、OH 、NaOH、NO2 、H2S、水- 固(砂石) 液体金属:Hg-Cu 合金;Cd、Sn、Zn-铜、 Pb-铜,Nb、K-不锈钢 中子辐照,紫外线照射 磨料:矿石、煤、岩石(润滑剂)、泥浆、水 溶液
滚动轴承的故障机理与诊断

温度诊断法
总结词
通过测量轴承的温度变化,判断轴承的工作状态是否正常。
详细描述
温度诊断法是一种间接的滚动轴承故障诊断方法。通过在轴承座或轴承端盖上安装温度传感器,监测轴承的工作 温度,可以判断轴承的工作状态是否正常。如果温度过高或温差过大,可能表明轴承存在故障,如润滑不良、摩 擦过大等。
04
滚动轴承故障诊断实例
实例一:振动诊断法的应用
01
总结词
振动诊断法是通过监测滚动轴 承的振动信号来判断其运行状
态的方法。
02
详细描述
振动诊断法具有非破坏性、实 时性等优点,通过分析振动信 号的频率、幅值和波形等信息 ,可以识别滚动轴承的故障类 型和位置,以及评估故障的严
重程度。
03
总结词
振动诊断法需要使用专业的振 动测量仪器,如振动分析仪或 频谱分析仪,对滚动轴承进行
促进智能化发展
随着工业4.0和智能制造的推进,对设备的监测和故障诊断要求越来越高。滚动轴承的故 障机理与诊断研究有助于推动设备智能化的发展,提高生产效率和产品质量。
对未来研究的建议
01
加强跨学科合作
滚动轴承的故障机理与诊断涉及多个学科领域,如机械工程、材料科学
、信号处理等。建议加强跨学科合作,综合运用各学科的理论和方法,
其在实践中的可行性和效果。
THANKS
声学诊断法
要点一
总结词
通过测量轴承的声学信号,分析其频率和幅值等信息,判 断轴承的故障类型和程度。
要点二
详细描述
声在 轴承座或轴承端盖上安装声学传感器,采集轴承的声学信 号,然后分析这些信号的频率和幅值等信息,可以判断轴 承是否存在故障以及故障的类型和程度。常见的故障类型 包括轴承内圈、外圈和滚动体的故障等。声学诊断法的优 点是可以在线监测轴承的工作状态,但受环境噪声影响较 大。
机械故障诊断的基本原理

14
第一节 机械故障诊断概述
中国矿业大学机电学院
5.按功能分:
(1)简易诊断 对机械系统的状态作出相对粗略的判断。 一般利用简易测量仪器对设备进行监测,根据测 得的数据,分析设备的工作状态。
(2)精密诊断 是在简易诊断基础上更为细致的一种诊断过程。 利用较完善的分析仪器或诊断装置,对设备进行 诊断,这种装置配有较完善的分析、诊断软件。
因
等。1,2 ,
22
中国矿业大学机电学院
对于同一种故障类型,当它们发生在不 同的机械系统上时,其故障特征参量也不 同,因此,在确定某种故障的特征参量 时,应结合具体的系统进行。
23
第二节 故障特征参量
中国矿业大学机电学院
二、故障特征参量的选取原则
1、高度敏感性
机械系统状态的微弱变化应引起故障特征参量的较 大变化。
1
A、B、C
a
2
-、B、C
结论:情况A是现象a的原因(结果)
在故障分析时,形成上述差异场合的方法有轮流 切换法和换件比较法。
31
第三节 机械故障诊断的一般思维方法 中国矿业大学机电学院
轮流切换法: 场合 先行(或后行)情况 被研究现象
1
A、B、C
a
2
A、-、C
a
3
A、B、-
a
4
-、B、C
结论:情况A是现象a的原因(结果)
第三节 机械故障诊断的一般思维方法 中国矿业大学机电学院
在应用剩余法进行推断时,有以下两点需提请注意: ①必须确认复杂现象的一部分(a、b、c)是某些情
况(A、B、C)引起的,而剩余部分(d)不可能是这些 情况(A、B、C)引起的;
②复杂现象剩余部分的原因(D),不一定是个单一 的情况,还可能是个复杂的情况。实际上多层次、 多原因的复杂故障树正是描述这种逻辑关系的。
建筑工程施工机械问题
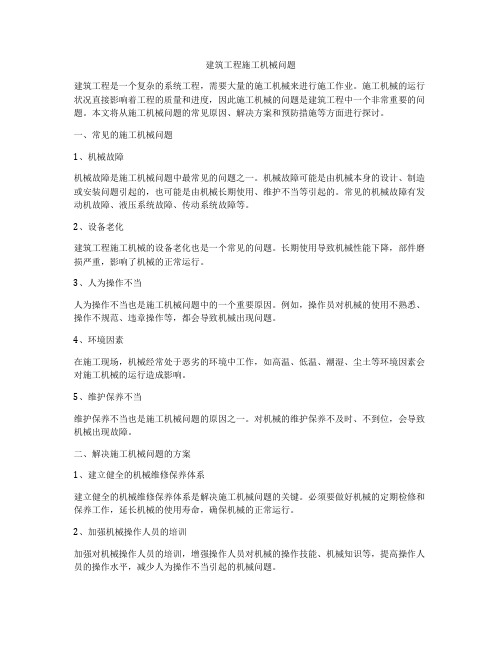
建筑工程施工机械问题建筑工程是一个复杂的系统工程,需要大量的施工机械来进行施工作业。
施工机械的运行状况直接影响着工程的质量和进度,因此施工机械的问题是建筑工程中一个非常重要的问题。
本文将从施工机械问题的常见原因、解决方案和预防措施等方面进行探讨。
一、常见的施工机械问题1、机械故障机械故障是施工机械问题中最常见的问题之一。
机械故障可能是由机械本身的设计、制造或安装问题引起的,也可能是由机械长期使用、维护不当等引起的。
常见的机械故障有发动机故障、液压系统故障、传动系统故障等。
2、设备老化建筑工程施工机械的设备老化也是一个常见的问题。
长期使用导致机械性能下降,部件磨损严重,影响了机械的正常运行。
3、人为操作不当人为操作不当也是施工机械问题中的一个重要原因。
例如,操作员对机械的使用不熟悉、操作不规范、违章操作等,都会导致机械出现问题。
4、环境因素在施工现场,机械经常处于恶劣的环境中工作,如高温、低温、潮湿、尘土等环境因素会对施工机械的运行造成影响。
5、维护保养不当维护保养不当也是施工机械问题的原因之一。
对机械的维护保养不及时、不到位,会导致机械出现故障。
二、解决施工机械问题的方案1、建立健全的机械维修保养体系建立健全的机械维修保养体系是解决施工机械问题的关键。
必须要做好机械的定期检修和保养工作,延长机械的使用寿命,确保机械的正常运行。
2、加强机械操作人员的培训加强对机械操作人员的培训,增强操作人员对机械的操作技能、机械知识等,提高操作人员的操作水平,减少人为操作不当引起的机械问题。
3、建立完善的机械故障应急处理机制建立完善的机械故障应急处理机制,及时处理机械故障,减少因机械故障导致的施工工期延误。
4、加强机械设备的管理加强机械设备的管理,定期对机械设备进行检查,修复和更新老旧设备,保证设备在使用时性能稳定。
5、优化施工机械的设计针对常见的施工机械问题,改进和优化施工机械的设计,提高机械的质量和可靠性。
三、预防施工机械问题的措施1、严格遵守机械设备使用规程严格遵守机械设备使用规程,规范操作流程,杜绝不规范操作、违章操作等导致的机械问题。
失效机理类型

失效机理类型失效机理是指产品或设备在正常使用过程中因各种原因导致功能无法正常运行或损坏的过程。
失效机理有很多不同的类型,包括机械失效、热失效、化学失效、电子失效等。
本文将重点讨论这些类型的失效机理。
机械失效是一种常见的失效机理,指的是由于受到外部或内部力的影响,导致产品或设备的机械部件不能正常工作。
机械失效可能是由材料疲劳、断裂、腐蚀、磨损等引起的。
例如,金属材料在长期受力的情况下容易发生疲劳断裂,机械设备的重要零部件经过长时间的使用和震动,可能导致裂纹产生,并最终引发断裂。
为减少机械失效的发生,可以采取定期维护、替换磨损部件、增强结构设计等措施。
热失效是指产品或设备在高温或低温条件下,导致材料结构、性能或功能的不可逆变化。
高温条件下,材料可能会发生熔化、软化、氧化等变化,导致功能失效。
低温条件下,材料会引起冷脆或冷疲劳等问题。
热失效可能会导致设备的性能下降、损坏或甚至完全失效。
为避免热失效,可以使用高温抗性材料、冷却系统等。
化学失效是指产品或设备在与化学物质接触后,引起材料或化学反应产生的物质变化,从而导致功能丧失或损坏。
化学失效可能是由于腐蚀、氧化、膨胀或溶解等反应引起的。
例如,金属与酸或碱接触后,可能发生腐蚀,导致金属的性能下降。
为防止化学失效,可以选择耐酸碱的材料、防护涂层等。
电子失效是指产品或设备中的电子元件(如电阻、电容、晶体管等)在使用过程中发生故障,导致设备无法正常工作。
电子失效可以是由于元件老化、电压过高或过低、电路连接不良等原因引起的。
为防止电子失效,可以进行定期检测、维护和更换电子元件。
此外,合理设计和制造电子产品也能减少电子失效的风险。
总之,失效机理是产品或设备不能正常工作或损坏的原因。
机械失效、热失效、化学失效和电子失效是常见的失效机理类型。
了解失效机理对于预防、检测和修复失效是非常重要的。
通过采取适当的预防和维护措施,可以最大限度地延长产品或设备的使用寿命,并确保其正常运行。
机械零部件故障模式原因和机理

实际零件工作中往往不是只受 单一载荷作用的,而是同时承 受几种类型载荷的复合作用。
17
基本载荷类型
应力分布情况 载荷类型 轴向载荷
弯曲载荷
扭转载荷
剪切载荷
接触载荷
18
载荷性质
静载荷
缓缓地施加于零件上的载荷,或恒定的载荷
冲击载荷
以很大速度作用于零件上的载荷,冲击载荷往往表现为 能量载荷
交变载荷
载荷的大小、方向随时间变化的载荷,其变化可以是周 期性的,也可以是无规则的
机械可靠性设计分析
(第二部分)
张建国
北京航空航天大学 工程系统工程系
1
机械零部件故障模式、原因和机理
故障模式分析
故障模式的基本概念 机械零件典型故障模式分类 失效分析方法
故障原因分析
受力状况 载荷类型 载荷性质 应力状态 工作环境 环境介质与零件失效 环境温度与零件失效 机械设计 材料性能与生产情况 使用维护
τ xy , τ yx , τ xz , τ zx , τ yz , τ zy , σ x , σ y , σ z
24
应力状态
定义:
零件的应力状态是指通过受载零件任一点所作的各个截 面上的应力状态
分类:
零件的应力状态可分为单向应力,多向应力等。 “软性”应力状态、“硬性”应力状态
25
应力状态
软性系数
34
使用维护情况
可能造成故障的使用维护情况
超载使用,润滑不良,清洁不好,腐蚀生锈,表面碰 伤,在共振频率下使用,违反操作规程,出现偶然事 故,没有定期维修或维修不当等,都会造成零件的早期 破坏。 例如对某发动机疲劳断裂的50根曲轴进行分析,结果表 明,其中40根曲轴疲劳断裂是由于修复后,轴颈圆角半 径太小(3mm,设计要求6mm)造成的。
转动机械常见故障及其频率特征资料重点

转动机械常见故障及其频率特征资料重点转动机械是指依靠旋转运动来完成工作的机械设备,包括电机、风机、泵等。
这些机械设备在长时间运行的过程中,常常会遇到一些故障。
了解并掌握这些故障及其频率特征,对于提高设备的可靠性和运行效率具有重要意义。
以下是一些转动机械常见故障及其频率特征的重点概述:1.轴承故障:轴承故障是转动机械中最常见的故障之一、轴承故障的频率特征包括频谱分析中的频谱峰值,通常以倍频为特征。
其他可能的特征包括振动加速度、速度和位移等参数的变化。
2.不平衡故障:不平衡是指转动机械在运行过程中由于质量不均匀分布导致的问题。
不平衡故障的频率特征主要包括由于不平衡引起的径向振动频率。
此外,还应注意检查频谱中的谐波振动频率,这些频率通常会出现在不平衡故障的频谱中。
3.错位故障:错位故障是指转动机械中轴心与旋转件中心不重合的问题。
错位故障的频率特征主要表现为以旋转频率为中心的低频分量。
同时,对于大型机械设备,还可能会出现由于错位引起的回转频率。
4.轮齿故障:对于齿轮传动的转动机械,轮齿故障是常见的问题之一、轮齿故障的频率特征主要包括齿轮传动频率及其倍频,以及其谐波振动频率。
5.润滑故障:润滑故障包括油液流量问题、油液质量问题和油温过高等。
润滑故障的频率特征主要体现在振动和声音信号中的周期性模式变化上。
以上仅是一些转动机械常见故障及其频率特征的重点概述。
在实际应用过程中,具体的故障和频率特征可能会有所不同,需要根据具体设备的特点进行分析和判断。
对于转动机械的故障诊断和预防,可以借助振动分析、声学分析、热成像等技术手段来进行监测和判断。
及早发现并处理这些故障,可以提高设备的可靠性和运行效率,减少意外停机和维修成本。
机械故障的产生机理

机械故障机理•1.磨损机理•⑴磨损过程•①跑合阶段•②稳定磨损阶段•③剧烈磨损阶段⑵磨损机理•①粘着磨损-咬合磨损•②磨粒磨损•磨粒——摩擦过程中表面凸出部分逐渐剥落的微粒和外部侵入的砂粒、灰尘等硬质微粒。
•磨粒磨损机理:磨粒及其棱面对摩擦表面的楔入凿削,形成磨粒磨损。
•③表面疲劳磨损•疲劳磨损机理:表面金属疲劳裂纹产生和扩展而产生的金属表面剥落。
•形式:麻点剥落;浅层剥落;硬化层剥落。
④腐蚀磨损•在摩擦过程中,金属同时与周围介质发生的化学或电化学反应而引起金属表面的腐蚀物剥落的现象称为腐蚀磨损。
•腐蚀磨损机理:Ⓐ氧化磨损——金属氧化膜被磨损而又被氧化的反复过程称为氧化磨损。
Ⓑ特殊介质腐蚀磨损——某些合金材料中一些元素被特殊腐蚀磨损的现象。
2.变形机理•⑴弹性变形机理•弹性变形——外力克服原子间作用力使原子间距发生变化的宏观结果。
在弹性变形中,应力和应变保持较好线性关系。
弹性变形具有可逆特性。
⑵塑性变形机理•金属塑性变形主要是滑移和孪生。
•①滑移:载荷剪应力分量造成的塑性变形。
•②晶体的一部分对应于一定的晶面沿一定方向进行相对移动。
⑶机件变形的原因①内应力、热应力、相变应力;②外载荷;③温度——金属弹性极限随温度升高而下降;④内因——机件内部缺陷3.断裂机理⑴疲劳断裂①高周疲劳机理—指低应力水平(低于材料的屈服极限或弹性极限)高寿命(大于105)的疲劳断裂,简称疲劳。
疲劳裂纹的产生→疲劳裂纹的扩展→瞬时断裂。
•②低周疲劳机理—机件在交变载荷作用下由于塑性应变的循环作用所引起的疲劳断裂。
•低周疲劳的交变应力很高接近或超过材料屈服极限,而加载频率很低,否则在循环过程中就不会出现塑性变形。
•低周疲劳寿命短,一般只有102~105。
⑵静载断裂①韧性断裂机理——是显微空洞形成、长大、连接直至最后导致断裂的破坏方式。
断口的微观特征有大量微坑,称为韧窝,宏观特征是断裂前有较大塑性变形。
②脆性断裂机理——在静拉伸应力的作用下,引起的一种脆性穿晶断裂破坏方式沿一定结晶面分离称为解理断裂。
旋转机械故障机理及诊断讲稿

相频响应曲线
当ζ=0时,当z<1,则ψ=0;当z>1,则ψ=π ;当z=1,则共振点前后相位角发生突然变化 当ζ很小时,在z<<1,即转子运行在低频范围 内,ψ≈0,即表示位移与激振力的相位相同 ;在z>>1,ψ≈π,在高频范围内,即表示位 移与激振力的相位相反 当ζ很大时,相位角ψ随z增加而增大。当z=1 (即共振)时,相位角ψ=π/2,与阻尼大小 无关,这是共振时的一个共同特征
当ω=p时,即z=1 B= e/2ζ,ψ=π/2回转半径 即为转轴的横向位移最大值B= e/2ζ 子临界转速的影响 弹性支承对转子临界转速的影响 组合转子对临界转速的影响
转子不平衡的故障机理及诊断
转子不平衡的分类
静不平衡 动不平衡 一般不平衡
转子临界转速及其影响因素
当ω<p时,ψ<π/2,在ω<<p,z≈0即转子运行 在低频范围内 ψ≈0,即表示位移与激振力的相 位相同,这时转子的重点和高点同相位
当ω>p时,ψ>π/2,在ω>>p ,z→∞,即转子 运行在高速范围内 ψ≈π,即表示位移与激振 力的相位相反,这时转子的振动很小,自动对心.
第一阶(和第二阶、第三阶……)共振频率是否 降低(轴裂纹使系统刚度下降,故共振频率也 有所降低)
共振峰的开裂(与裂纹有关的轴的不对称性导 致了两个横向振型的差别)
轴振动变化
3-2-1
p2=k/m;2n=r/m
..
.
x+2nx+ px2x=eω2 cosωt
.y.+2ny. + py2y=eω2 sinωt
故障模式机理分析报告范文

故障模式机理分析报告范文随着科技的不息进步和应用的广泛推广,各种设备和系统的故障现象也时有发生。
针对这些故障状况,进行故障模式机理分析是一种有效的方法,可以救助我们深度了解故障产生的原因和机理,从而指导我们更好地进行故障排除和预防。
一、故障描述在本次故障模式机理分析中,我们关注的是某工厂的生产线上的一个设备,该设备在应用过程中出现了频繁的停机现象。
设备的停机时间较长,严峻影响了生产效率,需要尽快找到故障原因。
二、故障模式分析依据工厂的实际状况和故障描述,我们可以初步裁定故障模式可能是由以下几个方面造成的:1. 供电问题:在设备应用过程中,供电不稳定可能会导致设备异常运行或者停机。
因此,我们需要对设备的供电电压波动状况进行监测和分析。
2. 传感器故障:设备的传感器起着关键的监测和控制作用,若果传感器出现故障或者损坏,可能会导致设备异常运行或者停机。
因此,我们需要对设备的传感器进行检查和测试,确保其工作正常。
3. 机械故障:设备的机械部件在长时间运行中,可能会出现磨损、松动等问题,导致设备停机。
因此,我们需要对设备的机械部件进行检查和维护,以确保其正常运转。
4. 系统软件问题:设备所应用的控制系统软件可能存在BUG,导致设备异常运行或者停机。
因此,我们需要对设备的软件系统进行检查和升级,确保其正常工作。
三、故障模式机理分析依据对故障模式的初步分析,我们可以进一步进行故障模式机理分析。
通过对各个方面可能造成故障的原因进行推理和分析,我们可以得出以下结论:1. 供电问题:设备所处的地区电压不稳定,可能是周边用电设备过多导致的。
解决方法是调整电网负载,确保稳定供电。
2. 传感器故障:设备传感器长时间运行导致故障,可能是传感器质量或者设计不合理导致的。
解决方法是更换高质量的传感器或进行传感器系统的调整和优化。
3. 机械故障:设备的机械部件磨损、松动可能是运行时间过长和缺乏维护导致的。
解决方法是定期对设备的机械部件进行检查、润滑和保养。
机械结构失效机理分析与可靠性改进

机械结构失效机理分析与可靠性改进引言:机械结构失效是指机械设备在工作过程中由于各种原因导致结构功能无法正常发挥,甚至发生故障,从而影响工作效率和安全性。
正确认识机械结构失效的机理,并采取相应的可靠性改进措施,对于提高机械设备的工作效率和延长使用寿命具有重要意义。
一、机械结构失效机理分析1. 疲劳失效机理疲劳失效是指由于机械结构长期受到交变载荷作用,导致材料内发生不可逆的损伤和破坏现象。
疲劳失效机理包括应力集中、裂纹扩展和断裂。
在设计阶段,应合理进行应力分析,避免应力集中的产生,并选择适当的材料,提高机械结构的抗疲劳性能。
2. 磨损失效机理磨损失效是指机械结构在工作过程中由于材料之间产生的相对运动而导致表面损伤和材料的逐渐磨损。
磨损失效机理包括磨粒磨损、疲劳磨损和润滑失效等。
在设计阶段,应选择适当的润滑剂,合理设计机械结构的摩擦副,并定期对机械设备进行维护保养,延长机械结构的使用寿命。
3. 腐蚀失效机理腐蚀失效是指机械结构在工作环境中受到化学物质的腐蚀作用,导致材料表面发生氧化、脱落、变薄等现象。
腐蚀失效机理包括电化学腐蚀、化学腐蚀和应力腐蚀等。
在设计阶段,应选择抗腐蚀性能好的材料,采取相应的防护措施,避免腐蚀对机械结构造成损害。
二、可靠性改进措施1. 强化质量控制在机械结构的生产过程中,应严格执行相关的质量控制标准,确保每个环节都符合要求。
通过加强质量控制,避免因质量问题导致的机械结构失效,并提高机械设备的整体可靠性。
2. 定期维护保养定期对机械设备进行维护保养,发现问题及时修复,并进行必要的更换和调整。
同时,建立完善的维修记录,以便进行历史数据的分析和对机械结构进行可靠性评估。
3. 学习借鉴他人经验要加强与同行业企业的交流和合作,在工作中学习借鉴他人的经验和教训。
通过借鉴他人的成功经验和教训,可以更好地总结机械结构失效机理,并找出改进机械设备可靠性的有效途径。
4. 加强原材料选择和质量检测在机械结构设计中,应选择适合的优质原材料,并进行必要的质量检测。
- 1、下载文档前请自行甄别文档内容的完整性,平台不提供额外的编辑、内容补充、找答案等附加服务。
- 2、"仅部分预览"的文档,不可在线预览部分如存在完整性等问题,可反馈申请退款(可完整预览的文档不适用该条件!)。
- 3、如文档侵犯您的权益,请联系客服反馈,我们会尽快为您处理(人工客服工作时间:9:00-18:30)。
一、机械故障机理故障机理1.1磨损机理1、磨损的概念两个相对运动的机件相互摩擦,结果其表面分子逐渐脱落,原有的尺寸,表面质量,几何形状发生变化称为磨损。
摩擦的主要形式有以下几类:(1)干摩擦:两个金属物体在摩擦表面之间完全没有润滑油或其它润滑介质,其表面是直接接触的相互摩擦运动,存在强烈磨损。
例如离合器摩擦片与压板之间,摩擦片与飞轮,自行车制动片与制动鼓。
(2)液体摩擦:摩擦表面之间被润滑油或其它润滑介质隔开,其表面不发生直接接触的摩擦。
摩擦力很小,几乎没有磨损。
例如,发动机稳定运转时曲轴轴颈与轴承之间的摩擦。
(3)边界摩擦:因润滑油粘度下降、油膜变薄,润滑油楔的动压力不足以保证液体摩擦,使油层厚度小于表面不平度的二分之一,其摩擦表面只由一层很薄的油膜隔开的摩擦。
摩擦力较小,磨损量较小。
例如,发动机高负载、低转速和高温条件下或是泄漏时曲轴轴颈与轴承之间。
(4)半液摩擦:介于液体摩擦和边界摩擦之间,但趋向于液体摩擦的摩擦。
施加在零件上的大部分载荷由液体层所承受,而小部分载荷由零件接触表面所承受。
例如,发动机在良好工况时曲轴轴颈与轴承之间。
(5)半干摩擦:介于干摩擦和边界摩擦之间,但趋向于干摩擦的摩擦。
施加在零件上的小部分载荷由液体层所承受,而大部分载荷由零件接触表面所承受。
例如,发动机在不良工况时曲轴轴颈与轴承之间。
2、磨损的过程磨损过程分跑和、稳定、和剧烈磨损三个阶段。
如图1-1,跑和开始时表面具有一定的粗糙度,真实接触面积小,磨损先快后慢。
剧烈磨损时机械效率下降,精度丧失,产生异常噪声。
图1-13、磨损机理(1)粘着磨损粘着磨损又称咬合磨损,在对于机械性能相差不大的两种金属之间时最常见的。
分冷粘着和热粘着两种形式。
若粘着点结合强度小于两边金属强度,则分离时从接触面分开,分离面比较光滑;若粘着点结合强度大于一边金属强度,则分离时从一边金属最薄弱处分开。
磨损量和接触压力、摩擦面积、距离成正比,和材料压缩屈服极限成反比。
下图为粘着磨损的主要形式及其损坏原因:磨损量磨损过程图1-2(2)磨粒磨损条件:是接触面间存在硬质粒子,或者当摩擦件的一方比另一方硬度大得多。
在摩擦过程中,表面凸出部分渐渐剥落,这些微粒加上外部侵入的沙尘形成磨粒,由于磨粒的棱面相对于摩擦表面的取向不同,作用在磨粒上的力分为垂直于表面的分力和平行于表面的分力。
因此,磨粒磨损的实质是微量切削、压痕损伤与疲劳破坏的综合结果。
垂直分力:楔入较软材料表面,造成擦伤压痕,对脆性材料导致表面疲劳剥落。
平行分力:留下细槽痕迹,对塑性材料则切下一个连续的切屑,对脆性材料则切下一个断屑,使产生裂纹。
下图为磨粒磨损的主要形式及其损坏原因:图1-3(3)表面疲劳磨损两接触面作滚动或滚动滑动复合摩擦时,在交变接触应力作用下使材料表面疲劳而产生的物理损伤现象。
机理:疲劳磨损也是裂纹产生和破坏的过程,裂纹不断扩展造成金属表面的剥落。
下图是表面疲劳磨损的主要形式:图1-4(4)腐蚀磨损机理:摩擦时金属同周围介质发生化学或者电化学反应,引起腐蚀产物剥落。
下图为腐蚀磨损的几种主要形式:图1-51.2变形机理任何机件在外力作用下都会产生一定的变形,有弹性变形和塑性变形两种类型的变形,这里主要介绍一下塑性变形的机理。
1、滑移载荷的剪应力分量造成塑性变形,剪应力超过受晶界面的滑移抗力,晶体的一部分将沿晶面和晶向相对另一部分产生滑移。
滑移主要发生在原子排列最精密的晶面,沿着原子排列最精密的方向。
这是因为原子排列最密的面上,原子结合力最强,相邻面的间距就越大,面结合能力就越弱。
2、孪生孪生变形时晶体的一部分相对于一定的晶面沿一定方向相对移动,移动距离和原子离开孪生晶面的距离成正比。
临界孪生应力比临界滑移应力要大很多,只有在滑移很困难时,才会出现孪晶变形。
两者往往交替进行。
3、机件变形的原因机件变形的原因有内应力包括热应力和相变应力,外载荷,温度,材料的结晶缺陷。
热应力—零件上相连的部分厚薄不同,冷却速度不同,收缩时间有先后,通常厚壁受拉,薄壁受压。
相变应力—零件由于组织变化发生体积改变所引起。
外载荷—机件结构不合理,如刚度不够,在外载荷的作用下会产生变形。
温度—金属的弹性极限随温度的升高而下降。
材料的结晶缺陷—材料的内部缺陷,在应力的持续作用下也会产生变形。
1.3断裂机理断裂时机械故障中一种最危险的破坏形式,因此避免机件的断裂显得十分重要。
断裂主要由以下几种形式:高周疲劳疲劳断裂低周疲劳韧性断裂断裂静载断裂脆性断裂应力腐蚀断裂氢脆断裂环境断裂高温蠕变断裂腐蚀疲劳断裂冷脆断裂1、疲劳断裂(一)高周疲劳机理低应力、高寿命的疲劳,例如曲轴、弹簧的失效。
分为三个过程:裂纹产生、裂纹扩展、瞬时断裂。
(1)疲劳裂纹的产生裂纹总在应力最高、强度最弱的机体上产生。
有三种形式:1。
夹杂物和基体界面的开裂。
在循环应力的作用下,夹杂物和基体界面分离,逐渐形成裂纹源。
2。
滑移带开裂。
金属在交变应力的作用下,驻留滑移带的表面产生“挤出脊”和“挤出沟”现象。
这些凝聚形成裂纹源。
3。
晶界开裂。
滑移带穿过晶界时,方向改变,终止在晶界处,形成高应力区,在交变应力的作用下,滑移带在晶界处引起变形不断增加,在晶界上产生裂纹。
(2)疲劳裂纹的扩展在没有应力集中的情况下,疲劳扩展分为二个阶段。
第一阶段从金属表面上驻留滑移带“挤出脊”和“挤出沟”或非金属夹杂物处开始,沿最大切应力方向的晶面向内扩展,由于晶粒位相不同、晶界阻碍,扩展方向逐渐转向和主应力垂直,速率较慢,若存在应力集中则直接进入第二阶段,方向通主应力垂直。
速率较快。
疲劳条纹主要在这阶段产生。
(3)瞬时断裂随着裂纹不断扩展,机件有效承载面逐渐减小,应力不断增大,到达强度极限时,发生瞬时断裂。
疲劳断口特征是脆性的,无明显塑性变形。
(二)低周疲劳机理(塑性疲劳)塑性应变的循环作用所引起的疲劳断裂。
加载频率很低,寿命短,交变应力很高,一般接近或超过材料的屈服强度。
高周和低周区分决定于塑性变形和弹性变形的相对比例,高周中弹性变形起支配作用,低周中塑性起支配作用。
两者都是循环塑性变形积累损伤的结果。
2、静载断裂根据断裂前产生的塑性变形量分为:(1)韧性断裂韧性断裂是显微空洞形成,长大,连接以致最终导致断裂。
断口微观特征:大量的微坑覆盖—韧窝。
断口宏观特征:明显的塑性变形。
(2)脆性断裂在静载拉伸应力作用下,引起一种脆性穿晶断裂,通常沿一定结晶面分离,也称为解理断裂。
3、环境断裂机件与特殊环境相互作用,从而引起断裂。
具有一定的环境特征。
(1)应力腐蚀断裂每种材料只对某些介质敏感,如黄铜和氨气,不锈钢和氯离子介质。
过程:首先是金属表面形成一层保护膜,,阻止腐蚀,由于拉应力和膜增厚增厚产生的附加应力,膜局部破裂,暴露在空气中,形成微电池,金属溶解,又形成新的保护膜,反复破换形成孔洞,造成应力集中,加速了塑性变形和保护膜的破裂。
造成了裂纹形成,扩展。
这是一种低应力的脆性断裂,危害十分严重。
(2)氢脆断裂氢脆是指金属材料在冶炼,加工,热处理,酸洗和电镀等过程中,或者在含氢介质中长期使用时,材料由于吸氢和氢渗而造成机械性能严重退化,发生脆断。
氢脆机理:1。
在金属凝固的过程中,溶入其中的氢没能及时释放出来,向金属中缺陷附近扩散,到室温时原子氢在缺陷处结合成分子氢并不断聚集,从而产生巨大的内压力,使金属发生裂纹。
2。
在应力作用下,固溶在金属中的氢也可能引起氢脆。
金属中的原子是按一定的规则周期性地排列起来的,称为晶格。
氢原子一般处于金属原子之间的空隙中,晶格中发生原子错排的局部地方称为位错,氢原子易于聚集在位错附近.金属材料所外力作用时,材料内部的应力分布是不均匀的,在材料外形迅速过渡区域或在材料内部缺陷和微裂纹处会发生应力集中。
在应力梯度作用下氢原子在晶格内扩散或跟随位错运动向应力集中区域。
由于氢和金属原子之间的交互作用使金属原子间的结合力变弱,这样在高氢区会萌生出裂纹并扩展,导致了脆断。
另外,由于氢在应力集中区富集促进了该区域塑性变形,从而产生裂纹并扩展。
还有,在晶体中存在着很多的微裂纹,氢向裂纹聚集时有吸附在裂纹表面,使表面能降低,因此裂纹容易扩展。
3。
某些金属与氢有较大的亲和力,过饱和氢与这种金属原子易结合生成氢化物,或在外力作用下应力集中区聚集的高浓度的氢与该种金属原子结合生成氢化物。
氢化物是一种脆性相组织,在外力作用下往往成为断裂源,从而导致脆性断裂。
(3)高温蠕变断裂蠕变就是在应力影响下,材料缓慢永久性移动或变形的趋势。
蠕变断裂是由低于材料屈服强度的应力长时间作用的结果。
同时蠕变随温度升高加剧。
温度升高提高了蠕变断裂的概率。
机理:蠕变初期,由于晶界滑动在三晶粒会交处形成裂纹核心或在晶界台阶处形成空洞核心已形成的核心达到一定尺寸后,在应力和空洞流的同时作用下,优先在与拉应力垂直的晶界上长大形成楔形或洞形裂纹孤立分散的空洞优先沿横向晶界互相连接,而形成终止在两个相邻的三晶粒交合点的“横向裂纹段”,此时,在其它与应力相垂直的晶界上这种“横向裂纹段”也相继产生相邻的“横向裂纹段”通过向倾斜晶界的扩展或与其上的空洞相联合而互相连接成“曲折裂纹”,此时,裂纹尺寸迅速扩大蠕变速度迅速增加“曲折裂纹”进一步互相连接起来,当裂纹扩展至临界尺寸时便产生蠕变断裂。
(4)腐蚀疲劳断裂在交变应力的作用下,腐蚀介质中的疲劳断裂。
机理—电化学反应。
(5)冷脆断裂当机件低于某一温度是,材料转变为脆性,冲击值下降,这种现象称为冷脆。
合金钢的低温脆化的原因是:(1)形变时位错源产生的位错被障碍物(如晶界、第二相等)阻塞时,局部应力超过钢的理论强度而产生微裂纹。
(2)几个塞积的位错在晶界合成一个微裂纹。
(3)两个滑移带相交处反应,引起不动位错,呈楔形微裂纹,它可沿解理面裂开。
1.4裂纹机理铸造裂纹锻造裂纹工艺裂纹焊接裂纹热处理裂纹磨削裂纹裂纹疲劳裂纹使用裂纹应力腐蚀裂纹蠕变裂纹裂纹在发展过程中很大一部分是用目前的无损检测方法都不能发现的,使用裂纹的形成机理在前面的断裂机理中已经讨论过。
下面几张表为几种常见工艺裂纹形成的原因和特征。
1、铸造热裂纹图1-62铸造冷裂纹图1-73、锻造冷裂纹图1-8 4、锻造过烧裂纹图1-9 5、焊接冷裂纹图1-10 6、焊接热裂纹图1-111.5 腐蚀机理化学腐蚀金属腐蚀电化学腐蚀。