production planning
production plan
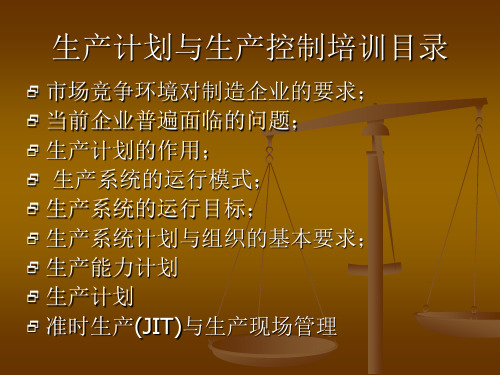
2) 改变人力数量:根据需求变化,调节人 力数量。 3) 改变工作时间. 增加工作班数、加班加点; 改变工作时间. 4) 延期交货; 5)采取措施,影响需求; 5)采取措施,影响需求; 6) 开发生产新产品;
*订货-生产式系统生产计划 订货计划工作原则: 1)按订单安排计划; )按订单安排计划; 2)近细远粗,及时调整; )近细远粗,及时调整; 3)上粗下细,给基层较大的计划权; 4)计划重点在任务委派、作业排序; 5)分批计划,综合安排。
技术 方案 10000件 10000件 20000件 20000件 30000件 30000件 40000件 40000件
收益期 望值 -27 2 7* -22
先进技术水平方案(较大能力水平) 先进技术水平方案(较大能力水平)的收益值分析表 技术 10000 20000 30000 40000 期望值 方案 10000件 10000件 20000件 20000件 30000件 30000件 40000件 40000件 0.2 -42 -46 -46 -66 0.4 -42 -6 -6 -26 0.3 -42 -6 34 14 0.1 -42 -6 34 54 -42 -14 2* -14
9)静态时差/生于工序数-最小规则(SS/ROP9)静态时差/生于工序数-最小规则(SS/ROPSlack/Remaining Operations); 10) 动态时差最小规则(DS, Dynamic slack); 动态时差最小规则(DS, 11)动态时差/剩余工时-最小规则(Dynamic 11)动态时差/剩余工时-最小规则(Dynamic slack/process time) ; 12)动态时差/剩余工序数12)动态时差/剩余工序数-最小规则 (Dynamic slack/Operation Remaining) ; 13)准备费用最小规则(NB13)准备费用最小规则(NB-The next best rule); 14) 剩余工序最小规则(FOPR-Fewest 剩余工序最小规则(FOPRoperation remaining).
生产计划—搜狗百科
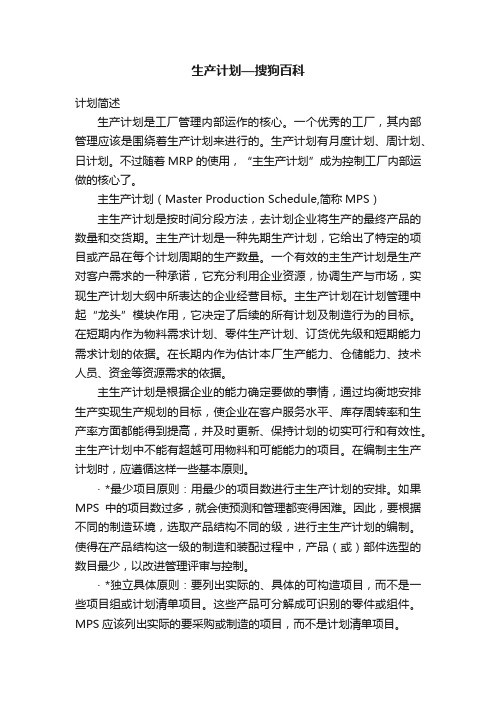
生产计划—搜狗百科计划简述生产计划是工厂管理内部运作的核心。
一个优秀的工厂,其内部管理应该是围绕着生产计划来进行的。
生产计划有月度计划、周计划、日计划。
不过随着MRP的使用,“主生产计划”成为控制工厂内部运做的核心了。
主生产计划(Master Production Schedule,简称MPS)主生产计划是按时间分段方法,去计划企业将生产的最终产品的数量和交货期。
主生产计划是一种先期生产计划,它给出了特定的项目或产品在每个计划周期的生产数量。
一个有效的主生产计划是生产对客户需求的一种承诺,它充分利用企业资源,协调生产与市场,实现生产计划大纲中所表达的企业经营目标。
主生产计划在计划管理中起“龙头”模块作用,它决定了后续的所有计划及制造行为的目标。
在短期内作为物料需求计划、零件生产计划、订货优先级和短期能力需求计划的依据。
在长期内作为估计本厂生产能力、仓储能力、技术人员、资金等资源需求的依据。
主生产计划是根据企业的能力确定要做的事情,通过均衡地安排生产实现生产规划的目标,使企业在客户服务水平、库存周转率和生产率方面都能得到提高,并及时更新、保持计划的切实可行和有效性。
主生产计划中不能有超越可用物料和可能能力的项目。
在编制主生产计划时,应遵循这样一些基本原则。
· *最少项目原则:用最少的项目数进行主生产计划的安排。
如果MPS中的项目数过多,就会使预测和管理都变得困难。
因此,要根据不同的制造环境,选取产品结构不同的级,进行主生产计划的编制。
使得在产品结构这一级的制造和装配过程中,产品(或)部件选型的数目最少,以改进管理评审与控制。
· *独立具体原则:要列出实际的、具体的可构造项目,而不是一些项目组或计划清单项目。
这些产品可分解成可识别的零件或组件。
MPS应该列出实际的要采购或制造的项目,而不是计划清单项目。
· *关键项目原则:列出对生产能力、财务指标或关键材料有重大影响的项目。
生产计划管理六个流程

生产计划管理六个流程英文回答:Production Planning and Management.Production planning and management (PP&M) is a vital aspect of any manufacturing company. It involves a series of six interconnected processes that help organizations optimize their production operations, reduce costs, and improve efficiency. These six processes are:1. Sales Forecasting and Demand Planning.Demand forecasting is the process of predicting future demand for a product or service. This helps companies determine the quantity of products they need to produce to meet customer demand.2. Production Scheduling.Production scheduling is the process of determining when and how products will be produced. It involves scheduling resources, including equipment, labor, and materials, to ensure that production is efficient and meets customer needs.3. Materials Management.Materials management involves planning and controlling the flow of materials throughout the production process. This includes procurement, inventory control, and storage.4. Capacity Planning.Capacity planning is the process of determining the maximum output that a production system can achieve. It helps companies ensure that they have the resources to meet customer demand and avoid production bottlenecks.5. Production Control.Production control is the process of monitoring andcontrolling the production process to ensure that it runs smoothly and efficiently. It involves tracking production progress, identifying and resolving problems, and making adjustments as needed.6. Quality Control.Quality control is the process of ensuring that products meet the required quality standards. It involves inspecting products at various stages of the production process and implementing measures to prevent defects.中文回答:生产计划管理六个流程。
生产计划专业术语英语
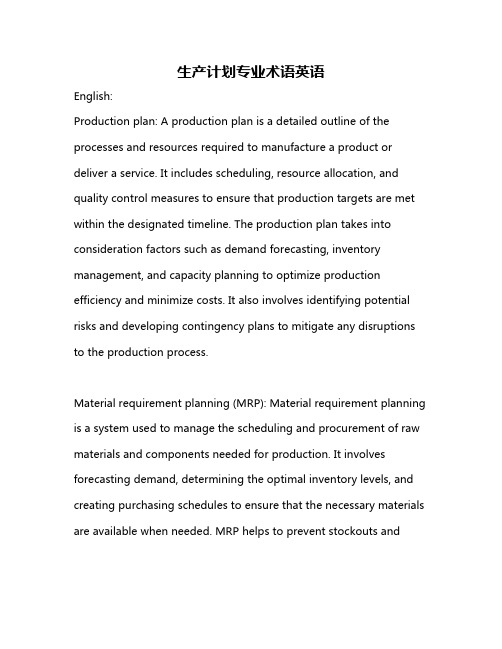
生产计划专业术语英语English:Production plan: A production plan is a detailed outline of the processes and resources required to manufacture a product or deliver a service. It includes scheduling, resource allocation, and quality control measures to ensure that production targets are met within the designated timeline. The production plan takes into consideration factors such as demand forecasting, inventory management, and capacity planning to optimize production efficiency and minimize costs. It also involves identifying potential risks and developing contingency plans to mitigate any disruptions to the production process.Material requirement planning (MRP): Material requirement planning is a system used to manage the scheduling and procurement of raw materials and components needed for production. It involves forecasting demand, determining the optimal inventory levels, and creating purchasing schedules to ensure that the necessary materials are available when needed. MRP helps to prevent stockouts andoverstock situations, thereby reducing inventory holding costs and improving production efficiency.Master production schedule (MPS): The master production schedule is a detailed plan that specifies the quantity and timing of the products to be manufactured over a specific time period. It takes into consideration factors such as customer demand, production capacity, and inventory levels to create a feasible and efficient production schedule. The MPS serves as a crucial communication tool between different departments within the organization and helps to coordinate and align production activities with overall business objectives.Capacity planning: Capacity planning involves determining the optimal level of production capacity needed to meet the demand for products or services. It considers factors such as equipment availability, labor resources, and production processes to ensure that the production facilities operate at their maximum efficiency without overloading or underutilizing their resources. Effective capacity planning is essential for optimizing the use of resources and meeting production targets while minimizing costs.中文翻译:生产计划:生产计划是制造产品或提供服务所需的详细流程和资源的大纲。
生产计划工作经验英文介绍

生产计划工作经验英文介绍Production Planning Expertise: A Comprehensive Overview.In the dynamic landscape of manufacturing, production planning plays a pivotal role in ensuring efficient utilization of resources, timely delivery of products, and overall operational excellence. This intricate process involves a meticulous orchestration of various elements to create a seamless flow of materials, labor, and equipment throughout the production process.Core Responsibilities of a Production Planner.The responsibilities of a production planner are multifaceted and encompass a diverse range of tasks, including:Demand forecasting: Analyzing historical data, market trends, and customer orders to predict future demand for products.Production scheduling: Creating and maintaining production schedules that optimize resource utilization, minimize lead times, and meet customer delivery requirements.Material planning: Determining the types andquantities of raw materials, components, and finished goods required to meet production targets.Capacity planning: Assessing production capabilities and ensuring that the necessary resources are available to meet demand.Inventory management: Establishing and maintaining inventory levels to minimize waste while ensuringsufficient stock to meet production needs.Process improvement: Identifying inefficiencies in the production process and implementing solutions to enhance productivity and reduce costs.Communication and coordination: Collaborating with various departments, including sales, engineering, and logistics, to ensure seamless coordination and information flow.Essential Skills and Qualifications.To excel as a production planner, individuals must possess a combination of technical expertise, analytical abilities, and interpersonal skills:Education: A bachelor's or master's degree in industrial engineering, manufacturing engineering, or a related field.Technical proficiency: In-depth understanding of production planning principles, scheduling techniques, and inventory management strategies.Analytical skills: Ability to analyze data, identify patterns, and make sound decisions based on complex information.Problem-solving skills: Capacity to diagnose and resolve production issues, implement creative solutions, and adapt to unforeseen circumstances.Communication and interpersonal skills: Effective communication abilities, both verbal and written, as well as the ability to build and maintain strong relationships with colleagues and stakeholders.Attention to detail: Meticulous attention to accuracy and precision in all aspects of production planning and execution.Proven Strategies for Effective Production Planning.Successful production planning hinges upon the implementation of proven strategies that enhance efficiency and optimize outcomes:Utilizing advanced planning software: Employing software tools specifically designed for productionplanning and scheduling can streamline processes, improve data accuracy, and facilitate decision-making.Adopting lean manufacturing principles: Implementing lean principles helps eliminate waste, reduce lead times, and improve overall production flow.Fostering a culture of continuous improvement: Encouraging employees to actively participate inidentifying and implementing process enhancements fosters a culture of innovation and excellence.Establishing strong supplier relationships: Establishing and maintaining collaborative partnerships with suppliers ensures reliable delivery of materials and components, contributing to smooth production flow.Leveraging predictive analytics: Utilizing data analysis techniques to forecast demand, identify potential disruptions, and optimize production planning.Benefits of Effective Production Planning.Effective production planning delivers a multitude of benefits to manufacturing organizations:Increased productivity: Optimized scheduling and resource allocation lead to reduced waste and increased output.Improved customer satisfaction: Timely delivery of high-quality products and services enhances customerloyalty and repeat business.Reduced costs: Minimizing inventory levels, optimizing resource utilization, and implementing lean principles reduce overall production costs.Enhanced flexibility: Adaptable production schedules enable organizations to respond quickly to changes in demand or market conditions.Sustainable operations: Efficient production processes contribute to environmental sustainability by reducingwaste and energy consumption.Conclusion.Production planning is a critical function in manufacturing that requires a comprehensive understanding of production principles, analytical abilities, and problem-solving skills. By embracing proven strategies, leveraging technology, and fostering a culture of continuous improvement, organizations can optimize their production processes, enhance efficiency, and achieve operational excellence.。
综合生产计划AggregateProductionPlanning
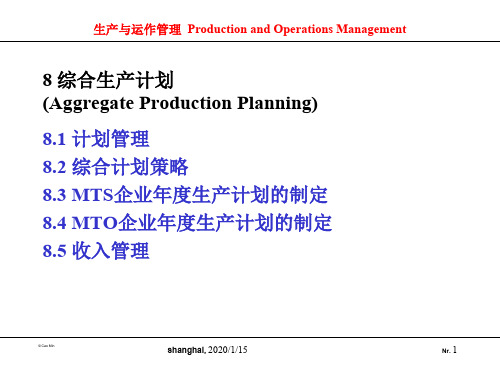
生产与运作管理 Production and Operations Management
生产计划指标
• 品种
• 产量 • 质量 • 产值:货币表示的产量指标
– 商品产值:计划期内生产的可供销售的产品价值(资金周转) – 总产值:货币表示的计划期内完成的工业生产活动总成果数
量 – 净产值:生产过程中新增价值
– 产品出产计划(Master Production Schedule, MPS,一般译成主生产计 划):以具体产品和工矿配件为计划对象
– 生产作业计划(Production Schedule):产品出产计划的执行计划,指 挥企业内部生产活动的计划
• 大型加工装配式企业包括:
– 厂级生产作业计划 – 车间级生产作业计划
50 100 125 25 300
单位产品台时 折换成代表产品C的 折换成假定产品
定额
产量
的产量
20
25
27
30
75
82
40
125
136
80
50
55
275
300
© Cao Min
shanghai, 2020/1/15
Nr. 12
生产与运作管理 Production and Operations Management
monthly or sometimes
Material Requirement Planning (MRP)
Capacity Req. quarterly time increments;
productionplannerJobdescription生产计划工作描述(范文)
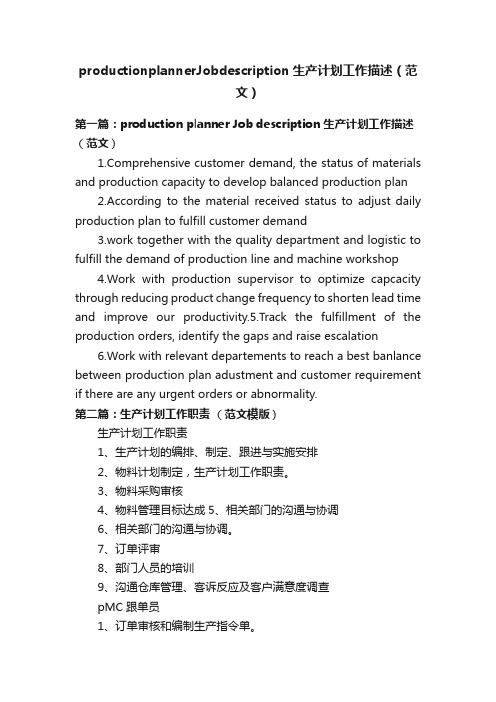
productionplannerJobdescription生产计划工作描述(范文)第一篇:production planner Job description 生产计划工作描述(范文)prehensive customer demand, the status of materials and production capacity to develop balanced production plan2.According to the material received status to adjust daily production plan to fulfill customer demand3.work together with the quality department and logistic to fulfill the demand of production line and machine workshop4.Work with production supervisor to optimize capcacity through reducing product change frequency to shorten lead time and improve our productivity.5.Track the fulfillment of the production orders, identify the gaps and raise escalation6.Work with relevant departements to reach a best banlance between production plan adustment and customer requirement if there are any urgent orders or abnormality.第二篇:生产计划工作职责(范文模版)生产计划工作职责1、生产计划的编排、制定、跟进与实施安排2、物料计划制定,生产计划工作职责。
制造计划、制造排程
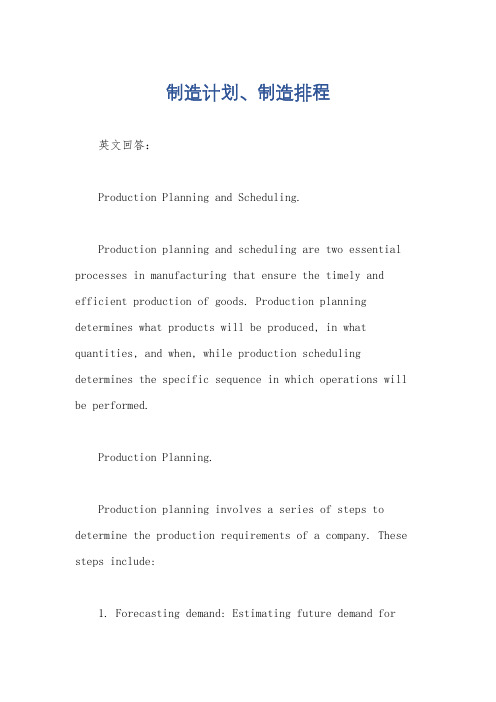
制造计划、制造排程英文回答:Production Planning and Scheduling.Production planning and scheduling are two essential processes in manufacturing that ensure the timely and efficient production of goods. Production planning determines what products will be produced, in what quantities, and when, while production scheduling determines the specific sequence in which operations will be performed.Production Planning.Production planning involves a series of steps to determine the production requirements of a company. These steps include:1. Forecasting demand: Estimating future demand forproducts based on historical data, market research, and other relevant factors.2. Determining production capacity: Assessing the available resources, including equipment, labor, and materials, to determine the production capacity of the company.3. Developing a master production schedule (MPS): Outlining the production targets for each product, taking into account demand forecasts and production capacity.4. Creating a material requirements plan (MRP): Determining the materials needed for production and the timing of their purchase or production.5. Developing a capacity plan: Ensuring that the production capacity is aligned with the production plan, considering factors such as equipment availability, labor capacity, and supplier lead times.Production Scheduling.Production scheduling involves sequencing the operations required to produce goods. The goal of scheduling is to minimize production time, reduce bottlenecks, and optimize resource utilization. Common scheduling techniques include:1. First-come, first-served (FCFS): Processing tasks in the order they arrive.2. Shortest job first (SJF): Prioritizing tasks with the shortest processing time.3. Critical ratio scheduling (CRS): Scheduling tasks based on their critical ratio, which is the ratio of remaining processing time to remaining slack time.4. Earliest due date (EDD): Scheduling tasks based on their due dates, giving priority to tasks with earlier due dates.5. Theory of constraints (TOC): Identifying andaddressing constraints in the production process to improve overall efficiency.Integration of Production Planning and Scheduling.Production planning and scheduling are closely integrated processes. The production plan provides the basis for scheduling, while scheduling provides feedback to the planning process. This integration helps ensure that production is aligned with demand, resources are utilized efficiently, and production goals are met.中文回答:生产计划和调度。
Production Planning and Control
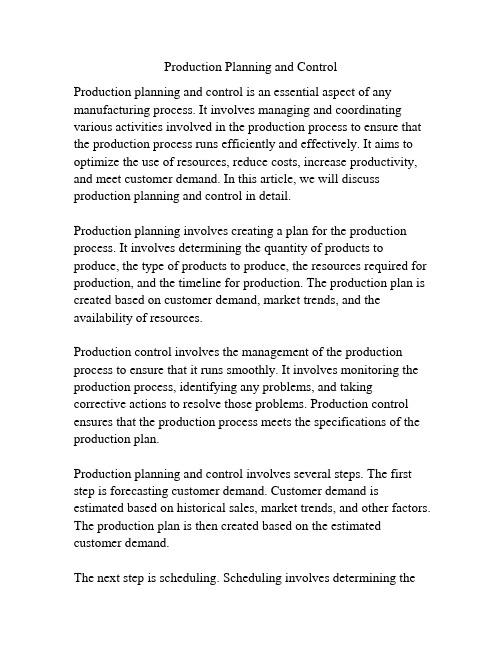
Production Planning and ControlProduction planning and control is an essential aspect of any manufacturing process. It involves managing and coordinating various activities involved in the production process to ensure that the production process runs efficiently and effectively. It aims to optimize the use of resources, reduce costs, increase productivity, and meet customer demand. In this article, we will discuss production planning and control in detail.Production planning involves creating a plan for the production process. It involves determining the quantity of products to produce, the type of products to produce, the resources required for production, and the timeline for production. The production plan is created based on customer demand, market trends, and the availability of resources.Production control involves the management of the production process to ensure that it runs smoothly. It involves monitoring the production process, identifying any problems, and taking corrective actions to resolve those problems. Production control ensures that the production process meets the specifications of the production plan.Production planning and control involves several steps. The first step is forecasting customer demand. Customer demand is estimated based on historical sales, market trends, and other factors. The production plan is then created based on the estimated customer demand.The next step is scheduling. Scheduling involves determining thetimeline for production. The production schedule is created based on the available resources, such as machinery, labor, and raw materials. The production schedule takes into consideration the lead time for each activity in the production process.Once the production plan and schedule are created, the next step is production control. Production control involves monitoring the production process to ensure that it is running efficiently. Production control involves several activities, such as production monitoring, quality control, and inventory management.Production monitoring involves tracking the production process to identify any problems or bottlenecks. Production monitoring also involves tracking the progress of the production process and ensuring that it is running on schedule.Quality control involves ensuring that the products produced meet the specifications defined in the production plan. Quality control involves inspecting the products at various stages of the production process to ensure that they meet the required standards. Inventory management involves managing the inventory of raw materials, work-in-progress, and finished products. Inventory management ensures that the required raw materials are available when needed and that there is enough finished product to meet customer demand.The success of production planning and control depends on several factors, such as effective communication, collaboration, and coordination between various departments involved in theproduction process. Effective communication ensures that everyone involved in the production process is aware of the production plan and their role in the process. Collaboration ensures that everyone is working together towards a common goal, and coordination ensures that the production process runs smoothly.In conclusion, production planning and control is an essential aspect of any manufacturing process. It involves managing and coordinating various activities involved in the production process to ensure that the production process runs efficiently and effectively. Production planning and control involves several steps, such as forecasting customer demand, scheduling, production control, and inventory management. The success of production planning and control depends on several factors, such as effective communication, collaboration, and coordination.Effective production planning and control aim to increase the efficiency of the production process by reducing the time taken to produce goods, optimizing the use of resources, and minimizing costs. To achieve this, production planners and controllers must be able to create and execute plans that map out every aspect of the production process, from planning and scheduling to inventory control and quality control.One of the primary goals of production planning and control is to minimize inventory levels while ensuring that raw materials and finished products are available when needed. This is done by creating a production schedule that optimizes the use of available resources and prioritizes the most urgent orders. By keeping inventory levels low, companies can reduce the costs associated with storing, handling and managing inventory.Another objective of production planning and control is to ensure that the production process runs smoothly and efficiently. This involves tracking the production process in real-time and identifying bottlenecks and other issues that might cause delays. Production planners and controllers must be able to analyze production data to identify potential issues before they become major problems, and take corrective action to keep the production process on track.Quality control is another important aspect of production planning and control. Manufacturers must ensure that their products meet the highest quality standards to maintain customer satisfaction and reputation. Quality control involves inspection of raw materials, components, and finished products to ensure that they meet the required specifications. To ensure that quality standards are met, production planners and controllers must work closely with quality control teams to ensure that all products meet the required quality standards.Effective communication is critical in ensuring that production planning and control works effectively. All parties involved in the production process, including suppliers, production staff, and managers, must be aware of the production plan and schedule. Effective communication is also critical in ensuring that any changes to the production plan can be quickly communicated to all those involved in the production process to avoid costly disruptions.Supply chain management is another essential element ofproduction planning and control. In today's globalized economy, many manufacturers rely on suppliers and partners to provide raw materials and components. Manufacturers must have a robust supply chain management system to ensure that they have access to the required materials and components when needed. Effective supply chain management involves close collaboration with suppliers, creating contingency plans, and implementing measures to mitigate any risks that might affect the supply chain.The effective implementation of production planning and control can lead to significant benefits for manufacturers. These benefits include increased efficiency, reduced costs, improved quality, enhanced customer satisfaction, and increased profitability. It is, therefore, essential that manufacturers invest in comprehensive production planning and control systems to optimize their production processes and remain competitive in today's fast-paced business environment.In conclusion, production planning, and control is an essential aspect of any manufacturing process. It involves managing and coordinating various activities involved in the production process to ensure that the production process runs efficiently and effectively. Effective production planning and control can lead to significant benefits for manufacturers, including increased efficiency, reduced costs, and improved quality. To achieve these benefits, manufacturers must invest in comprehensive production planning and control systems, effective communication, and supply chain management.。
第七章 生产计划大纲PP
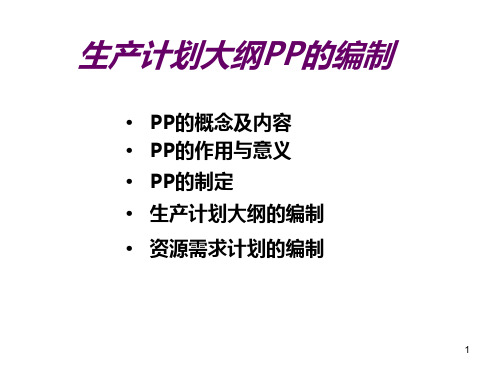
2 MTO环境下PPS编制
在MTS环境下,PPS是使生产满足预测需求量和拖欠订 货量,以此来确定月生产量和年生产量。 编制目标:决定月产量,以满足预测需求和未完成 订单。 考虑因素:期初的未完成订单应按照交货日期分布在 计划展望期内。
预 计 库 存
200
拖欠订货数=500 =5002)计算期初库存:当前库存 – 拖欠订货数=500-300=200 计算期初库存:
目标库 存 100
期初库存=100 100(库存减少) 3)计算库存变化:目标库存 – 期初库存=100 – 200 = -100(库存减少) 计算库存变化:
19
例1:编制MTS的PPS
销售 350 预测
期初 315 未完 成订 单 1470 预计 未完 成订 单 生产 计划 大纲
1435
350 350
年初拖欠量
1400 1365 1330 1295 1260 1225
年末目标拖欠量
1190 1155 1120 1085 1050
期末未 完成
1050
385 385 385 385 385 385 385 385 385 385 385 385
6
三、生产计划大纲的编制
1 生产计划PP的编制过程
收集经营规划相关信息 编制生产计划大纲初稿 编制资源需求计划
协调可用资源与资源需求 可用资源与需求资源平衡否 是 确定生计划大纲
7
否
生产计划PP编制过程 生产计划PP编制过程 PP
1)收集信息
由企业的计划、市场、工程、生产、财务各方部门提供信息。
分析资源清单 计算资源需求
比较可用资源和需求
协调差距
13
(1)分析资源清单
- 1、下载文档前请自行甄别文档内容的完整性,平台不提供额外的编辑、内容补充、找答案等附加服务。
- 2、"仅部分预览"的文档,不可在线预览部分如存在完整性等问题,可反馈申请退款(可完整预览的文档不适用该条件!)。
- 3、如文档侵犯您的权益,请联系客服反馈,我们会尽快为您处理(人工客服工作时间:9:00-18:30)。
An intelligent interactive support system forshort- and mid-term planning in aproduction planning and control systemKarsten Poeck, Christian HestermannUniversität WürzburgLehrstuhl für Informatik VI (Künstliche Intelligenz)Allesgrundweg 12, D-97218 Gerbrunn, Germanye-mail: {poeck|hester}@informatik.uni-wuerzburg.deFax: ++ 49 931 70561 201IntroductionAlthough production planning and control systems were developed and used for about thirty years, a whole bunch of problems remains unresolved. Simple data management tasks – like retrieval and manipulation of master data concerning products, orders, staff, machines and stocks – are handled quite well. However the more complex task of creating or adapting production schedules is not yet satisfactorily solved in systems currently available on the market. Intelligent knowledge based systems supporting but not replacing the human planner, are a promising approach to solve this task. We propose a support system that covers the whole range from completely interactive scheduling and rescheduling to totally automatic plan generation. In one extreme the human planner may completely construct the schedule in an interactive graphical environment whereas the system only checks the production requirements. For automatic plan generation the system applies constrained based heuristic search and an anytime variant of heuristic repair.In addition to these well known but not satisfying approaches we offer intelligent golden means: The person planning interactively is supported by the system which generates suggestions like e.g. a suitable resource and time-slot for a chosen activity. The automatic planning is capable of recognising its limitations and consulting the user asking him for solutions for difficult or unsolvable situations, e.g. by weakening or relaxing constraints.Instead of reinventing the wheel and building a system from scratch we decided to closely integrate the support system with a commercially successful production planning system.In the following sections we define the problem of short term planning more precisely, sketch the problem solving methods and conclude with a discussion of the achieved results and of previous work.2Short term planningInput data to short term planning are rough work schedules and due-dates for the orders that should be manufactured within the next few days. Each order consists of several activities. Production requirements normally imply a total or partial order on the activities. Each activity may need severalresources like • one or more working places, • staff, • materials, and finally • one or more tools. The task of short term planning is to select resources and time-slots for all activities of the orders to be scheduled. Several constraints must or should be fulfilled in the final schedule:•The due-dates of the orders have to be respected.•The temporal dependencies between the activities of an order must be kept.•The maximal capacities of the resources may not be exceeded.•The shift schedule of the staff has to be taken into account.Often it is not possible to fulfil all constraints and the relatively best schedule is to be found.3.Generation and modification of schedulesA canonical approach to short term planning is the following algorithm.1)Select an activity to be scheduled.2)Select resources and corresponding time-slots for the activity.3)Test the constraints.4)If constraints do not hold, try a limited number of local repairs to the schedule.These steps have to be repeated until the whole schedule is completed. If after the initial generation of the schedule constraints do not hold, an optimisation with iterative local repairs as in step 4 may follow.All steps but the third may either be done interactively by the human planner or automatically by the support system.•For the interactive scheduling we have prototypically implemented a planning table that deliberately imitates standard graphical production activity control systems. The table shows the current schedule in form of Gantt-diagrams from a resource- or order-oriented point of view. The planner may perform local changes in this table. In a separate table he may select activities to be scheduled or select resources and time-slots for one specific activity. This selection may be supported by the system pointing to urgent activities, e.g. those using heavily loaded resources, or proposing a valid resource for a chosen activity. To allow for greater flexibility the planner may also change the scheduling specification at problem solving time.•For the automated schedule generation we have enhanced standard constrained based search techniques with heuristic scheduling knowledge. In addition to forward checking and lookahead,e.g. [Keng & Yung 89], we also take explicit scheduling knowledge for the selection of theactual activity and the corresponding resources and time-slots into account. By explicitly representing and using the knowledge of human planners we are able to deal with the large differences between various production environments. Instead of chronological or dependency directed backtracking with constraint violations we apply – although developed independently –a variant of iterative repair [Zweben et al. 94]. The main differences from our propose-and-exchange method [Poeck & Puppe 92] to iterative repair are first that we explicitly look formulti-step repairs and may perform an A-search in the space of possible repairs and second that we use an anytime variant [Body & Dean 94]. The differences between the methods are discussed in greater detail in [Poeck 95].Unlike the fixed order based planning in ISIS [Fox 87] or the mainly resource based planning in OPIS [Smith et al. 86] this scheduling scenario allows us to offer different planning strategies custom tailored for the specific application. It covers generating of new schedules as well as correcting and adapting existing schedules, for example to fit in newly acquired orders or to react to the unforeseen breakdown of machines.4Extensions for mid-term planningMid-term planning has roughly the same goals as short-term. It essentially operates on orders with or without due-dates and resources. The differences are the following:•The detailed orders must be condensed. Only one resource, normally the machine, is considered;its availability results roughly from the working hours of the personnel. Often several machines of the same type are combined; doing this multiple times introduces planning on different hierarchical layers. We also allow the combination of several activities executed in sequence and in the same department.•For mid-term planning it is not necessary to do date calculations as detailed as in short-term planning. Instead an activity can be scheduled on a day-to-day or even weekly base. We are developing a quantitative temporal reasoning subsystem to cope with these requirements.•In addition to the resources the materials must be planned. In contrast to the classical MRP-approach the lead times are not stored in the parts' description data but are calculated from the capacity-situation thus drastically reducing the work-in-progress.•In short-term planning most orders are considered as single tasks processed on their own. Mid-term planning has to consider the fact that complex products consist of multiple purchase and production orders which have to be coordinated in order to meet the due-date of the customer's order.•The result of mid-term planning are earliest start- and latest finish-dates for the various orders and their activities as well as purchase order proposals for the materials needed. These data are in turn used by the short-term planning described above.Despite these differences the underlying problem structure is very similar to short-term planning. Orders and their activities plus the materials needed have to be scheduled regarding the constraints resulting from resource and material availability. That's my we may use the same scheduling method both for short- and mid-term planning.5Discussion and previous workUp to now we have implemented the scheduling toolbox COKE [Poeck & Gappa 93] for assignment problems. The main application of COKE is hitherto time table planning for schools. We have evaluated the time table planner retrospectively with data from a school in Karlsruhe [Poeck & Puppe 92], a computed schedule is currently in use in a school in Würzburg [Poeck 95]. We have prototypically extended this toolbox to handle the requirements of short term planning in close co-operation with the production planning and control system VPPS [Kernler 93, Mai & Jankowski 92] of infor GmbH. After designing a data model as an extension to wide-spread structures used in commercial production planning systems we have implemented a file based interface to VPPS to transfer problem specification data like orders with due-dates, availability of resources, etc. We intend to improve this prototype with a more efficient ODBC-interface to the corresponding relational database. We have extended the scheduling methods to handle continuos and multiple assignment. An interactive plan table has been developed that allows the interactive generation and manipulation of schedules. We are about to start a research project [Hestermann 95] in co-operation with the supplier of VPPS and three industrial partners to complete, evaluate and refine the presented methods within three industrial partners. We also intend to cover mid-term planning within the week or month range by applying intelligent data reduction mechanisms.ReferencesBoddy, M., Dean, T.L. (1994) Deliberation scheduling for problem solving in time constrained environments. AI 67, 245-285Fox, M.S. (1987). Constraint-Directed Search: A Case Study of Job-Shop Scheduling, Morgan Kaufmann. Hestermann, C. (1995). An intelligent co-operative support system for short- and mid-term planning in production planning and control systems (In German). Internal project report, University of Würzburg.Keng, N., Yun, D.Y.Y. (1989). A planning/scheduling methodology for the constrained resource problem, Proceedings of the 11'th IJCAI, 998-1003.Kernler, H. (1993). Production planning and control in the third generation – foundations, methods and suggestions, (In German), Hüthig Verlag Heidelberg.Mai, W, Jankowski, F. (1992). CIM market survey (In German). Series advances in CIM-technology, Vol. 4, vieweg. Poeck, K. (1995). Configurable problem solving methods for classification and assignment (in German). PhD-thesis, University of Würzburg (to be published in Infix Verlag).Poeck, K., Gappa, U. (1993). Making role-limiting shells more flexible. Knowledge Acquisition for Knowledge Based Systems, Proceedings of the 7th EKAW, Aussenac, N. et al. (Eds.), LNAI 723, Springer-Verlag, 103-122. Poeck, K., Puppe, F. (1992). COKE: Efficient solving of complex assignment problems with the propose-and-exchange method. Proceedings of the 5th International Conference on Tools with Artificial Intelligence, Arlington, Virginia, USA, 136-143.Puppe, F. (1993). Systematic Introduction to Expert Systems: Knowledge Representations and Problem-Solving Methods. Springer-Verlag.Smith, S.F., Fox, M.S., Ow, P.S. (1986) Constructing and Maintaining Detailed Production Plans: Investigations into the Development of Knowledge-Based Factory Scheduling Systems, AI Magazine, Fall 1986, 45--61Zweben, M., Daun, B., Davis, E., Deale, M. (1994). Scheduling and rescheduling with iterative repair. In [Zweben & Fox 94], 241-255.Zweben, M., Fox, M.S. (Eds, 1994). Intelligent Scheduling. Morgan Kaufmann.。