Lec12-Single-Cycle-dp
VB12分离纯化设备的优势
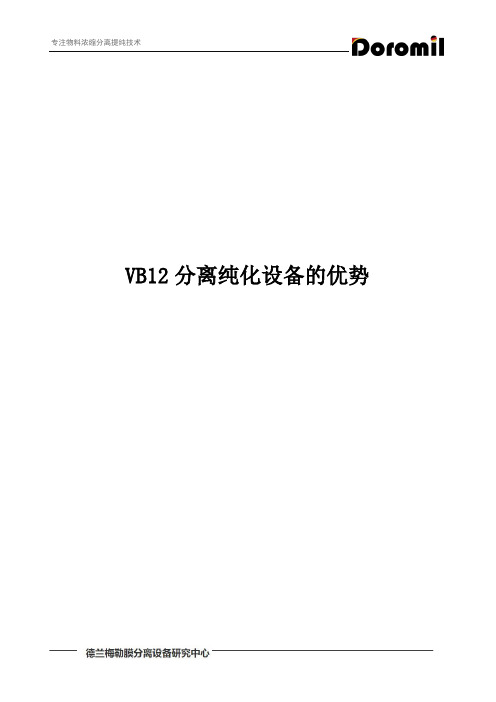
VB12分离纯化设备的优势
VB12又叫钴胺素,是一种含金属元素的维生素。
自然界中的VB12都是微生物合成的,高等动植物不能制造VB12。
VB12的功能很多,因此人们对于VB12的分离纯化技术也十分的关注。
下面,就为大家介绍一下VB12分离纯化设备的优势有哪些?
采用VB12分离纯化设备的优势:
1、设备高度一体化,全自动化控制,操作轻松方便,且保证生产连续稳定运行;
2、提高产品收率、纯度及出料浓度;
3、减少树脂耗量约50-90%;
4、减少化学药品、洗脱剂的耗量30-65%,减少废水排放量30-85%;
5、避免设备重复投资,且减少占地面积50-80%;
6、能使多级分离步骤同时进行,可将复杂的工艺简单化,越是复杂的分离过程,越能发挥其优越性。
以上就是为大家介绍的VB12分离纯化设备的优势,希望能够帮助到有需要的伙伴们。
GB 17006-10
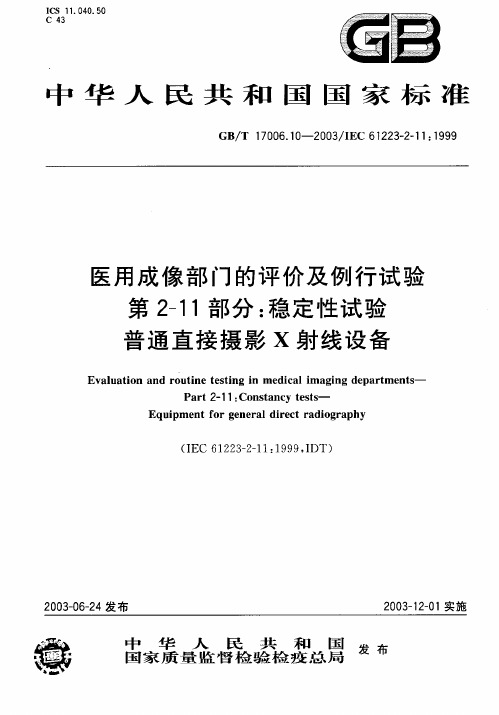
Equipmentf org enerald irectr adiography
(IEC 61223-2-11:1999,IDT )
2003-06-24发 布
2003-12-01实 施
舀兔
中 华 人 民 共 和 国 * .4;
i}y} 国家质量监督检验检疫总局 一’1.
GB/T 17006.10- 2003/IEC 61223-2-11:1999
x射 线 设 备 的 可 互 换部件如 : — 附 加 诊 板 ;
— 限 束 器 ;
— 息者 支架或其他处于辐射线束中的衰减材料 ; — 自动 控制系统的辐射探测器; — 防 散 射 沁线栅 ; 以 及 与 试验仪器 有关的物品 ; — x 射 线 摄 影暗匣和增感屏的组合 ; — 试 验 器 件 ; — x 射 线 摄 影胶片类型和乳剂号;
3 术语
3.1 要 求 的 程 度 在 本 部 分中 ,下列术语具 有特定的含义 : — “应 ”(shall):表示某 项要求具有强制性 ; — “宜 ”(should):表示某项要求 具有很 强的推荐性 ,但不 是强制的 ; — “可 ”(may):用来说明为达到某项要求所容许 的方 法 ; — “特 定的”(specific):用 以表示本 部分 中所 叙述 的或在其 他标准 中所 引用的确 定信息 ,通常 涉 及 到 特 殊 的 操 作 条件 、试验 安排 或与符合性有关的值 ; — “规 定的”(specified):用以表示制造商在随机文件中或在与考 虑中 的设 备有关 的其他 文件 中所 叙 述 的 确 定 信 息 ,通常涉及其预期 用途 ,或与其使用 或测定一致性试验有关 的参数或条件 。
lect_12FS
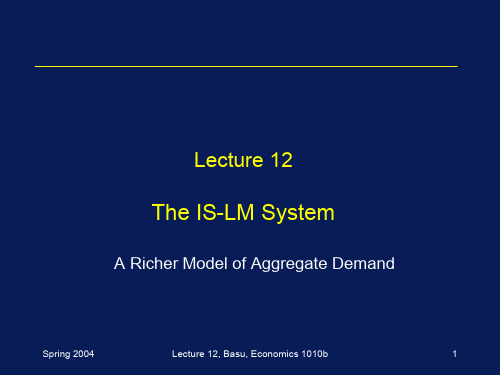
(
)
10
Think of capacity utilization as (1 – u ) for capital
Spring 2004 Lecture 12, Basu, Economics 1010b
III. The IS Curve
Spring 2004
Y = C(Y T ) + I ( r ) + G
dY dY = CY +1 dG dG The multiplier
dY 1 1 = = >1 dG 1 CY 1 MPC
Increased G increases Y more than one for one at all levels of r But we don’t yet know the equilibrium change in Y
7
The Classical System
Supply of goods:
Y = F K ,(1 u *)L = Y
Simple model of demand for goods = supply:
(
)
Y = C Y T + I (r ) + G
Determines real interest rate, r* Demand for money = real money supply: M = L r + π ,Y P
.
Loanable funds: S = supply of funds, I = demand Keynes’s insight: without full employment, equilibrium can come from changes in Y as well as r Note that S is increasing in Y (since MPC < 1)
THERMOLEC电热器类型FC、SC、FT和ST的安装、操作和维护指南说明书
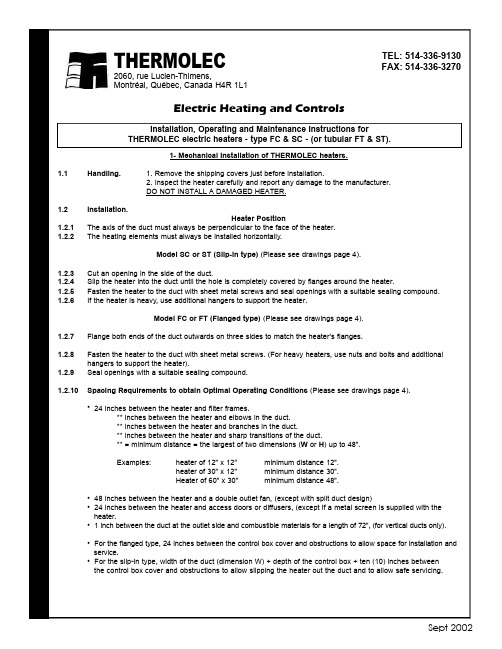
Electric Heating and ControlsSept 2002TEL: 514-336-9130FAX: 514-336-3270Installation, Operating and Maintenance Instructions forTHERMOLEC electric heaters -type FC & SC -(or tubular FT & ST).1- Mechanical Installation of THERMOLEC heaters.1.1Handling.1. Remove the shipping covers just before installation.2. Inspect the heater carefully and report any damage to the manufacturer.DO NOT INSTALL A DAMAGED HEATER.1.2Installation.Heater Position1.2.1The axis of the duct must always be perpendicular to the face of the heater.1.2.2The heating elements must always be installed horizontally.Model SC or ST (Slip-in type) (Please see drawings page 4).1.2.3Cut an opening in the side of the duct.1.2.4Slip the heater into the duct until the hole is completely covered by flanges around the heater.1.2.5Fasten the heater to the duct with sheet metal screws and seal openings with a suitable sealing compound.1.2.6If the heater is heavy, use additional hangers to support the heater.Model FC or FT (Flanged type) (Please see drawings page 4).1.2.7Flange both ends of the duct outwards on three sides to match the heater’s flanges.1.2.8Fasten the heater to the duct with sheet metal screws. (For heavy heaters, use nuts and bolts and additional hangers to support the heater).1.2.9Seal openings with a suitable sealing compound.1.2.10Spacing Requirements to obtain Optimal Operating Conditions (Please see drawings page 4).• 24 inches between the heater and filter frames.** inches between the heater and elbows in the duct.** inches between the heater and branches in the duct.** inches between the heater and sharp transitions of the duct.** = minimum distance = the largest of two dimensions (W or H ) up to 48”.Examples:heater of 12” x 12”minimum distance 12”.heater of 30” x 12”minimum distance 30”.Heater of 60” x 30”minimum distance 48”.• 48 inches between the heater and a double outlet fan, (except with split duct design)• 24 inches between the heater and access doors or diffusers, (except if a metal screen is supplied with the heater.• 1 inch between the duct at the outlet side and combustible materials for a length of 72”, (for vertical ducts only).• For the flanged type, 24 inches between the control box cover and obstructions to allow space for installation and service.• For the slip-in type, width of the duct (dimension W) + depth of the control box + ten (10) inches between the control box cover and obstructions to allow slipping the heater out the duct and to allow safe servicing.THERMOLEC2060, rue Lucien-Thimens,Montréal, Québec, Canada H4R 1L112.12Important Notes• Do not install a duct heater in a vertical duct directly above a ceiling diffuser or an opening in the ceiling.• Do not install standard heaters outdoors. Order a heater with weatherproof control box instead.• Do not install spray humidifiers upstream of duct. Install it downstream instead.• Do not cover the control box with thermal insulating materials.• Use special air intake louvers of weatherproof construction for preheat duct heaters to avoid intake of water or snow particles.Make sure that motorized damper blades are not blocked with snow or dirt. Inspect the dampers regularly to ensurea suitable airflow.2- Electrical Installation of THERMOLEC heaters.2.1Disconnect all power sources before opening the control box and working within.2.2Read the nameplate carefully and consult wiring diagram before starting to wire.2.3Supply wires:Use only wires suitable for 75°C. Wires shall be sized according to the Canadian Electrical Code requirements.All wires must be brought in through knock-outs.2.4Disconnecting means:Install a disconnect switch close to the heater according to the code unless a disconnect switch is already built intothe heater.2.5Control circuit wiring:Use class 2 wiring for control circuit connections to the duct heater.2.6Magnetic contactors:If magnetic contactors are mounted outside of the duct heater, use only contactors approved for:• 250,000 operations when controlled by auto-reset thermal cut-out (A) and by other switching devices in series with this cut-out (thermostat, step controller, air flow switch, etc.).• 100, 000 operations when controlled by auto-reset thermal cut-out (A) alone.• 100,000 operations when controlled by auto-reset thermal cut-out (A) plus manual reset cut-out in series.(A&M).• 6,000 operations when controlled by manual reset cut-out (M) alone.2.7External Controls ratings:Rating of external control devices shall be suitable for handling the VA ratings as marked on the nameplate,otherwise, a back-up relay must be used.2.8Air Flow Interlock:Heaters are generally supplied with one extra terminal marked (1) for fan interlock or air sensing device connection.Remove jumper between terminals I and C before connecting the fan interlock, Select a suitable air flow sensingdevice of the differential pressure sensing type, with snap acting contacts. A slow make, slow brake device maycause undue cycling and in some instances chattering of the contactors. When fresh air dampers are used, makesure the heater is properly interlocked to prevent it from being energized before the damper is fully open.3- Operating THERMOLEC Heaters.3.1Minimum air flow.Ensure that sufficient air flow as marked on the nameplate is passing through the heater. Air flow should be evenlydistributed across the entire face of the heater. Use air turning vane at duct elbows and splitter damper at ductbranch-offs to streamline the air flow in the heater. Use suitable air flow sensing device or interlock the heater withfan. An insufficient air flow will lead to the opening of the auto-reset thermal cut-out or damage to the heatingelements.3.2Warning.The air flowing through the duct where the heater is installed shall not contain any combustible particles, nor anyflammable vapor or gas.3.3Air Temperature.The air temperature should not exceed 27°C (81°F) at the heater inlet and 66°C (151°F) at the outlet.3.4Minimum static pressure and air direction.The heater is protected by a differential pressure switch. To keep the contact of this switch closed, it is necessary tomaintain a minimum total pressure of 0,07 inches of water for a constant flow.Unless otherwise specified, all Thermolec heaters operate horizontally or vertically with the airflow in eitherdirection. This unique feature allows the contractor maximum flexibility in installation and avoidance of problems.(Please see drawings page 4)3.5Manual-reset thermal cut-outThis protection device is standard on all heaters of less than 300V and 30 KW and is optional on all other heaters.Please check the auto-reset thermal cut-out BEFORE re-setting the manual thermal cut-out. If any defest has beendetected in the auto-reset thermal cut-out, it will be necessary to replace it before re-setting the manual-resetthermal cut-out.4- Maintenance.All THERMOLEC heaters have been designed to operate long term without problems. Those responsible for equipment and maintenance should be aware of the following suggestions.,4.1Visual Inspection.THERMOLEC strongly recommends a periodic inspection. This precautionary step will help to keep your installationsoperating well. Note these eventual first signs of problems: Accumulation of dust on the heating elements, signs ofoverheating on the heater frame, traces of water or rust on the control box4.2Electrical Inspection.Two weeks after startup , all electric connections to contactors should be checked and tightened up. Before eachheating season, check the resistance between the heating elements and ground.It is also recommended to check the electrical connections to heating elements, magnetic contactors, and mainpower lugs. This inspection is recommended monthly during the first four months of operation. After that, twoinspections per heating season are sufficient4.3What are the checkpoints?-Check all fuses;-Check the resistance to ground for each circuit;-Check the resistance phase to phase for each circuit;-Check the tightening of connections at all contactors and heating elements;-Check all contactors.4.4Off-season maintenanceWhere tubular heating elements are used, THERMOLEC strongly recommends that you start the heating systemfrom time to time. This precaution will prevent moisture from percolating through the terminal gaskets intothe heating element and accumulating in the insulating powder.Should a heater be shut off for a long period, we recommend that you check carefully the resistance to ground for eachcircuit. It is important not to power a heater when too a low resistance to ground has been measured. It is alsorecommended to pay attention to any other heater operating in normal conditions.Control components such as step controllers or modulating valves (SCR) should be maintained and checked according to respective manufacturers instructions. Any defective components should be replaced only with identical origin parts.Warranty1 -THERMOLEC LTD guarantees it’s heater resistance elements against any defect in workmanship and material for a period of two years and other built-in components for a period of one year, starting from the date of shipment from it’s factory.2 -THERMOLEC LTD will repair or replace without charge, in its factory or in the field at its own discretion, the heater or part, which upon manufacturer examination, is considered to be defective.3 -Misuse of this product, or repairs made by others without THERMOLEC LTD’s authorization, will void this warranty.4 -THERMOLEC LTD shall not be held responsible for damage or delay and shall not be held liable for any charges resulting from the removal or replacement of the allegedly defective heater.5 -THERMOLEC LTD shall not be held responsible for any incidental orconsequential damage or delay due to workmanship or material. No additional charge will be accepted for repair, replacement or modification if prior written authorization was not obtained from THERMOLEC LTD.6 -Any control device or accessory, supplied with the heater, to be mounted orconnected remotely, will only be guaranteed by the manufacturer per conditions stated in paragraph 5.Installation of the FLANGED type FC or FTInstallation of the SLIP-IN type SC or STHeaterHeater Heater too close to a fan Heater too close to a filter Filtre frameHeater too close to an elbowAvoidthese overheatingconditlionsHeater too close to a transitionMinimum recommended distancefor safety and serviceObstructionObstruction24”Type FC or FTType SC or STDimension “W” + 10”Dim. “W”Universal mounting of Thermolec heatersAir DirectionTHERMOLEC HEATERAir DirectionTHERMOLEC HEATER。
MJD350 300V PNP高电压传输器TO252(DPAK)商品说明书
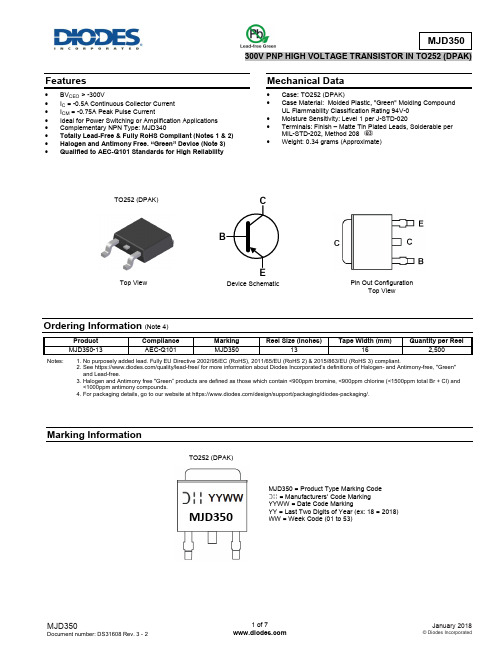
Features∙ BV CEO > -300V∙ I C = -0.5A Continuous Collector Current ∙ I CM = -0.75A Peak Pulse Current∙ Ideal for Power Switching or Amplification Applications ∙ Complementary NPN Type: MJD340∙ Totally Lead-Free & Fully RoHS Compliant (Notes 1 & 2) ∙ Halogen and Antimony Free. “Green” Device (Note 3) ∙ Qualified to AEC-Q101 Standards for High ReliabilityMechanical Data∙ Case: TO252 (DPAK)∙ Case Material: Molded Plastic, "Green" Molding Compound UL Flammability Classification Rating 94V-0 ∙ Moisture Sensitivity: Level 1 per J-STD-020∙ Terminals: Finish – Matte Tin Plated Leads, Solderable per MIL-STD-202, Method 208 ∙Weight: 0.34 grams (Approximate)Ordering Information (Note 4)Notes: 1. No purposely added lead. Fully EU Directive 2002/95/EC (RoHS), 2011/65/EU (RoHS 2) & 2015/863/EU (RoHS 3) compliant.2. See https:///quality/lead-free/ for more information about Diodes Incorporated’s definitions of Hal ogen- and Antimony-free, "Green" and Lead-free.3. Halogen and Antimony free "Green” products are defined as those which contain <900ppm bromine, <900ppm chlorine (<1500ppm tot al Br + Cl) and <1000ppm antimony compounds.4. For packaging details, go to our website at https:///design/support/packaging/diodes-packaging/.Marking InformationTop ViewDevice SchematicPin Out ConfigurationTop ViewMJD350 = Product Type Marking Code = Manufacturers’ Code Marking YYWW = Date Code MarkingYY = Last Two Digits of Year (ex: 18 = 2018) WW = Week Code (01 to 53)TO252 (DPAK)TO252 (DPAK)MJD350Thermal Characteristics(@T A = +25°C, unless otherwise specified.)Notes: 5. For a device mounted on FR-4 PCB with minimum recommended pad layout.6. Refer to JEDEC specification JESD22-A114 and JESD22-A115.Thermal Characteristics and Derating InformationElectrical Characteristics(@T A = +25°C, unless otherwise specified.)Note: 7. Measured under pulsed conditions. Pulse width ≤300μs. Duty cycle ≤2%.Typical Electrical Characteristics(@T A = +25°C, unless otherwise specified.)Package Outline DimensionsPlease see /package-outlines.html for the latest version.TO252 (DPAK)Suggested Pad LayoutPlease see /package-outlines.html for the latest version.TO252 (DPAK)Note:For high voltage applications, the appropriate industry sector guidelines should be considered with regards to creepage and clearance distances between device Terminals and PCB tracking.7°±1°Seating Plane。
功率模块引线键合界面温度循环下的寿命预测

功率模块引线键合界面温度循环下的寿命预测郭源齐;高涛;许杨剑;梁利华;刘勇【期刊名称】《机电工程》【年(卷),期】2018(035)001【摘要】针对功率模块引线键合部位在温度循环作用下的疲劳失效问题,对功率模块在温度循环作用下的疲劳寿命进行了研究,利用温度循环试验箱对3种不同封装材料的功率模块进行了温度循环实验.通过数值模拟,结合子模型技术,确定了引线键合的危险部位;并根据Coffin-Manson疲劳寿命预测理论,对上述引线键合界面进行了寿命预测.同时,基于内聚力模型和损伤演化理论提出了一套寿命预测方法,利用ABAQUS软件的用户自定义程序接口UEL,编制了相应的程序,对键合界面的疲劳寿命进行了预测.研究结果表明:两种寿命预测方法均具有一定的适应性,利用循环内聚力模型模拟能够得到与实验更吻合的结果,并且能再现键合界面的失效过程.【总页数】6页(P73-78)【作者】郭源齐;高涛;许杨剑;梁利华;刘勇【作者单位】浙江工业大学机械工程学院,浙江杭州310014;中国联合工程公司,浙江杭州310052;浙江工业大学机械工程学院,浙江杭州310014;浙江工业大学机械工程学院,浙江杭州310014;浙江工业大学机械工程学院,浙江杭州310014【正文语种】中文【中图分类】TM13;TN406【相关文献】1.功率模块IGBT失效机理与寿命预测研究综述 [J], 张树冰;刘雪婷2.IGBT功率模块寿命预测的研究与设计 [J], 王瑞3.温度循环载荷对柔性接头界面损伤的影响 [J], 王才;史宏斌;刘沛;屈转利;刘统斌;刘芹4.多轴载荷下基于权平均最大剪切应力临界面的疲劳寿命预测方法 [J], 陶志强;张鸣;朱煜;成荣;王磊杰;李鑫5.牵引负荷对补偿装置功率模块寿命预测的影响及分析 [J], 田航;陈民武;张振宇;贺超凡;鲁浩如因版权原因,仅展示原文概要,查看原文内容请购买。
废液瓶式弹簧返回12mm气压阀门VUVB-ST12-M32C-MZH-QX-D-1T1说明书

1/2
Feature Pneumatic connection, port 1 Pneumatic connection, port 3 Pneumatic connection, port 5 Materials note Material seals
Material housing Material Piston sValve function Type of actuation Valve size Standard nominal flow rate Operating pressure MPa Operating pressure Design structure Protection class Nominal size Exhaust-air function Sealing principle Assembly position Manual override Type of piloting Pilot air supply Flow direction Note on operating pressure
Vibration resistance
Shock resistance
- 1、下载文档前请自行甄别文档内容的完整性,平台不提供额外的编辑、内容补充、找答案等附加服务。
- 2、"仅部分预览"的文档,不可在线预览部分如存在完整性等问题,可反馈申请退款(可完整预览的文档不适用该条件!)。
- 3、如文档侵犯您的权益,请联系客服反馈,我们会尽快为您处理(人工客服工作时间:9:00-18:30)。
January 25, 2005
A single-cycle MIPS processor
2
Single-cycle implementation
In lecture, we will describe the implementation a simple MIPS-based instruction set supporting just the following operations.
Add 4 PC
Read Instruction address [31-0] Instruction memory
January 25, 2005
A single-cycle MIPS processor
7
Encoding R-type instructions
A few weeks ago, we saw encodings of MIPS instructions as 32-bit values. Register-to-register arithmetic instructions use the R-type format. — op is the instruction opcode, and func specifies a particular arithmetic operation (see the back of the textbook). — rs, rt and rd are source and destination registers. op 6 bits rs 5 bits rt 5 bits rd 5 bits shamt 5 bits func 6 bits
January 25, 2005
A single-cycle MIPS processor
3
Computers are state machines
A computer is just a big fancy state machine. — Registers, memory, hard disks and other storage form the state. — The processor keeps reading and updating the state, according to the instructions in some program.
ALU
ALUOp 000 001 010 110 111
January 25, 2005
Function and or add subtract slt
ALUOp
A single-cycle MIPS processor
9
Executing an R-type instruction
1. Read an instruction from the instruction memory. 2. The source registers, specified by instruction fields rs and rt, should be read from the register file. 3. The ALU performs the desired operation. 4. Its result is stored in the destination register, which is specified by field rd of the instruction word.
Control
State
January 25, 2005
A single-cycle MIPS processor
4
John von Neumann
In the old days, “programming” involved actually changing a machine’s physical configuration by flipping switches or connecting wires. — A computer could run just one program at a time. — Memory only stored data that was being operated on. Then around 1944, John von Neumann and others got the idea to encode instructions in a format that could be stored in memory just like data. — The processor interprets and executes instructions from memory. — One machine could perform many different tasks, just by loading different programs into memory. — The “stored program” design is often called a Von Neumann machine.
Chapter 5 – The Processor: Datapath and Control
January 25, 2005
A single-cycle MIPS processor
1
A single-cycle MIPS processor
An instruction set architecture is an interface that defines the hardware operations which are available to software. Any instruction set can be implemented in many different ways. Over the next few weeks we’ll see several possibilities. — In a basic single-cycle implementation all operations take the same amount of time—a single cycle. — A multicycle implementation allows faster operations to take less time than slower ones, so overall performance can be increased. — Finally, pipelining lets a processor overlap the execution of several instructions, potentially leading to big performance gains.
An example instruction and its encoding: add $s4, $t1, $t2 000000 01001 01010 10100 00000 1000000
January 25, 2005
A single-cycle MIPS processor
8
Registers and ALUs
Arithmetic: Data Transfer: Control: add lw beq sub sw and or slt
Today we’ll build a single-cycle implementation of this instruction set. — All instructions will execute in the same amount of time; this will determine the clock cycle time for our performance equations. — We’ll explain the datapath first, and then make the control unit.
RegWrite
32
Read Instruction address [31-0] Instruction memory I [25 - 21] I [20 - 16] I [15 - 11] Read register 1 Read register 2 Write register Write data Read data 1 Read data 2 Registers ALU
R-type instructions must access registers and an ALU. Our register file stores thirty-two 32-bit values. — Each register specifier is 5 bits long. — You can read from two registers at a time (2 ports). — RegWrite is 1 if a register should be written.
Mem Write Read data
address Wrem Read
Instruction [31-0] address Instruction memory
January 25, 2005
A single-cycle MIPS processor
6
Instruction fetching
The CPU is always in an infinite loop, fetching instructions from memory and executing them. The program counter or PC register holds the address of the current instruction. MIPS instructions are each four bytes long, so the PC should be incremented by four to read the next instruction in sequence.