SMED快速换模(完整版)
快速换模(SMED)

此阶段是快速换模改善的关 键动因——通常大量操作都 是外部任务,可在换模前后
完成
机器在运行
▪ 清理 ▪ 工具准备和回收 ▪ 组装子件 ▪ 文书工作
14
第2步——区分内部和外部任务
换模时间 时间 = 0
调整前
调整后
外部
内部
外部 内部
外部
▪ 在现有环境中观察活动 ▪ 决定内部活动是否能够外部化
床的对中和尺寸标定都是在刨机上完成的。
▪ 经他提议,工厂专门设置了独立的刨机工作台进行设置,效率得以提
升40%
资料来源:麦肯锡卓越运营中心
5
新乡重夫在丰田的一个项目中完善了理论,于1969年正式提出了SMED
1950
1957
1969
▪ 新乡成功地将一台1000吨冲压机的换模时间从4小时缩短到90分钟后
数秒
2
什么是SMED?
SMED的目的
SMED的目的是通过彻底检查从上一项工作结束到下一项 工作稳定运行之间的所有任务,安全地实现设备的最短停 机时间
丰田是SMED 方法的鼻祖
“...我之所以称之为‘60秒快速换模’,简称SMED,就是希 望所有的设置都能在10分钟内完成”
——新乡重夫(丰田),1969年
16
第3步——将内部操作外部化
换模时间 时间 = 0
调整前
外部
调整 后
外部
内部
内部
外部 内部
外部
外部
▪ 任何可以在机器运行时安全执行的操
作都应被外部化
资料来源:麦肯锡卓越运营中心
17
第3步——将内部操作外部化(接上页)
举例
在换模前将工具 放到指定区域, 省去换模时取工 具的时间
SMED快速换模(完整版)
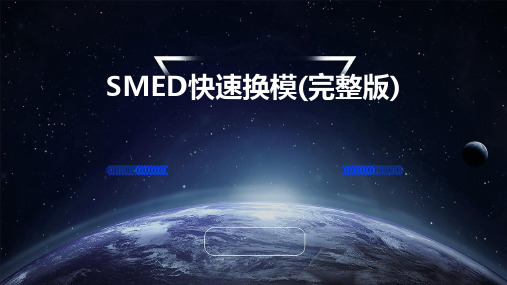
THANKS
感谢观看
安全与环境考虑
安全防护
在换模过程中,确保所有员工都佩戴必要的安全防护装备,如手 套、眼镜等。
环境整洁
保持工作区域整洁,避免因杂乱而导致的安全事故。
风险评估
在换模前进行风险评估,识别可能存在的安全隐患,并采取相应 措施进行预防。
04
SMED快速换模案例分析
案例一:某汽车制造企业的SMED应用
总结词
减少浪费
在传统的生产方式中,长时间的 换模时间会导致大量的等待和浪 费。SMED快速换模通过减少换 模时间来减少这些浪费,从而降
低生产成本。ห้องสมุดไป่ตู้
提高灵活性
SMED快速换模可以帮助企业更 快地适应市场需求变化,提高生
产线的灵活性。
SMED快速换模的应用范围
制造业
SMED快速换模适用于各种制造 业领域,特别是需要频繁更换模 具的行业,如汽车制造、电子制
案例三:某机械制造企业的SMED应用
总结词
优化生产布局,提高生产灵活性
详细描述
某机械制造企业通过对生产线的布局 进行优化,结合SMED快速换模方法, 实现了生产线的快速调整和切换,提 高了生产灵活性,满足了市场需求的 快速变化。
05
SMED快速换模未来发展趋势
智能化技术的应用
自动化设备
利用机器人和自动化设备进行快速换模,减少人工干预,提高生产 效率。
人员培训与沟通
培训
确保所有相关人员都接受过 SMED快速换模的培训,了解其 原理、操作流程和注意事项。
沟通
在换模前进行充分沟通,明确各 岗位人员职责,确保所有人对换 模计划和要求有清晰的认识。
设备与工具准备
设备
SMED快速换模(快速换型)
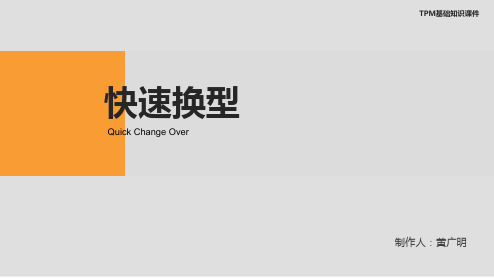
10.1 快速换型的改善流程:
初期状况
内部和外部活动 混乱不清
第一阶段
首先内部和 外部活动分开
第二阶段
将内部活动尽量 转变为外部活动
第三阶段
分别改善和简化 内部和外部活动
外部 内部 内部 外部 内部 外部
外部 内部
外部 工具提前准备 表单延后填写
少操作时间和简化动作 法则六:在内部作业转换中,必须只拆卸和安装模具。 法则七:基准不要动,调整基准浪费时间,高度等参数标准化,使用样板或刻度目视
化等 法则八:模具、工具以及材料必须事前整整齐齐地准备到设备旁边,而且模具必须事
前修理好。 法则九:能简则简。
10.3 快速换型的改善流程及奖励:
5.1 快速换型的第一步
1、记录当前的换型操作
■ 换型前后所生产的产品是什么? ■ 执行换型的频率是多少? ■ 每次换型(清场)花费的平均时间? ■ 执行了什么活动以及各活动的时间是多少? ■ 换型过程中涉及到哪些人? ■ 拍摄换型过程并将所有的活动记录在观测表单上
5.2 记录当前的换型操作及时间
快速换型
Quick Change Over
TPM基础知识课件
制作人:黄广明
目录
一. 什么是快速换型 二. 快速换型的目的 三. 换型时间的定义 四. 内部、外部活动的定义 六. 快速换型第一步(记录目前换型的时间) 七. 快速换型第二步(梳理内部外部活动) 八. 快速换型第三步(优化内部外部活动) 九. 快速换型第四步(制定换型标准) 十. 快速换型的改善流程
班组长能力(工作改善力)提升培训奖励
阶段一
要求 参与培训
奖励 一件饮料(6盒)/人
完整的快速换模(SMED)介绍
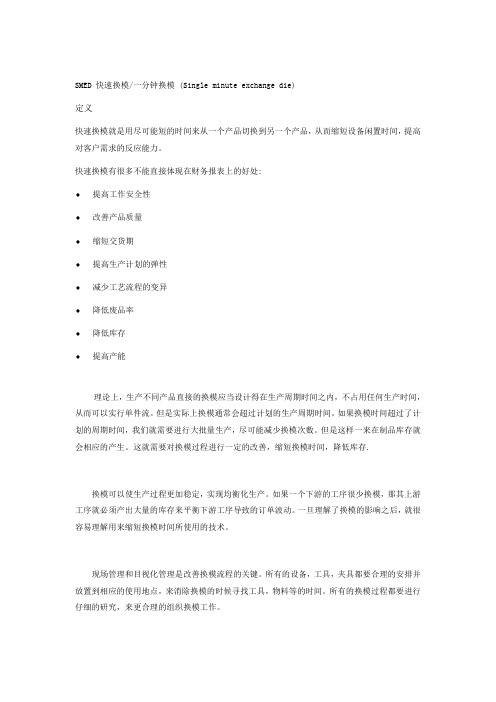
SMED 快速换模/一分钟换模 (Single minute exchange die)定义快速换模就是用尽可能短的时间来从一个产品切换到另一个产品,从而缩短设备闲置时间,提高对客户需求的反应能力。
快速换模有很多不能直接体现在财务报表上的好处:♦提高工作安全性♦改善产品质量♦缩短交货期♦提高生产计划的弹性♦减少工艺流程的变异♦降低废品率♦降低库存♦提高产能理论上,生产不同产品直接的换模应当设计得在生产周期时间之内,不占用任何生产时间,从而可以实行单件流。
但是实际上换模通常会超过计划的生产周期时间。
如果换模时间超过了计划的周期时间,我们就需要进行大批量生产,尽可能减少换模次数。
但是这样一来在制品库存就会相应的产生。
这就需要对换模过程进行一定的改善,缩短换模时间,降低库存.换模可以使生产过程更加稳定,实现均衡化生产。
如果一个下游的工序很少换模,那其上游工序就必须产出大量的库存来平衡下游工序导致的订单波动。
一旦理解了换模的影响之后,就很容易理解用来缩短换模时间所使用的技术。
现场管理和目视化管理是改善换模流程的关键。
所有的设备,工具,夹具都要合理的安排并放置到相应的使用地点,来消除换模的时候寻找工具,物料等的时间。
所有的换模过程都要进行仔细的研究,来更合理的组织换模工作。
所有的内部换模时间都尽可能转换为外部时间,以避免影响正常生产。
在换模之前,就需要预先放置好需要的工具,模具,夹具等。
一分钟换模技术也可以应用到精益设备,工具和夹具实施的所有方面。
传统的换模思维:♦每换一次模生产的数量越大,平均每个零件的加工成本越低♦减少换模数量能提高设备运行时间♦库存是质量问题,设备停机或是紧急订单的缓冲♦模式转变:“我们被经济批量公式给误导了,想当然的认为长的换模时间也是生产经营的一部分.”精益思维:♦库存不增加价值,占用空间并产生浪费。
♦库存需要额外的托盘和货架,追踪,盘点,运输和存储。
♦大批量使得生产交货期更长.♦错误的订单预测导致过多的库存,从而产生浪费快速换模的要素:1. 换模的活动可以划分为两大类:内部和外部a. 外部活动是指要换模的设备还在运行时能够完成的活动。
SMED快速换模经典教程讲解
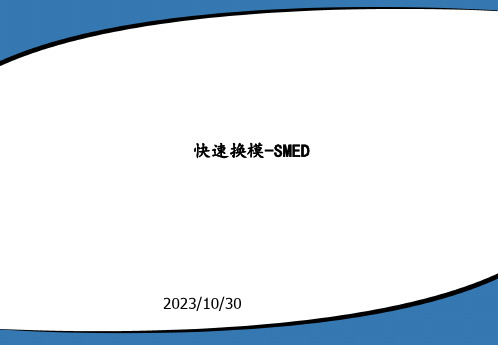
版权所有,不得翻录
第23页
第二步:区分内部与外部作业
■ 将机器运行时即能做的工作与必须停机才能做的工作分开
■ 浪费时间的实例内部时间外部时间
➢ 停机后才将模具或工具等移至机台 ➢ 在换模的时候才发现工具或模具缺陷 ➢ 在换模过程中更换或维修配件 ➢ 在模具安装好后才发现模具的缺陷 ➢ 在换模过程中到处找配件、螺钉、材料等 ➢ 没有合适的升降设备、作业标准等
20合2计3/10/30
SMED快速换模记录表
换模人:_____________
厂别:_____________
记录人:_____________
日期:_____________
本过程耗时 累计耗时
内部/外部 内部 外部
准备
拆装 替换
动作分类
定位 参数 对准 设定
试产 调整
首件 检查
作业 人数
改善建议
HITACHI 日立
机器类型 1000吨 冲压机
加工线
环型齿轮 切割机
铸模机
原切换时间 4小时
9.3小时
6小时 1.25小时
SMED切换 3分钟 9分钟
10分钟 3分钟
有效地运用SMED对换模进行改善,一般可以节省50%以上的换模时间
2023/10/30
版权所有,不得翻录
第17页
内容
课前秀 换模的概念 为什么要实施SMED SMED换模活动流程分析 案例介绍
阶段 5 持续改善
阶段 4
标准化内部及 外部作业
阶段 3 优化各作业
2023/10/30
版权所有,不得翻录
第20页
SMED实施过程:PDCA循环
快速换模SMED
SMED实施过程:PDCA循环
SMED快速换模完整版
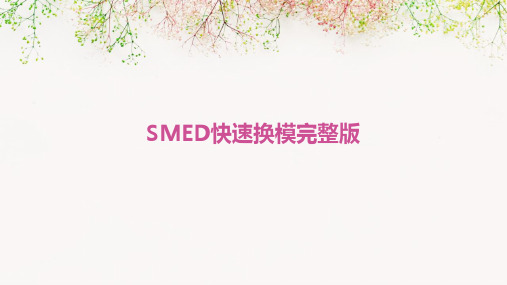
04
提高生产效率
通过减少换模时间,企业可以 更快地响应市场需求,提高生 产效率。
降低生产成本
减少换模时间可以降低生产过 程中的等待时间和资源浪费, 从而降低生产成本。
提升产品质量
通过减少生产过程中的停机时 间,可以减少产品在生产过程 中的缺陷和误差,提高产品质 量。
增强企业竞争力
快速响应市场和高效的生产流 程可以帮助企业在激烈的市场 竞争中获得优势。
分析换模流程
对换模流程进行详细分析,识 别出哪些环节可以优化,哪些 工具和设备可以改进。
制定改进措施
根据分析结果,制定具体的改 进措施,包括优化流程、改进 工具和设备等。
5S实施
01 整理 对生产现场进行整理,清除不必要的物品和垃圾,保 持现场整洁。
02
整顿
对生产现场进行整顿,将物品按照规定的位置和方式 摆放整齐,方便取用。
SMED快速换模完整版
目
CONቤተ መጻሕፍቲ ባይዱENCT
录
• SMED快速换模介绍 • SMED快速换模实施步骤 • SMED快速换模案例分析 • SMED快速换模的效益与挑战 • 如何持续优化SMED快速换模
01
SMED快速换模介绍
定义与特点
定义
快速
SMED(Single Minute Exchange of Die) 是一种快速、有效的换模技术,旨在将换模 时间从数小时缩短至数分钟。
05
如何持续优化SMED快速换模
定期评估与改进
定期评估SMED快速换模的实施效果
通过收集数据、分析换模时间、减少换模过程中的浪费等指标,评估SMED实施 的效果。
针对评估结果进行改进
根据评估结果,找出存在的问题和瓶颈,制定针对性的改进措施,持续优化 SMED实施效果。
快速换模(SMED)技巧与法则

快速换模(SMED)技巧与法则作者:佚名来源:未知时间:2009-10-08掌握了快速切换的思想步骤之后,所碰到的最大困难就是如何缩短内作业机外作业的动作时间。
以下几个技巧及法则若能确实做到,就能达到目的了。
法则一:并行操作所谓的平行作业就是指两个人以上共同从事切换动作。
平行作业最容易马上获得缩短内作业时间的效果。
又一个人慢条斯理地从事切换动作,也许需耗1小时才能完成。
若能由两人共同作业,也许会在40分钟或20分钟就能完成。
那么整个切换时间就由原先的1小时减为20分钟至40分钟之间。
而在平行作业中所需的人工时间或许会增多、不变、减少,都不是所要考虑的重点。
因为,缩短了切换的时间所获得的其他效果远大于人工成本的部分,此点是一般人较容易忽视的。
在从事平行作业时,两人之间的配合动作必须演练熟练,尤需注意安全,不可因为疏忽而造成意外伤害。
法则二:双脚勿动切换动作主要是依赖双手的动作完成,脚必须减少移动或走动的机会。
所以切换时所必须使用到的道具、模具、清洁等等都必须放在专用的台车上,并且要有顺序地整理好,减少寻找的时间。
模具或切换物品进出的动线也必须设计成很容易进出的方式,切换的动作顺序要合理化及标准化。
法则三:特殊道具所谓工具就是一般用途的器具;道具则是为专门用途的而特制的器具。
就像魔术师表演所用的**牌一样是经过特殊的设计的,如果到文具店买一般的**牌,那么魔术师要变出一些奇妙的魔术就会比较困难了。
所以魔术师所用的器具就称为道具,而不是工具。
切换动作是要尽可能使用道具不要使用工具。
因为道具可提高切换的效率,而缩短切换的时间。
此外,测定的器具也要道具化,,用块规或格条来替代用量尺或仪表的读取数值测定。
最重要的一点就是要设法减少道具的种类,以减少寻找、取放到局的时间。
法则四:剔除螺丝在切换动作时,螺丝是最常见到被用来固定模具的方法。
使用螺丝当然有其必要性,但是装卸螺丝的动作通常占去了很多的切换时间。
如果仔细观察,还会发现,滥用螺丝的地方真是太多了。
(最新整理)快速换模(SMED)
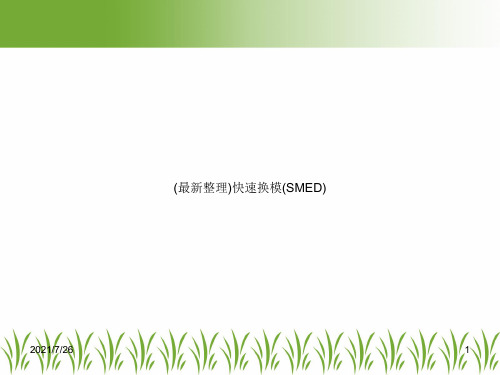
2021/7/26
11
4.1 并行作业
第四节 快速换模的技巧
并行作业是指两个人以上共同从事换模作业。
大型冲压机在进行拆卸模具时,四人同时作业。
2021/7/26
12
4.2 双脚勿动
第四节 快速换模的技巧
可把内部作业的调整动作移到外部作业,并事先做好设定的动作。
◆ 改善前:
模具A 模具夹具A
模具B 模具夹具B
◆ 改善后:
设备夹具 多功能夹具
2021/7/26
25
4.7 事先准备
第四节 快速换模的技巧
事前准备作业是属于外部作业。外部作业如果做得不好,就会影响内部作业的顺利进行,使
换模时间变长。
为了减少模具吊运时间,在冲压机旁边 划定模具临时存放区,换模之前将需更换模 具进行临时存放。
内部作业时间决定换模时间
2021/7/26
8
第三节 推行快速换模的目的
3.1 推行快速换模的必要性
传统生产方式
产品A
产品B
产品C
换模 时间 1h
加工 时间 10h
换模 时间 1h
加工 时间 10h
换模 时间 1h
加工 时间 10h
产品A 产品B
精益生产方式
产品C
10次循环加工
换模 时间 6 min
铸模机
原切换时间 4小时 9.3小时
6小时 1.25小时
SMED切换 3分钟 9分钟
10分钟 3分钟
2021/7/26
6
第二节 快速换模的基本含义
2.1 快速换模的定义
SMED(快速切换模具)

A:修正
8、标准化和文件化其结果
C:检查
7、确定程序和结果
D:实施
6、实验短期计划
5、流水线化内、外部作业
P:计划 4、找出平行的工作
3、将内部转换转换到外部去
2、分离内部转换与外部转换
1、记录当前的换型操作
四、SMED的实施过程
1、记录当前的换型操作
■ 各个转换的平均时间? ■ 执行了什么活动以及各活动的时间是多少? ■ 执行转换的频度是多少? ■ 转换过程中涉及到哪些人? ■ 转换前后所生产的部品是什么? ■ 不同部品转换的时间是多少? ■ 拍摄现行转换过程并将所有的活动记录在观测表单上?
★ 更换模具
1、使用回转台车
方法棒极了
四、SMED的实施过程
调试的消除
■ 试运行和调整占总切换时间的50% ■ 尽量消除调试,而不仅仅是减少 ■ 目标:一次性成功 ■ 在装配过程中使用标准程序,并进行双重检查 ■ 提高装配技能 ■ 提高装配可靠性的技巧
★ 使用标准设置以固定数字刻度/标尺 ★ 可视化的设置值和参照线
四、SMED的实施过程
4、找出并行的工作 提示…….
休 息 区
A1
台车区
A1
工作台
A10
工作台
A9
A7
A2 A6
A5
A1
A4
A3
制品取出放置区
A3
机械手夹具存放区
工作台
A10
模 具 存 放 区
A8
台
A10 车
存 放 区
四、SMED的实施过程
5、流水线化所有的操作
■ 分析每一个步骤的细节
■ 使用问题-原因-对策的集思广义来找出降低 每一步操作的时间
(完整word版)精益生产-SMED(快速换模)

SMEDSMED Single Minute Exchange of Die ( 快速换模),也叫快速换产。
SMEDS 50年代初期起源于日本,由Shigeo Sh in go在丰田企业发展起来,Single的意思是小于10分钟(Minutes),最初使用在汽车制作厂,以达到快速的模具切换(Excha nge of Dies) ,它帮助丰田企业产品切换时间由4小时缩短为3分钟。
SMED攵益:不需额外的库存即可满足客户要求,缩短交货时间即资金不压在额外库存上,减少调整过程中可能的错误,缩短切换的停车时间意味着更高的生产效率,即OEE提高。
什么是SMED法?SMED勺全称是“六十秒即时换模” (S ingle Minute Exchange of Die),是一种快速和有效的切换方法,快速换模法这一概念指出,所有的转变(和启动)都能够并且应该少于10分钟-----因此才有了单分钟这一说法。
所以又称单分钟快速换模法、10分钟内换模法、快速作业转换,用来不断设备快速装换调整这一难点的一种方法-将可能的换线时间缩到最短(即时换线)。
它可以将一种正在进行的生产工序快速切换到下一生产工序。
快速换模法同时也常指快速切换。
快速换模法能够并且常常是用于启动一个程序并快速使其运行,且处于最小浪费的状态。
SMED(Single Minutes Exchange of Die) 是在50 年代初期日本丰田汽车公司摸索的一套应对多批少量、降低库存、提高生产系统快速反映能力的有用技术。
这一方法是由日本的新乡重夫先生(Shigeo Shingo )首创的,并在众多企业实施论证过。
Single的意思是小于10分钟(Minutes),当新乡先生亲眼目睹发换型时间居然高达1小时的时候,他的反应“必须让流动顺畅起来”。
基于新乡先生的丰富经验,他开发了一个可以分析换模过程的方法,从而为现场人员找到了换型时间之所以长的原因,以及如何相应减少的方法。
丰田内部培训系列教材—smed(快速换模)
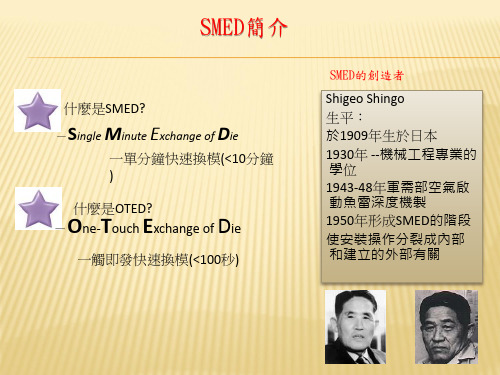
去除 ,簡化,自動化
---只按照此順序進行
各種簡化的實例圖解: •梨型槽的使用 •U型槽的使用 •C型墊片 •劈開螺絲 •減少使用螺絲
機器殼體 臺面
可視化設置值,参照線
中心夾具(v形片) 柱形杆 中心夾具(v形片)
可視化中心線
對於每种規格的可視化設計
SMED的实施过程
将内部操作转换为外部操作
■ 例 1:
3stup
优化各操作
内部 外部
内部 外部
内部
外部
1. 检查表 2. 三定 3. 改进部件 和工具的运输
外部
1预先准备 操作条件 2.功能标准化 3.部件集成化
外部
1. 消除各 种浪费
2. 快速工具
内部
内部
内部
1. 平行操作 2. 功能性夹具 3. 调试的消除 4. 机械化
全盛集团
第0步驟:
办法一:
改善前(一人切换)
改善后(二人切换)
大的机器设备在切换/装 配的各步骤间常常需要 一些来回移动
这些过多的移动浪费了 时间和付出的劳动
仔细考虑切换操作人员 的移动线路并制定出操 作的最合理的次序
发展并执行高效操作的 程序
考虑使用一人以上进行 品种切换。
每个人遵循一个固定的 程序
对于平行操作建立信号 /通知系统以确保安全
缺點:需有錄影設備
工程名
機器別
規格 NO
換模作業項目
作業者
時間
累計
實際
觀 測 者
時 間
作業工時
外 內工時 工
時
改善構想
內外部作業分開
第1步驟:
1.目的: (1)排除不良、不适当、不能使用之浪费。 (2)排除拿错、不知放置地方、不够用、缺少之浪费。 (3)排除无谓来回重复走动或搬运。 (4)排除设备停止后之清理、调整、修护、换装刀具与工具等之浪费。 (5)区分开内部和外部的作业
电器公司SMED快速换模

广东奥马电器股份有限公司一分厂
7
SMED快速换模
丰田生产模式TPS学习
SMED的基本法则:专用工装夹具、剔除螺丝、一切从简
2、提高内部换模效率: 简化模具取按动作
减少卸下和安装模具过程中的”转身”动作; 将多个拿放动作简化为一个动作; 单个动作一次放好; 使用装配架、标准模架等; 使用标准工具、同型号同大小的螺丝和螺
广东奥马电器股份有限公司一分厂
9
SMED快速换模
SMED的基本法则:并行工作
2、提高内部换模效率:多人并行工作
丰田生产模式TPS学习
大的机器设备在换模的各步骤 间常常需要一些来回移动这些 过多的移动浪费了时间和付出 的劳动
仔细考虑换模作业人员的移动 线路并制定出最合理的作业顺 序
发展并执行高效作业的程序
1
SMED快速换模
丰田生产模式TPS学习
SMED的基本法则:事前准备
1、尽量将内部作业时间转换为外部作业时间,缩短停机换模时间:
将内部作业时间转换为外部作业时间,做好前期准备。在还没有停机的时候 就做好前期准备,比如:如工装夹具准备、零部件准备、作业指导书准备、升降 工具、作业台准备等。
将取拿新模具,清洁新模具,取拿试产部件等活动在不需要停机时准备好。 然后,进行一些与模具有关的预备工作,比如:预装配、预设定、预清洁、 预热等等。
考虑使用一人以上进行模具/产 品品种切换。
每个人遵循一个固定的程序
对于平行操作建立信号/通知系 统以确保安全
广东奥马电器股份有限公司一分厂
10
SMED快速换模
丰田生产模式TPS学习
SMED的基本法则:一转即定
2、提高内部换模效率: 缩短调整时间
首先分析是要调整什么,是调整位置还是调整尺寸。 然后分析调整的原因,是因为累积误差还是标准不统一。 还要分析是否与安装、调整的熟练程度有关。 通过分析,找到对策,改善调整动作和方法,争取一次成功。
- 1、下载文档前请自行甄别文档内容的完整性,平台不提供额外的编辑、内容补充、找答案等附加服务。
- 2、"仅部分预览"的文档,不可在线预览部分如存在完整性等问题,可反馈申请退款(可完整预览的文档不适用该条件!)。
- 3、如文档侵犯您的权益,请联系客服反馈,我们会尽快为您处理(人工客服工作时间:9:00-18:30)。
SMED必要性分析
换模的速度和时间:
批量做大一点,少换几次模不就可以解决换模时间长的问题了吗?
库存量
Y
2500 PCS
换模时间
60 min
1250
30
PCS
min
125 PCS
库存掩盖了提升减少换模时间的积极性
3 min
X
SMED的必要性-案例分析:
案例: 有一来料加工的产品, 现在的换模时间为3问题:
缺少标准化的安装和调整流程和技术要求 每个调模工根据他们自己经验,按照他们认为合适的方式进行
安装和调整,缺少标准; 没有2个调模工以同样的方式安装和调整; 每个班次都觉得上个班次的调整达不到要求,要重新调整; 一些人认为安装和调整时间越长产品质量会更好。
传统换模时间的分配:
换模时间定义及构成 SMED六个基本要求 SMED四大原则 SMED基本法则
5、SMED 6步法 6、SMED实施过程和方法 7、SMED改善活动介绍 8、SMED学习总结
SMED简介
什么是SMED? Single Minute Exchange of Die(单分钟快速换模)
SMED 系统是一种能有效缩短产品切换时间的理论和方法 SMED 有些企业和学者也称为 QCD (Quick Die Change)
传统换模介绍
传统换模活动的十个步骤:
机台停机 旧产品零部件撤离现场 换模人员和工具准备 清洁工作台和模夹具 拆卸旧模具 搬运新模具及检查保养 装配新模具 通知前工序准备新零部件试产 搬运新零部件准备生产 运行调整
埃及金字塔是怎么建成的:
如果我们现场换模像建造金字塔, 那会是什么样?
(Exchange of Die); 它帮助丰田企业产品切换时间获得极大地缩短;
SMED概述:
快速换模始祖:新乡重夫(Shigeo Shingo,1909年-1990年)——日本工程师, 工业工程(IE)领域世界著名的品质管理专家,著名的丰田生产体系创始人之一。 他指出,“零损坏”就是品质要求的最高极限,被尊称为“纠错之父”。
测量、设置和较正
15%
拆装模具
5%
准备和清理工作 30%
试产和调整 50%
以自动机台换模时间为例:
我们现在拆装模具的时间在 60min,而调整的时间在90min, 两者的比例远大于5:50的比例, 拆装模具存在大量时间浪费!
传统换模活动的七大浪费:
缺陷( Defect)������
通过观察做出来的不良品进行调整
过度生产( Overproduction)������
由于调整时间过长,产生的产品批量过大
运输( Transportation)������
工具、工装和材料没有事前准备好,停机后多次运输
等待( Waiting)������
在换模调整期间,设备/机器停止运转
库存( Inventory)������
正式开始SMED之前:
换汽车轮胎典型时间 5-10分钟
有一句话是这样说的: 时间就是金钱!
耗时5.1秒钟
F1换轮胎典型时间 5-10秒
SMED概述:
SMED在50年代初期起源于日本; 由Shigeo Shingo(新乡重夫)在丰田企业发展起来; Single的意思是小于10分钟(Minute); 最初使用在汽车制作厂,以达到快速的模具切换
换模安排基于大批量的库存或排队等候
动作( Motion)������
四处走动来寻找、拿取工具、工装和材料等等
过渡处理( Processing)
������
调整数据输入依靠测量
首件检查
最根本的浪费:时间
浪费是可见的,像库存和不良品(废品或返工品),但可用的生产时间 却经常是隐性的,并经常被忽略…… 其实就是在埋葬宝藏!!! 时间是最大的浪费!!!
生 产 进 度
产品A
损失时间
停产时间
调整时间
产品B 时间
为什么换模需要那么多时间:
混淆了内部和外部的切换作业 内部作业:必须在机台停机时进行的作业 外部作业:可以在机台开机时进行的作业 很多作业是可以在机台开机时进行的,可实际上却在停机时进行
换模工作没有进行优化 没有制定合适的标准 — 谁人何时做什么 没有进行平行作业 — 2人以上同时作业 工具、工装、配件远离机台,难以取到 很多配件需要装配 有很多困难的装配、参数设置,需要进行调整
间为1分钟. 客户要求的批量为100。目标单位工时成本为1元,售价为2元。 每 小时的工时成本为48元。请问这批产品的利润是多少?
单位成本
换模时间 生产时间 批量数量
“ ……很多公司建立了一套完善的提高工人技能水平的 政策和方针,但很少有公司执行降低换模本身所需要的 技能水平的策略。”
—— 新乡重夫( Shigeo Shingo )
快速换模的境界:
境界一:No concept of Quick Changeover 没有快速换模观念 境界二:Single Minutes Exchange Die 单分钟换模 境界三:Zero Exchange Die 零换模 境界四:One Touch Exchange Die 一触换模 境界五:One Cycle Exchange Die 一周换模 境界六:No Need Exchange Die 无需换模
传统换模活动存在的问题:
在机台停机后物料才开始移动 成品被送到下一个工位 原材料在设备停止后才移走 新模具、各种配件运到机台
机台准备运行时才发现缺陷和缺少的配件 换模开始后才开始修复缺陷配件,需要调整或更换设备配件 微调开始后才发现缺陷产品
机台开动后,才发现不良的加工,夹具设定和仪器设定 内部作业开始后,操作者才发现缺陷的设备
精益生产培训系列课程--
SMED快速换模
法士特集团公司KTJ办公室
SMED快速换模
Green Belt
目录
1、SMED简介 2、传统换模介绍
传统换模的十个步骤 传统换模存在的问题 换模的七大浪费 传统换模的时间分配
3、SMED必要性分析
SMED优点 SMED成功案例
4、如何理解SMED