连铸结晶器总成
连铸区结晶器结构原理及注意要点

连铸区结晶器结构原理及注意要点连铸区结晶器结构原理及注意要点1设备组成可调式结晶器由框架与水箱、铜板、调宽液压缸、夹紧装置、足辊装置和润滑配管等零部件构成。
1.1框架与水箱结晶器水箱起支撑铜板和分配冷却水的作用。
宽面铜板的背面由宽面水箱支撑着;窄面铜板的背后由窄面水箱支撑着。
宽面冷却水从一端流到铜板下部,再通过铜板水槽流回水箱另一端。
外弧宽面铜板的水箱用左右、上下4根固定在结晶器支撑框架后梁上的顶杆在空间定位和确定出姿态,从而调整出结晶器腔型的倒锥度来。
在支撑框架后梁上的4根顶杆,通过它把外弧宽面铜板调整到外弧基准线的位置上。
内弧宽面铜板的水箱同样由4个固定在结晶器支撑框架上的夹紧装置抵住,并通过夹紧装置用内弧宽面铜板夹住两块窄面铜板,达到夹紧的目的。
结晶器的内外弧宽面冷却水箱分别挂在支撑框架的2根滑动轴上。
内外弧水箱在调宽时,可以沿着滑动轴前后移动。
1.2铜板结晶器铜板分为宽面铜板与窄面铜板。
结晶器铜板是直接影响结晶器寿命的重要零件。
对铜板材质性能有如下要求:⑴具有良好的导热性;⑵具有足够高的强度和硬度,以减少结晶器铜板的扭曲变形和机械磨损,保证结晶器铜板形状的稳定性;⑶具有较高的再结晶温度以防止连铸过程中铜板的软化和变形;⑷具有较高的抗蠕变能力和较高的热疲劳强度。
铜板采用铬锆铜,为了提高铜板的耐磨性和表面光洁程度,减少粘结和防止渗铜产生铸坯星状裂纹,在铜板表面进行镀层。
镀层为镍铁。
宽面铜板和窄面铜板均为平面。
铜板长度即为结晶器的长度,窄面铜板的宽度就是铸坯的厚度。
1.3结晶器足辊结晶器足辊设于结晶器的下方用以支撑和导向来自结晶器的铸坯,分为宽面和窄面足辊。
宽面足辊一对,窄面足辊三对。
足辊是结晶器的重要部分,要求与结晶器严格地对中,在振动时与结晶器一起振动。
在结晶器与足辊之间及辊子与辊子之间设有冷却喷嘴,以对铸坯进行喷淋冷却。
1.4结晶器调宽装置调宽装置是在结晶器的每个窄面中心线的上下两个部位各安装一只带位移传感器的油缸,油缸与窄面水箱之间铰接。
钢铁冶炼中的连铸结晶器设计分析
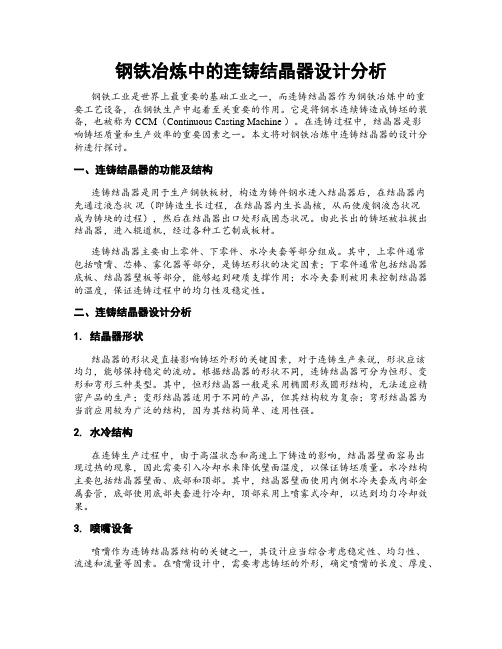
钢铁冶炼中的连铸结晶器设计分析钢铁工业是世界上最重要的基础工业之一,而连铸结晶器作为钢铁冶炼中的重要工艺设备,在钢铁生产中起着至关重要的作用。
它是将钢水连续铸造成铸坯的装备,也被称为CCM(Continuous Casting Machine )。
在连铸过程中,结晶器是影响铸坯质量和生产效率的重要因素之一。
本文将对钢铁冶炼中连铸结晶器的设计分析进行探讨。
一、连铸结晶器的功能及结构连铸结晶器是用于生产钢铁板材,构造为铸件钢水进入结晶器后,在结晶器内先通过液态状况(即铸造生长过程,在结晶器内生长晶核,从而使废钢液态状况成为铸块的过程),然后在结晶器出口处形成固态状况。
由此长出的铸坯被拉拔出结晶器,进入辊道机,经过各种工艺制成板材。
连铸结晶器主要由上零件、下零件、水冷夹套等部分组成。
其中,上零件通常包括喷嘴、芯棒、雾化器等部分,是铸坯形状的决定因素;下零件通常包括结晶器底板、结晶器壁板等部分,能够起到硬质支撑作用;水冷夹套则被用来控制结晶器的温度,保证连铸过程中的均匀性及稳定性。
二、连铸结晶器设计分析1. 结晶器形状结晶器的形状是直接影响铸坯外形的关键因素,对于连铸生产来说,形状应该均匀,能够保持稳定的流动。
根据结晶器的形状不同,连铸结晶器可分为恒形、变形和弯形三种类型。
其中,恒形结晶器一般是采用椭圆形或圆形结构,无法适应精密产品的生产;变形结晶器适用于不同的产品,但其结构较为复杂;弯形结晶器为当前应用较为广泛的结构,因为其结构简单、适用性强。
2. 水冷结构在连铸生产过程中,由于高温状态和高速上下铸造的影响,结晶器壁面容易出现过热的现象,因此需要引入冷却水来降低壁面温度,以保证铸坯质量。
水冷结构主要包括结晶器壁面、底部和顶部。
其中,结晶器壁面使用内侧水冷夹套或内部金属套管,底部使用底部夹套进行冷却,顶部采用上喷雾式冷却,以达到均匀冷却效果。
3. 喷嘴设备喷嘴作为连铸结晶器结构的关键之一,其设计应当综合考虑稳定性、均匀性、流速和流量等因素。
连铸结晶器总成(英)
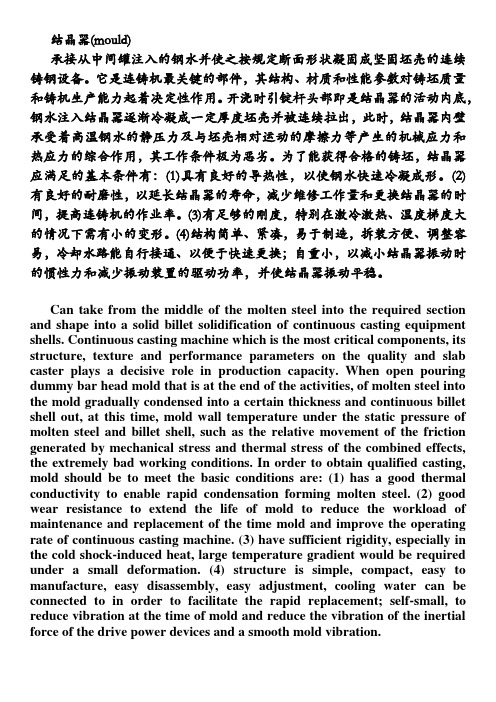
结晶器(mould)承接从中间罐注入的钢水并使之按规定断面形状凝固成坚固坯壳的连续铸钢设备。
它是连铸机最关键的部件,其结构、材质和性能参数对铸坯质量和铸机生产能力起着决定性作用。
开浇时引锭杆头部即是结晶器的活动内底,钢水注入结晶器逐渐冷凝成一定厚度坯壳并被连续拉出,此时,结晶器内壁承受着高温钢水的静压力及与坯壳相对运动的摩擦力等产生的机械应力和热应力的综合作用,其工作条件极为恶劣。
为了能获得合格的铸坯,结晶器应满足的基本条件有:(1)具有良好的导热性,以使钢水快速冷凝成形。
(2)有良好的耐磨性,以延长结晶器的寿命,减少维修工作量和更换结晶器的时间,提高连铸机的作业率。
(3)有足够的刚度,特别在激冷激热、温度梯度大的情况下需有小的变形。
(4)结构简单、紧凑,易于制造,拆装方便、调整容易,冷却水路能自行接通、以便于快速更换;自重小,以减小结晶器振动时的惯性力和减少振动装臵的驱动功率,并使结晶器振动平稳。
Can take from the middle of the molten steel into the required section and shape into a solid billet solidification of continuous casting equipment shells. Continuous casting machine which is the most critical components, its structure, texture and performance parameters on the quality and slab caster plays a decisive role in production capacity. When open pouring dummy bar head mold that is at the end of the activities, of molten steel into the mold gradually condensed into a certain thickness and continuous billet shell out, at this time, mold wall temperature under the static pressure of molten steel and billet shell, such as the relative movement of the friction generated by mechanical stress and thermal stress of the combined effects, the extremely bad working conditions. In order to obtain qualified casting, mold should be to meet the basic conditions are: (1) has a good thermal conductivity to enable rapid condensation forming molten steel. (2) good wear resistance to extend the life of mold to reduce the workload of maintenance and replacement of the time mold and improve the operating rate of continuous casting machine. (3) have sufficient rigidity, especially in the cold shock-induced heat, large temperature gradient would be required under a small deformation. (4) structure is simple, compact, easy to manufacture, easy disassembly, easy adjustment, cooling water can be connected to in order to facilitate the rapid replacement; self-small, to reduce vibration at the time of mold and reduce the vibration of the inertial force of the drive power devices and a smooth mold vibration.分类按拉坯方向上断面内壁的线型分结晶器的型式有弧形和直形两种;按其总体结构,不论弧形或直形均有套管式和组合式两种。
连铸连轧生产:结晶器
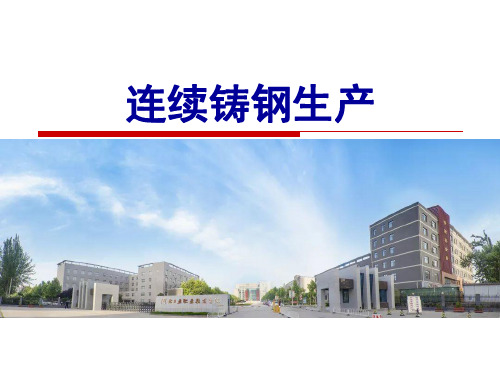
双锥度、多锥度甚至抛物线型锥度,以便更符合钢液凝固时体
积的变化规律,但是这种结晶器加工困难,使用并不普遍。
2.4.2 结晶器的重要参数
2 结晶器倒锥度
实际生产过程中要根据铸坯断面、拉速和钢的高温收缩率综 合选定合适的结晶器倒锥度,如果倒锥度选取过小,则坯壳与 结晶器铜板之间的气隙过大,可能导致铸坯变形,产生角部纵 裂纹等缺陷;如果倒锥度选取过大,会增加拉坯阻力,容易产 生横裂纹。
谢谢同学们!
对于板坯连铸机,目前都是采用宽度可调的结晶器。
2.4.1 结晶器的类型与构造
(3)多级结晶器:随着连铸技术的不断发展进步,连铸机 的拉速不断提高,出结晶器下口时坯壳的厚度越来越薄,为了 避免因坯壳厚度过薄导致漏钢等恶性事故,在结晶器下口安装 足辊、冷却板或冷却格栅,称为多级结晶器。
2.4.1 结晶器的类型与构造
1605
8
1702
1685
8.5
1803
1785
9
2007
1985
11ቤተ መጻሕፍቲ ባይዱ
2.4.2 结晶器的重要参数
3 结晶器断面 (3)板坯结晶器
B 结晶器窄边,与结晶器的辊缝制度以及动态轻压下工艺密
切相关,不同连铸机差别很大,所以无法推荐普遍适用的计算
公式。对于具有全程动态轻压下连铸机,可以参考
250mm 300mm 400mm
2.4 结晶器
2.4.2 结晶器的重要参数
1 长度 作为一次冷却,结晶器长度是一个非常重要的参数,它是保 证连铸坯出结晶器时能否具有足够安全坯壳厚度的重要因素。 如果长度太短,出结晶器下口时铸坯厚度达不到安全厚度,容 易产生漏钢事故;如果长度太长,拉坯阻力大,加工也困难。 所以,确定结晶器长度的主要依据是铸坯出结晶器下口时的坯 壳最小安全厚度,具体计算过程如下:
连铸圆坯结晶器

连铸机结晶器总成1、结晶器总成组合式结晶器由结晶器本体、支撑框架以及足锟等部件组成。
结晶器本体由4块铜板及支撑板组合而成,用螺栓连接为一体;支撑框架带有定位、固定装置和冷却水通道;足锟包括支架、锟子、轴承、水管和喷嘴等。
组合式结晶器可以配置液位检测装置、外置式电磁搅拌装置。
2、结晶器结构特点A、结晶器本体两块弧面铜板和两块侧面铜板组合成结晶器内腔,铜板上加工有若干冷却水槽(即水缝),用螺钉将铜板与支承板(也称为背板)连接。
支承板上设有冷却水通道,冷却水从振动台上的供水孔进入支撑框架再进入支承板,再通过支撑框架流回到振动台上的回水孔。
设计时,需要根据冷却水压强核算螺钉连接的受力及强度,并调整连接螺钉数量,直至满足要求。
一般情况下,两排螺钉之间布置5~6条水缝。
结晶器内腔角部的倒角一般采用早弧面和侧面铜板的结合部位垫有带45°斜面的铜质垫板形成;也有直接在侧面铜板上加工出倒斜角斜面的。
铜板厚度一般为45~50mm,主要取决于水缝深度和再加工要求。
可采用的材质有Cu—Ag和Cu—Cr—Zr。
如果连铸机拉速不高,相应铜板热面温度不超过250℃,可以采用Cu—Ag。
随着连铸技术发展和操作水平提高,连铸机拉速也相应提高,结晶器铜板有必要采用Cu—Cr—Zr合金,可以满足热面温度为350℃甚至更高的工况。
目前,国内方坯结晶器铜板次用Cu—Ag和Cu—Cr—Zr的都有,采用Cu—Cr—Zr的日趋增多。
为了提高结晶器使用寿命,铜板都会经过表面处理,即镀层。
典型的镀层材料有Cr、Ni、Ni—Fe、Ni—Co、Co—Ni。
Cr的硬度高,督促呢个化学稳定性好,但Cr与Cu的线膨胀系数差距较大,镀层结合力差,镀层易剥落。
Ni与Cu的结合力好,但其镀层硬度相对较低,高温耐磨性差。
现已很少采用单独镀Cr或Ni得铜板。
Ni—Fe、Ni—Co、Co—Ni都有硬度高、耐磨性好的特点,其中Ni—Fe的化学稳定性较差,其镀层韧性随着硬度增加会降低;Ni—Co的抗热交变性稍差;Co—Ni的材料成本较高。
品种钢优特钢连铸结晶器及二次冷却
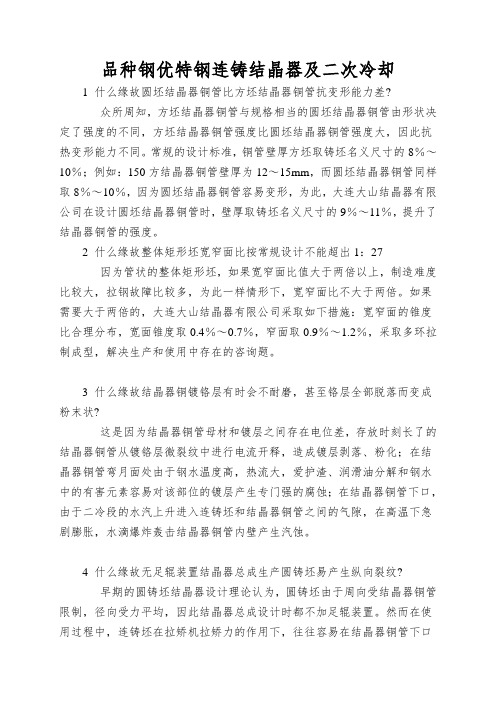
品种钢优特钢连铸结晶器及二次冷却1 什么缘故圆坯结晶器铜管比方坯结晶器铜管抗变形能力差?众所周知,方坯结晶器铜管与规格相当的圆坯结晶器铜管由形状决定了强度的不同,方坯结晶器铜管强度比圆坯结晶器铜管强度大,因此抗热变形能力不同。
常规的设计标准,铜管壁厚方坯取铸坯名义尺寸的8%~10%;例如:150方结晶器铜管壁厚为12~15mm,而圆坯结晶器铜管同样取8%~10%,因为圆坯结晶器铜管容易变形,为此,大连大山结晶器有限公司在设计圆坯结晶器铜管时,壁厚取铸坯名义尺寸的9%~11%,提升了结晶器铜管的强度。
2 什么缘故整体矩形坯宽窄面比按常规设计不能超出1:27因为管状的整体矩形坯,如果宽窄面比值大于两倍以上,制造难度比较大,拉钢故障比较多,为此一样情形下,宽窄面比不大于两倍。
如果需要大于两倍的,大连大山结晶器有限公司采取如下措施:宽窄面的锥度比合理分布,宽面锥度取0.4%~0.7%,窄面取0.9%~1.2%,采取多环拉制成型,解决生产和使用中存在的咨询题。
3 什么缘故结晶器铜镀铬层有时会不耐磨,甚至铬层全部脱落而变成粉末状?这是因为结晶器铜管母材和镀层之间存在电位差,存放时刻长了的结晶器铜管从镀铬层微裂纹中进行电流开释,造成镀层剥落、粉化;在结晶器铜管弯月面处由于钢水温度高,热流大,爱护渣、润滑油分解和钢水中的有害元素容易对该部位的镀层产生专门强的腐蚀;在结晶器铜管下口,由于二冷段的水汽上升进入连铸坯和结晶器铜管之间的气隙,在高温下急剧膨胀,水滴爆炸轰击结晶器铜管内壁产生汽蚀。
4 什么缘故无足辊装置结晶器总成生产圆铸坯易产生纵向裂纹?早期的圆铸坯结晶器设计理论认为,圆铸坯由于周向受结晶器铜管限制,径向受力平均,因此结晶器总成设计时都不加足辊装置。
然而在使用过程中,连铸坯在拉矫机拉矫力的作用下,往往容易在结晶器铜管下口内外弧方向产生偏磨,造成连铸坯与结晶器铜管内腔之间气隙分布不平均,阻碍连铸坯坯壳壁厚平均形成,因而易产生纵向裂纹。
板坯连铸机结晶器研究分解
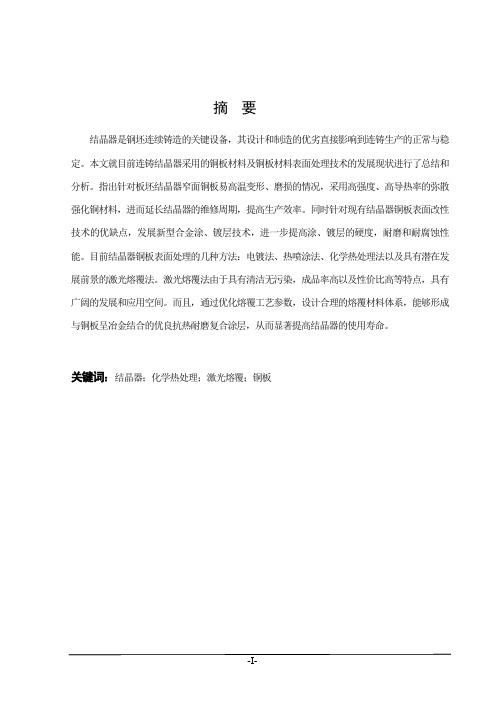
摘要结晶器是钢坯连续铸造的关键设备,其设计和制造的优劣直接影响到连铸生产的正常与稳定。
本文就目前连铸结晶器采用的铜板材料及铜板材料表面处理技术的发展现状进行了总结和分析。
指出针对板坯结晶器窄面铜板易高温变形、磨损的情况,采用高强度、高导热率的弥散强化铜材料,进而延长结晶器的维修周期,提高生产效率。
同时针对现有结晶器铜板表面改性技术的优缺点,发展新型合金涂、镀层技术,进一步提高涂、镀层的硬度,耐磨和耐腐蚀性能。
目前结晶器铜板表面处理的几种方法:电镀法、热喷涂法、化学热处理法以及具有潜在发展前景的激光熔覆法。
激光熔覆法由于具有清洁无污染,成品率高以及性价比高等特点,具有广阔的发展和应用空间。
而且,通过优化熔覆工艺参数,设计合理的熔覆材料体系,能够形成与铜板呈冶金结合的优良抗热耐磨复合涂层,从而显著提高结晶器的使用寿命。
关键词:结晶器;化学热处理;激光熔覆;铜板AbstractThe progress of mould plates was reviewed in continuous casting. The techniques such a solution or aging or forming or fine crystal and their combination were an effect tiveme thod which benefit for high conductivity and high strengthen of copper base alloy. Copper base composite maerial through dispersion technique and composite hardening and surface strengthening have more promising for mouldes in the future.Based on the current study stat of surface strength ening on copper crystallizer, several surface treatment means,such as electro plating thermal spraying,penetration and laserclad dingte chnique with potential development are described. Because of cleanliness without any pollution, high finished product ratio and high performance costratio, laser cladding has wide development and application range. Moreover, by optimizing process parameters and designing suitable material system, fine hea-t resistant and wear-resistant coating having metallurgy bonding with copper substrate can be fabricated, therefore, it may notably improve the service life of copper crystallizer.Key words:Copper crystallizer; Electroplating; Thermal Chemical heat treatme;Copper plate目录摘要 (I)Abstract (II)第1章绪论 (1)1.1连扎连铸简介 (1)1.2工艺流程 (3)1.3板坯连铸机质量优势 (4)1.4研究背景 (5)1.5国内外状况 (6)1.6结晶器概述 (7)1.7结晶器存在的问题 (9)1.8结晶器使用前的安全检查 (9)1.9本章小结 (10)第2章结晶器夹紧装置的选择计算 (11)2.1结晶器夹紧装置简介 (11)2.2结晶器夹紧受力分析及计算选择 (12)2.3结晶器宽边调整机构的安装 (14)2.4本章小结 (14)第3章结晶器调宽装置的选择计算 (15)3.1调宽装置简介 (15)3.2调宽装置的确定和基本参数的选择 (16)3.3调宽装置驱动选择 (18)3.4窄边调整机构的安装 (18)3.5本章小结 (19)第4章结晶器铜板及水箱的选择计算 (20)4.1结晶器铜板的设计 (20)4.1.1结晶器长度的选择 (20)4.1.2结晶器断面尺寸和倒锥度 (22)4.1.3结晶器铜板材质及表面镀层的选择 (23)4.1.4铜板厚度计算 (24)4.2水箱设计 (25)4.3本章小结 (26)第五章结晶器振动装置的应用和发展 (27)5.1振动装置的概述 (27)5.2结晶器的振动方式 (27)5.3总结 (30)5.4本章小结 (31)结论 (32)参考文献 (33)致谢 (35)第1章绪论1.1连扎连铸简介连铸连轧全称连续铸造连续轧制(Continue Casting Direct Rolling,简称CCDR),是把液态钢倒入连铸机中轧制出钢坯(称为连铸坯),然后不经冷却,在均热炉中保温一定时间后直接进入热连轧机组中轧制成型的钢铁轧制工艺。
连铸结晶器工作原理
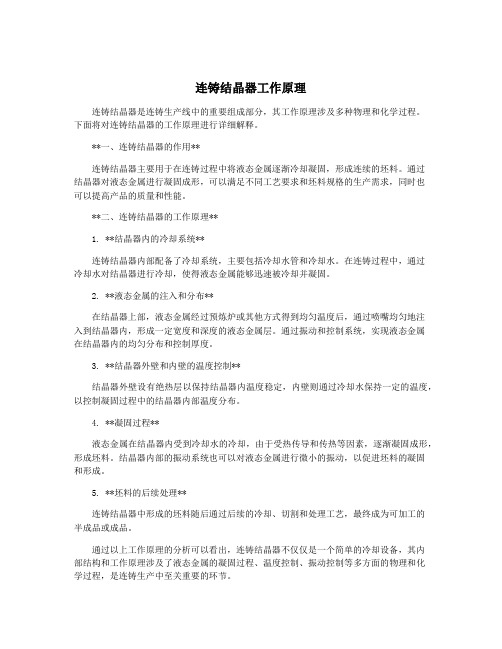
连铸结晶器工作原理连铸结晶器是连铸生产线中的重要组成部分,其工作原理涉及多种物理和化学过程。
下面将对连铸结晶器的工作原理进行详细解释。
**一、连铸结晶器的作用**连铸结晶器主要用于在连铸过程中将液态金属逐渐冷却凝固,形成连续的坯料。
通过结晶器对液态金属进行凝固成形,可以满足不同工艺要求和坯料规格的生产需求,同时也可以提高产品的质量和性能。
**二、连铸结晶器的工作原理**1. **结晶器内的冷却系统**连铸结晶器内部配备了冷却系统,主要包括冷却水管和冷却水。
在连铸过程中,通过冷却水对结晶器进行冷却,使得液态金属能够迅速被冷却并凝固。
2. **液态金属的注入和分布**在结晶器上部,液态金属经过预炼炉或其他方式得到均匀温度后,通过喷嘴均匀地注入到结晶器内,形成一定宽度和深度的液态金属层。
通过振动和控制系统,实现液态金属在结晶器内的均匀分布和控制厚度。
3. **结晶器外壁和内壁的温度控制**结晶器外壁设有绝热层以保持结晶器内温度稳定,内壁则通过冷却水保持一定的温度,以控制凝固过程中的结晶器内部温度分布。
4. **凝固过程**液态金属在结晶器内受到冷却水的冷却,由于受热传导和传热等因素,逐渐凝固成形,形成坯料。
结晶器内部的振动系统也可以对液态金属进行微小的振动,以促进坯料的凝固和形成。
5. **坯料的后续处理**连铸结晶器中形成的坯料随后通过后续的冷却、切割和处理工艺,最终成为可加工的半成品或成品。
通过以上工作原理的分析可以看出,连铸结晶器不仅仅是一个简单的冷却设备,其内部结构和工作原理涉及了液态金属的凝固过程、温度控制、振动控制等多方面的物理和化学过程,是连铸生产中至关重要的环节。
连铸的主要设备的组成
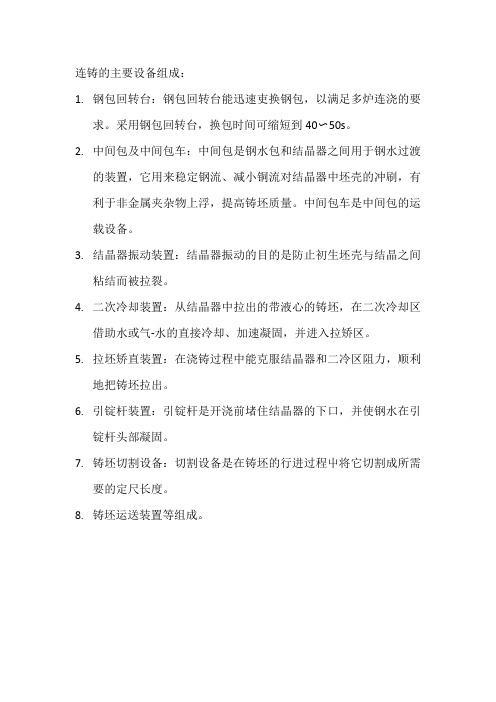
连铸的主要设备组成:
1.钢包回转台:钢包回转台能迅速吏换钢包,以满足多炉连浇的要
求。
采用钢包回转台,换包时间可缩短到40〜50s。
2.中间包及中间包车:中间包是钢水包和结晶器之间用于钢水过渡
的装置,它用来稳定钢流、减小铜流对结晶器中坯壳的冲刷,有利于非金属夹杂物上浮,提高铸坯质量。
中间包车是中间包的运载设备。
3.结晶器振动装置:结晶器振动的目的是防止初生坯壳与结晶之间
粘结而被拉裂。
4.二次冷却装置:从结晶器中拉出的带液心的铸坯,在二次冷却区
借助水或气-水的直接冷却、加速凝固,并进入拉矫区。
5.拉坯矫直装置:在浇铸过程中能克服结晶器和二冷区阻力,顺利
地把铸坯拉出。
6.引锭杆装置:引锭杆是开浇前堵住结晶器的下口,并使钢水在引
锭杆头部凝固。
7.铸坯切割设备:切割设备是在铸坯的行进过程屮将它切割成所需
要的定尺长度。
8.铸坯运送装置等组成。
简述结晶器在连铸生产中的作用

简述结晶器在连铸生产中的作用连铸是指将熔化的金属直接浇铸成连续的坯料,是铸造技术中一种重要的工艺。
在连铸过程中,结晶器是起着至关重要作用的设备之一。
它位于连铸机的浇注部位,主要用于控制坯料的结晶过程和形成坯料的结晶组织,以保证连铸坯料的质量和性能。
结晶器在连铸生产中的作用主要体现在以下几个方面:1. 控制结晶过程:结晶器可以通过控制结晶过程来影响坯料的结晶组织。
结晶器内部设有一定形状和尺寸的结晶孔道,通过调整结晶器的温度、冷却水流量等参数,可以控制坯料的结晶速度和结晶核的形成,从而影响坯料的晶粒尺寸和分布。
合理的结晶过程控制可以获得细小、均匀的晶粒,提高坯料的塑性和韧性。
2. 保证连铸坯料质量:结晶器可以有效地阻止浇注过程中的气体和杂质进入坯料中,减少坯料的气孔、夹杂和缺陷。
结晶器的结构设计和材料选择都需要考虑到其抗氧化、抗腐蚀、耐磨损等性能,以保证结晶器能够长时间稳定地工作,并确保坯料的质量。
3. 调整结晶组织:通过改变结晶器的结构和工艺参数,可以调整坯料的结晶组织,以满足不同材料和产品的要求。
例如,对于高强度钢材,可以采用细小晶粒的结晶器,以提高材料的强度和韧性;对于特殊用途的合金材料,可以采用特殊结构的结晶器,以获得特定的晶粒形态和组织结构。
4. 提高连铸效率:结晶器的优化设计可以提高连铸的效率和生产能力。
通过合理布置结晶器的数量和位置,可以实现多流道连铸,同时浇注多块坯料,提高连铸机的产能。
此外,结晶器还可以通过调节结晶器的冷却水流量和温度分布,优化坯料的冷却过程,提高连铸的速度和效率。
结晶器在连铸生产中起着至关重要的作用。
通过控制结晶过程、保证坯料质量、调整结晶组织和提高连铸效率,结晶器可以有效地提高连铸坯料的质量和性能,满足不同材料和产品的要求。
因此,在连铸生产中,合理选择和使用结晶器,不仅能够提高产品质量,还能够提高生产效率,降低生产成本,具有重要的经济和社会意义。
结晶器总结
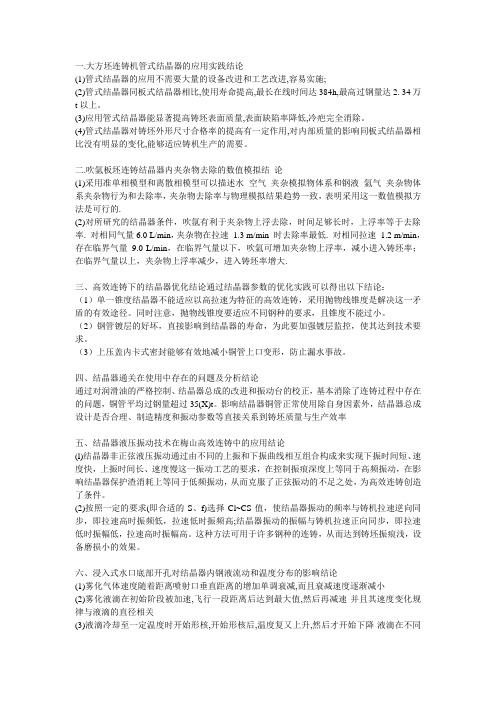
一.大方坯连铸机管式结晶器的应用实践结论(1)管式结晶器的应用不需要大量的设备改进和工艺改进,容易实施;(2)管式结晶器同板式结晶器相比,使用寿命提高,最长在线时间达384h,最高过钢量达2. 34万t以上。
(3)应用管式结晶器能显著提高铸坯表面质量,表面缺陷率降低,冷疤完全消除。
(4)管式结晶器对铸坯外形尺寸合格率的提高有一定作用,对内部质量的影响同板式结晶器相比没有明显的变化,能够适应铸机生产的需要。
二.吹氩板坯连铸结晶器内夹杂物去除的数值模拟结论(1)采用准单相模型和离散相模型可以描述水空气夹杂模拟物体系和钢液氩气夹杂物体系夹杂物行为和去除率,夹杂物去除率与物理模拟结果趋势一致,表明采用这一数值模拟方法是可行的.(2)对所研究的结晶器条件,吹氩有利于夹杂物上浮去除,时间足够长时,上浮率等于去除率. 对相同气量6.0 L/min,夹杂物在拉速 1.3 m/min 时去除率最低. 对相同拉速1.2 m/min,存在临界气量9.0 L/min,在临界气量以下,吹氩可增加夹杂物上浮率,减小进入铸坯率;在临界气量以上,夹杂物上浮率减少,进入铸坯率增大.三、高效连铸下的结晶器优化结论通过结晶器参数的优化实践可以得出以下结论:(1)单一锥度结晶器不能适应以高拉速为特征的高效连铸,采用抛物线锥度是解决这一矛盾的有效途径。
同时注意,抛物线锥度要适应不同钢种的要求,且锥度不能过小。
(2)钢管镀层的好坏,直接影响到结晶器的寿命,为此要加强镀层监控,使其达到技术要求。
(3)上压盖内卡式密封能够有效地减小铜管上口变形,防止漏水事故。
四、结晶器通关在使用中存在的问题及分析结论通过对润滑油的严格控制、结晶器总成的改进和振动台的校正,基本消除了连铸过程中存在的问题,铜管平均过钢量超过35(X)t。
影响结晶器铜管正常使用除自身因素外,结晶器总成设计是否合理、制造精度和振动参数等直接关系到铸坯质量与生产效率五、结晶器液压振动技术在梅山高效连铸中的应用结论(l)结晶器非正弦液压振动通过由不同的上振和下振曲线相互组合构成来实现下振时间短、速度快,上振时间长、速度慢这一振动工艺的要求,在控制振痕深度上等同于高频振动,在影响结晶器保护渣消耗上等同于低频振动,从而克服了正弦振动的不足之处,为高效连铸创造了条件。
常规板坯连铸机结晶器技术

常规板坯连铸机结晶器技术结晶器是连铸机中的铸坯成型设备, 是连铸机的核心设备之一。
其作用是将连续不断地注入其内腔的钢液通过水冷铜壁强制冷却,导出钢液的热量,使之逐渐凝固成为具有所要求的断面形状和一定坯壳厚度的铸坯,并使这种芯部仍为液相的铸坯连续不断地从结晶器下口拉出,为其在以后的二冷区域内完全凝固创造条件。
在钢水注入结晶器逐渐形成一定厚度坯壳的凝固过程中,结晶器一直承受着钢水静压力、摩檫力、钢水热量的传递等诸多因素引起的的影响,使结晶器同时处于机械应力和热应力的综合作用之下,工作条件极为恶劣,在此恶劣条件下结晶器长时间地工作,其使用状况直接关系到连铸机的性能,并与铸坯的质量与产量密切相关。
因此,除了规范生产操作、选择合适的保护渣和避免机械损伤外,合理的设计是保证铸坯质量、减小溢漏率、提高其使用寿命的基础和关键。
板坯连铸机一般采用四壁组合式(亦称板式)结晶器,也有一个结晶器浇多流铸坯的插装式结构。
ﻫ结晶器主要参数的确定ﻫ1 结晶器长度Hﻫ结晶器长度主要根据结晶器出口的坯壳最小厚度确定。
若坯壳过薄,铸坯就会出现鼓肚变形,对于板坯连铸机,要求坯壳厚度大于10~15mm。
结晶器长度也可按下式进行核算:ﻫﻫH=(δ/K)2Vc+S1+S2 (mm)ﻫﻫ式中δ——结晶器出口处坯壳的最小厚度,mmﻫK——凝固系数,一般取K=18~22 mm/min0.5ﻫ Vc——拉速,mm/minS1——结晶器铜板顶面至液面的距离,多取S1=100 mmﻫﻫS2——安全余量,S=50~100 mmﻫﻫ对常规板坯连铸机可参考下述经验:ﻫﻫ当浇铸速度≤2.0m/min时,结晶器长度可采用900~950mm。
ﻫﻫ当浇铸速度2.0~3.0m/min 时,结晶器长度可采用950~1100mm。
当浇铸速度≥3.0m/min时,结晶器长度可采用1100~1200mm。
ﻫﻫ 2 结晶器铜板厚度hﻫﻫ铜板厚度的确定是依据热量传热原理和高温下的使用性能,具体说,与铜板材质、镀层、机械性能、拉速、冷却水量的大小和分布等有关。
连铸机结晶器铜板简介及影响寿命因素

连铸机结晶器铜板简介及影响寿命因素作者:王腾飞戴昭颖张博来源:《科学与财富》2015年第23期摘要:本文简要介绍了京唐公司连铸机结晶器铜板的作用及镀层材质情况,并结合实际生产总结影响结晶器铜板寿命的因素及改进措施。
关键词:连铸机结晶器铜板;镀层材质;寿命前言:结晶器是连铸机的关键部件,铜板是结晶器的核心部件,钢水通过结晶器铜板向外导出热量而使钢水凝固结晶成一定厚度的坯壳,铜板在此过程中承受着高低温度产生的热应力、高温热膨胀带来的塑性变形、冷却收缩时带来的巨大拉应力、钢坯与铜板相对运动产生的摩擦力,这就要求结晶器铜板必须具有较高的热传导性,较高的抗拉强度,较高的再结晶温度,软化温度,热强性以抵抗变性,热疲劳能力,同时要有抵抗磨损的能力,提高过钢量,因此结晶器铜板在连铸过称中起到不可或缺的作用,提高结晶器铜板寿命更是降低炼钢成本的重要工作之一。
1 结晶器作用及其要求结晶器是连铸机的核心,其作用是将连续不断地注入其内腔的钢液通过水冷铜板强制冷却,导出钢液的热量,使之逐渐凝固成为具有所需要求的断面形状和一定均匀厚度的坯壳,并使这种芯部为液相的铸坯连续不断地从结晶器下口拉出,为其在二冷区域内完全凝固创造条件。
钢水在结晶器中的凝固对铸坯表面质量和铸机的正常生产有着重大影响,在高温钢水注入结晶器,逐渐形成一定厚度坯壳的凝固过程中,结晶器铜板一直处于钢水与冷却水的静压力、高温氧化、冷热疲劳产生的热裂纹、温度梯度大产生变形、冷却水和保护渣成份的化学腐蚀、高温蒸汽的侵蚀,引锭、拉坯、振动产生的摩擦、磨损和调锥宽导致的擦痕等诸多损伤。
(1)良好的导热性,能使钢液快速凝固。
每1Kg钢水浇注成坯并冷却到室温,放出的热量约为1340KJ/Kg,若板坯尺寸为250×1700mm,拉速为1m/min,结晶器每分钟带走的热量多达20万KJ。
而结晶器长度又较短,一般不超过1m,在这样短的距离内要能带走大量的热量,要求它必须具有良好的导热性能。
上引连铸的工作原理及影响因素分析

17电工材料2010N o.1上引连铸的工作原理及影响因素分析覃向忠,李镇鹏,刘辉(桂林金格电工电子材料科技有限公司,广西桂林541004)摘要:对用于生产金属或合金线材的上引连铸装置的工作原理及主要因素进行了分析,指出了影响上引连铸的关键因素,以期对实际生产有所帮助。
关键词:上引连铸;合金熔液;结晶器;固-液交界面中图分类号:TM205.1文献标志码:A文章编号:1671-8887(2010)01-0017-03Anal y sis of the Continuous U p Castin g Princi p leand the Aff ectin g FactorQ I N Xi a n g-z h o n g,L I Z he n-p e n g,L I U Hui(Guili n Coni nst Elect rical&Elect r onic Ma t eri al Co.L t d.,Guili n541004,Chi na) Abstract:The p ri nci p le of t he c o nti n uous u p casti n g e q ui p me nt w hic h ma n uf act ur es wi r ef r o m met al or all o y melt is i nt r oduce d.The mai n f act or t hat ma y i nf l ue nce t he q ualit y oft he c o nti n uous u p cast e d wi r e is a nal y ze d.K e y words:c o nti n uous u p casti n g;s ol uti o n of all o y;c o nti n uous casti n g m ol d;i nt e rf ace of t hes oli d a n d li q ui d1引言上引连铸是一种连续铸造的方法,其原理是利用金属熔液冷却结晶的机理,从熔融的金属或合金熔液中缓慢连续地抽出具有一定形状的固态金属线材、板材等。
连铸三大件生产工艺流程
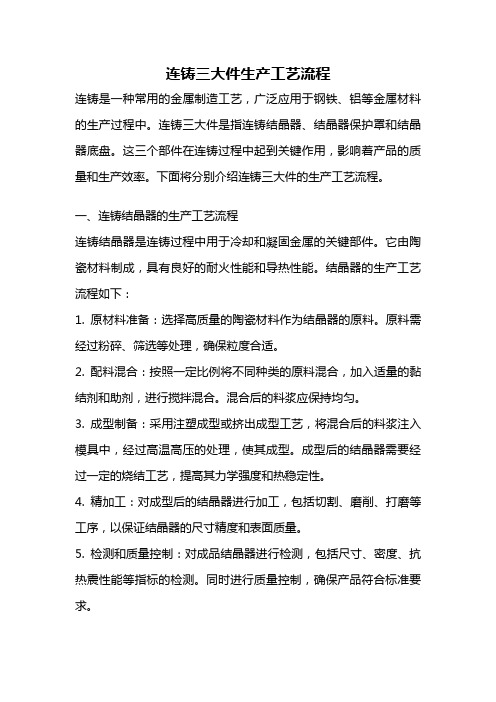
连铸三大件生产工艺流程连铸是一种常用的金属制造工艺,广泛应用于钢铁、铝等金属材料的生产过程中。
连铸三大件是指连铸结晶器、结晶器保护罩和结晶器底盘。
这三个部件在连铸过程中起到关键作用,影响着产品的质量和生产效率。
下面将分别介绍连铸三大件的生产工艺流程。
一、连铸结晶器的生产工艺流程连铸结晶器是连铸过程中用于冷却和凝固金属的关键部件。
它由陶瓷材料制成,具有良好的耐火性能和导热性能。
结晶器的生产工艺流程如下:1. 原材料准备:选择高质量的陶瓷材料作为结晶器的原料。
原料需经过粉碎、筛选等处理,确保粒度合适。
2. 配料混合:按照一定比例将不同种类的原料混合,加入适量的黏结剂和助剂,进行搅拌混合。
混合后的料浆应保持均匀。
3. 成型制备:采用注塑成型或挤出成型工艺,将混合后的料浆注入模具中,经过高温高压的处理,使其成型。
成型后的结晶器需要经过一定的烧结工艺,提高其力学强度和热稳定性。
4. 精加工:对成型后的结晶器进行加工,包括切割、磨削、打磨等工序,以保证结晶器的尺寸精度和表面质量。
5. 检测和质量控制:对成品结晶器进行检测,包括尺寸、密度、抗热震性能等指标的检测。
同时进行质量控制,确保产品符合标准要求。
二、结晶器保护罩的生产工艺流程结晶器保护罩是用于保护结晶器免受外界环境侵蚀和损坏的重要部件。
它通常由耐火材料制成,具有高温抗氧化性能。
结晶器保护罩的生产工艺流程如下:1. 原材料准备:选择高质量的耐火材料作为保护罩的原料。
原料需经过粉碎、筛选等处理,确保粒度合适。
2. 配料混合:按照一定比例将不同种类的原料混合,加入适量的黏结剂和助剂,进行搅拌混合。
混合后的料浆应保持均匀。
3. 成型制备:采用压制或注塑成型工艺,将混合后的料浆注入模具中,经过高温高压的处理,使其成型。
成型后的保护罩需要经过一定的烧结工艺,提高其力学强度和耐热性能。
4. 精加工:对成型后的保护罩进行加工,包括切割、磨削、打磨等工序,以保证保护罩的尺寸精度和表面质量。
结晶器振动技术简述讲解
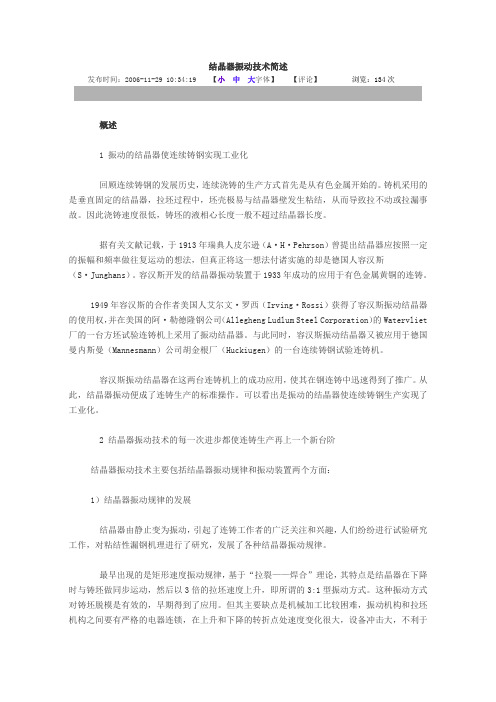
结晶器振动技术简述发布时间:2006-11-29 10:34:19 【小中大字体】【评论】浏览:134次概述1 振动的结晶器使连续铸钢实现工业化回顾连续铸钢的发展历史,连续浇铸的生产方式首先是从有色金属开始的。
铸机采用的是垂直固定的结晶器,拉坯过程中,坯壳极易与结晶器壁发生粘结,从而导致拉不动或拉漏事故。
因此浇铸速度很低,铸坯的液相心长度一般不超过结晶器长度。
据有关文献记载,于1913年瑞典人皮尔逊(A·H·Pehrson)曾提出结晶器应按照一定的振幅和频率做往复运动的想法,但真正将这一想法付诸实施的却是德国人容汉斯(S·Junghans)。
容汉斯开发的结晶器振动装置于1933年成功的应用于有色金属黄铜的连铸。
1949年容汉斯的合作者美国人艾尔文·罗西(Irving·Rossi)获得了容汉斯振动结晶器的使用权,并在美国的阿·勒德隆钢公司(Allegheng Ludlum Steel Corporation)的Watervliet 厂的一台方坯试验连铸机上采用了振动结晶器。
与此同时,容汉斯振动结晶器又被应用于德国曼内斯曼(Mannesmann)公司胡金根厂(Huckiugen)的一台连续铸钢试验连铸机。
容汉斯振动结晶器在这两台连铸机上的成功应用,使其在钢连铸中迅速得到了推广。
从此,结晶器振动便成了连铸生产的标准操作。
可以看出是振动的结晶器使连续铸钢生产实现了工业化。
2 结晶器振动技术的每一次进步都使连铸生产再上一个新台阶结晶器振动技术主要包括结晶器振动规律和振动装置两个方面:1)结晶器振动规律的发展结晶器由静止变为振动,引起了连铸工作者的广泛关注和兴趣,人们纷纷进行试验研究工作,对粘结性漏钢机理进行了研究,发展了各种结晶器振动规律。
最早出现的是矩形速度振动规律,基于“拉裂——焊合”理论,其特点是结晶器在下降时与铸坯做同步运动,然后以3倍的拉坯速度上升,即所谓的3:1型振动方式。
连铸机检修知识
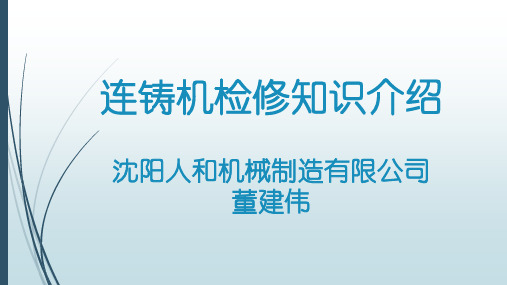
制造项目 (六号板坯连铸机工程)弯曲段、4-5段、6段、7段、8段、9-13段 (六号板坯连铸机工程)中间包车及中间包 (六号板坯连铸机工程)更换导轨2流 (220*1600不锈钢板坯连铸机项目)导向段1、导向段2 (板坯连铸机备件)扇形段1、扇形段2-3 (方坯连铸机备件)拉矫机 (200*1600mm板坯连铸机备件)扇形段1、扇形段2-3 扇形段内外弧辊子装配、侧弧辊子装配 (型钢炼钢厂异型坯连铸机备件)BB1扇形一段、BB2扇形一段 (型钢炼钢厂异型坯连铸机备件)拉矫机 1#、2#、3#、4#连铸机φ200、φ230、φ250自由辊和驱动辊 板坯项目弯曲段、扇形段2-3 5米板弧形扇形段 (9#大方坯连铸机项目)活动段、扇形1段、扇形2段、固定段 (9#大方坯连铸机项目)更换导轨、扇形段底座、拉矫机底座 (9#大方坯连铸机项目)中间罐车 (9#大方坯连铸机项目)横向移钢机
1#、2#、3#、4#板坯连铸辊修复 日照钢铁ESP扇形段修复
1#连铸机扇形段修复,2#连铸机弯曲段、扇形段修复 炼钢厂5#连铸机系统检修 弧形段修理、水平段修理 板坯连铸扇形段修复 2#、3#机弯曲段维修
内部令号 G11-076 G03-008 G04-013 G10-071 G11-075
2018YJ08-102 G11-079
14
四、我们的制造业绩(2018年1月至今)
序号 1 2 3 4 5 6 7 8 9 10 11 12 13 14 15 16 17
客户名称 唐山燕山钢铁有限公司 唐山燕山钢铁有限公司 唐山燕山钢铁有限公司 福建青拓实业股份有限公司 福建青拓实业股份有限公司 福建青拓实业股份有限公司 广东广青金属科技有限公司 河北天柱钢铁集团有限公司 莱芜钢铁集团有限公司 莱芜钢铁集团有限公司 河钢股份有限公司承德分公司 福建吴航不锈钢制品有限公司 湖南华菱湘潭钢铁有限公司 湖南华菱湘潭钢铁有限公司 湖南华菱湘潭钢铁有限公司 湖南华菱湘潭钢铁有限公司 湖南华菱湘潭钢铁有限公司
短流程连铸连轧成套装备的设备结构和主要组成部分介绍
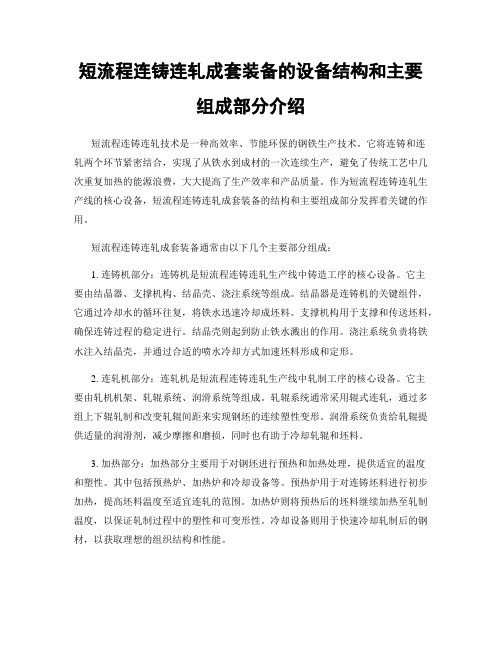
短流程连铸连轧成套装备的设备结构和主要组成部分介绍短流程连铸连轧技术是一种高效率、节能环保的钢铁生产技术。
它将连铸和连轧两个环节紧密结合,实现了从铁水到成材的一次连续生产,避免了传统工艺中几次重复加热的能源浪费,大大提高了生产效率和产品质量。
作为短流程连铸连轧生产线的核心设备,短流程连铸连轧成套装备的结构和主要组成部分发挥着关键的作用。
短流程连铸连轧成套装备通常由以下几个主要部分组成:1. 连铸机部分:连铸机是短流程连铸连轧生产线中铸造工序的核心设备。
它主要由结晶器、支撑机构、结晶壳、浇注系统等组成。
结晶器是连铸机的关键组件,它通过冷却水的循环往复,将铁水迅速冷却成坯料。
支撑机构用于支撑和传送坯料,确保连铸过程的稳定进行。
结晶壳则起到防止铁水溅出的作用。
浇注系统负责将铁水注入结晶壳,并通过合适的喷水冷却方式加速坯料形成和定形。
2. 连轧机部分:连轧机是短流程连铸连轧生产线中轧制工序的核心设备。
它主要由轧机机架、轧辊系统、润滑系统等组成。
轧辊系统通常采用辊式连轧,通过多组上下辊轧制和改变轧辊间距来实现钢坯的连续塑性变形。
润滑系统负责给轧辊提供适量的润滑剂,减少摩擦和磨损,同时也有助于冷却轧辊和坯料。
3. 加热部分:加热部分主要用于对钢坯进行预热和加热处理,提供适宜的温度和塑性。
其中包括预热炉、加热炉和冷却设备等。
预热炉用于对连铸坯料进行初步加热,提高坯料温度至适宜连轧的范围。
加热炉则将预热后的坯料继续加热至轧制温度,以保证轧制过程中的塑性和可变形性。
冷却设备则用于快速冷却轧制后的钢材,以获取理想的组织结构和性能。
4. 输送设备:输送设备主要包括钢坯输送机、辊道输送机、插入传送机等。
它们负责将钢坯从一个部分转移到下一个部分,确保整个生产过程的连续性和协调性。
钢坯输送机通常用于将连铸机产出的钢坯送至连轧机,通过链条或链板等方式进行传送。
辊道输送机用于将连轧机轧制完成的钢材送至下一环节,如冷却设备或整热处理设备。
- 1、下载文档前请自行甄别文档内容的完整性,平台不提供额外的编辑、内容补充、找答案等附加服务。
- 2、"仅部分预览"的文档,不可在线预览部分如存在完整性等问题,可反馈申请退款(可完整预览的文档不适用该条件!)。
- 3、如文档侵犯您的权益,请联系客服反馈,我们会尽快为您处理(人工客服工作时间:9:00-18:30)。
结晶器
结晶器(mould)
承接从中间罐注入的钢水并使之按规定断面形状凝固成坚固坯壳的连续铸钢设备。
它是连铸机最关键的部件,其结构、材质和性能参数对铸坯质量和铸机生产能力起着决定性作用。
开浇时引锭杆头部即是结晶器的活动内底,钢水注入结晶器逐渐冷凝成一定厚度坯壳并被连续拉出,此时,结晶器内壁承受着高温钢水的静压力及与坯壳相对运动的摩擦力等产生的机械应力和热应力的综合作用,其工作条件极为恶劣。
为了能获得合格的铸坯,结晶器应满足的基本条件有:(1)具有良好的导热性,以使钢水快速冷凝成形。
(2)有良好的耐磨性,以延长结晶器的寿命,减少维修工作量和更换结晶器的时间,提高连铸机的作业率。
(3)有足够的刚度,特别在激冷激热、温度梯度大的情况下需有小的变形。
(4)结构简单、紧凑,易于制造,拆装方便、调整容易,冷却水路能自行接通、以便于快速更换;自重小,以减小结晶器振动时的惯性力和减少振动装置的驱动功率,并使结晶器振动平稳。
分类按拉坯方向上断面内壁的线型分结晶器的型式有弧形和直形两种;按其总体结构,不论弧形或直形均有套管式和组合式两种。
套管式内壁铜管、内外水套组成的冷却水套和足辊是它的主要构件(图1)。
直形或弧形的铜管外面由冷却水套、法兰和密封元件等组成供水、供油系统。
为了保证铸坯有规整的外形尺寸,在结晶器底部安装了2~3组足辊,以利于提高拉速和防止铸坯脱方(见鼓肚与菱变)。
图l 弧形套管式结晶器
1一结晶器罩}2一内水套;3一润滑油盖;4一内壁铜管
5一放射源容器;6一盖板;7一外水套;8一进水管;
9一回水管;10一接收装置;l l一水环;
12一足辊;13一定位销
组合式由宽面及窄面4块复合壁板及外框架组成。
多用于板坯连铸、大断面方坯连铸及异型坯连铸。
组合结晶器的每块复合壁板又由用螺柱联结的内壁铜板(外侧面铣有冷却水沟)和外壁钢制水箱组成。
内壁铜板和外壁间构成冷却水缝,以通水冷却。
4块复合壁之间用夹紧机构压紧。
为了实现结晶器在线调宽以及形成所要求的倒锥度,在结晶器的窄面壁板的上、下部分别装有4组调整装置。
当组装好的结晶器及外框架放到振动台架上时,所有进、出水管自行接通。
为了更好地保护结晶器的下口、防止过早过快产生大的磨损,紧挨着结晶器下口装有足辊或保护栅板。
足辊或保护栅板与结晶器一起振动。
结晶器与二冷第一段(直线段或扇形段)通过振动框架直接对中,便于结晶器与二冷第一段的准确定位。
二者形成一个整体,可快速吊运。
结构参数和尺寸设计结晶器的结构参数主要有断面尺寸、倒锥度、长度、水缝面积及铜壁的厚度等。
图2板坯组合式结晶器
1~窄面调整机构;2一窄面铜板}3一外框架;4一水管;5一宽面调整机构;
6一宽面铜板;7、8一足辊
断面尺寸依据冷态铸坯的公称尺寸确定。
要获得冷态下的铸坯公称尺寸,在设计结晶器时,必须考虑铸坯的冷凝收缩和拉矫时铸坯的变形。
因此,结晶器的断面尺寸应比铸坯冷态的断面公称尺寸大,通常要大出1%~3%,且下口尺寸要小于上口尺寸,形成了倒锥度。
倒锥度依据铸坯的冷凝收缩来确定。
铸坯在浇铸过程中冷凝收缩,进而有可能与结晶器内壁脱离而产生气隙。
气隙有大的热阻,使结晶器的导热性能变差,铸坯坯壳减薄,甚至造成拉裂漏钢。
为了防止拉漏,就将结晶器制成下口尺寸小于上口尺寸的倒锥形,以减小内壁与坯壳间的气隙,增大结晶器的导热能力。
使出结晶器时的坯壳厚度增大,并可提高拉坯速度。
依据铸坯断面尺寸、钢种等因素,结晶器的倒锥度通常取值为(0.4~1.3)%/m,对套管式小断面结晶器,其倒锥度取值在(0.4~0.9)%/m;对板坯的组合式结晶器,其宽面多采用平行或仅有很小的倒锥度,而窄面的倒锥度取值在(0.9~1.3)%/m。
为了适应铸坯在结晶器内上、下各处有不同的收缩率,进一步减小气隙和提高拉速,小方坯结晶器制成多段不同倒锥度或抛物线形的倒锥度。
长度结晶器长度的确定受多种因素影响,但主要是取决于铸坯出结晶器时的坯壳厚度。
为防止拉漏,一般坯壳厚度不小于10~15mm(与铸坯断面大小有关)。
坯壳过薄会造成铸坯鼓肚、脱方、内裂以致漏钢。
为了增大连铸机的生产能力,就势必要提高拉速。
为在高拉速下保证坯壳的足够厚度,增加结晶器的长度是方法之一。
但结晶器长度增加,又带来坯壳与内壁间摩擦阻力的增大和气隙的增大,使导热性变差。
综合考虑多种因素,结晶器长度(mm)可按下式选取:
式中v为拉速,m/min;δ为允许的最小坯壳厚,mm;K为铸坯的凝固系数(mm/mim1/2。
)。
K主要取决于冷却条件、断面尺寸、钢水温度和钢种。
一般K=20~24mm/min1/2;式中的(80~120)是考虑液面波动而在结晶器上口与液面间留的裕量。
生产实践中,结晶器的长度在700~1000mm间选取。
水缝面积的确定钢水铸入结晶器,冷凝成形结成坯壳,将放出大量的热。
这些热量主要由冷却水带走。
为使冷却水尽可能多地带走热量,结晶器应有合理的水缝。
结晶器的水缝面积可按下式确定:
式中Qw为结晶器单位周边长的耗水量,m3/h•m;Lw为结晶器的周边长m;Vw为水缝内水的流速,m/s。
根据经验、结晶器内的耗水量Qw=100~160m3/h•m。
水缝中冷却水流速Vw=6~10m/s。
进水压力Pw=0.29~0.59MPa。
耗水量随断面尺寸不同而变,小断面铸坯取上限,大断面铸坯取下限。
铜壁厚度结晶器内壁厚度的确定主要考虑其使用寿命和强度。
对套管式结晶器,壁厚通常取6~10mm;对组合式结晶器,因考虑要多次刨修加工,壁厚取为20~50mm,最终厚度不小于10mm。
材质为保证结晶器有良好导热性、足够的抗磨损性、机械强度和硬度以延长其使用寿命,内壁材质主要使用铜基合金制造,常用的有紫铜、铜银合金(含银量为0.07%~0.1%)、磷脱氧铜及铜铍合金、铬锆铜合金等。
使用铜基合金主要目的是提高其再结晶温度,以改善其高温时的硬度和强度、延长内壁的使用寿命。
为了进一步提高内壁的耐磨性和光滑程度减少拉坯阻力,有的还在铜壁表面加镀层。
通常为镀铬或镀镍、钨、铁及分三层镀镍、镍磷合金及铬。
内壁的润滑为防钢水在冷凝过程中与结晶器内壁粘结,减小拉坯时的摩擦阻力,改善铸坯表面质量、延长结晶器的使用寿命,在生产中,还要对结晶器内壁进行润滑。
润滑是采用沸点高于结晶器内壁温度(约200℃左右)的液体润滑剂或保护渣,在结晶器振动的过程中,它们不断被带入钢液面下的内壁上,并在钢水或坯壳与结晶器内壁间形成一层油气膜或熔渣膜,以润滑内壁。
(注:专业文档是经验性极强的领域,无法思考和涵盖全面,素材和资料部分来自网络,供参考。
可复制、编制,期待你的好评与关注)。