精益生产中的七大浪费
精益生产之七大浪费

精益生产之七大浪费精益生产是一种以最小化浪费为目标,通过优化流程和提高效率来提高产品质量和客户满意度的管理方法。
在精益生产中,有七大浪费被认为是造成资源浪费和低效率的主要原因,它们是:过产、等待、运输、不合格、运动、库存和过程错误。
1. 过产(Overproduction):过产是指在没有实际需求的情况下进行生产活动,导致产品过度积压和资源浪费。
这不仅会给企业带来高成本,还会增加库存量和缩短产品寿命。
2. 等待(Waiting):等待是指生产过程中出现的不必要的停顿和延迟。
这可能是由于设备故障、物料不足、工人缺席等原因导致的。
等待会降低生产效率,增加生产周期,延迟产品交付。
3. 运输(Transportation):运输是指不必要的材料和产品的长距离运输。
这使得运输成为了一个独立的过程,需要额外的时间和资源。
这些额外的步骤可能会导致物料的损坏、遗失和延迟,进一步增加了生产成本。
4. 不合格(Defects):不合格是指生产中出现的错误、缺陷和质量问题。
不合格的产品需要进行修正、重新制造或报废,这增加了不必要的时间和资源。
这不仅会导致生产延误,还会降低产品质量和客户满意度。
5. 运动(Motion):运动是指工人在生产过程中进行不必要的移动和动作。
这可能是由于生产线布局不合理、工具和设备摆放不当等原因导致的。
这增加了工人的体力消耗,降低了生产效率,也增加了人为错误的可能性。
6. 库存(Inventory):库存是指未经加工的原材料和半成品的储存量。
过多的库存可能会导致资金占用、过期损失、储存空间浪费等问题。
此外,库存过多也会隐藏潜在的问题,如质量问题和需求变化的风险。
7. 过程错误(Processing):过程错误是指生产过程中出现的不必要的重复、增补和调整。
这可能是由于不合理的工艺流程、工具和设备的不良设计等原因导致的。
这会增加生产成本和时间,降低生产效率和产品质量。
有效管理和消除以上七大浪费是精益生产的关键。
精益生产之七大浪费及5S管理
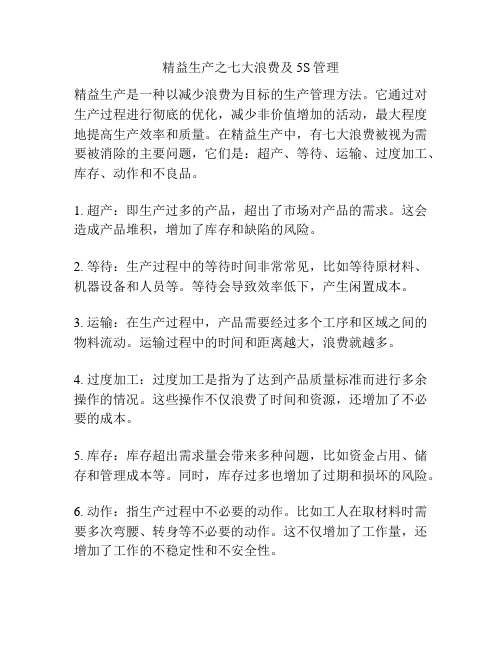
精益生产之七大浪费及5S管理精益生产是一种以减少浪费为目标的生产管理方法。
它通过对生产过程进行彻底的优化,减少非价值增加的活动,最大程度地提高生产效率和质量。
在精益生产中,有七大浪费被视为需要被消除的主要问题,它们是:超产、等待、运输、过度加工、库存、动作和不良品。
1. 超产:即生产过多的产品,超出了市场对产品的需求。
这会造成产品堆积,增加了库存和缺陷的风险。
2. 等待:生产过程中的等待时间非常常见,比如等待原材料、机器设备和人员等。
等待会导致效率低下,产生闲置成本。
3. 运输:在生产过程中,产品需要经过多个工序和区域之间的物料流动。
运输过程中的时间和距离越大,浪费就越多。
4. 过度加工:过度加工是指为了达到产品质量标准而进行多余操作的情况。
这些操作不仅浪费了时间和资源,还增加了不必要的成本。
5. 库存:库存超出需求量会带来多种问题,比如资金占用、储存和管理成本等。
同时,库存过多也增加了过期和损坏的风险。
6. 动作:指生产过程中不必要的动作。
比如工人在取材料时需要多次弯腰、转身等不必要的动作。
这不仅增加了工作量,还增加了工作的不稳定性和不安全性。
7. 不良品:生产出的不良产品无法被销售,这会导致浪费资源和劳动力。
为了减少这些浪费,精益生产倡导使用5S管理方法。
5S是指整理(Seiri)、整顿(Seiton)、清扫(Seiso)、清洁(Seiketsu)和素养(Shitsuke)。
- 整理:将工作场所中无用的东西清除出去,只保留必要的物品。
- 整顿:将工作场所中的物品有序地摆放,方便取用。
为每个物品设立明确的标识。
- 清扫:保持工作场所的清洁,清除尘土和垃圾。
维持一个良好的工作环境。
- 清洁:对设备、工具和工作区域进行定期的清洁和维护,确保其正常运行。
- 素养:让员工养成良好的工作习惯和态度,培养责任心和自我管理能力。
通过5S管理,可以降低生产过程中的浪费,提高工作效率和质量。
它强调提高工作环境和员工意识,促进生产过程的规范化、标准化和自律化。
精益生产的七大浪费概述

精益生产的七大浪费概述精益生产是一种管理哲学和方法论,旨在通过消除浪费来提高生产效率和质量。
在精益生产中,有七大浪费被广泛认可,包括:1. 运动:指的是任何不必要的移动或行动,例如工人需要频繁移动到不同的工作区域以完成任务。
精益生产鼓励将工作站布置得合理,以减少不必要的运动,从而提高效率。
2. 待料:指的是生产过程中等待原材料、工具或设备供应的时间。
这种等待会导致生产线停滞,降低生产效率。
精益生产鼓励将供应链优化,以减少待料时间。
3. 过产量:指的是生产超过需求的产品,或者在产品的某个阶段生产过多的零件。
过产量会导致库存积压、成本上升,甚至可能导致产品过期。
精益生产鼓励按需生产,以避免过产量的浪费。
4. 等待:指的是生产过程中因为等待其他任务完成而导致的停滞时间。
这种等待会导致生产线的延迟和低效。
精益生产鼓励优化工艺流程,减少等待时间。
5. 过度加工:指的是对产品进行超出需求或规格要求的加工步骤。
过度加工会增加生产成本和时间。
精益生产鼓励消除不必要的加工步骤,以提高效率和降低成本。
6. 错误:指的是在生产过程中出现的错误或瑕疵,例如产品缺陷或错误装配。
这些错误会导致废品产生和重工成本增加。
精益生产鼓励通过质量控制和错误预防来减少错误的发生。
7. 运输:指的是产品或物料在生产过程中频繁移动或运输的浪费。
这种浪费会增加时间和成本,同时也增加了损坏产品的风险。
精益生产鼓励优化布局和流程,减少不必要的运输。
通过有效地识别和消除这七大浪费,精益生产能够提高生产效率、降低成本,并提供更高质量的产品。
精益生产鼓励组织和管理层始终关注价值流,并持续改进以实现更高的效率和竞争力。
精益生产是一种以消除浪费为核心的管理哲学和方法论,旨在提高生产效率和质量。
在精益生产中,有七大浪费被广泛认可,并成为了改善生产流程的重要依据。
这七大浪费是运动、待料、过产量、等待、过度加工、错误和运输。
首先,运动是指不必要的移动或行动。
在生产过程中,员工频繁移动到不同的工作区域以完成任务会增加生产时间和劳动成本。
精益生产之七大浪费
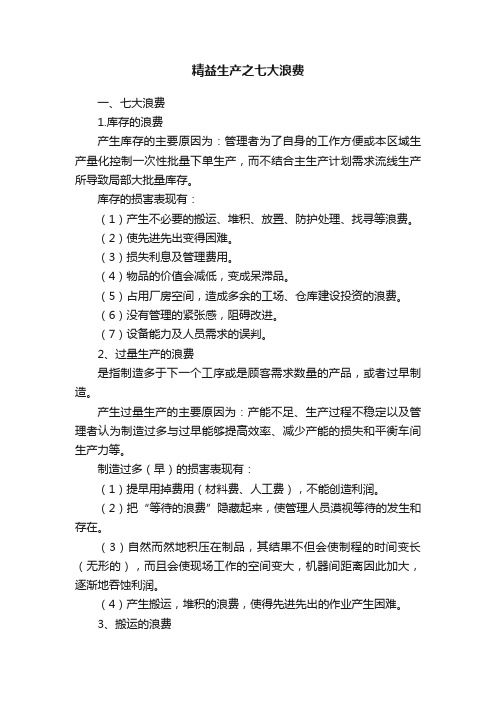
精益生产之七大浪费一、七大浪费1.库存的浪费产生库存的主要原因为:管理者为了自身的工作方便或本区域生产量化控制一次性批量下单生产,而不结合主生产计划需求流线生产所导致局部大批量库存。
库存的损害表现有:(1)产生不必要的搬运、堆积、放置、防护处理、找寻等浪费。
(2)使先进先出变得困难。
(3)损失利息及管理费用。
(4)物品的价值会减低,变成呆滞品。
(5)占用厂房空间,造成多余的工场、仓库建设投资的浪费。
(6)没有管理的紧张感,阻碍改进。
(7)设备能力及人员需求的误判。
2、过量生产的浪费是指制造多于下一个工序或是顾客需求数量的产品,或者过早制造。
产生过量生产的主要原因为:产能不足、生产过程不稳定以及管理者认为制造过多与过早能够提高效率、减少产能的损失和平衡车间生产力等。
制造过多(早)的损害表现有:(1)提早用掉费用(材料费、人工费),不能创造利润。
(2)把“等待的浪费”隐藏起来,使管理人员漠视等待的发生和存在。
(3)自然而然地积压在制品,其结果不但会使制程的时间变长(无形的),而且会使现场工作的空间变大,机器间距离因此加大,逐渐地吞蚀利润。
(4)产生搬运,堆积的浪费,使得先进先出的作业产生困难。
3、搬运的浪费不必要的搬运零件和产品,例如两个连续的生产工序,将产品在完成一个工序后,先运到仓库,然后再运到下一个工序。
较理想的情况是让两个工序的位置相邻,以便使产品能够从一个工序立即转到下一个工序。
产生搬运的主要原因为:车间布置采用批量生产,依工作站为区别的集中的水平式布置(也就是分工艺流程批量生产),无连续流生产的观念。
4、等待的浪费在生产过程中,操作员或者设备空闲。
产生等待的主要原因为:作业不平衡,安排作业不当、待料、品质不良等。
5、多余动作的浪费操作员所作的没有增值的动作,例如找零件,找工具、文件等。
产生多余动作的主要原因为:生产场地规划不好,生产模式设计不周全,生产动作不规范统一。
6、缺陷的浪费不良品和废品。
精益生产中的七大浪费

精益生产中的七大浪费 This manuscript was revised by the office on December 22, 2012精益生产中的七大浪费一、库存浪费◆精益生产认为:“库存是万恶之源”,所有改善行动会直接或间接地和消除库存。
①产生不必要的搬运、堆积、放置、防护处理、寻找等浪费②使先进先出的作业困难③损失利息及管理费用④物品的价值会减低,变成呆滞品⑤占用厂房空间、造成多余工场、仓库建设等⑥设备能力及人员需求的误判◆因库存造成无形损失,绝不亚于上述有形损失,精益生产者认为库存会隐藏问题,而“问题”在精益生产者被认为是宝藏,问题如果能不断地被发现解决,则利益便会不断地产生1、没有管理的紧张感,阻碍改进:2、库存量一多,因机械故障、不良产品所带来的不利后果不能马上显现出来,因而也不会产生对策。
3、由于有了充足的库存,出现问题时可以用库存先顶上,问题就可以慢慢解决甚至不用解决,最起码是被掩盖住了,不急迫了,不会被上级追究了,于是本部门的工作成绩就出来了。
二、过渡生产(制造过多或过早浪费)◆TPS强调的是“适时生产”。
◆多做能提高效率,提早做好能减少产能损失(不做白不做,机器还不是一样停着)1、提早用掉了材料费、人工费而已,并不能得到什么好处。
2、把“等待浪费”隐藏,使管理人员漠视等待的发生和存在。
3、积压在制品,使生产周期L/T变长无形的),而且会使现场工作空间变大,不知不觉中吞蚀我们的利润。
4、产生搬运、堆积浪费,先进先出变得困难。
三、品质缺陷(不良品浪费)◆任何的不良品产生,皆造成材料、机器、人工等的浪费。
◆及早发现不良品,容易确定不良来源,进而减少不良品的产生。
◆关键是第一次要把事情做对,“零缺陷”四、运输(搬运浪费)◆大部分人皆认同搬运是一种无效的动作,也有人认为搬运是必须的。
◆用“输送带”的方式来克服,行吗?1、取放浪费;2、等待浪费;3、在制品过多浪费;4、空间浪费。
精益生产中的七大浪费及改善方法
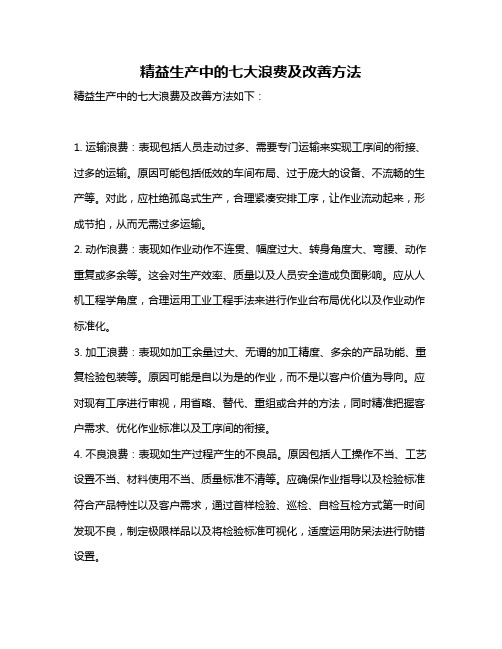
精益生产中的七大浪费及改善方法精益生产中的七大浪费及改善方法如下:1. 运输浪费:表现包括人员走动过多、需要专门运输来实现工序间的衔接、过多的运输。
原因可能包括低效的车间布局、过于庞大的设备、不流畅的生产等。
对此,应杜绝孤岛式生产,合理紧凑安排工序,让作业流动起来,形成节拍,从而无需过多运输。
2. 动作浪费:表现如作业动作不连贯、幅度过大、转身角度大、弯腰、动作重复或多余等。
这会对生产效率、质量以及人员安全造成负面影响。
应从人机工程学角度,合理运用工业工程手法来进行作业台布局优化以及作业动作标准化。
3. 加工浪费:表现如加工余量过大、无谓的加工精度、多余的产品功能、重复检验包装等。
原因可能是自以为是的作业,而不是以客户价值为导向。
应对现有工序进行审视,用省略、替代、重组或合并的方法,同时精准把握客户需求、优化作业标准以及工序间的衔接。
4. 不良浪费:表现如生产过程产生的不良品。
原因包括人工操作不当、工艺设置不当、材料使用不当、质量标准不清等。
应确保作业指导以及检验标准符合产品特性以及客户需求,通过首样检验、巡检、自检互检方式第一时间发现不良,制定极限样品以及将检验标准可视化,适度运用防呆法进行防错设置。
5. 等待浪费:表现如人员(以及设备)在等待,或者有时忙、有时闲的不均衡现象。
原因如生产线品种切换、工作量少、时常缺料、设备闲置等。
应实施生产均衡化,快速换模技术的运用,全员生产性防护,多技能工,消除不良浪费,提升供应商水准。
6. 过量生产:这是常被视为最大的浪费。
其结果导致库存、资金的占用以及潜在的报废风险。
应形成一个流、节拍化生产。
“一个流生产”是指从毛坯投入成品产出的整个制造加工过程,零件始终处于不停滞、不堆积、不超越的状态。
每道工序加工完一个制件后立即流到下一工序;工序间的在制品数量不超过前工序的装夹数量。
零件的运动不间断、不超越、不落地。
只有合格的产品才允许往下一道工序流。
节拍化生产要求是需求节拍与生产节拍平衡。
精益生产办公室七大浪费
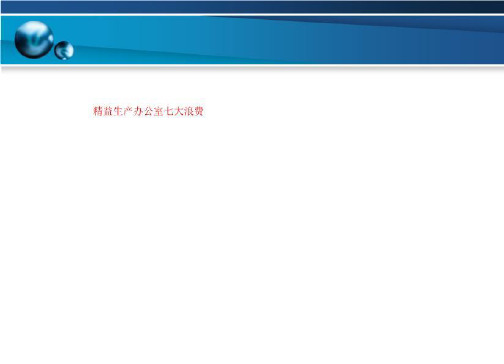
改 2工序和3工序颠倒的话
善 点
反转次数减少1次
5、动作的浪费
生产现场的作业动作不合理导致时间上的浪费。物品的取放、翻转、对准等。作业步行、弯 腰、转身等。
动作浪费的现象: 发动机合箱与装盖子处手压装配,不摇头、不转身、不插
发生原因:
秧 01.jpg
实施对策:
•工艺流程安排不合理 •没有实施标准作业 •人员的教育训练不足 •作业标准制定不合理
•以顾客需求的拉动生产 •一个流的生产
•客户订单的不准确 •生产计划安排有误
•看板管理的实施 •均衡化生产
管理要点:
•很多时候这种浪费往往不被现场监督者所重视,甚至被当成“超 产能手”受到赞扬
•生产能力过剩时,应尽量先考虑减少作业人员,但并非辞退人员, 而是更合理、更有效率地应用人员
7、库存的浪费
题 点
的方向
改 增加一个转向导轨,可减少一
善 点
名作业者
5、动作的浪费
附录:有关作业区域
关键是最合适・正常作业区域
6、生产过多(早)的浪费
产品变不成商品,没有任何价值
生产过多浪费的现象: 装配线转线处,曲柄加工的精车与后续挤螺纹之间
发生原因:
实施对策:
•人员过剩
•少人化作业
•设备稼动过剩 •生产批次大
•站立式作业才是真正的人性化管理(科学管理之父-泰勒)
4、加工本身的浪费
也称“过分加工的浪费”。一是指多余的加工,二 是指过分精确的加工。
加工本身浪费的现象: 曲柄精车粗糙度及配送中心机油泵齿轮穿架子等
发生原因:
•工艺的安排不合理 •作业内容偏离工艺文件 •模具治具不良 •作业没有标准化
实施对策:
精益生产七大浪费

精益生产七大浪费精益生产是一种管理哲学和方法论,旨在通过消除浪费、提高效率和优化价值流程来提升生产效能。
而精益生产中的七大浪费是指那些没有为产品或服务的生产和提供增加价值的活动或过程。
本文将围绕这七大浪费展开,分别进行详细解析和说明。
1. 运输浪费运输浪费是指物资、产品或信息在生产过程中的多余传递和搬运。
例如,在生产线上,如果没有优化工作站的布局,会导致物料的来回搬运、多余的运输过程,加大了时间和成本的浪费。
解决运输浪费的方法包括优化生产线布局,减少物料的运输距离和传递次数;采取合理的物流管理措施,确保物料的及时供应和准确投放;建立合理的生产计划,避免产生过多的中间库存。
2. 库存浪费库存浪费是指过多的原材料、在制品或成品存放在生产过程中所产生的时间、资金和空间的浪费。
为了解决库存浪费,可以采取以下措施:建立精确的需求预测和生产计划,避免过多的生产;与供应商建立稳定的合作关系,减少库存的积压;优化生产流程,避免产生过多的在制品。
3. 过程浪费过程浪费是指在生产过程中,因为制造步骤没有得到充分合理地优化,导致时间、资源和能量的浪费。
为了减少过程浪费,可以采取以下方法:优化生产流程,减少不必要的工序和步骤;引入先进的生产技术和设备,提高生产效率;提供员工培训和改善活动,增强员工的工作技能和问题解决能力。
4. 动作浪费动作浪费是指在生产过程中,工人或操作人员因为工作站布局不合理、工具不合适等原因,需要进行过多的移动、等待和修复等动作,从而造成时间和能量的浪费。
解决动作浪费的方法包括:对工作站进行优化布局,让操作人员能够更便捷地完成工作;提供适合的工具和设备,减少不必要的动作和劳动强度;建立高效的沟通和协作机制,减少信息传递和等待的时间。
5. 过度加工浪费过度加工浪费是指产品或服务的加工、处理或处理过程中,因为超出必要的要求或标准,而导致时间、资源和能量的浪费。
为了解决过度加工浪费,可以采取以下措施:确立明确的产品标准和质量要求,避免过度加工和处理;加强质量管理和监督,提高产品或服务的质量稳定性;进行产品优化和工艺改进,减少不必要的加工环节。
列举精益生产中的七大浪费
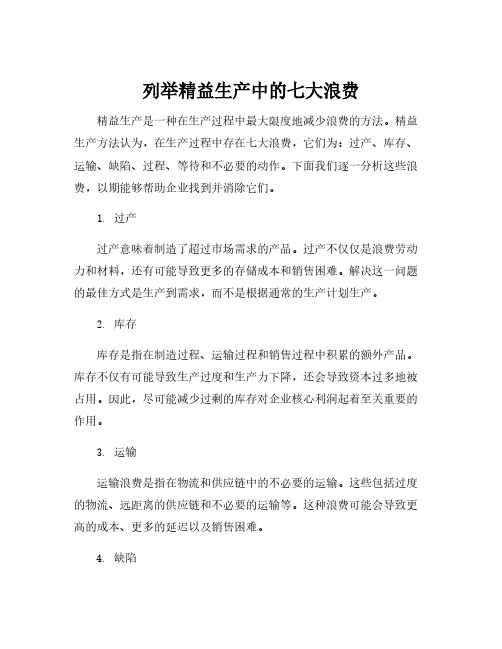
列举精益生产中的七大浪费精益生产是一种在生产过程中最大限度地减少浪费的方法。
精益生产方法认为,在生产过程中存在七大浪费,它们为:过产、库存、运输、缺陷、过程、等待和不必要的动作。
下面我们逐一分析这些浪费,以期能够帮助企业找到并消除它们。
1. 过产过产意味着制造了超过市场需求的产品。
过产不仅仅是浪费劳动力和材料,还有可能导致更多的存储成本和销售困难。
解决这一问题的最佳方式是生产到需求,而不是根据通常的生产计划生产。
2. 库存库存是指在制造过程、运输过程和销售过程中积累的额外产品。
库存不仅有可能导致生产过度和生产力下降,还会导致资本过多地被占用。
因此,尽可能减少过剩的库存对企业核心利润起着至关重要的作用。
3. 运输运输浪费是指在物流和供应链中的不必要的运输。
这些包括过度的物流、远距离的供应链和不必要的运输等。
这种浪费可能会导致更高的成本、更多的延迟以及销售困难。
4. 缺陷产品缺陷可能导致废品产生、产品延迟、客户不满、额外成本等问题。
这个问题通常涉及到的是特定生产过程或质量管控方面的基础问题。
企业应该尽可能及时发现和纠正这些错误以减少缺陷的出现。
5. 过程过程的重要作用是提高生产效率和生产效益。
如果过程中不断出现障碍,那么生产效率将大打折扣。
因此,企业应该通过样本分析、流程再造、员工培训等一系列措施来发现和解决过程中的问题。
6. 等待等待浪费通常是由周期时间差异、部件等待、人员速度不匹配等原因导致的。
这些问题可能导致工作环境不畅、效率低下。
因此,企业应该加强工作人员的培训、改进生产流程并确保供应链更稳定。
7. 不必要的动作不必要的动作可能是生产过程中一些不必要的或重复的动作。
这些问题通常是由于工人培训不足、生产流程和设备不完善,以及管理不到位等多种原因造成的。
因此,企业应该加强流程管理和员工培训以加强工作流程。
同时,确保员工有必要的设备和工具,尽可能自动化流程,降低人工干预。
总之,寻找和消除七大浪费是精益生产法的核心理念之一。
精益生产中的七大浪费

精益生产中的七大浪费消除七大浪费是精益生产的核心理念之一,七大浪费可用“TIM WOOD”表示(分别取7种浪费之英文首字母:运输、库存、动作、等待、过量生产、多余的工序、缺陷),以下对七大浪费作简要介绍。
一、七大浪费介绍第一种:运输的浪费主要表现为:车间布置采用批量生产,依工作站为区别的集中的水平式布置所致,无流线生产的观念。
第二种:库存的浪费主要表现为:管理者为了自身的工作方便或本区域生产量化控制一次性批量下单生产,而不结合主生产计划需求流线生产所导致局部大批量库存。
库存的损害表现有:(1):产生不必要的搬运、堆积、放置、防护处理、找寻等浪费。
(2):使先进先出的作业困难。
(3):损失利息及管理费用。
(4):物品的价值会减低,变成呆滞品。
(5):占用厂房空间,造成多余的工场、仓库建设投资的浪费。
(6):没有管理的紧张感,阻碍改进。
(7):设备能力及人员需求的误判。
第三种:动作的浪费主要因素表现为:生产场地不规划,生产模式设计不周全,生产动作不规范统一。
第四种:等待的浪费主要因素表现为:作业不平衡,安排作业不当、待料等。
第五种:过量生产的浪费主要因素表现为:管理者认为制造过多与过早能够提高效率或减少产能的损失和平衡车间生产力。
制造过多(早)的损害表现有:(1):提早用掉费用(材料费、人工费),不能创造利润。
(2):把“等待的浪费”隐藏起来,使管理人员漠视等待的发生和存在。
(3):自然而然地积压在制品,其结果不但会使制程的时间变长(无形的),而且会使现场工作的空间变大,机器间距离因此加大,逐渐地吞蚀利润。
(4):产生搬运,堆积的浪费,使得先进先出的作业产生困难。
第六种:多余的工序的浪费主要因素表现为:制造过程中作业加工程序动作不优化,可省略、替代、重组或合并的未及时检查。
第七种:缺陷的浪费主要因素表现为:工序生产无标准确认或有标准确认未对照标准作业,管理不严密、松懈所导致。
二、以制造业为例,消除浪费之优先顺序优先级#1 过量生产这是7种浪费中最严重的一种,因为:a)它衍生出了另外的6种浪费b)它掩盖了真正的生产能力,从而导致你做出诸如转包工作或是在不必要的方面投资这样错误的决定。
精益生产的浪费介绍

浪费之五:加工的浪费
在制造过程中,为了达到作业的目的,有一些加工程序是可以省略、替代、重组或合并的,若是仔细地加以检查,你将可发现,又有不少的浪费等着你去改善。
在参观日本三洋家用空调机生产线时,日方课长把我们领到热交换器的组装线旁,给我们讲述了如何通过重组和合并来消除浪费的事例:
精益生产(JIT)方式将所有浪费归纳成七种:
1 : 等待的浪费2 : 搬运的浪费3 : 不良品的浪费4 : 动作的浪费5 : 加工的浪费6 : 库存的浪费7 : 制造过多(早)的浪费
浪费之一:等待的浪费
等待就是闲着没事,等着下一个动作的来临,这种浪费是无庸置疑的。造成等待的原因通常有:作业不平衡、安排作业不当、停工待料、品质不良等。以生产部等待涂料为例,由于涂料不能按要求及时入厂,有可能无法按期交货,而当涂料入厂后,又需要抢进度,可能会出现加班、质量问题等。另有一种就是“监视机器”的浪费,有些工厂买了一些速度快、价格高的自动化机器,为了使其能正常运转或其他原因,例如:排除小故障、补充材料等等,通常还会另外安排人员站在旁边监视。所以,虽然是自动设备,但仍需人员在旁照顾,特称之为“闲视”的浪费。
浪费之六:库存的浪费
精益生产方式认为:“库存是万恶之源”。这是丰田对浪费的见解与传统见解最大不同的地方,也是丰田能带给企业很大利益的原动力。
精益生产方式中几乎所有的改善行动皆会直接或间接地和消除库存有关。精益生产方式为什么将库存看做是万恶之根源,而要想尽办法来降低它呢?因为库存会造成下列的浪费:
精益生产方式的思想之一就是要用一切办法来消除、减少一切非增值活动,例如检验、搬运和等待等造成的浪费,具体方法就是推行“零返修率”,必须做一个产品合格一个产品,第一次就做好,更重要的是在生产的源头就杜绝不合格产品、原材料流入生产后道工序,追求零废品率。
精益生产七大浪费

精益生产七大浪费在生产制造过程中,精益生产理论认为,存在着许多的浪费以及不必要的消耗,这些都会导致生产成本的增加,同时也使得生产效率得不到发挥,生产出来的产品也不能够达到最佳品质。
因此,精益生产理论提出了七大浪费,企业在生产制造过程中要尽力消除这些浪费,以提高效率和降低成本。
一、运输浪费:运输浪费指在物料运输过程中出现的不必要的搬运、装卸等环节。
企业应该尽量使用物料直接从生产线到达下一个工作站,从而避免因为不必要的运输而浪费时间和人力成本。
二、库存浪费:库存浪费指生产过程中存在的多余的材料、零部件或者产成品的储存问题。
因为多余的库存不仅浪费资金,而且会使得库存产品过期损坏或者占用大量的仓库空间,从而影响生产的顺畅。
三、动作浪费:动作浪费指在生产过程中存在的不必要的动作、分步操作等问题。
企业应该尽可能地精简工艺流程,避免重复的动作过程,从而减少不必要的动作浪费。
四、等待浪费:等待浪费指在生产过程中因为暂时没有物料、设备或者人员需要等待的时间浪费。
企业应该及时安排生产计划,避免不必要的等待时间,从而有效降低等待浪费。
五、加工浪费:加工浪费指因为产品设计或者操作问题造成的不必要的加工步骤、加工时间等问题。
企业需要加强与设计方面的沟通,避免因为设计问题造成生产加工浪费。
六、过度加工浪费:过度加工浪费指在生产过程中过度加工的产品或者组件,这会导致生产成本和加工周期的增加。
企业应该确保生产出的产品满足设计规范以及客户的需求,从而避免过度加工浪费。
七、废品浪费:废品浪费指在生产过程中出现的废品或者不良品,这会导致原材料以及制造成本的增加,同时也影响了产品的质量和信誉。
企业应该加强品质管理的力度,尽可能降低废品率,从而避免废品浪费的出现。
综上所述,精益生产理论的七大浪费都是可以避免的,企业在生产制造过程中应该加强对于生产环节的管理,尽量减少不必要的浪费,从而提高生产效率和产品质量,实现企业的可持续发展。
精益生产概述之七大浪费

精益生产概述之七大浪费精益生产是一种以消除浪费为核心的生产管理方法,旨在提高生产效率和质量。
七大浪费是精益生产的基本概念之一,它们是指在生产过程中存在的七种浪费现象,并且这些浪费都可以避免或减少。
以下是对七大浪费的简要概述。
1. 运输浪费:指在生产过程中不必要的物料运输或移动,例如将产品从一个车间搬到另一个车间,或者将材料从仓库搬到生产线。
运输浪费会增加生产时间和成本,并容易引起损坏或丢失。
2. 库存浪费:指生产过程中积压的过多原材料、半成品或成品库存。
库存浪费会增加库房和仓储成本,还可能导致过期、损坏或过时的物料。
3. 过程中的等待浪费:指在生产过程中由于机器故障、零部件不足或工人等待等原因导致的停工或非生产时间。
等待浪费会降低生产效率,增加生产周期,并导致交货延迟。
4. 过度加工浪费:指在生产过程中对产品进行过多或不必要的加工。
过度加工浪费会增加生产成本,并可能导致质量问题或产品过度精细化。
5. 度量浪费:指在生产过程中由于测量、追踪或监控不足导致的效率低下或质量问题。
度量浪费会增加错误率和修复成本,并且可能导致产品不符合客户要求。
6. 过剩生产浪费:指生产过程中超出客户需求的产品或数量。
过剩生产浪费会增加库存和仓储成本,并降低资金周转率。
7. 动作浪费:指生产过程中不必要的动作或无效的动作,包括重复、走动、等待、纠正错误等。
动作浪费会降低工人的效率和舒适度,增加生产时间和成本。
精益生产的目标是通过识别和消除这些浪费,提高生产效率和质量,实现产品的快速交付和客户满意度的提升。
通过精益生产的实施,企业可以提高生产线的流程,优化生产方式,减少生产成本,并最大限度地提高企业的竞争力和盈利能力。
精益生产的实施需要从各个方面入手,包括流程优化、员工参与和培训、设备改进等。
下面将进一步探讨精益生产的相关内容,以及其对企业的影响和益处。
首先,要实施精益生产,必须对生产流程进行优化。
通过识别和消除七大浪费,可以简化生产流程,降低生产周期,并提高产品的质量和交货效率。
精益生产七大浪费

1.直接的财务问题。说明库存和在制品增加,资金周转率低,制造时间变长,资金和利息被占用, 会造成库存空间的浪费,这在现金流量表中是很明显的。
2.产生次要问题。搬运和堆积会产生废物;先进先出的工作造成困难;产品积压导致不良品的发生, 物流阻断过程时间变长,现场工作空间变小,存在滞留仓库的风险和不良品的风险。
1. 优化工艺流程,对生产流程进行全面分析,找出其中的瓶颈和不必要的环节,进行优化和改进。 采用更高效的加工方法和设备,减少加工时间和工序。 2. 减少调整时间,通过标准化作业、快速换模等技术手段,减少设备调整和准备时间,提高设备的 利用率。 3. 提高加工精度,采用先进的加工技术和设备,提高加工精度,减少废品和返工,降低加工成本。 4. 引入自动化和智能化,利用自动化设备和智能化系统,提高生产的自动化水平,减少人工干预, 降低加工误差和浪费。 5. 加强质量控制,建立严格的质量控制体系,对原材料、半成品和成品进行严格检测,确保产品质 量符合标准,减少因质量问题导致的加工浪费。 6. 培训员工,加强员工培训,提高员工的技能水平和质量意识,使他们能够熟练掌握加工工艺和操 作方法,减少因操作不当导致的浪费。 7. 持续改进,建立持续改进的机制,鼓励员工提出改进建议,不断优化加工过程,提高生产效率和
5.建立持续改进文化
建立持续改进文化是实现精益生产的关键之一。通过建立持续改进文化,可以使员工充分认识到 浪费的危害和价值,从而积极参与到消除浪费的行动中来。例如,可以定期组织员工进行交流和 分享经验,以提高员工对精益生产的认识和实践水平。
(三)不良品的浪费
(1)不良品浪费对企业生产经营产生了诸多不利影响: (2)成本增加:不良品的产生会增加原材料、人力、设备等资源的浪费,导致生产成本的 增加。 (3)产能降低:不良品的产生会导致生产线停机、返工时间增加,进而降低了企业的产能。 (4)产品质量下降:不良品的产生会影响产品的质量,降低了产品的市场竞争力。 (5)顾客满意度下降:不良品的产生会导致交货延迟、产品质量问题等,降低了顾客的满 意度。
详解精益生产的七大浪费

详解精益生产的七大浪费①物料供应不及或前一道工序的能力不足,导致停工待料;②检验作业的过程中,虽然能够管控产品的品质,但是检验时,造成后道工序作业停顿;③因设备故障造成生产停顿、因发现品质问题造成停工待料;④生产型号切换造成生产停顿。
比如一个生产鞋子的工厂,在生产线的传送带上画一个网格。
正常生产时,每格要放一双鞋。
假设生产时中间有很多网格,说明之前的生产过程肯定有问题。
这时候生产线的主管要尽早处理,减少等待浪费。
2.搬运浪费在搬运过程中产生过多的放置、堆积、移动、整理,不仅费时费力,同时会造成搬运上的浪费。
例如:一间公司生产线的布置.从铸造到磨床,磨床之后到铣床,铣床之后到钻床,接着到焊接,最后到涂装部,完成之后进行检验,检验合格之后才送到包装部进行包装,最后入库。
在这些过程中,移动的次数高达八次之多,所以,在整个流程中,我们应该思考如何减少搬运次数,如何缩短搬运距离,其中,工厂的布置就显得尤为重要。
3.不良浪费在生产过程中,不可避免地会出现产品质量差的情况,而这些差的情况又会造成额外的成本,比如材料的损耗、设备的折旧、劳动力的损耗等。
这时候产品的价格也会受到影响,也许订单会流失,甚至公司的声誉也会受损。
这时候就要利用一系列的检验,比如进货检验、过程检验、产品检验(出货检验),把不良品降到最低,减少不良浪费。
4.动作浪费多余的动作会增加我们的工作强度,降低生产效率。
常见的12个浪费动作是:两只手闲着,一只手闲着,作业停止,动作幅度过大,左右手互换,走路过多,转弯角度过大,边走边换动作,作业技巧没有掌握,背伸动作,弯腰动作,重复或不必要的动作。
有些公司在生产线组装的时候,每道工序的移转都必须要借助一个用手按按键的动作,让每道工序的完成品得以转移到下一个工序,所以,“用手按按键”这个动作就是浪费。
假如今天不用手,改用脚来按按键,就能够移转到下一道工序,这时双手还能持续进行组装的动作,这样就不会造成动作的浪费。
精益生产之七大浪费及5S管理
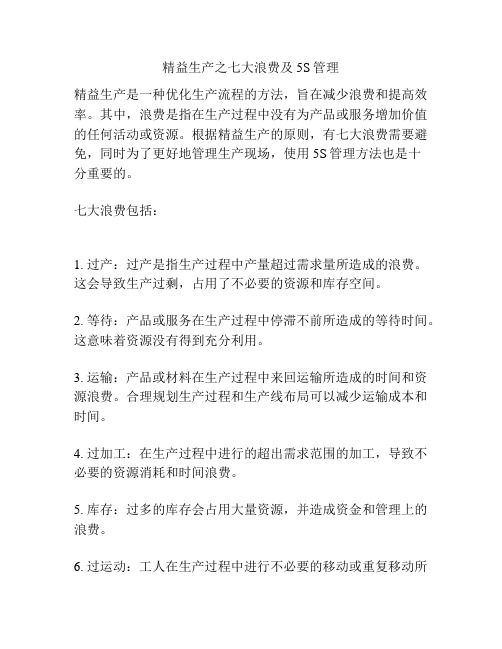
精益生产之七大浪费及5S管理精益生产是一种优化生产流程的方法,旨在减少浪费和提高效率。
其中,浪费是指在生产过程中没有为产品或服务增加价值的任何活动或资源。
根据精益生产的原则,有七大浪费需要避免,同时为了更好地管理生产现场,使用5S管理方法也是十分重要的。
七大浪费包括:1. 过产:过产是指生产过程中产量超过需求量所造成的浪费。
这会导致生产过剩,占用了不必要的资源和库存空间。
2. 等待:产品或服务在生产过程中停滞不前所造成的等待时间。
这意味着资源没有得到充分利用。
3. 运输:产品或材料在生产过程中来回运输所造成的时间和资源浪费。
合理规划生产过程和生产线布局可以减少运输成本和时间。
4. 过加工:在生产过程中进行的超出需求范围的加工,导致不必要的资源消耗和时间浪费。
5. 库存:过多的库存会占用大量资源,并造成资金和管理上的浪费。
6. 过运动:工人在生产过程中进行不必要的移动或重复移动所造成的浪费。
此外,工作场所的布局也可能导致不必要的运动。
7. 失效:产品或设备因为质量问题或故障导致不能正常使用所带来的浪费。
这包括废品、次品和修理等。
为了管理生产现场,5S管理方法可以帮助提高工作效率和质量。
5S分别代表整理、整顿、清扫、清洁和遵守。
1. 整理:整理工作场地,确定需要的物品和设备并清除不需要的物品。
2. 整顿:确定合理的工作流程和布局,确保工作区域的物品和设备放置得井井有条。
3. 清扫:保持工作区域的清洁和整洁,确保工作环境安全和舒适。
4. 清洁:定期进行清洁工作,包括设备和机器的保养和维护,以确保其正常运行。
5. 遵守:遵守标准和规定,执行工作流程,并及时纠正和改进。
精益生产的目标是通过减少浪费和提高效率来提供更高质量的产品和服务。
而5S管理方法可以帮助企业管理生产现场,提高工作效率和质量。
通过合理应用这些原则和方法,企业可以提升竞争力,并更好地满足客户需求。
精益生产的目标是通过减少浪费和提高效率来提供更高质量的产品和服务。
生产过程中的“七大浪费”

生产过程中的“七大浪费”在生产过程中,存在着许多浪费的现象,这些浪费无疑会对企业的生产效率和成本造成不良影响。
为了提高生产效率和降低成本,必须对这些浪费进行深入分析,找出它们的根源,并采取相应的措施进行改善。
在精益生产管理中,有一个概念叫作“七大浪费”,它们是:等待、运输、过程中的库存、过度生产、不良品、过度加工和人的潜力未被充分利用。
下面我将详细介绍这些浪费的定义和对企业的影响。
1.等待:指的是在生产过程中,由于缺乏协调和沟通,造成的等待时间的浪费。
比如,由于材料、工具、设备等的不准时供应,导致工人在生产线上等待。
这种浪费会导致生产效率的下降,增加交货周期,并增加生产成本。
2.运输:指的是生产过程中物料或产品需要进行搬运和运输的浪费。
比如,物料需要多次转运或者不必要的运输过程。
这些额外的运输会导致物料的损耗和错误,增加生产周期和成本。
3.过程中的库存:指的是在生产过程中,大量的半成品或者成品积压在过程中的库存中。
过多的库存会导致资金的占用,增加库存管理和仓储成本,并增加物料的损耗和过期的风险。
4.过度生产:指的是无视市场需求而进行的过度生产。
这种行为会导致产品的积压和过剩,增加产品的滞销和降低产品的价值,同时也会造成资源的浪费和生产成本的增加。
5.不良品:指的是在生产过程中出现的次品或者不合格品的浪费。
这些不良品会给企业带来额外的修复和返工成本,并降低企业的产品质量和信誉。
6.过度加工:指的是对产品进行的无必要的过度加工或处理。
这样的加工会增加不必要的工序和成本,并对产品的质量和交付周期产生负面影响。
7.人的潜力未被充分利用:指的是企业没有充分发挥员工的潜力和创造力,导致员工技术水平的降低和工作积极性的下降。
这种浪费会直接影响到生产效率和产品质量。
所有这些浪费都会对企业的生产效率和成本造成不良影响,因此,为了提高生产效率和降低成本,企业应该采取相应的措施来减少这些浪费。
例如,通过合理的生产计划和物料管理来减少等待时间和物料运输时间,优化生产工艺和流程来避免过度加工和不必要的工序,加强质量控制来减少不良品的产生,提供员工培训和激励机制来充分发挥员工的潜力等等。
精益生产七大浪费口诀
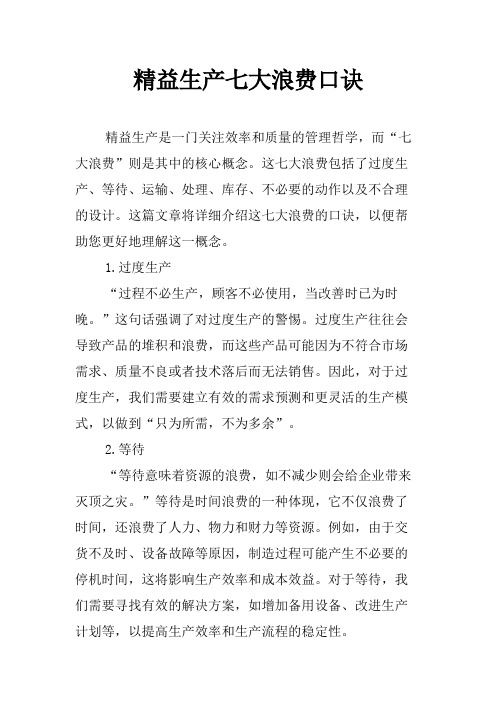
精益生产七大浪费口诀精益生产是一门关注效率和质量的管理哲学,而“七大浪费”则是其中的核心概念。
这七大浪费包括了过度生产、等待、运输、处理、库存、不必要的动作以及不合理的设计。
这篇文章将详细介绍这七大浪费的口诀,以便帮助您更好地理解这一概念。
1.过度生产“过程不必生产,顾客不必使用,当改善时已为时晚。
”这句话强调了对过度生产的警惕。
过度生产往往会导致产品的堆积和浪费,而这些产品可能因为不符合市场需求、质量不良或者技术落后而无法销售。
因此,对于过度生产,我们需要建立有效的需求预测和更灵活的生产模式,以做到“只为所需,不为多余”。
2.等待“等待意味着资源的浪费,如不减少则会给企业带来灭顶之灾。
”等待是时间浪费的一种体现,它不仅浪费了时间,还浪费了人力、物力和财力等资源。
例如,由于交货不及时、设备故障等原因,制造过程可能产生不必要的停机时间,这将影响生产效率和成本效益。
对于等待,我们需要寻找有效的解决方案,如增加备用设备、改进生产计划等,以提高生产效率和生产流程的稳定性。
3.运输“不必要的运输是现代生产的大敌。
”运输是生产过程中的必要环节,但也可能带来不必要的浪费。
例如,因为原材料和产品的运输而导致的等待和停机,以及运输过程中可能产生的损耗和质量问题。
因此,我们需要优化物流系统,缩短运输距离并降低运输成本,以提高生产效率和产品质量。
4.处理“在制造过程中避免处理,欢迎设备运行。
”处理是指在生产过程中需要对产品进行加工、检验、修复等处理,但这些处理可能会浪费时间、资源和质量。
处理不必要的问题通常是因为设计不足或者设备过时。
因此,我们需要改进生产流程并采用现代化的设备和工具,以减少处理次数和提高处理质量。
5.库存“库存过多,等待必定。
”库存是为满足客户需求而存储的产品和原材料,在库存管理不当的情况下,可能会带来许多成本和质量问题。
例如,库存过多会增加物料和产品的损耗、质量问题和过期等问题,同时也会占用企业的物流和仓储资源,增加成本。
- 1、下载文档前请自行甄别文档内容的完整性,平台不提供额外的编辑、内容补充、找答案等附加服务。
- 2、"仅部分预览"的文档,不可在线预览部分如存在完整性等问题,可反馈申请退款(可完整预览的文档不适用该条件!)。
- 3、如文档侵犯您的权益,请联系客服反馈,我们会尽快为您处理(人工客服工作时间:9:00-18:30)。
精益生产中的七大浪费
消除七大浪费是精益生产的核心理念之一,七大浪费可用“TIM WOOD”表示(分别取7种浪费之英文首字母:运输、库存、动作、等待、过量生产、多余的工序、缺陷),以下对七大浪费作简要介绍。
一、七大浪费介绍
第一种:运输的浪费
主要表现为:车间布置采用批量生产,依工作站为区别的集中的水平式布置所致,无流线生产的观念。
第二种:库存的浪费
主要表现为:管理者为了自身的工作方便或本区域生产量化控制一次性批量下单生产,而不结合主生产计划需求流线生产所导致局部大批量库存。
库存的损害表现有:
(1):产生不必要的搬运、堆积、放置、防护处理、找寻等浪费。
(2):使先进先出的作业困难。
(3):损失利息及管理费用。
(4):物品的价值会减低,变成呆滞品。
(5):占用厂房空间,造成多余的工场、仓库建设投资的浪费。
(6):没有管理的紧张感,阻碍改进。
(7):设备能力及人员需求的误判。
第三种:动作的浪费
主要因素表现为:生产场地不规划,生产模式设计不周全,生产动作不规范统一。
第四种:等待的浪费
主要因素表现为:作业不平衡,安排作业不当、待料等。
第五种:过量生产的浪费
主要因素表现为:管理者认为制造过多与过早能够提高效率或减少产能的损失和平衡车间生产力。
制造过多(早)的损害表现有:
(1):提早用掉费用(材料费、人工费),不能创造利润。
(2):把“等待的浪费”隐藏起来,使管理人员漠视等待的发生和存在。
(3):自然而然地积压在制品,其结果不但会使制程的时间变长(无形的),而且会使现场工作的空间变大,机器间距离因此加大,逐渐地吞蚀利
润。
(4):产生搬运,堆积的浪费,使得先进先出的作业产生困难。
第六种:多余的工序的浪费
主要因素表现为:制造过程中作业加工程序动作不优化,可省略、替代、重组或合并的未及时检查。
第七种:缺陷的浪费
主要因素表现为:工序生产无标准确认或有标准确认未对照标准作业,管理不严密、松懈所导致。
二、以制造业为例,消除浪费之优先顺序
优先级#1 过量生产
这是7种浪费中最严重的一种,因为:a)它衍生出了另外的6种浪费b)它掩盖了真正的生产能力,从而导致你做出诸如转包工作或是在不必要的方面投资这样错误的决定。
优先级#2 缺陷
消除残次品是第二项,当你生产出的低质量产品,相当于纯粹的浪费。
时间、能源和物料白白地消耗掉,而且,即使这样没有丢失顾客,你还是要将工作重新再做一次。
优先级#3 库存
库存占用资金,还需要投入劳动力、能源和固定资产(仓库)去管理它,库存最坏的影响就是可能制造假象使很多问题被掩盖。
优先级#4 动作浪费
是前面三个后接下来的候选项,如果考虑到工人的操作是否涉及安全方面或许它应该列为第一位。
根据消除的难易程度、改进影响的大小,多余动作这一项的级别会比较高,常常作为改善的目标。
优先级#5 多余的工序
简单理解就是不必要的或是耗费更多资源(能源、步骤、时间、或是物料)的流程。
一旦识别出来这样的流程就要快速排除,它影响会很大但并不像其他六种浪费那样易于发现。
优先级#6运输问题
比较显而易见,明显没有附加价值,本身也不会造成巨大的浪费。
如果运输造成不合格率上升、多余的流程(标注、登记、计数)、库存(分批移动节省运费),这时此种浪费的优先级就要上升了。
优先级#7 等待
是危害最小的一个。
因为除了劳动力你并不消耗资源,不会存在过量生产、运输或是多余动作造成的事故,不合格产品,也不会增加额外的库存。
这一点可能很难做到,但最好还是要告诉人们“宁可等着,也不要生产过量”,让问题暴露出来,以便能够挖掘到问题的核心所在。
消除7种浪费是丰田生产系统和构建企业中精益文化的基础,在经典TPS里是没有清晰区别消除七种浪费的优先级。
但在这个问题上做深入的讨论要适可而止,我们更应该花费更多的时间在现场进行实际的哪怕是很小的一点改善。