某公司SCM供应链管理(英文版)
供应链管理(Supply Chain Management , SCM)

供应链管理(Supply Chain Management , SCM)供应链管理的定义与内容供应链管理(Supply Chain Management ,简称SCM):就是指在满足一定的客户服务水平的条件下,为了使整个供应链系统成本达到最小而把供应商、制造商、仓库、配送中心和渠道商等有效地组织在一起来进行的产品制造、转运、分销及销售的管理方法。
供应链管理包括计划、采购、制造、配送、退货五大基本内容。
计划:这是SCM的策略性部分。
你需要有一个策略来管理所有的资源,以满足客户对你的产品的需求。
好的计划是建立一系列的方法监控供应链,使它能够有效、低成本地为顾客递送高质量和高价值的产品或服务。
采购:选择能为你的产品和服务提供货品和服务的供应商,和供应商建立一套定价、配送和付款流程并创造方法监控和改善管理,并把对供应商提供的货品和服务的管理流程结合起来,包括提货、核实货单、转送货物到你的制造部门并批准对供应商的付款等。
制造:安排生产、测试、打包和准备送货所需的活动,是供应链中测量内容最多的部分,包括质量水平、产品产量和工人的生产效率等的测量。
配送:很多“圈内人”称之为“物流”,是调整用户的定单收据、建立仓库网络、派递送人员提货并送货到顾客手中、建立货品计价系统、接收付款。
退货:这是供应链中的问题处理部分。
建立网络接收客户退回的次品和多余产品,并在客户应用产品出问题时提供支持。
现代商业环境给企业带来了巨大的压力,不仅仅是销售产品,还要为客户和消费者提供满意的服务,从而提高客户的满意度,让其产生幸福感。
科特勒表示:“顾客就是上帝,没有他们,企业就不能生存。
一切计划都必须围绕挽留顾客、满足顾客进行。
”要在国内和国际市场上赢得客户,必然要求供应链企业能快速、敏捷、灵活和协作地响应客户的需求。
面对多变的供应链环境,构建幸福供应链成为现代企业的发展趋势。
供应链管理方法供应链管理理论的产生远远落后于具体的技术与方法。
供应链管理

SCM School of Logistics, BWU
13
Chapter 1 Background of SCM 三、SCM的产生(Emergence of SCM)
“横向一体化”形成了一条从供应商到制造商再到分销商、 零售商,最终再到顾客的贯穿所有企业和顾客的“链”。由 于相邻节点企业或顾客表现出一种需求与供应的关系,当 把所有相邻企业或顾客依此连接起来,便形成了SC,见图 1-2。这条链上的节点企业必须达到同步、协调运行,才有 可能使链上的所有企业都能受益。于是便产生了SCM这一 新的经营与运作模式。
SCM School of Logistics, BWU
7
Course Explanation
对需求 作出快 速反应
高质量
个性化
优质
SCM School of Logistics, BWU
2
Course Explanation
三、教学方法与要求(Teaching Methods and Requirements)
本章是SCM出现的相关背景,主要包括21世纪全球 市场竞争的主要特点、新的竞争环境对企业管理模式的 影响以及供应链管理的产生。通过本章的学习,要求:
①理解21世纪全球市场竞争的4个主要特点; ②弄清新的竞争环境对企业管理模式产生的影响; ③了解SCM是如何产生的; ④了解几种典型的供应链结构; ⑤掌握如何学习SCM。
2
第八章 供应链的业务流程再造
3
第九章 供应链企业绩效评价
2
第十章 供应链管理环境下的企业管理
4
总复习
1
合计
32
SCM School of Logistics, BWU
供应链管理Supply Chain Management的定义与重要性

供应链管理SUPPLY CHAIN MANAGEMENT, SCMSCM seeks to synchronize a firm’s processes and those of its suppliers 供应链管理寻求试图使公司和其供应商的流程同步化 【Stone, 2008-6-20】 to match the flow of 物料、服务和信息with customer demand 客户需求. SCM has strategic implications 战略意义 because competitive priorities 竞争优先权【】Supply-Chain Management involves the coordination of key processes in the firm such as order placement, order fulfillment, and purchasing, which are supported by marketing, finance, engineering, information systems, operations, and logistics.Managing the flow of material is common to organizations in every segment of the economy: churches, governments, manufactures, wholesalers, retailers, and universities.This chapter looks at the supply chain management concept, which links one’s supplier’s suppliers and one’s customers’ customers. Also covered is logistics outsourcing or 3PL (third party logistics)(1) 供应链的重要特征Key attributes of supply-chain management(2) 供应链管理的壁垒Barriers to supply-chain management(3) 供应链管理和一体化supply-chain management and integration供应链管理:定义Definition of SCMSupply chain management, SCM 供应链管理 can be defined as “the systemic, strategic business functions within a particular company and across businesses in the supply chain 供应链, for the purpose of improving the long-term performance of the individual companies and the supply chain as whole 为了改进某个公司和整个供应链的长期绩效.”定义1:商业流程集成论供应链管理是集成从最终用户到最初供应商的商业流程,以向客户以及其他相关者提供产品、服务、信息,达到增值的目的。
供应链管理(英文课件)Chapter8-Supply Chain Integration
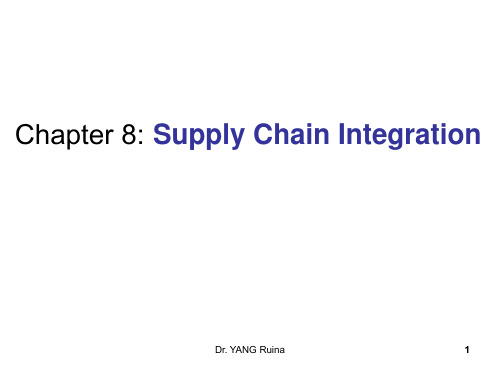
• minimizing inventory, transportation, and production costs.
– Supply Chain Planning processes are applied.
costs – more emergency production changeovers
Pull-Based Supply Chains
• Production and distribution are demand driven
– Coordinated with true customer demand rather than forecast demand.
Push-Based Supply Chains
• Longer reaction time to changing marketplace:
– Inability to meet changing demand patterns. – Obsolescence of supply chain inventory as
• Advantages and disadvantages of push and pull supply chains:
– new supply chain strategy that takes the best of both. – Push–pull supply chain strategy
Impact of the Push-Pull Strategy
• Pull portion
– High uncertainty – Simple supply chain structure – Short cycle time – Focus on service level. – Achieved by deploying a flexible and
供应链管理详细资料英文版
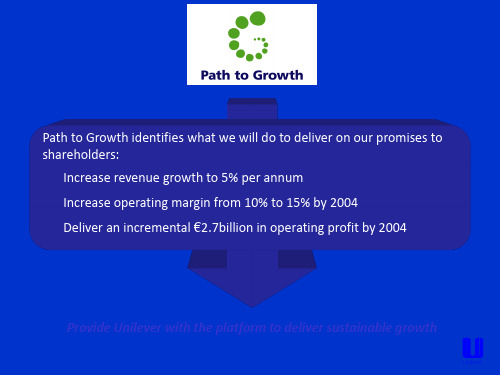
Increase revenue growth to 5% per annum
Increase operating margin from 10% to 15% by 2004
160
140
120
Peer Group
Peer Group:
Beiersdorf,Avon, Cadbury, Clorox, Coca Cola, Colgate, Danone, Eridania, Gillette, Heinz, Kao, Lion, L’Oreal, Nestle, P&G, Philip Morris, Reckitt Benckiser, Sara Lee, Shiseido, Pepsico
Professional Skills
❖ An excellent overall understanding of the business, it’s processes and their linkages
❖ Business behaviours
❖ Outstanding performance
By: Establishing a Global Buying programme Establishing a world class manufacturing programme
Resulting in (approximately): 100 fewer manufacturing sites €€1.6 billion buying savings by end 2002 €€0.5 billion manufacturing savings per annum
供应链管理(英文)
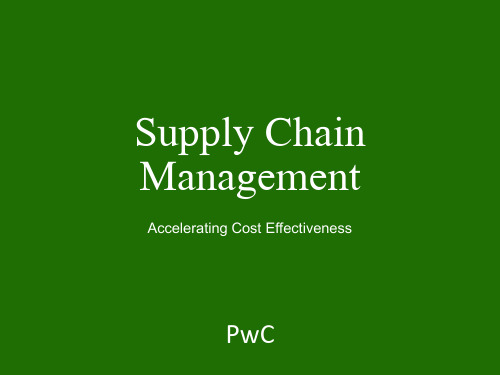
2
PricewaterhouseCoopers
Top Issues Facing SCM Professionals
Funding
11%
In a recent quantitative
Global Management
12%
survey, SCM
Organisation Structure
12%
professionals were
Procurement Planning
Manufacturing Planning
7
Distribution Planning
Demand Planning
PricewaterhouseCoopers
Cross-Functional Supply Chain Metrics
Purchasing Manufacturing
• Today, the talk is of "supply networks", "parallel chains", "enhanced concurrent activities", and “customer centric” with new information platforms and technology set to cut both inventory and lead-times throughout the delivery pipeline further.
Supply Chain Management
Accelerating Cost Effectiveness
PwC
Supply Chain Management
• The supply chain used to be a simple serial process with raw materials slowly moving in one direction through manufacturing production and onward via a distribution system to retailers and customers.
供应链管理系统双语英文翻译

1) A supply chain includes only the organizations directly involvedin supplying components needed for manufacturing.一个供应链仅包括直接参与提供所需的元件制造业的组织。
Answer: FALSE2) A supply chain consists of all parties involved, directly or indirectly, in fulfilling a customer request. Answer: TRUE供应链由所有各方,直接或间接参与,满足客户要求。
3) A supply chain could be more accurately described as a supply network or supply web.Answer: TRUE供应链可以更准确地描述为供应网络。
4) The objective of every supply chain is to maximize the overall value generated. TRUE每一个供应链的目的是生成的整体价值最大化。
5) The objective of every supply chain is to maximize the value generated for the manufacturing component of the supply chain. Answer: FALSE每一个供应链的目标是最大化为供应链的制造组件生成价值。
6) Every supply chain must include all 5 stages. Answer: FALSE每个供应链必须包括所有 5 个阶段。
7) The cycle view of a supply chain holds that the processes in a supply chain are divided into a series of activities performed at the interface between successive stages. Answer: TRUE供应链周期认为供应链流程分为一系列的活动上演在连续阶段之间的接口。
供应链管理及业务管理知识分析模式(英文版)

供应链管理及业务管理知识分析模式(英文版) Supply Chain Management and Business Management Knowledge Analysis ModelIntroduction:Supply chain management (SCM) and business management are two crucial aspects of a company's success and growth. SCM involves the coordination and management of all activities involved in buying, producing, and delivering products or services to customers. On the other hand, business management encompasses the planning, organizing, and controlling of all business operations to achieve organizational goals. This article aims to analyze the key knowledge areas within SCM and business management, highlighting their importance and interdependence.1. Supply Chain Management Knowledge Areas:1.1 Logistics Management:Logistics management focuses on the movement of goods and materials from suppliers to customers. It involves the transportation, warehousing, inventory control, and order fulfillment processes. Efficient logistics management ensures timely delivery, reduces costs, and enhances customer satisfaction.1.2 Procurement and Supplier Management:This knowledge area involves the selection, evaluation, and management of suppliers to ensure the reliable and cost-effective supply of materials or services. It includes activities such as sourcing, negotiation, contract management, and supplierperformance measurement.1.3 Demand Planning and Forecasting:Demand planning and forecasting involve the estimation of future customer demand for products or services. It helps in the optimization of inventory levels, production planning, and resource allocation. Accurate forecasting reduces stockouts, minimizes inventory carrying costs, and improves customer service.1.4 Inventory Management:Inventory management encompasses the control and optimization of inventory levels to meet customer demands while minimizing holding costs. It includes inventory classification, safety stock determination, replenishment strategies, and utilization of advanced inventory management techniques like just-in-time (JIT) and economic order quantity (EOQ).1.5 Risk Management:Supply chain risk management involves identifying, assessing, and mitigating risks associated with supply chain operations. It includes evaluating risks related to supplier reliability, demand volatility, transportation disruptions, natural disasters, and geopolitical factors. Effective risk management helps in minimizing potential disruptions and ensuring business continuity.2. Business Management Knowledge Areas:2.1 Strategic Planning:Strategic planning involves setting the long-term goals and direction of the company. It includes analyzing internal andexternal factors, conducting market research, defining the company's mission and vision, and formulating strategies to achieve competitive advantage. Strategic planning provides a roadmap for decision-making and resource allocation.2.2 Financial Management:Financial management focuses on the efficient utilization and allocation of financial resources within the company. It includes budgeting, financial analysis, cash flow management, and capital investment decisions. Effective financial management ensures profitability, liquidity, and sustainability of the business.2.3 Organizational Behavior:Organizational behavior refers to understanding individual and group dynamics within the company. It includes topics like motivation, leadership, communication, team dynamics, and organizational culture. Understanding and managing organizational behavior promotes employee engagement, productivity, and effective teamwork.2.4 Marketing and Sales Management:Marketing and sales management involves the identification of target markets, development of marketing strategies, and implementation of promotional activities to achieve sales objectives. It includes market research, product development, pricing, distribution, and customer relationship management. Effective marketing and sales management drive customer acquisition, retention, and revenue generation.2.5 Operations Management:Operations management focuses on the design, control, and improvement of production processes to deliver products or services efficiently. It includes capacity planning, production scheduling, quality management, and continuous process improvement. Effective operations management increases productivity, reduces costs, and ensures customer satisfaction.Conclusion:Supply chain management and business management are interconnected and essential for the success of any company. A comprehensive knowledge analysis model helps to identify and prioritize key knowledge areas within these domains. Companies that effectively manage their supply chains and employ sound business management principles gain a competitive edge, achieve operational excellence, and sustain long-term growth and profitability.3. Interdependence between Supply Chain Management and Business Management:The interdependence between supply chain management and business management is crucial for the overall success and growth of a company. While supply chain management focuses on the operational aspects of sourcing, production, and delivery, business management provides the strategic framework and direction for these activities. The knowledge areas within both domains are interconnected and rely on each other for effective decision-making and implementation.For example, strategic planning plays a significant role in both supply chain management and business management. A company'sstrategic objectives and goals influence its supply chain strategy, such as sourcing strategies, selection of suppliers, and distribution network design. On the other hand, the company's supply chain capabilities and constraints impact its overall strategic decisions, such as market entry strategies, product differentiation, and pricing.Similarly, financial management is essential for both supply chain management and business management. Efficient financial management helps in allocating resources effectively within the supply chain, such as optimizing inventory levels, implementing cost-saving measures, and improving cash flow. It also enables the company to make informed business decisions, such as investing in new technologies or expanding into new markets.Organizational behavior plays a critical role in both domains as well. Effective communication, teamwork, and leadership within the supply chain contribute to smooth coordination and collaboration among various stakeholders. In business management, understanding organizational behavior helps in creating a positive work culture, motivating employees, and fostering innovation, thereby leading to better business performance and customer satisfaction.Marketing and sales management are interconnected with supply chain management as well. Market research and customer insights are crucial in demand planning and forecasting, which informs supply chain decisions, such as production levels, inventory management, and transportation requirements. Conversely, supply chain capabilities influence marketing and sales strategies, such as product availability, delivery speed, and customer service levels.Integration between these knowledge areas ensures alignment between supply and demand, resulting in customer satisfaction and competitive advantage.Furthermore, operations management plays a key role in both supply chain management and business management. Efficient operations management techniques, such as lean manufacturing, Six Sigma, and total quality management, improve productivity, reduce waste, and enhance product/service quality. These improvements, in turn, enhance the company's overall performance and competitiveness. Additionally, operations management principles help in optimizing supply chain processes, such as production scheduling, inventory management, and order fulfillment, leading to cost savings, shorter lead times, and improved customer satisfaction.4. Importance of Supply Chain Management and Business Management Knowledge:The knowledge areas within supply chain management and business management are crucial for companies to remain competitive, adapt to changing market dynamics, and drive overall business success. Below are the key reasons why companies should prioritize and invest in these knowledge areas:4.1 Optimal Resource Utilization:Efficient supply chain management ensures optimal utilization of resources, such as raw materials, production capacity, and transportation, resulting in cost savings and improved profitability. Likewise, effective business management helps in allocatingfinancial, human, and technological resources to their best possible use, maximizing the value generated by the company.4.2 Enhanced Customer Satisfaction:Supply chain management focuses on meeting customer demands by ensuring the availability of products/services, on-time delivery, and quick response to customer queries. This improves customer satisfaction and loyalty. Business management, meanwhile, helps in developing effective marketing and sales strategies, understanding customer preferences, and delivering superior customer service, further enhancing customer satisfaction and building long-term relationships.4.3 Risk Mitigation and Resilience:Supply chain management knowledge areas, such as risk management and procurement, help in identifying and mitigating potential risks to the supply chain, including disruptions from suppliers, transportation issues, or natural disasters. Business management complements these efforts by implementing suitable risk management strategies at the organizational level, such as diversifying revenue streams, implementing robust financial controls, and building strong relationships with key stakeholders. This ensures business continuity and resilience.4.4 Competitive Advantage:Companies that excel in supply chain management gain a competitive advantage by offering better value to customers through lower costs, higher product quality, and faster delivery. Similarly, effective business management, through strategic planning, marketing, and operations, helps companies differentiatethemselves from competitors and create unique value propositions that attract and retain customers.4.5 Innovation and Agility:Both supply chain management and business management knowledge areas foster innovation and agility within organizations. Supply chain innovation, such as implementing advanced technologies like automation, AI, and IoT, improves operational efficiency, reduces costs, and enables faster response to market changes. Business management knowledge areas, such as strategic planning and organizational behavior, help in creating a culture of innovation, driving continuous improvement, and fostering agile decision-making.Conclusion:Effective supply chain management and business management are critical for the success of any company. The knowledge areas within these domains are interconnected and mutually dependent. Companies that prioritize and invest in these knowledge areas gain a competitive edge, achieve operational excellence, and sustain long-term growth and profitability. Understanding and implementing the key principles and practices within supply chain management and business management enable companies to optimize resources, enhance customer satisfaction, mitigate risks, and leverage opportunities for innovation and competitive advantage.。
- 1、下载文档前请自行甄别文档内容的完整性,平台不提供额外的编辑、内容补充、找答案等附加服务。
- 2、"仅部分预览"的文档,不可在线预览部分如存在完整性等问题,可反馈申请退款(可完整预览的文档不适用该条件!)。
- 3、如文档侵犯您的权益,请联系客服反馈,我们会尽快为您处理(人工客服工作时间:9:00-18:30)。
Software Configuration Management(SCM)Document Number: [nn]Date: Day, Month Day, Year[Project Name][Author 1][Author 2 - if none, leave blank line][Author 3 - if none, leave blank line][Author 4 - if none, leave blank line]Professor [Name]Software Engineering DepartmentMonmouth UniversityWest Long Branch, NJ 07764-1898Table of Contents1. SCOPE 41.1.I DENTIFICATION 4 1.2.S YSTEM O VERVIEW 4 1.3.D OCUMENT O VERVIEW 42. REFERENCED DOCUMENTS 53. REQUIREMENTS SUMMARY 53.1.B ACKGROUND,O BJECTIVES, AND S COPE 5 3.2.O PERATIONAL P OLICIES AND C ONSTRAINTS 6 3.3.D ESCRIPTION OF C URRENT S YSTEM OR S ITUATION 6 3.4.U SERS OR I NVOLVED P ERSONNEL7 3.4.1C ONFIGURATION R EQUIREMENTS8 3.5.S OFTWARE C ONFIGURATION M ANAGEMENT C RITERIA94. JUSTIFICATION 124.1A SSUMPTIONS AND C ONSTRAINTS12 4.2A DDITIONAL I TEMS FOR CONSIDERATION: 125. NOTES 131 Scope[This section shall be divided into the following paragraphs.]1.1 Identification[This paragraph shall contain a full identification of the system and the software to which this document applies, including, as applicable, identification number(s), title(s), abbreviation(s), version number(s), and release number(s).]1.2 System Overview[This paragraph shall briefly state the purpose of the system and the software to which this document applies. It shall describe the general nature of the system and software; summarize the history of system development, operation, and maintenance; identify the project sponsor, acquirer, user, developer, and support agencies; identify current and planned operating sites; and list other relevant documents.]1.3 Document Overview[This paragraph shall summarize the purpose and contents of this document and shall describe any security or privacy considerations associated with its use.]2 Referenced Documents[This section shall list the number, title, revision, and date of all documents referenced in this specification. This section shall also identify the source for all documents.]3 Requirements Summary[This section shall be divided into the following paragraphs to describe the risk management requirements as it currently exists.]3.1 Background, Objectives, and Scope[This paragraph shall describe the background, mission or objectives, and scope of the product or situation.][Example: Requirements regarding software configuration management (SCM) cover a broad arena. SCM is considered one of the integral processes that support the other activities in the standard. The developer's approach, described in the project's SDP, is to address all applicable contract clauses for SCM including:Configuration identificationConfiguration controlConfiguration status accountingConfiguration auditsPackaging, storage, handling, and delivery3.2 Operational Policies and Constraints[This paragraph shall describe any operational policies and constraints that apply to the current system or situation.][Example: SCM activities apply to all software products prepared, modified, and/or used to develop software products as well as to the products under development, modification, reengineering, or reuse. If a system/subsystem or SWI is developed in multiple builds, SCM in each build is to be understood to take place in the context of the software products and controls in place at the start of the build.]3.3 Description of Current System or Situation[This paragraph shall provide a description of the current system or situation, identifying differences associated with different states or modes of operation (for example, regular, maintenance, training, degraded, emergency, alternative-site, wartime, peacetime). The distinction between states and modes is arbitrary. A system may be described in terms of states only, modes only, states within modes, modes within states, or any other scheme that is useful. If the system operates without states or modes, this paragraph shall so state, without the need to create artificial distinctions. ]3.4 Users or Involved Personnel[This paragraph shall describe the types of users of the system, or personnel involved in the current situation, including, as applicable, organizational structures, training/skills, responsibilities, activities, and interactions with one another.][Example: Developer's key activities related to Software configuration management:Describe the approach to be followed for software configuration management, identifying risks/uncertainties and plans for dealing with them. Cover all contractual clauses pertaining to software configuration management.Participate in selecting CSCIs during system (architectural) design. Identify entities to be placed under configuration control. Assign a project-unique identifier to each SWI and each additional entity to be placed under configuration control, including software products to be developed or used and the elements of the software development environment. Use an identification scheme that identifies entities at the level of control and include version/revision/release status.Establish and implement procedures designating levels of control each identified entity must pass through, the persons or groups with authority to authorize changes and to make changes at each level, and the steps tobe followed to request authorization for changes, process change requests, track changes, distribute changes, and maintain past versions. Propose to the acquirer, in accordance with contractually established forms and procedures, changes that affect an entity already under acquirer control. Prepare and maintain records of configuration status of all entities that have been placed under project-level or higher configuration control. Maintain configuration status records for the life of the contract. Include, as applicable, version/revision/release, changes since being placed under project-level or higher configuration control, and status of associated problem/change reports.Support acquirer-conducted configuration audits as specified in the contract.Establish and implement procedures for packaging, storage, handling, and delivery of deliverable software products. Maintain master copies of delivered software products for the duration of the contract.Prepare a version description for the system.Meet general requirements and perform integral processes of the standard.]3.4.1 Configuration Requirements[This paragraph describes the configuration management requirements for the project.][Example: SCM requirements task the developer to "keep track of" everything during the course of the development. SCM is an activity, not an organization. SCM may be performed by members of the development team, individuals within a project tasked with that responsibility, a separate organization, or other arrangement suitable for the project.]3.5 Software Configuration Management Criteria[This paragraph describes the software configuration management criteria to be followed during the project.[Example: The standard requires the developer to establish levels of control for all work products. Some examples of possible levels of control and of things the developer might identify and control are:Author control:Engineering data -- notes, records, work-in-progress (i.e., dataspecified in documents associated with particular developmentactivities)Software development filesProject control:Source code files, data files, installation softwareInformation in documents agreed upon by the project to becorrectReuse librariesEvaluation recordsOrganizational control:General purpose software -- operating systems, databasemanagement systems, e-mail, word processors, spreadsheetsEngineering and development tools -- CASE tools, editors,compilers, debuggers, SCM tools, test softwareComputer system administrative tools and products -- diagnosticsoftware, network managers, archives, backupsEvaluation recordsAcquirer control:SpecificationsSome key goals of SCM requirements are to ensure that the developer: keeps track of all software and software product descriptions associatedwith the project; implements only authorized changes to requirements; and knows what software and associated products match a specific set of requirements or changes to those requirements.To implement changes to requirements, the acquirer and developer must agree upon what those changes are. When requirements have been defined and recorded as specifications and those specifications have been placed on contract, changes are implemented through contract modifications. When specifications have not been made a part of the contract, the acquirer and developer will need to provide a means for controlling and making changes to requirements. These means can be as informal as a phone call or hand-shake, or as formal as documents signed by authorized acquirer and developer representatives. The standard does not provide contractual forms or notices concerning changes in requirements, such as Engineering Change Proposals (ECPs), Engineering Change Notices (ECNs), or notification to users of changes in a particular version of the software. Although the standard does provide a reminder in the form of two "shell" requirements to support acquirer configuration management activities for (1) proposing changes to acquirer controlled entities, and (2) supporting configuration audits, these activities may not apply to all projects.All work products (including computerized files, the software products that constitute the development environment, and hardware), not just deliverables, are to be identified and controlled during the developmentand under developer software configuration management activity. The physically controlled items can include: computer files, magnetic media (tapes, diskettes, video cassettes), paper documents, books, manuals, and drawings.The standard leaves it up to the developer to describe what software configuration management records will be produced, when they will be produced, the level of detail of information that will be contained in each record and who is responsible for performing these activities.4 Justification[This section shall be divided into the following paragraphs.]4.1 Assumptions and Constraints[This paragraph shall identify any assumptions and constraints applicable to the changes identified in this section.]4.2 Additional Items for consideration:[This paragraph shall identify additional items that should be taken into consideration.][Example: Additional items that should be taken into consideration are: Describe the approach to be followed for software product evaluation, identifying risks/uncertainties and plans for dealingwith them. Cover all contractual clauses pertaining to softwareproduct evaluation.•Perform in-process evaluations of the software products generated. Perform a final evaluation of each deliverablesoftware product before its delivery.•Prepare and maintain records of each software product evaluation. Maintain these records for the life of the contract.Handle problems in software products under project-level orhigher configuration control in accordance with paragraph 5.17of the standard.•Maintain independence in software product evaluation. The persons responsible for evaluating a software product are not tobe the same persons who developed the product.•Meet general requirements and perform integral processes of the standard.5 Notes[This section shall contain any general information that aids in understanding this document (e.g., background information, glossary, rationale). This section shall include an alphabetical listing of all acronyms, abbreviations, and their meanings as used in this document and a list of terms and definitions needed to understand this document.]。