专用铣床液压系统设计
专用铣床液压系统设计

摘要1.铣床概述铣床是用铣刀对工件进行铣削加工的机床。
铣床除能铣削平面、沟槽、轮齿、螺纹和花键轴外,还能加工比较复杂的型面,效率较刨床高,在机械制造和修理部门得到广泛应用。
2.液压技术发展趋势液压技术是实现现代化传动与控制的关键技术之一,世界各国对液压工业的发展都给予很大重视。
液压气动技术具有独特的优点,如:液压技术具有功率传动比大,体积小,频响高,压力、流量可控性好,可柔性传送动力,易实现直线运动等优点;气动传动具有节能、无污染、低成本、安全可靠、结构简单等优点,并易与微电子、电气技术相结合,形成自动控制系统。
主要发展趋势如下:1.减少损耗,充分利用能量2.泄漏控制3.污染控制4.主动维护5.机电一体化6.液压CAD技术7.新材料、新工艺的应用3. 主要设计内容本设计是设计专用铣床工作台进给液压系统,本机床是一种适用于小型工件作大批量生产的专用机床。
可用端面铣刀,园柱铣刀、园片及各种成型铣刀加工各种类型的小型工件。
设计选择了组成该液压系统的基本液压回路、液压元件,进行了液压系统稳定性校核,绘制了液压系统图,并进行了液压缸的设计。
关键词铣床;液压技术;液压系统;液压缸ABSTRACT1. Milling machine is general to stateMilling machine is to carry out the machine tool of milling processing with milling cutter for workpiece. Milling machine excludes can milling plane, groove, gear teeth, thread and spline axle are outside, can still process more complex type surface, efficiency has high planer comparatively, when mechanical production and repair department get extensive application.2. Hydraulic technology develops tendencyHydraulic technology is that the one of crucial technical, world countries that realize modern transmission and control give great attention to the development of hydraulic industry. Hydraulic pneumatic technology has unique advantage , such as: Hydraulic technology has power weight than is big, volume is little, frequently loud and high, pressure and rate of flow may control sex well, it may be flexible to deliver power , is easy to realize the advantages such as the sport of straight line; Pneumatic transmission has energy saving, free from contamination, low cost and safe reliable, structural simple etc. advantage , and is easy to form automatic control system with microelectronics and electric in technology. Develop tendency mainly to be as follows:1. Reduce wastage , use energy2 fully. Leak control3. Pollute control4. Defend5 initiatively. Electromechanical unifinication6. Hydraulic CAD technical7. The application of new material and new technology3. Design content mainlyQuantity of production. May use the garden column milling cutter, garden flat and milling cutter of end panel and is various to process the small-sized workpiece of various types into type milling cutter.Designing have selected to form hydraulic element and the basically hydraulic loop of this hydraulic system , have carried out hydraulic systematic stability school nucleus , have drawn hydraulic system to seek , and have carried out the design of hydraulic big jar.Key words milling machine;hydraulic technology;hydraulic system;hydraulic big jar目录摘要 2 毕业设计任务书 5 第一章专用铣床液压系统设计 7 1.1 技术要求 7 1.2 系统功能设计 71.2.1 工况分析 71.2.2 确定主要参数,绘制工况图 81.2.3 拟定液压系统原理图 101.2.4 组成液压系统 10 1.3系统液压元件、辅件设计12 第二章专用铣床液压系统中液压缸的设计17 2.1 液压缸主要尺寸的确定 17 2.2 液压缸的结构设计 20 致谢24 参考文献 25毕业设计任务书一、设计课题专用铣床液压系统设计二、设计依据某铣床工作台为卧式布置(导轨为水平导轨,其静、动摩擦因数µs=0.2;µd=0.1),拟采用缸筒固定的液压缸驱动工作台,完成工件铣削加工时的进给运动;工件采用机械方式夹紧。
专用铣床液压系统设计课程设计

专用铣床液压系统设计课程设计专用铣床液压系统设计课程设计一、引言在现代机械加工领域,铣床是一种常用的机床设备。
为了提高铣床的运行效率和精度,液压系统被广泛应用于铣床中。
本课程设计旨在通过对专用铣床液压系统的设计,使学生掌握液压系统的原理和设计方法。
二、液压系统基础知识1. 液压系统概述液压系统是利用流体传递能量的一种动力传动系统。
它由液压泵、执行元件、控制元件和辅助元件等组成。
2. 液压传动基本原理液体在容器中形成封闭的流体传递介质,通过液压泵产生的高压油将能量传递到执行元件上,从而实现工作机构的运动。
3. 液压执行元件常见的液压执行元件包括油缸、马达和阀门等。
油缸通过受力面积差异实现线性运动,马达则通过转子与定子之间的摩擦力实现旋转运动。
三、专用铣床液压系统设计1. 设计目标专用铣床液压系统的设计目标是实现铣床的高效率、高精度和安全稳定的运行。
2. 系统组成专用铣床液压系统主要由液压泵、油缸、控制阀和辅助元件等组成。
液压泵负责产生高压油,油缸负责驱动工作台进行运动,控制阀则用于控制油液的流向和压力。
3. 液压系统参数选择根据铣床的工作要求和性能指标,选择合适的液压元件参数。
包括液压泵的流量、工作台的移动速度和承载能力等。
4. 液压系统布局设计根据铣床结构和工作台运动方式,合理布局液压元件。
保证油路畅通,减小能量损失和泄漏。
5. 液压系统控制策略设计根据铣床的工作过程,确定合理的控制策略。
可以采用手动控制或自动控制方式,实现对工作台运动的精确控制。
6. 液压系统安全保护设计在液压系统中添加安全保护装置,如过载保护阀、压力传感器和液压缸的行程限位装置等,以确保铣床的安全运行。
四、课程设计步骤1. 确定课程设计内容和目标明确课程设计的具体内容和目标,包括液压系统的基本原理、专用铣床液压系统的设计要求等。
2. 学习液压系统基础知识学生需要通过自学或教师讲解等方式,掌握液压系统的基本原理、执行元件和控制元件等知识。
课程设计-专用铣床液压系统设计1

液压课程设计一、负载分析负载扭矩:750060238.73 22300p n T m nππ⨯===⨯切削力:3238.7310397912022tTF ND⨯===静摩擦力:50000.21000 fsF N=⨯=动摩擦力:50000.1500 fdF N=⨯=惯性力:5000 4.08509.80.0460mF N=⨯=⨯液压缸各动作段负载列表如下:液压缸机械效率:0.9mη=二、绘制液压工况(负载速度)图:根据工况负载绘制负载图和速度图如下:行程(行程(三、初步确定液压缸的参数:1、初选液压缸的工作压力:根据液压缸的推力为4917 N ,按表10-2选用液压缸的工作压力521303510akgp p cm==⨯2、计算液压缸尺寸:选用差动液压缸,活塞杆面积如下关系:122A A =,于是0.707d D =根据表10-2取背压52810p p =⨯,当液压缸快进时作差动连接,此时, 由于管中有压力损失,液压缸有杆腔的压力必须大于无杆腔的压力,这项压力损失可按5510p ⨯估计,即回油管路压力损失5510p p ∆=⨯,从满足推力 出发,计算液压缸面积IF A4225521491715.91015.935100.58102IF F A m cm P P ===⨯=⨯-⨯⨯-液压缸直径D 为:4.5D ===按JB 2183-77圆整后,取就近标准值,则D=4.5cm ,活塞杆直径0.7070.7075 3.18d D cm ==⨯=,取d=3.0cm由此求得液压缸实际有效面积为:221222222 3.144.515.944 3.14()(5 3.5)8.8344A D cm A D d cm ππ==⨯==-=-=3、液压缸工作循环中各阶段的压、流量及功率计算: (1)、工进时液压缸需要的流量:3Im 1Im 3Im 1Im 15.910015901.59minmin15.9695.40.0954minmin ax axin in cm LQ AV cm LQ AV ==⨯====⨯==(2)、快进时液压缸需要的流量:2121()(15.98.83)4503181.5 3.1815minmin cmLQ A A V =-=-⨯==快进(3)、快退时液压缸的流量:2218.834503973.5 4.0minmin cmLQ A V ==⨯==快退(4)、快进时液压缸的压力:5221121111015715.71015.98.83aF A p n P p cm A A +∆+====⨯--启动52115008.8345268.426.841015.98.83an P p cm +⨯===⨯-加速5215568.8345134.813.481015.98.83a n P p cm +⨯===⨯-恒速(5)、工进时液压缸压力:522114967808.83356.825.681015.9I aF p A n P p cm A ++⨯====⨯(6)、快退液压缸压力:522252521111012612.6108.8315004515.9250.925.09108.835564515.914414.4108.83aaaF p A n P p cm A n P p cm n P p cm ++====⨯+⨯===⨯+⨯===⨯启动加速恒速(7)、快进功率:max 113.48 3.180.071600I P P Q kw⨯===快速恒速(8)、工进功率:Im 135.68 1.590.094600ax P P Q kw⨯===工进工进(9)、快退功率:14.4 4.00.096600P P Q kw ⨯===快退恒速快退行程(行程(行程(0.096四、拟定液压系统1.选择液压回路从工况图可以看出,该系统有如下特点:(1)、系统的流量、压力较小,可以用一个单向泵和溢流阀组成供油源如图a。
铣床液压课程设计

铣床液压课程设计一、课程目标知识目标:1. 理解铣床液压系统的基本原理和组成部分;2. 掌握铣床液压系统的主要参数及其对铣削加工的影响;3. 了解不同铣床液压系统的特点及其适用场景。
技能目标:1. 能够正确操作铣床液压系统,并进行基本的调试和故障排除;2. 能够根据加工需求,合理选择和调整铣床液压系统的参数;3. 能够运用铣床液压系统进行简单的铣削加工,并确保加工质量和效率。
情感态度价值观目标:1. 培养学生对机械加工和液压技术的兴趣,激发学习热情;2. 培养学生严谨的科学态度,注重实践操作的安全性和准确性;3. 培养学生的团队合作意识,学会在铣床液压系统操作中相互协作和沟通。
课程性质:本课程为实践性较强的技术学科,结合铣床液压系统的基础知识和操作技能,培养学生实际应用能力。
学生特点:学生为高年级中职或高职机械类相关专业的学生,具备一定的机械基础知识和动手能力。
教学要求:注重理论与实践相结合,强调操作技能的培养,同时关注学生情感态度价值观的引导。
将课程目标分解为具体的学习成果,以便进行有效的教学设计和评估。
二、教学内容1. 铣床液压系统原理:讲解液压系统的基本工作原理,包括液压泵、液压缸、控制阀等主要组成部分的功能和相互关系。
教材章节:第二章“液压系统基本原理”2. 铣床液压系统参数:学习液压系统的主要参数,如压力、流量、油温等,探讨这些参数对铣削加工的影响。
教材章节:第三章“液压系统参数及其调整”3. 铣床液压系统操作与调试:介绍铣床液压系统的操作方法,包括启动、停止、调整等,以及系统调试的基本步骤和注意事项。
教材章节:第四章“铣床液压系统的操作与维护”4. 铣床液压系统故障排除:分析常见的铣床液压系统故障现象,学习故障诊断和排除方法。
教材章节:第五章“液压系统的故障诊断与排除”5. 铣床液压系统在实际应用中的选择与调整:根据加工需求,指导学生如何选择合适的铣床液压系统,并进行参数调整,以提高加工质量和效率。
专用铣床液压系统设计课程设计
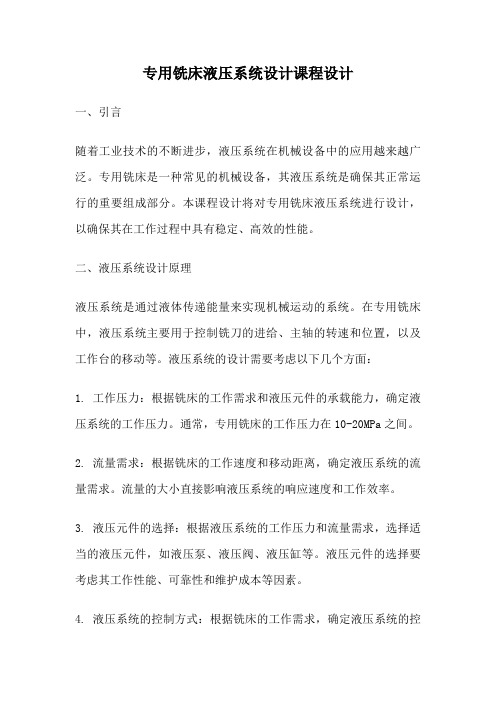
专用铣床液压系统设计课程设计一、引言随着工业技术的不断进步,液压系统在机械设备中的应用越来越广泛。
专用铣床是一种常见的机械设备,其液压系统是确保其正常运行的重要组成部分。
本课程设计将对专用铣床液压系统进行设计,以确保其在工作过程中具有稳定、高效的性能。
二、液压系统设计原理液压系统是通过液体传递能量来实现机械运动的系统。
在专用铣床中,液压系统主要用于控制铣刀的进给、主轴的转速和位置,以及工作台的移动等。
液压系统的设计需要考虑以下几个方面:1. 工作压力:根据铣床的工作需求和液压元件的承载能力,确定液压系统的工作压力。
通常,专用铣床的工作压力在10-20MPa之间。
2. 流量需求:根据铣床的工作速度和移动距离,确定液压系统的流量需求。
流量的大小直接影响液压系统的响应速度和工作效率。
3. 液压元件的选择:根据液压系统的工作压力和流量需求,选择适当的液压元件,如液压泵、液压阀、液压缸等。
液压元件的选择要考虑其工作性能、可靠性和维护成本等因素。
4. 液压系统的控制方式:根据铣床的工作需求,确定液压系统的控制方式。
常见的控制方式有手动控制、自动控制和数控控制等。
三、液压系统设计步骤1. 确定系统要求:根据专用铣床的工作特点和要求,明确液压系统的工作压力、流量需求和控制方式等。
2. 选择液压元件:根据系统要求,选择合适的液压元件。
液压泵的选择要考虑其流量和压力特性;液压阀的选择要考虑其控制特性和可靠性;液压缸的选择要考虑其负载能力和运动特性等。
3. 绘制液压系统图:根据系统要求和液压元件的选择,绘制液压系统图。
液压系统图应包括液压泵、液压阀、液压缸等液压元件的连接关系和管路布置。
4. 计算液压系统参数:根据系统要求和液压元件的特性,计算液压系统的参数,如泵的流量和压力、液压缸的负载和速度等。
5. 设计液压系统控制装置:根据系统要求和控制方式,设计液压系统的控制装置。
控制装置可以采用手动操作、电气控制或计算机控制等方式。
专用铣床的液压系统
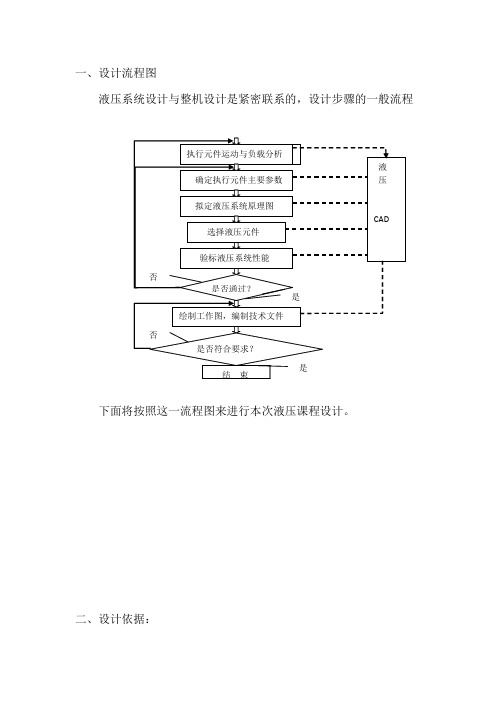
一、设计流程图液压系统设计与整机设计是紧密联系的,设计步骤的一般流程下面将按照这一流程图来进行本次液压课程设计。
二、设计依据:明确液压系统的设计要求 执行元件运动与负载分析 确定执行元件主要参数 拟定液压系统原理图 选择液压元件 验标液压系统性能是否通过?绘制工作图,编制技术文件是否符合要求? 结 束液压 CAD否否是是设计一台专用铣床的液压系统,铣头驱动电机的功率N=7.5KW,铣刀直径为D=100mm,转速为n=300rpm,若工作台重量400kg,工件及夹具最大重量为150kg,工作台总行程L=400mm,工进为100mm,快退,快进速度为5m/min,工进速度为50~1000mm/min,加速、减速时间t=0.05s,工作台用平导轨,静摩擦系数fj=0.2,动摩擦系数fd=0.1。
设计此专用铣床液压系统。
三、工况分析液压系统的工况分析是指对液压执行元件进行运动分析和负载分析,目的是查明每个执行元件在各自工作过程中的流量、压力、功率的变化规律,作为拟定液压系统方案,确定系统主要参数(压力和流量)的依据。
负载分析 (一) 外负载Fw=1000P/V=60000·1000P/ 3.14Dn=4774.65N (二) 阻力负载静摩擦力:Ffj=(G1+G2)·fj其中 Ffj —静摩擦力N G1、G2—工作台及工件的重量N fj —静摩擦系数 由设计依据可得:Ffj=(G1+G2)·fj=(4500+1500)X0.2=1200N 动摩擦力Ffd=(G1+G2)·fd 其中 Ffd —动摩擦力N fd —动摩擦系数同理可得: Ffd=(G1+G2)·fd=(4500+1500)X0.1=600N(三) 惯性负载机床工作部件的总质量m=(G1+G2)/g=6000/9.81=611.6kg惯性力Fm=m ·a==1019.37N其中:a —执行元件加速度 m/s ² 0t u u a t-=ut —执行元件末速度 m/s ² u0—执行元件初速度m/s ²t —执行元件加速时间s因此,执行元件在各动作阶段中负载计算如下表所示: (查液压缸的机械效率为0.96,可计算液压缸各段负载,如下表) 工况 油缸负载(N ) 液压缸负载(N ) 液压缸推力(N ) 启动 F=Ffj 1200 1250 加速 F=Ffd+Fm 1619.37 1686.84 快进 F=Ffd 600 625 工进 F=Ffd+ Fw 5374.65 5598.60 快退F=Ffd600625按上表的数值绘制负载如图所示。
液压与气压传动课程设计-设计一台专用铣床液压系统大学论文

液压与气压传动课程设计说明书专业:机械设计制造及其自动化班级: 13机二学号:姓名:指导教师:常州工学院机械与车辆工程学院2016年1月8日前言液压传动是用液体作为来传递能量的,液压传动有以下优点:易于获得较大的力或力矩,功率重量比大,易于实现往复运动,易于实现较大范围的无级变速,传递运动平稳,可实现快速而且无冲击,与机械传动相比易于布局和操纵,易于防止过载事故,自动润滑、元件寿命较长,易于实现标准化、系列化。
液压传动的基本目的就是用液压介质来传递能量,而液压介质的能量是由其所具有的压力及力流量来表现的。
而所有的基本回路的作用就是控制液压介质的压力和流量,因此液压基本回路的作用就是三个方面:控制压力、控制流量的大小、控制流动的方向。
所以基本回路可以按照这三方面的作用而分成三大类:压力控制回路、流量控制回路、方向控制回路。
液压传动与机械传动,电气传动为当代三大传动形式,是现代发展起来的一门新技术。
《液压与气压传动》课是工科机械类专业的重点课程之一。
既有理论知识学习,又有实际技能训练。
为此,在教学中安排一至二周的课程设计。
该课程设计的目的是:1、综合运用液压传动及其它先修课程的理论知识和生产实际知识,进行液压传动设计实践,从而使这些知识得到进一步的巩固,加深和发展。
2、熟悉和掌握拟定液压传动系统图,液压缸结构设计,液压元件选择以及液压系统的计算的方法。
3、通过课程设计,提高设计、计算、绘图的基本技能,熟悉设计资料和技术手册,培养独立分析问题和解决问题的能力,为今后毕业设计及设计工作打下必要的基础。
目录一任务书 (5)二液压系统设计步骤 (6)1 液压系统的工况分析 (6)2 拟定液压系统原理图 (8)3 液压系统的计算和选择液压元件 (14)3.1 液压缸主要参数的计算 (14)3.2 液压泵的流量、压力的计算和选择泵的规 (17)3.3 液压阀的选择 (19)3.4 确定管道尺寸 (20)3.5 液压油箱容积的确定 (21)4 液压系统验算及技术文件的编制 (22)4.1 压力损失验算和压力阀的调整压力 (22)4.2 系统温升的验算 (25)5 绘制工作图,编制技术文件 (27)三设计体会 (28)四参考文献30任务书设计课题:设计一台专用铣床液压系统。
专业铣床液压系统课程设计

驻马店职业技术学院机电工程系液压传动课程设计设计题目:专用铣床的液压系统设计学生姓名:田瑞娟唐能胜张鹏学号:专业:机电一体化机电三班指导教师:晁红芬2012年6月引言一、设计题目及工况分析1运动参数分析2动力参数分析3液压缸在各阶段的负载及工况图二、计算液压缸尺寸和所需流量1、工作压力的确定2计算液压缸尺寸3、确定液压缸所需的流量三、确定液压系统方案,拟定液压原理图1、确定执行元件的类型2、换向阀确定3、调速方式的选择4、快进转工进的控制方式的选择5、终点转换控制方式的选择6、实现快速运动的供油部分设计四、液压系统工作原理五、液压泵的选择1、计算泵的压力2、计算泵的流量设计题目要求设计一台专用铣床的液压系统。
已知最大切削阻力9×10³N,切削过程要求实现“快进→工进→快退→原位停止”的自动循环。
采用液压缸驱动,工作台的快进速度为⒋5m/min,快进速度与快退速度相等。
进给速度范围为60~1000mm/min,要求无极调速,最大有效行程为400mm,工作台往复运动的加速﹑减速时间为0.5s,工作台自重为3×10³N,工作及夹具最大重量为10³N,采用平导轨,工作行程为200mm。
一工况分析1、运动参数分析动作循环图动作循环图速度循环图2、动力参数分析工作台的快进速度为4。
5m/s,工作进给速度范围为60~1000mm/min,要求无级调速,工作台往复的加速、减速时间为0。
05s,快退速度与快进速度相等。
(1)计算各阶段的负载启动和加速阶段的负载F qF q=Fj+F g+F mF1——静摩擦阻力Fg——惯性阻力Fm ——密封产生的阻力。
按经验可取Fm=0.1F qF q =F j +F g +F m =0.2×4000+ma+0.1F q =800+05.081.9605.44000⨯⨯⨯+0.1F qF q =956.85N快速阶段的负载F kj F kj =F dm +F m F dm ——动摩擦阻力F m ——密封阻力,取F m =0.1F dm F kj =F dm +F m =0.1×4000+0.1F kj F kj =444.44N 减速阶段F js F js =F dm +F m -F gF m ——密封阻力,取F m =0.1F jsF js =F dm +F m -F g =400+0.1F js -4000⨯5.081.960101000-5.43-⨯⨯⨯F js =391.59N④工进阶段F gjF gj =F dm +F qx +F m F qx ——切削力F gj =F dm +F qx +F m =0.1×4000+9000+0.1F gj F gj =10444.44N⑤制动F zdF zd =F m +F dm -F g =0.1×4000+0.1F zd -5.018.96010100040003-⨯⨯⨯⨯F zd =429.34N⑥反向启动F fgdF fgd =F m +F jm +F g =0.2×4000+0.1F fgd -5.018.96010100040003-⨯⨯⨯⨯F fgd =956.85N⑦快速上升F ktF kt =F m +F dm =0.1F kt +400 F kt =444.44N⑧反向制动F fzd =F m +F dm -F g =0.1F fzd +400-5.018.9605.44000⨯⨯⨯F fzd =376.49N3液压缸在各阶段的负载(2)绘制工况图(3)绘制工况图工况图二、计算液压缸尺寸和所需流量1、工作压力的确定工作压力可根据最大负载来确定,最大负载为10444.44N现按表1有关要求,取工作压力P=2.5MPa表1负载F/kN<55~1010~2020~3030~50>50工作压力0.8~1 1.5~2 2.5~33~44~5≥5~7p/MPa12、计算液压缸尺寸1)液压缸的有效面积A11A =ηP F =2646419.0105.244.10444mm ≈⨯⨯ 液压缸内径D D=mm 89.7614.346414A 41=⨯=π根据第4章有关要求取标准值D=80mm (表格如下)液压缸内径尺寸系列 mm(2)活塞杆直径要求快进与快退的速度相等,故用差动连接的方式。
专用铣床液压系统设计课程设计

专用铣床液压系统设计课程设计引言:专用铣床液压系统设计是现代工程领域中一门重要的课程。
液压系统在工业生产中起着至关重要的作用,而专用铣床液压系统则是在铣床加工过程中用于控制和驱动铣刀、工作台等部件的关键系统。
本文将介绍专用铣床液压系统的设计过程和原理,并提供一些设计方案和注意事项。
一、液压系统的基本原理液压系统利用液体传递力和能量,实现机械设备的控制和驱动。
液压系统由液压泵、液压缸、液压阀和液压管路等组成。
液压泵通过机械能转化为液体压力能,液压阀控制液体的流动方向和流量,液压缸则将液体的压力能转化为机械能。
二、专用铣床液压系统设计的基本要求1. 功能要求:液压系统应能够实现铣床的各种操作,如起动、加工和停止等。
2. 系统稳定性:系统在工作过程中应具有较高的稳定性和可靠性,能够保证加工精度和加工质量。
3. 控制灵活性:液压系统应具备灵活的控制能力,能够满足不同加工工件的需求。
4. 安全性:液压系统设计应考虑到安全因素,如过载保护、漏油报警等。
5. 经济性:液压系统的设计应尽可能降低成本,并提高能源利用效率。
三、专用铣床液压系统设计的步骤1. 确定系统的工作压力和流量:根据铣床的加工要求和工作负荷,确定液压系统的工作压力和流量。
同时要考虑系统的泄漏和能量损失。
2. 选择液压元件:根据系统的工作压力、流量和控制要求,选择合适的液压泵、液压缸、液压阀等元件。
要考虑到元件的质量、可靠性和维修方便性。
3. 设计液压回路:根据铣床的工作过程和控制要求,设计合适的液压回路。
液压回路的设计应考虑到系统的稳定性、控制灵活性和安全性。
4. 设计液压管路:根据液压回路的设计,设计合适的液压管路。
液压管路的设计应考虑到管路的阻力、泄漏和安装方便性。
5. 进行系统的仿真和优化:通过液压系统仿真软件对系统的性能进行评估和优化,以确保系统的稳定性和可靠性。
6. 进行系统的实验验证:根据设计结果,进行液压系统的实验验证。
通过实验数据的分析和对比,评估系统的性能和可靠性。
专用铣床液压系统的设计

20** 届毕业设计(论文)材料系、部:学生姓名:指导教师:职称:专业:班级:学号:20**年05月20**届毕业设计(论文)课题任务书系:机械工程系专业:机械制造与自动化20**届毕业设计说明书专用铣床液压系统设计系、部:学生姓名:指导教师:职称专业:班级:完成时间:摘要1.铣床概述铣床是用铣刀对工件进行铣削加工的机床。
铣床除能铣削平面、沟槽、轮齿、螺纹和花键轴外,还能加工比较复杂的型面,效率较刨床高,在机械制造和修理部门得到广泛应用。
2.液压技术发展趋势液压技术是实现现代化传动与控制的关键技术之一,世界各国对液压工业的发展都给予很大重视。
液压气动技术具有独特的优点,如:液压技术具有功率传动比大,体积小,频响高,压力、流量可控性好,可柔性传送动力,易实现直线运动等优点;气动传动具有节能、无污染、低成本、安全可靠、结构简单等优点,并易与微电子、电气技术相结合,形成自动控制系统。
主要发展趋势如下:1.减少损耗,充分利用能量2.泄漏控制3.污染控制4.主动维护5.机电一体化6.液压CAD技术7.新材料、新工艺的应用3. 主要设计内容本设计是设计专用铣床工作台进给液压系统,本机床是一种适用于小型工件作大批量生产的专用机床。
可用端面铣刀,园柱铣刀、园片及各种成型铣刀加工各种类型的小型工件。
设计选择了组成该液压系统的基本液压回路、液压元件,进行了液压系统稳定性校核,绘制了液压系统图,并进行了液压缸的设计。
关键词铣床;液压技术;液压系统;液压缸ABSTRACT1. Milling machine is general to stateMilling machine is to carry out the machine tool of milling processing with milling cutter for workpiece. Milling machine excludes can milling plane, groove, gear teeth, thread and spline axle are outside, can still process more complex type surface, efficiency has high planer comparatively, when mechanical production and repair department get extensive application.2. Hydraulic technology develops tendencyHydraulic technology is that the one of crucial technical, world countries that realize modern transmission and control give great attention to the development of hydraulic industry. Hydraulic pneumatic technology has unique advantage , such as: Hydraulic technology has power weight than is big, volume is little, frequently loud and high, pressure and rate of flow may control sex well, it may be flexible to deliver power , is easy to realize the advantages such as the sport of straight line; Pneumatic transmission has energy saving, free from contamination, low cost and safe reliable, structural simple etc. advantage , and is easy to form automatic control system with microelectronics and electric in technology. Develop tendency mainly to be as follows:1. Reduce wastage , use energy2 fully. Leak control3. Pollute control4. Defend5 initiatively. Electromechanical unifinication6. Hydraulic CAD technical7. The application of new material and new technology3. Design content mainlyQuantity of production. May use the garden column milling cutter, garden flat and milling cutter of end panel and is various to process the small-sized workpiece of various types into type milling cutter.Designing have selected to form hydraulic element and the basically hydraulic loop of this hydraulic system , have carried out hydraulic systematic stability school nucleus , have drawn hydraulic system to seek , and have carried out the design of hydraulic big jar.Key words milling machine;hydraulic technology;hydraulic system;hydraulic big jar目录摘要 2 毕业设计任务书 5 第一章专用铣床液压系统设计 7 1.1 技术要求 7 1.2 系统功能设计 71.2.1 工况分析 71.2.2 确定主要参数,绘制工况图 81.2.3 拟定液压系统原理图 101.2.4 组成液压系统 10 1.3系统液压元件、辅件设计12 第二章专用铣床液压系统中液压缸的设计17 2.1 液压缸主要尺寸的确定 17 2.2 液压缸的结构设计 20 致谢24 参考文献 25毕业设计任务书一、设计课题专用铣床液压系统设计二、设计依据某铣床工作台为卧式布置(导轨为水平导轨,其静、动摩擦因数µs=0.2;µd=0.1),拟采用缸筒固定的液压缸驱动工作台,完成工件铣削加工时的进给运动;工件采用机械方式夹紧。
专用铣床液压传动系统设计

毕业设计(论文)专用铣床液压系统设计Special milling machine hydraulic system design系名:专业班级:学生姓名:学号:指导教师姓名:指导教师职称:二○**年六月任务书目录引言 (6)第一章概述 (7)1.1 设计的目的 (7)1.2 设计的要求 (7)1.3 设计题目 (8)第二章工况分析 (9)2.1 工作负载 (9)2.2 摩擦阻力 (9)2.3 惯性负载 (9)第三章绘制负载图、速度图和动作循环图 (11)第四章初步确定液压缸的参数 (13)4.1初步确定液压缸的参数 (13)4.2 计算液压缸的尺寸 (13)4.3 液压缸工况 (13)第五章拟定液压原理图 (16)5.1选择液压基本回路 (16)5.2 组成系统图 (18)第六章选择液压元件 (20)6.1液压传动系统 (20)6.2 液压装置的结构设计,绘制工作图及编译技术文件 (20)6.3 液压传动系统参数及元件选择 (20)6.4 确定系统工作压力 (21)6.5执行元件控制方案拟定 (21)6.6确定执行元件的主要参数 (21)6.7确定液压泵的工作压力和流量计算 (22)6.8控制阀的选择 (22)6.9确定油箱直径 (22)第七章液压系统的性能验算 (23)结论 (25)致谢 (26)参考文献: (27)专用铣床液压系统设计摘要液压系统是以电机提供动力基础,使用液压泵将机械能转化为压力,推动液压油。
通过控制各种阀门改变液压油的流向,从而推动液压缸做出不同行程、不同方向的动作。
完成各种设备不同的动作需要。
液压系统已经在各个工业部门及农林牧渔等许多部门得到愈来愈广泛的应用,而且愈先进的设备,其应用液压系统的部分就愈多。
所以像我们这样的大学生学习和亲手设计一个简单的液压系统是非常有意义的。
关键词液压传动、稳定性、液压系统Special milling machine hydraulic system designAbstract The special milling machines, hydraulic system design in the design programme and the hydraulic system shall be able to finish the work into fast forward, and backed out when the milling machine architecture to understand and grasp for the hydraulic knowledge on the basis of from a given conditions, and the value analysis of the theory with practice, the work of drawing in autocad software diagram of the hydraulic system, the principle of the assembly drawing and analyzing the parts, the process, Set down to a time too short, the time of the short, at the start of the larger, slow down a short time will result in oscillatory too much, so damage to equipment, make failure of the jug, the main argument is based on innovation innovation power, the motor drivers head first, revolution speed and work in the process of the maximum load and the itinerary for design calculations.Friction factor is also a need to think of it. although friction of the relatively small, but will also be affected. the design of the difficulty is mainly the principle of the analysis and design purpose is to achieve appropriate control, and to choose a relative rationality, high precision, economically affordable hydraulic components, and design talents widely used.Key words hydraulic transmission, control system, hydraulic system.引言目前,随着电子、信息等高新技术的不断发展及市场需求个性化与多样化,世界各国都把机械制造技术的研究和开发作为国家的关键技术进行优先发展,将其他学科的高技术成果引入机械制造业中。
半自动液压专用铣床液压系统课程设计精选全文完整版

可编辑修改精选全文完整版液压系统设计半自动液压专用铣床液压系统1.设计要求设计一台用成型铣刀在加工件上加工出成型面的液压专用铣床,工作循环:手工上料——自动夹紧——工作台快进——铣削进给——工作台快退——夹具松开——手工卸料。
2.设计参数设计参数见表11和表12。
其中:工作台液压缸负载力(KN):FL=2.2夹紧液压缸负载力(KN):Fc= 4.8工作台液压缸移动件重力(KN):G=3.5夹紧液压缸负移动件重力(N)G c=30 工作台快进、快退速度(m/min):V1=V3 =5.5夹紧液压缸行程(mm):L c=10工作台工进速度(mm/min):V2=55 夹紧液压缸运动时间(S):t c=1工作台液压缸快进行程(mm):L1=450导轨面静摩擦系数:μs=0.2工作台液压缸工进行程(mm):L2=80导轨面动摩擦系数:μd=0.1工作台启动时间(S)t=0.53.完成工作量液压系统原理图(A3);零件图和部件装配图各1张(A3);设计说明书1份,零部件目录表1份。
注:在进行零部件设计时,集成块和油箱部件可以任选。
表一〈一〉工况分析:1.运动参数分析根据主机要求画出动作循环图,然后根据动作循环图和速度要求画出速度与路程的工况图。
夹紧松开2.动力参数分析(1)计算各阶段的负载1.启动和加速阶段的负载Fq从静止到快速的启动时间很短,故以加速过程进行计算,但摩擦阻力仍按静摩擦阻力考虑。
F q =Fj+Fi+Fm其中Fm=0.1FqFq = Fj+Fg+FmFq=850N2.快速阶段的负载FkF k =Fdm+Fm=0.1×3500+0.1FkFk=389N3.工进阶段的负载FgjFgj = Fdm+ Fl+ Fm=0.1X3500+2200+85 =2833N4.快退阶段的负载FktFkt =Fk=388.89N5.夹紧缸最大夹紧力FmaxFmax =Fc+UsGc+Gc/gXLc/tc2+0.1Fmax=5340N6.夹紧缸最小夹紧力FminFmin = Fc+UdGc+Gc/gXLc/tc2+0.1Fmin=5337N速度与路程的工况图:负载与路程的工况图:表二液压缸负载与工作压力之间的关系:表三液压缸内径尺寸系列:(mm)表四活塞杆直径尺寸系列:(mm)〈二〉计算液压缸尺寸和所需流量:1.工作压力的确定,查表二,取工作压力P=1MPa 2.计算液压缸尺寸(1)液压缸的有效工作面积A1A1=FP=28331000000=2833(mm2)液压缸内径:D=(4A1/π)1/2=60(mm)查表三,取标准值D=63mm(2)活塞杆直径:要求快进与快退的速度相等,故用差动连接方式,所以,取d=0.7D=44.1mm,查表四,取标准值d=45mm。
专业铣床液压系统课程设计

专业铣床液压系统课程设计一、课程目标知识目标:1. 让学生掌握铣床液压系统的基本原理和组成部分,理解各部件的功能和相互关系。
2. 使学生了解液压系统在铣床操作中的应用,掌握液压系统的操作方法和注意事项。
3. 帮助学生理解液压系统的故障分析与维护方法,提高实际操作能力。
技能目标:1. 培养学生运用所学知识,分析并解决铣床液压系统实际问题的能力。
2. 提高学生实际操作铣床液压系统的技能,熟练掌握各项操作要领。
3. 培养学生团队合作意识,学会在团队中分工协作,共同完成液压系统的安装、调试和维护。
情感态度价值观目标:1. 培养学生对机械加工行业的热爱,激发学习兴趣,树立正确的职业观念。
2. 引导学生树立安全意识,注重操作规范,养成良好的操作习惯。
3. 培养学生勇于探索、积极进取的精神风貌,面对液压系统故障时,敢于挑战,善于解决问题。
课程性质:本课程为专业实践课程,注重理论知识与实际操作相结合,以培养学生的实际操作能力和解决实际问题的能力为主要目标。
学生特点:学生已具备一定的机械基础知识,对铣床操作有初步了解,但对液压系统知识掌握有限,需要结合实际操作进行深入学习。
教学要求:教师需采用理论讲解、案例分析、实际操作相结合的教学方法,注重引导学生主动参与,提高学生的实践操作能力。
同时,加强对学生的个别辅导,确保课程目标的达成。
二、教学内容1. 液压系统基础知识:介绍液压系统的基本原理、组成部分及其功能,包括液压泵、液压缸、液压阀、油箱、管路等。
教材章节:第二章 液压系统基础知识2. 铣床液压系统组成与工作原理:分析铣床液压系统的具体组成,讲解其工作原理及在铣床操作中的应用。
教材章节:第三章 铣床液压系统组成与工作原理3. 液压系统操作与维护:详细介绍液压系统的操作方法、注意事项,以及日常维护和故障排除方法。
教材章节:第四章 液压系统操作与维护4. 液压系统故障分析与处理:结合实际案例,分析液压系统常见故障及其原因,讲解故障处理方法。
哈工大液压传动课程大作业-动力滑台-铣床液压系统设计
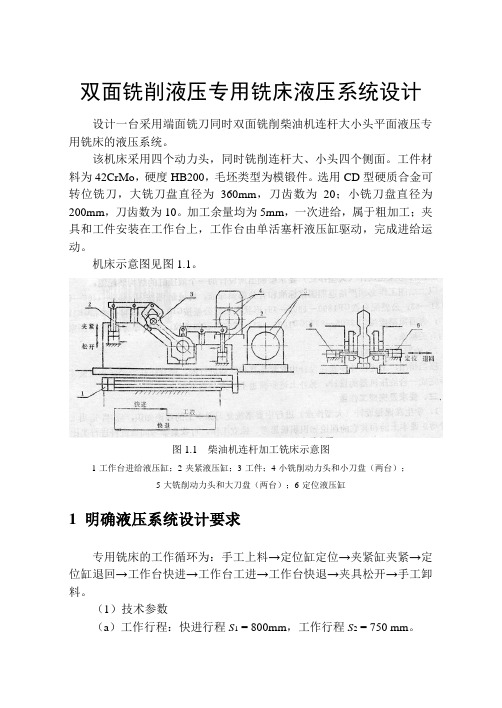
双面铣削液压专用铣床液压系统设计设计一台采用端面铣刀同时双面铣削柴油机连杆大小头平面液压专用铣床的液压系统。
该机床采用四个动力头,同时铣削连杆大、小头四个侧面。
工件材料为42CrMo,硬度HB200,毛坯类型为模锻件。
选用CD型硬质合金可转位铣刀,大铣刀盘直径为360mm,刀齿数为20;小铣刀盘直径为200mm,刀齿数为10。
加工余量均为5mm,一次进给,属于粗加工;夹具和工件安装在工作台上,工作台由单活塞杆液压缸驱动,完成进给运动。
机床示意图见图1.1。
图1.1 柴油机连杆加工铣床示意图1-工作台进给液压缸;2-夹紧液压缸;3-工件;4-小铣削动力头和小刀盘(两台);5-大铣削动力头和大刀盘(两台);6-定位液压缸1 明确液压系统设计要求专用铣床的工作循环为:手工上料→定位缸定位→夹紧缸夹紧→定位缸退回→工作台快进→工作台工进→工作台快退→夹具松开→手工卸料。
(1)技术参数(a)工作行程:快进行程S1 = 800mm,工作行程S2 = 750 mm。
(b)工作台轴向切削力:工作行程I(0~400 mm范围内),F t1 = 8400N (大小铣刀盘同时铣削);工作行程II(400~750 mm范围内),F t2 = 3600N (仅小铣刀盘铣削)。
(c)垂直于工作台导轨的切削分力:工作行程I,F n1 = 19000N,工作行程II,F n2 = 8000N(d)工作台运动部件质量:m = 1361kg(e)工作台快进、快退速度:v1 = v3 =400 mm/min(f)工作台工作速度:v2 = 40~80 mm/min可调(g)工作台导轨型式及摩擦系数:平导轨:静摩擦系数f s = 0.2,动摩擦系数f d = 0.1(h)工作台加速减速时间:∆t ≤ 0.2s(i)夹紧缸负载力:F c = 4000N(j)夹紧时间:t c =(1~2)s(k)夹紧缸行程:S c = 20 mm(l)定位缸负载力:F s = 500N(m)定位缸行程:S s = 100 mm(时间<5s)(n)上、卸料时间:t s = 30s(2)设计要求(a)由于切削时切削力有脉动,要求进给速度随负载的变化小。
专用铣床动力滑台液压系统设计

专用铣床动力滑台液压系统设计目录前言.........................................................................................................错误!未定义书签。
目录 (1)一、液压传动的发展概况 (2)二、液压传动的工作原理和组成 (3)三、液压传动的优缺点 (4)1、优点 (4)2、液压传动的缺点: (4)四、液压系统的应用领域 (5)1、液压传动在机械行业中的应用: (5)2、静液压传动装置的应用 (5)五、液压系统工况分析 (7)1、运动分析...................................................................................错误!未定义书签。
七、拟定液压系统图 (21)1、调速方式的选择 (21)2、快速回路和速度换接方式的选择 (22)液压工作原理: (23)八、液压元件选择 (25)1、选择液压泵和电机 (25)2、元、辅件的选择 (29)九、液压系统验算 (32)1.管路系统压力损失验算 (32)2、液压系统的发热与温升验算 (35)十、液压系统最新发展状况 (37)1、国外液压系统的发展 (32)2、远程液压传动系统的发展 (38)十一、注意事项 (40)十二、总结 (41)致谢 (42)参考文献 (43)一、液压传动的发展概况液压传动和气压传动称为流体传动,是根据17世纪帕斯卡提出的液体静压力传动原理而发展起来的一门新兴技术,是工农业生产中广为应用的一门技术。
如今,流体传动技术水平的高低已成为一个国家工业发展水平的重要标志。
第一个使用液压原理的是1795年英国约瑟夫·布拉曼(JosephBraman,1749-1814),在伦敦用水作为工作介质,以水压机的形式将其应用于工业上,诞生了世界上第一台水压机。
专用铣床液压系统设计

目录引言 (3)第一章设计任务及工况分析1.1 设计任务 (4)1.2 工况分析并初步确定液压缸参数 (4)1.2.1 负载分析及绘制负载图和速度图 (4)1.2 .2初步确定液压缸参数及绘制工况图 (7)第二章拟定液压系统原理图2.1 选择基本回路 (12)2.2 组成液压系统 (15)第三章液压系统计算与选择液压元件3.1液压泵、电机计算和选择 (18)3.2选择液压阀 (19)3.3选择辅助元件 (19)结论 (21)致谢 (22)参考文献 (23)专用铣床液压系统设计摘要:液压系统是以电机提供动力基础,使用液压泵将机械能转化为压力,推动液压油。
通过控制各种阀门改变液压油的流向,从而推动液压缸做出不同行程、不同方向的动作。
完成各种设备不同的动作需要。
液压系统已经在各个工业部门及农林牧渔等许多部门得到愈来愈广泛的应用,而且愈先进的设备,其应用液压系统的部分就愈多。
所以像我们这样的大学生学习和亲手设计一个简单的液压系统是非常有意义的。
本文首先介绍了液压的作用和工况分析,其次确定液压缸尺寸,然后进行了工艺规程设计。
关键词:工况分析液压元件设计液压缸设计Special Milling Machine Hydraulic System DesignAbstract Hydraulic system is powered motor basis, the use of hydraulic pump will translate into pressure on the mechanical energy, promote the hydraulic oil. Through various control valves to change the flow of hydraulic oil, thus promoting the hydraulic cylinders made of different itinerary, the movements in different directions. All kinds of different equipment to complete the actions required. Hydraulic system has been in various industrial sectors and agriculture, forestry, animal husbandry and fisheries, and many other departments are more widely used, and more advanced equipment, its application on the part of the hydraulic system more. So students like us to study and personally designed a simple hydraulic system is very meaningful.Key words: hydraulic transmission, control system, hydraulic system引言液压传动与机械传动、电气传动相比具有许多特殊优点,其应用已涉及二十多个专业领域的不同场合。
液压设计论文-专用铣床液压系统设计

学生课程设计(论文)题目:液压课程设计(论文)专用铣床液压系统设计学生姓名:学号:所在院(系):专业:班级:指导教师:职称:二〇一〇年六月二十五日**教务处制本科学生课程设计任务书注:任务书由指导教师填写。
摘要现代机械一般多是机械、电气、液压三者紧密联系,结合的一个综合体。
液压传动与机械传动、电气传动并列为三大传统形式,液压传动系统的设计在现代机械的设计工作中占有重要的地位。
因此,《液压传动》课程是工科机械类各专业都开设的一门重要课程。
它既是一门理论课,也与生产实际有着密切的联系。
为了学好这样一门重要课程,除了在教学中系统讲授以外,还应设置课程设计教学环节,使学生理论联系实际,掌握液压传动系统设计的技能和方法。
液压传动课程设计的目的主要有以下几点:1、综合运用液压传动课程及其他有关先修课程的理论知识和生产实际只是,进行液压传动设计实践,是理论知识和生产实践机密结合起来,从而使这些知识得到进一步的巩固、加深提高和扩展。
2、在设计实践中学习和掌握通用液压元件,尤其是各类标准元件的选用原则和回路的组合方法,培养设计技能,提高学生分析和嫁接生产实际问题的能力,为今后的设计工作打下良好的基础。
3、通过设计,学生应在计算、绘图、运用和熟悉设计资料(包括设计手册、产品样本、标准和规范)以及进行估算方面得到实际训练。
关键词现代机械,液压传动系统,液压传动课程设计ABSTRACTModern machinery is generally more mechanical, electrical, hydraulic three closely linked, combined with a complex. Hydraulic and mechanical drive, electrical drive listed as the three traditional forms, the design of hydraulic system design in modern machinery occupies an important position. Therefore, the "hydraulic transmission" program is the professional engineering machinery set up an all important course. It is a theory course, also closely linked to actual production. To learn that an important course, in addition to teaching in teaching the system outside the teaching process should be to set curriculum to enable students to integrate theory with practice, master the hydraulic system design skills and methods.Hydraulic transmission program is designed to mainly the following:1, integrated use of hydraulic transmission programs and other pre-production of curriculum theory and practice is to conduct hydraulic design practice, is the theoretical knowledge and practical production secrets combine to make this knowledge be further consolidated and deepened to improve and expand .2, in the design of learning and master the common hydraulic components, in particular the selection of components of various Biaozhun principles and loop combination method Pei Yang design skills, improve student Fenxi and graft Shengchan practical problems, for the future design lay a sound basis.3, by design, students should be in the computing, graphics, and familiar with the use of design information (including design manuals, product samples, standards and specifications) as well as estimates for the practical training.Keywords modern machinery, hydraulic system, hydraulic drive course design目录摘要 (I)ABSTRACT (II)1 设计方案拟定 (1)1.1方案分析 (1)1.2方案确定 (2)2 负载分析计算 (3)2.1负载分析 (3)2.2负载图和速度图的绘制 (3)3 液压缸主要参数的确定 (5)3.1初选液压缸的工作压力 (5)3.2确定液压缸的尺寸 (5)3.3绘制液压缸工况图 (6)4液压系统图的拟定 (7)4.1液压回路的选择 (7)4.1.1调速回路 (7)4.1.2换向回路和卸荷回路 (7)4.1.3快速运动回路 (8)4.1.4压力控制回路 (8)4.2液压系统合成 (9)5 液压元件的选择 (12)5.1液压泵和驱动电机 (12)5.2阀类元件及辅助元件 (12)5.3油管 (13)5.4油箱 (14)5.4.1邮箱总体尺寸设计 (14)5.4.2各种油管的尺寸 (15)5.4.3吸油管和过滤器之间管接头的选择 (16)5.4.4过滤器的选择 (16)5.4.5堵塞的选取 (16)5.4.6空气过滤器的选取 (16)5.4.7液位/温度计的选取 (17)5.4.8油箱内隔板及除气网的设置 (17)6 液压系统性能的验算 (18)6.1回路中压力损失 (18)6.1.1快进时压力损失 (18)6.1.2工进时压力损失 (18)6.1.3快退时压力损失 (19)6.2油液温升验算 (20)参考文献 (22)致谢 (23)1 设计方案的拟定题目:专用铣床液压系统设计设计一台专用铣床,铣头驱动电机的功率为7.0千瓦,铣刀直径为120mm ,转速350转/分,如工作台质量为480公斤,工件和夹具最大质量为150公斤,工作台行程为400mm ,工进行程为100mm ,快进快退速度为4.5米/分,工进速度为60~1000毫米/分,其往复运动的加速(减速)时间为0.05秒,工作台用平导轨静摩擦系数0.2s f =,动摩擦系数0.1d f =,试设计该机床的液压系统。
专用铣床床液压系统

• •
液压传动系统由哪几部分组成? 液压?简述如何避免?
•什么是液压泵的排量?流量? •如何计算泵的实际输出功率?驱动液压泵的电动机的功率? •液压缸的功用?种类? •什么是差动连接,应用场合? •比较普通单向阀和液控单向阀的区别。 •减压阀与溢流阀的主要区别是什么?
•顺序阀与溢流阀的主要区别是什么
•蓄能器的作用? •常用油管有哪几种,它们的适用范围有何不同。 •什么是平衡回路? •简述卸荷回路的作用? •调速回路的类型和调速方法? •进油路节流调速回路的特点? •如何计算执行元件的运动速度? •如何计算系统的压力?
如图所示液压系统,已知液压缸有效工作面积A1=A2=100cm2, 缸1负载 F=35000N,缸2运动时负载为0。不计压力损失,溢流 阀、顺序阀和减压阀的调定压力分别为4MPa、3MPa和2MPa。求 下列工况下A、B、C处的压力: (1) 液压泵启动后,两换向阀处于中位; (2) 1YA通电,液压缸1活塞运动时及运动到终点时。
(1) 说明各元件的名称和作用。 (2) 画出系统能完成的工作循环图, 判断各阶段的油路走向。 (3) 绘制电磁铁动作顺序表。 (4) 说明系统由哪些基本回路组成。
(1) 元件A ___阀,作用___;元件B ___ 阀,作用___;元件C ___阀,作 用__、元件D ___阀,作用__。 (2) 该系统的缸3、缸4 的动作顺序 ____。
如图所示,当电磁铁全部通电或全部断电时泵的供油压力是多少?
1.三位四通中位机能为“O”型 电液动换向阀; 2.液控单向阀; 3.二位三通电磁换向阀(弹簧复 位式); 4.双向变量马达; 5.先导式减压阀; 6.调速阀; 7.粗滤器; 8.先导式顺序阀; 9.蓄能器; 10.单向变量泵; 11.直动式溢流阀; 12.差动液压缸; 13、压力表; 14、压力继电器 15.单向变量马达。
- 1、下载文档前请自行甄别文档内容的完整性,平台不提供额外的编辑、内容补充、找答案等附加服务。
- 2、"仅部分预览"的文档,不可在线预览部分如存在完整性等问题,可反馈申请退款(可完整预览的文档不适用该条件!)。
- 3、如文档侵犯您的权益,请联系客服反馈,我们会尽快为您处理(人工客服工作时间:9:00-18:30)。
一台专用铣床的铣头驱动电机的功率N= 7.5KW ,铣刀直径D=120mm,转速n=350rpm,工作台重量G1=4000N,工件及夹具重量G2=1500N,工作台行程L=400mm,(快进300mm,工进100mm)快进速度为4.5m/min,工金速度为60~1000mm/min,其往复运动和加速(减速)时间t=0.05s,工作台用平导轨,静摩擦系数fs=0.2,动摩擦系数fd=0.1。
设计其液压控制系统。
二.负载——工况分析
1. 工作负载
2. 摩擦阻力
3. 惯性负荷
查液压缸的机械效率
0.9
cm
η=,可计算出液压缸在各工作阶段的负载情况,如下表表1
所示:
表1 液压缸各阶段的负载情况
三.绘制负载图和速度图
根据工况负载和以知速度1v 和2v
及行程S ,可绘制负载图和速度图,如下图(图1、图
2)所示:
图1(负载图)
图2(速度图)
四.初步确定液压缸的参数
1. 初选液压缸的工作压力。
查各类液压设备常用工作压力初选,
2.计算液压缸尺寸。
选用差动液压缸,无杆腔与有杆腔的有效面积为12
2A A =;回油路上有背压阀或调压阀,
取背压
52810p Pa
=⨯;回油管路压力损失
5
510p Pa ∆=⨯。
按JB2183—77取标准值 D=50mm
活塞杆的直径d 为:0.70.75035d D mm ==⨯=
由此求得液压缸的实际有效工作面积
3.液压缸工作循环中各阶段的压力、流量和功率的计算值如下表2所示:
表2 液压缸所需的实际流量、压力和功率
4.液压缸的工况分析
选择调速回路由图1可知,这台机床液压系统功率较小,滑台运动速度低,工作负载为阻力负载且工作中变化小,故可选用进口节流调速回路。
为防止铣完工作时负载突然消失引起运动部件前冲,在回油路上加被压阀。
由于系统选用节流调速方式,系统必然为开式循环系统。
(1)选择油源形式从工况图可以清楚看出,在工作循环内,液压缸要求油源提供快进、快退行程的低压大流量和工进行程的高压小流量的油液。
最大流量与最小流量之比=0.4/(1.58×10-2)≈25:其相应的时间之比
(t
1+t
2
)/t
2
=(3.3+5.3)/90=0.096。
这表明在一个工作循环中的大部分时间都处于
高压小流量工作。
从提高系统效率、节省能量角度看来,选用单定量泵油源显然是不合理的,为此可选用限压式变量泵或双联叶片泵作为油源。
考虑到前者流量突变时液压冲击较大,工作平稳性差,且后者可双泵同时向液压缸供油实现快速运动,最后确定选用双联叶片泵方案。
(2)选择快速运动和换向回路本系统已选择液压缸差动连接和双泵供油两种快速运动回路实现快速运动。
考虑到从工进转快退时回油路流量较大,故选用换向时间可调的电液换向阀式换向回路,以减小液压冲击。
由于要实现液压缸差动连接,所以选用三位五通电液换向阀。
(3)选择速度换接回路由于本系统滑台由快进转为工进时,速度变化大
(v
1/v
2
=4.5/0.1≈45),为减少速度换接时的液压冲击,选用行程阀控制的换接回
路。
(4)选择调压和卸荷回路在双泵供油的油源形式确定后,调压和卸荷问题都
已基本解决。
即滑台工进时,高压小流量泵的出口压力由油源中的溢流阀调定,无需另调压回路。
在滑台工进和停止时,低压大流量泵通过夜空顺序阀卸荷,高压小流量泵在滑台停止时虽未卸荷,但功率损失较小,故可不需要再设卸荷回路。
图3 整理后的液压系统原理图
将上面选出的液压基本回路组合在一起,并修改和完善,就可得到完整的液压系统工作原理,如图3所示。
在图3中,为了解决滑台工进时进、回油路串通使系统压力无法建立的问题,增设了单向阀6。
为了避免机床停止工作时回路中的油液流回油箱,导致空气进入系统,影响滑台运动的平稳性,图中添置了一个单向阀13。
图中增设了一个压力继电器14。
当滑台碰上死挡块后,系统压力升高,它发出快退信号,操纵电液换向阀换向。
(四)计算和选择液压件
1. 确定液压泵的规格和电动机功率
(1)计算液压泵的最大工作压力
小流量泵在快进和工进时都向液压缸供油,由表7可知,液压缸在工进时工作压力最大,最大工作压力为p1=3.86MPa,如在调速阀进口节流阀调速回路中,选取进油路上的总压力损失∑△p=0.6 MPa,考虑到压力继电器的可靠动作要求压差△p e=0.5MPa,则小流量泵的最高压力估算为
≧p
+∑△p+△=3.86+0.6+0.5=4.96 MPa
1
大流量泵只在快进和快退时向液压缸供油,由表7可见,快退时液压缸的工作压力为,比快进时大,考虑到快退时进油不通过调速阀,故其进油路压力损失
比前者小,现取进油路上的总压力损失,则大流量泵的最高工作压力估算为(2)计算液压泵的流量
由表7可知,油源向液压缸输入的最大流量为0.3,若取回油泄漏系数,则两个泵的总流量为
≧K=1.1×0.4×=0.44×=26.4L/min
考虑到溢流阀的最小稳定流量为3L/min,工进时流量为1.58× __D_Dd,则小流量泵的流量最少应为3.96L/min。
(3)确定液压泵的规格和电动机功率
根据以上压力和流量数值查阅产品样本,并考虑液压泵存在容积损失,最后确定选取PV2R12-6/33型双联叶片泵。
其小流量泵和大流量泵的排量分别为6Ml/r和33mL/r,当液压泵的转速时,其理论流量分别为5.6L/min和31L/mL/r,若取液压泵容积效率 ____D_Dd__
=(6×940×0.9/1000+33×940×0.9/1000)L/min
=(5.1+27.9) L/min=33 L/min
由于液压缸在快退时输入功率最大,若取液压缸总效率,这时液压泵的驱动
电动机功率为P≥=KW=1.19KW
根据此数值查阅产品样本,选用规格相近的Y100L-6型电动机,其额定功率为1.5KW,额定转速为940r/min。
五.拟定液压系统图
1.选择液压基本回路
从工况图可知:该系统的流量、压力较小,可选用定量泵和溢流阀组成的供油源,如图a所示。
铣床加工有顺锉和逆锉之分,宜采用出口节流调速,具有承受负切削的能力,如图b所示。
考虑到工作进给时负载大、速度低,而快进、快退行程中负载小、速度快,所以采用由换向阀联通的差动快速回路,如图c所示。
根据一般专用铣床的要求不高,采用电磁阀的快慢换接回路,其特点是结构简单。
选用简便的电气行程开关和挡铁控制行程方式。
为了实现工作台快退选用具单向阀的调速阀,图4为所设计的液压系统图。
六.选择液压元件
1.确定液压泵的容量及电动机功率
(1)液压泵的工作压力和流量计算。
进油路的压力损失取
5
310
p Pa
∆=⨯,回路泄露系数取 1.1
K=,则液压泵的最高
工作压力和流量为:
根据上述计算数据查泵的产品目录,选用YB-6型定量叶片泵。
(2)确定驱动电动机功率。
由工况图表明,最大功率出现在快退阶段,液压泵总
效率η=0.75,则电动机功率为:
2.控制阀的选择
根据泵的工作压力和通过各阀的实际流量,选取各元件规格,如表3所示。
格表3 各元件的规格
3.确定油管直径
进出液压缸无杆腔的流量,在快退和差动工况时为2Q ,所以管道流量Q 按
12/min L 计算。
取压油管流速3/v m s =
9.22d mm ≥==,取内径为10mm 的管道。
吸油管的流速1/v m s =,通过流量为6/min L ,则
11.29d mm ≥=,取内径为12mm 管道。
确定管道尺寸应与选定的液压元件接口处的尺寸一致。
4.确定油箱容积。