连铸坯表面裂纹形成及防止理化中心演示文稿
连铸坯表面裂纹形成及防止分析

浸入式水口对中,防止偏流 合理的浸入式水口设计(合适的出口直径,倾角) 合适的水口插入深度 合适的频率和振幅
(3) 结晶器振动
2 铸坯表面纵裂纹
(4) 出结晶器铸坯运行 二次冷却均匀性 (5) 调整钢水成分 钢中碳含量避开包晶区,C向下线或上线控制 钢中S<0.015% 残余元素Cu、As、Zn控制<0.1%
图2-4 拉速对纵裂纹的影响
2 铸坯表面纵裂纹
(3) 保护渣 液渣层厚度<10mm,纵裂纹增加(图2-5)。
图2-5 液渣层厚度对纵裂纹的影响
2 铸坯表面纵裂纹
(4) 结晶器液面波动 液面波动<±5mm,纵裂纹最少(图2-6);
图2-6 结晶器液面波动对纵裂纹的影响
2W (T1 T2 ) W
连铸坯表面裂纹 形成及防止
宋晔
内容
1 2 3 4 5 前言 铸坯表面纵裂纹 铸坯表面横裂纹 铸坯表面星形裂纹 结论
1.前言
连铸坯质量概念: ◆ 铸坯洁净度(夹杂物数量、类型、尺寸、 分布) ◆ 铸坯表面质量(表面裂纹、夹渣、气孔) ◆ 铸坯内部质量(内部裂纹、夹杂物,中 心疏松、缩孔、偏析) ◆ 铸坯形状缺陷(鼓肚、脱方)
2 铸坯表面纵裂纹
2.3 影响表面纵裂纹产生的因素
(1) 钢水成分
◆ [S]>0.015%,纵裂纹增加(图2-2);
◆ [C]=0.12~0.15%,纵裂纹产生严重(图2-3)
图2-2 钢中[S]与裂纹指数的关系
2 铸坯表面纵裂纹
பைடு நூலகம்
图2-3 含碳量对板坯宽面纵裂纹的影响
2 铸坯表面纵裂纹
(2) 拉速 拉速增加,纵裂纹指数增加(图2-4);
连铸坯缺陷的产生与防止措施 Microsoft Word 文档1

连铸坯裂纹的产生与防止措施连铸坯裂纹的分类 :铸坯表面裂纹包括表面纵裂纹、表面横裂纹、网状裂纹(星裂)、发裂、角部纵裂纹、角部横裂纹等;铸坯内部裂纹包括中间裂纹、角部裂纹、中心线裂纹、三角区裂纹、皮下裂纹、矫直裂纹等。
1.1 铸坯表面裂纹部纵裂纹等几种主要的缺陷形式。
铸坯表面裂纹主要有表面纵裂纹、表面横裂纹、网状裂纹、角部横裂纹、边铸坯表面裂纹是在结晶器内产生的,在二冷段得到扩展。
它会导致轧制板材表面的微细裂纹,影响最终产品的表面质量。
图1为表面裂纹示意图图 1 铸坯表面裂纹示意图1-表面纵裂纹;2-表面横裂纹;3-网状裂纹;4-角部横裂纹;5-边部纵裂纹1.1.1 表面纵裂纹连铸坯表面纵裂纹是指沿着拉坯方向在铸坯表面上发生的裂纹。
它可由工艺因素或设备因素引起。
由工艺因素引起的纵裂,大多出现在铸坯宽面的中央部位,是表面裂纹中最常见的一种裂纹缺陷。
纵裂主要是由于初生坯壳在结晶器内冷却强度不均匀,造成应力的集中,在坯壳相对较薄的地方坯壳厚度不足以承受这种应力,致使坯壳裂开而产生裂纹,并在二冷区得到扩展,形成表面纵裂纹。
图2 图3 图4为表面纵裂纹示意图图2图3 图41.影响连铸坯表面纵裂纹因素:实际生产过程中,主要有以下因素影响连铸坯表面纵裂纹的产生:1) 成品成分及钢水质量(1) 成品钢中碳含量处在亚包晶和包晶反应区时,由于初生坯壳在结晶器弯月面内激冷时收缩较大,容易造成初生坯壳厚薄不均,从而使铸坯发生纵裂纹的倾向增加。
因此,在实际生产中各连铸厂家都尽量控制其成品钢中碳含量,使其避开亚包晶和包晶反应区,从而减少铸坯纵裂纹的发生机率。
(2) 成品钢中硫、磷含量也会影响铸坯纵裂纹的产生。
钢中硫、磷含量增加时,钢的高温强度和塑性明显降低,在应力作用下就容易产生裂纹,因此,在实际生产中各连铸厂家都尽量控制其成品钢中硫、磷含量,尽量控制在0.02%以内。
(3) 钢中微合金如铌、钒等对铸坯纵裂纹的产生也有重要影响,因为微合金而产生的铸坯纵裂纹在铸坯表面上分布不规则,缺陷较短、数量较多。
连铸坯表面裂纹形成及防止(理化中心)

-
15
横裂纹产生原因
(1) 横裂纹产生于结晶器初始坯壳形成振痕的波谷处,振痕越深, 则横裂纹越严重,在波谷处,由于:一是奥氏体晶界析出沉淀物 (AlN,Nb(CN)),产生晶间断裂(如下图); 二是沿振痕波谷 S、P元素呈正偏析,降低了钢高温强度。这样,振痕波谷处,奥 氏体晶界脆性增大,为裂纹产生提供了条件。
不均匀性强,振痕深,表面易产 生凹陷或横裂纹;生产实践表明, C避开这个区间时,振痕浅了, 铸坯边部横裂减少; (2)降低钢中[N],防止氮化物沉 淀; 2. 结晶器振动特点 (1)振痕深度增加,横裂纹增加 (如图所示);
图: 振痕深度与横裂纹产生几率的关系
-
18
(2)振动频率f增加,振痕变浅,横裂纹减少(如图所示); (3)负滑脱时间增加,振痕深度增加(如图所示),方圆坯 tN=0.12~0.15s,板坯tN=0.20s。
图 铸坯表面的网状裂纹
-
23
铸坯表面星形裂纹产生原因
铸坯表面星形裂纹沿一次晶界分布,裂纹边界有脱C现象,说明是 在结晶器内高温下(1400℃)坯壳奥氏体转变之前形成的。
图 振动频率与振痕深度的关系
-
图 负滑脱与振痕深度的关系
19
Байду номын сангаас
3. 合适二冷强度
调整二冷水分布,在矫 直前铸坯温度>850℃,避 开脆性区(如图所示);
合适二冷水量并降低铸 坯横向中心与边部温度差, 避免回热温度过高。
图 矫直温度与横裂纹关系
-
20
防止横裂纹措施
(1) 采用高频率,小振幅结晶器振动负滑脱时间tN与拉速v成正比, 与频率和振幅f成反比。为防止横裂纹,就要减浅振痕,则必须降 低,要降低,则必须采用高频率(100~400min-1),小振幅 (±5mm)的结晶器振动机构。
铸坯表面横裂纹的形成机理
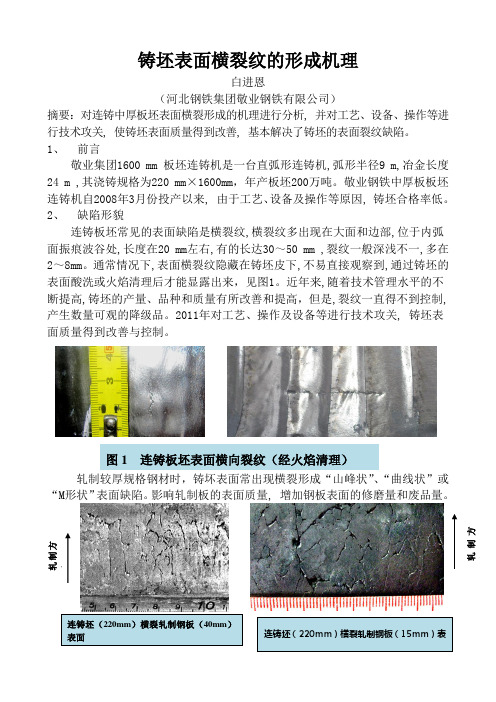
铸坯表面横裂纹的形成机理白进恩(河北钢铁集团敬业钢铁有限公司)摘要:对连铸中厚板坯表面横裂形成的机理进行分析, 并对工艺、设备、操作等进行技术攻关, 使铸坯表面质量得到改善, 基本解决了铸坯的表面裂纹缺陷。
1、 前言敬业集团1600 mm 板坯连铸机是一台直弧形连铸机,弧形半径9 m,冶金长度24 m ,其浇铸规格为220 mm ×1600mm ,年产板坯200万吨。
敬业钢铁中厚板板坯连铸机自2008年3月份投产以来, 由于工艺、设备及操作等原因, 铸坯合格率低。
2、 缺陷形貌连铸板坯常见的表面缺陷是横裂纹,横裂纹多出现在大面和边部,位于内弧面振痕波谷处,长度在20 mm 左右,有的长达30~50 mm ,裂纹一般深浅不一,多在2~8mm 。
通常情况下,表面横裂纹隐藏在铸坯皮下,不易直接观察到,通过铸坯的表面酸洗或火焰清理后才能显露出来,见图1。
近年来,随着技术管理水平的不断提高,铸坯的产量、品种和质量有所改善和提高,但是,裂纹一直得不到控制,产生数量可观的降级品。
2011年对工艺、操作及设备等进行技术攻关, 铸坯表面质量得到改善与控制。
轧制较厚规格钢材时,铸坏表面常出现横裂形成“山峰状”、“曲线状”或“M 形状”表面缺陷。
影响轧制板的表面质量, 增加钢板表面的修磨量和废品量。
图1 连铸板坯表面横向裂纹(经火焰清理)图2 钢板表面横裂实物图3、铸坯表面横裂纹形成机理结晶器振动的目的是防止初生坯壳与结晶器黏结漏钢,但不可避免地会在初生坯壳表面留下震动痕迹。
而铸坯横裂纹产生于振动痕迹的波谷处,振痕越深,横裂纹越严重。
裂纹的发生率还与振痕形貌有关,振痕越深,呈“沟槽”形,曲率半径越小,越容易发生横裂纹和角横裂。
连铸坯表面横裂起源于结晶器中振痕波谷处,最后在矫直过程中形成。
横裂形成具体分6个阶段:①靠结晶器壁生长正常的凝固组织,即细小等轴晶(坯壳晶、激冷层),其晶粒尺寸约500μm;②负滑脱凝壳向内运动,凝壳离开结晶器壁,温度达1 350℃;③导致表面晶粒异常长大,粗大化达到1mm~2mm;④在大晶粒晶界碳、氮化物析出,弱化的晶界产生微裂纹源;⑤在异常粗大的晶界上形成先共析相铁素体网,其强度是奥氏体的1/4,构成新的裂纹源;⑥在连铸坯矫直过程中微裂纹扩展成为裂纹。
浅谈连铸板坯表面夹杂与裂纹的分析及预防措施

板坯连铸表面夹杂与表面裂纹的分析及预防措施摘 要:针对马钢板坯连铸生产过程中出现的表面夹杂与裂纹进行分析研究,提出了改进措施.关键词:连铸坯;表面夹杂;表面裂纹前 言连铸板坯表面出现夹杂与裂纹是影响铸坯质量的重要缺陷.夹杂与裂纹的出现,轻者要进行表面精整,重者会导致大宗废品的出现,既影响了铸机的生产,又影响了铸坯的质量,增加了企业的成本.本文就马钢第一炼钢厂板坯(220mmx1 300mm)生产中出现的表面夹杂和表面裂纹问题,从多角度分析研究其产生的原因,并提出减少夹杂与裂纹的措施,为板坯连铸生产提高参考.㈠ 表面夹杂缺陷1.1 夹杂来源和形成机理分析马钢第一炼钢厂板坯夹杂主要有两种类型:Ⅰ类为块状分布呈黄或白色;Ⅱ类为连续分布呈青色.通过电镜扫描分析发现:Ⅰ类夹杂是因耐火材料成块脱落而造成的,这种夹杂的结晶与上水口砖及某种耐火泥的结晶基本相同.因此,可以推断Ⅰ类夹杂的来源主要是结晶器上口与其护板之间抹的耐火泥和石英下水口成块脱落.这是因为在成分,颜色,岩相结构3方面与夹杂基本相同.在Ⅱ类夹杂的基体中有大小不等的结晶相α—A120,颗粒.而α—A12O 3有来源于脱氧产物的特征.夹杂中还有SiO 2,SiO 2为石英下水口的熔融状态.因此,可以推断Ⅱ类型夹杂的来源是石英下水口吸附A12O 3后的产物.形成机理是,A12O 3容易在石英质水口壁上附集.由于水口砖质的不均匀性及钢流冲刷的作用,A12O 3被吸附的结果会演变成凸起状颗粒.随其与基体结合面的减小,钢流冲刷及颗粒的增大,最后脱离石英水口而进入结晶器内.以A12O 3,和SiQ 2为主要组成的夹杂物因其熔点高,在保护渣中不易被熔融吸附.当它存在于结晶器四壁的钢液弯月面处时,若操作稍有不慎,这种颗粒状夹杂物就很容易被卷入铸坯表面形成表面夹杂.1.2 减少夹杂的解决办法连铸提高钢的质量控制夹杂物的办法有两类:第一类是防止夹杂物的生成和带入,第二类是去除钢液中已存在的夹杂物。
连铸坯表面裂纹形成及防止
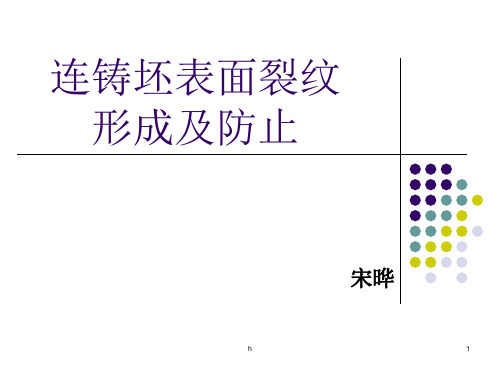
h
17
3 铸坯表面横裂纹
3 铸坯表面横裂纹
3.1表面横裂纹特征
横裂纹可位于铸坯面部或棱边
横裂纹与振痕共生,深度2~4mm,可达7mm,裂纹深处生成 FeO。不易剥落,热轧板表面出现条状裂纹。振痕深,柱状晶 异常,形成元素的偏析层,轧制板上留下花纹状缺陷。
铸坯横裂纹常常被FeO覆盖,只有经过酸洗后,才能发现。
连铸坯表面裂纹 形成及防止
宋晔
h
1内容Βιβλιοθήκη 1 前言 2 铸坯表面纵裂纹 3 铸坯表面横裂纹 4 铸坯表面星形裂纹 5 结论
h
2
1.前言
连铸坯质量概念: ◆ 铸坯洁净度(夹杂物数量、类型、尺寸、 分布) ◆ 铸坯表面质量(表面裂纹、夹渣、气孔) ◆ 铸坯内部质量(内部裂纹、夹杂物,中 心疏松、缩孔、偏析) ◆ 铸坯形状缺陷(鼓肚、脱方)
h
18
3 铸坯表面横裂纹
3.2横裂纹产生原因 (1) 横裂纹产生于结晶器初始坯壳形成振痕的
波谷处,振痕越深,则横裂纹越严重,在波谷 处,由于: -奥氏体晶界析出沉淀物,产生晶间断裂 -沿振痕波谷S、P元素呈正偏析,降低了钢高 温强度。
这样,振痕波谷处,奥氏体晶界脆性增大,为裂 纹产生提供了条件。
(2) 拉速
拉速增加,纵裂纹指数增加(图2-4);
图2-4 拉速对纵h 裂纹的影响
12
2 铸坯表面纵裂纹
(3) 保护渣 液渣层厚度<10mm,纵裂纹增加(图2-5)。
图2-5 液渣层厚度h 对纵裂纹的影响
13
2 铸坯表面纵裂纹
(4) 结晶器液面波动 液面波动<±5mm,纵裂纹最少(图2-6);
15
2 铸坯表面纵裂纹
(2) 结晶器钢水流动的合理性
连铸板坯表面从裂纹的原因及防止措施

维普资讯
20 0 2年 l 2月
・
炼
钢
De . 0 2 c2 0
2 ・ 第 1 6 8卷 第 6期
S el kn tema ig
V0 . 8 No 6 11 .
连 铸 板 坯 表 面 纵 裂 纹 的 成 因 及 防 止 措 施
汤 曙 光 焦 兴 利 刘 启 龙
大包 容量 / t
中包 / t
2 铸 机 状况
铸 机 状 况 见 表 1 。
结 晶器
长 9 0 i一 a rn 振幅/ mm
四偏 心 正弦 振动
3 0~ 3 o o
±5
3 铸 坯 表面 裂 纹 的影 响 因素
对 轧 出 的 中厚 板 仔 细 观 察 ,发 现 板 子 表 面有 很 细 的 、 规 则 的 、时 断 时 续 的纵 裂 纹 ,并 且 发 不 生 过 几 次 铸 坯 宽 面 中心 大 宗 纵 裂 纹 ,下 面 主 要 从
纵裂纹 的发生率有显著影 响 ,中包 过热 度每增加
l ℃ ,在 一 定 拉 速 的 条 件 下 ,出 结 晶 器 的坯 壳 厚 0 度 约 减 少 3 ;且 坯 壳 平 均 温 度 升 高 ,在 应 力 不 % 变 的情 况 下 ,由 于坯 壳 温 度 向钢 的 第 1脆 性 区移
联 系人 :汤曙 光 ,高级工 程师 ,安徽 省马鞍 山市 ( 4 0 1马 鞍 山钢 铁股份 公 司第一炼 钢厂 23 1 )
以下 几 方 面进 行 分 析 。
矫直 工作 拉速 / ri m・ n a
冶金 长度 / m
多点矫 直
0. ~ 2. 3 0
2 . 8 8 71
3 1 铸 温铸速 的影 响 .
连铸坯表面纵裂纹产生原因及控制措施

左 右 1 00 mm
。
2 3 1 .
.
宽 大 纵 裂 纹 宽 度 深 度 :
丨 0 - 20m m ,
2 0 - 3 0m m ,
长达几米 严重时会贯穿 板坯而报废
,
。
22 .
表 面 纵 裂 纹 原 因 分 析
2 2 .
.1
纵 裂 纹 起 源 于 结 晶 器 的 弯 月 面 区 初 生 凝 固
0 2 -
1
1
> 2 1
钢 液 面 波 动 范 围 mm ,
图 4 液 面 波 动 对 裂 纹 指 数 的 影 响
2 .
2. 4
结 晶 器 冷 却 效 果 及 热 流 的 影 响重 要 纵 裂 纹 一 般 均 发 生 在 结 晶 器 内 部 在 结 晶 器
,
,
结 晶 器 冷 却 效 果 对 连 铸 坯 纵 裂 纹 的 影 响 非 常 内 部 先 形 成 微 裂 纹 进 入 二 冷 区 后 发 展 成 明 显 的 裂 ,
,
晶器
流
于 W M 7 1 .
M2
/
宽面 铜板平 均热 流 为
侧 面 平 均 热 流 M W M 4 6 1 .
-
1.
2 /
,
为
<z>
>
右 1
cr >
i . i
a M
議
图 5 结 晶 器 热 流对 裂 纹 指 数 的 对 应 关 系
板 表 面 纵 裂纹 发 生 率 最 小 M W 3 l .
l- 1.
/ m2 ,
坯
。
经 统 计 分 析 侧 边 铜 板 热 流 与 宽 边 铜 板 热 流 之
连铸板坯角部横裂产生的原因及应对措施

铸坯角部横裂产生的原因及应对措施板坯可以在表面上观察到纵向裂纹,在尾部观察到中线裂纹。
要了解板坯中的角裂纹及孔隙,必须用沿板坯边部进行火焰切割处理,切割出50mm宽,2〜3mm深的槽。
在检查板坯的裂纹时,在高强低合金钢(HSLA)、包晶钢、中碳钢中发现了角部横裂,但是在低碳铝镇静钢中却很少发现裂纹。
包晶钢含有Nb,因此,角裂的百分比极高。
虽然在板坯的疏松边发现了角部横裂,但板坯中的大多数裂纹出现在板坯的固定边。
几乎板坯中所有的角部横裂纹与振动痕迹方向一致。
在出厂前,必须对板坯中的角裂纹和针孔进行处理。
处理板坯中出现的裂纹将增加产品成本,降低生产能力,耽误产品出厂日期。
经过火焰切割后的板坯样品送到米塔尔研究实验室进行分析,以便确定其中角部横裂纹的发生原因。
为减少角部横裂纹,米塔尔公司LazaroCardenas(MSLC)的操作人员、维修人员、技术人员组成了一支精干的团队,以降低板坯角部横裂纹的发生。
裂纹起因当铸流表面遭受到热力应变、机械力应变或相变时,若该应变量超过了铸件材料的最大应变值,板坯就会发生横裂。
在下列条件下板坯可能产生裂纹:(1)铸流表面温度下降至低延展区以下,拉伸应变导致铸件产生裂纹。
(2)结晶器上热收缩应变引起板坯内部热断裂,产生裂纹。
(3)结晶器上或结晶器附近所施加的外力引起表面热拉裂。
产品的延展性低是出现裂纹的主要原因。
影响板坯横裂的因素还包括化学作用。
减小温差,降低震动是避免板坯裂隙发生的主要措施。
角部裂分析对板坯切削样本(削痕深度2〜3mm)进行化学成分分析的结果如表1。
在这种钢中发现了严重的角部裂纹,主要原因是该种钢的Nb、V和C含量高,特别是C对包晶钢非常敏感。
理论上讲,Nb(C,N)在1090°C开始析出,当温度下降,析出量快速增长,当温度降低到900C时主要析出物为V(C,N),温度进一步下降到800C时,晶间继续析出。
众所周知,在温度降低过程中,Nb基及V基析出物沿奥氏体晶粒边界析出。
连铸坯表面裂纹形成及防止

1.前言
铸坯裂纹是影响连铸机产量和铸坯 质量的主要缺陷。据统计铸坯各类缺 陷中的50%为裂纹。铸坯出现裂纹, 重者会导致漏钢和废品,轻者需进行 精整。
2 铸坯表面纵裂纹
2.1 板坯表面纵裂纹特征 表面纵裂纹可能发生在板坯宽面中心区域或宽面到
棱边的任一位置产生。图2-1为板坯宽面中心区域的 纵 裂 纹 和 纵 裂 纹 的 显 微 形 貌 。 以 250×1200mm (C=0.08%)板坯为例: 细小纵裂纹:宽度1-2mm,深度3-4mm,长100mm左
5.结论
(1)连铸坯产生裂纹主要决定于: 钢成分对裂纹敏感性、 浇注工艺条件、连铸机设备状况。
(2)带液芯连铸坯在连铸机内运行过程中受外力作用是 坯壳产生裂纹的外因,钢的高温力学行为是产生裂纹 的内因,而设备、工艺因素是产生裂纹的条件。
(3)根据所浇钢种,对连铸机设备的调整应符合钢凝固收 缩规律,使其坯壳不受变形为原则,对工艺参数的优化, 使其得到合理的铸坯凝固结构。这样使连铸坯不产 生裂纹或控制裂纹不足以造成废品的所允许的范围 内。
图3-4 矫直温度与横裂纹关系
3 铸坯表面横裂纹
3.4 防止横裂纹措施
(1) 采用高频率,小振幅结晶器振动 为防止横裂纹,就要减浅振痕,则必须降低,要
降低,则必须采用高频率 (100~400min-1),小振幅 (±5mm)的结晶器振动机构。 (2) 合适的二次冷却水量
根据钢种不同,二冷配水量分布应使铸坯表面 温度分布均匀,应尽量减少铸坯表面和边部温度差。 采用动态二冷配水模型。
匀性强,振痕深,表面易产生凹陷 或横裂纹;生产实践表明,C= 0.15~0.18%或0.15~0.20%时, 振痕浅了,铸坯边部横裂减少; 降低钢中[N],防止氮化物沉淀; (2) 结晶器振动特点 振痕深度增加,横裂纹增加(图31); 振动频率f增加,振痕变浅,横裂纹 减少(图3-2);
连铸坯表面裂纹形成及防止

如比值太小,说明侧面铜板热流过低, 凝固坯壳厚度较薄,钢水静压力作用 使侧面鼓胀,加大了宽面坯壳变形, 在薄弱处产生微裂纹。
如比值过大,说明侧边热流过高,侧 边凝固坯壳生长过厚,当宽面鼓胀时, 侧边不能随之收缩而导致宽面坯壳薄 弱处应力集中产生微细裂纹。
侧面热流与宽面热流比值与裂纹关系
2 铸坯表面纵裂纹
矫直温度与横裂纹关系
3 铸坯表面横裂纹
3.4 防止横裂纹措施 (1) 采用高频率,小振幅结晶器振动 负滑脱时间tN与拉速v成正比,与频率和振幅f成反比。为防止横 裂纹,就要减浅振痕,则必须降低,要降低,则必须采用高频率 (100~400min-1),小振幅(±5mm)的结晶器振动机构。 (2) 合适的二次冷却水量 根据钢种不同,二冷配水量分布应使铸坯表面温度分布均匀, 应尽量减少铸坯表面和边部温度差。采用动态二冷配水模型。 (3) 合适保护渣性 保护渣用量和粘度,既要满足减浅振痕,又要防止坯壳粘结。最 少为 0.3kg/m2。
铸坯表面裂纹类型
1-横向角部裂纹 2-纵向角部裂纹 3-横裂纹 5-星形裂纹 4-宽面纵向裂纹 6-深振痕
20CrNiMoH连铸坯表面裂纹成因及防止措施

20CrNiMoH连铸坯表面裂纹成因及防止措施摘要:随着汽车领域发展越来越快,对齿轮钢的需求就变得非常大,所以齿轮钢变得越来越重要,不过齿轮钢在生产过程当中存在着很多的问题,其中较为严重的就是应力集中问题,会造成表面裂纹,所以必须采取有效的方法进行解决。
为了更有效的探究齿轮钢裂纹成因,在此以20CrNiMoH齿轮钢为例,分别利用金相显微镜、扫描电镜和能谱分析等方法对裂纹成因展开探究,分析发现连铸坯卷渣是主要因素,并提出有效的防止措施,希望给20CrNiMoH连铸坯表面裂纹防止带来有效的作用。
关键词:20CrNiMoH;连铸坯;表面裂纹成因;防止措施如今齿轮钢的需求非常大,生产规模也越来越大,但是受非金属杂质的影响,使得齿轮钢在生产时,会出现严重的应力集中情况,从而使得表面出现裂纹,一般裂纹的程度会受杂质性质、数量、形态以及分布情况等影响。
为有效解决这些问题,着重研究了20CrNiMoH,该齿轮钢的杂质较少,淬透性、可锻性、加工性、焊接性都很好,能够良好用在重型机械当中,不过利用EAF-LF-VD-CC流程进行生产时,20CrNiMoH连铸坯表面具有裂纹,为避免裂纹产生,就对连铸技术进行了改善,以防止裂纹问题,增强产品质量。
一、20CrNiMoH齿轮钢的生产过程通常20CrNiMoH齿轮钢的生产包括以下五个过程,分别为:EAF电弧炉、LF钢包精炼炉、VD真空精炼炉、连铸机以及棒材轧制。
(一)EAF电弧炉EAF电弧炉生产过程为:先精选出废钢,然后运用铁水代替部分废钢,铁水的加入时间应在第一次加料之后,并且炉料大概熔解20%时,这样是为了避免铁水发生飞溅。
在冶炼过程中应加入50%以上的铁水,这样才能有效调节稀释钢水里的残余元素。
(二)LF钢包精炼炉LF钢包精炼炉主要运用的是扩散脱氧以及造白渣技术,炉渣的碱度大于3,在脱氧过程当中,需要连续吹Ar并搅拌20min以上。
(三)VD真空精炼炉VD真空精炼炉的主要作用是净化钢水,其真空压力应为100Pa,吹氩时间大于15min。
连铸坯表面裂纹形成及防止汇总

图2-4 拉速对纵Biblioteka 纹的影响2 铸坯表面纵裂纹
(3) 保护渣 液渣层厚度<10mm,纵裂纹增加(图2-5)。
图2-5 液渣层厚度对纵裂纹的影响
2 铸坯表面纵裂纹
(4) 结晶器液面波动 液面波动<±5mm,纵裂纹最少(图2-6);
图2-6 结晶器液面波动对纵裂纹的影响
2W (T1 T2 ) W
3 铸坯表面横裂纹
3.2横裂纹产生原因 (1) 横裂纹产生于结晶器初始坯壳形成振痕的 波谷处,振痕越深,则横裂纹越严重,在波谷 处,由于: -奥氏体晶界析出沉淀物,产生晶间断裂 -沿振痕波谷S、P元素呈正偏析,降低了钢高 温强度。 这样,振痕波谷处,奥氏体晶界脆性增大,为裂 纹产生提供了条件。
这些力的的综合作用在坯壳上,当张应力超过钢的高温允许的 强度,则就在坯壳薄弱处萌生裂纹,出结晶器后在二冷区继续扩展。
2 铸坯表面纵裂纹
在结晶器弯月面区坯壳厚度生长不均匀的主要原 因是: (1)包晶相变(L+δ→γ)收缩特征,气隙过早形成, 导致坯壳生长不均匀。 (2)工艺因素影响结晶的坯壳生长不均匀。 显然要防止产生纵裂纹,就是要使结晶的弯月面初 生坯壳厚度均匀,避免坯壳产生应力梯度。要做到这点, 对于包晶相变的收缩特征是由Fe-C相图决定的,人为 无法改变,而重要的是准确控制影响结晶的初生坯壳生 长的工艺因素,来防止产生纵裂纹。
图3-1 振痕深度与横裂纹产生几率的关系
3 铸坯表面横裂纹
图3-2 振动频率与振痕深度的关系
3 铸坯表面横裂纹
图3-3 结晶器液面波动与角裂发生率的关系
(3) 结晶器液面波动 结晶器液面波动增加,横裂纹加重(图3-3)。
3 铸坯表面横裂纹
连铸板坯表面纵裂事故分析及预防措施.doc

YJ0712-连铸板坯表面纵裂事故分析及预防措施案例简要说明:依据国家职业标准和冶金技术专业教学要求,归纳提炼出所包含的知识和技能点,弱化与教学目标无关的内容,使之与课程学习目标、学习内容一致,成为一个承载了教学目标所要求知识和技能的教学案例。
本案例是连续铸钢产品质量缺陷案例,体现了铸坯质量特征、表面纵裂产生的原因、预防措施等知识点和岗位技能,与本专业连续铸钢课程连铸坯质量缺陷单元的教学目标相对应。
连铸板坯表面纵裂事故分析及预防措施1 背景介绍某炼钢厂连铸车间,采用超薄热带生产线,FTSC连铸板坯连铸机,机型直弧形,二冷气水雾化喷嘴,铸机基本半径5m,工作拉速2.8-5.2m/min,生产铸坯厚度87mm,结晶器液面控制方式Cs137射源控制。
主要生产薄板坯。
2 主要内容2.1事故经过2012年5月,FTSC工艺连铸薄板坯出现了大量的表面纵裂。
特别是浇注的ss400钢的裂纹率明显超高,占有缺陷铸坯的60~70%。
其主要发生在距中心四分之一宽度附近,距离中心300~400mm的区域。
当时,取样反馈的情况滞后于铸机生产,发现裂纹缺陷时已经造成至少两炉钢的裂纹质量缺陷。
因缺少铸坯离线检测的中间环节,这种铸坯纵裂纹对轧钢工序影响较大,最终导致质量异议事件2.2事故原因分析连铸板坯的裂纹表面纵裂由于在结晶器内凝固壳的生长不均匀,导致在特定部位拉伸应力的集中而产生。
对于薄板坯连铸来说,由于工艺的特殊性,其原因更为复杂多样。
(见图1)图1:铸坯表面纵裂(1)四孔水口通钢量大,对坯壳冲刷严重,使得在水口射流下方距中心260~430的区域坯壳减薄,导致结晶器出口处坯壳厚度比平均坯壳厚度减薄20%。
(2)钢水射流冲刷作用反映到坯壳表面温度上使得在距中心260~400的区域形成高温区,并随着拉速的增加而被加强,在结晶器出口处铸坯表面横向温度差达到1000C,高温、坯壳薄所造成的应力集中是产生铸坯纵裂纹的一个根源。
(3)结晶器漏斗区宽度为800mm,自由锥度设计较小,漏斗区内坯壳的收缩需要靠挤压窄面进行补充,但过大的局部锥度构成了形成纵裂纹的潜在因素。
连铸板坯角部横裂纹产生原因与控制

连铸板坯角部横裂纹产生原因与控制许孟春;李德军;张宁【摘要】The causes leading to the transverse corner cracks of continuous casting slabs are summarized. The effect of such factors as compositions in molten steel, mould control and proper-ties of casting powders on the transverse corner cracks are analyzed and thus the countermeasures for these cracks are proposed, including the adjustment of compositions in molten steel, optimiza-tion of the control for mould and optimization of the secondary cooling schedule and properties of casting powders.%综述了连铸板坯角部横裂纹的形成原因,分析了钢水成分、结晶器控制、保护渣性能等对角部横裂纹的影响,并提出了调整钢水成分、优化结晶器控制、优化二冷制度和保护渣性能等控制角部横裂纹产生的改进措施。
【期刊名称】《鞍钢技术》【年(卷),期】2015(000)002【总页数】7页(P9-14,19)【关键词】连铸板坯;角部横裂纹;钢水成分;结晶器【作者】许孟春;李德军;张宁【作者单位】鞍钢集团钢铁研究院,辽宁鞍山114009;鞍钢集团钢铁研究院,辽宁鞍山114009;鞍钢集团钢铁研究院,辽宁鞍山114009【正文语种】中文【中图分类】TF748近年来,随着我国交通运输、石油化工、重型机械、海洋工程、核电、军工等行业的技术进步和快速发展,对钢铁产品的质量、性能、规格等提出了更高的要求,对连铸坯的质量要求也更加严格。
连铸方坯中心裂纹成因分析及控制方法
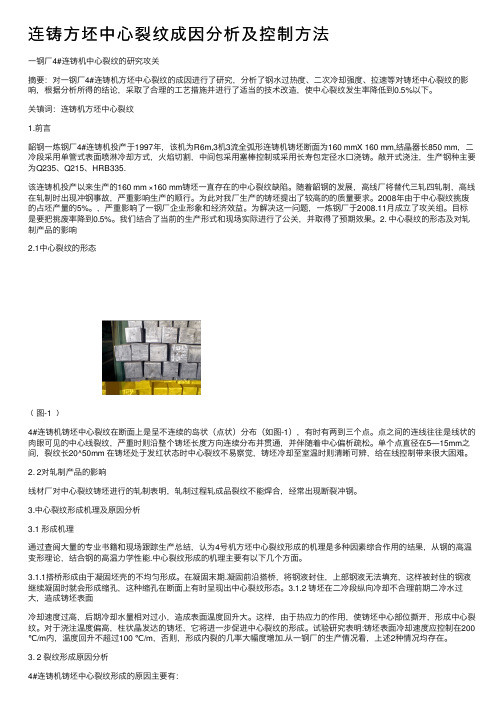
连铸⽅坯中⼼裂纹成因分析及控制⽅法⼀钢⼚4#连铸机中⼼裂纹的研究攻关摘要:对⼀钢⼚4#连铸机⽅坯中⼼裂纹的成因进⾏了研究,分析了钢⽔过热度、⼆次冷却强度、拉速等对铸坯中⼼裂纹的影响,根据分析所得的结论,采取了合理的⼯艺措施并进⾏了适当的技术改造,使中⼼裂纹发⽣率降低到0.5%以下。
关镇词:连铸机⽅坯中⼼裂纹1.前⾔韶钢⼀炼钢⼚4#连铸机投产于1997年,该机为R6m,3机3流全弧形连铸机铸坯断⾯为160 mmX 160 mm,结晶器长850 mm,⼆冷段采⽤单管式表⾯喷淋冷却⽅式,⽕焰切割,中间包采⽤塞棒控制或采⽤长寿包定径⽔⼝浇铸。
敞开式浇注,⽣产钢种主要为Q235、Q215、HRB335.该连铸机投产以来⽣产的160 mm ×160 mm铸坯⼀直存在的中⼼裂纹缺陷。
随着韶钢的发展,⾼线⼚将替代三轧四轧制,⾼线在轧制时出现冲钢事故,严重影响⽣产的顺⾏。
为此对我⼚⽣产的铸坯提出了较⾼的的质量要求。
2008年由于中⼼裂纹挑废的占坯产量的5%。
,严重影响了⼀钢⼚企业形象和经济效益。
为解决这⼀问题,⼀炼钢⼚于2008.11⽉成⽴了攻关组。
⽬标是要把挑废率降到0.5%。
我们结合了当前的⽣产形式和现场实际进⾏了公关,并取得了预期效果。
2. 中⼼裂纹的形态及对轧制产品的影响2.1中⼼裂纹的形态﹙图-1 ﹚4#连铸机铸坯中⼼裂纹在断⾯上是呈不连续的岛状(点状)分布(如图-1),有时有两到三个点。
点之间的连线往往是线状的⾁眼可见的中⼼线裂纹,严重时则沿整个铸坯长度⽅向连续分布并贯通,并伴随着中⼼偏析疏松。
单个点直径在5—15mm之间,裂纹长20^50mm 在铸坯处于发红状态时中⼼裂纹不易察觉,铸坯冷却⾄室温时则清晰可辨,给在线控制带来很⼤困难。
2. 2对轧制产品的影响线材⼚对中⼼裂纹铸坯进⾏的轧制表明,轧制过程轧成品裂纹不能焊合,经常出现断裂冲钢。
3.中⼼裂纹形成机理及原因分析3.1 形成机理通过查阅⼤量的专业书籍和现场跟踪⽣产总结,认为4号机⽅坯中⼼裂纹形成的机理是多种因素综合作⽤的结果,从钢的⾼温变形理论,结合钢的⾼温⼒学性能.中⼼裂纹形成的机理主要有以下⼏个⽅⾯。
- 1、下载文档前请自行甄别文档内容的完整性,平台不提供额外的编辑、内容补充、找答案等附加服务。
- 2、"仅部分预览"的文档,不可在线预览部分如存在完整性等问题,可反馈申请退款(可完整预览的文档不适用该条件!)。
- 3、如文档侵犯您的权益,请联系客服反馈,我们会尽快为您处理(人工客服工作时间:9:00-18:30)。
断裂前
断裂后
图:钢在600~900℃区域内发生脆断示意图
(2) 铸坯运行过程中, 受到外力(弯曲,矫直, 鼓肚,辊子不对中等)作 用时,刚好处于低温脆性 区的铸坯表面处于受拉伸 应力作用状态,如果坯壳
所受的ε临>1.3%,在振痕
波谷处就产生裂纹。
影响产生横裂纹因素
1. 钢成分 (1)C=0.10~0.15%,坯壳厚度
2.2 表面横裂纹产生的来源
横裂纹与振痕共生,深度2~4mm,可达7mm,裂纹深处生成FeO。 不易剥落,振痕深,柱状晶异常,形成元素的偏析层 铸坯横裂纹常 常被FeO覆盖,只有经过酸洗后,才能发现。
横裂纹产生原因
(1) 横裂纹产生于结晶器初始坯壳形成振痕的波谷处,振痕越深, 则横裂纹越严重,在波谷处,由于:一是奥氏体晶界析出沉淀物 (AlN,Nb(CN)),产生晶间断裂(如下图); 二是沿振痕波谷 S、P元素呈正偏析,降低了钢高温强度。这样,振痕波谷处,奥 氏体晶界脆性增大,为裂纹产生提供了条件。
连铸坯表面裂纹形成及防止理化中心 前言 2 铸坯工艺流程简介 3 铸坯质量常见缺陷及主要原因 4 合金元素对铸坯质量的影响
1.前言
连铸坯质量概念: ◆ 铸坯洁净度(夹杂物数量、类型、尺寸、分布) ◆ 铸坯表面质量(表面裂纹、夹渣、气孔) ◆ 铸坯内部质量(内部裂纹、夹杂物,中心疏松、缩孔、 偏析) ◆ 铸坯形状缺陷(鼓肚、脱方)
(2) 合适的二次冷却水量 根据钢种不同,二冷配水量分布应使铸坯表面温度分布均匀应尽 量减少铸坯表面和边部温度差。采用动态二冷配水模型。
(3) 合适保护渣性 保护渣用量和粘度,既要满足减浅振痕,又要防止坯壳粘结。
(4) 合适铸坯轿直温度,以避开脆性区。
(5) 矫直辊水平度管理(如图所示) 矫直辊水平度异常时,铸坯矫直应变比正常大(正常=1.19%,
异常为2.69%),使横裂多且深,所以应把辊水平度控制在2mm以内。
图 轿直辊水平度对铸坯横裂的影响
3 铸坯表面星形裂纹
3.1铸坯表面星形(网状)裂纹特征 裂纹位于铸坯表面被FeO覆盖,经酸洗后才能发现。表面裂纹 分布无方向性,形貌呈网状(如图所示),裂纹深度可达14mm,有的甚至达20mm。 金相观察表明,裂纹沿初生奥氏体晶界扩展。裂纹中充满FeO, 必须进行人工修复。
不均匀性强,振痕深,表面易产 生凹陷或横裂纹;生产实践表明, C避开这个区间时,振痕浅了, 铸坯边部横裂减少; (2)降低钢中[N],防止氮化物沉 淀; 2. 结晶器振动特点 (1)振痕深度增加,横裂纹增加 (如图所示);
图: 振痕深度与横裂纹产生几率的关系
(2)振动频率f增加,振痕变浅,横裂纹减少(如图所示); (3)负滑脱时间增加,振痕深度增加(如图所示),方圆坯 tN=0.12~0.15s,板坯tN=0.20s。
图 振动频率与振痕深度的关系
图 负滑脱与振痕深度的关系
3. 合适二冷强度
调整二冷水分布,在矫 直前铸坯温度>850℃,避 开脆性区(如图所示);
合适二冷水量并降低铸 坯横向中心与边部温度差, 避免回热温度过高。
图 矫直温度与横裂纹关系
防止横裂纹措施
(1) 采用高频率,小振幅结晶器振动负滑脱时间tN与拉速v成正比, 与频率和振幅f成反比。为防止横裂纹,就要减浅振痕,则必须降 低,要降低,则必须采用高频率(100~400min-1),小振幅 (±5mm)的结晶器振动机构。
2.铸坯工艺流程
缺陷的控制策略图
r 5.43102 M M
式中 M 钢水表面张力
M 钢水密度
钢水与铜壁弯月面的形成
1. 原渣层; 2. 烧结层; 3. 半溶融层; 4. 液渣层; 5. 钢液; 6. 凝固坯壳; 7. 渣圈; 8. 玻璃质渣膜;9. 结晶质渣膜;10. 结晶器
结晶器内钢水凝固 俯视图
图 铸坯表面的网状裂纹
铸坯表面星形裂纹产生原因
铸坯表面星形裂纹沿一次晶界分布,裂纹边界有脱C现象,说明是 在结晶器内高温下(1400℃)坯壳奥氏体转变之前形成的。
对于铸坯表面星状裂纹形成的原因,有不同的观点,大致有以下看 法: (1) 铜渗透和铜富集铜渗透结晶器下部。铜板渣层破裂,发生固/ 固摩擦接触,Cu局部粘附在坯壳上,Cu熔点是1040℃,Cu熔化沿 奥氏体晶界渗透,晶界破坯而失去塑性,产生热脆现象。在裂纹里 发现有铜(Cu=1.6%),也证明了这点。
1. 柱状晶生长;
2. 某些柱状晶生长加 快;
3. 凝固桥形成;
4. 小钢锭凝固,缩孔 形成;
5. 实际的低倍结构
第二部分:
铸坯常见质量缺陷
铸坯裂纹是影响连铸机产量和铸坯质量的主要缺陷。据 统计铸坯各类缺陷中的50%为裂纹。铸坯出现裂纹,重 者会导致漏钢、废品、质量异议,轻者需进行精整。
带液芯的铸坯在连铸机内运行和凝固过程中为什么会产 生裂纹,这是一个复杂的问题。当外力作用于带液芯的 坯壳上,究竟是否产生裂纹决定于钢的高温力学行为、 凝固的冶金行为和铸机设备运行状态。就裂纹而言,可 分为铸坯表面裂纹和铸坯内部裂纹两类
铸坯常见表面质量缺陷
1. 横向角部裂纹; 2. 纵向角部裂纹; 3. 横向裂纹; 4. 纵向裂纹; 5. 星形裂纹; 6. 深振痕; 7. 针孔; 8. 宏观夹杂;
2.1 表面纵裂纹产生的来源
1. 铸坯横断面低倍检验指出,纵裂纹起源于激冷层薄弱处(约23mm)。 2. 结晶器的模拟试验指出,纵裂纹起源于结晶的弯月面区(几十毫米 到150mm)周边坯壳厚度薄弱处。这说明纵裂纹起源于结晶器的弯 月面区初生凝固壳厚度的不均匀性。由于受力的作用:
15CrMoG漏钢
P22纵裂纹
漏钢处
(2) 拉速 1. 拉速增加,纵裂纹指数增加; 2. 拉速增加,渣膜厚度减少;
拉速对纵裂纹的影响
拉速对渣膜厚度的影响
(3) 保护渣 液渣层厚度<10mm,纵裂纹增加。 高凝固温度和高结晶器温度的保护渣,减少结晶器弯月面传热可 使纵裂发生率减少50%。
液渣层厚度对纵裂纹的影响
(1)铸坯凝固壳四周温度不均匀而产生的收缩力。 (2)铸坯收缩由钢水静压力产生的鼓胀力。 3. 在裂纹边缘出现有一定的脱碳层,说明裂纹是在高温下形成扩展的。
这些力的的综合作用在坯壳上,当张应力超过钢的高温允许的强度, 则就在坯壳薄弱处萌生裂纹,出结晶器后在二冷区继续扩展。
表面纵裂纹产生的原因
(1)包晶相变(L+δ→γ)收缩特征,气 隙过早形成,导致坯壳生长不均匀。