漏斗模型及其在生产精彩活动管理系统中地指导应用
销售漏斗应用及管理

– 衡量有多少缺口 – 什么行动能弥补这个缺口
预测不是项目金额简单叠加 经验系数可以通过实践修正趋于准确
销售漏斗和预测
• 销售漏斗表 • 重点项目跟踪表 • 销售预测表
每个销售人员都要掌握EXCEL的基本功能
目录
• 销售漏斗的原理 • 销售漏斗的使用 • 销售漏斗的管理 • 销售员成功路线图 • 思考
销售漏斗的使用和管理是销售最重要和最基本的技能
销售漏斗阶段定义
• 项目式销售,按项目推动 的进程,分为7个阶段
– 定位和挖掘目标客户 – 发现潜在的销售机会 – 引导和确认客户意向 – 影响及跟进客户立项 – 赢得客户的初步认可 – 与客户进行商务谈判 – 完成销售成交的活动
• 按客户在销售过程中表现 的状态,分为7个阶段
销售员成长过程
• 成长阶段
– 销售培训期间,0- 3个月 – 有定额的前3个月,4-6个月 – 有定额的4-6个月,7-9个月 – 有定额的7-9个月,10-12个月 – 有定额的10-12个月,13-15个月
销售培训阶段
• 目标
– 具备初步沟通能力(学会问问题) – 找到20个目标客户 – 挖掘 5个潜在客户
客户需求紧迫原因的问题
• 经营情况-商业驱动力-主动衍生的项目
– 客户为什么必须行动 – 作出决定的最后期限 – 如果计划被延迟了会有什么后果 – 如果计划如期完成会有什么回报 – 计划会给他们带来什么影响
是否具备竞争力的问题
• 正确的决策标准
– 正式的决策过程是什么 – 哪个决策标准最重要,为什么 – 谁决定决策标准
• 客户高层主管的可信度 • 文化的兼容性 • 影响决策的非正常因素 • 政治联盟
漏斗原则应用设计方案(一)

漏斗原则应用设计方案(一)漏斗原则应用设计方案1. 简介漏斗原则是一种经典的市场营销理论,它通过不断筛选和过滤潜在客户,最终仅留下对产品感兴趣且有购买意向的目标客户。
在设计方案中应用漏斗原则,可以提高营销效率,减少资源浪费,实现更精准的目标客户定位。
2. 方案实施步骤以下是漏斗原则应用设计方案的实施步骤:1.明确目标客户群体:分析产品的特点,确定适合的目标客户群体,如年龄、性别、地域等。
2.引起关注:通过各种宣传手段吸引潜在客户的关注,如社交媒体广告、线下活动等。
3.获取兴趣:提供有吸引力的内容,让潜在客户对产品或服务产生兴趣,如优惠活动、专题文章等。
4.培养意愿:与潜在客户建立联系,并持续提供有价值的信息和服务,增强其对产品的兴趣和购买意愿。
5.转化为目标客户:利用销售技巧和营销手段,将潜在客户转化为真正的目标客户,如个人咨询、推荐购买等。
6.维系客户关系:与目标客户保持良好的互动和沟通,提供售后服务和产品更新,提高客户忠诚度。
3. 方案优势通过漏斗原则应用设计方案,可以获得以下优势:•准确定位目标客户:根据产品特点和目标市场需求,精准找到潜在客户群体。
•提高营销效率:通过有针对性的宣传和营销手段,减少资源浪费,提高转化率。
•增强用户体验:通过持续提供有价值的内容和服务,提高用户对产品的满意度和忠诚度。
•打造品牌形象:通过与目标客户的互动,树立品牌形象,增强市场竞争力。
4. 总结漏斗原则应用设计方案是一种有效的市场营销策略,它能够帮助企业更好地找到目标客户,并通过有效的营销手段实现销售转化。
在实施方案时,需要结合产品特点和目标市场需求,灵活调整具体的营销策略和手段,以达到最佳的效果。
产品运营分析的万金油——漏斗模型
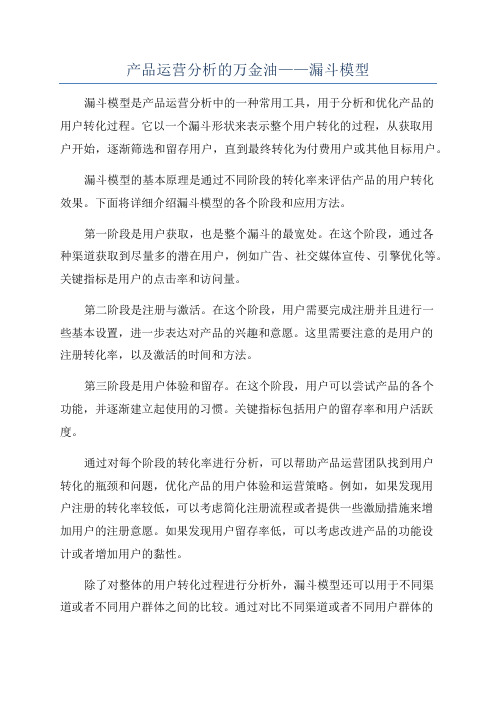
产品运营分析的万金油——漏斗模型漏斗模型是产品运营分析中的一种常用工具,用于分析和优化产品的用户转化过程。
它以一个漏斗形状来表示整个用户转化的过程,从获取用户开始,逐渐筛选和留存用户,直到最终转化为付费用户或其他目标用户。
漏斗模型的基本原理是通过不同阶段的转化率来评估产品的用户转化效果。
下面将详细介绍漏斗模型的各个阶段和应用方法。
第一阶段是用户获取,也是整个漏斗的最宽处。
在这个阶段,通过各种渠道获取到尽量多的潜在用户,例如广告、社交媒体宣传、引擎优化等。
关键指标是用户的点击率和访问量。
第二阶段是注册与激活。
在这个阶段,用户需要完成注册并且进行一些基本设置,进一步表达对产品的兴趣和意愿。
这里需要注意的是用户的注册转化率,以及激活的时间和方法。
第三阶段是用户体验和留存。
在这个阶段,用户可以尝试产品的各个功能,并逐渐建立起使用的习惯。
关键指标包括用户的留存率和用户活跃度。
通过对每个阶段的转化率进行分析,可以帮助产品运营团队找到用户转化的瓶颈和问题,优化产品的用户体验和运营策略。
例如,如果发现用户注册的转化率较低,可以考虑简化注册流程或者提供一些激励措施来增加用户的注册意愿。
如果发现用户留存率低,可以考虑改进产品的功能设计或者增加用户的黏性。
除了对整体的用户转化过程进行分析外,漏斗模型还可以用于不同渠道或者不同用户群体之间的比较。
通过对比不同渠道或者不同用户群体的转化率,可以找到最有效的渠道或者最有潜力的用户群体,从而优化产品的营销策略和资源分配。
总结来说,漏斗模型是产品运营分析的一种万金油工具,可以帮助产品团队了解和优化用户转化过程。
通过对每个阶段的转化率进行分析,可以找到转化的瓶颈和问题,并制定相应的优化策略。
漏斗模型还可以用于不同渠道和用户群体的比较,找到最有效的推广渠道和用户群体。
因此,漏斗模型是产品运营必备的工具之一。
漏斗模型分析课件

根据客户需求提供个性化、贴心的服务,如免费咨询、上门维修 等,让客户感受到关怀。
建立客户回访机制
定期对客户进行回访,了解产品使用情况,及时解决客户问题, 提高客户满意度。
提高客户参与度
增强互动
通过各种渠道与客户保持互动,如社交媒体、线上社区等,及时回应客户关切,提高客户黏性。
举办活动
定期举办各类活动,如产品体验活动、专家讲座等,邀请客户参与,提高客户的参与度和认同感。
A/B测试
通过对比实验,测试不同版本漏斗的效果,找 出最优方案。
用户调研
与用户进行互动,收集用户对漏斗的反馈和建议。
评估结果的应用
优化改进
01
根据评估结果,对漏斗的各个环节进行优化改进,提
高转化率和效果。
调整策略
02 根据评估结果,调整推广策略和运营策略,提高投入
产出比。
监控风险
03
根据评估结果,监控潜在的风险和问题,及时采取措
鼓励客户反馈
建立客户反馈机制,鼓励客户提供意见和建议,及时掌握客户需求和反馈,为产品研发和优化提供参考 。
06
漏斗模型案例分析
案例一:电商分析是一个经典案例,通过分析用 户行为路径,找出用户流失的关键点,进一步优化营销 策略和产品体验。
详细描述
电商平台在运营过程中,通常面临用户流失严重的问题 。通过对用户行为数据进行分析,可以构建一个漏斗模 型,将用户从曝光到订单成交的整个过程划分为多个环 节。通过对每个环节的用户流失情况进行深入分析,可 以找出用户流失的关键点,为企业的营销策略和产品优 化提供有力的数据支持。
详细描述
通过漏斗模型,企业可以清晰地看到每个阶 段中客户的流失情况,从而找出问题所在并 制定相应的解决方案。此外,漏斗模型还可 以帮助企业评估销售团队的业绩,为销售策 略的优化提供数据支持。
经典的销售漏斗理论与使用

销售转化率低
总结词:销售转化率低是销售漏斗理 论实践中的另一个挑战,直接影响销 售业绩和盈利能力。
详细描述:销售漏斗理论的核心目的 是通过优化销售过程,提高销售转化 率。然而,在实际应用中,由于市场 竞争激烈、客户需求变化快、销售团 队能力不足等原因,可能导致销售转 化率低下。这不仅影响了销售业绩, 还增加了销售成本和运营风险。
B公司客户转化提升案例
总结词
B公司通过深入了解客户需求和行为,制 定客户转化提升计划,成功提高了客户 转化率和收益。
VS
详细描述
司是一家在线教育平台,为了提高客 户转化率和收益,深入了解客户需求和行 为,制定了一系列客户转化提升计划。这 些计划包括提供更有针对性的课程、改进 用户体验、加强售后服务等。这些措施的 实施,使得B公司的客户转化率和收益得 到了显著提升。
客户培育与转化
建立联系
通过电话、邮件、短信等方式, 主动与潜在客户建立联系,了解 他们的需求和意向,提供相应的
解决方案。
培育信任
通过专业的产品知识和良好的服 务态度,逐步建立客户信任,提 高客户对产品的认知度和好感度
。
促进转化
根据客户的购买意愿和购买力, 制定相应的转化策略,如优惠活 动、促销套餐等,以促成潜在客
制定客户培育计划
针对不同阶段的客户,制定个性化的培育计划,提升客户满意度 和忠诚度。
提供有价值的内容
通过提供有价值的信息、教程、案例等,满足客户需求,增加客户 粘性。
建立良好的客户关系
通过定期回访、互动等方式,建立良好的客户关系,提高客户留存 率。
提升客户维护质量
定期回访客户
定期对客户进行回访,了 解客户需求和反馈,及时 解决问题。
产品销售中如何有效利用销售漏斗

产品销售中如何有效利用销售漏斗在当今竞争激烈的市场环境中,产品销售的成功与否很大程度上取决于销售策略的有效性。
销售漏斗作为一种强大的销售管理工具,可以帮助销售人员更好地理解和管理销售流程,提高销售效率和成功率。
那么,如何在产品销售中有效利用销售漏斗呢?一、销售漏斗的概念和作用销售漏斗形象地展示了潜在客户在购买过程中从最初的接触到最终成交的各个阶段。
它就像一个倒立的漏斗,顶部较宽,代表着大量的潜在客户;随着销售过程的推进,潜在客户逐渐减少,直到底部较窄的部分,代表着最终成交的客户。
销售漏斗的主要作用有以下几点:1、可视化销售流程让销售人员清晰地看到销售过程中的各个阶段,以及潜在客户在每个阶段的流动情况,从而更好地把握销售进度。
2、预测销售业绩通过对销售漏斗中各个阶段的客户数量和转化率的分析,可以较为准确地预测未来的销售业绩,为销售目标的制定提供依据。
3、发现销售瓶颈能够帮助销售人员快速识别销售流程中存在的问题和瓶颈,例如某个阶段的客户流失率过高,从而有针对性地采取措施加以改进。
4、合理分配资源根据销售漏斗中不同阶段客户的重要性和需求,合理分配销售资源,提高资源利用效率。
二、构建适合自己产品的销售漏斗不同的产品和行业,销售流程可能会有所不同。
因此,在利用销售漏斗之前,需要根据自己产品的特点和销售流程,构建一个适合的销售漏斗模型。
1、确定销售阶段一般来说,销售漏斗可以分为几个常见的阶段,如潜在客户、意向客户、洽谈客户、成交客户等。
但具体的阶段划分需要根据产品的复杂程度、销售周期的长短以及客户的购买决策过程来确定。
例如,对于一款简单的消费品,销售阶段可能相对较少,如认知阶段、兴趣阶段、购买阶段;而对于一款复杂的企业级软件产品,销售阶段可能会包括需求调研、方案演示、试用评估等多个环节。
2、设定阶段转化率每个销售阶段之间都存在一定的转化率,即从一个阶段进入下一个阶段的客户比例。
通过对历史销售数据的分析和行业经验的参考,合理设定每个阶段的转化率。
产品销售中如何运用销售漏斗分析提升转化率

产品销售中如何运用销售漏斗分析提升转化率在当今竞争激烈的市场环境中,产品销售的成功与否很大程度上取决于转化率的高低。
而销售漏斗分析作为一种有效的工具,可以帮助企业深入了解销售流程,识别潜在问题,并采取针对性的措施来提升转化率。
接下来,让我们一起探讨如何在产品销售中运用销售漏斗分析来实现这一目标。
一、理解销售漏斗的概念销售漏斗形象地展示了客户从最初的潜在客户阶段到最终成交的整个过程,就像一个逐渐变窄的漏斗。
它通常包括多个阶段,如潜在客户、意向客户、洽谈客户、成交客户等。
每个阶段都有一定数量的客户,随着销售流程的推进,客户数量逐渐减少,最终只有一部分客户成功转化为购买者。
通过对销售漏斗各阶段的数据分析,我们可以清晰地看到客户在不同阶段的流失情况,从而找出销售流程中的瓶颈和问题所在。
二、销售漏斗分析的关键指标1、潜在客户数量这是销售漏斗的源头,反映了市场推广和获客活动的效果。
足够的潜在客户数量是保证销售业绩的基础。
2、各阶段转化率计算每个阶段客户向下一阶段转化的比例,例如从潜在客户到意向客户的转化率、从意向客户到洽谈客户的转化率等。
这些转化率能够直观地显示销售流程中哪个环节存在较大的提升空间。
3、平均销售周期了解从潜在客户到成交客户所需的平均时间,可以帮助企业评估销售效率,发现是否存在流程繁琐、沟通不畅等导致销售周期过长的问题。
4、客户流失率分析在每个阶段客户流失的比例和原因,有助于采取措施减少客户的流失,提高留存率。
三、运用销售漏斗分析提升转化率的步骤1、数据收集与整理首先,要确保能够准确地收集销售漏斗各阶段的数据,包括客户的基本信息、跟进记录、成交状态等。
这些数据可以来自销售团队的记录、客户关系管理系统(CRM)等。
2、绘制销售漏斗图将收集到的数据整理成销售漏斗图,直观地呈现各个阶段的客户数量和转化率。
通过图形化的展示,更容易发现问题和趋势。
3、分析销售漏斗数据仔细研究销售漏斗图和相关指标,找出转化率较低的阶段和客户流失较多的环节。
销售漏斗模型在汽车制造企业销售管理中的应用质量
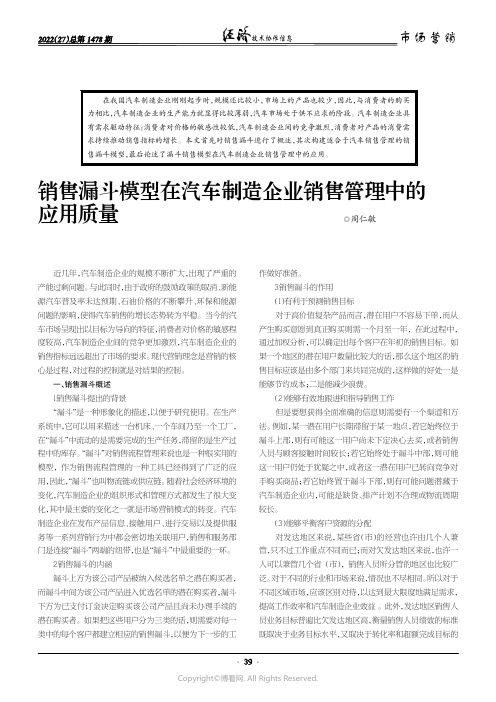
销售漏斗模型在汽车制造企业销售管理中的应用质量◎周仁敏场营销近几年,汽车制造企业的规模不断扩大,出现了严重的产能过剩问题。
与此同时,由于政府的鼓励政策的取消、新能源汽车普及率未达预期、石油价格的不断攀升、环保和能源问题的影响,使得汽车销售的增长态势转为平稳。
当今的汽车市场呈现出以目标为导向的特征,消费者对价格的敏感程度较高,汽车制造企业间的竞争更加激烈,汽车制造企业的销售指标远远超出了市场的要求。
现代营销理念是营销的核心是过程,对过程的控制就是对结果的控制。
一、销售漏斗概述1.销售漏斗提出的背景“漏斗”是一种形象化的描述,以便于研究使用。
在生产系统中,它可以用来描述一台机床、一个车间乃至一个工厂,在“漏斗”中流动的是需要完成的生产任务,滞留的是生产过程中的库存。
“漏斗”对销售流程管理来说也是一种很实用的模型,作为销售流程管理的一种工具已经得到了广泛的应用,因此,“漏斗”也叫物流链或供应链。
随着社会经济环境的变化,汽车制造企业的组织形式和管理方式都发生了很大变化,其中最主要的变化之一就是市场营销模式的转变。
汽车制造企业在发布产品信息、接触用户、进行交易以及提供服务等一系列营销行为中都会密切地关联用户,销售和服务部门是连接“漏斗”两端的纽带,也是“漏斗”中最重要的一环。
2.销售漏斗的内涵漏斗上方为该公司产品被纳入候选名单之潜在购买者,而漏斗中间为该公司产品进入优选名单的潜在购买者,漏斗下方为已支付订金决定购买该公司产品且尚未办理手续的潜在购买者。
如果把这些用户分为三类的话,则需要对每一类中的每个客户都建立相应的销售漏斗,以便为下一步的工作做好准备。
3.销售漏斗的作用(1)有利于预测销售目标对于高价值复杂产品而言,潜在用户不容易下单,而从产生购买意愿到真正购买则需一个月至一年,在此过程中,通过加权分析,可以确定出每个客户在年初的销售目标。
如果一个地区的潜在用户数量比较大的话,那么这个地区的销售目标应该是由多个部门来共同完成的,这样做的好处一是能够节约成本;二是能减少浪费。
企业管理理论中的创新管理模型有哪些

企业管理理论中的创新管理模型有哪些在当今竞争激烈的商业环境中,企业要想保持领先地位并实现可持续发展,创新管理已成为关键。
创新管理模型为企业提供了系统的方法和框架,帮助企业有效地识别、培育和实施创新。
以下是一些在企业管理理论中常见的创新管理模型:一、创新漏斗模型创新漏斗模型将创新过程比作一个漏斗。
在漏斗的顶部,是大量的创意和想法,这些想法可能来自企业内部的员工、外部的合作伙伴、客户甚至是竞争对手。
随着流程的推进,这些想法经过筛选、评估和优化,逐渐减少,最终只有少数具有高潜力和可行性的创新项目得以实施。
这个模型的优点在于能够帮助企业对众多的创意进行系统的梳理和筛选,集中资源在最有价值的项目上。
然而,其局限性在于可能会错过一些看似不太成熟但具有潜在突破的创意。
二、开放式创新模型开放式创新模型强调企业不仅要依靠内部的研发资源,还要积极整合外部的创新资源,包括供应商、客户、高校、科研机构等。
通过建立开放的创新生态系统,企业能够获取更广泛的知识和技术,加速创新的进程。
例如,宝洁公司通过建立“联系与发展”平台,与外部的创新者合作,成功推出了许多新产品。
这种模型的优势在于拓宽了创新的来源,提高了创新的效率和成功率。
但同时,也需要企业具备良好的合作管理能力,以确保与外部伙伴的有效协作和知识产权的保护。
三、破坏性创新模型破坏性创新模型由克莱顿·克里斯坦森提出,该模型认为创新可以分为维持性创新和破坏性创新。
维持性创新是在现有市场和技术基础上进行的改进和优化,而破坏性创新则是通过引入新技术或新商业模式,打破现有的市场格局,创造新的需求和市场。
例如,数码相机的出现对传统胶片相机市场造成了破坏性的影响。
破坏性创新往往来自于新进入者或处于市场边缘的企业,对于行业领先企业来说,需要警惕破坏性创新的威胁,并适时进行战略调整。
四、设计思维创新模型设计思维创新模型注重以用户为中心,通过深入了解用户的需求、痛点和期望,进行创造性的解决方案设计。
漏斗模型及其在生产管理中的应用
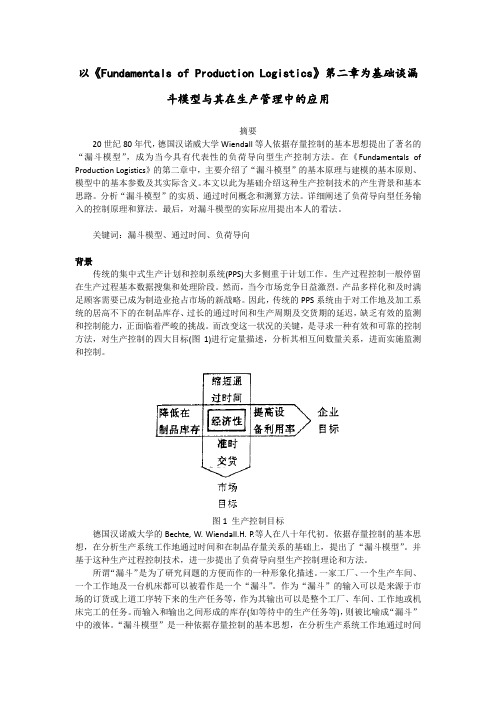
以《Fundamentals of Production Logistics》第二章为基础谈漏斗模型与其在生产管理中的应用摘要20世纪80年代,德国汉诺威大学Wiendall等人依据存量控制的基本思想提出了著名的“漏斗模型”,成为当今具有代表性的负荷导向型生产控制方法。
在《Fundamentals of Production Logistics》的第二章中,主要介绍了“漏斗模型”的基本原理与建模的基本原则、模型中的基本参数及其实际含义。
本文以此为基础介绍这种生产控制技术的产生背景和基本思路。
分析“漏斗模型”的实质、通过时间概念和测算方法。
详细阐述了负荷导向型任务输入的控制原理和算法。
最后,对漏斗模型的实际应用提出本人的看法。
关键词:漏斗模型、通过时间、负荷导向背景传统的集中式生产计划和控制系统(PPS)大多侧重于计划工作。
生产过程控制一般停留在生产过程基本数据搜集和处理阶段。
然而,当今市场竞争日益激烈。
产品多样化和及时满足顾客需要已成为制造业抢占市场的新战略。
因此,传统的PPS系统由于对工作地及加工系统的居高不下的在制品库存、过长的通过时间和生产周期及交货期的延迟,缺乏有效的监测和控制能力,正面临着严峻的挑战。
而改变这一状况的关键,是寻求一种有效和可靠的控制方法,对生产控制的四大目标(图1)进行定量描述,分析其相互间数量关系,进而实施监测和控制。
图1 生产控制目标德国汉诺威大学的Bechte, W. Wiendall.H. P.等人在八十年代初。
依据存量控制的基本思想,在分析生产系统工作地通过时间和在制品存量关系的基础上,提出了“漏斗模型”。
并基于这种生产过程控制技术,进一步提出了负荷导向型生产控制理论和方法。
所谓“漏斗”是为了研究问题的方便而作的一种形象化描述。
一家工厂、一个生产车间、一个工作地及一台机床都可以被看作是一个“漏斗”。
作为“漏斗”的输入可以是来源于市场的订货或上道工序转下来的生产任务等,作为其输出可以是整个工厂、车间、工作地或机床完工的任务。
广告中的漏斗模型如何应用
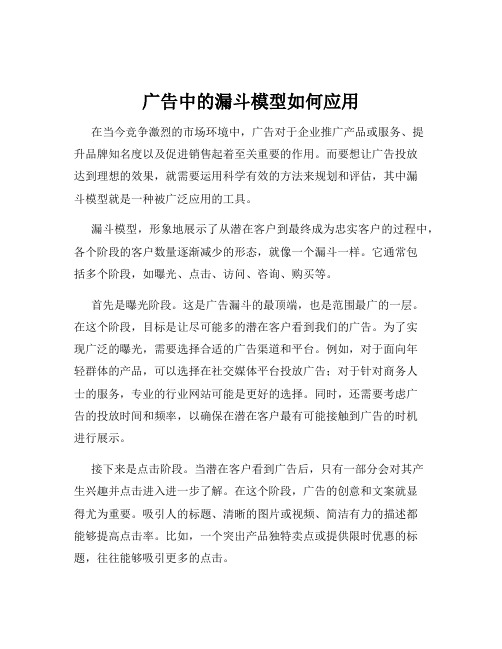
广告中的漏斗模型如何应用在当今竞争激烈的市场环境中,广告对于企业推广产品或服务、提升品牌知名度以及促进销售起着至关重要的作用。
而要想让广告投放达到理想的效果,就需要运用科学有效的方法来规划和评估,其中漏斗模型就是一种被广泛应用的工具。
漏斗模型,形象地展示了从潜在客户到最终成为忠实客户的过程中,各个阶段的客户数量逐渐减少的形态,就像一个漏斗一样。
它通常包括多个阶段,如曝光、点击、访问、咨询、购买等。
首先是曝光阶段。
这是广告漏斗的最顶端,也是范围最广的一层。
在这个阶段,目标是让尽可能多的潜在客户看到我们的广告。
为了实现广泛的曝光,需要选择合适的广告渠道和平台。
例如,对于面向年轻群体的产品,可以选择在社交媒体平台投放广告;对于针对商务人士的服务,专业的行业网站可能是更好的选择。
同时,还需要考虑广告的投放时间和频率,以确保在潜在客户最有可能接触到广告的时机进行展示。
接下来是点击阶段。
当潜在客户看到广告后,只有一部分会对其产生兴趣并点击进入进一步了解。
在这个阶段,广告的创意和文案就显得尤为重要。
吸引人的标题、清晰的图片或视频、简洁有力的描述都能够提高点击率。
比如,一个突出产品独特卖点或提供限时优惠的标题,往往能够吸引更多的点击。
点击之后是访问阶段。
客户点击广告后进入到我们的网站或页面,这时候页面的加载速度、设计布局和内容质量就成为关键。
如果页面加载缓慢,客户可能会失去耐心而离开;如果页面设计混乱、内容不清晰,客户也难以找到自己想要的信息。
因此,优化网站或页面的用户体验是提高访问转化率的重要环节。
页面应该简洁明了,导航清晰,重要信息易于查找,同时要提供有价值的内容,让客户感到值得停留和深入了解。
在访问之后,就是咨询阶段。
如果客户对我们的产品或服务感兴趣,可能会通过在线客服、电话、邮件等方式进行咨询。
在这个阶段,及时、专业、热情的回复至关重要。
客服人员需要具备丰富的产品知识和良好的沟通技巧,能够准确解答客户的疑问,消除他们的顾虑,从而推动客户进入下一个阶段。
漏斗原理在工作中的应用

漏斗原理在工作中的应用1. 什么是漏斗原理漏斗原理是一种市场营销分析方法,通过将市场活动中的用户流程分为不同的阶段,以便更好地理解和优化转化率。
它被广泛应用于各种领域,例如销售、客户服务、市场推广等。
2. 漏斗原理的基本原理漏斗原理基于用户行为分析和转化率优化的原理。
它将用户的整个体验过程分为多个阶段,从而可以追踪和分析用户在每个阶段的转化率。
通过不断优化每个阶段的转化率,可以最终提高整体的转化率。
3. 漏斗原理在销售中的应用在销售过程中,漏斗原理可以帮助销售人员更好地了解潜在客户的转化过程。
以下是漏斗原理在销售中的应用方式:•潜在客户阶段:在这个阶段,销售人员需要通过各种市场推广手段吸引潜在客户的注意力。
通过追踪和分析潜在客户的来源和行为,可以了解不同市场渠道的效果,并优化市场推广活动。
•兴趣阶段:在潜在客户表现出兴趣后,销售人员需要通过有效的沟通和推广活动,进一步培养客户的兴趣。
通过追踪和分析客户在兴趣阶段的行为,可以了解客户兴趣的变化,并提供更加有针对性的推广活动。
•意向阶段:在客户表达购买意向后,销售人员可以针对其具体需求进行销售和谈判。
通过追踪和分析客户在意向阶段的行为,可以了解客户购买意向的强度,并根据客户的反馈进行销售策略的调整。
•购买阶段:在客户决定购买后,销售人员需要完成交易,并提供售后服务。
通过追踪和分析客户在购买阶段的行为,可以了解客户的购买过程和满意度,并提供更好的售后服务。
4. 漏斗原理在市场推广中的应用在市场推广过程中,漏斗原理可以帮助市场人员更好地了解用户在每个阶段的行为和转化率。
以下是漏斗原理在市场推广中的应用方式:•广告曝光阶段:在这个阶段,市场人员需要通过各种广告平台将产品或服务展示给潜在客户。
通过追踪和分析广告曝光量和点击率,可以了解不同广告渠道的效果,并优化广告投放策略。
•点击阶段:在用户点击广告后,市场人员需要将用户引导到产品或服务的详细信息页面。
通过追踪和分析用户的点击行为,可以了解用户对产品或服务的兴趣和需求,并优化落地页的设计和内容。
经典的销售漏斗理论与使用

经典的销售漏斗理论与使用引言销售是商业中至关重要的环节,对于企业的发展和盈利起着关键作用。
为了提高销售效率和成果,销售漏斗理论应运而生。
销售漏斗理论是一种经典的销售管理方法,通过不断筛选和过滤,将潜在客户转化为实际购买者。
本文将介绍销售漏斗理论的基本概念和使用方法,并探讨其在实际销售中的应用。
什么是销售漏斗理论?销售漏斗理论是一种销售管理工具,用于描述和管理销售流程中的不同阶段。
它被比喻为一个倒置的漏斗,顶部为潜在客户,底部为最终的购买者。
在销售过程中,潜在客户会经历一系列的筛选和转化,最终只有一部分客户会成为实际购买者。
销售漏斗理论通常包括以下阶段: 1. 潜在客户:这是销售过程的初始阶段,潜在客户是指有可能购买企业产品或服务的人群。
2. 需求识别:在这个阶段,销售人员需要与潜在客户沟通,了解他们的需求和问题。
3. 兴趣唤起:在这个阶段,销售人员需要通过各种方式来唤起潜在客户的兴趣,使其对产品或服务产生浓厚的兴趣。
4. 评估和比较:在这个阶段,潜在客户会对不同供应商或产品进行评估和比较,从中选出最合适的产品或服务。
5. 购买决策:在这个阶段,潜在客户会最终做出购买决策,并选择购买企业的产品或服务。
6. 成交:这是销售过程的最后阶段,客户完成了购买,并进行支付。
销售漏斗理论的核心思想是,在销售过程中,客户群体会不断缩小,只有最有意愿和能力的客户会最终成交。
销售人员需要通过不断的沟通和推动,将潜在客户引导到最终的购买决策。
使用销售漏斗理论的好处使用销售漏斗理论有以下几个好处: 1. 高效管理销售流程:销售漏斗理论提供了一种清晰的销售流程管理方法,帮助销售团队更好地安排时间和资源,提高销售效率。
2. 优化销售策略:根据销售漏斗理论,销售人员可以更准确地了解潜在客户在销售过程中处于哪个阶段,从而制定相应的销售策略,提高销售成功率。
3.识别销售瓶颈:通过销售漏斗理论,销售团队可以发现销售过程中的瓶颈和问题,从而及时调整和改进销售策略,增加销售机会。
产品运营神器 | 漏斗模型
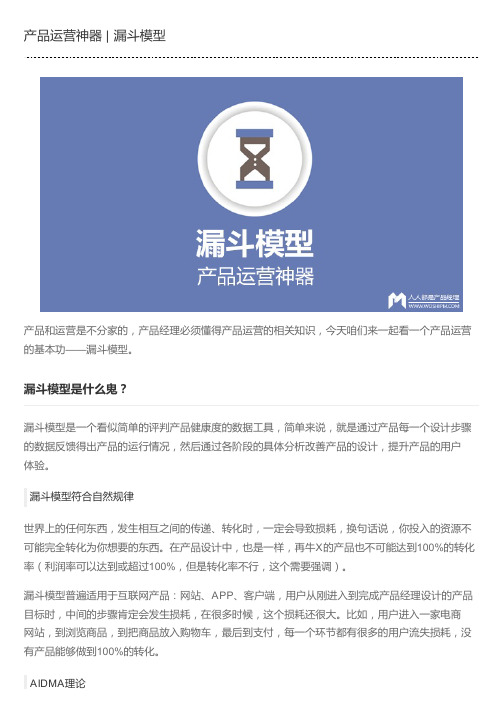
AIDMA理论AIDMA理论是漏斗模型的理论基础,它的基本要素如下图:Attention:关注Interest:兴趣Desire:渴望Memory:记忆Action:行动/购买举个例子:Glen公众号有5000粉丝,Glen写了一篇中等水平的文章,群发之后,不进行任何推广,一般一天之内会获得500左右的阅读量,有100个左右的朋友有更多的学习渴望,他们会收藏Glen 的文章,便于以后学习、记忆,更有10个左右的朋友给Glen赞赏一些零花钱。
以上就是一个漏斗模型的简单例子,如果以盈利为目的,从5000到500到100到10,每一个环节都会有损耗,最后的用户付费转化率为0.2%。
漏斗模型应用漏斗模型不只是AIDMA理论。
漏斗模型修正AIDMA理论是漏斗模型的基础,但是时代发展到21世纪,特别是移动互联网时代,漏斗模型有了更多的内涵,在传统的Attention、Interest、Desire、Memory、Action之外,应该还有Share。
在产品运行的漏斗中,每一个环节都可以产生让用户分享给其他人的交互点。
这个社交网络的时代,用户愿意在网络上分享自己的生活。
漏斗模型应用在产品设计的一些关键路径上设置数据反馈点,定时收集数据,进行漏斗传递的路径分析,得出产品运营健康度的评价。
举个例子,需要通过漏斗模型分析某流量型APP的游戏营收健康度。
这款APP的日活是400万,每天APP内“游戏中心”的游戏下载数是2万,日付费金额是5000,每日平均付费人数是80人。
借由以上关键数据反馈点,可以得出每一步的转化率:付费人数/下载次数:0.4%ARPU(每用户平均收入):55元根据转化率水平进行产品设计的优化:付费人数/下载次数比率偏低,则考虑是否是产品设计方面的展示不够明显,或者是运营活动没有做好,总之能够通过数据去分析产品的健康度,做出针对性的产品改进方案。
反向漏斗有时漏斗模型也可以逆向使用,推断产品正常运行所需要的一些基本要素。
高效销售漏斗管理:系统化地管理销售流程以增加销售机会
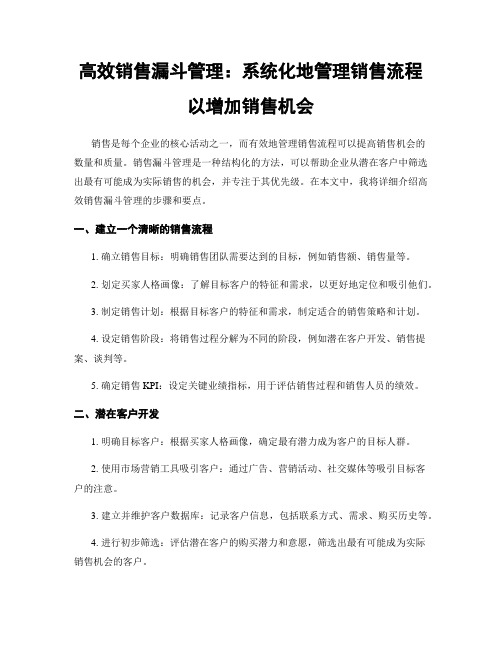
高效销售漏斗管理:系统化地管理销售流程以增加销售机会销售是每个企业的核心活动之一,而有效地管理销售流程可以提高销售机会的数量和质量。
销售漏斗管理是一种结构化的方法,可以帮助企业从潜在客户中筛选出最有可能成为实际销售的机会,并专注于其优先级。
在本文中,我将详细介绍高效销售漏斗管理的步骤和要点。
一、建立一个清晰的销售流程1. 确立销售目标:明确销售团队需要达到的目标,例如销售额、销售量等。
2. 划定买家人格画像:了解目标客户的特征和需求,以更好地定位和吸引他们。
3. 制定销售计划:根据目标客户的特征和需求,制定适合的销售策略和计划。
4. 设定销售阶段:将销售过程分解为不同的阶段,例如潜在客户开发、销售提案、谈判等。
5. 确定销售KPI:设定关键业绩指标,用于评估销售过程和销售人员的绩效。
二、潜在客户开发1. 明确目标客户:根据买家人格画像,确定最有潜力成为客户的目标人群。
2. 使用市场营销工具吸引客户:通过广告、营销活动、社交媒体等吸引目标客户的注意。
3. 建立并维护客户数据库:记录客户信息,包括联系方式、需求、购买历史等。
4. 进行初步筛选:评估潜在客户的购买潜力和意愿,筛选出最有可能成为实际销售机会的客户。
三、销售提案1. 了解客户需求:与潜在客户进行深入交流,了解他们的需求、问题和期望。
2. 为客户定制解决方案:根据客户的需求,提供适合的产品或服务解决方案。
3. 制定销售提案:根据客户需求和解决方案,制定详细的销售提案,包括价格、交付时间等。
4. 演示和演讲:通过演示产品功能、展示成功案例等方式,向客户展示解决方案的价值。
四、谈判与签约1. 谈判技巧:掌握有效的谈判技巧,例如倾听、提问、解决异议等,以达到双方满意的协议。
2. 处理异议和反馈:理解客户的异议和反馈,积极回应并迅速解决问题。
3. 制定最终协议:根据谈判结果,确立最终的销售协议,明确合作细节和权责。
4. 签订合同:与客户签署正式的销售合同,确保双方权益和责任得到保障。
基于漏斗模型和分布合作理论的生产计划控制系统
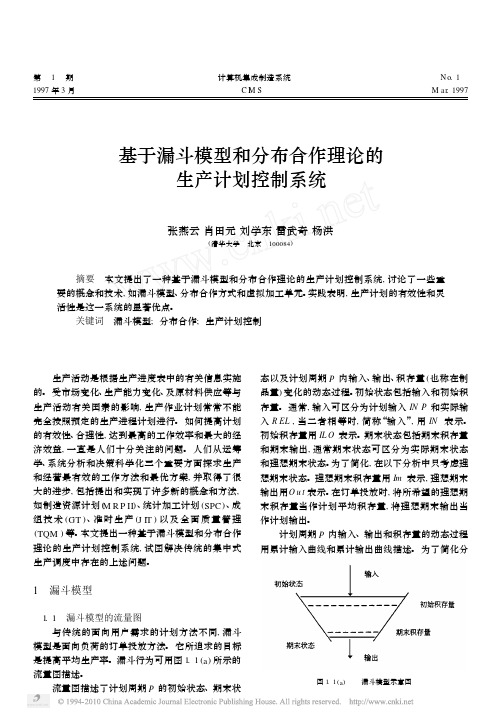
第1期1997年3月计算机集成制造系统 C I M S N o.1M ar.1997基于漏斗模型和分布合作理论的生产计划控制系统张燕云肖田元刘学东雷武奇杨洪(清华大学 北京 100084) 摘要 本文提出了一种基于漏斗模型和分布合作理论的生产计划控制系统,讨论了一些重要的概念和技术,如漏斗模型、分布合作方式和虚拟加工单元。
实践表明,生产计划的有效性和灵活性是这一系统的显著优点。
关键词 漏斗模型;分布合作;生产计划控制 生产活动是根据生产进度表中的有关信息实施的。
受市场变化、生产能力变化、及原材料供应等与生产活动有关因素的影响,生产作业计划常常不能完全按照预定的生产进程计划进行。
如何提高计划的有效性、合理性,达到最高的工作效率和最大的经济效益,一直是人们十分关注的问题。
人们从运筹学、系统分析和决策科学化三个重要方面探求生产和经营最有效的工作方法和最优方案,并取得了很大的进步,包括提出和实现了许多新的概念和方法,如制造资源计划(M R P II)、统计加工计划(SPC)、成组技术(GT)、准时生产(J IT)以及全面质量管理(TQM)等。
本文提出一种基于漏斗模型和分布合作理论的生产计划控制系统,试图解决传统的集中式生产调度中存在的上述问题。
1 漏斗模型1.1 漏斗模型的流量图与传统的面向用户需求的计划方法不同,漏斗模型是面向负荷的订单投放方法。
它所追求的目标是提高平均生产率。
漏斗行为可用图1.1(a)所示的流量图描述。
流量图描述了计划周期P的初始状态、期末状态以及计划周期P内输入、输出、积存量(也称在制品量)变化的动态过程。
初始状态包括输入和初始积存量。
通常,输入可区分为计划输入IN P和实际输入R EL,当二者相等时,简称“输入”,用IN表示。
初始积存量用IL O表示。
期末状态包括期末积存量和期末输出,通常期末状态可区分为实际期末状态和理想期末状态。
为了简化,在以下分析中只考虑理想期末状态。
理想期末积存量用Im表示,理想期末输出用O u t表示。
常用的产品数据分析方法之漏斗模型与归因模型人人都是产品经理
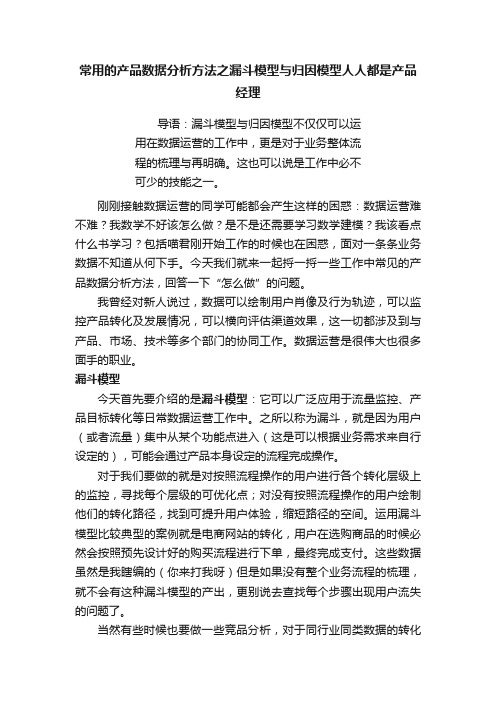
常用的产品数据分析方法之漏斗模型与归因模型人人都是产品经理导语:漏斗模型与归因模型不仅仅可以运用在数据运营的工作中,更是对于业务整体流程的梳理与再明确。
这也可以说是工作中必不可少的技能之一。
刚刚接触数据运营的同学可能都会产生这样的困惑:数据运营难不难?我数学不好该怎么做?是不是还需要学习数学建模?我该看点什么书学习?包括喵君刚开始工作的时候也在困惑,面对一条条业务数据不知道从何下手。
今天我们就来一起捋一捋一些工作中常见的产品数据分析方法,回答一下“怎么做”的问题。
我曾经对新人说过,数据可以绘制用户肖像及行为轨迹,可以监控产品转化及发展情况,可以横向评估渠道效果,这一切都涉及到与产品、市场、技术等多个部门的协同工作。
数据运营是很伟大也很多面手的职业。
漏斗模型今天首先要介绍的是漏斗模型:它可以广泛应用于流量监控、产品目标转化等日常数据运营工作中。
之所以称为漏斗,就是因为用户(或者流量)集中从某个功能点进入(这是可以根据业务需求来自行设定的),可能会通过产品本身设定的流程完成操作。
对于我们要做的就是对按照流程操作的用户进行各个转化层级上的监控,寻找每个层级的可优化点;对没有按照流程操作的用户绘制他们的转化路径,找到可提升用户体验,缩短路径的空间。
运用漏斗模型比较典型的案例就是电商网站的转化,用户在选购商品的时候必然会按照预先设计好的购买流程进行下单,最终完成支付。
这些数据虽然是我瞎编的(你来打我呀)但是如果没有整个业务流程的梳理,就不会有这种漏斗模型的产出,更别说去查找每个步骤出现用户流失的问题了。
当然有些时候也要做一些竞品分析,对于同行业同类数据的转化情况做到心中有数。
尽可能降低用户流失是我们的目标,但是如果可以做到不低于行业平均水准同时资源有限的话,降低这个转化漏斗的用户流失就需要被放置较低的优先级里。
还有一些比较经典的漏斗转化模型就是用于用户注册流程上:我们需要知道多少用户点击了注册按钮(漏斗的开端),多少用户完成了信息填写(多少用户放弃填写),多少用户点击发送验证码按钮(验证码到达率),成功完成注册的人数。
漏斗模型及其在生产管理中的应用
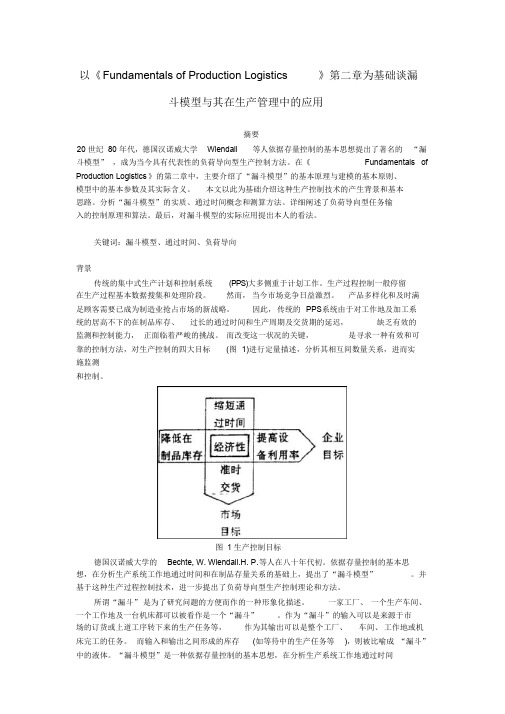
以《Fundamentals of Production Logistics 》第二章为基础谈漏斗模型与其在生产管理中的应用摘要20 世纪80 年代,德国汉诺威大学Wiendall 等人依据存量控制的基本思想提出了著名的“漏斗模型”,成为当今具有代表性的负荷导向型生产控制方法。
在《Fundamentals of Production Logistics 》的第二章中,主要介绍了“漏斗模型”的基本原理与建模的基本原则、模型中的基本参数及其实际含义。
本文以此为基础介绍这种生产控制技术的产生背景和基本思路。
分析“漏斗模型”的实质、通过时间概念和测算方法。
详细阐述了负荷导向型任务输入的控制原理和算法。
最后,对漏斗模型的实际应用提出本人的看法。
关键词:漏斗模型、通过时间、负荷导向背景传统的集中式生产计划和控制系统(PPS)大多侧重于计划工作。
生产过程控制一般停留在生产过程基本数据搜集和处理阶段。
然而,当今市场竞争日益激烈。
产品多样化和及时满足顾客需要已成为制造业抢占市场的新战略。
因此,传统的PPS系统由于对工作地及加工系统的居高不下的在制品库存、过长的通过时间和生产周期及交货期的延迟,缺乏有效的监测和控制能力,正面临着严峻的挑战。
而改变这一状况的关键,是寻求一种有效和可靠的控制方法,对生产控制的四大目标(图1)进行定量描述,分析其相互间数量关系,进而实施监测和控制。
图 1 生产控制目标德国汉诺威大学的Bechte, W. Wiendall.H. P.等人在八十年代初。
依据存量控制的基本思想,在分析生产系统工作地通过时间和在制品存量关系的基础上,提出了“漏斗模型”。
并基于这种生产过程控制技术,进一步提出了负荷导向型生产控制理论和方法。
所谓“漏斗”是为了研究问题的方便而作的一种形象化描述。
一家工厂、一个生产车间、一个工作地及一台机床都可以被看作是一个“漏斗”。
作为“漏斗”的输入可以是来源于市场的订货或上道工序转下来的生产任务等,作为其输出可以是整个工厂、车间、工作地或机床完工的任务。
- 1、下载文档前请自行甄别文档内容的完整性,平台不提供额外的编辑、内容补充、找答案等附加服务。
- 2、"仅部分预览"的文档,不可在线预览部分如存在完整性等问题,可反馈申请退款(可完整预览的文档不适用该条件!)。
- 3、如文档侵犯您的权益,请联系客服反馈,我们会尽快为您处理(人工客服工作时间:9:00-18:30)。
以《Fundamentals of Production Logistics》第二章为基础谈漏斗模型与其在生产管理中的应用摘要20世纪80年代,德国汉诺威大学Wiendall等人依据存量控制的基本思想提出了著名的“漏斗模型”,成为当今具有代表性的负荷导向型生产控制方法。
在《Fundamentals of Production Logistics》的第二章中,主要介绍了“漏斗模型”的基本原理与建模的基本原则、模型中的基本参数及其实际含义。
本文以此为基础介绍这种生产控制技术的产生背景和基本思路。
分析“漏斗模型”的实质、通过时间概念和测算方法。
详细阐述了负荷导向型任务输入的控制原理和算法。
最后,对漏斗模型的实际应用提出本人的看法。
关键词:漏斗模型、通过时间、负荷导向背景传统的集中式生产计划和控制系统(PPS)大多侧重于计划工作。
生产过程控制一般停留在生产过程基本数据搜集和处理阶段。
然而,当今市场竞争日益激烈。
产品多样化和及时满足顾客需要已成为制造业抢占市场的新战略。
因此,传统的PPS系统由于对工作地及加工系统的居高不下的在制品库存、过长的通过时间和生产周期及交货期的延迟,缺乏有效的监测和控制能力,正面临着严峻的挑战。
而改变这一状况的关键,是寻求一种有效和可靠的控制方法,对生产控制的四大目标(图1)进行定量描述,分析其相互间数量关系,进而实施监测和控制。
图1 生产控制目标德国汉诺威大学的Bechte, W. Wiendall.H. P.等人在八十年代初。
依据存量控制的基本思想,在分析生产系统工作地通过时间和在制品存量关系的基础上,提出了“漏斗模型”。
并基于这种生产过程控制技术,进一步提出了负荷导向型生产控制理论和方法。
所谓“漏斗”是为了研究问题的方便而作的一种形象化描述。
一家工厂、一个生产车间、一个工作地及一台机床都可以被看作是一个“漏斗”。
作为“漏斗”的输入可以是来源于市场的订货或上道工序转下来的生产任务等,作为其输出可以是整个工厂、车间、工作地或机床完工的任务。
而输入和输出之间形成的库存(如等待中的生产任务等),则被比喻成“漏斗”中的液体。
“漏斗模型”是一种依据存量控制的基本思想,在分析生产系统工作地通过时间和在制品存量关系的基础上,提出的负荷导向型生产控制理论和方法。
它的理论出发点是存量控制思想,即通过有目的地安排生产任务,使工作地在制品量维持在一定的水平上,从而确定和控制工作地平均通过时间及设备利用率,并由此对生产过程进行控制。
[1]在一个工作地,到达的加工任务(负荷),首先进入加工等待队列(在制品库存),经过一段通过时间,最后加工完毕离去(产出)如图2,我们可以根据任务的紧急程度进行排序。
而若长期观察,工作地平均通过时间是相对稳定的。
图2 以加工系统为原型构建的“漏斗模型”因此,可以利用“漏斗模型”对一个加工系统(工序、车间等)的负荷在制品库存通过时间和产出数值之间的相互关系进行动态统计分析,得出其数量关系,进而建立以加工系统在制品存量控制为核心的PPS系统。
由于在制品库存主要取决于加工任务的投料方法,这样就可以通过控制“漏斗”的输入(负荷导向型任务投料),调整在制品存量和平均通过时间,同时控制其输出(加工能力平衡),最终保证制造系统的平滑稳定和自动化生产。
提高系统柔性确保准时交。
.而且,根据“漏斗模型”原理,可以用各种图表跟踪显示生产过程中基本数据的动态变化清况,从而实现对生产过程的监测和诊断。
生产过程的主要观测指标与漏斗模型的建模基础在《Fundamentals of Production Logistics》的第二章中,作者对生产过程的基本参数进行了定义。
首先是工作量和运作时间,其描述公式如下其中WC代表工作量,单位为:小时;LS代表批量;tp代表每年产品处理时间,单位为:分钟/件;ts代表每一批的准备时间,单位为:分钟。
以此为基础,平均工作量计算公式如下其中WCm 代表平均工作量;WCi代表完成生产指令的工作量;n代表指令条数。
描述工作量的标准差其中WCs代表工作量的标准差;WCm平均工作量;WCi代表第i条指令的工作时间;n 代表生产指令的条数数量。
变异系数WCv其中WCv代表工作量的变异系数;WCs代表工作时量的标准差;WCm平均工作量。
订单(任务)加工时间也在模型中也称为运作时间,以TOP表示其中TOP代表运作时间,单位:工作日;WC代表工作容;ROUTmax 最大通过率即每个工作日能处理的任务(任务以需要加工的时间表示),最大通过率由生产能力决定,另外影响因素还包括限制能力因数、被机器故障影响的最大工作时间以及由多种因数影响到的操作者的工作极限能力变异系数之间的关系当观察的工作点数量只有一个,且最大输出率固定或者与单个运营的工作时间独立,那么一下公式成立。
即工作量变异系数与通过时间变异系数相等。
指令流出时间可以称为通过时间,以TTP表示其中TTP代表通过时间;Teop代表当前工序完成时间[SCD];Teprop代表前工序结束时间。
在一个观察周期,有一部分时间是交叉混合时间TIO,所谓“混合时间”就是指在制品(WIP)在完成前一道工序后到后一工序加工开始之前的这段时间。
混合时间包括:排队等待时间、运输时间、提前准备时间。
整个加工周期可以用以下的图3表示。
图3 生产加工时间构成示意图我们容易从图中看到,混合时间与运作时间、通过时间的关系其中TIO代表交叉操作时间;TTP代表通过时间;TOP代表运作时间,三者单位都为:工作日。
运作时间和产出时间关系式如下其中RFm代表平均流动率。
生产过程中也产生一定的延迟,其表现为计划通过时间与实际通过时间之差。
在生产控制的过程中,一个加工系统的加工效率可以通过输出率这样一个指标来衡量。
输出率即“有效的加工时间/观察阶段的总时间”计算公式如下:其中ROUTm代表平均输出率;TOi代表每个环节的工作量;n代表工作环节(指令)数量;PE代表调查期时长。
同样的,一个加工系统的负荷饱和程度可以通过系统的利用率来衡量,其计算公式如下:其中,Um代表平均利用率;ROUTm代表平均输出率;ROUTmax代表最大可能输出率。
在阐述漏斗模型的工作原理之前,还有一个指标需要指出。
WIP在制品,在漏斗模型中它被形象地视为漏斗中的液体,即没有完成加工的工件或任务。
代表从输入端到输出端这一段距离中的工件,是加工过程中的等待件和在生产线上加工着的工件的统称。
计算公式如下即:t1到t0期间的输入量减去期间的输出量的差,除以时间长度等于在制品量。
将上述生产过程中的基本参数和指标定义负荷导向型任务投料方法负荷导向型任务投料是一种根据现有的生产任务和加工能力进行自动投料的方法,按照其算法,可以在每个计划时间点,得出下个计划期(一天到一周)应投料的生产任务.其控制原理如下图所示.负荷导向型任务投料的步骤如下:(1)按生产任务的紧急程度(根据可支配缓冲时间计算)排序。
(2)确定原则上允许投料的生产任务。
即根据交货期时间界.对所有已知生产任务安排加工顺序流程。
在此,计划提前期是管理人员预先设置的控制参数。
通过排除在交货期时间界以外的生产任务,可以防止过早的任务投料。
(3)根据排序结果,对交货期紧急的任务优先安排,同时应保证与该生产任务相关工序的负荷,不超过其负荷界。
负荷界的具体算法如下:首先,确定下负荷百分比,其定义为EPS=BS×100%(1)ABBS=WIP+AB(2)其中:BS:负荷界(小时)WIP:计划平均在制品(小时)AB:计划完工量(小时)下负荷百分比(EPS)是负荷导向型任务投料的核心控制参数。
它直接关系到加工系统的在制品库存和平均通过时间大小。
其计算公式为:ESP=(1+MZ)×100%(3)P其中:MZ:计划平均通过时间P :计划周期其次,确定合理的负荷界(BS)。
由于ESP已经确定,计划完工期(AB)可由加工能力而定。
因此,可由(1)式算出负荷界。
总之,如果生产任务满足加工系统的时间界和负荷界的要求,则该任务可投料,否则拒绝投料。
生产过程的监测根据物流运作曲线,可以监测到工作地的生产任务从到达到完工期间流转或库存的变化情况。
然而,这些数据对于实现生产过程的控制目标是远远不够的。
因为,生产系统是一个复杂系统,它不仅包括主要工艺流程(即机床调试和加工活动),而且还有诸多的辅助工艺流程,如有关工艺装备、辅助设备和运输设备等的准备及结束活动。
因此,我们必须将简单工作地的“漏斗模型”)扩展为整个车间的“漏斗模型”,将一般的物流运作曲线图变为监测流转图。
这样,就可以监测到生产任务从计划下达到加工结束期间的全过程情况,这对于监测负荷导向型任务投料的实施及其反馈控制是十分必要的。
为此需要建立生产监测和诊断系统,其功能有:—、用各种图表跟踪显示生产系统工作现场的实际情况,并进行测算,如平均通过时间、平均在制品库存、设备利用率及交货期偏差等。
二、对实际值和计划值进行比较,得出偏差。
三、若有偏差。
找出故障和原因,提出可能实现的措施,如任务投料和加工能力的调整.四、监视措施的执行情况,不断地改进,直到满意为止。
生产过程的监测生产过程控制中使用漏斗模型的前提“漏斗模型”主要用于解决车间型制造系统的生产控制问题,适用于多品种、单件小批及成批生产类型。
尤其适用于订货型生产系统.对于大批量生产类型,及成组/柔性线流水线制造系统,不如看板和前进数控制法有效。
“漏斗模型”是典型的负荷导向型生产控制方法。
其实施要求具备良好的数据收集和数据处理系统,以及工作地基本数据的及时反馈系统.(要求掌握每天车间的生产情况,每周生成一次有关监测表。
因此,需要一定的投资和管理费用。
对于漏斗模型在生产系统中应用的看法不同于传统生产管理追求设备高利用率、忽视市场需求变化的思想倾向.“漏斗模型”的理论出发点是存量控制思想,即通过有目的地安排生产任务(确定生产任务的容和数量,以及任务投料和完工日期)、使工作地在制品量维持在一定的水平上,从而确定和控制工作地平均通过时间及设备利用率.为实现这一目标,必须重视生产过程的控制。
因此,“漏斗模型”方法的核心是建立计算机系统集中监测生产系统的状态,并利用负荷导向型任务投料算法,制定滚动的投料和作业计划。
所以,它与看板法相比,应用更为灵活广泛。
“漏斗模型”的两个基本变量是在制品库存和平均通过时间。
因此,首先应确定计划期(每周)适当的在制品库存水平,而确定在制品库存水平需要考虑平均通过时间、设备利用率、预测精确度、顾客的特殊要求及企业各部门间的利益关系等众多因素.其次,确定计划平均通过时间主要取决于计划停留时间,它有较大的不确定性,如果出现意外的紧急任务,将可能导致“通过时间综合症”。
要提高PPS系统的抗干扰能力,我们需要将准时生产制(JTT)思想引入“漏斗模型”,如设备预防维修、培养多能工、设置制造单元等。