漏钢统计情况
大方坯连铸机粘结漏钢的原因分析及控制23

大方坯连铸机粘结漏钢的原因分析及控制摘要:方坯连铸漏钢的类型及原因诸多,影响因素复杂,本文通过某次漏钢后残留的坯壳进行科学的检验及分析确定出了漏钢的类型,结合当时实际工况及技术参数阐述了漏钢的原因及提出应对措施。
关键词:方坯粘结漏钢原因措施1.前言:通常把断面大于220mm×220mm的铸坯称为大方坯,大方坯主要用于轧制硬线、管材、棒材、型材以及轴承钢、齿轮钢等特殊用钢。
大方坯连铸机对比小方坯铸机设备精度更高,投资成本更大,如果生产中发生发生漏钢事故危害极大,不但对设备造成较大损失还会导致停机甚至危害操作人员的安全。
国内冶金工作者对连铸的漏钢原因做了大量的研究及实践,本文主要针对韶钢7号大方坯连铸机某次漏钢进行完整的取样及分析找出了漏钢的类型及原因提出控制措施。
2.主要工艺及装备:韶钢7号连铸机是2013年从达利涅引进的5机5流大方坯连铸机,主要断面为280×280、320×320、320×425,铸机半径14m,冶金长度27m,拥有E-EMS、F-EMS,动态轻压下等技术,结晶器铜管为多锥度弧形,常用拉速0.5-0.9m/min。
3.漏钢原因调查3.1生产过程3.1.1漏钢炉次成份及温度3.1.3保护渣使用情况:所用结晶器保护渣为生产日期为2016年1月23日,2月中旬开始在7号机低碳系列钢使用,3月16日在15CrMoG钢四炉单流统计,渣耗量约0.60 kg/t。
3.1.4结晶器铜管磨损情况:1流铜管使用次数为342炉钢,与目标使用次数800炉相比,炉次较少,从漏钢后的铜管内壁状态反映铜管磨损状况良好。
漏钢后的铜管内壁情况如下图片:3.1.5振动台运行情况:现场调查未发现1流结晶器振动台运行异常的情况。
3.1.6浸入水口插入深度情况:由于漏钢1流浸入水口未能保留,其它流水口插入深度在120-130mm,渣线浸蚀及插入深度正常。
3.2 取样在漏钢后残留坯壳(650mm)上取样,从结晶器液面开始每隔90mm采用锯切方法截取横断面试样,其编号为1-4,试样宽度为90mm,最后做横截面热酸浸。
唐钢降低小方坯连铸漏钢工艺措施

03 1 ) 60 6
Ab ta t Ba e h t tsi fse lla a e i 01 sr c : s d t e sait o t e e k g n 2 0,i i nay e h e t r sa d m e ha s fic u i n cs t sa lz d t e f au e n c nim o n l so
河一
北m
M EAS URES T0 REDUCE S TEEL LEAKAGE N LLET I BI CAS TⅡ G
X u n Zo g u, a a f n a n y Lu n H ie g
冶~
全一
( . tewok ,T n sa rn a d SelCo a y,He e r n a d Se lGru No 2 Se l rs a g h n Io n te mp n b iIo n te o p,T n s a a gh n,He e , bi
损 坏设备 , 危及操作 人员安 全 。近 年来 , 着 国内连 随
铸工艺技术 的进 步 , 方坯 连 铸漏 钢 事故 得 到 了有 小 效 地抑制 , 仍 是一 种 不能 完 全 避免 的事故 。要 保 但
10个 品种 。铸 机 采 用 定 径 水 口和塞 棒 控 制 两 种 , 0
浸入式水 口加 保护 渣进行保 护浇铸 。
进行分析 , 并从 工艺 等方 面 采 取相 应措 施 控 制漏 钢
事 故 的发 生 。
2 铸 机 参 数 及 漏 钢 情 况
2 1 连 铸 机 的 主 要 工 艺参 数 .
唐 钢 二 钢 轧 厂 有 2 台 四 机 四 流 、 台 六 机 六 流 3
方坯连铸 机 , 际年 产能 力 3 0万 t浇 铸 的断 面有 实 8 ,
常见圆坯连铸漏钢原因及预防措施

常见圆坯连铸漏钢原因及预防措施杨文明胡茂会贾宁波易良刚攀钢集团成都钢矾有限公司摘要:本文通过漏钢形貌的分析和漏钢坯壳的解剖,结合生产现场实际情况,分析漏钢原因,提出解决措施。
0 前言连铸生产过程中所发生的事故,受损害最大的是漏钢,漏钢会造成设备的损坏,连铸停机,生产被迫中断,直接影响连铸机的产量,降低经济效益。
因此,在组织生产中应千方百计来避免连铸漏钢事故的发生。
1 生产工艺攀成钢公司电炉炼钢厂为搬迁改造工程,引进德国西门子70t高阻抗超高功率电弧炉+LF+VD+三流圆坯连铸机的生产工艺。
三流圆坯连铸机为弧型连铸机,弧形半径R=12m,流间距L=1700mm,结晶器铜管长度700mm,单锥度(0.9-1.4%)结晶器,采用长水口(吹Ar)保护+浸入式水口(保护渣)浇注,中间包通过塞棒控制注流,二冷气雾冷却。
主要生产规格为Ф220mm,Ф280mm、Ф350mm 和Ф388mm、Ф430mm的圆坯,相应规格目标拉速分别为1.25、0.90、0.55、0.45、0.36m/min。
最常见的漏钢规格是:Ф220mm和Ф350mm规格,2010年1-6月,所有规格的钢种的综合漏钢率0.61%,Ф350 mm规格浇铸低碳钢180炉,发生漏钢13次,漏钢率为2.41%。
2 常见漏钢形貌从漏钢形貌上可将圆坯的漏钢分为3种:1、裂纹漏钢2、粘结漏钢3、夹渣漏钢,我公司最常见的漏钢是裂纹漏钢,约占总漏钢的80%以上。
2.1夹渣漏钢夹渣漏钢的漏钢口呈圆形,直径10mm左右。
夹渣一般发生在皮下3-5mm,夹渣的直径3-5mm,也呈圆形。
2.2粘结漏钢粘结漏钢的漏钢口呈椭圆形或V形或锯齿形,漏口偏大,一般发生在浇铸前期,特别是第一炉钢。
2.3裂纹漏钢裂纹漏钢漏口纵向破裂,长度500-1000mm,漏口最宽处可达50mm。
从漏钢口往上延伸可以看见有裂纹,且多数伴随凹陷产生。
3 漏钢成因3.1夹渣漏钢出结晶器时,夹渣处铸坯钢质坯壳较薄,且强度低,经受不住钢水的静压产生漏钢。
连铸漏钢原因分析

该炉钢 的 有 关 连 铸 参 数 列 于 表 %。从 钢 种、 铸 坯 断 面 尺 寸 、过 热 度 和 拉 坯 速 度 的 匹 配 来 看 ,未 见 高 温 高 拉 速 的 违 规 操 作 ;结 晶 器 的 冷 却 水 量 、水 温及二冷控制均无异常。
表 ! 漏钢炉次钢水的化学成分( !")
#
!
)* +, -
) !. /01 2* !3
# $ #45 # $ 675 6 $ %5" # $ #67 # $ ##8 5 # $ #(( # $ #%" # $ #6( # $ #66
调查中发现,该 炉 钢 首 次 在 该 钢 种 上 使 用 非 预熔型机混保 护 渣,浇 铸 过 程 结 晶 器 内 钢 液 面 上 渣 条 频 繁 产 生 ,捞 出 后 发 现 多 夹 有 烧 结 状 团 块 ,液 渣层厚度偏薄,一般低于 & 99。
!""# 年 $" 月
%&’()*+ !""#
·经 验 交 流·
钢铁研究
,*-*.+&/ (0 1+(0 2 3’**4
连铸漏钢原因分析
第 # 期(总第 $56 期)
7( 8 # 晓 林 ,杨 治 争 (武汉钢铁集团公司 技术中心,湖北 武汉 5;""<")
出结晶器后,在高温下很难承受住拉应力、收缩应 力和钢水静压力的作用。
板坯连铸机漏钢成因分析及预防措施

;: 常规板坯连铸机参数及漏钢情况
; 5 9: 常规板坯连铸机的主要工艺参数 酒钢第二炼钢常规板坯连铸机主要工艺参数见 表 8。
第 ! 期8 8 8 8 8 8 8 8 8 8 8 8 程子建: 板坯连铸机漏钢成因分析及预防措施8 8 8
表 !" !##$ % !##& 年逐月漏钢情况
项目 产量 ( +) 综合合格率 (, ) 漏钢次数 !""# 年 %月 )’ """ **- )) ’ !月 $* #’* **- ) % &月 )) %#" **- $ ! ’月 $$ ("" **- )# % (月 ** ’&# **- ) % #月 )# &!$ **- )’ % $月 )" ((’ **- *’ & )月 $% $&# **- *& " *月 #% *&* **- *& " %" 月 !* ($& **- *! " %% 月 ($ )&" **- *$ " %! 月 $$ !’) **- *) " !""$ 年 %月 #"#&) **- *) " !月 #"""" **- *( " 合计
(
% "%’ (*" **- )* %&
表 ’" 漏钢情况统计结果
次数 % ! & ’ ( # $ ) * %" %% %! %& 时间 !""#."%."! !""#."%.%" !""#."%.&" !""#."%.&" !""#."!.%! !""#."&.") !""#."&.%# !""#."’.%! !""#."(.%( !""#."#.!( !""#."$."$ !""#."$.%$ !""#."$.%) 钢种 //’"" //’"" //’"" //’"" //’"" //’"" 5!&(67 5!&(6 5!&(6 ( 改) 5!&(67 ( 改) 5!&(67 ( 改) 5!&(67 ( 改) 5!&(67 ( 改) 规格 %#" 0 (!" %#" 0 (!" !!" 0 (&" !!" 0 (&" !!" 0 (&" !!" 0 (&" !!" 0 (&" !!" 0 (&" !!" 0 (&" !!" 0 (&" !!" 0 (&" !!" 0 (&" !!" 0 (&" 炉次 换包第 ! 炉 换包第 ! 炉 换包第 ! 炉 第( 炉 第) 炉 第 %& 炉 第( 炉 第# 炉 第 %! 炉 第* 炉 第# 炉 第) 炉 第( 炉 拉速 %- ! 1 2 134 %- !& 1 2 134 %- "( 1 2 134 %- " 1 2 134 %- "( 1 2 134 %- "& 1 2 34 %- "( 1 2 134 "- $( 1 2 134 "- *( 1 2 134 %- ") 1 2 134 %- " 1 2 134 %- " 1 2 134 "- $( 1 2 134 漏钢位置 内弧距坯头 #(" 11, 中间位置 内弧出结晶器, 距坯头 )%" 11, 中间位置 内弧中部距坯头 *"" 11 处 内弧中部偏西距结晶器上口 *"" 11 处 漏钢部位位于窄右出结晶器足辊位置 内外弧距结晶器上口 % &)" 11 外弧正中部, 漏钢点距结晶器上口 )(" 11 外弧中部偏西距结晶器上口 )"" 11 处 内弧出结晶器, 距坯头 )%" 11, 中间位置 内弧出结晶器下口位置 外弧宽面下口处 漏钢位置在结晶器窄左距上口 % 1 处 外弧宽面结晶器下口中部 漏钢形式 粘结漏钢 粘结漏钢 粘结漏钢 粘结漏钢 粘结漏钢 卷渣漏钢 粘结漏钢 粘结漏钢 粘结漏钢 粘结漏钢 粘结漏钢 机械外力划破坯壳 粘结漏钢
239唐钢降低连铸漏钢率

4
5
1.完善中间包称量系统 中间包液位 稳定中间 2.中间包液位稳定保持在400mm以 上。 不稳定 包液位
基本实现了中间 包液位恒定操作
一、二、三 2010年7月-9 期现场 月
李洋 代斌 栾海风 马昆 朱祥亮
制表:梁娟
审核:李波
2010年5月
八. 对策实施
1、对于工人进行理论培训,对于违反规定者严加考核
目标确定后,小组成员结合车间实际,从“人、机、料、法、环” 等五大方面找出了影响漏钢率的15条因素。
人
质量意识差 结晶器振动不平稳
机
钢水纯净度不高
料
钢水过热度不合适
水口不对中
结晶器锥度不合适
保护渣性能不好 钢种特性
开浇前准备工作不够
保护渣加入不均
漏 钢 率 高
考核不严细
管理不到位
中间包液位不稳
拉速不稳 中间包耐材脱落
二. 小组简介
1. 小组情况
小组名称 降 低 连 铸 漏 钢 率 QC 成立日期 小组 降低连铸漏钢率 2010 年 1 月
课题名称
平均 QC 受 72 学时 教育时间 小组 类型 攻关型
活动周期 小组人数 活动效果
2010 年 1 月~ 12 月 14 人 全年漏钢率降到 0.05% 以内
二. 小组简介
铸坯中夹杂数量平均 减少50% , 大于100μm夹杂数量 平均减少80% 。
转炉、吹 氩平台, 2010年5月-9 月 连铸浇钢 平台
李洋 代斌 栾海风 朱祥亮
3
1.完善结晶器使用管理规定。 采用合适 2.上线的结晶器必须保证其锥度 结晶器锥度 的结晶器 控制在0.6%/m~1.2%/m。 不合适 倒锥度
连铸机典型漏钢的特征及成因分析
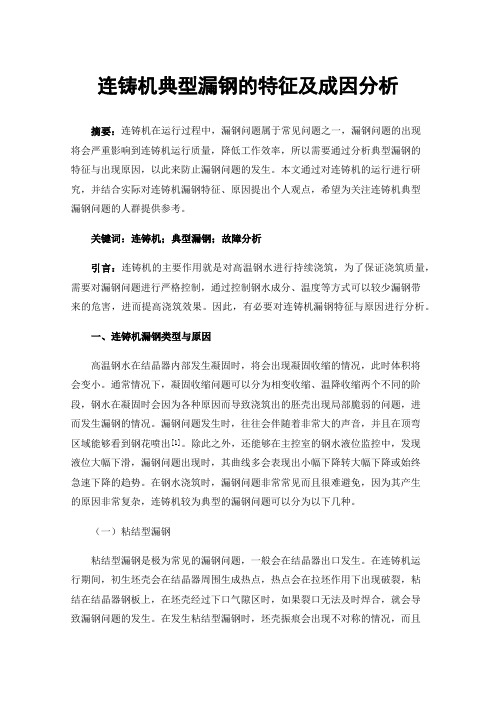
连铸机典型漏钢的特征及成因分析摘要:连铸机在运行过程中,漏钢问题属于常见问题之一,漏钢问题的出现将会严重影响到连铸机运行质量,降低工作效率,所以需要通过分析典型漏钢的特征与出现原因,以此来防止漏钢问题的发生。
本文通过对连铸机的运行进行研究,并结合实际对连铸机漏钢特征、原因提出个人观点,希望为关注连铸机典型漏钢问题的人群提供参考。
关键词:连铸机;典型漏钢;故障分析引言:连铸机的主要作用就是对高温钢水进行持续浇筑,为了保证浇筑质量,需要对漏钢问题进行严格控制,通过控制钢水成分、温度等方式可以较少漏钢带来的危害,进而提高浇筑效果。
因此,有必要对连铸机漏钢特征与原因进行分析。
一、连铸机漏钢类型与原因高温钢水在结晶器内部发生凝固时,将会出现凝固收缩的情况,此时体积将会变小。
通常情况下,凝固收缩问题可以分为相变收缩、温降收缩两个不同的阶段,钢水在凝固时会因为各种原因而导致浇筑出的胚壳出现局部脆弱的问题,进而发生漏钢的情况。
漏钢问题发生时,往往会伴随着非常大的声音,并且在顶弯区域能够看到钢花喷出[1]。
除此之外,还能够在主控室的钢水液位监控中,发现液位大幅下滑,漏钢问题出现时,其曲线多会表现出小幅下降转大幅下降或始终急速下降的趋势。
在钢水浇筑时,漏钢问题非常常见而且很难避免,因为其产生的原因非常复杂,连铸机较为典型的漏钢问题可以分为以下几种。
(一)粘结型漏钢粘结型漏钢是极为常见的漏钢问题,一般会在结晶器出口发生。
在连铸机运行期间,初生坯壳会在结晶器周围生成热点,热点会在拉坯作用下出现破裂,粘结在结晶器钢板上,在坯壳经过下口气隙区时,如果裂口无法及时焊合,就会导致漏钢问题的发生。
在发生粘结型漏钢时,坯壳振痕会出现不对称的情况,而且在多数时间都会在结晶器的内部残留一截坯壳。
粘结型漏钢的出现原因大致可以分为以下几种。
1.保护渣当保护渣自身的理化性能无法与钢种、钢水温度等参数匹配时,就有可能出现粘结型漏钢的问题,因为保护渣的熔化速度、熔点等参数性能都将会影响到连铸机的浇筑质量。
浅析漏钢的原因及预防

浅析漏钢的类型及预防连铸二车间技术组-郭幼永一、前言:板坯漏钢的形式多种多样但重点主要集中在粘结漏钢和开浇起步后的漏钢。
本文简要介绍常见漏钢的类型、漏钢的起因及相应的预防措施。
为各班组在实际浇钢过程中提供参考便于降低漏钢事故的发生。
二、漏钢的类型1、粘结漏钢粘结漏钢是连铸生产过程中的主要漏钢形式,据统计诸多漏钢中粘结漏钢占50%以上。
所谓粘结的引起是由于结晶器液位波动,弯月面的凝固壳与铜板之间没有液渣,严重时发生粘结。
当拉坯时磨擦阻力增大,粘结处被拉断,并向下和两边扩大,形成V型破裂线,到达出结晶器口就发生漏钢。
粘结漏钢的发生有以下情况:内弧宽面漏钢发生率比外弧宽面高(大约3:1);宽面中部附近(约在水口左右300mm)更易发生粘结漏钢;大断面板坯容易发生宽面中部漏钢;而小断面则发生在靠近窄面的区域;铝镇静钢比铝硅镇静钢发生漏钢几率高;保护渣耗量在0.25kg/t钢以下,漏钢几率增加。
2、发生粘结漏钢的原因:1)、形成的渣圈堵塞了液渣进入铜管内壁与坯壳间的通道;2)、结晶器保护渣Al2O3含量高、粘度大、液面结壳等,使渣子流动性差,不易流入坯壳与铜板之间形成润滑渣膜。
3)、异常情况下的高拉速。
如液面波动时的高拉速,钢水温度较低时的高拉速。
4)、结晶器液面波动过大,如浸入式水口堵塞,水口偏流严重,更换钢包时水口凝结等会引起液面波动。
3、防止粘结性漏钢预防措施在浇注过程中防止粘结漏钢的对策有:(1)监视保护渣的使用状况,确保保护渣有良好性能。
如测量结晶器液渣层厚度经常保持在8~15mm,保护渣消耗量不小于0.4kg/t钢,及时捞出渣中的结块等。
(2)提高操作水平,控制液位波动。
(3)确保合适的拉速,拉速变化幅度要小。
升降拉速幅度以0.05m/min为宜。
(4)严格控制钢水质量,提高钢水洁净度,减少钢中夹杂物。
(5)加强对结晶器铜板的检查,发现有龟裂或其他影响铜板平整度的因素,必须进行打磨处理,如果问题严重必须下线。
双流板坯连铸机漏钢率分析

双流板坯连铸机漏钢率的分析【摘要】自投产以来,漏钢率一直比较高,严重影响了生产的顺行,通过对近年来漏钢事故数据的分析,采取了一系列措施,在降低漏钢率方面发挥了有效的作用,很好地控制了漏钢事故的发生。
【关键词】漏钢;热流;摩擦力前言在连铸生产过程中,漏钢作为最严重的生产事故,会对整个生产过程造成重大影响,在处理漏钢过程中工人劳动强度增大,还极易发生安全事故。
因此,必须对各种形势的漏钢进行分析和研究,找出预防和减少漏钢事故的发生的措施。
1.2010年漏钢的统计与分析2.漏钢形式及原因分析连铸漏钢的形式较多,主要有开浇漏钢、悬挂漏钢、裂纹漏钢、粘结漏钢、卷渣漏钢等。
2.1开浇漏钢原:开浇漏钢是指引锭头刚拉出结晶器即发生的漏钢事故,主要是由操作的原因引起。
主要原因有:(1).结晶器密封不良,冷料加入不合适,铁屑层过薄等,钢水从缝隙入渗出。
(2).起步时间过早,凝固坯壳强度不够,造成起步拉断。
(3).起步过程中有异物随钢流进入结晶器坯壳处,造成坯壳出结晶器后漏钢。
2.2悬挂漏钢:结晶器角缝过大,铜板划伤,致使在结晶拉坯阻力增大造成坯壳拉断漏钢2.3裂纹漏钢:纵裂漏钢是由于保护渣选择不当,保护渣流动不均匀,结晶器传热不均导致坯壳厚度不均匀,冷却时坯壳破裂而产生的。
角部裂纹是沿结晶器窄面凝固厚度不够的坯壳收缩时受到拉伸应力而破裂,拉伸应力是由结晶器窄面锥度减小和窄面传热不均造成的。
2.4卷渣漏钢:由于结晶器渣块或异物裹入凝固壳局部区域,使坯壳厚度太薄造成。
2.5粘结漏钢:粘结性漏钢主要是指结晶器液面波动或者其它原因,导致弯月面附近润滑效果不好,坯壳与结晶器壁之间发生粘结,拉坯摩擦阻力增大,粘结处被拉裂,并向下和两侧扩展,形成“v”破裂线,随着铸坯往下移动,钢水直接与铜板接触,由于冷却水的作用,形成新的坯壳,随着结晶器的振动和铸坯的继续下移,此过程重复出现,直到薄坯壳在出结晶器下口时被拉裂,出现漏钢现象。
漏钢后坯壳四周明显不均匀。
连铸介绍

为什么高效连铸特别强调保证浇注钢水温度2010-03-19 22:02适宜的钢水温度(不同的钢种有不同的温度要求)可使高效连铸生产获得高质量的铸坯;而钢水过热度提高,钢坯坯壳减薄,钢水易于二次氧化,夹杂物增多,耐材严重冲蚀,易出现较肚、漏钢、柱状晶发达、中心偏析严重、缩孔严重等一系列问题。
高效连铸的生产实践和理论都得出了相同结论,即低温浇铸是提高拉速及改善铸坯质量的重要手段之一。
当然,温度低要有界限,温度过低会出现钢水流动性差、水口冻结、夹杂物难以上浮等问题。
所以高效连铸特别强调要保证浇注钢水温度;即钢水浇注温度均匀稳定地保证在规定的范围内。
高效连铸机的钢包支撑装置的特点高效连铸机的钢包支撑无论是回转台还是三包位行走小车,都应该做到换包快捷,易于上水口,易于阻挡下渣,最好能配有耐用的动态称重装置,以适合多炉连浇、保护浇铸等高效连铸的基本要求。
高效连铸机对中间包的要求(1)中间包容量大,钢水液面深度要保证足够的夹杂物上浮时间。
目前,年产60万吨的4机4流高效方坯连铸机中间包容量可达25吨,液面溢流标高900mm。
(2)中间包要有最佳温度场及热流分布(通过内腔形状,坝、挡墙等方法获取),以达到各水口之间的温度尽可能的均匀,即外侧水口与内侧水口温度差在±3℃为好。
(3)高效连铸由于连浇炉数高,要求中间包外壳体及底部不变形;炉衬经久耐用,最好是整体喷涂。
耐材不易腐蚀脱落污染钢水,尤其水口要经久耐用,最好配置水口快速更换装置。
高效连铸机对中间包车的要求高效连铸机作业率高,因此要求中间包车的事故率要低。
中间包车的升降系统要可靠耐用,升降平稳,以适应保护浇铸的要求。
称重装置尤其应可靠,使用寿命长,保证监控中间包液面高度,使中间包液面稳定,波动小,满足高效连铸的需要。
中间包车的横向移动要平稳精确,保证水口与结晶器的准确对位。
目前小方坯上多采用高低腿门式中间包车,这种中间包车易于操作,采用液压驱动,更快捷、平稳。
150t连铸LZ钢漏钢原因分析及对策

O . 1 5
4
0 . 1 6
l
总计
1 4 2
热速度呈下降状态 ;一般设计水速为 8 m / s ~1 0 m / s 时水流呈层
流状 , 此时吸热速度基本稳定 。 而1 #连铮 £ 产初期, 结晶器水量设定为 1 2 5 m 3 / h ~ 1 3 5 m 3 / h , 水的流速大于 1 2 m / s , 生产 L Z 钢时, 结晶器进出水温差为 4 ℃~ 4 6℃ ( 结占 酯趱 出水温差腔制在 6℃~ 8 ℃为宜) , 说明结晶器冷却水带走
1 3 m m。)
3 . 结晶器水量的计算。结 晶器水量的计算如下 :
Q m a x = [ ( L + 2 m) 2 - L Z ] X 1 0 0 X 6 0
Q mi n  ̄( L + 2 m) 2 _ L 2 1 X 8 0 X 6 0
式中Q ma x , Q m i n分别 为结 晶 器 冷 却 水 最 大 流 量 ,最 小
3 7 . H
l 3
3 7 . 1 4
0
0
O
0
3 5
1 0 0
之间, 连铸坯在凝固过程中, 当 8铁 一 铁转变时发生包晶反应, 并伴
随饺大线收缩, 坯壳与铜壁之间过早形成气隙, 此时导出热流小, 坯壳薄, 裂纹敏感I 生强, 同时作用于坯壳 匕 的应力超过钢的高温允许强度, 在坯壳
流量 ; L为 方坯 铜 管结 晶器 的外边 边 长 , d m;
( 2 ) 结 晶器铜管锥 度的影响 。 结 晶器铜管的倒锥度能更好地
适应坯壳收缩 , 减 少气 隙 , 提高传热效率。但使用过程中结晶器 内壁 与铸坯表 面间 的摩 擦使 结 晶器 内壁磨 损 ,从而 逐渐失 去
漏钢分析报告

漏钢分析报告1. 引言漏钢是指钢铁制品在加工过程中或使用过程中出现的钢材缺陷,其具体表现为钢材表面或内部出现不连续性的裂纹、砂眼、气孔等。
漏钢不仅会影响钢材的外观质量,还会降低钢材的强度、韧性和使用寿命。
本报告旨在对漏钢问题进行分析,排查漏钢的原因,并提出解决方案。
2. 漏钢原因分析2.1 材料原因钢材的成分和质量直接影响到钢材的使用性能。
如果钢材中存在夹杂物、夹杂气泡、非金属夹杂物等,在加工过程中很容易导致漏钢问题的发生。
因此,我们首先要检查钢材的材料质量,确保其符合相关的标准和要求。
2.2 设备原因钢材的加工设备也可能是导致漏钢问题的原因之一。
设备因老化、磨损、维护不到位等原因,可能导致钢材的加工过程中产生过大的摩擦或应力集中,进而引起钢材的缺陷。
因此,我们需要对加工设备进行定期的检修和维护,确保设备的正常运行。
2.3 工艺原因工艺参数的不合理设置也可能是导致漏钢问题的原因之一。
比如,熔炼温度过高或过低、加热时间过长或过短等,都可能导致钢材组织的不均匀或含有过多的气体,从而引起漏钢问题。
因此,我们需要对工艺流程进行优化,确保每一步的参数设定合理。
3. 解决方案3.1 完善原材料检测加强对钢材原材料的检测,确保原材料的质量符合要求。
可以采用无损检测技术,如超声波检测、X射线检测等,对钢材进行全面、准确的检测。
3.2 加强设备维护定期对加工设备进行检修和维护,确保设备的正常运行。
及时更换老化和磨损的配件,保证设备的精度和稳定性。
3.3 优化工艺流程对工艺参数进行优化,确保每一步的参数设定合理。
可以借助数值模拟和实验分析来确定最佳的工艺参数,减少漏钢问题的发生。
4. 漏钢监控与预警4.1 建立漏钢监控系统建立漏钢监控系统,通过实时检测、分析漏钢相关数据,提前发现潜在的漏钢问题。
可以采用传感器、图像识别等技术手段,对钢材进行在线监测。
4.2 制定漏钢预警方案针对漏钢问题制定相应的预警方案,在出现漏钢问题之前能够及时发出预警信号。
小方坯角部纵裂漏钢的原因分析
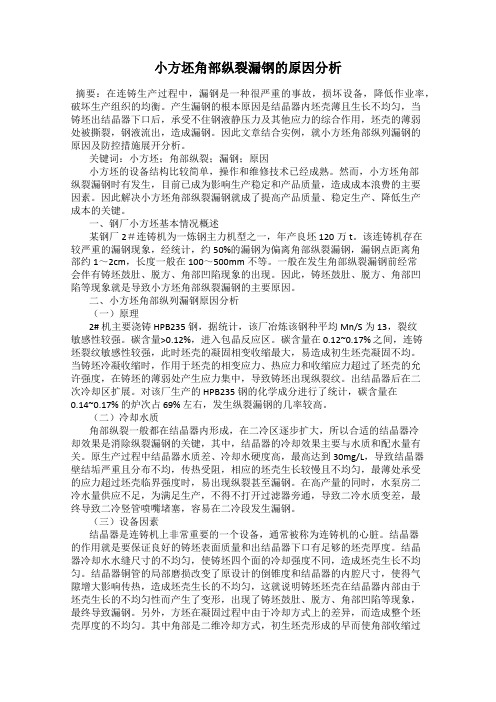
小方坯角部纵裂漏钢的原因分析摘要:在连铸生产过程中,漏钢是一种很严重的事故,损坏设备,降低作业率,破坏生产组织的均衡。
产生漏钢的根本原因是结晶器内坯壳薄且生长不均匀,当铸坯出结晶器下口后,承受不住钢液静压力及其他应力的综合作用,坯壳的薄弱处被撕裂,钢液流出,造成漏钢。
因此文章结合实例,就小方坯角部纵列漏钢的原因及防控措施展开分析。
关键词:小方坯;角部纵裂;漏钢;原因小方坯的设备结构比较简单,操作和维修技术已经成熟。
然而,小方坯角部纵裂漏钢时有发生,目前已成为影响生产稳定和产品质量,造成成本浪费的主要因素。
因此解决小方坯角部纵裂漏钢就成了提高产品质量、稳定生产、降低生产成本的关键。
一、钢厂小方坯基本情况概述某钢厂2#连铸机为一炼钢主力机型之一,年产良坯 120万t。
该连铸机存在较严重的漏钢现象,经统计,约50%的漏钢为偏离角部纵裂漏钢,漏钢点距离角部约1~2cm,长度一般在100~500mm不等。
一般在发生角部纵裂漏钢前经常会伴有铸坯鼓肚、脱方、角部凹陷现象的出现。
因此,铸坯鼓肚、脱方、角部凹陷等现象就是导致小方坯角部纵裂漏钢的主要原因。
二、小方坯角部纵列漏钢原因分析(一)原理2# 机主要浇铸 HPB235 钢,据统计,该厂冶炼该钢种平均 Mn/S 为 13,裂纹敏感性较强。
碳含量>0.12%,进入包晶反应区。
碳含量在 0.12~0.17% 之间,连铸坯裂纹敏感性较强,此时坯壳的凝固相变收缩最大,易造成初生坯壳凝固不均。
当铸坯冷凝收缩时,作用于坯壳的相变应力、热应力和收缩应力超过了坯壳的允许强度,在铸坯的薄弱处产生应力集中,导致铸坯出现纵裂纹。
出结晶器后在二次冷却区扩展。
对该厂生产的 HPB235 钢的化学成分进行了统计,碳含量在0.14~0.17% 的炉次占 69% 左右,发生纵裂漏钢的几率较高。
(二)冷却水质角部纵裂一般都在结晶器内形成,在二冷区逐步扩大,所以合适的结晶器冷却效果是消除纵裂漏钢的关键,其中,结晶器的冷却效果主要与水质和配水量有关。
关于对板坯漏钢及结晶器铜板有关情况的调研反馈
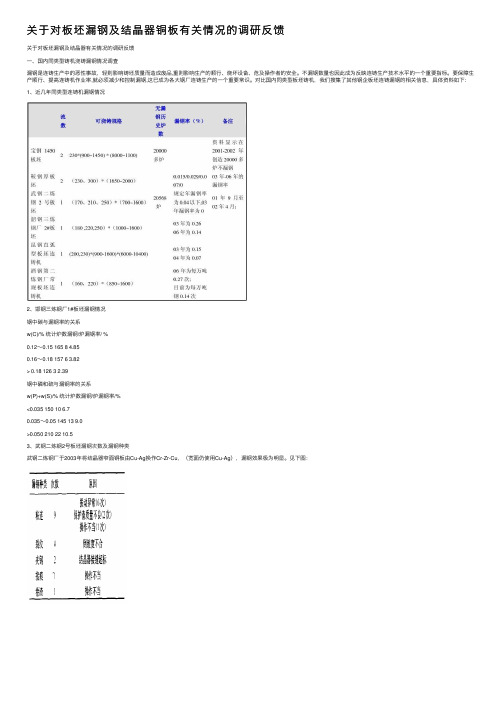
关于对板坯漏钢及结晶器铜板有关情况的调研反馈关于对板坯漏钢及结晶器有关情况的调研反馈⼀、国内同类型铸机浇铸漏钢情况调查漏钢是连铸⽣产中的恶性事故,轻则影响铸坯质量⽽造成废品,重则影响⽣产的顺⾏、烧坏设备、危及操作者的安全。
不漏钢数量也因此成为反映连铸⽣产技术⽔平的⼀个重要指标。
要保障⽣产顺⾏、提⾼连铸机作业率,就必须减少和控制漏钢,这已成为各⼤钢⼚连铸⽣产的⼀个重要常识。
对⽐国内同类型板坯铸机,我们搜集了其他钢企板坯连铸漏钢的相关信息,具体资料如下:1、近⼏年同类型连铸机漏钢情况2、邯钢三炼钢⼚1#板坯漏钢情况钢中碳与漏钢率的关系w(C)/% 统计炉数漏钢/炉漏钢率/ %0.12~0.15 165 8 4.850.16~0.18 157 6 3.82> 0.18 126 3 2.39钢中磷和硫与漏钢率的关系w(P)+w(S)/% 统计炉数漏钢/炉漏钢率/%<0.035 150 10 6.70.035~0.05 145 13 9.0>0.050 210 22 10.53、武钢⼆炼钢2号板坯漏钢次数及漏钢种类武钢⼆炼钢⼚于2003年将结晶器窄⾯铜板由Cu-Ag换作Cr-Zr-Cu,(宽⾯仍使⽤Cu-Ag),漏钢效果极为明显。
见下图:4、攀钢⼀号板坯连铸机5、国内钢企个⼈浇铸不漏钢先进指标1、2007年10⽉,武钢⼆炼钢连铸机长陈建钢连续5年浇钢7500炉50万吨⽆漏钢事故,硅钢浇铸质量合格率99.96%,再次刷新个⼈历史记录。
因此成为武钢的“防漏”专家,被称为“浇钢王”。
2、武钢三炼钢⼚3号连铸机机长马江⽣总结出⼀套预防漏钢的先进操作法。
⾃1998年8⽉以来,浇铸1.1万多炉,300万吨钢⽔不漏钢,创下了个⼈浇铸钢⽔不漏钢的国内最好⽔平。
3、攀钢新钢钒炼钢⼚板坯浇钢⼄班Ⅱ流刘关洪所带领的班组连浇不漏钢炉数达到15004炉,在攀钢率先突破1.5万炉不漏⼤关,这也是国产⼤坯连铸机⾸次达到这⼀⾼度。
韶钢宽厚板连铸机粘结漏钢的原因和预防措施

韶钢宽厚板连铸机粘结漏钢的原因和预防措施朱远坚黄回亮杨帆(广东韶关钢铁公司炼钢部, 韶关 512123)摘 要 本文分析韶钢宽厚板连铸机粘结漏钢的原因,并提出相应的预防措施。
关键词 连铸机 粘结漏钢 漏钢预报系统Causes and Countermeasures for Sticking Breakout inWide Slad CasterZhu Yuanjian Huang Huiliang Yang Fan(Shaoguan Iron and Steel Company, Shaoguan, 512123)Abstract The paper analyzes the reasons of sticking breakout in the wide plate continuous casting machine and takes corresponding measures.Key words wide slab casting, sticking breakout, breakout data acquisition system1 前言韶钢宽厚板连铸机于2008年10月9日一次热试成功投产,投产3年来没有发生漏钢事故,而在2012年5月,却连续发生2次黏结漏钢事故。
表1是2012年韶钢宽厚板连铸机黏结漏钢情况,可以看出在2012年中一共发生2次黏结漏钢事故,因此,降低和解决结晶器黏结漏钢势在必行,并找出相应的预防措施。
表12012年韶钢宽厚板连铸机黏结漏钢情况时间钢种断面(mm)拉速/m·min−1主要原因5.18 Q345C 2220×250 0.85 钢水条件不好,热相图温度整体下降5.26 Q345C 2220×250 0.85 钢水中[H]含量高,漏钢预报没有报警2韶钢宽厚板连铸机的基本参数铸机类型:立弯式;铸机半径:9500mm;生产断面:250/270mm×(1500~2300)mm;铸机冶金长度为31.7m。
酒钢二炼钢厂常规板坯漏钢原因调查及分析

2 酒钢 二 炼钢 厂 常规 板 坯
漏钢 情 况 调 查 、分 析
21 酒 钢 二 炼 钢 厂 常规 板 坯 漏钢 情 况 统 . 计 .见表 1 。 22简要分 析 .
钢 主要 以粘 结 性 质 为 主 ,粘 结 漏 钢 发 生 l 3次 . 比例 高 达 8 . %.其次 分 别 为偏 15 2 离 角纵 向裂纹 漏 钢 和卷渣 漏钢 。 从 漏 钢 产 生 的主 要 原 因 来 分 析 ,大
Q 4B 35
Q 3B 25 L
S_ o so 4 S 4o So
S 4O So S 4o So S 4o s o S4 o So
2 - ’
5 1 7 5 l 3
BO 1l6 2o.1 26084 06 . 36
5
粘结
中包水口穿孔 .液面波动 . 液渣流人受阻
换水口时塞棒开关幅度过大.液面波动;开浇提速过快 Q 3B 25L
Q 3B 25L
B 0 13 9 2 o .O1 1 偏离角纵裂漏钢 锥度过火 2 5 0 11 o 51.5 3
B 0138 2o. . ’ 25024 o51 2 O0 一
B0 147 2o.1 3 , 25O17 o51. - 2
率 示 于 图 2 。
生 各类 漏 钢 事故 1 5次 ,涉及 Q 3 B 、 25 L
维普资讯
酒钢科技
7
表 1 二炼 钢厂各 类漏钢 事故 统计
炉 号 生产 1 3期 中包 序 次
.
漏钢定性
主 要 原 因 分 析
钢 种
B 0 1o 3 2 o 25029 o5
板坯漏钢

板坯连铸漏钢原因分析及其防止措施楚志宝,李作鑫,杜金玉,王国强,李凯玉(济南钢铁集团总公司第一炼钢厂,山东济南 250101)摘要:通过统计分析板坯连铸生产中出现的漏钢事故,认为钢水温度低、拉速快和保护渣理化性能不合理易导致粘结漏钢;对弧不良、钢水温度高、拉速快是造成裂纹漏钢的主要原因;开浇和接头漏钢主要是中间包上水口和塞棒烘烤效果不好及出苗时间不足造成的。
提出了优化保护渣性能指标、强化设备检修精度、严格执行工艺技术规程和完善生产准备等防范漏钢的具体措施。
关键词:连铸板坯;粘结漏钢;裂纹漏钢;接头漏钢;保护渣中图分类号:TF777.1 文献标识码:BDiscussion on Breakout Reason in CC Slab and Its Countermeasures CHU Zhi-bao, LI Zuo-xin, DU Jin-yu, WANG Guo-qiang, LI Kai-yu (No.1 Steel-making Plant of Jinan Iron and Steel Group, Jinan 250101, China)Abstract:The breakout is statistically analyzed in practice production. It is shown that the breakout by sticking is caused by low temperature of molten steel and high withdrawal speed and illogicality capability of protecting slags. The most reason of cracking breakout is badness of arc and high temperature of molten steel and high withdrawal speed. The breakout reason of beginning pouring and joint is that the nozzle and stopper in the turndish are not good with firing and the exceed mould time is shortage. Then some countermeasures such as optimizing the capability of protecting slags and intensifying precision of the equipment and strictly executing the regulation of technique and perfecting the preparation of produce are put forward.Keywords:continuous casting slab;breakout by sticking;cracking breakout;joint breakout;protecting slag1 前言漏钢是连铸生产中的常见事故。
板坯连铸机漏钢原因分析及控制措施
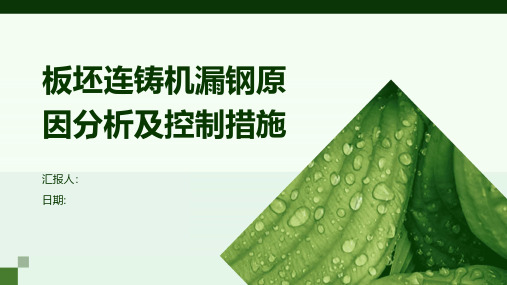
板坯连铸机漏钢原因分析及控制措施汇报人:日期:•板坯连铸机漏钢现象概述•漏钢原因分析•控制措施目录•实际应用与效果评估板坯连铸机漏钢现象概述01•漏钢现象:在板坯连铸过程中,高温钢水从铸机内部的裂缝或缺陷处泄漏出来的现象。
漏钢可能导致高温钢水接触工人或设备,引发严重的人身伤害和设备损坏。
安全风险产品质量下降生产效率降低漏钢会造成铸坯表面缺陷,严重影响板坯的质量和后续加工性能。
漏钢事故会中断连铸生产,导致生产效率降低,增加生产成本。
030201铸坯表面出现裂纹、孔洞或凹陷。
钢水泄漏导致的烟雾、火花或燃烧现象。
铸坯局部或整体形状变形。
设备异常声音或振动。
漏钢现象的常见表现漏钢原因分析02设备老化01连铸机设备长时间运行,关键部件磨损严重,未能及时更换或维修,容易导致漏钢。
设备安装精度02设备在安装过程中,如果存在安装精度不达标或者关键部位的紧固不牢固,会在运行过程中产生缝隙,进而导致漏钢。
冷却系统失效03连铸机的冷却系统对于防止漏钢起到关键作用,如果冷却系统发生故障,如冷却水流量不足、冷却水管破裂等,都会导致铸坯在凝固过程中受热不均,产生裂纹,从而引起漏钢。
拉坯速度过快在追求高效率的生产过程中,如果拉坯速度过快,会导致铸坯在凝固过程中的应力分布不均,增加漏钢的风险。
浇注温度过高如果浇注温度过高,超过了连铸机的设计能力,会导致铸坯在凝固过程中内部应力增大,容易产生裂纹,进而引发漏钢。
保护渣性能不佳保护渣对于防止铸坯表面氧化和吸气具有重要作用,如果保护渣的性能不佳,会导致铸坯表面质量下降,容易产生裂纹,从而引发漏钢。
操作人员在操作过程中,如果没有按照操作规程进行,如浇注速度控制不当、冷却水调节不及时等,都会导致连铸机运行不稳定,增加漏钢的风险。
操作不规范对于新上岗的操作人员,由于缺乏经验,对于异常情况反应不及时,也容易导致漏钢事故的发生。
缺乏经验在生产过程中,如果监控人员对于连铸机的运行状态监控不到位,如未能及时发现设备异常、工艺参数偏离等情况,也会导致漏钢事故的发生。
- 1、下载文档前请自行甄别文档内容的完整性,平台不提供额外的编辑、内容补充、找答案等附加服务。
- 2、"仅部分预览"的文档,不可在线预览部分如存在完整性等问题,可反馈申请退款(可完整预览的文档不适用该条件!)。
- 3、如文档侵犯您的权益,请联系客服反馈,我们会尽快为您处理(人工客服工作时间:9:00-18:30)。
漏钢统计情况摘要:本文分析了某某钢二炼钢厂板坯连铸机漏钢事故产生产的原因及防止板坯连铸机漏钢的措施。
采取相应控制措施之后,目前某某钢二炼钢厂常规板坯连铸机频繁漏钢的势头得到了明显的控制。
关键词:板坯粘结漏钢保护渣水口浸入深度The reason and countermeasure of slab caster breakoutYang Xiao qiang( The second steelmaking plant, JISCO,735100)Abstract: In this presentation, the breakout reason of slab cater of the second steelmaking plant was analyzed, andcorresponding precautions were adopted. Since then, the breakout event was under controlled obviously.keywords: slab caster sticking breakout mould powder immerge depth of mould nozzle1 前言某某钢第二炼钢厂常规板坯连铸机自2005年4月18日投产以来,铸机漏钢问题始终困绕着二炼钢厂的正常生产,对二炼钢厂的正常生产造成了重大的冲击,连铸机的漏钢问题成为制约二炼钢厂生产的瓶颈环节。
频繁的漏钢事故使连铸机设备的劣化趋势明显加剧,铸机检修质量无法保证。
为降低连铸机漏钢事故,二炼钢厂成立了攻关组,经过对漏钢事故的原因进行分析,采取了相应的措施,板坯连铸机结晶器漏钢事故得到了明显的控制。
2 某某钢第二炼钢厂常规板坯连铸机参数及漏钢相关情况简介2.1某某钢第二炼钢厂常规板坯连铸机的主要工艺参数表1 主要工艺参数序号项目单位技术指标铸机产量万吨/年2 生产钢种四大类二十多个品种3 连铸坯厚度mm 160,2204 连铸坯宽度mm 850~16005 铸机半径m 9.56 连铸机型式立弯式(连续弯曲,连续矫直)7 连铸机冶金长度m 31.98 铸机正常拉速m/min 1.0~1.49 结晶器长度mm 95010 振动方式液压(正弦,非正弦)11 二冷方式气水冷却(十四个控制回路)2.2漏钢统计情况从某某钢二炼钢厂常规板坯连铸机从2004年4月18日正式投产以来,共发生各种漏钢事故17次。
其中粘结漏钢14次,占到所有漏钢的82%。
其它三次漏钢为卷渣漏钢,裂纹漏钢,尾坯漏钢。
板坯连铸机漏钢事故成为制约全厂正常生产的瓶颈环节。
3 某某钢二炼钢厂常规板坯连铸机漏钢原因分析3.1粘结漏钢结晶器粘结漏钢形成的过程如图1所示。
在钢水浇注过程中,结晶器弯月面的钢水处于异常活跃的状态。
如图1所示,由于各种原因,浇铸过程中流入坯壳与结晶器铜壁之间的液态渣被阻断,当结晶器铜板与初生坯壳的摩擦力大于初生坯壳的强度时,初生坯壳被拉断,与铜板产生粘结。
这时,在被粘着的部分(1)和向下拉的铸坯(2)的界面凝固壳破断;在破断处流入钢液,重新形成新的薄坯壳(3);在振动和滑动时坯壳又被拉断,钢水补充后又形成另一个新的薄坯壳。
这一过程反复进行,直到新坯壳到达结晶器出口就产生漏钢。
3.2某某钢二炼钢厂板坯连铸机产生粘结漏钢的原因3.2.1工艺方面的原因(1)浇注过程中异常情况下结晶器液面波动大,使弯月面处的结晶器保护渣的注入时断时续,使铜板直接与钢液相接触,造成粘结漏钢。
图2 保护渣在结晶器中结构如图2所示,在浇注过程中结晶器液渣从弯月面处沿着铸坯坯壳与附着在结晶器铜上的固态渣膜之间的间隙,在铜板与坯壳之间起到润滑作用和改善传热。
当结晶器液面波动过大时,尤其在结晶器液面在大幅上涨,而振动台在下振的瞬间,结晶器铜板四周的固态渣圈对结晶器弯月面形成挤压,导致结晶器液渣层断流的机率大大增加。
另外,由于我厂的中包车升降液压系统设计原因,中包车在升降过程中不平稳,并且升降速度达到了30~40mm/s,无法调整,导致在升降中包过程中结晶器液面波动大。
根据我厂对粘结漏钢的统计,在所有粘结漏钢事故中,有五次发生在升完中包后约1分钟之内。
(2)水口插入深度与粘结漏钢的关系。
中包水口的插入深度是连铸所控制的重要工艺参数。
水口插入深度对液面波动影响较大,当插入深度深时,液面波动减少,熔渣表面的波动幅度减弱,降低保护渣卷入的可能性,但是钢水表面温度降低,这就不利于保护渣熔化,结晶器液渣层可能变薄。
同时,插入深度过深时高温区下移,对开成的坯壳造成冲击,若钢水过热度过高,可能导致形成的坯壳二次重熔,坯壳减薄,出结晶器易漏钢。
插入深度小时,结晶器液面波动大,对液渣层形成冲击,并且液渣层不均匀,易产生卷渣和粘结。
原则上在水口结构一定条件下,水口插入深度随拉速增加而增加。
根据现场的实际使用情况,二炼钢厂常规板坯连铸机的拉速控制在1.0~1.3m/min,水口插入深度控制在110~140mm,基本满足生产需要。
(3)铸机拉速调整幅度过大导致漏钢。
在大幅度提拉速过程中,容易导致结晶器液面波动大,增加了粘结的机率。
同时,在大幅度提拉速的过程中,短时间内结晶器液面层会迅速减少,根据现的实际测量,在正常浇注过程中提拉速幅度达到0.2m/min时,浇注20秒后,结晶器内的渣液层厚度由11mm减少到约7mm。
在我厂的粘结漏钢中由两次与引原因直接相关。
(4)换水口操作不当。
在换水口过程中,由于新旧水口在结晶器中大范围的搅动,造成结晶器液渣层迅速减少。
同时由于换水结晶器液面波动大,导致粘结的机率会大大增加。
(5)结晶器中结冷钢导致漏钢。
在浇注过程中,如果结晶器中结冷钢,则会使结晶器液层厚度不均匀,并且液渣的流动性变差。
同时在结冷钢处结晶器液渣层流动性变差,初生坯壳与结晶器铜板之间液渣层断流,导致粘结漏钢。
导致结晶器结冷钢的主要因素有:保护渣保温性能差、中包浸入式水口侧孔侵蚀异常、结晶器流场偏流、水口不对中。
另外由于我厂的结晶器设计是按照1.6m/min以上的工作拉速设计的,而由于种种原因,目前连铸机的正常拉速无法达到设计拉速。
对于所结晶器铜板厚度与水缝设计是否能够满足目前的拉速,目前正在核算。
(6)保护渣的适用性及选型。
连铸结晶器保护渣最主要的两项冶金功能是“润滑”和“控制传热”。
这两项功能的良好发挥是借助于熔融保护渣充填在结晶器壁和坯壳之间的缝隙内形成渣膜得以实现。
良好的保护渣对减少粘结漏钢起决定性的做用。
我厂在2005年10月份连续出现漏钢,分析原因发现保护渣在浇注过程中出现结晶器液渣层不稳定的现象,液渣层最厚达到了15mm,最薄只有不到5mm,说明此保护渣在浇注过程中出现了分熔现象,导致结晶器液渣层不稳定,在结晶器液渣层厚度降到7mm以下时,粘结漏钢的机率大大增加。
3.2.2设备方面的原因(1)结晶器振动台的精度。
我厂振动台的设计精度要求为:横向±0.1mm,纵向±0.1mm,相位差<±0.4°。
但于没有按照设备安装规范及时进行机整系统检修及精度调整,导致振动台失修,振动台的导轮与导向板之的间隙由设备安装时的0.02mm增大到了0.3mm,振动台报警频繁,结晶器振动的偏摆量明显加大。
结晶器振动偏摆加大,会使坯壳与结晶器铜板之间的间距不稳定,时大时小,从而使坯壳所受的摩擦力不均匀。
另外,振动偏摆,也会使结晶器与坏壳间缝隙大小产生差异,导致结晶器保护渣流人不均匀。
坯壳的薄弱处被拉破而导致漏钢。
(2)结晶器锥度。
由于我厂的结晶器液压自动调宽装置没有投入使用,所采取的措施对结晶器窄面使用顶杆进行固定,保证在浇注过程中结晶器锥的变化在标准范围之内。
目前结晶器窄面的锥度基本能够得到保证,但是宽面锥度经常出现严重超标的现象。
我厂某次漏钢事故后对最近两天的结晶器锥度变化情况统计情况见表2。
表2 结晶器锥度变化统计浇次宽面外弧宽面内弧窄左窄右上口下口标准0.5±0.2 0.5±0.2 6.9±0.2 1550.82 1532.61142浇次开浇0.83 0.74 0.72 0.91 0.92 0.8 6.95 7.04 1549.18 1532.2 停浇 1.59 1.18 1.02 0.21 0.62 0.39 6.45 6.75 1550.93 1532.66143浇次开浇0.56 0.75 0.69 0.67 0.86 0.64 7.11 6.87 1550.31 1532.5 停浇0.92 1.01 0.87 0.31 0.01 0.09 7.11 7.6 1550.88 1532.68144浇次开浇0.72 0.7 0.78 0.71 1.05 0.88 6.81 7 1550.46 1532.8 停浇0.41 0.05 0.04 1.16 1.33 1.08 6.87 7.07结晶器宽面锥度超标,对于保护渣的液渣流入通道产生影响,使粘结的机率大大增加。
3.3边裂漏钢这种漏钢主要是由于结晶器窄面铜板倒锥度在浇铸过程中变小或结晶器窄面铜的矩形度严重超标所致。
当窄面铜板锥度小时,坯壳与窄面铜板产生较大的气隙,使板坯窄面冷却强度降低、坯壳减薄,板坯窄面出现鼓肚现象,板坯内弧宽面距角部10~30 mm处坯壳薄弱处凹陷,并形成裂纹,进而导致漏钢。
2004年9月我厂发生大量的边部裂纹,并且导致一次边裂漏钢,主要原因为结晶器矩形度超标,结晶器内腔内弧长度比外弧长度大了1.7mm,铸坯断面尺寸内弧比外弧大10mm。
对结晶器窄面铜板进行调整之后,再没有出现铸坯边裂。
3.4开浇漏钢开浇漏钢产生的主要原因有:(1)开浇钢水热度过高,拉速起步后,使形成的坯壳二次重熔,导致出结晶器时的坯壳过薄,出结晶器后无法承受钢水的静压力。
(2)开浇前中包没有烘烤好,开浇后塞棒控制流失常,出苗时间不够强行起步并提拉速。
(3)结晶器中的冷料的冷却强度不够。
(4)开浇操作不规范,试棒时机控制不当,使钢水没有在引锭头上一次性形成完整的坯壳,导致引锭头上坯壳的强度不够。
4 减少二炼钢厂板坯连铸机漏钢的工艺优化及设备管理措施通过以上对某某钢二炼钢厂常规板坯连铸机投产以产生漏钢原因分析,主要从以下几个方面对工艺进行优化,并且加强设备的管理。
(1)要求上台钢水的[S]控制在0.020%以下,保证在凝固晶界处无FeS生成,提高初生坯壳强度,可减少粘结漏钢。
(2)坚持“恒温恒拉速”的原则,保持浇注工艺稳定,实现恒温浇注,保护渣熔化均匀,坯壳生长均匀。
(3)采用液面自动控制,使液面波动控制在±3mm。
同时在浇注过程中升降中包车时,先将拉速降到0.9m/min以下,然后点动操作,之后采用水平调整操作,使结晶器液面波动控制在最小的范围内。