硅钡冶炼操作规程
冶炼工操作规程

冶炼工操作规程一、引言冶炼工操作规程是为了确保冶炼过程的安全、高效进行而制定的操作指南。
本规程适合于冶炼工操作人员,旨在规范其操作行为,保障冶炼工作的顺利进行。
二、操作人员要求1. 冶炼工操作人员应具备相关的专业知识和技能,熟悉冶炼工艺流程和设备操作。
2. 操作人员应经过必要的培训和考核,取得相应的操作资格证书。
3. 操作人员应遵守公司的安全生产规定,严格执行操作规程,不得违章操作。
三、操作准备1. 操作人员应在操作前检查设备的运行状态,确保设备正常工作。
2. 操作人员应佩戴个人防护装备,包括安全帽、防护眼镜、防护手套等。
3. 操作人员应熟悉冶炼工艺流程和操作步骤,确保操作的准确性。
四、操作流程1. 准备工作:a. 检查冶炼炉的温度、压力等参数,确保设备处于正常工作状态。
b. 检查冶炼原料的质量和数量,确保满足冶炼工艺的要求。
c. 检查冶炼工具和设备的完好性,确保能够正常使用。
2. 开始冶炼:a. 根据冶炼工艺要求,将冶炼原料投入冶炼炉中。
b. 控制冶炼炉的温度、压力等参数,确保冶炼过程的稳定性。
c. 根据冶炼工艺要求,适时添加辅助材料,调整冶炼过程中的化学反应。
3. 监控冶炼过程:a. 定期检查冶炼炉的温度、压力、流量等参数,及时调整操作。
b. 监测冶炼炉内的燃烧情况,确保燃烧效率和燃料利用率。
c. 定期取样分析冶炼产物的成份,确保冶炼质量的稳定。
4. 冶炼结束:a. 根据冶炼工艺要求,住手冶炼过程。
b. 关闭冶炼炉的阀门和排放口,确保设备的安全。
c. 清理冶炼现场,保持工作环境的整洁。
五、安全注意事项1. 操作人员应严格遵守安全操作规程,不得擅自更改工艺参数或者操作步骤。
2. 操作人员应注意防火防爆措施,禁止在冶炼现场吸烟或者使用明火。
3. 操作人员应定期参加安全培训,提高安全意识和应急处理能力。
4. 操作人员应随时关注设备运行状态,及时发现并处理设备异常情况。
六、操作记录与报告1. 操作人员应按规定记录冶炼过程中的关键参数和操作情况。
关于硅钡钙合金冶炼工艺方式

关于硅钡钙合金冶炼工艺方式硅钡钙合金冶炼工艺方式1. 引言硅钡钙合金是一种重要的冶金原料,广泛应用于钢铁、铸造和化工等行业。
其冶炼工艺方式对于合金的质量和生产效益具有重要影响。
本文将探讨硅钡钙合金的冶炼工艺方式,从简单到复杂、由浅入深地介绍不同冶炼方式的原理、优缺点以及应用范围。
2. 真空冶炼工艺2.1 原理真空冶炼是指在高真空条件下进行的冶炼过程。
通过降低空气压力,减少氧气存在,从而避免合金中的氧化物形成。
真空冶炼可以有效控制硅钡钙合金的硫、氧含量,提高合金的纯度和品质。
2.2 优点2.2.1 纯度高:真空冶炼可以降低合金中的杂质含量,提高合金的纯度。
2.2.2 能耗低:由于真空冶炼过程中不需要加热燃烧炉,因此能耗相对较低。
2.2.3 适用范围广:真空冶炼可以适用于不同规模的工艺设备和生产线。
2.3.1 设备成本高:真空冶炼设备投资相对较高,对于小规模企业来说可能难以承担。
2.3.2 工艺复杂:真空冶炼需要精确控制多个参数,操作技术要求较高。
2.4 应用真空冶炼工艺方式广泛应用于高纯度硅钡钙合金的生产,尤其适用于要求合金纯度高、氧、硫含量极低的领域,如电子材料制造等。
3. 氧气活化冶炼工艺3.1 原理氧气活化冶炼是指在高温下,将空气中的氧气与硅钡钙合金中的碳等元素反应生成一氧化碳等气体,从而实现合金冶炼的一种方法。
通过控制氧气供给量和冶炼时间,可以得到不同成分和质量的合金。
3.2 优点3.2.1 冶炼速度快:氧气活化冶炼可以在较短的时间内完成合金的冶炼过程,提高生产效率。
3.2.2 应用范围广:氧气活化冶炼可以适用于不同规模的生产线,且灵活度较高。
3.2.3 能耗低:由于氧气活化冶炼过程中无需额外供热,因此能耗相对较低。
3.3.1 容易生成非均匀合金:氧气活化冶炼过程中,由于反应速率的不均匀性,合金可能存在非均匀成分的问题。
3.3.2 对设备和材料要求高:氧气活化冶炼需要高温环境、抗高温材料的设备,对设备和材料的要求较高。
工业硅、硅铁冶炼技术操作规程
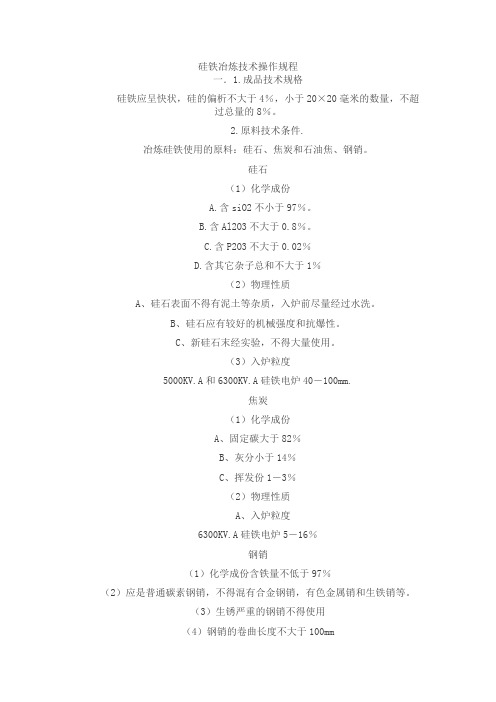
硅铁冶炼技术操作规程一.1.成品技术规格硅铁应呈快状,硅的偏析不大于4%,小于20×20毫米的数量,不超过总量的8%。
2.原料技术条件.冶炼硅铁使用的原料:硅石、焦炭和石油焦、钢销。
硅石(1)化学成份A.含siO2不小于97%。
B.含Al2O3不大于0.8%。
C.含P2O3不大于0.02%D.含其它杂子总和不大于1%(2)物理性质A、硅石表面不得有泥土等杂质,入炉前尽量经过水洗。
B、硅石应有较好的机械强度和抗爆性。
C、新硅石末经实验,不得大量使用。
(3)入炉粒度5000KV.A和6300KV.A硅铁电炉40-100mm.焦炭(1)化学成份A、固定碳大于82%B、灰分小于14%C、挥发份1-3%(2)物理性质A、入炉粒度6300KV.A硅铁电炉5-16%钢销(1)化学成份含铁量不低于97%(2)应是普通碳素钢销,不得混有合金钢销,有色金属销和生铁销等。
(3)生锈严重的钢销不得使用(4)钢销的卷曲长度不大于100mm(5)要纯净,不得混有泥土等杂质二、配料操作1、每班配料前要一次小车重量和磅秤的准确度。
2、在按照冶炼班长通知的料比组成进行配料。
每批料以200公斤硅石为基准,8500KV.A以上电炉每批料以300公斤硅石为基准。
3、称量要准确,误差正负1%,钢销要单称后再混入配料小车内。
4、每次只准称量一批料。
5、发现原料质量有变化和设备有问题时几时报告班长。
6、下班前要将配料场地清扫干净,所有的工具设备要精心保护交换。
7、下班前要把当班配料批数报告班长做好记录。
三、冶炼供电和电极操作1、正常冶炼操作使用电压:6300KV.A电炉104V-125V为宜8500KV.A电炉140V-188V为宜2、一次电压波动较大时,为保证炉用变压器正常运行和冶炼的适宜的功率,经炉长批准可在规定级别内调整二次电压。
3、严禁超负荷运行、4、三相电流应尽量保持平衡,最大波动不准超过25%。
5、冶炼保证应认真贯彻执行电器工作制度。
冶炼工操作规程

冶炼工操作规程一、概述冶炼工操作规程是为了确保冶炼过程的安全、稳定和高效运行而制定的操作指南。
本规程适用于冶炼工在冶炼作业中的操作要求和注意事项。
二、操作要求1. 安全操作冶炼工在进行操作前,必须熟悉相关设备的安全操作规程,并严格遵守安全操作规定。
在操作过程中,必须佩戴个人防护装备,如安全帽、防护眼镜、耳塞等,确保自身安全。
2. 设备检查冶炼工在开始操作前,必须对所使用的设备进行检查,确保设备状态良好。
如发现设备存在异常或故障,应及时报告维修人员进行处理。
3. 原料准备冶炼工在进行冶炼操作前,必须准备好所需的原料,并按照操作要求进行称量和配比。
在进行原料称量时,应注意准确性和稳定性,避免误差对冶炼过程造成影响。
4. 炉内操作冶炼工在进行炉内操作时,必须按照操作规程进行操作。
包括控制炉温、炉压、炉气流量等参数,调整炉内矿石和燃料的投入量和比例,保持炉内气氛的稳定等。
在操作过程中,应密切关注各参数的变化,并及时调整。
5. 废渣处理冶炼工在冶炼过程中产生的废渣必须按照规定的处理方法进行处理。
废渣处理包括收集、分离和处理等环节,冶炼工必须严格按照规程进行操作,确保废渣的安全处理和环境保护。
6. 检测和记录冶炼工在操作过程中,必须进行相关参数的检测和记录。
包括炉温、炉压、炉气流量、原料投入量等参数的检测和记录。
检测结果和记录必须准确无误,并及时上报相关部门。
三、注意事项1. 防火防爆冶炼工在操作过程中,必须注意防火和防爆措施。
禁止在易燃易爆场所使用明火,严禁吸烟。
在操作过程中,应注意炉内气氛的稳定,防止发生爆炸事故。
2. 环境保护冶炼工在进行操作时,必须严格遵守环境保护要求。
避免废气、废水和废渣对环境造成污染。
废气排放必须符合国家和地方的环境保护标准。
3. 事故应急冶炼工在操作过程中,如发生事故或异常情况,必须立即停止操作,并按照应急预案进行处理。
必要时,应及时报告相关部门,并采取措施控制事故的扩大。
四、操作流程冶炼工在进行冶炼操作时,应按照以下流程进行操作:1. 设备检查:检查冶炼设备的运行状态和安全性。
冶炼工操作规程

冶炼工操作规程引言概述:冶炼工是冶金生产线上的重要岗位,他们负责熔炼金属、合金等材料,保证生产线的正常运转。
为了确保冶炼工作的安全、高效进行,制定了一系列的冶炼工操作规程,包括操作流程、安全措施、设备使用等内容。
本文将详细介绍冶炼工操作规程的相关内容。
一、操作流程1.1 炉前准备工作:冶炼工在开始操作之前,需要对熔炼炉进行检查和准备工作。
包括清理炉体、检查燃料和冷却水等。
1.2 加料操作:根据生产计划和配方要求,冶炼工将金属、合金等原料放入炉内,注意加料顺序和比例。
1.3 炉内操作:冶炼工需根据工艺要求控制炉内温度、搅拌速度等参数,确保金属熔炼均匀。
二、安全措施2.1 个人防护:冶炼工操作时需佩戴防护眼镜、手套等个人防护用具,避免受伤。
2.2 灭火设备:在熔炼过程中,冶炼工需要随时准备好灭火器等灭火设备,确保安全。
2.3 紧急预案:制定紧急预案,包括事故处理流程、应急联系人等,确保在意外情况下能够及时处理。
三、设备使用3.1 熔炼炉操作:冶炼工需要熟练掌握熔炼炉的使用方法,包括启动、停止、调节等。
3.2 温度控制:根据工艺要求,冶炼工需要准确控制炉内温度,避免过热或过冷。
3.3 设备维护:定期对熔炼设备进行维护保养,确保设备运转正常。
四、质量控制4.1 取样检测:冶炼工需要定期对熔炼金属进行取样检测,确保产品质量符合标准。
4.2 工艺调整:根据检测结果,冶炼工需要及时调整工艺参数,保证产品质量稳定。
4.3 记录保存:冶炼工需要详细记录每一批产品的生产过程和检测结果,建立质量档案。
五、环境保护5.1 废气处理:冶炼工在操作过程中需注意废气排放问题,采取相应措施减少环境污染。
5.2 废水处理:对于产生的废水,冶炼工需要按照相关规定进行处理,达到排放标准。
5.3 资源循环利用:冶炼工需要提倡资源循环利用,减少能源消耗和废弃物排放。
结语:冶炼工操作规程是保障冶金生产安全、高效的重要依据,冶炼工在日常操作中要严格遵守规程,确保生产过程稳定、产品质量优良。
冶炼工操作规程
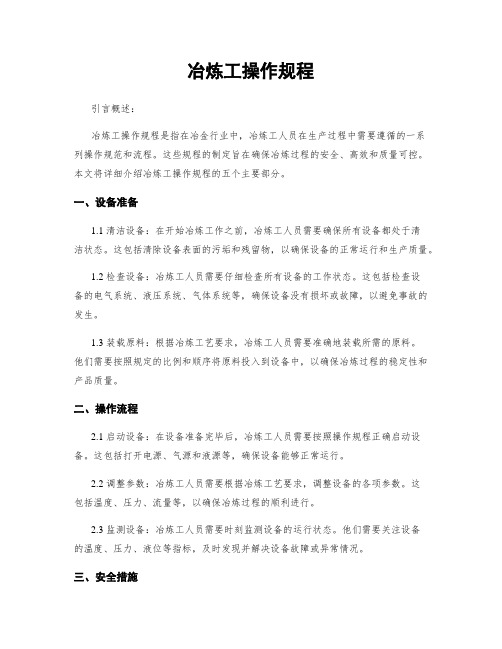
冶炼工操作规程引言概述:冶炼工操作规程是指在冶金行业中,冶炼工人员在生产过程中需要遵循的一系列操作规范和流程。
这些规程的制定旨在确保冶炼过程的安全、高效和质量可控。
本文将详细介绍冶炼工操作规程的五个主要部分。
一、设备准备1.1 清洁设备:在开始冶炼工作之前,冶炼工人员需要确保所有设备都处于清洁状态。
这包括清除设备表面的污垢和残留物,以确保设备的正常运行和生产质量。
1.2 检查设备:冶炼工人员需要仔细检查所有设备的工作状态。
这包括检查设备的电气系统、液压系统、气体系统等,确保设备没有损坏或故障,以避免事故的发生。
1.3 装载原料:根据冶炼工艺要求,冶炼工人员需要准确地装载所需的原料。
他们需要按照规定的比例和顺序将原料投入到设备中,以确保冶炼过程的稳定性和产品质量。
二、操作流程2.1 启动设备:在设备准备完毕后,冶炼工人员需要按照操作规程正确启动设备。
这包括打开电源、气源和液源等,确保设备能够正常运行。
2.2 调整参数:冶炼工人员需要根据冶炼工艺要求,调整设备的各项参数。
这包括温度、压力、流量等,以确保冶炼过程的顺利进行。
2.3 监测设备:冶炼工人员需要时刻监测设备的运行状态。
他们需要关注设备的温度、压力、液位等指标,及时发现并解决设备故障或异常情况。
三、安全措施3.1 穿戴防护装备:冶炼工人员在操作过程中需要穿戴符合安全要求的防护装备。
这包括防护眼镜、防护手套、防护服等,以保护自身免受化学物质、高温等危害。
3.2 防火措施:冶炼工人员需要严格遵守防火规程,确保冶炼现场的安全。
他们需要定期检查和维护设备的防火设施,并确保设备周围没有易燃物品。
3.3 废料处理:冶炼工人员需要正确处理冶炼过程中产生的废料。
他们需要按照规定的程序将废料分类、储存和处理,以避免对环境和人体健康造成危害。
四、质量控制4.1 产品抽样:冶炼工人员需要按照规定的抽样方法,定期对冶炼过程中产生的产品进行抽样检测。
他们需要将样品送往实验室进行分析,确保产品的质量符合要求。
操作规程冶金炼制操作

操作规程冶金炼制操作操作规程——冶金炼制操作一、前言冶金炼制操作是一项复杂而又精细的工艺,为了确保操作的安全性、有效性以及产品质量的稳定性,制定并遵守一套科学合理的操作规程就显得尤为重要。
本规程旨在对冶金炼制操作过程中的各个环节进行详细阐述,确保炉前操作人员能够准确、稳定地执行炼制操作。
二、操作前准备1. 安全措施在进行任何操作前,务必检查并遵守各项安全措施,包括佩戴个人防护装备、熟悉应急处理措施等。
2. 设备检查对炼制设备进行全面检查,包括检查电器设备、传感器、阀门等是否完好,并按照要求进行维护保养。
3. 物料准备根据作业指导书的要求,准备好所需的原料和辅助材料,并保证其质量符合标准。
三、操作流程1. 开炉操作1.1 炉前操作人员需按照炉前作业指导书的要求,检查炉体是否干净,清除杂物。
1.2 打开煤气阀门,点燃点火器点燃炉内煤气,待炉温达到预定温度后关闭点火器。
2. 加料操作2.1 按照操作指导书的要求,准确称量和配料。
2.2 将准备好的原料按照配比要求逐步加入炉内,并及时控制加料速度和时间。
2.3 在加料过程中,注意观察炉内情况,确保加料顺利进行,避免发生溢料或阻塞等情况。
3. 预热操作3.1 在加料完成后,根据操作指导书的要求,进行预热操作。
3.2 打开预热装置,并按照设定时间和温度要求进行预热操作。
3.3 在预热过程中,注意监控炉内温度变化,并及时调整预热设备。
4. 炼制操作4.1 根据炉前作业指导书的要求,进行炼制操作。
4.2 打开炉内控制设备,按照设定的工艺参数进行炼制操作。
4.3 在炼制过程中,密切关注炉内温度、压力等参数的变化,并进行必要的调整。
4.4 及时记录并汇报关键操作参数的变化,以保证炼制过程的稳定性。
5. 冷却操作5.1 炉后操作开始前,需等待炉内温度降至安全范围。
5.2 打开冷却设备,按照冷却工艺要求进行冷却操作。
5.3 在冷却过程中,注意监控冷却速度和温度变化,必要时进行调整。
冶炼工操作规程
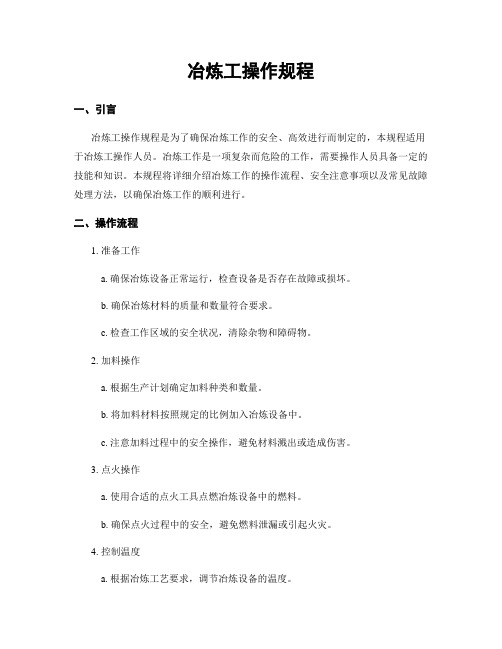
冶炼工操作规程一、引言冶炼工操作规程是为了确保冶炼工作的安全、高效进行而制定的,本规程适用于冶炼工操作人员。
冶炼工作是一项复杂而危险的工作,需要操作人员具备一定的技能和知识。
本规程将详细介绍冶炼工作的操作流程、安全注意事项以及常见故障处理方法,以确保冶炼工作的顺利进行。
二、操作流程1. 准备工作a. 确保冶炼设备正常运行,检查设备是否存在故障或损坏。
b. 确保冶炼材料的质量和数量符合要求。
c. 检查工作区域的安全状况,清除杂物和障碍物。
2. 加料操作a. 根据生产计划确定加料种类和数量。
b. 将加料材料按照规定的比例加入冶炼设备中。
c. 注意加料过程中的安全操作,避免材料溅出或造成伤害。
3. 点火操作a. 使用合适的点火工具点燃冶炼设备中的燃料。
b. 确保点火过程中的安全,避免燃料泄漏或引起火灾。
4. 控制温度a. 根据冶炼工艺要求,调节冶炼设备的温度。
b. 监测温度变化,及时调整控制参数以保持温度稳定。
5. 冶炼过程监控a. 定期检查冶炼设备的运行状态,确保设备正常运行。
b. 监测冶炼过程中的温度、压力等参数,及时发现异常情况并采取相应措施。
6. 冶炼结束a. 根据冶炼工艺要求,停止加热和加料操作。
b. 关闭冶炼设备,确保设备处于安全状态。
c. 清理工作区域,清除冶炼残渣和杂物。
三、安全注意事项1. 操作人员必须熟悉冶炼设备的结构和工作原理,了解各种操作控制参数的含义和作用。
2. 操作人员必须穿戴符合安全要求的个人防护装备,如防护服、安全帽、防护眼镜等。
3. 操作人员在操作过程中要保持专注,避免分心或走神,确保操作的准确性和安全性。
4. 操作人员必须遵守操作规程,严禁擅自更改操作参数或进行其他未经授权的操作。
5. 在发现设备故障或异常情况时,操作人员应立即停止操作,并及时报告相关人员进行处理。
6. 操作人员必须定期接受安全培训和考核,提高安全意识和应急处理能力。
四、常见故障处理方法1. 设备故障:操作人员应立即停止操作,并通知维修人员进行处理。
冶炼工操作规程

冶炼工操作规程一、引言冶炼工操作规程是为了确保冶炼工作的安全、高效进行而制定的操作指导文件。
本规程适合于冶炼工在冶炼过程中的操作,包括炉前准备、炉内操作、设备维护等内容。
二、安全要求1. 冶炼工必须经过相关培训并持有合格的操作证书方可上岗。
2. 冶炼工必须佩戴个人防护装备,包括安全帽、防护眼镜、耳塞、防护服等。
3. 冶炼工必须熟悉冶炼设备的安全操作规程,如紧急停机程序、事故处理等。
4. 冶炼工必须定期参加安全培训,提高安全意识和应急处理能力。
三、炉前准备1. 冶炼工在开始操作前必须对冶炼设备进行检查,确保设备正常运行并消除潜在的安全隐患。
2. 冶炼工必须了解冶炼工艺和操作流程,根据生产计划准备所需原料和辅助材料。
3. 冶炼工必须检查炉内温度、压力等参数,确保设备处于正常工作状态。
4. 冶炼工必须检查炉内炉料的质量和数量,确保符合生产要求。
四、炉内操作1. 冶炼工必须按照工艺要求进行炉内操作,如加料、加热、搅拌等。
2. 冶炼工必须根据炉内温度、压力等参数进行及时调整,确保冶炼过程的稳定和安全。
3. 冶炼工必须定期对炉内设备进行清洁和维护,保持设备的正常运行。
4. 冶炼工必须严格按照操作规程进行操作,不得擅自改变工艺参数或者操作方式。
五、设备维护1. 冶炼工必须定期对冶炼设备进行检修和维护,确保设备的正常运行。
2. 冶炼工必须及时处理设备故障,如停机维修、更换零部件等。
3. 冶炼工必须保持设备的清洁和整洁,防止灰尘和杂物对设备造成伤害。
4. 冶炼工必须按照设备维护计划进行维护工作,确保设备的可靠性和稳定性。
六、操作记录1. 冶炼工必须按照规定记录冶炼过程中的关键参数和操作情况。
2. 冶炼工必须准确填写操作记录表格,包括温度、压力、加料量等数据。
3. 冶炼工必须及时上报异常情况和设备故障,以便及时处理和修复。
七、总结与改进1. 冶炼工必须定期对冶炼工作进行总结和评估,发现问题并提出改进措施。
2. 冶炼工必须积极参预工艺改进和设备更新,提高冶炼工作的效率和质量。
冶炼工操作规程

冶炼工操作规程一、引言冶炼工操作规程是为了确保冶炼工作的安全、高效进行而制定的操作指南。
本操作规程适用于冶炼工在冶金企业进行冶炼操作的全过程。
二、工作准备1. 工作环境准备冶炼工在进行操作前,应检查工作环境是否符合安全要求,包括通风、照明、消防设备等是否正常运行。
2. 工具设备准备冶炼工在进行操作前,应检查所需的工具设备是否齐全、完好,包括熔炉、炉具、测量仪器等。
3. 材料准备冶炼工在进行操作前,应检查所需的原料、辅助材料是否准备充分,确保质量符合要求。
三、操作流程1. 操作前准备(1)穿戴防护装备:冶炼工应穿戴好防护服、安全帽、防护眼镜、耐酸手套等个人防护装备,确保自身安全。
(2)检查设备:冶炼工应检查熔炉、炉具等设备是否正常运行,有无异常情况。
(3)检查材料:冶炼工应检查原料、辅助材料的质量和数量是否符合要求。
2. 操作过程(1)点火:冶炼工应按照熔炉操作规程进行点火操作,确保熔炉内温度逐渐升高。
(2)加料:冶炼工应按照冶炼工艺要求,将准备好的原料、辅助材料逐步加入熔炉中,控制加料的速度和顺序。
(3)调温:冶炼工应根据冶炼工艺要求,调整熔炉内的温度,确保冶炼过程的顺利进行。
(4)搅拌:冶炼工应使用搅拌设备对熔炉内的物料进行搅拌,确保物料的均匀性和反应的充分性。
(5)取样检验:冶炼工应按照取样计划,定期在冶炼过程中进行取样检验,确保冶炼质量符合要求。
(6)排渣:冶炼工应按照排渣规程,定期对熔炉内的渣进行排除,确保熔炉内的物料纯净。
(7)冷却:冶炼工应在冶炼结束后,按照冷却规程对熔炉进行冷却处理,确保熔炉安全。
3. 操作注意事项(1)操作时应注意个人安全,严禁穿戴松散的衣物,防止被卷入设备中。
(2)操作过程中应随时注意设备的运行情况,如有异常及时报告上级。
(3)操作过程中应按照规定的程序进行,不得随意更改或省略操作步骤。
(4)操作结束后,应及时清理现场,保持工作环境的整洁。
四、事故处理1. 事故分类冶炼工操作中可能发生的事故包括但不限于:火灾、爆炸、中毒、触电等。
冶炼工操作规程

冶炼工操作规程引言概述:冶炼工作是一项复杂而重要的工作,需要严格的操作规程来确保工作的安全和高效。
本文将介绍冶炼工操作规程的五个方面,包括原料准备、炉前操作、炉内操作、炉后操作和安全措施。
一、原料准备:1.1 原料检查:冶炼工在操作前应子细检查原料的质量和数量,确保符合要求,并及时向上级报告异常情况。
1.2 原料配比:根据工艺要求和生产指标,冶炼工应准确计算和配比原料,确保冶炼过程的稳定性和产品质量。
1.3 原料预处理:对于某些原料,如矿石和废料,冶炼工应进行预处理,如破碎、磨粉等,以提高冶炼效果和降低能耗。
二、炉前操作:2.1 炉前准备:冶炼工应按照工艺要求准备炉前设备和工具,如炉衬、电极、浇注装置等,并进行必要的检修和维护。
2.2 炉前检查:在启动冶炼炉之前,冶炼工应对炉体、电极、电缆等进行全面检查,确保设备完好无损。
2.3 炉前操作:冶炼工应按照操作规程进行炉前操作,包括点火、预热、调整电极位置等,以确保炉内温度和电流的稳定。
三、炉内操作:3.1 炉内监控:冶炼工应通过监控系统对炉内温度、电流、压力等参数进行实时监测,及时发现异常情况并采取措施。
3.2 炉内调整:根据监测结果,冶炼工应及时调整炉内操作参数,如电极位置、电流强度等,以确保冶炼过程的稳定性和产品质量。
3.3 废渣处理:冶炼过程中会产生大量废渣,冶炼工应及时清理和处理废渣,以保持炉内的清洁和正常运行。
四、炉后操作:4.1 炉后处理:冶炼工在炉后应对炉体进行冷却和清理,清除残留物,并进行必要的维护和保养,以延长设备寿命。
4.2 产品处理:冶炼工应按照工艺要求对冶炼产物进行处理,如浇铸、热处理等,以获得符合要求的成品。
4.3 设备检修:在炉后操作中,冶炼工应对设备进行检修和维护,及时更换磨损部件,确保设备的正常运行和安全性。
五、安全措施:5.1 安全培训:冶炼工应接受必要的安全培训,了解操作规程和安全操作要求,并掌握相关的应急处理措施。
硅冶炼安全操作规程

硅冶炼安全操作规程一、前言硅是一种广泛应用的重要金属材料,在现代工业中具有重要的地位。
为了保障硅冶炼过程中的安全操作,防止事故发生,特制定本《硅冶炼安全操作规程》。
本规程适用于硅冶炼生产现场的工作人员,旨在规范化操作行为,提高工作安全性,保障人身安全和设备完整。
二、岗位职责1.操作人员:–执行操作指导书和设备操作要求;–熟悉硅冶炼流程及设备;–严格按照操作规程进行作业;–及时反馈设备异常情况;–遇到紧急情况及时报警并采取应急措施。
2.巡检人员:–巡视冶炼区,并做好记录;–定期检查设备状况;–及时消除危险隐患;–发现问题及时上报。
三、安全措施1.个人防护:–在操作过程中,必须佩戴安全帽、安全鞋、防护眼镜和防护服;–使用安全防护手套进行操作;–不得穿戴宽松的衣物、长发应盘起;–严禁饮酒、吸烟或服用药物等影响安全健康的行为。
2.设备安全:–首先,机器设备必须经过检查合格方可操作;–严禁操作人员私自修改机器设备;–操作之前必须确认设备处于正常工作状态;–定期检查设备,保持设备清洁。
3.灭火准备:–硅冶炼场地配备必要的灭火器材并轮流检查;–明确灭火通道,保持通道畅通;–定期组织灭火器材维护和演练。
4.废气排放:–尽量控制废气排放量,降低烟气浓度;–定期清理烟道和排烟风机,确保通畅;–废气排放必须符合国家标准,不得造成污染。
四、紧急情况应对1.漏电事故:–若发现漏电,应立即切断电源;–避免触碰带电设备;–如果有人触电,不得直接用手接触,应使用合适的工具断开电源,如木棍、干燥绝缘物等;–及时报告电气维修人员。
2.火灾事故:–发现火灾,首先切断气源或电源,然后启动灭火器进行灭火;–用湿毛巾或湿毛毯捂住口鼻;–没有灭火条件时,保持冷静,迅速撤离现场,报警并通知相关人员。
3.毒气泄漏事故:–发现有毒气泄漏,迅速切断气源,打开通风设备;–确保自身安全后,用湿毛巾或呼吸器、防毒面具捂住口鼻,尽快撤离现场;–立即向应急救援部门报告。
冶炼工操作规程
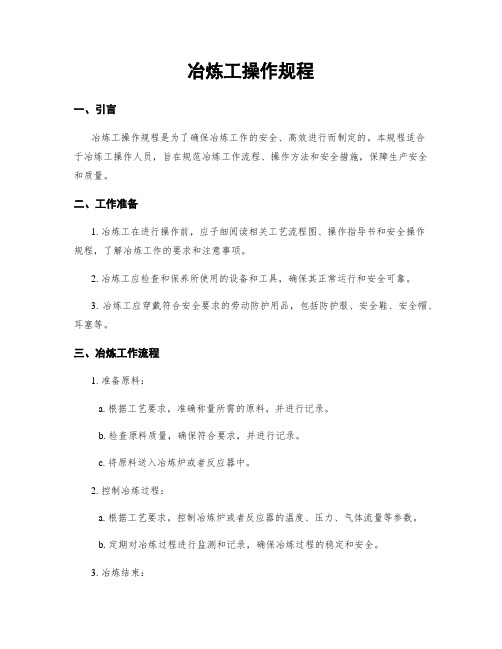
冶炼工操作规程一、引言冶炼工操作规程是为了确保冶炼工作的安全、高效进行而制定的。
本规程适合于冶炼工操作人员,旨在规范冶炼工作流程、操作方法和安全措施,保障生产安全和质量。
二、工作准备1. 冶炼工在进行操作前,应子细阅读相关工艺流程图、操作指导书和安全操作规程,了解冶炼工作的要求和注意事项。
2. 冶炼工应检查和保养所使用的设备和工具,确保其正常运行和安全可靠。
3. 冶炼工应穿戴符合安全要求的劳动防护用品,包括防护服、安全鞋、安全帽、耳塞等。
三、冶炼工作流程1. 准备原料:a. 根据工艺要求,准确称量所需的原料,并进行记录。
b. 检查原料质量,确保符合要求,并进行记录。
c. 将原料送入冶炼炉或者反应器中。
2. 控制冶炼过程:a. 根据工艺要求,控制冶炼炉或者反应器的温度、压力、气体流量等参数。
b. 定期对冶炼过程进行监测和记录,确保冶炼过程的稳定和安全。
3. 冶炼结束:a. 根据工艺要求,控制冶炼时间,并进行记录。
b. 关闭冶炼炉或者反应器,住手冶炼过程。
c. 对冶炼残渣进行处理,确保环境安全。
四、安全措施1. 操作前应检查设备和工具的安全状况,如有异常应及时报修或者更换。
2. 操作过程中应注意个人安全,避免触碰热源、有害物质和高温设备。
3. 严禁在操作过程中吸烟、使用明火或者进行其他可能引起火灾的行为。
4. 使用化学药品时应佩戴防护手套、眼镜等个人防护装备,并注意通风。
5. 如发现设备故障、泄漏或者其他安全隐患,应即将报告相关人员并采取措施进行处理。
五、应急处理1. 如发生设备故障、泄漏或者其他突发情况,应即将采取紧急停工措施,确保人员安全。
2. 在紧急情况下,冶炼工应按照应急预案执行,包括报警、疏散和救援等措施。
3. 在应急处理过程中,冶炼工应配合相关部门进行处理,并做好记录和报告工作。
六、工作总结1. 冶炼工应及时记录冶炼过程中的关键数据和操作情况,以备后续分析和总结。
2. 冶炼工应参预工作总结会议,分享经验和教训,提出改进意见。
冶炼车间操作规程范文

冶炼车间操作规程范文第一章总则第一条为规范冶炼车间的生产经营行为,提高工作效率和质量,确保工作安全,制定本操作规程。
第二条本规程适用于冶炼车间相关工作人员,在执行冶炼工作中必须严格遵守。
第三条冶炼车间的操作人员必须按照工作要求进行操作,严禁违章操作、蓄意破坏设备和低效率工作。
第四条冶炼车间的操作人员必须具备相关操作技能和高度责任感,不得疏忽大意,造成事故。
第五条冶炼车间的操作人员必须严格遵守安全作业规程,佩戴必要的个人防护设备,确保工作安全。
第六条本规程由冶炼车间负责人负责具体执行,必要时可以根据实际情况进行调整和补充。
第二章工作流程第一节前期准备工作第七条每天上班前,操作人员必须提前15分钟到岗位,检查设备是否完好,安全防护设施是否齐备。
第八条操作人员必须穿戴好工作服,佩戴好安全帽、防护眼镜、防护手套等个人防护设备。
第九条操作人员必须了解每天的工作任务,并按照工作计划准备好所需的工具和材料。
第十条操作人员必须对设备进行预热,根据工艺要求进行调整和检测,确保设备正常运转。
第二节操作工作第十一条操作人员必须按照工艺要求,把控好操作温度、操作时间和操作压力等关键参数。
第十二条操作人员必须严格遵守操作程序,确保每个步骤都正确无误,不得随意改变工艺。
第十三条操作人员在操作过程中必须保持清醒,注意观察设备运行情况,及时发现和处理异常情况。
第十四条操作人员在操作过程中必须严格遵守标准化操作要求,不得存在马虎行为和随意懈怠情况。
第十五条操作人员必须配合其他部门的工作,及时提供所需的材料和信息,确保各项工作顺利进行。
第十六条操作人员在操作过程中必须保持工作环境的整洁有序,不得有乱丢乱放的现象。
第三节后期收尾工作第十七条操作人员在工作结束后必须进行设备的清理、检查和维护,确保设备良好状态和正常运行。
第十八条操作人员必须将相关数据记录完整、准确地填写到各种表格中,便于工作的追溯和评估。
第十九条操作人员必须与其他部门的人员进行及时沟通和交流,确保工作的衔接和信息的畅通。
硅钡钙合金冶炼工艺

硅钡钙合金冶炼工艺引言硅钡钙合金是一种重要的合金材料,具有广泛的应用领域。
它由硅、钡和钙三种元素组成,具有优异的耐磨、耐蚀和耐高温性能,被广泛用于冶金、化工、建材等行业。
本文将介绍硅钡钙合金的冶炼工艺,包括原料选取、炉型选择、冶炼过程以及产品质量控制等方面的内容。
原料选取硅钡钙合金的主要原料为金属硅、氧化钡和氧化钙。
金属硅是一种常见的冶金原料,主要用于生产各种硅合金。
氧化钡和氧化钙则是作为添加剂,用于调整合金中的成分比例和性能。
在原料选取时,需要考虑以下几个因素: 1. 纯度:原料的纯度直接影响到最终产品的质量。
一般情况下,要选择纯度较高的原料。
2. 成本:原料价格对整个生产过程的经济效益有着重要影响。
需要综合考虑原料价格和产品质量之间的平衡。
3. 供应稳定性:原料供应的稳定性也是一个重要因素。
要选择可靠的供应商,确保原料供应的连续性。
炉型选择硅钡钙合金的冶炼可以选择多种炉型,常见的有电炉、燃气炉和电弧炉等。
不同的炉型具有不同的优缺点,需要根据生产规模、能源成本和工艺要求等因素进行选择。
1.电炉:电炉是一种常用的冶炼设备,具有加热速度快、温度控制精度高等优点。
适合中小规模生产,并且对原料纯度要求较高。
2.燃气炉:燃气炉适用于大规模生产,具有投资成本低、操作简单等优点。
但由于其加热速度相对较慢,对原料纯度要求较低。
3.电弧炉:电弧炉是一种高温冶炼设备,适用于大规模生产。
它具有加热速度快、温度控制精度高等优点,但能耗较高。
根据实际情况,可以选择合适的炉型进行硅钡钙合金的冶炼。
冶炼过程硅钡钙合金的冶炼过程主要包括原料预处理、混合、熔炼和浇铸等步骤。
1.原料预处理:将金属硅、氧化钡和氧化钙等原料进行粉碎和筛分,去除杂质和不可溶物。
对原料进行干燥处理,以保证冶炼过程的稳定性。
2.混合:将经过预处理的原料按一定比例混合均匀。
混合过程可以采用机械搅拌或人工搅拌的方式进行。
3.熔炼:将混合好的原料装入冶炼炉中,加入适量的助剂和脱氧剂。
冶炼工操作规程
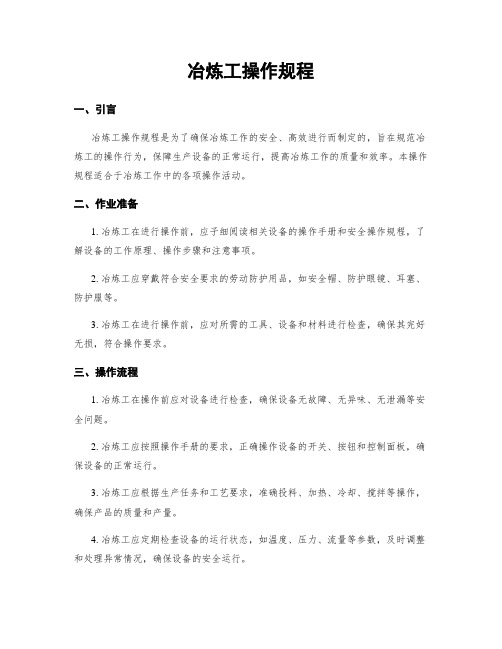
冶炼工操作规程一、引言冶炼工操作规程是为了确保冶炼工作的安全、高效进行而制定的,旨在规范冶炼工的操作行为,保障生产设备的正常运行,提高冶炼工作的质量和效率。
本操作规程适合于冶炼工作中的各项操作活动。
二、作业准备1. 冶炼工在进行操作前,应子细阅读相关设备的操作手册和安全操作规程,了解设备的工作原理、操作步骤和注意事项。
2. 冶炼工应穿戴符合安全要求的劳动防护用品,如安全帽、防护眼镜、耳塞、防护服等。
3. 冶炼工在进行操作前,应对所需的工具、设备和材料进行检查,确保其完好无损,符合操作要求。
三、操作流程1. 冶炼工在操作前应对设备进行检查,确保设备无故障、无异味、无泄漏等安全问题。
2. 冶炼工应按照操作手册的要求,正确操作设备的开关、按钮和控制面板,确保设备的正常运行。
3. 冶炼工应根据生产任务和工艺要求,准确投料、加热、冷却、搅拌等操作,确保产品的质量和产量。
4. 冶炼工应定期检查设备的运行状态,如温度、压力、流量等参数,及时调整和处理异常情况,确保设备的安全运行。
5. 冶炼工应及时清理设备和工作区域,保持设备的清洁和整洁,防止杂质和污染物对产品质量的影响。
四、安全措施1. 冶炼工在操作过程中应严格遵守安全操作规程,不得擅自更改操作步骤和参数。
2. 冶炼工应保持设备周围的通道畅通,防止堆放杂物和妨碍紧急疏散。
3. 冶炼工应定期参加安全培训和演练,提高安全意识和应急处理能力。
4. 冶炼工应随时关注设备的运行状态,如有异常情况应及时报告上级或者相关部门,采取紧急措施。
5. 冶炼工应定期检查和维护设备,及时更换损坏或者老化的零部件,确保设备的正常运行和安全性。
五、操作记录1. 冶炼工应按照规定的格式和要求,及时记录操作过程中的关键参数和数据,如温度、压力、流量等。
2. 冶炼工应保留操作记录,作为设备运行情况和产品质量的依据,以备后续分析和追溯。
六、操作纠错1. 冶炼工在操作过程中如发现错误或者疏漏,应即将住手操作,并及时报告上级或者相关部门。
- 1、下载文档前请自行甄别文档内容的完整性,平台不提供额外的编辑、内容补充、找答案等附加服务。
- 2、"仅部分预览"的文档,不可在线预览部分如存在完整性等问题,可反馈申请退款(可完整预览的文档不适用该条件!)。
- 3、如文档侵犯您的权益,请联系客服反馈,我们会尽快为您处理(人工客服工作时间:9:00-18:30)。
冶炼操作规程攀枝花市玉典电冶有限责任公司目录一、产品标准 2二、设备参数 3三、原材料技术条件 4四、工艺流程 4五、冶炼工艺 4六、开炉18七、简易配料计算举例20八、配电制度20九、安全规程20冶炼操作规程(适用于硅钡、硅铝钡、硅铝钡钙、硅钡钙通用部分)一、产品标准1.化学成份①硅钡:②硅铝钡③硅铝钡钙④硅钡钙注:需方对化学成份有特殊要求时,由供需双方另行商定。
2.交货状态:2.1粒度:20-70mm,需方有特殊要求时,另行商定。
2.2包装条件:防潮、防水,定量20公斤/袋(小包装)、大包装吨/袋,需方有特殊要求时,另行由供需双方商定。
二、设备参数:(一)变压器参数:1.变压器容量:3600KV A1800KV A2.电压:一次测电压:10KV10KV二次测电压:共五级,一级88V,共五级,一级72V,级差4V级差6V(二)炉体参数:3600KV A 800KV A1.电极直径(φ):630mm 520mm2.极心圆直径(φ):1680mm 1300mm3.炉膛直径(φ):3800mm 3000mm4.炉壳直径(φ内):5400mm 4418mm5.炉膛深度(H):1600mm 1400mm(3#1550mm、4#1400mm)6.电极行程(S):1500mm 1400mm按2002年4月1日发布的《入炉原材料质量标准》为依据;对于特殊品种及特殊要求的,另行规定。
四、工艺流程原材料采购→原料检验→原料加工→配料→称量→混合入炉→熔炼焖烧→出炉→浇铸→半成品检验→精整→入库→出厂五、冶炼工艺(一)配料1.配料计算:工艺员依据批次原材料成份变化和还原剂的固定碳、灰份、水份变化准确配料计算。
2.配料工配料前应明确知道各品种合格炉料的堆放地点;严禁私自使用不合格炉料;配料工接班后,要对计量器具进行一次校正,方能进行配料操作。
3.配料顺序①硅钡:硅石→重晶石→钢屑→还原剂。
②硅铝钡:硅石→重晶石→铝石→钢屑→还原剂。
③硅钡钙:硅石→重晶石→还原剂→石灰。
④硅铝钡钙:硅石→重晶石→铝石→还原剂→石灰。
4.配料计量:严格按工艺员下达的料比分品种计量;计量误差不大于±0.5kg;原料使用记录不得发生少记、多记、漏记。
5.严禁私拉乱配;严禁私自改动料比和发生料比传递错误;根据炉况实际确需料比调整,由工艺员负责;车间主任根据炉况变化有权改变还原剂数量±3kg,但不得连续2次以上增或减。
6.特殊情况,确需附加非料比料批,经分厂技术科长同意,方能附加,并准确计量与记录。
7.每班还原剂附加数量不得超过上限:1800KV A炉120kg,3600KV A炉180kg。
8.配料工按配料顺序均匀布料;炉台料份1800KV A炉不超过4份,3600KV A 炉不超过6份;布料形状为长方形,厚度不大于150mm。
9.配料过程中,应对硅石、重晶石、铝石等可冲洗炉料进行彻底冲洗。
(二)熔炼操作1.捣炉:冶炼过程中,因料比波动、原材料性质、加料操作等造成料面透气防止碳化物集结;处理不正常炉况(如亏碳补碳)等,均需进行捣炉操作。
1.1每次出炉后必须进行大捣炉一次,捣炉过程中严禁大翻膛,破坏坩埚,增加热量损失。
1.2大捣炉要快速、彻底、全面,一般要求在6min之内。
1.3特殊情况下,将透气性不好的区域全部挑开,要快速、彻底尽量减少散热。
1.4捣炉钎宜沿每相电极外围切线方向,掌握好插钎方法和角度,严禁发生捣伤电极事故。
1.5捣炉捣出炉料大块,应挑出,并尽量砸碎回收使用。
1.6边捣炉边压料,严禁以焦代料。
2.沉料:容量较小的矿热炉,难以完全自动下料,往往需辅以人工沉料操作,方能将炉料沉实、沉匀,并为加料创造良好的受料平台。
2.1首先将熟料沉于电极周围空腔内,沉实、沉匀,后把边缘熟料推向电极,再把新料加到规定的锥体高度焖烧;延长焖烧时间,提高炉内温度,提高化学反应速度,防止电极根部局部刺火。
2.2同一支电极的两个面,必须保持同时沉料,严禁半边操作;在操作技能成熟的条件下,应保持三支电极同时沉料;超过正常沉料间隔时间,应进行强迫沉料操作。
2.3沉料操作要快,沉料操作工具为大铲或扒子,从三角区开始沉料操作,大铲沉料时,大铲角度在50-80°之间,并来回抽动大铲,以利于炉料沉实;对于一次未沉实的炉料,应追加操作;防止沉料时工具熔化,影响产品质量,以发红为度。
2.4沉料工具避免接触电极,导致电极上抬。
2.5沉料后整理料面平面成外高内低形状,有利用落料点及落料效果的控制。
2.6出铁前约15分钟或出炉过程中,严禁1#电极沉料,防止生料造渣和炉眼堵塞。
3.上料:因炉内反应生成合金与合金的排除,炉料消耗,为向炉内补充炉料,形成上料操作;上料操作的规范性与否,直接影响电极的运行状况。
3.1上料操作严禁偏加料;均匀布料于电极周围。
3.2上料方向垂直于电极切线方向;上料以沉料仍然溢气强或弱刺火部位为3.3上料操作应做到:前脚弓、后脚蹬、前手低、后手高,手臂用力向前平推炉料。
3.4落料地点控制在离电极根部约5-10cm左右,有利于矿石于电极根部集结,还原剂与电极保持适当的距离;炉料厚、薄、轻、重于同一支电极应保持一致。
3.5上料量与炉料熔化量保持基本一致,防止料面升高;上料必须控制料面操作水平线,锥体上平面高度不超过炉口上沿15cm,炉心要保持略低于料面10-15cm,有利于电极下插以及炉况稳定与维护。
3.6料批必须单份用完用尽,严禁混料份使用。
3.7操作技能成熟的条件下,每批料可抽取1/4-1/3的重料定时加于电极根部,有利于碳化物的破坏、电极稳定下插,但不可抽取料份中的还原剂减少还原剂用量。
4.料面维护:料面维护是冶炼操作过程中非常重要的一环,料面维护的主要任务是保持料面平顶锥体状和料面透气性的均匀程度。
4.1为使电弧产生的高压、高热气流,到料面上每一点的压力降、温度降一致,气流热能均匀分布于整个炉膛,料面应保持平顶锥体状;严禁料面成尖锥状;电极与电极之间的炉料分界面应清晰明确,料沟深度保持10-20cm;防止同一支电极两人操作的交界面发生炉料堆砌。
4.2焖烧阶段,炉料因热作用或其它原因发生烧结,使局部料面透气性变差,发生局部溢气弱或不溢气,采取必要的操作(拉眼或松动炉料),保持较好的炉料透气性及均匀性,适当降低炉内气压、提高炉内化学反应速度,达到增产或处理炉况的目的。
4.2.1拉眼:一般在沉料焖烧中后期,发生电极根部刺火、焖烧时间间隔明显缩短、小面积溢气弱或不溢气时进行。
4.2.1.1严禁大通眼、独眼、同一部位重复拉眼操作。
4.2.1.2拉眼倾角最大化,保持拉透坩埚壁,防止触碰电极使电极上抬。
4.2.1.3拉透后,钎子退出约1/3长度,左右轻摆或向上轻挑松动炉料,保持料面较大面积均匀溢气,防止大通眼,可提高热能利用和合金元素回收率。
4.2.1.4发生刺火时,应在刺火部位正下方拉眼撤火,若三角区刺火,应在两支电极交界面低处拉眼撤火。
拉眼完毕,应在刺火部位少许覆盖炉料,防止刺火产生的高热高压气流烧损设备,降低设备使用寿命。
应进行松动炉料操作,以弥补大捣炉产生的遗漏面或因原材料质量、加料操作不规范等因素所造成的负面效应。
4.2.2.1松动炉料以不破坏坩埚为原则,操作要快速准确。
4.2.2.2松动炉料操作在一炉的时间段内,第二次及以后各次沉料后进行。
4.2.2.3松动炉料的过程中发现大块粘料或疙瘩,应及时挑出,推至炉心砸碎回收使用,严禁挑出炉外。
4.2.2.4松动炉料一般在电极外围炉料进行一周较为适宜。
(三)炉前操作1.开眼:开眼位置应尽可能降低,防止炉内积渣积铁;炉眼应保持较好的圆度,有利于增大合金流速,缩短出铁时间,减少热损失,同时有利于堵眼操作快速进行。
2.出铁:每班正常情况下,出铁三次,时间间隔约2.5-3h;出铁过程中要求合金及渣排完排尽,有利于电极深插,稳定炉况。
3.出铁口维护3.1出铁完毕后,应进行拉炉眼操作,防止炉眼因粘料或疙瘩堵塞出铁通道,为下一炉出铁创造良好的条件;拉炉眼过程中,防止钎子过度熔化,影响产品质量。
3.2保持炉嘴清洁卫生和保证不发生穿、跑、溢事故。
3.3出铁口是整个炉体最薄弱的环节,炉体碳素材料最易与空气接触的部位,发现出铁口周围有火焰溢出,应立即使用耐火泥堵塞其与空气接触的通道。
3.4保持炉嘴具有足够的长度,防止铁流烧包事故。
4.堵眼:堵眼要求深堵(便于出铁眼的打开)、快堵、堵实,严禁跑眼事故发生;严禁堵眼泥球掉入合金包中;堵眼泥渣避免拉带进入合金包;堵眼材料:电极糊:耐火泥=3:1。
5.脱硫操作5.1脱硫剂品种、数量应在出炉前准确称量,准备充分,并在炉前分炉分品种堆放。
脱硫剂放置场地干净无杂,脱硫剂粒度满足要求。
5.2打开出铁眼后(约30-60s),流量变大时,伴随出铁过程同步分批加入石灰石(每铲约2kg),促使硫化物上浮;石灰石加入完毕,再分批加入石灰,将硫化物固化于渣中。
6.1出铁后,将合金包推出,用钎子充分搅拌合金液。
6.2镇静时间除特殊情况下,应得到充分保证,有利于硫化物固化和合金液适当降温保护锭模。
1800KV A:5-10min,3600KV A:10-15min。
7.锭模内平整、干净无杂;防止穿模、漏模事故发生。
8.锅头:精整碎面及来源明确的合金可限量在锭模内冲兑;严禁在锭模内进行不明来源及影响产品质量的锅头冲兑;对质量要求严格的品种,严禁冲兑锅头(如武钢双14硅钡钙、首钢硅铝钡钙等)。
9.浇注9.1浇注高度不大于65cm,防止飞溅与氧化。
9.2浇注过程应保持较快的速度,提高合金表面质量。
9.3浇注过程在特殊情况下,应进行推渣操作。
9.4浇注厚度不大于120mm。
9.5浇注完毕合金包要及时彻底清渣,延长合金包使用寿命。
并将合金包放置于出铁口正下方,防止合金包滑跑。
10.出模:合金浇注后经一定时间冷却后进行脱模操作,严禁红热脱模和脱模后合金渗流现象发生。
11.初选入库11.1合金出模初整至小于300mm的块度,并对明显具有马蜂窝、粘料等不合格合金进行挑选,不合格合金不得进行精整工序。
11.2入库过程中,严禁发生混炉、兑假现象。
(四)电极的维护与使用1.电极壳制作与接长1.1电极壳的制作尺寸要求准确,保证较好的圆度(保证电极与铜瓦接触良好);焊缝均匀、平整、结实,防止焊缝破裂漏糊。
1.2电极筋片高度、数量、焊点满足要求,焊接牢固不穿眼,不降低焊点与电极壳接触处的强度,防止不能满足压力要求而发生穿孔现象。
1.3电极壳根据正常消耗及正常生产情况实际,定时接长,严禁发生回抱电极接长事件。
1.4加接电极壳时,防止大量灰尘和异物掉入电极筒内。
2.电极糊的加入:随电极下放与消耗,需不断加入电极糊保持糊柱高度,保2.1加入电极筒内的电极糊块度小于200mm,防止烧结偏析、悬料现象和杂物进入电极筒内。