水玻璃氯化铵法精密铸造工艺规程
免硬化解决分层水玻璃精密铸造制壳面层、过渡层新工艺

划时代的水玻璃精密铸造制壳工艺面层、过渡层新型工艺和配方各位精密铸造行业的专家、企业家们,衷心的请您耐心认真的了解本文介绍的内容,相信您一定可以感受到即将到来的呼之欲出的精铸工艺革命!我国传统的水玻璃精密铸造工艺,面层、过渡层以水玻璃为粘结剂,辅以石英粉,适当添加消泡剂、渗透剂配浆以后,将蜡模模组进行蘸浆、洒砂、风干,然后用氯化铵、或者氯化铝、氯化铝氯化镁混合作为硬化剂,浸泡,待水玻璃和氯化铵反应以后,起到硬化的作用,硬化以后仍需等待模组干燥,然后再进入到下一层的操作。
多年来,我国一直用氯化铵作水玻璃型壳的硬化剂。
以后又逐步发展为用氯化铝:氯化镁作硬化剂。
无论用何种硬化剂,都免不了需要硬化,都有其不可克服的缺点。
氯化铵虽能在较短时间内硬化型壳,但焙烧后型壳强度差,作高强度型壳的硬化,显然不行,加之硬化时有氨气逸出,散发出刺鼻的气味,故工作环境条件差,导致招工难,留人难。
用氯化铝,还是氯化铝和氯化镁混合溶剂硬化,又有铸件表面质量差,清砂困难等缺点。
为客服上述传统工艺的各种缺陷,我公司技术人员经过多年的生产实践和摸索,经历了无数次的试验失败和不断尝试,研究出一种新型工艺和配方(该工艺和配方已经进入了国家实用型专利的申请流程),利用量身定做的配浆设备、配浆配方、脱蜡装置等重要工艺因素,让水玻璃精密铸造工艺取得飞跃的进步。
本文介绍的新工艺,主要是体现在型壳的面层、过渡层制作彻底告别硬化时代,使铸件的表面质量得到很大的提高,其光洁度甚至可以与硅溶胶精铸工艺生产出来的铸件媲美。
避免了传统的制壳工艺带来的表面分层、表面粘砂,橘子皮等缺陷。
同时,由于没有了氯化铵挥发出来的氨味,工作环境得到明显的改善,同时工艺参数要求、操作要求没有传统的硬化工艺那么复杂和严格,操作简单,一般工人均可上手,减少了由于熟练工流失,新工人上岗时的废品损失,稳定了工厂的正常生产效率。
成本方面,制壳材料成本比传统硬化工艺非但没有增加,而且明显减少了铸件后处理的焊补打磨抛丸处理,大大降低了生产成本,提高了良品率,缩短了生产周期,提升了利润空间的同时,大大提升了客户满意度。
水玻璃铸造工艺守则

水玻璃铸造工艺守则文件编号:RMZZ/QG-JS-01版本: A修改状态:O受控状态:编制:吴光来日期:2004-3-1蜡料制备1.工艺要求:1.1 蜡液温度:70-90℃,严禁超过90℃。
1.2 稀蜡温度:65-80℃。
1.3 蜡膏保温缸水温:48-50℃。
1.4 蜡膏应搅拌均匀呈糊状,温度控制在45-48℃,其中不允许有颗粒状蜡料。
1.5 蜡料配方1.5.2 在生产过程中必须根据蜡模质量分析结果,适量增加或减少硬脂酸量,冬季的酸值取下限,夏季的酸值取上限。
2操作程序2.1 启动设备,检查运转是否正常,是否漏水、漏气、漏蜡,有问题应及时排除。
检查保温缸水温是否符合工艺要求。
2.2 按蜡料配比把石蜡、硬脂酸和回收蜡分别称好,加入化蜡槽内,加热至全熔状态,其温度不得超过90℃。
2.3 把蜡液送到蜡膏搅拌机盛蜡槽内。
2.4 将搅蜡缸内加入三分之二的蜡片,启动搅拌机进行搅蜡直至呈糊状蜡料为止。
3注意事项3.1 稀蜡需用100目筛过滤,去掉杂质后方能使用。
3.2 不允许有影响质量的空气和水分混入蜡膏中。
3.3 化蜡槽和盛蜡槽每月清理两次。
3.4 蜡膏保温缸、搅蜡缸属于压力容器,应定期检查有关紧固件及密封机构的使用情况,发现问题应及时处理,正常工作压力严禁超过0.50MPa。
4检查项目每班必须测量蜡液温度和保温水温度3-4次,控制在工艺要求范围内并做好原始记录。
蜡模制造1 工艺要求1.1 室温:16-28℃(最高不超过30℃)。
1.2 蜡膏压注温度:45~48℃,压力:0.3~0.5 MPa,保压时间:3~10秒。
1.3 压蜡冷却水温,14~24℃,冷却时间:20~100秒。
1.4蜡模冷却水温,14~24℃,冷却时间:10~60min。
1.5蜡模清洗液温度,20~28℃,清洗液中加入0.01% JFC。
1.6 脱模剂:ZF201.1.7蜡模表面光洁度,形状完整,轮廓清洗,尺寸合格,不允许有缩陷,凸包裂纹等缺陷。
精密铸造各工序操作规程及注意事项

精密铸造各⼯序操作规程及注意事项精密铸造各⼯序操作规程及注意事项压蜡⼯序⼯艺操作规程及注意事项⼀.⼯艺要求:室温:24±2℃,蜡缸温度:54±2℃射蜡嘴温度: 54±2℃压射压⼒:3.5-4.0mpa保压时间:视蜡模⼤⼩,壁厚⽽定(⼀般为6-8秒)冷却⽔温度:≤20℃⼆.操作程序:1.检查压蜡机油压,保温温度,操作按钮是否正常,按照技术规定调整压蜡机压射压⼒,射蜡嘴温度,保压时间,冷却时间等。
2.从保温箱中取出蜡缸,装在压蜡机上,挤出上部混有空⽓的蜡料。
3.将模具放在压蜡机⼯作台⾯上,调整射蜡嘴使之与模具注蜡⼝⾼度⼀致,检查模具所有芯⼦,活块位置是否正确,模具开合是否顺利。
4.打开模具,喷薄薄⼀层分型剂,合型,对准射蜡嘴。
5.双⼿按动⼯作按钮,压制蜡模。
6.抽出芯⼦,打开模具,⼩⼼取出蜡模,放在⼯作台⼀侧,合上模具开始压下⼀件,同时对该件粗略检查⽆缺陷后按要求放⼊冷却⽔中或放⼊存放盘中冷却,冷却时间为4⼩时,注意有以下缺陷的蜡模应报废:(1)因模料中卷⼊空⽓,蜡模局部有⿎起的;(2)蜡模任何部位有缺陷的;(3)蜡模有变形不能简单修复的;(4)尺⼨不符合规定的。
7.清除模具上残留的模料,注意只能⽤⽵⼑,不可⽤⾦属⼑⽚清除残留模料,防⽌模具型腔及分型⾯受损,⽤压缩空⽓⽓嘴吹净模具分型⾯。
芯⼦上的蜡屑等,视模具结构及使⽤情况每2-10件喷⼀次分型剂。
8.及时将蜡模从冷却⽔中轻轻取出,⽤压缩空⽓吹净蜡屑及⽔珠,并进⾏⾃检,将合。
放⼊存放盘中。
9.每班下班或模具使⽤完毕后,应⽤软布或棉棒清理模具,如发现模具有损伤或不正常,应⽴即报告领班,由领班处理。
并清扫压蜡机,⼯具及现场,做到清洁、整齐。
三.注意事项:1.压制蜡模时,⾸先必须进⾏检查,确认合格后,⽅可进⾏操作,压蜡模过程中不能轻易变动压制参数。
2.模具型腔不要喷过多的分型剂,并要均匀,必要时可⽤压缩空⽓⽓嘴辅助将分型剂吹均匀。
水玻璃制壳工艺

涂料配置1工艺要求1.1工艺材料主要技术参数1.1.1水玻璃1.1.2石英粉(用于表面涂料)1.1.3高铝合成粉(用于加固层涂料)1.1.4铝矾土粉(用于加固层涂料)1.1.5煤矸石粉(用于加固层涂料)1.2涂料配置1.3涂料粘度注:a.室内低于8度,涂料粘度应提高:表面层应提高2~3s,加固层应提高1~2s。
b.室内高于30度,涂层粘度应降低:表面层应降低2~3s,加固层应降低1~2s。
c.手工制壳的涂料粘度应增加:表面层应提高5~10s,加固层应提高2~3s。
2操作程序2.1检查涂料搅拌机运转是否正常,按1.2的规定分别计算水玻璃、粉料、JFC 的加入量,并准确称量。
2.2按1.1.1的规定,水玻璃加水处理合格后一次性加入涂料搅拌机中,加JFC 搅匀,粉料应分2~3次加入,边加边搅拌至全部完成,再搅拌60~90min。
可间断搅拌每次搅拌时间不得小于30min。
2.3配好的涂料应静置4~8h,使用前应充分搅拌,达到1.3的规定后方能使用。
3注意事项3.1若在表面层与加固层之间增加过渡层,其涂料粘度应在表面层的基础降低5~10s。
3.2涂料配比作为一次性配料的工艺要求,最终按室温调整到工艺规定的粘度。
4检查项目4.1水玻璃、耐火粉料按进货批次进行检验,检验结果应符合2.1和有关材料标准要求。
4.2涂料粘度采用体积100ml,流出孔φ6±0.02mm的标准流杯,每班测定1~2次,测定结果应符合1.3的规定。
4.3期采用不锈钢涂片或玻璃片测定涂料的覆盖性(涂料厚度及均匀性),要求达到涂料无堆积、涂层均匀。
4.4水玻璃模数、涂料的粘度和覆盖性的测定方法,按JB4007——85《熔模铸造涂料试验方法》的规定进行。
制壳1范围本标准规定了制造型壳(以下简称制壳)的工艺要求、操作程序、注意事项和检查项目。
本标准适用于水玻璃、石英砂、铝矾土砂、高岭石系列砂等材料的型壳制造。
2工艺要求2.1室温:15~32度,湿度40%~60%.2.2工艺材料主要技术参数2.2.1水玻璃涂料应符合标准CICBA/B02.07。
水玻璃铸造工艺
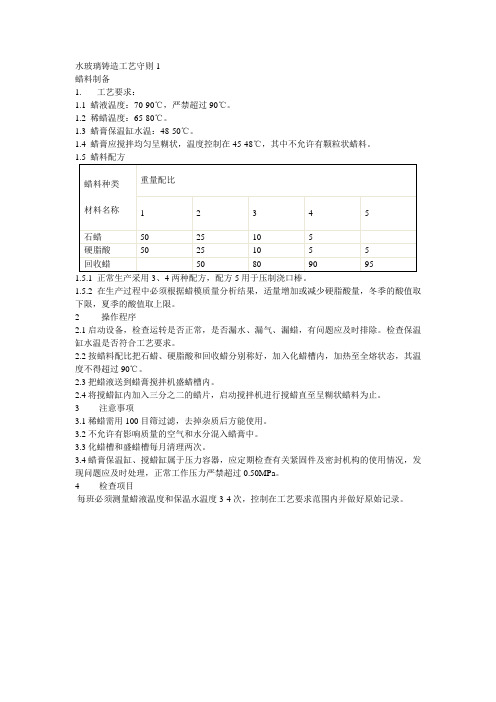
水玻璃铸造工艺守则1蜡料制备1. 工艺要求:1.1 蜡液温度:70-90℃,严禁超过90℃。
1.2 稀蜡温度:65-80℃。
1.3 蜡膏保温缸水温:48-50℃。
1.4 蜡膏应搅拌均匀呈糊状,温度控制在45-48℃,其中不允许有颗粒状蜡料。
1.5.1 正常生产采用3、4两种配方,配方5用于压制浇口棒。
1.5.2 在生产过程中必须根据蜡模质量分析结果,适量增加或减少硬脂酸量,冬季的酸值取下限,夏季的酸值取上限。
2 操作程序2.1 启动设备,检查运转是否正常,是否漏水、漏气、漏蜡,有问题应及时排除。
检查保温缸水温是否符合工艺要求。
2.2 按蜡料配比把石蜡、硬脂酸和回收蜡分别称好,加入化蜡槽内,加热至全熔状态,其温度不得超过90℃。
2.3 把蜡液送到蜡膏搅拌机盛蜡槽内。
2.4 将搅蜡缸内加入三分之二的蜡片,启动搅拌机进行搅蜡直至呈糊状蜡料为止。
3 注意事项3.1 稀蜡需用100目筛过滤,去掉杂质后方能使用。
3.2 不允许有影响质量的空气和水分混入蜡膏中。
3.3 化蜡槽和盛蜡槽每月清理两次。
3.4 蜡膏保温缸、搅蜡缸属于压力容器,应定期检查有关紧固件及密封机构的使用情况,发现问题应及时处理,正常工作压力严禁超过0.50MPa。
4 检查项目每班必须测量蜡液温度和保温水温度3-4次,控制在工艺要求范围内并做好原始记录。
蜡模制造1 工艺要求1.1 室温:16-28℃(最高不超过30℃)。
1.2 蜡膏压注温度:45~48℃,压力:0.3~0.5 MPa,保压时间:3~10秒。
1.3 压蜡冷却水温,14~24℃,冷却时间:20~100秒。
1.4蜡模冷却水温,14~24℃,冷却时间:10~60min。
1.5蜡模清洗液温度,20~28℃,清洗液中加入0.01% JFC。
1.6 脱模剂:ZF201.1.7蜡模表面光洁度,形状完整,轮廓清洗,尺寸合格,不允许有缩陷,凸包裂纹等缺陷。
2 操作程序2.1 手工制模2.1.1检查压型的分型面、型腔、脱模机构、定位销、紧固件应完整清洁。
精密铸造工艺规程

精密铸造工艺规程编制:审核:批准:日期:1 / 23文件目录2 / 23蜡型工艺规程一、工艺参数1.蜡料的配置(﹪)2.蜡料使用的温度3.压缩空气工作压力0.25—0.4 MPa4.搅料用碎蜡块加入量占蜡液的30%(碎蜡块30%蜡液70%)5.新蜡与硬脂酸的比例1∶16.作业环境温度0-30℃3 / 231.按配比称料、加温熔化。
2.在蜡液中加碎蜡块,搅拌成糊状(碎蜡块只许一次加成)。
3.装料调整好水温、压蜡。
4.冷凝、折模、蜡模水冷。
5.清理型腔、涂分型剂。
6.合型锁紧、重复压蜡。
7.修刮飞边、毛刺、修补缺陷。
8.用洗涤剂洗涤油迹,并用清水清洗一遍。
9.擦干水迹,分类入库。
4 / 23浇口棒蜡模工艺规程1.清擦模具,涂分型剂。
2.自由浇注蜡液。
3.将木棒擦入半凝固蜡液中,木棒擦入深度距离底部不能少于5-10㎜。
4.冷却取出,清擦合模。
5.修刮飞边毛刺,修补少量缺陷的蜡模。
5 / 23蜡模组焊工艺规程一、工艺参数二、操作规程1.将合格的蜡模依次焊上。
2.修刮蜡豆,插入车上。
3.组焊后应吹净蜡屑。
6 / 23制壳工艺规程一、配涂料用水玻璃的技术要求二、涂料配比7 / 23四、制壳工艺规范参数(比重氯化镁1.24-1.28,PH值5.5-5.6)五、操作规程1.按照工艺参数,配制好各种生产用料;2.每班检查涂料粘度、氯化镁浓度、氯化铵浓度;3.涂挂表面层涂料撒砂硬化干燥2遍;4.涂挂过度层涂料撒砂硬化干燥1遍;5.涂挂加强层涂料撒砂硬化干燥4-9遍;6.其余各层可直接硬化;7.铸件重量大于20kg,加强层不少于7.5层;8 / 239.若需铁丝加固,需在第3层硬化后,采用18#铁丝;10.铸件重量小于0.05kg,表面层2遍,加强层3遍;11.粘度计采用容量100ml,出口径φ6mm,蒸馏水标准4±0.5秒。
脱蜡工艺规程一、工艺参数1、脱蜡水氯化铵浓度4-8%。
2、水温大于95摄氏度。
3、热水脱蜡时间小于1小时,随着铸件重量的增加,可适当延长时间。
精密铸造工艺方案

精密铸造工艺方案1. 引言精密铸造工艺是一种通过采用特殊的工艺和设备,将金属材料熔化,倒入模具中,通过冷却固化得到具有高度精度和表面质量要求的金属制品的生产方法。
精密铸造广泛应用于航空、航天、汽车、电子、医疗设备等领域,对产品的质量和精度要求较高。
本文将介绍一种常见的精密铸造工艺方案。
2. 工艺流程下面是该精密铸造工艺的基本流程:1.模具制作:根据产品的形状和尺寸要求,使用数控加工技术制作出精密的金属模具。
2.材料准备:根据产品要求选择合适的材料,并将其加热至熔化温度。
3.熔炼和浇注:将熔化的金属倒入预热好的模具中,并确保充满整个模腔。
4.冷却和固化:等待熔融金属在模具内冷却和固化,使其获得所需的形状和性能特性。
5.反模和后处理:将固化的金属制品从模具中取出,并进行后续的加工、喷漆、抛光等处理。
3. 工艺优势精密铸造工艺相比于传统铸造工艺具有以下优势:•高精度:模具制作精密,可以满足对产品尺寸精度要求高的应用领域。
•优质表面:由于模具制作精度高,产品表面质量好,减少了后续加工工序。
•综合性能好:经过冷却和固化过程后,金属制品具有更好的力学性能和耐腐蚀性。
•生产效率高:工艺流程简洁明了,生产效率高,适合批量生产。
4. 工艺参数在进行精密铸造工艺时,以下参数需要特别注意:•浇注温度:金属材料的熔化温度决定了浇注温度,过高或过低都会影响产品的质量。
•冷却时间:确保熔融金属充分冷却和固化的时间,以使产品获得所需的强度和硬度。
•压力控制:在某些情况下,需要在浇注过程中施加一定的压力,以消除气孔和提高材料的密实性。
•退火处理:针对某些材料,进行退火处理可以消除内部应力,并提高材料的韧性。
5. 质量控制为了确保产品质量,精密铸造工艺中需要进行以下质量控制措施:•模具检验:对模具的精度进行检验,确保模具满足要求。
•材料检验:对使用的金属材料进行化学成分和物理性能的测试,以保证材料质量。
•视觉检验:对冷却固化后的金属制品进行目测和照明条件下的检查,发现任何缺陷。
水玻璃氯化铵法精密铸造工艺规程

水玻璃氯化铵法精密铸造工艺规程1.目的为了便于操作者熟悉和掌握水玻璃法精密铸造的工艺特点、技术特性,更好的在生产中加以应用,生产出优质的产品,特制定本规程。
2.适用范围本工艺规程适用于从蜡模配制到模壳浇注的全过程。
3.职责3.1 技术部是本规程的制定和归口部门。
3.2 各工序工作人员均应按此规程进行操作。
4.工艺规程4.1 制作蜡模4.1.1 压制蜡模的模具应符合产品的图纸要求,经检验合格后使用。
4.1.2 蜡料应按石蜡:硬脂酸1:1进行配料,融化后加蜡屑机械搅拌成糊状,加入压蜡机内往模具中注蜡。
4.1.3 蜡型要在模具中保压冷却才可取模,并及时对变形蜡模进行校正,放入冷水冷却,待完全冷却后方可进行取出毛刺、修整等工作。
4.1.4 修整好的蜡模经检验合格后,清洗表面油脂,方可与浇冒口组焊。
4.1.5 组焊好的模组,需将内外面的蜡屑清除干净后送涂挂制壳。
4.2 制壳4.2.1 选料面层料浆用320目锆英粉,加固层料浆用200目以上的高铝粉或焦宝石粉和石英粉,粘结剂用模数3.1~3.4,密度为1.30~1.40的40#水玻璃。
4.2.2 选砂面层用80~100目的棕刚玉,二层用40~70目的石英砂,三层用20~40目的石英砂,四层以后选用10~20目的石英砂。
4.2.3 料浆的配制面层与二层:将水玻璃加水稀释到密度为1.28~1.30,然后加锆英粉,其比例为1:1.1~1.2(要注意根据气温变化调节比例),进行机械搅拌,再加入清洗剂0.05%,消泡剂0.05%,继续搅拌,时间不少于6小时,静置4小时熟化,再搅拌均匀方可使用。
三层过渡层用密度为1.30~1.32的水玻璃加高铝粉和石英粉,比例为1:0.5:0.5。
加固层同三层,比例略为调厚一点。
4.2.4 料浆的粘度测定用100Ml的流量杯来测定,面层、二层及三层为28~35秒,加固层为45~50秒。
4.2.5 挂浆将检验合格后的模组浸入搅拌均匀的料浆中,上下移动两次,然后提出,用毛刷将字和死角处的气泡刺破并刷浆,把多余的料浆刷掉,整个模组要求挂浆均匀,无遗漏,五堆积,然后即可挂砂,整个挂浆过程时间不可过长,以免表面自然硬化,而无法挂砂。
精密铸造工艺流程

精密铸造工艺流程精密铸造是一种高精度、高质量的铸造工艺,其在航空航天、汽车、船舶、机械等领域有着广泛的应用。
精密铸造工艺流程的规范与否直接影响着产品的质量和性能,下面我们就来详细介绍一下精密铸造工艺流程。
首先,精密铸造的工艺流程包括模具设计、熔炼、浇注、凝固、脱模、清理和表面处理等环节。
模具设计是整个工艺流程的第一步,它直接关系到产品的成型质量和尺寸精度。
在模具设计中,需要考虑产品的结构特点、材料特性以及生产工艺等因素,确保模具能够满足产品的成型需求。
其次,熔炼是精密铸造的关键环节之一。
在熔炼过程中,需要选择合适的合金材料,并通过严格的配料、熔炼和处理工艺,确保合金的化学成分和温度达到要求,以保证浇注时的流动性和凝固过程中的组织结构。
接下来是浇注和凝固阶段。
在浇注过程中,需要控制浇注速度和温度,避免气泡和夹杂物的产生,确保铸件的内部质量。
而在凝固过程中,需要控制冷却速度,避免产生组织缺陷,保证铸件的力学性能和表面质量。
脱模和清理是精密铸造工艺中不可忽视的环节。
脱模需要根据具体产品和模具的特点,选择合适的脱模剂和脱模工艺,以避免产生脱模裂纹和表面缺陷。
清理工艺则包括除渣、除砂、除氧化皮等步骤,以确保铸件表面的光洁度和完整性。
最后是表面处理。
表面处理可以包括喷砂、抛光、喷漆、电镀等工艺,以提高产品的表面光洁度、耐腐蚀性和装饰性。
总的来说,精密铸造工艺流程是一个复杂而严谨的系统工程,需要各个环节的紧密配合和严格控制。
只有通过精密的工艺流程,才能保证产品的质量和性能达到设计要求。
希望本文对精密铸造工艺流程有所帮助,谢谢阅读!。
水玻璃铸造工艺(3篇)

第1篇一、引言水玻璃铸造工艺是一种传统的铸造方法,它利用水玻璃作为铸造材料,具有熔点低、流动性好、易于脱模等优点。
随着我国铸造工业的不断发展,水玻璃铸造工艺在铸造领域得到了广泛应用。
本文将从水玻璃的制备、铸造工艺流程、质量控制等方面对水玻璃铸造工艺进行详细介绍。
二、水玻璃的制备1. 水玻璃的原料水玻璃的原料主要有硅砂、碱金属氧化物、碱土金属氧化物等。
其中,硅砂是水玻璃的主要成分,其质量直接影响水玻璃的性能。
2. 水玻璃的制备方法(1)熔融法:将硅砂、碱金属氧化物、碱土金属氧化物等原料按照一定比例混合,加热熔融后,加入适量水冷却、固化,得到水玻璃。
(2)水解法:将硅砂、碱金属氧化物、碱土金属氧化物等原料按照一定比例混合,加入适量水,搅拌、加热,使原料水解,得到水玻璃。
(3)沉淀法:将硅砂、碱金属氧化物、碱土金属氧化物等原料按照一定比例混合,加入适量水,搅拌、加热,使原料发生化学反应,生成沉淀,经过过滤、洗涤、干燥等工序,得到水玻璃。
三、水玻璃铸造工艺流程1. 原料准备将硅砂、碱金属氧化物、碱土金属氧化物等原料按照一定比例混合,经过筛选、烘干等工序,确保原料的质量。
2. 水玻璃制备按照一定的工艺参数,将原料进行熔融、水解或沉淀等制备过程,得到符合要求的水玻璃。
3. 模具准备根据铸件形状、尺寸、材料等要求,选择合适的模具。
模具应具有良好的脱模性能、耐磨性和耐腐蚀性。
4. 铸造将水玻璃倒入模具中,进行凝固、硬化。
根据铸件形状、尺寸、材料等要求,选择合适的铸造温度、时间、压力等参数。
5. 脱模在铸件凝固、硬化后,进行脱模操作。
脱模过程中应避免对铸件造成损伤。
6. 后处理对铸件进行打磨、抛光、热处理等后处理工序,提高铸件质量。
四、质量控制1. 原料质量:严格控制原料质量,确保水玻璃的性能稳定。
2. 水玻璃制备:按照一定的工艺参数,确保水玻璃的制备质量。
3. 模具质量:选择合适的模具,确保模具的脱模性能、耐磨性和耐腐蚀性。
水玻璃铸造工艺守则

资源回收利用:对可回收利用的废弃物进行回收利用,提高资源利用效率
环保监管:加强环保监管,确保水玻璃铸造工艺的环保与安全要求得到落实
生产过程中的安全防护措施
穿戴防护用品:操作人员必须佩戴齐全的防护用品,如防护眼镜、手套、口罩等,以防止有害物质对人体的伤害。
工艺参数调整:根据产品要求和生产条件,合理调整硬化时间和温度,以获得最佳的工艺效果。
Part Five
水玻璃铸造工艺中的问题及解决方法
气泡的产生与消除
气泡产生的原因:水玻璃中的气体未完全排出、水玻璃涂抹不均匀、金属模具温度过高等
气泡消除的方法:增加排气孔、调整水玻璃涂抹方式、控制金属模具温度等
裂纹的产生与预防
注意事项:在操作过程中,要密切关注模具温度和浇注温度的变化,及时调整参数,避免出现异常情况
浇注速度与压力
浇注速度:控制浇注速度以保证金属液平稳、均匀地流入型腔
压力:通过控制压力来防止金属液在浇注过程中产生气孔、夹渣等缺陷
浇注速度与压力的协调:根据铸件的大小、形状和材质等因素,合理调整浇注速度和压力
原材料的质量要求
添加标题
添加标题
添加标题
添加标题
原材料质量标准:符合国家相关标准,无杂质、无污染
原材料种类:硅酸钠、水玻璃、耐火材料等
原材料检验方法:采用化学分析、物理测试等方法进行检验
原材料储存要求:保持干燥、通风良好,防止受潮、变质
生产过程中的质量控制
添加标题
添加标题
添加标题
添加标题
工艺控制:严格遵守工艺流程,确保每个环节的质量稳定
保持通风:在生产过程中,应保持通风良好,以减少有害气体的浓度,防止对操作人员造成危害。
精密铸造工艺规程

4.过滤网为200目
二、操作程序:
1.设备准备:
a脱蜡用蒸汽发生器压力应达1。0Mpa,最低不得小于0。7Mpa。
b对脱蜡釜进行预热1~2次。
C准备好过滤网,确保干净,整洁,无破损。
2.型壳准备:
A将封浆后已达到干燥时间的陶壳从挂架上取下,执下挂钩,盖板并将浇口杯处多余砂粒清理干净,放于脱蜡小车上,准备脱蜡。
2.蜡件凹陷处的修复:
2.1蜡件的凹陷应用专用修补蜡进行修补,修补后表面要平整。
3.蜡件气泡的修复:
3.1对蜡件上的气泡必须全部挑破,用专用修补蜡进行修补,修补后蜡件需平整无缺。
4.蜡件油纹的修复:
4.1蜡件油纹的修复,需用吸有三氯乙烯或三乙氯烷的棉花团,轻柔的对油纹处进行擦拭,注意不要伤到蜡件本身。
6.涂料基本搅拌均匀后,用4#詹氏杯测其粘度,若粘度过高,则加硅溶胶调整,过低则加耐火粉料调整。
工艺规程
LOQS-C2-S205
涂料配制
第2版共2页第2页
7.面层、二层锆浆,每次新配制后,务必要作好记录,严格按规定日期给予更换,即面层20-25天,二层25-30天。
8.在操作过程中,造成成粘度偏高,应加蒸馏水予以高速特别是真空沾浆机内泥浆更应如此。
4.打开模具,喷涂脱模剂,合模后将模具射蜡口对准射蜡嘴。
5.按动工作按钮,压制蜡模。
6.按拆装顺序,抽出抽芯,打开模具,用压缩空气,小心将蜡件取出,按要求入入冷却水或盘中冷却。
7.模件存在下列缺陷应予以报废。
A因模料卷入空气,使蜡件局部有鼓起的;
B蜡件某一部位有缺陷的;
C蜡件变形且不易修复者;
D尺寸不符合规定者;
8.涂挂二层前,首先将面层多余砂粒抖净,然后在硅溶胶原液中进行预湿2-5S,取出后滴4~7秒。
熔模铸造氯化铵硬化水玻璃型壳工艺[发明专利]
![熔模铸造氯化铵硬化水玻璃型壳工艺[发明专利]](https://img.taocdn.com/s3/m/6b384a5d59fafab069dc5022aaea998fcc22400b.png)
(19)中华人民共和国国家知识产权局(12)发明专利申请(10)申请公布号 (43)申请公布日 (21)申请号 201610788495.8(22)申请日 2016.08.26(71)申请人 朱伟杰地址 214161 江苏省无锡市滨湖区胡埭工业园张舍路7-1号(72)发明人 朱伟杰 潘玉洪 (51)Int.Cl.B22C 1/10(2006.01)B22C 1/18(2006.01)(54)发明名称熔模铸造氯化铵硬化水玻璃型壳工艺(57)摘要本发明涉及到熔模铸造氯化铵硬化液硬化水玻璃型壳工艺。
本发明包括:(1)控制氯化铵硬化液的浓度、温度、硬化时间,并且三者之间有密切的关系。
(2)没有必要控制硬化液中的氯化钠含量。
不需要更换硬化液,造成不必要的浪费。
(3)不需要控制硬化液的PH值,不需要用盐酸中和法或加热去氨法使硬化液的PH值;不存在硬化液中的过剩盐酸<0.5%。
(4)氯化铵硬化水玻璃型壳的硬化机理应该是:氯化铵(NH 4Cl )是强酸弱碱盐,水玻璃(Na 2O.mSiO 2)是强碱弱酸盐,两者水解后发生下列化学反应:上述两个化学反应方程式水解后生成的H +和OH -中和,生成电离度极小的H 2O,使两个方程式向右进行,生成硅胶mSiO 2.(n-1)H 2O又促进了水解;进而又中和,周而复始地进行下去,就会生成越来越多起到粘结作用的硅胶mSiO 2.(n-1)H 2O。
而不是“氯化铵水溶液硬化水玻璃型壳的理论基础,除了生成起粘结作用的硅胶以外,还生成氢氧化铵和氯化钠,氢氧化铵分解成氨气和水;氯化钠的比重(d=2.16)较大,常沉淀在硬化槽的底部。
”本发明提出了熔模铸造氯化铵硬化水玻璃型壳的工艺,减少了不必要的、人为的浪费;从而提高了生产效率,降低了生产成本,提高了企业的经济效益。
权利要求书1页 说明书4页 附图1页CN 107774884 A 2018.03.09C N 107774884A1.本发明涉及到熔模铸造氯化铵硬化液硬化水玻璃型壳工艺。
精密铸造各工序操作规程及注意事项

精密铸造各⼯序操作规程及注意事项精密铸造各⼯序操作规程及注意事项⽂件管理序列号:[K8UY-K9IO69-O6M243-OL889-F88688]精密铸造各⼯序操作规程及注意事项压蜡⼯序⼯艺操作规程及注意事项⼀.⼯艺要求:室温:24±2℃,蜡缸温度:54±2℃射蜡嘴温度: 54±2℃压射压⼒:3.5-4.0mpa保压时间:视蜡模⼤⼩,壁厚⽽定(⼀般为6-8秒)冷却⽔温度:≤20℃⼆.操作程序:1.检查压蜡机油压,保温温度,操作按钮是否正常,按照技术规定调整压蜡机压射压⼒,射蜡嘴温度,保压时间,冷却时间等。
2.从保温箱中取出蜡缸,装在压蜡机上,挤出上部混有空⽓的蜡料。
3.将模具放在压蜡机⼯作台⾯上,调整射蜡嘴使之与模具注蜡⼝⾼度⼀致,检查模具所有芯⼦,活块位置是否正确,模具开合是否顺利。
4.打开模具,喷薄薄⼀层分型剂,合型,对准射蜡嘴。
5.双⼿按动⼯作按钮,压制蜡模。
6.抽出芯⼦,打开模具,⼩⼼取出蜡模,放在⼯作台⼀侧,合上模具开始压下⼀件,同时对该件粗略检查⽆缺陷后按要求放⼊冷却⽔中或放⼊存放盘中冷却,冷却时间为4⼩时,注意有以下缺陷的蜡模应报废:(1)因模料中卷⼊空⽓,蜡模局部有⿎起的;(2)蜡模任何部位有缺陷的;(3)蜡模有变形不能简单修复的;(4)尺⼨不符合规定的。
7.清除模具上残留的模料,注意只能⽤⽵⼑,不可⽤⾦属⼑⽚清除残留模料,防⽌模具型腔及分型⾯受损,⽤压缩空⽓⽓嘴吹净模具分型⾯。
芯⼦上的蜡屑等,视模具结构及使⽤情况每2-10件喷⼀次分型剂。
8.及时将蜡模从冷却⽔中轻轻取出,⽤压缩空⽓吹净蜡屑及⽔珠,并进⾏⾃检,将合。
放⼊存放盘中。
9.每班下班或模具使⽤完毕后,应⽤软布或棉棒清理模具,如发现模具有损伤或不正常,应⽴即报告领班,由领班处理。
并清扫压蜡机,⼯具及现场,做到清洁、整齐。
三.注意事项:1.压制蜡模时,⾸先必须进⾏检查,确认合格后,⽅可进⾏操作,压蜡模过程中不能轻易变动压制参数。
熔模铸造水玻璃工艺

熔模铸造水玻璃工艺技术管理文件水玻璃铸造工艺守则文件编号:RMZZ/QG-JS-01版本:A修改状态:O受控状态:编制:日期:2004-3-1蜡料制备1.工艺要求:1.1蜡液温度:70-90℃,严禁超过90℃。
1.2稀蜡温度:65-80℃。
1.3蜡膏保温缸水温:48-50℃。
1.4蜡膏应搅拌均匀呈糊状,温度控制在45-48℃,其中不允许有颗粒状蜡料。
1.5蜡料配方蜡料种类材料名称重量配比 1 2 3 4 5 石蜡 50 25 10 5 ? 硬脂酸 50 25 10 5 5 回收蜡 ? 50 80 90 95 1.5.1正常生产采用3、4两种配方,配方5用于压制浇口棒。
1.5.2在生产过程中必须根据蜡模质量分析结果,适量增加或减少硬脂酸量,冬季的酸值取下限,夏季的酸值取上限。
2操作程序2.1?启动设备,检查运转是否正常,是否漏水、漏气、漏蜡,有问题应及时排除。
检查保温缸水温是否符合工艺要求。
2.2?按蜡料配比把石蜡、硬脂酸和回收蜡分别称好,加入化蜡槽内,加热至全熔状态,其温度不得超过90℃。
2.3?把蜡液送到蜡膏搅拌机盛蜡槽内。
2.4?将搅蜡缸内加入三分之二的蜡片,启动搅拌机进行搅蜡直至呈糊状蜡料为止。
3注意事项3.1?稀蜡需用100目筛过滤,去掉杂质后方能使用。
3.2?不允许有影响质量的空气和水分混入蜡膏中。
3.3?化蜡槽和盛蜡槽每月清理两次。
3.4?蜡膏保温缸、搅蜡缸属于压力容器,应定期检查有关紧固件及密封机构的使用情况,发现问题应及时处理,正常工作压力严禁超过0.50MPa。
4检查项目每班必须测量蜡液温度和保温水温度3-4次,控制在工艺要求范围内并做好原始记录。
蜡模制造1?工艺要求1.1室温:16-28℃(最高不超过30℃)。
1.2蜡膏压注温度:45~48℃,压力:0.3~0.5MPa,保压时间:3~10秒。
1.3压蜡冷却水温,14~24℃,冷却时间:20~100秒。
1.4蜡模冷却水温,14~24℃,冷却时间:10~60min。
水玻璃精密铸造

水玻璃精密铸造蜡料制备1.工艺要求:1.1 蜡液温度:70-90℃,严禁超过90℃。
1.2 稀蜡温度:65-80℃。
1.3 蜡膏保温缸水温:48-50℃。
1.4 蜡膏应搅拌均匀呈糊状,温度控制在45-48℃,其中不允许有颗粒状蜡料。
1.5 蜡料配方1.5.2 在生产过程中必须根据蜡模质量分析结果,适量增加或减少硬脂酸量,冬季的酸值取下限,夏季的酸值取上限。
2操作程序2.1 启动设备,检查运转是否正常,是否漏水、漏气、漏蜡,有问题应及时排除。
检查保温缸水温是否符合工艺要求。
2.2 按蜡料配比把石蜡、硬脂酸和回收蜡分别称好,加入化蜡槽内,加热至全熔状态,其温度不得超过90℃。
2.3 把蜡液送到蜡膏搅拌机盛蜡槽内。
2.4 将搅蜡缸内加入三分之二的蜡片,启动搅拌机进行搅蜡直至呈糊状蜡料为止。
3注意事项3.1 稀蜡需用100目筛过滤,去掉杂质后方能使用。
3.2 不允许有影响质量的空气和水分混入蜡膏中。
3.3 化蜡槽和盛蜡槽每月清理两次。
3.4 蜡膏保温缸、搅蜡缸属于压力容器,应定期检查有关紧固件及密封机构的使用情况,发现问题应及时处理,正常工作压力严禁超过0.50MPa。
4检查项目每班必须测量蜡液温度和保温水温度3-4次,控制在工艺要求范围内并做好原始记录。
蜡模制造1 工艺要求1.1 室温:16-28℃(最高不超过30℃)。
1.2 蜡膏压注温度:45~48℃,压力:0.3~0.5 MPa,保压时间:3~10秒。
1.3 压蜡冷却水温,14~24℃,冷却时间:20~100秒。
1.4蜡模冷却水温,14~24℃,冷却时间:10~60min。
1.5蜡模清洗液温度,20~28℃,清洗液中加入0.01% JFC。
1.6 脱模剂:ZF201.1.7蜡模表面光洁度,形状完整,轮廓清洗,尺寸合格,不允许有缩陷,凸包裂纹等缺陷。
2操作程序2.1 手工制模2.1.1检查压型的分型面、型腔、脱模机构、定位销、紧固件应完整清洁。
涂擦分型剂,装配并紧固压型。
精密铸造工艺流程

精密铸造工艺流程精密铸造工艺流程是指通过精密翻模蜡模铸造技术,制造出形状复杂、尺寸精确的零件。
下面是一个精密铸造工艺流程的简单介绍。
首先,确定铸造零件的设计要求和技术要求。
包括零件结构、尺寸、材料、工艺、表面质量等。
然后,根据零件的设计要求,制作蜡模。
蜡模是用粘合剂混合蜡粉制成,填充到铸型中,经过冷却和固化后,取出蜡模。
接下来,组装蜡模。
将多个蜡模件组合起来,形成最终的铸造模具。
在组装过程中,需要注意蜡模的准确定位和组合的牢固性。
然后,制备壳料。
壳料是用于包裹蜡模的硅溶胶或其他陶瓷材料。
制备壳料的过程中,需要先将硅溶胶或陶瓷材料加水,摇匀,然后加固化剂进行固化。
随后,浸泡蜡模。
将蜡模放入制备好的壳料溶液中浸泡,使其表面覆盖上一层薄壳(也称为翻模壳)。
浸泡的时间和温度要根据具体的工艺要求进行控制。
然后,加热蜡模。
将浸泡好的蜡模放入烘箱中进行加热,使蜡模在壳料中热变软,然后慢慢熔化流出,只留下一个空腔,形成空腔铸型。
接着,烘干空腔铸型。
将空腔铸型放入烘箱中,进行烘干,使其内部达到足够坚硬和稳定的状态。
然后,熔炼金属。
在高温熔炉中,将金属原料加热熔化,控制好熔炉中的温度和金属的成分。
随后,浇注金属。
将熔融的金属倒入预热好的铸型中,要控制好铸造温度和速度,使金属能够充分填充铸型的空腔,避免产生缺陷。
接着,冷却铸造件。
待金属充分冷却后,可以从铸型中取出铸造件。
然后,去除壳料。
将铸造件放入除膜设备中,通过高温煤气或水汽蒸汽,去除铸造件表面的壳料。
接下来,进行精加工。
根据零件的要求,进行机械加工、热处理和表面处理等工艺,以获得最终的精密铸造件。
最后,进行零件的检验。
对铸造件进行尺寸精度、外观质量、力学性能等方面的检测,确保零件达到设计要求。
以上就是精密铸造工艺流程的简要介绍。
精密铸造工艺需要严格控制各个环节的参数,确保产品质量。
通过精密铸造工艺,可以制造出高精度、高品质的零件,满足各种工业领域的需求。
- 1、下载文档前请自行甄别文档内容的完整性,平台不提供额外的编辑、内容补充、找答案等附加服务。
- 2、"仅部分预览"的文档,不可在线预览部分如存在完整性等问题,可反馈申请退款(可完整预览的文档不适用该条件!)。
- 3、如文档侵犯您的权益,请联系客服反馈,我们会尽快为您处理(人工客服工作时间:9:00-18:30)。
水玻璃氯化铵法精密铸造工艺规程
1.目的为了便于操作者熟悉和掌握水玻璃法精密铸造的工艺特点、技术特性,更好的在生产中
加以应用,生产出优质的产品,特制定本规程。
2.适用范围本工艺规程适用于从蜡模配制到模壳浇注的全过程。
3.职责
3.1 技术部是本规程的制定和归口部门。
3.2 各工序工作人员均应按此规程进行操作。
4.工艺规程
4.1 制作蜡模
4.1.1 压制蜡模的模具应符合产品的图纸要求,经检验合格后使用。
4.1.2 蜡料应按石蜡:硬脂酸1:1进行配料,融化后加蜡屑机械搅拌成糊状,加入压蜡机内往
模具中注蜡。
4.1.3 蜡型要在模具中保压冷却才可取模,并及时对变形蜡模进行校正,放入冷水冷却,待完
全冷却后方可进行取出毛刺、修整等工作。
4.1.4 修整好的蜡模经检验合格后,清洗表面油脂,方可与浇冒口组焊。
4.1.5 组焊好的模组,需将内外面的蜡屑清除干净后送涂挂制壳。
4.2 制壳
4.2.1 选料面层料浆用320目锆英粉,加固层料浆用200目以上的高铝粉或焦宝石粉和石英粉,粘结剂用模数3.1~3.4,密度为1.30~1.40的40#水玻璃。
4.2.2 选砂面层用80~100目的棕刚玉,二层用40~70目的石英砂,三层用
20~40目的石英砂,
四层以后选用10~20目的石英砂。
4.2.3 料浆的配制面层与二层:将水玻璃加水稀释到密度为1.28~1.30,然后加锆英粉,其比例
为1:1.1~1.2(要注意根据气温变化调节比例),进行机械搅拌,再加入清洗剂0.05%,消泡剂0.05%,继续搅拌,时间不少于6小时,静置4小时熟化,再搅拌均匀方可使用。
三层过渡层
用密度为1.30~1.32的水玻璃加高铝粉和石英粉,比例为1:0.5:0.5。
加固层同三层,比例略为
调厚一点。
4.2.4 料浆的粘度测定用100Ml的流量杯来测定,面层、二层及三层为28~35秒,加固层为
45~50秒。
4.2.5 挂浆将检验合格后的模组浸入搅拌均匀的料浆中,上下移动两次,然后提出,用毛刷将
字和死角处的气泡刺破并刷浆,把多余的料浆刷掉,整个模组要求挂浆均匀,无遗漏,五堆积,然后即可挂砂,整个挂浆过程时间不可过长,以免表面自然硬化,而无法挂砂。
4.2.6 撒砂撒砂的动作要快,避免料浆滴落堆积,撒砂要均匀无空白,撒完砂的模组应放在通
风处自然干燥再投入氯化铵溶液中硬化,从三层以后就可不必自然风干硬化直接投入氯化铵溶液中硬化。
4.2.7 硬化面层硬化15分钟,二三层硬化15~20分钟,加固层40~60分钟
4.2.8 风干根据实际情况酌情操作,控制“不湿不白”为原则。
4.2.9 模组在硬化时,应注意放气、翻身,保证模组的每一部分都硬化充分。
4.2.10 硬化剂的配制选用纯度95%以上的工业氯化铵加水配制,氯化铵溶液的浓度为22~28%, PH值不大于7.5,温度要求在15~25℃,冬天尽量在10℃以上,当硬化剂溶液使用时间较长,浓度有所降低时,要及时补充氯化铵以增加浓度,PH值大于7.5时,要加入浓盐酸进行调整。
4.3 脱蜡
4.3.1 涂刮好的模组,在停放三到四小时后即可进行脱蜡。
4.3.2 将模组浇口处的杂物清除干净后装入脱蜡框内,待脱蜡水温升至90℃,将框落入脱蜡釜中,注意脱蜡框要离开槽底部100mm左右,随即将气阀关小,水温保持在90~95℃,以免水
的沸腾翻滚,将杂物带入型腔,为了在脱蜡过程中对型壳补充硬化,须在水中加入适量的氯化铵。
4.3.3 待到型壳浇口处不再向上浮蜡时,将脱蜡框升离水面,手工将型腔内的
水快速倒出,然
后将型壳倒置放置在干净地面。
4.4 焙烧
4.4.1 脱净蜡的模壳应放置干燥4~6小时,方可入窑焙烧。
4.4.2 模壳焙烧时,浇口向下,先低温烘烤,然后升温焙烧,温度应控制在
800~850℃,保温
1~2小时,随炉冷到500℃以下即可出窑等待浇注,模壳在400℃时强度最大,
浇注时要注意观
察控制。
4.4.3 模壳在搬运过程中,浇口向下,避免沙粒或其它异物落入型腔,造成夹砂等缺陷。
最古早的也是最傳統的鑄造法為濕砂模鑄造法(GREEN SAND CASTING),也就是常聽人提的(翻砂),
造模所用的砂為砂水黏土填加劑混練而成,以中板模為模型,人力(地模,F1-F4)或自動造模機(DISA,新東)造型,優點為模具便宜,可大量生產,適用大多數金屬,價廉,缺點為尺寸精度差,鑄造表面粗糙
度差.
LOST WAX(脫臘法),歷史也很悠久,為傳統之精密鑄造法,是將所欲成品製成臘模後,反覆沾漿,再
將臘以熱溶出,形成模穴之鑄造法,優點為尺寸精度高,鑄造表面光滑,無分模
限制(設計自由度高),
缺點為無法生產大型鑄件,且生產成本高,單價昂貴!
水玻璃(CO2),為大型鑄件生產方式,最常用於鑄鋼鑄鐵,是將砂以水玻璃混合後,通入CO2使其硬化,為早期大型鑄件之生產方式,然其鑄造表面差,鑄後清箱困難,砂回收率低,亦有氣孔與砂孔缺陷,現已漸被樹脂砂模(如夫喃,亞士蘭樹脂)所取代.
(DIE CASTING)壓鑄法,以鋼鐵材料製造模具,用於銅,鋁,鋅等較低溫合金,以
加壓方式將金屬液壓入模穴中,優點為,精度高,鑄造表面佳,缺點為模具費用高,易
有氣孔缺陷(對品質有極大不良之影響).
LOST FOAM 消失模,一般台灣之消失模為FULL MOLD,即以大塊寶麗龍切割成
所要形狀,埋入樹脂砂模中成形,適用於大型鑄件,模具費低,鑄造表面差,另有以鋁
合金模具射出之EPS或EPMMA,經塗型後,埋入乾砂中,澆鑄中施以真空,具有與脫臘
相似之品質,且鑄造成本較低,售價與重力鑄造相仿,然台灣現僅有一家生廠產商.
Investment casting, also called lost-wax casting, is one of the oldest known metal forming techniques.
種類澆鑄熔液品質
1.翻砂(濕砂模) ~鐵銅鋁等 ~低,鑄造缺陷繁多
2.重力鑄造(金屬模) ~鋁合金等 ~高,容易有氣、縮孔缺陷
3.精密鑄造(脫臘鑄造)~適用金屬廣泛~高,相對成本較高
4.高壓鑄造(壓鑄) ~輕合金 ~高,容易有氣孔缺陷
5.消失模法(聚苯乙烯)~適用金屬廣泛~中等,容易變形扭曲
6.自硬性砂模(葫喃) ~鐵銅鋁等 ~低,適合大型鑄鐵件
7.氣硬性砂模(CO2) ~適用金屬廣泛~中等,不利自動造模
8.樹脂殼模法 ~適用金屬廣泛~高,相對成本較高
硅溶胶silica solution
水玻璃sodium silicate。