模具表面处理技术_2.pptx
合集下载
模具表面处理

模具表面处理
目的:通过强化模膛工作表面来提高锻模的寿命。
表面处理工艺如下:1.氮化模具经氮化处理后,可在模膛表面上形成一层硬度高、耐磨损、同时又不易和变形金属粘结的氮化层。
它可提高锻模寿命25%。
2.渗硼渗硼的模具有一层坚硬的硼化层。
它除了特别耐磨外,还有较好的耐蚀性和耐热性。
硼化层的厚度通常在0.05至0.35mm的范围内,当钢中的碳和合金元素含量较高时,宜取下限。
3.喷丸处理通过喷丸处理使模膛表面产生一层硬化层,以提高耐磨性。
4.在模膛表面复盖硬质合金保护层在模膛表面熔焊一层硬质合金,以提高其耐磨性和热稳定性。
模具表面处理技术PPT课件
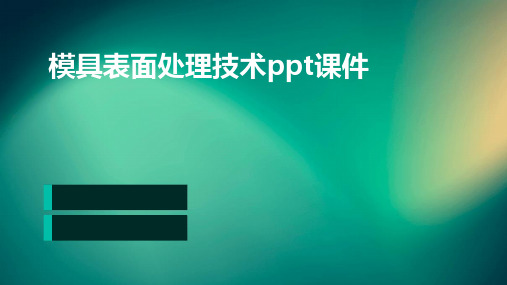
要点二
等离子喷涂技术
通过等离子喷涂将金属或非金属粉末熔融并喷射到模具表 面,形成均匀、致密的涂层,提高表面耐久性和抗腐蚀性 。
智能化和自动化技术的应用
智能监控系统
利用传感器和监测技术实时监测模具表面处理过程,实 现自动化控制和处理。
自动化处理设备
开发自动化表面处理设备,减少人工干预,提高处理效 率和一致性。
耐久性。
提高产品质量和生产效率
提高产品精度和一致性
通过表面处理技术,可以改善模具表 面的粗糙度和形貌,减小产品尺寸和 形状的误差,提高产品的精度和一致 性,从而提高生产效率。
降低生产成本
通过表面处理技术,可以提高模具的 耐磨性和耐久性,减少维修和更换模 具的频率和成本,降低生产成本。
降低生产成本
04 模具表面处理技术的优势 与挑战
提高模具使用寿命
增强模具表面硬度和耐磨 性
通过表面处理技术,可以在模具表面形成一 层高硬度的硬化层,从而提高模具的耐磨性 和抗疲劳性能,延长模具的使用寿命。
降低摩擦系数
通过表面处理技术,可以在模具表面形成一 层低摩擦系数的涂层,减小模具与材料之间 的摩擦力,降低磨损和摩擦热,提高模具的
优化生产流程
通过表面处理技术,可以优化模具的 设计和制造流程,减少加工时间和成 本,提高生产效率。
降低能耗和资源消耗
一些表面处理技术可以降低模具的能 耗和资源消耗,例如离子注入和激光 熔覆等,从而降低生产成本。
技术更新换代快
技术发展迅速
随着科学技术的不断发展,模具 表面处理技术也在不断更新换代 ,新的技术和工艺不断涌现。
常用的五金模具表面处理技术包括喷涂、电镀和化学热处理等。这些技术可以提 高模具表面的硬度和耐久性,降低生产成本和提高产品质量。
模具表面处理技术

530~550 12
20~30 50~60 15~25 30~50
100
30~60
0.3~0.5
≥600HV
0.20~0.28 ≥480HV 0.15~0.2 760~800HV
7.1.2 渗氮
17
4、离子渗氮(又称辉光离子渗氮)
原理:在一定真空度下,利用零件(阴极)与阳极间产生的辉 光放电现象进行的。通入一定的直流电,氨气被电离形成氮离 子和氢离子和电子,这时零件表面形成一层辉光,具有高能量 的氮离子以很大速度轰击零件表面,将动能转换成热能,使零 件表面升高到450~600℃;同时,氮离子在阴极即零件上获得电 子后,还原成为氮原子而渗入零件表面,并向内部扩散而形成 渗氮层。
一段渗氮法 渗氮温度、氨分解率保持不变。 (又称等温渗氮法)渗氮温度:450~530℃。
适合要求高硬度、低变形的浅层 渗氮,渗层氮含量分布变化明显。
二段渗氮法
第一阶段:采用较低的渗氮温度、较低的
氨分解率,使工件表层先形成弥散度高的 处理的工件变形稍大,硬度梯度
高硬度合金氮化物层。
平缓,但渗氮速率较快,生产周
酮、甲苯、甲醇等)。 分类:滴注式气体渗碳(应用最广)、吸热式气氛渗碳等。 渗碳过程:排气、强烈渗碳、扩散、降温。
例:20Cr、20CrMnTi等钢制模具零件的井式气体渗碳工艺
井式气体渗碳工艺
7.1.1 渗碳
12
4、渗碳后的热处理
模具零件渗碳后,表层高碳,心部低碳。为了获得理想的性能, 渗碳后需热处理,即淬火+回火。
常 用 渗 氮 模 具 用 钢 : 38CrMoAl 、 Cr12 、 Cr12MoV 、 3Cr2W8V 、 5CrNiMo、4Cr5MoSiV等;渗氮前一般需调质处理,以保证模具的 整体性能。
20~30 50~60 15~25 30~50
100
30~60
0.3~0.5
≥600HV
0.20~0.28 ≥480HV 0.15~0.2 760~800HV
7.1.2 渗氮
17
4、离子渗氮(又称辉光离子渗氮)
原理:在一定真空度下,利用零件(阴极)与阳极间产生的辉 光放电现象进行的。通入一定的直流电,氨气被电离形成氮离 子和氢离子和电子,这时零件表面形成一层辉光,具有高能量 的氮离子以很大速度轰击零件表面,将动能转换成热能,使零 件表面升高到450~600℃;同时,氮离子在阴极即零件上获得电 子后,还原成为氮原子而渗入零件表面,并向内部扩散而形成 渗氮层。
一段渗氮法 渗氮温度、氨分解率保持不变。 (又称等温渗氮法)渗氮温度:450~530℃。
适合要求高硬度、低变形的浅层 渗氮,渗层氮含量分布变化明显。
二段渗氮法
第一阶段:采用较低的渗氮温度、较低的
氨分解率,使工件表层先形成弥散度高的 处理的工件变形稍大,硬度梯度
高硬度合金氮化物层。
平缓,但渗氮速率较快,生产周
酮、甲苯、甲醇等)。 分类:滴注式气体渗碳(应用最广)、吸热式气氛渗碳等。 渗碳过程:排气、强烈渗碳、扩散、降温。
例:20Cr、20CrMnTi等钢制模具零件的井式气体渗碳工艺
井式气体渗碳工艺
7.1.1 渗碳
12
4、渗碳后的热处理
模具零件渗碳后,表层高碳,心部低碳。为了获得理想的性能, 渗碳后需热处理,即淬火+回火。
常 用 渗 氮 模 具 用 钢 : 38CrMoAl 、 Cr12 、 Cr12MoV 、 3Cr2W8V 、 5CrNiMo、4Cr5MoSiV等;渗氮前一般需调质处理,以保证模具的 整体性能。
模具表面处理技术
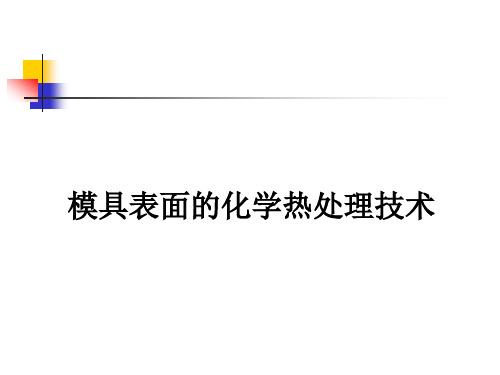
5、真空渗碳
真空渗碳炉是将工件放 置在真空炉内通过不断的向 炉内充入渗碳气氛,使碳原 子渗入工件表面。 与气体渗碳相比真空渗 碳温度高(约1100℃),渗 碳速度快,质量好。
二、渗氮
向工件表面渗入氮元素的工艺称为渗氮, 通常也称为氮化。 钢渗氮后可以获得比渗碳更高的表面硬度 和耐磨性,渗氮还可获得比渗碳更高的弯曲疲劳强 度。此外,由于渗氮温度较低(500一570℃之间), 故变形很小.渗氮也可以提高工件的抗腐蚀性 能.但是渗氮工艺过程较长,渗层也较薄,不能承 受太大的接触应力。目前主要应用于压铸模、挤压 模、冷作模具等。
3、气体法渗金属
一般在密封的罐中进行,把坩埚加热至渗金 属温度,被渗金属的卤化物气体掠过工件表面时 发生置换、还原、热分解等反应,分解出的活性 金属原子渗入工件表面。 以气体渗铬为例,其过程是:把干燥氢气通 过浓盐酸得到HCl气体后引入渗铬罐,在罐的进气 口处放置铬铁粉。当HCl气体通过高温的铬铁粉时, 制得了氯化亚铬气体。当生成的氯化亚铬气体掠 过零件表面时,通过置换、还原、热分解等反应, 在零件表面沉积铬,从而获得渗铬层。
碳氮共渗的分类
(1)碳氮共渗 以渗碳为主,共渗温度
820-870℃,渗剂为煤油、苯、甲苯、丙酮等, 同时通入氨气,或使用尿素、甲酰胺等。材料 一般为中、低碳钢及合金钢。
以渗氮为主,共渗温度 550-570℃,渗剂为尿素、甲酰胺、三乙醇胺等。 材料不受限制。
碳氮共渗已应用于压铸模、挤压模、塑料 模等。
渗铬过程
2、液体法渗金属
分为两种,一种是盐浴法,一种是热浸法。 目前最常用的盐浴法渗金属是TD法。它是在熔融 的硼砂浴中加入被渗金属粉末,工件在盐浴中被加热, 同时还进行渗金属的过程。 以渗钒为例:把欲渗工件放人 (80—85%)硼砂 Na2B407(20~15)%钒铁粉盐浴中,在950℃保温3—5 小时,即可得到一定厚度(几个微米到20微米)的渗钒 层。
模具表面强化技术(二)

• TiN、TiC涂层具有以下特点: • 1)涂层具有很高的硬度低的摩擦系数和自润 滑 性能,所以抗磨粒磨损性能良好。 • 2)涂层具有很高的熔点、化学稳定性好,基 体金属在涂层中 的溶解度小,以及较低的摩擦 系数,因而具有很好的抗粘着磨损能力。使用 中发生冷焊和咬 合的倾向也很小。 • 3)涂层具有较强的抗蚀能力。 • 4)涂层在高温下也具有良好的抗大气氧化能力:
• 四、气相沉积技术 • 气相沉积是通过气相中发生的物理、化学过程, 改变表面成分,在工件表面形成功能性 (例如超 硬耐磨层或具有特殊的光学、电学性能)或装饰 性的化合物涂层的新技术。 • 按过程的主要属性可将气相沉积分为化学气相 沉积 (CVD)和物理气相沉积(PVD)两大类。 • 气相沉积是模具 表面强化的新技术之一,己广 泛应用于各类模具的表面硬化处理,主要应用 的沉积层为TiC、 TiN、Ti (C, N) 。
• 三、化学镀 • 化学镀是将工件置于镀液中,镀液中的金属离子通 过获得由镀液中的化学反应而产生的 电子,在工件 表面上还原沉积而形成镀层。它从本质上说是一个 无外加电场的电化学过程。 • 化学镀可获得单一金属镀层、合金镀层、复合镀层 和非晶态镀层。 • 与电镀、刷镀相比,化 学镀的优点是:均镀能力和深 度能力好,具有良好的仿型性;沉积厚度可控,镀层 致密与基体结合良好;设备简单,操作方便。复杂形 状模具的化学镀,还可以避免常规热处理引起的变 形。
• 采用PVD技术可以在各种材料上沉积致密、光 滑、高精度的化合物(如TiC、 TiN)涂层,所以 十分适合模具的表面处理。目前,应用PVD法 沉积TiC、TiN等涂层已在模具生产中获得应用。 例如,Crl2MoV钢制油开关指形触头精冲模, 经PVD法沉积TiN后,表面硬度为2500~ 3000HV,摩擦系数减小,抗粘着和抗咬合性 改善。模具原使用1~3万次后即要刃磨,PVD 法处理后,使用10万次不需刃磨,尺寸无变化, 仍可使用。用于冲压和挤压粘性材料的冷作模 具,采用PVD法处理后,其使用寿命大为提高, 从发展趋势来看,PVD法将成为模具表面处理 的主要技术方法之一。
- 1、下载文档前请自行甄别文档内容的完整性,平台不提供额外的编辑、内容补充、找答案等附加服务。
- 2、"仅部分预览"的文档,不可在线预览部分如存在完整性等问题,可反馈申请退款(可完整预览的文档不适用该条件!)。
- 3、如文档侵犯您的权益,请联系客服反馈,我们会尽快为您处理(人工客服工作时间:9:00-18:30)。
Page 16
Page 4
任务6.1 表面化学热处理技术
一、渗碳
(二)固体渗碳
图6-1 滴注式气体渗碳炉工作示意 图6-2 固体渗碳装箱示意
Page 5
任务6.1 表面化学热处理技术
二、渗氮(氮化)
渗氮也称为氮化,是指在一定温度下使 活性氮原子渗入工件表面的表面化学热 处理工艺。
Page 6
任务6.1 表面化学热处理技术
Page 15
任务6.1 表面化学热处理技术
四、碳氮共渗与氮碳共渗
(二)氮碳共渗
气体氮碳共渗所用的温度常采用560~570℃,时间为2~3h。 与气体渗氮相比,低温气体氮碳共渗的特点有:
(1) 渗入温度低,时间短,工件变形小。
(2) 不受钢种限制,碳钢、低碳合金钢、工具钢及不锈钢 等材料均可进行低温气体氮碳共渗。 (3) 能显著提高工件的疲劳极限、耐磨性和耐蚀性。 (4) 共渗层硬而具有一定的韧性,不易剥落。
0.2~0.3
14~27 36~60
≤0.2
一段
490
24
15~35 0.2~0.3
40Cr 二段
Ⅰ Ⅱ
480±10 500±10
20 15~20
20~30 50~60
0.3~0.5
表面硬度
>58HRC 720~ 860HV
≥600HV
≥600HV
4Cr5MoV1 Si
一段
—
530~550
12
30~60
提高硬度、耐磨性、热硬性 提高硬度、强度、耐磨性、耐疲劳性、抗蚀性 提高硬度、强度、耐磨性、耐疲劳性、抗蚀性
挤压模冲头、芯杆针尖 冷、热挤压模等 热挤压模、冲头针尖
Page 2
任务6.1 表面化学热处理技术
表面化学热处理的作用主要有以下两个方面。 (1) 强化工件表面 (2) 保护工件表面
Page 3
任务6.1 表面化学热处理技术
一、渗碳
(一)气体渗碳
气体渗碳是将工件置于密闭的渗碳炉中加热 到900~950℃(常用930℃),通入渗碳气体( 如煤气、石油液化气和丙烷等)或易分解的有 机液体(如煤油、甲苯和甲醇等),在高温下通 过反应分解出活性碳原子,活性碳原子渗入 工件表面的高温奥氏体中,并通过扩散形成 一定厚度的渗碳层。
(二)离子渗氮
表6-3 部分模具钢的离子渗氮工艺与使用效果
模具名称
模具材料
离子渗氮工艺
使用效果
冲头
W18Cr4V
500~,6h
提高2~4倍
铝压铸模
3Cr2W8V
500~,6h
提高1~3倍
热锻模
5CrMnMo
480~,6h
提高3倍
冷挤压模
W6Mo5Cr4V2
500~,2h
提高1.5倍
压延模
Cr12MoV
四、碳氮共渗与氮碳共渗
(一)碳氮共渗
低温(500~600℃)
高温(900~950℃)
根据共渗温度 的不同
中温(700~880℃)
Page 14
任务6.1 表面化学热处理技术
四、碳氮共渗与氮碳共渗
气体碳氮共渗的特点如下: (1) 共渗层的力学性能综合了渗碳和渗氮的优点。
(2) 碳氮共渗使共渗层的奥氏体相温度降低。 (3) 氮的渗入使共渗层的奥氏体的稳定性提高,渗层的淬 火性提高,这样共渗后除可以用冷却速度较缓慢的介质 进行淬火而减少变形外,还可以用较便宜的碳素钢代替 低合金钢制造某些模具。 (4) 气体碳氮共渗的速度大于单独渗碳或渗氮的速度, 缩短了生产周期。
挤压模、冷挤模等
可消除表面白色的脆化层,耐磨性、耐疲劳性和变形均 优于氮化
挤压模、挤压工具等
相比渗碳和渗氮,具有更高的硬度、耐磨性、耐疲劳性、成型模、冷挤模、热挤模和模
热硬性、热强性,生产周期短
架等
提高硬度、耐磨性、抗粘附性、抗蚀性、耐热疲劳性
冷挤模、拉深模、挤压模穿孔 针
具有极好的表面硬度、耐磨性、抗粘附性、抗氧化性、 热硬性、良好的抗蚀性
项目6 模具表面处理技术
项目6 模具表面处理技术
表6-1 模具表面处理技术的作用及应用
处理工艺 渗碳 渗氮
离子渗碳
碳氮共渗
氮碳共渗
渗硼 碳氮硼三元共渗 盐浴覆层 (TD处理) 渗铬
作用
应用
提高硬度(52~56HRC)、耐磨性、耐疲劳性
挤压模、穿孔工具等
提高硬度、耐磨性、抗粘附性、热硬性、耐疲劳性、抗 蚀性(但周期长,表面有白色脆化层)
二、渗氮(氮化)
气体渗氮
常
用
离子渗氮
的
渗
真空渗氮
氮
方
电解催渗渗氮
法
氮碳共渗
Page 7
任务6.1 表面化学热处理技术
二、渗氮(氮化)
(一)气体渗氮
(1) 经过渗氮后钢表面形成一层极硬的合金氮化物,渗氮层的硬度 一般可达到68~72HRC,不需要再经过淬火便具有很高的表面硬 度和耐磨层,而且还可以保持到600~650℃而不明显下降。 (2) 渗氮后钢的疲劳极限可提高15%~35%。这是由于渗氮层的 体积增大,使工件表面产生了残余压应力。 (3) 渗氮后的钢具有很高的抗腐蚀能力。 (4) 渗氮处理后,工件的变形很小,适合精密模具的表面强化。
Page 8
任务6.1 表面化学热处理技术
二、渗氮(氮化)
(一)气体渗氮
表6-2 部分模具钢的气体渗氮工艺规范
牌号
处理 方法
30CrMnSi A
一段
Cr12MoV 二段
阶段 — Ⅰ Ⅱ
渗氮工艺规范 渗氮温度/℃ 时间/h
500±5
25~30
480
18
530
25
氨分解率 /%
20~30
渗氮层 深度/mm
500~,2h
提高5倍
Page 11
任务6.1 表面化学热处理技术
三、渗硫
渗硫 方法 可按 介质 的物 理状 态
熔盐渗硫 气体渗硫
Page 12
任务6.1 表面化学热处理技术
四、碳氮共渗与氮碳共渗
(一)碳氮共渗
液体碳氮共渗
固体碳氮共渗
根据使用介质 物理状况不同
气体碳氮共渗
Page 13
任务6.1 表面化学热处理技术
挤压模、拉深模
提高硬度、强度、耐磨性、耐疲劳性、抗蚀性
挤压模、冲头针尖
提高硬度、耐磨性、耐热疲劳性、抗蚀性、抗粘附性、 抗氧化性
挤压模
提高硬度、耐磨性、抗蚀性、抗粘附性、抗氧化性 挤压模、拉深模
镀硬铬
降低表面粗糙度,提高表面硬度、耐疲劳性、抗蚀性 挤压模、拉深模等
钴基合金堆焊 电火花表面强化 喷丸处理0.1ຫໍສະໝຸດ ~0.2760~ 800HV
Page 9
任务6.1 表面化学热处理技术
二、渗氮(氮化)
(二)离子渗氮
离子渗氮有如下特点: (1) 渗氮速度快,生产周期短。 (2) 渗氮层质量高。 (3) 工件的变形小。 (4) 对材料的适应性强。
Page 10
任务6.1 表面化学热处理技术
二、渗氮(氮化)
Page 4
任务6.1 表面化学热处理技术
一、渗碳
(二)固体渗碳
图6-1 滴注式气体渗碳炉工作示意 图6-2 固体渗碳装箱示意
Page 5
任务6.1 表面化学热处理技术
二、渗氮(氮化)
渗氮也称为氮化,是指在一定温度下使 活性氮原子渗入工件表面的表面化学热 处理工艺。
Page 6
任务6.1 表面化学热处理技术
Page 15
任务6.1 表面化学热处理技术
四、碳氮共渗与氮碳共渗
(二)氮碳共渗
气体氮碳共渗所用的温度常采用560~570℃,时间为2~3h。 与气体渗氮相比,低温气体氮碳共渗的特点有:
(1) 渗入温度低,时间短,工件变形小。
(2) 不受钢种限制,碳钢、低碳合金钢、工具钢及不锈钢 等材料均可进行低温气体氮碳共渗。 (3) 能显著提高工件的疲劳极限、耐磨性和耐蚀性。 (4) 共渗层硬而具有一定的韧性,不易剥落。
0.2~0.3
14~27 36~60
≤0.2
一段
490
24
15~35 0.2~0.3
40Cr 二段
Ⅰ Ⅱ
480±10 500±10
20 15~20
20~30 50~60
0.3~0.5
表面硬度
>58HRC 720~ 860HV
≥600HV
≥600HV
4Cr5MoV1 Si
一段
—
530~550
12
30~60
提高硬度、耐磨性、热硬性 提高硬度、强度、耐磨性、耐疲劳性、抗蚀性 提高硬度、强度、耐磨性、耐疲劳性、抗蚀性
挤压模冲头、芯杆针尖 冷、热挤压模等 热挤压模、冲头针尖
Page 2
任务6.1 表面化学热处理技术
表面化学热处理的作用主要有以下两个方面。 (1) 强化工件表面 (2) 保护工件表面
Page 3
任务6.1 表面化学热处理技术
一、渗碳
(一)气体渗碳
气体渗碳是将工件置于密闭的渗碳炉中加热 到900~950℃(常用930℃),通入渗碳气体( 如煤气、石油液化气和丙烷等)或易分解的有 机液体(如煤油、甲苯和甲醇等),在高温下通 过反应分解出活性碳原子,活性碳原子渗入 工件表面的高温奥氏体中,并通过扩散形成 一定厚度的渗碳层。
(二)离子渗氮
表6-3 部分模具钢的离子渗氮工艺与使用效果
模具名称
模具材料
离子渗氮工艺
使用效果
冲头
W18Cr4V
500~,6h
提高2~4倍
铝压铸模
3Cr2W8V
500~,6h
提高1~3倍
热锻模
5CrMnMo
480~,6h
提高3倍
冷挤压模
W6Mo5Cr4V2
500~,2h
提高1.5倍
压延模
Cr12MoV
四、碳氮共渗与氮碳共渗
(一)碳氮共渗
低温(500~600℃)
高温(900~950℃)
根据共渗温度 的不同
中温(700~880℃)
Page 14
任务6.1 表面化学热处理技术
四、碳氮共渗与氮碳共渗
气体碳氮共渗的特点如下: (1) 共渗层的力学性能综合了渗碳和渗氮的优点。
(2) 碳氮共渗使共渗层的奥氏体相温度降低。 (3) 氮的渗入使共渗层的奥氏体的稳定性提高,渗层的淬 火性提高,这样共渗后除可以用冷却速度较缓慢的介质 进行淬火而减少变形外,还可以用较便宜的碳素钢代替 低合金钢制造某些模具。 (4) 气体碳氮共渗的速度大于单独渗碳或渗氮的速度, 缩短了生产周期。
挤压模、冷挤模等
可消除表面白色的脆化层,耐磨性、耐疲劳性和变形均 优于氮化
挤压模、挤压工具等
相比渗碳和渗氮,具有更高的硬度、耐磨性、耐疲劳性、成型模、冷挤模、热挤模和模
热硬性、热强性,生产周期短
架等
提高硬度、耐磨性、抗粘附性、抗蚀性、耐热疲劳性
冷挤模、拉深模、挤压模穿孔 针
具有极好的表面硬度、耐磨性、抗粘附性、抗氧化性、 热硬性、良好的抗蚀性
项目6 模具表面处理技术
项目6 模具表面处理技术
表6-1 模具表面处理技术的作用及应用
处理工艺 渗碳 渗氮
离子渗碳
碳氮共渗
氮碳共渗
渗硼 碳氮硼三元共渗 盐浴覆层 (TD处理) 渗铬
作用
应用
提高硬度(52~56HRC)、耐磨性、耐疲劳性
挤压模、穿孔工具等
提高硬度、耐磨性、抗粘附性、热硬性、耐疲劳性、抗 蚀性(但周期长,表面有白色脆化层)
二、渗氮(氮化)
气体渗氮
常
用
离子渗氮
的
渗
真空渗氮
氮
方
电解催渗渗氮
法
氮碳共渗
Page 7
任务6.1 表面化学热处理技术
二、渗氮(氮化)
(一)气体渗氮
(1) 经过渗氮后钢表面形成一层极硬的合金氮化物,渗氮层的硬度 一般可达到68~72HRC,不需要再经过淬火便具有很高的表面硬 度和耐磨层,而且还可以保持到600~650℃而不明显下降。 (2) 渗氮后钢的疲劳极限可提高15%~35%。这是由于渗氮层的 体积增大,使工件表面产生了残余压应力。 (3) 渗氮后的钢具有很高的抗腐蚀能力。 (4) 渗氮处理后,工件的变形很小,适合精密模具的表面强化。
Page 8
任务6.1 表面化学热处理技术
二、渗氮(氮化)
(一)气体渗氮
表6-2 部分模具钢的气体渗氮工艺规范
牌号
处理 方法
30CrMnSi A
一段
Cr12MoV 二段
阶段 — Ⅰ Ⅱ
渗氮工艺规范 渗氮温度/℃ 时间/h
500±5
25~30
480
18
530
25
氨分解率 /%
20~30
渗氮层 深度/mm
500~,2h
提高5倍
Page 11
任务6.1 表面化学热处理技术
三、渗硫
渗硫 方法 可按 介质 的物 理状 态
熔盐渗硫 气体渗硫
Page 12
任务6.1 表面化学热处理技术
四、碳氮共渗与氮碳共渗
(一)碳氮共渗
液体碳氮共渗
固体碳氮共渗
根据使用介质 物理状况不同
气体碳氮共渗
Page 13
任务6.1 表面化学热处理技术
挤压模、拉深模
提高硬度、强度、耐磨性、耐疲劳性、抗蚀性
挤压模、冲头针尖
提高硬度、耐磨性、耐热疲劳性、抗蚀性、抗粘附性、 抗氧化性
挤压模
提高硬度、耐磨性、抗蚀性、抗粘附性、抗氧化性 挤压模、拉深模
镀硬铬
降低表面粗糙度,提高表面硬度、耐疲劳性、抗蚀性 挤压模、拉深模等
钴基合金堆焊 电火花表面强化 喷丸处理0.1ຫໍສະໝຸດ ~0.2760~ 800HV
Page 9
任务6.1 表面化学热处理技术
二、渗氮(氮化)
(二)离子渗氮
离子渗氮有如下特点: (1) 渗氮速度快,生产周期短。 (2) 渗氮层质量高。 (3) 工件的变形小。 (4) 对材料的适应性强。
Page 10
任务6.1 表面化学热处理技术
二、渗氮(氮化)