数控机床进给系统设计
CK6140数控车床进给系统设计(全套图纸+论文)

摘要CK6140型数控机床,主运动系统采用1.26和1.58两种公比的混合公比传动系统,并用双速电机驱动,结构简单转速范围广。
合理地确定有关结构参数及动力参数,并对传动轴、齿轮、键等进行粗算及检验计算。
粗选步进电机及滚珠丝杠,构成开环控制系统。
关键词:数控;机床;开环控制第1章绪论1.1数控机床的发展趋势我国数控机床产量持续高速增长,根据市场需求和技术发展趋势,应重点推进高效、精密为核心的数控机床“”级工程,加强民展性能、高可靠性数控功能部件,积极开展复合加工机床、超精密数控机床和可重构制造系统的工程化研究等机械加工装备产业、构建数字化企业的重要基础,镄的民展一直备受人们关注。
数控机床以其卓越的柔性的自动化的性能、优异而稳定的精度、灵捷而多样化的功能引起世人瞩目。
它开创了机械产品向机电一体化发展的先河,因此数控技术成为先进成为先进制造技术的一项核心技术。
通过持续的开发研究以及对信息技术的深化应用,促进了数控机床性能和质量的进一步提升,使数控机床成为国民经济和国防建设发展的重要制造装备。
近6年来,我国数控金切机床(简称数控机床)产量一直以年均增长超过30%速度发展。
据初步统计,2004年数控机床的产量为51860台,事比增长40.8%,数控机床的消费量约74000台,事比增长32%。
数控机床需求的旺盛也促进了2004年内建的三资和民营机床厂以及数控机床品种的明显增加。
与此同时,甸进口的数控机床数量也在逐年同步增加,而且进口数控机床的消费额的增长趋势更快。
2004年数控机床的进口数量同比年增长30%,而进口消费额的增长却达52%,从而导致国产数控机床在国内市场消费额中的所占比例已不足30%。
之所以出现这一现象,其主要原因在于国内市场对技术和附加值高的高效、精密和高性能大型、重型数控机床需求增长,需要靠进口解决。
振兴我国数控机床市场占有率应着重于剖析数控机床及由其组成的制造系统(生产线)的技术现况及民展趋势,探讨使其能适应变批量,多品种、高质量、低成本以及具有快速响应的柔性和符合环保的未来生产模式的解决方案。
立式数控铣床进给传动系统设计

课程设计任务书目录1.概述 (3)1.1技术要求 (3)1.2总体设计方案 (3)2.滚珠丝杠螺母副的选型和计算 (3)2.1主切削力及其切削分力计算 (3)2.2导轨摩擦力的计算 (4)2.3计算滚珠丝杠螺母副的轴向负载力 (4)2.4滚珠丝杠的动载荷计算与直径估算 (5)3.工作台部件的装配图设计 (9)4.滚珠丝杠螺母副的承载能力校验 (9)4.1滚珠丝杆螺母副临界压缩载荷的校验 (9)4.2滚珠丝杆螺母副临界转速的校验 (9)4.3滚珠丝杆螺母副额定寿命的校验 (10)5.计算机械传动系统的刚度 (10)5.1机械传动系统的刚度计算 (10)5.2滚珠丝杠螺母副扭转刚度的计算 (11)6.驱动电动机的选型与计算 (11)6.1计算折算到电动机轴上的负载惯量。
(11)6.2计算折算到电动机轴上的负载力矩 (12)6.3 计算坐标轴折算到电动机轴上的各种所需力矩 (13)6.4选择驱动电动机的型号 (14)7.确定滚珠丝杠螺母副的精度等级和规格型号 (14)7.1确定滚珠丝杠螺母副的精度等级 (14)7.2滚珠丝杠螺母副的规格型号 (15)8. 课程设计总结 (15)9.参考文献 (15)1.概述1.1技术要求工作台、工件和夹具的总质量m=918kg,其中,工作台的质量510kg;工作台的最大行程Lp=600 mm;工作台快速移动速度18000mm/min;工作台采用贴塑导轨,导轨的动摩擦系数为0.15,静摩擦系数为0.12;工作台的定位精度为30μm,重复定位精度为15μm;机床的工作寿命为20000h(即工作时间为10年)。
机床采用主轴伺服电动机,额定功率为5.5kw,机床采用端面铣刀进行强力切削,铣刀直径125mm,主轴转速310r/min。
切削状况如下:数控铣床的切削状况1.2总体设计方案为了满足以上技术要求,采取以下技术方案:(1)工作台工作面尺寸(宽度×长度)确定为400mm×1200mm。
数控机床横向进给系统及结构设计
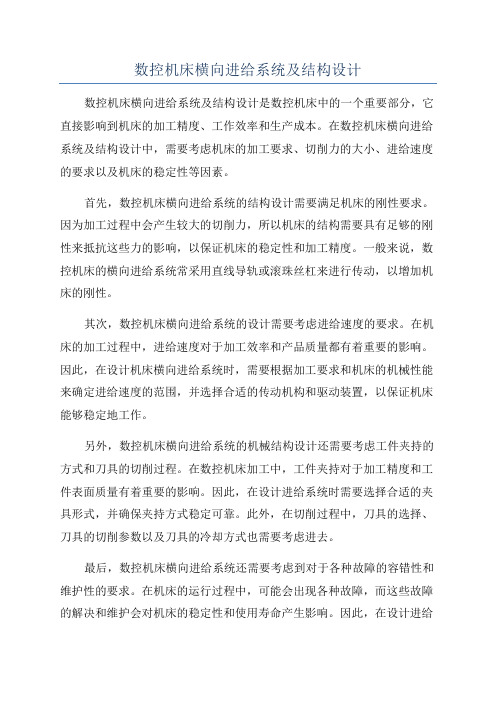
数控机床横向进给系统及结构设计数控机床横向进给系统及结构设计是数控机床中的一个重要部分,它直接影响到机床的加工精度、工作效率和生产成本。
在数控机床横向进给系统及结构设计中,需要考虑机床的加工要求、切削力的大小、进给速度的要求以及机床的稳定性等因素。
首先,数控机床横向进给系统的结构设计需要满足机床的刚性要求。
因为加工过程中会产生较大的切削力,所以机床的结构需要具有足够的刚性来抵抗这些力的影响,以保证机床的稳定性和加工精度。
一般来说,数控机床的横向进给系统常采用直线导轨或滚珠丝杠来进行传动,以增加机床的刚性。
其次,数控机床横向进给系统的设计需要考虑进给速度的要求。
在机床的加工过程中,进给速度对于加工效率和产品质量都有着重要的影响。
因此,在设计机床横向进给系统时,需要根据加工要求和机床的机械性能来确定进给速度的范围,并选择合适的传动机构和驱动装置,以保证机床能够稳定地工作。
另外,数控机床横向进给系统的机械结构设计还需要考虑工件夹持的方式和刀具的切削过程。
在数控机床加工中,工件夹持对于加工精度和工件表面质量有着重要的影响。
因此,在设计进给系统时需要选择合适的夹具形式,并确保夹持方式稳定可靠。
此外,在切削过程中,刀具的选择、刀具的切削参数以及刀具的冷却方式也需要考虑进去。
最后,数控机床横向进给系统还需要考虑到对于各种故障的容错性和维护性的要求。
在机床的运行过程中,可能会出现各种故障,而这些故障的解决和维护会对机床的稳定性和使用寿命产生影响。
因此,在设计进给系统时,需要考虑到对故障的容错性设计和维护的便利性,以保证机床能够稳定地运行。
综上所述,数控机床横向进给系统及结构设计是一个综合性的过程,需要考虑到机床的加工要求、切削力的大小、进给速度的要求以及机床的稳定性等因素。
通过合理的设计,可以使机床的进给系统更加稳定可靠,从而提高加工效率和产品质量。
数控机床纵向进给伺服系统设计综述
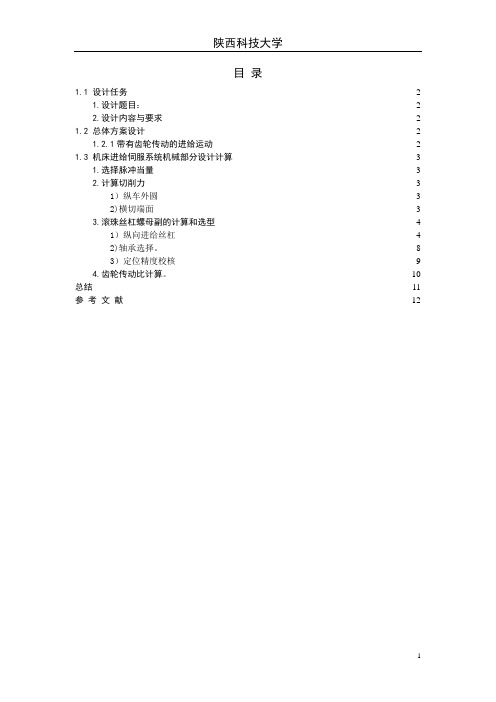
陕西科技大学目录1.1 设计任务 (2)1.设计题目: (2)2.设计内容与要求 (2)1.2 总体方案设计 (2)1.2.1带有齿轮传动的进给运动 (2)1.3 机床进给伺服系统机械部分设计计算 (2)1.选择脉冲当量 (2)2.计算切削力 (2)1)纵车外圆 (2)2)横切端面 (2)3.滚珠丝杠螺母副的计算和选型 (3)1)纵向进给丝杠 (3)2)轴承选择。
(7)3)定位精度校核 (8)4.齿轮传动比计算。
(9)总结 (10)参考文献 (11)数控机床纵向进给伺服系统设计1.1 设计任务1.设计题目:数控机床纵向进给伺服系统设计2.设计内容与要求课题说明某一数控机床纵向进给伺服系统设计要求如下:纵向最大进给力为5000N,工作台重300Kg,工件及夹具的最大重量为500Kg,工作台纵向行程680mm,进给速度1~4000mm/min,快速速度15m/min。
导轨为矩形,表面粘贴聚四氟乙烯软带(摩擦系数为:0.04)。
要求的定位精度为±0.006mm。
设计内容——传动系统设计,主要包括运动转换机构、连接支撑方式等。
设计参数如下:(1)纵向行程:680mm(2)最大加工直径:在床面上 400mm在床鞍上 210mm(3)最大加工长度:1000mm(4)纵向进给速度:0.001~4m/min(5)纵向快速速度:15m/min(6)工作台重:300Kg(7)工件及夹具的最大重量:500Kg(8)摩擦系数为:0.04(9)代码制:ISO1.2 总体方案设计1.2.1带有齿轮传动的进给运动图1—1图1—2数控机床的伺服进给系统采用闭环系统,由于是数控机床纵向伺服系统,总体方案,从电动机出来带有齿轮传动,配上滚珠丝杠(采用滚珠丝杠可以提高系统的精度和纵向进给整体刚度)。
1.3 机床进给伺服系统机械部分设计计算1.选择脉冲当量根据设计任务书要求确定脉冲当量,纵向为0.01mm/步,横向为0.005mm/步(半径)。
数控车床纵向进给传动系统设计(含全套CAD图纸)
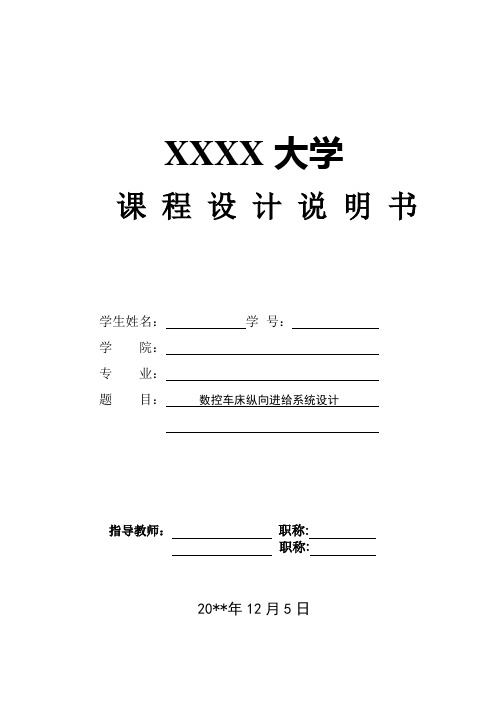
XXXX大学课程设计说明书学生姓名:学号:学院:专业:题目:数控车床纵向进给系统设计指导教师:职称:职称:20**年12月5日任务书学院专业班级学生:题目:数控车床纵向进给系统设计课程设计从20** 年12 月22 日起到20** 年1 月 5 日1、课程设计的内容和要求(包括原始数据、技术要求、工作要求等):课程设计的内容:(1)设计数控车床纵向进给系统传动设计;结构设计;主要零件设计(选择一个主要零件轴或齿轮)(2)编写设计说明书主要内容包括:机床的用途及主要技术参数,数控车床纵向进给系统传动的方案设计、动力计算、结构设计、零件设计、结果分析、设计体会及今后的改进等设计过程设计要求:车床控制精度:0.01mm(即为脉冲当量);最大进给速度:V max=5m/min。
设计参数:最大加工直径为D max=400mm,工作台及刀架重:110㎏;最大轴向力=160㎏;导轨静摩擦系数=0.2;行程=1280mm;步进电机:110BF003;步距角:0.75°;电机转动惯量:J=1.8×10-2㎏.cm.s-2;主要参考资料:机床课程设计指导书,挂图,机床设计手册、数控机床等教材2、对课程设计成果的要求〔包括图表、实物等硬件要求〕:(1)图纸进给系统装配图A1一张;消隙齿轮箱装配图A1 一张;(2)说明书方案设计、运动设计、结构设计、零件设计、结果分析、体会及今后的改进、参考资料3目录一、数控机床进给系统概述 (1)二、主要设计任务参数 (3)三、数控车床纵向进给系统传动的方案设计 (3)1、纵向进给系统设计的基本要求 (3)1、带有齿轮传动的进给运动................................... (3)2、经同步带轮传动的进给运动 (4)3、电机通过联轴器直接与丝杠联接 (5)四、运动设计 (5)1、降速比计算 (5)2、减速齿轮的确定 (6)五、丝杠螺母机构的选择与计算 (6)1、动载强度计算 (6)2、静强度计算 (7)3、临界转速校核 (8)4、额定寿命的校核 (8)六、动力计算 (8)1、传动件转动惯量的计算 (8)2、电动机力矩的计算 (9)七、丝杠螺母机构的传动刚度计算 (10)八、结构设计 (11)1、滚珠丝杠的支承 (11)2、滚珠丝杠螺母副间隙消除和预紧 (12)九、主要结构性能及特点的分析 (12)十、总结与体会 (13)参考文献 (14)一、数控机床进给系统概述数控机床伺服系统的一般结构如图图1-1所示:图1-1数控机床进给系统伺服相对于传统机床,数控机床有以下明显的优越性:(1) 提高生产率。
数控车床进给系统设计

数控车床进给系统设计一、进给系统的结构设计1.可靠性高:进给系统的关键零部件应采用优质的材料和加工工艺,以保证系统的稳定性和长寿命。
2.刚性好:进给系统的结构应具备足够的刚度,以保证在高速切削和大负载的工况下,机床能够保持稳定运行。
3.灵活性强:设计时应考虑到不同工件的加工要求,进给系统应能够快速调整和变换,以满足不同工件的加工需求。
二、进给系统的控制方法设计1.PTP控制方式:即点对点控制方式,根据工件形状和切削要求设计程序,实现工件形状的控制和切削路径的规划。
2.直线插补控制方式:通过数学模型进行直线切削路径的插补计算,实现工件形状的控制和切削路径的规划。
3.圆弧插补控制方式:通过数学模型进行圆弧切削路径的插补计算,实现工件形状的控制和切削路径的规划。
三、进给系统的传动方式设计传统数控车床进给系统的传动方式有液压传动和蜗杆传动两种,在设计进给系统时需要选择合适的传动方式,以满足不同加工工况的需求。
1.液压传动:液压传动以其可适应性强、能源利用率高等优点,在高负载和高速切削的工况下表现出较好的性能。
2.蜗杆传动:蜗杆传动以其结构简单、体积小、传动精度高等优点,在精密加工和高速加工的场合得到广泛应用。
四、进给系统的反馈装置设计进给系统的反馈装置是保证机床加工精度的重要组成部分,主要分为位置反馈和力反馈两种。
设计反馈装置时需要考虑以下几个因素:1.精度要求:根据机床加工的精度要求选择合适的反馈装置,以保证加工精度的稳定性。
2.反馈方式:根据加工工况选择合适的反馈方式,如光电编码器、脉冲等。
3.反馈信号的处理:对反馈信号进行合理的滤波和放大处理,以保证控制系统的稳定性和精度。
总之,数控车床进给系统的设计直接影响机床的加工精度和工作效率。
在设计进给系统时应考虑到结构、控制方法、传动方式和反馈装置等方面的因素,以满足不同加工要求。
同时,还需要对系统进行可靠性和稳定性分析,以确保数控车床的长期稳定运行。
数控机床横向进给设计
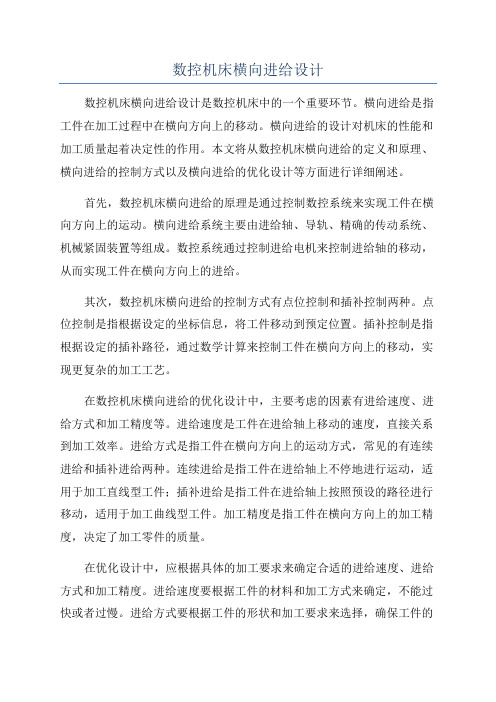
数控机床横向进给设计数控机床横向进给设计是数控机床中的一个重要环节。
横向进给是指工件在加工过程中在横向方向上的移动。
横向进给的设计对机床的性能和加工质量起着决定性的作用。
本文将从数控机床横向进给的定义和原理、横向进给的控制方式以及横向进给的优化设计等方面进行详细阐述。
首先,数控机床横向进给的原理是通过控制数控系统来实现工件在横向方向上的运动。
横向进给系统主要由进给轴、导轨、精确的传动系统、机械紧固装置等组成。
数控系统通过控制进给电机来控制进给轴的移动,从而实现工件在横向方向上的进给。
其次,数控机床横向进给的控制方式有点位控制和插补控制两种。
点位控制是指根据设定的坐标信息,将工件移动到预定位置。
插补控制是指根据设定的插补路径,通过数学计算来控制工件在横向方向上的移动,实现更复杂的加工工艺。
在数控机床横向进给的优化设计中,主要考虑的因素有进给速度、进给方式和加工精度等。
进给速度是工件在进给轴上移动的速度,直接关系到加工效率。
进给方式是指工件在横向方向上的运动方式,常见的有连续进给和插补进给两种。
连续进给是指工件在进给轴上不停地进行运动,适用于加工直线型工件;插补进给是指工件在进给轴上按照预设的路径进行移动,适用于加工曲线型工件。
加工精度是指工件在横向方向上的加工精度,决定了加工零件的质量。
在优化设计中,应根据具体的加工要求来确定合适的进给速度、进给方式和加工精度。
进给速度要根据工件的材料和加工方式来确定,不能过快或者过慢。
进给方式要根据工件的形状和加工要求来选择,确保工件的加工精度。
加工精度要根据工件的尺寸要求和加工精度要求来确定,必须保证工件的尺寸和形状与图纸要求一致。
此外,在数控机床横向进给的设计中,还要考虑进给轴的刚性和工件的稳定性。
进给轴的刚性要足够强,以确保工件在加工过程中的稳定性和精度。
工件的稳定性则要通过合适的夹持方式和工件支撑来保证,避免在加工过程中的振动和变形。
综上所述,数控机床横向进给的设计是数控机床中的一个关键环节。
数控机床进给系统设计
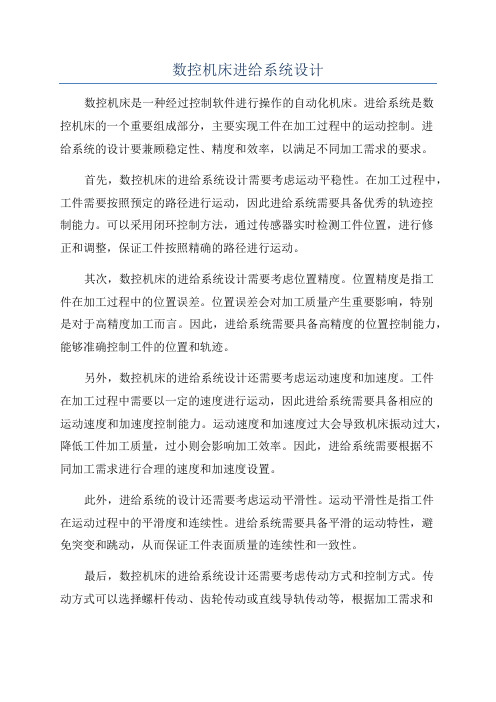
数控机床进给系统设计数控机床是一种经过控制软件进行操作的自动化机床。
进给系统是数控机床的一个重要组成部分,主要实现工件在加工过程中的运动控制。
进给系统的设计要兼顾稳定性、精度和效率,以满足不同加工需求的要求。
首先,数控机床的进给系统设计需要考虑运动平稳性。
在加工过程中,工件需要按照预定的路径进行运动,因此进给系统需要具备优秀的轨迹控制能力。
可以采用闭环控制方法,通过传感器实时检测工件位置,进行修正和调整,保证工件按照精确的路径进行运动。
其次,数控机床的进给系统设计需要考虑位置精度。
位置精度是指工件在加工过程中的位置误差。
位置误差会对加工质量产生重要影响,特别是对于高精度加工而言。
因此,进给系统需要具备高精度的位置控制能力,能够准确控制工件的位置和轨迹。
另外,数控机床的进给系统设计还需要考虑运动速度和加速度。
工件在加工过程中需要以一定的速度进行运动,因此进给系统需要具备相应的运动速度和加速度控制能力。
运动速度和加速度过大会导致机床振动过大,降低工件加工质量,过小则会影响加工效率。
因此,进给系统需要根据不同加工需求进行合理的速度和加速度设置。
此外,进给系统的设计还需要考虑运动平滑性。
运动平滑性是指工件在运动过程中的平滑度和连续性。
进给系统需要具备平滑的运动特性,避免突变和跳动,从而保证工件表面质量的连续性和一致性。
最后,数控机床的进给系统设计还需要考虑传动方式和控制方式。
传动方式可以选择螺杆传动、齿轮传动或直线导轨传动等,根据加工需求和机床类型进行选择。
控制方式可以选择基于位置、速度或力控制等,根据具体应用进行选择。
综上所述,数控机床的进给系统设计需要兼顾运动平稳性、位置精度、运动速度和加速度、运动平滑性、传动方式和控制方式等因素。
通过合理的设计和调试,可以提高数控机床的加工质量和效率,满足不同加工需求的要求。
- 1、下载文档前请自行甄别文档内容的完整性,平台不提供额外的编辑、内容补充、找答案等附加服务。
- 2、"仅部分预览"的文档,不可在线预览部分如存在完整性等问题,可反馈申请退款(可完整预览的文档不适用该条件!)。
- 3、如文档侵犯您的权益,请联系客服反馈,我们会尽快为您处理(人工客服工作时间:9:00-18:30)。
数控机床进给系统设计第一章、数控机床进给系统概述数控机床伺服系统的一般结构如图图1-1所示:图1-1数控机床进给系统伺服由于各种数控机床所完成的加工任务不同,它们对进给伺服系统的要求也不尽相同,但通常可概括为以下几方面:可逆运行;速度范围宽;具有足够的传动刚度和高的速度稳定性;快速响应并无超调;高精度;低速大转矩。
1.1、伺服系统对伺服电机的要求(1)从最低速到最高速电机都能平稳运转,转矩波动要小,尤其在低速如0.1r /min 或更低速时,仍有平稳的速度而无爬行现象。
(2)电机应具有大的较长时间的过载能力,以满足低速大转矩的要求。
一般直流伺服电机要求在数分钟内过载4-6倍而不损坏。
(3)为了满足快速响应的要求,电机应有较小的转动惯量和大的堵转转矩,并具有尽可能小的时间常数和启动电压。
电机应具有耐受4000rad/s2以上的角加速度的能力,才能保证电机可在0.2s以内从静止启动到额定转速。
(4)电机应能随频繁启动、制动和反转。
随着微电子技术、计算机技术和伺服控制技术的发展,数控机床的伺服系统已开始采用高速、高精度的全数字伺服系统。
使伺服控制技术从模拟方式、混合方式走向全数字方式。
由位置、速度和电流构成的三环反馈全部数字化、软件处理数字PID,使用灵活,柔性好。
数字伺服系统采用了许多新的控制技术和改进伺服性能的措施,使控制精度和品质大大提高。
数控车床的进给传动系统一般均采用进给伺服系统。
这也是数控车床区别于普通车床的一个特殊部分。
1.2、伺服系统的分类数控车床的伺服系统一般由驱动控制单元、驱动元件、机械传动部件、执行件和检测反馈环节等组成。
驱动控制单元和驱动元件组成伺服驱动系统。
机械传动部件和执行元件组成机械传动系统。
检测元件与反馈电路组成检测系统。
进给伺服系统按其控制方式不同可分为开环系统和闭环系统。
闭环控制方式通常是具有位置反馈的伺服系统。
根据位置检测装置所在位置的不同,闭环系统又分为半闭环系统和全闭环系统。
半闭环系统具有将位置检测装置装在丝杠端头和装在电机轴端两种类型。
前者把丝杠包括在位置环内,后者则完全置机械传动部件于位置环之外。
全闭环系统的位置检测装置安装在工作台上,机械传动部件整个被包括在位置环之内。
开环系统的定位精度比闭环系统低,但它结构简单、工作可靠、造价低廉。
由于影响定位精度的机械传动装置的磨损、惯性及间隙的存在,故开环系统的精度和快速性较差。
全闭环系统控制精度高、快速性能好,但由于机械传动部件在控制环内,所以系统的动态性能不仅取决于驱动装置的结构和参数,而且还与机械传动部件的刚度、阻尼特性、惯性、间隙和磨损等因素有很大关系,故必须对机电部件的结构参数进行综合考虑才能满足系统的要求。
因此全闭环系统对机床的要求比较高,且造价也较昂贵。
闭环系统中采用的位置检测装置有:脉冲编码器、旋转变压器、感应同步器、磁尺、光栅尺和激光干涉仪等。
数控车床的进给伺服系统中常用的驱动装置是伺服电机。
伺服电机有直流伺服电机和交流伺服电机之分。
交流伺服电机由于具有可靠性高、基本上不需要维护和造价低等特点而被广泛采用。
直流伺服电动机引入了机械换向装置。
其成本高,故障多,维护困难,经常因碳刷产生的火花而影响生产,并对其他设备产生电磁干扰。
同时机械换向器的换向能力,限制了电动机的容量和速度。
电动机的电枢在转子上,使得电动机效率低,散热差。
为了改善换向能力,减小电枢的漏感,转子变得短粗,影响了系统的动态性能。
交流伺服已占据了机床进给伺服的主导地位,并随着新技术的发展而不断完善,具体体现在三个方面。
一是系统功率驱动装置中的电力电子器件不断向高频化方向发展,智能化功率模块得到普及与应用;二是基于微处理器嵌入式平台技术的成熟,将促进先进控制算法的应用;三是网络化制造模式的推广及现场总线技术的成熟,将使基于网络的伺服控制成为可能。
1.3、主要设计任务参数车床控制精度:0.01mm(即为脉冲当量);最大进给速度:V max=5m/min。
最大加工直径为D=400mm,工作台及刀架重:110㎏;最大轴,向力=160㎏;导轨静摩擦系数=0.2;max行程=1280mm;步进电机:110BF003;步距角:0.75°;电机转动惯量:J=1.8×10-2㎏.m2。
第二章、数控车床纵向进给系统传动的方案设计数控机床进给驱动对位置精度、快速响应特性、调速范围等有较高的要求。
实现进给驱动的电机主要有三种:步进电机、直流伺服电机和交流伺服电机。
目前,步进电机只适应用于经济型数控机床,直流伺服电机在我国正广泛使用,交流伺服电机作为比较理想的驱动元件已成为发展趋势。
数控机床的进给系统当采用不同的驱动元件时,其进给机构可能会有所不同。
电机与丝杠间的联接主要有三种形式,如图2-1所示。
2.1、带有齿轮传动的进给运动数控机床在机械进给装置中一般采用齿轮传动副来达到一定的降速比要求,如图2-1a)所示。
由于齿轮在制造中不可能达到理想齿面要求,总存在着一定的齿侧间隙才能正常工作,但齿侧间隙会造成进给系统的反向失动量,对闭环系统来说,齿侧间隙会影响系统的稳定性。
因此,齿轮传动副常采用消除措施来尽量减小齿轮侧隙。
但这种联接形式的机械结构比较复杂。
(c)(a)(b)图2—1 电机与丝杠间的联接形式2.2、经同步带轮传动的进给运动如图2-1b)所示,这种联接形式的机械结构比较简单。
同步带传动综合了带传动和链传动的优点,可以避免齿轮传动时引起的振动和噪声,但只能适于低扭矩特性要求的场所。
安装时中心距要求严格,且同步带与带轮的制造工艺复杂。
2.3、电机通过联轴器直接与丝杠联接如图2-1c)所示,此结构通常是电机轴与丝杠之间采用锥环无键联接或高精度十字联轴器联接,从而使进给传动系统具有较高的传动精度和传动刚度,并大大简化了机械结构。
在加工中心和精度较高的数控机床的进给运动中,普遍采用这种联接形式。
根据进给系统的要求及设计要求,选择带有齿轮传动的进给运动,选用最佳降速比,可以提高机床的分辨率,并使系统折算到驱动轴上的惯量减少;尽量消除传动间隙,减少反向死区误差,提高位移精度等。
第三章、运动设计3.1、降速比计算功率步进电动机型号为110BF003,其主要技术参数为最大静转矩为7.84N m •,步距角0.75°,电机转动惯量:J =1.8×10-2 ㎏.m 2;快速空载启动时电动机转速500/min r 。
进给传动链的脉冲当量0.01/mm P δ=.选滚珠丝杠的螺距为12mm.由0.7512 2.53603600.01S i θδ⨯===⨯ (3—1) 式中 θ ——步进电动机的步距角δ ——脉冲当量,mm S ——丝杠螺距, mm 3.2、减速齿轮的确定选择一级减速器,选齿轮120Z =,250Z =,模数2m mm =,齿宽20b mm =。
选择斜齿轮调隙,齿轮的参数如表3—1。
3—1齿轮参数表第四章、丝杠螺母机构的选择与计算已知条件:工作台及刀架重:110㎏,所以重量为9.81101078G N =⨯=最大行程:1280mm ,失动量:0.01mm δ=,工作台最高速度:max 5/min v m = 查表选择丝杆预期寿命: 15000h L =小时 , 摩擦系数0.2μ=。
则导轨的静摩擦力F O 。
0.21078215.6O F G N μ==⨯= (4—1)最大轴向负载0max 1609.81568F N =⨯=4.1、动载强度计算当转速10/min n r >时,滚珠丝杠;螺母的主要破坏形式是工作表面的疲劳点蚀,因此要进行动载强度计算,其计算动载荷()Cc N 应小于或等于滚珠丝杆螺母副的额定动负荷,即c d H eq r C f F F =≤ (4—2)式中 d f ——动载荷系数,见表3 —1; H f ——硬度影响系数,见表3-2; eq F ——当量动负荷,N;r F ——滚珠丝杠;螺母副的额定动负荷,N ; 'T ——寿命,以610r 为一个单位。
660'10neqTT =(4—3) 式中 T ——使用寿命,h ;按设计机床要求取T=15000h N ——循环次数:eq n ——滚珠丝杠的当量转速,r/min 。
1000max 10005416.67/min 12eq V n r S ⨯=== (4—4)代入上式得666060416.6715000'3751010neqT T ⨯⨯=== (4—5)表4-1 动载荷系数d f1.22.51.5表4-2 硬度影响系数H f 、'H f52.5 40 1.35 3.85 1.40当工作载荷单调连续或周期行单调连续变化时,则00max21117.23eq F F F N +≈= (4—6) 式中 0F 0max F ——最大和最小工作载荷,N 。
查表4—1 4—2取d f =1.5 H f =1.56代入上式得1.5 1.561117.218851.9918.85c d H eq N KNC f F ⨯⨯==== (4—7)4.2、静强度计算当转速10/min n r ≤时,滚珠丝杠螺母的主要破坏形式为滚珠接触面上产生较大的塑性变形,影响正常工作。
因此,应进行静强度计算,最大计算静载荷0()c F N 为0max 'c d H orF f f F F =≤ (1—10)式中'H f ——硬度硬度影响系数,见表5—2;取'H f =1.67.0r F ——滚珠丝杠螺母副的额定静负荷,N 。
代入得0max ' 1.5 1.5615683669c d H F f f F N ==⨯⨯= (4—8)根据计算额定动负载荷和额定静负荷初选滚珠丝杠副型号为50125CBM -。
其基本参数为公称直径050d mm =,导程12S mm =,滚珠直径7.144Dw mm =。
额定动负荷39348Ca N =,额定静负荷0108290r F N =。
动载荷与静载荷载均满足要求。
4.3、临界转速校核对于高速长丝杠有可能发生共振,需要算其临界转速,不会发生共振的最高转速为临界 转速(/min).c n r22229910c cf d n L = (4—9)20 1.2wd d D =- (4—10)式中 ——临界转速计算长度,m ;——丝杠支撑方式系数。
两端固定时, 代入数据得20 1.250 1.27.14441.427w d d D mm=-=-⨯=2222224.730.041991099105548.3/min1.28c c f d n r L ⨯===远远小于其最大速度,故临界转速满足。
4.4、额定寿命的校核滚珠丝杠的额定动载荷39348aC N =,已知其轴向载荷max 1568a a F F N ==,滚珠丝杠的转速max 416.67/min n n r ==,运转条件系数 1.2w f =,则有3636639348()10()109145101568 1.2a a w C L r r F f =⨯=⨯=⨯⨯ (4—11) 69145103657996060416.67h L L h h n ⨯===⨯ (4—12) 滚珠丝杠螺母副的总工作寿命36579915000h L h h =≥,故满足要求。