数值模拟技术在大型锻件生产中的应用概述
数值模拟技术在锻造成形中的应用

数值模拟技术在锻造成形中的应用董海涛1 张治民1 宋志海2(1.中北大学材料科学与工程学院,山西030051;2.广东中山中粤马口铁工业有限公司,广东528437)摘要:锻造成形过程是一个非常复杂的弹塑性大变形过程,有限元法是用于锻造成形过程模拟中一种有效的数值计算方法。
本文介绍了数值模拟技术在金属锻造成形中应用的基本理论、模拟中的关键技术,阐述了锻造成形数值模拟技术的现状及发展趋势。
关键词:数值模拟;有限元法;锻造成形中图分类号:O242,T G316 文献标识码:AThe Application of the Numerical Simulatio n Techniquein the Fo rging FormationDong H a itao,Zhang Zhimin,Song Zhiha iAbstract:The for ging for ming proce ss i s a ve ry co mplica ted proce ss of t he evident ela stoplasticity defo rma2 tion,a nd t he finite ele me nt me thod is a n effective numerical calcula ting method used in the process of t he forging for ming simulation.This ar ticle has de scribed the basic theo ry of the nume rical simulation tec hnique applie d in t he metal for ging fo rmation and the ke y tec hnique during the simulation,meanwhile t he c ur rent sit uation and the development te nde ncy of the numerical simulation technique have bee n presented as well.K ey wo r ds:numerical simulation;f inite ele ment method;forging formation1 引言锻造工业一直是汽车、矿山、能源、建筑、航空、航天、兵器等工业的重要基础。
数值模拟技术在《铸造工艺与设备》课程教学中的应用
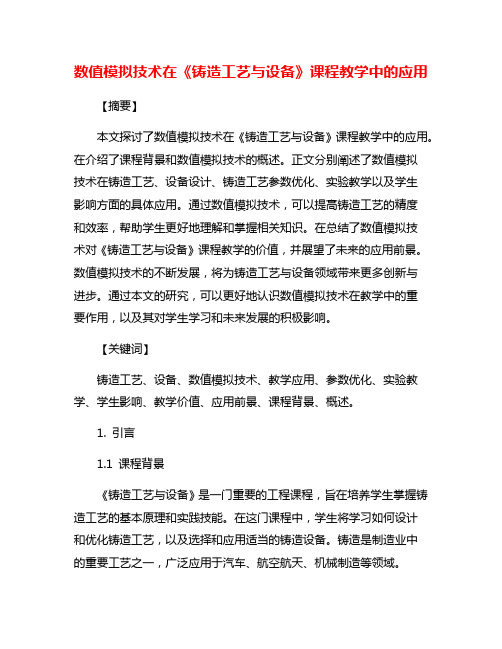
数值模拟技术在《铸造工艺与设备》课程教学中的应用【摘要】本文探讨了数值模拟技术在《铸造工艺与设备》课程教学中的应用。
在介绍了课程背景和数值模拟技术的概述。
正文分别阐述了数值模拟技术在铸造工艺、设备设计、铸造工艺参数优化、实验教学以及学生影响方面的具体应用。
通过数值模拟技术,可以提高铸造工艺的精度和效率,帮助学生更好地理解和掌握相关知识。
在总结了数值模拟技术对《铸造工艺与设备》课程教学的价值,并展望了未来的应用前景。
数值模拟技术的不断发展,将为铸造工艺与设备领域带来更多创新与进步。
通过本文的研究,可以更好地认识数值模拟技术在教学中的重要作用,以及其对学生学习和未来发展的积极影响。
【关键词】铸造工艺、设备、数值模拟技术、教学应用、参数优化、实验教学、学生影响、教学价值、应用前景、课程背景、概述。
1. 引言1.1 课程背景《铸造工艺与设备》是一门重要的工程课程,旨在培养学生掌握铸造工艺的基本原理和实践技能。
在这门课程中,学生将学习如何设计和优化铸造工艺,以及选择和应用适当的铸造设备。
铸造是制造业中的重要工艺之一,广泛应用于汽车、航空航天、机械制造等领域。
随着科学技术的不断发展,数值模拟技术在《铸造工艺与设备》课程中的应用也日益重要。
数值模拟技术是一种通过计算机模拟实际过程的方法,可以帮助工程师们更好地理解和优化铸造工艺。
通过数值模拟技术,学生可以在虚拟环境中进行实验和优化,提高工艺设计的准确性和效率。
本文将重点探讨数值模拟技术在《铸造工艺与设备》课程教学中的应用,希望通过深入研究和讨论,为学生提供更好的学习体验和提升其工程实践能力。
1.2 数值模拟技术概述数值模拟技术是一种通过计算机进行模拟和分析工程问题的技术手段。
它利用数学模型和计算机算法对复杂的工程问题进行模拟和仿真,从而更好地理解和优化工艺过程。
在铸造工艺与设备课程中,数值模拟技术被广泛应用于模拟铸造过程中的流体力学、热传导、凝固等物理现象,为工艺参数优化和设备设计提供重要参考。
大型锻件淬火组织场数值模拟

大型锻件淬火组织场数值模拟
大型锻件淬火组织场数值模拟是一种利用计算机技术来模拟大型锻件淬火组织变化的新技术。
它充分考虑了材料性能、淬火温度、淬火时间及外部环境因素对大型锻件淬火组织变化的影响,可以有效地对模拟的结果进行准确的预测,为企业提供实用的工艺指导意见。
大型锻件淬火组织场数值模拟的基本原理是通过计算机将淬火过程中的物理量、温度场等参数的变化情况进行模拟,并进行必要的参数校正,从而达到准确地反映淬火过程中各个位置上组织变化的目的。
该数值模拟方法可以计算出淬火过程中淬火温度场、应力场、硬度场、韧性场等参数的变化情况,从而非常精确地模拟淬火组织变化的过程。
大型锻件淬火组织场数值模拟的优势在于可以有效地模拟淬火组织变化的过程,使得企业更好地掌握工艺参数,从而可以有效地控制锻件的组织结构,从而提高产品性能。
此外,大型锻件淬火组织场数值模拟还可以节省成本,更有效地控制生产过程,避免不必要的试制,减少材料浪费。
大型锻件淬火组织场数值模拟的实施过程中,应根据淬火组织变化特点确定合适的模型,并结合工程实际情
况,对模型进行修正,以便更好地模拟淬火组织变化的过程。
在此基础上,可以根据实际需要选择合适的计算方法,设计合适的计算网格,以及选择相应的参数,并进行必要的数据处理,以便获得更准确的结果。
此外,大型锻件淬火组织场数值模拟也可以根据实际情况进行参数校正,以更好地模拟淬火组织变化的过程。
在校正参数的过程中,可以利用实验测试的结果作为参考,以便获得更准确的结果。
总之,大型锻件淬火组织场数值模拟是一种先进的技术,它可以有效模拟淬火组织变化的过程,帮助企业更好地掌握工艺参数,提高产品性能,节省成本,更有效地控制生产过程,从而取得良好的经济效益。
数值模拟技术在锻造中的应用
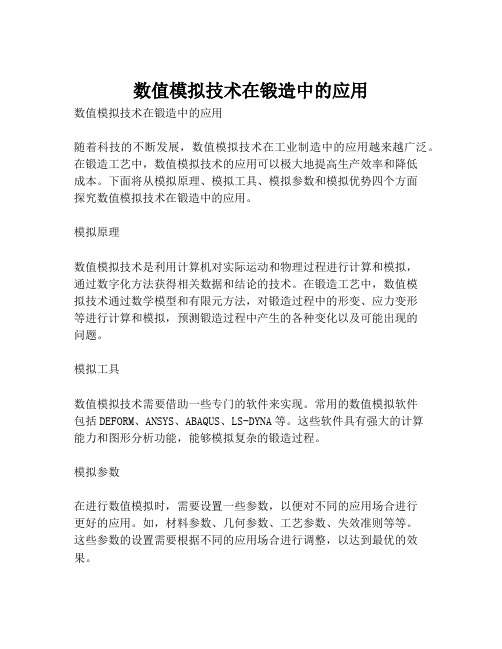
数值模拟技术在锻造中的应用数值模拟技术在锻造中的应用随着科技的不断发展,数值模拟技术在工业制造中的应用越来越广泛。
在锻造工艺中,数值模拟技术的应用可以极大地提高生产效率和降低成本。
下面将从模拟原理、模拟工具、模拟参数和模拟优势四个方面探究数值模拟技术在锻造中的应用。
模拟原理数值模拟技术是利用计算机对实际运动和物理过程进行计算和模拟,通过数字化方法获得相关数据和结论的技术。
在锻造工艺中,数值模拟技术通过数学模型和有限元方法,对锻造过程中的形变、应力变形等进行计算和模拟,预测锻造过程中产生的各种变化以及可能出现的问题。
模拟工具数值模拟技术需要借助一些专门的软件来实现。
常用的数值模拟软件包括DEFORM、ANSYS、ABAQUS、LS-DYNA等。
这些软件具有强大的计算能力和图形分析功能,能够模拟复杂的锻造过程。
模拟参数在进行数值模拟时,需要设置一些参数,以便对不同的应用场合进行更好的应用。
如,材料参数、几何参数、工艺参数、失效准则等等。
这些参数的设置需要根据不同的应用场合进行调整,以达到最优的效果。
模拟优势数值模拟技术在锻造中的应用具有很多优势。
首先,它能够模拟真实情况,预测锻造过程中可能出现的问题,有助于优化锻造工艺;其次,数值模拟技术可以节约时间和成本,为锻造过程提供了精准的指导;另外,数值模拟技术还可有效降低设备损坏的风险,提高锻造生产的安全性。
总的来说,数值模拟技术在锻造中的应用,能够提高生产效率和锻造品质,同时也为锻造工业带来了更广阔的发展空间。
在未来的发展中,数值模拟技术必将在锻造领域发挥越来越重要的作用。
大型轴类锻件锻造工艺过程数值模拟

大型轴类锻件锻造工艺过程数值模拟大型轴类锻件的锻造工艺过程一般包括预留料、加热、锻造、冷却等阶段。
在进行数值模拟之前,需要先确定锻件的材料性能参数,包括应力-应变曲线、热膨胀系数、变形参数等。
这些参数对于模拟结果的准确性和可靠性非常重要。
首先,在进行数值模拟之前,需要进行几何建模。
根据锻件的实际几何形状,使用计算机辅助设计软件对锻件进行三维建模。
同时,还需要考虑到毛坯的材料损失,合理设计锻造余量以提供合适的余量补偿。
接下来,进行网格划分。
将几何模型导入数值模拟软件,进行网格划分。
网格划分的密度和精细度对于模拟结果的准确性和计算时间都有影响。
因此,需要根据实际情况,合理选择网格划分方案。
然后,确定边界条件。
根据锻造工艺过程中的实际条件,设置边界条件。
这包括锻造温度、锻造速度、初始应变速率等。
通过准确设置边界条件,可以模拟实际的锻造过程,并预测锻件的应力、应变和温度分布。
进行数值模拟计算。
将几何模型、网格和边界条件输入数值模拟软件,进行计算。
通过数值模拟软件提供的求解器,可以得到锻件在锻造过程中的应力、应变和温度分布,以及变形和残余应力情况。
对模拟结果进行分析和评估。
根据模拟结果,可以对锻造工艺过程进行分析和评估。
比较模拟结果与实际测量值的差异,评估数值模拟的准确性和可靠性。
如果模拟结果与实际值相符合,说明数值模拟是准确的,可以用于指导实际的锻造工艺过程。
最后,根据模拟结果,对锻造工艺过程进行优化。
通过数值模拟分析,可以确定合适的锻造参数和工艺措施,以提高锻件的质量和性能。
比如,可以优化锻造温度、加热速度、锻造速度等参数,使得锻件在锻造过程中的应力和应变分布更加均匀,减少变形和残余应力。
总之,大型轴类锻件锻造工艺过程的数值模拟可以帮助优化锻造工艺,提高锻件的质量和性能。
通过建立合理的几何模型、网格划分和边界条件,进行数值计算和分析,可以对锻造工艺过程进行预测、分析和评估,为实际生产提供指导和参考。
【精品】有限元数值模拟在锻造中的应用

有限元数值模拟在锻造中的应用有限元数值模拟技术在金属塑性成形工艺中的应用田菁菁(河南科技大学材料科学与工程学院,河南洛阳471003)摘要:金属塑性成形过程是一个非常复杂的弹塑性大变形过程,有限元法是用于金属成形过程模拟中一种有效的数值计算方法。
本文详细介绍了弹塑性、刚塑性、粘塑性3种有限元法,系统地讨论了有限元模拟中的关键技术,即几何模型的建立、单元类型的选择、网格的划分与重划分、接触和摩擦问题等技术,并结合实例说明了三维有限元模拟在金属塑性成形领域中的具体应用。
最后,基于现存问题提出了自己的见解。
关键词:计算机应用;有限元法;综述;塑性加工1引言金属塑性成形过程是一个复杂的弹塑性大变形过程,影响因素众多,如模具形状、毛坯形状、材料性能、温度及工艺参数等,该过程涉及到几何非线性、材料非线性、边界条件非线性等一系列难题。
金属塑性成形工艺传统的研究方法主要采用“经验法”,这种基于经验的设计方法往往经历反复修正的过程,从而造成了大量的人力、物力及时间浪费。
21世纪的塑性加工产品向着轻量化、高强度、高精度、低消耗的方向发展。
塑性精密成形技术对于提高产品精度、缩短产品交货期、减少或免除切削加工、降低成本、节省原材料、降低能耗,当前的生产的发展,除了要求锻件具有较高的精度外,更迫切地是要解决复杂形状地成形问题,同时还要不断提高锻件地质量、减少原料的消耗、提高模具寿命,促使降低锻件成本、提高产品的竞争能力。
2有限元模拟在塑性成形领域的应用用于金属塑性成形过程数值模拟的有限元法根据本构方程的不同可以分为弹塑性有限元法、刚塑性有限元法和粘塑性有限元法,其中,刚塑性有限元法和弹塑性有限元法的应用比粘塑性有限元法更广泛。
2.1刚塑性有限元法刚塑性有限元法是1973年由小林史郎和C.H.李提出的。
由于金属塑性成形过程中大多数塑性变形量很大,相对来说弹性变形量很小,可以忽略,因此简化了有限元列式和计算过程。
刚塑性有限元法的理论基础是MarkOV变分原理,其表述是在所有满足运动学允许的速度场中,真实解使得以下泛函取极值:式中:为等效应力;为等效应变速率;为力面上给定的面力;为速度已知面上给定的速度;V为变形体的体积;S为表面积。
热处理数值模拟在锻造工艺优化中的应用探究
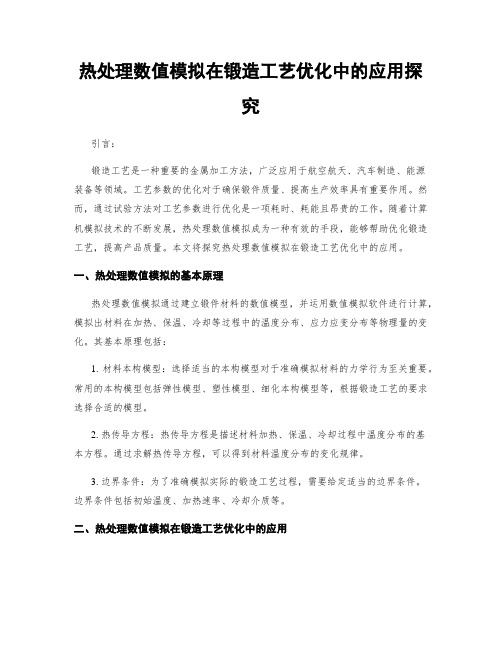
热处理数值模拟在锻造工艺优化中的应用探究引言:锻造工艺是一种重要的金属加工方法,广泛应用于航空航天、汽车制造、能源装备等领域。
工艺参数的优化对于确保锻件质量、提高生产效率具有重要作用。
然而,通过试验方法对工艺参数进行优化是一项耗时、耗能且昂贵的工作。
随着计算机模拟技术的不断发展,热处理数值模拟成为一种有效的手段,能够帮助优化锻造工艺,提高产品质量。
本文将探究热处理数值模拟在锻造工艺优化中的应用。
一、热处理数值模拟的基本原理热处理数值模拟通过建立锻件材料的数值模型,并运用数值模拟软件进行计算,模拟出材料在加热、保温、冷却等过程中的温度分布、应力应变分布等物理量的变化。
其基本原理包括:1. 材料本构模型:选择适当的本构模型对于准确模拟材料的力学行为至关重要。
常用的本构模型包括弹性模型、塑性模型、细化本构模型等,根据锻造工艺的要求选择合适的模型。
2. 热传导方程:热传导方程是描述材料加热、保温、冷却过程中温度分布的基本方程。
通过求解热传导方程,可以得到材料温度分布的变化规律。
3. 边界条件:为了准确模拟实际的锻造工艺过程,需要给定适当的边界条件。
边界条件包括初始温度、加热速率、冷却介质等。
二、热处理数值模拟在锻造工艺优化中的应用1. 确定最佳加热工艺:热处理数值模拟可以帮助确定最佳的加热工艺参数,以达到预期的材料性能。
通过模拟不同加热温度、加热时间等参数的变化对材料的显微组织和力学性能进行分析,选择最佳的加热工艺参数。
2. 预测变形和裂纹:锻造过程中会产生一定程度的变形和应力集中,甚至会引发裂纹。
热处理数值模拟可以预测锻造过程中的变形和应力分布,帮助预防裂纹的产生,通过优化工艺参数减少变形和应力集中,提高锻件的质量。
3. 优化冷却介质:冷却介质可以对锻件的性能产生重要影响。
热处理数值模拟可以模拟不同冷却介质的冷却速度和温度分布,并对材料的变化进行分析。
通过优化冷却介质,可以改善材料的相变行为和显微组织,提高锻件的综合性能。
大型锻件热处理过程的数值模拟研究
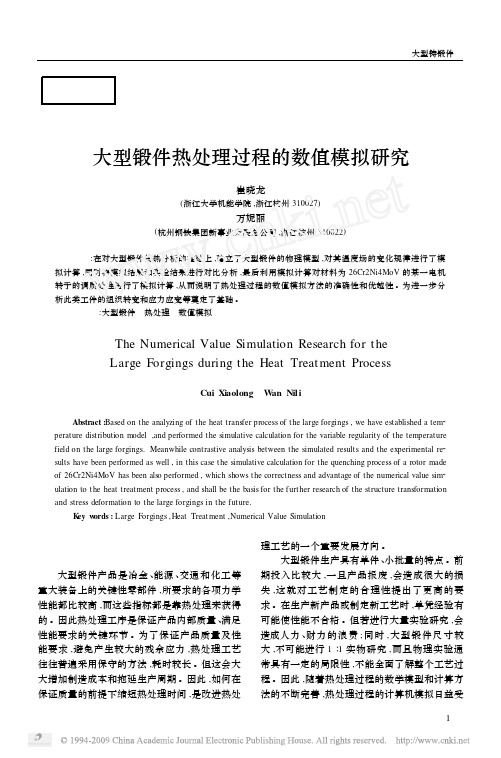
时间 (
8
10
12
14
16
18
20
无风
模拟值 实验值 绝对差值
724. 7 723. 3
1. 4
679. 1 682. 3
3. 2
646. 3 649. 8
3. 5
619. 5 617. 2
2. 3
595. 5 594. 0
1. 5
572. 7 574. 2
2
图 2 工件断面的几何形状
大型铸锻件
2. 2 建立差分方程
为了具体说明数值模拟在热处理过程中的
优越性 ,我们以图 2 所示的 L 形工件为例 ,用数
值模拟方法求解热处理时工件内温度场的变化
情况 ,然后和实验数据进行对比 。从而说明数值
模拟方法的准确性和优越性 。
用有限差分法求解 ,对内节点采用中心差
1. 5
550. 6 553. 4
2. 8
528. 7 525. 8
2. 9
507. 2 508. 8
1. 6
486. 1 487. 4
1. 3
A 向风
模拟值 实验值 绝对差值
648. 2 644. 8
3. 4
566. 1 567. 2
1. 1
512. 2 514. 5
2. 3
471. 7 473. 8
表 2 N 点温度变化过程( ℃)
6
8
10
12
765. 4 765. 8
0. 4
736. 0 733. 0
热微分方程[5 ] :
ρc
5T 5τ
=
λ(
52 T 5 x2
(工艺技术)大型轴类锻件锻造工艺过程数值模拟

1.2.1.1 不同型砧下大型轴类锻件倒棱滚圆过程的数值模拟研究 大型轴类锻件主要包括大型轧辊、传动轴、汽轮机转子等,一般用于机器设备的关
With a flat anvil rounded, the cross-sectional average diameter of forging increases by 2.8% compared to the original. (1) ( 2) The heading and stretching process of wind power axis are simulated. During the simulation, the impact of received-anvildistance on surface defects the final forging are discussed. Setting the received-anvil-distance of 60mm , which not only improve work efficiency, but also to ensure the surface of the final forging. (2) (3) The die forging process of wind power axis is simulated. During the simulation, the strain-stress distribution, temperature of the final forging and the size precision are discussed. The average diameter of the top of the final forging 1546mm, bottom diameter 405mm, are in line with process card requirements. (3)
成型数值模拟技术在大型自由锻件生产领域的分析与应用

成型数值模拟技术在大型自由锻件生产领域的分析与应用发布时间:2023-02-16T05:41:39.522Z 来源:《中国科技信息》第2022年第9月第17期作者:孙赫[导读] 目前,随着锻造工艺技术的不断提升,锻造工艺在生产领域的应用愈发广泛,包括:冶金、采矿、拖拉机、铁路货车、农业机械、石油化工、航空航天等行业部门而在平时的生活中,锻造产品也是不可或缺的组成部分。
孙赫中车齐齐哈尔车辆有限公司黑龙江齐齐哈尔 161002摘要:目前,随着锻造工艺技术的不断提升,锻造工艺在生产领域的应用愈发广泛,包括:冶金、采矿、拖拉机、铁路货车、农业机械、石油化工、航空航天等行业部门而在平时的生活中,锻造产品也是不可或缺的组成部分。
毫不夸张的说,一个国家的锻件产量如何,模锻件在锻件生产中比例的大小,以及锻造设备的先进程度和数量,这些都能反映出这个国家的真实工业水平。
本文以成型数值模拟技术在大型自由锻件生产领域的分析与应用为题,通过了解锻造工艺的分类与应用,分析大型自由锻件在生产领域的应用以及成型数值模拟的相关技术,根据零件图进行工艺设计及模具的设计和计算,然后再利用软件完成模具模型的建立。
关键词:铸锻工艺技术;大型自由锻件;成型数值模拟;生产领域引言:大型自由锻件是重大装备制造业的核心部件,被广泛应用于电力、冶金、铁路货车运输、石油化工、核能、国防军工等领域。
与此同时,随着国内外市场竞争的日趋激烈和新材料以及新产品的不断涌现,大型自由锻件企业必须对生产成本、生产及研发周期、材料利用率、产品性能等提出更高的要求,而基于传统经验模式的大型自由锻件设计、制造流程难以适应快速变化的产品及市场。
为了适应日益激烈的市场环境,提高企业竞争力,科技创新成为大型自由锻件企业提高自身科研实力、提高企业效益的重要手段。
一、锻造工艺(一)锻造的概念锻造是一种使金属塑性变形的加工技术,通过相应机械对工件施加外力使其发生塑性变形,使坯料变成指定形状和尺寸的锻件。
大型锻件淬火组织场数值模拟

大 型锻件 的热 处理 过程 比较 复 杂 。加 热 和冷
的温 度 一 间 曲线 和相 变 类 型 选定 组 织 转 变 数学 时 模 型进 行计 算 … 。淬 火 过 程 的 组 织 转 变 主 要 涉
及 扩散 型相 变 ( 光体 + 素体 、 氏体转 变 ) 珠 铁 贝 和 非 扩散 型相 变 ( 氏体转 变 ) 马 。
对于 马 氏体 这 种 非扩 散 型转 变 , 变 量 仅决 转 定于 温度 , 而与 时 间无 关 , 可采用 K 方 程计 算 转 M 变量 , 表达 式为 :
选取 4个 特 殊冷速 制 备试样 进行 金相 观察 。并 结 合 工程 应 用 , 算 ( 15i 型 锻 件 的 淬火 温 度 计 2 . j n大 分 布及 沿截 面 的组 织 分布 。
力 很强 。但 A S S没有 相变 和组 织场 演 化模 块 , NY 使 其在 处理 材料 热处 理 问题 上 有一定 的局 限性 。 本 文运 用 A D P L语 言 对 A S S进 行 二 次 开 NY 发, 计算 一种 贝氏体 钢在 不 同冷 速 下 的组 织 , 同时
对 于扩散 型 相 变 , 常 采 用 J A 通 M K方 程 来 描
m ×1 的试 样 , 淬火 相变仪 上按 固定冷 速 m 0mm 在 1 / i 、o / i 、0C mi、0 c / i 却 , m n 5C m n 2 o/ n 3 0c m n冷 o C 观 察 不 同冷速 下 得 到 的金 相 组 织 J 。金 相 图 片 见 图3 。可 以看 出 4个典 型 冷速 的模 拟计 算 结果 与 实验 观测结 果吻合 的 比较好 。 3 工程计 算实例 本 文在 上述 计算 的基 础 上 , 一 步模 拟计 算 进 直径 为 15 m, 度 为 2m 的大 型锻 件 , 8 0 . 长 在 9 %
数值模拟在锻造成形中的应用

数值模拟在锻造成形中的应用作者:孙乐民张巧芳张永振1引言锻造成形是现代制造业中的重要加工方法之一。
锻造成形的制件有着其他加工方法难以达到的良好的力学性能。
随着科技发展,锻造成形工艺面临着巨大的挑战 各行业对锻件质量和精度的要求越来越高,生产成本要求越来越低。
这就要求设计人员在尽可能短的时间内设计出可行的工艺方案和模具结构。
但目前锻造工艺和模具设计,大多仍然采用实验和类比的传统方法,不仅费时而且锻件的质量和精度很难提高。
随着有限元理论的成熟和计算机技术的飞速发展,运用有限元法数值模拟进行锻压成形分析,在尽可能少或无需物理实验的情况下,得到成形中的金属流动规律、应力场、应变场等信息,并据此设计工艺和模具,已成为一种行之有效的手段。
锻造成形大多属于三维非稳态塑性成形,一般不能简化为平面或轴对称等简单问题来近似处理。
在成形过程中,既存在材料非线性,又有几何非线性,同时还存在边界条件非线性,变形机制十分复杂,并且接触边界和摩擦边界也难以描述。
应用刚(粘)塑性有限元法进行三维单元数值模拟 是目前国际公认的解决此类问题的最好方法之一。
2 刚(粘)塑性有限元法刚(粘)塑性有限元法忽略了金属变形中的弹性效应,依据材料发生塑性变形时应满足的塑性力学基本方程,以速度场为基本量,形成有限元列式。
这种方法虽然无法考虑弹性变形问题和残余应力问题,但可使计算程序大大简化。
在弹性变形较小甚至可以忽略时,采用这种方法可达到较高的计算效率。
刚塑性有限元法的理论基础是Markov变分原理。
根据对体积不变条件处理方法上的不同(如Lagrange乘子法、罚函数法和体积可压缩法),又可得出不同的有限元列式 其中罚函数法应用比较广泛。
根据Markov变分原理,采用罚函数法处理,并用八节点六面体单元离散化,则在满足边界条件、协调方程和体积不变条件的许可速度场中 对应于真实速度场的总泛函为:∏≈∑π(m)=∏(1,2,…,m)(1)对上式中的泛函求变分,得:∑=0(2)采用摄动法将式(2)进行线性化:=+Δun(3)将式(3)代入式(2),并考虑外力、摩擦力在局部坐标系中对总体刚度矩阵和载荷列阵的贡献,通过迭代的方法,可以求解变形材料的速度场。
数值模拟技术在我国钢铁工业中的应用

数值模拟技术在我国钢铁工业中的应用【摘要】综述了近年来数值模拟技术在我国钢铁工业中的应用现状,着重分析了商业有限元分析软件的特点及其在解决钢铁冶金和加工领域中的问题时所具有的优势,并结合通钢RH数模从前处理、建立模拟文件、求解以及结果分析等方面介绍在优化精炼工艺方面应用情况。
【关键词】数值模拟;钢铁冶金过程;RH数模;应用1、前言冶金过程非常复杂而且多数是在高温状态下完成,因此很难对冶金过程进行直接的观察与测量。
虽然以相似原理为基础的冷态模拟实验使用较多,但有时会受到实验场地及实验经费的限制,而且多数缩小比例的冷态实验进行的只是定性分析,而在冶金过程动力学中所研究的化学反应速度、反应器内流体的流动与传质等现象,原则上都能用数学方法正确描述,这就使得用数学方法模拟冶金过程提供了可能,再加上计算机技术的飞速发展,对求解数学方程提供了有力手段,因此数值模拟在冶金工程领域得到了广泛的应用。
这种分析方法使钢铁工业从过去以经验和知识为依据,以“试错”为基本方法的工艺阶段向以模型化、最优化和柔性化为特点的工程科学阶段过渡。
该方法不仅可以在其他方法模拟费用较高或模拟难度较大时单独使用,还可以和其他模拟方法联合使用、彼此验证,以便于更精准的分析解决冶金工程中的物理问题。
生产前用计算机对生产过程、工艺参数及生产结果进行模拟和对整个系统进行优化,可以实现生产的超前规划和设计。
这样也就为钢铁工业的技术进步提供了新的可能。
2、数值模拟技术在我国钢铁冶金中的应用现状冶炼工序是钢铁生产的基础,它直接关系到钢铁产品的质量。
许多学者利用物理模型对冶金过程中诸如连铸中间包内钢水流动、高炉冷却壁的破损、连铸结晶器瞬态摩擦阻力、连铸结晶器内的流场、弯月面区域的传热等进行研究,在研究中往往要根据工厂的实际限制条件与研究的问题,设计、制作出不同比例的模型,另外还要采用一些控制手段来模拟工厂条件以及相应的测量手段来取得实验结果,其费用是可想而知的。
计算机数值模拟技术在大型锻件淬火过程中的应用

!"#"$%&’ ( )**+,&$-,./
研究与应用
计算机数值模拟技术在大型锻件 淬火过程中的应用
大连理工大学材料科学与工程学院 (辽宁 !!"#$%) 张立文 吕 成
大型锻件淬火过程中,温度场和组织场分布及其变 化极不均匀,因此产生较大的瞬时应力和残余应力,进 而使工件产生较大的变形甚至开裂,造成巨大的经济损 失。开展大锻件淬火过程中温度场、组织场及应力场的 研究,弄清它们与淬火工艺的关系,从而合理地制定淬 火工艺,对提高大锻件热处理后的性能及减少废品有很 大帮助。淬火过程计算机数值模拟技术利用数值分析技 术、可视化技术,基于传热学、力学及金属相变等理论 进行淬火温度场、组织场和应力场的模拟仿真,并根据 模拟结果预测和揭示锻件淬火过程中缺陷形成的机制和 规律,从而为改进和优化工艺提供决策依据,达到优化 工艺、保证产品质量、缩短生产周期和降低生产成本的 目的。 淬火过程的计算机模拟近年来已成为国内外的研究 热点,为各国热处理界所重视,与之相关的基础理论研 究发展极为迅速,随着研究工作的逐步深入,淬火过程 计算机数值模拟技术必将对生产产生不可估量的作用。 计算机作为将知识转化为生产力的强大工具,有可能使 热处理摆脱主要凭经验进行生产的落后状况,向着在正 确预测工艺结果的基础上实现精确控制的方向飞跃,这 给传统的热处理行业提供了一种全新的工具和解决问题 的途径。淬火过程计算机数值模拟技术是学科发展的前 沿领域,是改造传统热处理产业的必由之路。
’
9
9
+ + 式("")中温度应变" { { &" }和组织应变" &<1} 为: 9 9 " (", ("#) { ", ", ’, ’, ’) &.} * { $} $}* $ "" { " + + " (", ("() { ", ", ’, ’, ’) &<1} & { ", { " (} (} &( 其中, $ 为材料的热膨胀系数,( 为组织转变时比体积
数值模拟软件在锻造工艺中的应用

利 用拖 放 技术 将材 料 特性 、 机类 型 、 擦 、 传导 以 压 摩 热 及模 型 问导热 等需要 考虑 的各种 因素分 配给模 具和工
件 。完 成锻造模 拟后 ,结 果 自动 转入 可视化 和动画 处
相反. 数值 仿真技 术 由于其强 大的运算 能 力 、 能够 模拟
材 料流动 等异常 复杂 的锻造过 程 ,而越来 越 凸显其优
C /L-u n U i a j
【 btatT kn h aeo rcs fr peigtecnclpa ,h ae nrdcsteMS . A s c]aigtecs f oes o stn oi le tepprit ue h C r p u t h a t o
S e F r e ot r o n me ia smu a in a a y e t e e u t c mb ni t t e hy i s e t n up r o g s fwa e f r u rc l i l t , n lz s h r s ls o i ng wih h p sc t s,a d o p o i e a i o i n iy t e r u h a tsz n h pi g p r mee s r vd s a b ss t de tf h o g c s ie a d s a n a a tr .Th e u t f n m e ia i l t n e r s ls o u rc lsmu a i o a e a s r v d b r c ie t n u e te a c r c ft u ei a i u ai n r lo p o e y p a t o e s r h c u a yo c he n m rc lsm lto .
镦粗 工 艺 , 行数 值 模拟 , 结合 物理 实验 结 果加 以分析 , 进 并 为锻 造 生产现 场 中确 定毛 坯尺 寸 、 定成 形 制
数值模拟技术在大型锻件生产中的应用概述
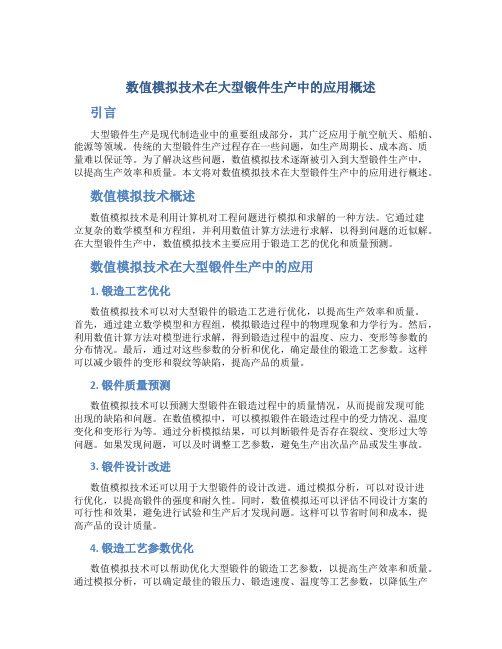
数值模拟技术在大型锻件生产中的应用概述引言大型锻件生产是现代制造业中的重要组成部分,其广泛应用于航空航天、船舶、能源等领域。
传统的大型锻件生产过程存在一些问题,如生产周期长、成本高、质量难以保证等。
为了解决这些问题,数值模拟技术逐渐被引入到大型锻件生产中,以提高生产效率和质量。
本文将对数值模拟技术在大型锻件生产中的应用进行概述。
数值模拟技术概述数值模拟技术是利用计算机对工程问题进行模拟和求解的一种方法。
它通过建立复杂的数学模型和方程组,并利用数值计算方法进行求解,以得到问题的近似解。
在大型锻件生产中,数值模拟技术主要应用于锻造工艺的优化和质量预测。
数值模拟技术在大型锻件生产中的应用1. 锻造工艺优化数值模拟技术可以对大型锻件的锻造工艺进行优化,以提高生产效率和质量。
首先,通过建立数学模型和方程组,模拟锻造过程中的物理现象和力学行为。
然后,利用数值计算方法对模型进行求解,得到锻造过程中的温度、应力、变形等参数的分布情况。
最后,通过对这些参数的分析和优化,确定最佳的锻造工艺参数。
这样可以减少锻件的变形和裂纹等缺陷,提高产品的质量。
2. 锻件质量预测数值模拟技术可以预测大型锻件在锻造过程中的质量情况,从而提前发现可能出现的缺陷和问题。
在数值模拟中,可以模拟锻件在锻造过程中的受力情况、温度变化和变形行为等。
通过分析模拟结果,可以判断锻件是否存在裂纹、变形过大等问题。
如果发现问题,可以及时调整工艺参数,避免生产出次品产品或发生事故。
3. 锻件设计改进数值模拟技术还可以用于大型锻件的设计改进。
通过模拟分析,可以对设计进行优化,以提高锻件的强度和耐久性。
同时,数值模拟还可以评估不同设计方案的可行性和效果,避免进行试验和生产后才发现问题。
这样可以节省时间和成本,提高产品的设计质量。
4. 锻造工艺参数优化数值模拟技术可以帮助优化大型锻件的锻造工艺参数,以提高生产效率和质量。
通过模拟分析,可以确定最佳的锻压力、锻造速度、温度等工艺参数,以降低生产成本和缩短生产周期。
数值模拟技术在大型锻件生产中的应用

1950年代:有限元方 法被提出,成为数值 模拟技术的重要工具
1960年代:有限差分方 法被广泛应用,成为数 值模拟技术的重要方法
之一
1970年代:有限体积方 法被提出,成为数值模 拟技术的重,成为数值模拟
技术的重要方法之一
1990年代:无网格方法 被提出,成为数值模拟
拓展大型锻件生 产市场,提高市 场份额
加强与下游企业 的合作,提高产 品竞争力
研发新型数值模 拟技术,提高生 产效率和质量
加强宣传推广, 提高品牌知名度 和影响力
技术研发:加大研发投入,提高数值模拟技术的准确性和效率
应用推广:扩大数值模拟技术在大型锻件生产中的应用范围,提高生产效率
人才培养:加强人才培养,提高数值模拟技术应用人员的专业素质
数值模拟技术在大型 锻件生产中的应用
汇报人:
目录
添加目录标题
数值模拟技术概述
大型锻件生产中的问题
数值模拟技术在大型 锻件生产中的应用
数值模拟技术在大型 锻件生产中的价值
数值模拟技术在大型锻 件生产中的未来发展
添加章节标题
数值模拟技术概述
数值模拟技术是一种通过计算机模拟来预测和优化物理、化学、生物等系统行为的技术。
合作发展:与其他企业、高校、研究机构等合作,共同推动数值模拟技术在大型锻件生产中 的发展
感谢您的观看
汇报人:
数值模拟技术可以应用于各种领域,包括工程、科学、医学等。
数值模拟技术可以帮助我们更好地理解和预测复杂系统的行为,从而提高生产效率和产品质 量。
数值模拟技术在大型锻件生产中的应用可以预测锻件的变形、应力分布等,从而优化生产工 艺和降低生产成本。
1940年代:数值模拟技 术开始应用于流体力学
三维扫描和数值模拟在现代锻造企业的结合应用

结 论 :辊 坯 摆 放 可 能 会 引起
冈3 BI , ( 域1 人 】 分 布 不 均带 来 后 工 序
住拳 部位 亢不满 ,此工 序未 发
现表而缺陷 ( 折 叠 ) 。根 据 现 场
生 产情 况 分 析住 前 轴 锻 件 工字 梁 上 出现 的 表面 徽 裂纹 比 例 很大 ,
( r 0I l e r bI 】 I e t
具 ■维 扫 描 分 析 : 如 图3 所示, 利 真 实 摸 具 状 态 进 行 数 值 模
拟。
坯料温度
造 数 值 模 拟 技 术 对生 产 线 所 使 用
t e mp e r a t u r e ):l 】 9 1 ℃
1 所 示 ,我 们 对 陔 J 品 各 成 形 工
l e n g t h ) :1 6 9 3 mr n
避免 r 锻 什 拳 火部 f 住后 [ 序 … 现 的充 满 、折 叠 等现 象 。
_ _ I 辊坯料 长 度 ( t wo — r o l l e r
序使r f { 的 馍具 三维 扫描 、 逆 向 建 模 、制 造 质 量 ,以及 【 : 线 模 具嘻 损 情 况等 进 行 质 量 分 析 、锻
提 供 可靠 的 数字化 分析。
关键 词 :前轴 ;三 维扫描 :数 值模拟
近 年 来 ,随 营 为z F、
程模拟
模具 i 维扫描分析:如
b. 1 l e t l e n g t h) : I 97 4 m m
V O L V O、ME R I T O R 等旧外高端
客 提 供 增 值 产 . ; , J 时 ,企 业 通过 _ _ f 断 研 发 、 创新 等 ・ 系列 技 术 成 川 ,与 相 芙利 益 方
数值模拟技术在大型锻件生产中的应用概述
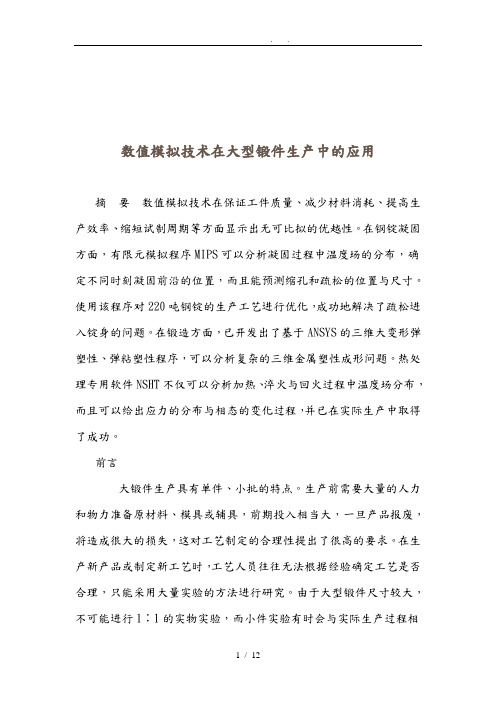
数值模拟技术在大型锻件生产中的应用摘要数值模拟技术在保证工件质量、减少材料消耗、提高生产效率、缩短试制周期等方面显示出无可比拟的优越性。
在钢锭凝固方面,有限元模拟程序MIPS可以分析凝固过程中温度场的分布,确定不同时刻凝固前沿的位置,而且能预测缩孔和疏松的位置与尺寸。
使用该程序对220吨钢锭的生产工艺进行优化,成功地解决了疏松进入锭身的问题。
在锻造方面,已开发出了基于ANSYS的三维大变形弹塑性、弹粘塑性程序,可以分析复杂的三维金属塑性成形问题。
热处理专用软件NSHT不仅可以分析加热、淬火与回火过程中温度场分布,而且可以给出应力的分布与相态的变化过程,并已在实际生产中取得了成功。
前言大锻件生产具有单件、小批的特点。
生产前需要大量的人力和物力准备原材料、模具或辅具,前期投入相当大,一旦产品报废,将造成很大的损失,这对工艺制定的合理性提出了很高的要求。
在生产新产品或制定新工艺时,工艺人员往往无法根据经验确定工艺是否合理,只能采用大量实验的方法进行研究。
由于大型锻件尺寸较大,不可能进行1∶1的实物实验,而小件实验有时会与实际生产过程相差过大。
而且物理实验通常只能给出工艺过程某个阶段的结果,无法全面了解整个工艺过程,具有一定的局限性。
由于大锻件生产的这些特殊性,采用先进的数值模拟技术改变工艺制定过程中仅凭经验决定的现状是具有重要意义的。
1 数值模拟技术在现代制造中的地位和作用随着计算机技术的飞速发展,人类社会已经步入了信息时代。
计算机与网络不仅改变了人们生活方式,也同样改变了传统机械制造的概念与方法。
随着计算机辅助技术(CAX)的广泛应用,计算机已经深入到工业生产的各个环节之中。
一个现代的产品制造过程可以由图1来描述。
当接到生产任务时,首先采用CAD(Computer Aided Design)系统进行产品设计,其设计结果将由CAE(Computer Aided Engineering)系统对其生产工艺的可行性与合理性进行评估,如果其不满足制造要求或所需要成本太高,将返回到CAD系统中进行重新设计:如果通过了CAE的评估,就将采用CAM(Computer Aided Manufacturing)系统进行实际的生产制造。
- 1、下载文档前请自行甄别文档内容的完整性,平台不提供额外的编辑、内容补充、找答案等附加服务。
- 2、"仅部分预览"的文档,不可在线预览部分如存在完整性等问题,可反馈申请退款(可完整预览的文档不适用该条件!)。
- 3、如文档侵犯您的权益,请联系客服反馈,我们会尽快为您处理(人工客服工作时间:9:00-18:30)。
数值模拟技术在大型锻件生产中的应用数值模拟技术在保证工件质量、减少材料消耗、提高生摘要在钢锭凝固产效率、缩短试制周期等方面显示出无可比拟的优越性。
可以分析凝固过程中温度场的分布,确方面,有限元模拟程序MIPS 定不同时刻凝固前沿的位置,而且能预测缩孔和疏松的位置及尺寸。
成功地解决了疏松进吨钢锭的生产工艺进行优化,使用该程序对220的三维大变形弹ANSYS在锻造方面,已开发出了基于入锭身的问题。
塑性、弹粘塑性程序,可以分析复杂的三维金属塑性成形问题。
热处淬火及回火过程中温度场分布,理专用软件NSHT不仅可以分析加热、并已在实际生产中取得而且可以给出应力的分布及相态的变化过程,了成功。
前言大锻件生产具有单件、小批的特点。
生产前需要大量的人力和物力准备原材料、模具或辅具,前期投入相当大,一旦产品报废,将造成很大的损失,这对工艺制定的合理性提出了很高的要求。
在生产新产品或制定新工艺时,工艺人员往往无法根据经验确定工艺是否合理,只能采用大量实验的方法进行研究。
由于大型锻件尺寸较大,的实物实验,而小件实验有时会与实际生产过程相1∶1不可能进行差过大。
而且物理实验通常只能给出工艺过程某个阶段的结果,无法全面了解整个工艺过程,具有一定的局限性。
由于大锻件生产的这些特殊性,采用先进的数值模拟技术改变工艺制定过程中仅凭经验决定的现状是具有重要意义的。
1 数值模拟技术在现代制造中的地位和作用随着计算机技术的飞速发展,人类社会已经步入了信息时代。
计算机及网络不仅改变了人们生活方式,也同样改变了传统机械制造的概念与方法。
随着计算机辅助技术(CAX)的广泛应用,计算机已经深入到工业生产的各个环节之中。
一个现代的产品制造过程可以由图1来描述。
当接到生产任务时,首先采用CAD(Computer Aided Design)系统进行产品设计,其设计结果将由CAE(Computer Aided Engineering)系统对其生产工艺的可行性及合理性进行评估,如果其不满足制造要求或所需要成本太高,将返回到CAD系统中进行重新设计:如果通过了CAE的评估,就将采用CAM(Computer Aided Manufacturing)系统进行实际的生产制造。
这一生产模式已在工业发达国家得到了广泛的应用,并且近年来更提出了并行工程技术(Concurrent Engineering)与虚拟制造技术(Virtual Manufacturing)等新概念和新方法,将产品设计、工艺制定、生产制造及经管中的CAD、CAE、CAM、CAPP、MRP等计算机辅助技术,通过先进的信息技术结合起来,从而达到进一步缩短产品设计、制造周期,提高产品质量,降低成本,增强产品竞争能力的目的。
但不论哪一种方法,等仍是整个计算机辅助技术的核心与基础。
CAD/CAE/CAM.图1 现代产品制造过程示意图数值模拟技术是CAE的关键技术。
通过建立相应的数学模型,可以在昂贵费时的模具或辅具制造之前,在计算机中对工艺的全过程进行分析。
不仅可以通过图形、数据等方法直观地得到诸如温度、应力、载荷等各种信息,而且可预测可能存在的缺陷;通过改变工艺参数对不同技术方案进行模拟分析,可以从各技术方案的对比中归纳总结出规律,进而实现工艺的优化。
数值模拟技术在保证工件质量,减少材料消耗,提高生产效率,缩短试制周期等方面显示出无可比拟的优越性。
在工业发达国家,数值模拟技术已被认为是生产中必不可少的一个环节,目前在国内数值模拟技术也早已走出象牙塔,并已在实际生产中取得了巨大成功。
本文所提到的例子,都具有明确的生产背景,是近十多年来我们利用数值模拟方法解决大锻件生产实际问题中较为成功的例子。
2 数值模拟技术在大型锻件生产中的应用实例从八十年代中期开始,清华大学机械工程系由刘庄教授领导的课题组就一直从事数值模拟技术在大锻件生产上应用的研究,进行了大量有意义的工作。
从钢锭浇注、锻件生产及锻后热处理,所进行的研究工作覆盖了大锻件热加工生产的各个环节,完成了可以用于钢锭凝固过程模拟及缺陷预测,锻造过程模拟及工艺优化,淬、回火过程温.度及应力场分析的计算程序。
通过与各生产厂家的密切合作,这些程序已经在生产中得到了实际应用,计算结果与实际情况相当吻合,充分证明了程序的可靠性。
而且利用这些软件已经对很多实际生产工艺进行了优化,取得了显著的经济效益。
这些软件可以为大锻件的热加工工艺制定提供一个全面的CAE解决技术方案,能够有效地提高工艺制定的合理性,提高生产效率。
2.1 钢锭凝固过程模拟及缺陷预测众所周知,大型锻造用钢锭中一般存在缩孔、疏松、夹杂和偏析等缺陷。
这些缺陷的存在会增大材料的消耗,而且可能会影响到后续锻造工序。
认识缺陷形成及分布的规律,并进而提出合理的铸锭工艺,对于提高大锻件质量、缩短生产周期、降低材料消耗具有重大意义。
从八十年代中期开始,作者与第一重型机器厂合作,对钢锭凝固过程的温度场进行了大量研究,建立了钢锭凝固中传热过程的数学模型。
同时对发热剂、保温剂的发热机理进行了深入的探讨,并建立了相应的数学模型。
在此基础上开发出一套专用的有限元模拟程序MIPS。
MIPS可以分析凝固过程中温度场的分布,确定不同时刻凝固前沿的位置,而且能预测缩孔及疏松的位置及尺寸。
使用该程序对一重220吨钢锭的生产工艺所进行的优化,成功地解决了疏松进入锭身的问显示了工艺改进前后,缩孔及疏松的模拟结果。
2题。
图(a)原工艺 (b)改进工艺图2 220吨钢锭上缩孔疏松缺陷的分布采用MIPS软件并结合正交设计的方法,对钢锭结构等工艺参数对缩孔大小的影响进行了研究,得出了“冒口端部条件对缩孔疏松的影响最显著,其次是侧壁耐火砖的导热系数,再次是锭身锥度,而锭身高径比则影响不大”的结论。
这对于工艺人员掌握钢锭生产规律,并优化工艺会有很大的帮助。
MIPS软件不仅在普通钢锭的凝固模拟及缺陷预测中取得了成功,而且已成功地应用到无冒口或小冒口钢锭,定向结晶锭以及空心钢锭的研究当中。
尤其在定向结晶锭中,通过引入流场,对凝固过程中的传质过程进行了数学描述,从而能够准确地预测出钢锭的偏析情况。
在大型钢锭凝固过程中,锭模出现裂纹甚至报废的现象也是不容忽视的。
在MIPS软件成功应用的基础上,我们又开发了三维钢锭锭模的应力分析程序,有助于解决这一问题。
2.2 锻造过程模拟及工艺优化这是大锻件生产钢锭需要经过锻造才能达到产品所希望的形状,关键的一环,它的成功与否直接影响着整个生产。
以前开发的一些程序,由于大多针对某一具体的工艺过程,不具备造型功能,在模具运动或边界条件的施加等方面存在着很大的局限性,通用性比较差。
一旦遇到新的问题,通常要对程序作较大的修改,无法满足锻造过程模拟的需要。
针对这一问题,我们采用与世界上成熟的商品化软件,如ANSYS相结合的道路,利用ANSYS完善的前、后期处理功能,成功地解决了ANSYS不能进行网格重划的难题,开发出了一套二维和三维的弹塑性、弹粘塑性大变形通用的锻造过程模拟程序。
该程序可以与ANSYS实现无缝集成,从而具有了较强的通用性。
该软件可以描述多个模具及其运动,能有效地控制加载;不仅可以得到金属流动、应力、应变的变化,而且可以得到载荷力,模具受力等信息,有助于在制定工艺时选择合适设备,评估模具的磨损甚至破坏。
多向模锻工艺综合了模锻和挤压工艺的特点,可以制造外形复杂、中空、无飞边锻件。
过去,这方面的研究多采用物理实验方法,如采用在铅试样对称面上划网格或做低倍实验等来研究金属的流动情况。
由于多向模锻件外形复杂、中空,且在封闭型腔内成形,影响因素较多,金属变形流动过程极为剧烈、复杂,所以这些物理实验方法都存在着一定的局限性,如网格法对于剧烈的变形将失去作用,低倍实验对于复杂的流动也会得不到清晰的金属流线。
更重要的是,通过这些实验,只能对变形过程的某一方面进行研究,而得不到对变形全过程的认识;而且由于模具的加工、调试费工费时,需要大量的资金投入。
而采用数值模拟方法,可以完全避免这些缺陷,得到整个变.形全过程的各种信息。
由于多向模锻的特点,对其工艺过程进行数值模拟具有很大的难度,而且也颇具代表性。
由于等径三通的形状特点,其多向模锻挤压成形的工艺过程应为一个三维问题,见图3。
为使问题简化,本文采用了平面应变模型,主要分析两正交管轴线所组成对称面上的金属流动及模具受力情况。
图4显示的模拟结果表明,在水平冲头先挤入的技术方案中,当水平冲头挤到打靠位置时,冲头上部的坯料金属会因为较快地向上流动,会脱离开水平冲头,从而在坯料与水平冲头之间形成一个空腔。
这一结果与实际吻合得相当好,由于模拟采用了平面简化模型,在空腔的大小上与实际还有一些差别,但模拟结果仍能揭示出该工艺的变形特点。
图3 等径三通锻件图图4 三通挤压过程的模拟结果在成功开发了二维分析程序的基础上,我们已经开发出了基于ANSYS 的三维大变形弹塑性、弹粘塑性程序,可以分析复杂的三维金属塑性成形问题。
图5所示为生产大型曲轴TR法镦锻成形工艺的数值模拟结果。
通过模拟计算可以有效地确定水平进给速度与垂直进给速度对成形的影响,可以帮助工艺人员确定适宜的速度匹配技术方案,从而达到优化工艺的目的。
图5 曲轴TR法镦锻工艺的模拟结果(等效塑性变形的分布)3 热处理过程模拟热处理工序是热加工的最后一道工序,是保证产品内部质量、满足性能要求的关键环节。
为保证产品的质量及性能要求,避免产生较大的残余应力,热处理工艺的制定普遍倾向于采用保守一点的方法,所以是耗时较长的工序之一。
较长的加热、保温时间会大大增加能源的消耗,也会拖延产品投入市场的时间。
如何在保证质量的前提下,缩短热处理加工工时,是改进热处理工艺的一个重要发展方向。
经过十年来的大量研究工作,在使用数值模拟技术进行大锻件热处理工艺的分析和优化方面,我们积累了大量的经验和数据。
所开发的热处理专用软件NSHT不仅可以分析加热、淬火及回火过程中温度场分布,而且可以给出应力的分布及相态的变化过程。
通过数值模拟不仅可以对整个工艺过程有更加深入、全面的认识,而且可以用来对工艺进行优化。
我们与一重集团合作,采用NSHT软件对材质为26Cr2Ni4MoV的6MW转子工艺进行了优化。
图6是改进前的淬、回火热处理规范。
通过对加热、淬火及回火不同技术方案的模拟计算表明:a 淬火规范b 回火规范图6 6MW转子原工艺热处理规范示意图●原工艺技术方案中,为达到蓄积热量,高速通过奥氏体化相变区的目的而在660℃保温8小时实际上可以取消,改为以适当的加热速度通过相变区,进入保温阶段,可以缩短加热所需要的时间。
●原工艺中空水交替冷却,最后油冷可以采用水淬激冷至心部超过珠光体相变区,然后空冷通过贝氏体相变区,操作既方便又能满足应力的要求。