锂离子电池工艺配料
锂电池各项工序控制重点

锂电池各项工序控制重点锂离子电池的生产要一丝不苟,各个工序需要做到尽善尽美。
新能源前线整理了锂电池实际生产的工艺流程。
(一) 配料:1.溶液配制:a) PVDF(或CMC)与溶剂NMP(或去离子水)的混合比例和称量;b) 溶液的搅拌时间、搅拌频率和次数(及溶液表面温度);c) 溶液配制完成后,对溶液的检验:粘度(测试)\溶解程度(目测)及搁置时间;d) 负极:SBR+CMC溶液,搅拌时间和频率。
2.活性物质:a) 称量和混合时监控混合比例、数量是否正确;b) 球磨:正负极的球磨时间;球磨桶内玛瑙珠与混料的比例;玛瑙球中大球与小球的例;c) 烘烤:烘烤温度、时间的设置;烘烤完成后冷却后测试温度。
d) 活性物质与溶液的混合搅拌:搅拌方式、搅拌时间和频率。
e) 过筛:过100目(或150目)分子筛。
f) 测试、检验:对浆料、混料进行以下测试:固含量、粘度、混料细度、振实密度、浆料密度。
(二)涂布1.集流体的首检:a) 集流体规格(长宽厚)的确认;b) 集流体标准(实际)重量的确认;c) 集流体的亲(疏)水性及外观(有无碰伤、划痕和破损)。
2.敷料量(标准值、上、下限值)的计算:a) 单面敷料量(以接近此标准的极片厚度确定单面厚度);b) 双面敷料量(以最接近此标准的极片厚度确定双面的极片厚度。
)3.浆料的确认:是否过稠(稀)\流动性好,是否有颗粒,气泡过多,是否已干结.4.极片效果:a) 比重(片厚)的确认;b) 外观:有无划线、断带、结料(滚轮或极片背面)是否积料过厚,是否有未干透或烤焦,有无露铜或异物颗粒;5.裁片:规格确认有无毛刺,外观检验。
(三)制片(前段):1.压片:a) 确认型号和该型号正、负极片的标准厚度;b) 最高档次极片压片后(NO.1或NO.1及NO.2)的厚度、外观有无变形、起泡、掉料、有无粘机、压叠。
c) 极片的强度检验;2.分片:a) 刀口规格、大片极片的规格(长宽)、外观确认;b) 分出的小片宽度;c) 分出的小片有无毛刺、起皱、或裁斜、掉料(正)。
锂离子电池的制作流程

锂离子电池的制作流程1.负极材料的制备:2.正极材料的制备:锂离子电池的正极材料有多种选择,常见的有锂铁磷酸盐(LiFePO4)和三元材料(如锰酸锂、钴酸锂和镍酸锂的复合物)。
正极材料的制备通常采用固态反应或湿法合成。
然后,将正极材料与导电剂和粘结剂混合,并添加适量的溶剂,制成正极材料浆料。
3.电解液的制备:电解液是锂离子电池中起电导和传递锂离子作用的重要组成部分。
一般采用有机溶剂和锂盐混合制备电解液。
有机溶剂通常是碳酸酯、环状碳酸酯或甘醇醚等。
锂盐主要有氟化锂、磷酸锂或六氟磷酸锂等。
制备电解液时需要注意溶剂和锂盐的纯度和配比,以及获得高电导率的条件。
4.卷绕和层叠:卷绕和层叠是组装锂离子电池的关键步骤。
首先,在电解液中混合正负极材料与导电剂的浆料,制备正负极片。
然后,将正负极片和隔膜交替层叠在一起,形成电池芯。
层叠过程中需要注意电极片之间的对齐和紧密贴合,以及避免正负极短路。
5.紧凑和封装:将层叠好的电池芯放在压力机中,经过一定的压力和温度下进行紧凑处理。
这一步骤有助于提高电池芯的紧凑度和一致性。
然后,将电池芯封装在铝塑复合膜或铝箔袋中,并进行密封。
封装过程中需要注意避免氧气和水分的进入,以提高电池的安全性和稳定性。
6.电池性能测试和整理:整理是指将制作好的电池按照一定的标准进行测试和分类整理。
主要测试项包括电池容量、内阻、循环寿命、温度特性等。
根据测试结果,将电池按照性能等级进行分类。
以上就是锂离子电池的制作流程。
锂离子电池的制作过程需要严格的操作和控制,以确保电池的性能和安全性。
同时,不同厂商和应用场景可能有所差异,上述流程仅为一般制作流程的概述。
锂离子电池制作工序控制重点

锂离子电池制作工序控制重点(一) 配料:1.溶液配制:a) PVDF(或CMC)与溶剂NMP(或去离子水)的混合比例和称量;b) 溶液的搅拌时间、搅拌频率和次数(及溶液表面温度);c) 溶液配制完成后,对溶液的检验:粘度(测试)\溶解程度(目测)及搁置时间;d) 负极:SBR+CMC溶液,搅拌时间和频率。
2.活性物质:a) 称量和混合时监控混合比例、数量是否正确;b) 球磨:正负极的球磨时间;球磨桶内玛瑙珠与混料的比例;玛瑙球中大球与小球的比例;c) 烘烤:烘烤温度、时间的设置;烘烤完成后冷却后测试温度。
d) 活性物质与溶液的混合搅拌:搅拌方式、搅拌时间和频率。
e) 过筛:过100目(或150目)分子筛。
f) 测试、检验:对浆料、混料进行以下测试:固含量、粘度、混料细度、振实密度、浆料密度。
(二)涂布1.集流体的首检:a) 集流体规格(长宽厚)的确认;b) 集流体标准(实际)重量的确认;c) 集流体的亲(疏)水性及外观(有无碰伤、划痕和破损)。
2.敷料量(标准值、上、下限值)的计算:a) 单面敷料量(以接近此标准的极片厚度确定单面厚度);b) 双面敷料量(以最接近此标准的极片厚度确定双面的极片厚度。
)3.浆料的确认:是否过稠(稀)\流动性好,是否有颗粒,气泡过多,是否已干结.4.极片效果:a) 比重(片厚)的确认;b) 外观:有无划线、断带、结料(滚轮或极片背面)是否积料过厚,是否有未干透或烤焦,有无露铜或异物颗粒;5.裁片:规格确认有无毛刺,外观检验。
(三)制片(前段):1.压片:a) 确认型号和该型号正、负极片的标准厚度;b) 最高档次极片压片后(NO.1或NO.1及NO.2)的厚度、外观有无变形、起泡、掉料、有无粘机、压叠。
c) 极片的强度检验;2.分片:a) 刀口规格、大片极片的规格(长宽)、外观确认;b) 分出的小片宽度;c) 分出的小片有无毛刺、起皱、或裁斜、掉料(正)。
3.分档称片:a) 称量有无错分;b) 外观检验:尺寸超差(极片尺寸、掉料、折痕、破损、浮料、未刮净等)。
锂电池制造的13大流程及关键参数
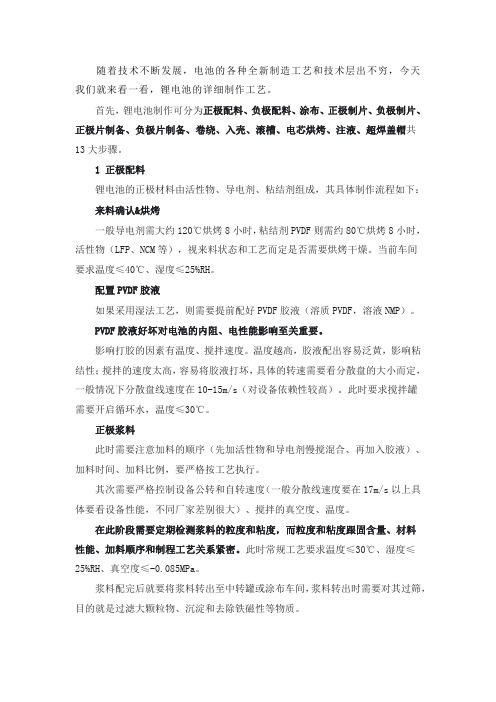
随着技术不断发展,电池的各种全新制造工艺和技术层出不穷,今天我们就来看一看,锂电池的详细制作工艺。
首先,锂电池制作可分为正极配料、负极配料、涂布、正极制片、负极制片、正极片制备、负极片制备、卷绕、入壳、滚槽、电芯烘烤、注液、超焊盖帽共13大步骤。
1正极配料锂电池的正极材料由活性物、导电剂、粘结剂组成,其具体制作流程如下:来料确认&烘烤一般导电剂需大约120℃烘烤8小时,粘结剂PVDF则需约80℃烘烤8小时,活性物(LFP、NCM等),视来料状态和工艺而定是否需要烘烤干燥。
当前车间要求温度≤40℃、湿度≤25%RH。
配置PVDF胶液如果采用湿法工艺,则需要提前配好PVDF胶液(溶质PVDF,溶液NMP)。
PVDF胶液好坏对电池的内阻、电性能影响至关重要。
影响打胶的因素有温度、搅拌速度。
温度越高,胶液配出容易泛黄,影响粘结性;搅拌的速度太高,容易将胶液打坏,具体的转速需要看分散盘的大小而定,一般情况下分散盘线速度在10-15m/s(对设备依赖性较高)。
此时要求搅拌罐需要开启循环水,温度≤30℃。
正极浆料此时需要注意加料的顺序(先加活性物和导电剂慢搅混合、再加入胶液)、加料时间、加料比例,要严格按工艺执行。
其次需要严格控制设备公转和自转速度(一般分散线速度要在17m/s以上具体要看设备性能,不同厂家差别很大)、搅拌的真空度、温度。
在此阶段需要定期检测浆料的粒度和粘度,而粒度和粘度跟固含量、材料性能、加料顺序和制程工艺关系紧密。
此时常规工艺要求温度≤30℃、湿度≤25%RH、真空度≤-0.085MPa。
浆料配完后就要将浆料转出至中转罐或涂布车间,浆料转出时需要对其过筛,目的就是过滤大颗粒物、沉淀和去除铁磁性等物质。
大颗粒影响涂布到最后可能导致电池自放过大或短路的风险;浆料铁磁性物质过高会导致电池自放电过大等不良。
此时的工艺要求是温度≤40℃,湿度≤25%RH,筛网≤100目,粒度≤15um(参数仅供参考)。
锂离子电池基本原理配方及工艺流程

锂离⼦电池基本原理配⽅及⼯艺流程锂离⼦电池原理及⼯艺流程⼀、原理1.0 正极构造LiCoO2+ 导电剂+ 粘合剂(PVDF) + 集流体(铝箔)正极2.0 负极构造⽯墨+ 导电剂+ 增稠剂(CMC) + 粘结剂(SBR) + 集流体(铜箔)负极3.0⼯作原理3.1 充电过程:⼀个电源给电池充电,此时正极上的电⼦e从通过外部电路跑到负极上,正锂离⼦Li+从正极“跳进”电解液⾥,“爬过”隔膜上弯弯曲曲的⼩洞,“游泳”到达负极,与早就跑过来的电⼦结合在⼀起。
负极上发⽣的反应为6C + xLi++ x e?→Li x C63.2 电池放电过程放电有恒流放电和恒阻放电,恒流放电其实是在外电路加⼀个可以随电压变化⽽变化的可变电阻,恒阻放电的实质都是在电池正负极加⼀个电阻让电⼦通过。
由此可知,只要负极上的电⼦不能从负极跑到正极,电池就不会放电。
电⼦和Li+都是同时⾏动的,⽅向相同但路不同,放电时,电⼦从负极经过电⼦导体跑到正极,锂离⼦Li+从负极“跳进”电解液⾥,“爬过”隔膜上弯弯曲曲的⼩洞,“游泳”到达正极,与早就跑过来的电⼦结合在⼀起。
3.3 充放电特性电芯正极采⽤LiCoO2、LiNiO2、LiMn2O2,其中LiCoO2本是⼀种层结构很稳定的晶型,但当从LiCoO2拿⾛x个Li离⼦后,其结构可能发⽣变化,但是否发⽣变化取决于x的⼤⼩。
通过研究发现当x > 0.5时,Li1-x CoO2的结构表现为极其不稳定,会发⽣晶型瘫塌,其外部表现为电芯的压倒终结。
所以电芯在使⽤过程中应通过限制充电电压来控制Li1-X CoO2中的x值,⼀般充电电压不⼤于4.2V那么x⼩于0.5 ,这时Li1-X CoO2的晶型仍是稳定的。
负极C6其本⾝有⾃⼰的特点,当第⼀次化成后,正极LiCoO2中的Li被充到负极C6中,当放电时Li回到正极LiCoO2中,但化成之后必须有⼀部分Li留在负极C6中⼼,以保证下次充放电Li的正常嵌⼊,否则电芯的压倒很短,为了保证有⼀部分Li留在负极C6中,⼀般通过限制放电下限电压来实现:安全充电上限电压≤ 4.2V,放电下限电压≥ 2.5V。
锂电池配料工序简介

配料简介配料:用专门的溶剂和粘接剂分别与粉末状的正负极活性物质混合,经高速搅拌均匀后,制成浆状的正负极物质;工艺流程:检验原材料→称料→烘料→打胶→加料→测粘度→调粘度→洗锅关键操作控制重点:车间温度常温,湿度≤30%真空度≤-0.08mpa转速的调节原材料的称重搅拌过程控制点原材料及作用:正极原材料:a.锰酸锂、KS-15、SP、PVDF(761A)、NMPb.磷酸亚铁锂、KS-15、SP、PVDF(900)、NMP负极原材料:碳黑、SP、CMC、SBR(1)导电石墨(KS-15):非极性物质,易被非极性物质污染,易在非极性物质中分散;不易吸水,也不易在水中分散。
被污染的石墨,在水中分散后,容易重新团聚。
一般粒径D50为20μm左右。
颗粒形状多样且多不规则,主要有球形、片状、纤维状等。
(2)水性粘合剂(SBR):小分子线性链状乳液,极易溶于水和极性溶剂。
(3)防沉淀剂(CMC):高分子化合物,易溶于水和极性溶剂。
(4)粘合剂(PVDF):非极性物质,链状物,分子量从300,000到3,000,000不等;吸水后分子量下降,粘性变差。
(5) NMP:弱极性液体,用来溶解/溶胀PVDF,同时用来稀释浆料。
(6)去离子水(或蒸馏水):稀释剂,酌量添加,改变浆料的流动。
(7)导电剂碳黑(SP):非极性物质,葡萄链状物,含水量3-6%,吸油值~300,粒径一般为 2-5 μm;主要有普通碳黑、超导碳黑、石墨乳等,在大批量应用时一般选择超导碳黑和石墨乳复配;通常为中。
(8)锰酸锂:较有前景的锂离子正极材料之一,相比钴酸锂等传统正极材料,锰酸锂具有资源丰富、成本低、无污染、安全性好、倍率性能好等优点,是理想的动力电池正极材料。
(9)磷酸铁亚锂:磷酸铁亚锂为近来新开发的锂离子电池电极材料,主要用于动力锂离子电池,作为正极活性物质使用,人们习惯也称其为磷酸铁锂。
主要设备:搅拌机配料时注意事项:1、防止混入其它杂质;2、防止浆料飞溅;3、浆料的浓度(固含量)应从高往低逐渐调整,以免增加麻烦;4、在搅拌的间歇过程中要注意刮边和刮底,确保分散均匀;5、浆料不宜长时间搁置,以免沉淀或均匀降低;6、需烘烤的物料必须密封冷却之后方可以加入,以免组分材料质变化;7、搅拌时间的长短以设备能、材料加入量为主;搅拌桨的使用以浆料分散难度进行更换,无法更换的可将转速由慢到快进行调整,以免损伤设备;8、出料前对浆料进行过筛,除去大颗粒以防涂布时造成断带;9、搅拌速度对分散速度的影响。
锂离子电池基本工艺介绍

锂离子电池基本工艺介绍一、正负极材料制备1.正极材料制备:常见的正极材料有锂铁磷酸铁、锂钴氧化物和锂镍锰酸等。
制备过程中,先按一定配比混合原料,并加入适量的粘结剂和导电剂,形成混合物。
然后在高温下进行焙烧和研磨,最后得到所需的正极材料。
2.负极材料制备:常见的负极材料是石墨。
制备过程中,石墨粉末和粘结剂混合,形成糊状物。
然后在导电剂的作用下涂布在铜箔上,并经过干燥和压制,最后得到负极片。
二、电池装配1.正负极片处理:正负极片通过一个铜箔或镍箔连接条与锂离子电解液接触。
正极片上涂覆了正极活性物质的混合物,负极片则上涂覆了负极活性物质的混合物。
2.卷绕装配:正负极片按一定规则卷绕在一起,并用隔膜层隔开。
隔膜层起到隔离正负极材料并允许离子传导的作用。
正负极片之间要保持适当的压力和接触性,以确保电池性能稳定。
3.外壳封装:卷绕的电池芯片通常会被放置在一个金属壳体中。
壳体可以是铝合金或不锈钢制成的圆筒状结构。
电池芯片和壳体之间应用密封圈封闭,以防止电池内部液体泄漏。
三、电池成熟1.注液注电:将电池芯片与电解液连接,通入适量的电解质。
电解液是锂盐溶液,可以传输锂离子,并完成电池的充放电过程。
然后,在适当的电流和电压下对电池进行充电,以使电池活化。
2.射频焊接:使用射频焊接设备将电池芯片和连接条之间进行焊接,以确保连接的牢固性和可靠性。
焊接时需要注意温度和时间的控制,以避免过热损害电池。
3.成品检测:对已组装好的电池进行各项性能测试,包括容量测试、内阻测试、充放电性能测试等。
这些测试可以确保电池的质量和性能符合要求。
这些是锂离子电池制备的基本工艺过程。
在实际生产中,还需要进行更加详细和严格的材料筛选、工艺优化和质量控制措施,以确保电池的稳定性和安全性。
锂电池生产工艺及参数

锂电池生产工艺及参数锂电池是一种高能量密度、长寿命、环保的电池,被广泛应用于移动设备、电动汽车、储能系统等领域。
下面将介绍锂电池的生产工艺及参数。
一、正极材料制备工艺1. 混合材料:将锂铁磷酸、碳酸锂、氧化镍、氧化钴等按一定比例混合,加入适量的粘合剂和溶剂,搅拌均匀。
2. 涂布:将混合材料涂布在铝箔或铜箔上,形成正极片。
3. 干燥:将正极片放入烘箱中,进行干燥处理。
4. 压片:将干燥后的正极片放入压片机中,进行压片处理。
5. 切割:将压片后的正极片切割成适当大小。
二、负极材料制备工艺1. 混合材料:将石墨、聚丙烯、碳黑等按一定比例混合,加入适量的粘合剂和溶剂,搅拌均匀。
2. 涂布:将混合材料涂布在铜箔上,形成负极片。
3. 干燥:将负极片放入烘箱中,进行干燥处理。
4. 压片:将干燥后的负极片放入压片机中,进行压片处理。
5. 切割:将压片后的负极片切割成适当大小。
三、电解液制备工艺1. 配制电解液:将碳酸二甲酯、乙二醇、丙二醇、氟化锂等按一定比例混合,搅拌均匀。
2. 过滤:将配制好的电解液过滤,去除杂质。
四、电池组装工艺1. 组装:将正极片、负极片和隔膜按一定顺序叠放,形成电池芯。
2. 注液:将电解液注入电池芯中。
3. 封口:将电池芯封口,形成成品电池。
五、电池参数1. 电压:锂电池的电压一般为3.6V或3.7V。
2. 容量:锂电池的容量一般以毫安时(mAh)为单位,表示电池能够供应的电流量。
3. 充放电倍率:锂电池的充放电倍率表示电池能够承受的最大充放电电流。
4. 循环寿命:锂电池的循环寿命表示电池能够进行多少次充放电循环。
以上是锂电池的生产工艺及参数,锂电池的制备工艺和参数不断改进和提高,以满足不同领域的需求。
锂离子电池生产工艺流程详解
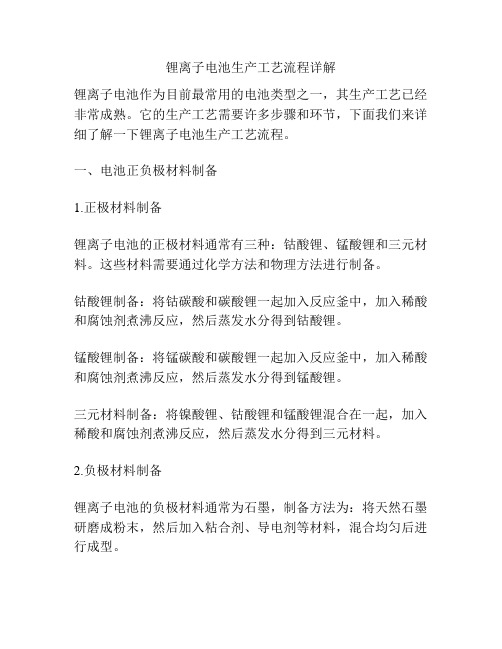
锂离子电池生产工艺流程详解锂离子电池作为目前最常用的电池类型之一,其生产工艺已经非常成熟。
它的生产工艺需要许多步骤和环节,下面我们来详细了解一下锂离子电池生产工艺流程。
一、电池正负极材料制备1.正极材料制备锂离子电池的正极材料通常有三种:钴酸锂、锰酸锂和三元材料。
这些材料需要通过化学方法和物理方法进行制备。
钴酸锂制备:将钴碳酸和碳酸锂一起加入反应釜中,加入稀酸和腐蚀剂煮沸反应,然后蒸发水分得到钴酸锂。
锰酸锂制备:将锰碳酸和碳酸锂一起加入反应釜中,加入稀酸和腐蚀剂煮沸反应,然后蒸发水分得到锰酸锂。
三元材料制备:将镍酸锂、钴酸锂和锰酸锂混合在一起,加入稀酸和腐蚀剂煮沸反应,然后蒸发水分得到三元材料。
2.负极材料制备锂离子电池的负极材料通常为石墨,制备方法为:将天然石墨研磨成粉末,然后加入粘合剂、导电剂等材料,混合均匀后进行成型。
二、电池组件制备1.正负极片制备将正极材料和负极材料分别涂覆在铝箔和铜箔上,然后将它们一层一层叠合在一起,形成正负极片。
2.隔膜制备将聚丙烯材料加入溶剂中,制成聚丙烯膜,然后在聚丙烯膜表面涂覆聚合物电解质,制成隔膜。
3.电解液制备锂离子电池的电解液通常为有机溶剂,例如碳酸二甲酯、碳酸乙酯等。
电解液还需要添加锂盐,通常为氟化锂或磷酸锂等物质。
三、电池组装1.正负极片堆叠将正负极片和隔膜一层一层堆叠,形成电池芯。
2.注入电解液将电池芯浸泡在预先准备好的电解液中,使电解液充分渗透到电池芯中。
3.封口在注入电解液后,需要对电池进行封口,避免电解液泄漏。
四、成品测试将已经组装好的电池进行各种测试,如容量测试、内阻测试、循环寿命测试等。
五、包装和出厂将测试合格的电池进行包装,如塑料、纸盒等包装,然后成品出厂。
以上就是锂离子电池生产工艺的详细流程,生产工艺环节多且繁琐,需要高度的科学精神和技术水平的支持。
因此,锂离子电池生产工艺的研究和提升,对于电池的性能和使用效果都有非常重要的影响。
锂离子电池的发展历程虽然只有30多年,但其在可再生能源、电子产品、电动汽车等领域的应用增速却是非常迅猛的。
锂离子电池生产工艺

锂离子电池生产工艺介绍锂离子电池是目前应用最广泛的可充电电池之一,具有高能量密度、长寿命和较轻的重量等优点。
本文将详细介绍锂离子电池的生产工艺,包括原材料准备、电池组装和测试等环节。
原材料准备1.正负极材料准备:–正极材料一般采用氧化物,如锰酸锂、三元材料等。
采购时需确保材料的纯度和性能指标符合要求。
–负极材料通常选择石墨,也有一些新型材料如硅等。
选定后需进行研磨和筛分等处理,以获得均一的颗粒粒径。
2.电解液准备:–电解液一般由有机溶剂和锂盐组成,如碳酸乙烯酯和氟酸锂。
需要严格控制溶剂的纯度和水分含量。
–需要进行溶剂和锂盐的混合、过滤和脱气等处理步骤。
电池组装1.正负极制备:–将正负极材料与粘结剂、导电剂等混合,制成浆料。
–利用涂布工艺将浆料均匀涂覆在导电片上,形成正负极片。
2.整体装配:–切割正负极片成合适的尺寸,并为其分配统一的重量。
–将正负极片与隔膜层一层层叠放,并注入电解液。
–组装后的电芯需要进行卷绕或堆叠,取决于电池的结构设计。
3.导电连接:–通过焊接或压接等方式连接正负极与电池的外部引线。
4.封装:–将组装好的电芯放入保护壳中,确保密封良好。
电池测试1.容量测试:–利用恒流充放电法对电池进行容量测试,以确定其额定容量。
–通过计算充放电时间和电流之间的关系,得到电池的容量曲线。
2.循环寿命测试:–将电池进行多次循环充放电,并测试其容量衰减情况。
–通过循环测试,评估电池的寿命和性能稳定性。
3.安全性能测试:–对电池进行短路、过充、过放等安全性能测试。
–检测电池在异常工况下的表现和反应。
结论锂离子电池的生产工艺包括原材料准备、电池组装和测试等环节。
合理控制材料的质量和工艺参数对电池的性能非常重要。
通过严格的测试和有效的质量控制,可以确保锂离子电池的高性能和安全可靠性。
同时,不断优化生产工艺和提高生产效率也是锂离子电池行业的发展方向。
磷酸铁锂生产配料及工艺

磷酸铁锂生产配料及工艺
本文档旨在介绍磷酸铁锂电池的生产配料和工艺。
磷酸铁锂(LiFePO4)作为一种重要的锂离子电池正极材料,其制备过程需要精确的配料和工艺控制。
配料
磷酸铁锂的制备配料主要包括以下成分:
1. 磷酸盐:作为磷酸铁锂的主要成分之一,可选择磷酸氢二钠(Na2HPO4)或磷酸氢二铵(NH4H2PO4)。
2. 铁源:常用的铁源包括硫酸亚铁(FeSO4)或硫酸亚铁七水合物(FeSO4·7H2O)。
3. 锂源:可选择碳酸锂(Li2CO3)或其他锂盐作为锂源。
在配料过程中,需要注意确保以上成分的纯度和质量,以及合适的配比比例。
工艺
磷酸铁锂电池的生产工艺主要包括以下步骤:
1. 配料和混合:按照经过优化的配方,将磷酸盐、铁源和锂源
按照一定比例进行称量,并进行充分的混合搅拌,确保均匀性。
2. 烧结:将混合后的配料进行烧结处理。
烧结过程一般在高温
下进行,以使各种成分发生化学反应,形成磷酸铁锂结晶。
3. 粉碎和分类:烧结后的产物进行粉碎和分类处理,以获得粒
径合适的磷酸铁锂粉末。
4. 表面处理:为了改善磷酸铁锂的电化学性能,可以对粉末进
行表面处理,如涂覆碳涂层等。
5. 制备电池:将磷酸铁锂粉末与电解液等其他组件组装成电池,形成完整的磷酸铁锂电池。
以上是磷酸铁锂生产配料及工艺的基本介绍。
在实际生产中,
还需要根据具体情况进行工艺参数的调整和优化,以提高磷酸铁锂
电池的性能和品质。
> 注意:文档中提供的信息仅为基本介绍,实际操作中应遵循相关法律法规和标准,具体配方和工艺应根据实际情况进行调整和确保合规。
锂离子电池工艺配料

1.正负极配方配料过程实际上是将浆料中的各种组成按标准比例混合在一起,调制成浆料,以利于均匀涂布,保证极片的一致性。
配料大致包括五个过程,即:原料的预处理、掺和、浸湿、分散和絮凝。
1.1正极配方(LiCoO2(钴酸锂)+导电剂(乙炔黑)+粘合剂(PVDF)+集流体(铝箔))LiCoO(10μm):93.5%;其它:6.5%如Super-P:4.0%;PVDF761:2.5;2NMP(增加粘结性):固体物质的重量比约为810:1496a) 正极黏度控制6000cps(温度25转子3);b) NMP重量须适当调节,达到黏度要求为宜;c) 特别注意温度湿度对黏度的影响●钴酸锂:正极活性物质,锂离子源,为电池提高锂源。
钴酸锂:非极性物质,不规则形状,粒径D50一般为6-8 μm,含水量≤0.2%,通常为碱性,PH值为10-11左右。
锰酸锂:非极性物质,不规则形状,粒径D50一般为5-7 μm,含水量≤0.2%,通常为弱碱性,PH值为8左右。
●导电剂:提高正极片的导电性,补偿正极活性物质的电子导电性。
提高正极片的电解液的吸液量,增加反应界面,减少极化。
非极性物质,葡萄链状物,含水量3-6%,吸油值~300,粒径一般为2-5 μm;主要有普通碳黑、超导碳黑、石墨乳等,在大批量应用时一般选择超导碳黑和石墨乳复配;通常为中性。
●PVDF粘合剂:将钴酸锂、导电剂和铝箔或铝网粘合在一起。
非极性物质,链状物,分子量从300000到3000000不等;吸水后分子量下降,粘性变差。
●NMP:弱极性液体,用来溶解/溶胀PVDF,同时用来稀释浆料。
●正极引线:由铝箔或铝带制成。
1.2负极配方(石墨+导电剂(乙炔黑)+增稠剂(CMC)+粘结剂(SBR)+ 集流体(铜箔))负极材料:94.5%;Super-P:1.0%;SBR:2.25%;CMC:2.25%水:固体物质的重量比为1600:1417.5a)负极黏度控制5000-6000cps(温度25转子3)b)水重量需要适当调节,达到黏度要求为宜;c)特别注意温度湿度对黏度的影响2.正负极混料★石墨:负极活性物质,构成负极反应的主要物质;主要分为天然石墨和人造石墨。
锂离子电池生产工艺

锂离子电池生产工艺
锂离子电池生产工艺
锂离子电池的生产工艺分为三个主要环节:制备负极材料、制备正极材料和组装组件。
1、制备负极材料
制备负极材料的主要工艺流程如下:
(1)锂离子电池的负极材料主要是铅、锌、锰等金属,其制备以溶液成形法为主。
首先,将金属粉末和锂离子混合进行搅拌,得到金属锂溶液;
(2)将锂溶液倒入板材中,使用振动器将其均匀涂敷;
(3)将涂敷的板材入炉,进行变形固化以及表面阴极处理;
(4)现场检验和包装。
2、制备正极材料
制备正极材料的主要工艺流程如下:
(1)正极的主要原料是镁、锰硅混合物,制备正极要遵循一定的烘烤和制作步骤;
(2)将锰硅混合物按照配方计算好后,用混料机混合,混合均匀后进行粉碎、粒度控制,使其符合工艺要求;
(3)将粉碎后的材料倒入喷抛机中,把它们喷抛到锅炉铁板中,形成正极片;
(4)将正极片进行表面烘烤和清洗,以提高电池性能;
(5)现场检验和包装。
3、组装组件
组装组件的主要工艺流程如下:
(1)将负极、正极、分离膜、润湿剂按照一定的标准放入容器中进行组装;
(2)容器配有螺钉,用来固定正极和负极,以防止元件之间的松动,防止短路;
(3)把容器中的组件放入封装机中,按封装标准进行封装;
(4)将封装后的组件发送到充放电测试台,检验其质量,确保其真空度与安全性;
(5)安装电芯,进行综合质量测试;
(6)将组件发送到包装线,进行外观检查和完整性检验,最后进行包装。
锂离子生产工艺流程知识培训

锂离子生产工艺流程知识培训锂离子电池的生产工艺流程涉及多个环节,包括材料处理、电极制备、电池组装和包装等。
以下是一个简要的锂离子电池生产工艺流程:1. 材料准备:- 正负极活性材料:根据电池设计规格,选择合适的正负极活性材料,如锂铁磷酸盐(LiFePO4)或氧化钴锂(LiCoO2)。
- 导电剂:添加导电剂(如碳黑)和粘结剂(如聚合物)到活性材料中,以提高电极的导电性和结构稳定性。
2. 电极制备:- 正极制备:将正极活性材料、导电剂、粘结剂等混合,并涂覆在铝箔上,形成正极片。
- 负极制备:将负极活性材料、导电剂、粘结剂等混合,并涂覆在铜箔上,形成负极片。
3. 电解液配制:- 电解液由溶剂、锂盐和添加剂组成。
常用的溶剂是有机碳酸酯,锂盐通常是六氟磷酸锂(LiPF6)。
- 添加剂可用于提高电解液的稳定性、安全性和电池性能,如添加抑制锂金属析出的抑制剂。
4. 电池组装:- 正负极叠层:将正负极片与隔膜交替叠放,形成正负极叠层结构。
- 注入电解液:将电解液注入正负极叠层,使其完全浸润电极材料,并保持电池内部的湿度均匀分布。
- 封装:将装配好的电极叠层置于电池壳体中,并密封起来,确保电池内部不外泄。
5. 充放电测试:- 对新组装的电池进行充放电测试,检查电池的性能、容量和循环寿命等指标。
6. 包装:- 完成充放电测试后,对合格的电池进行包装,以保护电池并方便运输和销售。
值得注意的是,以上流程仅概述了锂离子电池的基本生产工艺流程。
实际的生产过程可能因不同的厂商、电池类型和规模而有所差异。
在实施生产工艺之前,建议进行详细的研究和培训,并遵循相关的安全操作规程和质量控制标准。
锂离子电池配料

锂离子电池配料
粘度:小①:2500mpas 小②:2400mpas 涂布干粉数: 正极:156.52 kg 负极:64.18 kg 制片标准增重: 正极增重:6.42±0.05g/pcs 负极增重:2.56±0.05g/pcs 容量计算: LiMn2O4占干重比例=144.4681/(144.4681+4.226+2.871+5.009) =92.2681976% LiMn2O4克容量105mah/g 电容量=6.42×92.3%×105mah/g=622.1943mah/g 功率 P=UI=3.7×0.6=2.22wh
锂离子电池配料
一 、正负极原材料: A:正极材料 1、主料:锰酸锂、钴酸锂、镍钴锰酸锂(三元) -晶格置换; 2、导电剂:人造石墨,碳黑,乙炔黑, 微米级:S-0(10E-6),纳米级:SP(10E-9); 3、溶剂-胶体:NMP(甲基吡咯烷酮) 4、粘合剂:PVDF
锂离子电池配料
B:负极材料 1、主料:中科活性碳(石墨); 2、粘结剂与增稠剂:SBR(粘结剂,液体浓 度50%),CMC—羧甲基纤维素稠剂; 3、消泡剂:NMP (甲基吡咯烷酮) 4、溶剂:去离子水(H2O)
①Q=(m/M)×NA×q(e) ②I=Q/t ⇒ I=***mah/g
3、功率计算:
P=UI(U-标称电压3.7V;I-电容量) 三元 国安(LiMn2O4) LiMn2O4 克容量(mah) 150-155 140 105 压实: 3.4-3.5 3.9-4.0 2.9-3.0 例:①锰酸锂克容量(LiMn204) :1×7/7+55×2+16×2=1/181 I=(1/181) ×1.6×10e-19×6.02×10e-23×10e3MA/A÷3600S=147.83mah/g ②6C+xLi++xe-==LixC6
锂电池生产工艺

锂电池生产工艺锂电池生产工艺锂电池是一种先进的能量存储设备,具有高比能量、长寿命、快速充电等优点,被广泛应用于电动车、手机、笔记本电脑等领域。
锂电池的生产工艺是将正极、负极、电解质和隔膜等组件组合起来,在高真空、洁净度高的工作环境下,通过一系列工艺流程制备而成。
下面就详细介绍锂电池生产工艺的具体步骤。
一、制备正极材料正极材料主要由氧化物、钴酸锂、磷酸铁锂等组成,其生产过程分为两个基本步骤:混合和烧结。
首先将正极材料的各个成分按照一定比例混合均匀,再压缩成一定密度的颗粒,最后放入烧结炉中在高温下进行烧结,使得颗粒之间相互熔合,形成均匀的晶粒结构。
二、制备负极材料负极材料主要由石墨、硅和锡等组成。
其生产过程分为混合、预浸和干燥三个环节。
首先将负极材料的各个成分按一定比例混合均匀,再将混合后的材料浸渍在有机溶液中,使其成为一个可输送的浆料,接着进行干燥,将材料干燥成一定的形状和密度。
三、盐溶液制备锂电池中使用的盐溶液主要包括电解质和溶剂两部分。
电解质一般使用的是锂盐,常见的有氯化锂、氟化锂和硫酸锂等,而溶剂则包括聚烯烃、聚碳酸酯、醚酯类和酯类溶剂等。
制备电解液的方法一般是将锂盐和溶剂混合,加热搅拌,使得锂盐完全溶解在溶剂中,形成均匀透明的溶液。
四、隔膜制备锂电池的隔膜是负责隔离正负极的关键组件,其材料主要包含聚烯烃、聚酰亚胺和聚酯等材料。
其生产过程分为两个基本步骤:制备和成型。
首先将材料进行混合均匀,再通过挤压、拉伸等工艺成型成为一定的薄膜结构,最后进行打孔等工艺,使得隔膜具有适当的孔隙大小和分配。
五、组装与封装在锂电池组装过程中,首先要将正极、负极和隔膜等组件按照规定的比例进行堆积组装,同时将电解液注入到电池壳体中。
接着进行封装和组装,即将电池壳体完成密封,使得电解液不会泄漏,同时进行检测和测试保证其质量和可靠性达到要求。
综上所述,锂电池生产工艺涵盖了多个环节,其中每个环节的方法和技术都有一定的特点和要求,需要严格的管理和操作。
锂电池的工艺步骤
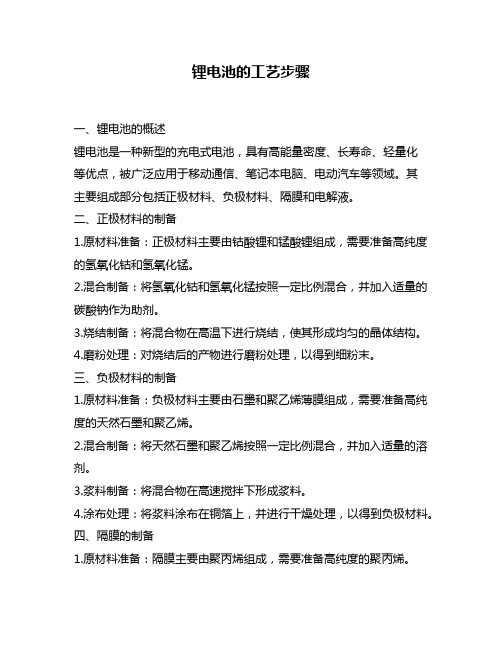
锂电池的工艺步骤一、锂电池的概述锂电池是一种新型的充电式电池,具有高能量密度、长寿命、轻量化等优点,被广泛应用于移动通信、笔记本电脑、电动汽车等领域。
其主要组成部分包括正极材料、负极材料、隔膜和电解液。
二、正极材料的制备1.原材料准备:正极材料主要由钴酸锂和锰酸锂组成,需要准备高纯度的氢氧化钴和氢氧化锰。
2.混合制备:将氢氧化钴和氢氧化锰按照一定比例混合,并加入适量的碳酸钠作为助剂。
3.烧结制备:将混合物在高温下进行烧结,使其形成均匀的晶体结构。
4.磨粉处理:对烧结后的产物进行磨粉处理,以得到细粉末。
三、负极材料的制备1.原材料准备:负极材料主要由石墨和聚乙烯薄膜组成,需要准备高纯度的天然石墨和聚乙烯。
2.混合制备:将天然石墨和聚乙烯按照一定比例混合,并加入适量的溶剂。
3.浆料制备:将混合物在高速搅拌下形成浆料。
4.涂布处理:将浆料涂布在铜箔上,并进行干燥处理,以得到负极材料。
四、隔膜的制备1.原材料准备:隔膜主要由聚丙烯组成,需要准备高纯度的聚丙烯。
2.挤压制备:将聚丙烯加入挤压机中进行挤出,形成薄膜。
3.拉伸处理:对挤出的薄膜进行拉伸处理,以增强其机械强度和导电性能。
五、电解液的制备1.原材料准备:电解液主要由碳酸锂、乙二醇和二甲基碳酸酯组成,需要准备高纯度的原材料。
2.混合制备:将碳酸锂、乙二醇和二甲基碳酸酯按照一定比例混合,并进行搅拌处理。
3.过滤处理:对混合物进行过滤处理,以去除杂质和颗粒。
六、锂电池的组装1.正负极片的组装:将正极片和负极片分别与铜箔和铝箔连接,并在其中加入隔膜。
2.电解液注入:将电解液注入正负极片之间的隙缝中,使其充分浸润。
3.封装处理:将正负极片和电解液封装在金属壳体中,并进行真空密封处理。
七、锂电池的测试1.容量测试:使用恒定电流放电法对锂电池进行容量测试,以确定其额定容量。
2.循环寿命测试:对锂电池进行循环充放电测试,以确定其循环寿命和稳定性。
3.安全性测试:对锂电池进行短路、过充、过放等安全性测试,以确保其安全可靠。
锂离子电池制作工艺

锂离子电池制作工艺
锂离子电池是一种高效、环保、轻便的电池,已经广泛应用于手机、笔记本电脑、电动车等领域。
锂离子电池的制作工艺主要包括原材料准备、正负极材料制备、电解液制备、组装和封装等步骤。
一、原材料准备
1.正负极材料:正极材料通常采用钴酸锂或磷酸铁锂,负极材料通常采用石墨或硅基材料。
2.电解液:锂离子电池的电解液通常由有机溶剂和锂盐组成,有机溶剂可以是碳酸酯类或磷酸酯类,锂盐可以是六氟磷酸锂或硫酸锂等。
3.隔膜:隔膜是将正负两极分开的关键部件,通常采用聚丙烯或聚乙烯等高分子材料制成。
二、正负极材料制备
1.正极材料制备:将钴酸锂或磷酸铁锂与碳酸钠、氧化钴或氧化铁等混合,经过高温煅烧后,形成颗粒状的正极材料。
2.负极材料制备:将石墨或硅基材料与聚丙烯酸或羟丙基甲基纤维素等混合,制成浆料后涂布在铜箔上,经过干燥和压制后形成负极片。
三、电解液制备
1.有机溶剂的准备:将碳酸二甲酯、碳酸二乙酯等有机溶剂加入反应釜中,加入少量锂盐催化剂,在高温高压下反应得到有机溶剂。
2.锂盐的准备:将六氟磷酸锂或硫酸锂等锂盐加入反应釜中,与有机溶剂进行配比和搅拌,得到电解液。
四、组装和封装
1.组装:将正负极片按一定比例叠放在一起,用隔膜将其分开,并注入电解液。
2.封装:将组装好的电池放入壳体中,并进行密封处理。
同时,在壳体上安装保护电路板,以保证电池的安全性和稳定性。
以上就是锂离子电池的制作工艺。
需要注意的是,在制作过程中要严格控制各个环节的质量,确保电池的稳定性和安全性。
同时,还需要不断进行技术创新和改进,以提高电池的性能和使用寿命。
锂离子电池原理及混料配料工艺流程

工 艺 流 程一、 原理1.正极构造LiFePO 4(磷酸铁锂)+导电剂+粘合剂(PVDF)+集流体(铝箔)2.负极构造石墨+导电剂+增稠剂(CMC)+粘结剂(SBR)+ 集流体(铜箔)3.工作原理3.1 充电过程:一个电源给电池充电,此时正极上的电子e 从通过外部电路跑到负极上,正锂离子Li+从正极“跳进”电解液里,“爬过”隔膜上弯弯曲曲的小洞,“游泳”到达负极,与早就跑过来的电子结合在一起。
正极上发生的反应为LiFePO 4→Li 1-x FePO 4+Xli ++Xe(电子)负极上发生的反应为6C+XLi ++Xe →Li x C 63.2 电池放电过程放电有恒流放电和恒阻放电,恒流放电其实是在外电路加一个可以随电压变化而变化的可变电阻,恒阻放电的实质都是在电池正负极加一个电阻让电子通过。
由此可知,只要负极上的电子不能从负极跑到正极,电池就不会放电。
电子和Li+都是同时行动的,方向相同但路不同,放电时,电子从负极经过电子导体跑到正极,锂离子Li+从负极“跳进”电解液里,“爬过”隔膜上弯弯曲曲的小洞,“游泳”到达正极,与早就跑过来的电子结合在一起。
二 工艺流程1、正极极片制备1.1原料的烘干(1)磷酸铁锂:真空烘烤。
(2)导电剂:常压烘烤。
(3)粘合剂:常压烘烤。
1.2浆料搅拌a) 将NMP倒入真空搅拌机中, PVDF加入其中;b) 正极干料平均分四次加入。
c) 真空下高速搅拌,时间为3-5小时;d) 出料准备涂布。
1.3 涂布a) 在精密的涂布机上面把浆料均匀地涂覆在铝箔表面,涂布厚度可以根据不同的要求进行调整。
2、负极极片制备2.1 原料不需要烘干。
2.2 浆料制备a) 纯净水倒入真空搅拌机中。
B) 加CMC,搅拌,完全溶解;c) 加入SBR和去离子水,搅拌60分钟;d) 负极干料分四次平均顺序加入搅拌机中。
e) 高速真空搅拌3-5小时;f) 出料准备涂布2.3 涂布a) 在精密的涂布机上面把浆料均匀地涂覆在铜箔表面,涂布厚度可以根据不同的要求进行调整。
- 1、下载文档前请自行甄别文档内容的完整性,平台不提供额外的编辑、内容补充、找答案等附加服务。
- 2、"仅部分预览"的文档,不可在线预览部分如存在完整性等问题,可反馈申请退款(可完整预览的文档不适用该条件!)。
- 3、如文档侵犯您的权益,请联系客服反馈,我们会尽快为您处理(人工客服工作时间:9:00-18:30)。
1.正负极配方配料过程实际上是将浆料中的各种组成按标准比例混合在一起,调制成浆料,以利于均匀涂布,保证极片的一致性。
配料大致包括五个过程,即:原料的预处理、掺和、浸湿、分散和絮凝。
1.1正极配方(LiCoO2(钴酸锂)+导电剂(乙炔黑)+粘合剂(PVDF)+集流体(铝箔))LiCoO(10μm):93.5%;其它:6.5%如Super-P:4.0%;PVDF761:2.5;2NMP(增加粘结性):固体物质的重量比约为810:1496a) 正极黏度控制6000cps(温度25转子3);b) NMP重量须适当调节,达到黏度要求为宜;c) 特别注意温度湿度对黏度的影响●钴酸锂:正极活性物质,锂离子源,为电池提高锂源。
钴酸锂:非极性物质,不规则形状,粒径D50一般为6-8 μm,含水量≤0.2%,通常为碱性,PH值为10-11左右。
锰酸锂:非极性物质,不规则形状,粒径D50一般为5-7 μm,含水量≤0.2%,通常为弱碱性,PH值为8左右。
●导电剂:提高正极片的导电性,补偿正极活性物质的电子导电性。
提高正极片的电解液的吸液量,增加反应界面,减少极化。
非极性物质,葡萄链状物,含水量3-6%,吸油值~300,粒径一般为2-5 μm;主要有普通碳黑、超导碳黑、石墨乳等,在大批量应用时一般选择超导碳黑和石墨乳复配;通常为中性。
●PVDF粘合剂:将钴酸锂、导电剂和铝箔或铝网粘合在一起。
非极性物质,链状物,分子量从300000到3000000不等;吸水后分子量下降,粘性变差。
●NMP:弱极性液体,用来溶解/溶胀PVDF,同时用来稀释浆料。
●正极引线:由铝箔或铝带制成。
1.2负极配方(石墨+导电剂(乙炔黑)+增稠剂(CMC)+粘结剂(SBR)+ 集流体(铜箔))负极材料:94.5%;Super-P:1.0%;SBR:2.25%;CMC:2.25%水:固体物质的重量比为1600:1417.5a)负极黏度控制5000-6000cps(温度25转子3)b)水重量需要适当调节,达到黏度要求为宜;c)特别注意温度湿度对黏度的影响2.正负极混料★石墨:负极活性物质,构成负极反应的主要物质;主要分为天然石墨和人造石墨。
非极性物质,易被非极性物质污染,易在非极性物质中分散;不易吸水,也不易在水中分散。
被污染的石墨,在水中分散后,容易重新团聚。
一般粒径D50为20μm左右。
颗粒形状多样且多不规则,主要有球形、片状、纤维状等。
★导电剂:提高负极片的导电性,补偿负极活性物质的电子导电性。
提高反应深度及利用率。
防止枝晶的产生。
利用导电材料的吸液能力,提高反应界面,减少极化。
(可根据石墨粒度分布选择加或不加)。
★添加剂:降低不可逆反应,提高粘附力,提高浆料黏度,防止浆料沉淀。
增稠剂/防沉淀剂(CMC):高分子化合物,易溶于水和极性溶剂。
异丙醇:弱极性物质,加入后可减小粘合剂溶液的极性,提高石墨和粘合剂溶液的兼容性;具有强烈的消泡作用;易催化粘合剂网状交链,提高粘结强度。
乙醇:弱极性物质,加入后可减小粘合剂溶液的极性,提高石墨和粘合剂溶液的兼容性;具有强烈的消泡作用;易催化粘合剂线性交链,提高粘结强度(异丙醇和乙醇的作用从本质上讲是一样的,大量生产时可考虑成本因素然后选择添加哪种)。
★水性粘合剂(SBR):将石墨、导电剂、添加剂和铜箔或铜网粘合在一起。
小分子线性链状乳液,极易溶于水和极性溶剂。
增稠剂/防沉淀剂(CMC):高分子化合物,易溶于水和极性溶剂。
★负极引线:由铜箔或镍带制成。
去离子水(或蒸馏水):稀释剂,酌量添加,改变浆料的流动性。
2.1正极混料●原料的掺和:(1)粘合剂的溶解(按标准浓度)及热处理。
(2)钴酸锂和导电剂球磨:使粉料初步混合,钴酸锂和导电剂粘合在一起,提高团聚作用和的导电性。
配成浆料后不会单独分布于粘合剂中,球磨时间一般为2小时左右;为避免混入杂质,通常使用玛瑙球作为球磨介子。
●干粉的分散、浸湿:(1)原理:固体粉末放置在空气中,随着时间的推移,将会吸附部分空气在固体的表面上,液体粘合剂加入后,液体与气体开始争夺固体表面;如果固体与气体吸附力比与液体的吸附力强,液体不能浸湿固体;如果固体与液体吸附力比与气体的吸附力强,液体可以浸湿固体,将气体挤出。
当润湿角≤90度,固体浸湿。
当润湿角>90度,固体不浸湿。
正极材料中的所有组员都能被粘合剂溶液浸湿,所以正极粉料分散相对容易。
(2)分散方法对分散的影响:A、静置法(时间长,效果差,但不损伤材料的原有结构);B、搅拌法;自转或自转加公转(时间短,效果佳,但有可能损伤个别材料的自身结构)。
1、搅拌桨对分散速度的影响。
搅拌桨大致包括蛇形、蝶形、球形、桨形、齿轮形等。
一般蛇形、蝶形、桨型搅拌桨用来对付分散难度大的材料或配料的初始阶段;球形、齿轮形用于分散难度较低的状态,效果佳。
2、搅拌速度对分散速度的影响。
一般说来搅拌速度越高,分散速度越快,但对材料自身结构和对设备的损伤就越大。
3、浓度对分散速度的影响。
通常情况下浆料浓度越小,分散速度越快,但太稀将导致材料的浪费和浆料沉淀的加重。
4、浓度对粘结强度的影响。
浓度越大,柔制强度越大,粘接强度越大;浓度越低,粘接强度越小。
5、真空度对分散速度的影响。
高真空度有利于材料缝隙和表面的气体排出,降低液体吸附难度;材料在完全失重或重力减小的情况下分散均匀的难度将大大降低。
6、温度对分散速度的影响。
适宜的温度下,浆料流动性好、易分散。
太热浆料容易结皮,太冷浆料的流动性将大打折扣。
●稀释。
将浆料调整为合适的浓度,便于涂布。
2.1.1原料的预处理(1)钴酸锂:脱水。
一般用120℃常压烘烤2小时左右。
(2)导电剂:脱水。
一般用200℃常压烘烤2小时左右。
(3)粘合剂:脱水。
一般用120-140℃常压烘烤2小时左右,烘烤温度视分子量的大小决定。
(4) NMP:脱水。
使用干燥分子筛脱水或采用特殊取料设施,直接使用。
2.1.2物料球磨a)将LiCoOSuper-P倒入料桶,同时加入磨球(干料:磨球=1:1),在滚瓶及上进行球磨,转2速控制在60rmp以上;b)4小时结束,过筛分离出球磨;2.1.3操作步骤a) 将NMP倒入动力混合机(100L)至80℃,称取PVDF加入其中,开机;参数设置:转速25±2转/分,搅拌115-125分钟;b) 接通冷却系统,将已经磨号的正极干料平均分四次加入,每次间隔28-32分钟,第三次加料视材料需要添加NMP,第四次加料后加入NMP;动力混合机参数设置:转速为20±2转/分c) 第四次加料30±2分钟后进行高速搅拌,时间为480±10分钟;动力混合机参数设置:公转为30±2转/分,自转为25±2转/分;d)真空混合:将动力混合机接上真空,保持真空度为-0.09Mpa,搅拌30±2分钟;动力混合机参数设置:公转为10±2分钟,自转为8±2转/分e)取250-300毫升浆料,使用黏度计测量黏度;测试条件:转子号5,转速12或30rpm,温度范围25℃;f)将正极料从动力混合机中取出进行胶体磨、过筛,同时在不锈钢盆上贴上标识,与拉浆设备操作员交接后可流入拉浆作业工序。
2.1.4注意事项a) 完成,清理机器设备及工作环境;b) 操作机器时,需注意安全,避免砸伤头部。
2.2负极混料2.2.1原料的预处理:(1)石墨:A、混合,使原料均匀化,提高一致性。
B、300~400℃常压烘烤,除去表面油性物质,提高与水性粘合剂的相容能力,修圆石墨表面棱角(有些材料为保持表面特性,不允许烘烤,否则效能降低)。
(2)水性粘合剂:适当稀释,提高分散能力。
★掺和、浸湿和分散:(1)石墨与粘合剂溶液极性不同,不易分散。
(2)可先用醇水溶液将石墨初步润湿,再与粘合剂溶液混合。
(3)应适当降低搅拌浓度,提高分散性。
(4)分散过程为减少极性物与非极性物距离,提高势能或表面能,所以为吸热反应,搅拌时总体温度有所下降。
如条件允许应该适当升高搅拌温度,使吸热变得容易,同时提高流动性,降低分散难度。
(5)搅拌过程如加入真空脱气过程,排除气体,促进固-液吸附,效果更佳。
(6)分散原理、分散方法同正极配料中的相关内容★稀释:将浆料调整为合适的浓度,便于涂布。
2.2.2物料球磨将负极和Super-P倒入料桶同时加入球磨(干料:磨球=1:1.2)在滚瓶及上进行球磨,转速控制在60rmp以上;4小时结束,过筛分离出球磨;2.2.3操作步骤a) 纯净水加热至至80℃倒入动力混合机(2L)b)加CMC,搅拌60±2分钟;动力混合机参数设置:公转为25±2分钟,自转为15±2转/分;c) 加入SBR和去离子水,搅拌60±2分钟;动力混合机参数设置:公转为30±2分钟,自转为20±2转/分;d) 负极干料分四次平均顺序加入,加料的同时加入纯净水,每次间隔28-32分钟;动力混合机参数设置:公转为20±2转/分,自转为15±2转/分;e) 第四次加料30±2分钟后进行高速搅拌,时间为480±10分钟;动力混合机参数设置:公转为30±2转/分,自转为25±2转/分;f)真空混合:将动力混合机接上真空,保持真空度为-0.09到0.10Mpa,搅拌30±2分钟;动力混合机参数设置:公转为10±2分钟,自转为8±2转/分g)取500毫升浆料,使用黏度计测量黏度;测试条件:转子号5,转速30rpm,温度范围25℃;h)将负极料从动力混合机中取出进行磨料、过筛,同时在不锈钢盆上贴上标识,与拉浆设备操作员交接后可流入拉浆作业工序。
2.2.4注意事项a) 完成,清理机器设备及工作环境;b) 操作机器时,需注意安全,避免砸伤头部。
★配料注意事项:1、防止混入其它杂质;2、防止浆料飞溅;3、浆料的浓度(固含量)应从高往低逐渐调整,以免增加麻烦;4、在搅拌的间歇过程中要注意刮边和刮底,确保分散均匀;5、浆料不宜长时间搁置,以免沉淀或均匀性降低;6、需烘烤的物料必须密封冷却之后方可以加入,以免组分材料性质变化;7、搅拌时间的长短以设备性能、材料加入量为主;搅拌桨的使用以浆料分散难度进行更换,无法更换的可将转速由慢到快进行调整,以免损伤设备;8、出料前对浆料进行过筛,除去大颗粒以防涂布时造成断带;9、对配料人员要加强培训,确保其掌握专业知识,以免酿成大祸;10、配料的关键在于分散均匀,掌握该中心,其它方式可自行调整。
3.电池的制作3.1极片尺寸3.2拉浆工艺a)集流体尺寸正极(铝箔),间歇涂布;负极(铜箔),间歇涂布b)拉浆重量要求3.3裁片(正负极拉浆后进行以下工序):裁大片裁小片称片(配片)烘烤轧片极耳焊接3.4轧片要求电极压片后厚度(mm)压片后长度(mm)正极0.125-0.145 362-365负极0.125-0.145 400-4033.5配片方案序号正极重量(克)负极重量(克)备注1 5.49-6.01 2.83-2.86 正极可以和重1-2个档次的负极进行配片2 6.02-6.09 2.87-2.903 6.10-6.17 2.91-2.944 6.18-6.25 2.95-2.985 6.26-6.33 2.99-3.016 6.34-6.41 3.02-3.053.6极片烘烤电极温度时间(小时)真空度正极120±5 6-10 ≦-0.09Mpa负极110±5 6-10 ≦-0.09Mpa备注:真空系统的真空度为-0.095-0.10Mpa保护气为高纯氮气,气体气压大于0.5Mpa3.7极耳制作正极极耳上盖组合超声波焊接, 铝条边缘与极片边缘平齐负极镍条直接用点焊机点焊,要求点焊数为8个点,镍条右侧与负极片右侧对齐,镍条末端与极片边缘平齐3.8隔膜尺寸3.9卷针宽度3.10压芯电池卷绕后,先在电芯底部贴上24mm的通明胶带,再用压平机冷压2次;3.11电芯入壳前要求胶纸镍条。