乙苯、苯乙烯精馏塔设备选型
乙苯制苯乙烯
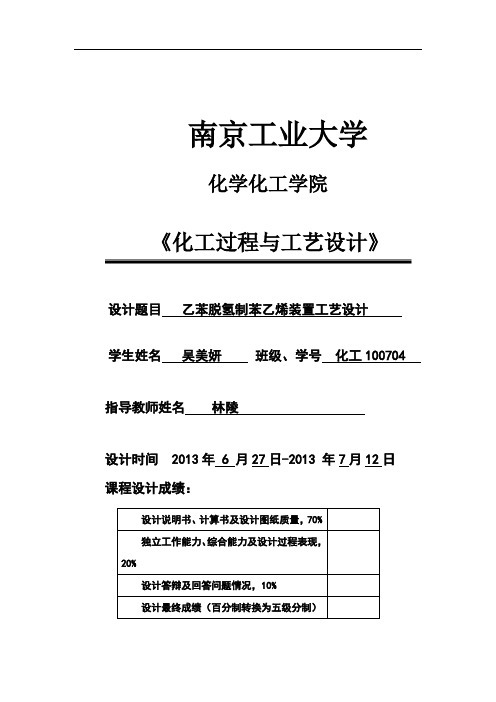
南京工业大学化学化工学院《化工过程与工艺设计》设计题目乙苯脱氢制苯乙烯装置工艺设计学生姓名吴美妍班级、学号化工100704 指导教师姓名林陵设计时间 2013年 6 月27日-2013 年7月12日课程设计成绩:指导教师签字目录第一部分设计说明书前言·······················错误!未定义书签。
第一章概述····················错误!未定义书签。
工艺路线与产品················错误!未定义书签。
···················错误!未定义书签。
···················错误!未定义书签。
···················错误!未定义书签。
精馏塔设计方案的选定

一、引言精馏塔是化工生产中常见的一种分离设备,通过利用不同组分在液相和气相之间的传质传热差异,实现物质的分离纯化。
精馏塔的设计方案的选定对于生产过程的效率和质量具有重要影响。
本文将从选择塔型、确定塔盘数以及优化操作参数三个方面,介绍精馏塔设计方案的选定。
二、选择塔型精馏塔的塔型选择是设计中的核心问题之一。
常见的精馏塔塔型包括板式塔、填料塔和结构塔。
不同塔型的选择将影响塔的装填方式、气液分布和传质效果。
1. 板式塔板式塔是将塔内空间分为多个水平的塔盘,用来支承塔板。
塔板可分为穿孔板、泡沫塔板和波纹塔板。
穿孔板适用于低液速和正常气速的流体,泡沫塔板适用于气速较高的流体,而波纹塔板适用于高液速和低气速的流体。
根据具体的操作条件和物料属性,选取适宜的塔盘型式。
2. 填料塔填料塔是通过将填料充满整个塔体来提供大量的表面积,增加气液接触,从而增强传质效果。
常用填料有环形填料、球形填料和片状填料等。
根据塔的高度和具体的应用要求,选择合适的填料类型。
3. 结构塔结构塔通过设置各种结构件,如槽板、静雾层和液下分布器等,来提高气液接触效果。
结构塔的选择需考虑到操作远程和疏水性等因素。
在特殊的工艺要求下,结构塔是一种较好的选择。
三、确定塔盘数塔盘数的确定会直接影响到塔的高度和设备投资。
为保证精馏的有效塔盘数,需要考虑到塔盘间的液体波动度、气液分布和传质效果等因素。
1. 传质传热效果传质传热效果是决定有效塔盘数的关键因素之一。
在设计中,需通过实验和计算确定传质传热的塔效,并据此确定有效塔盘数。
2. 液波动度液波动度是塔内液面上下波动的幅度,对有效塔盘数有一定的影响。
一般来说,液波动度较大时,需要增加塔盘数以提高塔的分离效果。
3. 落液区间精馏塔的下部是用于落液的区间,该区间的长度也会影响到有效塔盘数。
通常情况下,落液区间应满足液滴在下部区间内平均停留数秒的要求,并根据设计手册的要求确定有效塔盘数。
四、优化操作参数精馏塔设计方案的选定还要考虑到操作参数的优化。
苯-乙苯常压精馏塔设计

5塔板工艺尺寸计算- - - - - - - - - - - -- - - - - - - - - - - -- - - - -12
5.1塔径计算- - - - - - - - - - - -- - - - - - -- - -- - - - - - -- - - - -12
do——筛孔直径,m
D——塔径,m
uo'——液体通过降液体系的速度,m/s
ev——液沫夹带量,kg液/kg气
R——回流比
Vs——气体体积流量,m/s
Rmin——最小回流比
Wc——边缘无效区宽度,m
HT——塔板间距,m
K——稳定系数
H——板式塔高度,m
Hd——降液管内清夜层高度,m
HF——进料处塔板间距,m
塔型的选择:
本设计中采用筛板塔。筛板塔的优点是结构比浮阀塔更简单,易于加工,造价约为泡罩塔的60%,为浮阀塔的80%左右。处理能力大,比同塔径的泡罩塔可增加10~15%。塔板效率高,比泡罩塔高15%左右。压降较低。缺点是塔板安装的水平度要求较高,否则气液接触不匀。
设计的依据与技术来源:
本设计依据于精馏的原理(即利用液体混合物中各组分挥发度的不同并借助于多次部分汽化和部分冷凝使轻重组分分离),并在满足工艺和操作的要求,满足经济上的要求,保证生产安全的基础上,对设计任务进行分析并做出理论计算。
9辅助设备的计算及选型- - - - - - - - - - - - - - - - - - - - - - - - - -26
9.1、裙座- - - - - - - - - - - - - - - - - - - - - - - - - - - - - - -- - - - -26
乙苯苯乙烯装置简介和重点部位及设备
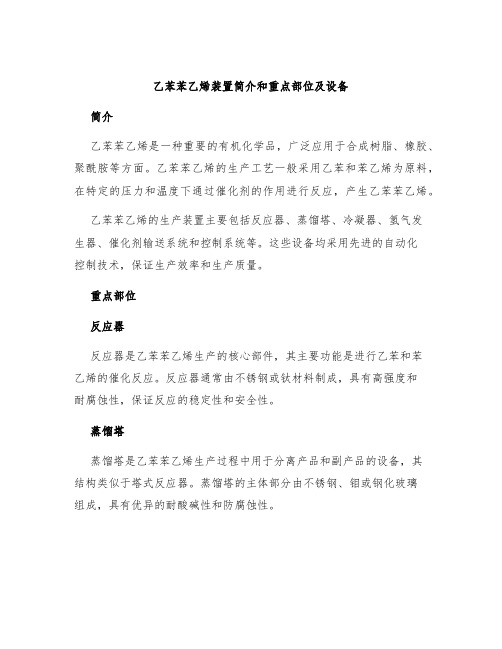
乙苯苯乙烯装置简介和重点部位及设备简介乙苯苯乙烯是一种重要的有机化学品,广泛应用于合成树脂、橡胶、聚酰胺等方面。
乙苯苯乙烯的生产工艺一般采用乙苯和苯乙烯为原料,在特定的压力和温度下通过催化剂的作用进行反应,产生乙苯苯乙烯。
乙苯苯乙烯的生产装置主要包括反应器、蒸馏塔、冷凝器、氢气发生器、催化剂输送系统和控制系统等。
这些设备均采用先进的自动化控制技术,保证生产效率和生产质量。
重点部位反应器反应器是乙苯苯乙烯生产的核心部件,其主要功能是进行乙苯和苯乙烯的催化反应。
反应器通常由不锈钢或钛材料制成,具有高强度和耐腐蚀性,保证反应的稳定性和安全性。
蒸馏塔蒸馏塔是乙苯苯乙烯生产过程中用于分离产品和副产品的设备,其结构类似于塔式反应器。
蒸馏塔的主体部分由不锈钢、钼或钢化玻璃组成,具有优异的耐酸碱性和防腐蚀性。
冷凝器主要用于将反应产生的气体冷却成液态,便于进一步处理和收集。
冷凝器通常采用板式、管壳式或环形式等不同的结构形式,具有高效的冷却效果和低能耗。
氢气发生器氢气发生器是乙苯苯乙烯生产过程中必须的设备之一,其主要功能是将乙苯和苯乙烯中的杂质和催化剂去除,保障反应系统稳定、安全。
氢气发生器的最新型号采用了先进的膜技术,能够保证高效的反应速率和较小的能耗。
设备催化剂输送系统催化剂输送系统是乙苯苯乙烯生产过程中的重要设备之一。
催化剂是主要的反应物之一,其精准输送对于反应的催化速率和品质影响极大。
催化剂输送系统采用自动化控制技术,能够监控催化剂的输送精度,确保反应系统的稳定性和安全性。
控制系统控制系统是乙苯苯乙烯生产过程中的核心设备之一,主要包括PLC、变频器等。
该系统利用先进的仪表和自动化控制技术,对反应温度、压力、流量等参数进行精准监控和控制,确保反应系统的稳定性和安全性。
同时,控制系统也能够实现数据采集和分析,为工艺优化和质量管控提供有力的支持。
乙苯苯乙烯装置是一套复杂的生产设备系统,由多个部件相互配合完成反应、分离、处理等工艺过程。
乙基苯-苯乙烯精馏塔设计

乙基苯-苯乙烯精馏塔是用于分离乙基苯和苯乙烯的设备,下面是一般的设计步骤:
1. 确定馏分需求:首先需要明确产品要求和馏分纯度,例如乙基苯和苯乙烯的纯度要求。
2. 确定操作压力:根据物料的性质和工艺要求,选择合适的操作压力。
通常情况下,较低的操作压力可以提高苯乙烯的收率,但也会增加设备成本和操作难度。
3. 确定塔的类型:根据馏分过程的要求,选择合适的塔类型。
常见的选择包括板式塔和填料塔。
填料塔通常适用于高液体负荷和较大的塔径,而板式塔适用于较低的液体负荷和较小的塔径。
4. 确定塔内部组件:根据塔的类型和操作要求,选择合适的塔板或填料。
对于填料塔,选择具有良好质量传递和液体分布性能的填料材料。
对于板式塔,选择合适的塔板类型和开孔面积,以满足分离要求。
5. 进行热量平衡计算:根据进料和产品的物料性质,计算出所需的加热蒸汽和冷凝水量,以实现适当的回流比和塔顶温度。
6. 进行塔的设计计算:根据物料的性质、操作压力和分离要求,进
行塔的设计计算。
这包括确定塔径、塔高、塔板数目或填料高度以及其他塔内部组件的具体参数。
7. 进行塔的模拟和优化:使用流程模拟软件进行塔的模拟和优化,以验证设计参数的合理性,并进一步优化操作条件和设备配置。
8. 进行塔的机械设计:根据设计参数和机械强度要求,进行塔的机械设计,包括塔壳厚度、支撑结构和附件的选择等。
9. 进行安全和环保考虑:在设计过程中,要考虑安全和环保因素,确保塔的运行安全可靠,并满足相关的环境保护要求。
请注意,乙基苯-苯乙烯精馏塔的设计涉及复杂的化工工艺和设备工程知识,建议在实际设计中寻求专业工程师的帮助和指导。
精馏塔的设计及选型

精馏塔的设计及选型目录精馏塔的设计及选型 (1)目录 (1)1设计概述 (1)1.1工艺条件 (1)1.2设计方案的确定 (1)2塔体设计计算 (3)2.1有关物性数据 (3)2.2物料衡算 (6)2.3塔板数的确定 (6)2.4精馏塔的工艺条件及相关物性数据 (10)2.5塔体工艺尺寸的设计计算 (13)2.6塔板工艺尺寸的设计计算 (17)2.7塔板流体力学验算 (21)2.8负荷性能图 (25)2.9精馏塔接管尺寸计算 (31)3精馏塔辅助设备的设计和选型 (36)3.1原料预热器的设计 (36)3.2回流冷凝器的设计和选型 (39)3.3釜塔再沸器的设计和选型 (44)3.4泵的选择 (47)3.5筒体与封头 (48)1设计概述1.1工艺条件(1)生产能力:2836.1kg/d(料液)(2)工作日:250天,每天4小时连续运行(3)原料组成:35.12%丙酮,64.52%水,杂质0.35%,由于杂质含量较小且不会和丙酮一起蒸馏出去,所以可以忽略。
所以此母液可以视为仅含丙酮和水两种成分,其质量组成为:35.12%丙酮,水64.88%(下同)(4)产品组成:馏出液99%丙酮溶液,回收率为90%,由此可知塔釜残液中丙酮含量不得高于5.16%即每天生产99%的丙酮905.54kg。
(5)进料温度:泡点(6)加热方式:间接蒸汽加热(7)塔顶压力:常压(8)进料热状态:泡点(9)回流比:自选(10)加热蒸气压力:0.5MPa(表压)(11)单板压降≤0.7kPa1.2设计方案的确定(1)、精馏方式及流程:在本设计中所涉及的浓度范围内,丙酮和水的挥发度相差比较大,容易分离,且丙酮和水在操作条件下均为非热敏性物质,因此选用常压精馏,并采取连续精馏方式。
母液经过换热器由塔底采出液预热到泡点,在连续进入精馏塔内,塔顶蒸汽经过塔顶冷凝器冷凝后,大部分连续采出,采出部分经冷却器后进入储罐内备用,少部分进行回流;塔底液一部分经过塔釜再沸器气化后回到塔底,一部分连续采出,采出部分可用于给原料液预热。
苯乙苯精馏塔工艺设计与塔顶冷凝器选型设计

分类号: TQ051.8 单位代码: 108密级:一般学号: 2305024026 本科毕业论文(设计)题目:苯-乙苯精馏塔工艺设计与塔顶冷凝器选型设计专业:化学工程与工艺姓名:刘朋指导教师:张理平职称:教授答辩日期:二00九年六月六日目录前言 - 0 -第一章设计任务书 - 1 -1.1 设计题目 ......................................................- 1 - 1.2 设计要求 ......................................................- 1 -1.3 主要物性数据 ..................................................- 1 - 第二章工艺计算 - 3 -2.1 物料衡算 ........................................................................... ....................................- 3 -2.2 相图的绘制 .......................................................................... .................................- 4 -2.3回流比的确定2.4理论塔板数的计算2.5实际塔板数确定2.5.1全塔效率 ET2.5.2实际板数2.6 塔的工艺条件及物性数据计算 ....................................- 7 -2.6.1操作压强 .................................................- 7 -2.6.2板间距的选择和塔径的初步确定 .............................- 8 -2.6.3塔板结构2.6.4塔板的校核2.6.4.1精馏段塔板的校核2.6.4.2提馏段塔板的校核2.6.5塔板负荷性能图2.7设计结果一览表第三章塔的附属设备设计 3.1冷凝器的设计 .................................................- 11 -3.1.1热负荷3.1.2冷凝水出口温度3.1.3流动空间及流速的确定3.1.4有效平均温差及传热面积3.2 初选换热器的规格 ....................................................................... ......................- 12 -3.3 换热器的验算 .................................................- 16 -3.3.1 总传热系数 K o 的验算 ....................................- 16 -3.3.2 计算压强降 .............................................- 18 - 3.3.3 计算壳程压力降 .........................................- 18 -3.3.4 选型结果 ...............................................- 19 - 参考文献 - 30 -主要符号说明 - 31 -谢辞 - 32 -前言塔设备是化工、石油化工和炼油等生产中最重要的设备之一,他可以使气(或汽)或液液两相紧密接触,达到相际传质及传热的目的。
(化工安全)乙苯、苯乙烯装置简介和重点部位及设备
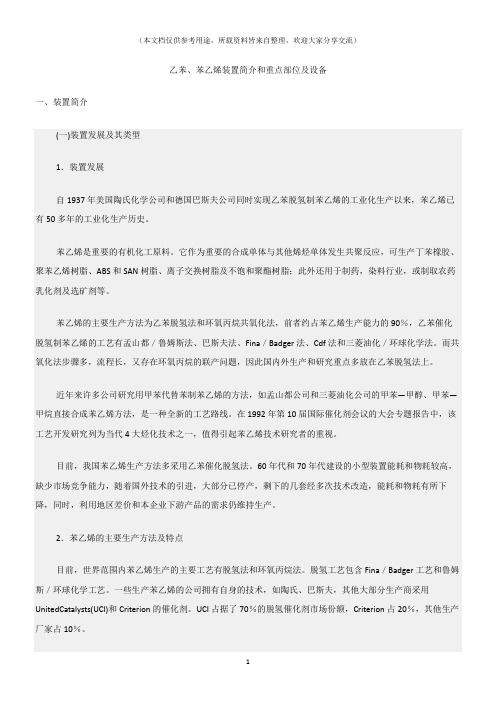
乙苯、苯乙烯装置简介和重点部位及设备一、装置简介(一)装置发展及其类型1.装置发展自1937年美国陶氏化学公司和德国巴斯夫公司同时实现乙苯脱氢制苯乙烯的工业化生产以来,苯乙烯已有50多年的工业化生产历史。
苯乙烯是重要的有机化工原料。
它作为重要的合成单体与其他烯烃单体发生共聚反应,可生产丁苯橡胶、聚苯乙烯树脂、ABS和SAN树脂、离子交换树脂及不饱和聚酯树脂;此外还用于制药,染料行业,或制取农药乳化剂及选矿剂等。
苯乙烯的主要生产方法为乙苯脱氢法和环氧丙烷共氧化法,前者约占苯乙烯生产能力的90%,乙苯催化脱氢制苯乙烯的工艺有孟山都/鲁姆斯法、巴斯夫法、Fina/Badger法、Cdf法和三菱油化/环球化学法。
而共氧化法步骤多,流程长,又存在环氧丙烷的联产问题,因此国内外生产和研究重点多放在乙苯脱氢法上。
近年来许多公司研究用甲苯代替苯制苯乙烯的方法,如孟山都公司和三菱油化公司的甲苯—甲醇、甲苯—甲烷直接合成苯乙烯方法,是一种全新的工艺路线。
在1992年第10届国际催化剂会议的大会专题报告中,该工艺开发研究列为当代4大烃化技术之一,值得引起苯乙烯技术研究者的重视。
目前,我国苯乙烯生产方法多采用乙苯催化脱氢法。
60年代和70年代建设的小型装置能耗和物耗较高,缺少市场竞争能力,随着国外技术的引进,大部分已停产,剩下的几套经多次技术改造,能耗和物耗有所下降,同时,利用地区差价和本企业下游产品的需求仍维持生产。
2.苯乙烯的主要生产方法及特点目前,世界范围内苯乙烯生产的主要工艺有脱氢法和环氧丙烷法。
脱氢工艺包含Fina/Badger工艺和鲁姆斯/环球化学工艺。
一些生产苯乙烯的公司拥有自身的技术,如陶氏、巴斯夫,其他大部分生产商采用UnitedCatalysts(UCl)和Criterion的催化剂。
UCI占据了70%的脱氢催化剂市场份额,Criterion占20%,其他生产厂家占10%。
在乙苯脱氢制苯乙烯的工艺技术方面,除德国巴斯夫公司外,各家外商技术基本相同,大都是采用高真空绝热脱氢反应和反应热能回收技术,蒸馏都是真空高效填料塔技术(EB/SN分离塔),各项经济指标大体相同。
苯乙烯精馏操作指南
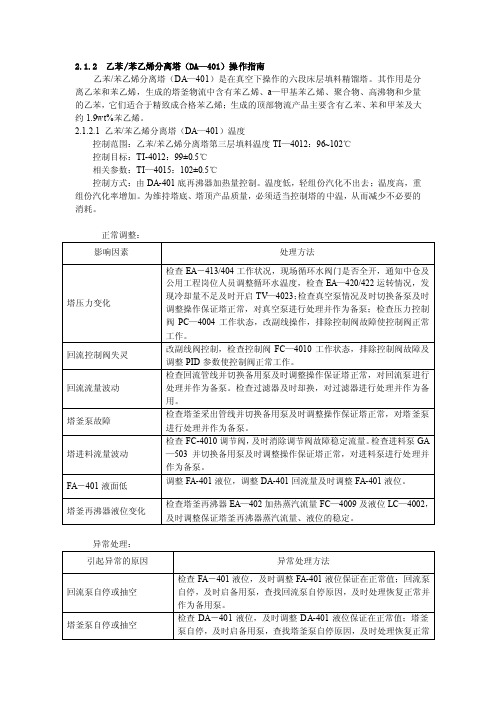
2.1.2 乙苯/苯乙烯分离塔(DA—401)操作指南乙苯/苯乙烯分离塔(DA—401)是在真空下操作的六段床层填料精馏塔。
其作用是分离乙苯和苯乙烯,生成的塔釜物流中含有苯乙烯、a—甲基苯乙烯、聚合物、高沸物和少量的乙苯,它们适合于精致成合格苯乙烯;生成的顶部物流产品主要含有乙苯、苯和甲苯及大约1.9wt%苯乙烯。
2.1.2.1 乙苯/苯乙烯分离塔(DA—401)温度控制范围:乙苯/苯乙烯分离塔第三层填料温度TI—4012:96~102℃控制目标:TI-4012:99±0.5℃相关参数:TI—4015:102±0.5℃控制方式:由DA-401底再沸器加热量控制。
温度低,轻组份汽化不出去;温度高,重组份汽化率增加。
为维持塔底、塔顶产品质量,必须适当控制塔的中温,从而减少不必要的消耗。
正常调整:异常处理:2.1.2.2 乙苯/苯乙烯分离塔(DA—401)加热量控制范围:再沸器蒸汽流量FC—4009:10~18t/h控制目标:FC—4009:16.5±0.5t/h控制方式:再沸器通过控制蒸汽凝液液位来达到加热塔釜物流的目的。
正常调整:正常时再沸器液位LC—4002与再沸器蒸汽流量FC—4009串级进行控制,当出现波动时,通过手动控制LC—4002阀位来调节EA—402再沸器液位。
异常处理:控制范围:DA-401底液面:20~90%控制目标:LC-4001:50±5%控制方式:由塔底液外送流量FC—4002与DA-401底液面LC—4001串级控制。
液面过高将会造成携带甚至冲塔现象,液面过低易造成塔底泵抽空,以致损坏设备。
正常调整:正常时通过调整LC—4001液位的设定值来保证塔釜液位的稳定,在出现异常时通过手动调整FC—4002流量来控制塔釜液位。
2.1.2.4乙苯/苯乙烯分离塔(DA—401)塔压控制范围:0.0233~0.035MpaA控制目标:0.0247 MpaA控制方式:塔的压力由压力调节器PC—4004自动按目标值进行控制,抽真空的动力由液环真空泵GB—401提供。
精馏塔的设计及选型

精馏塔的设计及选型精馏塔是一种用于分离混合物中各成分的设备,主要应用于化工、石油和制药等工业领域。
正确的设计和选型对于实现有效的分离和提高生产效率至关重要。
以下是精馏塔设计及选型的一般步骤和考虑因素。
1.确定物料的组成和性质:了解待分离混合物的组成和性质是进行精馏塔设计和选型的第一步。
这包括成分的相对量、沸点、密度、粘度、腐蚀性等物理和化学属性。
2.确定分离效果要求:根据分离效果要求,确定需要达到的纯度和回收率。
这将影响塔的设计和操作参数的选择。
3.选择塔的类型:根据待分离混合物的性质和要求,选择适合的精馏塔类型。
常见的类型包括板式塔、填料塔和结构塔等。
-板式塔:采用一系列平行的水平板作为分离装置。
适用于低流量、需高纯度产物的应用。
-填料塔:内部填充着填料颗粒,增加了接触面积和传质效果。
适用于高流量、需较高分离效果的应用。
-结构塔:能够同时进行提馏和萃取操作。
适用于需要一次完成多个分离过程的应用。
4.确定操作参数:根据混合物组成和性质以及分离效果要求,确定适当的操作参数,如温度、压力、进料量和塔底回流比等。
5.确定塔的尺寸和规格:根据分离效果要求、操作参数和生产能力,确定塔的尺寸和规格。
这包括塔的高度、直径、板数(或填料层数)等。
6.材料选择:根据待处理混合物的化学性质、温度和压力等条件,选择合适的材料以防止腐蚀和泄漏。
常见的材料包括不锈钢、碳钢和玻璃钢等。
7.能耗和经济性考虑:在设计和选型时,需要考虑能耗和经济性。
选择合适的操作参数和塔结构,以提高分离效率和降低能耗,并综合考虑成本因素。
8.安全性考虑:在设计和选型时,需要考虑安全性。
选择适当的压力容器等级,并确保设备具有良好的密封性和安全措施。
9.考虑后期维护和清洁:在设计和选型时,应考虑后期的维护和清洁工作。
选择易于维护和清洁的塔结构和材料,以减少维护成本和工作量。
最后,精馏塔的设计和选型是一个复杂的过程,需要综合考虑多个因素,如物料性质、分离效果要求、生产能力、经济性和安全性等。
乙苯-苯乙烯精馏塔的设计报告

乙苯-苯乙烯精馏塔的设计报告1.设计要求:用一连续精馏塔分离苯、甲苯、乙苯及苯乙烯的混合物,其组成分别为0.04、0.06、0.5和0.4,要求塔顶产品中苯乙烯≤0.05,塔底产品中乙苯≤0.25。
已知泡点进料,操作回流比为4。
试完成上述分离过程的流程模拟,并确定相关操作参数(进料位置、总板数、操作压力等),并完成相应设计报告。
热力学方法采用PR方程。
2 进料参数:泡点进料。
组分苯甲苯乙苯苯乙烯组成0.04 0.06 0.5 0.43 首先利用Aspen中的DSTWU模块进行分离模拟,采用PENG-ROB方程,得到如下所示结果简捷计算结果与塔板的回流数,确定回流比为4,实际上是最小回流比的1.2倍。
选择依据如下:做回流比随理论塔板数变化表,合理的理论板数应该在曲线斜率绝对值较小的区域内选择。
结论:采用4为回流比,实际板数为24,进料板位置是17.初步分离效果如下所示可以看出,塔顶的苯乙烯的摩尔分率为0.04小于0.05,塔底的乙苯的摩尔分率为0.247小于0.25,也达到了分离要求。
塔顶冷凝器和塔底再沸器的操作压力的选择:一般来说,塔顶冷凝器使用循环水来冷却是非常经济的,所以要求塔顶的出料温度需要达到一定的要求。
由于冷凝器的压力越高,塔顶的温度越高,当操作压力为9kpa的时候,塔顶的出料温度为51.85℃。
塔底再沸器的操作压力选择.塔底再沸器一般采用饱和蒸汽加热,由于塔底再沸器的温度随着操作压力的升高而升高,当操作压力为16kpa时,塔底的出料温度为85摄氏度,可以采用绝对压力为57.875kpa,温度为85℃的饱和蒸汽加热,所以选择再沸器的操作压力为16kpa.此时的结果是如图所示。
至此,初步确定操作参数如下:.分离效果如图所示回流比R 实际板数 进料板 塔顶冷凝器压力 塔底再沸器压力 425189kpa16kpa下面过程是用RadFrac模块对上述过程进行严格和验证。
下面是在RadFrac模块中输入的数据和计算结果这个是在逐板压降为0.3kpa的情况下得出的计算结果(16-9/24 ),实际的分离效果.如图所示。
乙苯-苯乙烯精馏塔设计
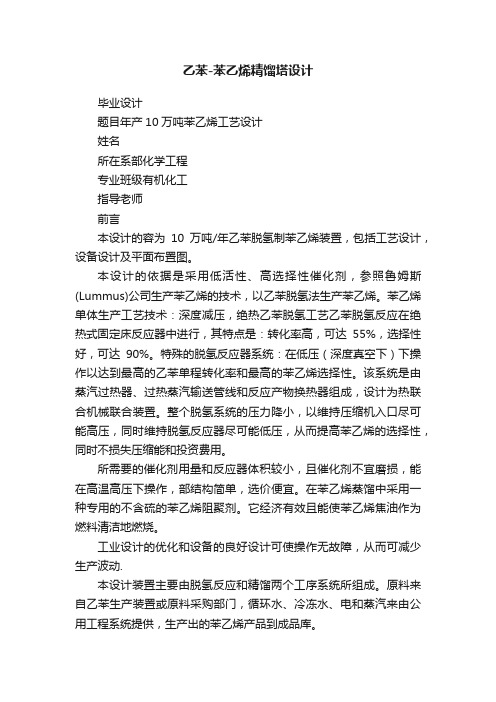
乙苯-苯乙烯精馏塔设计毕业设计题目年产10万吨苯乙烯工艺设计姓名所在系部化学工程专业班级有机化工指导老师前言本设计的容为10万吨/年乙苯脱氢制苯乙烯装置,包括工艺设计,设备设计及平面布置图。
本设计的依据是采用低活性、高选择性催化剂,参照鲁姆斯(Lummus)公司生产苯乙烯的技术,以乙苯脱氢法生产苯乙烯。
苯乙烯单体生产工艺技术:深度减压,绝热乙苯脱氢工艺乙苯脱氢反应在绝热式固定床反应器中进行,其特点是:转化率高,可达55%,选择性好,可达90%。
特殊的脱氢反应器系统:在低压(深度真空下)下操作以达到最高的乙苯单程转化率和最高的苯乙烯选择性。
该系统是由蒸汽过热器、过热蒸汽输送管线和反应产物换热器组成,设计为热联合机械联合装置。
整个脱氢系统的压力降小,以维持压缩机入口尽可能高压,同时维持脱氢反应器尽可能低压,从而提高苯乙烯的选择性,同时不损失压缩能和投资费用。
所需要的催化剂用量和反应器体积较小,且催化剂不宜磨损,能在高温高压下操作,部结构简单,选价便宜。
在苯乙烯蒸馏中采用一种专用的不含硫的苯乙烯阻聚剂。
它经济有效且能使苯乙烯焦油作为燃料清洁地燃烧。
工业设计的优化和设备的良好设计可使操作无故障,从而可减少生产波动.本设计装置主要由脱氢反应和精馏两个工序系统所组成。
原料来自乙苯生产装置或原料采购部门,循环水、冷冻水、电和蒸汽来由公用工程系统提供,生产出的苯乙烯产品到成品库。
此设计过程中,为了计算方便,忽略了一些计算过程,故有一定的误差,另由于计算时间比较仓促,有些问题不能够直接解决。
设计中有不少错误之处,请指导老师予以批评指正,多提出宝贵意见。
苯乙烯设计任务书一、设计题目:年产10万吨苯乙烯的生产工艺设计二、设计原始条件:2、操作条件:年工作日:300天,每天24小时,乙苯总转化率为55%乙苯损失量为纯乙苯投料量为4.66%配料比:原料烃/水蒸汽=1/2.6(质量比)温度T:第一反应器进口温度630℃,出口温度580℃第二反应器进口温度630℃,出口温度600℃压力P:床层平均操作压力1.5 * 105 Pa(绝)3、选择性:C8H10→C8H8+H2 (1)C8H10→C6H6+C2H4 (2)C8H10+H2→C7H8+CH4 (3)1、2、3(1)90%(2)3%(3)7%4、5、6(1)92%(2)3%(3)5%4、催化剂条件:(1)采用11#氧化铁催化剂,d=3mm,h=13mm (2)允许通入乙苯空速为:(0.5~0.9)Nm3乙苯/(m3Cat.h) (3)=1050kg/m3 =1500kg/m35、参考数据:(1)反应器直径D=2 m(2)取热损失为反应热为4%(3)k=exp(11.281-2545/RT)(4)K=exp(15.344-14656.5734/T)(5)Cat的有效系数η1=0.7 η2=0.667(6)填料情况:取瓷环为25×25的拉西环,所填高度为250mm,锥形高度为250mm,锥角取900(7)压力:第一反应器进口压力为1.8 * 105 Pa,出口压力为1.2 * 105 Pa,平均压力为1.5 * 105 Pa,压降ΔP=0.6 * 105 Pa。
推荐-乙苯、苯乙烯装置简介和重点部位及设备
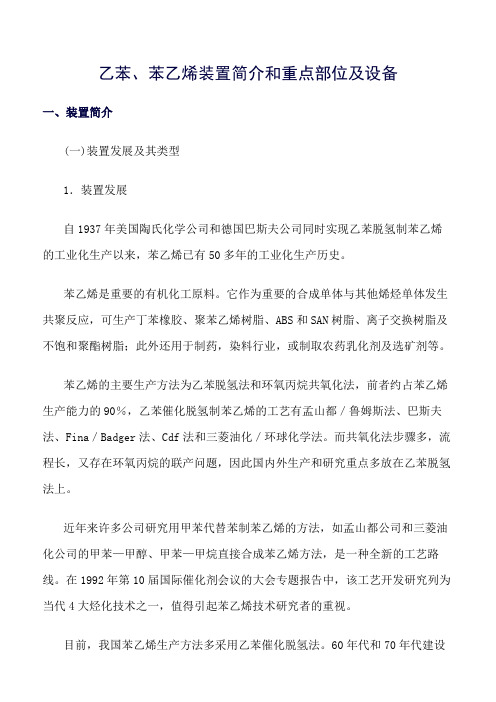
乙苯、苯乙烯装置简介和重点部位及设备一、装置简介(一)装置发展及其类型1.装置发展自1937年美国陶氏化学公司和德国巴斯夫公司同时实现乙苯脱氢制苯乙烯的工业化生产以来,苯乙烯已有50多年的工业化生产历史。
苯乙烯是重要的有机化工原料。
它作为重要的合成单体与其他烯烃单体发生共聚反应,可生产丁苯橡胶、聚苯乙烯树脂、ABS和SAN树脂、离子交换树脂及不饱和聚酯树脂;此外还用于制药,染料行业,或制取农药乳化剂及选矿剂等。
苯乙烯的主要生产方法为乙苯脱氢法和环氧丙烷共氧化法,前者约占苯乙烯生产能力的90%,乙苯催化脱氢制苯乙烯的工艺有孟山都/鲁姆斯法、巴斯夫法、Fina/Badger法、Cdf法和三菱油化/环球化学法。
而共氧化法步骤多,流程长,又存在环氧丙烷的联产问题,因此国内外生产和研究重点多放在乙苯脱氢法上。
近年来许多公司研究用甲苯代替苯制苯乙烯的方法,如孟山都公司和三菱油化公司的甲苯—甲醇、甲苯—甲烷直接合成苯乙烯方法,是一种全新的工艺路线。
在1992年第10届国际催化剂会议的大会专题报告中,该工艺开发研究列为当代4大烃化技术之一,值得引起苯乙烯技术研究者的重视。
目前,我国苯乙烯生产方法多采用乙苯催化脱氢法。
60年代和70年代建设的小型装置能耗和物耗较高,缺少市场竞争能力,随着国外技术的引进,大部分已停产,剩下的几套经多次技术改造,能耗和物耗有所下降,同时,利用地区差价和本企业下游产品的需求仍维持生产。
2.苯乙烯的主要生产方法及特点目前,世界范围内苯乙烯生产的主要工艺有脱氢法和环氧丙烷法。
脱氢工艺包含Fina/Badger工艺和鲁姆斯/环球化学工艺。
一些生产苯乙烯的公司拥有自身的技术,如陶氏、巴斯夫,其他大部分生产商采用UnitedCatalysts(UCl)和Criterion的催化剂。
UCI占据了70%的脱氢催化剂市场份额,Criterion占20%,其他生产厂家占10%。
在乙苯脱氢制苯乙烯的工艺技术方面,除德国巴斯夫公司外,各家外商技术基本相同,大都是采用高真空绝热脱氢反应和反应热能回收技术,蒸馏都是真空高效填料塔技术(EB/SN分离塔),各项经济指标大体相同。
精馏塔的设计及选型
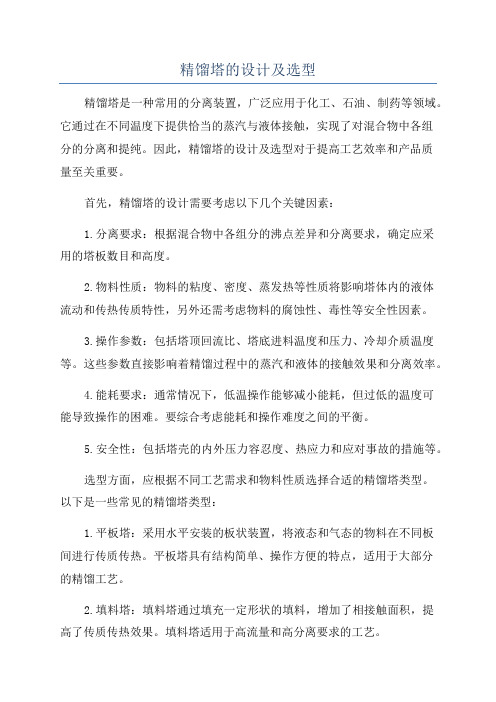
精馏塔的设计及选型精馏塔是一种常用的分离装置,广泛应用于化工、石油、制药等领域。
它通过在不同温度下提供恰当的蒸汽与液体接触,实现了对混合物中各组分的分离和提纯。
因此,精馏塔的设计及选型对于提高工艺效率和产品质量至关重要。
首先,精馏塔的设计需要考虑以下几个关键因素:1.分离要求:根据混合物中各组分的沸点差异和分离要求,确定应采用的塔板数目和高度。
2.物料性质:物料的粘度、密度、蒸发热等性质将影响塔体内的液体流动和传热传质特性,另外还需考虑物料的腐蚀性、毒性等安全性因素。
3.操作参数:包括塔顶回流比、塔底进料温度和压力、冷却介质温度等。
这些参数直接影响着精馏过程中的蒸汽和液体的接触效果和分离效率。
4.能耗要求:通常情况下,低温操作能够减小能耗,但过低的温度可能导致操作的困难。
要综合考虑能耗和操作难度之间的平衡。
5.安全性:包括塔壳的内外压力容忍度、热应力和应对事故的措施等。
选型方面,应根据不同工艺需求和物料性质选择合适的精馏塔类型。
以下是一些常见的精馏塔类型:1.平板塔:采用水平安装的板状装置,将液态和气态的物料在不同板间进行传质传热。
平板塔具有结构简单、操作方便的特点,适用于大部分的精馏工艺。
2.填料塔:填料塔通过填充一定形状的填料,增加了相接触面积,提高了传质传热效果。
填料塔适用于高流量和高分离要求的工艺。
3.萃取塔:萃取塔用于通过溶剂与物料之间的分配系数差异实现对其中一组分的特殊分离,常见于提取和精制工艺。
在选择精馏塔时,除了考虑上述因素,还应综合考虑塔体和设备的可靠性、维修易用性、成本等因素。
综上所述,精馏塔设计及选型需要充分考虑分离要求、物料性质、操作参数、能耗要求和安全性等方面。
根据工艺需求和物料性质选择合适的精馏塔类型,并综合考虑设备的可靠性和成本等因素,以实现高效、安全、经济的精馏过程。
最新化工原理课程设计 乙苯-苯乙烯板式精馏塔的工艺设计

化工原理课程设计乙苯-苯乙烯板式精馏塔的工艺设计化工原理课程设计题目乙苯-苯乙烯板式精馏塔的工艺设计年级专业学号学生姓名2009年 12月 21日目录No table of contents entries found.第一节化工原理课程设计(精馏装置)的内容1.1设计题目课程设计题目——乙苯-苯乙烯板式精馏塔的工艺设计:设计一座乙苯-苯乙烯连续精馏塔,要求年处理原料液(40%乙苯)30000t/a,塔底馏出液中含乙苯不高于2%。
塔顶馏出液中含乙苯为98%(以上均为质量%)。
1.2操作条件1.塔顶压强4kPa(表压);2.进料热状况,自选;3.回流比,自选;4.塔釜加热蒸汽压力506kPa;5.单板压降不大于0.7kPa;6.年工作日300天,每天24小时连续运行。
1.3设计内容1.设计方案的确定及工艺流程的说明;2.塔的工艺计算;3.塔和塔板主要工艺结构的设计计算;4.塔内流体力学性能的设计计算;5.塔板负荷性能图的绘制;6.塔的工艺计算结果汇总一览表;7.辅助设备的选型与计算;8.生产工艺流程图及精馏塔工艺条件图的绘制;9.对本设计的评述或对有关问题的分析与讨论。
1.4基础数据1.安托因方程㏒P=A+B/(C+t)表12.组分的液相粘度µ(mpa.s)表23.组分的液相密度ρ(kg/m3)表34.组分的表面张力σ(mN/m)表4双组分混合液体的表面张力m σ可按下式计算:AB B A BA m x x σσσσσ+=(B A x x 、为A 、B 组分的摩尔分率)第二节 设计方案的确定及工艺流程的说明2.1设计方案的确定及工艺流程的说明原料液经卧式列管式预热器预热至泡点后送入连续板式精馏塔(筛板塔),塔顶上升蒸汽流采用强制循环式列管全凝器冷凝后一部分作为回流液,其余作为产品经冷却后送至贮罐;塔釜采用热虹吸立式再沸器提供汽相流,塔釜产品经卧式列管式冷却器冷至贮罐 2.1流程图第三节 精馏塔(精馏段)计算3.1塔的工艺计算 3.1.1 全塔物料衡算(一)料液及塔顶底产品含苯的摩尔分率乙苯和苯乙烯的相对摩尔质量分别为106.168和104 .152kg/kmol 。
精馏塔设备设计及选型

第四章设备设计及选型4.1 设备设计标准➢《钢制压力容器》GB150-98➢《压力容器用钢板》GB6654-96➢《化工装置用不锈钢大口径焊接钢管技术要求》HG20537.4-92➢《安全阀的设置和选用》HG/T20570.2-95➢《设备进、出管口压力损失计算》HG/T20570.9-95➢《钢制化工容器设计基础规定》HG20580-98➢《钢制化工容器材料选用规定》HG20581-98➢《钢制化工容器强度计算规定》HG20582-98➢《钢制化工容器结构设计规定》HG20583-98➢《钢制化工容器制造技术规定》HG20584-98➢《化工设备设计基础规定》HG/T20643-98➢《压力容器无损检测》JB4730-2005➢《钢制压力容器焊接工艺评定》JB4708-2000➢《钢制压力容器焊接规程》JB/T4709-2000➢《钢制压力容器产品焊接试板的力学性能检验》JB4744-2007➢《压力容器用钢锻件》JB4726-2000➢《石油化工塔型设备设计规范》SH 3030-19974.2 设备设计及选型塔设备是化工、石油化工和炼油等生产中最重要的设备之一,塔可以使气液相或者液液相之间进行紧密接触,达到较为良好的相际传质及传热的目的。
在塔设备中常见的单元操作有:吸收、精馏、解吸和萃取等。
此外工业气体的冷却与回收、气体的湿法净制和干燥,以及兼有气液两相传质和传热的增湿和减湿等效果。
4.2.1 塔设备设计原则➢具有适宜的流体力学条件,可使气液两相良好接触;➢结构简单,处理能力大,压降低;➢强化质量传递和能量传递。
4.2.2 塔设备的设计目标作为主要用于传质过程的塔设备,首先必须使气液两相能充分接触,以获得较高的传质效率。
此外,为满足工业生产的需要,塔设备还得考虑下列各项要求:(1)生产能力大。
在较大的气(汽)液流速下,仍不致发生大量的雾沫夹带、拦液、或液泛等破坏正常操作的现象;(2)操作稳定、弹性大。
- 1、下载文档前请自行甄别文档内容的完整性,平台不提供额外的编辑、内容补充、找答案等附加服务。
- 2、"仅部分预览"的文档,不可在线预览部分如存在完整性等问题,可反馈申请退款(可完整预览的文档不适用该条件!)。
- 3、如文档侵犯您的权益,请联系客服反馈,我们会尽快为您处理(人工客服工作时间:9:00-18:30)。
设备计算部分:苯乙烯是含有饱和侧链的一种简单芳烃,是有机化工重要产品之一,为无色透明液体,常温下具有辛辣香味,易燃。
苯乙烯难溶于水,25摄氏度时其溶解度为0.066%,能溶于甲醇,乙醇,乙醚等溶剂中③苯乙烯用途苯乙烯(SM)是合成高分子工业的重要单体,它不但能自聚为聚苯乙烯树脂,也易与丙烯腈共聚为AS塑料,与丁二烯共聚为丁苯橡胶,与丁二烯、丙烯腈共聚为ABS塑料,还能与顺丁烯二酸酐、乙二醇、邻苯二甲酸酐等共聚成聚酯树脂等。
由苯乙烯共聚的塑料可加工成为各种日常生活用品和工程塑料,用途极为广泛。
一、精馏塔参数计算:1.1塔径的计算以所设计塔为中型估计塔径V l g ∗ρgl0.3=8.256∗1.580.3=0.0563根据上述所算出的参数及所设板距(620mm),经读图可知如下C20=0.163可得液泛速度u=C ρL−ρGρG=0.163∗788.09−1.6871.687=2.89取液泛分率等于0.8塔的有效截面积A u=7.6540.8∗2.89=3.31m2则塔的总截面积为4.315m2塔径D=4Aπ=4∗4.3153.14=2.564m将塔径整数化D=2.6m得塔截面积A=5.306m21.2精馏塔其他部件主要参数1.2.1凹形降液管宽度Wd 和截面积Af 在精馏段 由因塔径D=2.0m ,选用单溢流弓形降液管查手册参数图得验算液体在降液管中停留时间,即故降液管设计合理 1.2.2降液管底隙高度h 0取液体通过降液管底隙的流速u 0=0.1m/s 依式计算降液管底隙高度0h , 即:000.00230.0250.910.1s w L h m l u ===⨯ 1.2.3降液管的尺寸和停留时间设计中依据堰长与塔径之比由图可查,为使液体中夹带的气泡得以分离,液体在降液管内应有足够的时间停留,由实践经验可知,液体在降液管停留时间不应小于3~5s ,因此确定降液管的尺寸和停留时间。
θ=13.68s A =0.112∗4.5=0.4131.2.4受液盘受液盘有凹形和平形两种型式.平形受液盘一般需在塔板上设置进口堰,以保证降液管液封,并使液体在板上分布均匀。
设置进口堰既占用板面,又易使沉淀物淤积此处造成阻塞。
采用凹形受液盘不须设置进口堰。
凹形受液盘既可在低液量时形成良好的液封,且有改变液体流向的缓冲作用,并便于液体从侧线的抽出.液封盘一般在降液管正下方,汇聚液体保持液面液封、分布均匀。
,因此选择凹型受液盘66.0/=D l W ss L H A hTf 555.1336000157.06.03545.036003600>=⨯⨯⨯==θ0722.0=Tf A A 124.0=DW d23545.0m A f =1、堰长2、溢流堰高度由选用平直堰,堰上液层高度3、溢流装置计算取板上请液层高度 则同理可得提馏段:ℎOW =0.04m 1.2.5塔板布置1、取边缘区宽度W d =0.035m ,安定区宽度W s =0.065m ①精馏段:依下式计算开孔区面积212sin 180x A R R απ-⎛⎫= ⎪⎝⎭ ()()1.30.1820.0650.40322d s D x W W m =-+=-+= 1.30.0350.61522c D R W m=-=-=故:210.40320.615sin 1800.615A απ-⎛⎫= ⎪⎝⎭ 20.915m =②提馏段:依下式计算开孔区面积m D l W 65.15.266.066.0=⨯==OWW W h h h -=3/2)(100084.2Wh OW L L E h =m h OW 03.0)65.1.036000157.0(1100084.23/2=⨯⨯⨯=m h L 07.0=m h h h OW L W 04.003.007.0=-=-='''21'2sin180xA x RRαπ-⎛⎫= ⎪⎝⎭210.22320.365sin1800.365π-⎛⎫= ⎪⎝⎭=0.304m2()()''''0.80.1120.0650.22322d sDx W W m=-+=-+=''0.80.0350.36522cDR W m=-=-=1.2.6、筛孔数n与开孔率ϕ取筛孔的孔径d0为5mm正三角形排列,一般碳钢的板厚δ为4mm,取0/ 3.5t d=故孔中心距t=3.5 ⨯ 5.0=17.5m依下式计算塔板上筛孔数n ,即33221158101158100.915346017.5n Atα⎛⎫⎛⎫⨯⨯==⨯=⎪ ⎪⎝⎭⎝⎭孔依下式计算塔板上开孔区的开孔率ϕ,即:2A0.907%7.5%(/)A t dαϕ===(在5~15%范围内)精馏段每层板上的开孔面积为20.0750.9150.0686oA A mαϕ=⨯=⨯=气孔通过筛孔的气速1.0415.16/0.6086soVu m sA===提馏段每层板上的开孔面积为''20.1010.3040.0307oA A mαϕ=⨯=⨯=气孔通过筛孔的气速''0'0.62720.42/0.0307s o V u m sA ===1.2.7、塔有效高度 精馏段;(20-1)*0.4=7.6m提馏段有效高度(16-1)*0.4=6m ;在进料板上方开一人孔,其高为0.8m ,一般每6~8层塔板设一 人孔(安装、检修用),需经常清洗时每隔3~4层块塔板处设一人孔。
设人孔处的板间距等于或大于600m 。
根据此塔人孔设6个。
故:精馏塔有效高度 7.6+6.0+0.5*6=16.6m 总高度为16.6+0.6+0.5=17.7m二、换热器:2.1基本要求:该换热器作用是由于进料的温度较高因此在进料前安装换热器,使物料温度降为泡点温度,以便在接下来的工序得以正常使用,冷却介质为常温的冷水,保证在工艺条件下,长期运转,安全可靠,不泄露,维修清洗方便,满足工艺要求。
采用间壁式换热器2.2换热器类型的选择:因两种流体的温差较大,换热的难度较大,故选用浮头式间壁式换热器,并且使用能够耐腐蚀,承受较大压力的材料,以及采用逆流换热的方式。
2.3换热物料的实际参数2.4、换热器各项参数的确定及计算1、热流量;换热器中Q=4786480.943KJ/h=1329578.04W= 1329578.04J/s2、终端温差:热介质140.85137.89冷介质20.00 25.32温差 120.85115.57则平均温差经校正可计算得:φ=R2+1R−1ln1−P1−PRR2+1)2<0.8'0.9234.9632.16om m tt t Cϕ∆∆∆=⨯==67.785x0.6=40.6713、流量传热系数K、实际总传热面积:为求得传热面积A,须先求出传热系数K,而K 值又与给热系数、污垢系数、污垢热阻等有关。
在换热器直径、流速等参数均未确定时,给热系数也无法计算,只能进行试算。
由传热面积计算公式可得:A =203.65m 2 (1)传热计算 ①管程给热系数αiCp=2.345kJ ·kg -1·K -1330.980.0160.7540.02081010Prp ic μλ-⨯⨯⨯==−6×2.345×1030.05557=36.12 ()0.80.320.30.02080.0230.023*******.044/0.021Re 0.754Pr i i i i W C m d λα⎛⎫==⨯⨯⨯=∙ ⎪ ⎪⎝⎭=0.023x 0.0560.015x11520.8x36.120.3=73.84 W ·m -2·K -1 ②壳程对流传热系数αo已知壳程雷诺数Re 0=627.7,Cp=2.491 kJ ·kg -1·K -1Pr 0=c p μλ=2.491∗1.151=0.129 30.5500330.36Re 4.187100.72710 4.860.626e p d c μλαϕμλ-⨯⨯⨯===100=()(Pr)Pr取 1.05μϕ=,则α0=506.8 W ·m -2·K -1 ③确定污垢热阻查《化工原理》Rsi =0.18(m2·K)/kW 、Rs0=0.18(m2·K)/kW④总传热系数K 0:00011oW mi i ibd d d so sid d dK R R αλα=++++即计算结果为 K 0=11506.8+0.18×10−3+0.002×1916.8×17+0.18×10−3×1915+1970.84×15=50.05所需传热面积A 0=209.65与换热器面积相差不大,故可以适用。
4、压力降的计算:根据管径越小,结构越紧凑,越便宜,常用外径为19mm ;使u i =10m/s ,设所需单程管数为n ,Φ19mm Х2mm 的管内径为0.015m ,从管内体积流量:Vs =n ×π4×0.0152×10×3600=4078.69m 3/h①管程流体阻力的计算流速 u i =Vs/S i =4078.69/36000.1090=10.3942m/s雷诺数 Re =duρμ=设管为光滑管,根据雷诺数范围,摩擦系数 λ=64Re =0.0350 则管内阻力损失1p ∆=λld u 22 ρ=0.0350×60.015×10.39422×1.02=0.71358kPa回弯阻力损失2p ∆=3×0.096582×6.82=0.0342k Pa有 12()i i s p p p p F N N ∑∆=∆+∆ 则管程总损失△p t = 1p ∆+2p ∆ Fi ∗Ns ∗Np = 7.1358+0.0342 ∗1.5∗2∗2=4.281kPa 式中:F i ——结垢校正因数,无因此,对φ19×2mm 的管子,取为1.5; Np ——管程数,Np =2; Ns ——串联的壳程数, Ns =2;同理壳程损失:12() 1.0(4.95 1.543) 1.157.467i p p p kpa''∑∆=∆+∆⨯=+⨯=x2=0.5kPa 则通过核算,管程及壳程的阻力损失都不超过30kPa ,故该换热器适用。
2.5、折流板采用弓形折流板,取弓形折流板圆缺高度为壳体内径的25%,则切去的圆缺高度为h=0.25×400=100mm,取折流板间距B=0.3D ,则:B=0.3×400=120mm, 可取B=120mm. 折流板数NB=(传热管长)/(折流板间距)-1=4000/200-1=8块。