PCB工艺流程取放板操作教材
PCB制造工艺流程详解课件
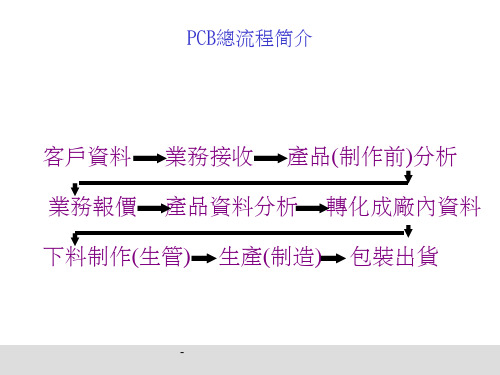
-
钻孔介绍(3)
I. 钻孔:
目的:
➢ 在板面上钻出层与层之间线路 连接的导通孔
主要原物料:钻头;鋁盖板;紙垫板
➢
钻头:碳化钨,钴及有机黏着剂组合而成
➢
盖板:主要为铝片,在制程中起钻头定位;
散热;减少毛头;保護基板的作用
➢
垫板:主要为紙漿墊板,在制程中起保护
钻机台面;清洁钻针沟槽胶渣作用.
➢ 下PIN:
铆钉
➢ 利用铆钉将多张内层板钉在一
2L
起,以避免后续加工时产生层间
3L
滑移
4L
• 主要原物料:铆钉;P/P
5L
➢ P/P(PREPREG):由树脂和玻璃纤
维布组成,据玻璃布种类可分为
1060;1080;2116;7628等几种
2L
➢ 树脂据交联状况可分为:
3L
A阶(液態);B阶(半固態);C阶(固態)
毛頭形成原因:鑽孔後孔邊緣的未切斷的銅絲及未切斷 的玻璃布
Deburr之目的:去除孔邊緣的毛邊,防止鍍孔不良 重要的原物料:刷輪
-
鍍銅介紹(3)
☺ 去膠渣(Desmear):
smear形成原因: 鑽孔時造成的高溫超過玻璃化轉移溫度
(Tg值),而形成膠糊狀,產生膠渣 Desmear之目的:裸露出各層需互連的銅環,另膨松劑可
-
防焊流程简介(5)
I. 印刷
目的:利用丝网上图案,将防焊油墨准确的 印在板子上。
主要原物料:油墨 常用的印刷方式:
A 印刷型(Screen Printing) B 淋幕型 (Curtain Coating) C 喷涂型 (Spray Coating) D 滚涂型 (Roller Coating)
PCB工艺流程课件(PPT 42张)
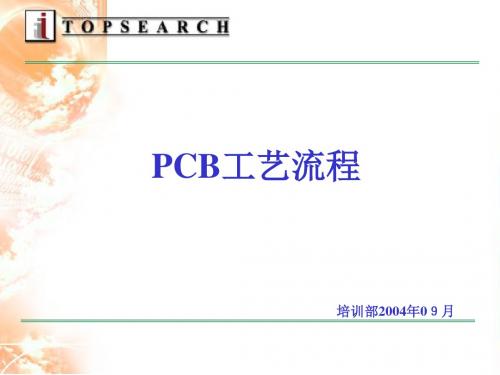
7.3. 预局:将湿菲林局至板面干爽
7.4. 曝光:图形转移
7.4.1. 将绿油菲林上的图形转移到黄菲林上.
7.4.2. 曝光:将黄菲林对准板面上的线路图形放 在板面上,然后曝光
7.5. 显影:将未经曝光的湿菲林冲走 7.6. 后局:将湿菲林烘干到要求的硬度
8.0. 白字
8.1. 网印:将文字印刷到板面上
PCB工艺流程
培训部2004年09月
课程内容
PCB工艺流程简介及工序目的 PCB工艺流程介绍 PCB工艺流程录象
一 PCB工艺流程 (简图)
界 料 内层干菲林 内层蚀板 棕化 黑氧化 压板 钻 孔 沉铜<孔金属化> 喷锡
表面处理
成 型
开/短路测试
镀金手指
包 装
出 货
外层干菲林 绿油<湿菲林> 外层蚀板 图形电镀
4.0. 钻孔
根据钻孔加工方式,大致可分为以下两 种:
一种是机械钻孔,另一种是激光钻孔
根据钻孔加工类型,大致可分为以 下两类: 1.一次钻加工 2.分步钻加工
主轴 钻嘴
销钉 线路板 台板
销钉 盖板 底板
主轴 销钉 线路板 台板 钻嘴 销钉 盖板
底板
主轴 钻嘴
销钉 线路板 台板
销钉 盖板 底板
白 字
二 制作流程 1. 界料:
界料就是按照ME制作的工作指示,将大面积 的原状始材料切割成生产所需的尺寸.
2. 局板:
将板材放在局炉内烘烤,降低板内湿度,消除内应力
3. 内层
3.1. 内层干膜
3.1.1. 磨板:
粗化铜板表面,以利于增加板面与药膜的结合
力
清洁板面,除掉板面杂物
除去铜板表面的防氧化层
PCB(印刷线路板)工艺流程
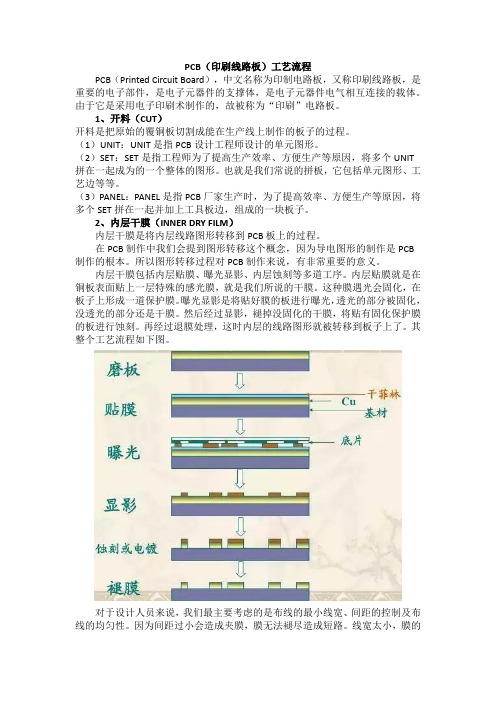
PCB(印刷线路板)工艺流程PCB(Printed Circuit Board),中文名称为印制电路板,又称印刷线路板,是重要的电子部件,是电子元器件的支撑体,是电子元器件电气相互连接的载体。
由于它是采用电子印刷术制作的,故被称为“印刷”电路板。
1、开料(CUT)开料是把原始的覆铜板切割成能在生产线上制作的板子的过程。
(1)UNIT:UNIT是指PCB设计工程师设计的单元图形。
(2)SET:SET是指工程师为了提高生产效率、方便生产等原因,将多个UNIT拼在一起成为的一个整体的图形。
也就是我们常说的拼板,它包括单元图形、工艺边等等。
(3)PANEL:PANEL是指PCB厂家生产时,为了提高效率、方便生产等原因,将多个SET拼在一起并加上工具板边,组成的一块板子。
2、内层干膜(INNER DRY FILM)内层干膜是将内层线路图形转移到PCB板上的过程。
在PCB制作中我们会提到图形转移这个概念,因为导电图形的制作是PCB制作的根本。
所以图形转移过程对PCB制作来说,有非常重要的意义。
内层干膜包括内层贴膜、曝光显影、内层蚀刻等多道工序。
内层贴膜就是在铜板表面贴上一层特殊的感光膜,就是我们所说的干膜。
这种膜遇光会固化,在板子上形成一道保护膜。
曝光显影是将贴好膜的板进行曝光,透光的部分被固化,没透光的部分还是干膜。
然后经过显影,褪掉没固化的干膜,将贴有固化保护膜的板进行蚀刻。
再经过退膜处理,这时内层的线路图形就被转移到板子上了。
其整个工艺流程如下图。
对于设计人员来说,我们最主要考虑的是布线的最小线宽、间距的控制及布线的均匀性。
因为间距过小会造成夹膜,膜无法褪尽造成短路。
线宽太小,膜的附着力不足,造成线路开路。
所以电路设计时的安全间距(包括线与线、线与焊盘、焊盘与焊盘、线与铜面等),都必须考虑生产时的安全间距。
(1)前处理:磨板磨板的主要作用:基本前处理主要是解决表面清洁度和表面粗糙度的问题。
去除氧化,增加铜面粗糙度,便于菲林附着在铜面上。
pcb板制造工艺流程及控制方法
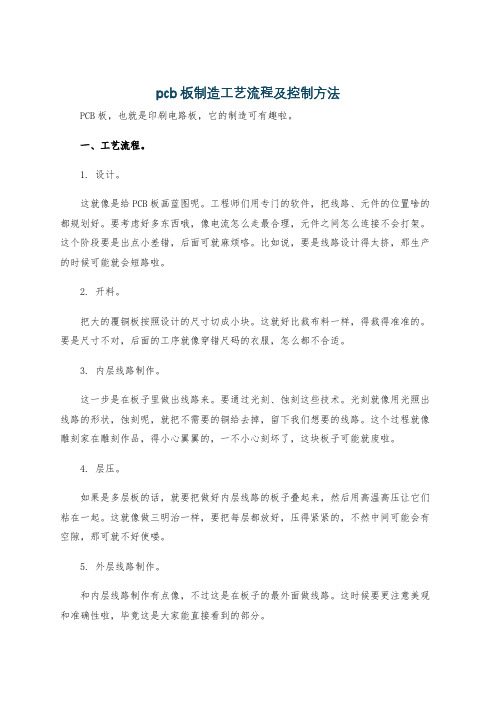
pcb板制造工艺流程及控制方法PCB板,也就是印刷电路板,它的制造可有趣啦。
一、工艺流程。
1. 设计。
这就像是给PCB板画蓝图呢。
工程师们用专门的软件,把线路、元件的位置啥的都规划好。
要考虑好多东西哦,像电流怎么走最合理,元件之间怎么连接不会打架。
这个阶段要是出点小差错,后面可就麻烦咯。
比如说,要是线路设计得太挤,那生产的时候可能就会短路啦。
2. 开料。
把大的覆铜板按照设计的尺寸切成小块。
这就好比裁布料一样,得裁得准准的。
要是尺寸不对,后面的工序就像穿错尺码的衣服,怎么都不合适。
3. 内层线路制作。
这一步是在板子里做出线路来。
要通过光刻、蚀刻这些技术。
光刻就像用光照出线路的形状,蚀刻呢,就把不需要的铜给去掉,留下我们想要的线路。
这个过程就像雕刻家在雕刻作品,得小心翼翼的,一不小心刻坏了,这块板子可能就废啦。
4. 层压。
如果是多层板的话,就要把做好内层线路的板子叠起来,然后用高温高压让它们粘在一起。
这就像做三明治一样,要把每层都放好,压得紧紧的,不然中间可能会有空隙,那可就不好使喽。
5. 外层线路制作。
和内层线路制作有点像,不过这是在板子的最外面做线路。
这时候要更注意美观和准确性啦,毕竟这是大家能直接看到的部分。
6. 阻焊和字符印刷。
阻焊就像是给线路穿上防护服,防止它们在焊接的时候短路。
字符印刷呢,就是印上一些标识,像元件的编号之类的,这样我们在组装的时候就能轻松找到对应的元件啦。
7. 表面处理。
这是为了让PCB板在焊接元件的时候更容易,像镀锡、镀金之类的。
就像给板子的表面做个美容,让它更好地和元件结合。
8. 成型。
把板子按照设计的形状切割出来。
这是最后的一步啦,就像给PCB板做个最后的造型。
二、控制方法。
1. 质量控制。
在每个工序之后都要检查,就像我们做完一件事要检查有没有漏洞一样。
比如在线路制作之后,要用检测仪器看看线路有没有断开或者短路的地方。
要是发现问题,要及时调整或者把有问题的板子挑出来,可不能让它混到好板子里面去。
PCB工艺流程详解(三)
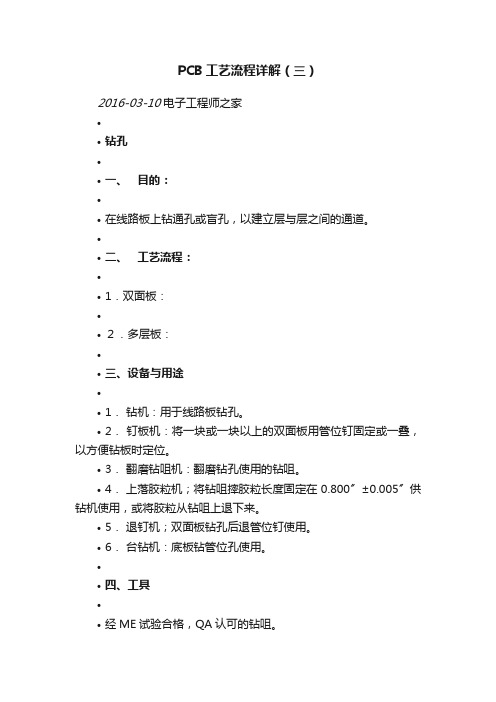
PCB工艺流程详解(三)2016-03-10电子工程师之家••钻孔••一、目的:••在线路板上钻通孔或盲孔,以建立层与层之间的通道。
••二、工艺流程:••1.双面板:••2.多层板:••三、设备与用途••1.钻机:用于线路板钻孔。
•2.钉板机:将一块或一块以上的双面板用管位钉固定或一叠,以方便钻板时定位。
•3.翻磨钻咀机:翻磨钻孔使用的钻咀。
•4.上落胶粒机;将钻咀摔胶粒长度固定在0.800〞±0.005〞供钻机使用,或将胶粒从钻咀上退下来。
•5.退钉机;双面板钻孔后退管位钉使用。
•6.台钻机:底板钻管位孔使用。
••四、工具••经ME试验合格,QA认可的钻咀。
•五、操作规范••1.取拿钻咀,搬运上落生产板时需戴手套,以免污染钻咀及线路板。
•2.钻咀使用前,须经检查OK,确保摔胶粒长度在0.800〞±0.005〞之内。
•3.搬运、摆放生产板过程中,不得有拖板、摔板、板上齐板等现象发生,严防擦花线路板。
•4.钻板后检查内容包括:孔径大小、孔数、孔位置,内层偏移(多层板)、孔形状、披锋、擦花。
••六、环境要求:••温度:20±5℃,湿度:≦ 60%。
••七、安全与环保注事项:••1.钻机运行时,头、手及其它物品不得伸入钻机内,需紧急停机时可按钻机两边红色紧急停机键。
•2.取放钻咀需拿手套,且不得接触刀刃部分,以防扎伤。
•3.不得私自接触钻机及其它机器电源开关、变压器,有问题需通知SE或专业人员维修。
•4. 发现吸尘机有异常声音或吸尘袋泄漏,应先关闭钻机及吸尘机,再通知管理人员并更换吸尘袋。
•5. 用废的物料严格按规定方法处理,防止污染环境。
••沉铜&板电••一、工艺流程图:•••二、设备与作用。
••1.设备:•除胶渣(desmear)、沉铜(PTH)及板电(PP)三合一自动生产线。
•2.作用:•本工序是继内层压板、钻孔后通过化学镀方法,在已钻孔板孔内沉积出一层薄薄的高密度且细致的铜层,然后通过全板电镀方法得到一层0.2~0.6mil厚的通孔导电铜(简称一次铜)。
PCB全流程讲义
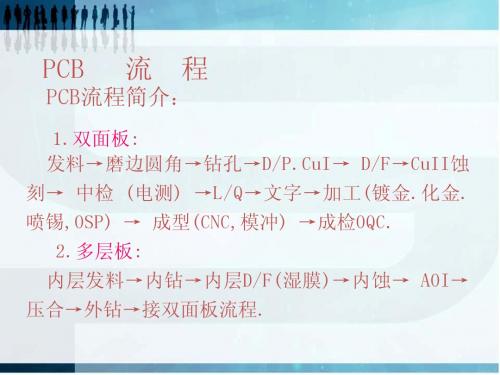
上机台 盖铝片 a.保护基板,不易刮伤 b.起降温作用,减少断针 c.防止刮伤 a.防止孔偏 b.防止板子松动,防止断针 a.钻头公差±1mil b.四层板用R2以上之钻咀
贴胶带 插钻头
设定程式 设定机台号:便于问题的追踪 钻孔
钻
孔
内钻 下板 刮巴厘 2.厂内孔径±1mil,孔位公差±3mil 下板 对麦拉 IPQC 下流程 NPTH孔公差±1mil. 3.PTH孔径大于6.1mm,以钻孔方式钻孔. NPTH孔孔径大于6.1mm以模冲或CNC 方式成型.
电
镀(D/P) D/P)
★PTH(化学铜)
(4)去脂平整: 作用:去除表面油污、氧化物、指印等.在板面形成一层带正电 的皮膜,利于孔吸附活化槽带负电的Sn,Pd胶团 (5)微蚀:为H2SO4+H2O2蚀刻掉Cu基体表面20-40u"的Cu层,使Cu箔表面粗糙, 提高结合力. (6)酸 洗:对板子清洁处理作用,避免污染. (7)预活化:活化前处理与活化液配套使用,减少对活化的污染. (8)活 化:活化的作用是在绝缘基体上吸附一层具有催化能力的钯,使基 体表面具有还原Cu的能力. (9)速化处理:用酸将附着在钯团外的锡壳剥掉,露出钯原子,促使铜原子 吸附. (10)化学镀铜.利用化学反应方式使孔内沉积一层化学CU,厚度在20-40 u". ★化学镀Cu质量的验证. a.背光试验法:化学铜Cu后的试样沿一排孔的中心切下,并用细砂纸 打磨切口处留下的毛边将制作的试样放置在灯光台下,在显影放大镜下观察 孔透光的情况,将孔积Cu的完整性分为若干级,不透光的为最佳,透光度4.0级 需重走D/P.
文 字
一.作业流程: 刷磨 磨刮刀 制网→架网→试印→烤烘→下制程 调墨 1. 张网: 线路25-30N, 防焊20-25N, 文字16-21N 325目 110目 90目 250目 网目: 每平方英寸网布以开孔状或丝网条状. 网版:文字为正片制网. 2.架网:贴透明胶(依成型为准) →固定网版→测高度(3-8cm)→压克力 归0→对板→上PIN →定位→调网→试印. 3.调墨:文字Ink型号 4.试印 5. 烘烤:温度150℃ 时间30min.
PCB制作工艺流程

PCB制作工艺流程一、开料目的:以制造流程单之规格,将大面积的敷铜泊基板依制前设计所规化的工作尺寸裁切尺寸及厚度发料并裁板。
1、裁板作业流程:仓库→裁板室→调整尺寸→裁板→检查测量2、磨边作业流程:设置长、宽→磨边→水洗一→水洗二→水洗三→挤干→吹干→烘干二、内层1、内层前处理目的:将除去板面氧化物及油污,再加磨刷粗化铜面增加感光材料于铜面的附著力。
作业流程:上板→化学清洗(H2SO4:3%~5%,压力:1.5±0.5㎏/C㎡)→溢流水洗(压力:1.5±0.5㎏/C㎡)→磨刷→中压水洗(压力:3.0±0.5㎏/C㎡)→微蚀刻(SPS:100~120g/1, H2SO4:1%~3%,压力:1.5±0.5㎏/C㎡)→溢流水洗(压力:1.5±0.5㎏/C㎡)→酸洗(H2SO4:1%~3%)→溢流水洗(压力:1.5±0.5㎏/C㎡)→烘干→检查注意事项:1、做板之前要做刷痕实验、水纹实验,刷痕宽度:1.0±0.2㎝,水纹:15秒以上;2、内层板厚分为两种:47mil的为普通基板,其他为特殊基板,特殊基板要做标记,还要测板厚;3、检查压力表;2、涂布目的:以抗蚀性材料附著力在铜面上,制作内层线路GND、VCC作业流程:进料→粘尘→下降→入料→涂布→烘烤(第一阶段:145℃;第二阶段:125℃;第三阶段:115℃;第四阶段:55℃;第五阶段:35℃) →出料→检查注意实项:1、粘尘纸200片后换一次;2、油墨刮刀压力调整(压力:1.0~3.0㎏/C㎡);3、检测膜厚(8.0±1.5mil),检查脏点等3、曝光(半自动曝光)目的:曝光灯发出紫外光投射在已贴有干膜的板面上,将曝光菲林上线路图形转移到感光干膜上,未吸紫外光的干膜显影时会溶解于显影液中作业流程:检查底片→架底片→调整对准度→放板→吸真空→曝光→检查注意事项:1、每天清洁机台,做能量测试;2、室内温度:22.0±2℃,湿度:55±5%;3、黑色底片每曝光2000次后报废,每曝光500次后底片检查;4、每曝光前用手动滚轮清洁一次底片,底片每曝光10片清洁一次,每50片上机检查一次;5、底片L2朝上,L3朝下;6、灯管亮到熄灭:12秒;7、抽真空度至少600~700MMHG;8、抽真空后用刮刀赶气;9、放板时,把底片翻开看到压条后,沿着压条放板,避免刮伤底片4、显影目的:显影是把尚未发生聚合反应的区域用显影液将之冲洗掉,已感光部分则因已发生聚合反应而洗不掉乃留在铜面上成为蚀刻之阻剂膜5、蚀刻目的:以蚀刻液将铜表面去除,留有抗蚀油墨之线路,制作内层线路GND、VCC 6、去墨剥膜目的:将线路上之抗蚀材料去掉,露出铜线路完成制作内层线路ND、VCC(4,5,6)工作流程:显影(温度:31.0±2℃;浓度:碳酸钠:1.0±0.2wt%,传送速度:4.0±0.5m/min;压力:1.75±0.25㎏/C㎡)→水洗(压力:1.5±0.3㎏/C㎡)→蚀刻(温度:40~45℃;传动速度:4.0±0.5m/min;喷压:上压3.0±0.5㎏/C㎡,下压2.8±0.5㎏/C㎡;铜含量:105~115g/l) →水洗(压力:1.5±0.3㎏/C㎡)→检查→软化去墨(温度:45~50℃;传动速度:4.5±0.5m/min;浓度:NaOH1.0~0.2%;去墨第一段0.1~0.2㎏/C㎡;去墨第二段0.5~0.2㎏/C㎡;去墨第三段1.5~0.2㎏/C㎡)→水洗→酸洗(温度:RT;压力:1.5±0.3㎏/C㎡,H2SO4浓度:1~3%)→水洗→烘干(温度:90.0±10℃)→检查→收板注意事项:1、每天退槽一次;2、有线路的板含有线路的板面朝上,没有线路的板不作要求;3、每天用报废板做显影、蚀刻实验,检查参数是否合格;4、检查压力表;5、每班换水一次;6、滤网每天清洗一次;7、检查喷嘴7、黑化处理工作流程:上料→碱性清洁(16″)→水洗(6″)→水洗(11″)→微蚀(8″)→水洗(1″)→水洗(5″)→预侵(6″)→黑化(15″)→热纯水洗(8″)→水洗(5″)→水洗(16″)→后侵(16″)→纯水洗(3″)→纯水洗(8″)→热纯水洗(16″)→滴干→烘干(35″)注意事项:1、开机前须检查各槽液位是否正常;2、插板时须一片一片的插;3、黑化好的板做首件、自主检查时需垂直向上取板且手指不能拿入单元内;4、黑化OK板预叠前所停放的时间不能超过一小时;5、生产的合格黑化板必须在24小时之内压合完毕,否则超过时间需要新烘烤或重工;6、卸板时需两手平行从飞靶上取出,轻放板上,防止动作不规范造成板面刮伤;7、检查黑化颜色均匀不均匀、漏不漏铜、刮伤、有没有烘干;8、HTG170以上只能在白班做;9、检查压力表;10、参数:微蚀35±2℃,室温32.8℃,黑化75±5℃,热水洗50±3℃,后侵28±5℃,热纯水洗50±3℃,烘干一:120±10℃,烘干二:120±10℃,烘干三:120±10℃,共用35分,清洁:50分8、棕化处理(TG150℃以上的不做棕化)作业流程:上料→酸洗(温度:30±5℃,浓度: 5±2%H2SO4,压力:上压1.5±0.2㎏/C㎡,下压1.5±0.2㎏/C㎡)→水洗(压力:上压1.0±0.2㎏/C㎡,下压1.0±0.2㎏/C㎡)→清洁(温度:50±2℃,压力:上压1.5~2.5㎏/C㎡,下压1.5~2.5㎏/C㎡,碱度:0.96±0.1N)→纯水洗(压力:上压1.0±0.2㎏/C㎡,下压1.0±0.2㎏/C㎡)→预侵(温度:30±3℃,强度:70~100%,酸度:0.06~0.12N,速度:3.6±0.2m/min)→棕化(温度:38~45℃,酸度:1.8~2.3N,CB2218A强度:90~120%,CB2218B强度:150±30%,H2O2:11.5±2g/l,CU2+<50g/l,微蚀量:40~80u″,速度:3.6±0.2m/min)→纯水洗(压力:上压1.0±0.2㎏/C㎡,下压1.0±0.2㎏/C㎡)→干燥1(温度:90±5℃)→干燥2(温度:90±5℃)→收板→检查注意事项:1、每天须做首件,检查各个参数是否合格;2、生产的合格棕化板必须在小时之内压合完毕;3、做完后,检查颜色均匀度、是否漏铜、是否刮伤;4、检查压力表;9、压合①、PP裁切工作流程:安装PP→调整刀具(上下间隙为0.08mm)→开机→长度设定(控制单位inch换mm,裁板尺寸依OP单规定)→速度设定→张数设定→加工作业(在更换裁切不同的TG材料前必须把机台上的粉尘清理干净后方可裁切)→手动部分→收料注意事项:1、温度:22±5℃,湿度:50±10℃;2、PP的经向、纬向一定要根据OP来裁切:3、裁切OK的PP可以静至一个月,超过时间不能用;4、裁切好的TG180℃PP用红色大字报表示,TG140℃的PP用白色大字报表示,TG150℃的PP用黄色大字报表示;5、裁好HTG的PP不能超过6小时;6、裁切首片,测量尺寸是否与OP单要求的尺寸相符;②、预叠(温度:20~18℃,湿度:55±5%)⑴、熔合(六层板或六层板以上)工作流程:开机(检查三点组合)→机台调整(检查定位pin位置是否于板的对位孔相重合)→参数设定→加工作业→关机⑵、铆合(六层板或六层板以上)工作流程:开机→机台调整→调整铆钉→加工作业→关机注意事项:1、预叠前,先看板是否有刮伤、颜色是否均匀等,方可叠合;2、熔合、铆合必须做首件,检查是否合格;3、熔合、铆合要求L2、L5朝外,L3、L4向里;4、隔2小时测量一次铆钉高度,铆钉高度的范围:1.27±0.2mm;5、熔合的温度不做限制,但是就好在340~360℃,时间:加光板的是30~33秒,其他的是22秒③、叠合(温度:22±2℃,湿度:60±5℃)工作流程:准备工作(铜箔、无尘纸、粘尘布、钢板)→清洁机台→检查铜箔→选择排版数→参数设定→叠板注意事项:1、读取工单叠合图所用铜箔规格、产商等,检查机台铜箔是否一致,否则更换;2、根据生产胺尺寸计算在钢板上的排版面积,排版所在钢板上的利用率尽可最大,在排版台上调整红外线固定排版位置或方向;3、根据SOP规定,生产板层数设定排版层数,排版总高度必须高于防滑块高度;4、把板放在红外线固定位置上,叠板时不能在叠台上齐板或抖动PP,叠板动作要轻快;5、六层板要求11叠,四层板12叠④、压合作业流程:开机→设立压合参数→上机→热压→冷压→下机注意事项:1、热板温度测试:180℃恒温10分钟状态,每个热盘取9点,使用感温探针直接测试;2、每6个月测试一次热板,正常热板温差为3.0℃±1.5℃;3、热盘平行度测试:①取直径3.0mm铅条,各热盘放置5根铅条并注意避开盘面滚珠依左右平均放置;②放置后以100psi压力压合10分钟;③取该热盘每一点值与该热盘所有点的平均值对比其差异值小于±0.03mm,否则进行维修,每年测试一次;4、热压真空度:700mmHg以上,热盘温度及压力:依附件之温度及压力设定;5、冷压系统压力设定:100~125㎏/C㎡(板面压力为85~105psi),时间:50min,冷压的降温速率为5℃/min下,冷压后板面的实际温度设定为53℃以下压合程式一览表:阶段T(℃)(±5℃)t(min)(±0.1min)P(psi)(±3psi)t(psi)(±0.1min)1 150 13 100 132 150 12 300 123 195 25 400 254 195 65 400 655 185 5 300 56 180 3 150 37 170 2 50 2 Total 125 125阶段T(℃)(±5℃)t(min)(±0.1min)P(psi)(±3psi)t(psi)(±0.1min)1 150 13 100 152 150 12 300 133 195 25 400 274 195 65 400 605 185 5 300 56 180 3 150 37 170 2 50 2Total 125 125压合程式执行完毕;②超出5分钟外来电时,将压合板取出,把表面PP及铜箔撕掉,再做一次黑化制程,后续正常作业(注:1、黑化制程不能做微蚀处理;2、只能适用于无阻抗控制板子)压合扳子取出→PP及铜箔撕掉→黑化→后续正常作业2、在压合程式第二阶段时停电停机因此时PP的树脂开始融化流动,有大量气泡存在不能重工3、在压合程式第三阶段(高压段)时停电停机①在压合程式第三阶段(高压段上压1~50分钟)时停电停机,因此时PP的树脂开始融化流程,有大量气泡存在不能重工②在压合程式第三阶段(高压段上压50分钟以上)时停电停机,此时树脂已固化,保证足够固化时间即可来电后接着该压合程式执行,下压后须测TG值、热冲击爆实验、介质厚度测试,判定是否合格10、裁切→捞边→铣靶→钻靶→磨边①磨边作业流程:开机→送板→磨边(根据不同板厚调整刀具的位置每次更换刀具后应做一次对应位置检测,进给量每边磨掉0.5mm左右即可)→洗板(传输速度:5.5±0.5m/min,水洗压力:第一段1.0±0.5㎏/C㎡,第二段1.5±0.5㎏/C㎡,第三段1.0±0.5㎏/C㎡)→烘干→收板11、钻孔多层板作业流程:钻孔工具准备→程式输入→裁定位PIN→上料→钻孔作业→下机台检验→刷磨去毛头双面板作业流程:磨板边→上PIN→钻孔工具准备→程式输入→上料→钻孔作业→下PIN→下机台检验→刷磨去毛头注意事项:1、核对OP,所取钻头是否合乎OP上之尺寸;2、检查钻头条件:进刀速、转速、孔限数设定,这些参数根据钻针大小、材质来设定的;3、打PIN (PIN直径:0.123″,深度12.5mm);4、铝垫板必须能涵盖所有的孔,以免断针;5、孔径15.7mil以下(﹤1.5mil),钻孔片数双面板2片,4-10层板2片;孔径15.7mil以上(≧15.7mil),钻孔片数双面板3片,4-6层板3片,8-10层板2片;6、钻孔前要空跑孔数,确认无误;7、胶带距离板边小于0.8cm;8、冰水机温度:19±2℃;9、喷锡板使用手推磨机600﹟,化金板、化银板、OSP 板、金手指板使用800﹟~1000﹟;10、检查备针是否备错,测量大小;11、钻孔、刷磨完后,用X-RAY孔位检查机检查是否钻偏;12、温度:22~25℃,湿度:45~50%;13、检查铝片上的压痕,确认压力角是否水平重工流程:检查并输入钻孔程式→上料→找孔→下料→检查①因停电、停气、断针等造成的漏孔、孔未钻透的板子检查后按照重工流程重工②因用错针造成孔小的板须重工12、去胶渣与化学铜目的:钻孔中造成高温产生胶渣黏于内层铜箔上,此胶渣会造成内层OPEN,所以要去胶渣工作流程:上板→酸洗(压力:1.0±0.2㎏/C㎡,H2SO4:3~5%)→水洗(压力:1.7±0.3㎏/C㎡)→刷磨(刷痕:1.0±0.2cm,电流:2.8±0.5A)→水洗(压力:1.7±0.3㎏/C㎡)→高压水洗(38±2㎏/C㎡)→超音波水洗(温度:40±5℃,电流:2.5±0.2A)→水洗(压力:1.7±0.3㎏/C㎡)→烘干(温度:75±5℃)→收板注:传动速度:3.5±0.5m/min;刷磨完成后的板子,须于12小时内完成一铜电镀作业13、一铜线工作流程:上架(抽样方式检视板子是否有严重凹陷及刮伤)→膨胀剂(Normal FR-4 材料:温度67~73℃,强度:10~16%;HTG材料:温度72~80℃,强度:13~16%,NaOH浓度:0.75~1.1N)→高锰酸钾(Normal FR-4 材料:温度72~78℃;HTG材料:温度76~80℃,NaOH浓度:1.0~1.4N,KmnO4浓度:45~65g/L,Mn6+:须保持在25g/L以下)→预中和(H2SO4浓度:2~4%,H2O2浓度:1.0~2%)→中和(温度:42~46℃)→碱性清洁(温度:47~51℃,碱当量:0.012~0.018N)→微蚀(温度:25~30℃,H2O2浓度:2~5%,SPS浓度:40~70g/L,CU﹥25g/L更槽)→预侵(温度:28~32℃,比重:1.100~1.1600,CU:少于1500PPM)→活化(温度:42~46℃,强度:70~100%,氯化亚钾﹥3g/L,比重:1.140~1.1820,CU:少于2000PPM,铁:少于100PPM)→化学铜(温度:30~36℃,CU2+:1.7~2.3g/L,NaOH:9.0~13g/L,甲醛浓度:3~5g/L,EDTA浓度:25~30g/L)→酸侵(H2O2浓度:100~120ml/L)→镀铜(温度:20~30℃,电流密度:14±2ASF,CuSO4.5H2O浓度:60~80g/L,H2SO4浓度:100~120ml/L,HCL浓度:40~80PPM,EP1100B-2:0.7~3.0ml/L,EP1100C-2:2.8~17ml/L)→烘烤(温度控制:95±5℃,速度:4.5±0.5m/min)→下架注意事项:1、每班分析膨胀剂后在添加,每周更换滤芯,每生产84万平方尺换槽;2、高锰酸钾槽,电流控制在1500±50A,不生产时控制在1000±50A,每生产100万平方尺后换槽;3、中和槽每生产15万平方尺后换槽;4、碱性清洁槽每生产6.7万平方尺后换槽;5、预侵槽每生产30万平方尺换槽;6、活化槽每日槽液浓度分析后添加,滤芯2周换一次,每一年换槽一次或CU﹥2000PPM换槽;7、化学铜槽每天依分析后添加,控制在14 ~26 ,每天二次试验控制在8-10级;8、镀铜槽:阳极铜块每星期检视、添加一次一年更换一次,每周做一次Hull Cell试验,每周分析一次槽液,每次分析后添加。
《PCB制板全流程》课件
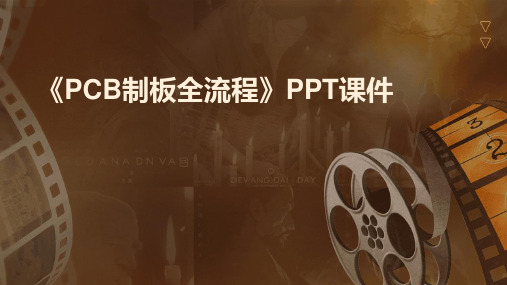
PCB发展趋势
总结词
高密度互连、多层板、柔性板和IC封装基板 是PCB发展的主要趋势。
详细描述
随着电子设备的小型化和智能化发展,PCB 也在不断进步。高密度互连是当前PCB的一 个重要发展趋势,它能够实现更密集的电路 设计和更小的体积。多层板技术能够提高电 路设计的复杂度和设备性能。柔性板能够适 应各种弯曲和折叠的设备形态,具有广泛的 应用前景。而IC封装基板则能够实现芯片级
《PCB制板全流程》PPT课件
• PCB制板简介 • PCB设计流程 • PCB制造工艺 • PCB质量检测与控制 • PCB制板常见问题与解决方案
01
PCB制板简介
PCB定义
总结词
PCB是印刷电路板,是一种重要的电子部件,用于实现电子设备中各个电子元 件的连接。
详细描述
PCB是印刷电路板的简称,是一种将电子元件通过电路连接起来的重要电子部 件。它通常由绝缘材料制成,如FR4或CEM-1,上面覆盖着一层导电线路,用 于实现电子元件之间的信号传输和电力供应。
PCB应用领域
总结词
PCB广泛应用于通信、计算机、消费电子、汽车电子、工业控制等领域。
详细描述
PCB作为电子设备中不可或缺的一部分,被广泛应用于各个领域。通信领域中,PCB用于实现信 号传输和处理;计算机领域中,PCB用于主板、显卡、内存等硬件的制造;消费电子领域中, PCB用于各种智能终端、家用电器等的电路设计;汽车电子领域中,PCB用于实现车辆控制和安
电磁兼容问题表现为电磁噪声、辐射干扰或敏感度过高,可能影响 其他电子设备的正常工作。
解决方案
优化PCB布局和元件选择,减小电磁干扰;采用适当的屏蔽措施, 如金属罩或导电涂料;进行电磁兼容性测试和优化。
最实用的PCB工艺流程培训教材

PCB制造专家
2020/8/ 7
实物组图
开料机
开料后待磨边的板
磨边机
清洗后的板 PCB制造专家
洗板机
2020/8/ 7
磨边机及圆角机
2、内层图形
将开料后的芯板,经前处理微蚀粗化铜面后,进行压干膜或印刷 湿膜处理,然后将涂覆感光层的芯板用生产菲林对位曝光,使需要的线路部 分的感光层发生聚合交联反应,经过弱碱显影时保留下来,将未反应的感光 层经显影液溶解掉露出铜面,再经过酸性蚀刻将露铜的部份蚀刻掉,使感光 层覆盖区域的铜保留下来而形成线路图形。此过程为菲林图形转移到芯板图 形的过程,又称之为图形转移。
PCB制造专家
2020/8/ 7
6、以基材分类:
环
纸基印制板
氧
玻璃布基印制板
树 脂
合成纤维印制板
陶瓷基底印制板
金属芯基印制板
PCB制造专家
20线20/8路7/ 板基材结构
三、多层PCB板的生产工艺流程
开料 内层 压合 钻孔 一铜 干膜 二铜 阻焊 文字 表面处理 成型 电测试 FQC FQA 包装 成品出厂
PCB制造专家
2020/8/ 7
D、显影原理、蚀刻与退膜
感光膜中未曝光部分的活性基团与弱碱溶液反应,生成可 溶性物质溶解下来;未曝光的感光膜与显影液反应被溶解 掉,曝光的感光膜不与弱碱溶液反应而被保留下来,从而 得到所需的线路图形。
蚀刻 退膜
PCB制造专家
2020/8/ 7
实物组图(1)
前处理线
涂膜线
曝光机组
显影后的板
PCB制造专家
显影缸
2020/8/ 7
显影前的板
实物组图(2)
蚀刻缸
蚀刻后的板
514-SMTPCB拿取放作业指导书

文件编号日期工序
机种版本
【目的】
为了使作业员更好的了解如何对PCB拿,取,放的标准操作,并给初学者以指导.【范围】
适用于SMT 车间的所有人员.【职责】
1.生产:执行对PCB拿取放的标准.
2.技术:培训所有人员对PCB的拿取放达成共识.
3.IPQC人员:检查所有人员是否正确的拿取放PCB.【操作内容】
1,PCB板的拿板方式如右图所示:双手捧住PCB的两边(图片1)。
2,PCB板的取板方式:如下图注意两手的动作(图2)。
3,PCB板的放板方式:如右边图所示双手紧抓PCB 两边(图3)。
4,使用正确的PCB拿取放方法作业可以减少人为的抺板,撞件。
注意事项:接触PCB必须带防静电手套.防静电手环。
在印刷工位前装板时要认真检查板面是否有异物.静电手套 ,静电手环 批准:
审核
制作: 李强
工程名
PCB拿取放方法
5,印刷、QC 、维修以及SMT 所有工位在防静电框内装PCB 或PCBA 时,每层只能装 1片拼扳PCB 或PCBA.(一层内严禁多片排放和叠放)
WI-SMT-4-W12514
2018.6.11PCB拿取放作业所有机种
C1
作业顺序及方法
使用工具深 圳 特 发 东 智 科 技 有 限 公 司
PCB拿取放作业指导书
文件名称
图1
图2
图3。
PCB制板工艺操作手册

PCB制板工艺操作手册第1章基础知识 (3)1.1 PCB概述 (3)1.2 制板工艺流程简介 (4)第2章材料准备 (5)2.1 基材选择 (5)2.2 覆铜板处理 (5)2.3 干膜制备 (6)第3章设计与布线 (6)3.1 PCB设计规范 (6)3.1.1 设计原则 (6)3.1.2 设计要求 (6)3.1.3 设计工具 (7)3.2 布线技巧 (7)3.2.1 布线规则 (7)3.2.2 层叠设计 (7)3.2.3 焊盘和过孔设计 (7)3.3 设计审查 (7)3.3.1 审查内容 (7)3.3.2 审查方法 (8)3.3.3 审查流程 (8)第4章制板前处理 (8)4.1 覆铜板切割 (8)4.1.1 材料准备 (8)4.1.2 切割操作 (8)4.1.3 质量检查 (8)4.2 钻孔与孔金属化 (8)4.2.1 钻孔 (8)4.2.2 孔金属化 (8)4.2.3 质量检查 (8)4.3 黑化处理 (8)4.3.1 材料准备 (9)4.3.2 黑化处理操作 (9)4.3.3 清洗与干燥 (9)第5章光绘与显影 (9)5.1 光绘工艺 (9)5.1.1 设备准备 (9)5.1.2 光绘参数设置 (9)5.1.3 光绘操作步骤 (9)5.1.4 注意事项 (9)5.2 显影工艺 (9)5.2.1 显影设备准备 (9)5.2.3 显影操作步骤 (10)5.2.4 注意事项 (10)5.3 质量检查 (10)5.3.1 检查方法 (10)5.3.2 检查内容 (10)5.3.3 处理措施 (10)第6章化学镀与电镀 (10)6.1 化学镀铜 (10)6.1.1 原理概述 (10)6.1.2 化学镀铜溶液组成 (10)6.1.3 操作步骤 (11)6.1.4 注意事项 (11)6.2 电镀铜 (11)6.2.1 原理概述 (11)6.2.2 电镀铜溶液组成 (11)6.2.3 操作步骤 (11)6.2.4 注意事项 (11)6.3 电镀锡铅 (11)6.3.1 原理概述 (11)6.3.2 电镀锡铅溶液组成 (12)6.3.3 操作步骤 (12)6.3.4 注意事项 (12)第7章蚀刻与去膜 (12)7.1 蚀刻工艺 (12)7.1.1 蚀刻原理 (12)7.1.2 蚀刻前准备 (12)7.1.3 蚀刻操作 (12)7.1.4 蚀刻后处理 (12)7.2 去膜工艺 (13)7.2.1 去膜原理 (13)7.2.2 去膜前准备 (13)7.2.3 去膜操作 (13)7.2.4 去膜后处理 (13)7.3 质量检查 (13)7.3.1 蚀刻质量检查 (13)7.3.2 去膜质量检查 (13)7.3.3 异常处理 (13)第8章表面处理 (13)8.1 热风整平 (13)8.1.1 工艺简介 (14)8.1.2 工艺流程 (14)8.1.3 注意事项 (14)8.2 沉金处理 (14)8.2.2 工艺流程 (14)8.2.3 注意事项 (14)8.3 阻焊油墨印刷 (15)8.3.1 工艺简介 (15)8.3.2 工艺流程 (15)8.3.3 注意事项 (15)第9章焊接与组装 (15)9.1 表面贴装技术 (15)9.1.1 表面贴装概述 (15)9.1.2 焊膏印刷 (15)9.1.3 贴片 (16)9.1.4 回流焊接 (16)9.2 通孔焊接 (16)9.2.1 通孔焊接概述 (16)9.2.2 焊料选择 (16)9.2.3 焊接过程 (16)9.3 检验与返修 (16)9.3.1 检验 (16)9.3.2 返修 (17)第10章质量控制与验收 (17)10.1 制板过程质量控制 (17)10.1.1 制程参数监控 (17)10.1.2 在线检测 (17)10.1.3 抽样检测 (17)10.1.4 工艺优化与改进 (17)10.2 成品验收标准 (17)10.2.1 外观检查 (17)10.2.2 尺寸测量 (17)10.2.3 功能性测试 (17)10.2.4 无铅焊接适应性测试 (18)10.3 故障分析与排除方法 (18)10.3.1 故障分类 (18)10.3.2 故障原因分析 (18)10.3.3 故障排除方法 (18)10.3.4 预防措施 (18)第1章基础知识1.1 PCB概述印刷电路板(Printed Circuit Board,简称PCB)是电子设备中用于支撑和连接电子元件的一种基础组件。
PCB工艺流程课件

弹出如下图选择安装路径,点击
,更改安装位置;点击继续安装在默
认“C:\Program Files\Circuit Workstati文件夹中
选择安装目录后,单击下一步,根据提示,单击安装钮完成软件的安装。 软件安装完毕,桌面和开始菜单中会出现CircuitWorkstation图标。
2) 相机安装
光绘文件和钻孔文件生成后,需要把它们的坐标统一。(Protel 99 SE中默 认为不统一。) 因为钻孔文件的默认坐标系是Center plots on,所以需把Gerber 文件的坐标系改成和钻孔的一致。在sp2的Protel99SE中,右键单击Gerber output1 文件,选择属性(Properties),如图选择高级(Advanced)选项,去掉其它 (Other)中的Center plots on选项复选框,单击OK即可。
• 1.2 结构
底板 标尺
上刀片 下刀片 压杆 后支点
• 1.3、技术参数 • 1)产品用途:进行PCB覆铜板的快速裁剪; • 2)裁剪材料:能适合0-1mm各种薄金属板材(铜、铝等),0-3mm各种软性板材(PVC、
PP、覆铜板、复合板等)的快速裁剪;
• 3)设备采用杠杆原理,使得裁剪轻松省力; • 4)最大裁板宽度:300mm,最大裁板长度:不限制; • 5)最大裁板厚度:3mm; • 6)刀具材料:采用进口钨钢高速刀具钢; • 7)★带透明保护罩,保障安全操作; • 8)★配置不锈钢刻度盘,具有垂直和纵向尺寸标尺 精确裁板。
下面输出钻孔加工文件。在CAM Outputs文件栏中,单击鼠标右键,选择 CAM Wizard,出现同下图的加工文件类型选择界面,此次选择数控钻孔文件NC Drill。
单击下一步,在后续数字格式设置界面中,同样设置单位为毫米,整数和小数位数 为4:4,单击Finish(完成),生成钻孔文件NC Drill Output1。
PCB流程教材
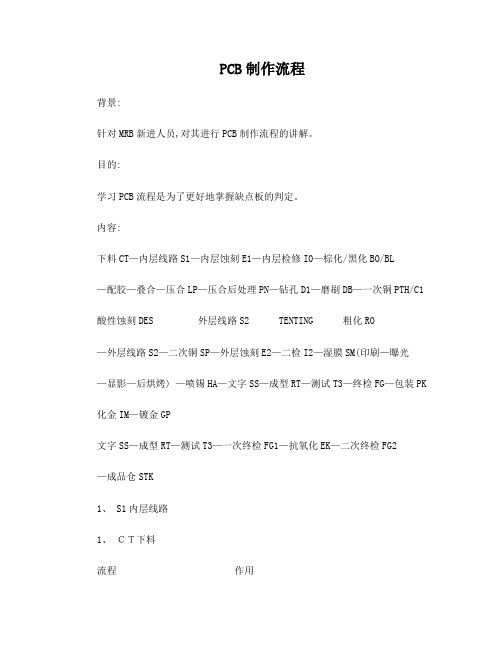
PCB制作流程背景:针对MRB新进人员,对其进行PCB制作流程的讲解。
目的:学习PCB流程是为了更好地掌握缺点板的判定。
内容:下料CT—内层线路S1—内层蚀刻E1—内层检修I0—棕化/黑化BO/BL—配胶—叠合—压合LP—压合后处理PN—钻孔D1—磨刷DB—一次铜PTH/C1 酸性蚀刻DES 外层线路S2 TENTING 粗化RO—外层线路S2—二次铜SP—外层蚀刻E2—二检I2—湿膜SM(印刷—曝光—显影—后烘烤) —喷锡HA—文字SS—成型RT—测试T3—终检FG—包装PK 化金IM—镀金GP文字SS—成型RT—测试T3—一次终检FG1—抗氧化EK—二次终检FG2—成品仓STK1、 S1内层线路1、CT下料流程作用上板将要裁切的基板垫上面板,以保护基板裁切通过马带动钻石锯片,将大块基板按设计经纬方向裁切成工单所需尺寸磨圆角基板裁切所需尺寸后,板角尖厉,磨圆角是减少板面刮伤以及便于下制程作业下料按工单叠放板子以送下制程目的:对客户所需产品的基板类型进行一定尺寸的裁切。
2、内层干膜前处理流程作用放板自动放板,并保持一定的间距酸洗去除板面油污,指污及轻微氧化水洗*3 清洗板面残留药液及微粒,保持微蚀槽微蚀提升铜面粗糙度,增加铜面表面积和干膜附着力水洗*3清洗微蚀槽后铜面药液及微粒超音波水洗利用超音波振荡清洗板面水洗3 充分清除板面残留物吹干干燥板面,防止氧化3、压膜流程作用板面清洁清洁板面,除去静电中心对位双边整板,使板子中心与干膜贴附贴/压膜一定温度下,压力下将干膜贴在板面上翻板冷却充分冷却,避免影响曝光底片的胀缩收板自动收板至台车4、曝光流程作用自动放板自动放板并保持一定间距板面清洁去除板面灰壁,膜屑等异物定位保证板与底片位置正确曝光利用照相机原理,通过UV光照射及黑白底片的遮挡,使板面遮护膜发生反应,形成聚合与未聚合之干膜,达成影象转移静置待聚合反应完全收板自动收板4.1 干膜的组成:1、粘合剂 2、单体 3、光引发剂 4、增塑剂PE聚脂 MalayPhoto resist 干膜PET 聚乙烯4.2 底片种类分为棕片和黑片,一般对曝光要求不是很高的板子用的都是棕片,因为黑片的成本较高且夺命较长。
(完整版)PCB全流程讲解精讲
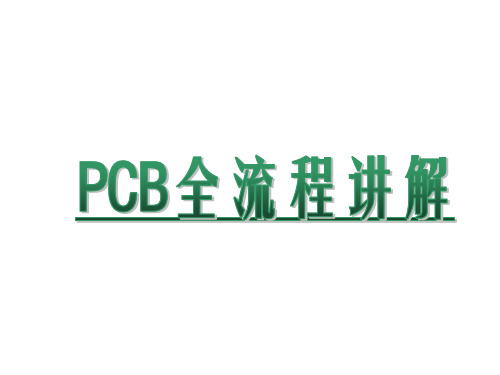
压板(铆合)
铆合:(铆合;预叠) 目的:(四层板不需铆钉)
铆钉
2L
3L
➢ 利用铆钉将多张内层板钉在一起,以避免
4L
后续加工时产生层间滑移;邦定是将板边 熔合窗位置加热与P/P黏结,进一步防止
5L
层间滑移。
主要原物料:铆钉;P/P
➢ P/P(PREPREG):由树脂和玻璃纤维布组成,
人工对AOI的测试缺点进行确认
注意事項: ➢ VRS的确认人员不光要对测试缺点进行确认,另外就是对
一些可以直接修补的确认缺点进行修补
压板(流程)
流程介绍:
棕化
铆合
叠板
压合
后处理
目的:
邦定
➢ 将铜箔(Copper)、胶片(Prepreg)与氧化处理后的内层 线路板压合成多层板
压板(棕化)
棕化: 目的: ➢ (1)粗化铜面,增加与树脂接触表面积 ➢ (2)增加铜面对流动树脂之湿润性 ➢ (3)使铜面钝化,避免发生不良反应 主要原物料:棕化药水
Layer 1 Layer 2 Layer 3 Layer 4 Layer 5 Layer 6
压板(压合)
压合: 目的:通过热压方式将叠合板压成多层板 主要原物料:牛皮纸;钢板
压力
可叠很多层
加热盘
钢板 牛皮纸 承载盘
压板(结构)
压板机的结构: 液压系统:多层板的压合机多数都采用液压系统提供各开口的闭合与加压。 即:压机顶部的热盘固定于压机的主体结构上,其它各开口的热盘由液压系统推动闭合与加压。 如下图所示:
内层制作(流程及目的)
流程介绍:
开料
前处理
PCB板生产工艺和制作流程(详解)
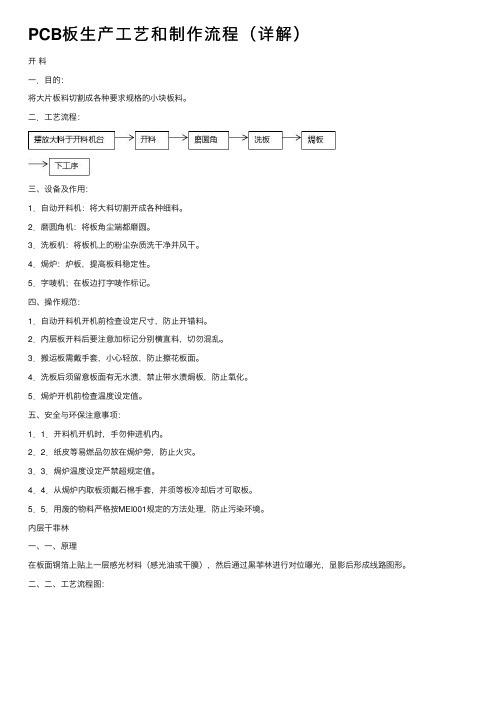
PCB板⽣产⼯艺和制作流程(详解)开料⼀.⽬的:将⼤⽚板料切割成各种要求规格的⼩块板料。
⼆.⼯艺流程:三、设备及作⽤:1.⾃动开料机:将⼤料切割开成各种细料。
2.磨圆⾓机:将板⾓尘端都磨圆。
3.洗板机:将板机上的粉尘杂质洗⼲净并风⼲。
4.焗炉:炉板,提⾼板料稳定性。
5.字唛机;在板边打字唛作标记。
四、操作规范:1.⾃动开料机开机前检查设定尺⼨,防⽌开错料。
2.内层板开料后要注意加标记分别横直料,切勿混乱。
3.搬运板需戴⼿套,⼩⼼轻放,防⽌擦花板⾯。
4.洗板后须留意板⾯有⽆⽔渍,禁⽌带⽔渍焗板,防⽌氧化。
5.焗炉开机前检查温度设定值。
五、安全与环保注意事项:1.1.开料机开机时,⼿勿伸进机内。
2.2.纸⽪等易燃品勿放在焗炉旁,防⽌⽕灾。
3.3.焗炉温度设定严禁超规定值。
4.4.从焗炉内取板须戴⽯棉⼿套,并须等板冷却后才可取板。
5.5.⽤废的物料严格按MEI001规定的⽅法处理,防⽌污染环境。
内层⼲菲林⼀、⼀、原理在板⾯铜箔上贴上⼀层感光材料(感光油或⼲膜),然后通过⿊菲林进⾏对位曝光,显影后形成线路图形。
⼆、⼆、⼯艺流程图:三、化学清洗1. 1.设备:化学清洗机2. 2.作⽤:a. 除去Cu表⾯的氧化物、垃圾等;b. 粗化Cu表⾯,增强Cu表⾯与感光油或⼲膜之间的结合⼒。
3. 3.流程图:4. 4. 检测洗板效果的⽅法:a. a. ⽔膜试验,要求≥30s5. 5. 影响洗板效板的因素:除油速度、除油剂浓度、微蚀温度、总酸度、Cu2+浓度、压⼒、速度6. 6. 易产⽣的缺陷:开路(清洗效果不好导致甩菲林),短路(清洁不净产⽣垃圾)。
四、辘⼲膜1. 1. 设备:⼿动辘膜机2. 2. 作⽤:在铜板表⾯上贴上⼀层感光材料(⼲膜);3. 3. 影响贴膜效果的主要因素:温度、压⼒、速度;4. 4. 贴膜易产⽣的缺陷:内短(菲林碎导致Cu 点)、内开(甩菲林导致少Cu);五、辘感光油1. 1. 设备:辘感光油机、⾃动粘尘机;2. 2. 作⽤:在已清洗好的铜⾯上辘上⼀层感光材料(感光油);3. 3. 流程:4. 4. 影响因素:感光油粘度、速度;焗板温度、速度。
《PCB工艺流程》课件

根据电路的复杂性,确定PCB板的层数。
4
确定布线方式
选择适当的布线方式,确保信号传输的有效性。
5
制定PCB布局规则
定义PCB布局规则,包括元件间距、信号线走向等。
PCB制作流程
1
制作印刷电路板
通过特殊工艺制作出印刷电路板的基本结构。
2
印刷底片
使用光敏材料制作出印刷电路板的底片。
3
感光
通过感光化学反应形成电路路径。
作用
PCB提供了电子元件连接的支持平台,实现电子设备的正常运行。
种类
常见的PCB种类包括单面板、双面板和多层板,根据电子设备的需求选择合适的种类。
PCB的设计流程
1
原理图设计
通过软件绘制电路的原理图,为后续设计提供基础。
2
确定PCB板的尺寸
根据电路的复杂程度和实际需求,确定PCB板的尺寸。
3
确定PCB板的层数
印刷电路板质量问题
可能出现印刷不清晰、电 路线路打断等问题,需要 提高制作工艺。
夹持力问题
可能出现夹持力不足、松 动等问题,需要注意元器 件的安装和焊接。
结论
1 PCB工艺流程的重要性
PCB工艺流程的良好实施,能够确保电子设备的稳定性和可靠性。
2 PCB工艺流程的改进方向
面对生产常见问题,需要不断改进制作工艺和质量管理体系。
4
显影
去除未感光区域的感光胶,暴露出电路路径。
5
金属化
在显影后,通过化学镀铜使电路路径导电。
PCB质量检测
1 监测层间短路
使用专业设备检测PCB板的层间短路情况。
2 测量电导率
检测PCB板的电导率,确保电路通畅。
PCB工艺流程取放板操作

PCB工艺流程取放板操作1. 准备工作:在进行取放板操作之前,需要先进行准备工作。
这包括清洁工作台和操作区域,确认所需工具和物料的准备情况,确保工作环境干净整洁。
2. 取板操作:首先是取板操作。
在这一步中,工作人员需要根据PCB设计图纸和工艺要求来取出需要加工的PCB板。
取板时需要注意轻拿轻放,以免造成板材损坏,同时要确保板材的平整和完整性。
3. 放板操作:放板操作是取板操作的逆过程。
在这一步中,工作人员需要将已经加工完成的PCB板放回到相应的位置或者传递给下一个工序。
放板时要小心操作,以免造成PCB板的损坏。
4. 检查工作:在取放板操作完成后,需要进行检查工作。
检查工作包括检查所取出的板材是否符合要求,是否有损坏或变形等情况。
同时也需要确认所放回的板材是否正确无误。
5. 记录和整理:最后是记录和整理工作。
在取放板操作完成后,工作人员需要及时进行记录,包括所取板材的数量、质量情况等信息。
同时还需要整理工作台和操作区域,将工具和物料按照要求归位。
综上所述,取放板操作是PCB工艺流程中的重要环节,需要严格按照规范和步骤来进行操作,以确保PCB制作的质量和效率。
同时,工作人员在进行取放板操作时需要小心操作,尽量避免造成板材的损坏。
PCB(Printed Circuit Board)即印刷电路板,是电子设备中最常用的一种基础材料。
在PCB制作的工艺流程中,取放板操作是其中一个关键步骤。
正确的取放板操作可以有效地保证PCB板的质量,提高加工效率。
因此,在整个PCB制作流程中,取放板操作的规范流程和严格要求都非常重要。
首先,对于取放板操作,需要有专门的工作人员进行操作,他们需要熟悉PCB的相关知识,掌握取放板的技巧和规范操作流程。
在PCB制作过程中,主要的取放板操作环节包括:下料、插孔、贴片和烘烤等。
不同的工序在取放板操作时会有一些具体的差别,但总体上都需要遵循以下几个基本步骤:首先是准备工作。
在进行取放板操作之前,需要对操作区域进行整理和清洁,确保工作环境干净整洁。
- 1、下载文档前请自行甄别文档内容的完整性,平台不提供额外的编辑、内容补充、找答案等附加服务。
- 2、"仅部分预览"的文档,不可在线预览部分如存在完整性等问题,可反馈申请退款(可完整预览的文档不适用该条件!)。
- 3、如文档侵犯您的权益,请联系客服反馈,我们会尽快为您处理(人工客服工作时间:9:00-18:30)。
培训内容
了解PCB的基础知识 熟悉PCB生产的主要工序及其流程 掌握正确取放、搬运PCB的方法
一、PCB简介
PCB的定义(含义、分类、结构) PCB的作用 PCB的应用领域 PCB常用单位
什么是PCB?
➢ 印制电路板(Printed Circuit Board,PCB),也常被 称为印刷线路板(Printed Wiring Board,PWB)。
–安士(盎司,oz):重量单位,在PCB行业中,为 厚度单位。( 转换过程:将1oz重的铜均匀平铺在 1平方英寸(inch2)的范围内所形成的铜厚度) 1oz=28.3g=1.34mil
二、PCB制造流程
制造流程(八大工序)
内层
压板
钻孔
湿工序
FQC
成型
表面处理
湿菲林
内层—开料
目的:按工程制作(MI)要求,将大块的板料 切割成符合尺寸要求的小板。
1、磨板
2、贴干膜 3、曝光后 4、显影后
5、电铜电锡后 6、退膜后 7、蚀刻后 8、退锡后
流程
内层 压板 钻孔
湿工序 湿菲林 表面处理 成型
FQC
湿工序—外检
目的:检查外层线路是否有开短路、线间线 宽是否符合规格及其外观品质。
流程
内层 压板 钻孔
湿工序 湿菲林 表面处理 成型
FQC
湿菲林—印阻焊油
流程
内层 压板 钻孔
湿工序 湿菲林 表面处理 成型
FQC
本节回顾
• PCB制造流程(八大工序)
内层
压板
钻孔
湿工序
FQC
成型
表面处理
湿菲林
三、正确取放板操作
• PCB制造工艺流程较复杂,要求严格,任何不小心都有可 能造成品质上的缺陷,甚至导致报废。
主要原因就是员工的取放板或搬运作业不够规范,如 碰撞、折弯、摩擦、脱手、挤压等~
目的:在铜面上(焊盘面)进行镀面加工处理。 作用:
1、增强焊盘的可焊性 2、抗氧化
1、沉银
2、沉金
处
理
前
3、喷锡
4、防氧化膜
流程
内层 压板 钻孔
湿工序 湿菲林 表面处理 成型
FQC
成型
目的:把各单元从整件板中分离出来及进行外型加工
1.锣板
主
锣轴刀来自2.啤板冲 针
凹模
线路板
3、V-CUT
刀具
PCB工艺流程取放板操作教 材
纪律宣导
➢ 上课时请把手机调为振动或无声状态; ➢ 上课时不得随意离开座位,不得做任何影响课堂秩序
的事情,如有问题请举手向讲师说明情况; ➢ 上课时请认真做笔记,考试时禁止抄袭,发现抄袭者
,考试成绩作零分处理; ➢ 保持室内干净整洁,垃圾随身带走。
培训目的
PCB简介 PCB制造流程 正确取放板操作
√
正确操作
---戴胶手套 ---双手持板边 ---手不入单元
Χ
不正确操作
---没戴手套 ---手指入单元
• 图片判断5
√
正确操作
---保持板的平直
Χ
不正确操作
---板严重弯曲
• 图片判断6
√
正确操作
---统一方向整齐摆放 ---板面不与其它板边碰撞
Χ
不正确操作
---不统一方向摆放 ---板面与其它板边相碰
➢ PCB有“电子系统产品之母”之称,标准的PCB上头没有 零件,是组装电子零件用的基板,是所有电子信息产品 不可或缺的基本构成要件,也是全球电子元件产品中市 场份额占有率最高的产品。
PCB按层数分类:
1、单面板: 只有一面线路
2、双面板: 双面都有线路
3、多层板: 双面及板中间都有线路
四层板结构示意图
• 图片判断2
√ 正确操作
---戴干净棉线手套 ---手指不入单元 ---双手持板边
Χ
不正确操作
---没戴手套 ---单手抓板、板弯曲 ---手指入单元
• 图片判断3
√
正确操作
---板平放于工作台面 ---板面不与其它碰撞
Χ
不正确操作
---板未平放于工作台面 ---板底面与工作台边产
生磨擦
• 图片判断4
主轴
钻咀
铝片 生产板 垫板
机台
流程
内层 压板 钻孔
湿工序 湿菲林 表面处理 成型
FQC
湿工序—沉铜
目的:在孔内壁沉上铜层。 作用:
导通各线路层,实现信号和电流层级间的传递。
沉铜前
流程
内层 压板 钻孔
湿工序 湿菲林 表面处理 成型
FQC
沉铜后
湿工序—外层线路
目的:将外层线路菲林片上的图形转移到板上
目的:在板的两面印上阻焊油墨
作用:
磨板
1. 保护线路图形
2. 绝缘
印油墨
曝光 显影
流程
内层 压板 钻孔
湿工序 湿菲林 表面处理 成型
FQC
湿菲林—印字符
目的:在板面印上字符 作用:
表明元器件的名称,为电子元器件装配及维修提供标识
流程
内层 压板 钻孔
湿工序 湿菲林 表面处理 成型
FQC
表面处理
123
1米
45 6
流程
内层 压板 钻孔
湿工序 湿菲林 表面处理 成型
FQC
1.2米
磨板 印油墨
曝光 显影 蚀刻 退膜
内层—内层线路
目的:将内层线路菲林片上的 图形转移到板上形成线路。
紫外线光
流程
内层 压板 钻孔
湿工序 湿菲林 表面处理 成型
FQC
内层—内检
目的:检查内层线路是否有开短路、线间线 宽是否符合规格及其外观品质。
本节回顾
1、戴干净专用手套,手不进单元。 2、轻拿轻放,不能拖、拉板,以免擦花板面。 3、双手持板边,板面保持自然平直,不严重变形或曲折。 4、板面不与其它板或任何硬物发生碰撞或磨擦。
4、磨斜边 加工后 角
加工前
度
流程
内层 压板 钻孔
湿工序 湿菲林 表面处理 成型
FQC
厚度
电测
目的:检测各条线路有无开路或短路。
开路
短路
主 机
开短路检测
流程
内层 压板 钻孔
湿工序 湿菲林 表面处理 成型
FQC
FQC--目视检查
目的:检查PCB外观品质
包装
目的:保护产品在运输过程中不被损坏
阻焊油 字符 孔
线路1(外层) 线路2 线路3(内层)
线路4(外层)
焊盘
绝缘层
PCB的作用\运用领域
➢ 导电、传输信号; ➢ 为电子元件固定、组装提供平台支撑;
PCB常用单位介绍
–英寸(inch):英制长度单位 1inch=25.4mm
–密尔(mil):PCB或晶片布局的长度单位 1inch=1000mil
所有员工都能按照规范操作!
1、戴干净专用手套,手不进单元。 2、轻拿轻放,不能拖、拉板,以免擦花板面。 3、双手持板边,板面保持自然平直,不变形或曲折。 4、板面不与其它板或任何硬物发生碰撞或磨擦。
• 图片判断1
练习:
√ 正确操作 ---戴手套 ---手指不入单元 ---双手持板边
Χ 不正确操作 ---没戴手套 ---单手持板 ---手指入单元
流程
内层 压板 钻孔
湿工序 湿菲林 表面处理 成型
FQC
压板
目的:进行线路板的叠加 作用:形成多层线路板之雏形。
高温加热
铜箔
内层板 纤维片(半固化片)
流程
内层 压板 钻孔
湿工序 湿菲林 表面处理 成型
FQC
钢板
压力
钻孔
目的:在多层板上钻出符合要求的孔。 孔的作用:
➢ 提供安装、固定元器件之孔位; ➢ 为后工序实现各层线路导通做准备;