增碳剂的生产流程及选样
增碳剂配方

增碳剂配方
增碳剂配方
一、原料:
(1)碳酸钙:60克;
(2)硫酸铵:20克;
(3)碳酸铵:20克;
(4)硫酸钠:20克;
(5)灰垢:30克;
(6)石灰石:20克;
(7)烧碱:20克;
(8)硫黄:10克。
二、配方:
(1)将碳酸钙、硫酸铵、碳酸铵、硫酸钠的总量加入搅拌桶中,搅拌混合均匀,形成基料;
(2)将灰垢、石灰石、烧碱、硫黄以同样的比例混合在基料中,与基料搅拌均匀;
(3)将混合物倒入模具中,经道模压机压制成碳剂;
(4)完成后,将碳剂进行天然烘焙,使之软硬适度,从而使其变得坚实,不易水解。
三、使用方法:
(1)将配制好的碳剂放置在水池中,等待水流经过;
(2)每次添加量为20-30克,每次添加碳剂后,应等待水流完
全透过,以防止碳剂淤积;
(3)用碳剂增碳,可以提高水质,增碳剂用量不宜过多,否则会影响水质。
炼钢设计原理增碳剂

炼钢设计原理增碳剂
增碳剂是指添加到炼钢炉中的能够增加钢液碳含量的原料,通常是纯碳或含碳化合物的物质。
增碳剂的选择对炼钢的质量和生产效率都有很大影响,因此炼钢设计原理中对增碳剂
的选择非常重要。
增碳剂的选择要考虑以下几个方面:
首先,增碳剂的纯度要求高。
增碳剂的纯度直接影响到炼钢的质量,杂质含量过高会对钢
材性能产生不利影响。
其次,增碳剂的颗粒度要适中。
增碳剂的颗粒度对炼钢工艺有重要影响,颗粒度太粗容易
造成碳元素的不均匀分布,颗粒度太细则会影响增碳剂的溶解速度。
再次,增碳剂的添加方式也要考虑。
增碳剂可以通过喷吹或加入坩埚中等方式添加到炉内,不同的添加方式影响着增碳剂在炉内的分布和溶解速度。
最后,增碳剂的用量也要合理。
增碳剂的用量决定了钢液中碳元素的含量,过量使用增碳
剂会影响钢液的凝固过程,导致晶粒粗大,影响钢材的力学性能。
在炼钢设计原理中,增碳剂的选择和操控要根据炼钢过程中的具体情况来确定,需要综合
考虑各种因素,以保证最终获得符合要求的钢材。
只有在合理选择和操控增碳剂的情况下,炼钢工艺才能取得良好的效果。
增碳剂作为炼钢过程中的重要原料,其质量和用量的选择
至关重要,对钢材的质量和性能都有着不可忽视的影响。
铸造增碳剂生产线

铸造增碳剂生产线引言铸造增碳剂是一种用于铸造行业的关键材料,能够提供合适的碳含量以改善铸造材料的力学性能。
铸造增碳剂生产线是用于生产铸造增碳剂的重要设备,能够实现高效、稳定的生产过程。
本文将介绍铸造增碳剂生产线的工作原理、主要组成部分以及操作流程。
工作原理铸造增碳剂生产线的工作原理基于物料的混合、反应和加工过程。
主要包括下列步骤:1.物料预处理:将所需原料进行筛选、破碎等处理,确保原料质量符合生产要求。
2.混合物料:将经过预处理的原料按照配方比例混合均匀,以确保最终产品的化学成分均匀。
3.反应处理:将混合后的物料送入反应器中,进行化学反应。
这一步骤旨在实现增碳剂的主要反应过程,通常需要一定的温度和压力条件。
4.加工成型:经过反应处理后的物料会被送入加工成型设备中,形成具有一定机械强度和形状的增碳剂产品。
5.降温处理:加工成型后的增碳剂产品需要经过降温处理,以达到适宜的储存和使用温度。
6.检测质量:对生产出的增碳剂产品进行质量检测,确保产品符合相关的技术标准和要求。
主要组成部分铸造增碳剂生产线通常由以下主要组成部分组成:1.原料处理设备:包括物料筛选装置、破碎设备等,用于对原料进行预处理。
2.混合设备:用于将经过预处理的原料按照一定的配方比例混合均匀。
3.反应器:提供一定的温度和压力条件,用于进行化学反应。
4.加工成型设备:将反应后的物料进行成型,形成增碳剂产品。
5.降温设备:用于对加工成型后的增碳剂产品进行降温处理。
6.检测设备:用于对增碳剂产品的质量进行检测,以确保产品符合要求。
7.控制系统:用于对生产线的各个设备进行控制和监测,确保生产过程稳定和安全。
操作流程铸造增碳剂生产线的操作流程如下:1.将原料送入原料处理设备,进行筛选和破碎处理。
2.经过预处理的原料送入混合设备,按照配方比例进行混合。
3.将混合后的物料送入反应器,设定合适的温度和压力条件,进行化学反应。
4.反应后的物料进入加工成型设备,经过成型处理,形成增碳剂产品。
铸造中增碳剂使用

提出了当前对增碳剂的认识存在的误区,以及优质增碳剂的选择。把加增碳剂的熔炼新工艺与传统熔炼(只加生铁)工艺进行对比,分析了增碳剂对熔炼的影响,说明使用中应当注意的问题,阐明了增碳剂的正确使用方法。
关键词:增碳剂;熔炼;
一种含碳量很高的黑色或者灰色颗粒(或块状)的焦碳后续产物,加入到金属冶炼炉里,提高铁液里碳的含量,一方面可以降低铁液里氧的含量,另一方面更重要的是提高冶炼金属或者铸件的力学性能。
所谓增碳剂,就是要在加入后可以有效提高铁液中碳的含量,所以增碳剂的固定碳含量一定不能太低,否则要达到一定的含碳量,就需要加入相比高碳的增碳剂更多的样品,这样无疑增加了增碳剂中其他不利元素的量,使铁液不能获得较好的收益。
低的硫、氮、氢元素是防止铸件产生氮气孔的关键,这样就要求增碳剂的含氮量越低越好。
2、增碳剂加入量对吸收率的影响
在一定的温度和化学成分相同的条件下, 铁液中碳的饱和浓度一定。铸铁中碳的溶解极限为〔C %〕= 113 + 010257 T - 0131〔Si %〕- 0133〔P %〕- 0145 〔S %〕+ 01028〔Mn %〕( T 为铁液温度) 。在一定饱和度下, 增碳剂加入量越多, 溶解扩散所需时间就越长, 相应损耗量就越大, 吸收率就会降低。
4、铁液搅拌对增碳剂吸收率的影响
在增碳剂未完全溶解前, 搅拌时间长, 吸收率高。搅拌有利于碳的溶解和扩散, 减少增碳剂浮在表面被烧损。搅拌还可以减少增碳保温时间, 使生产周期缩短, 避免铁液中合金元素烧损。但搅拌时间过长, 不仅对炉子的使用寿命有很大影响, 而且在增碳剂溶解后, 搅拌会加剧铁液中碳的损耗。因此, 适宜的铁液搅拌时间应以保证增碳剂完全溶解为适宜。
回转炉煅烧增碳剂

回转炉煅烧增碳剂1. 介绍回转炉煅烧增碳剂的概念和作用回转炉煅烧增碳剂是一种用于钢铁生产中的辅助材料,主要用于增加炉料中的碳含量。
它由多种原料混合而成,经过特定的工艺处理后形成颗粒状,方便在回转炉中使用。
回转炉煅烧增碳剂在钢铁冶炼过程中起到了重要的作用,可以提高钢铁的质量和生产效率。
2. 回转炉煅烧增碳剂的原料和制备工艺回转炉煅烧增碳剂的原料主要包括焦炭、石墨、石油焦、木炭等。
这些原料经过破碎、筛分等处理后,按照一定比例混合,再进行加热、煅烧等工艺处理,最终形成所需的颗粒状增碳剂。
制备工艺主要包括以下几个步骤: 1. 原料准备:将焦炭、石墨、石油焦、木炭等原料进行破碎、筛分等处理,确保原料的粒度符合要求。
2. 混合配比:根据所需的成分比例,将不同原料按照一定比例混合。
3. 加热处理:将混合后的原料放入高温炉中进行加热处理,使其达到一定的温度。
4. 煅烧处理:将加热后的原料进行煅烧处理,使其形成颗粒状增碳剂。
5. 冷却和包装:将煅烧后的增碳剂进行冷却,并进行包装,以便于储存和运输。
3. 回转炉煅烧增碳剂的作用机理回转炉煅烧增碳剂在钢铁冶炼过程中的作用主要有两个方面:3.1 增碳作用回转炉煅烧增碳剂中的原料富含碳元素,当增碳剂投入回转炉中时,其碳元素会与炉料中的铁元素进行反应,生成高碳的铁合金。
这样可以增加炉料中的碳含量,提高钢铁的碳含量,使钢铁的强度、硬度等力学性能得到提高。
3.2 清洁作用回转炉煅烧增碳剂中的原料中还含有一定比例的灰分和硫等杂质。
当增碳剂投入回转炉中时,这些杂质会与炉料中的杂质进行吸附、还原等反应,从而减少钢铁中的杂质含量,提高钢铁的纯净度和质量。
4. 回转炉煅烧增碳剂的应用回转炉煅烧增碳剂主要应用于钢铁冶炼过程中。
在回转炉中,增碳剂可以通过喷吹、撒播等方式加入,与炉料一起进行反应。
增碳剂的投入量和投入时间可以根据具体的冶炼工艺和产品要求进行调整。
通过使用回转炉煅烧增碳剂,可以有效提高钢铁的质量和生产效率。
增碳剂的参数

增碳剂的参数
增碳剂是一种用于钢铁生产过程中增加碳含量的添加剂,其参数主要包括以下几个方面:
1. 粒度:增碳剂一般是粉末状或颗粒状,其粒度对于钢铁生产
过程中的使用效果有很大影响。
一般来说,粒度越细的增碳剂,其反应速度越快,但是也容易产生粉尘污染问题。
2. 碳含量:增碳剂中的碳含量是非常重要的参数,一般需要根
据具体生产需要来选择适当的碳含量。
碳含量越高的增碳剂,在使用过程中就需要使用的量越少,同时还可以降低生产成本。
3. 含杂质:增碳剂在生产过程中需要经过高温处理,如果含有
过多的杂质,就会对生产过程产生负面影响。
因此,在选择增碳剂时,需要注意其含杂质的情况,选择纯度较高的产品。
4. 熔点:增碳剂在生产过程中需要与钢水充分混合,因此其熔
点也是一个重要参数。
熔点过高的增碳剂需要更高的温度才能达到熔化状态,而熔点过低的增碳剂则容易在生产过程中出现结块问题。
总之,在选择增碳剂时,需要综合考虑以上各个参数,根据具体的生产需要来选择适当的产品,以确保生产过程的稳定性和经济效益。
- 1 -。
增碳剂的生产工艺

增碳剂的生产工艺增碳剂是一种广泛应用于冶金、化工、建材等行业的产品,其生产工艺主要包括以下几个步骤:原材料选用、制粒、煅烧、破碎和包装。
首先,原材料的选用是增碳剂生产的关键环节。
一般来说,选用的原材料主要包括石墨、石油焦、木炭等。
这些原材料具有较高的碳含量和热值,能够为增碳剂的生产提供足够的碳原子,并具备良好的导电性和抗热性。
其次,制粒是将选用的原材料进行粉碎、混合和造粒的过程。
首先,原材料经过破碎机进行初步破碎,将颗粒大小控制在一定范围内。
然后,将破碎后的原料放入混合机中,与其他辅助成分进行充分混合。
最后,通过造粒机将混合好的原料进行制粒,以得到具有一定大小和形状的颗粒状增碳剂。
接下来,煅烧是将制粒好的增碳剂进行高温处理的过程。
煅烧的目的是使原材料中的有机物和水分脱除,并提高增碳剂的密度和热值。
一般采用的煅烧设备有回转窑和热风炉。
在煅烧的过程中,需要控制好温度和时间,以保证增碳剂的质量和性能。
然后,破碎是将经过煅烧的增碳剂进行粉碎的过程。
破碎的目的是使增碳剂的颗粒大小更加均匀,以便于后续的包装和使用。
常用的破碎设备有颚式破碎机和圆锥破碎机。
通过合理地选择破碎机的参数和操作方式,可以得到满足不同需求的增碳剂产品。
最后,包装是将破碎好的增碳剂进行包装和储存的过程。
一般来说,增碳剂会被包装成袋装或散装两种形式。
袋装一般采用编织袋或纸塑复合袋,以保证增碳剂的密封性和耐候性。
而散装主要用于大型生产企业或直接供应给用户的情况,需要配备相应的储存和装卸设备。
综上所述,增碳剂的生产工艺包括原材料选用、制粒、煅烧、破碎和包装等步骤。
通过合理地控制每个步骤的参数和操作方式,可以生产出满足不同需求的增碳剂产品。
同时,优化生产工艺,提高生产效率和产品质量,对于增碳剂企业的发展具有重要意义。
石墨化石油焦增碳剂的生产流程

石墨化石油焦增碳剂的生产流程石墨化石油焦增碳剂是一种重要的碳素材料,其生产流程涉及多个步骤。
下面将详细介绍石墨化石油焦增碳剂的生产流程。
石墨化石油焦增碳剂的生产需要选择合适的石油焦作为原料。
石油焦是一种副产品,是石油加工过程中产生的固体残渣。
选择高质量的石油焦作为原料是确保石墨化石油焦增碳剂质量的关键。
接下来,将选定的石油焦进行破碎和磨粉处理。
破碎可以将石油焦块状物料打碎成适当的颗粒大小,磨粉则是将破碎后的石油焦进一步细化成所需的颗粒度。
这一步骤的目的是增加石墨化石油焦增碳剂的反应活性和提高生产效率。
然后,将磨粉后的石油焦与一定比例的石墨粉混合。
石墨粉是一种含有高纯度碳素的材料,可以提供额外的碳源,有助于增加石墨化石油焦增碳剂的碳含量。
混合石油焦和石墨粉的比例需要根据具体需求进行调整,以达到预期的碳含量。
接着,将混合后的物料放入高温炉中进行石墨化处理。
石墨化是指在高温条件下,石油焦和石墨粉中的碳元素发生结构转变,形成石墨结构。
这一过程主要是通过碳元素的热解和重排反应来实现的。
高温炉的温度通常在2000℃以上,短时间内完成石墨化处理,确保物料中的碳元素充分转变为石墨结构。
在石墨化过程中,还需要控制适当的保温时间和炉内气氛。
保温时间的控制可以影响石墨化反应的程度,过短的时间可能导致石墨化不完全,而过长的时间则可能造成石墨结构过度长大。
而炉内气氛的选择通常是惰性气体,如氮气或氩气,以避免物料与氧气发生反应。
经过石墨化处理的物料需要进行冷却和筛分。
冷却可以使物料温度降至室温,筛分则是将物料按照颗粒大小进行分类,以得到符合要求的石墨化石油焦增碳剂。
这一步骤的目的是去除过大或过小的颗粒,确保产品的均匀性和一致性。
总结起来,石墨化石油焦增碳剂的生产流程包括原料选择、破碎磨粉、原料混合、石墨化处理、冷却筛分等步骤。
每个步骤都需要严格控制操作条件和参数,以确保产品的质量和性能。
石墨化石油焦增碳剂在冶金、化工等领域有着广泛的应用,其生产流程的优化和改进对于提高产品质量和降低生产成本具有重要意义。
增碳剂的生产流程及选样

一、工艺流程
二、产品描述:
产品选用优质太西无烟煤经800- 1200C煅烧炉煅烧加工制成,是炼钢的理想原料。
三、?用途:
主要用于钢铁冶炼,在钢铁冶炼过程中,有少量的炭已燃烧,并且刚中有氧、硫及磷,加入增碳剂后,一方面增加钢种炭的含量,同
时增碳剂中的碳与钢中的氧、硫及磷产生化学反应,可发挥钢的机械性能。
在冶炼过程中做还原剂用.?性能:
替代传统的石油焦增碳剂,降低炼钢成本.?特性:?低灰.?硫?磷?高发热量•高比电阻
高机械强度?高化学活性•高精煤?回收率.?质量技术指标:?灰分?<6?%水分<
%?军发份<?%固定碳>90%?匕重>cm3含硫<%盐酸可容率<%.?规格:?0---20mm,?按用户要求加工.?固定碳含量(?C%):90---95 。
特点与加工过程:生产的增碳剂主要原料选定用优质的宁夏太西低灰、低硫、低磷、洗精煤,经过煅炉高温煅烧、破碎精选而成,使用过程中,无烟、无异味、增碳稳定、回收率高。
性能:杂质信号少、增碳回收率高,效果明显。
用途:电炉、转炉、炼钢增碳用。
四、规格:
成份含量(%
粒?度,?1-3mm,1-5mm,3-5m m或者根据客户要求;
产品包装:10公斤、25公斤小袋包装,或者1000公斤吨袋包装,或者10公斤25公斤小袋然后装入1000公斤吨袋;或者10公斤25公斤小袋50公斤小袋包装,然后直接装入集装箱;可根据客户要求包装;。
增碳剂生产工艺

增碳剂是一种用于钢铁冶炼中的添加剂,可以提供额外的碳含量,以调整钢铁的化学成分和性能。
以下是常见的增碳剂生产工艺:
原料准备:增碳剂的主要原料包括焦炭、石油焦、木炭、褐煤焦等。
这些原料需要经过破碎、磨粉等处理,以获得适合生产的颗粒度和粉末形态。
配料混合:根据增碳剂的配方要求,将不同比例的原料进行混合。
混合可以通过机械搅拌或喷淋的方式进行,确保原料充分混合均匀。
加热和干燥:将混合好的原料送入加热炉或干燥炉中,通过高温加热或烘干的方式,去除原料中的水分和挥发物,提高原料的热值和稳定性。
压制成型:将干燥的原料送入压力机或造粒机中,进行压制成型。
常见的成型方式包括挤压、压块、造粒等,以获得适合使用的增碳剂颗粒。
焙烧和炭化:将成型好的增碳剂放入焙炉或炭化炉中进行热处理。
热处理的温度和时间根据增碳剂的要求而定,旨在使原料中的碳素发生炭化反应,提高碳含量和热值。
冷却和包装:经过焙烧和炭化后的增碳剂需要进行冷却处理,以降低温度并保持稳定性。
冷却后,增碳剂经过质量检验和筛分等工序,然后进行包装和储存,以便运输和使用。
需要注意的是,具体的增碳剂生产工艺会因厂商、设备和技术等因素而有所不同。
上述工艺仅为一般性描述,实际生产过程可能还涉及其他工序和技术细节。
在实际生产中,应根据具体情况进行工艺设计和操作控制,以确保增碳剂的质量和性能符合要求。
增碳剂的生产工艺

增碳剂的生产工艺增碳剂是一种用于冶金、化工以及其他工业领域的重要原材料,它可以提高钢铁、铸铁、铝制品等金属的碳含量,同时提高其硬度和强度。
增碳剂的生产工艺包括原料选取、制备、加工和包装等环节。
首先,在增碳剂的生产过程中,原料的选择非常重要。
一般而言,增碳剂的主要原料是具有高碳含量的石墨,选择高质量的石墨具有很大的影响。
因此,在原料选择上,需要考虑石墨的碳含量、杂质含量以及石墨的形态等因素。
制备环节是生产增碳剂的核心环节之一。
制备过程中,需要将原料石墨进行破碎和磨粉处理,以便使石墨颗粒达到一定的大小和细度。
这是为了提高增碳剂的反应效果和加工性能。
制备过程中还会添加一定比例的粘结剂,以增加增碳剂的粘结力,使其在使用过程中不易碎裂。
加工环节是制备增碳剂的关键步骤之一。
加工操作通常采用压制成型和煅烧两个步骤。
首先,将制备好的石墨粉末与粘结剂混合均匀,然后通过一定的压制工艺将混合物压制成型。
压制的目的是使石墨颗粒充分结合,并给予增碳剂良好的力学强度和形状。
然后,将压制而成的增碳剂进行煅烧处理,这一步是为了去除残留的有机物质和改善增碳剂的高温性能。
包装环节是生产增碳剂的最后一个环节。
在包装过程中,需要使用适合的包装材料和方法,以防止增碳剂在运输和使用过程中因受潮或受污染而发生质量变化。
常见的包装形式包括纸箱、编织袋和塑料袋等。
同时,在包装过程中需要注明增碳剂的产品名称、规格、批次、生产日期等相关信息,以便追溯产品来源和管理。
总结起来,增碳剂的生产工艺主要包括原料选取、制备、加工和包装等环节。
通过严格控制每一个环节,可以保证增碳剂的质量稳定、性能优良。
随着工业化的不断发展和需求的增加,增碳剂的生产工艺也在不断改进和完善,以适应市场需求和产品质量的提升。
增炭剂生产工艺
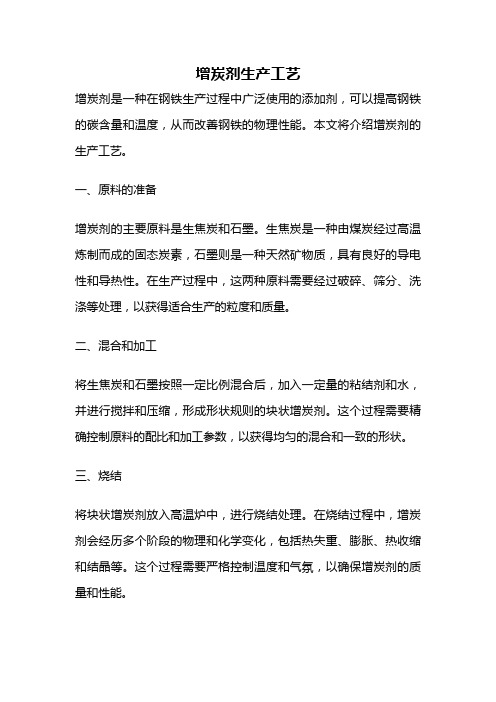
增炭剂生产工艺
增炭剂是一种在钢铁生产过程中广泛使用的添加剂,可以提高钢铁的碳含量和温度,从而改善钢铁的物理性能。
本文将介绍增炭剂的生产工艺。
一、原料的准备
增炭剂的主要原料是生焦炭和石墨。
生焦炭是一种由煤炭经过高温炼制而成的固态炭素,石墨则是一种天然矿物质,具有良好的导电性和导热性。
在生产过程中,这两种原料需要经过破碎、筛分、洗涤等处理,以获得适合生产的粒度和质量。
二、混合和加工
将生焦炭和石墨按照一定比例混合后,加入一定量的粘结剂和水,并进行搅拌和压缩,形成形状规则的块状增炭剂。
这个过程需要精确控制原料的配比和加工参数,以获得均匀的混合和一致的形状。
三、烧结
将块状增炭剂放入高温炉中,进行烧结处理。
在烧结过程中,增炭剂会经历多个阶段的物理和化学变化,包括热失重、膨胀、热收缩和结晶等。
这个过程需要严格控制温度和气氛,以确保增炭剂的质量和性能。
四、包装和存储
经过烧结处理后,增炭剂需要进行包装和存储。
一般采用塑料袋或纸箱包装,并在包装上标注产品名称、规格、生产日期等信息。
在存储过程中,增炭剂需要放置在干燥、通风、无阳光直射的地方,以避免吸湿和氧化。
增炭剂的生产工艺需要精确控制各个环节,从原料准备到烧结处理,再到包装和存储,都需要严格按照工艺要求进行。
只有这样,才能生产出质量稳定、性能优良的增炭剂产品,为钢铁生产提供可靠的支持。
增碳剂——精选推荐

一、基本介绍增碳剂是炼钢时用的一种添加剂。
它是生产优质钢材必不可少的原料。
另外,也是生产电极糊的原料。
增碳剂是个广义词,就是所有能给铁水增加碳含量的物质的统称。
采用石墨粉剂经压制成型,生产铸件时可大幅度增加废钢用量,减少生铁用量或不用生铁,在电炉熔炼中,将增碳剂放在中间,(炉中放一部分料后放增碳剂)加入量度是金属量的1-3%。
增碳剂特点是碳在铁液中吸收效果好,不返渣,使用增碳剂可大幅度降低铸件生产成本。
海关HS编码: 38249030。
二、用途增碳剂在铸造时使用,可大幅度增加废钢用量,减少生铁用量或不用生铁。
目前绝大多数增碳剂都适用于电炉熔炼,也有少部分吸收速度特别快的增碳剂用于冲天炉。
电炉熔炼的投料方式,应将增碳剂随废钢等炉料一起往里投放,小剂量的添加可以选择加在铁水表面。
但是要避免大批量往铁水里投料,以防止氧化过多而出现增碳效果不明显和铸件碳含量不够的情况。
增碳剂的加入量,根据其他原材料的配比和含碳量来定。
不同种类的铸铁,根据需要选择不同型号的增碳剂。
增碳剂特点本身选择纯净的含碳石墨化物质,降低生铁里过多的杂质,增碳剂选择合适可降低铸件生产成本。
三、分类增碳剂分炼钢用增碳剂(中华人民共和国黑色冶金行业标准,YB/T192-2001炼钢用增碳剂)和铸铁用增碳剂,以及其他一些添加材料也有用到增碳剂,譬如刹车片用添加剂,作摩擦材料。
增碳剂属于外加炼钢、炼铁增碳原料。
优质增碳剂是生产优质钢材必不可少的辅助添加剂。
增碳剂的原料有很多种,生产工艺也各异,有木质碳类,煤质碳类,焦炭类,石墨类等,其中各种分类下又有很多小种类。
优质增碳剂一般指经过石墨化的增碳剂,在高温条件下,碳原子的排列呈石墨的微观形态,所以称之为石墨化。
石墨化可以降低增碳剂中杂质的含量,提高增碳剂的碳含量,降低硫含量。
国内目前是3种:一是石墨粉,就是石墨电极加工的吸尘粉。
二是断后石油焦,国内的一些钢铁厂,就是用煅后石油焦(经过煅烧后的石油焦),做增碳剂的。
石墨化增碳剂生产工艺
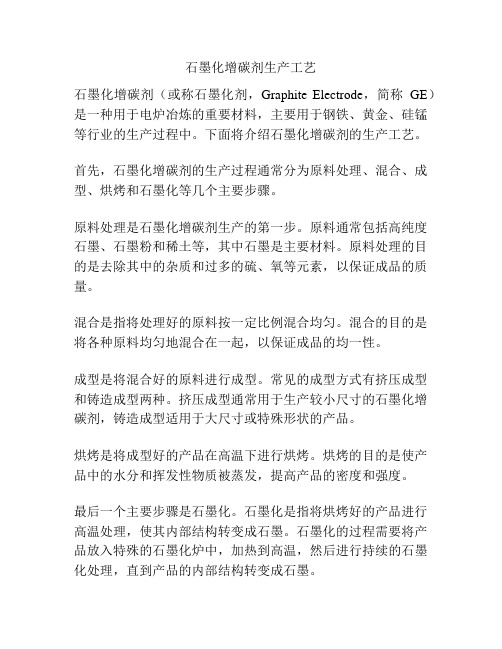
石墨化增碳剂生产工艺石墨化增碳剂(或称石墨化剂,Graphite Electrode,简称GE)是一种用于电炉冶炼的重要材料,主要用于钢铁、黄金、硅锰等行业的生产过程中。
下面将介绍石墨化增碳剂的生产工艺。
首先,石墨化增碳剂的生产过程通常分为原料处理、混合、成型、烘烤和石墨化等几个主要步骤。
原料处理是石墨化增碳剂生产的第一步。
原料通常包括高纯度石墨、石墨粉和稀土等,其中石墨是主要材料。
原料处理的目的是去除其中的杂质和过多的硫、氧等元素,以保证成品的质量。
混合是指将处理好的原料按一定比例混合均匀。
混合的目的是将各种原料均匀地混合在一起,以保证成品的均一性。
成型是将混合好的原料进行成型。
常见的成型方式有挤压成型和铸造成型两种。
挤压成型通常用于生产较小尺寸的石墨化增碳剂,铸造成型适用于大尺寸或特殊形状的产品。
烘烤是将成型好的产品在高温下进行烘烤。
烘烤的目的是使产品中的水分和挥发性物质被蒸发,提高产品的密度和强度。
最后一个主要步骤是石墨化。
石墨化是指将烘烤好的产品进行高温处理,使其内部结构转变成石墨。
石墨化的过程需要将产品放入特殊的石墨化炉中,加热到高温,然后进行持续的石墨化处理,直到产品的内部结构转变成石墨。
整个生产过程中,需要严格控制每个步骤的工艺参数。
如在烘烤过程中,需要控制温度和时间,以保证产品的质量和性能。
同时,生产过程中还需要进行质量检验,以确保产品符合相关的标准要求。
总结来说,石墨化增碳剂的生产工艺包括原料处理、混合、成型、烘烤和石墨化等步骤。
通过严格控制每个步骤的工艺参数和进行质量检验,可以生产出符合要求的石墨化增碳剂产品。
这些产品在电炉冶炼过程中起着重要的作用,推动了相关行业的发展。
石墨化石油焦增碳剂的生产流程

石墨化石油焦增碳剂的生产流程石墨化石油焦增碳剂是一种用于增碳和改善石墨质能力的关键原料。
它通过一系列的生产流程制备而成。
本文将介绍石墨化石油焦增碳剂的生产流程。
生产石墨化石油焦增碳剂的第一步是石油焦的制备。
石油焦是一种具有高固定碳含量和低杂质含量的石墨质材料。
它是从石油煤焦化过程中生成的副产品。
在焦化过程中,石油原料被加热至高温,使其发生裂解和重组,产生石油焦。
石油焦具有良好的石墨化能力和导电性能,是制备石墨化石油焦增碳剂的理想原料。
第二步是石墨化处理。
石墨化处理是通过对石油焦进行高温处理,使其结构发生变化,增加其石墨化程度。
这一步骤通常在电阻炉中进行,石油焦被置于高温环境中,在缺氧条件下进行热处理。
在高温下,石油焦中的非石墨化碳被热解,石墨化程度得以提高。
通过控制石墨化处理的温度和时间,可以调整石墨化石油焦增碳剂的石墨化程度和导电性能。
第三步是增碳处理。
在这一步骤中,石墨化石油焦增碳剂被与其它原料混合,并进行再次加热处理。
这一步骤的目的是将石墨化石油焦增碳剂中的石墨化碳与其它原料中的非石墨化碳结合,增加石墨化石油焦增碳剂的总碳含量。
增碳处理通常在高温环境下进行,原料与石墨化石油焦增碳剂混合后,经过加热处理,使其结合成为一体。
第四步是粉碎和筛分。
在增碳处理后,石墨化石油焦增碳剂需要经过粉碎和筛分的过程,以获得所需的粒度和均匀度。
粉碎通常使用破碎机进行,将增碳剂块状物料破碎成细粉末。
然后,通过筛分设备,将粉末按照所需的粒度进行筛分,以得到符合要求的产品。
最后一步是包装和贮存。
石墨化石油焦增碳剂经过粉碎和筛分后,需要进行包装和贮存。
一般情况下,石墨化石油焦增碳剂被装入塑料袋或大型容器中,并进行密封,以防止湿气和杂质的侵入。
然后,将包装好的产品存放在干燥的仓库中,以确保其质量和性能不受影响。
石墨化石油焦增碳剂的生产流程包括石油焦的制备、石墨化处理、增碳处理、粉碎和筛分以及包装和贮存等多个步骤。
每个步骤的控制和操作都对最终产品的质量和性能具有重要影响。
煤生产增碳剂生产工艺

煤生产增碳剂生产工艺
煤是一种重要的能源资源,煤中含有较高的碳含量,可以作为碳源用于生产碳剂。
碳剂是一种在冶金、化工等领域广泛应用的物质,用于增加炼钢、铸铁等过程中的碳含量,改善金属品质。
下面将介绍煤生产碳剂的工艺过程。
首先,选取适合的煤炭种类作为原料。
煤炭种类影响着碳剂的质量和性能,一般选取含碳高、灰分低的大块煤炭。
原料煤经过破碎、筛分等预处理工序,将煤炭粉碎成合适的颗粒大小。
然后,将预处理后的煤炭送入垂直加热炉。
垂直加热炉是碳剂生产中常用的设备,炉内温度控制在800℃以上。
煤炭在高温下进行碳化反应,煤中的有机物质逐渐分解,放出大量的可燃气体和挥发物质。
接下来,将煤炭在高温下进行反应的气体收集出来,经过净化处理。
收集的气体中含有大量的有机物质,经过冷凝、吸附等工艺,将有机物质分离出来,得到较为纯净的碳化气体。
然后,通过气体分离和净化系统,将碳化气体中的一部分燃烧产生的CO2气体分离出来,保留其他可用的气体组分。
CO2气体可用于其他工艺过程中,例如作为化肥生产中的原料。
最后,经过气体分离和净化处理后得到的可用气体组分进行储存和输送。
碳化气体可用于其他领域,例如冶金工艺中用作碳源,化工工艺中用作原料等。
储存和输送的设备需要具备安全可靠的特性,以保证碳化气体的稳定供应。
总结起来,煤生产碳剂的工艺过程主要包括原料煤的预处理、煤炭的高温碳化反应、气体的分离和净化处理,以及储存和输送等环节。
通过科学合理的工艺控制,可以获得高质量的碳剂产品,为相关行业的生产提供重要的支持。
优质增碳剂的检验标准
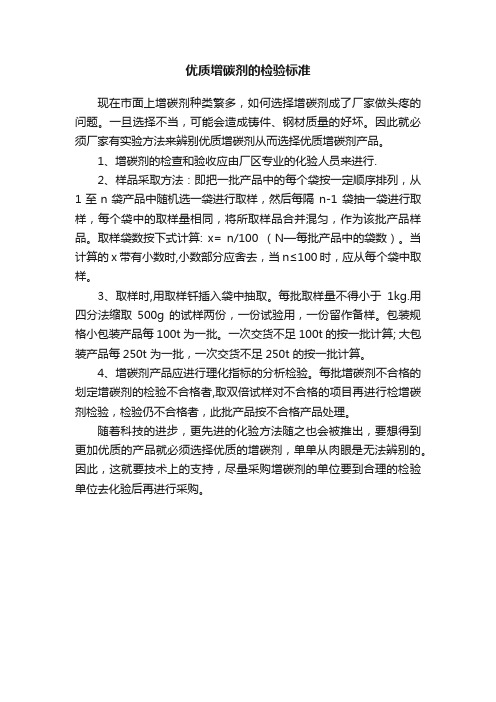
优质增碳剂的检验标准
现在市面上增碳剂种类繁多,如何选择增碳剂成了厂家做头疼的问题。
一旦选择不当,可能会造成铸件、钢材质量的好坏。
因此就必须厂家有实验方法来辨别优质增碳剂从而选择优质增碳剂产品。
1、增碳剂的检查和验收应由厂区专业的化验人员来进行.
2、样品采取方法:即把一批产品中的每个袋按一定顺序排列,从1至n袋产品中随机选一袋进行取样,然后每隔n-1 袋抽一袋进行取样,每个袋中的取样量相同,将所取样品合并混匀,作为该批产品样品。
取样袋数按下式计算: x= n/100 (N—每批产品中的袋数)。
当计算的x带有小数时,小数部分应舍去,当n≤100 时,应从每个袋中取样。
3、取样时,用取样钎插入袋中抽取。
每批取样量不得小于1kg.用四分法缩取500g 的试样两份,一份试验用,一份留作备样。
包装规格小包装产品每100t为一批。
一次交货不足100t 的按一批计算; 大包装产品每250t 为一批,一次交货不足250t 的按一批计算。
4、增碳剂产品应进行理化指标的分析检验。
每批增碳剂不合格的划定增碳剂的检验不合格者,取双倍试样对不合格的项目再进行检增碳剂检验,检验仍不合格者,此批产品按不合格产品处理。
随着科技的进步,更先进的化验方法随之也会被推出,要想得到更加优质的产品就必须选择优质的增碳剂,单单从肉眼是无法辨别的。
因此,这就要技术上的支持,尽量采购增碳剂的单位要到合理的检验单位去化验后再进行采购。
增碳剂生产安全规程

增碳剂生产安全规程1. 背景介绍增碳剂是一种用于钢铁冶炼和铸造过程中的重要辅助材料,可以有效提高钢铁的碳含量,改善钢铁的性能。
然而,增碳剂的生产过程中存在一定的安全风险和隐患,因此有必要制定相应的生产安全规程,以确保生产过程中的人身安全和设备环境的安全。
2. 生产设备与工艺2.1 生产设备增碳剂生产线主要包括料仓、破碎机、混合机、压力机、干燥机、包装机等设备。
这些设备应定期进行维护保养,并配备相应的安全防护装置。
2.2 生产工艺增碳剂生产工艺主要包括原料准备、配比混合、成型压制、干燥烘烤和包装等环节。
在每个环节中都需要注意以下事项: - 原料准备:使用符合质量标准的原料,并确保原料储存区域干燥通风良好,避免火源和静电积聚。
- 配比混合:严格按照配比要求进行混合,避免过量或不足。
混合过程中应使用密闭设备,并注意防止粉尘扬散。
- 成型压制:确保压力机设备正常运行,操作人员需穿戴好防护装备,并遵守相关操作规程。
- 干燥烘烤:控制好干燥温度和时间,避免过高温度引发火灾。
同时,要定期清理干燥机内部的积尘。
- 包装:使用符合标准的包装材料,并保持包装区域整洁。
包装后的增碳剂应储存于干燥通风的库房中。
3. 安全管理措施3.1 安全培训所有从事增碳剂生产工作的人员都应接受必要的安全培训,了解生产过程中存在的安全风险和隐患,学习正确使用安全防护装备和应急处理措施。
3.2 安全设施在生产现场设置明显的安全警示标识,包括危险品标识、禁止吸烟标识、防护装备使用标识等。
同时,配备灭火器、消防栓等消防设施,并定期进行检查和维护。
3.3 环境监测对生产环节中可能产生的有害气体、粉尘等进行定期监测,确保环境达到相关标准要求。
并采取必要的通风措施,保持生产现场空气清新。
3.4 废弃物处理废弃物的处理应符合环保要求,采取合理的收集、运输和处置方式。
禁止将废弃物随意倾倒或排放到环境中,以免造成污染。
4. 应急预案制定完善的应急预案,针对可能发生的事故情况制定相应的处理措施和应急救援方案。
- 1、下载文档前请自行甄别文档内容的完整性,平台不提供额外的编辑、内容补充、找答案等附加服务。
- 2、"仅部分预览"的文档,不可在线预览部分如存在完整性等问题,可反馈申请退款(可完整预览的文档不适用该条件!)。
- 3、如文档侵犯您的权益,请联系客服反馈,我们会尽快为您处理(人工客服工作时间:9:00-18:30)。
增碳剂的生产流程及选样 Prepared on 24 November 2020
一、工艺流程
二、产品描述:
产品选用优质太西无烟煤经800-1200℃煅烧炉煅烧加工制成,是炼钢的理想原料。
三、用途:
主要用于钢铁冶炼,在钢铁冶炼过程中,有少量的炭已燃烧,并且刚中有氧、硫及磷,加入增碳剂后,一方面增加钢种炭的含量,同时增碳剂中的碳与钢中的氧、硫及磷产生化学反应,可发挥钢的机械性能。
在冶炼过程中做还原剂用.性能:
替代传统的石油焦增碳剂,降低炼钢成本.特性:低灰.硫磷高发热量.高比电阻
高机械强度高化学活性.高精煤回收率.质量技术指标:灰分<6%水分<
%挥发份<%固定碳>90%比重>cm3含硫<%盐酸可容率<%.规格:0---20mm,按用户要求加工.固定碳含量(C%):90---95。
特点与加工过程:生产的增碳剂主要原料选定用优质的宁夏太西低灰、低硫、低磷、洗精煤,经过煅炉高温煅烧、破碎精选而成,使用过程中,无烟、无异味、增碳稳定、回收率高。
性能:杂质信号少、增碳回收率高,效果明显。
用途:电炉、转炉、炼钢增碳用。
四、规格:
规格成份含量(%)
固定碳灰份挥发份硫水份%(min)%(max)
c 95
c 94
c 93
c 92
c 918
c 90
粒度,1-3mm,1-5mm,3-5mm,或者根据客户要求;
产品包装:10公斤、25公斤小袋包装,或者1000公斤吨袋包装,或者10公斤25公斤小袋然后装入1000公斤吨袋;或者10公斤25公斤小袋50公斤小袋包装,然后直接装入集装箱;可根据客户要求包装;。