《汽车车身铝合金板材复合涂层加速腐蚀试验方法》(编制说明)
《汽车涂层户外加速腐蚀试验方法》编制说明

《汽车涂层户外加速腐蚀试验方法》编制说明一、工作简况1.1 任务来源《汽车涂层户外加速腐蚀试验方法》团体标准是由中国汽车工程学会批准立项,文件号中汽学函【2018】55号,任务号为2018-2(由学会填写)。
本标准由中国汽车工程学会防腐蚀老化分会提出,海南热带汽车试验有限公司、美国Q-Lab公司中国代表处、众泰汽车工程研究院、重庆长安汽车股份有限公司、中国科学院金属研究所、一汽解放青岛汽车有限公司、一汽-大众汽车有限公司、中国第一汽车股份有限公司天津技术开发分公司、安徽江淮汽车集团股份有限公司、湖南湘江关西涂料有限公司、新疆吐鲁番自然环境试验研究中心等单位起草。
1.2编制背景与目标在一辆汽车中钢材所占的比例约为72%~88%,通过汽车腐蚀调查表明,除意外交通事故损坏或部分零部件磨损外,腐蚀是汽车损坏、报废的重要原因。
在总的腐蚀损失中有相当大的比例是由于大气腐蚀造成的。
据统计,我国每年汽车腐蚀造成的经济损失达1000亿以上。
为了避免金属腐蚀,通常会对车身、底盘等重要金属部件采用涂层等表面防护体系进行防护,因此,研究带涂层金属的腐蚀规律,提升其耐腐蚀能力具有非常重要的意义。
为了缩短试验周期,开发最优性价比的表面处理材料及工艺,设计出最优性价比的产品,我们认为有必要开展“汽车涂层户外加速腐蚀试验方法”研究,将有利于提高整车涂层的整体防腐性能,延长整车涂层使用寿命。
同时,为汽车涂层防腐与老化工作输入平台性技术成果。
1.3主要工作过程本标准于2016年10月开始标准学习;2016年10月到2018年10月份进行了标准相关的试验操作工作;2019年1月至5月进行了标准编写工作;2018年12月份至9月份对标准进行了申报、修改及讨论。
预计2019年12月底之前完成标准的公布工作。
2019年1月11日由海南热带汽车试验有限公司主持召开了标准工作组筹备会议,成立标准工作筹备小组,进入标准工作组筹备阶段。
2019年1月由海南热带汽车试验有限公司向中国汽车工程学会(以下简称中汽学会)提出制订《汽车涂层户外加速腐蚀试验方法》标准的申请,2019年3月成立了标准工作组,提出撰写思路并进行分工。
漆膜循环交变腐蚀实验国标

漆膜循环交变腐蚀实验国标漆膜循环交变腐蚀实验是一种常用的材料腐蚀性能评估方法,用于评价涂层材料在复杂腐蚀环境下的耐蚀性能。
根据国际标准ISO 11997-2《涂层和涂料-腐蚀试验-循环交变暴露于盐雾/湿热环境下的涂层》制定了漆膜循环交变腐蚀实验的国家标准,该标准为涂层材料的研发和应用提供了指导。
漆膜循环交变腐蚀实验是通过模拟真实环境中的腐蚀作用,加速涂层材料的老化过程,评估其在复杂腐蚀环境下的性能。
实验中使用盐雾和湿热两种环境交替暴露涂层样品,通过观察涂层的腐蚀程度和性能变化,判断其耐蚀性能。
实验开始前,首先制备涂层样品。
一般选择金属基材,如铁、铝等,涂覆所需涂料,然后在样品上形成一层均匀的涂层。
涂层的厚度和质量要符合要求,确保实验结果的准确性和可靠性。
实验过程中,涂层样品被放置在特制的暴露槽中,该槽能够模拟盐雾和湿热环境。
在一定的温度和湿度条件下,涂层样品先暴露于盐雾环境中,然后转移到湿热环境中,两种环境循环交替进行。
在每个环境下的暴露时间可以根据需要调整。
实验结束后,通过观察涂层样品的腐蚀情况和性能变化,可以评估涂层的耐蚀性能。
常见的评估指标包括涂层的腐蚀程度、腐蚀产物的生成情况、涂层的附着力等。
根据实验结果,可以判断涂层的耐蚀性能是否符合要求,为涂层材料的研发和应用提供科学依据。
漆膜循环交变腐蚀实验国标ISO 11997-2的制定对于涂层材料的研发和应用具有重要意义。
该标准明确了实验的步骤和要求,提供了可靠的测试方法,使得涂层材料的评估更加科学和准确。
同时,该标准的制定也为涂层行业提供了统一的技术规范,促进了涂层材料的质量提升和应用推广。
漆膜循环交变腐蚀实验国标为涂层材料的耐蚀性能评估提供了重要的参考依据。
通过模拟复杂腐蚀环境,加速涂层材料的老化过程,评估其性能变化,可以有效判断涂层的耐蚀性能。
国际标准ISO 11997-2的制定为涂层材料的研发和应用提供了科学的指导,推动了涂层行业的发展。
汽车铝合金零部件表面涂膜的耐丝状腐蚀试验-2023标准

汽车铝合金零部件表面涂膜的耐丝状腐蚀试验1 范围本标准规定了汽车铝合金零部件表面涂膜的耐丝状腐蚀试验仪器设备、试样准备、试验过程、检查评价方法及试验报告内容等要求。
本标准适用于铝制车轮等零部件,评定其表面被测试涂膜/基材的耐丝状腐蚀性能。
其它类型产品参考执行。
2 规范性引用文件下列文件中的内容通过文中的规范性引用而构成本文件必不可少的条款。
其中,注日期的引用文件,仅该日期对应的版本适用于本文件;不注日期的引用文件,其最新版本(包括所有的修改单)适用于本文件。
GB/T 6682 分析实验室用水规格和试验方法GB/T 9286 色漆和清漆划格试验GB/T 10125 人造气氛腐蚀试验盐雾试验GB/T 13452.2 色漆和清漆漆膜厚度的测定GB/T 30786-2014 色漆和清漆腐蚀试验用金属板涂层划痕标记导则GB/T 30789.2 色漆和清漆涂层老化的评价缺陷的数量和大小以及外观均匀变化程度的标识第2部分:起泡等级的评定GB/T 30789.3 色漆和清漆涂层老化的评价缺陷的数量和大小以及外观均匀变化程度的标识第3部分:生锈等级的评定3 术语和定义下列术语和定义适用于本文件。
3.1丝状腐蚀 filiform corrosion发生在电泳、色漆、清漆或相关产品涂膜下的形状为丝状的一种腐蚀现象,呈细丝状不规则分布,一般从涂膜的切割边缘或局部损伤处开始产生。
注:通常腐蚀丝生长的长度和方向是不规则的,但可能接近平行,长度大致相等。
腐蚀丝通常沿着加工方向并且很少彼此交叉,需要腐蚀性离子激发。
3.2CASS试验 CASS test铜加速乙酸盐雾试验,在受控环境下将加入氯化铜和冰乙酸的5%氯化钠酸性溶液进行雾化的一种试验方法。
4 试验原理丝状腐蚀往往在一定的温度和湿度条件,在适量的酸、碱或盐的诱导下,发生在涂膜薄弱或涂膜破损之处。
在海边或工业环境下具备发生丝状腐蚀的条件。
涂膜膜下基材腐蚀通常从划痕处开始发生,其典型形式是明显可见的细丝状。
汽车零部件及材料实验室循环腐蚀试验方法
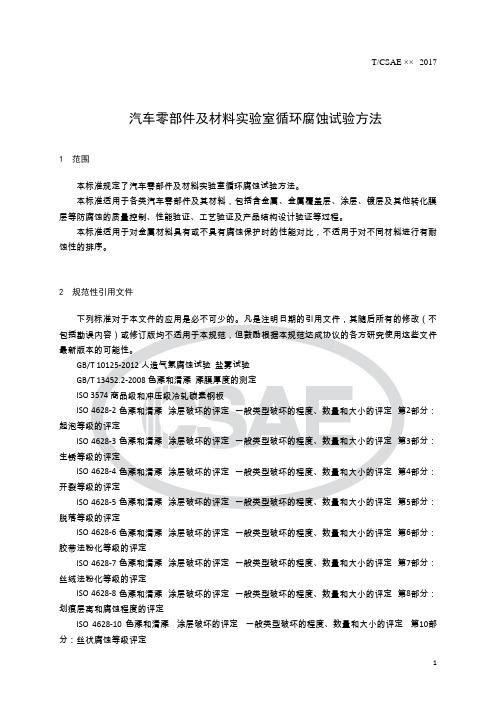
6.4 测定质量损失
T/CSAE ××-2017
试验结束后,应立即取出参比试样,除掉试样背面的保护膜,使用物理或化学方法去除腐蚀产 物。除锈操作的具体步骤可参考GB/T 10125-2012中5.2.3章节,例如,在23 ℃±2 ℃下于20%±5% (质量分数)分析纯级别的柠檬酸二铵(NH4)2HC6H5O7水溶液中充分浸泡。浸泡后,在室温下用 水清洗试样,再用乙醇清洗,干燥后称重。除锈操作的亦可参考ISO 8407中的规定,例如,用 50%(体积分数)的盐酸溶液(密度1.18 g/mL),其中加入3.5 g/L的六次甲基四胺缓蚀剂,浸泡 试样除去腐蚀产物,之后用清水在室温下清洗,然后再用乙醇清洗,最后干燥。
5.2.2 箱内至少放置两个盐溶液收集器,一个靠近喷嘴,一个远离喷嘴。收集器用玻璃等惰性材料 制成漏斗形状,直径为100 mm,收集面积约80 cm2,漏斗管插入带有刻度的容器中,要求收集的是 盐溶液,而不是从试样或其他部位滴下的液体。
5.2.3 通过喷嘴喷淋的溶液,喷淋量可调,且均匀喷淋在试样上。试验箱的形状和尺寸应能使箱内 溶液的收集速度为:在8.1章节表1的第1步至第3步中的12分钟喷淋时间内,盐溶液平均沉降率在80 cm2的水平面积为39 mL~79 mL。
a) 试样划刻线以外部分的外观,如气泡、生锈、开裂、脱落、粉化、丝状腐蚀等;
b) 试样划刻线部位的外观、划痕层离程度、划痕腐蚀程度等;
c) 质量变化;
d) 显微形貌变化。
7
T/CSAE ××-2017 11 试验报告 11.1 试验报告必须写明采用的评价标准和得到的试验结果。如有必要,应有每个试样的试验结 果,每组相同试样的平均试验结果和试样的照片。 11.2 根据试验目的及要求,试验报告可包括如下内容:
《乘用车车身试验舱加速腐蚀试验方法》编制说明

《乘用车车身试验舱加速腐蚀试验方法》编制说明(标准征求意见稿)a.工作简况1、任务来源本标准依据中国汽车工程学会2015年12月12日印发中汽学函[2015]73号《中国汽车工程学会技术规范起草任务书》/任务书编号2015-3制定,标准名称《乘用车车身试验舱加速腐蚀试验方法》。
本标准主要完成单位:浙江吉利汽车研究院有限公司、杭州库德表面处理技术有限公司、一汽-大众汽车有限公司、安徽江淮汽车集团股份有限公司、重庆长安汽车股份有限公司、中国第一汽车股份有限公司天津技术开发分公司、北京汽车研究总院有限公司、华晨汽车集团控股有限公司、奇瑞汽车股份有限公司、长城汽车股份有限公司、比亚迪汽车工业有限公司、上汽通用五菱汽车股份有限公司、上海汽车集团股份有限公司商用车技术中心、深圳华淮循环材料有限公司、通标标准技术服务(上海)有限公司、中汽中心盐城汽车试验场有限公司、海南热带汽车试验有限公司、威凯检测技术有限公司、上海热策电子科技有限公司、上海格麟倍信息科技有限公司、中国兵器工业第五九研究所2、主要工作过程2015年12月由中国汽车工程学会(以下简称中汽学会)向浙江吉利汽车研究院有限公司指派制定《乘用车车身试验舱加速腐蚀试验方法》标准。
2016年1月成立了标准工作组,提出撰写思路并进行分工。
标准工作组于2016年3月在上海召开了标准启动会,会议确认了标准工作计划、撰写大纲、章节目录和工作分工。
2016年8月,标准工作组完成了标准初稿的编制、函审及修改。
2016年12月,标准工作组在成都进行了标准初稿的评审。
2016年10月-2017年8月,标准工作组对标准稿进行试运行(现场评估),并修改,形成标准定稿版本。
2017年9月,标准工作组在沈阳进行了标准定稿的评审。
2017年10月,向中国汽车工程学会提交标准送审稿。
2017年12月,单项标准终审会议(长沙)。
2018年1月,标准发布。
3 主要参加单位和工作组成员及主要工作本标准负责起草单位:浙江吉利汽车研究院有限公司、杭州库德表面处理技术有限公司。
汽车车身铝合金板材复合涂层加速腐蚀试验方法
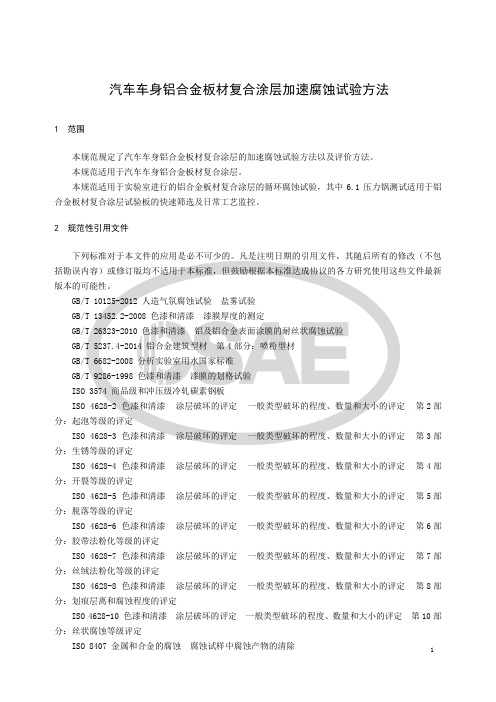
汽车车身铝合金板材复合涂层加速腐蚀试验方法1 范围本规范规定了汽车车身铝合金板材复合涂层的加速腐蚀试验方法以及评价方法。
本规范适用于汽车车身铝合金板材复合涂层。
本规范适用于实验室进行的铝合金板材复合涂层的循环腐蚀试验,其中6.1压力锅测试适用于铝合金板材复合涂层试验板的快速筛选及日常工艺监控。
2 规范性引用文件第2部第3部ISO 4628-4 色漆和清漆涂层破坏的评定一般类型破坏的程度、数量和大小的评定第4部分:开裂等级的评定ISO 4628-5 色漆和清漆涂层破坏的评定一般类型破坏的程度、数量和大小的评定第5部分:脱落等级的评定ISO 4628-6 色漆和清漆涂层破坏的评定一般类型破坏的程度、数量和大小的评定第6部分:胶带法粉化等级的评定ISO 4628-7 色漆和清漆涂层破坏的评定一般类型破坏的程度、数量和大小的评定第7部分:丝绒法粉化等级的评定ISO 4628-8 色漆和清漆涂层破坏的评定一般类型破坏的程度、数量和大小的评定第8部分:划痕层离和腐蚀程度的评定ISO 4628-10 色漆和清漆涂层破坏的评定一般类型破坏的程度、数量和大小的评定第10部分:丝状腐蚀等级评定T/CSAE 71-2018 汽车零部件及材料循环腐蚀试验方法3 术语和定义下列术语和定义适用于本文件。
3.1 划痕层离宽度(Delamination)划痕处各类膜层失去附着力的宽度。
从划刻线的边缘起到膜层失去附着力最远处的距离。
3.2 划痕腐蚀宽度(Corrosion)划痕处各类膜层具有可见腐蚀的宽度。
从划刻线的边缘起到腐蚀最远处的距离。
3.3 划痕腐蚀深度(Hole)划痕处各类膜层具有可见腐蚀点,向基材金属纵深发展的深度。
3.4 丝状腐蚀发生在电泳、色漆、清漆或相关产品涂膜下的形状为丝状的一种腐蚀,呈细丝状不规则分布,一般从涂膜的切割边缘或局部损伤处开始产生。
注:通常腐蚀丝生长的长度和方向是不规则的,但可能接近平行,长度大致相等。
汽车涂层户外加速腐蚀试验方法

汽车涂层户外加速腐蚀试验方法汽车涂层作为保护车身油漆和提升车辆外观质感的重要部分,其抗腐蚀性能对汽车的使用寿命和外观保持起着至关重要的作用。
因此,进行汽车涂层户外加速腐蚀试验具有重要的意义。
本文将介绍一种常用的汽车涂层户外加速腐蚀试验方法。
一、试验设备:1.腐蚀试验箱:具有可控的温湿度环境;2.均匀试样悬挂装置:用于悬挂试样,确保试样表面均匀暴露在腐蚀环境中;3.盐雾生成装置:用于生成氯化钠盐雾;4.盐雾沉积器:用于将盐雾沉积在试样表面;5.温度传感器:用于测量试样表面的温度;6.盐雾滴定仪:用于测量试样表面盐雾的滴定量。
二、试验流程:1.试样准备:将待测试的汽车涂层均匀涂覆在试样上,并保证涂层的厚度均匀;2.悬挂试样:将试样通过均匀试样悬挂装置悬挂在试验箱中,确保试样表面均匀暴露在腐蚀环境中;3.试验环境设定:设置试验箱的温度和湿度,一般温度为35℃,相对湿度为95%;4.盐雾喷洒:打开盐雾生成装置,生成氯化钠盐雾,并通过盐雾沉积器将盐雾沉积在试样表面;5.盐雾暴露时间:根据试验需求,设置盐雾暴露的时间,一般为48小时;6.温湿度循环:在盐雾暴露结束后,设置试验箱温度为50℃,相对湿度为50%,进行温湿度循环,循环时间一般为2小时;7.滴定量测试:使用盐雾滴定仪测量试样表面的盐雾滴定量,用于分析涂层腐蚀程度;8.试验结束:根据试验的要求,根据滴定量及其他腐蚀表现来评估涂层的腐蚀性能。
三、试验注意事项:1.试样的选择:要选择代表性的试样,具有与实际使用情况相似的涂层结构和性能;2.涂层的均匀性:确保涂层的厚度和均匀性;3.试验环境设置:根据试验需求合理设置试验箱的温度和湿度,保证试验的可靠性和真实性;4.盐雾喷洒和滴定量测试:要准确控制盐雾喷洒和准确测量滴定量,以获得准确的腐蚀程度分析结果;5.试验时间:根据试验的要求,合理设置试验时间。
通过以上试验方法和注意事项,可以对汽车涂层的抗腐蚀性能进行评估和提升,以确保汽车在户外环境中的外观和使用寿命。
不同品牌汽车的零部件及材料加速腐蚀试验方法及评价对标分析
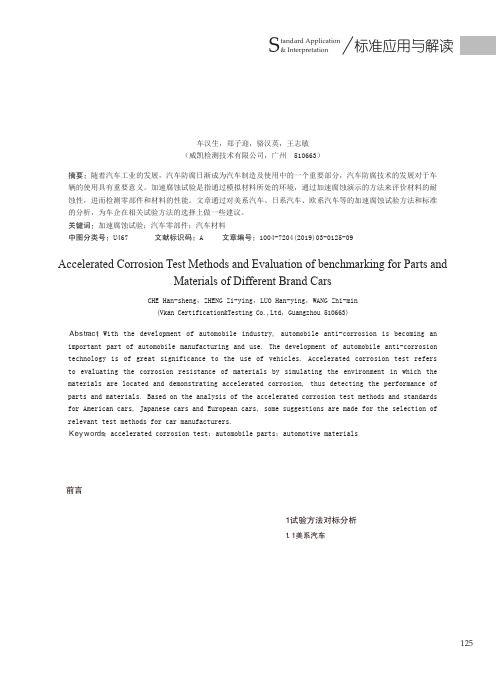
0 h 3 min
1c’
3 h 3 min
2 h 54 min
1a’ 5 h 57 min
0 h 3 min
2a
6 h 0 min
0 h 30 min
2b
6 h 30 min
2 h 0 min
3a
8 h 30 min 15 h 30 min
3a
24 h 0 min
—
重复步骤 1a-3a 4 次(不含第 1 次)
环。 盐 溶 液 成 分: 氯 化 钠 NaCl:0.9 %, 无 水 氯 化 钙
CaCl2:0.1 %,碳酸氢钠 NaHCO3:0.075 %。 1.2 欧系汽车 1.2.1 PSA 汽车 1)试验标准,D13 5486-2012,《材料和覆盖层 循
环加速腐蚀试验》。 2)具体测试条件: 喷雾阶段(如表 2) 过渡阶段(如表 3) 热循环阶段(如表 4) 盐溶液成分:氯化钠:5 %,通过 0.005 mol/L 的硫
辆的使用具有重要意义。加速腐蚀试验是指通过模拟材料所处的环境,通过加速腐蚀演示的方法来评价材料的耐
蚀性,进而检测零部件和材料的性能。文章通过对美系汽车、日系汽车、欧系汽车等的加速腐蚀试验方法和标准
的分析,为车企在相关试验方法的选择上做一些建议。
关键词:加速腐蚀试验;汽车零部件;汽车材料
中图分类号:U467
S 标准应用与解读 tandard Application & Interpretation
1.1.2 通用汽车 1) 试 验 标 准:GMW14872-2013,《 实 验 室 循 环 腐 蚀试验》。 2)具体测试条件 室温阶段:温度 25±3 ℃,相对湿度 45 %± 1 0 % R H , 持续时间 8 h; 高湿阶段:温度 49±2 ℃,相对湿度约 100 %RH, 持续时间 8 h; 干燥阶段:温度 60±2 ℃,相对湿度≤ 30 %RH,持 续时间 8 h; 盐溶液成分:氯化钠:0.9 %,氯化钙:0.1 %,碳酸 氢钠:0.075 %; 总 试 验 时 间: 根 据 样 品 的 安 装 部 位, 依 据 GMW14872 的表 A1 和 A2 规定的测试周期。见图 5 试验 流程和图 6 测试周期。 3)标准特点 喷雾方式与传统盐雾不一样,每循环喷淋 1-4 次, 通过手动或自动喷头直接喷射到样品表面,直到润湿为 止。 测试过程中需要加入标准板“coupon”控制腐蚀速率, 具体见图 7 和 8。 除了常规的汽车零部件,有些特殊的部位需要增加 环境应力,例如高温、冷凝液或泥浆等。以汽车排气管 为例,该部件的循环腐蚀测试方法,应依据标准 GMW 14872-2013 Option 4 进行试验。每个循环包含 3 个试验 阶段: 室温阶段:温度 25±3℃,相对湿度 45 %± 10 %RH,持续时间 8 h,该阶段内对样品和标准板进行 4 次盐雾喷洒,前 2 次喷洒间隔 1 h,在第 2 次喷洒结 束 0.5 h 后,对样品进行 4 h 的 482 ℃的高温试验,高温 试验结束 0.5 h 后,对样品和标准板进行 2 次间隔 1 小时 的盐雾喷洒(标准板不随样品进行高温试验); 高湿阶段:温度 49±2 ℃,相对湿度约 100 %RH, 持续时间 8 h; 干燥阶段:温度 60±2 ℃,相对湿度≤ 30 %RH,持
汽车车身铝合金板材加速防腐试验方法的研究

目 前 ,国 内 外 各 知 名 车 企 都 在 纷 纷 研 究 采 用 铝 合 金 汽 车 车 身 ,部 分 高 端 品 牌 车 身 铝 合 金 的 应
作者简介:田冰星(1983—),男,工程师,学士学位,研究方向为汽 车开发涂装工艺同步工程分析及车身防腐技术研究。
用比例已经达到较高的水平,如奥迪 A8 白车身铝 合金比例达到 65.3%,特斯拉 S 系列铝合金比例达 到 97%,这也是目前车身铝合金比例最高的车型。 我国自主品牌汽车起步较晚,除蔚来汽车 ES8\ES6 系列产品白车身铝合金比例达到 96%外,其他汽车 车 身 铝 合 金 使 用 才 刚 刚 开 始 ,并 仅 仅 用 于 一 些 结 构简单的零件。
2019 中国汽车工程学会涂装技术分会学术年会优秀论文
The Best Papers of Coating Technology, Conference 2019, Branch of SAE-China
汽车车身铝合金板材加速防腐试验方法的研究
田冰星 邢汶平 肖毅川
(安徽江淮汽车集团股份有限公司技术中心,合肥 230601)
2 铝合金板材腐蚀机理简介
2.1 汽车车身铝合金板材介绍 常见的铝合金系列,主要包括 1000/2000/3000/
4000/5000/6000/7000 等多个系列,不同系列的铝合
车身防腐蚀
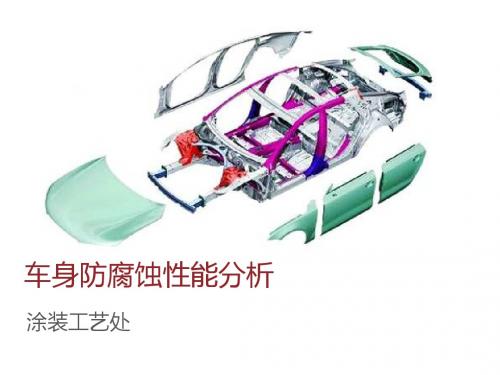
7 严重腐蚀
8 非常严重腐蚀
9 穿孔
参照上图对样车各零部件进行腐蚀等级评估
16
二
目标-外观锈蚀评价等级
外观锈蚀等级划分:
等级 腐蚀率 客户认可度
0
1 2 3 4
无明显腐蚀
微量腐蚀:1到2个小的红锈点 轻微腐蚀:一些小的红锈点 轻度腐蚀:很多小的红锈点(生锈面积≤10%) 适度腐蚀:中等尺寸的红锈点(生锈面积25±15%)
腐蚀强度
受关注程度
●● ●●● ●●●● ●
●●●● ●●● ● ●●●
注:●代表腐蚀强度大小和受关注程度大小,●代表最小,●●●●代表最大
汽调查数据显示,汽车运行动态时间;静态时间=1:(15-20)
9
二
目标-微环境
汽车区域腐蚀强度:
腐蚀强度:标准钢板在单位时间内的腐蚀深度,单位:μm/a
按照QC/T 732实验的实车数据
车身防腐蚀性能分析
涂装工艺处
目录
一 二 三 四 五
现状 目标 设计结构 工艺
材料
2
一
现状-召回
2006-2014全球锈蚀召回案例问题分类统计
25 20 20
召回数量
15
10
5 1 2 1 电器 召回问题分类 底盘 1 车身
0
内饰 附件
3
100
120
140
20
40
60
80
投诉 一
0 江淮汽车 北京现代 长城汽车 长安汽车 奇瑞 上海通用 比亚迪 广汽 一汽 东风汽车 上汽通用五菱 吉利汽车 江铃汽车 东风悦达起亚 进口汽车 上海大众 上汽
8
7
6
5 4 3 2 1
《整车海运外观腐蚀模拟试验及评价方法》编制说明

《整车海运外观腐蚀模拟试验及评价方法》编制说明一、工作简况1.1任务来源《整车海运外观腐蚀模拟试验及评价方法》团体标准是由中国汽车工程学会批准立项,文件号中汽学函【2020】93号,任务号为2020-35。
本标准由中国汽车工程学会防腐蚀老化分会提出,泛亚汽车技术中心有限公司、上海汽车集团股份有限公司乘用车技术中心、上海汽车集团股份有限公司商用车技术中心、上汽通用五菱汽车股份有限公司、重庆长安汽车股份有限公司、浙江吉利汽车研究院有限公司、上海奇瑞汽车技术中心、东风日产乘用车技术中心、北京汽车股份有限公司、广州汽车研究院、上海菲瑟汽车技术服务有限公司、海南热带汽车试验有限公司、中汽中心盐城汽车试验场有限公司、中国重汽集团公司、弘埔技术(香港)有限公司等单位起草。
1.2编制背景与目标随着中国汽车工业的蓬勃发展,国产汽车的出口量也逐渐增加。
出口方式主要为海运和空运。
空运耗时短,环境优,运输过程不会造成明显腐蚀。
但其劣势也很明显,高昂的运输成本大大降低了产品出口的利润,所以绝非企业出口首选。
很多大型产品出口的主要运输方式仍为海运。
海运以其低廉的运输成本受到企业的欢迎,但其所带来的腐蚀问题依然是众多出口企业所关心的问题。
以某汽车公司为例,该公司需要采用海运的方式整车运往南非,运输周期为30-60天。
在海洋运输环境下,汽车裸露零部件的表面容易发生大面积的生锈问题,腐蚀对汽车外观造成的不良影响不仅会使企业蒙受经济损失,而且对出口企业的形象和声誉也会造成不良影响。
本标准建立的目的在于制定出一套符合整车海洋运输的腐蚀试验和评价方法,以验证整车防腐设计是否满足外观腐蚀设计要求,从而帮助汽车工程人员提前发现汽车设计的薄弱环节并采取相应的防护措施。
1.3主要工作过程本标准于2019年1月开始成立标准起草团队、广泛收集国内外主机厂的相关数据并考虑地域、季节和板材等客观差异,初步建立技术路线。
2019年3月开始收集了海运腐蚀相关数据并建立腐蚀试验工况,初步建立海运腐蚀试验标准和外观腐蚀评价标准2019年5月在浙江余姚召开了第一次标准评审会,会议对标准编制的进展和标准内容进行了详细的介绍。
汽车行业循环盐雾腐蚀试验方法

汽车行业循环盐雾腐蚀试验方法一、这是一个实验室加速腐蚀试验方法,可以用来确定汽车组件和部件的耐腐蚀性。
它的性质,即是循环测试样品暴露在随时间变化的气候,试样放置在一个封闭的腔,暴露在气候变化,包括以下3个部分重复循环:4小时暴露在一个连续的间接触喷雾中性(pH值6.5至7.2)盐水溶液,属于淘汰率在1.02.0ml/80cm2/小时,在35度的室温中进行标准测试,其次是2小时在60度/20%到30%RH气候干燥的空气中进行测试,然后是2小时冷凝水气候曝光(润湿)的95%到100%RH 在50度中周期重复,因此在测试期间的数量是可变的的,测试周期的各个部分之间最大的过渡时间也规定如下:从盐喷洒到空气中干燥30分钟内。
从空气干燥15分钟内润湿。
从润湿盐喷洒在30分钟内。
二、这是一个实验室加速腐蚀试验方法,可以用来确定汽车组件和部件的耐腐蚀性。
它的性质,即是循环测试样品暴露在随时间变化的气候,试样放置在一个封闭的腔,暴露在气候变化,包括以下3个部分重复循环。
2小时暴露在一个连续的接触喷中性(pH值6.5至7.2)盐水溶液,属于淘汰率在1.02.0ml/80cm2/小时,在35度试验室内进行标定。
其次是4小时在60度.20%到30%RH气候干燥的空气,然后是2小时冷凝水气候曝光(润湿)的95%到100%RH在50度.周期重复,因此在测试期间的数量是可变的的,测试周期的各个部分之间的最大的过渡时间也规定如下:从盐喷洒到空气中干燥30分钟内。
从空气干燥15分钟内润湿。
从润湿盐喷洒在30分钟内。
汽车行业循环盐雾腐蚀试验方法三、这是一个实验室加速腐蚀试验方法,可以用来确定汽车组件和部件的耐腐蚀性。
它的性质,即是循环测试样品暴露在随时间变化的气候,测试样品被放置在一个封闭的腔,暴露在一个相对较短的时间,接触到热/潮湿和炎热/干燥环境,盐雾包括气候变化,整个测试周期包括一个主循环和一个子周期,整个测试周期需要24小时来执行,重复整个周期,因此在测试期间的数量是可变的的,曝光10分钟的连续喷盐水溶液的间接室温度在35度,主要测试周期开始。
《汽车用热冲压钢板高韧性铝硅镀层》编制说明

《汽车用热冲压钢板高韧性热镀铝硅合金镀层》编制说明一、工作简况1.1 任务来源《汽车用热冲压钢板高韧性铝硅镀层技术标准》团体标准是由中国汽车工程学会批准立项。
文件号中汽学函【2020】08号,任务号为2020-08:。
本标准由中国汽车工程学会汽车轻量化技术创新战略联盟提出,东北大学、育材堂(苏州)材料科技有限公司等单位起草。
1.2编制背景与目标近年来,由于节能环保的迫切需求以及对汽车安全性要求的提高,汽车轻量化和碰撞安全性已经成为汽车制造业关注和亟待解决的焦点问题。
超高强钢因其优异的强度性能可以实现减重,从而达到轻量化的目的。
然而,高强度钢零件的制造采用传统的冷冲压方式,回弹控制难,零件尺寸稳定性低,且一直伴随着冲压开裂问题,因此,其应用限制越来越明显。
在这种情况下,热冲压成形技术应运而生。
热冲压成形过程中,将钢板加热至高温形成全奥氏体组织,并在该热状态下零件的冲压成形,随后通过模具快速冷却,使得钢板形成马氏体组织,极大地提高了零件的强度。
最终的热冲压零件强度可达到1500MPa以上,远高于采用传统冷冲压方式的高强钢零件。
热冲压用钢包括无镀层(以下简称裸板)产品和镀层产品。
在热冲压成形过程中,采用裸板冲压成形时,需在氮气或氩气等保护气氛下加热,以避免产生氧化皮和脱碳,然而送料和成形过程中的氧化则无法避免。
氧化皮将影响到板料与模具接触表面的状态,既降低了模具和板料界面的接触换热系数,又增大了钢板与模具的摩擦系数。
冲压时,脱落的氧化铁皮将磨损模具表面,影响零件的成形质量以及模具寿命。
更重要的是,需要将该氧化层去除后才能进入汽车装配和涂装,因此裸板的热冲压成形构件必须进行喷丸处理或酸洗,以去除该氧化层后再进行汽车装配和涂装。
喷丸处理会导致零件残余应力释放而发生变形,导致汽车的装配精度下降;酸洗处理导致严重环保问题且会增加构件的氢致开裂风险。
且上述两种方式还存在潜在的环保问题并伴随着成本的增加。
此外,汽车厂普遍希望汽车部件具有更优异的耐蚀性能。
汽车整车防腐蚀评价体系和典型腐蚀现象介绍
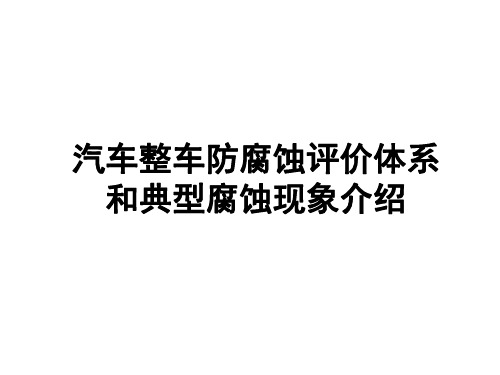
5级大面积腐蚀大尺寸的锈点 锈蚀面积占部件总面积的75±15%
6级 全面积腐蚀 ,锈蚀面积占部件总 面积的100%
7级 严重腐蚀有少量锈垢堆积, 不易脱落
8级 非常严重腐蚀有大量锈垢堆积、 开裂或呈片状脱落
9级 穿孔腐蚀
14
穿孔、断裂、扩展延伸孔
整车防腐蚀评价体系和典型腐蚀现象介绍
第一部分:整车防腐蚀质量评估方法 第二部分:整车防腐蚀质量评估标准 第三部分:其他车型典型腐蚀现象
热
路腐蚀
断裂,
罩
安全风
险
更改材质, 铝箔
皮胶套, 阻挡涂装
制 门动 铰管 链定
位
弹
簧
18
其他可能引起失效的腐蚀问题
方向机万向节及万向节臂出现大量锈垢,可能会引起机械故障
雨刮器臂两端连杆锈垢堆积
19
20
11
Ø车身内部区域+发动机舱+车底区域:
可见程度
高度/中度可见区
低可见区域 可见程度 高度可见区 中度/低度可见区域 可见程度 高度可见区 中度/低度可见区域
车身内部区域
打开储物箱、座椅滑动到最大、没有灰尘等,司机或乘客坐 在车内,或者上下车、开车时,容易看到的区域零部件,比 如安全带、面板紧固件、头枕杆、手刹、座椅滑轨等
户抗议 较明显但可接受 大多能接受,挑剔的客
户抗议
质量要求 6个腐蚀年
防腐蚀质量等级 汽车各系统、零部件不能出现功能失效或者穿孔
10
Ø外表面区域:
可见程度 高度/中度可见区
低可见区域
定义
当车辆停在地上,关闭门窗等开闭件,站在车辆附近能明 显看到外表面金属板和车身相关部件。表面包括前舱盖、 顶盖、后备门、侧围、翼子板和保险杠/蒙皮,以及其他易 见的车身附件
《汽车车身铝合金板材复合涂层加速腐蚀试验方法》(报批稿)

ICS 32.020T40团体标准T/CSAE **-2020汽车车身铝合金板材复合涂层加速腐蚀试验方法Accelerated corrosion test methods of composite coating for aluminum alloy sheets of automotive body(报批稿)在提交反馈意见时,请将您知道的该标准所涉必要专利信息连同支持性文件一并附上。
2020-xx-xx发布2020-xx-xx实施中国汽车工程学会发布目 次前言 (1)1 范围 (1)2 规范性引用文件 (1)3 术语和定义 (1)4 试验溶液 (2)5 试验设备 (2)5.1 设备材料 (2)5.2 试验箱 (2)6 试验方法 (3)6.1 压力锅测试 (3)6.2 循环腐蚀试验 (4)7 试验周期 (5)8 结果评价 (6)8.1 试验后试样的处理 (6)8.2 试验结果的评价 (6)9 试验报告 (6)9.1 试验报告说明 (6)9.2 试验报告内容要求 (6)附录A试样划痕的操作规范 (8)附录B试样评价的技术规范 (11)前 言本标准按照GB/T1.1-2009《标准化工作导则 第1部分:标准的结构和编写》给出的规则起草。
请注意本标准的某些内容可能涉及专利,本标准的发布机构不承担识别这些专利的责任。
本标准由中国汽车工程学会汽车防腐蚀老化分会提出。
本标准起草单位:安徽江淮汽车集团股份有限公司、浙江众泰汽车制造有限公司、美国Q-Lab公司中国代表处、中国第一汽车股份有限公司天津技术开发分公司、北京奔驰汽车有限公司、阿克苏诺贝尔(中国)投资有限公司、威凯检测技术有限公司武汉分公司、深圳市美信检测技术股份有限公司、海南热带汽车试验有限公司、辽宁忠旺集团有限公司忠旺研究院、上海凯密特尔化学品有限公司、常州市武进晨光金属涂料有限公司、北京新能源汽车股份有限公司、广西南南铝加工有限公司、帝业化学品(上海)有限公司、上海菲瑟汽车技术服务有限公司、上汽大众汽车有限公司、比亚迪汽车工业有限公司、东风商用车有限公司、重庆长安汽车股份有限公司、一汽解放青岛分公司、上海涂料研究所、苏州市信测标准技术服务有限公司、通标标准技术服务(上海)有限公司、上海华测品正检测技术有限公司、宝钢股份技术中心、通标标准技术服务(重庆)有限公司。
盐雾腐蚀试验箱-汽车车身铝合金板材复合涂层加速腐蚀试验方法研究

盐雾腐蚀试验箱| 汽车车身铝合金板材复合涂层加速腐蚀试验方法研究大气腐蚀&促进腐蚀的环境因素腐蚀的定义欧洲卷材涂料协会给出腐蚀的定义:使物质达到其自然的,最低能量状态的力量。
腐蚀是一个电化学过程,它使提炼的金属恢复到其自然的氧化状态。
大气腐蚀在ISO 9223标准中对大气腐蚀作出了定义:大气腐蚀是在金属表面形成一层水膜的过程。
水膜可能很薄以至于肉眼很难看清。
影响腐蚀的环境因素水(相对湿度,与水物质的影响),氧(氧化反应),离子影响腐蚀的关键离子种类及其来源海水中广泛存在氯离子,钠离子,硫酸盐和镁离子,下图是海水离子的组成。
假设在1kg的海水中,96.5%(965g)是水,3.5%(35g)是盐。
在3.5%的盐中,占比最大的是氯化物占55%,其次是钠占30.6%,然后是硫酸盐占比7.7%,还含有钙,钾等一些离子。
汽车车身铝合金板材复合涂层加速腐蚀试验方法研究背景和目标•汽车轻量化的快速发展•铝合金涂层耐腐蚀性能检测方法行业内没有明确要求,为汽车腐蚀风险带来巨大隐患。
•开展实验室循环腐蚀与户外腐蚀对比试验,实现:✓适用于铝合金涂层耐腐蚀性能的验证✓适用于开发应用于铝合金基材的涂料及前处理材料性能验证✓适用于铝合金涂层防腐性能的质量控制汽车车身铝合金板材复合涂层加速腐蚀试验样板样板:53种,1200多片样板的差异包括:•底材:内板5000系列,外板6000系列,型材•前处理:硅烷,磷化,锆化•电泳:3种•面漆:2种如下图是汽车涂层体系,可以看到包括了前处理,电泳,中涂,色漆,清漆等涂层。
汽车车身铝合金板材复合涂层加速腐蚀试验设计在53种试验样板中,选取其中一种进行试验,如N0.46,样板宽为100mm,长为200mm。
底材是铝板,进行磷化前处理,电泳涂层厚度是18um,面漆是白色的,其中中涂涂层厚度为30um,色漆涂层厚度为15um,清漆涂层厚度为35um。
在试验前对样板进行划痕(划痕应透过涂层达到金属底材)。
- 1、下载文档前请自行甄别文档内容的完整性,平台不提供额外的编辑、内容补充、找答案等附加服务。
- 2、"仅部分预览"的文档,不可在线预览部分如存在完整性等问题,可反馈申请退款(可完整预览的文档不适用该条件!)。
- 3、如文档侵犯您的权益,请联系客服反馈,我们会尽快为您处理(人工客服工作时间:9:00-18:30)。
《汽车车身铝合金板材复合涂层加速腐蚀试验方法》编制说明一、工作简况1.1任务来源《汽车车身铝合金板材复合涂层加速腐蚀试验方法》团体标准是由中国汽车工程学会批准立项,文件号中汽学函【2018】57号,任务号为2018-4(由学会填写)。
本标准由中国汽车工程学会防腐蚀老化分会提出,安徽江淮汽车集团股份有限公司、浙江众泰汽车制造有限公司、美国Q-Lab公司中国代表处、中国第一汽车股份有限公司天津技术开发分公司、北京奔驰汽车有限公司、阿克苏诺贝尔(中国)投资有限公司、威凯检测技术有限公司武汉分公司、深圳市美信检测技术股份有限公司、海南热带汽车试验有限公司、辽宁忠旺集团有限公司忠旺研究院、上海凯密特尔化学品有限公司、常州市武进晨光金属涂料有限公司、北京新能源汽车股份有限公司、广西南南铝加工有限公司、帝业化学品(上海)有限公司、上汽大众汽车有限公司、比亚迪汽车工业有限公司、东风商用车有限公司、重庆长安汽车股份有限公司、上海涂料研究所、苏州市信测标准技术服务有限公司、通标标准技术服务(上海)有限公司、上海华测品正检测技术有限公司、宝钢股份技术中心、通标标准技术服务(重庆)有限公司等单位起草。
1.2编制背景与目标随着节能减排绿色出行的环保观念深入人心,汽车材料轻量化成为汽车主机厂及OEM工程师的共识。
铝合金材料在传统燃油车领域应用日益广泛,在新能源汽车领域则担当了主要角色。
然而铝合金涂层耐腐蚀性能检测方法行业内没有明确要求,甚至部分铝合金零件不进行任何表面处理,凭借自然氧化膜进行腐蚀防护,为汽车使用寿命带来巨大安全隐患。
因此中国汽车行业急需一份汽车车身铝合金复合涂层加速耐腐蚀试验方法,作为铝合金车身及零部件耐腐蚀性能评估及生产管控的依据。
目前,国内汽车行业没有针对铝合金涂层耐腐蚀性能的试验方法。
为满足对汽车铝合金零部件的质量验证和质量改进,铝合金氧化膜一般采用GB/T 10125 中CASS方法进行测试,铝合金粉末喷涂借鉴建筑行业铝合金粉末喷涂标准测试,但评价标准各车企差距较大,因与钢铁腐蚀机理不同,无法借鉴。
国外德国宝马、大众等公司已经推出了铝合金加速腐蚀试验方法,用来考察相关零部件的耐蚀性能。
目前中国自主汽车品牌铝合金防腐技术与验证方法处于发展初期,开发与国内大气腐蚀相关性好、试验方法方便快捷的铝合金复合涂层加速腐蚀试验方法符合中国汽车工业车身轻量化的发展需求。
1.3主要工作过程本标准于2018年1 月开始收集标准并学习研讨。
2018年5月11日由江淮汽车、众泰汽车以及QLAB公司三方主要标准参与人进行方案研讨,形成初步的方案。
2018年5月23日由江淮汽车主持召开了标准工作组筹备会议,成立标准工作筹备小组,发布标准制作过程的初步试验方案并讨论确认,进入标准工作组筹备阶段。
2018年6标准工作小组确认了本标准需要开展的试验具体方案,通过采用四种实验室试验舱加速腐蚀试验与户外海南整车道路强化腐蚀试验结果进行对比,得出最佳的实验舱加速腐蚀试验方法。
具体确认了AASS/CASS/FILIFORM/CATC四H 种户内试验结果和户外海南整车道路强化腐蚀试验结果做对比。
2018年7月完成试验样板制板工作,一共1470块样板。
2018年8月-2019 年2月开始进行各项试验。
其中,2018年12月组织召开第二次标准研讨会,对第一轮试验得出的一部分数据进行发布并讨论下阶段工作安排。
2019年4月完成第一轮试验数据收集以及分析工作。
2019 年5 月在余姚根据第一轮试验数据进行发布并对结果进行讨论,初步确定本标准的试验方法,并制定第二轮补充试验方案,对试验过程参数进行优化并确认具体试验验证方案。
2019年6月-7 月完成第二轮试验样板制作。
2019年8月进行试验准备并陆续开展各项试验。
同时根据第一轮试验结论编制标准初稿。
2019年9月,召开征求意见稿评审会议。
2019年10月,形成征求意见稿并公开征求意见,起草组根据反馈意见进行修改后形成标准送审稿。
2019年12月,完成标准终评工作并提交发布版标准。
、标准编制原则和主要内容2.1标准制定原则在充分比较学习了国内外关于铝合金材料的耐腐蚀性试验方法的基础上,以及前期开展的铝合金板材中性盐雾及中性循环交变试验结果,初步得出车身铝合金板材腐蚀试验方法目前较多使用的是在酸性条件下的加速试验方法。
因此本标准考虑铝合金板材腐蚀属性的情况下,选取几种酸性条件下的腐蚀环境,通过增加循环交变的条件、加速腐蚀速率等方式开展实验室加速试验验证工作。
通过实验室的加速腐蚀试验结果和户外海南整车道路强化腐蚀试验结果,从腐蚀量、腐蚀形态等方面进行对比,得出最优的加速腐蚀试验方法。
根据试验结果编制实验室加速腐蚀试验方法。
本标准的制定充分考虑汽车行业铝合金车身的发展,确保标准的科学性、先进性、严谨性、可操作性,以促进汽车车身铝合金板材复合涂层防护技术的发展。
2.1.1通用性原则本标准提出的汽车车身铝合金板材复合涂层加速腐蚀试验方法,其他类型的汽车铝合金材料复合涂层可参照执行。
2.1.2指导性原则本标准提出的方法能指导汽车主机厂及OEM开展汽车铝合金板材复合涂层的耐腐蚀性能测试工作,并为含铝车身的涂装工艺过程质量控制及材料选型验证等提供指导作用。
2.1.3协调性原则本技术规范以中国典型气候试验场为腐蚀环境,参考国外车企相近标准制定铝合金涂层腐蚀试验及评价方法。
部分内容与外资车企标准相同或技术上相同,但在其他内容上却互不包括对方的内容。
2.1.4兼容性原则本标准提出的汽车车身铝合金板材复合涂层加速腐蚀试验方法充分考虑了汽车铝合金车身的涂层防腐蚀性能,具有普遍适用性。
2.2标准主要技术内容本标准共分为9 章,规定了汽车车身铝合金板材加速腐蚀试验的试验步骤、试验周期以及结果评价等。
内容包括范围、规范性引用文件、术语和定义、试验溶液、试验箱、试验步骤、试验周期、结果评价、试验报告等,提供资料性附录,明确试验方法中的试验划痕工作及结果评价等内容。
2.3关键技术问题说明本标准提出的汽车车身铝合金板材加速腐蚀试验方法主要规范了试验条件和试验步骤,并规范了试验结果评价方法。
通过各种加速腐蚀试验方法的对比总结出了与户外整车道路强化腐蚀试验最接近的实验舱加速腐蚀试验方法,本标准提出的试验方法和评价方法合理,具有科学性和较好的适用性。
2.4标准主要内容的论据在标准的编制过程中,对行业相关的技术信息进行了调研,国内外铝合金涂层耐腐蚀性的试验方法应用见表1。
因国内主机厂目前汽车车身铝合金板材涂层的耐腐蚀试验方法还没有统一,本标准是根据铝合金本身的材料性能,采用几种酸性条件下的腐蚀试验方法进行试验对比,并与整车海南道路强化腐蚀试验和盐水试验的结果做对比见表2,然后对参数进行优化,得出与整车腐蚀结果最相近的一种实验舱内加速腐蚀的试验方法。
本标准试验方法首先通过压力锅沸水试验检测铝合金复合涂层的附着力,如果不合格就建议不继续进行耐腐蚀试验检测。
本标准利用四种实验舱加速腐蚀试验方法,分别为铜加速乙酸盐雾(CASS)试验、酸性盐雾(AASS)试验、丝状腐蚀试验(FILIFORM)、以及一种循环腐蚀试验方法(CATC)H ,与海南整车道路强化腐蚀试验和盐水试验两种户外试验的结果进行对比,得出与户外结果最接近的一种试验方法,然后再进行参数优化,最终确定试验方法和试验参数。
表2 加速腐蚀试验方法一览表2.5标准工作基础编写组主要起草单位安徽江淮汽车集团股份有限公司已经批量生产全铝车身,现场设备工艺和材料都已调试合格,条件完善,前期已经通过中性盐雾试验对铝合金板材做了2000小时的盐雾试验,未出现腐蚀现象,但在海南强化腐蚀试验车上挂板试验却出现了漆膜划痕边缘区域起泡现象。
QLAB公司、阿克苏诺贝尔公司、威凯以及美信等检测公司,参与过铝合金轮毂等零部件材料的检测,都具备各项试验的检测能力和丰富的检测经验。
在标准的编制过程中,同时参考了以下国内外标准:GB/T 5237.4-2017 铝合金建筑型材第4 部分:喷粉型材GB/T 6682-2008 分析实验室用水国家标准GB/T 9286-1998 色漆和清漆漆膜的划格试验GB/T 10125-2012 人造气氛腐蚀试验盐雾试验GB/T 13452.2-2008 色漆和清漆漆膜厚度的测定GB/T 26323-2010 色漆和清漆铝及铝合金表面涂膜的耐丝状腐蚀试验GB/T 30789.2-2014 色漆和清漆涂层老化的评价缺陷的数量和大小以及外观均匀变化程度的标识第2 部分:起泡等级的评定GB/T 30789.3-2014 色漆和清漆涂层老化的评价缺陷的数量和大小以及外观均匀变化程度的标识第3 部分:生锈等级的评定GB/T 30789.4-2015 色漆和清漆涂层老化的评价缺陷的数量和大小以及外观均匀变化程度的标识第4 部分:开裂等级的评定GB/T 30789.5-2015 色漆和清漆涂层老化的评价缺陷的数量和大小以及外观均匀变化程度的标识第5 部分:剥落等级的评定GB/T 30789.6-2015 色漆和清漆涂层老化的评价缺陷的数量和大小以及外观均匀变化程度的标识第6 部分:胶带法评定粉化等级GB/T 30789.7-2015 色漆和清漆涂层老化的评价缺陷的数量和大小以及外观均匀变化程度的标识第7 部分:天鹅绒布法评定粉化等级GB/T 30789.8-2015 色漆和清漆涂层老化的评价缺陷的数量和大小以及外观均匀变化程度的标识第8 部分:划痕或其他人造缺陷周边剥离和腐蚀等级的评定GB/T 30789.9-2014 色漆和清漆涂层老化的评价缺陷的数量和大小以及外观均匀变化程度的标识第9 部分:丝状腐蚀等级的评定ISO 3574-1999 商品级和冲压级冷轧碳素钢薄板ISO 8407 金属和合金的腐蚀腐蚀试样中腐蚀产物的清除通过大量的对比试验结果,本标准提出的《汽车车身铝合金板材复合涂层加速腐蚀试验方法》有一定的先进性、通用性、科学性和可操作性。
三、主要试验(或验证)情况分析标准工作组主要进行了四种实验室加速腐蚀试验AASS、CASS、FILIFORM、CATCH以及户外整车道路强化腐蚀试验,对试验结果进行了整理汇总和分析,并通过最大单边腐蚀长度以及腐蚀面积两项评价指标进行评价,得出以下结论:1、最大单边腐蚀长度1.1从4 个实验室实验舱加速腐蚀试验的结果来看见表3,24 种试板的最大单边腐蚀长度总计的顺序为:CASS(240h)>filiform (678h,北奔的试验舱试验过程中没有控制风速,导致数据偏大)>AASS>CATC。
H1.2从实验室试验与户外整车道路试验的数据对比来看,威凯CATCH试验数据与海南试验数据最接近,相关性最好。
2、腐蚀面积2.1 从4 个户内实验舱加速腐蚀试验的结果来看,见表4,24 块试板的平均腐蚀面积总计的顺序为:CASS(240h)>filiform (678h,北奔的的试验舱试验过程中没有控制风速,导致数据偏大)>AASS>CATC。