淬火工艺
淬火的工艺特点及应用范围
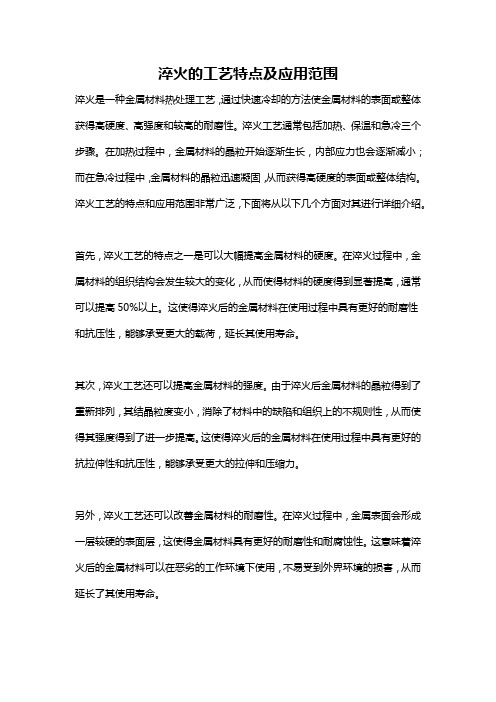
淬火的工艺特点及应用范围淬火是一种金属材料热处理工艺,通过快速冷却的方法使金属材料的表面或整体获得高硬度、高强度和较高的耐磨性。
淬火工艺通常包括加热、保温和急冷三个步骤。
在加热过程中,金属材料的晶粒开始逐渐生长,内部应力也会逐渐减小;而在急冷过程中,金属材料的晶粒迅速凝固,从而获得高硬度的表面或整体结构。
淬火工艺的特点和应用范围非常广泛,下面将从以下几个方面对其进行详细介绍。
首先,淬火工艺的特点之一是可以大幅提高金属材料的硬度。
在淬火过程中,金属材料的组织结构会发生较大的变化,从而使得材料的硬度得到显著提高,通常可以提高50%以上。
这使得淬火后的金属材料在使用过程中具有更好的耐磨性和抗压性,能够承受更大的载荷,延长其使用寿命。
其次,淬火工艺还可以提高金属材料的强度。
由于淬火后金属材料的晶粒得到了重新排列,其结晶粒度变小,消除了材料中的缺陷和组织上的不规则性,从而使得其强度得到了进一步提高。
这使得淬火后的金属材料在使用过程中具有更好的抗拉伸性和抗压性,能够承受更大的拉伸和压缩力。
另外,淬火工艺还可以改善金属材料的耐磨性。
在淬火过程中,金属表面会形成一层较硬的表面层,这使得金属材料具有更好的耐磨性和耐腐蚀性。
这意味着淬火后的金属材料可以在恶劣的工作环境下使用,不易受到外界环境的损害,从而延长了其使用寿命。
此外,淬火工艺还可以加工金属材料的综合性能。
在淬火过程中,金属材料的内部应力会被有效减少,从而使得材料具有更好的韧性和延展性。
这意味着淬火后的金属材料可以在使用过程中更加安全可靠,不易出现断裂和变形的情况。
综上所述,淬火工艺具有提高金属材料硬度、强度和耐磨性的特点,适用范围非常广泛。
其主要应用领域包括机械制造、汽车制造、航空航天、军工制造、模具制造、矿山开采等行业。
在这些领域中,金属材料通常需要具有较高的耐磨性和强度,以应对复杂多变的工作环境和加载情况。
淬火工艺正是可以满足这些需求的理想选择,因此受到了广泛的应用。
十种常用淬火方法
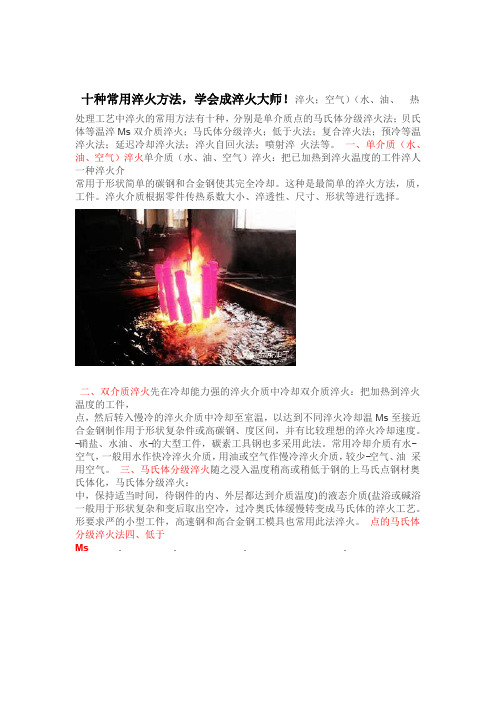
十种常用淬火方法,学会成淬火大师!淬火;空气)(水、油、热处理工艺中淬火的常用方法有十种,分别是单介质点的马氏体分级淬火法;贝氏体等温淬Ms双介质淬火;马氏体分级淬火;低于火法;复合淬火法;预冷等温淬火法;延迟冷却淬火法;淬火自回火法;喷射淬火法等。
一、单介质(水、油、空气)淬火单介质(水、油、空气)淬火:把已加热到淬火温度的工件淬人一种淬火介常用于形状简单的碳钢和合金钢使其完全冷却。
这种是最简单的淬火方法,质,工件。
淬火介质根据零件传热系数大小、淬透性、尺寸、形状等进行选择。
二、双介质淬火先在冷却能力强的淬火介质中冷却双介质淬火:把加热到淬火温度的工件,点,然后转入慢冷的淬火介质中冷却至室温,以达到不同淬火冷却温Ms至接近合金钢制作用于形状复杂件或高碳钢、度区间,并有比较理想的淬火冷却速度。
-硝盐、水油、水-的大型工件,碳素工具钢也多采用此法。
常用冷却介质有水-空气,一般用水作快冷淬火介质,用油或空气作慢冷淬火介质,较少-空气、油采用空气。
三、马氏体分级淬火随之浸入温度稍高或稍低于钢的上马氏点钢材奥氏体化,马氏体分级淬火:中,保持适当时间,待钢件的内、外层都达到介质温度)的液态介质(盐浴或碱浴一般用于形状复杂和变后取出空冷,过冷奥氏体缓慢转变成马氏体的淬火工艺。
形要求严的小型工件,高速钢和高合金钢工模具也常用此法淬火。
点的马氏体分级淬火法四、低于Ms . . . .Mf而高于低于Ms点的马氏体分级淬火法:浴槽温度低于工件用钢的Ms常尺寸较大时仍可获得和分级淬火相同的结果。
时,工件在该浴槽中冷却较快,用于尺寸较大的低淬透性钢工件。
五、贝氏体等温淬火法使其发生贝氏体等温淬火法:将工件淬入该钢下贝氏体温度的浴槽中等温,。
贝氏体等温淬火工艺主要三个步下贝氏体转变,一般在浴槽中保温30~60min贝氏体等温处理;常用于合金奥氏体化处理;②奥氏体化后冷却处理;③骤:①钢、高碳钢小尺寸零件及球墨铸铁件。
六、复合淬火法的马氏体,以下得体积分数为Ms10%~30%复合淬火法:先将工件急冷至常用于合金然后在下贝氏体区等温,使较大截面工件得到马氏体和贝氏体组织,工具钢工件。
淬火 工艺
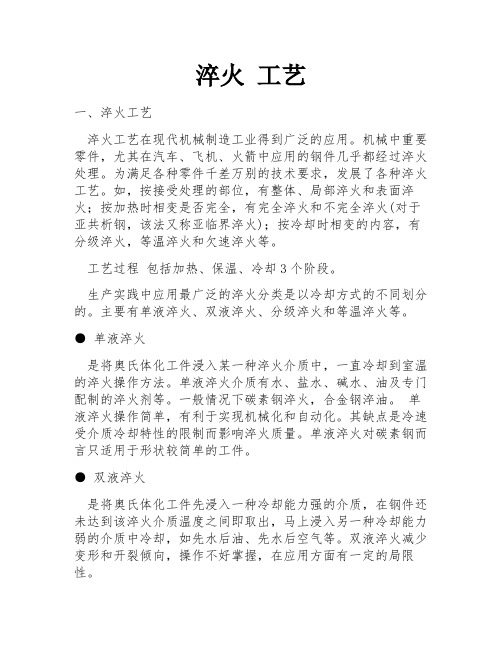
淬火工艺一、淬火工艺淬火工艺在现代机械制造工业得到广泛的应用。
机械中重要零件,尤其在汽车、飞机、火箭中应用的钢件几乎都经过淬火处理。
为满足各种零件千差万别的技术要求,发展了各种淬火工艺。
如,按接受处理的部位,有整体、局部淬火和表面淬火;按加热时相变是否完全,有完全淬火和不完全淬火(对于亚共析钢,该法又称亚临界淬火);按冷却时相变的内容,有分级淬火,等温淬火和欠速淬火等。
工艺过程包括加热、保温、冷却3个阶段。
生产实践中应用最广泛的淬火分类是以冷却方式的不同划分的。
主要有单液淬火、双液淬火、分级淬火和等温淬火等。
● 单液淬火是将奥氏体化工件浸入某一种淬火介质中,一直冷却到室温的淬火操作方法。
单液淬火介质有水、盐水、碱水、油及专门配制的淬火剂等。
一般情况下碳素钢淬火,合金钢淬油。
单液淬火操作简单,有利于实现机械化和自动化。
其缺点是冷速受介质冷却特性的限制而影响淬火质量。
单液淬火对碳素钢而言只适用于形状较简单的工件。
● 双液淬火是将奥氏体化工件先浸入一种冷却能力强的介质,在钢件还未达到该淬火介质温度之间即取出,马上浸入另一种冷却能力弱的介质中冷却,如先水后油、先水后空气等。
双液淬火减少变形和开裂倾向,操作不好掌握,在应用方面有一定的局限性。
● 马氏体分级淬火(分级淬火)是将奥氏体化工件先浸入温度稍高或稍低于钢的马氏体点的液态介质(盐浴或碱浴)中,保持适当的时间,待钢件的内、外层都达到介质温度后取出空冷,以获得马氏体组织的淬火工艺。
分级淬火由于在分级温度停留到工件内外温度一致后空冷,所以能有效地减少相变应力和热应力,减少淬火变形和开裂倾向。
分级淬火适用于对于变形要求高的合金钢和高合金钢工件,也可用于截面尺寸不大、形状复杂地碳素钢工件。
这种冷却方法的特点是先将工件浸入温度略高于Ms的浴槽,在浴槽中保温至工件表面与中心均冷至浴槽的温度,然后取出空冷。
浴槽温度一般为Ms+(10~20)℃。
浴槽中介质的成分采用硝盐浴、碱浴、中性盐浴● 贝氏体等温淬火是将钢件奥氏体化,使之快冷到贝氏体转变温度区间(260~400℃)等温保持,使奥氏体转变为贝氏体的淬火工艺,有时也叫等温淬火。
20crmnti钢淬火的工艺
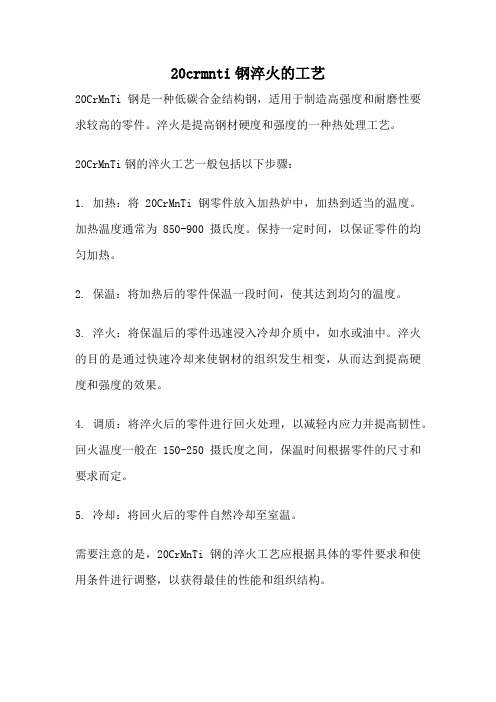
20crmnti钢淬火的工艺
20CrMnTi钢是一种低碳合金结构钢,适用于制造高强度和耐磨性要求较高的零件。
淬火是提高钢材硬度和强度的一种热处理工艺。
20CrMnTi钢的淬火工艺一般包括以下步骤:
1. 加热:将20CrMnTi钢零件放入加热炉中,加热到适当的温度。
加热温度通常为850-900摄氏度。
保持一定时间,以保证零件的均匀加热。
2. 保温:将加热后的零件保温一段时间,使其达到均匀的温度。
3. 淬火:将保温后的零件迅速浸入冷却介质中,如水或油中。
淬火的目的是通过快速冷却来使钢材的组织发生相变,从而达到提高硬度和强度的效果。
4. 调质:将淬火后的零件进行回火处理,以减轻内应力并提高韧性。
回火温度一般在150-250摄氏度之间,保温时间根据零件的尺寸和要求而定。
5. 冷却:将回火后的零件自然冷却至室温。
需要注意的是,20CrMnTi钢的淬火工艺应根据具体的零件要求和使用条件进行调整,以获得最佳的性能和组织结构。
淬火工艺的基本原理及应用

淬火工艺的基本原理及应用1. 淬火工艺的基本原理淬火是金属材料热处理中的一种重要工艺,通过迅速冷却金属材料,使其产生组织和性能的变化,从而提高材料的硬度、强度和耐磨性。
淬火工艺的基本原理主要包括以下几个方面:•相变原理:淬火过程中,金属材料经历了相变过程,其中最常见的是奥氏体转变为马氏体。
相变过程中的晶体结构变化,导致了材料硬度的提高。
•冷却速度:淬火工艺中,冷却速度是至关重要的。
快速冷却可以使材料快速达到马氏体转变的条件,从而得到高硬度的淬硬层。
•冷却介质:常用的淬火介质有水、油和盐水等。
不同的冷却介质会对淬火效果产生不同的影响。
•温度控制:淬火温度的控制对淬火效果有重要影响。
过高或过低的温度都会影响到材料的组织和性能。
2. 淬火工艺的应用淬火工艺在金属材料的加工和制造过程中有着广泛的应用。
主要应用在以下几个方面:2.1 工具制造淬火工艺在工具制造中起着重要的作用。
通过淬火可以使工具材料达到更高的硬度和耐磨性,提高工具的使用寿命。
常见的应用包括刀具、冲压模具、钳工工具等。
2.2 零件制造淬火工艺在零件制造中也具有广泛的应用。
通过淬火可以改变材料的性能,提高零件的强度和硬度,满足特定的使用要求。
常见的应用包括汽车发动机零件、机械传动零件、轴承等。
2.3 钢铁冶炼淬火工艺在钢铁冶炼中也是重要的一环。
通过淬火可以改变钢材的组织和性能,使其具有更好的强度和韧性。
常见的应用包括高强度钢、合金钢等。
2.4 热处理工艺淬火是热处理中不可或缺的环节。
热处理是通过控制材料的加热和冷却过程,使其达到更好的组织和性能。
淬火作为其中的一个关键步骤,对最终的材料性能起着决定性的作用。
3. 淬火工艺的优化为了进一步提高淬火工艺的效果,可以采取以下优化措施:•加入淬火剂:在淬火过程中,加入一定的淬火剂可以使冷却效果更加均匀,避免金属材料出现裂纹等问题。
•控制冷却速度:通过控制冷却速度,可以使材料达到最佳的淬火效果,避免出现过渡结构和过渡硬度。
十种常用淬火方法汇总

淬火方法大全,用过3个就是大师!十种常用淬火方法汇总热处理工艺中淬火的常用方法有十种,分别是单介质(水、油、空气)淬火;双介质淬火;马氏体分级淬火;低于Ms点的马氏体分级淬火法;贝氏体等温淬火法;复合淬火法;预冷等温淬火法;延迟冷却淬火法;淬火自回火法;喷射淬火法等。
一、单介质(水、油、空气)淬火单介质(水、油、空气)淬火:把已加热到淬火温度的工件淬人一种淬火介质,使其完全冷却。
这种是最简单的淬火方法,常用于形状简单的碳钢和合金钢工件。
淬火介质根据零件传热系数大小、淬透性、尺寸、形状等进行选择。
二、双介质淬火双介质淬火:把加热到淬火温度的工件,先在冷却能力强的淬火介质中冷却至接近Ms点,然后转入慢冷的淬火介质中冷却至室温,以达到不同淬火冷却温度区间,并有比较理想的淬火冷却速度。
用于形状复杂件或高碳钢、合金钢制作的大型工件,碳素工具钢也多采用此法。
常用冷却介质有水-油、水-硝盐、水-空气、油-空气,一般用水作快冷淬火介质,用油或空气作慢冷淬火介质,较少采用空气。
三、马氏体分级淬火马氏体分级淬火:钢材奥氏体化,随之浸入温度稍高或稍低于钢的上马氏点的液态介质(盐浴或碱浴)中,保持适当时间,待钢件的内、外层都达到介质温度后取出空冷,过冷奥氏体缓慢转变成马氏体的淬火工艺。
一般用于形状复杂和变形要求严的小型工件,高速钢和高合金钢工模具也常用此法淬火。
四、低于Ms点的马氏体分级淬火法低于Ms点的马氏体分级淬火法:浴槽温度低于工件用钢的Ms而高于Mf时,工件在该浴槽中冷却较快,尺寸较大时仍可获得和分级淬火相同的结果。
常用于尺寸较大的低淬透性钢工件。
五、贝氏体等温淬火法贝氏体等温淬火法:将工件淬入该钢下贝氏体温度的浴槽中等温,使其发生下贝氏体转变,一般在浴槽中保温30~60min。
贝氏体等温淬火工艺主要三个步骤:①奥氏体化处理;②奥氏体化后冷却处理;③贝氏体等温处理;常用于合金钢、高碳钢小尺寸零件及球墨铸铁件。
六、复合淬火法复合淬火法:先将工件急冷至Ms以下得体积分数为10%~30%的马氏体,然后在下贝氏体区等温,使较大截面工件得到马氏体和贝氏体组织,常用于合金工具钢工件。
淬火的方法20

淬火的方法20淬火是一种非常重要的制作金属工艺,能够使金属具备更加强大的力量和韧性。
在制作的过程中,我们需要经过多个步骤才能够完成。
这些步骤包括加热、保温、冷却等,每个步骤都需要严格的控制条件才能够取得最好的效果。
下面我将为大家介绍淬火的方法有哪些。
一、传统炭火淬火传统炭火淬火方法是金属淬火的最早工艺。
这种方法的特点是温度控制比较困难,因为炭火火情的不稳定性,但是金属淬火的品质很高,得到的回火组织非常精密,比较适合制作高弹性的弹簧和刀具等冲击负荷较大的应用。
二、油淬火油淬火法是一种简单易行、广泛应用的淬火方法。
淬火时,将需要淬火的工件放在800℃左右的淬火炉中加热,然后快速浸入预先准备好的醇类或石油类淬火介质中。
油淬火具有深淬度、淬火速度适中等特点,对于一些较为脆性的金属也比较适用。
三、水淬火水淬火法是淬火中应用比较早,温度较低的淬火方法。
在水中冷却,工件的表面快速冷却,使其内部组织发生相变,从而提高金属材质的硬度和抗拉强度,但是也容易产生裂纹和金属组织变形缺陷,需要特别注意。
四、空气淬火空气淬火是一种以空气为淬火介质将高温的钢材快速冷却。
这种方法可以降低材料奥氏体晶粒的尺寸,从而提高金属的硬度和强度。
空气淬火方法可以进行自然冷却、局部冷却或全局冷却。
五、冷却剂淬火冷却剂淬火主要指的是在淬火介质中添加一定量的冷却剂,从而加快淬火时的冷却速度,得到高硬度的金属材料。
常用的冷却剂包括盐水、盐酸、硫酸和醋酸等。
冷却剂淬火适用于制作强度要求较高的金属材料。
六、淬火加回火淬火加回火法是金属淬火与回火相结合的方法。
在淬火完成后,将工件进行回火处理,可以提高其强度和韧性,并且有效避免淬火产生的脆性缺陷和变形缺陷,也可以根据实际需要对不同部位进行微量回火,达到最佳效果。
七、快速淬火快速淬火是在高温下进行的一种淬火方法,一般快速冷却介质用会水冷,淬出来的工件会拥有很高的硬度,有加深工件的界面硬度和活性表面积等优点,适合用于制备化工、机械、新材料、数码设备等领域的高新产品。
淬火的工艺

淬火是一种热处理工艺,用于提高金属材料的硬度和强度。
下面是通用的淬火工艺步骤:
1.加热(Heating):将待淬火的金属材料加热到适当的温度。
这个温度通常称为"淬火温
度"或"临界温度",它取决于材料的组成和硬化要求。
2.保温(Soaking):在达到淬火温度后,将材料保持在该温度下一定的时间以确保温度
均匀分布,使材料内部也达到所需的温度。
3.急冷(Quenching):将加热保温完成的材料迅速浸入冷却介质中,如水、油或盐溶液。
冷却介质的选择取决于材料的类型和硬化要求。
4.温度回火(Tempering):在材料的冷却过程中,会形成一些脆性的残余应力。
为了增
加材料的韧性和减少内部应力,可以将材料加热到较低的温度进行回火处理。
回火温度和时间根据材料的硬化要求来确定。
注意,淬火工艺的参数如加热温度、保温时间、冷却介质的选择等都取决于具体的金属材料和应用要求。
因此,在实际操作中,需要根据材料的特性和硬化要求进行相应的工艺调整和测试。
此外,不同类型的钢材可能需要不同的淬火工艺,例如气体淬火、盐浴淬火或真空淬火。
对于高合金钢和特殊钢,可能还需要采用复杂的淬火工艺来满足其特殊的要求。
因此,在具体应用中,请遵循相关的标准和工艺指南,并参考专业人士的建议。
淬火以及淬火工艺

低合金钢:
淬火温度也应根据其临界点(Ac1及Ac3)来 选定,但考虑到合金元素的作用,为了加 速奥氏体化, 过共析低合金钢:Ac1+(50~110 °C) , 亚共析低合金钢:Ac3+(30~100 °C); 高速钢、高铬钢及不锈钢应根据合金碳化 物溶入奥氏体的程度选定。一般高速钢的 淬火加热温度比其Ac1高出30°C以上。
第八章 淬火及淬火工艺
主要内容
1. 淬火加热 2. 淬火介质 3. 钢的淬透性 4. 淬火工艺 5. 表面淬火 6. 淬火缺陷
前
言1
淬火是热处理工艺中最重要的工艺。 从广义上说,淬火是将合金在高温下所 具有的状态以过冷、过饱和状态固定至室 温,或使基体转变成晶体结构与高温状态 不同的亚稳状态的热处理形式。
常用的盐浴成分及其正常使用温度见表8. 5。
8. 1. 3. 3固体介质
流态床加热采用固体粒子(石墨、石英砂或刚玉等)作为加 热介质。当通人一定流速的气流时,粒子就会呈悬浮状像 流体一样地运动,在粒子堆表面呈沸腾状态,内部粒子则 呈快速湍流运动,这种称为粒子被流态化。通过电加热使 流动粒子很快被加热到所需温度,靠它们来加热工件。 使用这种加热介质的炉子名称曾很多,如流动粒子炉、流 化床、流态床或沸腾层炉等,目前国家标准中称之为流态 床。采用这种加热介质的优点很多:①升温快(20多分钟可 升至850°C ),炉温较均匀且易控制;②使用温度范围广 泛(高、中、低温均可);③工件处理后表面无氧化脱碳;④ 启动方便,节省电能等。但它还存在一些缺点,如工作电 压较高(60~80V),有粉尘逸出,炉子生产能力较小等,均 待进一步改进。
原因如下:
(1)奥氏体中溶人碳量的增加使MS点降低,淬火后所得的 残余奥氏体量将增多,结果使淬火钢的硬度下降; (2)奥氏体的晶粒粗化,淬火后得到粗大马氏体,使钢的脆 性大为增加; (3)空气介质加热时钢的脱碳氧化严重,降低淬火钢的表面 质量;
淬火工艺流程
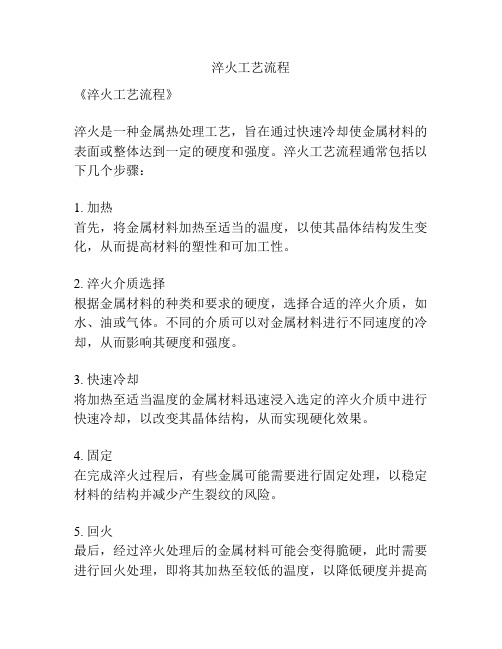
淬火工艺流程
《淬火工艺流程》
淬火是一种金属热处理工艺,旨在通过快速冷却使金属材料的表面或整体达到一定的硬度和强度。
淬火工艺流程通常包括以下几个步骤:
1. 加热
首先,将金属材料加热至适当的温度,以使其晶体结构发生变化,从而提高材料的塑性和可加工性。
2. 淬火介质选择
根据金属材料的种类和要求的硬度,选择合适的淬火介质,如水、油或气体。
不同的介质可以对金属材料进行不同速度的冷却,从而影响其硬度和强度。
3. 快速冷却
将加热至适当温度的金属材料迅速浸入选定的淬火介质中进行快速冷却,以改变其晶体结构,从而实现硬化效果。
4. 固定
在完成淬火过程后,有些金属可能需要进行固定处理,以稳定材料的结构并减少产生裂纹的风险。
5. 回火
最后,经过淬火处理后的金属材料可能会变得脆硬,此时需要进行回火处理,即将其加热至较低的温度,以降低硬度并提高
韧性。
淬火工艺流程的确切操作方式和参数需要根据具体的金属材料和要求来确定,对于不同种类的金属和不同用途的制品,淬火工艺流程也会有所差异。
同时,精准控制淬火工艺流程,能够有效提高金属材料的硬度和强度,从而满足不同场合的使用要求。
热处理工艺-淬火
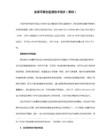
分级淬火由于在分级温度停留到工件内外温度一致后空冷,所以能有效地减少相变应力和热应力,减少淬火变形和开裂倾向。分级淬火适用于对于变形要求高的合金钢和高合金钢工件,也可用于截面尺寸不大、形状复杂地碳素钢工件。
● 贝氏体等温淬火
是将钢件奥氏体化,使之快冷到贝氏体转变温度区间(260~400℃)等温保持,使奥氏体转变为贝氏体的淬火工艺,有时也叫等温淬火。一般保温时间为30~60min。
常用的淬火介质有水、水溶液、矿物油、熔盐、熔碱等。
● 水
水是冷却能力较强的淬火介质。来源广、价格低、成分稳定不易变质。缺点是在C曲线的“鼻子”区(500~600℃左右),水处于蒸汽膜阶段,冷却不够快,会形成“软点”;而在马氏体转变温度区(300~100℃),水处于沸腾阶段,冷却太快,易使马氏体转变速度过快而产生很大的内应力,致使工件变形甚至开裂。当水温升高,水中含有较多气体或水中混入不溶杂质(如油、肥皂、泥浆等),均会显著降低其冷却能力。因此水适用于截面尺寸不大、形状简单的碳素钢工件的淬火冷却。
过共析钢的淬火加热温度不能低于AC1,因为此时钢材尚未奥氏体化。若加热到略高于AC1温度时,珠光体完全转变承奥氏体,并又少量的渗碳体溶入奥氏体。此时奥氏体晶粒细小,且其碳的质量分数已稍高与共析成分。如果继续升高温度,则二次渗碳体不断溶入奥氏体,致使奥氏体晶粒不断长大,其碳浓度不断升高,会导致淬火变形倾向增大、淬火组织显微裂纹增多及脆性增大。同时由于奥氏体含碳量过高,使淬火后残余奥氏体数量增多,降低工件的硬度和耐磨性。因此过共析钢的淬火加热温度高于AC1太多是不合适的,加热到完全奥氏体化的ACm或以上温度就更不合适。
采用高温淬火可获得较多的板条状马氏体或使全部板条马氏体提高强度和韧性。如16Mn钢在940℃淬火,5CrMnMo钢在890℃淬火,20CrMnMo钢在920℃淬火,效果较好。
锻造铝合金淬火工艺

锻造铝合金淬火工艺
锻造铝合金淬火工艺主要包括以下步骤:
1.淬火前的准备:淬火前要清除冷变形加工时附着在表面上的油垢
及污物,常用汽油、丙酮、香蕉水等擦试,也可以浸泡于碱性溶液中。
碱性溶液的成分是:每分溶液含50g磷酸钠、1g氢氧化钠和3g水玻璃。
溶液温度50~60℃,浸泡时间5~10min。
也可以用洗涤剂配成溶液除油垢。
2.淬火操作:
a)加热炉膛温度均匀,控温精度在±(2~3)℃范围内,最
大不超过±5℃。
b)淬火转移时间根据零件成分、形状和生产条件而定:一般
小零件转移时间不超过25s,大零件不超过40s,板材不
超过30s,超硬铝不超过15s。
c)工件淬火加热捆扎用铝带、铝丝或铁丝。
铁丝应无镀锌
层,不能用铜丝捆扎,夹具不能用铜制作,以防铜、锌扩
散入零件,降低工件抗蚀性和产生局部熔化。
d)在硝盐炉中加热时,零件与槽底、槽壁的距离以及零件浸
入液面下的深度不小于100mm。
零件之间应有一定间隙,
不要紧靠。
e)在空气炉中加热零件离炉门200mm以上,离电热元件隔板
100mm以上。
零件放置位置不得防碍热风循环。
板材加
热,板材之间距离不小于20mm。
f)焊接铝件不得在硝盐槽中加热,以防硝盐钻进使焊缝腐
蚀。
g)为防止硝盐腐蚀,盐浴的杂质总质量分数不超过2%。
碱中
碳酸钠质量分数不超过1%。
淬火 工艺

淬火工艺淬火是一种常见的金属热处理工艺,通过控制金属的加热和冷却过程,使其获得理想的力学性能和组织结构。
淬火工艺的应用广泛,包括钢铁、铝合金、铜合金等各种金属材料,可用于增强材料的硬度、强度和耐磨性。
本文将从淬火的基本原理、工艺步骤以及应用领域等方面进行介绍。
淬火是通过将金属加热至适当温度,保持一段时间后迅速冷却而实现的。
其基本原理是利用金属的相变规律来改善金属的力学性能。
在加热过程中,金属内部的晶体结构会发生改变,原有的晶粒会长大并重新排列。
当金属冷却时,晶粒会重新结晶并形成细小而均匀的组织结构,从而提高金属的硬度和强度。
淬火工艺包括加热、保温和冷却三个步骤。
首先,将金属材料置于加热炉中,加热至淬火温度。
不同金属材料的淬火温度不同,通常需要根据具体材料的特性来确定。
在加热过程中,需要控制加热速度和温度均匀性,以确保金属材料能够达到适当的温度。
其次,保温是指将金属材料在一定温度下保持一段时间,使其内部晶粒重新排列并长大。
保温时间的长短也需要根据具体材料来确定。
最后,冷却是将加热保温后的金属材料迅速冷却至室温。
冷却速度的快慢也会对淬火效果产生影响,通常采用水、油、盐等不同介质进行冷却,以控制金属的组织结构和性能。
淬火工艺的应用非常广泛。
在钢铁行业中,淬火可用于生产各种工具钢、合金钢和汽车零部件等。
例如,汽车发动机的曲轴、凸轮轴等零部件经过淬火处理后,能够提高其硬度和耐磨性,延长使用寿命。
在铝合金和铜合金等材料中,淬火可用于改善材料的强度和塑性,提高其抗拉强度和耐腐蚀性。
此外,淬火也常用于制造刀具、模具等工具,在提高硬度和耐磨性的同时,保持一定的韧性,以提高工具的使用寿命和效率。
淬火是一种重要的金属热处理工艺,通过控制金属的加热和冷却过程,使其获得理想的力学性能和组织结构。
淬火工艺的应用广泛,可用于增强材料的硬度、强度和耐磨性。
在实际应用中,需要根据具体材料的特性和要求来选择合适的淬火工艺参数,以获得最佳的处理效果。
淬火处理方法

淬火处理方法一、引言淬火处理是一种常用的金属材料热处理方法,通过控制材料的冷却速度和温度,使其获得理想的力学性能和组织结构。
本文将介绍淬火处理的原理、工艺和影响因素,以及常见的淬火方法。
二、淬火处理的原理淬火处理的原理是利用材料在高温下形成的奥氏体晶格结构,通过快速冷却使其转变为马氏体,从而获得高强度和良好的韧性。
淬火处理的基本原理是通过淬火介质的选择和冷却速度的控制,使材料中的奥氏体尽可能转变成马氏体,从而改善材料的力学性能。
三、淬火处理的工艺1. 加热:将待处理材料加热到适当的温度,使其达到奥氏体化的温度区间。
加热温度一般根据材料的组织结构和性能要求确定。
2. 保温:在加热达到所需温度后,需要保持一定时间,使材料均匀加热,促进奥氏体的形成。
3. 冷却:淬火介质的选择和冷却速度的控制是决定淬火效果的关键。
常用的淬火介质有水、油和空气等。
其中,水冷却速度最快,油次之,空气冷却速度最慢。
4. 回火:淬火后的材料通常会出现过硬和脆性的问题,为了改善材料的韧性,需要进行回火处理。
回火温度和时间的选择需要根据材料的具体情况进行调整。
四、淬火方法1. 正火:将材料加热到适当温度,保温一段时间后,通过水冷却使其快速冷却。
正火适用于大多数碳钢和合金钢材料。
2. 深冷:在材料加热到适当温度后,通过快速冷却使其达到低温状态,然后再进行回火处理。
深冷适用于特殊的合金钢材料。
3. 水淬:将材料加热到适当温度,然后通过水冷却使其快速冷却。
水淬适用于碳钢和合金钢材料。
4. 油淬:将材料加热到适当温度,然后通过油冷却使其快速冷却。
油淬适用于一些高碳钢材料。
5. 空冷:将材料加热到适当温度后,自然冷却至室温。
空冷适用于一些低碳钢材料。
五、淬火处理的影响因素1. 材料的化学成分:材料的化学成分会直接影响淬火的效果和性能。
合理调整化学成分,可以改善材料的硬度、韧性和耐磨性。
2. 材料的组织结构:材料的组织结构与淬火效果密切相关。
淬火
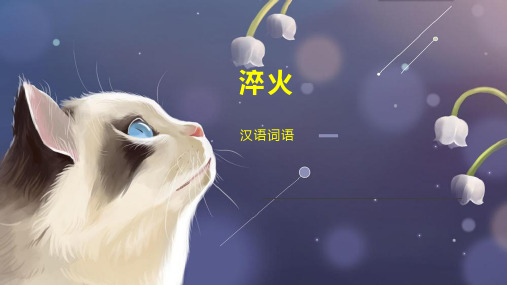
工件局部或表层快速加热奥氏体化后,加热区的热量自行向未加热区传到,从而使奥氏体化区迅速冷却的淬 火。
应用
淬火工艺在现代机械制造工业得到广泛的应用。机械中重要零件,尤其在汽车、飞机、火箭中应用的钢件几 乎都经过淬火处理。为满足各种零件千差万别的技术要求,发展了各种淬火工艺。如,按接受处理的部位,有整 体、局部淬火和表面淬火;按加热时相变是否完全,有完全淬火和不完全淬火(对于亚共析钢,该法又称亚临界 淬火);按冷却时相变的内容,有分级淬火,等温淬火和欠速淬火等。
HR-150型电动洛氏硬度计将金属工件加热到某一适当温度并保持一段时间,随即浸入淬冷介质中快速冷却的 金属热处理工艺。常用的淬冷介质有盐水、水、矿物油、空气等。淬火可以提高金属工件的硬度及耐磨性,因而 广泛用于各种工、模、量具及要求表面耐磨的零件(如齿轮、轧辊、渗碳零件等)。通过淬火与不同温度的回火 配合,可以大幅度提高金属的强度、韧性下降及疲劳强度,并可获得这些性能之间的配合(综合机械性能)以满 足不同的使用要求。另外淬火还可使一些特殊性能的钢获得一定的物理化学性能,如淬火使永磁钢增强其铁磁性、 不锈钢提高其耐蚀性等。淬火工艺主要用于钢件。常用的钢在加热到临界温度以上时,原有在室温下的组织将全 部或大部转变为奥氏体。随后将钢浸入水或油中快速冷却,奥氏体即转变为马氏体。与钢中其他组织相比,马氏 体硬度最高。淬火时的快速冷却会使工件内部产生内应力,当其大到一定程度时工件便会发生扭曲变形甚至开裂。 为此必须选择合适的冷却方法。根据冷却方法,淬火工艺分为单液淬火、双介质淬火、马氏体分级淬火和贝氏体 等温淬火4类。
工艺
加热温度 保温
冷却 工件硬度
淬火加热温度(4张)以钢的相变临界点为依据,加热淬火时要形成细小、均匀奥氏体晶粒,淬火后获得细小 马氏体组织。碳素钢的淬火加热温度范围如图《淬火加热温度》所示,由本图示出的淬火温度选择原则也适用于 大多数合金钢,尤其低合金钢。亚共析钢加热温度为Ac3温度以上30~50℃。从《淬火加热温度》图中可以看出 高温下钢的状态处在单相奥氏体(A)区内,故称为完全淬火。如亚共析钢加热温度高于Ac1、低于Ac3温度,则 高温下部分先共析铁素体未完全转变成奥氏体,即为不完全(或亚临界)淬火。过共析钢淬火温度为Ac1温度以 上30~50℃,这温度范围处于奥氏体与渗碳体(A+C)双相区。因而过共析钢的正常的淬火仍属不完全淬火,淬 火后得到马氏体基体上分布渗碳体的组织。这-组织状态具有高硬度和高耐磨性。对于过共析钢,若加热温度过高, 先共析渗碳体溶解过多,甚至完全溶解,则奥氏体晶粒将发生长大,奥氏体碳含量也增加。淬火后,粗大马氏体 组织使钢件淬火态微区内应力增加,微裂纹增多,零件的变形和开裂倾向增加;由于奥氏体碳浓度高,马氏体点 下降,残留奥氏体量增加,使工件的硬度和耐磨性降低。常用钢种淬火的温度如图《淬火加热温度》所示,表为 常用钢种淬火的加热温度。
十种常用淬火方法

十种常用淬火方法,学会成淬火大师!热处理工艺中淬火的常用方法有十种,分别是单介质(水、油、空气)淬火;双介质淬火;马氏体分级淬火;低于Ms点的马氏体分级淬火法;贝氏体等温淬火法;复合淬火法;预冷等温淬火法;延迟冷却淬火法;淬火自回火法;喷射淬火法等。
一、单介质(水、油、空气)淬火单介质(水、油、空气)淬火:把已加热到淬火温度的工件淬人一种淬火介质,使其完全冷却。
这种是最简单的淬火方法,常用于形状简单的碳钢和合金钢工件。
淬火介质根据零件传热系数大小、淬透性、尺寸、形状等进行选择。
二、双介质淬火双介质淬火:把加热到淬火温度的工件,先在冷却能力强的淬火介质中冷却至接近Ms点,然后转入慢冷的淬火介质中冷却至室温,以达到不同淬火冷却温度区间,并有比较理想的淬火冷却速度。
用于形状复杂件或高碳钢、合金钢制作的大型工件,碳素工具钢也多采用此法。
常用冷却介质有水-油、水-硝盐、水-空气、油-空气,一般用水作快冷淬火介质,用油或空气作慢冷淬火介质,较少采用空气。
三、马氏体分级淬火马氏体分级淬火:钢材奥氏体化,随之浸入温度稍高或稍低于钢的上马氏点的液态介质(盐浴或碱浴)中,保持适当时间,待钢件的内、外层都达到介质温度后取出空冷,过冷奥氏体缓慢转变成马氏体的淬火工艺。
一般用于形状复杂和变形要求严的小型工件,高速钢和高合金钢工模具也常用此法淬火。
四、低于Ms点的马氏体分级淬火法低于Ms点的马氏体分级淬火法:浴槽温度低于工件用钢的Ms而高于Mf 时,工件在该浴槽中冷却较快,尺寸较大时仍可获得和分级淬火相同的结果。
常用于尺寸较大的低淬透性钢工件。
五、贝氏体等温淬火法贝氏体等温淬火法:将工件淬入该钢下贝氏体温度的浴槽中等温,使其发生下贝氏体转变,一般在浴槽中保温30~60min。
贝氏体等温淬火工艺主要三个步骤:①奥氏体化处理;②奥氏体化后冷却处理;③贝氏体等温处理;常用于合金钢、高碳钢小尺寸零件及球墨铸铁件。
六、复合淬火法复合淬火法:先将工件急冷至Ms以下得体积分数为10%~30%的马氏体,然后在下贝氏体区等温,使较大截面工件得到马氏体和贝氏体组织,常用于合金工具钢工件。
淬火工艺——精选推荐

淬火工艺钢的淬火是将钢奥氏体化后以适当的冷却速度冷却,使工件在横截面内全部或在一定范围内发生马氏体不稳定组织结构转变的热处理工艺。
一. 淬火工件的工艺流程一般工件:淬火→清洗→回火→喷砂(或喷丸等)表面清理→检验。
轴类零件及易变形工件:淬火→清洗→回火→校直→去应力处理→喷砂→检验。
二. 淬火前的准备(1)核对工件数量、材质及尺寸,并检查工件有无裂纹、碰伤、缺边、锐边、尖角及锈蚀等影响淬火质量的缺陷。
(2)根据图样及工艺文件,明确淬火的具体要求,如硬度、局部淬火范围等。
(3)根据淬火要求,设计选用合适的工夹具,有的工件进行适当的绑扎,在易产生裂纹的部位,采取相应的防护措施,如用铁皮或石棉绳包扎及堵孔等。
(4)表面不允许氧化、脱碳的工件,应在盐浴炉或预抽真空保护气氛炉中加热,或采取以下防护措施:a. 涂料防护b. 将工件装入盛有木炭或已使用过的铸铁屑的铁箱中,加盖密封。
(5)大批工件必须作单件或小批量试淬,制订工艺后方可进行批量淬火,并在生产过程中经常抽检。
三. 装炉(1)允许不同材质但具有相同加热工艺的工件装入同一炉中加热。
(2)装炉工件均应干燥、不得有油污及其他脏物。
(3)截面大小不同的工件装入同一炉时,大件应放在炉膛后部,大、小工件分别计算保温时间。
(4)装炉时必须将工件有规律摆放在装炉架或炉底板上,用钩子、钳子或专用工具堆放,不得将工件直接抛入炉内,以免碰伤工件或损坏炉衬。
(5)细长工件必须在井式炉或盐炉中垂直吊挂加热,以减少变形。
(6)在箱式炉中装工件加热时,一般为单层排列,工件间隙10~30mm。
小件允许适当堆放,但保温时间应适当增加。
四. 加热1. 加热方式(1)碳钢及合金钢工件,一般可直接装入比规定的淬火温度高20~30℃的炉中加热。
(2)高碳高合金钢及形状复杂的工件应先预热。
2. 加热温度选择。
3. 工件加热时间的计算:炉中的工件应在规定的加热温度范围内保持适当的时间,保证必要的组织转变和扩散。
淬火工艺及要求

烈火锤打造刀刃——淬火工艺及要求
淬火是一种重要的热处理工艺,通过控制材料的加热、保温和冷
却过程,使材料获得特定的组织和性能,从而提高材料的硬度、强度
和耐磨性。
淬火工艺的要求包括以下几个方面:
一、温度控制:淬火的第一步是将材料加热到适当的温度。
一般
来说,淬火温度应该略低于材料的临界温度,以避免材料发生坍塌或
过度退火。
温度的控制必须非常准确,否则会影响淬火的效果。
二、保温时间:材料在达到淬火温度后需要保温一定时间,以保
证材料内部的温度均匀。
保温时间的长短与材料的尺寸和厚度有关,
一般来说要根据实际情况选择。
三、淬火介质:淬火介质是指将材料从高温迅速冷却的介质,通
常是水、油、盐水或空气。
选择合适的淬火介质可以使材料获得更好
的淬火效果和性能。
四、冷却速率:冷却速率是影响淬火效果和性能的一项关键因素。
冷却速率有多种方式,如改变淬火介质的温度和流量、改变材料的深度、宽度和厚度等。
不同的材料需要不同的冷却速率。
五、温度回火:淬火后的材料会出现应力和脆性,需要通过温度
回火的方式来消除。
温度回火的温度和时间需要根据材料的组织和性
能来确定。
总之,淬火工艺需要结合材料的特点和实际情况来进行。
只有掌握了淬火工艺,并且在实际生产中不断进行改进和提高,才能使材料获得更好的性能和效果。
1144淬火工艺
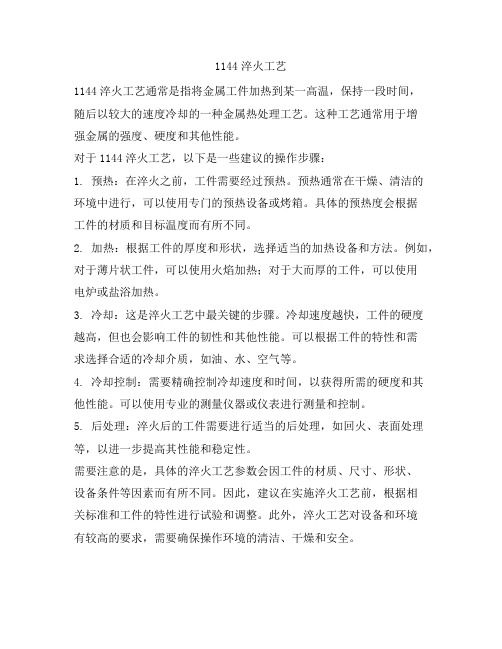
1144淬火工艺
1144淬火工艺通常是指将金属工件加热到某一高温,保持一段时间,
随后以较大的速度冷却的一种金属热处理工艺。
这种工艺通常用于增
强金属的强度、硬度和其他性能。
对于1144淬火工艺,以下是一些建议的操作步骤:
1. 预热:在淬火之前,工件需要经过预热。
预热通常在干燥、清洁的
环境中进行,可以使用专门的预热设备或烤箱。
具体的预热度会根据
工件的材质和目标温度而有所不同。
2. 加热:根据工件的厚度和形状,选择适当的加热设备和方法。
例如,对于薄片状工件,可以使用火焰加热;对于大而厚的工件,可以使用
电炉或盐浴加热。
3. 冷却:这是淬火工艺中最关键的步骤。
冷却速度越快,工件的硬度
越高,但也会影响工件的韧性和其他性能。
可以根据工件的特性和需
求选择合适的冷却介质,如油、水、空气等。
4. 冷却控制:需要精确控制冷却速度和时间,以获得所需的硬度和其
他性能。
可以使用专业的测量仪器或仪表进行测量和控制。
5. 后处理:淬火后的工件需要进行适当的后处理,如回火、表面处理等,以进一步提高其性能和稳定性。
需要注意的是,具体的淬火工艺参数会因工件的材质、尺寸、形状、
设备条件等因素而有所不同。
因此,建议在实施淬火工艺前,根据相
关标准和工件的特性进行试验和调整。
此外,淬火工艺对设备和环境
有较高的要求,需要确保操作环境的清洁、干燥和安全。
古代的淬火工艺
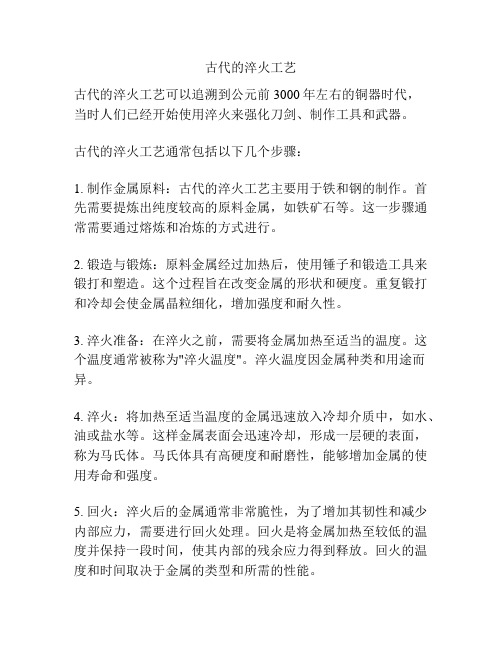
古代的淬火工艺
古代的淬火工艺可以追溯到公元前3000年左右的铜器时代,
当时人们已经开始使用淬火来强化刀剑、制作工具和武器。
古代的淬火工艺通常包括以下几个步骤:
1. 制作金属原料:古代的淬火工艺主要用于铁和钢的制作。
首先需要提炼出纯度较高的原料金属,如铁矿石等。
这一步骤通常需要通过熔炼和冶炼的方式进行。
2. 锻造与锻炼:原料金属经过加热后,使用锤子和锻造工具来锻打和塑造。
这个过程旨在改变金属的形状和硬度。
重复锻打和冷却会使金属晶粒细化,增加强度和耐久性。
3. 淬火准备:在淬火之前,需要将金属加热至适当的温度。
这个温度通常被称为"淬火温度"。
淬火温度因金属种类和用途而异。
4. 淬火:将加热至适当温度的金属迅速放入冷却介质中,如水、油或盐水等。
这样金属表面会迅速冷却,形成一层硬的表面,称为马氏体。
马氏体具有高硬度和耐磨性,能够增加金属的使用寿命和强度。
5. 回火:淬火后的金属通常非常脆性,为了增加其韧性和减少内部应力,需要进行回火处理。
回火是将金属加热至较低的温度并保持一段时间,使其内部的残余应力得到释放。
回火的温度和时间取决于金属的类型和所需的性能。
古代的淬火工艺技术相比现代有所限制,但仍然能够显著改善金属制品的硬度和强度。
这些技术在古代的军事装备、农具和工具等领域发挥了重要作用,并且为后来的金属工艺和冶金学奠定了基础。
- 1、下载文档前请自行甄别文档内容的完整性,平台不提供额外的编辑、内容补充、找答案等附加服务。
- 2、"仅部分预览"的文档,不可在线预览部分如存在完整性等问题,可反馈申请退款(可完整预览的文档不适用该条件!)。
- 3、如文档侵犯您的权益,请联系客服反馈,我们会尽快为您处理(人工客服工作时间:9:00-18:30)。
淬火工艺钢的淬火是将钢奥氏体化后以适当的冷却速度冷却,使工件在横截面内全部或在一定范围内发生马氏体不稳定组织结构转变的热处理工艺。
一. 淬火工件的工艺流程一般工件:淬火→清洗→回火→喷砂(或喷丸等)表面清理→检验。
轴类零件及易变形工件:淬火→清洗→回火→校直→去应力处理→喷砂→检验。
二. 淬火前的准备(1)核对工件数量、材质及尺寸,并检查工件有无裂纹、碰伤、缺边、锐边、尖角及锈蚀等影响淬火质量的缺陷。
(2)根据图样及工艺文件,明确淬火的具体要求,如硬度、局部淬火范围等。
(3)根据淬火要求,设计选用合适的工夹具,有的工件进行适当的绑扎,在易产生裂纹的部位,采取相应的防护措施,如用铁皮或石棉绳包扎及堵孔等。
(4)表面不允许氧化、脱碳的工件,应在盐浴炉或预抽真空保护气氛炉中加热,或采取以下防护措施:a. 涂料防护b. 将工件装入盛有木炭或已使用过的铸铁屑的铁箱中,加盖密封。
(5)大批工件必须作单件或小批量试淬,制订工艺后方可进行批量淬火,并在生产过程中经常抽检。
三. 装炉(1)允许不同材质但具有相同加热工艺的工件装入同一炉中加热。
(2)装炉工件均应干燥、不得有油污及其他脏物。
(3)截面大小不同的工件装入同一炉时,大件应放在炉膛后部,大、小工件分别计算保温时间。
(4)装炉时必须将工件有规律摆放在装炉架或炉底板上,用钩子、钳子或专用工具堆放,不得将工件直接抛入炉内,以免碰伤工件或损坏炉衬。
(5)细长工件必须在井式炉或盐炉中垂直吊挂加热,以减少变形。
(6)在箱式炉中装工件加热时,一般为单层排列,工件间隙10~30mm。
小件允许适当堆放,但保温时间应适当增加。
四. 加热1. 加热方式(1)碳钢及合金钢工件,一般可直接装入比规定的淬火温度高20~30℃的炉中加热。
(2)高碳高合金钢及形状复杂的工件应先预热。
2. 加热温度选择。
3. 工件加热时间的计算:炉中的工件应在规定的加热温度范围内保持适当的时间,保证必要的组织转变和扩散。
加热时间是指从工件装入炉,通电加热起至出炉的整个加热过程保持的时间。
加热时间与工件的有效厚度、钢种、装炉方式、装炉量、装炉温度、炉的性能及密封程度等因素有关。
4. 有效厚度的选择(同时适用于退火和正火工艺)(1)圆棒形工件以直径计算。
(2)扁平工件以厚度计算(保温系数选取上限)。
(3)实心圆锥体按离大端1/3高度处的直径计算。
正火工艺一. 目的及应用正火是将钢材或各种金属机械零件加热到临界点Ac3或Accm以上的适当温度,保温一定时间后在空气中冷却,得到珠光体基体组织的热处理工艺。
二. 工艺规范(1)常用钢号的正火加热温度及硬度值。
(2)正火保温时间的计算,可参照淬火工艺规程。
(3)正火工件的冷却一般为空冷,大件正火也可采用风机冷却、喷雾冷却等,以获得理想的效果。
三. 操作要点(1)正火温度工艺规范相近的工件,允许同炉处理。
(2)对表面质量要求高的工件加热应采取防止氧化或脱碳的气体保护措施。
(3)工件一般采用工作温度或稍高于工作温度装炉。
若互相重叠装料,应相应延长保温时间1/4。
(4)工件应均匀放置在炉膛有效工作区里。
(5)工件出炉后,应散开放置在干燥处空冷,不得将工件堆积,不得放在潮湿处。
回火工艺退火工艺退火是将钢材或各种金属机械零件加热到适当温度,保温一段时间,然后缓慢冷却,可以获得接近平衡状态组织的热处理工艺。
在机械制造行业,退火通常作为工件制造加工过程中的预备热处理工序。
一. 完全退火完全退火是将钢件或各种机械零件加热到临界点Ac3以上的适当温度、在炉内保温缓慢逐渐冷却的工艺方法。
其目的是为了细化组织、降低硬度、改善机械切削加工性能及去除内应力。
完全退火适用于中碳钢和中碳合金钢的铸钢件、焊接件、轧制件等。
完全退火工艺曲线见图。
3. 工件装炉:一般中、小件均可直接装入退火温度的炉内,亦可低温装炉,随炉升温。
4. 保温时间:保温时间是指从炉子仪表到达规定退火加热温度开始计算至工件在炉内停止加热开始降温时的全部时间。
工件堆装时,主要根据装炉情况估定,一般取2~3h。
5. 工件冷却:保温完成后,一般停电(火),停止加热,关闭炉门逐渐缓冷至500℃即可出炉空冷。
对某些合金元素含量较高、按上述方式冷却后硬度仍然偏高的工件,可采用等温冷却方法,即在650℃附近保温2~4h后再炉冷至500℃。
二. 去应力退火去应力退火是将工件加热到Ac1以下的适当温度,保温一定时间后逐渐缓慢冷却的工艺方法。
其目的是为了去除由于机械加工、变形加工、铸造、锻造、热处理以及焊接后等产生的残余应力。
1. 去应力退火工艺曲线见图1-3。
2. 不同的工件去应力退火工艺参数见表C。
3. 去应力退火的温度,一般应比最后一次回火温度低20~30℃,以免降低硬度及力学性能。
4. 对薄壁工件、易变形的焊接件,退火温度应低于下限。
5. 低温时效用于工件的半加工之后(如粗加工或第一次精加工之后),一般采用较低的温度。
表C 去应力退火工艺及低温时效工艺化学热处理工艺渗碳、渗氮、碳氮共渗渗碳是为了增加钢件表层的含碳量和一定的碳浓度梯度,将钢件在渗碳介质中加热并保温使碳原子渗入钢件表层的化学热处理工艺称为渗碳,渗碳钢一般采用普通碳钢、优质碳素结构钢和低碳合金结构钢,也可采用Q235钢。
开炉前的准备:(1)渗碳工件表面不应有锈蚀、污垢、裂纹及伤痕等缺陷。
(2)工件表面不需渗碳部分可采用表面镀铜或涂防渗碳涂料防止渗碳,也可在渗碳后,对不需要渗碳的部分切削去渗碳层。
镀铜层的厚度一般应大于0.03mm;防渗碳涂料的厚度一般应大于0.3mm,要求涂层致密。
(3)采用滴注式渗碳时,渗碳剂一般是甲醇(形成载气);煤油或丙酮、醋酸乙酯(形成富化气),有条件时也可以采用其他方式的可控气氛渗碳。
为取得高质量渗碳,减少碳黑,最好选用航空煤油滴注。
(4)准备好试样和中间试样。
试样宜取自同批零件,试样表面不允许有锈蚀、油污。
中间试样一般为Φ10mm×10钢试棒。
渗碳操作:①开炉前检查设备(参照井式气体渗碳炉操作规程)②根据停炉时间和炉罐情况,按工艺文件规定,进行炉罐渗碳。
炉罐渗碳时间,对于新炉罐一般为6-12h,对于旧炉罐一般为2-4h左右。
③装炉:a.将材质相同、渗碳层技术要求相同、渗碳后热处理方式相同的工件,放在同一炉生产。
试样放在料筐的有代表性的位置。
每炉装载量和装料高度应小于设备规定的最大装载量和装料高度。
b.为保证炉内渗碳气氛的循环畅通,使渗碳层均匀,工件间应留有纵横大于5mm的间隙。
c.料筐装入炉内时,要垂直摆放,各层料筐应齐整,不得有间隙,同时悬吊放入中间试样棒。
d.工件入炉后,将炉盖盖紧,不允许有漏气现象,滴入渗碳剂后,应保持炉内压力为196-490Pa。
将废气点燃,火苗高度为200-300mm。
④渗碳a.渗碳工艺曲线:根据材质及渗碳层显微组织的要求,由有关工艺文件规定渗碳工艺曲线,一般对于要求严格控制碳化物的低合钢钢工件,可参考工艺曲线图;对于不要求严格控制碳化物的低碳钢、低合金钢工件,可参考工艺曲线图关于渗碳工艺曲线说明如下:赶气:其目的是赶走炉内空气,使炉内空气恢复到工艺规定的碳势气氛。
保温:其目的是使炉内工件温度均匀。
保温时间一般是40min到1h。
渗碳温度和渗碳时间:渗碳温度一般为900~940℃,渗碳时间应根据要求的渗碳层深度确定,它与渗碳温度、炉内气氛的碳势及工件特征等因素有关。
渗碳剂的选择及应用:采用滴注式渗碳时,可根据生产厂条件选择渗碳剂。
选用普通煤油作渗碳剂,炉内碳黑较多。
选用航空煤油,不易产生碳黑,甲醇作载气,煤油作富化气,炉内碳黑较少。
用甲醇作载气,丙酮或醋酸乙醋作富化气,炉内碳黑则更少,可进行气氛的碳势控制。
渗碳剂用量根据工件装载量和表面积大小等因素进行调整。
渗氮渗氮的常见缺陷一、硬度偏低生产实践中,工件渗氮(软氮化)后其表面硬度有时达不到工艺规定的要求,轻者可以返工,重者则造成报废。
造成硬度偏低的原因是多方面的:设备方面:如系统漏气造成氧化;材料:如材料选择欠佳;前期热处理:如基体硬度太低,表面脱碳严重等;预先处理:如进炉前的清洁方式及清洁度。
工艺方面:如渗氮(软氮化)温度过高或过低,时间短或氮势不足等等。
所以具体情况要具体分析,找准原因,解决问题。
二、硬度和渗层不均匀装炉方式不当;气压调节不当;温度不均;炉内气流不合理。
三、变形过大变形是难以杜绝的,对易变形件,采取以下措施,有利于减小变形:渗氮(软氮化)前应进行稳定化处理;渗氮(软氮化)过程中的升、降温速度应缓慢;保温阶段尽量使工件各处的温度均匀一致。
对变形要求严格的工件,如果工艺许可,尽可能采用较低的氮化(软氮化)温度。
四、处观质量差渗氮(软氮化)件出炉后首先用肉眼检查外观质量,钢件经渗氮(软氮化)处理后表面通常呈银灰(蓝黑色)色或暗灰色(蓝黑色),不同材质的工件,氮化(软氮化)后其表面颜色略有区别,钛及钛合金件表面应呈金黄色。
五、脉状氮化物氮化(特别是离子氮化)易出现脉状氮化物,即扩散层与表面平行走向呈白色波纹状的氮化物。
其形成机理尚无定论,一般认为与合金元素在晶界偏聚及氮原子的扩散有关。
因此,控制合金元素偏聚的措施均有利于减轻脉状氮化物的形成。
工艺参数方面,渗氮温度越高,保温时间越长,越易促进脉状组织的形成,如工件的棱角处,因渗氮温度相对较高,脉状组织比其它部位严重得多。
感应加热工艺高频感应加热原理用交流电流流向被卷曲成环状的导体(通常为铜管),由此产生磁束,将金属放置其中,磁束就会贯通金属体,在与磁束自缴的方向产生窝电流(旋转电流)……感应作用此时,由于金属内的电阻产生焦耳热(1平方R),使温度上升,这就是感应加热。
由此,对金属等被加热物体,在非接触的状态下就能加热。
(发热有焦耳热及磁滞损失产生的热,但主要有焦耳热引起的。
)中频感应加热原理应用电磁感应原理,置工件于交流磁场中,产生涡流损耗而发热,达到熔炼、透热、淬火等加热的要求。
这种加热方式,具有加热快、烧损少、劳动强度低,能保证产品质量和易于组织自动生产线等优点热处理工艺模拟加热炉炉壁温度模拟(使用MARC软件模拟)工件冷却过程模拟(使用ANSYS软件模拟)大型井式渗碳炉炉气模拟(物理模拟装置)典型工件热处理工艺举例铝合金轮毂热处理炉加工工艺曲线图:常用齿轮钢材的调质热处理工艺。