YG油管防腐蚀涂料
油气田井下油管的防腐技术

油气田井下油管的防腐技术在石油工业中起着至关重要的作用,可以延长油管的使用寿命、提高生产效率,并保证油气的安全输送。
以下是一些常见的油气田井下油管防腐技术:
1. 油管涂层防腐技术
-环氧涂层:环氧涂层是最常用的油管防腐材料之一,具有良好的耐腐蚀性能和粘附性,可以有效防止金属表面受到腐蚀。
-聚乙烯涂层:聚乙烯涂层具有良好的机械性能和耐腐蚀性能,广泛应用于海底油气管道等环境中。
-聚胺脂涂层:聚胺脂涂层具有优异的耐化学腐蚀性能和耐磨损性能,适用于高腐蚀环境下的油管防腐。
2. 阴极保护技术
-镀锌:将油管表面镀上一层锌,利用锌的阳极保护作用保护油管不受腐蚀。
-牺牲阳极保护:在油管系统中加入一些更容易氧化的金属,如锌、铝等,使其成为“牺牲阳极”,保护油管不受腐蚀。
3. 管道涂层检测技术
-非破坏检测:采用超声波、X射线、磁粉探伤等非破坏检测技术对油管涂层进行定期检测,及时发现问题并进行修复。
-电化学阻抗谱分析:通过电化学阻抗谱分析技术,监测涂层的电化
学性能变化,评估防腐涂层的状况和耐腐蚀性能。
4. 管道防腐维护管理
-定期检查维护:定期对油管涂层进行检查和维护,及时修复涂层损坏或腐蚀部位。
-建立档案记录:建立完善的管道防腐维护档案,记录每次维护和检测的结果,制定科学的预防性维护计划。
通过以上技术手段和管理措施,可以有效延长油气田井下油管的使用寿命,确保油气输送系统的安全稳定运行。
同时,保障油气资源的开发利用,促进石油工业的持续发展。
钢制管道液体环氧涂料内防腐涂层技术标准

钢制管道液体环氧涂料内防腐涂层技术标准
1.涂料选择:选用环氧树脂涂料和固化剂等原材料,严格按照相关标
准验收。
2.表面处理:切割焊接缝口、封头、阀门等部位必须做好预处理工作,表面完全清洁,铁锈、油脂、灰尘等杂质彻底清除。
3.底漆涂装:在表面处理完毕后,进行底漆涂装,根据实际情况选择
特定颜色和年限的涂料。
4.涂装工艺:采用湿涂法进行内壁涂装,刷涂、滚涂、喷涂均可,能
否涂匀、涂厚均匀、无气泡、无疏漏是关键要求。
5.涂层测试:采用介电强度、耐化学药品、湿热老化、磨损、剥离、
附着力等常规测试方法,保证涂层质量符合要求。
6.质量验收:按照国家相关标准进行检验,合格后才能投入使用。
石油管道及设备用水性防腐涂料的研究

1 4 环 氧乳 液 一聚 丙烯 酸酯 互 穿聚 合 物 网络 的合成 . 工艺( 组分 B)
在装 有搅拌 、 加热套 、 氮气导 管 、 冷凝器 和温度计的三 E烧 l
瓶 中 加入 环 氧 乳 液 和 交联 剂 , 然后 通 人 N 5m n 10m / i) i(0 L mn ,
T b e 1 P o e t s o t r o n o r s n p o e t e c a i g o to e m i l e n a i t a l r p r i fwa e b r e c r o i r t c i o tn sf r p r lu p p i s a d f cl e e o v e e n is i
p oe tv o tng n mea u sr ts r t cie c a i s i tls b ta e .
K e o ds: n io e t lpr tc in; er l u pi ln c ro in p o e to I N ; p x mu so yW r e vr m n a oe t o p toe m pei e; o so r t ci n; P e o y e lin
氧乳液 一聚丙烯酸酯互穿 聚合物网络 ( IN) LP 。
1 5 漆 浆制 备 ( 分 A) . 组
将水性胺环氧加 成物 、 去离 子水 和少 量醇类 或 醇醚类 溶 剂混合后高速分散 , 搅匀 , 加入功能性 助剂 , 中速搅 拌 2 n 0mi,
表 1 油 田管 道 及 设 备 用 水 性 防 腐涂 料 性 能 检 验 结 果
2 结 果 与讨 论
2 1 基料 的合成 .
H3
2 1 1 固化 剂 的 合 成 稳 定性 及 贮 存 稳 定 性 . .
管道防锈防腐刷漆方法

管道防锈防腐刷漆方法
管道防锈防腐刷漆的方法主要包括以下几个步骤:
1.清洁表面:首先需要彻底清洁管道表面,去除表面的油污、灰尘和锈蚀物,可以使用洗涤剂和水冲洗,或者使用钢丝刷擦拭。
2.打磨表面:使用砂纸、砂轮或钢丝刷等工具对管道表面进行打磨,去除粗糙和不平整的部分,使表面光滑。
3.涂刷底漆:选择适合的底漆涂刷在管道表面,底漆可以提供保护和附着力,增加涂层的耐久性。
4.涂刷防腐漆:选用适合的防腐漆涂刷在底漆表面,遵循涂刷防腐漆的规定涂刷厚度和层数。
根据所在环境的不同,可以选择不同种类的防腐漆。
5.二次涂刷:根据需要,可以进行二次涂刷,增加涂层的耐久性和保护效果。
6.干燥和固化:等待涂层完全干燥和固化,根据涂刷所用的防腐漆的要求和环境条件,时间可能会有所不同。
需要注意的是,在进行管道防锈防腐刷漆之前,应先进行必要的检查和准备工作,确保管道表面光滑、干燥、清洁,并将管道与环境绝缘,以保证涂漆效果和涂层的质量。
一、环氧系列防腐涂料

一、环氧系列防腐涂料一、简介随着现代工业的发展,一批新兴工业领域的出现和许多现代工程的兴建,对防腐涂料承受环境的能力和使用寿命提出了更高的要求。
常用的防腐涂料已不能满足这些需要。
人们提出的“重防腐涂料(Heavy Duty Coating)”的概念,一般指在苛刻的腐蚀环境使用,包括底漆和面漆的配套涂料。
简单地说:重防腐涂料就是使用寿命更长,可适应更苛刻的使用环境的涂料称为重防腐涂料。
在化工大气和海洋环境里重防腐涂料一般可使用10年或15年以上,在酸、碱、盐和溶剂介质里,并在一定温度的腐蚀条件下,一般应能使用5年以上。
重防腐涂料的应用涉及现代化各个领域,大型的工矿企业:化工、石油化工、钢铁及大型矿山冶炼的管道、贮槽、设备等;重要的能源工业:天然气、油管、油罐、输变电、核电设备及煤矿矿井等;现代化的交通运输:桥梁、船舶、集装箱、火车和汽车等;新兴的海洋工程:海上设施、海岸及海湾构造物及海上石油钻井平台等。
环氧树脂是由环氧氯丙烷和双酚A在碱催化下缩合而成的聚合物,随分子量的不同,可分为液体和固体环氧树脂。
以环氧树脂为主要成膜物质的涂料称为环氧涂料。
每年世界上约有40%以上的环氧树脂用于制造环氧涂料,其中大部分用于防腐领域。
环氧防腐涂料是目前世界上用得最为广泛、最为重要的重防腐涂料之一。
环氧树脂类防腐蚀涂料种类很多,大致可分为:胺固化环氧涂料、聚酰胺固化环氧涂料、胺加成物固化环氧涂料、环氧粉末涂料、环氧改性涂料。
二、环氧系列防腐涂料性能特点环氧系列涂料产品具有涂膜坚韧、耐磨、附着力好、耐化学腐蚀、耐强碱、耐水、耐溶剂、耐油等性能优异的特性,并有良好的绝缘性。
主要体现在以下几个方面:1、极好的附着力环氧树脂结构中含有不易水解的脂肪基(-C-)和醚键(-C-O-C-),能够产生电磁引力。
另外,在固化过程中活泼的环氧基和介质表面上的游离键起反应而形成牢固的化学键,从而使环氧树脂涂层获得极好的附着力。
2、优异的防腐蚀性能环氧树脂固化涂层,含有稳定的苯环、醚键等,结构致密,耐酸、耐碱、耐有机溶剂、耐水。
石油化工设备和管道涂料防腐蚀设计标准

石油化工设备和管道涂料防腐蚀设计标准
石油化工设备和管道涂料防腐蚀设计标准主要涉及以下方面:
1. 材料选择:根据介质的性质和工艺要求,选择适合的防腐蚀
涂料。
常见的涂料包括环氧涂料、聚氨酯涂料、聚酯涂料等。
同时,
对涂料本身的化学稳定性、耐腐蚀性能和耐高温性能也要进行评估。
2. 涂层厚度:根据设备和管道的使用环境和预计的腐蚀情况,
确定适当的涂层厚度。
涂层厚度应能够提供足够的防护,防止腐蚀介
质侵蚀基材。
3. 表面处理:在涂装前,需要对设备和管道的表面进行处理,
以去除氧化物、污染物和残留物,并提供良好的附着力。
常见的表面
处理方法包括除锈、砂光和化学处理等。
4. 涂装技术:涂装应遵循相关的技术规范,确保涂料均匀、牢
固地覆盖在设备和管道表面。
常见的涂装方法包括刷涂、喷涂和电泳
涂装等。
5. 涂层检测:涂装完成后,需要进行涂层的质量检测。
常见的
检测方法包括厚度测量、附着力测试、耐盐雾测试和耐腐蚀性能测试等。
通过检测结果,评估涂层的防腐蚀性能是否符合设计要求。
以上是石油化工设备和管道涂料防腐蚀设计标准的一些主要内容,具体的标准和要求可能会因不同的国家、地区和工程项目而有所不同。
在实际设计中,需要参考相关的国家标准、行业规范和工程实践经验。
8710防腐涂料成分

8710防腐涂料成分
8710防腐涂料是一种具有化学惰性、耐酸、碱、盐腐蚀,且涂膜结构致密、防水渗透性好、附着力强且坚韧丰满的给水管道常用防腐涂料。
其详细成分如下:
1.聚氨酯树脂和改性环氧树脂:是8710防腐涂料的主要成分,使其具有良好的漆膜韧性、耐磨性、耐腐蚀性和抗微生物侵蚀的性能。
2.防锈涂料和助剂:用于提高涂料的防锈性能。
3.沥青:可提高涂料的防水性和耐腐蚀性。
4.防锈颜料:使涂料具有防锈作用。
5.助剂:调整涂料的物理和化学性质,以达到理想的施工和使用效果。
6.溶剂:用于调节涂料的粘度,便于施工。
该涂料属于双组分涂料,即两组份分别包含不同的成分,混合后形成最终的防腐涂层。
在使用时,应严格按照配比进行混合,以保证涂层的质量和性能。
此外,IPN8710互穿网络防腐涂料还具有良好的耐冲击性和耐候性,适用于多种设备和环境的防腐保护。
重防腐涂料的标准

重防腐涂料的标准重防腐涂料作为防腐涂料的骄子,自20世纪60~70年代开始应用以来,得到了迅速发展,应用范围越来越广,尤其是这样那样的防腐难题进一步推动了重防腐涂料技术的革命,重防腐涂料从生物工程、石油、化工等行业吸取营养,嫁接高技术,使重防腐涂料发挥着越来越大的作用,发展前景十分诱人。
重防腐涂料标准的重要标志即厚膜化。
今天我要为大家介绍的是有关重防腐涂料标准的相关知识。
重防腐涂料介绍重防腐涂料:它的英文名称为heavy-duty coating,指相对常规防腐涂料而言,能在相对苛刻腐蚀环境里应用,并具有能达到比常规防腐涂料更长保护期的一类防腐涂料。
厚膜化是重防腐涂料的重要标志。
一般防腐涂料的涂层干膜厚度为100μm或150μm左右,而重防腐涂料干膜厚度则在200μm或300μm以上,还有500μm~1000μm,甚至高达2000μm。
防腐涂料,一般分为常规防腐涂料和重防腐涂料,是油漆涂料中必不可少的一种涂料。
常规防腐涂料是在一般条件下,对金属等起到防腐蚀的作用,保护有色金属使用的寿命;重防腐涂料特点①能在苛刻条件下使用,并具有长效防腐寿命,重防腐涂料在化工大气和海洋环境里,一般可使用10年或15年以上,即使在酸、碱、盐和溶剂介质里,并在一定温度条件下,也能使用5年以上。
②厚膜化是重防腐涂料的重要标志。
一般防腐涂料的涂层干膜厚度为100μm或150μm左右,而重防腐涂料干膜厚度则在200μm或300μm以上,还有500μm~1000μm,甚至高达2000μm。
重防腐涂料种类【环氧树脂漆】厚膜型环氧富锌底漆,环氧云铁防锈漆,环氧玻璃鳞片,环氧煤沥青漆,环氧地坪漆。
【氯乙烯油漆】底漆,面漆,机床漆,锤纹漆,防火漆,防腐漆,清漆,过氯乙烯腻子。
【氯化橡胶油漆】氯化橡胶各色面漆,氯化橡胶铝粉防锈底漆,氯化橡胶防锈底漆,氯化橡胶铁红铝粉防锈漆,氯化橡胶船底防污漆。
【丙烯酸油漆】丙烯酸聚氨酯罩光清漆,各色丙烯酸聚氨酯磁漆,丙烯酸道路划线漆。
防腐蚀涂料施工步骤与方法

防腐蚀涂料施工步骤与方法防腐蚀涂料的施工是为了保护金属表面免受腐蚀侵害,延长使用寿命。
在进行防腐蚀涂料施工时,需要遵循一定的步骤和方法,以确保涂层的质量和效果。
本文将介绍防腐蚀涂料施工的步骤与方法,并提供一些建议和注意事项。
一、表面处理在进行防腐蚀涂料施工之前,首先需要对金属表面进行处理。
通常,表面处理包括清洁、除锈和喷砂。
清洁是确保金属表面干净、无尘的关键步骤,可以使用溶剂或洗涤剂进行清洁。
除锈是将金属表面的锈蚀物、铁锈等物质去除,可以采用机械除锈、化学除锈或电解除锈等方法。
喷砂是通过高速气流将砂粒喷射到金属表面,去除残留的污物和光洁表面,以提供良好的附着力。
二、底漆涂层在进行防腐蚀涂料施工之前,需要先施工底漆涂层。
底漆涂层可以增加涂层的附着力和耐久性,起到保护金属表面的作用。
底漆涂层应根据涂料的类型和金属表面的情况选择合适的底漆,并按照涂料生产厂家的建议进行施工。
底漆涂层的施工方法可以采用刷涂、喷涂或浸涂,根据具体情况选择适合的方法。
三、主涂层施工底漆涂层干燥后,可以进行主涂层的施工。
主涂层是防腐蚀涂料的关键部分,具有阻隔腐蚀性物质的作用。
根据具体需求,可以选择不同类型的主涂层涂料,如环氧树脂、聚氨酯、丙烯酸等。
主涂层的施工方法也可以采用刷涂、喷涂、滚涂等,根据涂料的特性和涂覆面积选择合适的方法。
四、涂覆层数为了提高防腐蚀涂层的效果和耐久性,通常需要涂覆多层涂料。
在涂覆每一层涂料之前,需要确保上一层涂料的干燥和固化。
涂覆多层涂料可以增加涂层的厚度和防护性能,提高耐腐蚀性能。
五、涂层检测与维护在防腐蚀涂料施工完成后,需要对涂层进行检测和维护,以确保涂层的质量和效果。
涂层检测可以采用常规的物理和化学测试方法,如涂层厚度、附着力、耐磨性等。
对于长期暴露在恶劣环境下的涂层,可以定期进行维护和修补,以延长涂层的使用寿命。
六、安全注意事项在进行防腐蚀涂料施工时,需要注意以下安全事项:1.避免直接接触涂料,应佩戴防护手套和面具。
刷油、防腐蚀涂料、衬里、绝热工程工程量计算

• 防火涂料需描述的项目特征包括除锈级别,涂刷(喷)品种,涂刷( 喷)遍数、漆膜厚度,耐火极限(h),耐火厚度(mm)。
• 防火涂料工程量以“m2”为计量单位,按设计图示表面积尺寸以面 积计算。
• 防火涂料工作内容包括除锈,调配、涂刷(喷)。
• 三、H型钢制钢结构、金属油管内壁防静电
• 管道、设备与矩形管道刷油需描述的项目特征包括除锈级别,油漆品 种,涂刷遍数、涂膜厚度, 标志色方式、品种。除锈级别根据锈蚀 等级, 分为A、B、C、D 四级,见表8-1。
下一页 返回
第一节 刷油工程工程量计算
• 管道、设备与矩形管道刷油工程量以“m2”计量,按设计图示表面 积尺寸以面积计算;以“m”计量,按设计图示尺寸以长度计算。其 中,管道刷油以“m”计算时,按设计图示中心线以延长米计算,不 扣除附属构筑物、管件及阀门等所占长度。设备筒体、管道表面包括
• 管廊钢结构防腐蚀工程量以“kg”为计量单位,按管廊钢结构的理 论质量计算。
• 计算设备、管道内壁防腐蚀工程量,当壁厚大于10mm 时,按其 内径计算;当壁厚小于10mm 时,按其外径计算。
上一页 下一页 返回
第二节 防腐蚀涂料工程工程量计算
• 设备、管道、一般钢结构、管廊钢结构防腐蚀工作内容包括除锈,调 配、涂刷(喷)。
第八章刷油、防腐蚀涂料、衬里、绝热 工程工程量计算
• 第一节刷油工程工程量计算 • 第二节防腐蚀涂料工程工程量计算 • 第三节衬里工程工程量计算 • 第四节绝热工程工程量计算
返回
第一节 刷油工程工程量计算
• 一、管道、设备与矩形管道刷油
• 刷油亦称为涂覆,是安装工程施工中常见的重要内容,将普通油脂漆 料涂刷在金属表面,使之与外界隔绝,以防止气体、水分的氧化侵蚀 ,并能增加光泽,更美观。刷油可分为底漆和面漆两种。刷漆的种类 、方法和遍数可根据设计图纸或有关规范要求确定。设备、管道以及 附属钢结构经除锈后,就可在其表面进行刷油(涂覆)。
防腐蚀涂料配方

防腐神器:全能防腐蚀涂料配方大公开!
你是否曾为处理不好钢铁、铝合金等金属材料的腐蚀问题而大伤脑筋?快来看看我们的全能防腐蚀涂料配方大公开!
一、配料清单:
1.丙烯酸酯树脂
2.硬脂酸甘油酯
3.多异氰酸酯
4.钛白粉
5.纳米氧化铝
二、制作步骤:
1.将丙烯酸酯树脂加入烘干过的钢材表面,晾干后将硬脂酸甘油酯涂抹在上面。
2.混合多异氰酸酯和钛白粉,匀成膏状,涂抹在表面。
3.最后再涂上一层纳米氧化铝,晾干后即可使用。
三、使用效果:
这种防腐蚀涂料的耐腐蚀性能非常好,使用寿命长达30年以上,即使在恶劣环境下也能很好地保护金属表面。
同时,其表面光滑,颜色饱满,能美化整体装饰效果。
四、注意事项:
1.虽然此涂料能够有效防腐蚀,但在使用前需对所涂金属表面进行打磨、清洗、处理等工艺步骤,以保证涂层的附着力。
2.在制作过程中需要注意配料比例,严格按照说明书进行配比,以免出现质量问题。
3.使用涂料时需要注意露天干燥时间和环境温度,若环境温度较低则需要增加干燥时间。
以上是全能防腐蚀涂料的配方以及使用效果,希望能够帮助到你解决腐蚀问题,让你的钢铁、铝合金等金属材料更加持久耐用。
管道的防腐方法

管道的防腐方法
管道在运输液体或气体过程中,容易受到腐蚀的影响,因此需要进行防腐处理。
以下是几种常见的管道防腐方法:
1. 防腐涂层:将管道表面涂上一层特殊的防腐涂料,可以有效地防止管道受到腐蚀的侵害。
这种方法需要根据管道的材质和使用环境来选择适合的防腐涂料。
2. 阴极保护:通过在管道表面安装阴极保护系统,使管道表面成为阴极,在电化学原理的作用下,可以有效地减缓管道的腐蚀速度。
这种方法适用于金属管道。
3. 热浸镀锌:将管道浸入熔融的锌中,使锌附着在管道表面,形成一层锌层,可以起到防腐的作用。
这种方法适用于钢管道。
4. 玻璃钢管道:玻璃钢管道具有耐腐蚀、耐磨损、重量轻等优点,可以在一定程度上替代金属管道。
玻璃钢管道需要在制造时就进行防腐处理,通常采用表面涂层的方式。
以上是常见的几种管道防腐方法,企业可以选择适合自己的防腐方式,提高管道的使用寿命,降低维护成本。
- 1 -。
油气田井下油管的防腐技术

油气田井下油管的防腐技术油气田井下油管的防腐技术是为了保护油管不被腐蚀或受损,延长其使用寿命并确保油气输送的安全性。
以下是几种常见的井下油管防腐技术:1. 耐蚀涂层技术:在油管表面涂覆耐蚀涂层是一种常用的防腐技术。
这些涂层可以是有机涂层,如环氧树脂、聚乙烯等;也可以是无机涂层,如锌、铝等金属涂层。
涂层的选择要根据环境条件确定,以提供最佳的防腐效果。
2. 阴极保护技术:阴极保护是一种通过施加电流,使油管成为阴极,从而降低其对应腐蚀的技术。
常见的阴极保护方法有两种:外部阴极保护和内部阴极保护。
外部阴极保护是通过在油管周围埋设阳极,并连接到直流电源上,以形成阴极保护电位。
内部阴极保护是在油管内部放置阳极,通常是以镁合金或铝合金制成,然后通过电流源供电。
3. 电泳防腐技术:电泳防腐技术是将油管浸入特定的涂料中,形成一个带电颗粒悬浮液,然后在外加电场的作用下,使涂层颗粒在油管表面均匀沉积。
这种方法可以形成均匀且致密的涂层,提供有效的防腐保护。
4. 高温耐蚀合金技术:对于高温、高压和腐蚀性介质环境下的油气田井下油管,常采用高温耐蚀合金材料进行防腐。
这些合金具有优异的耐腐蚀性能和高温稳定性,能够在恶劣环境中保护油管免受腐蚀损害。
5. 定期维护和检查:除了使用防腐技术,定期的维护和检查也是保护井下油管的重要手段。
定期清洗、除锈和重新涂覆涂层,及时修复损坏或脱落的涂层,对油管进行定期检查以发现并处理潜在腐蚀问题,都是关键的防护措施。
总之,井下油管防腐技术的选择和应用需要根据具体情况来确定,包括油气田环境条件、油气成分、运行压力和温度等。
合理选择和应用防腐技术,同时进行定期维护和检查,能够有效延长油管的使用寿命并保障油气输送的安全性。
钢质管道液体环氧树脂涂料内防腐层技术标准

钢质管道液体环氧树脂涂料内防腐层技术标准钢质管道液体环氧树脂涂料内防腐层技术标准主要包括以下内容:
1. 涂料材料要求:涂料应为环氧树脂涂料,具有优良的防腐性能、附着力和耐腐蚀性能。
涂料应符合相关国家或地区标准要求。
2. 表面处理:管道表面应进行除锈和清洁处理,确保表面无杂质、油污、锈蚀等。
可采用喷砂或喷丸等方法进行表面处理。
3. 涂料施工:涂料应按照涂料生产商的施工工艺要求进行施工。
涂料应均匀涂覆在管道内壁上,形成均匀的涂层。
涂料的厚度应符合设计要求。
4. 涂层质量控制:涂层施工完成后,应进行涂层质量检查。
检查涂层的附着力、厚度、外观等指标,确保涂层质量符合要求。
5. 温度和湿度控制:涂料施工过程中应控制施工环境的温度和湿度。
温度和湿度对涂料的干燥和固化速度有影响,应按照涂料生产商的要求进行控制。
6. 涂层养护:涂料施工完成后,应进行养护措施。
涂层需要一定的时间进行干燥和固化,期间应防止外界物质的侵入和损坏。
7. 检测和验收:涂层施工完成后,应进行涂层的检测和验收。
检测涂层的厚度、附着力、耐腐蚀性能等指标,确保涂层符合要求。
总之,钢质管道液体环氧树脂涂料内防腐层技术标准包括涂料材料要求、表面处理、涂料施工、涂层质量控制、温度和湿度控制、涂层养护、检测和验收等方面的要求,旨在确保涂层质量符合设计要求
并具有良好的防腐性能。
油管内涂层施工方案设计

油管内涂层施工方案设计1. 引言油管内涂层施工是为了保护油管内壁而进行的一项关键性工作。
涂层的选择和施工方案的设计直接影响到油管的性能和使用寿命。
本文将介绍油管内涂层施工方案的设计过程,包括涂层材料的选择、涂层施工工艺的确定和涂层质量控制的方法。
2. 涂层材料的选择涂层材料的选择是油管内涂层施工方案设计的第一步。
涂层材料应具备以下特点:•耐腐蚀性:油管内壁常受到化学品腐蚀的影响,因此涂层材料应具备良好的耐腐蚀性能,能够有效抵抗化学物质的侵蚀。
•耐磨性:由于油管运输过程中的颗粒物和摩擦力,涂层应具备较高的耐磨性,以延长油管的使用寿命。
•密封性:涂层应具备良好的密封性,以防止管道内部液体或气体泄漏。
•热稳定性:涂层应具备良好的热稳定性,能够承受高温条件下的使用。
根据以上要求,常用的油管内涂层材料包括环氧树脂、聚脂酯、聚氨酯等。
根据具体的工程要求和使用环境,选择适合的涂层材料。
3. 涂层施工工艺的确定涂层施工工艺是指涂层的施工过程和方法。
在确定涂层施工工艺时,需要考虑以下因素:3.1 表面处理在涂层施工前,需要对油管内壁进行表面处理,以保证涂层与油管壁的粘结力。
常见的表面处理方法包括喷砂、磨料抛光等。
根据油管的材料和涂层材料的要求,选择合适的表面处理方法。
3.2 涂层施工方式涂层施工方式主要有手工涂覆、喷涂和涂料喷涂等。
根据涂层材料的性质和施工效率的要求,选择合适的涂层施工方式。
3.3 涂层层厚控制涂层的层厚控制是涂层施工中的关键步骤之一。
通过控制涂层的层厚,可以保证涂层在使用过程中的耐腐蚀性、耐磨性等性能。
涂层层厚的控制可以通过涂料的定量喷涂或测量仪器进行。
4. 涂层质量控制为了确保涂层施工质量,需要对涂层进行严格的质量控制。
涂层质量控制包括以下方面:4.1 涂层的外观检查涂层的外观检查主要包括色泽、平整度、光泽度等方面的检查。
通过目视检查和光学仪器的检测,判断涂层施工质量是否符合要求。
4.2 涂层的附着力测试涂层与油管壁的附着力是涂层质量的关键指标之一。
管道防腐漆施工做法

管道防腐漆施工做法
管道防腐漆施工的做法可以按照以下步骤进行:
1. 准备工作:清洁管道表面,除去附着物和杂质。
可以使用喷水清洗、钢丝刷擦洗或砂纸打磨等方法。
2. 预处理:对于新的管道表面,需要先进行底漆处理。
选用适当的底漆,按照说明进行涂刷。
底漆的目的是增强粘结力和防止腐蚀。
3. 涂刷防腐漆:选择合适的防腐漆,可以根据管道材质、使用环境等因素来确定。
可以采用刷涂、喷涂等方式进行涂刷。
涂刷时要注意涂膜的均匀性和厚度,一般需要涂刷两道。
4. 干燥处理:根据防腐漆的要求,进行干燥处理。
可以进行自然干燥,或者使用干燥设备进行加热或通风干燥。
5. 检验和验收:经过干燥后,可以进行防腐漆的质量检验。
检查是否涂刷均匀,有无漏涂或起泡等问题。
检验合格后,进行最终的验收。
需要注意的是,在施工过程中要严格按照产品说明书和相关标准进行操作,并采取必要的安全措施,如佩戴防护服、呼吸器等。
此外,施工环境必须干燥、清洁,避免尘埃、水汽等对施工质量的影响。
管道外层腐蚀的防治方法

管道外层腐蚀的防治方法管道在输送各种介质的过程中,由于环境的恶化和介质的腐蚀性,管道的外层容易遭受腐蚀。
为了延长管道的使用寿命和确保管道的安全运行,以下是针对管道外层腐蚀的防治方法:1.防腐蚀涂层防腐蚀涂层是管道外层腐蚀防治的重要措施。
常见的防腐蚀涂层有环氧树脂涂层、聚氨酯涂层、聚酯涂层等。
这些涂层具有耐腐蚀、防水、防霉等特性,能够有效地保护管道外层免受腐蚀。
在涂覆涂层时,需要注意施工要点和注意事项,如清洁表面、控制涂层厚度、避免涂层破损等。
2.阴极保护阴极保护是通过降低管道的电位以达到防止腐蚀的目的。
阴极保护有两种方法:外加电流法和牺牲阳极法。
外加电流法是通过外部电源提供电流来保护管道,而牺牲阳极法是利用活泼金属作为阳极,牺牲阳极来保护阴极管道。
阴极保护具有施工简便、维护容易等优点,但需要注意电源选择、安装质量等问题。
3.表面处理表面处理可以改变管道表面的物理和化学性质,从而提高防腐蚀性能。
表面处理的方法包括机械处理、化学处理和物理处理。
机械处理包括打磨、喷砂、抛光等,化学处理包括酸洗、钝化、磷化等,物理处理包括真空镀膜、离子溅射等。
表面处理可以有效地提高防腐蚀性能,但在选择处理方法时需要注意适用性和施工难度。
4.防腐蚀合金防腐蚀合金是一种具有较好防腐蚀性能的管道材料。
常见的防腐蚀合金有不锈钢、高合金钢等。
这些合金具有较好的耐腐蚀性能,能够有效地提高管道的防腐蚀能力。
在应用防腐蚀合金时,需要注意选材合理,根据介质和环境选择适用的合金材料。
5.缓蚀剂缓蚀剂是一种能够抑制管道腐蚀的化学物质。
常见的缓蚀剂有有机缓蚀剂、无机缓蚀剂和复合缓蚀剂。
这些缓蚀剂能够与管道表面反应,形成一层保护膜,从而减缓管道的腐蚀速度。
在选择和使用缓蚀剂时需要注意种类、特点、应用场景和施工方法,避免出现副作用。
6.选材合理选材合理是管道外层腐蚀防治的重要措施之一。
在选择管道材料时,需要考虑材料的耐腐蚀性、机械强度、加工工艺等因素。
管道防腐油漆方案
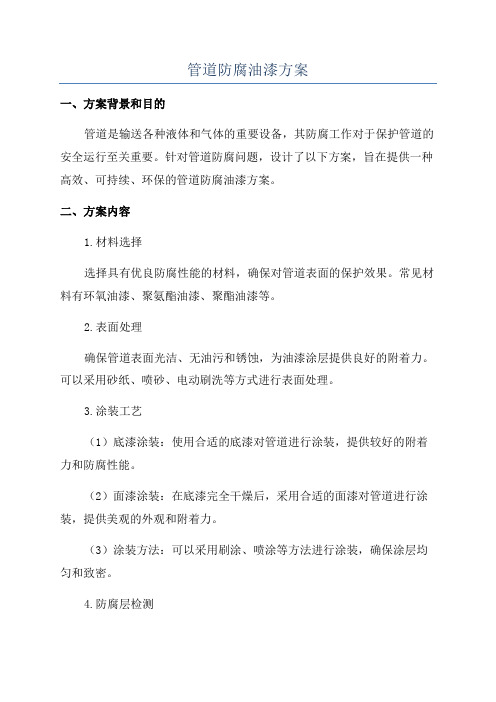
管道防腐油漆方案一、方案背景和目的管道是输送各种液体和气体的重要设备,其防腐工作对于保护管道的安全运行至关重要。
针对管道防腐问题,设计了以下方案,旨在提供一种高效、可持续、环保的管道防腐油漆方案。
二、方案内容1.材料选择选择具有优良防腐性能的材料,确保对管道表面的保护效果。
常见材料有环氧油漆、聚氨酯油漆、聚酯油漆等。
2.表面处理确保管道表面光洁、无油污和锈蚀,为油漆涂层提供良好的附着力。
可以采用砂纸、喷砂、电动刷洗等方式进行表面处理。
3.涂装工艺(1)底漆涂装:使用合适的底漆对管道进行涂装,提供较好的附着力和防腐性能。
(2)面漆涂装:在底漆完全干燥后,采用合适的面漆对管道进行涂装,提供美观的外观和附着力。
(3)涂装方法:可以采用刷涂、喷涂等方法进行涂装,确保涂层均匀和致密。
4.防腐层检测对涂层进行定期检测,确保涂层的防腐性能良好。
可以采用刮擦法、电位法等方法进行检测。
5.环境保护选择无污染、低挥发、无重金属的防腐油漆,减少对环境的影响。
在涂装过程中,做好防护措施,避免油漆的溅落和污染。
6.安全操作在涂装过程中,必须严格遵守操作规程,采取安全措施,防止火灾和中毒等事故的发生。
对于有毒有害的油漆,操作人员必须佩戴相应的防护设备。
三、方案优势和预期效果1.高效:采用优良的防腐油漆材料和先进的涂装工艺,使涂层的防腐性能更为出色,延长管道的使用寿命。
2.可持续:选用环保的防腐油漆,减少对环境的污染,并进行定期检测和维护,确保涂层的防腐性能。
3.美观:涂装过程中,使用合适的面漆,使管道具有良好的外观,提高整体美观度。
4.安全:严格遵守操作规程,采取安全措施,避免火灾和中毒等事故的发生。
以上是一种针对管道防腐油漆方案的概述,根据具体情况,可以进一步详细制定方案,并根据实际需求进行调整和优化。
SHY-99专用防腐涂料介绍
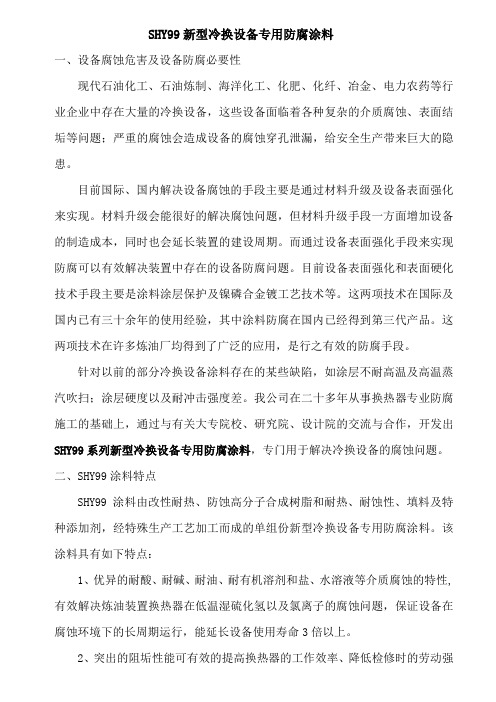
SHY99新型冷换设备专用防腐涂料一、设备腐蚀危害及设备防腐必要性现代石油化工、石油炼制、海洋化工、化肥、化纤、冶金、电力农药等行业企业中存在大量的冷换设备,这些设备面临着各种复杂的介质腐蚀、表面结垢等问题;严重的腐蚀会造成设备的腐蚀穿孔泄漏,给安全生产带来巨大的隐患。
目前国际、国内解决设备腐蚀的手段主要是通过材料升级及设备表面强化来实现。
材料升级会能很好的解决腐蚀问题,但材料升级手段一方面增加设备的制造成本,同时也会延长装置的建设周期。
而通过设备表面强化手段来实现防腐可以有效解决装置中存在的设备防腐问题。
目前设备表面强化和表面硬化技术手段主要是涂料涂层保护及镍磷合金镀工艺技术等。
这两项技术在国际及国内已有三十余年的使用经验,其中涂料防腐在国内已经得到第三代产品。
这两项技术在许多炼油厂均得到了广泛的应用,是行之有效的防腐手段。
针对以前的部分冷换设备涂料存在的某些缺陷,如涂层不耐高温及高温蒸汽吹扫;涂层硬度以及耐冲击强度差。
我公司在二十多年从事换热器专业防腐施工的基础上,通过与有关大专院校、研究院、设计院的交流与合作,开发出SHY99系列新型冷换设备专用防腐涂料,专门用于解决冷换设备的腐蚀问题。
二、SHY99涂料特点SHY99涂料由改性耐热、防蚀高分子合成树脂和耐热、耐蚀性、填料及特种添加剂,经特殊生产工艺加工而成的单组份新型冷换设备专用防腐涂料。
该涂料具有如下特点:1、优异的耐酸、耐碱、耐油、耐有机溶剂和盐、水溶液等介质腐蚀的特性,有效解决炼油装置换热器在低温湿硫化氢以及氯离子的腐蚀问题,保证设备在腐蚀环境下的长周期运行,能延长设备使用寿命3倍以上。
2、突出的阻垢性能可有效的提高换热器的工作效率、降低检修时的劳动强度减少了非计划性停工造成的经济损失。
3、独特的耐高温性能保证了涂层在置换扫线时,可通过240℃·10kg高温蒸汽24小时吹扫,涂层完好无损。
4、良好的导热性能保证了稳定的换热效果,提高了换热设备运行状态物理指标:耐腐蚀指标适用范围及年限1.适用于石油炼制、石油化工、化纤、化肥、氯碱、发电、冶金、食品、制药等行业生产所需的冷凝器、油冷器、换热器、空冷器、贮冷器、凝汽器及压力容器的腐蚀防护。
- 1、下载文档前请自行甄别文档内容的完整性,平台不提供额外的编辑、内容补充、找答案等附加服务。
- 2、"仅部分预览"的文档,不可在线预览部分如存在完整性等问题,可反馈申请退款(可完整预览的文档不适用该条件!)。
- 3、如文档侵犯您的权益,请联系客服反馈,我们会尽快为您处理(人工客服工作时间:9:00-18:30)。
附着力 A 级 SY/T 0544—2010 331 涂层完好 JY/T 014 GB/T 9274—1988
耐油田污水煮(100℃,4200h)
模拟罗家寨气田水脱氧溶液(90℃, 漆膜不起泡、 总压 32MPa,H2S 分压 3.2 MPa, CO2 分压 3.2 MPa,168h) 不脱落, 附着力≤ 2 级 GB/T 9274—1988
耐碱性(20%NaOH,70℃,1100h) 涂层完好
酚醛树脂具有较好的耐温性能常被用作黏合剂, 因其固有的脆性大的缺点如用于涂料工业需要进行改 性以提高漆膜的耐冲击性、机械强度、尺寸稳定性等。 不同化合物改性得到的酚醛树脂性能差别较大:聚乙 烯醇缩醛改性酚醛树脂增强了材料的机械强度,但降 低了耐热性;聚酰胺改性酚醛树脂提高材料的耐冲击 性同时保持了酚醛树脂的优点(良好的耐酸性能、机 械性能、耐热性能);环氧改性酚醛树脂既提高了材 料机械性能,又提高了耐温性;有机硅改性酚醛树脂 有效提高了材料的机械性能和耐温性,与环氧树脂共 聚反应后增强了材料的耐化学介质腐蚀性能。 实验选用有机硅改性酚醛树脂与环氧树脂高温共 聚反应,研究了 A、B 两种环氧树脂不同比例对涂料及 涂层性能的影响,测试了涂料的力学强度、耐温性及 耐化学品性能。实验结果见表 3。 表 3 环氧树脂 A 与 B 不同配比条件下涂层的性能
近年来,油管的防腐蚀已引起国内外油田和防腐 界的高度重视,相继形成使用耐蚀合金管材、涂镀层 管材等系列防腐蚀技术措施。以 AMF-Tuboscope 和 PA 公司为代表自 20 世纪 80 年代开始研究油管涂料,已 经形成系列化油管涂料,销售量占国际市场的 90% 以 上,国内市场售价高于 180 元 /kg。上海图博科特石油 管道涂层有限公司研发出性能接近国外公司的油管涂 料,已在国内各油田推广应用,价格在 150 元 /kg 左 右,中国石油集团海洋工程有限公司通过酚醛树脂与 环氧树脂的交联技术,改性耐磨填料和硬质填料的最 佳配比,研制出 YG 油管防腐蚀涂料。经过室内实验和 现场应用表明,施工工艺简单,在抗 H2S、CO2 性能方 面优于所检索到的同类产品,价格低于国内同类产品 40%,实用性较强。
2015 年增刊·石油科技论坛 133
自主创新重要产品
表 2 油管防腐蚀涂料的性能测试
检测项目 耐冲击(J) 抗弯曲(常温,2.5°) 附着力(MPa) 耐磨性(L/mm) 耐盐雾性(8500h) 高温高压(70MPa,180℃, pH=12.5,24h) 热分解温度(℃) 测试结果 12.5 无裂纹 13.6 3.6 涂层完好 检验标准 SY/0315—2005 SY/T 0315—2005 GB/T 5210—2006 ASTMD968 GB/T 1771—2007
段绍明 等:YG 油管防腐蚀涂料
YG 油管防腐蚀涂料
段绍明 张丽萍 张其滨 韩忠智 郭晓军 刘杨宇 中国石油集团海洋工程有限公司天津中油渤星工程科技有限公司
摘 要:为改变我国高性能油管防腐涂料主要依赖国外进口局面,针对国内油气田井下管材腐蚀因素,参考进口 油管防腐涂料性能,开发出适应于涂敷作业线的高性能溶剂型 YG 油管防腐蚀涂料。由高玻璃化温度的双酚 A 环氧树 脂和改性酚醛树脂在加热条件下进行反应形成耐温高分子聚合物作为成膜物,采用经过硅烷偶联剂处理的超细硅微粉 等耐磨填料,提高涂层致密性、附着性及耐磨性。涂层在高温高压试验(180℃,70MPa)中,pH 值为 12.5 碱性介质 中浸泡 24h,涂层无裂纹、鼓泡、脱落等现象,热分解温度不小于 260℃,满足了酸性油气田油管防腐蚀要求。 关键词:油管涂料;环氧;树脂酚醛;防腐蚀;高温高压;耐磨性 DOI:10.3969/j.issn.1002-302x.2015.z1.040 中图分类号:TQ630.7 文献标识码:A
外不同厂家的 4 个型号产品,与环氧树脂 A 加热共聚 形成了成膜物,测试涂层性能,实验结果见表 4。 表 4 不同厂家有机硅改性酚醛树脂涂层性能
酚醛 树脂 F-A F-B F-C F-D 剪切强度 (MPa) 6.1 8.3 8.8 7.8 抗弯曲 (2.5°) 开纹 无裂纹 无裂纹 有裂纹 耐冲击 (cm) 30 50 50 45 耐土酸 (h) 780 1000 1200 850 耐油田污水 (h) 3600 4000 4400 3800
等混合溶剂加入反应釜内搅拌加热溶解后加入改性硅 微粉、沉淀硫酸钡等颜料和助剂,高速搅拌 0.5h 后研 磨至细度小于 80m m,加入改性酚醛树脂分散均匀后制 成涂料的基料;使用时将基料直接涂覆在基材表面后 升温加热至 150℃,后降温至室温时涂覆第二道漆膜, 再升温加热固化直至 210℃,保温 1h。具体实验参考 配方见表 1,性能测试指标见表 2。 表 1 YG 油管防腐蚀涂料参考配方
ห้องสมุดไป่ตู้
2 试验结果及研究
2.1 耐温成膜树脂研究
环氧树脂的玻璃化温度越高,涂层在固化后的机 械强度越大、耐温性越高,但同时涂层交联密度低, 耐化学腐蚀性下降,综合考虑油管涂料的使用环境, 确定选用 A、B 两种环氧树脂进行复配。
基金项目:中国石油天然气集团公司项目 “低成本油管防腐涂料及涂层技术研究”。 获专利情况:“耐酸碱腐蚀的油管涂料及制造方法”(专利号:200610078244.7)、“抗硫化氢腐蚀的油管涂料及制造方法”(专 利号:200610078245.1)获国家发明专利;“抗硫化氢腐蚀涂层的钻井油管”(专利号:200620018267.4)获国家实用新型专利。 第一作者简介:段绍明,1970 年生,毕业于中国石油大学应用化学专业,高级工程师,目前从事防腐保温技术研究。电话: 022-66310067,E-mail:duanshm@
原材料名称 A 环氧树脂 B 环氧树脂 改性酚醛树脂 颜填料 助剂 混合溶剂 质量(kg) 40~60 60~80 50~60 130~150 12~20 80~150
1 制备实验与性能测试
YG 油管防腐蚀涂料利用改性酚醛树脂与高玻璃化 温度的双酚 A 型环氧树脂在高温下交联反应,形成具 有耐高温的高分子化合物,由超细硅微粉等耐磨填料、 助剂等组成的单组分烘烤型防腐蚀涂料,形成的涂层 在高温环境下具有较高的附着力、致密性及耐磨性, 防腐蚀性能良好。 将环氧树脂 A、环氧树脂 B、丙二醇苯醚、环己酮